ARI PALTRA-V User manual

Rev. 0040330000 1423 english (englisch) - Translated original instructions -
1.0 General information on operating instructions 2-2
2.0 Notes on possible dangers ................................ 2-2
2.1 Significance of symbols ............................................. 2-2
2.2 Explanatory notes on safety information .................... 2-2
3.0 Storage and transport ........................................ 2-3
4.0 Description .......................................................... 2-4
4.1 Area of application ...................................................... 2-4
4.2 Operating principles.................................................... 2-4
4.3 Diagram and parts list................................................. 2-5
4.3.1 Wafer type ................................................................ 2-5
4.3.2 Double flanged ......................................................... 2-6
4.3.3 Manual gear.............................................................. 2-6
4.4 Technical data – remarks............................................ 2-6
4.5 Kennzeichnung........................................................... 2-7
5.0 Installation ........................................................... 2-8
5.1 General remarks on installation.................................. 2-8
5.2 Installing wafer type valves (Fig. 501) ........................ 2-9
5.3 Installing flanged valves (Fig. 502)........................... 2-10
5.4 Installing additional modules and piping elements ... 2-10
5.5 Requirements at the place of installation.................. 2-10
5.6 Installation requirements for setting up and
dismantling actuators ................................................ 2-10
6.0 Putting the valve into operation .......................2-11
7.0 Care and maintenance...................................... 2-12
7.1 Manual gear ..............................................................2-13
7.1.1 Removal and installation .........................................2-13
7.2 Electric actuator removal and installation (AUMA SA).. 2-13
7.3 Electric actuator adjustment......................................2-14
7.4 Other actuators..........................................................2-14
7.5 Tightening the stem seal ...........................................2-14
7.6 Replacing the stem seal ............................................2-15
7.7 Replacing the bottom cover gasket ...........................2-16
7.8 Replacing the seat ring..............................................2-16
7.8.1 Wafer type (Fig. 501)...............................................2-16
7.8.2 Double flanged (Fig. 502)........................................2-17
7.9 Tightening torques ....................................................2-18
8.0 Troubleshooting ................................................ 2-18
9.0 Troubleshooting table ...................................... 2-19
10.0 Dismantling the valve and the actuation
arrangement .................................................... 2-20
11.0 Warranty / Guarantee ...................................... 2-20
Operating and installation instructions
In accordance with EC Directive 2014/68/EU on Pressure Equipment
In accordance with EC Directive 2006/42/EC on Machinery
Segmented ball valve PALTRA®-V
Contents
BR 501 - PALTRA®-V BR 502 - PALTRA®-V

Page 2-2 Rev. 0040330000 1423 - Translated original instructions -
Operating and Installation Instructions
PALTRA®-V
1.0 General information on operating instructions
These operating instructions provide information on mounting and maintaining the valves.
Please contact the supplier or the manufacturer in case of problems which cannot be
solved by reference to the operating instructions.
They are binding for transport, storage, installation, start-up, operation, maintenance and
repair.
You must read the operating instructions before putting the valve into operation.
The notes and warnings must be observed and adhered to.
Handling and all other work must be carried out by expert personnel or all activities super-
vised and checked.
It is the owner’s responsibility to define areas of responsibility and competence and to
supervise personnel.
In addition, current regional safety requirements must be applied and observed when taking
the valves out of service as well as when maintaining and repairing them.
The manufacturer reserves the right to introduce technical modifications or improvements
at any time.
These operating instructions comply with the requirements of EU Directives.
2.0 Notes on possible dangers
2.1 Significance of symbols
2.2 Explanatory notes on safety information
In these operating and installation instructions dangers, risks and items of safety informa-
tion are highlighted to attract special attention.
Information marked with the above symbol and “ATTENTION ! ” describe practices, a fail-
ure to comply with which can result in serious injury or danger of death for users or third
parties or in material damage to the system or the environment. It is vital to comply with
these practices and to monitor compliance.
All other information not specifically emphasised such as transport, installation, operating
and maintenance instructions as well as technical data (in the operating instructions, prod-
uct documentation and on the device itself) must also be complied with to the fullest extent
in order to avoid faults which in turn can cause serious injury to persons or damage to prop-
erty.
ATTENTION !
. . . Warning of general danger.

- Translated original instructions - Rev. 0040330000 1423 Page 2-3
Operating and Installation Instructions
PALTRA®-V
3.0 Storage and transport
- Storage at -20°C to +65°C.
- During storage, the valves must be protected against impurities.
- Avoid storage outdoors exposed to the effects of rain, sunlight or frost.
- The paint is a base coat to protect against corrosion during transport and storage. Do not
damage paint protection.
ATTENTION !
- Protect against external force (like impact, vibration, etc.).
- Valve mountings such as actuators, handwheels, hoods must not be used to
take external forces, e.g. they are not designed for use as climbing aids or as
attachment points for lifting gear.
- Suitable materials handling and lifting equipment should be used.
See technical data sheet for weights.
Fig. 1: Fig.501 Fig. 2: Fig.502

Page 2-4 Rev. 0040330000 1423 - Translated original instructions -
Operating and Installation Instructions
PALTRA®-V
4.0 Description
4.1 Area of application
Valves are used for „controlling the flow of liquids, gases and vapours in chemical and other
processing plants and for plant engineering“.
It is the responsibility of the machine planner / owner to ensure compliance.
The special markings on the valve must be taken into account.
Refer to the technical data sheet to see which materials are used in standard versions.
Please contact the supplier or the manufacturer if you have any questions.
4.2 Operating principles
The valve is closed by turning the actuator stem.
The stem moves through 90°.
The position of the segmented ball can be determined from the mark on the shaft end face
when the actuator is dismantled (marking groove points in the direction of the control open-
ing).
ATTENTION !
- Refer to the technical data sheet for applications, limits on use and possibilities.
In particular, you must check the material stability.
- Certain media require or preclude the use of special materials.
- The valves are designed for standard operating conditions. If conditions exceed
these requirements, e.g. aggressive or abrasive media, the owner should state
the higher requirements when ordering.
- Careful selection and sizing of the valve based on the anticipated operating
conditions is essential for low-noise, low-vibration operation.
- You must state whether the valves are to be used in explosive atmosphere
(ATEX) when ordering.
(Special version owing to the marking / design)
- As a general rule, we recommend that you do not install valves immediately
downstream from pipe bends or tees. Particularly with control applications, you
should allow a section equivalent to at least 2 x DN before and 6 x DN after the
valve in accordance with DIN EN 60534.
ATTENTION !
- The actuator stem is partially open and there is a crushing hazard

