Beck 901 EX Series User manual

Beck GmbH
Druckkontrolltechnik
Ferdinand-Steinbeis-Straße 4
71144 Steinenbronn
Operating instructions – Pressure Switch – Model - 901...EX Rev.10 Page 1 of 18
Ident:
0607017-BA-901-R10-2017_englisch_Druckversion.doc
Operating Instructions
Pressure switch
Model 901....EX

General instructions
Safety instructions
Beck GmbH
Druckkontrolltechnik
Ferdinand-Steinbeis-Straße 4
71144 Steinenbronn
Telephone
Telefax
E-Mail
Internet
VAT-no.
+49 7157 52 87-0
+49 7157 52 87-83
http://www.beck-sensors.com
DE162391354
Bank Accounts
Kreissparkasse Esslingen-Nürtingen (BLZ 611 500 20) 57 011 970
S.W.I.F.T. ESSLDE66 IBAN: DE33 6115 0020 0057 0119 70
Commerzbank Stuttgart (BLZ 600 400 71) 876 179 300
S.W.I.F.T. COBADEFF600 IBAN: DE70 6004 0071 0876 1793 00
Landesbank Baden-Württemberg (BLZ 600 501 01) 2 214 306
S.W.I.F.T. SOLADEST IBAN: DE36 6005 0101 0002 2143 06
UniCredit Bank - HypoVereinsbank Stuttgart (BLZ 600 202 90) 388 773 332
S.W.I.F.T. HYVEDEMM473 IBAN: DE66 6002 0290 0388 7733 32
Location: Steinenbronn
Amtsgericht Böblingen HRB 6050
Managing Directors: Rainer Beck,
Hans-Peter Funk, Dr. Ernst Thielicke
Operating instructions – Pressure Switch – Model - 901...EX Rev.10 Page 2 of 18
1
General instructions.............................................................................................................3
1.1
Safety instructions............................................................................................................3
1.1.1
General safety instructions ........................................................................................................ 3
1.1.2
Safety instructions for potentially explosive areas ..................................................................... 4
1.1.3
Notes on environmental protection............................................................................................ 4
2
Correct purpose of use ........................................................................................................5
2.1
Application area................................................................................................................5
2.2
CE conformity...................................................................................................................5
3
Storage and transportation..................................................................................................6
3.1
Packaging ........................................................................................................................6
3.2
Storage and transportation conditions..............................................................................6
4
Installation.............................................................................................................................6
4.1
Installation........................................................................................................................7
4.2
Connection.......................................................................................................................7
5
Start-up..................................................................................................................................9
5.1
Parameterisation..............................................................................................................9
6
Maintenance / service...........................................................................................................9
6.1
Time intervals...................................................................................................................9
6.2
Troubleshooting..............................................................................................................10
7
Repairs ................................................................................................................................10
8
Dismantling.........................................................................................................................10
8.1
Disposal .........................................................................................................................10
9
Appendix .............................................................................................................................11
9.1
Technical data and dimensioned drawing.......................................................................11
9.1.1
Pressure switch 901.................................................................................................................12
9.1.2
Pressure switch 901 Prescal
®
.................................................................................................. 13
9.2
Dimensioned drawings and accessories.........................................................................14
9.2.1
Pressure switch 901.................................................................................................................14
9.2.2
Pressure switch 901 Prescal
®
.................................................................................................. 15
9.3
Declaration of Conformity...............................................................................................16
9.4
EC design test certification.............................................................................................17
9.5
Proof of compliance with explosion protection regulations..............................................18

General instructions
Safety instructions
Beck GmbH
Druckkontrolltechnik
Ferdinand-Steinbeis-Straße 4
71144 Steinenbronn
Operating instructions – Pressure Switch – Model - 901...EX Rev.10 Page 3 of 18
1 General instructions
These operating instructions contain all of the information that is required for an efficient start-up
and safe operation of Model 901….EX pressure switches.
Please read these operating instructions before carrying out installations, start-ups,
maintenance and repairs.
Please ensure that these operating instructions are available at all times.
Please follow the applicable instructions and safety regulations.
All of the work that is described in these operating instructions must be carried out by quali-
fied and authorised experts.
In order to avoid problems, the prescribed maintenance must be carried out at regular in-
tervals by appropriately trained personnel.
Symbols used
The meanings of the symbols that are used are as follows:
Useful, important additional information.
Dangers and safety instructions. Important – please read!
Failure to comply with these instructions can have a detrimental
effect on persons and the operation of the equipment.
Important instructions for use in potentially explosive areas.
Danger – please read!
1.1 Safety instructions
1.1.1 General safety instructions
Please follow the applicable
Instructions and system-specific regulations (e.g. installation
standards etc.)
Safety regulations and accident prevention regulations
All work must be carried out by authorised and qualified personnel. These qualifications
and authorisations include:
Training, experience and knowledge of the regulations, standards
Only personnel with appropriate product knowledge must carry out start-ups and
maintenance
All repairs must be carried out by personnel who have been authorised to do so by
the manufacturer
Only original parts must be used
Ignoring these operating instructions and making modifications to the equipment are not
permitted and can lead to hazardous situations

