BERG KOMPBERG BSDF Series Operating instructions

09.2019
OPERATING AND MAINTENANCE MANUAL
Screw compressors
KOMPBERG®BSDF
PART I

Operating and Maintenance Manual 09/2019 –part I
Screw compressors
2
Ladies and Gentlemen,
We heartily welcome you among our valued Customers and thank you for your trust
to purchase the BERG compressor.
We are sure you will be fully satisfied with both the choice you have made and
the cooperation you started with us. Our compressors are machines of top quality,
which is the guarantee for a long years and reliable performance.
Our sales and service staff is available to answer all your queries regarding the
installation and operation of your compressor. You are also encouraged to use our
warranty and post-warranty technical service.

Operating and Maintenance Manual 09/2019 –part I
Screw compressors
3
1. Information concerning the document...................................................................5
1.1. Scope and intended use of the manual.......................................................................5
1.2. Intended use of the compressor and conditions of safe use........................................5
1.3. Qualification requirements for operation of the compressor........................................6
1.4. Operation....................................................................................................................6
1.5. Other remarks and instructions...................................................................................7
1.6. Warranty.....................................................................................................................7
2. Operating safety rules...........................................................................................7
2.1. Basic requirements for safe transport and positioning of the screw compressor .........8
2.2. Operating safety requirements....................................................................................9
2.3. Other hazards.............................................................................................................9
2.4. Meaning of pictograms..............................................................................................10
3. Identification plate...............................................................................................10
4. Setting ................................................................................................................11
4.1. Room requirements ..................................................................................................11
4.2. Requirements concerning electrical system..............................................................11
4.3. Compressed air connection ......................................................................................13
4.4. Compressed air treatment ........................................................................................13
5. Operation description of the screw compressor..................................................14
5.1. Operation description of the screw compressors with microprocessor controller.......14
5.2. Operation description of the screw compressors with inverter...................................15
5.3. ULTRA SPEED function –in screw compressors with motor power of 5.5 kW - 90 kW
and frequency converter..................................................................................................16
5.4 Description of the compressed air treatment system..................................................16
6. Start-up...............................................................................................................18
6.1. Start-up preparation..................................................................................................18
6.2. Restart (after longer downtime).................................................................................19
7. Procedure in case of compressor self-deactivation or shut down by using the
emergancy stop......................................................................................................19
8. Maintenance.......................................................................................................20
8.1 General requirements................................................................................................20
8.2. Maintenance and inspections....................................................................................21
8.2.1. Maintenance at the beginning of the compressor use and after oil and V-belts
(where applicable) change...........................................................................................21
8.2.2 Daily maintenance.............................................................................................21
8.2.3 Periodic maintenance........................................................................................21
8.2.4 Warranty and post-warranty inspections............................................................22
8.2.5 General remarks................................................................................................23
8.3 Basic components requiring maintenance and descriptions of maintenance
operations........................................................................................................................24
8.3.1. Air filter cartridge ...............................................................................................24
8.3.2. Filter mat ..........................................................................................................25
8.3.3. Oil filter..............................................................................................................26
8.3.4. Oil separator......................................................................................................26
8.3.5. Oil level..............................................................................................................28
8.3.6. Water condensate draining................................................................................29
8.3.7. Oil change and recommendations concerning oil...............................................29
8.3.8. Handling wastes produced while operating the compressors............................30
8.3.9 Pressure switch.................................................................................................30
8.3.10Oil temperature gauge(where applicable)..........................................................31

Operating and Maintenance Manual 09/2019 –part I
Screw compressors
4
8.3.11 Oil cooler / air cooler.........................................................................................31
8.3.12. Electric motor...................................................................................................31
8.3.13. Safety valve.....................................................................................................32
8.3.14 Radial / axial fan...............................................................................................34
9.Troubleshooting.....................................................................................................36
10. Appendices.......................................................................................................39
10.1. Compressor with the heating system–guidelines concerning operation ..................39
10.2. Compressor with additional water cooling...............................................................40
10.2.1. Water connection.............................................................................................40
10.2.2. Description of construction and operation of the screw compressors with
additional water cooling (complement to the description in section 5 ).........................40
11.Condensate drains ............................................................................................41
Condensate drains in the compressors on the air receiver models..................................41

Operating and Maintenance Manual 09/2019 –part I
Screw compressors
5
1. Information concerning the document
This operating and maintenance manual is an integral part of the machine. It includes the
information necessary to start, operate and maintain the compressor and requirements for
its safe operation.
Following the manual rules will help you:
Avoid hazards,
Reduce repair costs and downtime,
Increase the machine reliability and life.
Getting familiar with this manual in detail, using the machine in accordance with
descriptions included in it and following all safety conditions are the basis for correct and
safe operation of the machine.
In addition to the operating and maintenance manual and the regulations applied in the
country of destination and health and safety at work regulations applied locally at the
workstation, the generally recognised technical rules for safe and correct work are also
valid.
1.1. Scope and intended use of the manual
The operating and maintenance manual is intended for qualified / suitably trained operating
personnel of the compressor. The personnel assigned to operation of the compressor must,
before starting work, get familiar with the manual contents, in particular the “Health and
safety at work regulations” section.
The manual includes
Description of daily service and maintenance of the compressor and control system,
Technical documentation of the electrical part. It includes the data necessary to perform
correct connections and repairs of the electrical equipment,
Technical documentation of the mechanical part. It includes the data necessary to perform
repairs of the mechanical equipment,
Technical documentation of the control system. It includes the data necessary to switch on
and off, and set operating parameters of the compressor.
The qualified personnel is understood to be the persons who because of received training,
experience and knowledge of important standards, documentation and regulations
concerning safety and operating conditions were authorised to carry out necessary
operations and are able to recognise and avoid possible hazards.
1.2. Intended use of the compressor and conditions of safe use
The compressor is designed to produce only compressed air. It should be installed in
accordance with the stipulations concerning the compressor installation and connection.
The compressor must not be used for any other purposes that are non-compliant with its
intended use. The manufacturer shall not be liable for any damage resulting from that
reason. In that case, the risk is born by the machine user only.
During the compressor operation, you must follow the procedures given in the
“Maintenance” section as regards scope and frequency of maintenance work and materials
to be used.