- Translated original instructions - Rev. 0040330000 1423 Page 2-5
Operating and Installation Instructions
PALTRA®-V
4.3 Diagram and parts list
Refer to the technical data sheet for information about materials with designations and fig-
ure numbers.
4.3.1 Wafer type
Fig. 3:Segmented ball valve PALTRA®-V BR 501
No. Description
1 Body
2 Clamping ring
3 Segmented ball with V-cut
4Stem
5Pivot
6 Packing box flange
7 Gland follower
8 Subshaft cover
9/10 Back-up-ring
11 Bearing strip
12/13 Axial-washer
14 Disc spring
15/16 Gasket
17 Gasket
18 Box packing
19 O-ring
20 Thread pin
21 Stud
22 Socket screw
24 Hexagon nut
25 Seat ring
27 Back-up-ring
28 Gasket
29 Key
30 Mounting bracket
1
2
3
4
5
6
7
8
9
10
11
12
13 14 17
18
19
21
22
24 29 30

Page 2-6 Rev. 0040330000 1423 - Translated original instructions -
Operating and Installation Instructions
PALTRA®-V
4.3.2 Double flanged
4.3.3 Manual gear.
4.4 Technical data – remarks
Fig. 4: Segmented ball valve PALTRA®-V BR 502
No. Description
1 Body
2 Housing flange
3 Segmented ball with V-cut
4Stem
5Pivot
6 Packing box flange
7 Gland follower
8 Subshaft cover
9/10 Back-up-ring
11 Bearing strip
12/13 Axial-washer
14 Disc spring
15/16 Gasket
17 Gasket
18 Box packing
19 O-ring
20 Hexagonal screw
21 Stud
22 Socket screw
24 Hexagon nut
25 Seat ring
27 Back-up-ring
28 Gasket
29 Key
30 Mounting bracket
Fig. 5: Gear PALTRA®-V
- Gear (operated using handwheel, clockwise rotation closes)
The CLOSED position can be adjusted to ± 5° using an adjustable end stop screw.
The screws are self-sealing and self-locking.
- Refer to the separate operating and maintenance instructions of the manufacturers for
actuators (electric, pneumatic or hydraulic).
1
2
3
4
5
6
7
8
9
10
11
12
13 14 17
18
19
20
21
22
24
2930
End stop screw CLOSED End stop screw OPEN
Position indicator
Lock nut

- Translated original instructions - Rev. 0040330000 1423 Page 2-7
Operating and Installation Instructions
PALTRA®-V
For example
- Principal dimensions,
- Pressure-temperature ratings, etc. refer to the technical data sheet.
4.5 Marking
The name plate of the valve is attached either to the body (Fig. 501) or to the flange (Fig.
502).
Fig. 6 : Name plate
No. Value
1 Figure / Product
2 Nominal pressure [PN]
3 Nominal diameter [DN]
4 Manufactured by ARI-Armaturen / Högfors /
5CEmarking
6 Notified body [0496]
7 Serial number [SN]
8 Year of manufacture [JJJJ]
12 Marking at approval
13 QR-Code marking [ARI-ID]
15 Kvs-value [Kvs]
16 min. permissible temperature [t min]
17 max. permissible temperature [t max]
18 max. permissible differential pressure [Δp]
19 Sealing element
Manufacturer’s address: See section “ Pkt 11.0 Warranty / Guarantee"
HÖGFORSHÖGFORS
SALO FINSALO FIN

Page 2-8 Rev. 0040330000 1423 - Translated original instructions -
Operating and Installation Instructions
PALTRA®-V
5.0 Installation
5.1 General remarks on installation
The following points should be taken into account in addition to the general principles gov-
erning installation work:
ATTENTION !
- Remove flange covers if present.
- Connection flanges must mate exactly.
- Clean the pipework carefully before installing the valve. The interior of the valve
and the pipeline must be free of foreign particles, as these could damage the
valve’s shut-off surfaces.
- The installation position should be selected so that the flow approaches the
valve from the segmented ball side. The maximum differential pressure must be
observed (see technical data sheet).
- Steam line systems should be designed to prevent water accumulation.
- Install pipelines so that damaging transverse, bending and torsional forces are
avoided.
- Do not install the valve close to a pump or a curved pipe section due to the
turbulent flow that they cause. There must be as little turbulence as possible in
the flow at the valve.
- The pipes must be provided with appropriate support. An inadequately
supported section of pipework will cause excessive stress on the valve,
possibly resulting in leakage from the shut-off surfaces.
- Pipework temperature variations will cause thermal contractions and
expansions which must be allowed to occur freely, for example with the aid of
bellows expansion joints. Without these or other similar solutions, pipework
expansions will excessively burden the joints.
- Protect valves from dirt during construction work.
- Valve mountings such as actuators, handwheels, hoods must not be used to
take external forces, e.g. they are not designed for use as climbing aids or as
attachment points for lifting gear.
- Flooding of the valve is not permissible.
- Suitable materials handling and lifting equipment should be used for assembly
work. During assembly work, ensure that the valve is fixed adequately.
See technical data sheet for weights.
- The preferred installation position relative to the stem direction is horizontal.
- The unmounted valve may only be operated if all safety precautions are
observed. Crushing hazard!
- When installed vertically, large actuators must be supported.
- Avoid mechanical damage to the seat during transport, storage and installation.
- Protect actuators from excessive ambient temperatures; refer to the operating
instructions for the actuators.
- With actuators mounted, you must disconnect the power supply before starting
work.
- The valve should be installed in the open position.

- Translated original instructions - Rev. 0040330000 1423 Page 2-9
Operating and Installation Instructions
PALTRA®-V
- Planners / construction companies or the owner are responsible for positioning and
installing products.
- The valves are designed for deployment in systems that are not affected by the weather.
- For applications outdoors or in adverse conditions like corrosive environments (seawater,
chemical vapours, etc.), special designs or protective measures are recommended.
- The valves are not approved for subsurface installation.
5.2 Installing wafer type valves (Fig. 501)
- Please check the type of neck-welded flange in the Production Card.
- Make sure that mounting shims totally cover contact surfaces.
- During installation make sure that flanges and shims are coaxial and parallel to each
other.
- The segmented ball must be in the closed position during installation.
- Check that there are no obstructions inside the valve before installation.
Installation order.:
Preassemble the unit comprised of the valve, mounting shims and flanges. Secure it using
a few of the bolts but tighten them only slightly.
Tack-weld the preassembled unit to the pipeline.
Remove the valve and the mounting shims from the pipeline, then weld the flanges all
around the perimeter.
Insert the valve and tighten the stud bolts evenly in crosswise sequence.
ATTENTION !
- The sealing element (25 and possibly also 15/16) between the counter flange and
the body (Fig. 7 + Fig. 8) is pressed tightly via the bolts of the flanges. This must
be taken into account when determining the bolt tightening torques required for
operational tightness.
Fig. 7: Seat ring TC (PTFE) Fig. 8: Seat ring KC (Stellite)
27
28
25
15
16
25

