AXOR Industries MACK NANO User manual


AXOR Industries Service Manual NanoMack®ver.1 rev.02/'17
2
All rights reserved. Reproduction in whole or in part is prohibited without prior
written consent of the copyright owner. All specications are subject to change
without prior notication.
This manual has been carefully checked. However, Axor does not assume liability
for errors or inaccuracies.
Release Notes
ver.1 rev. 03/'16 First preliminary edition.
ver.1 rev. 07/'16
Notes about supply.
Nota about ground connection.
Notes about DC motor settings.
Corrections.
ver.1 rev. 12/'16
Added steeper motor connections.
Added senting and conguration on encoders.
Chapter 1, 2, 4, 5 update.
Corrections.
ver.1 rev. 02/'17 Corrections.
THIS MANUAL CONTAINS A DESCRIPTION OF NANO MACK®
AND A GUIDELINES FOR THE DRIVE'S INSTALLATION.
USING THE DRIVE INCORRECTLY CAN INJURE PEOPLE OR MANAGE THINGS.
FULLY RESPECT THE TECHNICAL DATA AND INDICATIONS ON CONNECTION
CONDITIONS.

AXOR Industries Service Manual NanoMack®ver.1 rev.02/'17
3
Summary
1) Description
1.1 Description 6
1.2 General view NanoMack 8
1.3 Technical Data 10
1.4 Product plate and Ordering Code 11
2) Installation
2.1 General Advices 14
2.2 Environmental conditions 16
2.3 Cables 17
2.4 Note about cable shielding 19
2.5 Base installation procedure 20
2.6 Supply connections 21
2.7 Motor power connection 23
2.8 Digital inputs connection 25
2.9 Digital outputs connections 26
2.10 Analog inputs connections 27
2.11 Clock/Dir inputs connections 28
2.12 Feedback signals connections 29
2.13 CanBus or RS485 connections 32
2.14 Nano Mack Led 33
3) Diagnostic
3.1 Alarms 35
4) Operative Modes
4.1 Operative Modes 39
4.2 Digital Speed 40
4.3 Analog Speed 41
4.4 Digital Torque 43
4.5 Analog Torque 44
4.6 Gearing 45
4.7 Clock/Dir Command 46
4.8 Homing - Procedures 49
4.9 Homing - Settings 53
4.10 Homing - Example 57
4.11 CanBus - Settings 59
4.12 Analog to Position Control 60

AXOR Industries Service Manual NanoMack®ver.1 rev.02/'17
4
Summary
3) SpeederOne Interface
5.1 Speeder One Interface 63
5.2 Nano Mack main menu 65
5.3 Nano Mack Operative Modes 69
5.4 Nano Mack Status 70
5.5 Speed window 71
5.6 Current window 72
5.7 Motor window 73
5.8 Analog I/O window 78
5.9 Digital I/0 window 79
5.10 Position window 82
5.11 Homing window 83
5.12 Oscilloscope 85
Conformity 92

5
AXOR Industries Service Manual NanoMack®ver.1 rev.02/'17
Chapter 1
Description
1.1 Description 6
1.2 General view NanoMack 8
1.3 Technical Data 10
1.4 Product plate and Ordering Code 11
1) Description

6
AXOR Industries Service Manual NanoMack®ver.1 rev.02/'17
1.1 Description
OPERATIVE MODES
DIGITAL
SPEED CONTROL
It is speed piloting utilising a digital reference. standard
ANALOG
SPEED CONTROL
It is speed piloting utilising an analogue reference
(differential or common mode). standard
DIGITAL TORQUE
CONTROL
It is torque piloting utilising a digital reference. standard
ANALOG TORQUE
CONTROL
It is torque piloting utilising an analogue reference. standard
POSITION MODE
Available soon.
The positioner can be managed via hardware (by using the
digital inputs) or via USB (by using the Axor's Speeder
One interface).
It supports 32 programmable position proles; a single task
or a sequence of tasks are permitted.
The Homing Procedure is implemented. It uses the signal
coming from the homing sensor and eventually the zero
signal of the encoder.
standard
GEARING
It is possible to pilot the drive with the quadrature signals
of an emulated encoder from a Master drive or with the
quadrature signals of an incremental encoder from a Master
motor.
standard
PULSE/DIRECTION
It is possible to connect the drive to a motor piloting it
with the CLOCK and DIR signals: the DIR signal denes
the clockwise/counter clockwise rotation, while the CLOCK
signal denes the speed rotation.
standard
CW/CCW
It is possible to connect the drive to a motor piloting it with
the CLOCK and DIR signals: if pulses arrive at the CLOCK
input, the motor rotates clockwise (CW); while if pulses
arrive at the DIR input, the motor rotates counter clockwise
(CCW).
standard
CANBUS
It can be congured and controlled using CanBus. It
supports the following Can Open protocols:
• part of the DS301-V4.02
• part of the DSP402-V2.0
standard
SQUARE WAVE The motor is piloted with a “square wave” signal.
This is useful for adjustments of the speed loop. standard
ANALOG TO
POSITION
The motor moves between two programmable positions
corrisponding the min and max voltages at the dedicated
pins.
standard
RS485 MODBUS-RTU It allows to communicate and control the drive by using the
RS485 interface. optional
The NANO MACK
®
is a very compact digital drive capable of piloting AC brushless motors, DC brushed
motors and stepper motors, up to 400W. It can be supplied by a DC voltage equal to 12÷48Vdc.