Operating and Maintenance Manual 09/2019 –part I
Screw compressors
6
Warning bout forbidden use
The compressor must not be used for any other purposes that are non-compliant with its
intended use.
Under no circumstances must the limit operating parameters of the compressor be
exceeded and changed - refer to section 10 "Technical data".
To use it for compression of other gases than air, it is required to obtain the manufacturer’s
consent. The above consent must be in written form.
The compressor must not be used in potentially explosive atmospheres within the meaning
of Directive 2014/34/EU.
The compressor must not suck any toxic, acid-containing, flammable or explosive gases
and vapours.
Never direct a jet of compressed air at people or animals.
Safe use of the compressor
The compressor must be operated in accordance with all guidelines included in this
operating and maintenance manual.
The sucked air must be clean and must not contain any harmful substances.
The heated cooling air may be used for heating purposes if only its harmfulness to people
and animals is excluded. Otherwise, it is necessary to provide the appropriate treatment of
cooling air.
Compressed air may only be used for breathing after its appropriate treatment.
Compressed air not subjected to the appropriate treatment must not be used in production
processes in which there is contact of air with food.
The compressor delivered is designed to compress only air. To use it for
compression of other gases, it is required to obtain the manufacturer’s consent. The
above consent must be in written form. The compressor must not be used for any
other purposes that are non-compliant with its intended use.
Fulfil the obligation to register the compressor air receiver in the Office of Technical
Inspection (UDT).The compressor documentation is accompanied by the set of the
required documentation of the air receiver (if applicable) and safety valve.
1.3. Qualification requirements for operation of the compressor.
The personnel who installs, operates and maintains the compressor should have the
appropriate education and qualifications enabling safe operation of electro technical and
electrical equipment.
Installation, operation and maintenance of the compressor may only be carried out by the
persons who are familiar with this operating and maintenance manual, follow instructions
included in it, know safety regulations and recognised technical rules.
1.4. Operation
While operating the compressor:
-Observe the instructions provided in the Operating and Maintenance Manual and Warranty
Book.
-Follow the periodic inspection schedule during both warranty period and after its completion.
Regular performance of periodic inspections is necessary to ensure the required reliability
and life of the BERG equipment. The inspections performed according the schedule reduce
the number of repairs and their cost.
-The technical and operating inspections should be carried out in accordance with the
schedule and conditions by the factory service or authorised service, using the
manufacturer’s consumables and spare parts.
-During the warranty period, use only the manufacturer’s consumables and spare parts.

Operating and Maintenance Manual 09/2019 –part I
Screw compressors
7
The detailed list of maintenance operations can be found in the "Maintenance
and inspections" section.
1.5. Other remarks and instructions
-This Operating and Maintenance Manual provides all information on how to install, start and
operate the compressor. This manual should also be used when any maintenance work is
carried out,
-The Manual should be read and always available to the compressor operator,
-During the maintenance work and periodic inspections, the provisions of the Warranty Book
should be observed,
-The Maintenance section provides all measures and requirements necessary to keep the
compressor in a correct technical state,
-Record all operating data, maintenance operations performed etc. into the Warranty Book.
Observe all reference and local safety regulations relating to the compressor, including
those listed herein and in the following sections,
-Failure to follow the requirements included in this Operating and Maintenance Manual and
Warranty Book and/or unauthorised changes in the compressor or its integral units
delivered by us shall make the warranty null and void.
-During warranty period, any repairs must be performed by the manufacturer service or
authorised service centre listed in the Warranty Book.
1.6. Warranty
BERG KOMPRESSOREN GmbH hereinafter referred to as the Warrantor provides the
warranty for the products sold, ensures correct operation of the offered products provided
that they are used in accordance with their intended use and operating conditions specified
in this documentation.
The Purchaser shall lose its warranty rights for the product when:
-The machine is used in a way non-compliant with its intended use,
-Unauthorised modifications are carried out on the product,
-Interventions are carried out by unauthorised persons,
-Any repair attempts are carried out by unauthorised persons,
-The obligation to carry out periodic inspections is not observed,
-Non-original consumables are used.
The manufacturer reserves the right to make modifications in the product,
resulting from continuous technical development, without prior notice.
2. Operating safety rules
The present rules are valid for BERG screw compressors. In addition to the general health
and safety at work and the Office of Technical Inspection (UDT) regulations applicable to
compressors, their assemblies and accessories, the safety instructions given below should
be followed in particular. The operators are supposed to observe safe work practices. It is
the user’s responsibility to continuously maintain the compressor fully operable.
Components and equipment considered to be no longer suitable for safe operation should
be promptly replaced. Adjustments, installation, operation, maintenance and servicing
should be entrusted only to properly trained, qualified and authorized staff.
The limit values (pressure, temperature, time settings etc.) are given in the Technical Data
section.
The limit values may not be changed by the user.
The manufacturer accepts no responsibility for any personal injuries, damage of equipment
or the compressor itself, at present and in the future, resulting from user’s negligence and
failure to observe the installation, operation and maintenance requirements contained

