ARRI DRW-1 User manual

!
!
!
!
!
!
Digital Remote Wheels!
DRW-1 SUP2.2!
!
!
!
!
Date 01.08.2019!
!
!
!
USER MANUAL

!
!
Imprint!
Copyright © 2018 Arnold & Richter Cine Technik GmbH & Co. Betriebs KG.
All rights reserved.
No parts of this document may be reproduced without prior written consent of Arnold & Richter !
Cine Technik GmbH & Co. Betriebs KG. Specifications are subject to change without NOTE. !
Errors, omissions, and modifications excepted.
ARRI, ALEXA, AMIRA, LDS and LENS DATA SYSTEM are trademarks or registered trademarks !
of Arnold & Richter Cine Technik GmbH & Co. Betriebs KG.
All other brands or products are trademarks or registered trademarks of their respective holders !
and should be treated as such. Original version.
For further assistance:
Arnold & Richter Cine Technik GmbH & Co. Betriebs KG
Türkenstr. 89
80799 München
Germany
www.arri.com!
!
!
!
Document revision history!
!
Version SUP Order Nr Release Date !
1.1 2.2 K4.0021085 F06781 01.08.2019
!
!
Scope!
This document describes the components, the setup and programming of the !
DRW-1 Digital Remote Wheels.
!
!
Disclaimer!
Before using the products described in this manual, be sure to read and understand all the !
respective instructions.
Otherwise the customer must contact ARRI before using the product.
While ARRI endeavours to enhance the quality, reliability and safety of their products, customers
agree and acknowledge that the possibility of defects thereof cannot be eliminated entirely. !
To minimize the risk of damage to property or injury (including death) to persons arising from defects
in the products, customers must incorporate sufficient safety measures in their work with the system
and heed the stated conditions of use.
ARRI or its subsidiaries do not assume any responsibility for losses incurred due to improper handling
or configuration of the TRINITY or other system components.
ARRI assumes no responsibility for any errors that may appear in this document. !
The information is subject to change without NOTICE.
For product specification changes after this manual was published, refer to the latest published !
ARRI data sheets or release notes, etc., for the most up-to-date specifications.
Not all products and/or types are available in every country. Please check with an ARRI sales
representative for availability and additional information.
Neither ARRI nor its subsidiaries assume any liability for infringement of patents, copyrights or other
intellectual property rights of third parties by or arising from the use of ARRI products or any other
liability arising from the use of such products. No license, express, implied or otherwise, is granted
under any patents, copyrights or other intellectual property right of ARRI or others.
ARRI or its subsidiaries expressly exclude any liability, warranty, demand or other obligation for any
claim, representation, cause, action, or whatsoever, express or implied, whether in contract or not,
including negligence, or incorporated in terms and conditions, whether by statue, law or otherwise. !
In no event shall ARRI or its subsidiaries be liable for or have a remedy for recovery of any special,
direct, indirect, incidental, or consequential damages, including, but not limited to lost profits, lost
savings, lost revenues or economic loss of any kind or for any claim by a third party, downtime, !
good-will, damage to or replacement of equipment or property, any cost or recovery of any material !
or goods associated with the assembly or use of our products, or any other damages or injury of the
persons and so on or under any other legal theory. In the event that one or all of the foregoing clauses
are not allowed by applicable law, the fullest extent permissible clauses by applicable law are
validated. !
Imprint
2

!
!
Table of contents!
!
!
!
!
!
!
!
!
!
!
!
!
!
!
!
!
!
!
!
!
!
!
!
!
!
!
!
!
!
!
!
!
!
!
!
!
!
!
!
!
!
!
!
!
!
!
!
!
!
!
!
!
!
!
!
!
!
!
1
For your safety ..…………………………………………………………………………
4
2
Functions ..………………………………………………………………………………..
5
3
DRW-1 Setup …………………………………………………………………..………..
6
4
Connecting the LBUS cables ..………………………………………………………….
8
5
Selecting the axes ……………………………………………………………………….
9
6
Brake……………………………………………………………………………………….
9
7
Fluid Drag Ring…………………………………………………………………………..
9
8
Remote Control Setup / Auto Assignment………………………..……………
10
9
Remote Control Setup / Additional Setups ……………………..……………
12
10
Power Disconnection ……………………………………………………………………
15
11
Sets…………..…………………………………………………………………………….
15
12
Technical Data…………………………………………………………………………….
15
13
Pinout….…….…………………………………………………………………………….
15
14
International Declarations.……………………………………………………………….
16
3
Table of Contents

!
!
1 For your safety!
!
!
!
!
!
!
!
!
!
!
!
!
!
!
!
!
!
!
!
!
!
!
1.1!
Risk Levels and Alert Symbols!
!
Safety warnings, safety alert symbols, and signal words in these instructions indicate
different risk levels: !
!
!
!
For your safety
The DRW-1 in combination with the SRH-3 stabilized remote head and related products
should only be used by experienced and trained operators. !
This product is not designed for inexperienced users and should not and must not be
used without proper training.!
!
ARRI recommends that all users of the DRW-1 and the stabilized remote head
read the manual in its entirety prior to use.
!Warning
4
DANGER indicates an imminent hazardous situation which, if not avoided, !
will result in death or serious injury.
WARNING indicates a potentially hazardous situation which, if not avoided,
may result in death or serious injury.
CAUTION indicates a potentially hazardous situation which, if not avoided,
may result in minor or moderate injury.
NOTICE
NOTE explains practices not related to physical injury. No safety alert
symbol appears with this signal word.
NOTE
Provides additional information to clarify or simplify a procedure.
!DANGER
!Warning
!CAUTION
NOTICE
The product is solely and exclusively available for commercial customers and shall be
used by skilled personnel only. !
Every user should be trained according to ARRI guidelines. !
Use the product only for the purpose described in this document. !
Always follow the valid instructions and system requirements for all equipment
involved.

!
!
2 Functions!
!
2.1!
Functions top view!
!
!
!
!
!
!
!
!
!
!
!
!
!
!
!
!
!
!
!
!
!
!
!
!
!
2.2 !
Functions bottom view!
!
!
!
!
!
!
!
!
!
!
!
!
!
!
!
!
!
!
!
!
!
!
!
Functions
Fluid Drag Ring
(Friction)
Clamp Lever
Mounting Bracket
Swivelling Rods
Clamp Lever Swivelling Rods
P T R Selector
Hand Wheel
(150mm diameter)
Brake !
(for the selected axis)
SRH Remote!
Mounting Bracket
Clamp Lever Wheel Carrier
P T R Selector
Clamp Lever
Wheel Carrier
Brake !
(for the selected axis)
Wheel Carrier
Hand Wheel
(150mm diameter)
Cover mounting bay
for the additional 3. axis
Locking Screw
Hand Wheel
Crank
RMB-3 mounting threads
Wheel Carrier
Wheel Carrier
Clamp Lever
Swivelling Rods
Swivelling Rods
SRH Remote!
Mounting Bracket
Clamp Lever
Mounting Bracket
3/8“ Thread
3/8“ Thread
Circular arranged threads
for Mitchell and Euro mounts
Circular arranged threads
for Mitchell and Euro mounts
DRW-1 Mounting Base
Cover Screws
5

