ARMOUR FIREFLY VTOL Configuration guide

www.armour.gr
www.armour.gr
GENERAL MANUAL

Prohibitions
Important / Caution
Prompt / Skills
Annotations
1. Symbols in the Manual
2
www.armour.gr
Tips

2. Safety Instructions
2.1 Acknowledgement
This product is a professional aviation tool, where wrong operations may lead to
damage to the goods or casualties.
User must bear the corresponding criminal responsibility caused by this product.
For proper usage and your safety, please read the instructions carefully before
using or consult the manufacturer.
2.2 Precautions
2.2.1 Air Traffic Control
Subject to the country that you will use the FF VTOL, appropriate approval of the
Air Traffic Management Bureau (ATMB) of Civil Aviation Administration must be
obtained and strictly to abide by national laws and regulations.
2.2.2 Flight Area
(1) If the use of the FF VTOL is for Civilian proposes, and subject to the country
laws, It is prohibited to fly over the no-fly zone delineated by the public security
department, including airports, railways, flammable and explosive materials
storages (factories), dangerous goods stores (factories), power stations, high
voltage lines, military facilities, personnel-intensive areas, and public security
departments.
(2) If any important protection or ambiguous target exists in the intended flight area,
it is necessary to report to the local authorities for approval.
2.2.3 Geographic Environment
(1) The flight area must be surveyed to ensure that the flight path is out of
obstructions.
(2) Flights in mountain or between buildings are prohibited since the product may
experience strongly change the shear wind.
2.2.4 Personnel Situation
(1) All staffs and operators must be in good condition, with energy and
concentration. Operators with sickness, emotional or fatigue state are not allowed
to operate the unmanned aircraft.
(2) From the night before the flight until the end of the flight, all operators are
prohibited from alcohol.
3
www.armour.gr

3. Overview
FIREFLY (FF) UAV is a composite vertical take-off and landing UAV design and
manufacturing by International Armour and Partners, applies fixed wing combined
with the quad rotor complex fix wing layout, which solves the problem of vertical
take-off and landing in a simple and reliable way.
Along with its advantages of long endurance, high speed, and long distance.
An industrial-grade flight control and navigation system is specially developed for
the FF UAV, ensure that the UAV could complete the whole flight, cruise, flight
state transition, vertical take-off and landing and other flight stages without operator
intervention.
The FF UAV does not require any runway, take-off and airspace, which ensure it
can operate smoothly in complex terrain and building-intensive areas such as
mountains, hills and jungles.
This advantage has greatly expand the UAV application range, which makes the
FF UAV ideal for many applications.
3.1 Features
- Layout :Simple and reliable structure from the application of conventional fixed-
wing and quad rotor combination as the layout pattern。
- Practical and Efficient: Fixed wing UAV with long endurance, high speed, long
distance, and heavy payload
- Vertical Take-off and Landing: Equip with a vertical take-off and landing
features can significantly reduce requirements on landing space.
- Low Cost of use:Do not require any complex cumbersome launch and recovery
equipment. Additional recovery sensors are also not necessary for this UAV.
Vertical take-off and landing can minimize the possibility of damage to the fuselage
and equipment on board.
- Easy to Operate: Applying integrated dedicated flight control and navigation
system, achieving fully autonomous flight.
Operators without professional training and operational experience could also
operate the UAV by simply sending flight plans.
- Compact System: Do not require any complex auxiliary equipment. Along with
simple transportation, expansion, maintenance, and withdrawal.
4
www.armour.gr

3.2. Basic Performance Parameter
Total Flight Weight: <18Kg
Payload: 1.5Kg
Cruising Speed: 24-25m/s
Maximum Flight Speed: 31m/s
Stall Speed: 14m/s, (wind speed < 3m/s)
Flight Time: < 2.0 hours (Pure electrical)
Wing Span: 3.5m
Wing speed level: <14m/s
Practical Ceiling: 3900m (Pure electrical)
3.3. UAV Composition
5
www.armour.gr
QTY Description
1 FF VTOL bundle
- Quad motor system installed
- Main motor installed
- Servo installed
- Avionics installed
1 Flight controller support VTOL
1 Standard Fysky radio control
- 18 channels
- Used for ground setting
1 Service Autopilot
2 8S 10000mAh Li-po for FF
(1 Set as spare part)
2 42000mAh (18650, Li-ion) battery (6s, 25.2v)
Weight 3.6kg
For FF fix wing
(1 Set as spare part)
1 Dual output charger
6-12S x 2
1200w
1 Telemetry 900mMhz
- Range 30-50km
- Built in battery 6000mAh for 6 hours
- Sbus x 1, Serial x 1
- Wifi, Bluetooth
1 1.8m fiberglass antenna, 2 section 10db, 902 - 928 MHz
1 Nose FPV camera, AV output
1 Analog video link with AV input, Range 10km
Receiver & Antenna
1 Compact carrying case
1270 x 360 x 460mm, 5kg