Operating and Maintenance Manual 09/2019 –part I
Screw compressors
8
herein. No responsibility is also taken for failure to observe valid safety standards relating
to the equipment and qualified staff.
2.1. Basic requirements for safe transport and positioning of the screw
compressor
In addition to the general health and safety at work and the Office of Technical Inspection
(UDT) regulations, the following rules must be observed:
-Use only the lifting equipment that is compliant with the H&S and UDT regulations to lift the
compressor. Fix in place all rotating or loose parts of the machine before its lifting. It is
strictly forbidden to stay in the hazardous zone of the lifting equipment operation. The
compressor movement can be accelerated or slowed down only within the permissible
limits.
-When the compressor is transported, the transport straps should be pulled under the
machine and secured above the housing in such a way that they do not place pressure on
it. If the transport harness is fastened and secured incorrectly, the machine may get
damaged.
-If the compressor is transported on wooden pallets, it should be secured against movement
during transport. Fasten the compressor frame with cargo straps to appropriate holders on
the vehicle platform to prevent it from sliding or overturning.
-All screw and pipe connections should be of appropriate size and designed for a given
operating pressure.
-The compressor is not designed to operate outdoors; it cannot be exposed to weather
conditions.
-The compressor should be positioned in a closed room, where ambient air is cool and
clean. Never block air flow to and from the room. Ensure sufficient inflow of cooling air and
discharge of hot air outside the room. Temperature in a room with the compressor should
be within the range of + 5C to + 40C.
-The air sucked in should contain no vapours or flammable gases, e.g. paint thinners, that
might cause internal fire.
-There can be no objects close to the air inlet that could be sucked in with a jet of air.
-The pressure conduit connecting the compressor with the compressed air line should allow
free expansion due to generated heat. It must not touch hot objects or flammable materials.
The detailed requirements concerning the machine positioning in the compressor room are
described in section 4.1.
Fig. 1 Transport of the machine with a
forklift.

Operating and Maintenance Manual 09/2019 –part I
Screw compressors
9
2.2. Operating safety requirements
In addition to the requirements contained in the sections: Screw compressor operation
description; Start up; Maintenance; the following rules should be observed.
-The compressor is only designed to compress air.
-All safety equipment must be in place while operating the machine.
-The factory-mounted safety equipment must not be removed. Please, remember to remove
any transport brackets (if applicable)before first start-up of the compressor. The transport
brackets are only used to protect the machine during transport.
-There are hot parts in the compressor e.g. conduits, air and oil coolers, screw block. They
will scald when touched.
-No unauthorized modifications in the control system are allowed. After power failure,
the compressor must be restarted when the power supply is recovered.
-It is prohibited to remove the green and yellow protective conductors that prevent electric
shock.
-No additional equipment can be mounted on the air receiver(except for the equipment
allowed for use by the manufacturer).
-No welding operations or any other repairs can be performed on the air receiver.
-The plugs and other air receiver accessories can only be removed after the air receiver
depressurisation to the ambient pressure.
-General safety rules should be observed while depressurising the air receiver. Air must be
vented slowly. Keep the air stream away from people.
-Do not allow oil spill around the compressor.
-It is strictly prohibited to service the safety valves or to change their settings.
-Do not change settings of the pressure switches above the value given in the identification
plate or in the Operating and Maintenance Manual.
-Fulfil the obligation to register the compressor air receiver in the Office of Technical
Inspection (UDT). Two sets of the required documents of the air tank (if provided) and
safety valve are included with the compressor documentation. The compressor
documentation is accompanied by the set of the required documentation of the air receiver
(if applicable) and safety valve.
-Do not remove the temperature sensor (transmitter) or pressure transmitter.
2.3. Other hazards
The compressor installation, switching on/off and maintenance must be carried out by the
qualified personnel who strictly follows the data included in the product technical
documentation and safety rules to avoid any hazards. The risks that could not have been
eliminated during the design stage are described in the table below.
Fig. 2 Transport of the machine with a
crane.

Operating and Maintenance Manual 09/2019 –part I
Screw compressors
10
Unit
Residual risk
Action
Precautions
Air cooler, guard,
frame
Minor cuts
Touching
Avoid touching, wear
protective gloves.
Fan guard and fan
Injuries
Inserting sharp
objects through the
protection mesh
when the fan is
running.
Do not insert any objects
through the protection
mesh and do not put any
objects on it.
Screw block, oil tank,
end cooler, pressure
conduits
Danger of scalds
Touching
Avoid touching, wear
protective gloves.
Metal parts and
electric cables
Electric shock
Damage of electric
cable insulation
upstream the motor
breaker, live metal
parts
Suitable guard for the
power supply cable;
check the cable insulation
for damage.
2.4. Meaning of pictograms
Pictograms (safety symbols) located on and inside the compressor are described below.
Explanation is provided below any of them.
For technical reasons, it is not always possible to attach the pictograms in the very vicinity
of the points of risk.
3. Identification plate
The identification plate as shown below is attached to the compressor housing or frame.
When contacting us regarding your compressor, please provide the data given on the
identification plate: compressor type, year of manufacture and factory number.
AUTOMATIC MACHINERY
MAY START
RISK OF SCALDING
RISK OF ELECTRIC
SHOCK

OperatingandMaintenanceManual 09/2019 –part I
Screwcompressors 11
4. Setting
4.1. Room requirements
-The compressor requires no foundations. It must be positioned on a hard and even surface.
Take into consideration the floor load capacity, if the machine is installed in a building.
-Strictly observe the minimum distances from walls and other machines. When several
compressors are installed, pay attention to the direction of cooling air flow; no compressor
should suck air which is heated by other machine. Minimum distances from the room walls
and other objects are given in the drawings below.
-Protect the room in which the compressor is installed from negative temperatures.
The inlets and outlets to and from the room should be located in such a manner to protect
the interior from weather conditions.
-Heat generated during compression should be extracted outside (or to other rooms), and
fresh air should be supplied from the outside.
-If the gravity ventilation is insufficient (windows, openings in a wall etc.) in the compressor
room, air exchange should be provided by fans. To ensure correct heat extraction, the fans
should have total capacity about 15 to 20% higher than the total cooling air requirement for
all compressors installed in the room. The required cooling air volume is specified in the
Technical Data section.
-Ambient temperature in the room should be from + 5C to +40C.
-Provide sufficient room for maintenance operations.
-It is necessary to consult our specialists when you want to install a duct supplying air from
the outside or use air for heating the rooms.
-The compressor room should be well lighted to ensure trouble-free and safe service of the
equipment.
-To improve ventilation in the compressor room, the machine can be connected to the
discharge air duct; in such case, please contact BERG.
The suitable ventilation in a room will prevent the possibility of negative pressure generation
or undesired temperature increase.
When there are any problems in ensuring the suitable ventilation in a room, please contact
BERG.
4.2. Requirements concerning electrical system
-The compressors (as a standard) are designed to be supplied by a four-conductor 400 V
AC, 50 Hz power line.
-The compressors are equipped with PE terminal.
-The power cable cross sectional area should be matched to the current drawn by the
compressor.
-The compressors can only be operated on three-phase earthed system (TN).
Fig. 3 Compressors with motor power
from 30 kW to 55 kW. Fig. 4 Compressors with motor power
from 75 kW to 315 kW.

