ATORN DFT Series User manual

Operators manual
DFT
Gages for coating thickness measurements

ATORN DFT FE and ATORN DFT FE+NF
Gages for coating thickness measurements
© 2019 by ATORN Service, Ludwigsburg, Germany
This document is protected by copyright. All rights reserved. This document
may not be reproduced by any means (print, photocopy, microfilm or any oth-
er method) in full or in part, or processed, multiplied or distributed to third par-
ties by electronic means without the written consent of ATORN Service.
Subject to correction and technical changes.
Note: Designations not marked with ® or ™ may also be protected by law.
Document no. 1002229
Issue date 2019-11-22 (for software version 1.0.2)
Distribution Further sources of supply
ATORN Service www.atorn.de
Schliefenstraße 40
71636 Ludwigsburg
Germany

ATORN DFT i
1 Safety information . . . . . . . . . . . . . . . . . . . . . . . . . . . . . . . . . . 1
1.1 Intended use . . . . . . . . . . . . . . . . . . . . . . . . . . . . . . . . . . 1
1.2 Environmental conditions . . . . . . . . . . . . . . . . . . . . . . . . . . 1
1.3 Safety of the electrical equipment . . . . . . . . . . . . . . . . . . . . 2
2 Description . . . . . . . . . . . . . . . . . . . . . . . . . . . . . . . . . . . . . . . . 3
2.1 Measurement reading view (example) . . . . . . . . . . . . . . . . . 3
2.2 Gage . . . . . . . . . . . . . . . . . . . . . . . . . . . . . . . . . . . . . . . 4
2.3 Keys . . . . . . . . . . . . . . . . . . . . . . . . . . . . . . . . . . . . . . . . 5
2.4 Menus - function overview . . . . . . . . . . . . . . . . . . . . . . . . . 6
2.5 Gage concept . . . . . . . . . . . . . . . . . . . . . . . . . . . . . . . . . 8
2.6 Technical data . . . . . . . . . . . . . . . . . . . . . . . . . . . . . . . . . 9
3 Setup . . . . . . . . . . . . . . . . . . . . . . . . . . . . . . . . . . . . . . . . . . . 17
3.1 Installing batteries. . . . . . . . . . . . . . . . . . . . . . . . . . . . . . 17
3.2 Switching on the gage . . . . . . . . . . . . . . . . . . . . . . . . . . 17
3.3 Switching off the gage . . . . . . . . . . . . . . . . . . . . . . . . . . 17
4 Getting started . . . . . . . . . . . . . . . . . . . . . . . . . . . . . . . . . . . . 18
5 Settings for measurement . . . . . . . . . . . . . . . . . . . . . . . . . . . . 19
5.1 Creating a new batch . . . . . . . . . . . . . . . . . . . . . . . . . . . 20
5.2 Opening a batch . . . . . . . . . . . . . . . . . . . . . . . . . . . . . . 21
5.3 Assigning a different calibration to the opened batch . . . . . 22
6 Measurement . . . . . . . . . . . . . . . . . . . . . . . . . . . . . . . . . . . . . 23
6.1 Notes on coating thickness measurement . . . . . . . . . . . . . . 23
6.2 Before you start . . . . . . . . . . . . . . . . . . . . . . . . . . . . . . . 23
6.3 Measuring - Procedure . . . . . . . . . . . . . . . . . . . . . . . . . . 24
7 Calibration. . . . . . . . . . . . . . . . . . . . . . . . . . . . . . . . . . . . . . . 25
7.1 Calibration - When necessary?. . . . . . . . . . . . . . . . . . . . . 26
7.2 Selecting the appropriate calibration method . . . . . . . . . . . 26
7.3 Performing a calibration . . . . . . . . . . . . . . . . . . . . . . . . . 28
7.4 Calibration- Assigning/changing names . . . . . . . . . . . . . . 35
7.5 Calibration - Reset . . . . . . . . . . . . . . . . . . . . . . . . . . . . . 35
8 Data transfer . . . . . . . . . . . . . . . . . . . . . . . . . . . . . . . . . . . . . 36
8.1 Transfer batch files in the PHASCOPE PAINT app. . . . . . . . 36
8.2 Transfer single readings online to an Excel file via PC-Datex 38

ii ATORN DFT
9 Glossary . . . . . . . . . . . . . . . . . . . . . . . . . . . . . . . . . . . . . . . . . 40
9.1 Glossary - Display symbols . . . . . . . . . . . . . . . . . . . . . . . . 43
9.2 Glossary - Display texts. . . . . . . . . . . . . . . . . . . . . . . . . . . 44
10 About . . . . . . . . . . . . . . . . . . . . . . . . . . . . . . . . . . . . . . . . . . . 47