Page 2-10 Rev. 0040330000 1423 - Translated original instructions -
Operating and Installation Instructions
PALTRA®-V
5.3 Installing flanged valves (Fig. 502)
- Preassemble the unit comprised of the valve, flanges and flange gaskets using between 4
and 6 studs. Be careful not to tighten the studs too tight on the nuts.
- Make sure that all parts are coaxial and parallel to each other.
- Assemble and tighten the valve with the remaining fasteners.
- After installing the valve, make sure that it will not be under excessive stress and that the
flanges are parallel and coaxial to each other. The valve may only be pressurised after the
flanges have been completely installed. Incorrect installation could result in leakage or
damage to the sealing elements.
5.4 Installing additional modules and piping elements
Optional accessories (limit switches, etc.) that are supplied with valves must be fitted as
required for their functions as shown in the system plan.
If piping elements are supplied with the product by the manufacturer or enclosed with the
valves, the system owner must ensure that they are operated safely under reasonably fore-
seeable conditions and in compliance with limit values. Protective measures must be imple-
mented based on a hazard analysis in accordance with DIN EN 16668:2016, 5.1.3
“Protection against exceeding the allowable limits”. If the nature or conditions of the
intended use, including all foreseeable circumstances, are such that protective measures
are necessary (e.g. to prevent inadmissible pressure increases), the manufacturer should
be notified immediately. The system owner is thus personally responsible for ensuring
operational safety.
5.5 Requirements at the place of installation
The place of installation should be easily accessible and provide ample space for mainte-
nance as well as for removing the actuators. The valve should preferably be installed hori-
zontally with the actuator at the side. Inclined or horizontal installation without supports is
only permissible with lightweight actuators.
Permissible actuator weights for unsupported valves installed horizontally relative to the
stem:
35 kg for DN 80 - 100
40 kg for DN 125 - 150
55 kg for DN 200 - 250
65 kg for DN 300
The pipes must be lagged to protect the actuators from excessive heat. Sufficient space
must be allowed for maintaining the stem seal.
5.6 Installation requirements for setting up and dismantling actuators
Normally, valves are supplied complete with the actuator fitted. It is not permitted to set up
or dismantle actuators with valves operating at the service temperature and pressure. The
actuators must be installed as described in the operating instructions for conversion or
maintenance.
When connecting the electric actuators, you must comply with the specifications of the Low
Voltage Directive. Connection (grounding) of electric actuators must only be carried out by
qualified personnel.

- Translated original instructions - Rev. 0040330000 1423 Page 2-11
Operating and Installation Instructions
PALTRA®-V
6.0 Putting the valve into operation
- Flush the pipelines thoroughly after installation.
- Check the valve for damage / defects due to transportation and handling.
- Ensure that no cavitation occurs. Prolonged operation under cavitation conditions can
cause parts of the valve to be eroded and destroyed.
- It is not recommended to use the first and last 10% of the segmented ball total travel
distance in control applications.
- After prolonged operation in a small opening position (5°-15°), the segmented ball should
be adjusted to a wider angle (25°-30°) before closing in order to flush and clean the seat
surface. At smaller opening angles, the debris from the pipeline could stick or collect
between the valve body and the segmented ball.
- Always close the valve using the actuator’s mechanical end stops; be careful not to
exceed the maximum torque limit.
- A valve fitted with an electric actuator must always be opened electrically, with the
end stop serving as the closing limit. You can open and close the segmented ball in
an emergency by turning the handwheel of the electric actuator.
• In these cases, however, note that the handwheel’s end stop has been set to turn the
valve disc 2 or 3 revolutions beyond the optimal closed position. This means that
optimal tightness is achieved by turning the handwheel back 2 or 3 revolutions in the
opening direction from the gear’s mechanical closing limit.
When putting the valve into operation, check that the box packing (18) is tight. If leakage
occurs from the stem (4), you should tighten the box packing (18) slowly and evenly with
hexagonal screws (20) or hexagon nuts (24) until there is no more leakage (see also sec-
tion 7.0 Care and maintenance).
ATTENTION !
- Before putting the valve into operation, check the material, pressure, tempera-
ture and direction of flow.
- Regional safety instructions must be adhered to.
- Residues in piping and valves (dirt, weld beads, etc.) inevitably lead to leakage
and / or damage.
- Touching the valve when it is operating at high (> 50°C) or low (< 0°C) media
temperatures can cause injury.
Affix a warning notice or provide protective insulation as appropriate!
- To prevent hydraulic jerks with a liquid medium, you must not slam valve
closed. If necessary, chokes or dampers must be fitted.
Before putting a new plant into operation or restarting a plant after repairs or
modification, always make sure that:
- All work has been completed correctly.
- The valve is in the correct position for its function.
- Safety devices have been attached.

Page 2-12 Rev. 0040330000 1423 - Translated original instructions -
Operating and Installation Instructions
PALTRA®-V
7.0 Care and maintenance
PALTRA®-V segmented ball valves are durable and reliable. A correct and professional,
appropriately selected and carefully installed valve will not require maintenance during its
life cycle.
Leakage from the seat ring is often caused by wear and tear, pipework impurities or dam-
age resulting from pressure impacts. Impurities can be removed by opening the segmented
ball and allowing the flow to flush the shut-off surfaces clean.
The probability of hydro-stress can be reduced to a minimum by using bypass valves.
The scope of maintenance and repair work consists of:
- Cleaning internal surfaces
- Replacement of the seat ring
- Tightening or replacement of the stem seal
- Replace pivot seal
It is possible to carry out this work when the valve is installed provided the pipeline is not
under pressure. The valve must be removed from the pipe for all other repair work.
The owner must define maintenance and maintenance intervals to meet requirements.
ATTENTION !
- We recommend actuating the valve at least once a month.
- If leakage occurs from the stem (4), you should tighten the box packing (18)
slowly and evenly with hexagon nut (24) until there is no more leakage.
ATTENTION !
- Always ensure that the lubricant is compatible with the medium.
- You are only allowed to replace the seat ring (25) after the system has cooled
down and is depressurised.
- Before dismantling the valve, refer to section 10.0.
- When operating the valve, there is a risk of crushing between the segmented
ball and the body.
- Only carry out maintenance work in the piping if the segmented ball valve is
secured against operation (actuator disconnected from the mains and secured
against reconnection).