3.3.1 UAV airframe composition
6
3.3.2 Ground Station
Ground station for FF UAV is shown
below, where it is easy to carry and
applicable with any laptop with Window
10 system.
Ground station telemetry transfer rate:
115200bps
Com port number: Simply plug-in USB to
your laptop, which will automatically set
up required software, then launch the
GCS40 software after the set up.
www.armour.gr
Or use WiFi connect, select WIFI “D04_Radio”, Password:88888888. Launch
GCS software, select TCP to UAV, enter Telemetry IP address 192.168.6.1, port
number 8899, then click open.

4.1 Preparation
4.1.1 Fuel (applicable for Gasoline engine only)
Gasoline:93#(Country IV) or 92#(Country V)
Lubrication Oil: FD Level 2 Stroke Oil
Gasoline/Oil mixing ratio: 30:1
4.1.2 Battery
Make sure all batteries, including battery equipped with avionics (autopilot
instrument, control servo, etc.) power supply battery, power system battery, hover
system battery, and ground station power supply battery are well-prepared and fully
charged.
4.1.3 Mission Equipment Installation Mission equipment could be changed based
on actual needs of the mission.
All mission equipment must be installed in specified area of the fuselage, where
they should not exceed the nominal load range.
Corresponding shock treatments are also necessary to protect those Mission
Equipment.
7
It is strictly forbidden to change the position of the fuselage and exceed the
nominal load.
4. UAV Operation
www.armour.gr

4.1.4 Mission Planning
Flight plan could be planned in the ground station according to the mission
requirement.
UAV can perform variety of actions as indicated by the flight plan at certain
coordinate.
Operators can amend the flight plan based on the actual situation.
4.1.5 Contingency Plans
Reasonable contingency plans should be planned near the ground station, where
its altitude ought to be the same with the normal operation altitude.
When the UAV is out of service, like its data link is interrupted, the engine is
accidentally turned off, or the GPS could not receive any satellite signal, then
UAV can return to a safe location.
Carefully survey the landing site, determine the appropriate direction for
landing from measurement, such as conditions permit.
Also, operators should allocate 2 to 3 spare landing point, once the landing
conditions change, select the most appropriate landing point for landing
according to the actual situation
4.2 UAV Assembly
FF UAV structure is simple, do not require any complex auxiliary equipment,
along with its easy start up, convenient transportation, maintenance, and
withdrawal.
During daily storage and transportation, the UAV can be stored in a box/case,
which can be assembled for flight.
8
www.armour.gr

4.2.1 Body –Centre Wing Assembly
9
www.armour.gr

4.2.2 Hover Arm
Hover Arm is the most important component on achieving vertical Take-off and
landing.
The following components and tools are necessary for installation.
HoverArm (Install the screws)
Corresponding Side Wing (Hex Wrench(M6))
10
Installation Procedures
(1) Properly install the quad motor propeller.
Due to the limitation of the external packaging volume, the quad motor is not
installed on the hover motor when the UAV is shipped.
User must follow the instructions shown below for proper installation.
Propeller: APC 18 x 5.5 Propeller: APC 18 x 5.5
Propeller: APC 18 x 5.5 Propeller: APC 18 x 5.5
Propeller: APC 18 x 8e www.armour.gr

4.2.2 Hover Arm
Hover Arm is the most important component on achieving vertical Take-off and
landing.
The following components and tools are necessary for installation.
HoverArm (Install the screws)
Corresponding Side Wing (Hex Wrench(M6))
11
Clock wise
Anti Clock wise Clock wise
Clock wise
Anti Clock wise
2) Install the hovering arm to the centre wing
Make sure the hovering arm is in the right side.
Check the rotation direction of each quad motor to install the arm to the right side.
www.armour.gr

12
2) Install the hovering arm to the centre wing
Make sure the hovering arm is in the right side.
Check the rotation direction of each quad motor to install the arm to the right side.
www.armour.gr

