ASEPCO PN05 Installation guide

Weirless Radial diaphragm™ tank-bottom (90 degree)
valve
Installation, operating, and maintenance manual
m-radialdiaphragmvalve-en-02 1
Contents
1 Declaration of conformity 3
2 Safety notes 4
3 Overview 7
3.1 Valve description 7
4 When you unpack your valve 8
4.1 Unpacking your valve assembly 8
4.2 Packaging disposal 8
4.3 Inspection 8
4.4 Components supplied 8
4.5 Storage 8
5 Start-up check list 9
6 Diaphragm selection 10
7 Installation 11
7.1 Install the valve body 11
7.2 Install and remove diaphragm - manual actuator 11
7.3 Install and remove diaphragm - pneumatic actuator 15
8 Actuators — AJSand AKSseries 19
8.1 Maintaining a manual actuator 19
8.2 Maintaining a pneumatic actuator 23
9 Cleaning and sterilisation 33
10 Specifications 34
11 Troubleshooting 35
11.1 Technical support 36
12 Parts list 37
12.1 Replacement diaphragms 37
12.2 Actuator maintenance kits 37
13 Welding guidelines 39
13.1 Welding check list 39
13.2 Positioning of the tank valve 40
13.3 Location of tank valve 40
13.4 Making the hole for the tank valve 40

2 m-radialdiaphragmvalve-en-02
13.5 Insertion depth of tank valve 40
13.6 Welding instructions 40
13.7 External tack welding of the tank valve: 41
13.8 Final external welding of the tank valve 42
13.9 Final internal welding of the tank valve 43
13.10 Grinding / polishing 43
13.11 Final control (optional) 43
14 Warranty 45
15 Information for returning products 46
16 Name and address of manufacturer 47
17 Trademarks 47
18 Publication history 47
19 Disclaimers 47
20 Appendix A 48

1 Declaration of conformity
MANUFACTURER: ASEPCO,
1161 Cadillac Ct
Milpitas CA 95035
PRODUCT DESCRIPTION:
Pneumatic actuators are machined from 304 Stainless Steel and are designed to withstand
some dings and drops. All actuators have a position indicating shaft that extends when the
valve is open (for visual confirmation of valve position) and contain as few o-rings and
seals as possible which require very simple maintenance on an annual basis. Additionally,
to prevent any galling, we machine all our actuator bodies out of 304 Stainless Steel, our
diaphragm shafts out of 316 Stainless Steel and our actuator shafts out of Galltough or
304. All ASEPCO actuators can withstand operating temperature of 135° C (or 275° F).
PART NUMBERS: PN05, PN10, PN20, PN30, PN40
APPLICABLE EUROPEAN DIRECTIVES:
ATEX: 2014/34/EC
APPLICABLE INTERNATIONAL STANDARDS:
ATEX: EN ISO 80079-36:2016, EN ISO 80079-37:2016
ISO 9001:2015 Quality Management System
NOTIFIED BODY
DNV Nemko Presafe AS, ATEX NB 2460 retains a copy of the Technical File
ATEX product marking: 2460 II2G Exc IIA T4
The product described in this Declaration of Conformity complies with the Applicable European
Directives and relevant sections of the Applicable International Standards. The signature on this
document authorizes the distinctive European mark to be applied to the equipment described. A
Technical Construction File is available for inspection by designated bodies.
Authorized Signature: Date: 11 May 2016
Important safety information is contained in the installation manual; read and
understand this information prior to installing or using this equipment.
This Document applies only to the equipment described above and is invalid if not reproduced in its entirety.
EC Declaration of Conformity
m-radialdiaphragmvalve-en-02 3

