BENDIX IN-20258 User manual

ÂILLIED Bendix
~
Aerospace
1.
General
Bendix
General
Aviation
Avionics
Division
MAINTENANCE
MANUAL
IN-20258
MULTIFUNCTION
COLOR
INDICATOR
SECTION
V
MAINTENANCE
PRACTICES
This section contains inspection procedures, cleaning information,
repair
information,
and
semiconductor
and
integrated
circuit
service information
for the
IN-20258
Multifunction Color
Indicator.
2.
Inspection
Perform a routine visual inspection
any
time the radar indicator
is
removed
from
the
aircraft.
Pay
special
attention
to
the following
areas.
A.
Oust
Caver
Inspect the dust caver for dents, deformation or
damage
to the
finish
that
should
be
repaired.
B.
Chassis
Inspect chassis for loose or missing hardware, deformation,
damaged
fasteners,
or
damaged
connectors. Also
check
for corrosion or
damage
to the
finish
that
should
be
repaired.
C.
Connectors
Inspect connecter
body
for broken
parts;
check
insulation for cracks.
Check
pins for
damage,
corrosion, misalignment, or
bad
plating.
Check
for broken, loose, or poorly soldered connections to terminals of
connectors. Inspect cable
clamps
for pinched wires.
o.
Terminal Connections
Inspect for corrosion
and
loose connections.
E.
Wi
ring
Inspect chassis wiring
and
subassemblies for
any
physical
damage
or
charring.
F.
Capacitors
Inspect for case or
body
damage
and
for loose, broken, or corroded
terminal connections.
G.
Resistors
and
Diodes
Inspect for
blistered,
charred, or cracked bodies.
Check
for loose,
broken, or corroded terminal connections.
I.B.
21400C
PART
4 5-1
Mar/86
The document reference is online, please check the correspondence between the online documentation and the printed version.

2.
H.
~
General
Aviation
~
Avionics
Division
MAINTENANCE
MANUAL
IN-20258
MULTIFUNCTION
COLOR
INDICATOR
Filters
and
Inductors
Inspect for
damage
to
body
or casing
and
for loose, broken, or corroded
terminal connections.
Check
for secure
mounting
to chassis.
1. Transformers
Inspect case for
damage
and
for signs of excessive heating.
Check
for
loose, broken, or corroded terminal connections.
J. Transistors
and
Integrated Circuits
Inspect for
damage
to
body
or case
and
for secure attachment to socket.
K.
Terminal
Connections, Soldered
(1)
Inspect for cold soldered or rasin
joints.
Bad
joints
can
be·
recognized
by
a
dull,
porous appearance.
(2)
Check
for excessive solder,
insufficient
solder, or solder
splashes resulting
from
a previous
repair.
(3)
Check
for corrosion
at
the terminal connections.
L.
Rotary Switches
Check
for proper mechanical operation;
no
binding or looseness should
be
evident.
M.
Printed Circuit
Boards
Inspect for loose,
broken
or corroded terminal connections
and
damage
such
as
cracks, burns or charred track. Also,
check
for
insufficient
solder, proper binding, fungus,
mold
or other deposits
that
should
be
repaired.
N.
Cathode-Ray
Tube
Inspect tube face for
burned
spots or ether discrepancies
which
could
cause deterioration of the display.
Check
tube for secure mounting.
O.
CRT
Fi
lter
Check
CRT
filter
for
scratches
or
other blemishes
which
could cause
deterioration of the display.
1.B.
21400C
PART
4
5-2
Jun/84
The document reference is online, please check the correspondence between the online documentation and the printed version.

~
General
Aviation
~
Avionics
Division
MAINTENANCE
MANUAL
IN-2025B
MULTIFUNCTION
COLOR
INDICATOR
3.
Cleaning
Perform a routine cleaning
any
time
the radar indicator
is
removed
from
the
aircraft.
A.
Recommended
Cleaning
Agents
Table 5-l
lists
the
recommended
cleaning agents to
be
used
during
overhaul of the
IN-2025B.
TYPE
USED
TO
CLEAN
Denatured
Alcohol
Exterior surfaces (except
CRT
filter)
and
interior
surfaces.
Isopropyl
Alcohol
Printed
circuit
boards.
Glass Cleaner
(Windex
or
CRT
filter.
or equivalent)
Recommended
Cleaning
Agents
Table
5-l
B.
Recommended
Cleaning Procedures
WARNING:
GOGGLES
ARE
TO
BE
WORN
WHEN
USING
PRESSURIZED
AIR
TO
BLOW
OUST
AND
DIRT
FROM
EQUIPMENT.
ALL
PERSONNEL
SHOULD
BE
CLEARED
FROM
THE
IMMEDIATE
AREA.
WARNING:
OPERATIONS
INVOLVING
THE
USE
OF
A
CLEANING
SOLVENT
SHOULD
BE
PERFORMED
UNDER
A
VENTILATED
HOOD.
AVOlD
BREATHING
SOLVENT
VAPOR
AND
FUMES;
AVOlD
CONTINUOUS
CONTACT
WITH
THE
SOLVENT.
CAUTION:
USE
ONLY
RECOMMENDED
CLEANING
SOLVENTS
ON
ELECTRICAL
PARTS.
MANY
AVAILABLE
CLEANING
SOLVENTS
CAN
SOFTEN
AND
PERMANENTLY
DAMAGE
INSULATING
MATERIALS.
CAUTION:
ALUMINUM
ELECTROLYTIC
CAPACITORS
CAN
BE
DAMAGED
BY
HALOGENATED
HYDROCARBON
SOLVENTS.
BENDIX
AVIONICS
RECOMMENDS
11
lSOPROPYL
ALCOHOL"
AS
A
SAFE
CLEANING
SOLVENT
FOR
PRINTED
CIRCUIT
BOARDS
CONTAINING
ALUMINUM
ELECTROLYTIC
CAPACITORS.
OTHER
SOLVENTS
WHICH
MAY
BE
USED
ARE
AS
FOLLOWS:
I.B.
21400C
5-3
PART
4 Jun/84
The document reference is online, please check the correspondence between the online documentation and the printed version.