- Translated original instructions - Rev. 0040330000 1423 Page 2-13
Operating and Installation Instructions
PALTRA®-V
7.1 Manual gear
7.1.1 Removal and installation
Avoid dismantling the manual gear from the valve. The manual gear was adjusted at the
factory such that no leakage occurs from the valve. If you dismantle the manual gear, this
adjustment must be repeated.
Work steps – removal:
- Turn the segmented ball (3) to the “closed” position.
- Mark the position of the manual gear in relation to the valve.
- Unscrew the bolts for the gear at the valve and remove the gear.
- Remove the keys (29)
Work steps – installation:
- Install the manual gear with the segmented ball in the “closed” position. Make sure that the
manual gear is in the “closed” position as well.
- Insert the keys (29).
- Install the manual gear in its original position. Bolt the manual gear to the valve. Tighten
the bolts evenly in crosswise sequence. Apply locking agent to the threads.
- Adjust the manual gear as instructed in section 7.2.
7.2 Electric actuator removal and installation (AUMA SA)
Avoid dismantling the actuator from the valve. The actuator was adjusted at the factory
such that no leakage occurs from the valve. If you dismantle the actuator, this adjustment
must be repeated.
Work steps – removal:
- Turn the segmented ball to the “closed” position.
- Switch off the power supply to the actuator.
- Loosen the actuator bolts and remove the actuator.
- It may be necessary to remove the actuator coupling piece, for example when replacing
the stem seal.
• In this case, mark the height of the coupling piece on the stem (4).
• Loosen the locking screw and pull the coupling piece off of the stem.
- Remove the keys (29).
Work steps – installation:
- Install the manual gear with the segmented ball in the “closed” position. Make sure that the
actuator is in the “closed” position as well.
- Insert the keys (29).
ATTENTION !
- Before starting maintenance work, you must depressurise the piping system.
Ignoring these regulations can put your life at risk and damage the piping
system.
ATTENTION !
- Before starting maintenance work, you must depressurise the piping system.
Ignoring these regulations can put your life at risk and damage the piping
system.

Page 2-14 Rev. 0040330000 1423 - Translated original instructions -
Operating and Installation Instructions
PALTRA®-V
- If necessary, attach and lock the actuator coupling piece at its original height on the
stem (4).
- Mount the actuator to the valve. Bolt the actuator to the valve. Tighten the bolts evenly in
crosswise sequence. Apply locking agent to the threads.
- Adjust the actuator as instructed in section 7.2.
7.3 Electric actuator adjustment
- Use the actuator handwheel to move the segmented ball into the half-open position.
- Check that the segmented ball moves in the right direction when the switches are
actuated.
- For detailed instructions concerning the actuator’s adjustment, see the manual supplied
with the actuator.
- The actuator is correctly adjusted if all conditions in the following checklist are met:
• The limit switch for the “closed” position must stop the disc from turning when the disc
is parallel to the shim. You can check that the disc’s position is correct by measuring the
distance “X” (Fig. 22). This distance must be equal on both sides of the disc.
• The torque switches are adjusted to the values specified by the valve manufacturer
(contact the valve supplier or manufacturer for details).
• The mechanical stop for the “open” position has been set to turn the actuator’s
handwheel 2 to 4 revolutions beyond the “open” position of the limit switch until contact
with the stop.
• The limit switch for the “open” position must stop the disc from turning when the
segmented ball is at 90° to the shim. There is a free gap of 2 to 5 handwheel
revolutions between the limit switch and the mechanical stop.
7.4 Other actuators
For detailed instructions concerning the actuator’s removal, installation and adjustment,
contact the supplier or manufacturer.
7.5 Tightening the stem seal
Tightening the stem seal is included in regular maintenance. Avoid excessive tightening.
The seal is sufficiently tight when no more leakage occurs.
The studs with associated hexagon nut are marked pos.20 and pos.24 in the diagrams and
parts lists (section 4.3).
ATTENTION !
- If any of the conditions in the above checklist are not met, the valve could be
damaged or the actuator blocked.

Page 2-15 Rev. 0040330000 1423 - Translated original instructions -
Operating and Installation Instructions
PALTRA®-V
7.6 Replacing the stem seal
To dismantle:
- Remove the actuator and the keys (29).
- Unscrew the hexagon nut (24).
- Remove the gland (6).
- Lift out shaft seal bushing (7).
- Remove the O-rings (19) from shaft seal
bushing (7).
- Remove the box packing (18).
To install:
- Carefully clean all surfaces. Prior to
commencing the installation work, check that
there are no sharp edges on the valve stem
that could damage the O-ring or the shim.
- Install the box packing (18) on the stem and
press it into place.
- Install the O-rings (19) on the shaft seal
bushing (7) and press them into place.
- Install the gland (6) and fasten it with the hexagon nuts (24).
- Install and adjust the manual gear or the actuator (see above).
ATTENTION !
- Before starting maintenance work, you must depressurise the piping system.
Ignoring these regulations can put your life at risk and damage the piping
system.
24
21
19
4
6
18
7
9
12
29
Fig. 9

Page 2-16 Rev. 0040330000 1423 - Translated original instructions -
Operating and Installation Instructions
PALTRA®-V
7.7 Replacing the bottom cover gasket
To dismantle:
- Unscrew the bottom cover bolts (22).
- Remove the subshaft cover (8) with the
bottom cover gasket (17) and the axial
washer (13) and disc spring (14).
To install:
- Carefully clean all surfaces.
- Insert the axial washer (13) with the
reinforcement mesh facing the subshaft
cover (8). Insert the back-up ring (10) and
the disc spring (14) above it as shown.
- Insert the subshaft cover (8) with the cover
gasket (17).
- Fasten the subshaft cover (8) with the
Socket screws (26).
7.8 Replacing the seat ring
The valve must be removed from the piping
prior to replacing the seat ring (25).
It is not necessary to remove the actuator in order to replace the seat ring.
The segmented ball must be moved into the “closed” position before starting the replace-
ment.
7.8.1 Wafer type (Fig. 501)
To replace the PTFE seal (TC):
- Unscrew the thread pins (20) and remove the counter flange (2).
- Remove the PTFE seal (25).
- Prior to installing new parts, carefully clean all surfaces of the body, segmented ball and
counter flange. Check the condition of sealing surfaces before starting the installation
work.
- Install the new PTFE seal. The segmented ball must be in the partially open position.
- Install the counter flange (2).
- Tighten the grub screws (20) alternately and evenly
To replace the stellited seal (KS):
- Unscrew the thread pin (20) and remove the counter flange (Pos. 2).
- Remove the shims (15, 16) and the seat ring (25). Note that the new shims must have the
same arrangement in terms of thickness as before the replacement.
- Prior to installing new parts, carefully clean all surfaces of the body, segmented ball and
counter flange. Check the condition of sealing surfaces before starting the installation
work.
- Keep the segmented ball in the “closed” position while replacing the seat ring.
ATTENTION !
- Before starting maintenance work, you must depressurise the piping system.
Ignoring these regulations can put your life at risk and damage the piping
system.
22
17
1
8
10
13
14
Fig. 10