ATORN DFT 1
Safety information
1 Safety information
If you use the instrument as intended and observe the safety information, the
instrument poses no danger.
Please read and follow this Operator's Manual and observe the safety infor-
mation. Also observe generally applicable safety and accident prevention reg-
ulations.
1.1 Intended use
The gage is intended solely for measurement of coating thicknesses.
Only accessories approved or recommended by ATORN Service may be con-
nected to the gage.
Any use beyond this is not the intended use. The risk of damage ensuing there-
from is borne solely by the user.
1.2 Environmental conditions
Storage and transport temperature: 0 … +50 °C
Temperature
When exposed to sunshine, the areas behind glass windows (e.g. in an
automobile) can easily reach temperatures in excess of +50 °C. This can
cause damage to the instrument.
►Do not keep or store the instrument and accessories behind glass
windows, or near to sources of heat such as radiators etc.!
Acid
The gage and accessories are not acid-proof.
►Do not place the instrument or accessories in contact with acids or liquids
which contain acid!

2 ATORN DFT
Safety information
Potentially explosive environment
The gage and accessories are not suitable for use in potentially posted
environments.
►Operate the gage and accessories only outside of potentially explosive
areas!
1.3 Safety of the electrical equipment
Only accessories approved or recommended by ATORN Service may be con-
nected to the gage!
USB cable
Damaged USB cable
Kinking or pinching the USB cable can result in a broken wire. Data trans-
mission is then no longer possible.
►Connect only an undamaged USB cable with a max. length of 3 m to the
gage.
►Always coil up the USB cable for storage.
Batteries/rechargeable batteries
•Use the following alkaline or lithium battery type: Mignon, 1.5 V,
LR6 - AA
or
•Use the following NiMH rechargeable battery type: Mignon, 1.2 V,
HR6 - AA
Servicing and repairs
Modifications, repairs as well as maintenance and service work on the instru-
ment and accessories may be carried out only by service personnel authorized
by ATORN Service.
Exception: Changing the batteries/rechargeable batteries.

ATORN DFT 3
Description
2 Description
The gages in the ATORN DFT series
measure coating thicknesses easily,
quickly and in a nondestructive man-
ner. Gage construction with an inte-
grated measuring probe allows sin-
gle-hand measurements, preferably
on flat and cylindrical samples.
This operator's manual describes the
following gage types in the ATORN
DFT series:
•ATORN DFT FE
Gage type for measurements on fer-
rous base materials (Fe) only
•ATORN DFT FE+NF
Gage type for measurements on
both as measurements on ferrous
(FE) as well as on non-ferrous metal
base materials (NF)
Additional information can be found
in the data sheet, page 9
2.1 Measurement reading view
(example)
1 Measuring application
NF/FE: Nonferrous coating material on
ferrous base material
NC/NF: Electrically nonconducting and
nonferrous coating material on electri-
cally conducting nonferrous metals
2 Batch name (batch type abbrev.)
3 Tolerance limits
4 Measurement reading
5 Statistics values
6 Key assignment line (example:
delete symbol, open block statis-
tics, symbol for opening calibra-
tion)
7 Battery indicator
8 Unit of measurement
A list of all display symbols and texts
can be found starting on page 43.
1
2
3
4
3
5
6
NF/FE
Batch 01 (IDV)
No 1 n 10
X 46.8 s 1.81
Min 44.9 Max 48.5
BLOCK
47.3 µm
44.5
49.0
Example of the measurement
reading view showing statis-
tics with set tolerance limits
7
8

4 ATORN DFT
Description
2.2 Gage
1 Eyes for a carrying strap
2 Signal lamp to indicate measurement acquisition and limit violations
3 Display
4 Keys, On/Off key, for description see page 5
5 Positioning support for reliable placement of the gage on the surface
6 Probe
7 USB port
8 Battery compartment cover
Gage dimensions can be found in the data sheet, page 14
Front of gage
1
2
3
4
5
6
7
8
Rear side of gage

ATORN DFT 5
Description
2.3 Keys
There are 4 keys for operating the gage.
The bottom line of the display always shows the functions of the 4 keys (see
illustration below). The assignment depends on the opened menu page.
The function shown on the display is assigned to the key directly underneath (example).
The key has two functions:
•It switches the gage on and off when the key is held for at least 1 s
•Function shown in the bottom line of the display
The key has two functions:
•It moves the cursor/mark down when is shown in the bottom line of
the display
•It opens the main menu when is not shown in the bottom line of the
display
A description of the remaining key symbols can be found starting at page 43
SEL