4 m-radialdiaphragmvalve-en-02
2 Safety notes
This safety information should be used in conjunction with the rest of this operating
manual.
In the interests of safety, this valve and actuator should only be used by competent,
suitably trained personnel after they have read and understood the manual and considered
any hazard involved. If the valve is used in a manner not specified by ASEPCO, the
protection provided by the valve and actuator may be impaired. Any person who is
involved in the installation or maintenance of this equipment should be fully competent to
carry out the work. In the UK this person should also be familiar with the Health and Safety
at Work Act 1974 or its equivalent in other regions.
This symbol, used on the product and in the manual, means:
Possibility of severe personal injury, loss of life, or equipment damage
in indicated situation. Ensure all instructions are followed.
This symbol, used on the product and/or in the manual, means:
Caution, high pressure air and/or high process pressure hazard.
This symbol, used on the product and in the manual, means: Caution,
hot surface.
This symbol, used on the product and in the manual, means: Caution,
risk of electric shock.
This symbol, used on the product and in the manual, means: Personal
Protective Equipment (PPE) must be worn at all times.
Do not use ASEPCO products outside of their specified operating
range.
If valve is installed in a line carrying hazardous fluids then safety
procedures specific to the particular fluid and application must be put
in place to protect against injury to persons.
To avoid moisture build up and increased actuator wear, use only clean
dry air to operate pneumatic actuators.

Avoid personal injury and property damage from any sudden release
of process pressure. Before performing any maintenance operations:
lDisconnect any operating lines providing air pressure, electric
power, or a control signal to the actuator. Be sure the actuator
cannot suddenly open or close the valve.
lDo not remove the actuator from the valve while the valve is still
pressurised.
lUse bypass valves or completely shut off the process to isolate the
valve from process pressure. Relieve process pressure on both
sides of the valve. Drain the process media from both sides of the
valve.
lCheck with your process safety engineer for any additional
measures that must be taken to protect against process media.
Ensure that chemicals that come in direct contact with valve assembly
and its components are compatible with the valve body, actuator,
diaphragm, to be used in the fluid path. If you need assistance please
contact your local sales office.
Exterior surfaces of the valve may become hot during operation. The
unit should be allowed to cool prior to conducting any repositioning or
maintenance operations.
Do not open the valve clamp during steaming or while the valve is
under pressure.
Important: Pneumatic actuators should have their seals replaced every
3 years for standard actuators and every year for ATEX actuators.
Manual actuators should have their seals replaced every 10 years. See
"Parts list" on page37, for replacement kit part numbers.
The valve and actuator surfaces will be hot following sterilisation in an
autoclave and may cause injury when handled. Suitable personal
protective equipment must be worn and care must be taken when
handling the valve and actuator.
m-radialdiaphragmvalve-en-02 5

6 m-radialdiaphragmvalve-en-02
ASEPCO products should be used only in services and within pressure
and temperature ranges designated in its product information or
specifications or as specifically approved by ASEPCO in writing.
Misuse of ASEPCO products may result in personal injury or property
damage. If any ASEPCO valve shows signs of leakage, do not operate—
remove it from the line, and repair or replace it.

3 Overview
This manual is the primary information source for the installation, operation and
maintenance of ASEPCO Weirless Radial diaphragm tank-bottom (90 degree) valves. The
manual also covers the use of manual and pneumatic actuators. A separate manual is
available for our 180 degree flow path Weirless Radial diaphragm in-line valve range.
3.1 Valve description
All valves assemble using a hygienic clamp to form a seal, surpassing anything available
from weir-style valves. No tools are needed for maintenance.
There are three components to all the valves:
•Valve body: Our valve bodies are a single piece machined out of stainless steel bar
stock with fittings welded on per customer requirements
•Actuator: Manual and pneumatic actuators are available in plastic or stainless steel.
A number of options are available for the actuators, but for any particular valve the
options available depend on the type and size of the valve. See "Specifications" on
page34.
•Diaphragm: Our radial diaphragms have two primary sealing surfaces: a shutoff seal
at the inlet (seat) and a seal at the shoulder between the inside and outside of the
valve. For most valves, a number of different diaphragm materials are available. See
"Parts list" on page37 for a list of available diaphragm materials.
m-radialdiaphragmvalve-en-02 7

8 m-radialdiaphragmvalve-en-02
4 When you unpack your valve
4.1 Unpacking your valve assembly
Unpack all parts carefully, retaining the packaging until you are sure all components are
present and in good order. Check against the components supplied list below.
4.2 Packaging disposal
Dispose of packaging materials safely and in accordance with regulations in your area. The
outer carton is made of cardboard and can be recycled.
4.3 Inspection
Check that all components are present. Inspect components for damage in transit. If
anything is missing or damaged, contact your local sales office immediately.
4.4 Components supplied
lValve
lActuator
lDiaphragm
lClamp
lUser Manual
4.5 Storage
This product has an extended shelf life. However, care should be taken after storage to
ensure that all parts function correctly.
Diaphragm shelf life
Shelf life for diaphragms is 5 years.
Please observe the storage recommendations and use-by dates which apply to diaphragms
that you may wish to bring into service after storage when used with this product.