General instructions
Safety instructions
Beck GmbH
Druckkontrolltechnik
Ferdinand-Steinbeis-Straße 4
71144 Steinenbronn
Operating instructions – Pressure Switch – Model - 901...EX Rev.10 Page 4 of 18
1.1.2 Safety instructions for potentially explosive areas
The 901..EX pressure switch is suitable for use in areas where there
is a risk of gas or dust explosion
Please follow the applicable
Instructions and system-specific regulations
The labelling of the product must point out that important explosion protection characteris-
tics must be adhered to during use.
G = Gas; D = Dust
Device category 1, 2, 3 or Equipment Protection Level EPL in the 3 zonal areas
Gas parameters: temperature class (T1…T6), explosion group (A, B, C)
Dust parameters: Explosion group (IIIA, B: non-conductive; IIIC: conductive);
Surface temperature, glow and ignition temperature
When work is being performed such as installation, making electrical connections, making
repairs or opening the housing, it must be ensured that
no potentially explosive atmosphere is present
no electrical voltage is present
unintentional activation is ruled out
Dust deposits must be avoided (installation location, protection, cleaning etc.) in order to
prevent dangerous surface temperature increases
For the installation procedure it is necessary to take care that no electrostatic charging will
be done (no high volume flow, cleaning only with damp cloth,…)
It must be ensured that all technical and organisational protective measures are complied
with and that the operation and effectiveness thereof is checked
No modifications must be made to the equipment, since they may lead to a risk of explo-
sion (ignition)
The specifications of the EC design certificate are binding and must be complied with
If the number of the EC design certificate is followed by an “X”, special conditions or devia-
tions from the standard conditions exist
Installation, start-ups and repeated testing may only be carried out by appropriately quali-
fied personnel
The operator must issue a release for work before any activity (installation etc.) is carried
out in potentially explosive areas.
1.1.3 Notes on environmental protection
Please help to protect the environment. Please pay attention to the environmental notes in these
operating instructions:
Chapter 3.1 “Storage“: Handling of packaging materials
Chapter 8.1 “Disposal“: with regard to the product and its components

Correct purpose of use
Application area
Beck GmbH
Druckkontrolltechnik
Ferdinand-Steinbeis-Straße 4
71144 Steinenbronn
Operating instructions – Pressure Switch – Model - 901...EX Rev.10 Page 5 of 18
2 Correct purpose of use
2.1 Application area
Purpose of use
The adjustable pressure switches have the following main purpose
Factory-set pressure switch monitoring overpressure, vacuum or differential pres-
sure of liquid and gaseous – also aggressive – media
Pressure setting and switching differential are factory-set by the Manufacturer
The pressure switch 901 Prescal© uses a scaled adjustment knob to enable the ad-
justment of trip and reset pressure without the use of a screwdriver.
The media that are being monitored occur in the following different phases
Gaseous (main application)
Potentially explosive gasses and dust (natural gas, bio-gas, solvents etc.)
Liquid
Flammable liquids (petrol, solvent etc.)
Use in zones in potentially explosive areas
Pressure switches are used to monitor the pressure difference in
areas of closed systems where there is a risk of gas explosion.
The device may be used in areas where there is a risk of gas or dust explosion
Two separate zonal areas can be connected via pressure connections P1 and P2 (are-
as 1 and 2)
Zone 1,2 or zone 21,22 may apply to the pressure connections (areas 1 and 2)
The surroundings (area 3) can be zone 1,2 or zone 21,22
2.2 CE conformity
The product complies with the following European directives:
Explosion protection directive
RoHS directive
Other information and verification can be found in the
Conformity declaration (see Chapter 9.3)
Area-1 Surrounding
Area-2 Equipment category
Equipment Protection
Level
Zone 0 Zone 1,2 1/2 G
Ga/Gb
Zone 21,22 Zone 21,22 2D
Db
Zone 1,2
Zone 1,2
2G
Gb
Zone 21,22 Zone 21,22 2D
Db
Surroun-
ding
Area-1
Area -2

Storage and transportation
Packaging
Beck GmbH
Druckkontrolltechnik
Ferdinand-Steinbeis-Straße 4
71144 Steinenbronn
Operating instructions – Pressure Switch – Model - 901...EX Rev.10 Page 6 of 18
3 Storage and transportation
3.1 Packaging
The equipment is protected by packaging. The packaging is environmentally compatible and recy-
clable. The following main materials are used:
Cardboard
PE foam or PE film
Please use appropriate recycling companies to dispose of the packaging
3.2 Storage and transportation conditions
The following points must be observed in order to prevent damage:
Avoid severe mechanical stress caused by throwing, stacking and dropping.
Keep out of wet and rainy environments
Do not subject to direct sunlight for long periods
The storage temperature must not be lower than -40 °C or higher than +85 °C
4 Installation
The following checks must be performed prior to installing the equipment:
The equipment must not show signs of damage or obvious modifications
The IP protection class of the equipment must correspond with the usage
and environmental conditions
An operator zone definition must be available
Check whether the equipment category corresponds with the specified zones
With intrinsically safe systems (“i") the “associated operating materials" (barrier) must al-
ways be installed outside the potentially explosive area.
The labelling of the product must point out that important explosion protection characteris-
tics must be complied with during use.
G = Gas, D= Dust
Equipment Protection Level
EPL/zone area
Parameters:
Temperature class
(T1...T6)
Explosion group (A, B, C)
Additional information for use in areas
where there is a risk of dust explosion:
The details of the maximum surface temperature are valid only for a dust allowance of a
maximum of 5 mm.
At higher dust deposits must be reduced with the surface temperature.
Determining the maximum permissible surface temperature
Dust cloud with ignition temperature -T
CL
: T
max1
= 2/3 T
CL
Dust layers with glow temperature -T
5mm
:T
max2
= T
5mm
– 75
o
C
The smaller value of both must be considered for the maximum permitted surface tempera-
ture. To prevent from dangerous temperature rises dust deposits should be avoided (ap-
propriate mounting position, use of protection covers, regular cleaning..)
For the installation procedure it is necessary to take care that no electrostatic charging will
be done (no high volume flow, cleaning only with damp cloth,…)
Equipment Pro-
tection Level
EPL
Zone
Equipment
category 0
20
1
21
2
22
1 G,D Ga,Da yes yes yes
2 G, D Gb,Db no yes yes
3 G,D Gc ;Dc no no yes

