Bernard Controls ST Series Installation manual

instructions de mise en service,
instructions for start-up,
BetrieBsanleitung,
NR 1113 REV. C
ST
Gamme
Range
Reihe

2 3
Internal wiring diagrams and examples of power supply circuits Page 3
Control panel design examples Page 4
1 Safety information Page 5
2 Assembly Page 5
3 Handwhee loperation and declutching Page 5
4 Electrical connections and preliminary tests Page 5
5 Setting of travel limit switches Page 6
6 Torque limiter Page 6
7 Proportional optical indicator Page 7
8 Position feedback potentiometer (option) Page 7
9 «TAM» position transmitter (option) Page 7
10 Precautions Page 8
11 Maintenance and storage instructions Page 9
BERNARD CONTROLS international network Page 20
TABLE OF CONTENtS
Schémas de cablage interne et exemples de circuits de puissance Page 3
Exemples de réalisation de coffrets de commande Page 4
1 Sécurité Page 10
2 Montage Page 10
3 Commande manuelle et debrayage Page 10
4 Raccordement et tests electriques Page 10
5 Réglage des contacts de fin de course Page 11
6 Limiteur de couple Page 11
7 Indicateur de position optique Page 12
8 Potentiometre de recopie de position (option) Page 12
9 Transmetteur de position type tam (option) Page 12
10 Précautions Page 13
11 Entretien et stockage des servomoteurs Page 14
Le reseau international BERNARD CONTROLS Page 20
SOMMAIRE
Interne verdrahtung und schaltungsbeispiele stromversorgung Seite 3
Schaltungsbeispiele steuerung Seite 4
1 Sicherheits- und warnhinweise Seite 15
2 Montage Seite 15
3 Handradbetâtitung und auskupplung Seite 15
4 Elektroanschlusse und deren uberprufung Seite 15
5 Einstellung der wegendschalter Seite 16
6 Einstellung der drehmomentschalter Seite 17
7 Optische stellungsanzeige Seite 17
8 Potentiometer zur positionsdruckmeldung (option) . Seite 17
9 Stellungsgeber, typ «tam» (option) Seite 18
10 Vorsichtsmassnahmen Seite 19
11 Wartung und instandhaltung der servomotoren Seite 19
BERNARD CONTROLS - internationale Seite 20
INHALTSVERZEICHNIS
SCHEMAS DE CABLAGE INTERNE - EXEMPLES DE CIRCUITS DE PUISSANCE
INTERNAL WIRING DIAGRAMS - EXAMPLES OF POWER SUPPLY WIRING
INTERNE VERDRAHTUNG - SCHALTUNGSBEISPIELE STROMVERSORGUNG
Autres versions (VCC par ex.) : nous consulter /
Other versions (VDC i.e): please consult us /
Andere Ausführungen (z.B. Gleichspannung) : Nehmen SIe Rücksparache mit uns !
3 PHASES 1 PHASE
Légende : C1 = contacteur ouverture ; C2 = contacteur fermeture
Legend: C1 = opening contactor ; C2 = closing contactor
Legende : C1 = Schütz Öffnen ; C2 = Schütz Schliessen

(Fig. 1)
(Fig. 2)
5
1 SÉCURITÉ
Cet appareil répond aux normes de sécurité en vigueur. Toutefois, seule
une installation, une maintenance et une utilisation effectuées par
un personnel qualifié et formé permettront d’assurer un niveau de sécurité
adéquat.
Avant montage et démarrage, lire attentivement l’ensemble de ce document.
2 MONTAGE
Le servomoteur doit être boulonné sur l’appareil à motoriser.
Les servomoteurs BERNARD peuvent fonctionner dans n’importe quelle
position. Cependant, les presse-étoupe ne devraient par être orientés
vers le haut (étanchéité) et le moteur de préférence pas placé en posi-
tion basse (condensation d’eau interne potentielle).
Note 1 : ne pas transporter les servomoteurs par le volant (risque
de dommages mécaniques).
Note 2 : si le servomoteur a été fourni monté sur la vanne, les réglages
de base ont en principe été effectués ; se reporter alors
aux seuls § 3,4, 10 et 11.
Note 3 : voir §.11 pour les précautions de stockage avant mise en route
Note 4 : pour les boîtes à écrou (forme A), bien veiller à leur graissage
avant montage.
3 COMMANDE MANUELLE ET DEBRAYAGE
Les servomoteurs de la gamme ST sont tous équipés d’une commande
manuelle à débrayage automatique à priorité électrique. Le sens de
manoeuvre est normalement indiqué sur le volant. Le servomoteur ST6
possède une poignée d’embrayage du volant. Pour passer en mode
manuel, aligner la flèche de la poignée d’embrayage avec le repère
triangulaire (Fig. 1) situé sur le carter (il peut être nécessaire de tourner
le volant de quelques degrés pour dégager les crabots). Le passage
en mode électrique s’effectue automatiquement au démarrage du moteur,
ou bien manuellement si on le désire.
4 RACCORDEMENT ET TESTS ÉLECTRIQUES
Si le servomoteur est équipé d’une commande type INTELLI, INTEGRAL
ou POSIGAM, veuillez vous reporter aux documentations spécifiques.
Sinon, tous les fils électriques venant des différents éléments du servo-
moteur sont ramenés sur un bornier (Fig.2) dont les bornes portent des
numéros correspondant au schéma de câblage inclus dans ce document
ou à un schéma spécifique exécuté sur demande.
Le contact de protection thermique du moteur et les deux contacts du
limiteur de couple doivent être intégrés dans votre logique de commande
(cf. exemples de câblage) afin de limiter les risques de casse mécanique.
ATTENTION
Pour les servomoteurs antidéflagrants, veuillez aussi lire
attentivement les instructions spécifiques NR1132
avant de procéder au montage et au démarrage.
EXEMPLES DE RÉALISATION DE COFFRETS DE COMMANDE
CONTROL PANEL DESIGN EXAMPLES
SCHALTUNGSVORSCHLAG EINER BEISEITIGEN EXTERNE ANTRIEBSTEUERUNG
Les servomoteurs sont représentés en position médiane
Actuators are represented in an intermediate position
Schaltkontake der Schalter LE und LF dargestellt für Antriebe in Mittelposition (nicht AUF, nicht ZU)

(Fig. 3)
(Fig. 4)
(Fig. 5)
(Fig. 6)
6 7
Une fois le câblage terminé, les points suivants sont à contrôler :
a) A partir des informations gravées sur la plaque d’identification du ser-
vomoteur, vérifier que l’alimentation électrique utilisée est correcte,
b) Vérifier que les presse-étoupes ont bien été resserrés après câblage,
c) A l’aide de la commande manuelle, amener la vanne en position mé-
diane,
d) Actionner la commande électrique d’ouverture. Vérifier que le sens
de rotation du servomoteur est correct. Actionner manuellement
le contact de fin de course «OPEN» (ouvert) ; le moteur doit s’arrêter.
Vérifier de la même manière la commande électrique de fermeture
et le contact de fin de course «CLOSED» (fermé).
e) Actionner la commande électrique d’ouverture. Actionner manuelle-
ment le contact du limiteur d’effort «OPEN» ; le moteur doit s’arrêter.
Vérifier de la même manière le contact du limiteur d’effort «CLOSED»
pendant une manoeuvre de fermeture.
En cas de problème sur un de ces tests, vérifier l’ensemble du cablâge.
Remarque : pour toute utilisation en extérieur, nous recommandons
l’utilisation de la résistance de chauffage optionnelle. Dès l’installation
sur site, alimenter la résistance pour éviter toute condensation.
5 RÉGLAGE DES CONTACTS DE FIN DE COURSE
Ce chapitre ne concerne pas les servomoteurs ST INTELLI+ qui sont
équipés de capteurs de position absolus pour lesquels les réglages
s’effectuent par programmation.(cf. notice NR1112).
5.1 DESCRIPTION ET FONCTION DU BLOC À CAMES
ET DES CONTACTS FIN DE COURSE (Fig.3)
Les cames actionnant les micro-contacts forment un ensemble mono-
bloc dont les éléments peuvent être réglés indépendamment les uns des
autres. Les cames blanche et noire servent aux contacts fin de course. Les
autres cames sont pour des contacts additionnels optionnels (2 à 4 selon
version). Les cames se manoeuvrent de la façon suivante :
a) Introduire un petit tournevis dans la fente entourée d’une bague
de la même couleur que la came à déplacer,
b) Appuyer légèrement pour libérer la came,
c) Tourner dans un sens ou dans l’autre pour amener la came dans
la position recherchée,
d) Relâcher la pression en s’assurant que la tête est remontée en position
d’origine, ce qui verrouille automatiquement la came.
5.2 MODE OPÉRATOIRE DE RÉGLAGE DU BLOC
À CAMES :
a) Amener la vanne en position fermée.
b) Régler la position de la came du contact de fin de course «CLOSED».