3.B.
~
General
Aviation
~
Avionics
Division
MAINTENANCE
MANUAL
IN-2025B
MULTIFUNCTION
COLOR
INDICATOR
SAFE
SOLVENTS
XYLENE
ETHYL
ALCOHOL
BUTYL
ALCOHOL
METHYL
ALCOHOL
PROPYL
ALCOHOL
CALGONITE
(A
BRAND
OF
DETERGENT)
PRINTED
CIRCUIT
BOARDS
CONTAINING
ALUMINUM
ELECTROLYTIC
CAPACITORS
SHALL
NOT
BE
CLEANED
WITH
THE
FOLLOWING
SOLVENTS:
UNSAFE
SOLVENTS
FREON
TF,
TMC
CARBON
TETRACHLORIDE
CHLOROFORM
TRICHLOROETHYLENE
TRICHLOROETHANE
ALL
(A
BRAND
OF
DETERGENT)
METHYLENE
CHLORIDE
(1)
Perform
exterior
cleaning
as
follows:
(a)
Wipe
dust caver
and
exterior of chassis with a
lint-free
elath
dampened
with denatured alcohol.
(b)
Use
a clean camel's hair (or equivalent) brush saturated with
denatured alcohol
ta
remove
any
foreign matter
from
rear
connecter.
(c)
Clean
CRT
filter
with a
lint-free
elath
slightly
dampened
with
Windex
glass cleaner.
(d)
Open
any
blocked ventilation hales
in
the dust caver
by
first
saturating the debris clogging the apertures with denatured
alcohol
and
then
blowing
the loosened material out with
an
air
stream.
(2) Perform
interior
chassis cleaning
as
follows:
I
.B.
21400C
PART
4
CAUTION:
AVOlD
AIR-BLASTING
DELICATE
PARTS.
(a)
Remove
dust
and
other
dirt
from
all
surfaces, including
parts
and
wiring, using a
soft
bristle,
camel's hair (or
equivalent) brush
in
conjunction with a clean, dry
air
jet
(25
to
38
psi).
5-4
Jun/84
The document reference is online, please check the correspondence between the online documentation and the printed version.

1
BENDIX/KING
MAINTENANCE
MANUAL
IN-20258
MULTIFUNCTION
COLOR
INDICATOR
(b)
Any
dirt
that cannat
be
removed
in
previous step
should
be
removed
using
a soft
bristle,
camel's hair
brush
saturated
with isopropyl alcohol.
Use
a clean, dry
air
jet
(25
ta
38 psi)
ta
remove
excess isopropyl alcohol
and
loosened
dirt.
(3)
Perform
printed circuit
board
cleaning
as
follows:
CAUTION:
AVOlD
AIR-8LASTING
DELICATE
PARTS.
{a)
Remove
dust
and
other
dirt
from
board
surfaces
and
components
using
a soft
bristle,
camel's
hair
{or
equivalent)
brush
in
conjunction with a clean,
dry
air
jet
{25
ta
38 psi).
{b)
Any
dirt
that
cannet
be
removed
in previous step
should
be
removed
using
a soft
bristle,
camel
hair (or equivalent)
brush
saturated
with
isopropyl alcohol.
Use
a clean,
dry
air
jet
(25
to
38
psi) to
remove
excess isopropyl alcohol
and
loosened
dirt.
{4)
Perform
connecter cleaning
as
follows:
4.
Repair
(a)
Wipe
dust
and
dirt
from
bodies, shells
and
cable
clamps
using
lint-free
cloth
moistened
with denatured alcohol.
(b)
Wipe
dry
with
a clean, dry,
lint-free
elath.
(c)
Remove
dirt
and
lubricant
from
inserts,
insulation
and
terminals
using
soft
bristle,
camel's hair {or equivalent)
brush
saturated
with
denatured alcohol.
(d)
Ory
insert
with
clean,
dry
air
jet
(25
ta
38
psi).
WARNING:
VOLTAGE
DANGEROUS
TO
LIFE
EXISTS.
REMOVE
ALL
POWER
TO
INDICATOR
8EFORE
PROCEED
WITH
REPAIR.
A.
Repair
Precautions
(1)
Refer
ta
paragraph
4.8. for special
ESDS
handling precautions.
(2)
Perform
repairs
and
replace
components
with
power
disconnected
from
the
equipment.
(3)
Use
a conductive table
top
for repairs
and
connect the table
ta
the
ground
conductor of the
60-Hz
power
line.
{4)
Replace
connectors, coaxial cable, shielded conductors,
and
twisted pairs
ONLY
with
identical items.
1.8.
21400C
PART
4
5-5
Dec/92
The document reference is online, please check the correspondence between the online documentation and the printed version.

BENDIX/KING
MAINTENANCE
MANUAL
IN-2025B
MULTIFUNCTION
COLOR
INDICATOR
(5)
Reference
ta
"component
side" of a printed
circuit
board
in
this
manual
means
the side
on
which
the
components
are located;
"track side" refers
ta
the other side.
(6)
When
repairing
circuits,
carefully observe lead dress
and
component
orientation.
Keep
leads
as
short
as
possible
and
observe correct repair techniques.
(7)
Observe
cable routing throughout instrument assembly, prior to
disassembly,
ta
enable a proper
reinstallation
of the cabling
during reassembly procedures.
B.
Electrostatic Discharge Sensitive
(ESDS)
Deviees
Deviees
sensitive to
electrostatic
discharge are
used
in
this
equipment.
These
deviees, including
Metal
Oxide
Semiconductors
(MOS),
sorne
metal
film
resistors,
and
ether deviees, are susceptible
to
damage
by
electrostatic
charges or high-voltage
fields.
Because
of the
very
high
resistances
in
ESDS
deviees, they
can
be
damaged
by
electrical
sources
that
cannat deliver
enough
current
ta
damage
conventional semiconductors. Therefore, special precautions
must
be
taken during handling
and
rep~ir
procedures to prevent
damaging
the
deviee.
The
most
common
low-energy
source causing
damage
to
ESDS
deviees is the
human
body,
which
generates
and
retains
static
electricity,
in
conjunction with nonconductive garments
and
floor
covering.
An
individual
can
easily develop several thousand volts
of
electrostatic
charge while
simply
walking
across the floor or
moving
around
in a chair. Electrostatic charges of
20
kV
have
been
measured
on
personnel,
and
35
kV
has
been
measured
on
their
garments.
The
capacitive elements in
all
MOS
deviees
can
be
destroyed
by
a
voltage
field,
even
when
assembled
into the
circuit.
Similar
capacitive elements in
linear
integrated
circuits,
hybrids,
and
in
bipolar integrated
circuits
are also susceptible
ta
field
voltages.
Not
all
electrostatic
damage
will
result
in
immediate
catastrophic
failure.
Damaged
deviees
may
remain
operating within the
minimum
limits but could experience early
field
failure or
erratic
performance.
The
following precautions are
recommended
for
ESDS
circuits
and
are
especially important
in
low
humidity
or
dry
conditions
when
electrostatic
problems
are
more
prevalent.
CAUTION:
ESDS
DEVICES
INCLUDE,
BUT
ARE
NOT
LIMITED
TO,
C-MOS,
J-MOS,
PMOS,
NMOS,
SOCMOS,
HMOS,
MOS/FET,
MICROWAVE
MIXER
DIODES,
SOME
BIPOLAR
DEVICES,
AND
SOME
METAL
FILM
RESISTORS.
I.B.
21400C
5-6
PART
4
Dec/92
The document reference is online, please check the correspondence between the online documentation and the printed version.