Operating and Maintenance Manual 09/2019 –part I
Screw compressors
12
-The compressor must be supplied from the distribution board equipped with a slow blow
fuse and circuit-breaker that enables the compressor power supply to be completely
disconnected.
-Electrical connection of the compressor should be performed in accordance with the
attached electrical diagram.
-Only authorised personnel or qualified electrician is allowed to perform electrical
connections.
-Use the required safety measures in accordance with the suitable regulations.
-Calculate the power cable cross sectional area and fuse sizes according to the local
regulations and operating conditions.
-Below there are presented the recommended power cable cross sectional areas and fuse
sizes for standard compressors.
-A user takes a full responsibility for selection of an electrical system and power supply
connection for the compressor.
Recommended power cable cross sectional area and fuse sizes
Item
Compressor type
Recommended power
cable cross sectional
area
Fuse size
NH gL/gG, 500V, 100kA
mm2
D gL/gG, 500V, 50kA
1
KOMPBERG
BSDF 30
3x25+PE
80
2
KOMPBERG
BSDF 37
3x35+PE
100
3
KOMPBERG
BSDF 45
3x50+PE
125
4
KOMPBERG
BSDF 55
3x50+PE
125
5
KOMPBERG
BSDF 75
3x70+PE
160
6
KOMPBERG
BSDF 90
3x95+PE
200
7
KOMPBERG
BSDF 110
3x120+PE
250
8
KOMPBERG
BSDF 132
3x150+PE
315
9
KOMPBERG
BSDF 160
3x240+PE
400
10
KOMPBERG
BSDF 200
3x300+PE
500
11
KOMPBERG
BSDF 250
2x(3x185)+PE
630
12
KOMPBERG
BSDF 315
2x(3x240)+PE
800

Operating and Maintenance Manual 09/2019 –part I
Screw compressors
13
4.3. Compressed air connection
It is recommended to use galvanized steel or plastic tubes for the
compressed air system.
When the compressed air treatment equipment (filters, dryer) is installed, the
existing compressed air piping should be replaced with a new one, unless
air supplied previously was treated by similar equipment.
Each BERG compressor should be connected to the compressed air network
by using a flexible conduit or flexible connector (axial expansion joint) and
shut-off valve.
4.4. Compressed air treatment
Depending on the required quality of compressed air, some compressed air treatment
equipment such as water separators, filters or dryer should be additionally installed
downstream the compressor.
Our specialists will select the appropriate equipment free of charge.
Fig.5 Compressed air connection - compressors with motor power 30 kW up to 160 kW.
Fig.6 Compressed air connection - compressors with motor power from 200 kW.
Elbow
Connector
Pneumatic hose
Outlet flange
Rubber flanged
expansion joint
Delivery manifold

Operating and Maintenance Manual 09/2019 –part I
Screw compressors
14
5. Operation description of the screw compressor
5.1. Operation description of the screw compressors with microprocessor
controller
The compressor is started by pressing the START button on the controller. When the button
is pressed, the compressor drive is started (the start can be delayed). During the initial
start-up phase, the motor operates in the star configuration. When it is switched to the delta
configuration, the solenoid valve which controls the suction regulator operation is
energised, and compressed air is supplied to the actuator of the suction regulator. After a
few seconds, needed for overpressure to be generated (approx. 0.2 MPa), the suction
regulator opens in the suction regulator actuator. The ambient air, sucked through the air
filter, flows into the screw block in which it is compressed. All the time the compressor is
running, oil is injected into the screw block to provide lubrication, cooling and sealing. When
the appropriate pressure (approx. 0.5 MPa) is reached in the pre-separator or the oil tank,
the minimum pressure valve is opened and compressed air is delivered to the compressed
air system. The minimum pressure valve functions also as the check valve. When
compressed air is being delivered, this valve maintains the minimum overpressure (approx.
0.5 MPa) in the oil system, that is necessary to ensure correct lubrication and cooling.
The oil contained in the air being delivered is separated:
-initially in the pre-separator or inside the oil tank,
-precisely in the oil separator.
The oil flows from the screw block via the thermostat to the oil cooler, and then returns via
the oil filter to the screw block.
The treated compressed air flows through the minimum pressure valve to the end cooler,
and then to the compressed air receiver.
The compressor is adapted to intermittent operation. The intermittent operation involves
delivery of compressed air until the maximum overpressure set in the controller is reached.
On reaching that pressure, the solenoid valve which controls the suction regulator
operation is de-energised, or power supply is switched on and, consequently, the suction
regulator is closed. The compressor switches to the so-called idle run, the overpressure in
the screw block drops down to the value of approx. 0.2 MPa which ensures sufficient
injection of oil into the screw block. When the idle run time (3 - 5 minutes) set in the
controller elapses, the motor power supply is turned off and the compressor switches to
the stand-by mode.
The compressor is restarted when the overpressure in the system drops to the minimum
value set in the controller.
The compressor operation can be stopped at any time by pressing the STOP button on the
control panel.
The operation is resumed by pressing the START button.
When the overpressure in the system exceeds the start value set in the controller on the
compressor start, the compressor will start only after the overpressure drops to the set
minimum value.
When the compressor is stopped by pressing the EMERGENCY STOP (STOP
AWARYJNY) button and when the power returns after a power supply failure, the
compressor can be started by resetting the EMERGENCY STOP button and pressing
the OPERATION button.
The microprocessor controller has an additional function, preventing the compressor from
starting under pressure, by measuring the time necessary to unload pressure from the
screw block.