7
AXOR Industries Service Manual NanoMack®ver.1 rev.02/'17
1.1 Description
STANDARD AND ADDITIONAL FEATURES
SPEEDER ONE
SOFTWARE
INTERFACE
The Axor Speeder One interface allows user to set and
manage all Nano Mack®’s parameters, just using an USB
single access cable.
standard
SAFETY
SAFETY
The converter is protected from short circuitry, the Max/Min
Voltage, over-temperature of the converter & motor, I2t of
drive, I2t of motor, etc.
standard
DIGITAL INPUTS/ OUTPUTS
4 DIGITAL INPUTS
(D.IN1÷D.IN4)
PROGRAMMABLE
The digital inputs are programmable with the option present
in chapter 5. standard
2 DIGITAL or
ANALOG OUTPUTS
PROGRAMMABLE
The digital outputs are programmable with the option present
in chapter 5. standard
1 ANALOG COMMON
MODE INPUT
(An.Ref.Torque)
It is used for controlling the current from the drive
(±10V - 12bit). standard
1 ANALOG
DIFFERENTIAL
INPUT
(+/- An.Diff.Ref.)
It is used for piloting the drive with an analogue speed
reference from an external controller (±10V - 12bit). standard
FEEDBACK
INCREMENTAL
ENCODER
Incremental encoder (A, B, Z). standard for motors:
BL, DC, SM
COMMUTATION
ENCODER
Commutation encoder (A, B, Z) + hall (U,
V, W). standard for motor: BL
SENSORLESS standard for motors: BL, SM
ARMATURE standard for motor: DC
HALL Only hall (U, V, W).
Available soon.
standard for motor: BL, DC
TACHOGENERATOR optional for motor: DC
BL: Brushless motor
DC: Brushed motor
SM: Stepper motor

8
AXOR Industries Service Manual NanoMack®ver.1 rev.02/'17
1.2 General view NanoMack
23
43
21.5
USB
Ø 4
123 4 5 6 2 8
1 17
1 7
RUN
ALARM
READY
(
flash
)
I2 t
(
flash
)
LED
2 18
6574
Dimensions in mm
BRUSHLESS
&
D.C. MOTORS
NANO
F
EEDBACK
2 4 6 8
1357
+
-
3 4 5 6
MOTORPWR
J2
M1
CONTROL 1
2
17
18
J1
USB
1 2
MKN48/8-B-X-CB-Sxxx
X000/X000
00000000 00000000
M1 J2
J1

9
AXOR Industries Service Manual NanoMack®ver.1 rev.02/'17
1.2 General view NanoMack
3
BL
BRUSHLESS
DC
BRUSHED
SM
STEPPER
CONTROL M O D E
FEEDB A C K
MOTO R
MOTO R
MOTO R