BENDIX/KING
MAINTENANCE
MANUAL
IN-20258
MULTIFUNCTION
COLOR
INDICATOR
(1)
Storage
Store
and
transport all
ESDS
deviees in conductive material.
Do
not insert
ESDS
deviees into conventional
plastic
"snow"
or
plastic
trays
used
for storing
and
transporting standard
semiconductor deviees. Special
bags
or containers
must
have
a
maximum
resistivity
of
10
ohms/cm,
or the leads of the deviee
must
be
shorted together through a conductive material (special
foam)
having
a
maximum
resistivity
of
10
4
ohms/cm.
Modules,
circuit
boards, or assemblies containing
ESDS
deviees
must
be
stored
in
static
shielding
bags
with
a
maximum
resistivity
of
10
4
ohms/cm
on
the outer layer of the
bag,
and
10
12
ohms/cm
resistivity
in
the inner layer.
A caution label shall
be
attached to the outside of
all
containers containing
ESDS
deviees.
The
ESDS
labels are
identified
in
the advisory information located in the front of
this
manual.
Do
not
remove
deviee
from
container until
actually
used
or tested.
(2)
Work
Station
1.8.
21400C
PART
4
All
equipment,
tools, materials,
and
personnel
at
the
work
station
must
be
maintained at the
same
electrical
potential.
All
grounding
connections shall
have
common
point,
and
that
point shall
be
connected to electrical ground.
Soldering irons shall
be
isolated
from
the
power
line
by
transformer, or shall
be
direct current isolated.
The
soldering iron
must
be
grounded
and
have
a resistance of less
than 0.2
ohm
from
the
tip
to
ground
when
the iron
is
hot.
Test
equipment
shall
have
all
exposed
metallic surfaces
electrically
connected to the
test
equipment
power
system
ground
(through
200
ohms
or
less).
Do
not
use
rubber mats, carpets,
and
rugs
in the
work
station
area.
Use
grounded
conductive mats.
Do
not
allow
nonconductive
items
on
the
workbench.
This
includes
such
items
as
plastic
ash
trays, cellophane wrappers,
plastic
tools, styrofoam coffee cups, etc.
Maintain the relative
humidity
higher than
40
percent
(minimum)
in the
work
area.
Keep
all material
and
work
surfaces
CLEAN
in
the
work
area.
Wash
with
damp
cloth
when
necessary.
5-7
Dec/92
The document reference is online, please check the correspondence between the online documentation and the printed version.

BENDIX/KING
MAINTENANCE
MANUAL
IN-20258
MULTIFUNCTION
COLOR
INDICATOR
Keep
the
work
station
static-safe.
Periodically
check
the area
with
a
static
meter.
When
a
dangerous
reading
is
observed,
remove
the
nonconductor
or take precautions to prevent contact
with
ESDS
deviees.
(3)
Personne
1
When
handling
electrostatic
discharge sensitive deviees or
assemblies,
wear
a skin-contact wrist strap connected to the
work
station
common
ground.
WARNING:
DO
NOT
CONNECT
PERSONNEL
DIRECTLY
TO
EARTH
OR
BUILDING
GROUND.
COMMERCIAL
GROUNDING
STRAPS
CONTAIN
AN
INTERNAL
RESISTANCE
OF
ABOUT
ONE
MEGOHM
IN
THE
CORD
TO
BLEED
THE
ELECTROSTATIC
CHARGE
FROM
THE
BODY
WHILE
PROTECTING
PERSONNEL
FROM
ELECTRICAL
SHOCK.
DO
NOT
WEAR
GROUND
STRAP
WHEN
TROUBLESHOOTING
OR
TESTING
HIGH
VOLTAGE
CIRCUITS
WITH
POWER
APPLIED.
Do
not
wear
smocks,
gloves, finger cots, or sleeve protectors
made
of
plastic,
nylon, or rubber
in
the area
where
ESDS
deviees are handled.
When
the operator
is
properly
grounded,
contact with the
operator's
hand
will provide
sufficient
ground
for
hand
tools
or
ether tools that
may
be
electrically
isolated
from
ground.
(4)
Special Troubleshooting Precautions
In
addition to the
above
considerations, the following specifie
precautions
should
be
observed
when
troubleshooting or
repairing
modules
containing
ESDS
deviees.
Do
not
use
high
velocity
dry
air
for applying heat during
troubleshooting. Special infrared heat deviees should
be
used.
Do
not
use
Freon
spray during troubleshooting.
To
cool
components,
use
antistatic
quick-chill sprays.
Remember,
even
when
the
ESDS
deviee
is
installed
on
a printed
circuit
board
it
can
STILL
be
damaged
by
electrostatic
discharge.
C.
General
Repair
and
Replacement
Procedures
The
repair or replacement of
worn,
damaged
or defective parts
involves standard repair techniques.
1
1.8.
21400C
PART
4 5-8
Dec/92
The document reference is online, please check the correspondence between the online documentation and the printed version.

