Bluerock Tools Z1/LRB/TS User manual

OPERATIONAL MANUAL
MODEL: 12” Z1/LRB/TS CORE DRILLING MACHINE
WITH TILTING STAND / LARGE ROLLING BASE
\
by BLUEROCK ® Tools
Volume
1

MWS-12”Z1TS CORE DRILL
UNPACKING THE ITEM
CAUTION: This machine is packed together with items that may be sharp, oily and overly
heavy objects. Remove the machine from the packaging in a safe manner. Check to ensure
all accessories are included with the item while unpacking. If any parts are found to be
missing, contact the retailer as soon as possible. Do not throw away the packaging until the
item is out of the guarantee period. Dispose of the packaging in an environmentally
responsible manner. Recycle if possible. Keep all plastic bags away from children due to risk
of suffocation.
WEEE - Waste Electrical & Electronic Equipment. Note this machine should be disposed of as electrical & electronic waste.
SLURRY DISPOSAL
NOTE: It is recommended to dispose of the drilling slurry (the muddy/dusty water material) in
an environmentally responsible manner. The disposal of slurry directly into sewage
systems, sewers, lakes, rivers, or direct earth without treatment can be environmentally
harmful and possibly illegal. Ask your local public authorities about current regulations in
your area.
©THE NEWMAN TRADING COMPANY LLC DBA BLUEROCK® TOOLS 2016
1100 SW 16th St • Suite D
Renton, WA 98057
Phone 206.604.8363 • Fax 425.572.5167
www.bluerocktools.com

12”Z1/TS CORE DRILL
Table&of&Contents&
SAFETY' 1!
PRE-OPERATIONAL SAFETY CHECKS! 1!
OPERATIONAL SAFETY CHECKS! 1!
HEALTH WARNINGS! 2!
SPECIFICATIONS' 4!
INCLUDED'ACCESSORIES' 4!
ADDITIONAL'AVAILABLE'ACCESSORIES' 5!
ADDITIONAL ACCESSORIES FOR THIS MACHINE CAN BE FOUND IN BLUEROCK ®TOOLS ONLINE SHOP AT
WWW.BLUEROCKTOOLS.COM OR FROM YOUR LOCAL RETAILER.! 5!
OPERATIONS' 6!
PURPOSE! 6!
OPERATIONAL PRINCIPLES! 6!
MACHINE COMPONENTS! 6!
TRANSPORTING THE MACHINE! 7!
RUNNING THE MACHINE! 8!
INSTALLING CORING BITS! 9!
TROUBLESHOOTING'10!
GENERAL'MAINTENANCE'11!
OCCASIONAL'MAINTENANCE'11!
PARTS'LIST'–'MOTOR'AND'GEARBOX'13!
BREAKDOWN'VIEW'–'MOTOR'14!
BREAKDOWN'VIEW'–'GEARBOX'15!
PARTS'LIST'–'TILTING'STAND'16!
BREAKDOWN'VIEW'–'DRILLING'STAND'17!

12”Z1/TS CORE DRILL
1
Safety
DO NOT USE THIS MACHINE UNLESS YOU HAVE READ THE
OPERATING INSTRUCTIONS!
Safety glasses must be worn at all
times in work areas.
Long and loose hair must be
contained.
Appropriate footwear must be worn.
Close fitting/protective clothing
must be worn.
Safety gloves should be worn at all
times and jewelry must not be worn.
Hearing protection should be
worn when using this machine.
Hard-hat must be worn while using
machine.
Dust mask must be worn while
using this machine.
Read operational manual prior to use.
PRE-OPERATIONAL SAFETY CHECKS
ØExamine the power cord and plug for damage. This tool is supplied with a ground plug and must always be used with
a properly grounded circuit.
ØExamine the body of the machine and inspect for damage or defects.
OPERATIONAL SAFETY CHECKS
ØONLY to be operated by qualified personal who have read instructions.
oNOTE: Failure to read and follow instructions could result in electrical shock, fire, property damage and/or
serious injury!
ØDO ensure all non-essential people are clear of the immediate work area.
ØDO be attentive at all times. Keep your eye on the work piece. Always be in a sensible state of mind and do not use
the machine if you cannot fully concentrate.
ØDO keep body parts, clothing & power cords clear of turning/cutting pieces.Stay alert and use common since when
using this tool.
ØDO allow machine to reach operating speed before starting a hole.
Chapter
1