5 Start-up check list
lEnsure that a suitable diaphragm for your process has been installed into the valve
assembly, please refer to the advice in "Diaphragm selection" on the next page for
additional information.
lEnsure that all pipes, valves and other equipment in your fluid path are properly
supported and secured.
lEnsure that secure connections are achieved between the valve and any piping.
lManual actuators - Ensure that easy and safe access is provided to the actuator handle,
to enable rapid shut off in case of emergency.
lPneumatic actuators - Ensure proper and safe connection has been made to a suitable
air supply.
m-radialdiaphragmvalve-en-02 9

10 m-radialdiaphragmvalve-en-02
6 Diaphragm selection
Diaphragm materials must be selected with consideration to heat-resistance, chemical-
resistance, steam-resistance, durability and handling as well as the number, temperature
and duration of CIP/SIP cycles. It is critical that you select the appropriate diaphragm
materials for your process. For material specifications and further information or assistance
with material selection, visit www.wmftg.com or contact your local sales office.
Ensure the chemicals to be used with valve assembly are compatible
with the valve body, actuator, diaphragm, to be used in the fluid path.
If you need assistance please contact your local sales office.
Examine the diaphragm at least once a week for signs of wear. If you have any concerns
with the condition of the diaphragm, contact your local sales office.
Diaphragm replacement
It is best practice to replace a diaphragm:
• At least annually - For fewer than five SIP cycles a week that are less than two hours
each at less than 135C
• At least every six months - For five or more SIP cycles a week that are less than
two hours each at less than 135C.
The following table summarises the availability of each diaphragm material for the
different valve sizes.
Material
Valve Size Availability
0.5" 1" 1.5" 2" 3" 4"
Silicone u u u u u u
Silicone Plus uuuuun/a
EPDM u u u u u u
EPDM Plus uuuuun/a
Viton A u u n/a un/a n/a
Viton A
(steam resistant)
uuuuun/a
Viton GF n/a un/a u u n/a
PTFE n/a u u u u n/a

7 Installation
There are three basic steps to follow to install an ASEPCO valve:
Step 1: Install the valve body.
Step 2: Attach the diaphragm to the actuator assembly
Step 3: Insert the actuator/diaphragm assembly into the valve body and clamp them
together.
Please use the following detailed instructions for each of these steps to ensure proper
functioning of the valve.
7.1 Install the valve body
There are two basic options for installing a valve body, either you can use a hygienic clamp
to clamp it into place, or you can weld it into place.
Clamping the valve body in place
You can use a single-hinge clamp, a double bolt clamp or a double hinge clamp for this
purpose. Ask your engineering team about the most appropriate clamp to use.
ASEPCO valves are compatible with a wide range of clamps from a variety of
manufacturers.
ASEPCO supplies every valve with a clamp to assemble the actuator/diaphragm assembly
to the valve body.
Welding the valve body in place
If you are welding the valve into place, please refer to "Welding guidelines" on page39.
7.2 Install and remove diaphragm - manual actuator
Install an elastomer diaphragm
1. Close the valve until the position indicator is flush with the handle or the threaded
shaft is fully extended. Place the actuator handle down on a flat surface to ensure
that the position indicator is flush with the handle.
m-radialdiaphragmvalve-en-02 11

12 m-radialdiaphragmvalve-en-02
2. Turn the diaphragm clockwise onto the diaphragm/actuator assembly shaft until it is
finger-tight.
3. Rotate the handle counter-clockwise two turns.
4. Insert the diaphragm/actuator assembly into the valve body.
Position indicator
slightly extended
Valve
body
5. Fasten the clamp and finger-tighten.
Install a PTFE diaphragm
1. Verify that the O-ring is installed on the diaphragm shoulder seal.
O-ring
NOTE! Only install the components provided, do not install any additional gaskets.