Installation
Installation
Beck GmbH
Druckkontrolltechnik
Ferdinand-Steinbeis-Straße 4
71144 Steinenbronn
Operating instructions – Pressure Switch – Model - 901...EX Rev.10 Page 7 of 18
The following standards and directives are useful:
EN 1127-1: Explosion protection – basic concepts and methodology
Standards for areas with risk of gas explosion (“G”, “D”):
EN 60079-10: Classification of potentially explosive areas
EN 60079-14: Electrical installations in potentially explosive areas
EN 60079-17: Inspection and maintenance
EN 60079-25: Intrinsically safe systems
4.1 Installation
Choose the installation location from the following aspects;
Ease of access for installation, connection and operation
Protection from direct effects of the weather, such as rain and sun
The IP protection class of the equipment must suit the ambient conditions
In order to prevent dangerous temperature increases on the surface of the equipment, dust
deposits must be avoided (installation location, protective cover, cleaning measures etc.)
4.2 Connection
When work is being performed such as installation, making electrical
connection, making repairs or opening the housing, it must be ensured that
No electrical voltage is present
Unintentional activation is not possible
Proceed as follows in potentially explosive areas:
Check whether the equipment category corresponds with the
specified zones
No potentially explosive atmosphere is present
A release for work must have been issued by the operator
Adherence to the applicable regulations and documentation for the equipment
Special notes for intrinsically safe (“i”) systems:
Each intrinsically safe operating material must have an associated operating mate-
rial inserted before it, outside of the potentially explosive zone.
Separate cable routing for intrinsically safe and non-intrinsically safe power circuits.
For operating voltages of less than 42V AC or 60V AC: Intrinsically safe and non-
intrinsically safe power circuits can be routed together in this case. This only applies
to safety barrier with galvanic separation.
Separation of intrinsically safe/non-intrinsically safe connecting parts: at least 50mm
(tight string length)
Distance between different intrinsically safe power circuits: at least 6mm
Distances between non-insulated conductive parts leading to connecting parts:
air gap of at least 3mm (housing-terminals-conductor tracks, earth etc.)
Power supply
Each intrinsically safe operating material must have an associated
operating material inserted before it, outside of the potentially
explosive zone:
Pay attention to maximum characteristics (U, I, P, L, C)
Select connecting cables
The following points must be observed when selecting the cable:
Select cable material that complies with the local resistance
requirements (mechanical, chemical)
Cable cross-section in accordance with electrical power and data sheet

Installation
Connection
Beck GmbH
Druckkontrolltechnik
Ferdinand-Steinbeis-Straße 4
71144 Steinenbronn
Operating instructions – Pressure Switch – Model - 901...EX Rev.10 Page 8 of 18
The following points must be observed when selecting cables for intrinsically safe power
circuits:
Diameter of individual conductors: greater than 0.1mm
Insulation strength of the individual wires: greater than 0.2 mm
Test voltage for intrinsically safe cables:
- between wires, shield and earth: 500V AC
Shield: The shield area must be 60% of the surface coverage or twisting
Labelling of intrinsically safe power circuits: colour preferably light blue
L and C cable characteristics must be available
(C
i
=110nF/km; L
i
=1 mH/km)
Cable routing
If there is a risk of mechanical damage, the cable must be provided with additional
protection (protective tube etc.)
The cable diameter must be complied with in order to provide a tight connection in
the cable lead-in.
The screwed cable connection and the screws of the housing cover must be tight-
ened in order to comply with the IP protection class. Over-tightening damages the
housing.
Connecting the cable
Please ensure that the cables that are being connected are not live.
otherwise there is a risk of igniting a potentially explosive atmosphere
Attach the shield
Attach shield at one end (in non-potentially explosive area)
Attach braiding of shield to earth potential over a wide area.
No potential equalisation current must be flowing between potentially
explosive areas and non-potentially explosive areas.
Separation using a capacitor is permitted in this case
for EMC purposes (total max. 10 nF).
Earthing
The external earthing terminal on the housing must be connected
to the potential equalisation of the potentially explosive area with
low resistance
(removal of electrostatic charge between 0.2-1 MOhms is considered to be earthing)
No potential equalisation current must be flowing between potentially explosive are-
as and non-potentially explosive areas
Minimum cross-section: 2 x 1.5 mm² or 1 x 4 mm²
Intrinsically safe power circuits: Housings made from metal do not need to be
earthed.
(If this is necessary anyway – functional earthing, earthing in one location only…)
Documentation
Operating instructions, conformity declaration, EC design test certificate
System and zonal plan
Proof of adherence to explosion protection regulations (see Appendix 9.5)
Equipment selection: category, Equipment Protection Level EPL, temperature
class, explosion group, …
Proof of adherence to intrinsic safety requirements