!
!
3 DRW-1 Setup
3.1
Mounting the DRW-1 base!
!
The bottom of the DRW-1 mounting base offers multiple mounting options:
3/8” threads for long camera dovetail plates,
like the O’Connor plate (08283), !
Euro style quick release plate (2575-120),
Sachtler sideload plate M (1164),
Cartoni Camera plate Focus12-18-22 (AH859)
Cartoni Camera plate - Cine style slide (AH833)
Below are three circular threaded sets for Mitchell !
and Euro mounts. !
The following brackets can be used: !
Mitchell Mount K2.0010427, Euro Mount K2.0010426 !
and the O'Connor Mitchell Base 08281.
!
NOTE
To ensure a tight fit, use a minimum of two 3/8” !
screws when a dovetail plate is used and four !
screws for the Euro Mount and the Mitchell Mount.
3.2!
Mounting the DRW-1 modules
!
There are three M3 threads positioned at the left,
at the bottom, and the right side of the DRW-1
module.
Place the DRW-1 module carefully into the
DRW-1 carrier and tighten all three screws!
using a 3mm hex key.
NOTE
Ensure that all three screws are tightened evenly,
otherwise the DRW-1 module will have a loose fit,
which may affect the application.
3.3 !
Mounting the hand wheel!
!
Turn the location pin of the drive shaft to a 12:00 o’clock position.
Turn the blue fluid drag ring (friction) to the right to reach full friction.
Locate the groove inside the mounting hole of the hand wheel and
bring it into the 12:00 o’clock position too.
Now place the wheel onto the conic drive shaft. !
When the hand wheel has reached its final position, !
tighten the blue locking screw.
NOTE
Turn the fluid drag ring (friction) fully back to the left to reach
the lowest possible friction level.
DRW-1 Setup
M3 Screw
M3 Screw
Location Pin
Drive Shaft
Fluid Drag Ring
(Friction)
6

!
3.4 !
Mounting the Remote Control
!
The bottom of the remote control offers four M6 threads.
Open the clamp lever of the remote mounting bracket, remove
the bracket from the rods of the DRW-1 mounting base.
Place the DRW-1 SRH remote mounting bracket
to the bottom of the remote control.
Tighten the four included M6 screws.
!
!
!
!
!
3.5!
Adding the optional third hand wheel!
!
The ARRI engraved cover can be removed
after the two screws at the bottom holding !
the cover have been unscrewed.
Now the third wheel carrier can be mounted to the bay.
Redo step 3.2.
NOTE
Ensure that all three screws are tightened evenly,
otherwise the DRW-1 module will have a loose fit,
which may affect the application.!
!
!
!
!
!
!
!
!
!
!
!
!
!
!
!
!
!
DRW-1 Setup
Do not use any screws longer than M6x12. !
Longer screws may cause damage.
!Danger
7

!
!
4 Connecting the LBUS cables!
!
!
4.1 Introduction
Each DRW-1 module is equipped with two LBUS connectors
and daisy-chain technology. Up to three DRW-1 modules !
can be connected in series.!
Each DRW-1 module has two identical bidirectional LBUS !
interfaces that provide the DRW-1 module with power and !
control signals.
4.2 Connecting the DRW-1 modules
The DRW-1 Set comes with the following LBUS cables:
1 x Cable LBUS 0.3m/1ft K2.0006750
1 x Cable LBUS 0.5m/1.5ft K2.0006751
!
!
The illustration shows how one wheel is !
linked to the other and then with the remote.
The LBUS jacks are located on the sides of !
the remote control.
Risk of electric shock and fire!
Short-circuits may entail lethal damage!
Before use, read and follow all relevant instructions.
Use solely and exclusively as described in the instructions.
Never open. Never insert objects.
For operation, always use a power source as indicated in the instructions.
Always unplug the cable by gripping the plug, not the cable.
Never try to repair. All repair work should be done by a qualified ARRI Service Center.
Never remove or deactivate any safety equipment (incl. warning stickers or paint
marked screws).
Always protect from moisture, cold, heat, dirt, vibration, shock, or aggressive
substances.
!DANGER
Risk of fire!
Risk of short-circuits and back currents to power supplies/batteries:
Always use original ARRI/cmotion LBUS cables to external power sources !
(D-Tap, XLR)! ARRI/cmotion LBUS cables to external power sources provide !
a protection circuit to prevent back currents to power supplies/batteries.
!DANGER
LBUS Setup
8
NOTICE
Visit the ARRI website to verify that the Master Grips, OCU-1, DRW-1 and DEH-1,
LBUS controllers you want to use have the latest firmware.

!
!
5 Selecting the axes
Each DRW-1 module has a selection button for !
Pan, Tilt and Roll, at the top.
Initially Roll of P T R will be selected and visible, !
after the SRH remote panel had been connected !
to the LBUS.
By pressing the button Pan, Tilt and Roll, the desired
axis for each wheel can be selected.
NOTE
Ensure that each wheel is assigned to only one individual axis. !
Avoid assigning two wheels to the same axis.
NOTE
A blue blinking LED indicates a problem in the LBUS daisy chain.
!
6 The brake
!
The DRW-1 wheels are equipped with a brake
lever, which goes back to the ARRI Gear Head.
The brake lever allows the operator to engage or !
disengage the wheel from the selected motor axis.
NOTE
An unlocked wheel will be indicated by a green LED,
A locked wheel will be indicated by a red LED.
NOTE
Disengaging the wheels can also support operation.
When you need to reproduce a movement and you want the position of the crank
to be at a certain angle, for example at the end of the movement, than first move the
head to the desired end position, disengage the wheel and bring the crank to the
required angle.
Now engage the wheel again and move the head backwards to the starting point.
Start the movement from the beginning.
!
7 Fluid Drag Ring (friction)
!
The DRW-1 wheels are equipped with a fluid drag ring, !
which allows friction to be adjusted.
!
This unique feature allows the operator to control the !
accuracy of the head through a mechanical friction !
adjustment instead of a software value such as ramp.
Due to the mechanical friction, the ramp values !
in the remote control can be set to 0 or close to 0. !
The mechanical friction ensures that the DRW-1 wheels !
and remote head respond quickly and accurately.!
Wheel Setup
Unlocked
Locked
9
Softer
Harder