BENDIX/KING
MAINTENANCE
MANUAL
IN-20258
MULTIFUNCTION
COLOR
INDICATOR
Make
a wiring
diagram
or
sketch before
removal
of
any
part requ1r1ng
unsoldering
of
several
lead
wires.
Show
color
coding
or wire
marking
and
the
approximate
location
and
identify
of
the terminals
to
which
the wires are connected.
Also,
show
where
lacing
is
removed
or
where
dress is important.
Whenever
maintenance is
performed
on
the chassis cabling,
make
continuity checks throughout the cable to
check
that the cable
is
still
wired
correctly.
Refer
to the
main
frame
schematic
diagram
shown
in figure 7-1.
NOTE:
Always
add
a
small
amount
of rosin flux or rosin-core
solder while resoldering connections.
After replacing or repairing
any
printed
circuit
board
or assembly,
perform
the functional
test
in
PART
3 of
this
manual
to determine
proper operation of the repaired unit.
O.
Replacing Resistors, Capacitors
and
Diodes
(1}
Before
removing
diodes
or polarized capacitors
(electrolytics},
note
polarity
markings
and
orientation
on
circuit
board.
(2}
Using
a small cutting tool
(small
diagonal cutter}, carefully
eut
off
both
component
leads, leaving
about
1/16
inch
of
lead
protruding
from
circuit board.
Remove
component.
(3}
1
1.8.
21400C
PART
4
NOTE:
If
desired
to
disconnect only
one
lead for
component
substitution
(such
as
may
be
required during
troubleshooting}, refer to paragraph 4.0.(5}.
CAUTION:
DO
NOT
APPLY
HEAT
AT
A
PLATED-THRU-HOLE
FOR
MORE
THAN
8
SECONDS.
USE
20
TO
50
WATT
SOLDERING
IRON
ONLY.
Grasp
a eut
off
lead
(on
component
side of
board}
with
small
needle-nosed pliers.
Apply
soldering iron (with a
little
flux
on
the
tip)
to
circuit
board
where
lead passes through
circuit
board. Track side
can
also
be
used.
If
track side
is
used
for
unsoldering, ensure that the correct lead
and
circuit
board
point
is
located.
As
soon
as
solder melts, carefully
remove
cutoff lead
from
component
side.
If
excessive force
is
applied, the plated-thru-hole
may
be
pulled out of the
board
with the lead.
5-8.1
Dec/92
The document reference is online, please check the correspondence between the online documentation and the printed version.

BENDIX/KING
MAINTENANCE
MANUAL
IN-20258
MULTIFUNCTION
COLOR
INDICATOR
(4)
Using
soldering iron, reheat point
on
circuit
board
from
which
a lead
has
been
removed.
When
remaining
solder melts, apply
and
actuate solder sucker
to
remove
solder.
Repeat
for
remaining
lead.
Use
solder sucker
as
required until hales in
board
are clean (as indicated
by
no
solder
on
the walls, top,
or
bottom
of the hales in the
circuit
board).
NOTE:
Final cleaning (in the
circuit
board) will
be
done
just
prior
to
installing
new
component.
(5)
If
only
one
lead
is
being disconnected, for
component
substitution during troubleshooting, proceed
as
follows:
1
1.8.
21400C
PART
4
(a)
From
component
side, grasp lead close to
circuit
board
with
small
needle-nosed
pliers.
(b)
From
track side of
circuit
board,
heat point
on
circuit
board
where
lead passes
through
board.
When
solder melts,
carefully
lift
lead
upward
until lead
has
cleared
circuit
board.
(c)
Repeat
paragraph 4.0.(4}
and
ensure
that
all
solder
is
removed
from
hale.
5-8.2
Dec/92
The document reference is online, please check the correspondence between the online documentation and the printed version.

4.0.
(5)
(d)
~
General
Aviation
._..-
Avionics
Division
MAINTENANCE
MANUAL
IN-20258
MULTIFUNCTION
COLOR
INDICATOR
Replace
lead
as
instructed
in
procedures
in
paragraph
4.0.{13).
NOTE:
Do
not
bend
or
crimp
component
leads
ta
hold
component
in position prior to soldering.
It
is
recommended
that
component
leads
remain
straight
when
protruding
through board.
Keeping
the leads
straight
makes
component
replacement easier
and
prevents
damage
to
the
circuit
board
when
removing
components.
(6)
Bend
leads of
new
component
sa
that
component
fits
freely into
hales in
circuit
board.
(7)
If
component
has
polarity
markings
(electrolytics,
diodes), ensure
that
component
is oriented the
same
as
the
removed
component.
Insert
new
component
through
hales in
circuit
board.
Ensure
that
component
is
flush with
circuit
board
or
is
in
the
same
position
as
the
removed
component.
(8)
Use
flux
and
solder sparingly
and
solder the
component
to
circuit
board
from
the track side
of
the board.
Do
not
use
excessive
heat.
Ensure
that
position of
component
does
not
change
during
soldering.
(9) Carefully inspect solder
joints
ta
ensure that excess solder
has
not
been
used
and
that
no
short
circuits
are
in
evidence. Solder
should
fill
the
circuit
board
hale through
which
the
component
lead
is
inserted.
(10)
Using
small diagonal cutters or
end
nippers, snip excess leads
from
components.
(11)
If
more
than
one
component
is
being replaced, repeat the
above
paragraphs for
each
component.
(12)
When
all
components
have
been
replaced,
use
a small brush or pipe
cleaner
and
solvent to clean
new
solder
joints.
Ensure
that all
flux
and
solder rasin is
removed.
Use
a
round
toothpick to help
remove
heavy
deposits
of
rasin. Solder
joints
should
be
smooth,
bright,
and
clean
when
properly soldered
and
cleaned.
(13) Replace single lead
(from
component
on
which
one
lead
was
lifted
for substitution)
by
inserting lead through hale in
circuit
board
and
resoldering to board.
Use
flux
and
solder sparingly.
I.B.
21400C
PART
4
5-9
Jun/84
The document reference is online, please check the correspondence between the online documentation and the printed version.