Operating and Maintenance Manual 09/2019 –part I
Screw compressors
15
5.2. Operation description of the screw compressors with inverter
The compressor is started by pressing the START button on the controller - it is not
necessary to start the inverter separately. When the button is pressed, the compressor
drive is started. After a few seconds delay, the solenoid valve which controls the suction
regulator is energized, and compressed air is supplied to the suction regulator actuator.
After a few seconds, needed for overpressure to be generated (approx. 0.2 MPa), the
suction regulator opens in the suction regulator actuator. The ambient air, sucked through
the air filter, flows into the screw block in which it is compressed. All the time the
compressor is running, oil is injected into the screw block to provide lubrication, cooling and
sealing. When the appropriate pressure (approx. 0.5 MPa) is reached in the pre-separator
or the oil tank, the minimum pressure valve is opened and compressed air is delivered to
the compressed air system. The minimum pressure valve functions also as the check valve.
When compressed air is being delivered, this valve maintains the minimum overpressure
(approx. 0.5 MPa) in the screw block, pre-separator or oil tank, that is necessary to ensure
correct lubrication and cooling.
The oil contained in the air being delivered is separated:
-initially in the pre-separator or inside the oil tank,
-precisely in the oil separator.
The oil flows from the screw block via the thermostat to the oil cooler, and then returns via
the oil filter to the screw block.
The treated compressed air flows through the minimum pressure valve to the end cooler,
and then to the compressed air receiver.
The compressor responds to the compressed air requirement by increasing/decreasing the
motor speed when the pressure decreases/increases. When the maximum operating
pressure is reached, the motor speed decreases to the minimum one (as set in the inverter
controller).If no compressed air is drawn, the suction regulator closes and the compressor
operates in idle run. If no compressed air is drawn, the drive will switch off after approx. 3
to 5 minutes. The compressor switches to the stand-by mode. During the idle run, the
overpressure inside the screw block or oil tank drops down to the value of approx. 0.2 MPa
which ensures sufficient injection of oil into the screw block. The compressor is restarted
when the overpressure in the system drops to the minimum value set in the controller.
The compressor operation can be stopped at any time by pressing the STOP button on the
control panel.
The operation is resumed by pressing the START button.
When the overpressure in the system exceeds the start value set in the controller on the
compressor start, the compressor will start only after the overpressure drops to the set
minimum value.
When the compressor is stopped by pressing the EMERGENCY STOP (STOP
AWARYJNY) button and when the power returns after a power supply failure, the
compressor can be started by resetting the EMERGENCY STOP button and pressing
the OPERATION button.
The microprocessor controller has an additional function, preventing the compressor from
starting under pressure, by measuring the time necessary to unload pressure from the
screw block.
Refer to the microprocessor controller manual delivered with each
compressor for detailed operation and setup procedures.
Refer to the inverter manual delivered with each compressor for detailed
operation and setup procedures.

Operating and Maintenance Manual 09/2019 –part I
Screw compressors
16
5.3. ULTRA SPEED function –in screw compressors with motor power of 5.5
kW - 90 kW and frequency converter
This function regulate the speed so that the power currently consumed is close to the
nominal power of the engine. This results in rotation speed increase and thus capacity
increase at operating pressure lower then nominal pressure.
This function is implemented by a second PID regulator located in the inverter and
controlled by the DWEZ functionality.
The ultraspeed function enables higher compressor performance by setting a lower
operating pressure. It provides the maximum possible compressor capacity for a given
operating pressure while maintaining the nominal power of the device. The ultraspeed
function is especially useful at times of excessive demand for compressed air. In the
ultraspeed function, the main parameter managed by the controller is the main engine
power. Lowering the operating pressure below the nominal pressure, it is possible to
achieve higher capacity by increasing the speed of the main engine while maintaining the
nominal power. The scope of performance is presented in the Technical data table
contained in part II of the OMM.
5.4 Description of the compressed air treatment system
The system is the part of the compressor equipment mounted directly in the compressor.
The system comprises the following:
Pre-filter
The pre-filter (type Q) is used to separate the oil emulsion and solid contaminants
from the compressed air. High porosity of non-woven fabric, which the cartridge is
made of, ensures high dust collection ability, which guarantees the removal of
99% of solid and liquid particles larger than 3 µm (3-rd class in accordance with
ISO 8573.1). The particles together with condensate flow down to the filter tank
bottom and are removed automatically from there by the condensate drain.
The oil content does not exceed 0.6 mg/m3
End filters of compressed air
The fine filter (type P) is made of multi-layer thick micro non-woven fabric. Using
the diffusion phenomenon on the single fibre and coalescence phenomenon, it
removes 99.9% of solid particles larger than 1micron and ensures to reach the oil
residual content downstream the filter not higher than 0.1 mg/m3 (2-ndclass in
accordance with ISO 8573.1).
It is also possible to install very fine filters (type S).
The type S filter is also made of multi-layer thick micro non-woven fabric with
better adsorption properties. It removes 99.9% of solid particles larger
than0.01micron and ensures to reach the oil residual content downstream the
filter not higher than 0.01 mg/m3 (1-stclass in accordance with ISO 8573.1).
The fine (P) and very fine (S) filters are always installed downstream the dryer.
Number of filters and their filtration accuracy is determined depending on the
requirements concerning purity of compressed air.
Automatic condensate drain
The purpose of the condensate drains is to remove the precipitated water and oil
condensate from the compressed air system.
The automatic condensate drains are connected to the dryer and filters with threaded
connector. The drain is connected with the hose to the drain ports located on the
compressor wall. In the case of the compressors on the air receiver, the hose is run
outside the machine.

