ARI 1108 Installation instructions

INSPECTION &
MAINTENANCE BULLETIN
ARI 1108 & HP1108
Safet Relief Valve
These instructions are applicable to the following models:
ARI 1108
ARI HP1108
Only facilities with AAR Activity Code C5 are certified to recondition, repair, retest and qualify
tank car safety relief valves. Personnel performing inspection and test must be certified Level I
per AAR Manual of Standards and Recommended Practices, M-1002, Appendix T, 1.4.3.
American Railcar Industries, Inc.
Updated 3/1/2017
1

New Valves for Re lacement of Existing Equi ment
New valves are tested, sealed and packaged at the time of manufacture. A new valve can be applied
provided it is still in its original packaging and tested within 6 months of the installation date. A valve
with a test date older than 6 months must have the O-rings replaced and retested.
Safety relief valves are spring-loaded devices that can store a significant amount of energy.
Assembly and disassembly must be performed by trained, qualified personnel.
Disassembly Procedure
Disassembly of the Top Guide and O-ring Retainer
1. Remove the 2 seal wires, items #9.
2. Remove the four bolts, item #3, securing the top guide, item #24 to the valve body, item #19.
3. Lift off the top guide, item #24. It may be necessary to loosen the guide by tapping with
a soft-faced hammer.
4. Peel off the bumper washer, item #23.
5. Using two wrenches, one applied to the hex on the retainer, item #20, and the other to the
locknut, item #1, loosen and remove the locknut.
6. Remove the O-ring retainer with the use of a wheel puller or gently prying under and around the
lip with a screwdriver.
7. Using a packing removal pick, remove the O-rings, items #21 & 22, from the retainer taking
care not to mar the O-ring grooves.
8. Lay the valve on its side. Using a packing removal pick or a thin blade screwdriver, pry the
gasket, if attached, from the gasket face. Take care not to mar the sealing surface.
American Railcar Industries, Inc.
Updated 3/1/2017
2

Disassembly of the spring and stem
1. Clean the stem threads with a wire brush and lubricate the threads with a light oil, like WD-40.
2. Loosen and remove the locknut, item #11. Do NOT remove the spring adjustment nut at
this time.
3. Measure and record the distance from the end of the stem to the spring adjustment nut.
This dimension will be used at reassembly.
4. Place the valve into a press with the spring in the upward position and a means to prevent the stem
from dropping out.
5. Using a press yoke to allow access to the spring adjustment nut, compress the valve spring to
remove all force from the nut. Remove the adjustment nut.
6. Slowly back off the press head until the valve spring, item #14, expands to the relaxed state.
7. Remove the spring follower, item #13, the spring guide, item #15, and the spring, item #14.
8. Remove the valve body and stem from the press taking care to prevent the stem from
dropping out.
9. Lay the valve body on its side and withdraw the stem.
Ins ection of Valve Com onents
To Stem Guide
The inside of the top stem guide should be free of paint, debris, nicks, burrs or other discontinuities.
Visually inspect the inside of the guide and the mating area on the upper stem. Any sign of significant
wear should be reported to ARI Engineering for review and disposition.
Valve Stem
Remove all scale, residue and other foreign material from the stem with a wire brush. Inspect the stem
for signs of corrosion or pitting. Any evidence of corrosion or pitting is grounds for replacement.
The seating surface and O-ring contact areas can be cleaned with 400 grit emery cloth. Any discontinuity
that would prevent sealing is grounds for replacement. Machining, grinding, welding or other alterations
are not permitted.
The stem must be inspected for cracking using either magnetic particle or dye penetration inspection
methods. Cracking is unacceptable. If found, the stem must be replaced.
Place the stem in a set of V-blocks and measure straightness with a dial indicator. The stem must be
straight within .015 TIR. If out of tolerance, the stem must be replaced. Straightening by bending or heat
is not permitted.
O-Ring Retainer
Clean the O-ring setting surfaces inside the retainer with 400 grit emery cloth. Visually inspect the
O-ring grooves. They must be free of pits, corrosion or gouges that would prevent proper sealing of
the O-rings.
American Railcar Industries, Inc.
Updated 3/1/2017
3

