ATI Technologies DKG-M User manual

Quick-Change Installation and Operation Manual
Document #9620-20-c-dkgm dkft-03
Pinnacle Park
•
1031 Goodworth Drive
•
Apex, NC 27539
•
Tel: 919.772.0115
•
Fax: 919.772.8259
•
www.ati-ia.com
•
Email: info@ati-
ia.com
C - 1
Table of Contents
C. Control and Signal Modules..................................................................................................3
DKG-M and DKF-T—EtherNet/IP Control & Quick Connect Pass-through Modules.............. 3
1. Product Overview..............................................................................................................3
1.1 Master Module ......................................................................................................................... 3
1.2 Tool Module ............................................................................................................................. 3
2. Installation .........................................................................................................................5
2.1 Installing................................................................................................................................... 5
2.2 Removal................................................................................................................................... 5
2.3 EtherNet/IP Configuration........................................................................................................ 6
2.4 Utility Schematic....................................................................................................................... 6
3. Product Information..........................................................................................................7
3.1 Master Module ......................................................................................................................... 7
3.1.1 Class 1 Connection Information .............................................................................. 7
3.1.2 Integrated Web Server............................................................................................. 7
3.1.3 IP Address Configuration......................................................................................... 7
3.1.4 Ethernet Switch Settings.......................................................................................... 9
3.1.5 Ethernet Switch Diagnostics.................................................................................. 10
3.1.6 DIP Switches on the Master Module ..................................................................... 11
3.1.7 Module and Network Status LED .......................................................................... 12
3.1.8 Using Ethernet Quick-Connect.............................................................................. 13
3.2 Arc Prevention Circuit ............................................................................................................ 14
3.2.1 Arc Prevention Circuit Behavior during Coupling .................................................. 14
3.2.2 Arc Prevention Circuit Behavior during Uncoupling .............................................. 14
3.3 Tool Module ........................................................................................................................... 15
3.3.1 Tool-ID Switches.................................................................................................... 15
3.4 Tool-Side TSI ......................................................................................................................... 16
3.4.1 TSI Behavior for Module with Firmware Version 2.52 or Later.............................. 16
3.4.2 TSI Behavior for Module with Prior to Firmware Version 2.52 .............................. 17
3.5 Software................................................................................................................................. 18
4. Operation .........................................................................................................................20
4.1 Recommended Sequence of Operation ................................................................................ 20
5. Diagnostic Functions and Error Handling.....................................................................22
5.1 Power Status.......................................................................................................................... 22
5.2 Valve Power Status................................................................................................................ 22
5.3 Error on Latch or Unlatch Output........................................................................................... 22
5.4 “COMM OK” bit ...................................................................................................................... 22
5.5 “Tool Power is On” bit ............................................................................................................ 22
5.6 “Unlatch Enabled” bit.............................................................................................................. 22
6. Maintenance.....................................................................................................................23
6.1 Pin Block Inspection and cleaning......................................................................................... 23
6.2 Seal Replacement.................................................................................................................. 24
7. Troubleshooting..............................................................................................................25
8. Recommended Spare Parts and Accessories............................................................... 26
9. Specifications..................................................................................................................26
10. Drawings..........................................................................................................................27

Quick-Change Installation and Operation Manual
Document #9620-20-c-dkgm dkft-03
Pinnacle Park
•
1031 Goodworth Drive
•
Apex, NC 27539
•
Tel: 919.772.0115
•
Fax: 919.772.8259
•
www.ati-ia.com
•
Email: info@ati-
ia.com
C - 2
Glossary of Terms
TERM DEFINITION
Auxiliary Power 24VDC Power Supply interface provided that supports Switched and Unswitched circuits.
Clear Errors An output supplied to the ATI Master EtherNet/IP node to clear all error conditions.
Comm. Error An input indicating the status of the Tool-ID communication between Master and Tool
modules.
EOAT End-Of-Arm-Tool (end effector).
Error on Latch
Output An input indicating a short circuit overload condition exists with the Latch output.
Error on Unlatch
Output An input indicating a short circuit overload condition exists with the Unlatch output.
Latch The output supplied to the ATI Master EtherNet/IP node to couple the Tool Changer.
Locked A proximity sensor input indicating that the coupling mechanism is in the Locked position.
MDI and MDI-X
MDI stands for Media Dependant Interface. The X refers to the fact that transmit wires on an
MDI Ethernet device must be connected to receive wires on an MDIX Ethernet device.
Straight through cables connect pins 1 and 3 (transmit) on an MDI device to pins 1 and 3
(receive) on an MDIX device. Similarly pins 2 and 4 are receive on an MDI device and
transmit on an MDIX device
Input and Logic
Power Good An input indicating the presence of Input Power (sourced from the Un-switched Power
Supply) at the ATI Master.
RTL A proximity sensor input that senses when the ATI Tool is in close proximity. RTL stands for
Ready To Lock.
RTLV An input provided for health status monitoring of the RTL Relay.
Switched
Auxiliary Power One circuit of the Auxiliary Power Supply that is tied into the E-stop circuit and will be
switched off when the circuit is broken.
Tool-ID An input from the Master node reporting the values from the Tool-ID switches on the Tool
module.
Tool Present A hard-wired input (sourced from the Tool) indicating that the Master and Tool modules are
electrically connected to each other.
TSI The Tool Stand Interlock feature is a custom ATI safety solution and circuit designed to only
allow Tool Changer release while in the stand or storage location.
TSIV An input supported for monitoring of a Tool Stand limit switch used with the TSI circuit.
TSRV An input provided for health status monitoring of the TSI Relay.
Unlatch The output supplied to the ATI Master EtherNet/IP node to uncouple the Tool Changer.
Unlocked A proximity sensor input indicating that the coupling mechanism is in the Unlocked position.
Valve Power
Available An input indicating the presence of Valve Power (= Switched Auxiliary Power) at the ATI
Master.