!
8 Remote Control Setup
!
8.1!
Auto Assignment DRW-1!
!
SUP2.2 introducing the so-called Auto Assignment. !
!
For a fast and easy setup, this menu!
will show up, as soon the DRW-1 is !
connected to the remote control.!
!
The Auto Assignment will set: !
!
• DRW-1 Tilt, Pan and Roll axes
• SENSITIVITY to 0
• DEADBAND to 0
• RAMP to 0!
• MODE Angle
!
!
8.2
Quick Setup!
!
1. Daisy chain the single modules with each other
2. Connect the LBUS cable to the remote control
3. Select Pan, Tilt, Roll for each DRW-1 module
4. Press OK at the the touchscreen
Selecting OK automatically sets all required values.!
!
!
NOTE!
Press Cancel if the DRW-1 has already been
assigned and personal values have already been set.!
!
Press OK to overwrite your previous settings.!
!
The Auto Assignment function can be deactivated in the settings for the remote control.!
8.3
Selecting the Mode
There are two ways to use the DRW-1: Angle Mode (preset) and Speed Mode.!
!
Angle Mode the right choice when !
extremely precise movements are needed.!
!
Every movement of the DRW-1 is transferred to !
the remote head with the exact degree of precision.!
!
Speed Mode is the right mode when high !
dynamic action needs to be covered.!
Touch Menu at the lower right corner of the
home screen to reach the Main Menu.
In the Main Menu select Head to reach
the head menu.!
Touch Mode to toggle between Angle and Speed.
Press Save after the Mode is selected."
Remote Control Setup
10
1
2
3
4

!
!
8.4
Speed setup in Angle Mode!
!
NOTE!
In order to operate the DRW-1 correctly in Angle Mode, !
the following settings shall be made:!
•Speed 100
•SENSITIVITY set to 0
•DEADBAND set to 0
•RAMP set to 0
•Ratio set to 0
In the factory preset setup, the Speed is !
assigned to the knobs K1, K2 and K3.
!
NOTE!
In order to achieve a faster movement in Angle Mode, the Ratio values must be adjusted. !
See page 12.!
!
!
8.5!
Speed setup in Speed Mode!
!
NOTE!
In order to operate the DRW-1 correctly in Speed Mode, !
the following settings shall be made:!
!
Speed 01 - 100
•SENSITIVITY set to 0
•DEADBAND set to 0
•RAMP set to 0
•Ratio set to 0!
A lower Speed value will under crank the movement
of the remote head. !
A higher Speed value will over crank the movement !
of the remote head.
!
!
8.6
Ramp (K4, K5, K6)!
!
In the factory preset setup, ramp is assigned to the knobs K4, K5 and K6.
Initially, ramp should be set to 0.
NOTE
A high positive ramp value will delay the !
response of the remote head!!
The DEH-1will start and stop progressively !
softer as the value increases.!
!
NOTE!
By unassigning K4. K5. K6 you can set individual !
ramp values for start and stop for each axis. !
The setting is then made via the touchscreen, by Selecting !
Menu, Controls, Position, Ramp Start and Ramp Stop.!
Remote Control Setup
11
100
100

!
!
8.6!
Ratio (Angle Mode)!
!
Because the ARRI DRW-1 wheels are the digital version of the ARRI Geared Head 2, !
the DRW-1 wheels also offer the classic 3-speed drive with the original gear ratio.!
!
NOTE!
Once the DRW-1 wheels are connected to the remote control, the Ratio value !
is set to the classic Medium Speed of the ARRI Geared Head 2.!
!
!
!
!
!
!
!
!
!
!
!
!
!
!
!
!
!
!
!
!
!
!
NOTE!
To adapt the DRW-1 to the other classic gear ratios
of the ARRI Geared Head 2, the gear ratios listed
above must be programmed for each axle.!
!
Selecting Menu, will open the Main Menu.!
!
Selecting Controls, will open the Controls Menu!
!
Selecting Ratio opens a new submenu in !
which the required speed ratio of the Pan,
Tilt and Roll axes can be adjusted.!
NOTE
In Angle Mode changing the ratio value !
will move the remote head to a new position.
!
Therefore use the +and - keys to change !
the ratio value carefully.!
!
Press OK "
Remote Control Setup
12
Tilt Speeds:
Turns
Movement
Ratio
value
Angle per !
one Turn
Slow
17.5
for 60° Tilt
-21
5,51°
Medium (preset)
9.25
for 60° Tilt
0
10,14°
Fast
4.75
for 60° Tilt
22
19,06°
Tilt Speeds:
Turns
Movement
Ratio
value
Angle per !
one Turn
Slow
65
for full 360° Pan
-22
3,45°
Medium (preset)
35.5
for full 360° Pan
0
6,49°
Fast
19
for full 360° Pan
23
12,45°
Roll Speeds:
Turns
Movement
Ratio
value
Angle per !
one Turn
Slow
17.5
for 60° Tilt
-22
3,45°
Medium (preset)
9.25
for 60° Tilt
0
6,49°
Fast
4.75
for 60° Tilt
22
12,45°

!
!
8.7
Changing Direction!
!
For a fast adjustment, the home screen !
of the remote control offers a short cut.
!
This field indicates the selected !
direction of the assigned controller.!
Selecting Dir will open the Direction submenu. !
!
Selecting the field in the middle toggles between !
Standard and Reverse.!
!
Press OK
!
!
!
!
9 Additional Setups!
9.1
Assigning the DRW-1
NOTE !
The DRW-1 shall be assigned to the
corresponding axes of the remote head.
For a fast selection, the home screen of !
the remote control offers a short cut.
Selecting the indicated area below the single !
axis will open the assignment submenu.
!
Select DRWP in the submenu to assign!
the Pan axis of the DHE-1 to the Pan axis !
of the remote head.
Press Assign.!
!
Select DRWT in the submenu to assign!
the Tilt axis of the DHE-1 to the Tilt axis !
of the remote head.
!
Press Assign.!
!
!
!
!
Unassigning Controllers
To unassign a selected controller, touch Unassign.!
!
NOTE
After the controller has been unassigned, !
the function is only available via the touchscreen.
Assign Pan Setpoint
DRWP DRWT K1 K2
Assign Pan Setpoint
DRWP DRWT K1 K2
13
Remote ControlSetup

!
9.2
Selecting Position will open up a submenu for: !
Deadband, Sensitivity, Filter, Ramp and !
Ramp Mode.
!
9.3!
Deadband !
!
Selecting Deadband opens a new touchscreen !
slider that allows to change the Deadband !
values on the selected axis.
!
Deadband sets the starting point of the control. !
This value defines when the setpoint will react !
after the control was changed.!
!
NOTE!
If the DRW-1 wheels is used as a controller, !
Deadband shall be set to 0!!
Otherwise there would be a delay in response!
!
9.4 !
Sensitivity!
!
Selecting Sensitivity will open a new touchscreen !
slider that allows you to change the sensitivity of the !
control device for the selected axis.
NOTE
Redo the procedure for the other axes and press OK.!
9.5
Filter!
!
Additional low pass filter function for encoder !
based controllers, like the DRW-1.!
!
When the DRW-1 is used in a car or a train, !
vibrations of the vehicle may be transmitted to !
the DRW-1's encoders.!
This can lead to irritations in the pan and tilt axis.!
In case of such irritations, the operator can use !
the Filter function to set a low-pass filter value,
which allows to eliminate these disturbing vibrations. !
!
NOTE!
A too high Filter value may cause a delay in !
response.!
Remote Control Setup
14

