ASEG GALLONI MODULAR 6 Operating instructions

1
ELECTRONIC INDUCTION CENTRIFUGAL CASTING MACHINE
MOD. MODULAR 6
WITH OPTICAL PYROMETER
OPERATING AND MAINTENANCE MANUAL
EDITION 07-2007

2
CONTENTS
Preface
3
Declaration of Conformity
4
Warnings and precautions
5
Induction heating principle
6
Electronic centrifugal casting machine mod. MODULAR 6
7
Installation instructions
8
Control panel
10
Temperature controller
11
Operating instructions
12
Crucibles
14
Technical information on melting process
15
Melting and casting process
16
Maintenance
19
Normal outfit
20
Wiring diagram components
21
Wiring diagram
22
Operational Board
23
Demolition and disposal
24
Index of the revisions
25
MODULAR 6

3
The manufacturer of this electronic induction centrifugal casting machine congratulates you on your choice which
will fully satisfy your most demanding casting needs.
Since you are the real user of our machine please do not hesitate to let us have your comments, suggestions on the
function of the machine you bought or to ask for any information.
HAVE A GOOD WORK !
This manual gives you the information you need to obtain the best use of your new electronic centrifugal casting
machine.
The more you understand about your casting machine before using it, the greater will be your satisfaction when
you find out its ease of use, its operation speed and its performance quality.
PREFACE
MODULAR 6

4
THE COMPANY
ASEG GALLONI SPA
20078 SAN COLOMBANO AL LAMBRO (MI)
VIA CARAVAGGIO 16
DECLARES UNDER ITS OWN RESPONSIBILITY THAT THE PRODUCT
ELECTRONIC CASTING MACHINE MOD. MODULAR 6
SERIAL NO. _________
IS IN CONFORMITY WITH THE MACHINE DIRECTIVE 98/37/CEE AND TO
THE ELECTROMAGNETIC COMPATIBILITY DIRECTIVE (EMC) 89/336/CEE
AND SUBSEQUENT MODIFICATION 92/31/CEE, TO THE LOW TENSION
DIRECTIVE 73/23CEE AND SUBSEQUENT MODIFICATION 93/68/CEE.
SAN COLOMBANO, THE_______________
___________________________
DECLARATION OF CONFORMITY
MODULAR 6

5
WARNINGS AND PRECAUTIONS
IT IS FORBIDDEN TO REMOVE THE PANELS FROM THE MACHINE IF IT
HAS NOT BEEN PREVIOUSLY UNPLUGGED.
DANGER
THE ELECTRIC SYSTEM OF THE ROOM WHERE THE MACHINE IS
INSTALLED, MUST HAVE AN ELECTRICAL GROUND IN COMPLIANCE
WITH THE REGULATIONS IN FORCE.
ATTENTION
PERSONS WHO HAVE THE “PACE-MAKER” MIGHT BE
AFFECTED
ATTENTION
UNPLUG THE MACHINE FOR ITS PERIODIC CLEANING AND USE VACUUM
CLEANER OR DRY CLOTH: DO NOT USE COMPRESSED AIR, WATER OR
CLEANSING AGENTS.
ATTENTION
INFLAMMABLE LIQUIDS AND GASES MUST BE PLACED DISTANT FROM
THE MACHINE DURING ITS USE
DURING THE MELTING AND CASTING PROCESS THE OPERATOR MUST
WEAR PROTECTIVE GLOVES AND GOGGLES PRESCRIBED BY THE
SAFETY REGULATIONS IN THE FOUNDRIES.
WARNING
DANGER
MODULAR 6

6
THE INDUCTION HEATING PRINCIPLE
The induction heating principle consists in placing a metal within the influence of an oscillating magnetic field at
a determined frequency such as the one generated by an induction coil. In the centrifugal casting machine mod.
MODULAR 6 the frequency is 80 KHz.
All metals have induced within them “eddy currents” and the metal electrical resistance to these
currents provokes a temperature rise and eventual melting.
The “eddy currents” form a molecular movement in the melting metal and give a thermic homogeneity to the
melting mass as depicted by the pictures.
The induction heating results to be the best thermic energy source for melting and offers the following
advantages:
– unchanged metallurgical characteristics: elasticity, homogeneity, and ductility
– silent and clean working conditions
– higher purity of the molten metal
– great productivity
– high melting temperatures without jeopardizing the machine components
PICTURE 1 PICTURE 2
MODULAR 6

7
ELECTRONIC CENTRIFUGAL CASTING MACHINE MODULAR 6
Centrifugal casting into flask
This electronic induction centrifugal casting machine has been built using the best technology and has a control
lay-out which is very operator-friendly.
It is designed for melting and casting the following alloys for dental use:
•
precious and non precious alloys for ceramic and resin
•
chrome cobalt molybdenum.
With the temperature controller it is possible to read and hold the casting temperature, obtaining the complete
fluidity of the metal which will be cast into the flask during centrifugation and reach the thinnest part of the model.
To facilitate the molten alloys to smoothly flow out of the crucible during spinning the MODULAR 6 fits a
sloping crucible holding plate which also ensures a complete and smooth flow of those alloys with a low specific
weight. The MODULAR 6 fits a universal flask cradle i.e. with an easy movement of the lever it is possible to
adjust the flask support and any sprue button of the flask will be easily centered with the crucible exit hole. This
universal cradle is particularly suitable when using the technique of the free expansion without metal casting rings
.Normally 5 standard flask sizes are used; the smallest flask size of 30 mm diam. must be inserted in the ceramic
container given as normal outfit and both of them must be put in the burn-out furnace. This ceramic container will
maintain a constant temperature of the small flask during spinning.
ATTENTION: This machine must be only utilized for the intended purpose in accordance with the
seller’s instructions. Any other use is to be considered improper and consequently dangerous. The
manufacturer cannot be held liable for any damages caused for improper, wrong and unreasonable
uses.
ATTENTION: The use of non-genuine crucible which do not correspond to the parameters of the
machine final test will considerably shorten the life of the power generator.
TECHNICAL CHARACTERISTICS
Electrical singlephase 3 kW - see nameplate
Dimensions and Weight 600 mm w x 680 mm d x 930 mm h - 106 Kg
Frequency 80 KHz
Crucible capacity precious alloys max. 80 gr
chrome-cobalt molybdenum from 15/20 up to
100 gr
Flasks 30 mm diam. x 50 mm h. - to be used with
ceramic container A100.001
50-70-80-90 mm diam. x 55 mm h.
Water cooling 2 litres/m’ - 3 bar
MODULAR 6