10
AXOR Industries Service Manual NanoMack®ver.1 rev.02/'17
1.3 Technical Data
NanoMack®Technical Data
Power Supply Vdc 12 ÷ 48 Vdc ( 9
Vdc min - 65 Vdc max )
Backup Logic
Supply Vdc 12 ÷ 24 Vdc - 100mAdc max ( 9
Vdc min - 30 Vdc max )
Size MKN 48
1/2 5/10 8/16 10/20
Rated Current Arms 1 5 8 10
Peak current x 3'' Arms 2 10 16 20
PWM output
frequency kHz 8 default (16 and 24 with derating )
External Fuse Protection
Power in Line F1 10 A (T-type = time-lag)
Ambient condition
during operation
Temperature
From 0°C to +40°C (without condensation)[Class
3K3 according to EN 60721-3-3].
From +40°C to +55°C the drive must be derated
2.5%/°C in reference to nominal and peak current.
Humidity From 10% to 85% (without condensation) [Class 3K3
according to EN 60721-3-3].
Vibration Class 3M1 according to EN 60721-3-3.
Ambient condition
during transport
Temperature From -25°C to +70°C [Class 2K3 according to EN
60721-3-2].
Humidity Relative humidity max 85% (without condensation)
[Class 2K3 according to EN 60721-3-2].
Vibration Class 2M1 according to EN 60721-3-2.
Ambient condition
during storage
Temperature From -20°C to +55°C [Class 1K3 according to EN
60721-3-1].
Humidity Relative humidity from 5% to 85% (without
condensation) [Class 1K3 according to EN 60721-3-1].
Vibration Class 1M1 according to EN 60721-3-1.
Control signals
Digital inputs +24Vdc - 7mA (PLC compatible)
Digital/Analog outputs +24Vdc - 20mA (PLC compatible)
Clock/Dir digital inputs +5 - max. frequency 500kHz
+24V - max. frequency 100kHz
Differential analog inputs
(+/- An.Diff.Ref.) ±10V (±5%) - 12bit
Common mode analog input
(An.Ref.Torque) ±10V (±5%) - 12bit
Mechanical specications
Drive assembly Panel mount
External dimensions mm 74 x 43 x 23
Weight g60

11
AXOR Industries Service Manual NanoMack®ver.1 rev.02/'17
1.4 Product plate and Ordering Code
On the side of each NANO MACK®there is a product plate like the follow:
Ordering code:
DC
STEPPER
BRUSHLESS
+
M
-
M
/
/
_
_
B
A
A
B
V
W
U
/
M1 MOTOR
3
4
5
6
BRUSHLESS &D.C. MOTORS
BACKUP
:
P
OWER
:
12÷48VDC
12÷24V
DC
NANO
F
EEDBACK
2468
1 3 5 7
+
-
3 4 5 6
MOTORPWR
J2
M1
CONTROL 1
2
17
18
J1
USB
1 2
MKN48/8-B-X-CB-Sxxx
X000/X000
00000000 00000000
MKN 48 / 5 - B - X - CB - Sxxx
SIZE
DRIVE LINE
Feedback:
X= Standard
Specic number presence (opt):
S xxx
001÷999=specic number
Motor type:
B= Standard:
BL Brushless
DC Brushed
S= Optional:
SM Stepper
BL Brushless
DC Brushed
MODEL
Control Mode:
CB = CanBus (std)
MB = RS485 Mod Bus-RTU (opt)

12
AXOR Industries Service Manual NanoMack®ver.1 rev.02/'17

13
AXOR Industries Service Manual NanoMack®ver.1 rev.02/'17
Chapter 2
Installation
2) Installation
2.1 General Advices 14
2.2 Environmental conditions 16
2.3 Cables 17
2.4 Note about cable shielding 19
2.5 Base installation procedure 20
2.6 Supply connections 21
2.7 Motor power connection 23
2.8 Digital inputs connection 25
2.9 Digital outputs connections 26
2.10 Analog inputs connections 27
2.11 Clock/Dir inputs connections 28
2.12 Feedback signals connections 29
2.13 CanBus or RS485 connections 32
2.14 Nano Mack Led 33

14
AXOR Industries Service Manual NanoMack®ver.1 rev.02/'17
2.1 General Advices
During the transport of the device respect the following indications:
• The transport must be made by qualied personnel.
• The temperature range must be between -25°C and +55°C [class 2K3 according to EN 60721-
3-2].
• The max. humidity must be 85% (without condensation) [class 2K3 according to EN 60721-3-
2].
• The system contains elements which are sensitive to electrostatic discharges. These elements can
be damaged by careless manipulation.
Discharge static electricity from your body before touching the converter.
Avoid contact with material that insulates well (synthetic bres, lms of plastic material and so
forth).
• We suggest to check the device condition at its arrival to survey eventual damages.
• Avoid shocks (the Nano Mack
®
has class 2M1 is according to EN 60721-3-2).
Transport
The unused drives must be storage in an environment having the following characteristics:
• temperature from -20°C to +55°C;
• max. relative humidity 85% (without condensation);
• max. time with the drive powered off (without supply connections): 1 YEAR.
After this time, before enable the drive, it is necessary activate the capacitors following this procedure:
remove all electrical connections, then supply the input terminals of the supply with the dc voltage for
30 minutes.
In order to avoid this procedure, we suggest to power on the drive with its rated voltage for 30 minutes,
before the max. time is reached.
Storage
We recommend an accurate maintenance plane, according to using norms (for example CEI EN
60439-1).
In particular, we recommend the following:
• if the casing is dirty, clean it with isopropanol or similar;
• if the drive is dirty: the cleaning is reserved to the producer;
• monthly clean drives from external dirt and dust deposits.
ADOPT ALL NECESSARY MEASURE TO AVOID DUST DEPOSITS INSIDE THE DRIVE.
Maintenance
The disposal should be carried out by a certied company.
Disposal