Start-up
Parameterisation
Beck GmbH
Druckkontrolltechnik
Ferdinand-Steinbeis-Straße 4
71144 Steinenbronn
Operating instructions – Pressure Switch – Model - 901...EX Rev.10 Page 9 of 18
5 Start-up
Before voltage is applied to the equipment the following checks must be performed:
Check that screws are firmly seated in
Connecting terminals, protective earth conductor terminals and
potential equalisation terminals
Housing cover
Check
The torque of the cable lead-in
The tightness of the seal provided by the cable lead-in
Check whether the equipment is ready for operation
The parameterisation for this application must have been performed
All interfaces such as inputs and outputs for control purposes must be connected
and ready for operation
5.1 Parameterisation
Equipment parameterisation
Define all application-specific parameters.
Once the power supply is applied, the equipment is ready for operation immediately.
6 Maintenance / service
The equipment can only be guaranteed to operate safely and reliably
in the long term if regular inspections and servicing are carried out. These include the following:
For cleaning the devices it is necessary to take care that no electrostatic charging will be done (no
high volume flow, cleaning only with damp cloth,…)
An inspection includes
Visual inspection
oMechanical damage
oNon-permitted dust deposits
oOther irregularities or error messages from the equipment
Checking of components (wearing parts) whose functionality or purpose changes and af-
fects the operation of the equipment
Documentation of what was done by whom, and when
Maintenance includes
Functionality checking
oOperating statuses such as alarms etc.
Checking calibration values (= calibration)
oTriggering of alarms by known process parameters (test pressure etc.)
Correction of calibration values (= calibration) must be carried out in the factory
Documentation of what was done by whom, and when
6.1 Time intervals
Inspection:
The condition of the equipment must be checked at regular intervals. The time interval is extreme-
ly dependent on the local situation and the degree of use, and must therefore be adapted to re-
quirements. Extremely short time intervals can be specified such as once per day, every new shift
etc.
Defined by the operator in accordance with local requirements

Repairs
Troubleshooting
Beck GmbH
Druckkontrolltechnik
Ferdinand-Steinbeis-Straße 4
71144 Steinenbronn
Operating instructions – Pressure Switch – Model - 901...EX Rev.10 Page 10 of 18
Maintenance
The interval from the applicable usage regulations must be taken
into consideration
As a manufacturer we recommend a maximum interval of 1 year
6.2 Troubleshooting
A list of possible faults (fault indications) can be found in the table below.
The table contains an explanation of how to detect faults.
A list of possible causes and remedial measures also follows.
Fault indication
Possible cause
Measures
Contact won’t switch
Defective diaphragm
Replace pressure switch
Spring defective
Pressure connection blocked
Pressure outside working range
7 Repairs
The following points must be noted before carrying out any work whatsoever on the equipment:
When work is being performed such as installation, making electrical
connections or opening the housing, it must be ensured that
No electrical voltage is present
Unintentional activation is not possible
Repairs must only be carried out by the manufacturer
The following must be observed in potentially explosive areas:
No potentially explosive atmosphere is present
A release for work must have been issued by the operator
The applicable regulations and all documentation for this
equipment must be adhered to
Only original spare parts from the manufacturer must be used
The spare parts must comply with the required equipment category
Interventions that influence explosion protection must only be carried out by experts
A prerequisite is adequate qualification (“capable person”) with regard to explosion
protection and the use of the equipment
8 Dismantling
The following points must be noted before carrying out any work whatsoever on the equipment:
Ensure that the equipment may be removed and that appropriate
replacement measures have been taken.
All of the instructions in chapter 7 “
Repairs
” must be followed
Exposed cable (ends) must be marked, and it must be ensured that
No electrical voltage is present
Unintentional activation is not possible
8.1 Disposal
The equipment is made from recyclable materials and is designed to make
the housing and the electronics easy to separate. Please ensure that all
parts are disposed of in accordance with legal regulations.
Please contact us if you cannot dispose of the equipment properly.

Appendix
Technical data and dimensioned drawing
Beck GmbH
Druckkontrolltechnik
Ferdinand-Steinbeis-Straße 4
71144 Steinenbronn
Operating instructions – Pressure Switch – Model - 901...EX Rev.10 Page 11 of 18
9 Appendix
9.1 Technical data and dimensioned drawing
Temperature ranges
Ambient temperature:
from -20 °C to +85 °C
Medium temperature:
up to +85 °C
Storage temperature:
from -40 °C to +85 °C
Diaphragm material
Depending on media NBR, Silicone, FKM (Viton
®
), EPDM.
For types 901.30 and 901.8x only Silicone diaphragms, others upon request.
Electrical rating
Values indicated for resistive load
for Gas 1/2G or 2G: 60 mA/30 VDC or 100 mA/24 VDC
for Dust 2D: 30V; 60mA ; 0.6W
Electrical connection
Arrangement of contacts
for 901.1.., 901.30, 901.41, 901.51 EX only for 901.2.. EX
for 901.6.., 901.8.., 901.9.. EX only for 901.7.. EX
Certifications
CE conformity in according with ATEX-directive 2014/34/EU.
EC-type certification by the specified EXAM body (ID 0158) with the following ATEX labelling:
1/2G: Ex ia IIB T4 Ga/Gb or 2G: Ex ia IIC T4 Gb
2D : Ex ia IIIB T135
o
C Db
Characteristics:
1/2G or 2G : U
i
= 24/30 V; I
i
= 100/60 mA;
2D : 30V; 60mA ; 0.6W
L
i
= 0 mH; C
i
= 0 nF
Life
Minimum 10
6
cycles.
Damping
Restrictors alternatively with 0.3/0.5/0.8 mm diameter.
Accessories
Protection caps with IP 54
(intended for use in potentially explosive atmospheres)
Various mounting brackets
Mounting position
Mounting in any position, but needs to be specified for settings below 100 mbar.