6 ATORN DFT
Description
2.4 Menus - function overview
Main menu for the "Industrial" batch template package (Standard)
Statistics > Display of the statistics for the opened batch
Batch
Modify >
Settings and en-
tries for the
opened batch
MEASURE > Switch to the measurement view
Tolerance Limits > Activation of limit monitoring and
setting of the limits
Batch Info > Input of information
View Settings > Measurement view
Batch - statistics display
Block - statistics display
Units > Set the unit of measurement
Block Size > Activation of automatic block for-
mation and setting of the block
size
Offset > Set the offset value
More Settings > MEASURE
Counted Average
Measurement Mode
(Single Reading, Free Running)
Measurement acquisition
Value Resolution
Save Measurements
Air Reference
Calibration assign
Batches > New >
List of saved batches
(After a batch has been selected, it can be opened, copied
or deleted.)
Calibrations > New >
List of saved calibrations

ATORN DFT 7
Description
After a calibra-
tion has been
saved, the fol-
lowing func-
tions are avail-
able)
Rename Rename a selected calibration
Quick Activate a semi-automatic calibration routine
Reset Delete all coating thickness correction values
from the selected calibration
Delete Delete a selected calibration
Gage Settings
>
Language Select the display language
Display Settings > Brightness
Flip Display
Indication Settings > Key press signal
Audible signal
Optical Indication
Vibration
Connections > USB Mode
WiFi
Date & Time >
More Settings > Units (for new batches)
Default Value Resolution
Usage (batch template package
setting)
Probe Settings > Probe Raw Values
Line Frequency Setup
Delete All Calibrations
About > Information about software version
and probe as well as legal informa-
tion such as copyright, data protec-
tion conditions, enhanced labeling

8 ATORN DFT
Description
2.5 Gage concept
In order to measure, a Batch (file) and a suitable Calibration (reference) must
be created in the gage for the Measuring Application. A description of the
terms measuring application, batc h and calibration can be found in Chapter
"Glossary".
The essential content of the batch and calibration files and their relationship to
each other are shown schematically in the following illustration:
A measuring application is defined in the gage by a batch file and a calibration file
and their linking to each other.
Measuring application
Batch
(settings)
•Limit monitoring
•Grouping of measured read-
ings
•Offset value
•Counted average
•Measuring mode (single
readings, free running)
•Measurement acquisition
(automatic after placement
the probe on the sample,
manual)
•Measurement view, decimal
places for the measured
reading
•Unit of measurement
•Save readings (yes/no)
Calibration
(recorded by reference measure-
ment)
•Material properties of the
sample
•Geometric shape of the sam-
ple
•Surface roughness
•1 or 2 reference coating
thicknesses
•Air reference value
Gage

Technical Data
DFT
Coating Thickness Measurement on Virtually all Metals
Non-destructive measurements
Universal applicable coating thickness gage
1.1 Technical Data
Easy and convenient
operation
Compact and robust case

10
DFT
Description
The gage models ATORN DFT measure coating thicknesses easily, quickly and non-destruc-
tively
Gage properties • Ideal for onsite applications (outside and inside) due to the compact size, the light weight
and the robust and durable instrument design
• Probe integrated in the gage for single-handed operation
• IP65, dust-tight and water repellant and resistant
• The 3-point-support ensures a stable and sure positioning on the surface
• Intuitive operation of the menu navigation and graphic display
• The measurement presentation flips automatically and thus allows optimum reading in dif-
ferent measuring positions
• Different languages selectable
• Automatic selection of the measuring method corresponding to the base material (only for
gage type FE+NF)
• Patented conductivity compensation for measurements on non-magnetic base materials
Applications Steel, iron, cast iron base materials (FE) Non-ferrous metal base materials (NF)*
Examples
*Only measurable with variant type FE+NF
• Zinc, chromium, copper, paint, varnish or
plastic on steel, iron or cast iron
(NF, NC/FE)
• Paint, varnish or plastic coatings on alu-
minium, copper or brass (NC/NF)
• Anodized coatings on aluminium
The gages are applicable for measurements both on smooth and rough surfaces
Gage Types FE FE+NF
Gage type for measurements on ferrous base
materials (Fe) only
Gage type for measurements on both as mea-
surements on ferrous (FE) as well as on non-fer-
rous metal base materials (NF)
High-end gages with large data memory for 250,000 measured readings in 2500 batches, USB
and wireless interfaces for data transfer as well as batch template packages Industrial and Cor-
rosion for easy and fast creation of measurement task files (batches). The package Corrosion con-
tains 5 batch types with preconfigurations especially for coating thickness measurement in the
corrosion protection area, e.g. according to the measuring regulation SSPC PA2.