Page 2-17 Rev. 0040330000 1423 - Translated original instructions -
Operating and Installation Instructions
PALTRA®-V
- Install the shims (15, 16) and the seat ring (25).
- Install the counter flange (2).
- Tighten the grub screws (20) alternately and evenly
7.8.2 Double flanged (Fig. 502)
To replace the PTFE seal (TC):
- Unscrew the hexagonal screw (20) and remove the housing flange (2).
- Remove the PTFE seal (25).
- Prior to installing new parts, carefully clean all surfaces of the body, segmented ball and
housing flange. Check the condition of sealing surfaces before starting the installation
work.
- Install the new PTFE seal. The segmented ball must be in the partially open position.
- Install the housing flange (2).
- Tighten all hexagonal screw (20) evenly in crosswise sequence.
To replace the stellited seal (KS):
- Unscrew the hexagonal screw (20) and remove the housing flange (2).
- Remove the shims (15.16) and the seat ring (25). Note that the new shims must have the
same arrangement in terms of thickness as before the replacement.
- Prior to installing new parts, carefully clean all surfaces of the body, segmented ball and
housing flange. Check the condition of sealing surfaces before starting the installation
work.
- Keep the segmented ball in the “closed” position while replacing the seat ring.
- Install the shims (15,16 and the seat ring (25).
- Install the housing flange (2).
Fig. 11: Arrangement PTFE seal

Page 2-18 Rev. 0040330000 1423 - Translated original instructions -
Operating and Installation Instructions
PALTRA®-V
- Tighten all hexagonal screw (20) evenly in crosswise sequence.
7.9 Tightening torques
8.0 Troubleshooting
In the event of malfunction or faulty operating performance check that the installation and
adjustment work has been carried out and completed in accordance with these Operating
Instructions.
If malfunctions cannot be eliminate with the help of the following table
“9.0 Troubleshooting table”, the supplier or manufacturer should be consulted.
M 8 = 20 (± 5) Nm
M 10 = 25 (± 5) Nm
M 12 = 45 (± 5) Nm
M 16 = 100 (± 5) Nm
-
ATTENTION !
- It is essential that the safety regulations are observed when identifying faults.
Fig. 12: Arrangement stellited seal

- Translated original instructions - Rev. 0040330000 1423 Page 2-19
Operating and Installation Instructions
PALTRA®-V
9.0 Troubleshooting table
ATTENTION !
- Read section 10.0 before carrying out installation and repair work!
- Read section 6.0 before recommissioning!
Fault Possible cause Corrective measures
No flow Valve closed Open the valve
Little flow Valve not sufficiently open Open the valve
Strainer screen clogged Clean / replace the screen
Piping system clogged Check the piping system
Valve is impossible or dif-
ficult to open or close
Service conditions (e.g. medium, tem-
perature) may be outside the specified
limits
Replace the valve. Consult the sup-
plier or manufacturer
Power failure Check the power supply
Actuator fault Overhaul the actuator or replace it
Wrong direction of rotation Turn in the correct direction (anti-
clockwise for opening)
Box packing (18) is too tight Loosen the hexagon nuts (24)
Solid matter is blocking the seg-
mented ball
Flush or clean the segmented ball
Key (29) on stem has sheared off Determine the cause and replace the
key (29)
Liquid has solidified between the
bearings
If possible, flush the bearings and the
stem via the flushing connections
Valve is leaking Segmented ball not completely closed Move the segmented ball into the
“closed” position
Solid matter is being deposited inside Move the segmented ball and flush
the valve in the open position
Mechanical end stop for closing is set
wrong
Readjust the end stop
Seat ring (25) or sealing surface on
segmented ball (3) is damaged
Replace the seat ring (25) (see sec-
tion 7.8) or regrind the segmented
ball contour (3)
Box packing (stem pack-
ing) is leaking
Fastening of box packing (18) is loose Tighten the hexagonal nuts (24)
evenly in small steps
Box packing (18) or O-ring (19) is
damaged
Replace the box packing (18) and the
O-ring (19), see section 7.6
Leakage at bottom cover
gasket
Socket screws (22) are loose Tighten the socket screws (22)
Bottom cover gasket (17) is damaged Replace the bottom cover gasket (17)

Page 2-20 Rev. 0040330000 1423 - Translated original instructions -
Operating and Installation Instructions
PALTRA®-V
10.0 Dismantling the valve and the actuation arrangement
11.0 Warranty / Guarantee
The extent and period of warranty cover are specified in the "Standard Terms and Condi-
tions of Albert Richter GmbH & Co. KG“ valid at the time of delivery or, by way of departure,
in the contract of sale itself.
We guarantee freedom of faults in compliance with state-of-the-art technology and the con-
firmed application.
No warranty claims can be made for any damage caused as the result of incorrect handling
or disregard of operating and installation instructions, technical data sheets and relavant
regulations.
This warranty also does not cover any damage which occurs during operation under condi-
tions deviating from those laid down by specifications or other agreements.
Justified complaints will be eliminated by repair carried out by us or by a specialist
appointed by us.
No claims will be accepted beyond the scope of this warranty. The right to replacement
delivery is excluded.
The warranty shall not cover maintenance work, installation of external parts, design modifi-
cations or natural wear.
Any damage incurred during transport should not be reported to us but rather to the compe-
tent cargo-handling depot, the railway company or carrier company immediately or else
claims for replacements from these companies will be invalidated.
ARI-Armaturen Albert Richter GmbH & Co. KG, D-33750 Schloß Holte-Stukenbrock
Telephone (+49 5207) 994-0 Telefax (+49 5207) 994-158 or 159
ATTENTION !
The following points must be observed:
- Pressureless piping system.
- Medium must be cool.
- Plant must be drained.
- Purge piping systems in case of caustic, inflammable, aggressive or toxic
media.
Table of contents
Other ARI Control Unit manuals
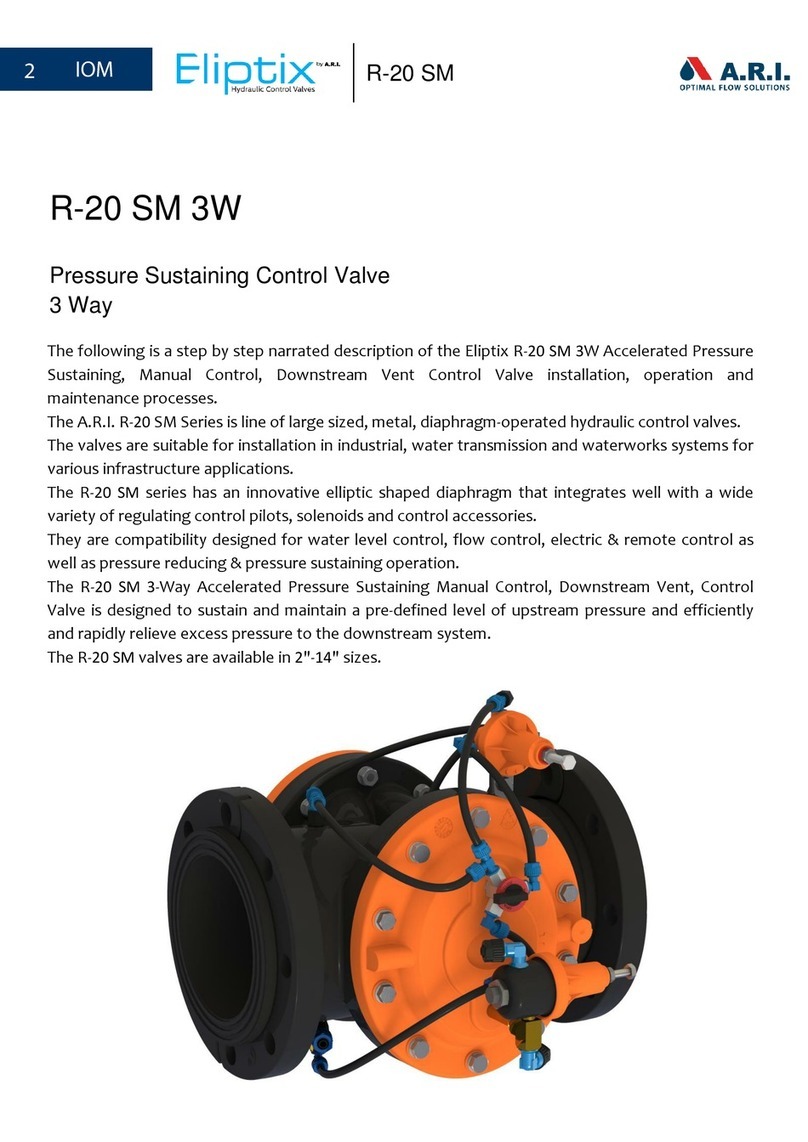
ARI
ARI Eliptix R-20 SM Series User manual