Quick-Change Installation and Operation Manual
Document #9620-20-c-dkgm dkft-03
Pinnacle Park
•
1031 Goodworth Drive
•
Apex, NC 27539
•
Tel: 919.772.0115
•
Fax: 919.772.8259
•
www.ati-ia.com
•
Email: info@ati-
ia.com
C - 3
C. Control and Signal Modules
DKG-M and DKF-T—EtherNet/IP Control &
Quick Connect Pass-through Modules
1. Product Overview
The EtherNet/IP modules enable the user to control and communicate with ATI's Heavy Automation Robotic
Tool Changers using EtherNet/IP. It also passes the EtherNet/IP network through a managed switch to the
tool side. With the default switch settings it supports EtherNet/IP Quick Connect. This allows utilizing
EtherNet/IP on the Robot- and on the Tool-side with short connection times.
Control of the Tool Changer is realized through the Master Node along with the reporting of Tool Changer
I/O, such as Lock, Unlock, and Ready-to-Lock signals. The Tool-side module supports Tool-ID reported
through the Master-side and functions as a pass-through for the EtherNet/IP network and power to
downstream equipment.
When the Tool Changer is coupled, the Master and Tool modules pass signals using a spring-loaded pin
block. A flexible boot surrounds the pin block to seal the connection from moisture and liquid while coupled
(see Figure 1.1 and for more information refer to Section 10—Drawings).
General fault reporting is supported for the presence of power for Logic/Inputs and the Tool Changer valve.
Advanced diagnostic and fault reporting is supported for output short circuit and overload conditions as well
as for the presence of Tool-ID. Refer to Sections 3—Product Information and Section 4—Operation for more
information on these attributes.
The DKG Module incorporates ATI’s exclusive Arc Prevention Circuit which extends the life of all electrical
power contacts on the pin block. Refer to Section 3.2—Arc Prevention Circuit for more information about
this feature.
A single or double solenoid valve is provided with the Master valve adapter for Lock/Unlock control of the
Tool Changer. The user is required to provide a pneumatic supply source to the Tool Changer.
The Unlock signal to the solenoid valve is routed through a “Tool Stand Interlock” (TSI) safety circuit that
prevents the robot from unlocking the Tool from the Master when the mated assembly is not in a Tool Stand.
1.1 Master Module
One standard 4-Pin Mini connector is provided on the Master for the power supply of the DKG’s
EtherNet/IP interface and sensor inputs. The same 4-Pin connector also supplies the output power to the
Tool module. One 4-Pin M12 D-Coded connector is provided on the Master module for EtherNet/IP
communications interface with the Master and downstream tooling.
1.2 Tool Module
The DKF Tool module employs a thumbwheel switch for setting the Tool-ID input. This allows the user
to distinguish between the different Tools that are being used in a robotic cell or on a production line.
The Tool-ID is reported through the Master module bitmap. See Section 3—Product Information for
EtherNet/IP bitmap and detailed I/O information.
One 4-Pin M12 D-Coded connector is provided on the Tool module for EtherNet/IP communications
interface with the downstream tooling.

Quick-Change Installation and Operation Manual
Document #9620-20-c-dkgm dkft-03
Pinnacle Park
•
1031 Goodworth Drive
•
Apex, NC 27539
•
Tel: 919.772.0115
•
Fax: 919.772.8259
•
www.ati-ia.com
•
Email: info@ati-
ia.com
C - 4
Figure 1.1—DKG-M DKF-T EtherNet/IP Modules

Quick-Change Installation and Operation Manual
Document #9620-20-c-dkgm dkft-03
Pinnacle Park
•
1031 Goodworth Drive
•
Apex, NC 27539
•
Tel: 919.772.0115
•
Fax: 919.772.8259
•
www.ati-ia.com
•
Email: info@ati-
ia.com
C - 5
2. Installation
The control/signal modules are typically installed by ATI prior to shipment. The steps below outline the field
installation or removal as required.
2.1 Installing
1. It may be necessary to clean the mounting surface on the Valve Adapter prior to installing the
module in order to remove any debris that may be present.
2. Using the ledge feature as a guide place the module into the appropriate location on the Valve
Adapter. Align the module with the Valve Adapter using the dowels in the bottom of the ledge
feature. Refer to Figure 2.1.
3. If fasteners do not have pre-applied adhesive, apply Loctite 242®to the supplied M6 SHCS
fasteners. Install the (2) M6 socket head screws securing the module to the Valve Adapter and
tighten to 70 in-lbs.
4. Power, signal, auxiliary, sensor, and valve cables can be connected to the module after attaching
the module to the Tool Changer body. Ensure that the connectors are cleaned prior to being
secured as appropriate.
Figure 2.1—Module Installation
2.2 Removal
1. Prior to removing the module use a marker pen to scribe a line or indication between the Tool
Changer and module body as a reminder where the module is to be re-installed.
2. Depending upon the service or repair being done, customer connections up to the module may or
may not need to be disconnected. Also, proximity sensor and valve cables may or may not need to
be disconnected.
3. Remove the socket head cap screws and lift the module from the Tool Changer. Refer to
Figure 2.1.
WARNING: Do not perform maintenance or repair on Tool Changer or modules unless
the tool is safely supported or docked in the tool stand and all energized circuits (e.g.
electrical, air, water, etc.) have been turned off. Injury or equipment damage can occur
with tool not docked and energized circuits on. Dock the tool safely in the tool stand and
turn off all energized circuits before performing maintenance or repair on Tool Changer or
modules.

Quick-Change Installation and Operation Manual
Document #9620-20-c-dkgm dkft-03
Pinnacle Park
•
1031 Goodworth Drive
•
Apex, NC 27539
•
Tel: 919.772.0115
•
Fax: 919.772.8259
•
www.ati-ia.com
•
Email: info@ati-
ia.com
C - 6
2.3 EtherNet/IP Configuration
Various parameters for the EtherNet/IP modules need to be configured prior to operating the Tool
Changer. Please refer to Section 3—Product Information of this manual for detailed information on
installation and operation of the EtherNet/IP modules.
2.4 Utility Schematic
Refer Section 10—Drawings of this manual for customer interface and wiring details for the DKG-
M/DKF-T modules.
WARNING: All pneumatic fittings and tubing must be capable of withstanding the
repetitive motions of the application without failing. The routing of electrical and
pneumatic lines must minimize the possibility of over stressing, pullout, or kinking
the lines. Failure to do so can cause some critical electrical and/or pneumatic lines
not to function properly and may result in injury to personnel or damage to
equipment. Follow the robot manufacturer’s guidelines and carefully route hoses
and cables to avoid damage.
CAUTION: Ethernet cabling layout is critical to the overall performance of the
system. Interface connections from the controller up the robot arm to the ATI
Master should be minimized (less than 3 connections, e.g.). Use of hi-flex, robot
rated cable is essential for long term performance.
CAUTION: It is recommended, not to use fasteners with pre-applied adhesive
more than three times. Fasteners used more than three times may come loose
and cause equipment damage. Discard fasteners used more than three times
and install new fasteners with pre-applied adhesive.