Respecter la même procédure pour l’ouverture.
Effectuer une fermeture et une ouverture complète avec la commande
électrique afin de vérifier que la vanne s’arrête bien dans les positions
souhaitées.
5.3 CAS DE L’ARRÊT EN FERMETURE DE LA VANNE PAR
LIMITEUR DE COUPLE :
Le contact de fin de course «CLOSED» peut servir à shunter le contact
du limiteur de couple en début d’ouverture, afin d’assurer un couple
de décollage de vanne supérieur au couple maximum fixé (voir p.2).
Suivre la procédure du § 5.2, toutefois lors de la commande électrique
en fermeture, s’assurer que le contact de fin de course «CLOSED» est bien
actionné peu avant l’arrêt de la motorisation par ouverture du contact
limiteur d’effort «CLOSED».
6 LIMITEUR DE COUPLE
Le servomoteur est livré avec un système limiteur d’effort (Fig. 4) éta-
lonné en atelier. Son réglage est effectué suivant les valeurs spécifiées
à la commande ou, par défaut, à 100% du couple maximum du servomoteur.
Si le limiteur de couple est actionné en cours de manoeuvre vérifier :
- que la tige de vanne est propre et bien graissée
- que la tige de vanne ne grippe pas dans l’écrou de manoeuvre
- que le presse étoupe de la tige de vanne n’est pas trop serré.
Si une augmentation de couple est nécessaire, et après accord du four-
nisseur de la vanne, le réglage du limiteur peut être ajusté comme suit :
- pour reprendre le réglage, le limiteur de couple doit être au repos
- suivant le sens de manoeuvre de la vanne, déterminer sur quelle vis
de réglage agir,
- ajuster la nouvelle valeur de couple du limiteur à l’aide d’un tournevis
et de l’échelle graduée en pourcentage. 100% correspond au couple
maximum du servomoteur.
Sur les servomoteurs ST INTELLI+, qui sont équipés de capteurs de couple
absolus, ce réglage s’effectue par programmation.(cf. notice NR1112).
Remarque : Le limiteur d’effort fournit un contact électrique maintenu.
7 INDICATEUR DE POSITION OPTIQUE (Fig. 5)
Le disque de l’indicateur est entraîné en rotation par le bloc cames des
fins de course.
Amener la vanne en position fermeture complète et positionner le disque
afin de faire apparaître le symbole dans le voyant du couvercle.
Amener la vanne en position ouverture complète pour contrôler que le
symbole apparaît bien dans le voyant. Réajuster si nécessaire.
8 POTENTIOMETRE DE RECOPIE DE POSITION (OPTION)
Le potentiomètre de recopie de position (fig.6) est entraîné par le bloc
cames des fins de course. Sauf cas de réalisation spéciale, le potentio-
mètre a une résistance totale de 1000 ohms 1W. La plage utile du poten-
tiomètre dépend de la course (typiquement 730 à 1000 ohms). Le poten-
tiomètre n’a pas de butée mécanique et possède une zone non-résistive
(zone morte) en début et en fin de piste.
Le 0% correspond à une vanne fermée. Le 100% à une vanne ouverte.
Pour monter l’ensemble potentiomètre sur la platine du servomoteur,
emboîtez-le sans l’indicateur de position et vissez-le sur la colonette de
maintien. Revissez l’indicateur de position.

(Fig. 7)
(Fig. 8)
8 9
Le réglage du zéro du potentiomètre s’effectue à l’aide de la vis repérée
«0% position». Mettre le servomoteur en position fermée. La mesure de
résistance s’effectuera entre les bornes 16 et 17.
Tout en maintenant manuellement en position la pignonnerie située juste
sous la plaque marquée «0% position», tourner la vis du potentiomètre
jusqu’à obtenir une valeur de résistance qui dépasse 0 Ohm et augmente
régulièrement puis tourner en sens inverse afin de revenir à une valeur
proche de 0 Ohm.
Mettre le servomoteur en position ouverte et noter la valeur de résistance
pour le 100%. Revenir en position fermée et vérifier que la valeur du 0%
est bien répétable et proche de 0 Ohm.
Remarques : Si l’équipement possède 2 potentiomètres, chaque potentio-
mètre est réglé indépendamment l’un de l’autre.
Inversion du signal
Pour changer le sens de variation du signal, croiser les fils du potentio-
mètre au niveau du bornier du servomoteur (exemple : pour un raccorde-
ment 16/17/18, inverser 16 et 18).
9 TRANSMETTEUR DE POSITIONTYPETAM (OPTION - FIG.7)
Le TAM transmet un signal 0-20mA ou 4-20mA, proportionnel à la posi-
tion de la vanne.
Raccordement électrique
Effectuer le raccordement électrique conformément au schéma de
câblage général du servomoteur. Voir aussi des exemples de branchement
typiques ci-contre.
L’alimentation doit être comprise entre 12 et 32V en courant continu
redressé filtré ou stabilisé et avec une charge maxi admissible précisée
dans le tableau ci-après.
Adaptation du signal au sens de rotation (Fig.8)
Le transmetteur, en standard, délivre un signal qui augmente de la posi-
tion fermée à la position ouverte, le sens d’ouverture de l’organe entrainé
correspondant au sens antihoraire.
Pour que le signal diminue de la position fermée à la position ouverte
ou si l’organe entrainé ouvre dans le sens horaire, le signal peut être inversé
en déplaçant les cavaliers : sens direct 1-3 / 2-4 , sens inverse 1-2 / 3-4.
Réglages
Brancher un milliampèremètre avec ou sans charge pour lire le courant
de sortie.
- Le réglage doit toujours commencer par le 0/4mA.
- Amener le servomoteur dans la position qui doit correspondre au signal
0/4mA (en standard c’est la fin de manoeuvre de l’organe entrainé dans
le sens horaire ou position fermée).
- Tout en maintenant manuellement en position la pignonnerie située
juste sous la plaque marquée «0% position», tourner la vis du poten-
tiomètre jusqu’à atteindre la plage où le courant à sa valeur minimale.
Chercher la zone où le signal augmente régulièrement puis tourner en
sens inverse afin de revenir à la valeur minimale précédemment trouvée.
Le potentiomètre est ainsi calé en début de piste.
- Régler ensuite précisément le 0/4 mA grâce à la vis du TAM marquée
«0/4mA».
- Amener maintenant le servomoteur dans la position qui doit
correspondre au signal 20mA (en standard c’est la fin de manoeuvre
de l’organe entrainé dans le sens antihoraire ou position ouverte).
- Tourner la vis de réglage repérée «20mA» pour lire exactement
sur le milliampèremètre 20mA.
- Revenir en position fermée et vérifier que la valeur du 0% est bien
répétable et proche de 0/4 mA
10 PRÉCAUTIONS
Immédiatement après la mise en service, veiller à remonter les couvercles,
en s’assurant de l’état de propreté de leurs joints.
Ne jamais laisser le matériel électrique du servomoteur sans son couvercle
de protection.
Dans le cas d’introduction d’eau éventuelle, assécher le matériel électrique
et vérifier l’isolation électrique avant remise en place du couvercle.
11 ENTRETIEN ET STOCKAGE DES SERVOMOTEURS
Entretien
Les servomoteurs ST sont graissés à vie et ne requièrent en conséquence
aucun entretien particulier. Il convient toutefois de vérifier périodiquement
l’état de la tige de vanne et son écrou, ceux-ci devant être propres et bien
lubrifiés.
Si les motorisations sont rarement sollicitées, nous recommandons d’éta-
blir un programme périodique de manoeuvres d’entretien.
Stockage
Un servomoteur est composé d’éléments électriques et d’une partie mé-
canique lubrifiée à la graisse. Malgré l’étanchéité de l’enveloppe de cet
ensemble, les risques d’oxydation, de gommage et de grippage peuvent
apparaître lors de la mise en service du servomoteur si son stockage n’a
pas été correctement réalisé.
Alimetation
VOLT Charge maxi
admissible Ohm
12 150
34 750
30 1050

(Fig. 1)
(Fig. 2)
10 11
1 SAFETY INFORMATION
This device complies to current applicable safety standards.
Installation, maintenance and use of this apparatus by skilled and trained
staff only.
Please read carefully the whole document prior to mounting and starting-up.
2 ASSEMBLY
Actuator should be secured directly to the valve using proper bolts
or via a proper interface.
After assembly, the actuator can operate in any position. However,
cable glands should not be oriented upwards (loss of water tightness)
and the motor will preferably not be positioned at the bottom (potential
internal condensation trap)
Note 1 : do not handle the actuator by handwheel, it could damage the
gears.
Note 2 : if the actuator was delivered mounted on the valve, the basic
settings should have been done. In this case, refer to § 3, 4,
10 and 11 only.