Appendix
Technical data and dimensioned drawing
Beck GmbH
Druckkontrolltechnik
Ferdinand-Steinbeis-Straße 4
71144 Steinenbronn
Operating instructions – Pressure Switch – Model - 901...EX Rev.10 Page 12 of 18
9.1.1 Pressure switch 901
Factory-set pressure setting
Pressure connection
Type Tube connection Threaded connection
5.0 mm 6.5 mm 10.0 mm M 10 x1 G 1/8 G 1/4 G 1/2
901.1…EX
PA PA, PPS PA, PPS PA, PVDF,
CuZn40, V
2
A PA, PVDF,
CuZn40, V
2
A
PVDF,
CuZn40, V
2
A CuZn40
901.2…EX
PA PA, PPS PA, PPS PA, PVDF,
CuZn40, V
2
A PA, PVDF,
CuZn40, V
2
A
PVDF,
CuZn40, V
2
A CuZn40
901.30 EX
PA
901.41 EX
PA, PPS PA, PPS PA, PVDF,
CuZn40, V
2
A PA, PVDF,
CuZn40, V
2
A CuZn40, V
2
A CuZn40
901.51 EX
CuZn40 CuZn40, V
2
A CuZn40, V
2
A
PA = polyamide, PVDF = polyvinyldifluoride, PPS = polyphenylensulfide, CuZn40 = brass, V
2
A = stainless steel
Overpressure range
Type Factory-set
trip pressure
between and
Standard switching
differential
lower end upper end
of range of range
Tolerance
band in % of
trip pressure
Maximum
positive
working
pressure
standard/
extended
Maximum
negative
working
pressure
standard/
extended
901.1...EX
5 mbar 200 mbar 2.5 mbar 50 mbar ±10 % 0.5/4 bar –/–1 bar
200 mbar 1000 mbar 50 mbar 150 mbar ±10 % 1/4 bar –/–1 bar
901.41 EX
500 mbar 3000 mbar 200 mbar 600 mbar ±10 % 10 bar –1 bar
901.51 EX
1.0 bar 12 bar 0.2 bar 1.5 bar ±10 % 25 bar –1 bar
Vacuum range
Type Factory-set
trip pressure
between and
Standard switching
differential
lower end upper end
of range of range
Tolerance
band in % of
trip pressure
Maximum
positive
working
pressure
standard/
extended
Maximum
negative
working
pressure
standard/
extended
901.2…EX
– 5 mbar – 200 mbar
2.5 mbar 50 mbar ±10 % 0.5/4 bar –1 bar
– 200 mbar – 900 mbar
50 mbar 150 mbar ±10 % 1/4 bar –1 bar
Differential pressure range
Type Factory-set
trip pressure
between and
Standard switching
differential
lower end upper end
of range of range
Tolerance
band in % of
trip pressure
Maximum
positive
working
pressure
standard/
extended
Maximum
negative
working
pressure
standard/
extended
901.30..EX
5 mbar 50 mbar 2.5 mbar 25 mbar ±10 % 100 mbar –100 mbar