!
10 Power Disconnection!
!
!
!
!
!
!
!
11 Sets
!
11.1
DRW-1, Two Wheels Set KK.0021212
contains!
2 x DRW-1 Module K2.0019319
2 x Hand Wheel complete 50 N2.25004.A
1 x DRW-1 Mounting Base K2.0019325
1 x Cable LBUS 0.3m/1ft K2.0006750
1 x Cable LBUS 0.5m/1.5ft K2.0006751
1 x DRW-1 Foam Set 90.0020791
4 x M6x12 stainless hex screws O5.15436.0!
1 x DRW-1 User Manual K4.0021085!
!
11.2!
Optional Third Wheel Set KK.0021211 !
!
contains
1 x DRW-1 Module K2.0019319
1 x Hand Wheel complete 150mm N2.25004.A
1 x Cable LBUS – LBUS (0.5m/1ft) K2.0006751
1 x DRW-1 THIRD-WHEEL-SET-PACKING-SET 90.0021210!
!
12 Technical Data
12.1 !
Weight / Dimensions
Weight:
DRW-1 Modul 0,7kg / 1,5lb
DRW-1 Mounting Base 1,5kg / 3,3lb
Hand Wheel 0,8kg / 1,7lb
Outer dimensions foam 518 x 392 x 229 mm
20,39 x 15,43 x 9,01“
12.2!
Environment
Temperature Range -20°C - 50°C
-04°F - 122°F!
!
13 Pinout
!
Appendix
15
To disconnect the device safely from the power source, remove both cables !
from the remote head and remote control.!
Mount and operate the device in an orientation to ensure easy access to the
connectors.
!CAUTION
42 Appendix
15.2 Pinouts
LBUS Connector
1 GND Ground
2 CAN-L CAN bus
3 V-BAT Power supply in-/output
4 CAN-H CAN bus

!
EU–Declaration of Conformity
!
!
Brand Name: ARRI !
Product Description: Camera Stabilizer System:
•ARRI Stabilized Remote Head SRH-3 Pro Set including ARRI Stabilized Remote Head – SRH-3 !
and ARRI Remote Remote control – Remote control-1
+ Europe Setting for Software 01.14.00 or later and Antenna Proant 333 Ex-It 2400 Foldable, Accessories
regarding Apendix I
The designated products conform to the specifications of the following European directives:
1. Directive 2014/53/EU of the European Parliament and the Council of 16 April 2014 on the
harmonisation of the laws of the Member States relating to the making available on the market of
radio equipment - OJ L 153, 22 May 2014, p. 62–106
2. Directive 2011/65/EU of the European Parliament and the Council of 8 June 2011 on the restriction
of the use of certain hazardous substances in electrical and electronic equipment - OJ L 174, 1
July 2011, p. 88–110
The compliance with the requirements of the European Directives was proved by the application of the
following standards:
Essential Requirements regarding No 1
•Art. 3.1 a following 2014/35/EU !
o EN 62368-1: 2014 + AC:2015-05 + AC:2015-11; EN 60950-1:
2006+A11:2009+A1:2010+A12:2011+AC2011+A2:2013 ; EN 62479 :2010
•Art. 3.1 b following 2014/30/EU!
o EN 301 489-1 V2.1.1; EN 301 489-17 V3.1.1; EN 61000-4-2:2009; EN 61000-4-3:2006 !
A1:2009 A2:2010 ; EN 55032: 2012, EN 55035 :2017
•Art. 3.2 !
o EN 300 328 V2.1.1;!
Essential Requirements regarding No 2!
• EN 50581: 2012;
To evaluate the respective information, we used: !
http://ec.europa.eu/growth/single-market/european-standards/harmonised-standards/index_en.htm
Year of affixed CE-marking: 2018
Munich 13.12.2018 !
!
Sign Sign
!
Walter Trauninger Dr. Sebastian Lange!
Managing Director Head of Quality Management
APENDIX-I !
!
List of additional accessories:!
!
Item Model name!
1 ARRI Digital Remote Wheels - DRW-1
"
16
International Declarations

!
14 International Declarations
17
International Declarations
Trade Register Munich
HRB 85742
VAT ID No. DE129484267
Information pursuant to Section 2(1)
DL-InfoV (Germany) at
www.tuev-sued.com/imprint
Managing Directors:
Dr. Jens Butenandt
Holger Lindner
Phone: +49 9421 55 22-0
Fax: +49 9421 55 22-99
www.tuev-sued.de
TÜV SÜD Product Service GmbH
Äußere Frühlingstraße 45
94315 Straubing
Germany
Prüfbericht / Test Report
Nr. / No. TR-25880-43304-01 (Edition 01)
Auftraggeber
Applicant
FoMa Systems GmbH
Geräteart
Type of equipment
Digital Remote Wheel
Typenbezeichnung
Type designation
DRW-1
Seriennummer /
Serial number
Prototype
Auftragsnummer /
Order No.
---
Prüfgrundlage
Test standards
EN 55032:2012 (KN32)
EN 55035:2017 (KN35)
CISPR 32:2015
2018-11-27
Page 1 of 42

!
"
18
International Declarations
TÜV SÜD Product Service GmbH
Äußere Frühlingstraße 45
94315 Straubing
Germany
Phone: +49 9421 5522-0
Fax: +49 9421 5522-99
Web: www.tuev-sued.de
Test Report No. TR-25880-43304-01 (Edition 01)
Page 2 of 42
Summary
Prüfergebnisse / Test Results
Auftragsnummer / Order No.
---
Die Prüfungen wurden nach folgenden Vorschriften durchgeführt:
Tests were performed according to:
EN 55032:2012 (KN32); EN 55035:2017 (KN35); CISPR 32:2015
Durchgeführte Prüfung
Test performed
Prüfergebnis
Test result
Radiated Emissions (Class A limits)
Pass
Conducted Emissions at Mains Power Ports
N/A
Conducted Emissions at Communication Ports
N/A
Enclosure Port - Radio-frequency electromagnetic field Amplitude modulated
Pass
Enclosure Port - Power-frequency magnetic field
Pass
Enclosure Port - Electrostatic discharge
Pass
Signal Port - Radio-frequency continuous conducted
Pass
Signal Port - Electrical fast transient
Pass
DC Power Port - Radio-frequency continuous conducted
Pass
DC Power Port - Electrical fast transient
Pass
Bemerkungen / Remarks:
The EuT is Battery powered. Therefore a test of the DC line is not necessary according the used standard.
Die Prüfergebnisse beziehen sich ausschließlich auf das zur Prüfung vorgestellte Prüfmuster. Ohne schriftliche Genehmigung des
Prüflabors darf der Prüfbericht auszugsweise nicht vervielfältigt werden. The test results relate only to the individual item which has been
tested. Without the written approval of the test laboratory this report may not be reproduced in extracts.
Datum / Date
Geprüft von / Tested by
Freigabe durch / Checked by
Prüfergebnis / Test Result
Pass
2018-11-27
Thomas Winterberger
Responsible for testing
Hannes Adelsberger
Reviewer