Note 3 : see §.11 for details on storage precaution prior to starting-up.
Note 4 : greasing of A form drive bush has to be done prior to mounting
actuator on valve.
3 EMERGENCY HANDWHEEL AND DECLUTCH
All ST range actuators are provided with an automatical declutchling
handwheel, with motor drive priority. Operating direction is normally
indicate on the handwheel.
The ST6 actuator has a handwheel clutch button. In order to operate
manually the actuator, turn the arrow of the button in front of the trian-
gular sign (Fig. 1) on the housing (it could be necessary to turn the hand-
wheel of a few degrees to positionate the claws).
When the motor start, the button return automatically in its declutched
position.
4 ELECTRICAL CONNECTIONS AND PRELIMINARYTESTS
If the actuator is equipped with INTEGRAL, MINIGRAL or MINIGAM
commands, please report to the specific documentation for wiring
details. Otherwise, all components of the actuator are wired to a common
terminal strip (Fig.2). Remove the cover and pass the cables through
the cable glands (M20). Refer to the standard wiring diagram on page
1 (or to the specific wiring diagram provided on request) for details
on the terminals numbering system. Both torque and travel limit switches
must be integrated into your control system (see wiring examples) in order
to prevent potential damage to the actuator or valve.
WARNING
For explosionproof actuators, please also read carefully
the special instructions NR1132 prior to mounting
and starting-up
Les servomoteurs doivent donc être stockés sous abri dans un endroit
propre et sec et protégé des changements successifs de température.
Eviter le stockage à même le sol.
Pour les motorisations équipées de résistance de chauffage, alimenter
celle-ci dans le cas de présence d’humidité (tension standard 230 volts,
sans précision particulière à la commande).
Vérifier que les bouchons plastique provisoires des entrées de câble
sont bien en place. En cas de présence d’humidité, remplacer ceux-ci par
des bouchons filetés métalliques.
S’assurer de l’étanchéité des couvercles des boîtiers renfermant les éléments
électriques.
Contrôle après stockage
a) Durée du stockage inférieure à 1 an :
- Contrôle visuel de l’équipement électrique.
- Actions manuelles sur les contacts, boutons, sélecteurs, etc... pour
en contrôler le bon fonctionnement mécanique. Procéder à quelques
manoeuvres manuelles.
- Vérifier la bonne consistance de la graisse.
b) Durée du stockage supérieure à 1 an :
- Le stockage à long terme entraîne un changement dans la consis-
tance de la graisse. En faible épaisseur sur les axes ou tourillons,
elle se dessèche. Il est donc nécessaire de procéder au démontage
et au dégraissage de toute la partie mécanique du servomoteur et
remonter celui-ci avec de la graisse neuve.
- Contrôle visuel de l’équipement électrique.
- Actions manuelles sur les contacts, boutons, sélecteurs, etc... pour en
contrôler leur bon fonctionnement mécanique.
Graissage
SHELL TIVELA COMPOUD (ST6 : 2kg / ST14 : 3kg / ST30 : 3,5kg / ST70 : 4,5kg).

(Fig. 3)
(Fig. 4)
(Fig. 5)
(Fig. 6)
12 13
The following items must be checked:
a) Make sure that power supply voltage is in accordance with the data
engraved on the actuator nameplate
b) Check that all cable glands are correctly tightened
c) Move the valve manually to an half-open position,
d) Operate an electrical opening and check that the motor rotates
in the right direction. Press manually on the «OPEN» travel limit
switch; the motor should stop In the same way, check that
the closing electrical command as well as the «CLOSED» travel limit
switch are working correctly
e) Operate an electrical opening. Press manually on the «OPEN»
torque limit switch; the motor should stop. In the same way,
operate an electrical closing check that the «CLOSED» torque limit
switch is working correctly
If any misfunction was detected at this stage, please check the overall wiring.
Remark: for all outdoor installation, we do recommend to use the optional
heating resistance. To avoid any condensation, supply heat resistance
as soon as the actuator is on site.
5 SETTING OF TRAVEL LIMIT SWITCHES
This chapter does not concern the ST INTELLI+. In fact, it is equipped
with absolute position encoders and setting is done by programming
(see NR1112 instructions).
5.1 TRAVEL LIMIT SWITCHES DESCRIPTION AND
FUNCTION (Fig.3)
The cams operating the limit switches are on a cylindrical block which
does not require any disassembly. Each cam can be set independently of
the others. The white and black cams are for open and close travel limits.
The other ones are for optional additional limit switches (2 or 4).
How to operate the cams:
a) Put a screwdriver in the slot of the button encircled by the same color
as the cam to be set
b) Press lightly to disengage the cam of locked position
c) By turning the screwdriver rotate the cam to the position in which
it can trip the limit switch
d) Remove screwdriver and ensure that the button has come back
to its original position, thus locking the cam in chosen place
5.2 PROCEDURE OFTRAVEL LIMIT SWITCHES SETTING
a) Manually drive the valve to the closed position
b) Set the cam of the «CLOSED» travel limit switch
Proceed in the same way in open position.
Perform complete electrical valve opening and closing operations to check
if the valve stops at correct positions.
5.3 CASE OF VALVE CLOSING ON TORQUE LIMITER
The travel limit switch «CLOSED» can be used to shunt the «Opening»
torque limiter contact to allow to unseat the valve even if the torque
is then exceeding the maximum set torque (see p.2).
Proceed in the same way as in §5.2, making sure that, when closing
electrically, the travel limit switch «CLOSED» is activated slightly
before and remains activated when the actuator stops on torque limiter
«CLOSED».
6 TORQUE LIMITER
The actuator is delivered with a factory calibrated torque limit system
(Fig.4). The torque values used for the setting are the one specified
on the order form or, by default, 100% of the actuator maximum torque value.
If the torque limiter is activated during an operation, check:
- that the valve stem is clean and well lubricated
- that the valve stem does not jam in the nut
- that the valve stuffing box is not too tight
If torque has to be increased, consult the valve manufacturer before
proceeding as follows:
- open the limit switches compartment (cover with mechanical position
indicator)
- the torque limiter shall be released in order to proceed to any adjustment
- according to the valve travel direction, determine which adjustment
screw to use
- Turn the setting screw to set the new torque limit value reported
on the 0-100% graduated scale
The 100% corresponds to the maximum torque of the actuator.
On the ST INTELLI+, setting of torque limiter is done by programming
(see NR1112 instructions).
Remark: The torque limiter provides a maintained contact
7 PROPORTIONAL OPTICAL INDICATOR (Fig. 5)
The indicator disc is driven by the camblock system.
Turn electrically the valve to the completely closed position and rotate the
disc until the symbol appears in the window.
Turn electrically the valve to the completely open position to check that
the is visible in the window. Adjust if required.
8 POSITION FEEDBACK POTENTIOMETER (OPTION)
The actuator signal feedback potentiometer (Fig. 6) is driven by the travel
camblock system. The standard model of potentiometer has a total resistance
of 1000 ohms, 1W. Its actual working range depends on the valve stroke
(typically 730 to 1000 ohms). The potentiometer has no mechanical
stop and has a non-resistive area (dead zone) at both the beginning
and the end of track. 0% position corresponds to a closed valve. 100%
to an open valve.
To mount the potentiometer device on the switch plate, clip it without
the position indicator on the camblock and screw it on the support
column. Screw the position indicator back.

(Fig. 7)
(Fig. 8)
14 15
Setting of potentiometer zero is achieved thanks to the «0% postion» screw.
Drive the actuator to the closed position.
Resistance value is measured between terminals 16 and 17.
Hold the pinion located just under the plate with the «0% position»
marking while driving the potentiometer screw. Adjust the potentiometer
so that the resistance value exceeds 0 Ohm and regularly increases then
turn backwards to reach a value as close to 0 Ohm as possible.
Mettre le servomoteur en position ouverte et noter la valeur de résistance
pour le 100%. Revenir en position fermée et vérifier que la valeur du 0%
est bien répétable et proche de 0 Ohm.
Drive the actuator to the open position and write down the resistance
value corresponding to the 100% position.
Come back to the closed position and check that, for the 0% position,
the resistance shows a close to zero repeatable value.
Note: If actuator is equipped with 2 potentiometers, each potentiometer is
set independently of the other.
Signal inversion:
To inverse the signal variation direction, invert potentiometer wires
on the actuator terminal board (e.g. for a connection on 16/17/18, invert
16 and 18).
9 «TAM» FEEDBACKPOSITIONTRANSMITTER(OPTION- Fig.7)
The TAM transmitter delivers a 0/4 to 20 mA signal linearly proportional
to the valve position.
Electric connections
Refer to the actuator standard wiring diagram. See also some typical
wiring examples below. FIltered or stabilised power supply should be provided
within the 12 to 32 VDC range. Maximum admissible ohmic load values
are given in the table :
Signal direction inversion (Fig.8)
The TAM transmitter, when supplied with a standard actuator, provides
a signal that rise from close position to open position, the standard opening
direction being counter-clockwise.