Valve Body
The area around the valve seat must be free of debris, corrosion and foreign objects. Cleaning can be
accomplished with a light brush off blast using glass bead media. The seating surface must be free
of nicks, burrs and gouges. The area should be cleaned and lightly polished with 400 grit emery cloth.
Any discontinuity that would prevent the valve from sealing is grounds for replacement. Machining,
grinding, welding or other alterations are not permitted.
Turn the valve body over to inspect the mounting flange and gasket groove. The gasket groove must
be free for residual gasket material, corrosion, nicks, burrs and gouges. Any discontinuity that would
prevent sealing is grounds for replacement.
Valve S ring
Remove all scale, residue and other foreign material from the spring with a wire brush. Inspect the spring
for signs of corrosion or pitting. Any evidence of corrosion or pitting is grounds for replacement.
The spring must be inspected for cracking using either magnetic particle or dye penetration inspection
methods. Cracking is unacceptable. If found, the spring must be replaced.
Stand the spring upright on a level surface. Place a straight edge against the outside and measure for
straightness. Turn the spring 90 degrees and measure again. The spring must straight within ¼”. If out
of tolerance, the stem must be replaced.
Aluminized springs cannot be inspected with magnetic particle or dye penetration methods. After
cleaning, visually inspect the coating. Any evidence of peeling or flaking of the aluminum is grounds for
replacement.
S ring Guide
Remove all scale, residue and other foreign material from the guide with a wire brush. Inspect the guide
for signs of corrosion or pitting. If any is found, the guide must be replaced.
Inspect the interior of the guide for signs of wear caused by the spring follower. Wear could be an
indication of a bowed spring, misassembled spring or misalignment of the valve with the safety valve
nozzle. If wear is noted, measure the outside diameter in the affected area then at 90 degrees. Compare
the readings. If the difference exceeds 0.030” replace the spring guide.
S ring Follower
Remove all scale, residue and other foreign material from the stem with a wire brush. Inspect the
follower. Any evidence of corrosion or pitting is grounds for replacement.
Visually inspect the outside diameter of the follower for signs of significant wear. Wear could be an
indication of a bowed spring, misassembled spring or misalignment of the valve with the safety valve
nozzle. If wear is noted, measure the inside diameter in the affected area then at 90 degrees. Compare
the readings. If the difference exceeds 0.030” replace the spring follower.
O-Rings
O-rings must be replaced any time the retainer is removed from the stem.
American Railcar Industries, Inc.
Updated 3/1/2017
4

Assembly Procedure
1. With the valve body on its side, insert the stem into the body from the top.
2. Place the valve in the press ensuring the spring is seated in the body and the stem is aligned.
Install the spring and spring follower then position the yoke, and compress the spring enough to
apply the adjustment nut. With the nut fully engaged, further compress the spring and tighten
the nut to the previously recorded dimension from the nut to the end of stem.
3. Release the press and move the valve to the workbench.
4. Install the O-rings in the O-ring grooves of the O-ring retainer taking care not to tear, stretch
or otherwise damage the O-rings. Sharp tools should never be used for this operation.
5. Place the retainer with the O-rings on the stem.
6. Install the bumper washer on the retainer.
7. Install the locknut on the stem with a wrench applied to the hex on the retainer and screw that
one to the nut. Torque to 30 ±5 ft-lbs
8. Place the top guide over the studs and secure with the 4 nuts. Torque to 30 ± 5 ft-lbs.
9. Move the valve to the test stand.
10. After testing is complete, install the stem locknut and, using two wrenches, tighten to
30 ±5 ft-lbs.
11. Install new seal wires, item #9.
Guidelines for Testing and Adjustment
Determining A licable Pressure Values
The ARI 1108 safety relief valve is designed to operate at 75 psig. The start-to-discharge pressure (STD)
must be 75 psig +/- 3 psig and vapor-tight at 60 psig minimum.
The ARI HP1108 safety relief valve is designed to operate in a range from 225 psig to 330 psig.
The start-to-discharge pressures (STD) are as follows:
Test Stand and Gauge Requirements
The test stand must have a mounting that complies with AAR M-1002, Section C-III, Appendix E, Figure
E21 A. Test stand pressure gauge must meet the requirements of AAR M-1002, Section C-III, Appendix
D section 4.5, Test Gauge Standards. Gauges must be date tagged.
Start-to-Discharge Tolerance Vapor-Tight
Pressure (psig) (psig) Pressure (psig)
225 6.75 180
247.5 7.4 196
255 7.7 204
280.5 8.4 224
300 9.0 240
330 10.0 264
American Railcar Industries, Inc.
Updated 3/1/2017
5