2. Verify that the diaphragm insert is screwed into the diaphragm, just finger-tight.
3. Mount the diaphragm on the actuator shaft and turn clockwise until it is fully seated.
DO NOT FORCE! Finger-tight is sufficient.
Actuator
Shaft end
Diaphragm
Valve
NOTE! Do not install gaskets between the valve body and the actuator.
4. Insert the actuator and diaphragm assembly into the valve body.
5. While keeping pressure against the valve body, rotate the handle counter-clockwise
until the O-ring contacts the actuator flat surface. The position indicator should be
protruding from the bottom of the actuator. For smaller diaphragm sizes, the side
travel marks should be showing. While the diaphragm will be slightly retracted, the
shoulder seals will remain in the same position.
Indicator ush -
Closed Position
Indicator out -
Open Position
6. Make sure that the actuator flange and the valve flange are close enough to easily
reinstall the clamp.
7. Reinstall the clamp on the actuator/valve assembly by hand. A double-bolt, high-
pressure clamp is can be used, alternating between the two bolts to ensure even
tightening.
8. Using a torque-controlled socket wrench set to 2.26Nm (50in-lbs), tighten the clamp.
If using a double-bolt clamp, tighten the clamp by alternating between the two bolts
until the bolts are fully torqued.
NOTE! Unlike elastomer diaphragm materials, the following steps are necessary to finish
preparing a new PTFE diaphragm for optimum performance:
9. Open the valve and steam the valve for 15 minutes.
10. Close the valve and steam again for 30 minutes.
11. Check the valve seat for integrity. There should be no loss of pressure.
m-radialdiaphragmvalve-en-02 13

14 m-radialdiaphragmvalve-en-02
NOTE! Alternatively, if steam is not available in your process system, please refer to
technical bulletin 19-1000 (Appendix A).
Remove the diaphragm
1. Open the valve.
2. Remove the clamp.
Valve
body
Actuator
Handle
3. Close the valve until the position indicator is flush with the handle or until the travel
marks are covered by the handle. Place the actuator handle down on a flat surface to
ensure that the position indicator is flush with the handle.
Position indicator
(Flat surface)
4. Remove actuator and diaphragm assembly from the valve body by grasping the
diaphragm edge and pulling downward from the valve body.
5. Turn the diaphragm counter-clockwise to unscrew and remove from the actuator.
Diaphragm

7.3 Install and remove diaphragm - pneumatic actuator
Install an elastomer diaphragm
1. Shut off the air so the actuator is fully closed.
2. Thread the diaphragm clockwise onto the actuator until it is finger-tight.
3. Insert the actuator/diaphragm assembly into the valve body.
4. Attach and turn on the air source to compress the diaphragm.
5. Install and tighten the clamp while the diaphragm is retracted.
6. Shut off the air source to fully close the valve.
m-radialdiaphragmvalve-en-02 15

16 m-radialdiaphragmvalve-en-02
Install a PTFE diaphragm
1. Verify that the O-ring is installed on the diaphragm shoulder seal.
2. With the air source off or disconnected, thread the diaphragm onto the actuator shaft
and turn it clockwise until it stops. This ensures that the diaphragm is fully threaded
onto the actuator.
DO NOT FORCE! Finger-tight is sufficient.
3. Insert the actuator and diaphragm assembly into the valve body.
Diaphragm
NOTE! Do not install gaskets between the valve body and the actuator.
Verify that the actuator is in the closed position (the indicator at the top of the
actuator is flush with the actuator).
Indicator ush = Closed position Indicator out = Open position

4. Turn the air source on and fully open the actuator; so that the diaphragm is retracted
from the valve seat. The position indicator should be protruding from the top of the
actuator. This pulls the diaphragm back to allow firm compression of the shoulder
seal.
5. Make sure that the actuator flange and the valve flange are close enough to easily
reinstall the clamp.
6. Reinstall the clamp on the actuator/valve assembly by hand. A double-bolt, high-
pressure clamp can be used, alternating between the two bolts to ensure even
tightening.
It might be necessary to push down on the actuator assembly while assembling the
clamp.
7. Using a torque-controlled socket wrench set to 2.26Nm (50in-lbs), tighten the clamp.
If using a double-bolt clamp, tighten the clamp by alternating between the two bolts
until the bolts are fully torqued.
Unlike elastomer diaphragm materials, the following steps are necessary to finish
preparing a new PTFE diaphragm:
8. Open the valve and steam the valve for 15 minutes.
9. Close the valve and steam again for 30 minutes.
10. Check the valve seat for integrity. There should be no loss of pressure.
Remove the diaphragm
Do not open the valve clamp during steaming or while the valve is
under pressure.
1. De-pressurise the system.
2. Open the valve (by turning the air on).
3. Remove the clamp.
4. Close the valve (by turning the air off).
m-radialdiaphragmvalve-en-02 17