8
INSTALLATION INSTRUCTIONS
THE ELECTRIC SYSTEM OF THE ROOM WHERE THE CASTING MACHINE
IS INSTALLED, MUST HAVE AN ELECTRICAL GROUND IN COMPLIANCE
WITH THE REGULATIONS IN FORCE.
ATTENTION
THE ROOM WHERE THE MACHINE IS INSTALLED MUST BE FREE FROM
SPRINKLINGS OF WATER, SAND BLASTING UNITS, ACID VAPOURS AND
DUST.
ATTENTION
IT IS FORBIDDEN TO REMOVE THE PANELS FROM THE MACHINE IF IT
HAS NOT BEEN PREVIOUSLY UNPLUGGED.
DANGER
INFLAMMABLE LIQUIDS AND GASES MUST BE PLACED DISTANT FROM
THE MACHINE DURING ITS USE
DANGER
MODULAR 6

9
After having removed the machine from the packing material install it proceeding as follows:
1 Fill the tank with normal or better demineralized water up to 3 cm (1”) from the rim and close it with its cover.
The two hoses, coming from the pump filter, must be dipped into water down to the tank bottom.
As the machine is operated, the water pump will automatically start the water circulation. Should the water
circulation fail or be insufficient, the pressure switch placed on the water pump will not allow power output.
It is recommended to periodically check the flow of the circulating water, which must be 2 litres per minute
and it is measured at the machine water outlet by means of the special bottle included in the standard outfit.
2 Check the voltage of the mains. Any variation beyond 10% plus or minus than the voltage indicated by the
nameplate does not allow regular operation of the machine. Connect the line cord to the singlephase 230 V
mains with regular grounding. A possible automatic safety breaker must have a 0,5 A differential switch.
3 IMPORTANT: the machine is electrically controlled by an overload safety switch in compliance with the CE
regulations which cuts off power in case of current overloads due to faults in the machine or to current surges
of the mains.
This switch is located up on the left of the front side of the machine and it is indicated with A2 in the drawing
table A of the trouble shooting manual.
Should it cut off, unplug the machine, remove the front panel and set it again on the ON position. Fit the front
panel, switch on the machine and should the overload switch remain on the ON position it means the cutting
off was due to any occasional cause, should it cut off again it is necessary to ask for the technical service and
to look for the cause.
With the due precautions the machine can be switched ON by an authorized operator with the removed
panel.
IMPORTANT NOTICE
For prevent the crucible holding plate Afrom breaking,
which slides against the flask when spinning is started,
place the ring Bin such a way to stop the travel of the
crucible holding plate abt 2 mm from the flask.
The ring B must be positioned in relation to the
length of the flask. Do not place it too distant from
the flask otherwise the crucible exit nozzle will not
reach the sprue button of the flask and the metal
might spill during spinning.
When using small flasks with 48-50 mm ø the small plate
Cis placed on the flask support to enable the sprue
button of the flask to be easily centered with the crucible
exit hole.
MODULAR 6

10
A MAIN SWITCH: it switches ON and OFF the machine.
C GREEN LED: when illuminated it shows that the heating power is available. This happens if the water
flow is two litres per minute, the induction coil is surrounding the crucible and the machine cover is
closed.
D ORANGE LED: when illuminated it indicates that the generator does not supply heating power because
water temperature has exceeded 60 °C or because the generator itself is faulty.
E POTENTIOMETER FOR HEATING POWER REGULATION AND CENTRIFUGE STOP: power
output is stepless. After each casting cycle bring the potentiometer to 0 to stop the centrifuge and have the
machine ready for the next cycle.
F TEMPERATURE CONTROLLER WITH DIGITAL DISPLAY (°C): it displays the actual
temperature of the metal being melted and the chosen casting temperature which is held by controlling the
power output.
H LEVER FOR RAISING AND LOWERING THE INDUCTION COIL
I LEVER FOR LOCKING INDUCTION COIL MOVEMENT
L OPTICAL SENSOR
PICTURE 3 PICTURE 4
CONTROL PANEL
D
C
F
E
A
L
I
H
MODULAR 6