15
AXOR Industries Service Manual NanoMack®ver.1 rev.02/'17
2.1 General Advices
• This manual is exclusively addressed to technical personnel with the following require-
ments:
- Technician with knowledge on movimentation of elements sensitive to electrostatic
discharges (for the transport).
- Technician with appropriate technical training and with vast knowledge on electrotech-
nics/drive technical eld (for the installation and operation of servodrives).
Using the drive incorrectly can injure people or damage things. Fully respect the technical
data and indications on connection conditions.
• As well as the points described in this manual, current regulations regarding safety and accident
prevention must be followed in order to prevent accidents and residual risks.
• The user must analyse possible machine risks and take the necessary measures to avoid injuries to
people and damage to things because of unpredictable movements.
• The converters contains elements which are sensitive to electrostatic discharges. These elements can
be damaged by careless manipulation.
Discharge static electricity from your body before touching the converter.
Avoid contact with material that insulates well (synthetic bres, lms of plastic material and so
forth).
• During operation, the converter surface can become hot. Protect the user from accidental contact
and keep the indicated distances from all objects.
• The command and power connections can still hold current even when the motor has stopped.
•The Nano Mack®is equipped with electronic protections that deactivate it in case of irregularities.
The motor, as a result, is not controlled and can stop or go into neutral (for a time determined by the
type of system).
•During installation, avoid letting any residue with metallic components fall inside the drive.
•Protect the Nano Mack®from excessive mechanical vibrations in the electrical box.
Security standard

16
AXOR Industries Service Manual NanoMack®ver.1 rev.02/'17
During the storage and the installation respect the followings environmental conditions:
2.2 Environmental conditions
Environmental conditions
Storage temperature From -20°C to +55°C
Working environmental temperature
From 0°C to +40° C (no derating).
From +45°C to +55°C the drive must be derated
2.5%/°C in reference to nominal and peak current.
Humidity From 10% to 85% (without condensation)
Altitude
Up to 1000m without restriction.
From 1000 to 2500m of altitude the converter must be
derated in the output current of 1.5% every 100m.
Enclosure protection IP20
Pollution level
LEVEL 2 (Norm EN60204/EN50178)
The drives are designed to be utilized in an electrical
box protected against the inltration of polluting agents
such as water, oil, conductive dust and others.
Notes:
• The electrical box must have suitably filtered air vents.
Leave the necessary space both above and below the drives.
You must pay particular attention to the sizing of the (eventual) cooling system, remember-
ing the electrical box size and power internal dissipation of the drive(s).
Monthly control the functioning of the extracted air filter and cooling air filter of the electrical cabinet,
in particular control the functioning and cleaning of fans and filters.
• Monthly check the internal cleaning of the electrical panel and define an accurate cleanig plane,
according to using norms (for example CEI EN 60439-1).
• Monthly check drive case for excess dust or dirt, that could interfere with the correct dissipation of
the drive; in case of malfunctions contact Axor.

17
AXOR Industries Service Manual NanoMack®ver.1 rev.02/'17
The following table illustrates the technical characteristics of all cables:
Cables (as norm EN60204)
Type Section Notes
for the
Main Supply 1.5mm2/15AWG
for the
Backup
Supply
0.10-0.33 mm2/
26-22AWG
for the
Motor's Power 1.5mm2/15AWG
It must be shielded.
It must have a capacity of ≤150pF/m.
In the conguration without lter, the cable can
reach a maximum length of 10m.
for the
Control signals
and
I/O signals
from PLC/CNC
0.10-0.33 mm2/
26-22AWG See "Note about cable shielding"
for the
Encoder signals
(commutation)
0.10-0.33 mm2/
26-22AWG
It must be shielded.
It must have a capacity less than 120pF/m.
for the
Encoder signals
(serial)
0.10-0.33 mm2/
26-22AWG
Capacitance 800 ÷ 1000Hz : ≤90pF/m
Characteristic Impedance at 10MHz : 110 ± 10 Ω
for the
CanBus
communication
0.25mm2/0.34mm2
Cable capacitance: max 60 nF/km.
Impedance characteristics : 100...120Ω.
Lead resistance (loop): 159,8 Ω/km.
The length depends upon the transmission speed:
• 1000kbit/s 20m max;
• 500kbit/s 70m max;
• 250kbit/s 115m max.
for the system
setting
via SpeederOne
interface
-Mini USB B 5P to USB A type male.
The cable length must be 3m max.
Notes:
• Avoid crossing, overlapping and twisting cables together. If it is absolutely necessary to cross them,
do so at 90°.
• Use only copper conductors for cabling.
2.3 Cables