If an opposite signal variation is required, simply move 2 jumpers on the board
near the potentiometer.
Direct signal: jumpers on 1-3 and 2-4
Reversed signal: jumpers on 1-2 and 3-4
Settings
Connect a milliampermeter at the place of burden.
- Always start by adjusting the 0/4mA.
- Drive actuator to the position corresponding to the 0/4 mA (closed
in standard),
- Hold the pinion located just under the plate with the «0% position»
marking while driving the potentiometer screw. Adjust the potentiometer
so that the output current reaches a minimum value. Turn backwards
until the current value regularly increases then turn backwards again
and stop as soon as the minimum value determined here above
has been reached. The potentiometer is then positioned at the very
beginning of its track.
- Then, use the TAM adjustment screw marked as «0/4mA» to adjust
the current to a value as close to the 0/4 mA as possible.
- Drive actuator to the position corresponding to the 20 mA (open
in standard),
- Turn the screw marked «20mA» in order to read exactly 20 mA
on the milliampermeter.
- Come back to the closed position and check that, for the 0% position,
the signal current shows a close to 0/4 mA and repeatable value.
10 PRÉCAUTIONS
Close the cover immediately after start-up and make sure that the cover
seals are not damaged and remain clean.
It is important to ensure a proper protection covers closing in order
to avoid any water entry.
In case of water entry, dry thoroughly and check electric insulation before
replacing covers.
11 MAINTENANCE AND STORAGE INSTRUCTIONS
Maintenance
All ST actuators are lubricated for lifetime and therefore require no specific
maintenance.
The condition of the valve stem and its nut must nevertheless be checked
periodically to make sure they are clean and well lubricated.
We recommend that a program of periodic maintenance should be drawn
up for actuators that are operated unfrequently.
Storage
The actuator includes electric equipment as well as grease lubricated gear
stages. In spite of the weatherproof enclosure, oxidation, jamming and
other alterations are possible if actuator is not correctly stored.
The actuators should therefore be stored under a shelter in a clean, dry
place and protected from wide changes in temperature.
Avoid placing the actuators directly on the floor. For the actuators equip-
ped with a heating resistance, it is recommended that to connect and
power supply it especially if the storage area is humid (standard voltage
230 volts, unless otherwise specified).
Power Supply DC
(VOLT) Max. admissible
load Ohm
12 150
34 750
30 1050

(Abb. 1)
(Abb. 2)
16 17
Check that the temporary sealing plugs of the cable entries are well in
place. In case of humidity, use metal threaded plugs.
Make sure that the covers and the boxes are well closed to ensure
weatherproof sealing.
Control after storage
a) Storage not exceeding one year
- Visual inspection of electric equipment.
- Operate manually the microswitches, buttons, selectors, etc.,
to insure they are operating correctly.
- Drive the actuator manually for a few travels.
- Verify the correct grease consistency.
b) Storage exceeding one year
- Long time stocking may affect grease consistency. The grease thin
layer on stem dries up. Remove all the old grease of the actuator
mechanical parts and replace with new grease.
- Visual inspection of electric equipment.
- Operate manually the microswitches, buttons, selectors, etc.,
to insure they are operating correctly.
Lubrication
SHELL TIVELA COMPOUD (ST6: 2kg / ST14: 3kg / ST30: 3.5kg / ST70: 4.5kg).
1 SICHERHEITS- UND WARNHINWEISE
Dieses Gerät entspricht den gültigen gesetzlichen Sicherheitsrichtlinien.
Die erforderliche Sicherheit kann allerdings erst gewährleistet werden,
wenn die Installation, die Wartung und die Bedienung durch qualifiziertes,
ausgebildetes Personal erfolgt. Vor Installation und Inbetriebnahme dieses
Gerätes lesen Sie bitte diese Anleitung sorgfältig und vollständig durch.
2 MONTAGE
Der Stellantrieb wird direkt auf der zu automatisierenden Armatur
befestigt.
Die BERNARD-Stellantriebe sind in jeder Einbaulage betriebsfähig.
Allerdings sollten die Kabelverschraubungen nicht nach oben zeigen
(Dichtigkeitsverlust) und der Motor nicht zu nahe am Boden aufgestellt
werden (Gefahr von Kondenswasserbildung im Inneren).
Anmerkung 1 : Den Stellantrieb nicht am Handrad tragen (Gefahr von
mechanischen Schäden).
Anmerkung 2 : Bei den mit schon angebautem Ventil gelieferten
StellantriebenwurdendieGrundeinstellungengrundsätzlich
schon vorgenommen; siehe dann nur die § 3, 4, 10 und 11.
Anmerkung 3 : Für Lagerungshinweise vor einem Transport des Geräts
siehe § 11.
Anmerkung 4 : Vor der Montage müssen die Gewindebuchsen (in der Form A)
sorgfältig geschmiert werden.
3 HANDRADBETÄTIGUNG UND AUSKUPPLUNG
Alle Stellantriebe der ST-Baureihe sind mit einem beim Einschalten
des Motors automatisch auskuppelnden Handrad ausgestattet.
Die Drehrichtung wird im Normalfall auf dem Handrad angezeigt.
Der Stellantrieb ST6 verfügt über einen Drehknopf zum
Einkuppeln des Handrads. Um den Handbetrieb zu aktivieren, bringen
Sie den Pfeil am Drehknopf mit der dreieckigen Markierung (Abb. 1)
amGehäuse zur Deckung(manchmal muss das Handradein wenig gedreht
werden, um die Schaltklauen zu lösen). Wenn der Motorbetrieb einges-
chaltet wird, dann geht der Drehknopf automatisch in die ausgekuppelte
Position.
4 ELEKTROANSCHLÜSSE UND DEREN ÜBERPRÜFUNG
Falls der Stellantrieb über eine INTELLI-, INTEGRAL- oder POSIGAM-
Steuerung verfügt, konsultieren Sie bitte die jeweilige Dokumentation.
Andernfalls sind alle Leitungsdrähte der verschiedenen Stellantriebs-
Bauteilen auf einer Anschlussleiste verdrahtet (Abb.2). Die Klemmen-
nummern auf der Anschlussleiste entsprechen den der vorliegenden
Dokumentation (oder einem spezifischen Kunden-Diagramm auf Anfrage)
beigefügten Stromlaufplänen.
ACHTUNG!
Vor Installation und Inbetriebnahme explosionsgeschützter
Stellantriebe lesen Sie bitte auch sorgfältig die spezielle
Bedienungsanleitung NR1132.

(Abb. 3)
(Abb. 4)
18 19
Um mechanische Schäden auszuschließen, müssen Sie sowohl
den Kontakt des Temperaturwächters vom Motor als auch die beiden
Kontakte der Drehmomentschalter in Ihre Steuerungslogik integrieren (vgl.
Schaltungsbeispiele).
Nach Abschluss der Verkabelung sind noch folgende Schritte durchzuführen:
a) Prüfen Sie anhand der Informationen auf dem Typenschild des
Stellantriebes, ob die richtige Stromversorgung ausgewählt wurde.
b) Prüfen Sie, ob die Kabelverschraubungen nach erfolgter Verkabelung
richtig festgezogen wurden.
c) Bringen Sie das Ventil manuell in Mittelstellung.
d) Aktivieren Sie einen Steuerbefehl zum Öffnen des Ventils. Prüfen
Sie, ob die Drehrichtung des Stellantriebs korrekt ist. Betätigen
Sie manuell den Wegendschalter für die Position «Endlage AUF»
(geöffnet) -- der Motor muss von Ihrer Steuerung abgeschaltet
werden und anhalten. Prüfen Sie auf die gleiche Weise den Steuerbefehl
zum Schließen und den Endschalter Position «Endlage ZU»
(geschlossen).
e) Aktivieren Sie einen Steuerbefehl zum Öffnen des Ventils.
Betätigen Sie manuell den Drehmomentschalter der Laufrichtung
«ÖFFNEN «, der Motor muss anhalten; Prüfen Sie auf die gleiche
Weise während eines Schließvorgangs den Drehmomentschalter
der Laufrichtung «SCHLIEßEN».
Bei Problemen während eines dieser Tests müssen Sie die gesamte
Verkabelung noch einmal überprüfen.
Hinweis : Bei jeder Außenmontage des Stellantriebes empfehlen
wir die Verwendung eines optionalen Heizwiderstandes. Nach vor Ort
erfolgter Installation wird der Widerstand mit Strom versorgt, um jegliche
Kondenswasserbildung zu verhindern.