!
19
International Declarations
Trade Register Munich
HRB 85742
VAT ID No. DE129484267
Information pursuant to Section 2(1)
DL-InfoV (Germany) at
www.tuev-sued.com/imprint
Managing Directors:
Dr. Jens Butenandt
Holger Lindner
Phone: +49 (0) 9421 55 22-0
Fax: +49 (0) 9421 55 22-99
www.tuev-sued.de
TÜV SÜD Product Service GmbH
Äußere Frühlingstraße 45
94315 Straubing
Germany
TÜV SÜD Product Service
RESPONSIBLE FOR
NAME
DATE
SIGNATURE
Project Management
Thomas Winterberger
2018-11-28
Authorised Signatory
Hannes Adelsberger
2018-11-28
Signatures in this approval box have checked this document in line with the requirements of TÜV SÜD Product Service document control rules.
ENGINEERING STATEMENT
The measurements shown in this report were made in accordance with the procedures described on test pages. All reported testing
was carried out on a sample equipment to demonstrate limited compliance with FCC 47 CFR Part 15B and ICES-003. The sample
tested was found to comply with the requirements defined in the applied rules.
RESPONSIBLE FOR
NAME
DATE
SIGNATURE
Testing
Thomas Winterberger
2018-11-28
Laboratory Accreditation
DAkkS Reg. No. D-PL-11321-11-02
Laboratory recognition
Registration No. BNetzA-CAB-16/21-15
Industry Canada test site registration
3050A-2
EXECUTIVE SUMMARY
A sample of this product was tested and found to be compliant with FCC 47 CFR Part 15B and ICES-003:2017 and 2016.
Report on the FCC and IC Testing of the
FoMa Systems GmbH
Digital Remote Wheel. Model: DRW-1
In accordance with FCC 47 CFR Part 15B and
ICES-003
Prepared for: FoMa Systems GmbH
Oskar-Sembach-Ring 11
91207 Lauf - Germany
FCC ID: ---
ICES: ---
COMMERCIAL-IN-CONFIDENCE
Date: 2018-11-28
Document Number: TR-25880-43304-02 | Issue: 01
DISCLAIMER AND COPYRIGHT
This non-binding report has been prepared by TÜV SÜD Product Service with all reasonable skill and care. The document is confidential to the
potential Client and TÜV SÜD Product Service. No part of this document may be reproduced without the prior written approval of TÜV SÜD
Product Service. © 2018 TÜV SÜD Product Service.
ACCREDITATION
Our BNetzA Accreditation does not cover opinions and interpretations and any expressed are outside the scope of our BNetzA Accreditation.
Results of tests not covered by our BNetzA Accreditation Schedule are marked NBA (Not BNetzA Accredited).