11
DFT
Batch Template Packages Templates for Creation Measurement Tasks
Industrial
The packages contain various batch types. That are batch templates with especially designed
measurement tasks for specific coating thickness measurement applications.
Template package contains following batch types:
•Individual
Batch template for free configuration: All metrological standard functions are available
and calibration method Zero + 1 Foil is used
•Elementary
Template with minimum configuration: No further metrological function settings (customiz-
able), only calibration method Zero is used
•Smooth Surface
Preconfigured batch template for measurements on smooth surfaces: Settings of tolerance
limit values (customizable) and calibration method Zero + 1 Foil is used.
•Rough Surface
Preconfigured batch template for measurements on rough surfaces: Display and storage
of the mean value of a given number (n) of measurements (customizable, single readings
are also stored) and the calibration method Zero + 2 Foils is used.
Corrosion
Template package containing batch types with especially designed measurement tasks for mea-
surements of corrosion-protective coatings. The template package contains following batch types:
•Individual
Batch template for free configuration: All metrological standard functions are available
and calibration method Flexible is used
•IMO PSPC
Preconfigured batch template containing 90/10 rule, calibration method and evaluation
for coating thickness measurement according to requirements of "Performance Standard
for Protective Coatings" of the International Maritime Organization (IMO PSPC), calibra-
tion method 2 Foils is used
•SSPC PA2
Preconfigured batch template with settings (partly customizable), calibration method and
evaluation regulations for coating thickness measurement according to guideline SSPC-
PA2 of the Society for Protective Coatings (SSPC), calibration method 2 Foils is used
•ISO 19840
Preconfigured batch template with settings (partly customizable), calibration method and
evaluation regulations for coating thickness measurement according to standard
ISO 19840, calibration method 2 Foils is used
•AS 3894.3
Preconfigured batch template with settings (partly customizable), calibration method and
evaluation regulations for coating thickness measurement according to Australian stan-
dards AS 2331.1.4 and AS 3894.3-B, calibration method 1 Foil is used
•SIS 184160
Preconfigured batch template with settings (partly customizable), calibration method and
evaluation regulations for coating thickness measurement according to Swedish standard
SIS 184160, calibration method 2 Foils is used
Metrological Standard Functions Measurement Tasks
Batch File containing all metrological function settings and the linking to calibration necessary for the
measurement task as well as the measured readings and evaluations
Block creation Measured readings grouped in measurement blocks
Tolerance limits/Nominal thickness Adjustable, depending on the selected batch type
Offset value/Correction value Adjustable, is deducted automatically from the measured reading. Thus, one obtains the thickness
of the top coating if for instance the interim coating is known.
Measurement reading acquistion Automatic upon placement of the gage probe

12
DFT
Measurement reading storage On/Off switchable
Measurement units µm/mm or mils/inches
Measurement modes Single reading mode
After each placing of the gage probe the measuring reading is displayed and stored automati-
cally.
Free running mode
After placing the gage probe the continuous display of the measured readings appears without
automatic storage. Useful for quick checking of coating thicknesses over a defined surface area,
e.g. in tank construction.
Resolution of measurement reading Low (up to 1 decimal place), Medium (up to 2 decimal places), High (up to 3 decimal places)
Air reference value acquisition During measurement, the air reference value is used to reference the zero point determination.
Regular measurement of the air reference value is necessary to achieve high measurement accu-
racy. Automatic capture of the air value always when the gage probe is lifted from the surface.
Calibration For a correct measurement of the coating thickness, the gage must record the properties (per-
meability, electrical conductivity, geometry) of the test piece. This adjustment is carried out by a
calibration. A calibration is specified by the reference specimen (comparable in shape, material,
permeability/electrical conductivity to the test piece) and by the foil standards used (calibration
method).
Calibration Methods
•Flexible
Adjustment of the gage to geometrical form and base material of the test piece: Zero point
determination and adjustment to up to two coating thickness values by using calibration
foils. On recalibration, the individual calibration steps can be skipped.
•Zero
Adjustment of the gage to the base material and the geometry shape of the test piece
•1 Foil
Adjustment of the gage to test piece: Adjustment to a coating thickness value by using 1
calibration foil (especially for measurement tasks in the corrosion field)
•2 Foil
Adjustment of the gage to test piece: Adjustment to 2 coating thickness values by using 2
calibration foils (especially for measurement tasks in the corrosion field)
•Zero + 1 Foil
Adjustment of the gage to the base material and the geometry shape of the test piece:
Adjustment to the base material and to 1 coating thickness value by using 1 calibration
foil
•Zero + 2 Foil
Adjustment of the gage to the base material and the geometry shape of the test piece:
Adjustment to the base material and to 2 coating thickness values by using 2 calibration
foils
General Features
Test methods
Gage type FE and FE+NF
Gage type FE+NF
Automatic selection of the test method corre-
sponding to the base material
• Magnetic induction method (ISO 2178, ASTM D7091, measurement of non-magnetic
coatings on magnetic substrates)
• Eddy current method (ISO 2360, ASTM D7091, measurement of non-conductive coatings
on non-magnetic substrate metals)
Factory Calibration Each individual gage is factory calibrated at several reference points with the greatest care to
ensure the highest possible degree of trueness.
Metrological Standard Functions Measurement Tasks