Appendix
Technical data and dimensioned drawing
Beck GmbH
Druckkontrolltechnik
Ferdinand-Steinbeis-Straße 4
71144 Steinenbronn
Operating instructions – Pressure Switch – Model - 901...EX Rev.10 Page 13 of 18
9.1.2 Pressure switch 901 Prescal
®
Adjustable setting
Pressure connection
Type Tube connection Threaded connection
5.0 mm 6.5 mm 10.0 mm M 10 x1 G 1/8 G 1/4 G 1/2
901.61-65 EX
PA PA, PPS PA, PPS PA, PVDF,
CuZn40, V
2
A PA, PVDF,
CuZn40, V
2
A
CuZn40, V
2
A CuZn40
901.66-68 EX
CuZn40, V
2
A CuZn40, V
2
A
CuZn40, V
2
A CuZn40
901.71-76 EX
PA PA, PPS PA, PPS PA, PVDF,
CuZn40, V
2
A PA, PVDF,
CuZn40, V
2
A
CuZn40, V
2
A
901.77-78 EX
CuZn40, V
2
A CuZn40, V
2
A
CuZn40, V
2
A CuZn40
901.8… EX PA
901.91-93 EX
CuZn40 CuZn40, V
2
A CuZn40, V
2
A
PA = polyamide, PVDF = polyvinyldifluoride, PPS = polyphenylensulfide, CuZn40 = brass, V
2
A = stainless steel
Overpressure range
Type Adjustment range
for trip pressure
from to
Tolerance
band in % of Switching
differential Maximum positive
working pressure
standard/extended
Maximum negative
working pressure
standard/extended
901.61 EX 5 20 mbar ±10 % 3 mbar 0,5/4 bar –/–1 bar
901.62 EX 10 50 mbar ±10 % 5 mbar 0,5/4 bar –/–1 bar
901.63 EX 25 100 mbar ±10 % 10 mbar 0,5/4 bar –/–1 bar
901.64 EX 50 250 mbar ±10 % 20 mbar 1/4 bar –/–1 bar
901.65 EX 100 500 mbar ±10 % 50 mbar 1/4 bar –/–1 bar
901.66 EX 250 1000 mbar
±10 % 150 mbar 10 bar –1 bar
901.67 EX 500 1500 mbar
±10 % 250 mbar 10 bar –1 bar
901.68 EX 1000 3000 mbar
±10 % 500 mbar 10 bar –1 bar
901.91 EX 1.0 6.0 bar ±10 % 0.5 – 2.0 bar 25 bar –1 bar
901.92 EX 4.0 9.0 bar ±10 % 0.5 – 2.0 bar 25 bar –1 bar
901.93 EX 7.0 12.0 bar ±10 % 0.5 – 2.0 bar 25 bar –1 bar
Vacuum range
901.71 EX –5 –20 mbar ±10 % 3 mbar 0,5/4 bar –/–1 bar
901.72 EX –10 –50 mbar ±10 % 5 mbar 0,5/4 bar –/–1 bar
901.73 EX –25 –100 mbar ±10 % 10 mbar 0,5/4 bar –/–1 bar
901.74 EX –50 –125 mbar ±10 % 20 mbar 0,5/4 bar –/–1 bar
901.75 EX –75 –200 mbar ±10 % 25 mbar 1/4 bar –/–1 bar
901.76 EX –100 –300 mbar ±10 % 30 mbar 1/4 bar –1 bar
901.77 EX –200 –500 mbar ±10 % 75 mbar 1/4 bar –1 bar
901.78 EX –300 –700 mbar ±10 % 75 mbar 1/4 bar –1 bar
Differential pressure range
901.81 EX 5 20 mbar ±10 % 3 mbar 100 mbar –100 mbar
901.82 EX 10 50 mbar ±10 % 5 mbar 100 mbar –100 mbar

Appendix
Dimensioned drawings and accessories
Beck GmbH
Druckkontrolltechnik
Ferdinand-Steinbeis-Straße 4
71144 Steinenbronn
Operating instructions – Pressure Switch – Model - 901...EX Rev.10 Page 14 of 18
9.2 Dimensioned drawings and accessories
9.2.1 Pressure switch 901

Appendix
Beck GmbH
Druckkontrolltechnik
Ferdinand-Steinbeis-Straße 4
71144 Steinenbronn
Operating instructions – Pressure Switch – Model - 901...EX Rev.10 Page 15 of 18
9.2.2 Pressure switch 901 Prescal
®

Appendix
Declaration of Conformity
Beck GmbH
Druckkontrolltechnik
Ferdinand-Steinbeis-Straße 4
71144 Steinenbronn
Operating instructions – Pressure Switch – Model - 901...EX Rev.10 Page 16 of 18
9.3 Declaration of Conformity

Appendix
EC design test certification
Beck GmbH
Druckkontrolltechnik
Ferdinand-Steinbeis-Straße 4
71144 Steinenbronn
Operating instructions – Pressure Switch – Model - 901...EX Rev.10 Page 17 of 18
9.4 EC design test certification
Note: More documentation for EC design test certification you can download from our website.