4.
E.
~
General
Aviation
~
Avionics
Division
MAINTENANCE
MANUAL
IN-20258
MULTIFUNCTION
COLOR
INDICATOR
Replacing Semiconductors
on
Printed
Circuit
Boards
Never
remove
or
install
a semiconductor deviee with the supply voltage
turned on. Plugging-in or
removing
a
transistor
can
produce voltage
transients
that
might
damage
the deviee.
When
removing
or
installing
soldered-in diodes,
always
apply a heat
sink
between
semiconducting
body
and
solder terminal or standoff.
The
heat sink will
dissipate
heat
from
soldering iron
and
prevent diode
from
being
damaged.
Always
use
a
law
wattage soldering iron
and
apply
heat only
long
enough
to
make
a
good
solder
joint.
CAUTION:
DO
NOT
REMOVE
HEAT
SINK
UNTIL
SOLDER
JOINT
HAS
COOLEO.
(1)
Note
tab location, lead spacing, or lead
numbers
before
proceeding.
(2)
Grasp
the
component
with
two
fingers
and
alternately
apply
soldering iron with a
little
flux
on
the
tip
ta
each
component
lead, rocking
component
as
each
lead
becomes
unsoldered.
Do
not
overheat
circuit
board. Repeat,
alternately
heating leads
and
rocking
component
until
component
is
removed.
NOTE:
Acup-shaped desoldering
tip
can
be
used
with advantage,
simultaneously unsoldering
all
leads.
(3) Reheat
each
point
on
circuit
board
from
which
a lead
has
been
removed.
When
remaining solder melts,
use
solder sucker
as
required
until
hales in
board
are clean (as indicated
by
no
solder
on
the walls, top, or
bottom
of the hales
in
the
circuit
board).
(4)
Using
solvent
and
pipe cleaner
tip,
carefully
scrub bath sides of
the
circuit
board
(hales, pads,
etc.)
from
which
component
was
removed.
(5)
Insert
new
component
into hales
on
circuit
board ensuring
that
component
orientation
(transistor
tab,
etc.)
is
same
as
the
component
that
was
removed.
Ensure
that
component
height
above
(or flush with)
circuit
board
is
same
as
component
height
that
was
removed.
NOTE:
Do
not
bend
or
crimp
component
leads to
hold
component
in
position
prier
to soldering.
It
is
recommended
that
component
leads
remain
straight
when
protruding through
board.
Keeping
the leads
straight
makes
component
replacement
easier
and
prevents
damage
to the
circuit
board
when
removing
components.
I.B.
21400C
5-10
PART
4 Jun/84
The document reference is online, please check the correspondence between the online documentation and the printed version.

4.E.
(6)
(7)
(8)
(9)
(10)
General
Aviation
Avionics
Division
MAINTENANCE
MANUAL
IN-20258
MULTIFUNCTION
COLOR
INDICATOR
Use
flux
and
solder sparingly. Solder
component
to printed
circuit
board
from
track side of board.
Do
not
use
excessive heat
and
ensure that the position of
component
does
not
change
during
soldering.
Carefully inspect solder
joints
to ensure excess solder has not
been
used
and
that
no
short
circuits
are in evidence. Solder
should
fill
the
circuit
board
hole through
which
the
component
lead
is
inserted.
Using
small diagonal cutters or
end
nippers, snip excess leads
from
components.
If
more
than
one
component
is
being
replaced, repeat the preceding
procedures for
each
component.
When
all
components
have
been
replaced,
use
a small brush or pipe
cleaner
and
solvent to clean
new
solder
joints.
Ensure
that
all
flux
and
solder rosin is
removed.
Use
a
round
toothpick to help
remove
heavy
deposits of rosin. Solder
joints
should
be
smooth,
bright,
and
clean
when
properly soldered
and
cleaned.
F.
Replacing
Power
Transistors
(1)
Unsolder leads
and
remove
attaching hardware.
Remove
transistor
and
insulator.
NOTE:
A
plastic
insulator covers
each
power
transistor
on
the
rear heatsink.
Using
a
small
needle
nose
pliers,
pull out
the
plastic
plugs covering the
transistor
mounting
screws,
and
unscrew
the
mounting
screws.
(2)
Apply
Thermal
Joint
Compound
Type
120
(Wakefield Engineering,
Inc.} to
mounting
surface of
transistor
insulator
and
to
mounting
surface of replacement
transistor.
(3)
Reinstall
transistor
insulator
and
power
transistor
using
hardware
removed
in step (1).
NOTE:
Electrical contact to the
transistor
case
is
made
through
the
mounting
hardware
on
sorne
power
transistors.
Always
reinstall
the original hardware.
Do
not
omit
washers
and
spacers.
Torque
the
mounting
screws
to 3-to-6 inch
pounds.
(4)
After
installing
replacement
transistor,
but before
making
any
electrical
connections,
measure
resistance
between
case of
transistor
and
the chassis to ensure that insulation
is
effective.
The
resistance
measured
should
be
greater than
10
megohms.
(5)
Reconnect
leads to
transistor
and
solder
in
place.
I.B.
21400C
5-11
PART
4 Jun/84
The document reference is online, please check the correspondence between the online documentation and the printed version.

4.
~
General
Aviation
~
Avionics
Division
MAINTENANCE
MANUAL
IN-20258
MULTIFUNCTION
COLOR
INOICATOR
G.
Replacing
Multi-Lead
Components
(IC's,
etc)
(1) Preferred
Method
(a)
Remove
component
by
clipping
each
lead along
both
sides.
Clip off leads
as
close to the
component
as
possible.
Oiscard
component.
(b)
Heat
hole
from
track side
and
remove
clipped lead
from
each
ho
le.
(c)
Melt
the solder in
each
hole
and,
using a desoldering suction
tool,
remove
solder
from
each
hale.
(d)
Insert replacement
component
observing correct orientation.
CAUTION:
AVOlD
USE
OF
EXCESSIVE
HEAT.
(e) Solder
component
in
place
from
the track side of the board.
Avoid
solder runs.
No
solder is required
on
contacts
where
no
track
exists.
(2) Optional
Method
With
a
Pace
Madel
PRC-150
Bench-Top
Repair Center (Silver Spring,
Maryland),
any
multi-lead
component
can
be
quickly
and
easily
removed
without
damaging
the
component
or the
PC
board.
H.
Wiring
Repairs
NOTE:
When
necessary to disturb the dress of the wires, carefully
ensure that the original dress is maintained
when
replacing
wires.
Replace
damaged
wiring
with
same
size
wire
and
color code.
Ensure
that
no
bare wires are touching chassis, other
bare
wires,
metal
cases,
or
ether parts.
If
wire is
being
removed
from
a terminal or
component,
tag wire to
prevent incorrect connections.
I. Replacing
Ribbon
Cables
and
Connectors
The
connectors attached to the ribbon cables are not repairable.
The
cable
and
the connecter are a
molded
assembly.
Replace
the cable
assembly
with
the proper part
number
listed
in
Section
VI.
I.B.
21400C
PART
4
5-12
Jun/84
The document reference is online, please check the correspondence between the online documentation and the printed version.