13
DFT
Data memory The memory content is preserved even when there is no voltage supply; subsequent viewing of
the measured single readings and evaluations
• Memory capacity of 250,000 measured readings in 2500 batches and up to 100 cali-
brations
Evaluation Statistics
• Batch template package Industrial: Display of mean value, standard deviation, min/ max
values and number of measurements per block, per batch, coefficient of variation, number
of measured values lower/upper the set limit values
• Batch template package Corrosion: Depending of the selected measuring regulation; e.g.
for SSPC-PA2, display per measurement location (Spot)/area section (Area): Number of
(Spots), mean value, coefficient of variation, min./max. values, Range, measured read-
ings < 80 %/> 120 % of limit values (coating thickness restriction level 3)
Graphic Presentations
•Histogram
• Run-Chart, showing the progress of measured readings
Probe Single tip axial probe with spring-loaded measuring system and with wear-resistant probe tip
built-in into gage
Probe tip radius: 2 mm, Probe tip material: Hard metal
Measurement interval More than 140 measurements per minute
Display of measurement acquisition Audible by a short beep and visual by colored illuminated LED; Additional by gage vibration
Display for limit monitoring • Limit violation: Audible by 2 short beeps and visual by red illuminated LED; Additional
by gage vibration
• Measured readings between the limits: Audible by 1 short beep and visual by green
illuminated LED; Additional by gage vibration
Languages German and English
Presettings for batches Each new batch is created with a preset measurement unit and resolution for the displayed mea-
sured value. The batch template package is also preselected here. You can adapt these preset-
tings to your requirements. However, you can also change the unit of measurement and the res-
olution for the measured value display as well as further batch type presettings at any time in
the batch that has already been created.
Display • Graphic display with automatic flipping measuring presentation view (deactivatable) to
read measurement results in many different gage positions
• Setting of brightness and contrast (definable for Office, Sunlight and Night)
Data transfer • USB: Data transfer of single readings to a PC, Data import to MSExcel via PC-Datex soft-
ware; You can gratis download the PC-Datex program from Fischer-Homepage,
www.helmut-fischer.com
• WiFi: Data transfer of batches to App PHASCOPE® PAINT; Creation and export of reports
via App; You can gratis download the App from Google Play Store and Apple App Store
USB port 2.0 Type C
• For service purpose
• For connection to PC for data transfer, max. cable length: 3 m (118 inches)
Wireless interfaces WiFi: WiFi module integrated in gage, Standards IEEE 802.11b/g/n
WiFi: Frequency range: 2412 … 2484 MHz, max. output power: 17.80 dBm
Admissible climatic conditions during
storage and transport
Ambient temperature Relative Humidity
0 … +50 °C
(+32 … +122 °F)
5 … 85 %RH, at 25 °C (77 °F), non-condensing
General Features

14
DFT
Admissible climatic conditions during
operation
Ambient temperature Relative Humidity Altitude of location Pollution Degree
0 … +50 °C
(+32 … +122 °F)
5…85%RH,
at 25 °C (77 °F),
non-condensing
up to 2000 m
(6561.7 ft (US))
(above sea level)
3
Surface temperature max. +60 °C (+140 °F)
Protection class (housing) IP65, measurements under water are not permissible
Weight (incl. batteries) about 251 g
Power supply • 2 batteries: Mignon, Alkaline or Lithium, LR6 - AA, 1.5 V
• 2 rechargeable batteries: Mignon, NiMH, HR6 - AA
Battery life
Specifications valid for +20 °C (+68 °F) ambi-
ent temperature and Alkaline batteries used
> 8 h for continuous measuring, brightness set to sunlight and deactivated wireless interface
Dimensions
Gage
General Features
73 mm (2.9 ")
130 mm (5.1 ")
45 mm
(1.8 ")
38 mm
(1.5 ")
50 mm
(2 ")
Probe
12 mm
(0.47 ")