5 EINSTELLEN DER WEGENDSCHALTER
Dieses Kapitel bezieht sich nicht auf die INTELLI+ Antriebe die mit
absoluten Weg.- u. Drehmomentsensoren ausgestattet sind. Das Einstellen
erfolgt beim Intelli+über die Programmierung. (siehe Anleitung NR1112).
5.1 BESCHREIBUNG UND FUNKTION DES NOCKEN-
SCHEIBENBLOCKS UND DER WEGENDSCHALTER
(Abb.3)
Die Nockenscheiben zum Betätigen der Wegendschalter bilden einen
Monoblock und können unabhängig voneinander eingestellt werden.
Die weiße und schwarze Nockenscheibe sind für die Wegendschalter
bestimmt. Die anderen Nockenscheiben sind für optionale Schalter
bestimmt (2 bis 4 Stück, je nach Modell).
Die Bedienung der Nockenscheiben erfolgt folgendermaßen:
a) Stecken Sie einen kleinen Schraubendreher in den Schlitz, dessen
Außenring farblich der zu verstellenden Nockenscheibe entspricht.
b) Üben Sie einen leichten Druck aus, um die Nockenscheibe zu entriegeln.
c) Drehen Sie nach rechts oder links, um die Nockenscheibe in die
gewünschte Stellung zu bringen.
d) Nehmen Sie den Schraubendreher heraus und prüfen Sie, ob sich
der Kopf wieder in der Ausgangsstellung befindet; dadurch wird
die Nockenscheibe automatisch wieder verriegelt.
5.2 VORGEHENSWEISE ZUR EINSTELLUNG DES
NOCKENSCHEIBENBLOCKES:
a) Bringen Sie das Ventil durch Handbetrieb in die geschlossene Stellung.
b) Nehmen Sie die Einstellung der Nockenscheibe für den Schließkontakt
vor (siehe Beschreibung unter 5-1).
Die gleiche Vorgehensweise gilt für das Öffnen.
Mit der elektrischen Steuerung führen Sie nun einen vollständigen
Schließ- und Öffnungsvorgang durch und prüfen dabei, ob das Ventil
an den gewünschten Stellen anhält.
5.3 DREHMOMENTABHÄNGIGES ABSCHALTEN IN
SCHLIESSRICHTUNG (ENDLAGE ZU)
Der Endschalter «CLOSED» kann zum Drehmomentschalter ÖFFNEN
parallel geschaltet werden, um den Drehmomentschalter zu überbrücken
damit ein höheres Drehmoment (Anfahrmoment) als das ursprünglich
festgelegte maximale Drehmoment zu erreichen, um dadurch das Ventil
aus dem oft sehr festen Sitz heraus öffnen zu können.
Gehen Sie wie in Abschnitt 5.2 beschrieben vor. Wurde der Motor
inderEndlageZUüberdenDrehmomentschalterSCHLIEßENabgeschaltet
ist darauf zu achten (die entsprechende Einstellung vorzunehmen), dass
der Endschalter «CLOSED» (ZU) kurz vorher betätigt wird.
6 DREHMOMENTBEGRENZER (DREHMOMENTSCHALTER)
Der Stellantrieb wird mit werksjustiertem Drehmomentbegrenzer (Abb. 4)
geliefert. Die werksseitige Einstellung erfolgt gemäß den bei der Bestel-
lung angegebenen Werten oder, wenn diese fehlen, wird das maximalen
Drehmoment ( 100%) des Stellantriebs eingestellt.
Falls sich der Drehmomentbegrenzer (die Drehmomentschalter) während
eines Betriebvorgangs einschaltet, prüfen Sie:
- ob die Ventilspindel sauber und genügend geschmiert ist,
- ob die Ventilspindel nicht in der Gewindebuchse festsitzt,
- ob die Stopfbuchse der Ventilspindel nicht zu fest angezogen ist.
Wenn das Drehmoment erhöht werden muss und der Ventilzulieferer sein
Einverständnis gibt, kann die Begrenzereinstellung wie folgt verändert
werden :
- Der Drehmomentbegrenzer muss sich in Ruhestellung befinden.
- Bestimmen Sie die einzustellende Schraube (ÖFFNEN oder SCHLIESSEN)
je nach Steuerungsrichtung des Ventils.t
- Stellen Sie den neuen Drehmomentwert des Begrenzers mit Hilfe eines
Schraubendrehers ein. Den neuen Wert können Sie auf der Anzeigeskala
in Prozent ablesen. 100 % entsprechen dem maximalen Drehmoment
des Stellantriebs.
Bei INTELLI+ Antrieben, die mit absoluten Drehmomentsensoren aus-
gestattet sind erfolgt das Einstellen über die Programmierung.
Hinweis : Der Drehmomentbegrenzer gibt Dauerkontakt.

(Fig. 7)
(Fig. 8)
(Abb. 5)
(Abb. 6)
20 21
7 OPTISCHE STELLUNGSANZEIGE (Abb. 5)
Die Anzeigescheibe wird vom Nockenscheibenblock der Endschalter
angetrieben. Bringen Sie das Ventil in die vollständig geschlossene
Stellung und drehen Sie an der Scheibe, bis das Symbol im Schauglas
des Deckels erscheint.
Bringen Sie das Ventil in die vollständig geöffnete Stellung und prüfen
Sie, ob das Symbol im Schauglas erscheint. Bei Bedarf neu justieren.
8 POTENTIOMETER ZUR POSITIONSRÜCKMELDUNG
(OPTION - Abb. 6)
Das Potentiometer zur Positionsrückmeldung (Abb. 7) wird vom
Nockenscheibenblock der Endschalter angetrieben. Bis auf spezielle
Ausführungen hat das Potentiometer einen Gesamtwiderstand von
1000 Ohm, 1 W. Der nutzbare Bereich des Potentiometers hängt vom
Hub der Armatur ab ( typisch 0 bis 730 Ohm ).
Das Potentiometer hat keinen mechanischen Anschlag und weist eine
widerstandsfreie Zone (Totzone) am Ein- und Auslauf auf.
0 % entspricht einem geschlossenen Ventil. 100 % entsprechen
einem offenen Ventil. Um das Potentiometer auf die Stellantriebsplatte
(Schalterplatte) zu montieren, stecken Sie es bei abgenommenem
Stellungsanzeiger auf und schrauben es auf die Haltesäule. Schrauben
Sie den Stellungsanzeiger wieder an.
Die Schraube mit der Markierung «0 % Position» ermöglicht die Einstellung
des Potentiometers (Rutschkupplung): Den Stellantrieb in Stellung ZU brin-
gen. Der Widerstand wird zwischen den Klemmen 16 und 17 gemessen.
Halten Sie mit der Hand das Zahnradgetriebe, das sich direkt unter
der Platte mit der Markierung «0 % Position» befindet, in seiner Lage
fest. Drehen Sie dann an der Schraube des Potentiometers, bis Sie einen
höheren Widerstandwert erreichen, der 0 Ohm übersteigt und konstant
zunimmt. Drehen Sie dann gegen den Uhrzeigersinn, um wieder einen
Wert nahe bei 0 Ohm zu erreichen.
Bringen Sie den Stellantrieb in Stellung AUF und merken Sie sich den
Widerstandswert für 100 %. Kehren Sie zur Stellung ZU zurück und
prüfen Sie, ob der Wert von 0 % wiederholbar ist und nahe bei 0 Ohm liegt.
Hinweise : Bei Systemen mit zwei Potentiometern werden beide Potentiometer
unabhängig voneinander eingestellt.
Signal-Umkehrung :
Um die Richtung des Signals umzukehren, kreuzen Sie die Potentiometer-
Drähte auf der Klemmenleiste des Stellantriebs (beispielsweise tauschen
Sie bei dem Anschluss 16/17/18 die Klemmen 16 und18 ).
9 STELLUNGSGEBER,TYPTAM (OPTION- Abb.7)
Der Stellungsgeber des Typs TAM ermöglicht die Fernübertragung eines
Signals von 0 bis 20 mA oder von 4 bis 20 mA im linearen Verhältnis zur
Ventilstellung.
Elektrische Anschlüsse :
Die Anschlüsse des Stellantriebes sind gemäß der Standardverdrahtung
(Hauptstromlaufplan) vorzunehmen. Berücksichtigen Sie auch die folgenden
Schaltungsbeispiele für den Stellungsgeber TAM. Der Wert der Stromversor-
gung muss zwischen 12 und 32 V (linearer Gleichstrom, gefiltert oder stabil)
liegen; die zulässige Last finden Sie in der unteren Tabelle.
Signalanpassung zur Drehrichtung (Abb. 8)
Der Stellungsgeber des Typs TAM gibt bei einem Standard-Stellantrieb
ein Signal ab, dessen Wert von der geschlossenen bis zur offenen Stel-
lung zunehmend größer wird. Die Öffnungsrichtung des angetriebenen
Elements ist gegen den Uhrzeigersinn gerichtet.