13
3) Wing Assembly
Make sure the lock pin are firmly locked. www.armour.gr

14
4.2.3 Tail plane Assembly
Make sure the DuPont connector are firmly plug in
1) Connecting the DuPont connector of the elevator to the DuPont plug on the
hovering arm.
2) Make sure they are plugged in the correct polarity and locked.
www.armour.gr

15
Make sure all screws are firmly installed.
www.armour.gr

16
3) Centre of Gravity
Before each flight, or equipped, replaced the mission equipment, the user need to
manually measure the current centre of gravity of the UAV from the design.
If the current centre of gravity deviation is too large (more than 3 mm deviation from
factory marked position), user need to move the mission equipment installation
location, make sure it comply with factory UAV design requirement.
110mm
CG
Do not squeeze the folded DuPont cable during installation, user must use the
screws provided along with the product.
Also, be ensure that they are firmly installed and prevent any
connection screw from loosening situation.
4.2.4 Electrical Connection
FF UAV electrical connection is simple and reliable.
The electrical interface is mainly concentrated on both sides of the wing.
As shown below, from top to bottom, they were airspeed interface, control
signal interface and power interface respectively.
Connect the two side wing cable plugs to the specified cable side connector on
the corresponding side of the fuselage with the correct polarity.
Installed the battery in the appropriate installation position, and firmly fixed,
where they cannot experience any loosening situation. Also, the user can
connect the batteries according to their situations.
www.armour.gr

17
4.2.4 Electrical Connection
FF UAV electrical connection is simple and reliable.
The electrical interface is mainly concentrated on both sides of the wing.
As shown below, from top to bottom, they were airspeed interface, control signal
interface and power interface respectively.
A) Connect the two side wing cable plugs to the specified cable side connector on
the corresponding side of the fuselage with the correct polarity.
B) Installed the battery in the appropriate installation position, and firmly fixed,
where they cannot experience any loosening situation. Also, the user can
connect the batteries according to their situations.
www.armour.gr

18
VTOL battery installation
VTOLbattery installation
The VTOL battery sensor switch will detect the battery plugin firmly or not.
If the battery does not plugs in firmly then the voltage display on software
will be “0”.
Each device is recommended to use the specified type of batteries
provided by factory.
www.armour.gr

Clock wise
Anti Clock wise Clock wise
Clock wise
Anti Clock wise
19
4.3 Pre-flight Inspection
4.3.1 Connection/installation Inspection
(1) Check the entire UAV cable connection is intact and ensure that each
connector is tightly plugged.
(2) Check the engine propeller installation is loose or not, it is necessary to ensure
that it is firmly installed. Otherwise, flight should be prohibited.
(3) Check the airspeed tube is intact, without any vandalism.
(4) Connect to the ground station power supply, self-pilot instrument power,
steering gear power, the engine starting power one by one.
Note: After connecting to power supply, open the ground station software.
Once the connection is completed, then proceed the ground station inspection.
4.3.2 Engine/motor Inspection
(1) Check the forward engine/motor propeller is installed correctly.
(2) Check the rotor motor propeller is installed correctly.
The rotation direction of the forward engine is in clockwise (observe from
the nose to the tail).
It should be consistent with the rotation direction of the propeller.
The top left and bottom right rotor motor are in clockwise.
The top right and bottom left rotor motor are in anti-clockwise (Observe from
the top of the fuselage, see diagram below for detail explanations)
www.armour.gr