15
DFT
*
The following specifications are valid for mea-
surements by using the Single reading mea-
surement mode
The values for measurement range, trueness,
repeatability precision and measurement errors
are valid for electrically non-conductive coating
materials on steel or iron (NC/FE). The values
may differ for measurements on non-ferrous coat-
ing materials (NF).
Measurement Ranges* Steel, iron, cast iron base materials (FE) Non-ferrous metal base materials (NF)
0 … 2500 µm (98.4 mils) 0 … 2000 µm (78.7 mils)
Trueness* Steel, iron, cast iron base materials (FE) Non-ferrous metal base materials (NF)
Based on factory calibration standards and
20 °C (68 °F) for specimen and ambient tem-
perature
1070…1075 µm: ≤ 1.5 µm
1075 … 1000 µm: ≤ 2 % of nominal value
1000 … 2500 µm: ≤ 3 % of nominal value
1070 … 1050 µm: ≤ 1 µm
1050 … 1000 µm: ≤ 2 % of nominal value
1000 … 2000 µm: ≤ 3 % of nominal value
30.9 …32.9mils: ≤0.06mils
32.9 … 39.4 mils: ≤ 2 % of nominal value
39.4 … 98.4 mils: ≤ 3 % of nominal value
30.9 …32.9 mils: ≤ 0.04 mils
32.9 … 39.4 mils: ≤ 2 % of nominal value
39.4 … 78.7 mils: ≤ 3 % of nominal value
Repeatability Precision* Steel, iron, cast iron base materials (FE) Non-ferrous metal base materials (NF)
Based on factory calibration standards, 5 sin-
gle readings per standard and 20 °C (68 °F)
for specimen and ambient temperature
70 … 1050 µm: ≤ 0,25 µm
50 … 2500 µm: ≤ 0,5 % of reading
170 … 1100 µm: ≤ 0,5 µm
100 … 2000 µm: ≤ 0,5 % of reading
0…92.4 mils: ≤ 0.01 mils
2…98.4mils: ≤0.5% of reading
0.9 …73.9 mils: ≤ 0.02 mils
3.9 … 78.7 mils: ≤ 0.5 % of reading
Influence*
Steel, iron, cast iron base materials (FE) Non-ferrous metal base materials (NF)
The following values are valid for a coating thickness with a nominal value of 75 µm / 2.95 mils.
The quantity of influences are stated with the expanded measurement uncertainty U with the expanded factor of k = 2 (defines an interval
with the confidence level of 95.45 %) - according to ISO/IEC Guide 98-3:2008-09 "Guide to the expression of uncertainty in measurement".
Curvature (R), measurement error from nominal value with reference to master calibration on flat surface
No measurement error within the trueness as of
R = 75 mm ± 5 mm (2.95 " ± 0.2 ")
Measurement error 10 % for
R = 15 mm ± 1 mm (0.59 " ± 0.04 ")
A minimum of R = 2 mm (0.08 ") is required
No measurement error within the trueness as
of R = 550 mm ± 60 mm (21.65 " ± 2.36 ")
Measurement error 10 % for
R=109mm±8mm (4.29"±0.32")
A minimum of R = 2 mm (0.08 ") is required
Edge distance (R), specification from probe tip center, measurement error from nominal value
A minimum of R = 12 mm (0.47 ") is required
No measurement error within the trueness
A minimum of R = 12 mm (0.47 ") is required
No measurement error within the trueness
Edge distance (X), specification from probe tip center, measurement error from nominal value
A minimum of X = 12 mm (0.47 ") is required
No measurement error within the trueness
A minimum of X = 12 mm (0.47 ") is required
No measurement error within the trueness
Base material thickness (D), measurement error from nominal value
Steel, iron, cast iron base materials (FE)
No measurement error within the trueness as of
D = 0.86 mm ± 0.09 mm
(33.85 mils ± 3.54 mils)
Measurement error 10 % for
D = 0.44 mm ± 0.02 mm
(17.32 mils ± 0.79 mils)
Copper base material (Cu)
No measurement error within the trueness as
of D = 0.09 mm ± 0.009 mm
(3.54 mils ± 0.35 mils)
Measurement error 10 % for
D = 0.035 mm ± 0.002 mm
(1.38 mils ± 0.079 mils)
Measuring
spot
Measuring spot
in the center of
the circular sur-
face
Measuring
spot = Probe
pole center
Measuring
spot