!
Trade Register Munich
HRB 85742
USt.-Id.-Nr.: VAT ID No. DE129484267
Information pursuant to Section 2(1)
DL-InfoV (Germany) at
www.tuev-sued.com/imprint
Managing Directors:
Dr. Peter Havel
Dr. Jens Butenandt
Holger Lindner
Phone: +49 9421 55 22-0
Fax: +49 9421 55 22-99
www.tuev-sued.de
TÜV SÜD Product Service GmbH
Äußere Frühlingstraße 45
94315 Straubing
Deutschland Germany
DRW-1 Module, K2.0019319DRW-1 Module, K2.0019319Digital Remote WheelDigital
Remote WheelArnold & Richter Cine Technik GmbH & Co Betriebs KGArnold &
Richter Cine Technik GmbH & Co Betriebs KG
Prüfbericht / Test Report
Nr. / No. TR-80986-44626-01(Edition 1)
Auftraggeber
Applicant
Arnold & Richter Cine Technik GmbH & Co Betriebs KG
Geräteart
Type of equipment
Digital Encoder Head
Typenbezeichnung
Type designation
DEH-1, K2.0022594
Auftragsnummer /
Order No.
---
Prüfgrundlage
Test standards
EN 60950-1:2006 + A11:2009 + A1:2010 + A12:2011 + A2:2013 + AC:2011