4.H.
J.
~
General
Aviation
._.-
Avionics
Division
MAINTENANCE
MANUAL
IN-20256
MULTIFUNCTION
COLOR
INDICATOR
Replacing
Cathode-R~
Tube
If
the cathode-ray tube is
found
defective, replace
CRT
using,procedure
recommended
in
paragraph
S.M.
After replacement, perform the Overall
CRT
Alignment
procedure given in Section
IV.
K.
High-Voltage
Power
Supply
If
the high-voltage
power
supply
module
is
found
defective, replace
this
molded
component.
After replacement, perform the
High
Voltage
Power
Supply
adjustment
and
the Overall
CRT
Alignment
located
in
Section
IV
of
this
manual.
5.
Disassembly/Assembly
This paragraph provides disassembly instructions for the
IN-20256
Radar
Indicator.
Many
disassembly procedures contain
an
item
number
reference
in
parentheses following the part
noun
name
in
the procedure.
These
item
numbers
apply
to figure
6-1
PART
4, Parts List.
WARNING:
VOLTAGE
DANGEROUS
TO
LIFE
EXISTS
IN
THIS
EQUIPMENT.
REMOVE
ALL
POWER
FROM
THE
EQUIPMENT
BEFORE
PROCEEDING.
NOTE:
References to
left
side
and
right side
in
the following procedures
refers to your
left
or right side
when
looking at the front panel.
Assembly
is
in the reverse arder of disassembly unless otherwise
specified.
A.
Oust
Caver
Removal
(1}
Loosen
the
two
screws
in
the slotted hales,
one
on
each
side near
the
front.
(2) Release the
two
quarter-turn fasteners
on
the
rear,
near
each
si
de.
(3) Slide the dust caver
(2)
off the rear.
B.
Display
Board
and
Processor
Board
Removal
(1)
Remove
the dust caver (reference paragraph S.A.}.
(2)
Locate
the display
board
(166)
and
processor board
(170}
on
the
right side.
NOTE:
The
processor
board
is attached to the solder side of the
display
board
with six
screws
and
two
ribbon cables.
The
two
boards are
removed
together
from
the
frame
and
then
separated
if
desired.
I.B.
21400C
5-13
PART
4
Jun/84
The document reference is online, please check the correspondence between the online documentation and the printed version.

5.B.
~
General
Aviation
~
Avionics
Division
MAINTENANCE
MANUAL
IN-2025B
MULTIFUNCTION
COLOR
INOICATOR
{3)
There
are
11
screws
visible
on
the display board.
Only
five
screws
hold
the
boards
to the frame.
The
other six
screws
hold
the processor
board
to the display board. Refer to figure
5-1
and
remove
the five
screws
and
washers
holding the display board.
D
SCIEIS
"A"
HOLD
THE
IOAID
TO
TKE
FIAME.
&3109341
Display
Board
Removal
Figure
5-1
A
(4)
Tilt
the top of the boards
away
from
the
frame,
lift
the boards
away
from
the frame,
and
lay the boards
flat
on
the
bench.
{5)
Unplug
the
two
ribbon cable connectors
{P1024
and
Pl026)
from
the
bottom
edge
of
the display board.
(6)
Unplug
the ribbon cable connector
(P1023)
from
the
bottom
edge
of
the processor board.
(7)
Remove
the display
board
(with processor
board
attached)
from
the
frame.
{8)
To
separate the
two
boards,
remove
the six
screws
(171)
and
washers
holding
them
together
and
unplug·
the
two
ribbon cable
connectors
(P2022
and
P2029)
located
along
the top
edge
of
the
processor board.
1.B.
21400C
PART
4 5-14
Jun/84
The document reference is online, please check the correspondence between the online documentation and the printed version.

5.
~
General
Aviation
~
Avionics
Division
MAINTENANCE
MANUAL
IN-20258
MULTIFUNCTION
COLOR
INDICATOR
C.
Master/Slave Data
Board
Removal
(1)
Remove
the dust caver (reference paragraph S.A.).
(2)
Locate
the master/slave data
board
(7S)
on
the
left
side.
(3)
Remove
the
five
screws
(76)
and
washers
holding the
board
on
the
frame.
(4)
Tilt
the top of the
board
away
from
the
frame
and
lay the
board
on
the bench.
(5)
Unplug
the ribbon cable connecter
(P1111)
located near the
bottom
edge
and
remove
the
board
from
the indicator.
D.
Memory
Board
Removal
(1)
Remove
the dust caver (reference paragraph S.A.).
(2)
Place the indicator
on
its
top.
(3)
Locate
the
memory
board
(79)
on
the
bottom
of the indicator.
NOTE:
The
memory
board
is attached
by
four 5/8-inch-long screws
which
pass through bushings
on
the interconnect board
and
are threaded into the
mounting
plate
in
the
HV
power
supply
assembly.
(4)
Remove
the four 5/8-inch
screws
(80)
and
washers
securing the
memory
board.
(5)
Lift
the
rear
edge
of the
memory
board
away
from
the indicator.
(6)
Unplug
the ribbon cable connecter
(P6009)
from
interconnect board,
near
the
front
edge,
and
remove
the
memory
board.
The
ribbon
cable
is
soldered to the
memory
board.
E.
Sweep
Board
Removal
(1)
Remove
the dust caver (reference paragraph S.A.).
(2)
Locate
the
sweep
board
(143)
on
the top.
(3)
Remove
the four
screws
(144)
and
washers
holding the
board
on
the
main
frame.
(4)
From
the
rear,
remove
the three flat-head
screws
(147)
holding the
board-mounted
heatsink ta the rear panel (128).
I.B.
21400C
S-15
PART
4
Jun/84
The document reference is online, please check the correspondence between the online documentation and the printed version.