100 Clark Street, St. Charles, Missouri 63301
AMERICAN RAILCAR INDUSTRIES, INC.
636.940.6020
•
FAX: 636.940.6100
www.americanrailcar.com
•
sales@americanrailcar.com
02/2010
Valve Leak Testing
1. Safety Relief Valve leak tests must be conducted in accordance with AAR M-1002, Section C-III,
Appendix T. The inspector must be Level I qualified or higher.
2. Apply the safety valve to the test stand.
3. Cycle the valve by applying shop air or nitrogen to the stand.
4. Plug the valve body drain opening using putty or a foam ear plug. Fill the cavity to the top of the
O-ring retainer.
5. Increase air pressure under the valve until the valve opens or “pops.”
6. Reduce pressure until the valve is closed and there are no bubbles present.
7. Refill the chamber and begin slowly increasing pressure under the valve until the first bubble
appears. This is the start-to-discharge pressure (STD) and must be within the tolerances provided
in the previous section, Guidelines for Testing and Adjustment.
8. If the start-to-discharge pressure falls outside the specified range, adjust the valve spring by
tightening the adjustment nut to increase the discharge pressure and loosen to decrease. Repeat
Steps 4-6.
9. NOTE: If adjusting the spring tension produces the opposite of the desired effect, the spring
could be defective and must be replaced.
10. Once the proper start-to-discharge pressure is attained, slowly decrease the pressure until the
bubbles stop. This is the vapor-tight pressure and must be within the tolerances provided in the
previous section, Guidelines for Testing and Adjustment.
11. A vapor-tight pressure falling below the specified minimum could indicate a problem with the
O-rings not sealing properly. Release all pressure from under the valve and remove the O-ring
Retainer following the instructions under section, Disassembly of the Top Guide and O-ring
Retainer, steps 2-6. Visually inspect the O-rings for nicks, gouges or improper setting in the
retainer. Visually inspect the seating surface. A finger nail run across the surface can pick up
discontinuities that are not readily visible. Any defect must be corrected.
12. Once the start-to-discharge and vapor-tight pressures are attained, test a second time to confirm
the settings then tighten the stem locknut and install the seal wires per steps 10 & 11 in the
Assembly Procedure section.
13. Mark the valve per AAR M-1002, Section C-III, Appendix A, Paragraph 7.1.2.
The undertaking of repair or replacement by the Purchaser, or its agents, without the expressed written consent of American
Railcar Industries, Inc. (ARI) shall void ARI’s warranty and relieve ARI of all responsibility. Under no circumstances shall ARI
be liable for any direct, incidental, consequential or other damages of any kind in connection with the installation, operation,
maintenance, repair, inspection or other use of any product purchased from it.
This manual suits for next models
1
Table of contents
Other ARI Control Unit manuals
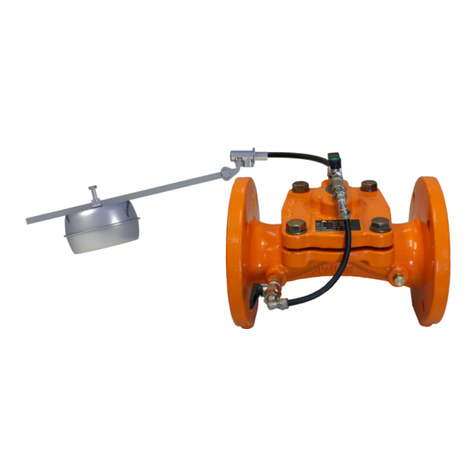
ARI
ARI Eliptix R-30-X User manual