Wenn ein umgekehrtes Signal erforderlich ist, kann dies mit zwei Kontakt-
brücken (neben dem Potentiometer) erreicht werden:
- Im Uhrzeigersinn (direct signal) : Brücken 1-3 und 2-4.
- In Gegenrichtung (reversed signal): Brücken 1-2 und 3-4.
Einstellungen
Schließen Sie ein Milliamperemeter mit oder ohne Bürde an, um den
Ausgangsstrom zu messen.
- Die Einstellung hat immer bei 0/4 mA zu erfolgen.
- Bringen Sie den Stellantrieb in die Stellung, die dem Signal 0/4 mA
entspricht (als Voreinstellung ist dies die Endsstellung des angetriebenen
Elements im Uhrzeigersinn bei einer Armatur normal die Endlage ZU ).
- Während Sie nun manuell das Zahnradgetriebe, das sich direkt unter
der Platte mit der Markierung «0 %-Position» befindet, in seiner Lage
festhalten, drehen Sie die Potentiometerschraube (Rutschkupplung),
um den Bereich mit dem minimalen Stromwert zu erreichen. Suchen
Sie nun mit der (Potentiometerschraube) den Bereich, in dem das Signal
regelmäßig zunimmt, und drehen Sie dann zurück, um zu dem vorherigen
Minimalwert zurückzukehren. Dadurch hat das Potentiometer seine feste
Anfangsposition.
- Eine genaue Einstellung von 0/4 mA erfolgt durch die TAM-Schraube mit
der Bezeichnung «0/4 mA».
- Bringen Sie nun den Stellantrieb in die Stellung, die dem Signal 20 mA
entspricht (als Voreinstellung ist dies die Endstellung des angetriebenen
Elements gegen den Uhrzeigersinn -- bei einer Armatur normal die
Endlage AUF).
Stromversorgung
(VOLT) Max. zulässige
Last Ohm
12 150
34 750
30 1050

22 23
Kontrolle nach längerer Lagerung
a) Lagerungsdauer von weniger als 1 Jahr :
- Führen Sie eine Sichtprüfung der Elektrik durch.
- Betätigen Sie Wegendschalter, Drehmomentschalter, Knöpfe, Wahlschalter
usw., um den einwandfreien Betrieb der mechanischen Teile zu überprüfen.
- Führen Sie mehrere manuelle Schaltbewegungen durch.
- Überprüfen Sie das Schmierfett auf gute Beschaffenheit.
b) Lagerungsdauer von mehr als 1 Jahr :
- Eine Langzeitlagerung hat Einfluss auf die Beschaffenheit
von Schmierfetten. Die dünne Schmierfettschicht auf Achsen und
Lagerzapfen trocknet aus.
- Alle mechanischen Teile im Stellantrieb müssen deshalb ausgebaut,
mit frischem Schmierfett versehen und wieder eingebaut werden.
- Führen Sie eine Sichtprüfung der Elektrik durch.
- Betätigen Sie Wegendschalter, Drehmomentschalter, Knöpfe,
Wahlschalter usw., ... um den einwandfreien Betrieb der mechanis-
chen Teile zu überprüfen.
Schmiermittel
SHELL TIVELA COMPOUD (ST6: 2kg / ST14: 3kg / ST30: 3.5kg / ST70: 4.5kg).
- Drehen Sie an der Einstellschraube mit der Markierung «20 mA», bis Sie
auf dem Milliamperemeter genau 20 mA ablesen.
- Kehren Sie zur geschlossenen Stellung zurück und prüfen Sie, ob der
Wert von 0 % wiederholbar ist und nahe bei 0/4 mA liegt.
10 VORSICHTSMASSNAHMEN
Unmittelbar nach Inbetriebnahme müssen die Deckel wieder aufgesetzt
und festgeschraubt werden; dabei ist auf die Sauberkeit der Deckel-
dichtungen zu achten.
Zum Schutz der elektrischen Teile lassen Sie niemals die Stellantriebe
ohne Deckel stehen ( zum Beispiel auch nicht beim kurzfristigen Verlas-
sen der Baustelle).
Falls Wasser in das System eingedrungen ist, sind die elektrischen Teile
zu trocknen und ist der Elektroschutz zu überprüfen, bevor der Deckel
wieder angebracht wird.
11 WARTUNGUNDINSTANDHALTUNGDERSERVOMOTOREN
Instandhaltung
Die Einmalschmierung der ST-Stellantriebe reicht für ihre gesamte
Lebensdauer; sie bedürfen daher keiner besonderen Wartung. Die Ventils-
pindel und die Spindelmutter (Gewindebuchse) sollten jedoch regelmäßig
kontrolliert werden; auf Sauberkeit und einwandfreie Schmierung ist zu
achten. Falls die Automatisierung allgemein nur selten beansprucht wird,
empfehlen wir, die Stellantriebe zur Wartung von Zeit zu Zeit zu betätigen.
Lagerung
Ein Stellantrieb besteht aus elektrischen Bauteilen und aus fettgeschmier-
ten mechanischen Teilen. Obwohl die Hülle dieser Einheit sehr dicht ist,
können nach einer unsachgemäßen Lagerung bei der Inbetriebnahme des
Stellantriebs Schäden auftreten, wie Oxydation, Verklebung oder Blockierung.
Stellantriebe müssen in sauberen und trockenen Räumen gelagert und
gegen aufeinanderfolgende Temperaturschwankungen geschützt werden.
Stellantriebe nicht direkt auf dem Boden lagern.
Falls die Stellantriebe mit Heizwiderständen ausgerüstet sind, müssen
diese bei Feuchtigkeitsbildung mit der entsprechenden Spannung
versorgt werden (Standardspannung 230 Volt, ohne nähere Angaben
über die jeweilige Steuerung).
Kunststoff-Hilfsverschlüsse der Kabeleingänge und Kabelverschraubungen
auf festen Sitz und Dichtigkeit überprüfen. Bei Feuchtigkeitsbildung sind
sie durch Schraubverschlüsse aus Metall zu ersetzen. Die Gehäusedeckel
der elektrischen Bauteile sind auf Dichtigkeit zu überprüfen.

BERNARD CONTROLS
4 rue d’Arsonval - BP 70091 - 95505 Gonesse Cedex - France
Tel: +33.1. 34.07.71.00 - Fax: +33.1.34.07.71.01
E-mail: mail@bernardcontrols.com
Internet: http://www.bernardcontrols.com
AUSTRIA
IPU ING PAUL UNGER
WIEN
Tel. : +43 1 602 41 49
BELGIUM
BERNARD CONTROLS BENELUX
Info.benelux@bernardcontrols.com
BRUXELLES
Tel. : +32 (0)2 343 41 22
BRAZIL
JCN
SAO PAULO
Tel. : +55 11 39 02 26 00
CHINA
BERNARD CONTROLS CHINA
bcc.info@bernardcontrols.com
BEIJING
Tél. : +86 (0) 10 6789 2861
CZECH REPUBLIC
FLUIDTECHNIK BOHEMIA s.r.o.
brno@fluidbohemia.cz
BRNO
Tel. : +420 548 213 233-5
DENMARK
ARMATEC A/S
GLOSTRUP
www.armatec.dk
Tel. : +45 46 96 00 00
EGYPT
ATEB
gm@atebco.com
ALEXANDRIA
Tel. : +203 582 76 47
FINLAND
TALLBERG TECH OY AB
pekka.tontti@tallberg.fi
ESPOO
www.soffco.fi
Tel. : +358 0 207 420 740
GERMANY
BERNARD CONTROLS DEUFRA
bcd.mail@bernardcontrols.com
TROISDORF
Tel. : +49 22 41 98 340
GREECE
PI&MS Entreprises Ltd
HALANDRI
Tel. : +30 210 608 61 52
HUNGARY
APAGYI TRADEIMPEX KFT
BUDAPEST
Tel. : +36 1 223 1958
IRAN
ASIA INSTRUMENTS Co. Ltd.
TEHRAN
www.asiainstrumentsltd.com
Tel. : +98 21 8850 3065
ITALY
BERNARD CONTROLS ITALIA
info.it@bernardcontrols.com
RHO /MILANO
Tel. : +39 02 931 85 233
MALAYSIA
ACTUATION & CONTROLS
ENGINEER
JOHOR BAHRU
Tel. : +60 7 23 50 277 / 23 50 281
MIDDLE-EAST
BERNARD CONTROLS
MIDDLE-EAST
bernact@emirates.net.ae
DUBAI - U.A.E.