Operating and Maintenance Manual 09/2019 –part I
Screw compressors
17
The condensate removed from the machine must be directed to the appropriate tank and
then disposed in accordance with the applicable environmental protection regulations.
Electrical system
The dryer is connected directly to the compressor terminal block. The dryer is started
directly when voltage is supplied to the power supply terminal block.
Further operation is performed automatically by means of the compressor controller that
first starts the dryer and then compressor. After the compressor start, the dryer continues
operation for the set time and then it is stopped.
Fig. 7 Condensate drain in the compressor
Fig. 8 Condensate drain in the compressor with dryer

Operating and Maintenance Manual 09/2019 –part I
Screw compressors
18
6. Start-up
6.1. Start-up preparation
Each compressor unit is tested in the factory and carefully inspected to ensure proper
machine performance and meeting the specifications declared.
Strictly obey the following rules before starting the machine for the first time:
-Get thoroughly familiar with the compressor Operating and Maintenance Manual and the
Warranty Book.
-Check the power cables for possible damage, short-circuits and electrical breakdowns.
Only authorised / qualified electrician can perform work on electrical equipment and
components.
-Make sure the power supply voltage is correct and the required protections are in place;
do not connect the compressor to a power source of different voltage than that specified in
the Operating and Maintenance Manual.
-Connect the phase wires correctly so that the rotation direction is as indicated on the screw
block, motor, belt transmission guard or coupling guard.
Checking - in the electrical box on relay K1 (photo below) the upper diode should be green
(confirmation of 3 phases), the lower diode should be yellow / orange (confirmation of
correct phase connection in accordance with the correct direction of rotors rotation, marked
on the screw block, belt transmission cover or clutch cover).
-Check the oil level in the screw block or in the oil tank and top it up, if necessary.
-Check the tension of V-belts or inspect the elastic coupling condition.
-Connect the compressor to the compressed air system with a flexible conduit.
-A compressed air receiver tank is necessary for proper compressor operation.
-When the compressed air receiver tank is located outside the compressor room, install the
pressure gauge, connected to the tank or pressure conduit supplying the tank, in a visible
location.
-Do not operate the compressor above the maximum operating pressure that is given on
the identification plate. It is not recommended to operate the compressor at the delivery
pressure below 0.5 MPa. Please contact our technicians when it is necessary to set that
overpressure.
-Check if all doors/covers are closed.
-Open the valve that shuts off the compressor from compressed air system.
-Check the “EMERGENCY STOP” button position.
-Switch on the compressor power supply.
green diode
yellow/orange diode

Operating and Maintenance Manual 09/2019 –part I
Screw compressors
19
When the compressor and compressed air system condition is checked, you can proceed
with starting the compressor.
To start the compressor, press the "START" button on the control panel. The compressor
motor starts working and depending on the overpressure in the compressed air system, the
machine switches to the loaded operation mode or, if the overpressure in the compressed
air system is higher than the minimum start pressure, it switches to the stand-by mode and
starts again after its drop.
Incorrect rotation direction of the screw block rotors for more than 5 seconds
will damage the screw compressor.
6.2. Restart (after longer downtime)
Follow the procedure described below to start the compressor which has been out of use
or stored for over 3 months:
-Check if there is no water in the oil tank. If necessary, remove water from the tank.
-Turn the compressor shaft several times by hand in the rotating direction.
-Lubricate the rotors in the screw block. To do this, remove the air filter and its housing
from the suction regulator or disconnect the hose supplying air from the filter to the
suction regulator. Pour oil into the suction regulator. The necessary oil volume depends
on the compressor power. In the case of power up above 30 kW, pour 0.5 l of oil.
-After pouring the oil, wait one minute and check its level once again.
-Turn the compressor shaft several times by hand in the rotating direction.
-Check the oil level in the tank.
-Check the tension of the V-belts or the condition of the flexible coupling.
-Check that all doors / covers are closed.
-Open the valve shutting offthe compressor from the compressed air network.
-Turn on the machine power.
-Check the position of the "EMERGENCY STOP" button.
After checking of the compressor and compressed air system condition, you can start the
compressor.
Press the "START" button on the control panel. The compressor motor starts running and,
depending on the overpressure in the compressed air system, the machines witches to
loadmodeor, if the overpressure in the network is higher than the minimum switch-on
pressure, it switches to standby mode and starts again when the pressure drops.
Perform the trial run of the compressor screw block lasting for at least a few minutes.
During the trial run, check the machine for correct operation, noise, vibration, oil leaks and
tightness of connections in the compressed air system.
-Do not operate the compressor above the maximum pressure stated on the compressor
identification plate. Compressor operation at a discharge pressure below 0.5 MPa is not
recommended. If you need to set this overpressure, please contact our specialists.
7. Procedure in case of compressor self-deactivation or shut down
by using the emergancy stop.
7.1.Self-deactivation
Read the information displayed on the controller and then follow the instructions in the
user's manual. If the compressor has turned itself off and there are no messages on the
controller:
1. Disconnect the power supply by the main switch.
2. Close the shut-off valve in the compressed air network (mounted behind the
compressor).
3. Wait 5 minutes till the internal compressor systems have been emptied from pressure.