S.E.
(S)
(6)
~
General
Aviation
._..-
Avionics
Division
MAINTENANCE
MANUAL
IN-202SB
MULTIFUNCTION
COLOR
INDICATOR
Carefully
lift
up
the right side of the
sweep
board
from
the
main
frame
ta reach the cable connectors
on
the underneath side.
Carefully disconnect the five cable connectors
(P1002,
P1021,
P1022,
P1414,
and
P1013)
from
the
sweep
board,
and
remove
the
board
from
the indicator.
F.
Rear
Panel
and
Rear
Connecter
Board
Removal
NOTE:
The
rear panel
(128)
and
the rear connecter
board
(118)
are
constructed
as
an
assembly
(116)
and
are easily
removed
as
a
single unit.
(1)
Remove
the dust caver (reference paragraph S.A.).
(2)
On
the rear panel,
remove
the five flat-head
screws
(147)
along
the
top
edge.
NOTE:
The
three centermost
screws
attach ta the
heatsi~k
on
the
sweep
board.
(3)
On
the rear panel,
remove
the flat-head
screws
(117)
from
the
two
bottom
corners.
NOTE:
Before proceeding, observe the location of the
sponge
located
between
the rear connecter
board
and
the
"T"
board
(198).
The
sponge
must
be
replaced
in
the
same
position.
(4) Carefully
tilt
the top of the rear
panel
away
from
the frame.
(5)
Unplug
the 20-pin ribbon cable connecter (Pl006)
from
the
rear
connecter board.
The
connecter
is
located
along
the side of the
board.
(6)
Unplug
the 2-wire connecter
(P1019)
from
the rear connecter board.
This
cable connects to the
neck
coil
on
the
CRT.
(7)
Unplug
the 40-pin ribbon cable connecter
(P1007)
from
the
bottom
edge
of the rear connecter board.
NOTE:
This cable
can
also
be
unplugged
from
the interconnect
board
(Pl008).
(8)
Unplug
the 4-pin connecter
PSOOS
from
the rear connecter board.
This
connecter
has
two
wires attached
which
may
also
be
unplugged
from
the interconnect
board
{P5001).
(9)
The
rear panel
assembly
is
still
attached
by
a
ground
wire to the
"T
11
board
on
the
CRT
socket. Carefu
lly
pu
11
the
grou
nd
wi
re
from
the
push-on
pin located near the
bottom
edge
of the
..
T
..
board.
Refer
to figure 5-2.
I.B.
21400C
5-16
PART
4 Jun/84
The document reference is online, please check the correspondence between the online documentation and the printed version.

ÂLILIEI) Bendix
~
Aerospace
Bendix
General
Aviation
Avionics
Division
S.F.
MAINTENANCE
MANUAL
IN-2025B
MULTIFUNCTION
COLOR
INDICATOR
(10)
Remove
the rear
panel
and
connecter
board
assembly.
NOTE:
Completely
removing
the rear
panel
from
the connecter
board
requires unsoldering the items
mounted
on
the rear
panel
(heatsink),
or
unmounting
them.
However,
the
panel
and
connecter
board
may
be
partially
separated for service
as
follows.
(11)
On
the rear panel,
remove
the four flat-head
screws
around
P5005,
and
remove
the four flat-head
screws
around
P5004.
(12)
Observe
the
two
slots in the top
edge
of the rear panel.
Remove
the flat-head
screw
located near the
bottom
of
each
slot.
A
eut-out in the black heatsink
is
provided for access to the
screws.
(13) Pivot the
bottom
of the connector
board
away
from
the rear
panel
to obtain access to the other side.
Be
careful to
avoid
breaking
the wires soldered to the board.
(14)
When
replacing the rear
panel
assembly,
it
may
be
necessary to
unp
1
ug
the
11
T"
board
when
reconnecti
ng
the
pus
h-on
whi
te-b
1
ack
ground
wire to the
"T"
board.
Be
sure to replace the
sponge
between
the
"T"
board
and
the
connec
tor
board.
NOTE:
The
small
two-wire connector
(P1019)
from
the
CRT
neck
coil
(192)
is
not
keyed,
but
is
wired
so
it
may
be
installed
in
any
position. Polarity
does
not
have
to
be
considered
when
plugging the connector
onto
the board.
G.
Removi
ng
the
"T
11
Board
(1)
Remove
the dust caver (reference paragraph S.A.).
(2) Refer to steps
(2)
through
(9)
in
paragraph
5.F.,
and
remove
the
rear
panel
assembly.
NOTE:
It
is
not
necessary to separate the rear
panel
from
the
rear connector board.
(3) Locate the
"T"
board
plugged
onto
the
CRT
base.
NOTE:
The
"T
11
board
contains the socket
(XV
1001)
for the
CRT.
(4) Carefully pull the
"T"
board
straight
back
and
unplug
it
from
the
CRT.
I.B.
21400C
5-17
PART
4
Mar/86
The document reference is online, please check the correspondence between the online documentation and the printed version.