Quick-Change Installation and Operation Manual
Document #9620-20-c-dkgm dkft-03
Pinnacle Park
•
1031 Goodworth Drive
•
Apex, NC 27539
•
Tel: 919.772.0115
•
Fax: 919.772.8259
•
www.ati-ia.com
•
Email: info@ati-
ia.com
C - 7
3. Product Information
The DKG-M DKF-T modules enable the user to control and communicate with the Tool Changer through a
network using an M12 D-coded 4-Pin EtherNet/IP interface connector. Control of the Tool Changer is
realized through the Master node along with the reporting of various Tool Changer I/O. The Tool module
supports Tool-ID reported through the Master and functions as a pass-through for EtherNet/IP and Auxiliary
Power signals to downstream equipment.
The DKG-M DKF-T modules employ a 4-Pin Mini connector for output supply power and input/logic power,
for the power supply of its EtherNet/IP interface and sensor inputs. Please refer to Section 10—Drawings for
specific module wiring and connector interface information.
Prior to using the Tool Changer and the EtherNet/IP modules, various hardware settings must be configured.
Communicating with the EtherNet/IP Modules requires knowledge of EtherNet/IP standards and operation.
3.1 Master Module
The module operates as a Server on the EtherNet/IP network. It supports Class 3 Connected Explicit
Messaging, UCMM Explicit Messaging, and Class 1 Connected Cyclic I/O Messaging. The Master
Node does not support any Client functionality.
3.1.1 Class 1 Connection Information
Instance
Size in
Bytes
Configuration
128
0
Input
7
8
Output
37
8
3.1.2 Integrated Web Server
The module’s integrated web server hosts several web pages. One of the pages provides
configuration options for communication settings (reference Figure 3.1).
A web browser, such as Internet Explorer or Mozilla Firefox, is required to access the web
server. The module’s web pages use simple HTML and do not require any plug-ins.
To bring up the main page of the web server, type the module’s IP address into the browser’s
address field and then press enter. Click on the “Communications” button on the menu bar to
open the Communication Settings menu. There you can change the module’s IP address, enable
or disable the DHCP option and modify the port settings of the integrated Ethernet switch
3.1.3 IP Address Configuration
The DKG’s IP address settings are only loaded upon power up, consequently the DKG must be
power cycled for new IP address setting changes to be used. There are four ways the DKG’s IP
address can be configured.
The DKG is shipped with
−DHCP disabled
−IP address is set to 136.129.1.1. The subnet mask is 255.255.0.0 and the Gateway is
set to 0.0.0.0.
−The option “Static IP Address Last Octet Set by DIP Switches” is enabled, DIP
switch 1 is set to ON, DIP switch 2-10 are set to OFF.
The plastic window and seal will have to be removed to access the DIP switches, as shown in
the drawings in Section 10.
Note: When replacing the window, ensure that the seal is re-positioned correctly to prevent
fluid ingress.
Method 1:Set IP address to 136.129.1.1 by setting DIP switch 9 to the ON position. If DIP
switch 9 is set to the ON position during power up the IP address will be set to the default
value of 136.129.1.1, regardless of the value of the DHCP, manual IP Address, or DIP Switch

Quick-Change Installation and Operation Manual
Document #9620-20-c-dkgm dkft-03
Pinnacle Park
•
1031 Goodworth Drive
•
Apex, NC 27539
•
Tel: 919.772.0115
•
Fax: 919.772.8259
•
www.ati-ia.com
•
Email: info@ati-
ia.com
C - 8
Octet settings. The gateway will be set to the default value of 0.0.0.0, and the subnet mask to
the default value of 255.255.0.0.
Method 2:Set IP address to a static value stored on the DKG’s Communication Settings web
page (DIP switch 9 must be in the OFF position).
Method 3:Same as method 2, but if the option “Static IP Address Last Octet Set by DIP
Switches” is enabled, the first three octets of the IP address are specified by the value of the
static IP address and the last octet of the IP address is set by the values of DIP switches 1–8
at power up, where DIP switches 1–8 represent bits 0–7 of the octet, in that order. The DIP
switches evaluate to a bit value of 1 when in the ON position, and a bit value of 0 when in the
OFF position.
Note: If the DIP switches evaluate to an octet of 0 (DIP switches 1–8 all off) or 255 (DIP
switches 1–8 all on), the last octet will be set to 1, in order to avoid using an illegal network
address. If the DIP switches evaluate to an octet of 255 (DIP switches 1–8 all on) the switch
settings will also be reset to the default settings described in Section 3.1.4.
Method 4:Let a DHCP server take care of the IP address assignment (DIP switch 9 must be in
the OFF position). If used, this option can be enabled in the DKG’s web pages. To use this
method, a DHCP server must be present in the network. If no DHCP server is responding
within 30 seconds after power-up, the DKG module will use the static IP address that is entered
on the communication page of the web server, without using the value of DIP switches 1–8 for
the last octet.

Quick-Change Installation and Operation Manual
Document #9620-20-c-dkgm dkft-03
Pinnacle Park
•
1031 Goodworth Drive
•
Apex, NC 27539
•
Tel: 919.772.0115
•
Fax: 919.772.8259
•
www.ati-ia.com
•
Email: info@ati-
ia.com
C - 9
Figure 3.1—DKG Integrated Web Server Communication Settings Page
3.1.4 Ethernet Switch Settings
The DKG module has an integrated Ethernet switch where the settings of two ports can be
changed using the web server. The DKG module gets shipped with the following switch
settings:
Robot Side Port:
Auto Negotiation:Enabled
Speed:100MPS
DuplexFull Duplex
Auto-MDIX1:Enabled
MDI Setting:MDI
1Auto-MDIX = Auto Crossover

Quick-Change Installation and Operation Manual
Document #9620-20-c-dkgm dkft-03
Pinnacle Park
•
1031 Goodworth Drive
•
Apex, NC 27539
•
Tel: 919.772.0115
•
Fax: 919.772.8259
•
www.ati-ia.com
•
Email: info@ati-
ia.com
C - 10
Tool Side Port:
Auto Negotiation:Disabled
Speed:100MPS
DuplexFull Duplex
Auto-MDIX:Disabled
MDI Setting:MDI-X2
The default settings support EtherNet/IP Quick Connect.
The Ethernet switch can be reset to these known default settings by setting DIP switch 1
through 8 to the ON position and performing a power cycle.
Important note: In order to support a standard (not Quick Connect) EtherNet/IP application
Auto Negotiation and Auto Crossover must be enabled on the Robot and the Tool Side Port.
Otherwise there can be communication errors.
3.1.5 Ethernet Switch Diagnostics
On the Diagnostics page of the web server (see also Figure 3.2) the DKG-M module displays
the current status of the robot and tool side port settings, as well as their diagnostic counters.
This is the same information that is reported over the Ethernet Link Object 0xF6 in the
EtherNet/IP protocol.
2MDI-X = Crossover

Quick-Change Installation and Operation Manual
Document #9620-20-c-dkgm dkft-03
Pinnacle Park
•
1031 Goodworth Drive
•
Apex, NC 27539
•
Tel: 919.772.0115
•
Fax: 919.772.8259
•
www.ati-ia.com
•
Email: info@ati-
ia.com
C - 11
Figure 3.2—DKG Integrated Web Server Diagnostics Page
3.1.6 DIP Switches on the Master Module
The DKG-M module has 10 DIP switches which have the following functions:
DIP 1 through 8: last octet of the DKGs IP address. See Section 3.1.3 for details
DIP 9: set DKG-M IP address settings to the default values. See
Figure 3.3 for details.
DIP 10: must always be in the OFF position.