Operating and Maintenance Manual 09/2019 –part I
Screw compressors
20
4. Check that the system has been emptied by slowly unscrewing the oil filler cap (use
protective clothing). The compressed air may be hot.
5. Take the device out of operation, protecting it against inadvertent starting.
6. Call for service.
7.2. Shutdown by using the emergancy stop.
1. Disconnect the power supply by the main switch.
2. Close the shut-off valve in the compressed air network (mounted behind the
compressor).
3. Wait 5 minutes till the internal compressor systems have been emptied from pressure.
4. Check that the system has been emptied by slowly unscrewing the oil filler cap (use
protective clothing). The compressed air may be hot.
5. Take the device out of operation, protecting it against inadvertent starting.
6. Call for service.
8. Maintenance
8.1 General requirements
To ensure proper functioning, the compressor must undergo maintenance procedures. The
following general requirements must be met while performing the maintenance:
-Place the warning sign as shown below in a visible location, while the maintenance work is
in progress:
WARNING
MACHINE UNDER REPAIR
-All maintenance work should be performed by authorised and trained personnel. Contact
the factory service in case of technical problems.
-Before any maintenance work is started on the compressor, disconnect it from power
supply and protect from unauthorized and accidental starting.
-Check if the supply voltage is lacking.
-Any maintenance and repair work can only be carried out when the compressed air system
is completely unloaded i.e. air pressure in the system is reduced to ambient pressure.
-Before restarting the machine, make sure that there is nobody working on the compressor
and there are no people in the vicinity.
-Use appropriate tools for maintenance and repair work.
-Use only original spare parts.
-For cleaning purposes never use flammable or corrosive solvents that could damage the
machine components. Take appropriate safety measures against toxic vapours from
cleaning agents. Biodegradable detergents should be used.
-The workplace must be kept absolutely clean when maintenance work is carried out. Do
not allow any parts to get contaminated. Parts and exposed holes should be covered with
a clean cloth, paper or adhesive tape.
-Upon finishing the maintenance work, make sure no tools or other objects are left on or
inside the compressor.
-Before restarting the machine after maintenance, check operating pressures,
temperatures, time settings, and test the switching and control equipment for proper
functioning.
-Protect the motor, air filters, electric components, control equipment etc. from penetration
of moisture.
-Do not perform any welding or any other works generating heat close to the oil system.
-Under no circumstances should the noise absorbing material be removed or relocated.
The manufacturer accepts no responsibility for any damage and personal injuries resulting
from failure to observe thepresent safety rules orfrom carelessness duringoperation, work
This manual suits for next models
10
Table of contents
Other BERG Air Compressor manuals
Popular Air Compressor manuals by other brands
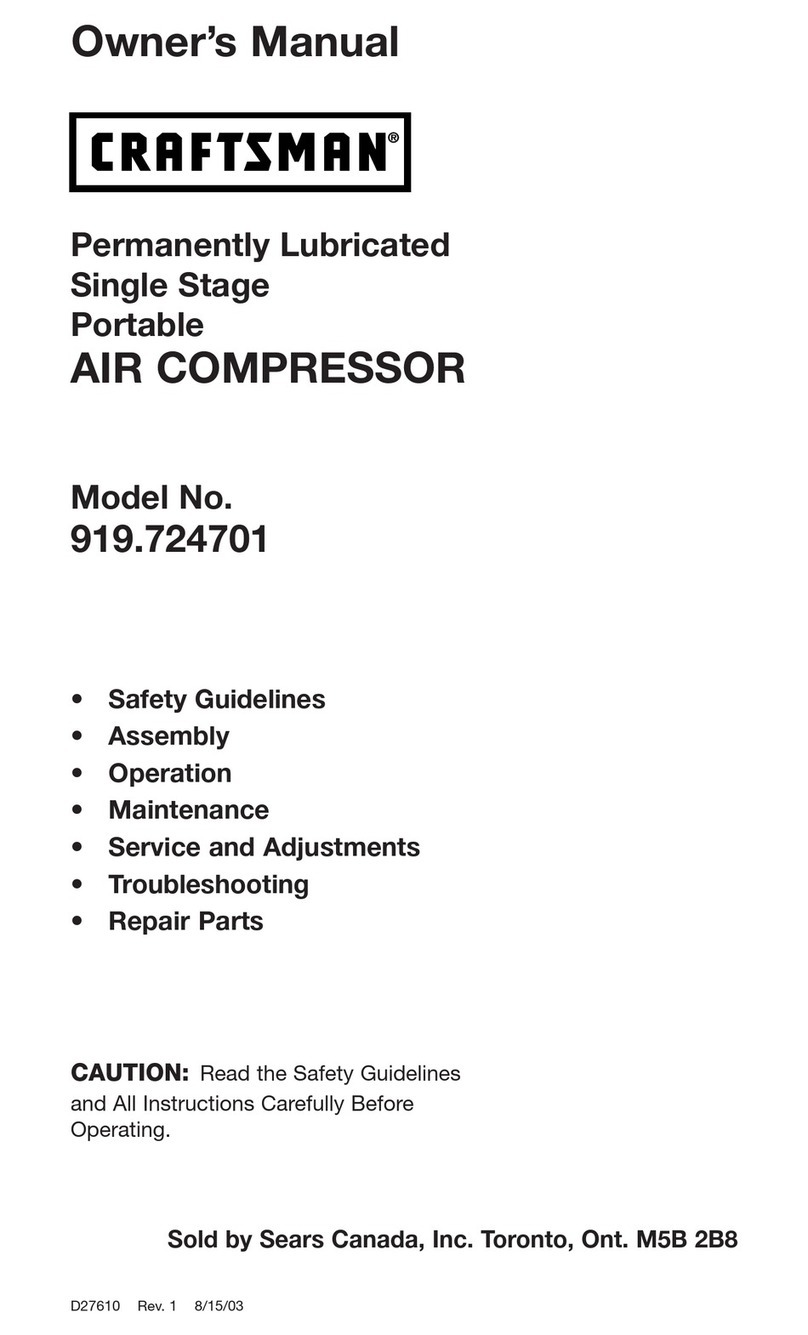
Craftsman
Craftsman AIR COMPRESSOR 919.724701 owner's manual