Tel. : +971 4 39 80 726
MOROCCO
AQUATEL sarl
CASABLANCA
Tel. : +212 22 66 55 71
NETHERLANDS
BERNARD CONTROLS BENELUX NV
hans.nobels@bernardcontrols.com
AN ZWAAG
Tel. : +31 (0)229-298083
NEW ZEALAND
MRCTRANSMARK NZ LTD
bill.sunley@mrctransmark.com
AUCKLAND
Tel. : +64 9 276 4149
NORWAY
KSB LINDFLATEN AS
firmapost@lindflaten.no
LYSAKER
Tel. : +476 71 29 900
POLAND
MARCO
WARSAW
Tel. : +48 22 864 55 43
PORTUGAL
PINHOL, GOMES & GOMES LDA.
[email protected]om.pt
CARNAXIDE
Tel. : +351 21 425 68 50
RUSSIA
BERNARD CONTROLS RUSSIA
bernard@amotek.net
c/o AMOTEK - MOSCOW
Mob.: +7 917 562 8591
Tel./Fax : +7 495 343 43 80
RUSSIA
A.E.T. (agent)
ST PETERSBURG
Tel./Fax : +7 812 320 55 97
Mob.: +7 812 956 35 14
SINGAPORE
ACTUATION & CONTROLS ENG.
(ASIA)
SINGAPORE
Tel. : +65 65 654 227
SPAIN
BERNARD CONTROLS SPAIN
bernardserv[email protected]
MADRID
Tel. : +34 91 30 41 139
SOUTH AFRICA
A-Q-RATE AUTOMATION CC
BERTSHAM
Tel. : +27 11 432 58 31
SOUTH KOREA
RENTEC CO Ltd (Water market)
totor[email protected]om
GYEONGGI-DO
Tel. : +82 31 399 73 23
SOUTH KOREA
YOO SHIN E&I Co. Ltd
(Oil & Gas market)
SEOUL
Tel. : +82 2 406 62 78
SWITZERLAND
MATOKEM AG
info@matokem.ag
ALLSCHWIL
www.matokem.ch
Tel. : +41 61 483 15 40
THAILAND
BERNARD CONTROLS
SOUTH-EAST ASIA
j.chounramany@bernardcontrols.com
BANGKOK
Tel. : +66 2 640 82 64
TURKEY
OTKONSAS
ISTANBUL
Tel. : +90 216 326 39 39
UNITED ARABS EMIRATES