Quick-Change Installation and Operation Manual
Document #9620-20-c-dkgm dkft-03
Pinnacle Park
•
1031 Goodworth Drive
•
Apex, NC 27539
•
Tel: 919.772.0115
•
Fax: 919.772.8259
•
www.ati-ia.com
•
Email: info@ati-
ia.com
C - 12
3.1.7 Module and Network Status LED
The module status LED is identified on the module as “MS”. It provides device status for
power and proper operation. Refer to Table 3.1 for an outline of this LED’s operation. The
network status LED is identified on the module as “NS”. It provides network status for power
and communication. Refer to Table 3.2 for an outline of this LED’s operation.
Figure 3.3—EtherNet/IP Master Module LEDs and DIP Switch Settings
SHOWN IN FACTORY DEFAULT SETTING
1
ON
6
23 4 5789
Turn On to
Set IP
Address
To Default
OFF
10
NS
LED
MS
LED
Default Settings
IP Address: 136.129.1.1
Subnet Mask: 255.255.0.0
Gateway: 0.0.0.0
Switch 1 “ON”
Switches 2 – 8
and 10 “Off”
Table 3.1—Module Status LED
Status LED Function Note
No Power Off No power applied. Check voltage is 24 VDC.
Operational Green Normal operation.
Standby Flashing Green No Tool Module attached. Tool-ID in bitmap not available.
Configuration missing, incomplete or incorrect.
Recoverable Fault Flashing Red Recoverable fault.
Unrecoverable Fault Red Unrecoverable fault.
Table 3.2—Network Status LED
Status LED Function Note
No Power/ Off Line/No
IP Address Off
Device not on line. Device may not have an IP address or
may be powered off.
On Line, Not Connected. Flashing Green Device is on line, but connection is not established.
Device not allocated to a Master.
OK
On line, Connected Green Device is on line with connections established.
Device is allocated to a Master.
Connection Timeout Flashing Red One or more I/Os are timed out.

Quick-Change Installation and Operation Manual
Document #9620-20-c-dkgm dkft-03
Pinnacle Park
•
1031 Goodworth Drive
•
Apex, NC 27539
•
Tel: 919.772.0115
•
Fax: 919.772.8259
•
www.ati-ia.com
•
Email: info@ati-
ia.com
C - 13
3.1.8 Using Ethernet Quick-Connect
Using Ethernet Quick-Connect requires that the tool changer reports to the PLC when it is
making electrical contact between master and tool before the PLC can start communicating to
any downstream nodes.
The “Tool Electrical Lock” signal for EtherNet/IP Quick Connect indicates to the controller
that all electrical connections to the tool-side devices are made and power is applied. This
signal comes from the tool changer. The DKG module reports “Tool Electrical Lock” as Tool
Power Is On in the bitmap (Byte 4, bit 7 - refer to Section 3.5—Software).
In Figure 3.4 actions shown in red are the typical application actions, but may vary and are
outside the scope of the manual. Refer to section E-3 of the ODVA EtherNet/IP specification
(Edition 1.14) for specific requirements and actions of the controller.
Figure 3.4—Quick Connect Sequence Diagram
Section 4.1—Recommended Sequence of Operation describes in detail the behavior of the Tool
Power Is On, Tool Present, RTLV, TSIV, and TSRV bits during the operation of the Tool
Changer

Quick-Change Installation and Operation Manual
Document #9620-20-c-dkgm dkft-03
Pinnacle Park
•
1031 Goodworth Drive
•
Apex, NC 27539
•
Tel: 919.772.0115
•
Fax: 919.772.8259
•
www.ati-ia.com
•
Email: info@ati-
ia.com
C - 14
3.2 Arc Prevention Circuit
The DKG Module incorporates ATI’s exclusive Arc Prevention Circuit. The Arc Prevention Circuit
extends the life of all electrical power contacts by eliminating arcing caused by inductive loads and high
inrush current during coupling/uncoupling. The Arc Prevention Circuit makes it possible to
couple/uncouple without switching power off and prevents damage to the contacts.
In the DKG Module, the Arc Prevention Circuit controls the ON/OFF status of the Output Power V+.
The behavior of the Arc Prevention Circuit is more fully described in the following sections.
3.2.1 Arc Prevention Circuit Behavior during Coupling
The behavior of the Arc Prevention circuit during coupling can be more clearly understood by
referring to Figure 3.5, which shows the power-on timing diagram for the Arc Prevention
Circuit. Starting at the top of the diagram, electrical contact between Master and Tool Pin
Contacts occurs. The LATCH command is issued initiating locking of the Master and Tool.
The Arc Prevention Circuit will turn on Output power. The time delay between when the
electrical contacts become fully engaged to when power is actually available to the EOAT
(time t1in the diagram) is less than 100ms.
Important: The Arc Prevention Circuit will only allow power to pass to the Tool after the
LATCH command has been issued and the Master and Tool module’s electrical contacts are
fully engaged. The Tool Power Is On (Byte 4, bit 7 - refer to Section 3.5—Software) indicates
when this is the case.
Figure 3.5—Arc Prevention Circuit Power-On Timing
3.2.2 Arc Prevention Circuit Behavior during Uncoupling
The behavior of the Arc Prevention Circuit during uncoupling can be more clearly understood
by referring to Figure 3.6 which shows the power-off timing diagram for the Arc Prevention
Circuit. Starting at the top of the diagram, the UNLATCH command is issued thus initiating
uncoupling of the Master and Tool.
Immediately after the UNLATCH command is issued, the Arc Prevention Circuit will turn off
Output power. The power-off time delay between the UNLATCH command and the switching
off of power (designated t2in the diagram) is less than 50ms.
Sometime after power is turned off and the Master and Tool begin to separate, electrical
contact between Master and Tool Pin Contacts will be lost. This occurs with a delay,
designated t3in the diagram, after the UNLATCH command is issued. The magnitude of time
t3is a function of many factors, including the weight of the EOAT, the friction between Master
and Tool alignment pins, etc. but is usually not shorter than 100ms.