11
TEMPERATURE CONTROLLER
1 Temperature is controlled with an infrared optical pyrometer.
2 Always place the lid cover on the graphite crucible.
3 The temperature controller does not function before reaching 800°C (1472 °F) and measures temperatures up
to 1550 °C (2822 °F).
The performance and the power of the machine enable to reach temperatures up to 2000 °C. For the best
accuracy of the temperature measurement the temperature controller is adjusted to display casting
temperatures up to 1550 °C
4 The temperature controller is always connected. The upper display
A
indicates the actual temperature of the metal being melted. The lower
display
B
indicates the chosen casting temperature. To set the casting
temperature SET POINT use the up or down buttons in the lower part
of the controller. The up button (
∧
∧∧
∧
) increases the SET POINT value
the down button (
∨
∨∨
∨
) decreases the SET POINT value.
To memorize the SET POINT value keep button F pushed until the
set point value will appear again on the display. If wishing to exclude
the SET POINT push button Oand the numbers 100.0 appear on the
display Band controller will show current temperature on display
A.
Should a number different from 100.0 appear on the display, push
button (∧) until 100.0 is reached.
To restore SET POINT setting, push button
O
again.
5 For chrome-cobalt the displayed temperature is accurate when the blue filter closes the window of the machine
cover. We recommend to exclude the SET POINT and to work on the maximum power position.
The blue glass filter must not close the window when melting precious alloys.
♦ PRECAUTIONS TO BE TAKEN DURING TEMPERATURE CONTROL
A During melting process, if some metal pieces stick isolated against the crucible wall while metal lying on the
crucible bottom is melting, temperature reading will be inaccurate. Check the melting process in the crucible
and using the appropriate rod drop the isolated metal pieces into the molten metal. These operations are made
with closed machine cover. The rods will be introduced through the mesh of the machine cover.
B When using the graphite crucibles it is the graphite which acquires heat from the coil and transfers it to the
metal. The light emitted by the heated graphite will be read by the optical sensor and consequently it is
necessary to regulate power in such a way to have a slow melting process so that the gradual temperature
increase is transferred to the metal and the colour of the crucible is similar to the colour of the melting metal.
C The alloys for dental application are more than 150 and during melting each of them emits a different light,
named “emissivity”, that is detected by the photodiode and transformed into temperature degrees with the
possible errors ranging from ± 2% to 5%.
D When the molten alloy takes a spherical shape, it has completely adhered to the crucible wall and the
superficial layer of oxyde breaks, it is the correct moment to start centrifugation.
An eventual waiting time of 5 t 15 seconds will depend on alloy quality and quantity and if metal is partially
recovered from previous castings. Take note of the thermal level value shown on the display A at the moment
of centrifugation : it will be an indication for all subsequent castings.
PICTURE 5
A
B
MODULAR 6

12
OPERATING INSTRUCTIONS
For a correct use of the electronic centrifugal casting machine MODULAR 4 proceed as follows:
1 The built-in water pump for closed circuit water cooling will automatically start the water circulation as the
machine is switched on.
2 Balance the centrifugal arm. Loosen the handwheel
which blocks the centrifugal arm. Balance is made
with the cold flask on before putting it in the furnace.
Move the counter weight to reach the balance using
the red signs as reference to each flask size. Block the
centrifugal arm.
3 Turn main switch A.
4 Bring the potentiometer E on 0.
5 Remember that the power is cut off when the machine
cover is lifted and it will be reset when the cover is
lowered. With a graphite crucible such temporary
lack of power is acceptable, but not in the case of a
ceramic crucible for casting high temperature
precious alloys or chrome-cobalt-molybdenum. In
the latter case, the flask should be introduced before
starting metal heating. The slight temperature
decrease of the flask before casting will have no
negative influence on the casting results.
6 Never start heating power if the crucible with the
metal has not been placed in the induction coil lest
probable damages in the power generator.
7 Put the crucible with the necessary quantity of metal
in the crucible holding plate. Set the casting
temperature (SET-POINT) in the controller F
according to the type of alloy to be melted.
8 With the right hand seize the lever H(picture 7
phase A) and with the thumb push the lever Ito the
left. With the left hand slide the crucible holding
carriage so that when raising the lever H with the
right hand, the reference pin, placed under the
crucible holding carriage will enter in the hole of the
coil support. When the lever H is up to end, push
lever Icompletely to the right (phase B).
9 Close the casting drum pulling the cover and give heating power with the
potentiometer Estarting from 0. Check if the led C is illuminated (if led Cis not
illuminated check if water circulation is missing or insufficient). The led Dmust be
ON.
10 Regulate heating power with the potentiometer Euntil the melting of the alloy is
reached.
11 When the metal is molten and ready to be cast, with the right hand seize lever H
(picture 8 phase C) and with the left hand bring lever I to the left in order to release
lever H. Lower lever Hmanually to the bottom (phase D). DO NOT DROP IT. Bring
lever I to the right to block lever Hat the bottom. The spinning of the centrifugal arm
and disconnection of heating power will automatically take place. During spinning
the cover will be locked.
ATTENTION: WHILE SPINNING NEVER RAISE LEVER H.
A
B
PICTURE 7
D
C
F
E
A
L
I
H
PICTURE 6
MODULAR 6