ARI
ARI D-040 Owner's manual
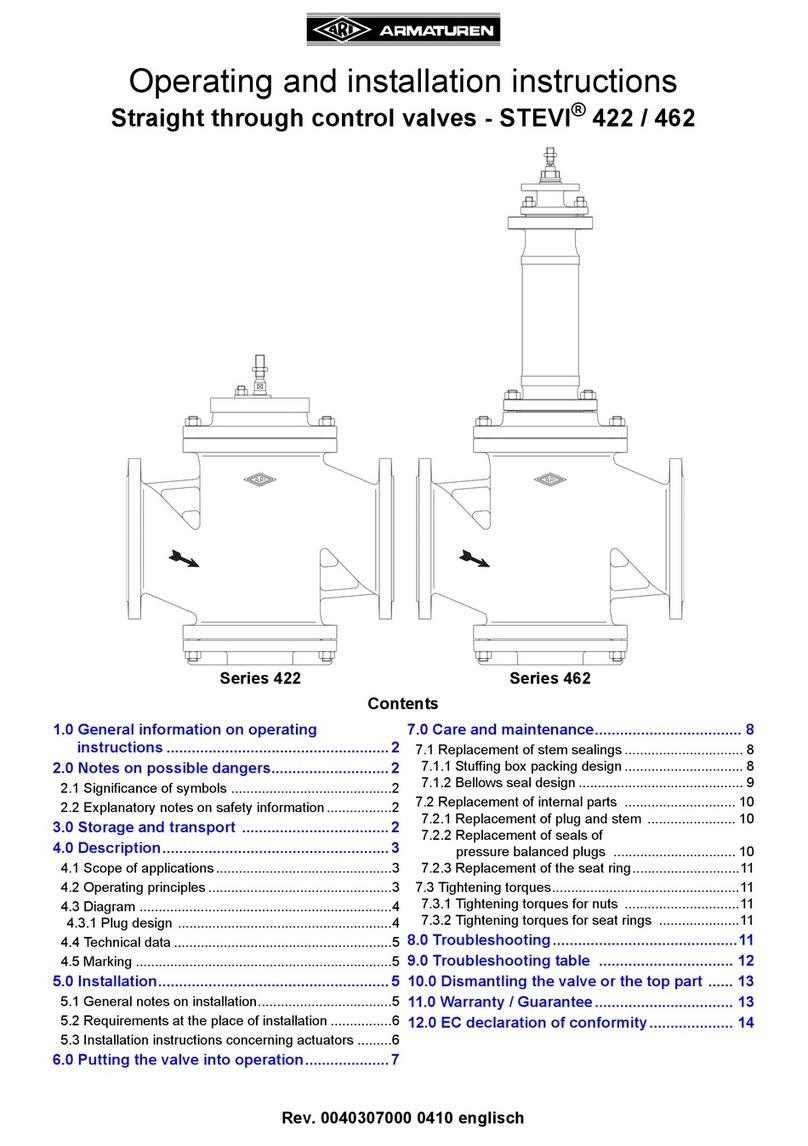
ARI
ARI Stevi 422 Series User manual
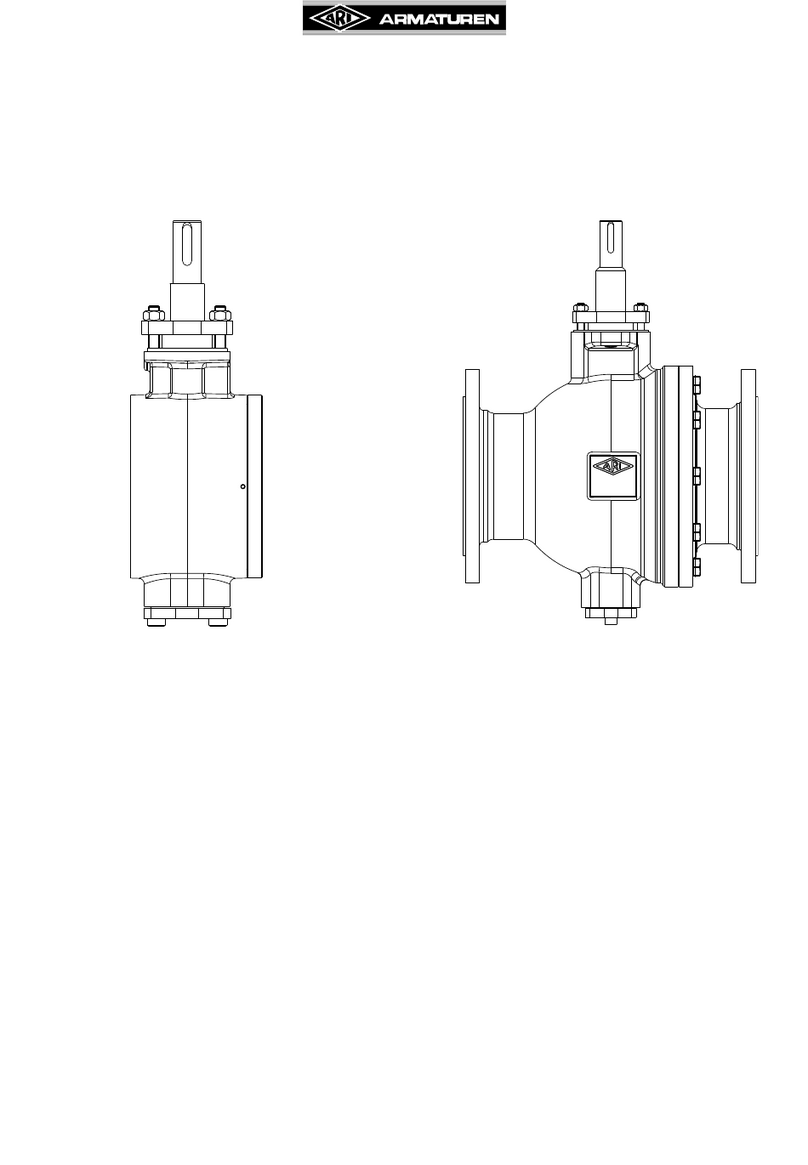
ARI
ARI PALTRA-V User manual