Quick-Change Installation and Operation Manual
Document #9620-20-c-dkgm dkft-03
Pinnacle Park
•
1031 Goodworth Drive
•
Apex, NC 27539
•
Tel: 919.772.0115
•
Fax: 919.772.8259
•
www.ati-ia.com
•
Email: info@ati-
ia.com
C - 15
Figure 3.6—Arc Prevention Circuit Power-Off Timing
3.3 Tool Module
In addition to providing Tool-ID, the Tool module also functions as a pass-through for EtherNet/IP and
Auxiliary Power signals to downstream equipment, for more details refer to Section 10—Drawings.
3.3.1 Tool-ID Switches
A pushbutton switch is provided on the Tool module for setting the Tool-ID number. There are
ten possible Tool-ID values available. To change the Tool-ID value, remove the four screws
that attach the clear window over the Tool-ID switch. Use the pushbuttons to set the Tool-ID to
the desired value.
Note: When there is no Tool mated to the Master, the Tool Present bit will become low and
each Tool-ID bit will be assigned a value of 1, which translates to a Tool-ID of 15.
Since a Tool-ID of 15 is impossible, (there are only 0–9 digits on the thumbwheel
switch) one could use this as an added indication that the Tool is not present.
Figure 3.7 shows the location of the Tool-ID switch and push buttons. After adjustment is
completed, ensure that the seal and window are re-positioned correctly to prevent a leakage
path to inside the module.
Figure 3.7—DKF Tool Module, Tool-ID Switch Settings
(Refer to the bitmap in Table 3.5 for details of how the Tool-ID is reported)
Tool-ID
Pushbuttons

Quick-Change Installation and Operation Manual
Document #9620-20-c-dkgm dkft-03
Pinnacle Park
•
1031 Goodworth Drive
•
Apex, NC 27539
•
Tel: 919.772.0115
•
Fax: 919.772.8259
•
www.ati-ia.com
•
Email: info@ati-
ia.com
C - 16
3.4 Tool-Side TSI
The Tool Stand Interlock (TSI) circuit is provided to ONLY allow Tool release while in the stand or
storage location as indicated by actuation of a customer-integrated switch. The customer must integrate
a single throw, double pole (Normally Open, spring return) limit switch to work with this feature
(reference Figure 3.8). The limit switch should be mounted to the end effector in such a way that the
switch is "made" only when the Tool is in the stand or storage location.
There is both a firmware and hardware interrupt for the Unlatch command. There are two different
versions of firmware that can be identified by the label on the module and/or viewing the web browser.
When the firmware determines the Unlatch is enabled, it will be reported in the bitmap in the form of
the "Unlatch Enabled" bit. (refer to Section 3.5—Software).
As an additional safety measure, a “hard-wired” interrupt of the UNLATCH signal is provided when the
RTL sensors indicate that Master and Tool are coupled and the Tool is not in the Tool Stand.
If the tool changer is given the UNLATCH command, the TSRV input must be on or the tool changer
will not unlatch. The TSRV input is driven by the TSI switch when it is made in the tool stand.
The following TSI status signals are also reported in the bitmap (refer to Section 3.5—Software):
RTLV (Ready to Lock Verify): Ready to Lock Verify status of RTL bypass relay in the Master module.
TSIV (TSI Limit Switch Verify): Status of 2nd contact of the limit switch that is located on the Tool.
TSRV (TSI Relay Verify): Status of the TSI Relay in the Tool module.
Section 4.1—Recommended Sequence of Operation describes in detail the behavior of the RTLV, TSIV,
and TSRV bits during the operation of the Tool Changer.
3.4.1 TSI Behavior for Module with Firmware Version 2.52 or Later
The DKG-M DKF-T modules with firmware 2.52 or later, rely on the status of the Ready-To-
Lock (RTL) sensors, the Tool Present Signal, and the TSIV input to determine when it is
appropriate to unlatch the Tool. The Tool Present signal indicates if the Master and Tool are
coupled while the TSIV input indicates when the TSI mechanical switch on the Tool is
actuated, thereby indicating that the Tool is in the stand.
There is both a firmware and hardware interrupt for the Unlatch command. Firmware
compares the Tool Present signal with the TSIV input and enables the Unlatch command only
if it meets the conditions in Table 3.3.
Table 3.3—UNLATCH Enable Logic and Truth Table
Tool
Present
TSIV UNLATCH
Enabled Status of Master Body
0
0
1
No Tool, positioned in free air
1
0
0
Tool is present, positioned in free air
1
1
1
Tool is present, positioned in Tool Stand
For example, if the DKG module receives an UNLATCH command and the Tool Present
signal indicates that Master and Tool are coupled but the TSIV indicates that the Tool is not in
the Tool Stand then the UNLATCH command is ignored.

Quick-Change Installation and Operation Manual
Document #9620-20-c-dkgm dkft-03
Pinnacle Park
•
1031 Goodworth Drive
•
Apex, NC 27539
•
Tel: 919.772.0115
•
Fax: 919.772.8259
•
www.ati-ia.com
•
Email: info@ati-
ia.com
C - 17
3.4.2 TSI Behavior for Module with Prior to Firmware Version 2.52
The DKG-M DKF-T modules with firmware prior to 2.52, rely on the status of the Ready-To-
Lock (RTL) sensors and the TSIV input to determine when it is appropriate to unlatch the Tool.
The RTL sensors indicate if the Master and Tool are coupled while the TSIV input indicates
when the TSI mechanical switch on the Tool is actuated, thereby indicating that the Tool is in
the stand.
There is both a firmware and hardware interrupt for the Unlatch command. Firmware
compares the RTL sensor signals with the TSIV input and enables the Unlatch command only
if it meets the conditions in Table 3.4.
Table 3.4—UNLATCH Enable Logic and Truth Table
RTL1 &
RLT2
TSIV UNLATCH
Enabled Status of Master Body
0
0
1
No Tool, positioned in free air
0
1
1
No Tool, positioned in Tool Stand (This is a
transient state which is only true just prior to
RTL being made)
1
0
0
Tool is present, positioned in free air
1
1
1
Tool is present, positioned in Tool Stand
For example, if the DKG module receives an UNLATCH command and the RTL sensor
signals indicate that Master and Tool are coupled but the TSIV indicates that the Tool is not in
the Tool Stand then the UNLATCH command is ignored.
Figure 3.8—Tool Stand Interlock (TSI)
CAUTION: This Tool Changer is equipped with Tool
Stand Interlock (TSI). Special procedures are
required to uncouple the tool changer.