13
12 To stop spinning bring potentiometer E to zero. The cover is unlocked about 10
seconds after spinning has completely stopped.
13 Starting the heating power potentiometer from 0 repeat the cycle.
After about one hour of continuous work it is recommended to allow the water
to cool down even if the orange led is still illuminated. The orange led will be
OFF when water temperature reaches 45 °C and power will be automatically
interrupted.
CAUSE OF CRUCIBLE BREAKAGE THAT CAN OCCUR WITH HIGH-
TEMPERATURE ALLOYS AND PARTICULARLY WITH CHROME-
COBALT-MOLYBDENUM
– Check the melting process carefully. The melt must take place uniformly
throughout the alloy mass.
– If the metal pieces in the crucible does not lie together the pieces lying on the
crucible bottom will melt quickly whereas the isolated pieces on the top will
reach the melt with difficulty. If the operator waits until the metal on the top
melts it might happen that the metal on the crucible bottom reaches a so high
temperature to cause the crucible itself to melt and to break with the consequent
loss of metal.
– To prevent this risk, it is necessary to touch, with the steel rod supplied with the
outfit, the metal pieces on the top to join them with the pieces on the crucible
bottom. Regulate the heating power properly.
C
D
PICTURE 8
ATTENTION
THE CASTING MACHINE REGULATES THE WORK OF THE LABORATORY. IT
IS ADVISABLE TO KEEP IN STOCK THOSE PARTS WHICH ARE SUBJECT TO
WEAR-OUT, ARE NOT COVERED BY WARRANTY AND MIGHT NOT BE
AVAILABLE FOR A PROMPT DELIVERY.
CRUCIBLES
CRUCIBLE HOLDING PLATE code A107.126
DURING THE MELTING AND CASTING PROCESS WITH THE GRAPHITE
CRUCIBLE THE CERAMIC LID COVER MUST BE ON THE CRUCIBLE TO
PROTECT THE OPERATOR FROM POSSIBLE SPARKS OF MOLTEN METAL
WARNING
ATTENTION
PRACTICAL RECOMMENDATIONS FOR THE MELTING PROCESS WITH DIF-
FERENT ALLOYS WILL FOLLOW IN THE NEXT CHAPTER.
MODULAR 6

14
♦ Galloni experience has designed a line of graphite and ceramic crucibles to be used in the electronic
centrifugal casting machine mod. MODULAR 6. Their quality is superior:
–
in their compatibility with the alloys on the market
–
in their shape which optimizes the result of the casting pieces.
♦ The crucible is an integral part of the electronic casting machine, therefore it is imperative to use the Galloni
original crucibles to prevent the machine from being jeopardized.
♦ During heating the crucible might release gases or substances which affect the alloy: the careful use of Galloni
crucibles ensures the original purity of the alloys.
♦ Warranty fails if non original crucibles are used.
♦ Store crucibles in a dry place.
♦ Crucible production presents different technical difficulties also in connection with the materials which cannot
always be of the same quality and therefore the constant crucible life cannot be guaranteed.
♦ ATTENTION: Do not put the sprue button of the previous casting in the crucible in such a way that the button
edge is wedged against the crucible sides because during heating its expansion will cause the crucible to break.
♦ ATTENTION: When the crucible is hot it becomes brittle. Avoid pressing with the steel rod on the metal
pieces settled in the crucible.
–
A100.481 Highly resisting silicon nitride ceramic crucible for chrome-cobalt-molybdenum (100 gr)
– A100.425 Ceramic crucible for chrome-cobalt-molybdenum (100 gr).
– A100.059 Special graphite crucible for precious alloys (80 gr) up to 1450 °C.
– A100.460 Sinter crucible in glass carbon for all alloys containing over 30% palladium (80 gr) or
normal precious alloys.
CRUCIBLES
A100.059 A100.460
A100.425A100.481
MODULAR 6

15
TECHNICAL INFORMATION ON MELTING PROCESS
INFORMATION ON INDUCTION MELTING PROCESS
♦ The electromagnetic field (melting heat) heats the graphite crucible which transfers the heat to the alloy and
melts it.
♦ The electromagnetic field does not heat the ceramic crucible, it is the alloy which acquires the heat by
induction from the coil and melts.
♦ If the quantity of alloy in the ceramic crucible is small, its small mass will acquire a small part of the induction
field which will be not sufficient to reach the melt. It is necessary to follow the indications of the smallest alloy
quantities permitted in the ceramic crucibles given in the next chapters.
♦ The metals and the alloys have different behaviours towards the magnetic field. For example: the same mass of
gold behaves differently from the same mass of alloy for ceramic techniques or Chrome-Cobalt, therefore the
heating power must be regulated accordingly.
♦ The magnetic field generated by the induction coil which surrounds the crucible, reaches the highest efficiency
in the area indicated by W, therefore place the metal in this area.
♦ The metal must occupy the area indicated by Aand must be put together and close to the crucible sides. If, for
example, some small alloy plates or rods are put in the crucible vertically, these will not build a sufficient mass
to acquire the electromagnetic field (Fig. C).
♦ For heating process it is necessary to follow the instructions given in the next chapters.
♦ When the casting wax model is designed, take care to make the reduced sprue button Band not the large button
D otherwise the latter, if recovered, will not enter into the crucible properly and it will have difficulties to
reach the melt. Furthermore due to its thermal expansion, it may break the crucible.
D
C
MODULAR 6