ARI
ARI D-060 Installation and operating instructions
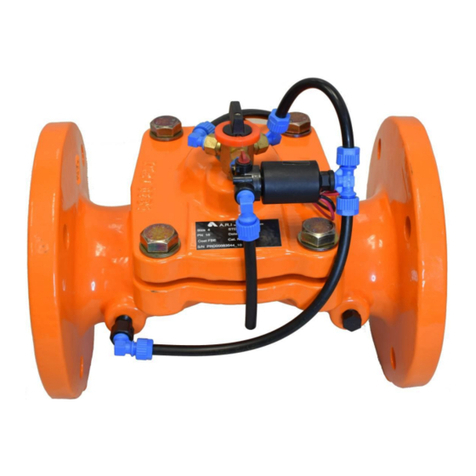
ARI
ARI Eliptix R-30ME User manual

ARI
ARI VB-060 User manual

ARI
ARI Eliptix R-20-SM 3W User manual
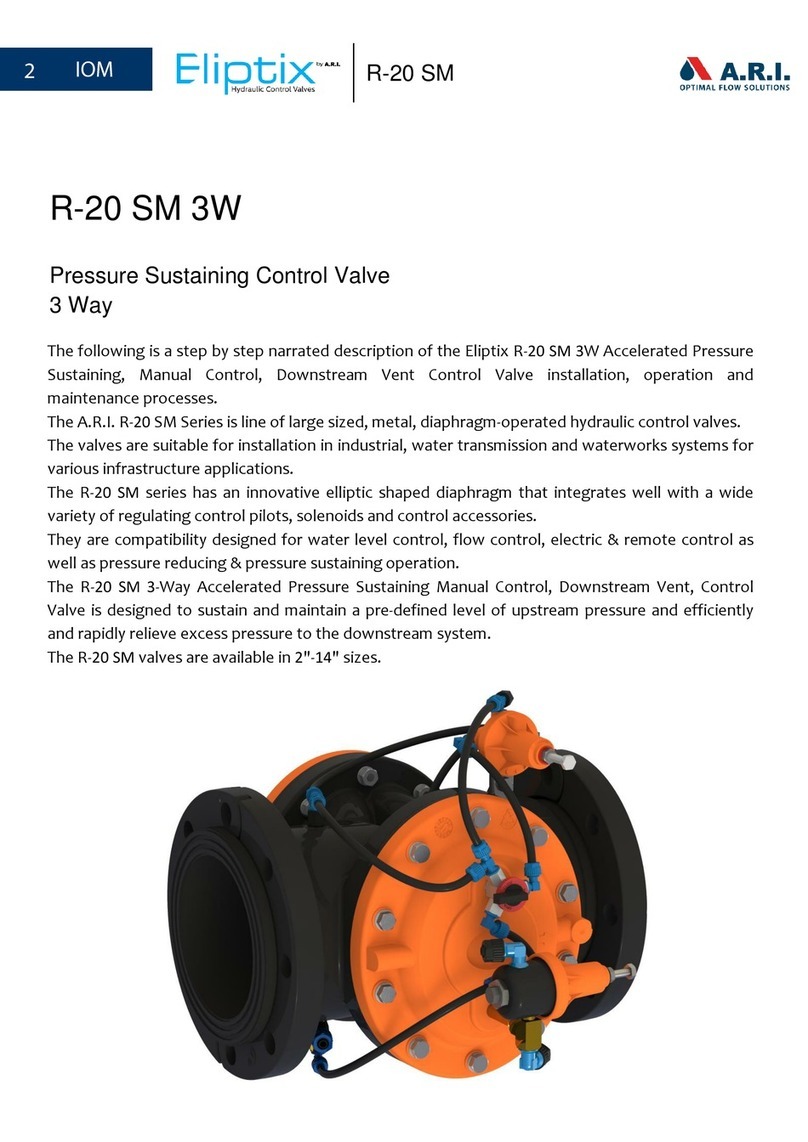
ARI
ARI Eliptix R-20 SM Series User manual