ARI
ARI S-050 Owner's manual

ARI
ARI D-040 Owner's manual

ARI
ARI VB-060 User manual
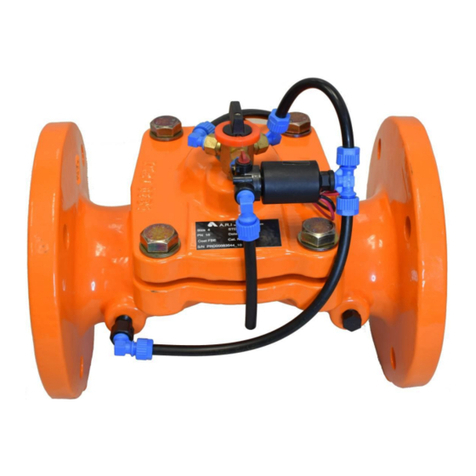
ARI
ARI Eliptix R-30ME User manual
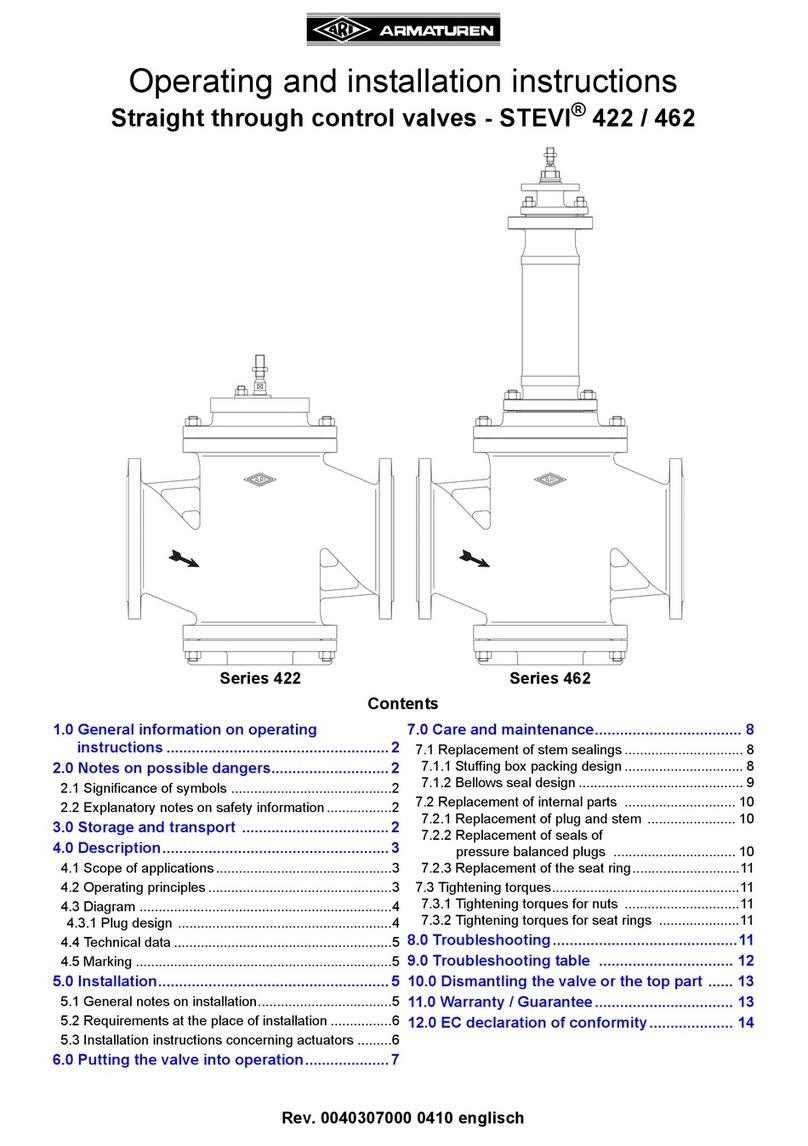
ARI
ARI Stevi 422 Series User manual
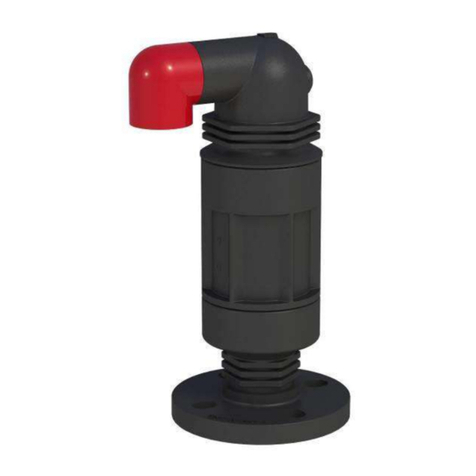
ARI
ARI D-040L Owner's manual
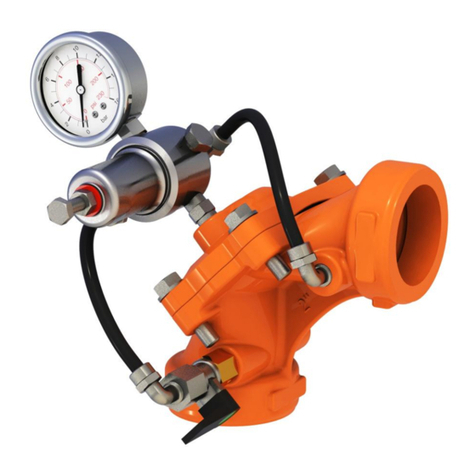
ARI
ARI Eliptix R-31 Q 2W User manual