Quick-Change Installation and Operation Manual
Document #9620-20-c-dkgm dkft-03
Pinnacle Park
•
1031 Goodworth Drive
•
Apex, NC 27539
•
Tel: 919.772.0115
•
Fax: 919.772.8259
•
www.ati-ia.com
•
Email: info@ati-
ia.com
C - 18
3.5 Software
The EDS file for the Master node is available from the ATI website (www.ati-
ia.com/download/edsfiles) or by e-mail. Reference the part number given below:
DKG-M Node EDS File
9031-20-1027
An I/O bitmap for the Master node is provided in the table below. The default setting from the factory
for the Master module is IP Address 136.129.1.1.
Table 3.5—I/O Bitmap, Robot Inputs from ATI Master, (9121-DKG-M),
EtherNet Default IP Address 136.129.1.1
Byte
Bit#
Name
Description/Function
1
0
Locked
Tool Changer Locked Proximity Sensor Input
1
Unlocked
Tool Changer Unlocked Proximity Sensor Input
2
Input and Logic Power Good
Input and Logic Power Present Input
3
Valve Power Available
Valve Power Present Input
4
RTL1
Ready-to-Lock 1 Proximity Sensor Input
5
RTL2
Ready-to-Lock 2 Proximity Sensor Input
6 RTLV Ready-to-Lock Verify Input
7
-
(Reserved)
2
0
Tool-ID 1
Tool-ID
1
Tool-ID 2
Tool-ID
2
Tool-ID 4
Tool-ID
3
Tool-ID 8
Tool-ID
4
TSIV
TSI Limit Switch Verify
5 TSRV TSI Relay Verify
6
Unlatch Enabled
Unlatched Enabled Status Information
7
Tool Present
Hard-Connect Tool Present Input
3
0
-
(Reserved)
1
-
(Reserved)
2 Error on Latch Output Latch output overloaded
3
Error on Unlatch Output
Unlatch output overloaded
4
-
(Reserved)
5
-
(Reserved)
6
-
(Reserved)
7
-
(Reserved)
4
0
-
(Reserved)
1
-
(Reserved)
2
-
(Reserved)
3
-
(Reserved)
4 - (Reserved)
5
-
(Reserved)
6
COMM OK
Indicates EtherNet/IP Connectivity is Established
7 Tool Power Is ON
Indicates that Arc Prevention Circuit is turned ON
and power is provided to the Tool
5 -8
0 - (Reserved)
1
-
(Reserved)
2
-
(Reserved)
3
-
(Reserved)
4
-
(Reserved)
5
-
(Reserved)
6 - (Reserved)
7
-
(Reserved)

Quick-Change Installation and Operation Manual
Document #9620-20-c-dkgm dkft-03
Pinnacle Park
•
1031 Goodworth Drive
•
Apex, NC 27539
•
Tel: 919.772.0115
•
Fax: 919.772.8259
•
www.ati-ia.com
•
Email: info@ati-
ia.com
C - 19
Table 3.1—I/O Bitmap, Robot Outputs to 9121-DKG-M Module,
Ethernet Default IP Address 136.129.1.1
Byte
Bit#
Name
Description/Function
1
0 Latch (Lock) Latch Solenoid Valve Output
1 Unlatch (Unlock) Unlatch Solenoid Valve Output
2 - (Reserved)
3 Clear Errors Reset errors, allow affected I/O to be reactivated
4 - (Reserved)
5 - (Reserved)
6 - (Reserved)
7 - (Reserved)
2 - 8
0 - (Reserved)
1 - (Reserved)
2 - (Reserved)
3 - (Reserved)
4 - (Reserved)
5 - (Reserved)
6 - (Reserved)
7 - (Reserved)