18
AXOR Industries Service Manual NanoMack®ver.1 rev.02/'17
2.3 Cables
Following is the crimping process:
d... wire cross section
D... cross section of insulation
A... stripping length
Connector Article Code Wire cross
section
Max cross
insulation
section D
A length
J1
crimp contact:
SPHD-001T-P05
housing connector:
PHDR-18VS
26...22 AWG
0,13...0,33 mm21,5 mm ~ 1,5...2 mm
J2
crimp contact:
SPHD-001T-P05
housing connector:
PHDR-08VS
26...22 AWG
0,13...0,33 mm21,5 mm ~ 1,5...2 mm
Crimp tool: WC-240

19
AXOR Industries Service Manual NanoMack®ver.1 rev.02/'17
Symbol Description
It suggests a conductive connection as much as possible to the chassis, or the heat-
sink, or the mounting panel of the electrical box.
It refers to the earth connection.
It refers to the connection of the shield to the connector's metal ring.
2.4 Note about cable shielding
The conductor of the analogic signal must be twisted and shielded, and the shield must be connected to
ground remove the outside sheath and afx the shield to the zinced pannel by using an u-clamp.
Control signal cables
Motor cables
The shield of the motor cable (power and signal cables) are connected as follows:
• drive side (0,2 m) remove the outside sheath and x shield to the zinced pannel, by using a
u-clamp:
To reduce the capacitive and inductive coupling, these cables must be run keeping a distance of more
than 30cm from the power cables (10 cm if they are shielded).
If it is absolutely necessary to cross the control cables with the I/O's, do so at 90°, in order to reduce
the effect of the magnetic elds.
The table below illustrates the symbols used in the following pages:
10Max 0,2m