18 m-radialdiaphragmvalve-en-02
5. Remove the actuator and diaphragm assembly by grasping the diaphragm edge and
pulling it away from the valve body.
6. Disconnect the actuator from the air source.
7. Turn the diaphragm counter-clockwise to unscrew it and remove it from actuator.

8 Actuators — AJSand AKSseries
8.1 Maintaining a manual actuator
(a) MNXX AJS series
Step 1: Remove the actuator and diaphragm assembly from the valve
Step 2: Remove the diaphragm
Follow the instructions for "Remove the diaphragm" on page14.
Step 3: Disassemble the actuator and replace O-rings and washers
Sleeve
Guide bushing
Key sleeve
Bearing race set
Shaft
Key
Set screw
Manual nut
Bearing race set
Snap ring
Manual knob
O-ring
1. Using a 1/8" hex key, remove the set screw on the handle.
2. Pull the knob off the sleeve.
3. Using an O-ring tool, take out the O-ring from the centre of the knob.
4. Replace the old O-ring with a new O-ring from the kit.
5. Put some of the lubricant (provided in the kit) on the O-ring.
6. Using a pair of pliers, pull the JM wiper out of the knob.
7. Replace with the new JM wiper.
JM wiper
8. Remove the snap ring from the top of the sleeve.
9. Grab the shaft and nut and pull them out of the sleeve. (One bearing race will come
out with these parts.)
10. Using an O-ring tool or a pick, remove the bearing left in the sleeve.
m-radialdiaphragmvalve-en-02 19

20 m-radialdiaphragmvalve-en-02
11. Turn the sleeve over and let the key sleeve drop out.
12. Using a small rod or similar object (your hex key or the back of a ballpoint pen
should be sufficient), push the guide bushing assembly out of the sleeve.
Step 4: Reassemble the actuator
1. Lubricate the O-ring for the guide bushing assembly and press the guide bushing
assembly into the sleeve.
2. Drop the key sleeve back into the sleeve.
3. Using the shaft, turn the key sleeve around until it drops completely into place.
4. Place one of the bearing and race sets on top of the key sleeve (in the order of race-
bearing-race). Press firmly into place.
5. Put the remaining lubricant provided on the threads of the shaft.
6. Insert the shaft into the key sleeve.
7. Screw the nut down over the shaft.
8. Place the second bearing and race set over the nut. Press it into place.
9. Re-insert the snap ring.
10. Before replacing the knob onto the sleeve, stretch the JM wiper by pulling the edges
outward. This helps slip the knob over the sleeve.
11. Rotate the nut counter-clockwise until the shaft is fully extended. Slip the knob onto
the shaft and sleeve.
12. Hold the entire assembly so that the set-screw hole in the knob is facing you. Rotate
the actuator counter-clockwise until the hole in the knob lines up with the hole in the
nut.
13. Insert the set screw and tighten with an hex key. Do not let the assembly shift while
you are doing this or you will lose your alignment.
Step 5: Replace the diaphragm
Follow the instructions for "Install an elastomer diaphragm" on page11 or "Install a PTFE
diaphragm" on page12.
(b) MNXX-01 AKS Series
Step 1: Remove the actuator and diaphragm assembly from the valve
Step 2: Remove the diaphragm
Follow the instructions for "Remove the diaphragm" on page14.
This manual suits for next models
4
Table of contents
Popular Control Unit manuals by other brands