Appendix
Proof of compliance with explosion protection regulations
Beck GmbH
Druckkontrolltechnik
Ferdinand-Steinbeis-Straße 4
71144 Steinenbronn
Operating instructions – Pressure Switch – Model - 901...EX Rev.10 Page 18 of 18
9.5 Proof of compliance with explosion protection regulations
Project
Name
Date
Requirement Complies with Requirement Complies with
Application area
II
(Gas) III
(Dust) II
(Gas) Temperature
class (Gas) Temperature
class (Gas) Temp.
(Dust)
T1
T1 400
o
C
T2
T1-T2 300
o
C
Explosion
group A A T3
T1-T3 200
o
C
B A,B,C A,B T4
T1-T4 135
o
C
C A,B,C A,B,C T5
T1-T5 100
o
C
T6
T1-T6 85
o
C
Requirement Permitted Equip.
Protection Level
EPL (G=Gases)
Certified for
Ignition protection class
Zone 2,22
Gc,Dc Zone 2/22
1,21
Gb,Db Zone 1,2 /21,22 Ex ia IIB / Ex ia IIIB
0,20
Ga,Da Zone 0,1,2/ 20,21,22 Ex ia IIC
CHARACTERICTICS
Intrinsically safe operating materials Associated operating
materials
Designation
Pressure switch Cable
Switch amplifier
Model 901 ..EX
Application area 2G 2D 1/2G
Ignition protection class
Ex ia … Gb
Ex ia…Db Ex ia.. Ga
Explosion group IIC IIIB IIB
Temperature class T4 T135C T4
Certification BVS 06 ATEX E141X
U
i,a
30V
I
i,a
60mA
P
i,a
600mW
L
i,a
0 1mH
C
i,a
0 0,1µF
Kabelkennwerte: 1
mH
/
km
; 110
nF
/
km
Requirement complied with
Application area
Ignition protection class
Explosion group
Temperature class
Equipment Protection Level EPL/Zone
Proof of intrinsic safety
Associated operating mate-
rials
(barriers)
Require-
ment Intrinsically safe operating
materials
(including cable)
Com-
pliant
U ≤
30V
I
≤
60mA
P ≤
600mA
L ≥
1mH
(1km cable)
C ≥
0,1µF
(1km cable)
Table of contents
Other Beck Switch manuals
Popular Switch manuals by other brands
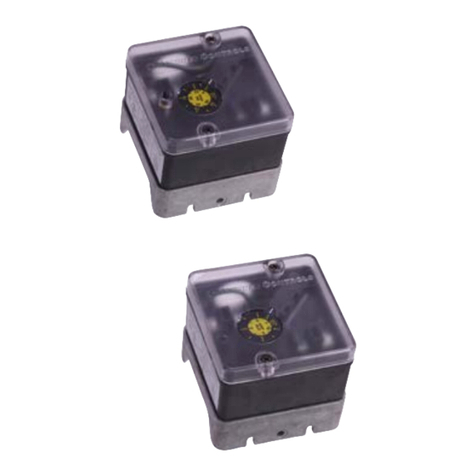
Easterseals Crossroads
Easterseals Crossroads Antunes Controls G Series Installation information
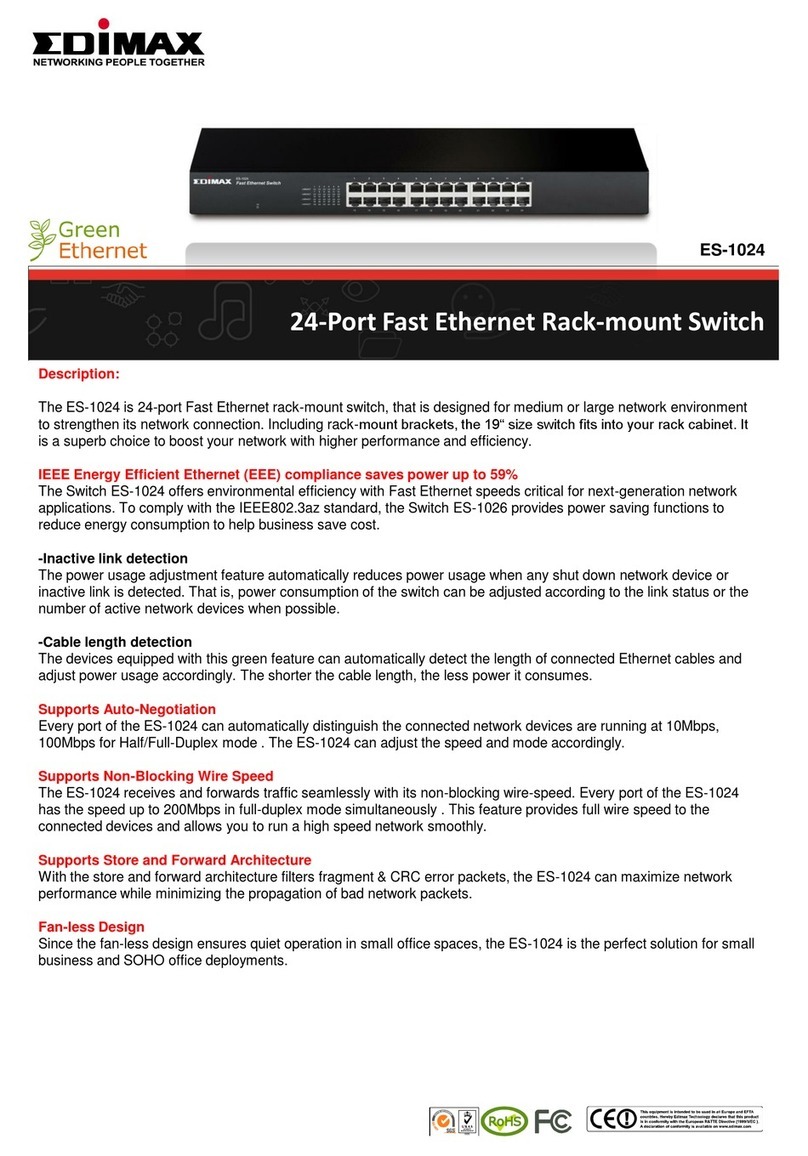
Edimax
Edimax ES-1024 datasheet
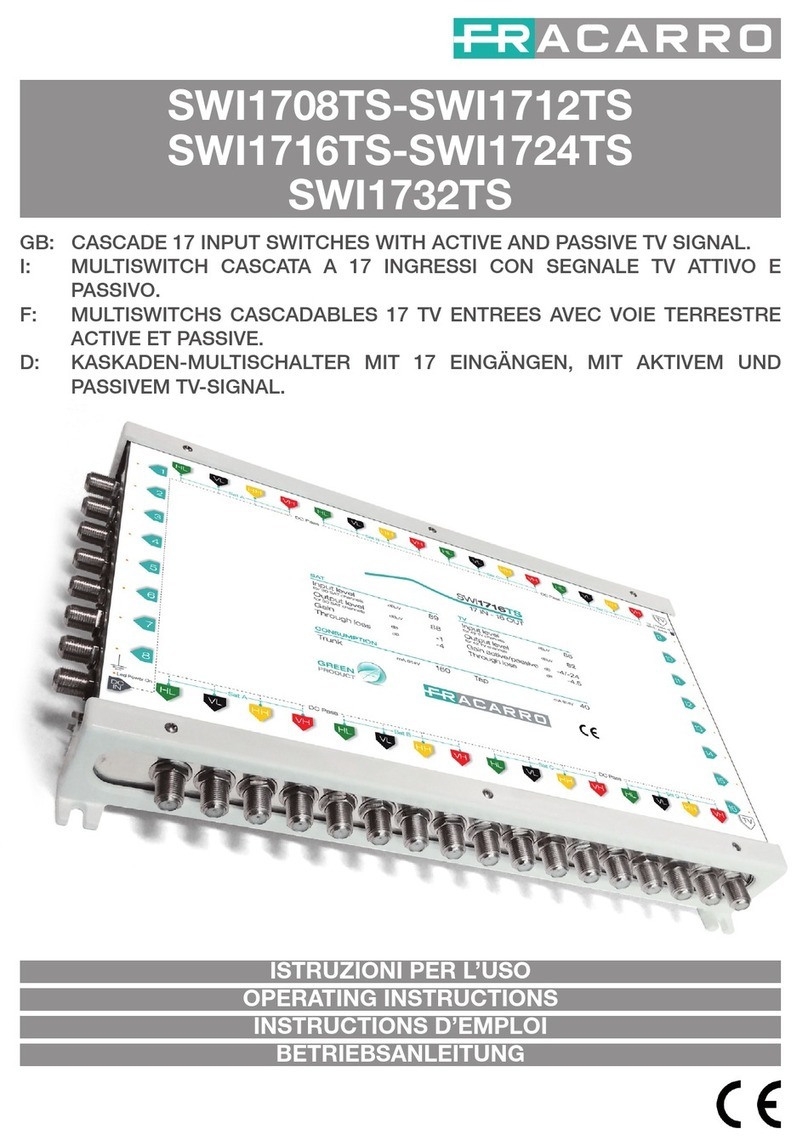
Fracarro
Fracarro SWI1732TS operating instructions