16
MELTING AND CASTING PROCESS
MELTING AND CASTING OF CHROME -COBALT MOLYBDENUM WITH HIGHLY
RESISTING SILICON NITRIDE CERAMIC CRUCIBLE REF. A100.481 OR WITH
CERAMIC CRUCIBLE A100.425 CAP. 100 GR.
Chrome-Cobalt Molybdenum alloys melt differently from precious alloys. Precious alloys must be heated slowly
and remain in the crucible to heat-soak whereas Chrome-Cobalt Alloys must be melted quickly to ensure
unchanged properties of the alloys and as soon as the complete fluidity has been reached they must be cast. We
recommend to turn heating power potentiometer on a value between 80-100.
♦ Place the flask and the crucible on the centrifugal arm. Put CCM in the crucible (min.quantity 15-20 grs, max.
quantity 100 grs) taking care to put the metal on the crucible bottom and against the crucible walls. Start
melting process turning heating power switch to the highest position. Once the melting process has started do
not open the cover otherwise the heating power will be interrupted. If necessary collect the metal on the
crucible bottom using the steel rod which will be introduced through the mesh of the machine cover. Operate
very quickly to prevent the steel from melting. When CCM has reached the complete fluidity it is ready to be
cast.
♦ Melting must be checked by eye or by the temperature controller using the blue screen placed under the
machine cover. Move the screen by rotating the black knob on the cover. DO NOT SET THE SET POINT.
♦ After casting, Chrome-Cobalt alloys leave a thin trace of metal on the side of the crucible which spontaneously
gets detached from the crucible and must be removed by means of a small tongs. If the trace of metal is thick
and does not come out of the crucible it indicates that the alloy was not completely molten. Do not remove it
from the crucible to avoid damaging it.
♦ After the first casting, check the crucible for cracks:
–
if it shows large cracks do not use it for another melt
–
if it shows small cracks it is a normal settling of material which will not bring any technical problem
♦ The crucible is working under severe conditions. It reaches the temperature of 1500°C in 30/60 seconds, it
then cools down during spinning and is then subjected to the next cycle. The contractions are detrimental to the
crucible.
♦ The crucible life will be longer if castings are made successively one after the other: overage life 15-20
castings. If castings are made in interrupted sequences i.e. with long interval between one and the following
melting, crucible will cool down continuously and its life will be shorter: average life 8-10 castings.
A100.425A100.481
MODULAR 6

17
MELTING AND CASTING PROCESS
MELTING AND CASTING OF PRECIOUS ALLOYS WITH CRUCIBLE COMPOSED OF
AN INTERNAL GRAPHITE LINER A100.059 CAPACITY 80 gr Au
♦ The crucible is composed of an internal graphite liner of high quality. It is suitable for all precious alloys and
for ceramic alloys with a casting point of max 1450°C, excluding the precious alloys which have over 30%
palladium contents.
♦ For remelting old sprues, buttons, shanks, it is necessary to cut them into small pieces so that they perfectly
adhere to the crucible walls for an efficient heat transfer from crucible to metal. Generally it is recommended
to use 70% of new metal and 30% of old metal. The new metal usually in shape of small plates must be put first
in the crucible and when melting starts the old metal is added.
♦ During melting the graphite crucible produces a reducing atmosphere which will almost completely deoxidize
the precious alloy. Avoid the use of flux of whatever kind. Should the alloy be not completely clean, use pure
boric acid (H3B03) or deoxidizers supplied by the precious alloys manufacturers.
♦ It is always recommended a slow and gradual heating which can be easily reached since the machine OKAY
PLUS has a stepless heating power regulator: Recommended position from 20 to 40. Remember that the metal
is close to the melting point when the colour of the metal is approximatly the same as the graphite liner colour.
♦ All alloys have a “melting interval” expressed in temperature degrees, indicating the start of the melt and the
liquidus point ex. 1150-1200 °C. After the alloy has reached its liquidus point ( a complete melt) it is necessary
to attain the ideal casting temperature. This period of “overheating” the alloys is referred to as the “heatsoaking
interval”. The ideal casting temperature is generally 50-200 °C higher than the liquidus point of the alloy and
it must be left at this temperature from 5 to 30 seconds according to its quantity.
⇒EXAMPLE = Precious alloy with melting interval 1150-1200 °C and casting temperature 1350 °C.
–
Set the SET-POINT on 1350 °C and when this temperature has been reached, place the flask on the centrifugal
arm (when the machine cover is opened, power is interrupted and it will be automatically reset when cover is
closed). The operator will decide when it is the correct moment to cast. The heatsoaking interval from 5 to 30
seconds, depending on the metal quantity, is generally indicated by the alloy manufacturer or by personal
experience.
–
If necessary, collect the unmolten pieces on the crucible bottom using the steel rod which will be introduced
through the lid on the crucible.
A100.059
MODULAR 6

18
MELTING AND CASTING OF NON-PRECIOUS OR PRECIOUS ALLOYS FOR THE CERAMIC
TECHNIQUE WITH PALLADIUM CONTENTS OVER 30%.
♦ Non-precious alloys used for the ceramic technique melt in a particular way and do not always run together and
become a fluid mass. Certain alloys are molten when the piece of metal loses its shape and slumps. Some of
them need a slow heating and only by experience it is possible to determine which heating power rate must be
used. Use crucible A100.481
♦ The alloy must be put in the crucible as described in the section Chrome-Cobalt-Molybdenum melting and
casting process. Consider the points mentioned on page 15.
♦ For the precious alloys with palladium it is possible to use the ceramic crucible A100.481 in a min. quantity of
20 grs. We recommend the use of the Sinter glass carbon crucible A100.460 in which it is possible to melt
quantities of alloy from 5 to 80 grs.
♦ The use of the sinter crucible A100.460 requires a particular attention.
Put the alloy into the crucible and slowly heat it on a medium/high power position until the alloy reaches a dark
red colour. Increase the heating power slowly and gradually to enable the alloy to take the heat from the
crucible wall and reach the fluidity, checking that the colour of the crucible is same as the colour of the alloy.
If necessary use a very small portion of deoxidizer supplied by the precious alloys manufaturers. The crucible
has a long active life if it is used properly (40-60 castings).
♦ All alloys have a “melting interval” expressed in temperature degrees, indicating the start of the melt and the
liquidus point ex. 1150-1200 °C. After the alloy has reached its liquidus point ( a complete melt) it is necessary
to attain the ideal casting temperature. This period of “overheating” the alloys is referred to as the “heatsoaking
interval”. The ideal casting temperature is generally 50-200 °C higher than the liquidus point of the alloy and
it must be left at this temperature from 5 to 30 seconds according to its quantity.
⇒EXAMPLE = Precious alloy with melting interval 1150-1200 °C and casting temperature 1350 °C.
–
Set the SET-POINT on 1350 °C and when this temperature has been reached, place the flask on the centrifugal
arm. When the machine cover is opened, power is interrupted and it will be automatically reset when cover is
closed. The operator will decide when it is the correct moment to cast. The heatsoaking interval from 5 to 30
seconds depending on the metal quantity is generally indicated by the alloy manufacturer or by personal
experience.
♦ Heating process must take place slowly and gradully. It might be necessary with the use of a steel rod, to
collect the unmolten pieces on the crucible bottom. When the metal has slowly reached the complete melt, wait
5-10 seconds and then cast.
A100.481 A100.460
MELTING AND CASTING PROCESS
MODULAR 6