East Coast Datacom
East Coast Datacom DMM-4DC Operation manual
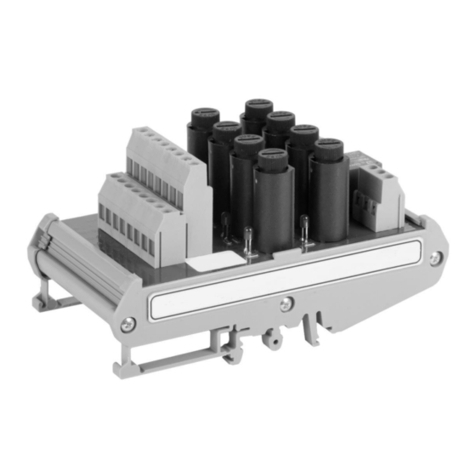
ARMTEL
ARMTEL ARMT.665200.104UM user manual
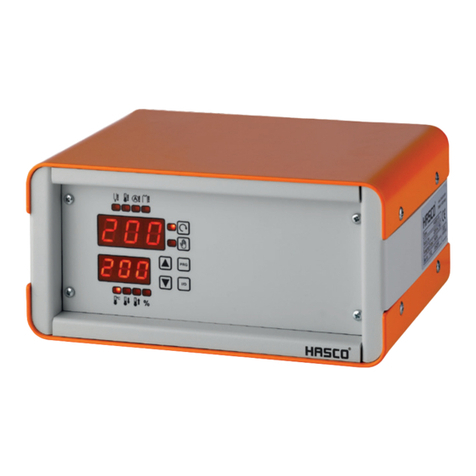
Hasco
Hasco H1250 Series operating instructions
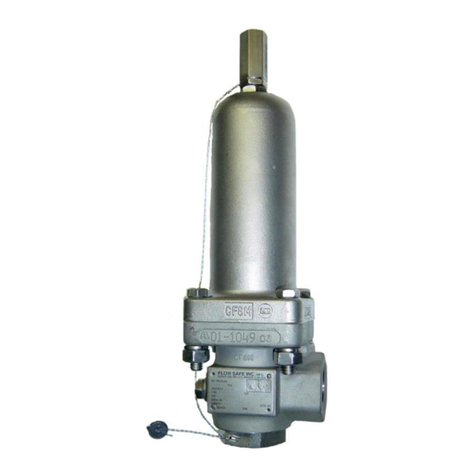
Flow Safe
Flow Safe F88 Series Installation, operation & maintenance manual
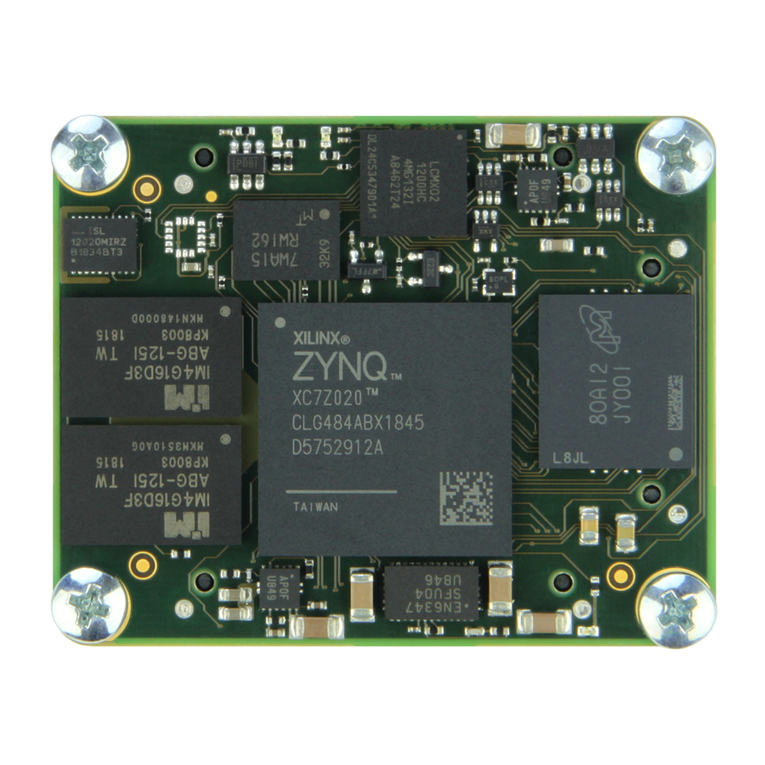
Trenz Electronic
Trenz Electronic TE0720 Schematics

Sel
Sel SEL-2600 instruction manual