ARI
ARI D-060 Installation and operating instructions

ARI
ARI Eliptix R-20-SM 3W User manual
Popular Control Unit manuals by other brands
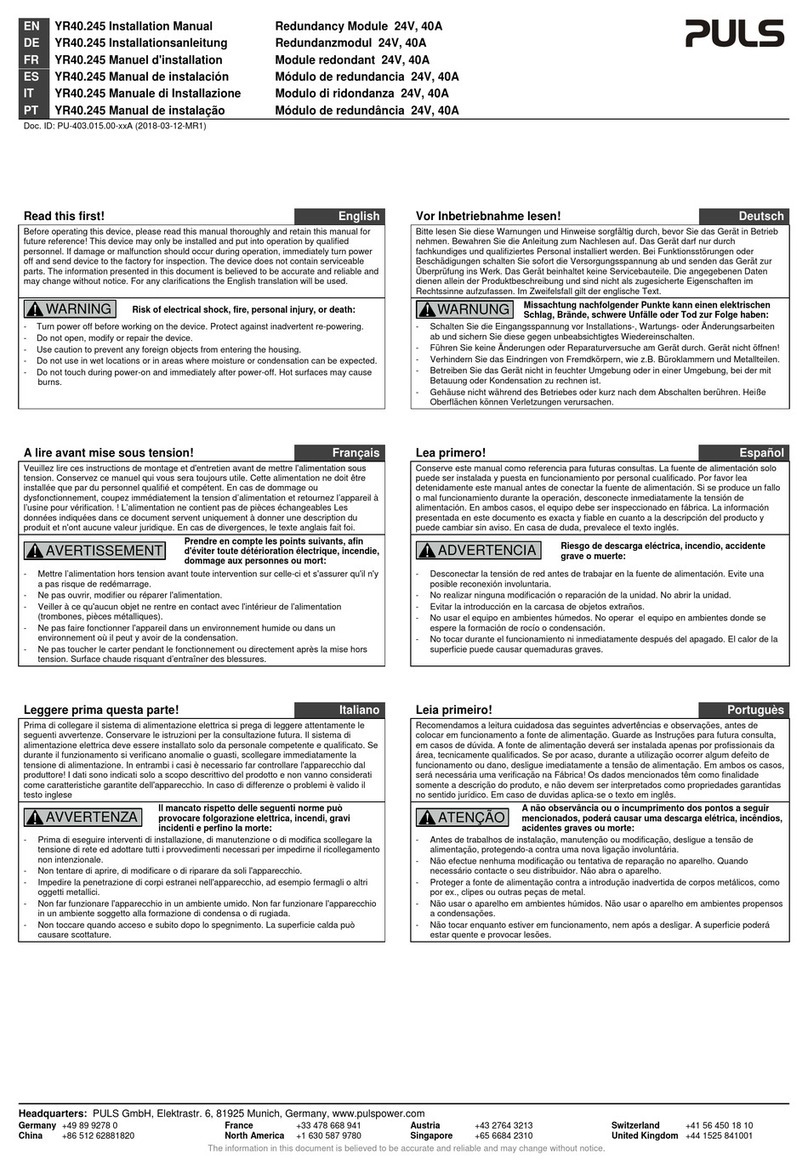
Puls
Puls DIMENSION YR40.245 installation manual