19
MAINTENANCE
1 During normal operation if there are some difficulties to reach melting temperature or the power disconnects
automatically, check the conditions of the induction coil which might be short-circuited for several reasons:
excess of dust, small metal pieces between turns, turns touching each other etc. Clean the coil periodically
using a toothbrush.
To replace the induction coil unplug the machine.
2 MAINTENANCE FOR THE CLOSED CIRCUIT WATER COOLING SYSTEM
–
TANK: change the water twice a year and clean the tank walls.
Should the green led not illuminate, this may mean the lack of water circulation due to lack of water, clogged
water pump filter or pump jamming.
–
To clean the water filter Funscrew the cover and remove it. Clean it with compressed air or ultrasonic
cleaner.
–
PUMP: after long periods of inactivity the pump might be mechanically jammed. Loosen the screw Vof the
metallic collar which holds the water pump. Remove the pump and with a pliers or wrench turn the central
clutch in order to rotate the pump and release it. Assemble as
before and check the normal running.
Pump jamming causes the burning of the fuse located in the
fuse-holder B4. To replace it, unplug the machine, remove the
front panel and replace the 5 A - 5x20 mm for 60 Hz motor.
– Should the water pressure need adjustment, turn the screw R about
1 turn: turning it clockwise the water pressure will be increased
and anticlockwise it will be decreased.
UNPLUG THE MACHINE FOR ITS PERIODIC CLEANING AND USE A
VACUUM CLEANER OR DRY CLOTH: DO NOT USE COMPRESSED AIR,
WATER OR LIQUID CLEANSING AGENTS.
ATTENTION
THE ELECTRONIC CASTING MACHINE MOD. MODULAR 4 MUST BE
EXCLUSIVELY USED WITH ORIGINAL ASEG GALLONI CRUCIBLES
OTHERWISE THE OPERATION OF THE MACHINE WILL BE JEOPARDIZED
AND WARRANTY FAILS.
ATTENTION
PICTURE 9
R
MODULAR 6