20
4.3.3 Ground Station Inspection
For your safety, please unplug all power source or supply when proceeding ground
station software inspection.
This is due to parts of the inspection criteria may drive the motor or the engine.
(1) Remote Control Checking: This checking mainly confirms the remote control
corresponding to the joystick and the plane system is consistent.
The user shaking the ailerons, elevators, throttle, steering, and the hand switching
function to joysticks and switches are also the criteria of this checking.
Besides, the operator is responsible to the inspector the pre-flight check page long
with its corresponding channel status, which ensures the actual action of the
remote control is consistent with the inspection page.
Otherwise, corresponding adjustments need to be made on the remote control
(2) Posture Checking: Manually changing the posture of the UAV, compare with
the direction indicated by horizon instrument whether consistent or not.
(3) Magnetic Compass Calibration: Accuracy of the magnetic compass will
directly affect the flight quality of the UAV. If the difference of the magnetic
compass is greater than 30°, system re-boot or re-calibration is required.
(4) Flight Plan Inspection: Request the long-range flight plan of the UAV to
confirm whether the task route is reasonable or not. And to confirm whether the
landing route is set and reasonable.
After completing those inspections listed above, the operator can now
connect the power supply to proceed with follow-up inspections.
(5) Proceed avionics equipment power, power supply, GPS status checking.
Also, check the main power of the avionics equipment, steering gear power and
power supply are appropriate or not.
(6) Servo Control Surface Inspection: Give instructions through the ground