Baker Hughes
Baker Hughes Masoneilan 10000 Series instruction manual
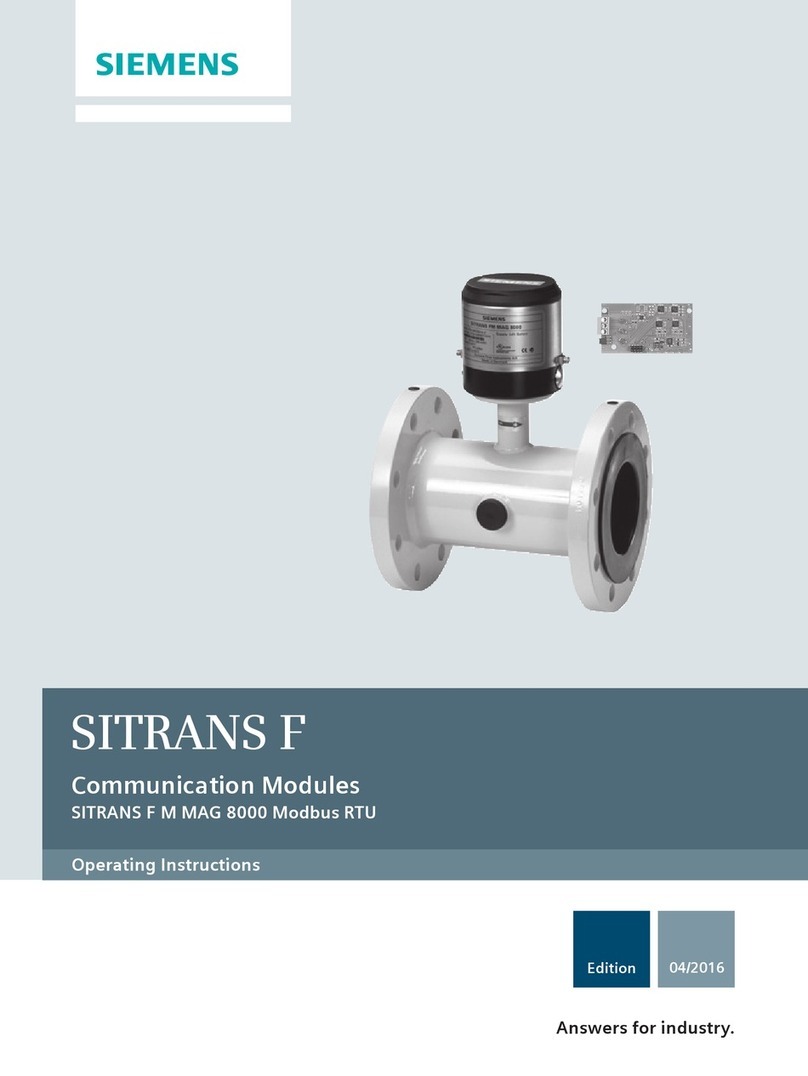
Siemens
Siemens SITRANS F operating instructions
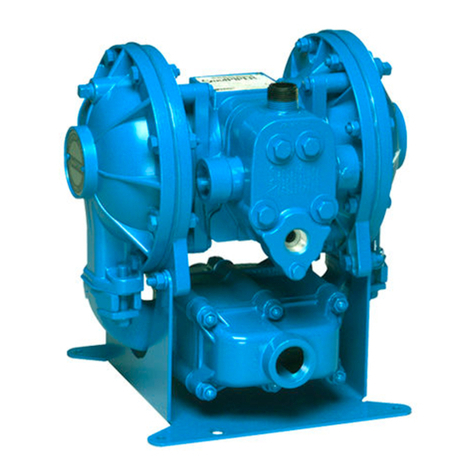
Warren rupp
Warren rupp Sandpiper SA1 Service & operating manual
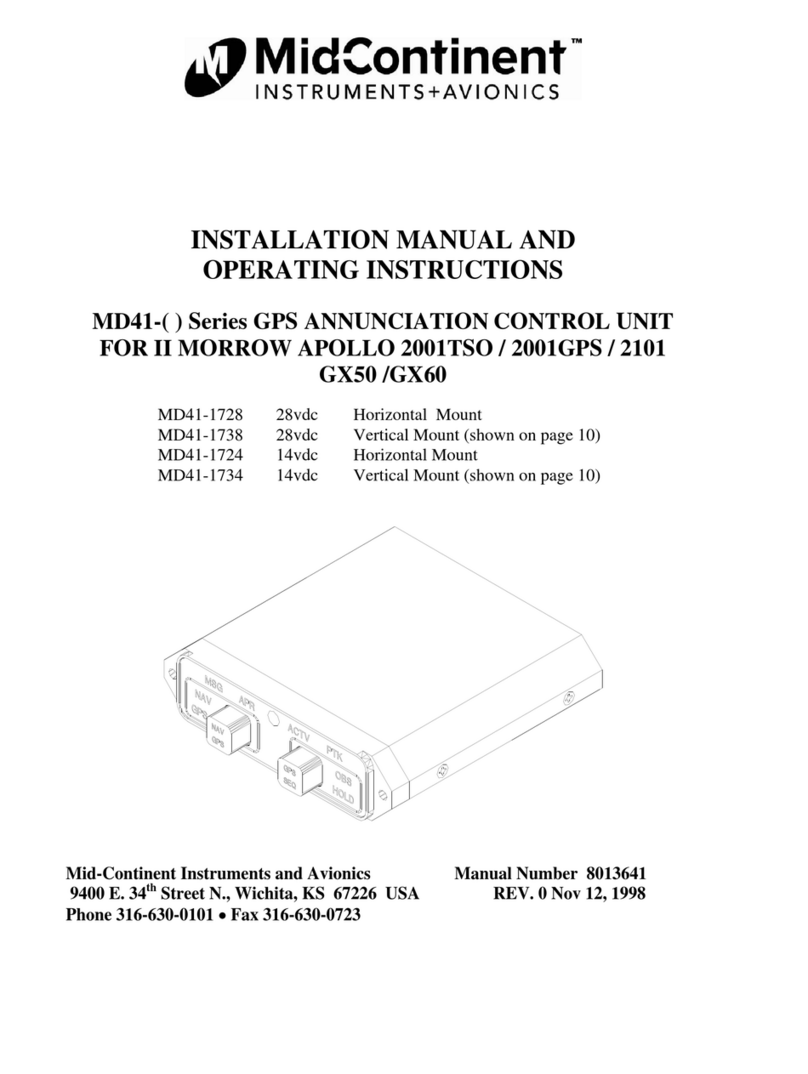
Midcontinent
Midcontinent MD41 Series Installation manual and operating instructions
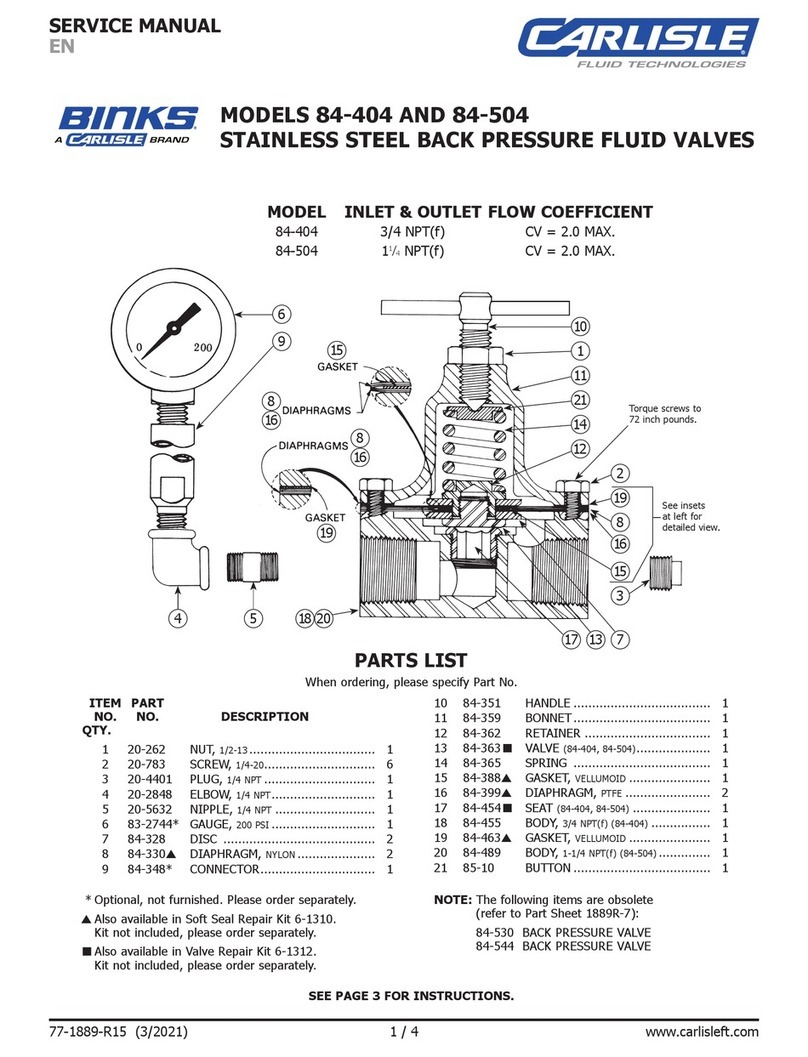
Carlisle
Carlisle BINKS 84-404 Service manual