5.G.
(5)
~
General
Aviation
_..-
Avionics
Division
MAINTENANCE
MANUAL
IN-20258
MULTIFUNCTION
COLOR
INDICATOR
Observe
that there are three wires with
push-on
pins,
one
two-wire
connecter,
and
one
ribbon cable connecter
plugged
into the
11
T
11
board.
CAUTION:
The
three
push-on
pins
on
the
11
T
11
board
are not keyed,
but the wires are color coded.
They
must
be
connected
to the proper pins. Refer to figure 5-2.
(6)
Unplug
the three wires connected to the
11
T"
board
with
push-on
pins at El,
E2,
E3.
Refer to figure 5-2.
(7)
Unplug
connectors
Pl020
and
Pl415
from
the
np
board,
and
remove
the board.
(8)
When
replacing the
"T
11
board,
refer
to figure
5-2
for board
orientation
and
location of the
three
wires
with
push-on
connecter
pins. Also, observe
that
the two-wire connecter
(P1415)
has
four
pins
and
may
be
plugged
into the board without concern for
key
positions.
CAUTION:
Don•t
forget to properly position the
sponge
between
the
"T"
board
and
the
rear
connecter
board
before
installing
the rear panel assembly.
VIOLET
WIRE
TO
POWER
SUPPLY
HOOULE
Al
A3613718
·.
··
....
..........
··.
,.------,
1 1
1 1
L--
---..1
WHT-BLK
WIRE
(GND)
TO
REAR
COHNECTOR
~D
Pl020
TO
SWEEP
BOARD
CRT
SOCKET
XVlOOl
Pl415
2
WIRES
TO
POWER
SUPPLY
BLACK
OR
RED
WIRE
TO
POWER
SUPPL
Y
HOOULE
Al
Connections to
11
T
11
Board,
Rear
View
Figure 5-2
I.B.
21400C
PART
4 5-18
Jun/84
. : .
The document reference is online, please check the correspondence between the online documentation and the printed version.
Table of contents
Other BENDIX Measuring Instrument manuals
Popular Measuring Instrument manuals by other brands
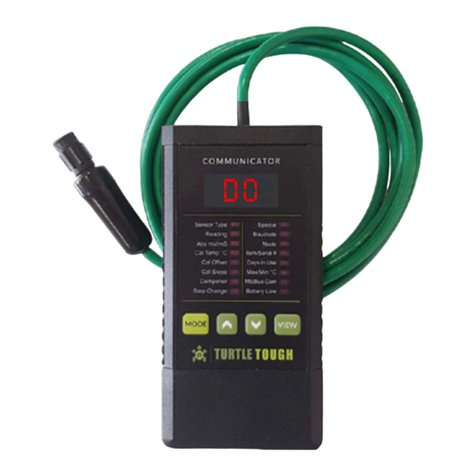
Turtle Tough
Turtle Tough DSS HandHeld FIELD Communicator manual
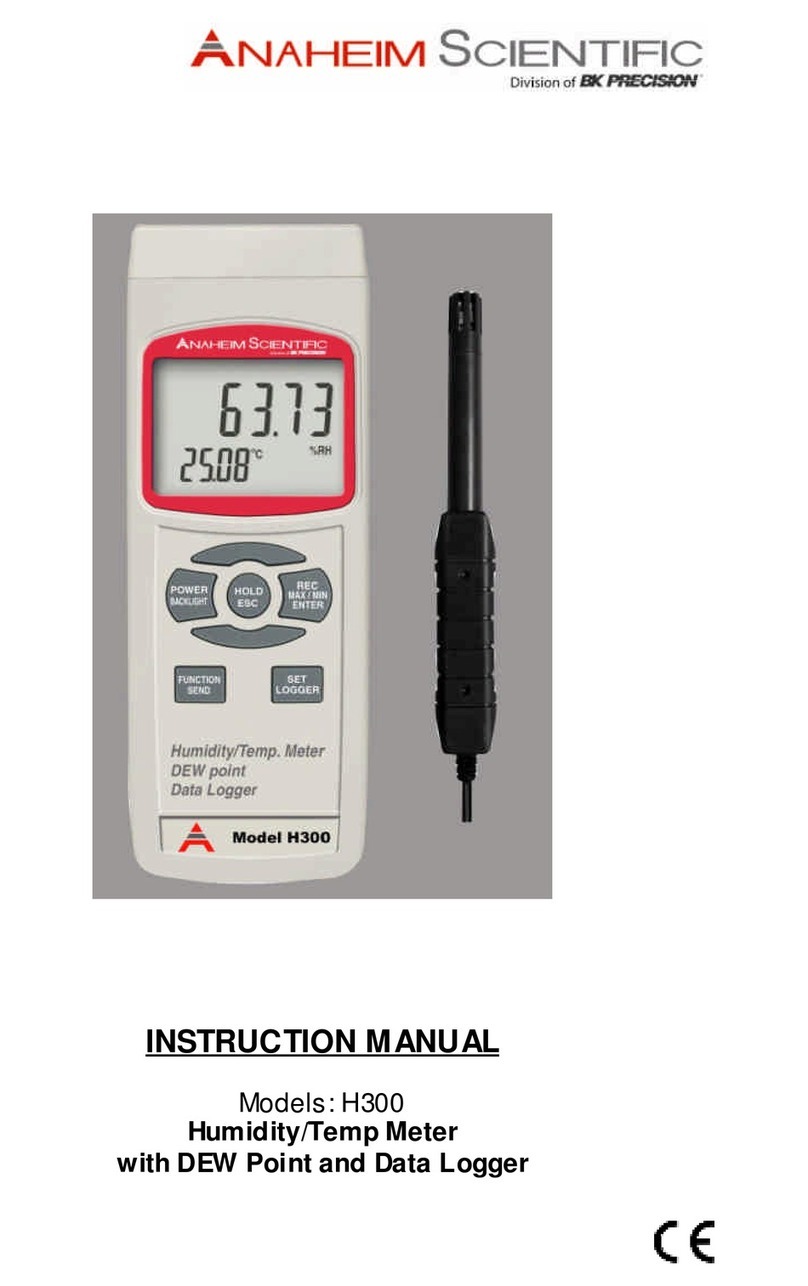
Anaheim Automation
Anaheim Automation H300 instruction manual

Dräger
Dräger Polytron 5200 Instructions for use
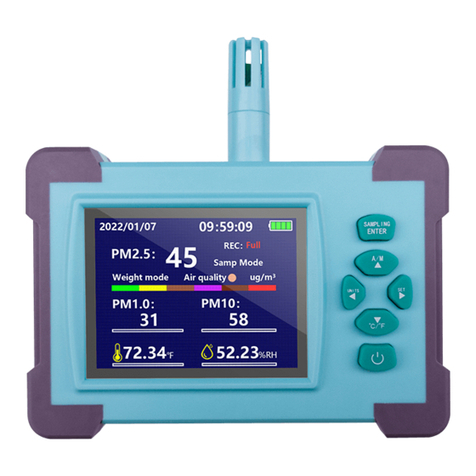
Deyi
Deyi SR-516A manual
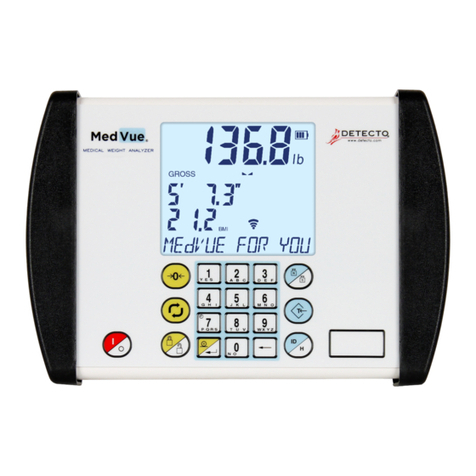
Detecto
Detecto MedVue MVWIFI Installation, configuration, and operation manual

Endress+Hauser
Endress+Hauser Levelflex FMP56 operating instructions