EMIRATES HOLDINGS
emhold@emirates.net.ae
ABU DHABI
Tel. : +97 12 644 73 73
UNITED-KINGDOM
ZOEDALE Plc
BEDFORD
Tel. : +44 12 34 83 28 2
USA/CANADA/MEXICO
BERNARD CONTROLS Inc
bsales@bernardcontrols.com
HOUSTON - TEXAS
Tél. : +1 281 578 66 66
This manual suits for next models
2
Table of contents
Languages:
Other Bernard Controls Controllers manuals
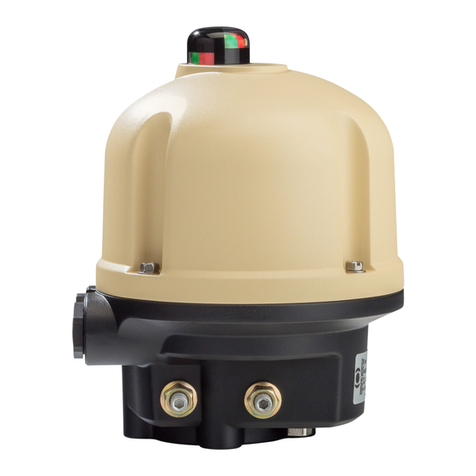
Bernard Controls
Bernard Controls AQL Range User guide
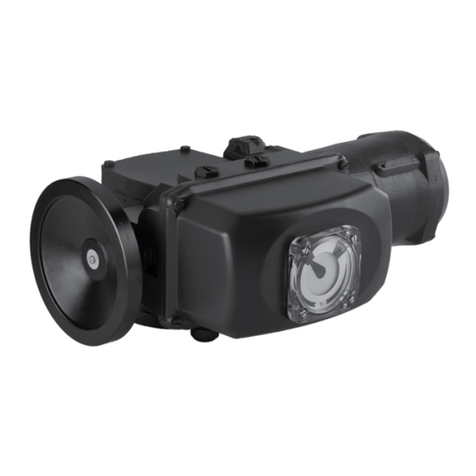
Bernard Controls
Bernard Controls SD Series Instructions for use
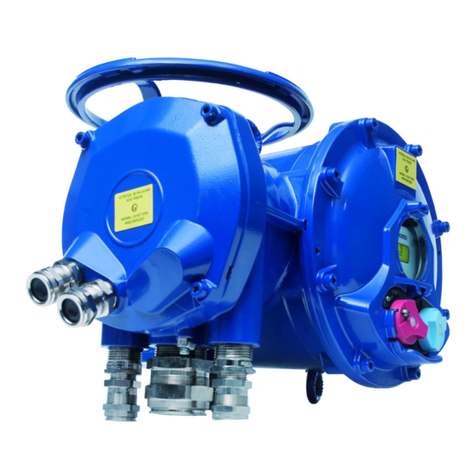
Bernard Controls
Bernard Controls SQX Series Installation manual
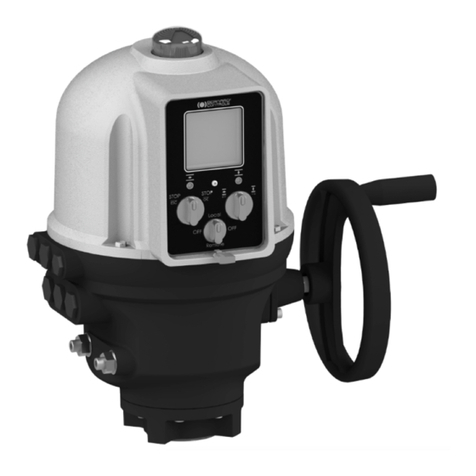
Bernard Controls
Bernard Controls AQ Logic Series User guide
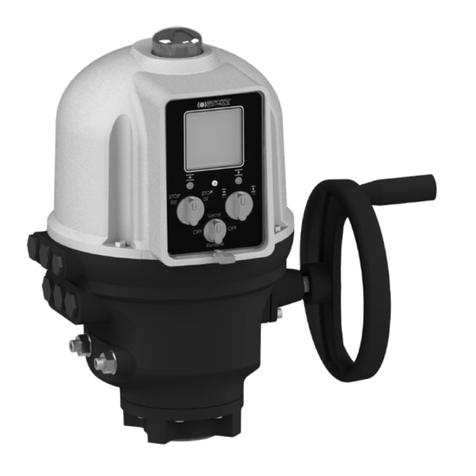
Bernard Controls
Bernard Controls AQ Logic Series User guide
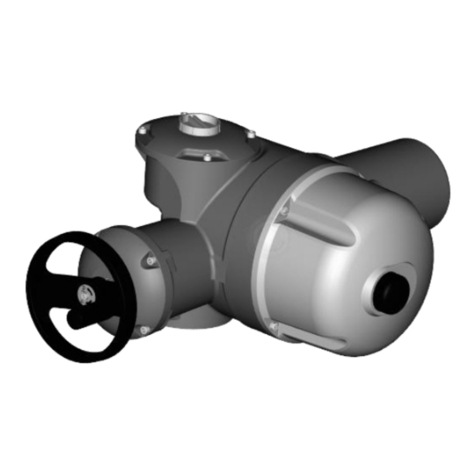
Bernard Controls
Bernard Controls AT SWITCH RANGE User guide
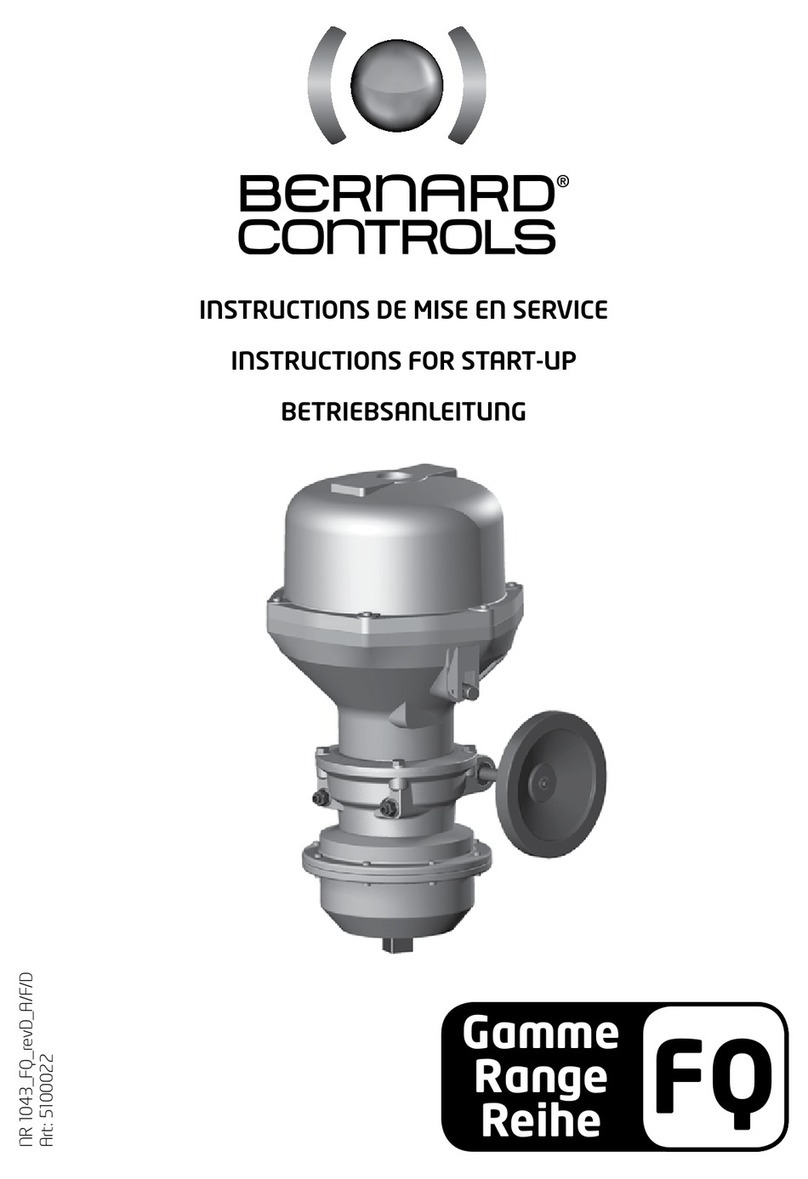
Bernard Controls
Bernard Controls Gamme FQ Series Installation manual
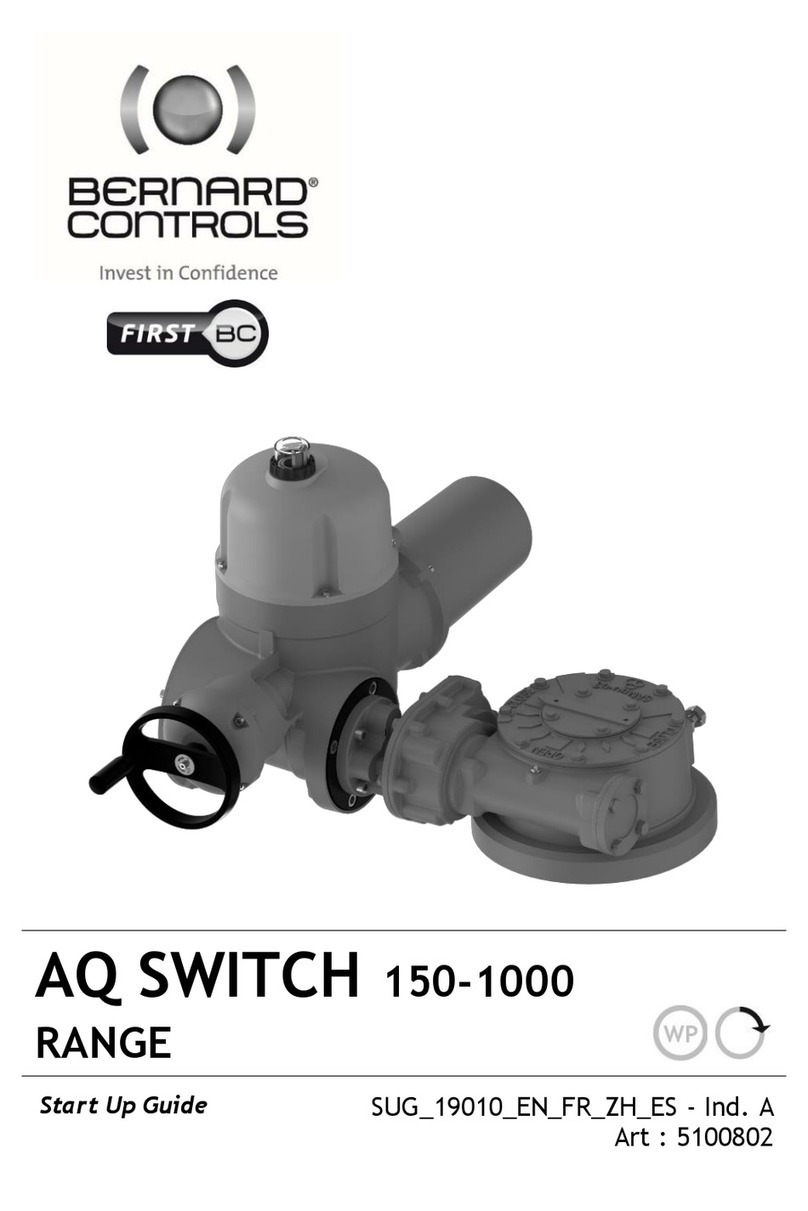
Bernard Controls
Bernard Controls AQ SWITCH 150-1000 User guide
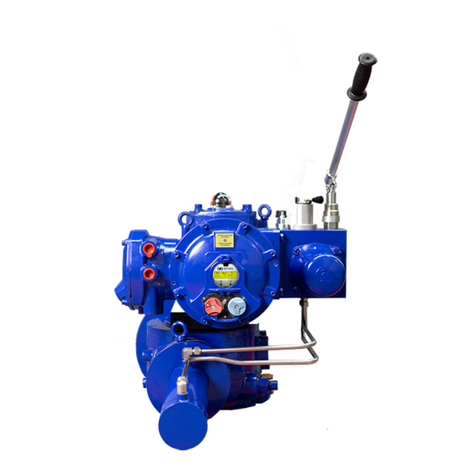
Bernard Controls
Bernard Controls FSE Series User guide
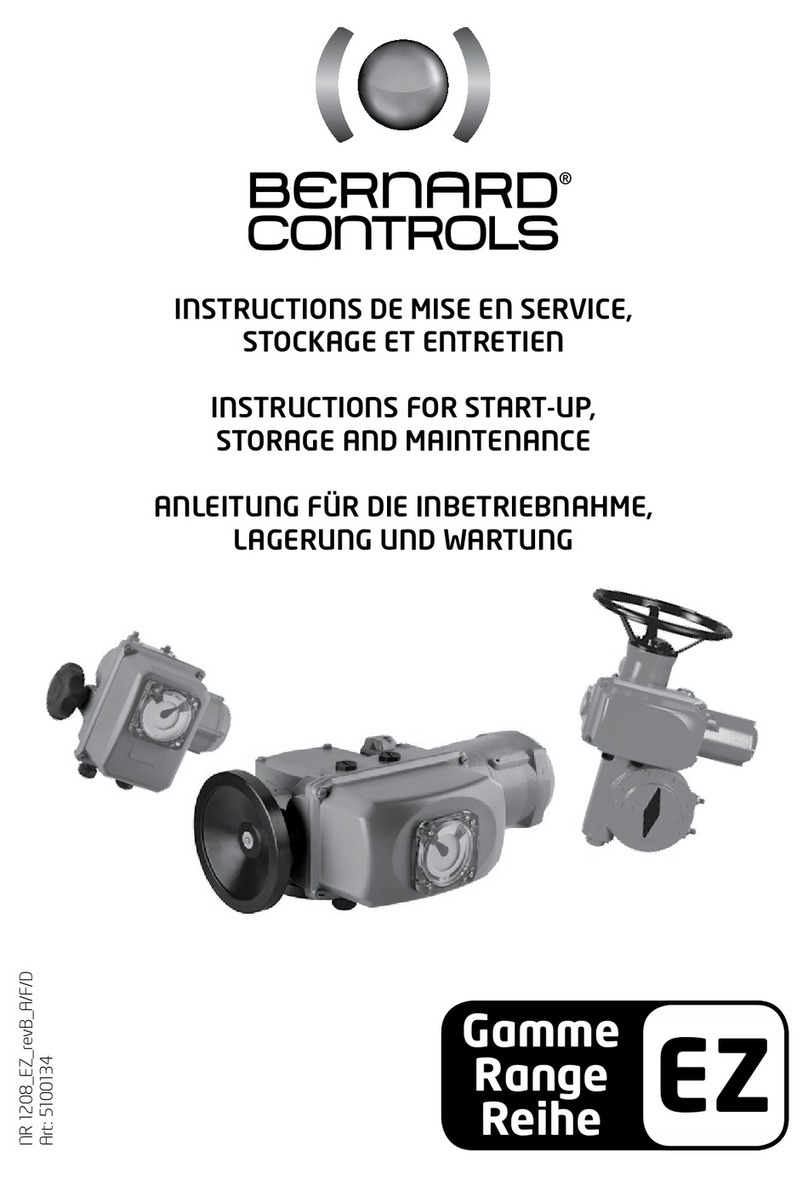
Bernard Controls
Bernard Controls EZ Series Instructions for use