Axminster
Axminster air AWC30HP manual
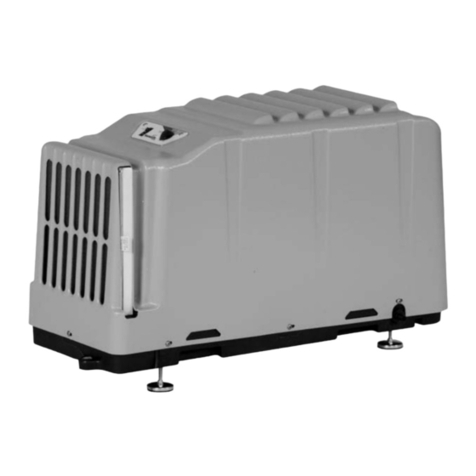
Sakura
Sakura Dry-Boy SDB-45 Installer's & owner's manual
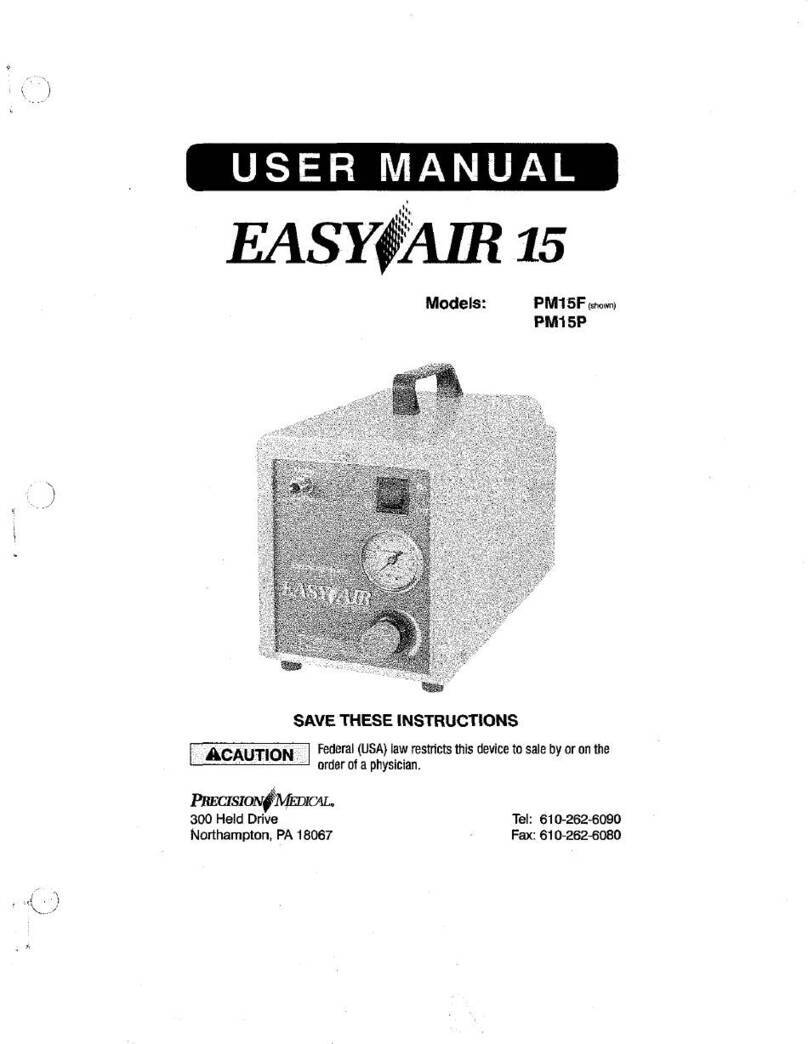
Precision Medical
Precision Medical EASY AIR 15 user manual
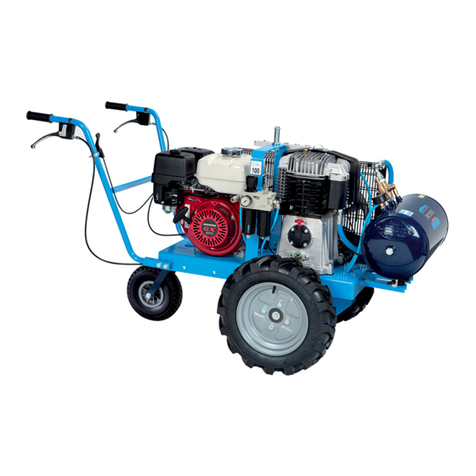
CAMPAGNOLA
CAMPAGNOLA MC 550 Use and maintenance manual
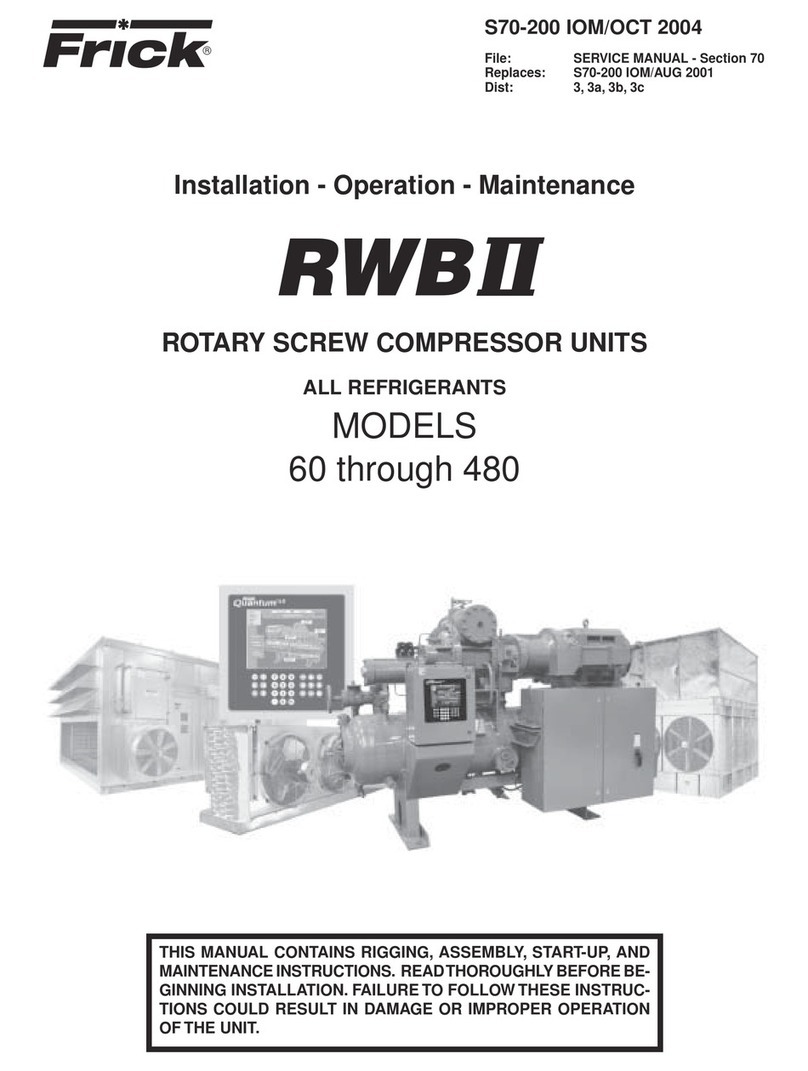
Frick
Frick RWB II Installation operation & maintenance