DFT
www.atorn.de
Base material Steel, iron, cast iron base materials (FE) Non-ferrous metal base materials (NF)
Influence on base material (FE) permeability in
regard to factory calibration standards (master
calibration): 137 FN ± 0.2 FN
Measurement error of 10 % for ferrite content of
122 FN ± 1.1 FN
Influence of the el. conductivity of the base
material (NF) in the range from 30 to
100 % IACS: Measurement error ≤ 2 %, valid
for the total measurement range
Temperature no influence In a range of ± 20 °C: ± 3 µm
In a range of ± 68 °F: ± 0.12 mils
Scope of Supply
Gage; 2 batteries; USB cable type C to type A (1 m (39.4 inches)); guideline; calibration set
suitable to gage type
• Calibration set for gage type FE
(Test plate NF/FE (603-477) and 3 calibration foils (ca. 25 µm/0.98 mils (505-953),
75 µm/2.95 mils (505-955) and 540 µm/21.26 mils (505-965))
• Calibration set for gage type FE+NF
(Test plates NF/FE (603-477) and ISO/NF (603-478) as well as 3 calibration foils (ca.
25 µm/0.98 mils (505-953), 75 µm/2.95 mils (505-955) and 540 µm/21.26 mils
(505-965))
Order Information
Gages Description Order No.
ATORN DFT FE Gage type for measurements on ferrous base materials (Fe) only xxxxxxxx
ATORN DFT FE+NF Gage type for measurements on both as measurements on ferrous (FE) as well as on non-ferrous
metal base materials (NF)
xxxxxxxx
Influence*
Steel, iron, cast iron base materials (FE) Non-ferrous metal base materials (NF)
The following values are valid for a coating thickness with a nominal value of 75 µm / 2.95 mils.
The quantity of influences are stated with the expanded measurement uncertainty U with the expanded factor of k = 2 (defines an interval
with the confidence level of 95.45 %) - according to ISO/IEC Guide 98-3:2008-09 "Guide to the expression of uncertainty in measurement".
PHASCOPE® is a registered trade mark of Helmut Fischer GmbH Institut für Elektronik und Messtechnik in Germany and other countries.
MSExcelTM is a registered trade mark of Microsoft Corporation, USA.
22112019
This manual suits for next models
2
Table of contents
Popular Measuring Instrument manuals by other brands

Victron energy
Victron energy BMV-700 Quick installation guide
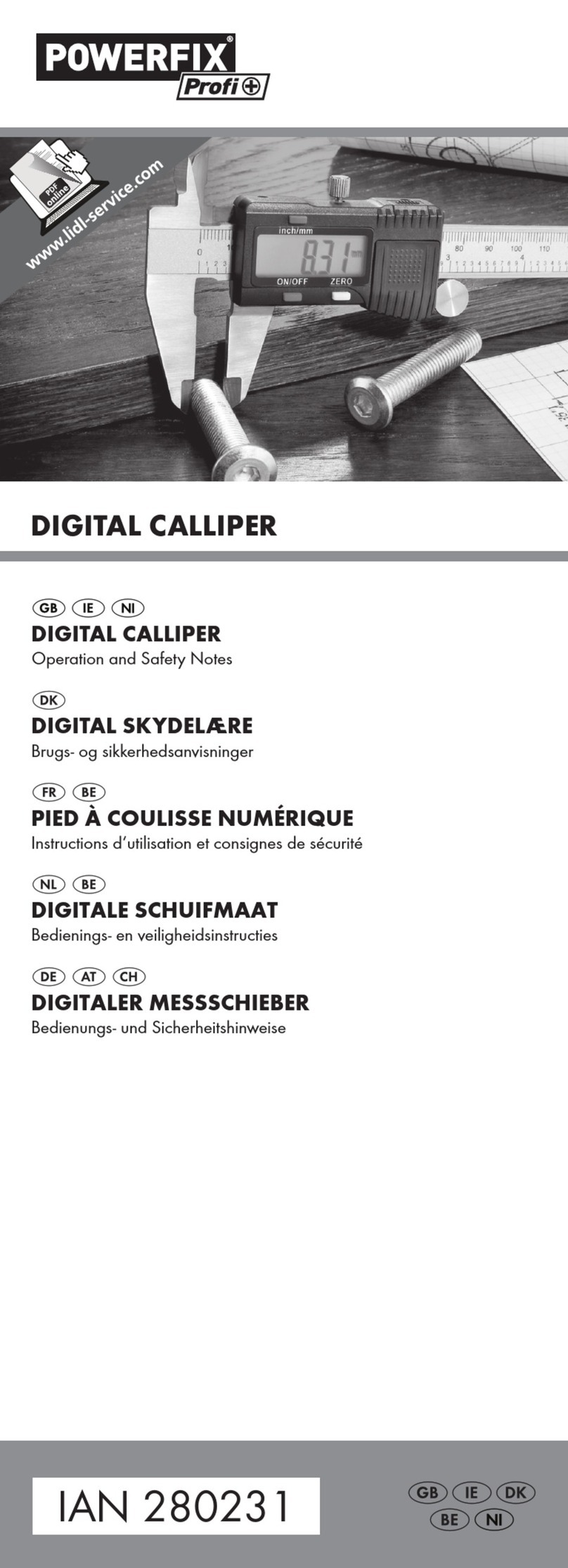
Powerfix Profi
Powerfix Profi 280231 Operation and safety notes