20
AXOR Industries Service Manual NanoMack®ver.1 rev.02/'17
This procedure must be done only by qualified personel which are familiar with drives. If
you need more information contact Axor.
a) Power off all the supplies of the electrical box.
b) Verify:
the drive-motor coupling the stall current (Io) of the motor should be equal to/or greater
than the nominal output current of the drive;
the positioning of the drive into the electrical box;
the pollution level and the ventilation;
the connection to earth of the electrical box where the drive is installed .
c) Execute the wiring following this order, avoiding that wiring's pieces, cables, wires, screws, conduc-
tive objects, etc. do not enter into the drive through its slits:
1- Connect the cables for the motor's power (U, V, W).
2- Connect the external shield of the motor's cable: it must be shielded utilising a u-clamp to
the zinced panel of the electrical box.
3- Connect the AGND pin of J1 connector (pin 2 or pin 12) to ground bar of the electrical box.
4- Connect the chassis of the drive to the ground bar of the electrical box by the zinced pannel
5- Connect the motor's feedback cable.
6- Connect the power supply cable (+AT/-AT) in the Nano Mack®.
Always insert a fuse F1 (see chapter 1.3 "Technical Data").
7- Connect the backup supply cable in the Nano Mack®.
8- Connect the PC to the Nano Mack
®
utilising an USB cable. The cable length must be 3m max.
9- Supply the drive with the backup supply and then the power supply.
10- Open the Speeder One interface.