Panasonic
Panasonic AV620264 manual

Ross
Ross Carbonite Solo Installation and cabling guide
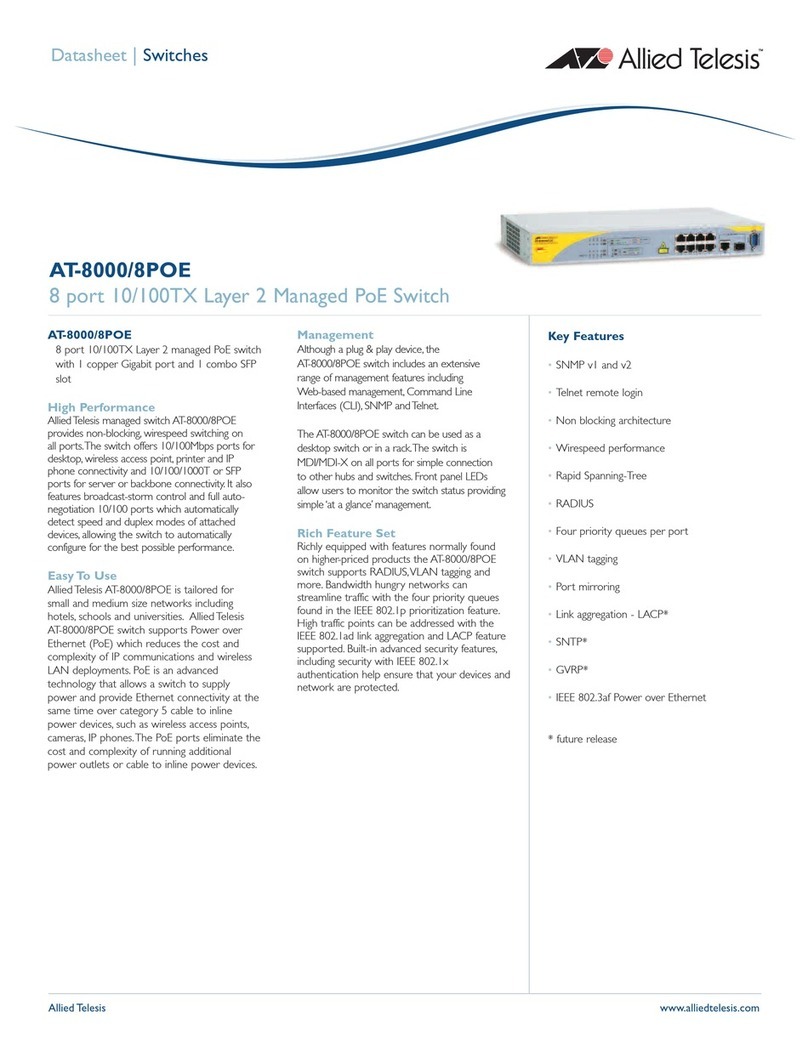
Allied Telesis
Allied Telesis AT-8POE datasheet