Quick-Change Installation and Operation Manual
Document #9620-20-c-dkgm dkft-03
Pinnacle Park
•
1031 Goodworth Drive
•
Apex, NC 27539
•
Tel: 919.772.0115
•
Fax: 919.772.8259
•
www.ati-ia.com
•
Email: info@ati-
ia.com
C - 20
4. Operation
4.1 Recommended Sequence of Operation
This recommended Sequence of Operations procedure is to be used as a general guide when
programming a robot or PLC for use with a Tool Changer and DKG-M DKF-T control/signal modules.
This procedure is intended for "automatic" modes used during normal application processes.
Recommendations for operation in “teach” or “manual” modes where the operator has the teach pendant
in-hand will be addressed in a separate Troubleshooting Guide.
1. StartThe robot and Tool Changer Master are free of the stand or storage location, the
Tool Changer is uncoupled and the Tool Changer locking mechanism may be fully
retracted (unlocked condition) or fully extended (missed Tool condition, i.e., Locked and
Unlocked inputs are false). The Tool is by itself in the Tool Stand.
a. The RTL inputs (RTL1 & RTL2) are false.
b. RTLV is false.
c. The ATI Tool and any downstream device is offline.
d. The Input and Logic Power Good is true. The Valve Power Available input is true
provided the Switched AUX power supply is on.
e. Tool Power is On is false.
f. TSIV is false.
2. Unlock the Master. (This must be done prior to the Master entering the Tool to prevent the
ball bearings from impinging on the Tool bearing race.)
a. The Latch output command is made false and the Unlatch output command is made
true.
b. The Unlocked input goes true and remains true, indicating that the Tool Changer
locking mechanism is fully retracted and the Unlatch operation is complete.
3. Robot and Master move into the Tool, are parallel and within 0.125” to 0.06” of the Tool
(i.e., the module contact pins are touching, but the RTL sensors have not yet sensed the