20
NORMAL OUTFIT
CODE DESCRIPTION QUANTITY
A032.014 5x20 - 200 mA fuse for operational board nr 1
A032.025 5x20 - 2A fuse for operational board nr 1
A032.039 5x20 - 5 A glass fuses for cooling water pump motor 60 Hz nr 1
A054.006 Eyebolt holes stopper nr 4
A100.001 Ceramic container for small flasks nr 1
A100.059 Crucible with internal graphite liner and cover nr 1
A100.425 Ceramic crucible nr 1
A100.481 Silicon nitride ceramic crucible nr 1
A120.05 7x15 4ma screw nr 2
A100.121 Eyebolt to be gripped when moving the machine nr 4
A120.73 4x6 4ma cross screw nr 2
P00138 Flask and crucibles tongs nr 1
P04002 Steel rod to collect the metal on the crucible bottom nr 1
Bottle of 2 litres capacity to check water outlet nr 1
MODULAR 6
Table of contents
Popular Laboratory Equipment manuals by other brands
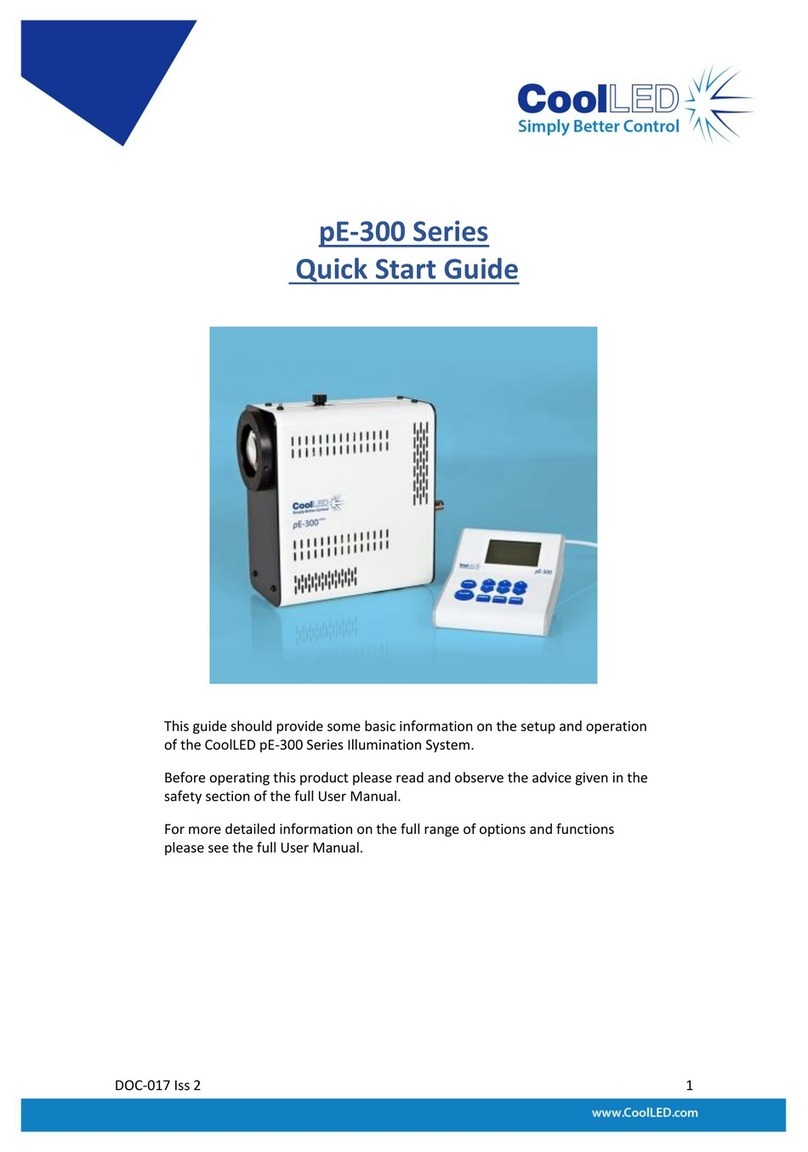
CoolLED
CoolLED pE-300 Series quick start guide
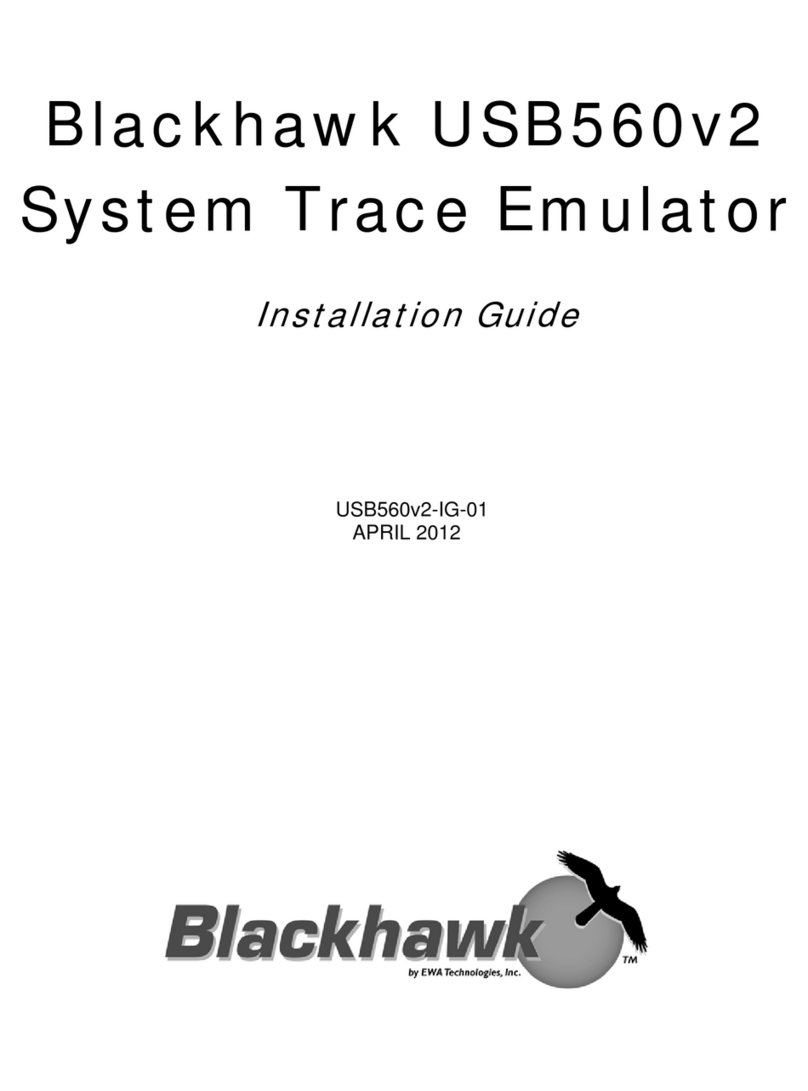
BlackHawk Labs
BlackHawk Labs USB560v2 installation guide
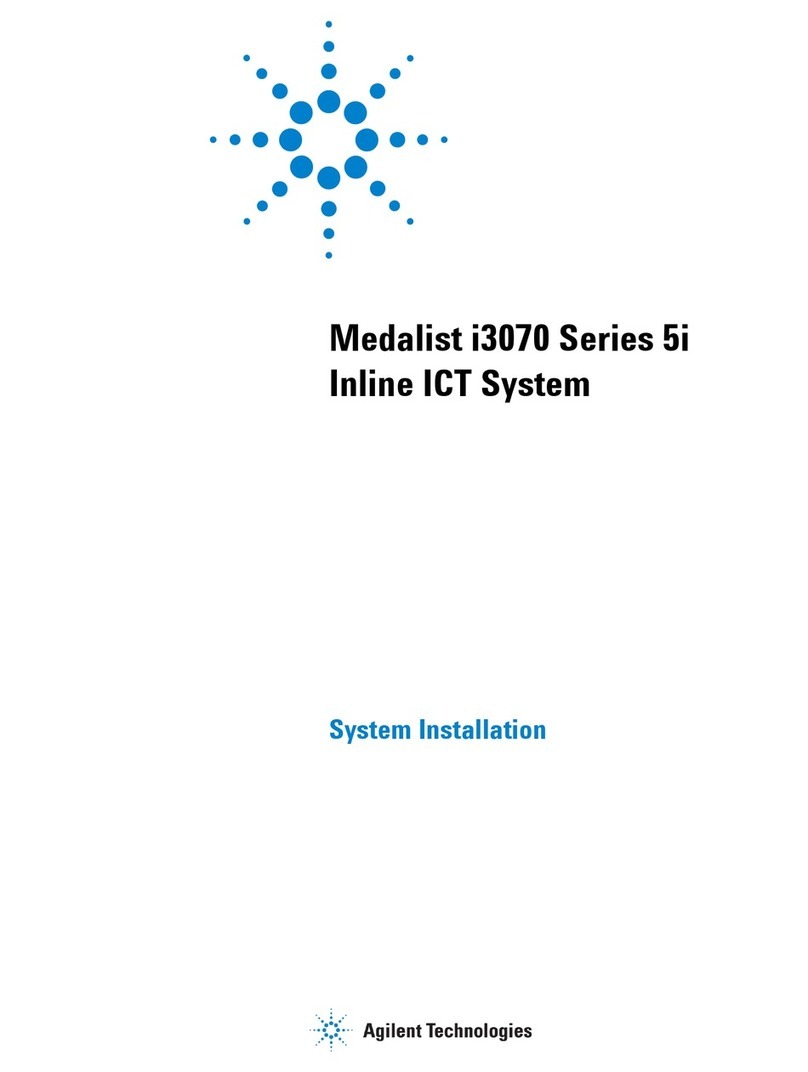
Agilent Technologies
Agilent Technologies Medalist i3070 Series System installation