ARI
ARI S-050 Owner's manual
Popular Control Unit manuals by other brands
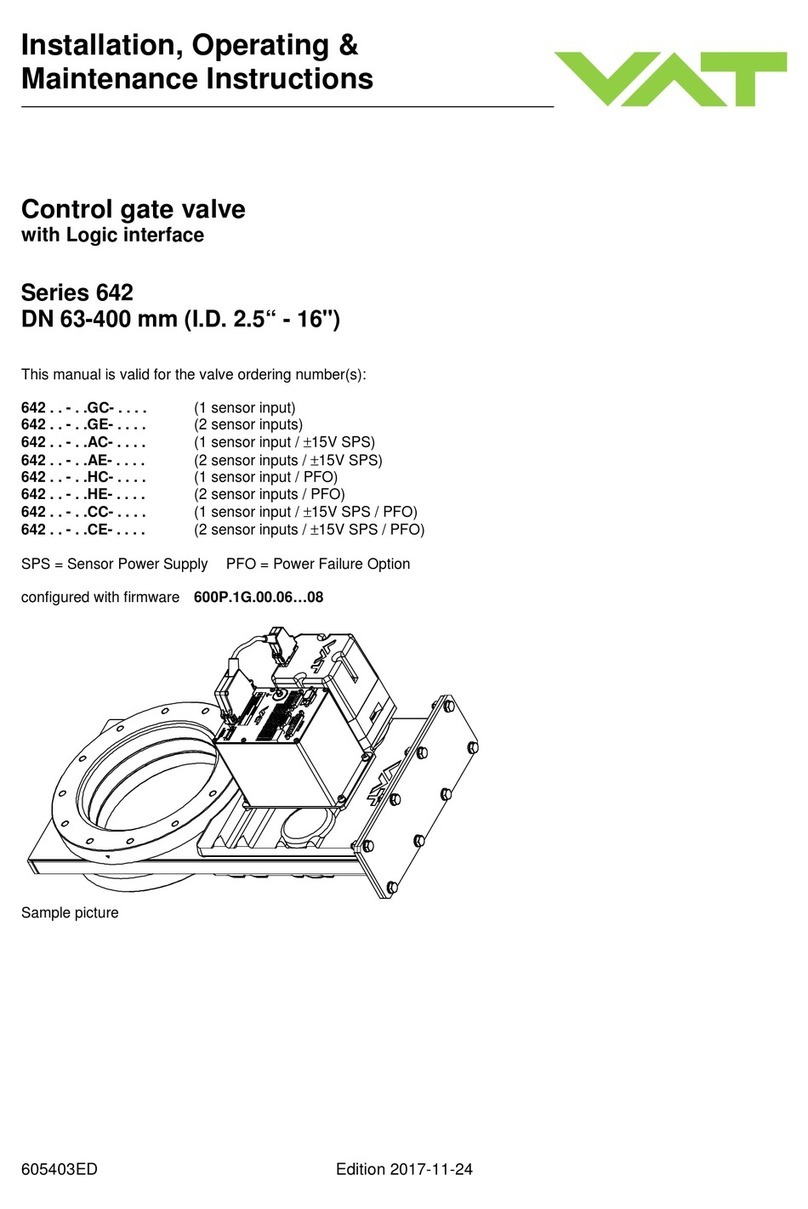
VAT
VAT 642 Series Installation, operating, & maintenance instructions
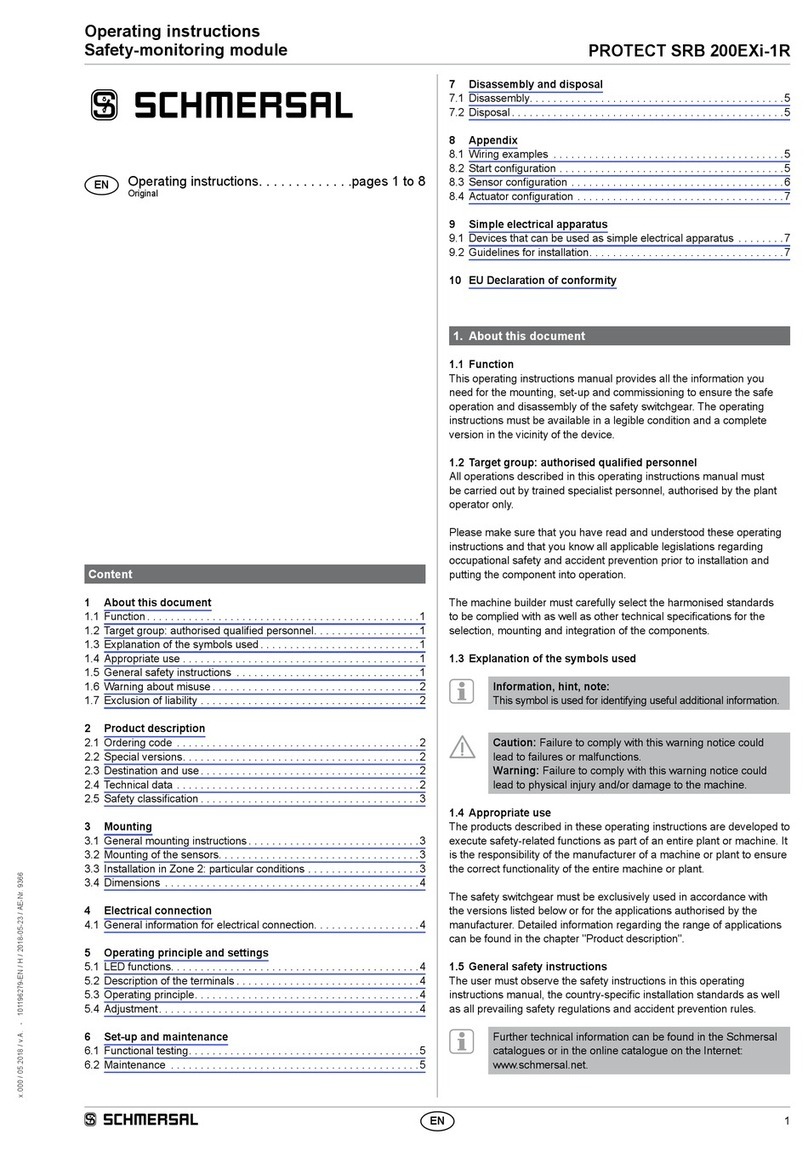
schmersal
schmersal PROTECT SRB 200EXi-1R operating instructions