targets on the Tool).
a. The Tool Present and TSIV inputs go true, indicating that the Master and Tool are in
close proximity of each other and verifying the operation of the TSI limit switch.
b. When the Tool Present input goes true, Tool-ID becomes available within 50ms.
c. Power is not yet available on the Tool. The bit “Tool Power is On” is false.
4. Robot and Master move within 0.06” of the Tool.
a. The RTL inputs are true, indicating that it is okay to couple the Tool.
b. RTLV is true.
5. Couple the Tool Changer.
a. The Unlatch output is made false and the Latch output is made true.
b. With the Latch output made true, Power becomes available on the Tool and the bit
“Tool Power is ON” turns on.
c. The Unlocked input goes false a short time later, indicating piston travel.
Subsequently, the Locked input goes true and remains true, indicating that the
coupling operation is complete.
d. Sometime thereafter3, communications should be established with the downstream
Ethernet device(s).
3The time it takes to establish connection with a downstream EtherNet/IP node depends on the power up and
reconnect time of the individual EtherNet/IP equipment that is installed on the tool.
This manual suits for next models
1
Table of contents
Other ATI Technologies Controllers manuals
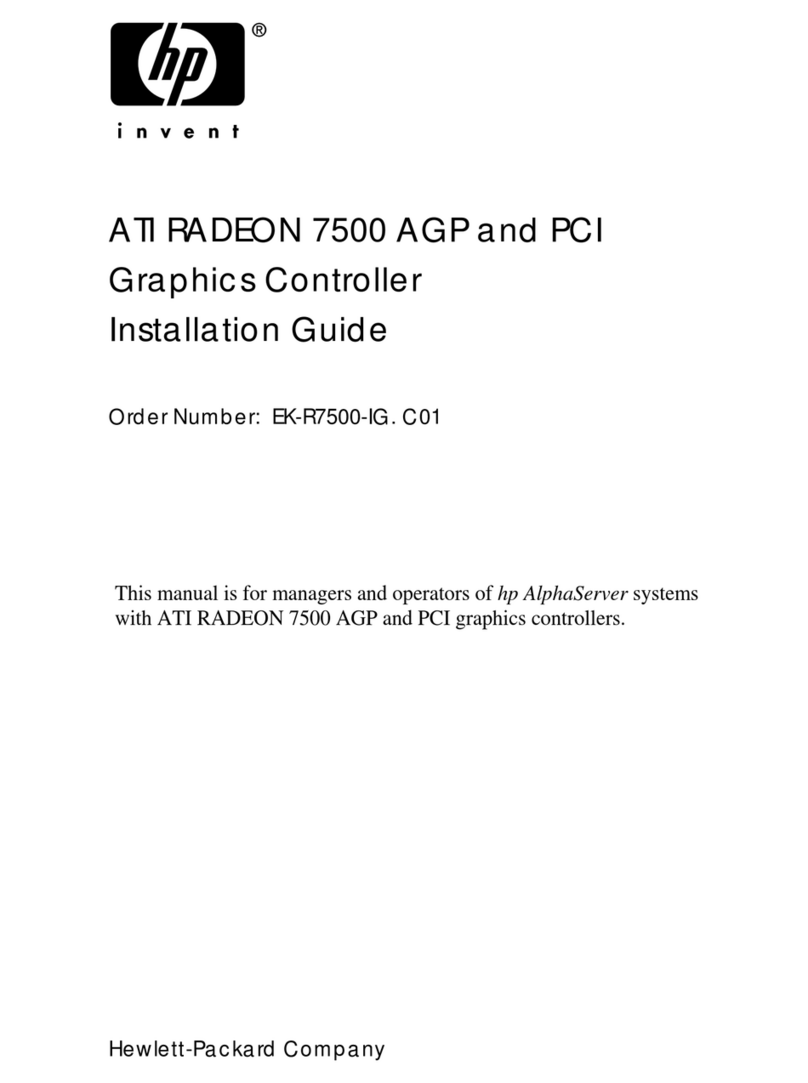
ATI Technologies
ATI Technologies 100-432001 - RADEON 7500 Multi-monitor Graphics... User manual
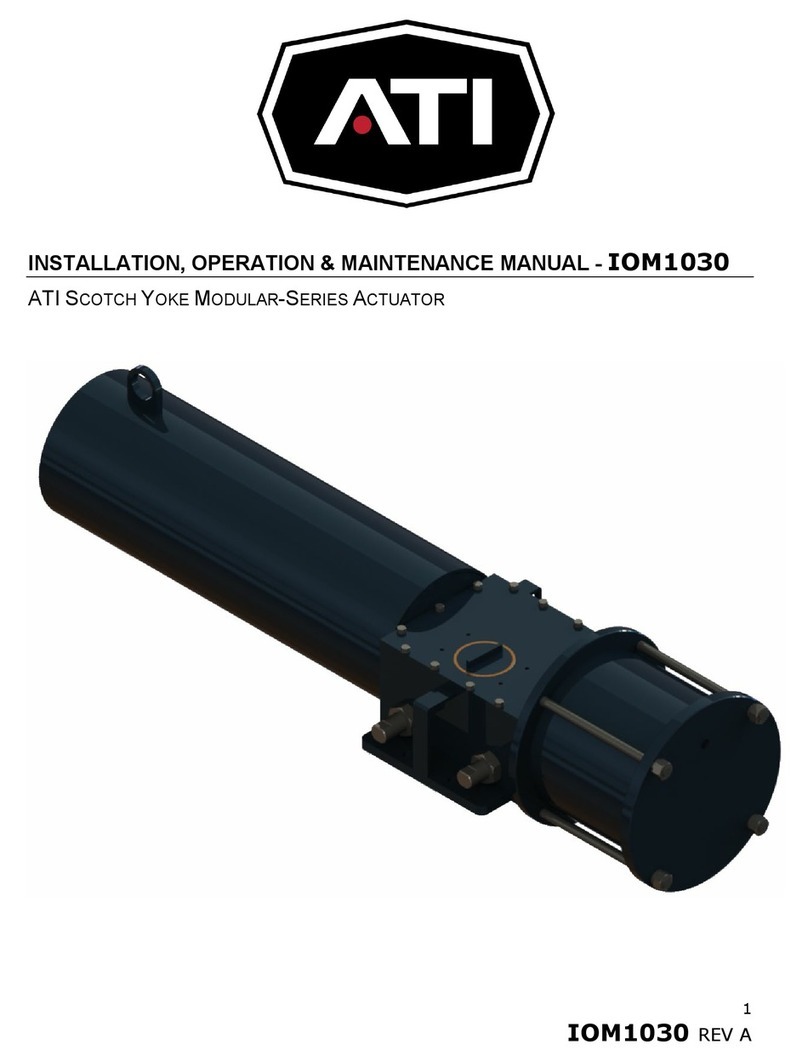
ATI Technologies
ATI Technologies IOM1030 Instruction manual
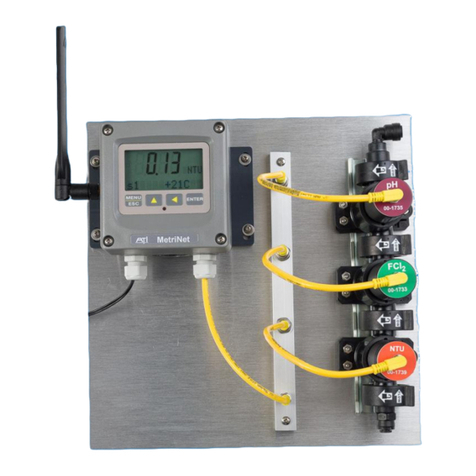
ATI Technologies
ATI Technologies MetriNet Q52 User manual
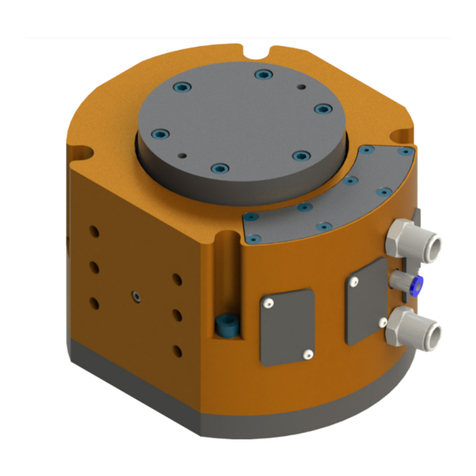
ATI Technologies
ATI Technologies 9150-PCFC-12 User manual
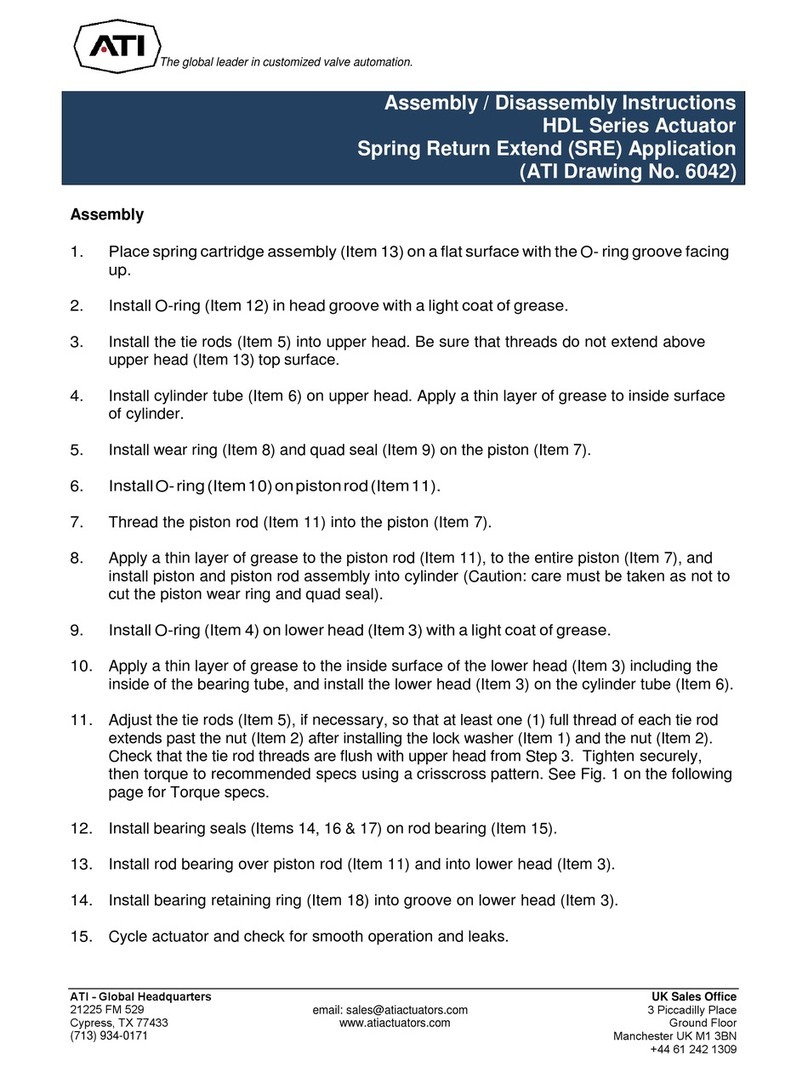
ATI Technologies
ATI Technologies HDL Series User manual
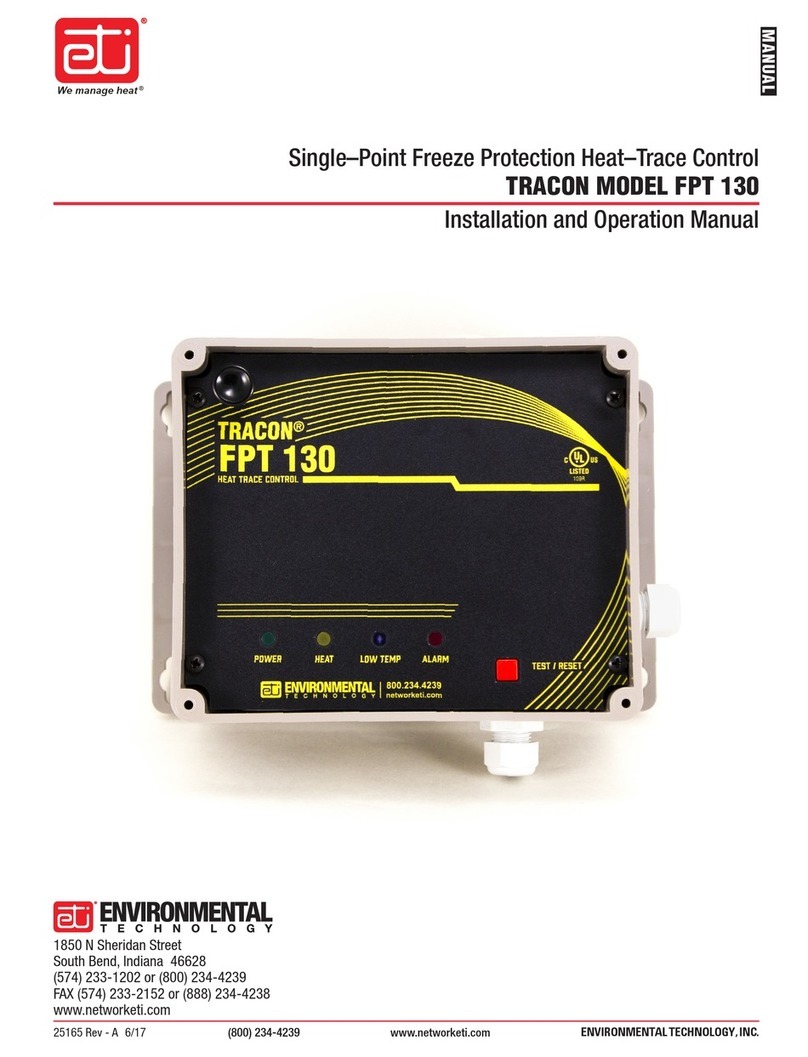
ATI Technologies
ATI Technologies TRACON FPT 130 User manual