December 12, 2018
Page 1 of 34
20
International Declarations
Other manuals for DRW-1
1
Table of contents
Other ARRI Controllers manuals
Popular Controllers manuals by other brands
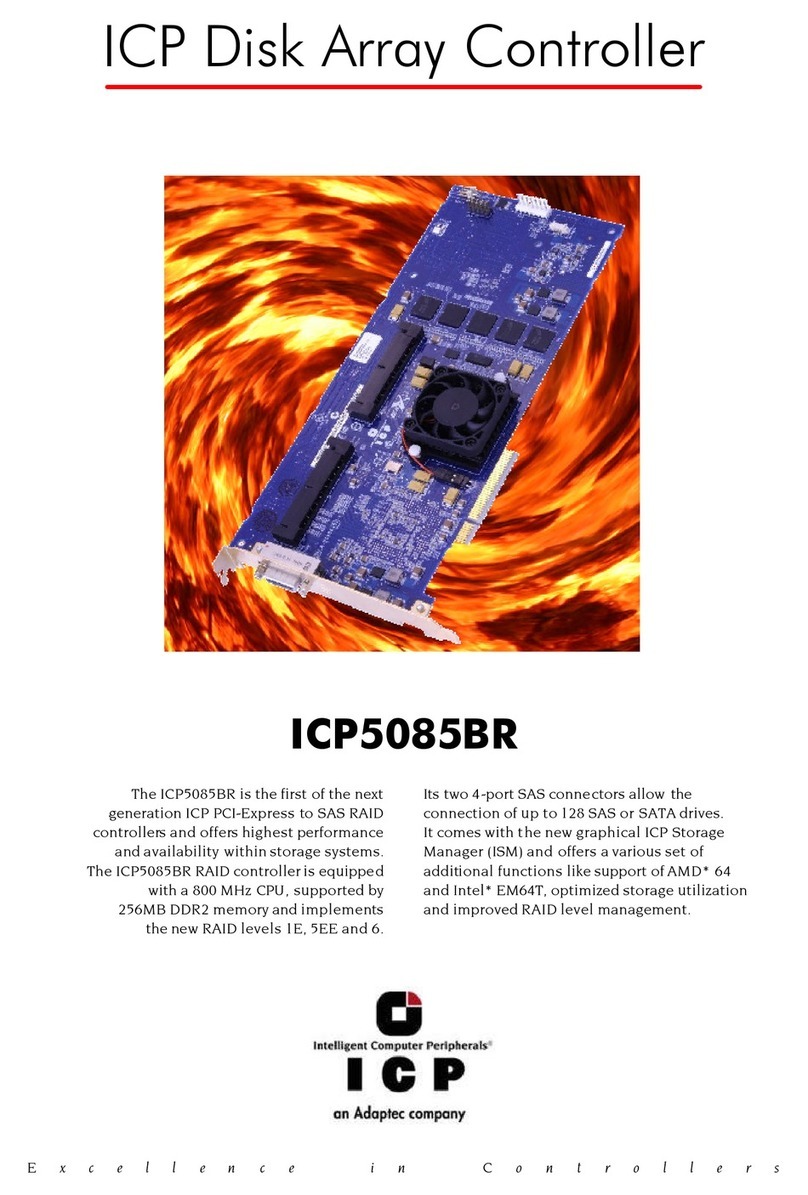
ICP
ICP ICP5085BR specification
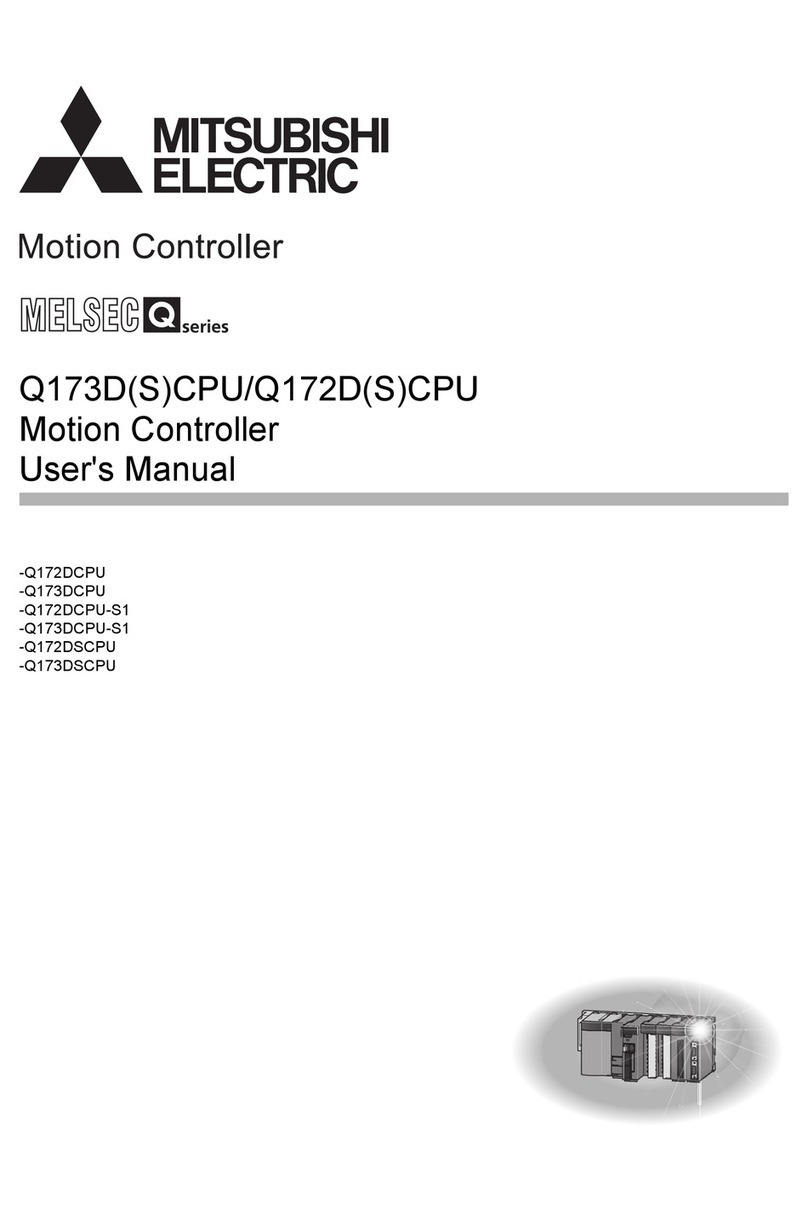
Mitsubishi Electric
Mitsubishi Electric Melsec-Q172DCPU user manual
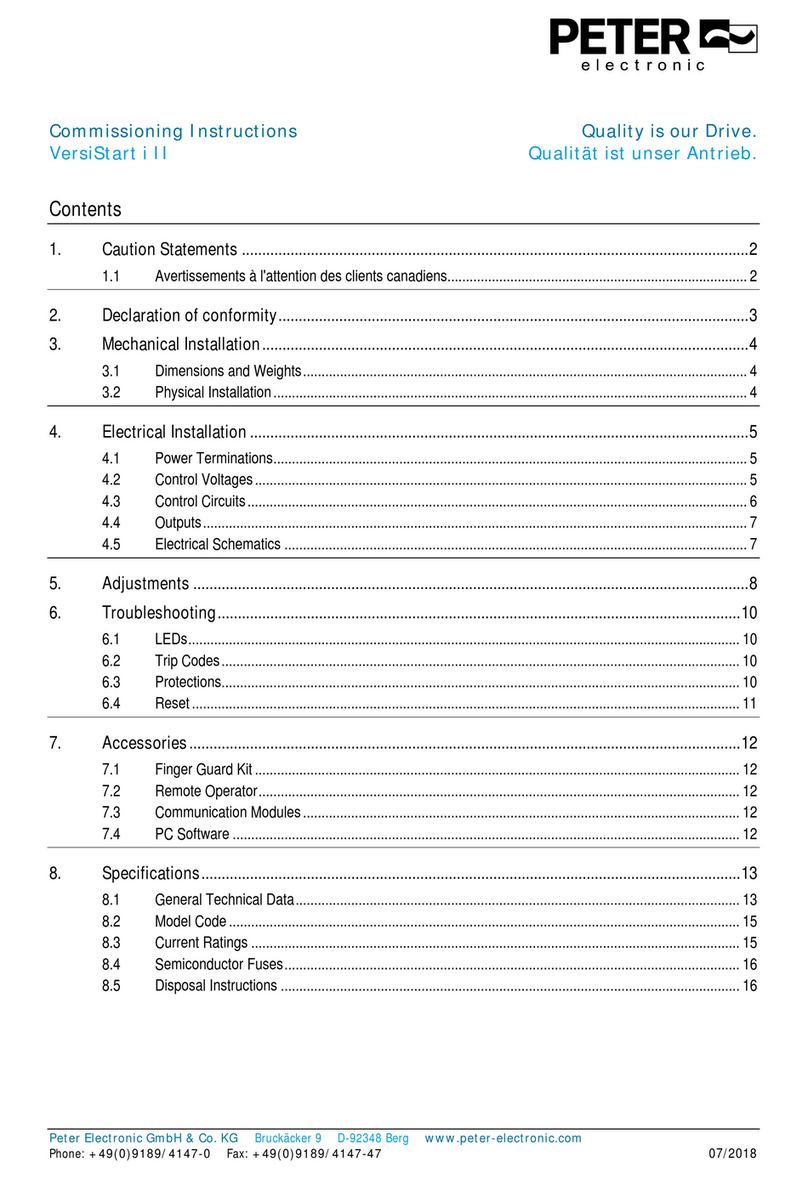
Peter electronic
Peter electronic VersiStart i II Commissioning instructions
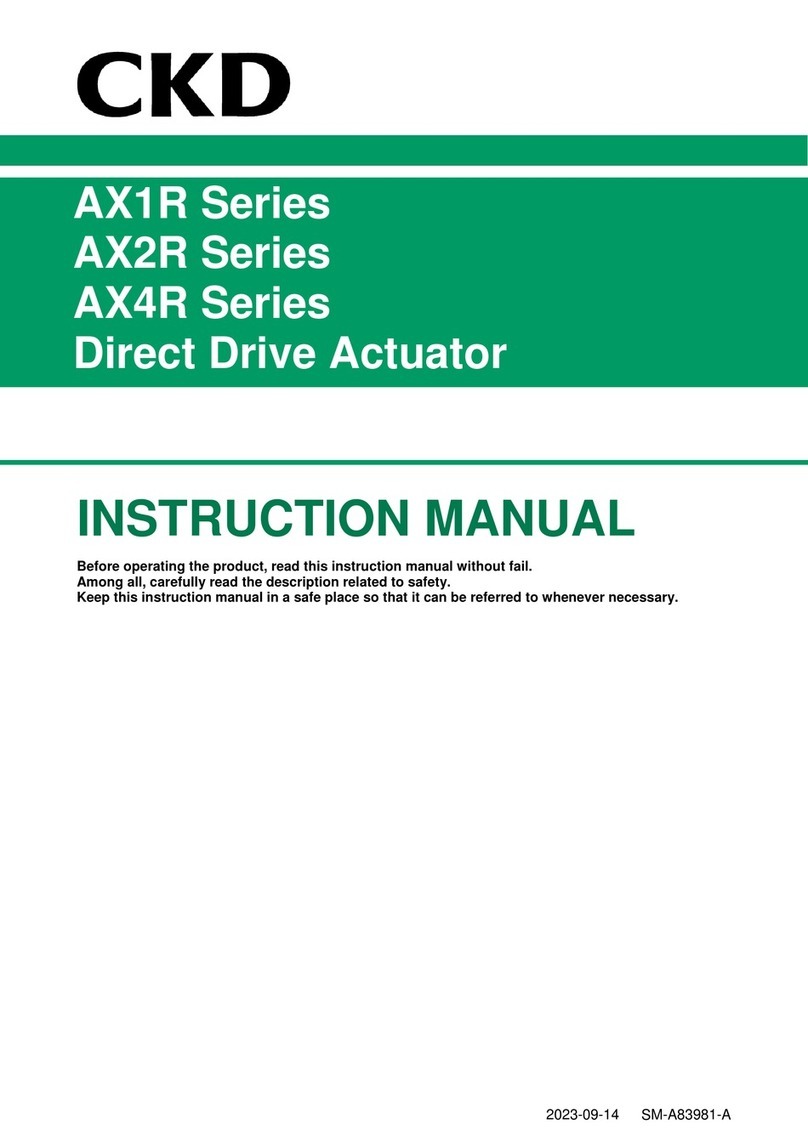
CKD
CKD AX1R Series instruction manual
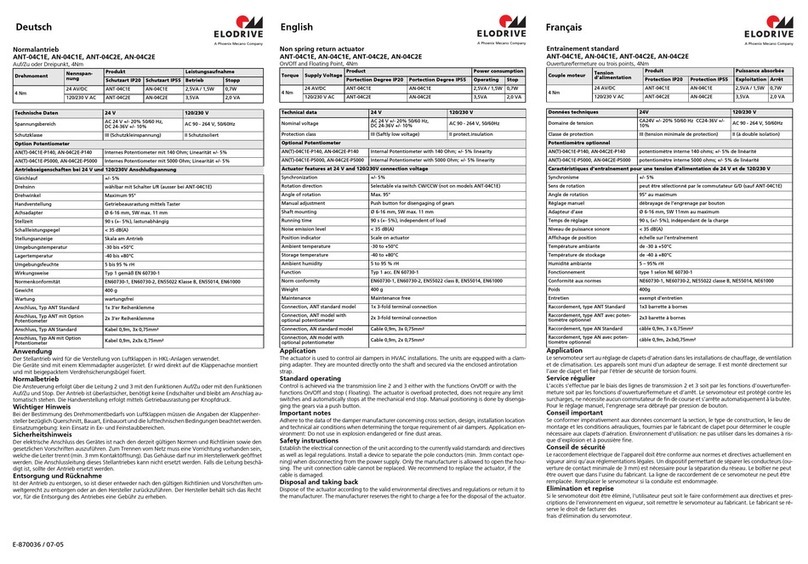
Phoenix Mecano
Phoenix Mecano Elodrive ANT-04C1E quick start guide
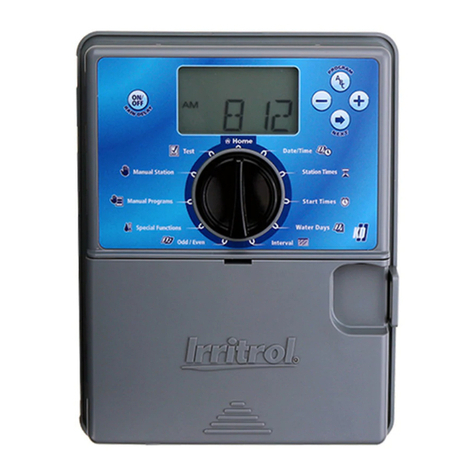
Irritrol
Irritrol KD2 user guide
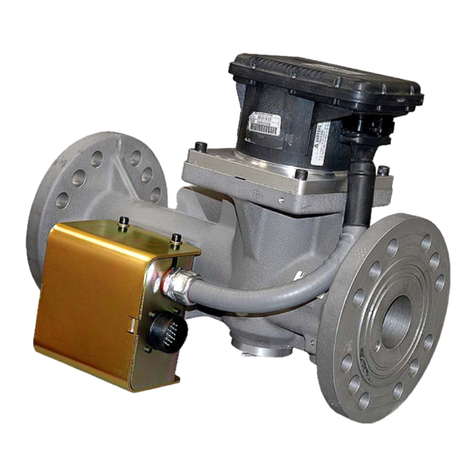
Woodward
Woodward TecJet 52 Installation and operation manual
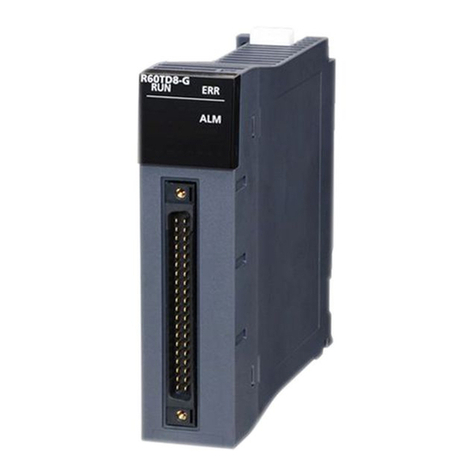
Mitsubishi Electric
Mitsubishi Electric R60TD8-G user manual