HP
HP 436A Operating and service manual

Apacer Technology
Apacer Technology AL100 user manual
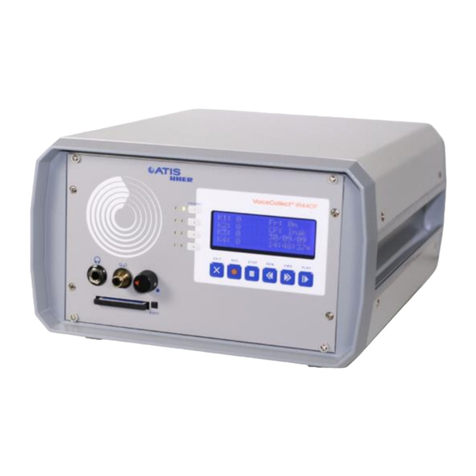
VoiceCollect
VoiceCollect IR44CF-II Service maintenance manual
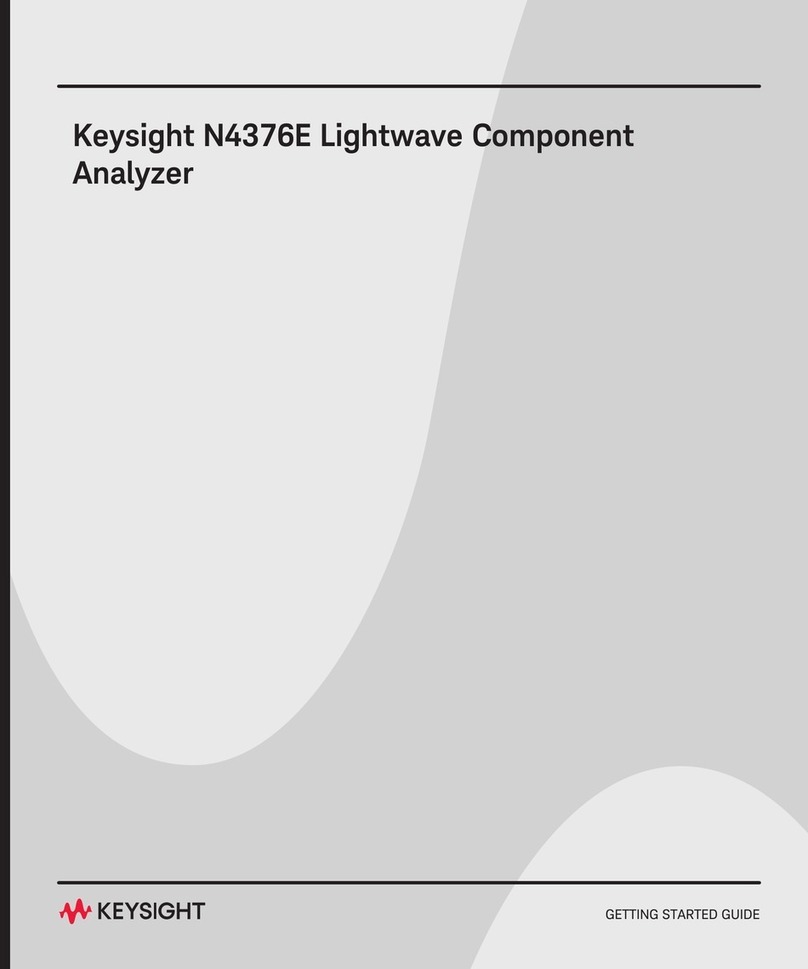
Keysight
Keysight N4376E Getting started guide