11- Execute the tests on the drive and the motor.
2.5 Base installation procedure
Other manuals for MACK NANO
1
Table of contents
Other AXOR Industries Servo Drive manuals
Popular Servo Drive manuals by other brands
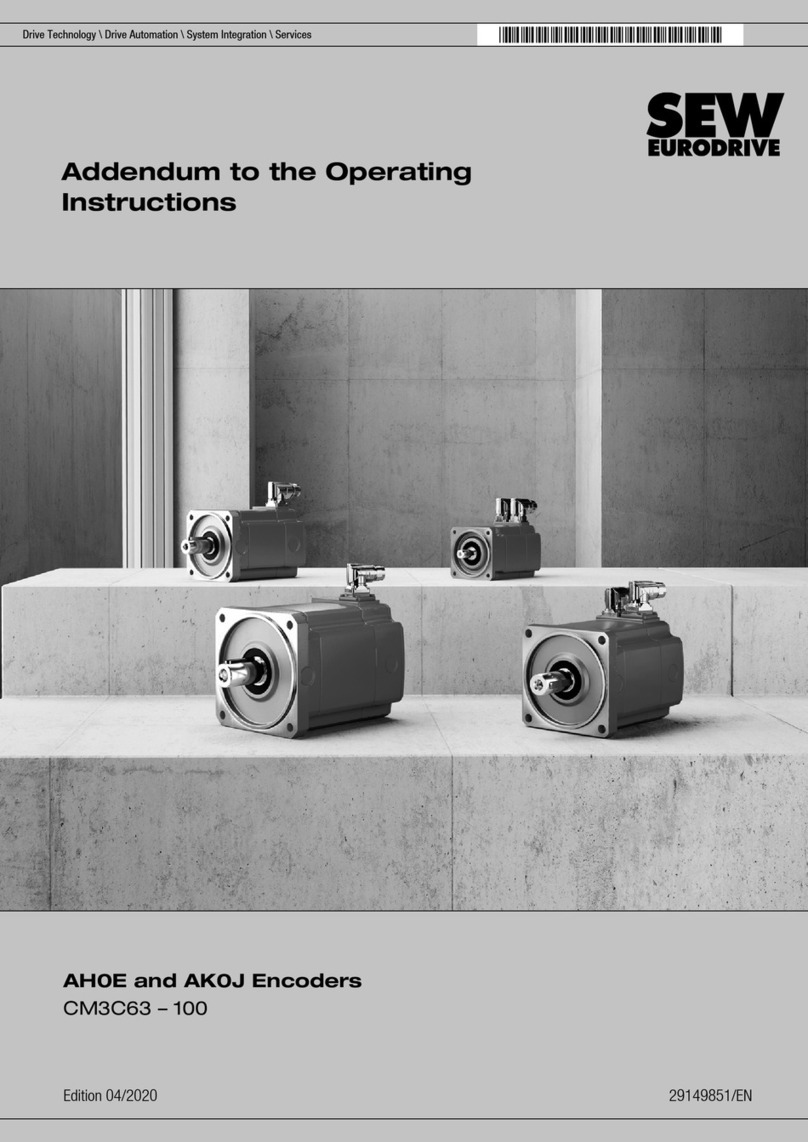
SEW-Eurodrive
SEW-Eurodrive CM3C Series Addendum to operating manual
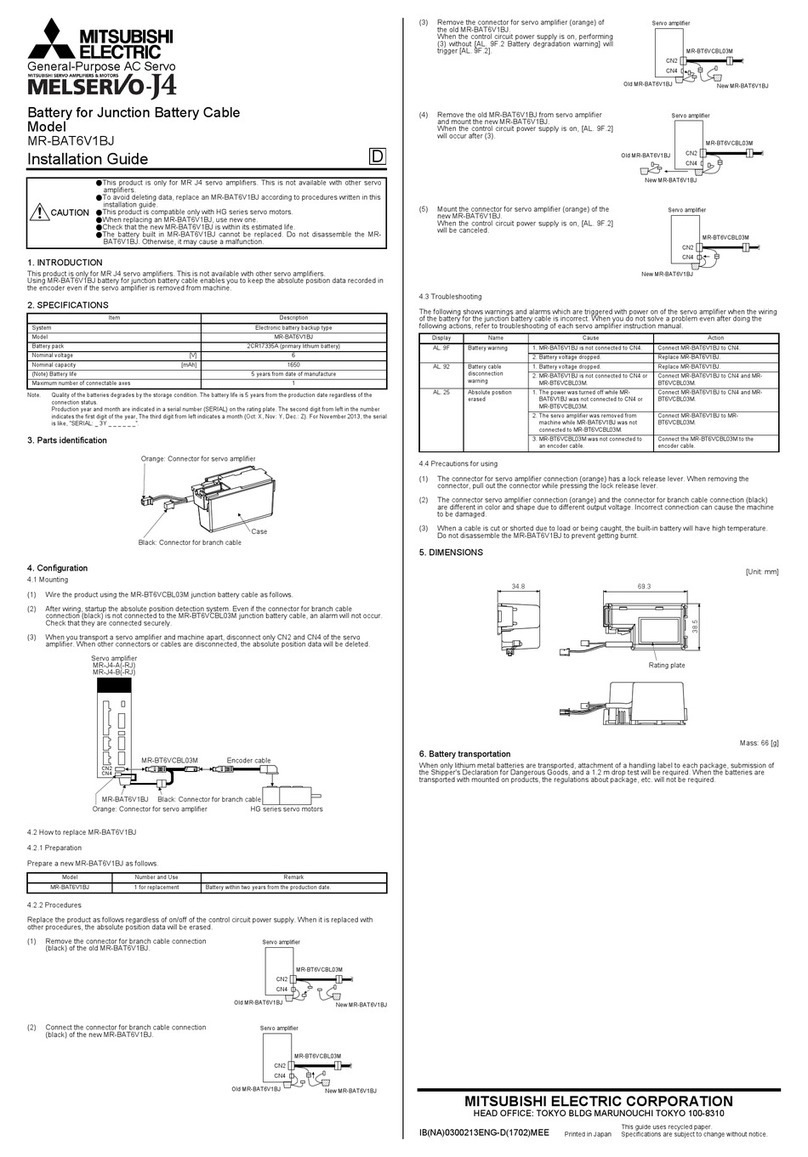
Mitsubishi Electric
Mitsubishi Electric MELSERVO-J4 series installation guide
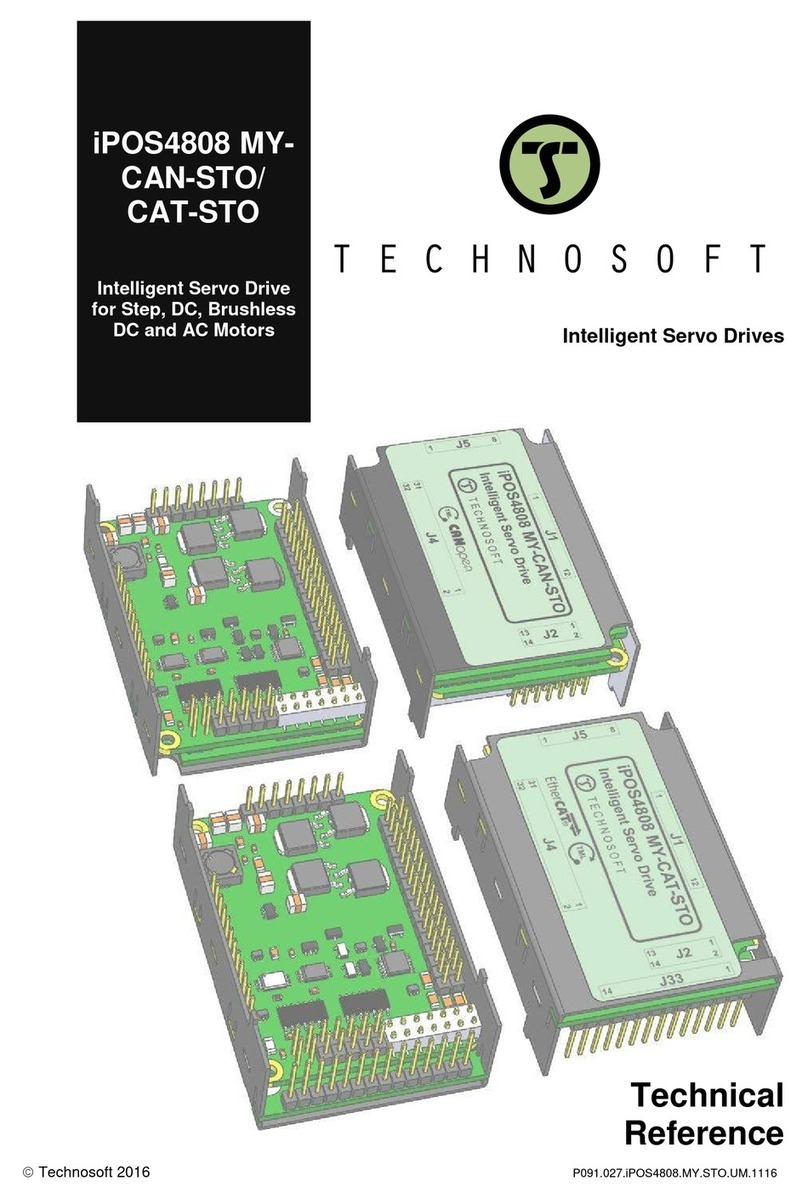
Technosoft
Technosoft iPOS4808 MYCAN-STO Technical reference
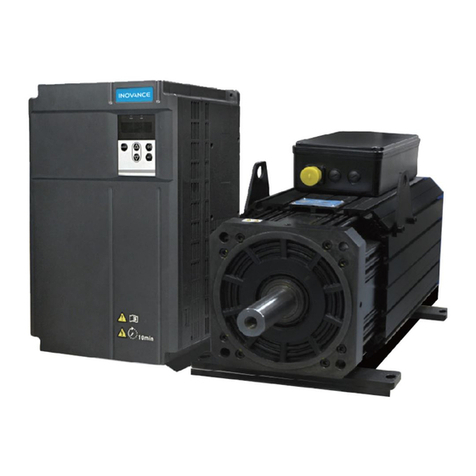
Inovance
Inovance IS650P Series user guide
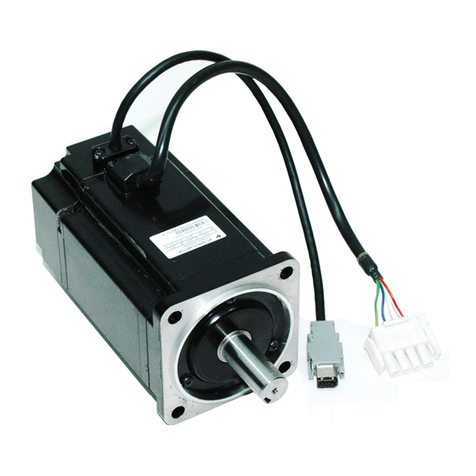
YASKAWA
YASKAWA SGM H Series user manual
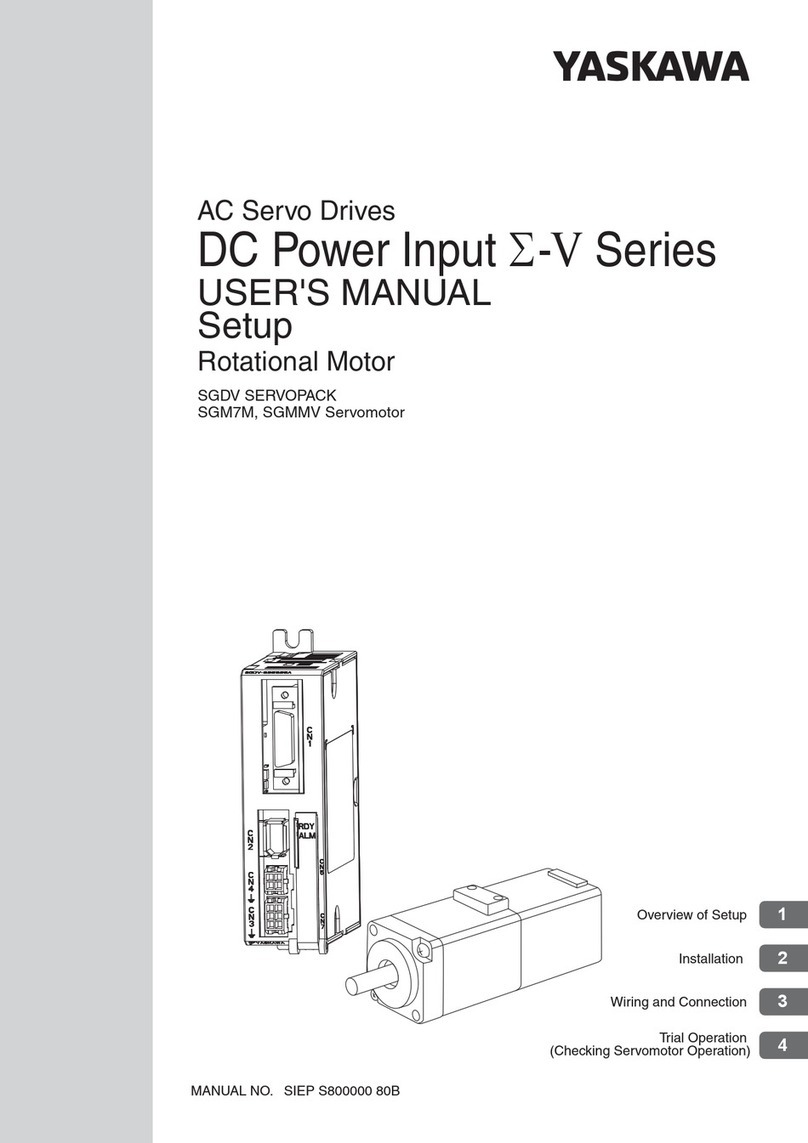
YASKAWA
YASKAWA E-V Series user manual