Santerno
Santerno SINUS PENTA Series Guide
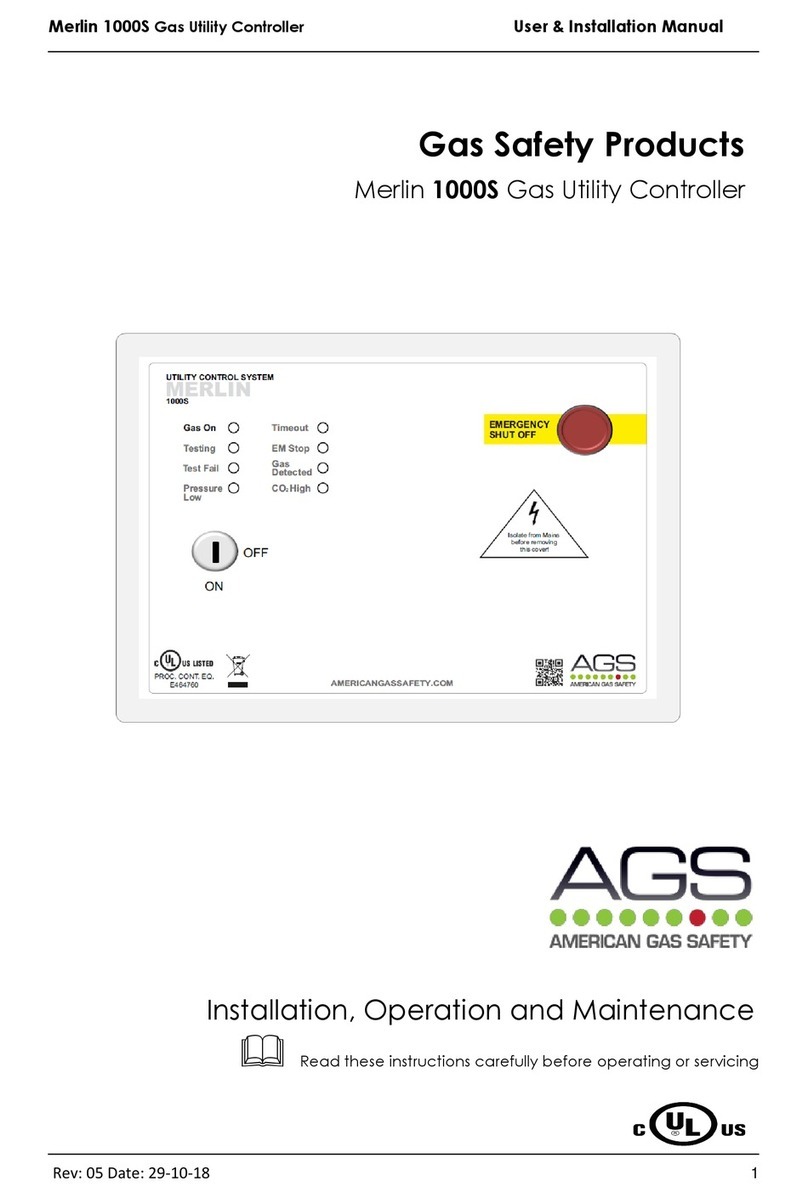
AGS
AGS Merlin 1000S Installation, operation and maintenance guide
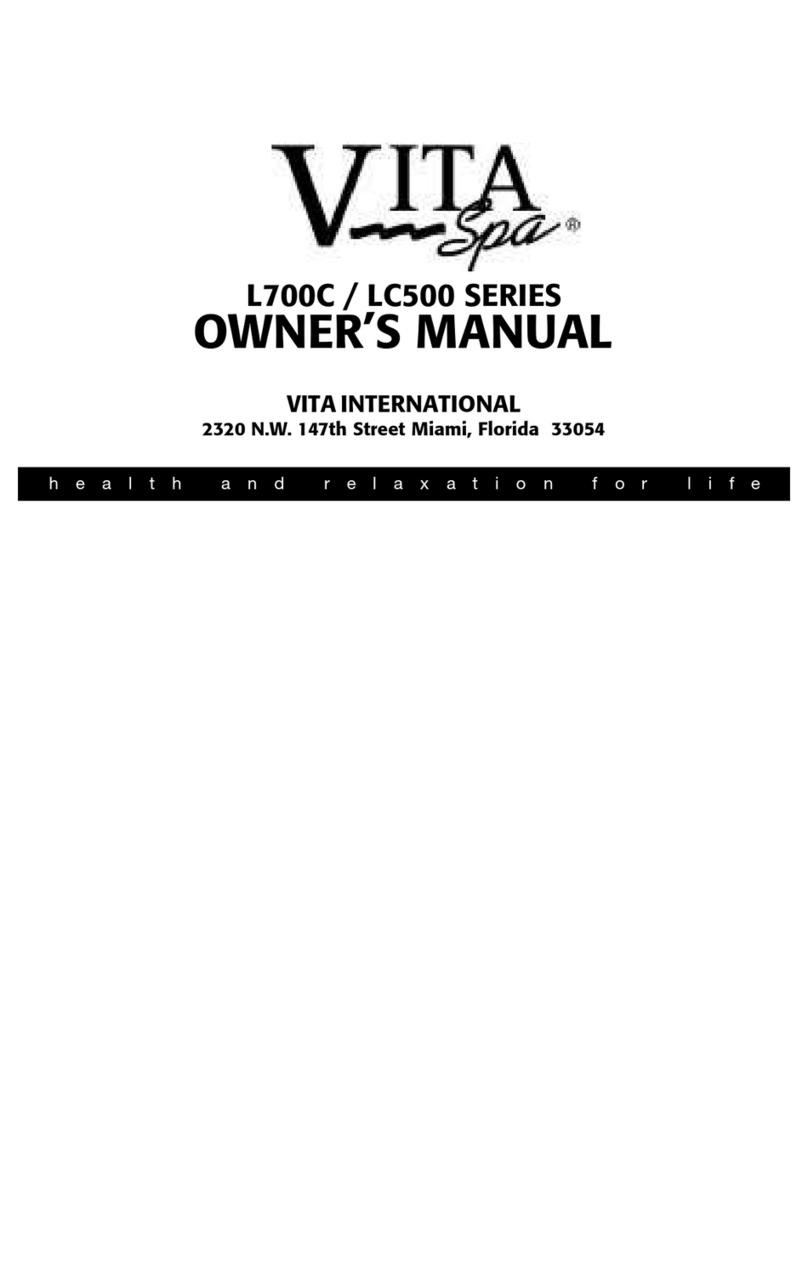
Vita Spa
Vita Spa L700C Series owner's manual
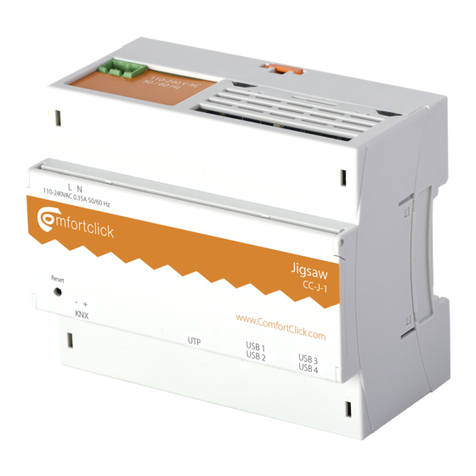
ComfortClick
ComfortClick Jigsaw manual