Next
Next HC660 HYDROCLEAN installation instructions
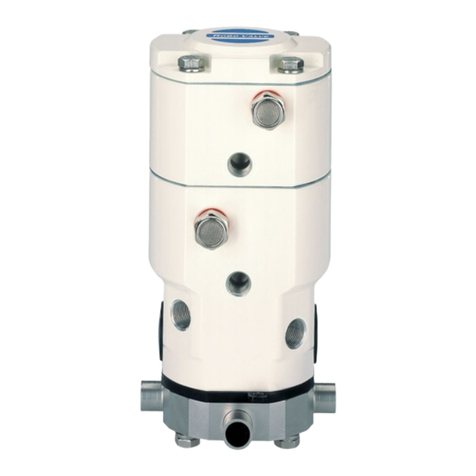
Burkert
Burkert 2035 operating instructions
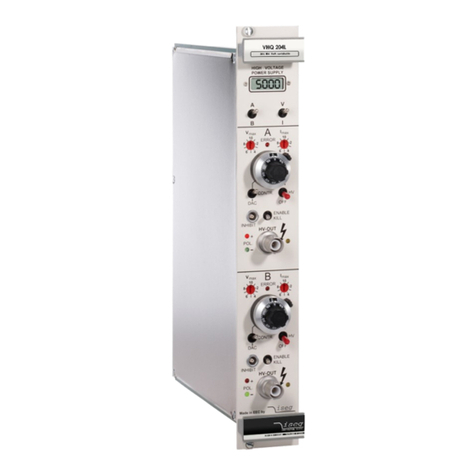
iseg
iseg VHQ Series technical information

Grundig
Grundig GSS HRM 325 Assembly instruction