station to check the aileron, elevator and rudder surface deflection and whether the
rotation direction of the rotor is consistent with the instructions.
If they are the same, then proceed to the next inspection; if not, the operator needs
to re-examine the cable connection.
www.armour.gr
This manual suits for next models
1
Table of contents
Popular Drone manuals by other brands
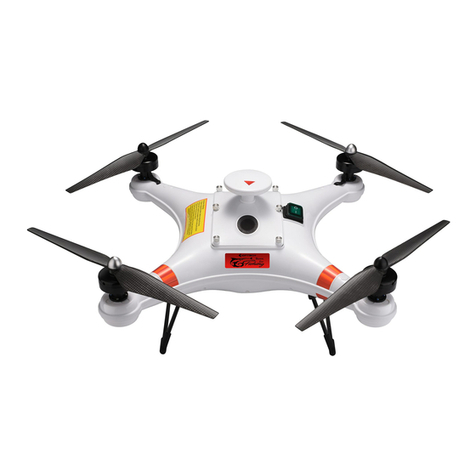
Ultimate Drone Fishing
Ultimate Drone Fishing Poseidon Pro Pre-Flight Checklist
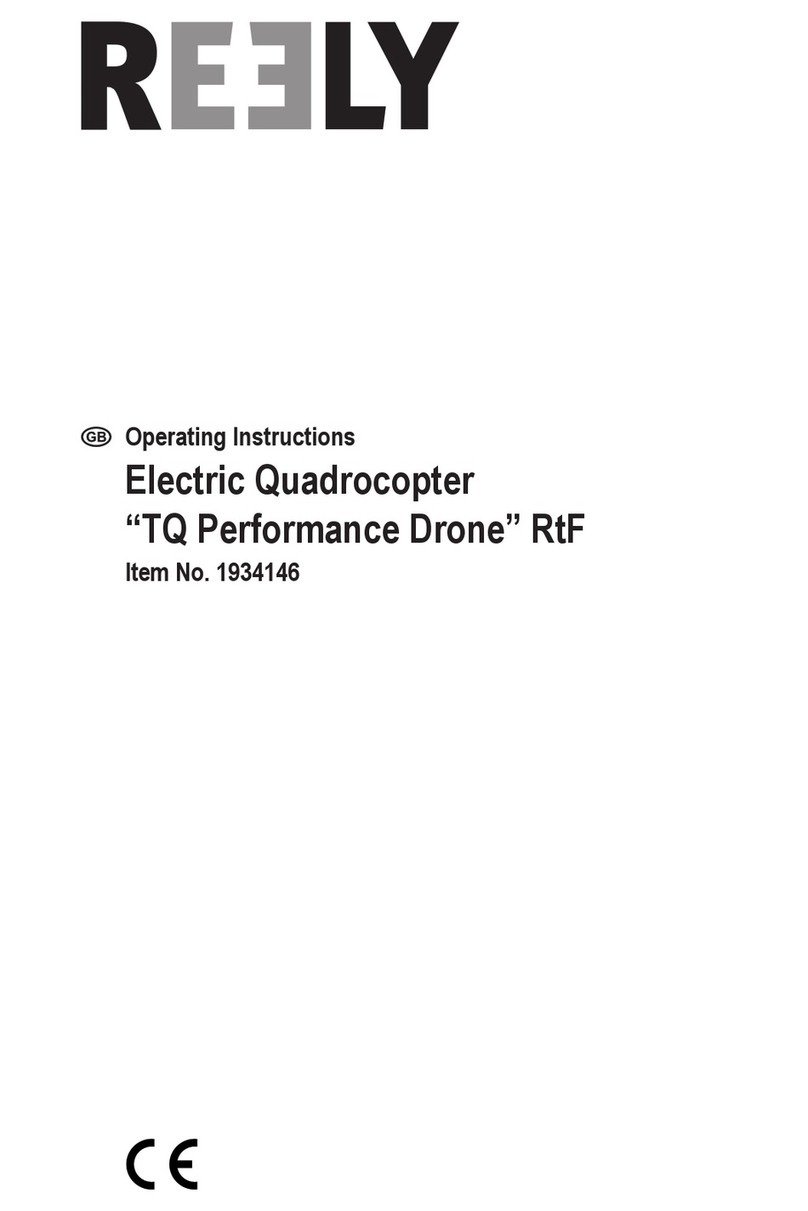
Reely
Reely TQ Performance Drone RtF operating instructions
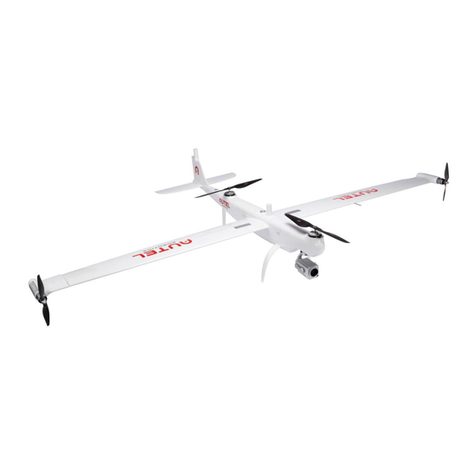
Autel Robotics
Autel Robotics Dragon Fish quick guide
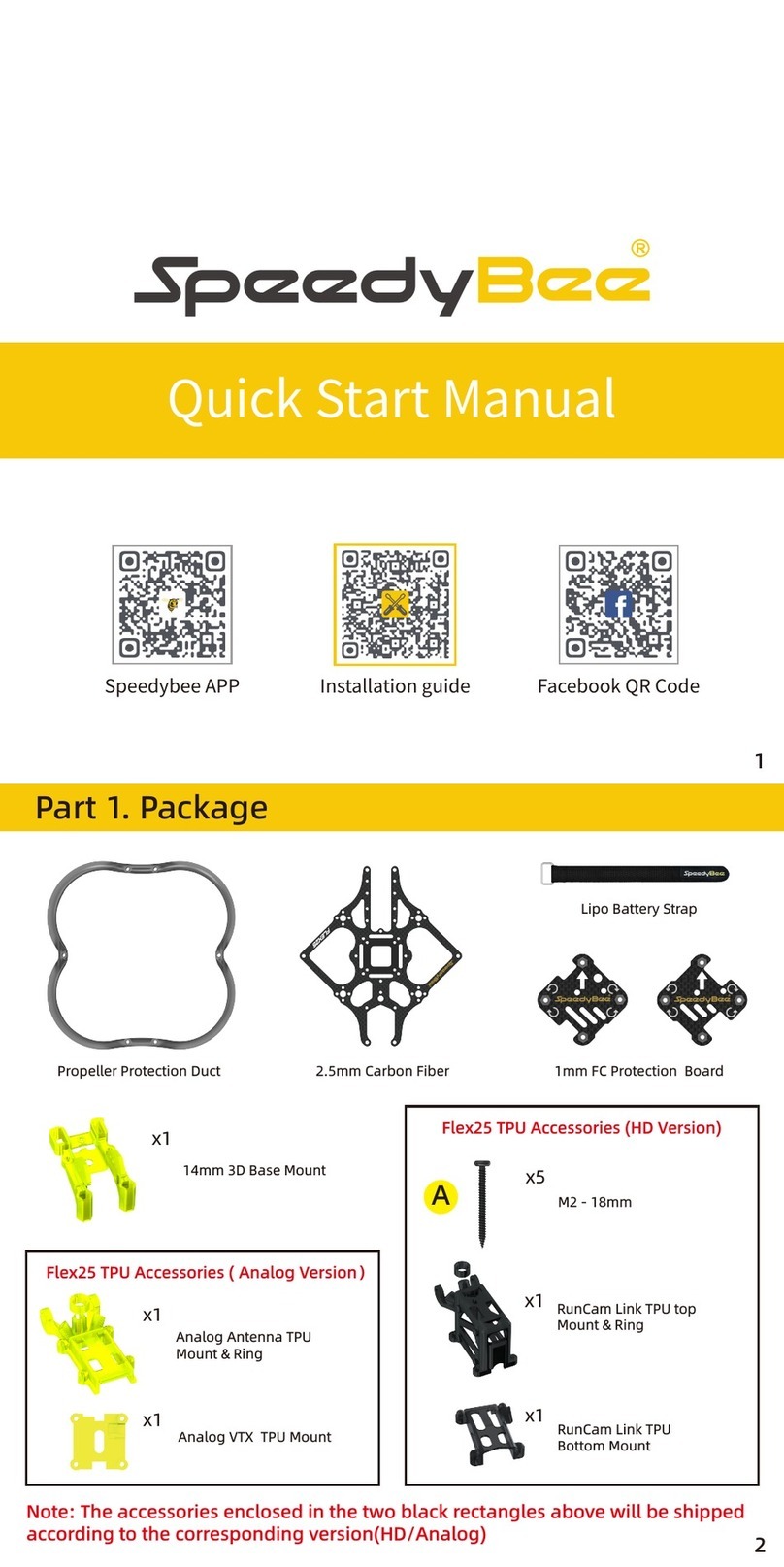
SpeedyBee
SpeedyBee Flex25 Quick start manual
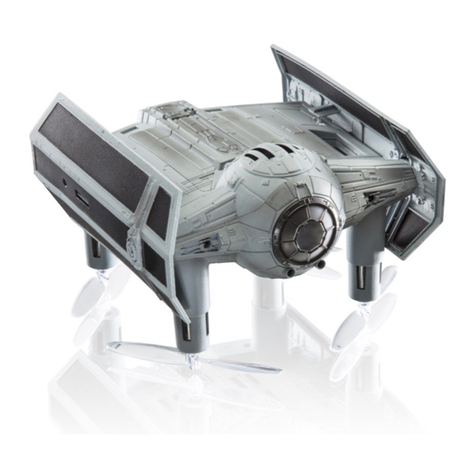
Propel Trampolines
Propel Trampolines Tie advanced x1 manual
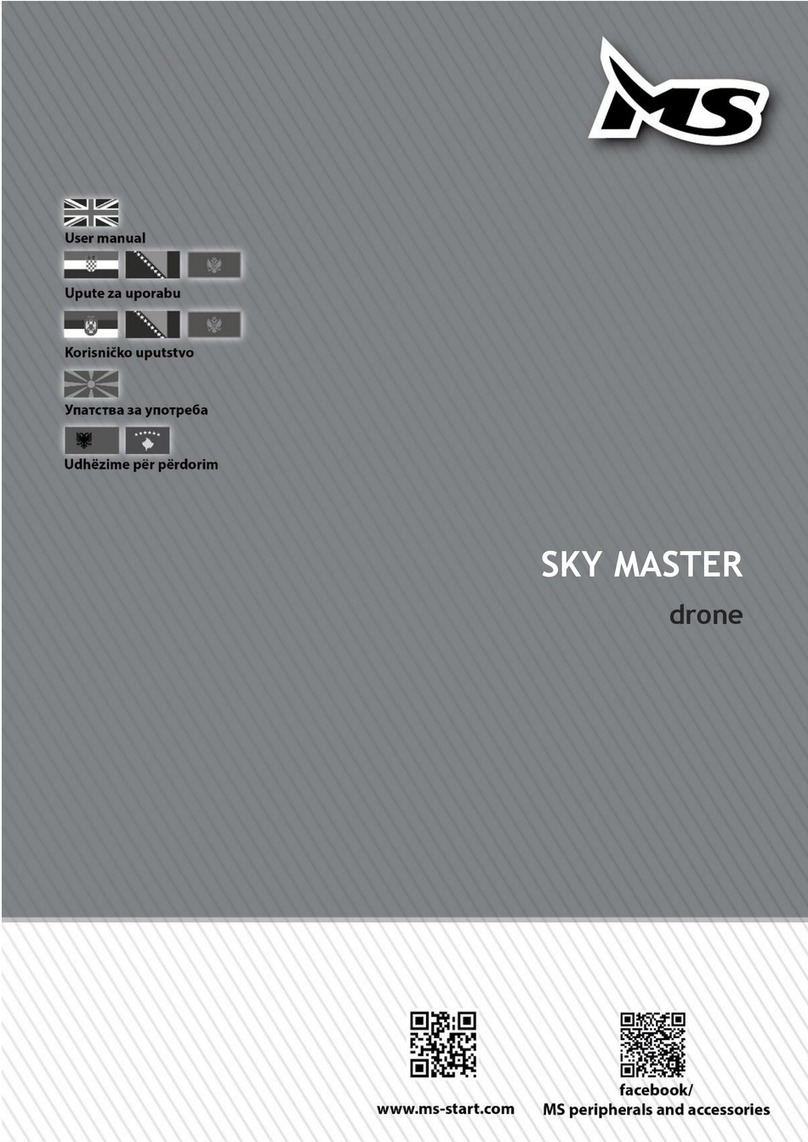
MS
MS SKY MASTER user manual