Affymetrix
Affymetrix GeneChip Fluidics Station 450 user guide
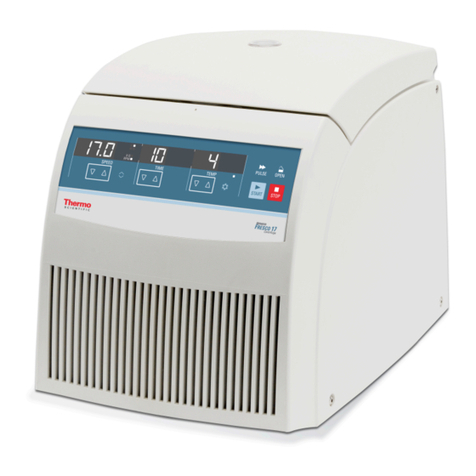
Thermo Scientific
Thermo Scientific Heraeus Fresco 21 Instructions for use
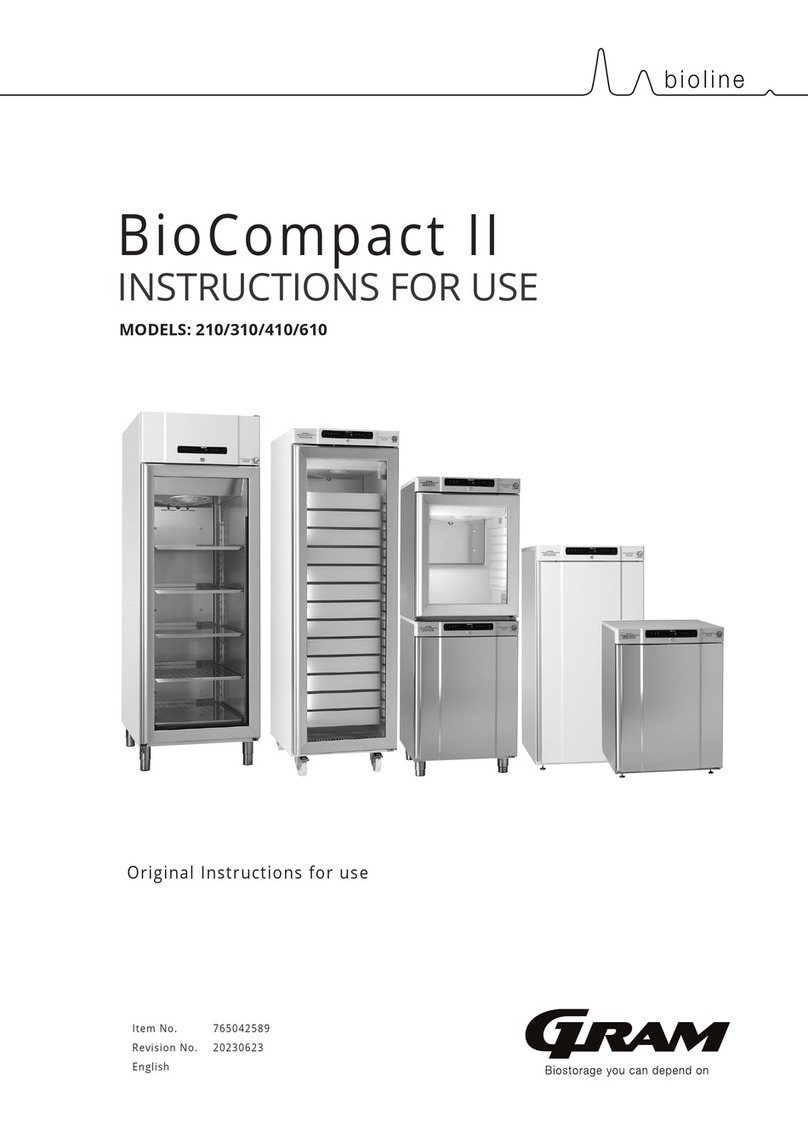
Gram
Gram bioline BioCompact II 210 Instructions for use