12”Z1/TS CORE DRILL
2
ØDO unplug machine while changing or adjusting cutting bits so as not to accidentally turn machine on.
ØDO remove adjusting wrenches prior to turning the machine on.
ØDO guard against electric shock by only operating this tool on a properly functioning GFCI (Ground Fault Circuit
Interrupt) circuit.
ØDO be mindful that power tools can expose an operator to vibrations transmitted trough contact with the machine.
Prolonged exposure can lead to medical issues which should be discussed with a medical professional.
ØDO tie in a drip loop in the power cord to prevent water from running into the power receptacle.
ØDO use a dust extraction system for cutting materials that create dust. The operator should also wear a protective
respiratory device.
ØDO NOT make adjustments to machine while the machine is running.
ØDO NOT switch off the machine when it is under load, except in an emergency.
ØDO NOT remove or modify grounding plug. Only to be used on a properly grounded GFCI circuit.
ØDO NOT leave the machine running when not in use.
ØDO NOT hold the work piece by hand or using body. Always mechanically clamp or secure work piece.
ØDO NOT allow operator to make contact with grounded surfaces such as metal objects.
ØDO NOT allow liquids to enter the machine’s ventilation system.
ØDO NOT operate machine outside of machine specifications.
ØDO NOT touch moving parts while the machine is running as death or dismemberment could occur.
ØDO NOT operate machine overhead (Inverted) when drilling “wet” type cores.
ØDO NOT remove machines electrical components while connected to a power source. Only to be removed for service
by qualified personal and put back on the machine after service is complete.
ØDO NOT allow children or untrained personal to operate machine.
ØDO NOT use this machine in the rain or a wet environment.
ØDO NOT operate in the presence of explosive materials as power tools create sparks which may ignite dust or fumes.
ØDO NOT drill into an area that may contain a live electrical wire/circuit.
ØDO NOT use this machine without safely securing to the work piece being drilled.
ØDO NOT use full water pressure when drilling with “wet” type bits! You only need minimal water to drill with these
machines. Extreme water pressure can cause water to enter the gearbox!
ØDO NOT operate this machine on a lower voltage as it may result in reduced power level and the machine could
become unstable while cutting. This could also limit the motor life.
oNOTE: Use of long small gauge power extension cords can result in decreased voltage. As local voltages
can vary, it may be a good idea to test the voltage at the end of the extension cord to ensure proper voltage
requirements are met. You might also consult an electrician to make sure the length of cord matches up
with the proper wire gauge for this size motor. Make sure to use outdoor cords when operating outdoors.
HEALTH WARNINGS
ØCertain dust created by drilling contains chemicals known to cause cancer, birth defects or other reproductive harm.
The examples of these chemicals are below:
oLead from lead based paint.

12”Z1/TS CORE DRILL
3
oCrystalline silica from bricks, cement and assorted masonry products.
§TO REDUCE RISK OF EXPOSURE TO THESE CHEMICALS, WORK IN A WELL VENTILATED
AREA WITH VACUUM SYSTEMS, RESPIRATORS AND WITH ALL SUITABLE SAFETY
EQUIPMENT.

12”Z1/TS CORE DRILL
4
Specifications
ELECTRICAL DATA
Voltage
110V, 50-60Hz, Single Phase
Current
21.6 Amps (30A Circuit Use Recommended)
Motor Size
2600W
Power Connection
US Standard 3 Prong Type B Plug
MECHANICAL DATA
Cutter Range
1” to 12” Max Diameter (300mm)
Cutting Speed
460/900 RPM Two Speed Gearbox
1) Gear 2 (900 rpm) for 1”-4” Holes
2) Gear 1 (460 rpm) for 4”-12” Holes
Tool Holder
Direct Arbor 1-1/4” 7 UNC Spindle
Safety Clutch
Yes
Water hose and Valve
Yes
Rolling/Vacuum/Tilting Base
Yes
Travel
21”
SHIPPING DATA
Shipping Weight
78 Lbs
Shipping Carton
40” x 20” x 17”
Included Accessories
DESCRIPTION
QTY
Instruction Manual
1
Wrenches
2
Feed Handle
1
Water Hose and Valve
1
Alternate Hose
1
Top Bolt for Binding in Ceilings
1
Hex Wrench
3
Spare Brushes (set)
1
Vacuum Base Accessories
1
Chapter
2

12”Z1/TS CORE DRILL
5
Note
UPON RECEIPT, CHECK CAREFULLY TO ENSURE THAT THE
MACHINE IS IN GOOD CONDITION AND HAS ALL
ACCESSORIES LISTED ABOVE.
Additional Available Accessories
Additional accessories for this machine can be found in BLUEROCK ® Tools
online shop at www.bluerocktools.com or from your local retailer.
DESCRIPTION
120V Vacuum Pump 1 L/S Displacement
1” Wet Coring Bit
1.25” Wet Coring Bit
1.5” Wet Coring Bit
1.75” Wet Coring Bit
2” Wet Coring Bit
2.5” Wet Coring Bit
3” Wet Coring Bit
3.5” Wet Coring Bit
4” Wet Coring Bit
4.5” Wet Coring Bit
5” Wet Coring Bit
6” Wet Coring Bit
7” Wet Coring Bit
8” Wet Coring Bit
9” Wet Coring Bit
10” Wet Coring Bit
11” Wet Coring Bit
12” Wet Coring Bit
1” Dry Coring Bit
1.25” Dry Coring Bit
1.5” Dry Coring Bit
1.75” Dry Coring Bit
2” Dry Coring Bit
2.5” Dry Coring Bit
2.75” Dry Coring Bit
3” Dry Coring Bit
3.5” Dry Coring Bit
4” Dry Coring Bit
5” Dry Coring Bit
1-1/4” 7 UNC to 5/8” 11 UNC Core Bit Adapter
10” Extension Rod
18” Extension Rod

12”Z1/TS CORE DRILL
6
Operations
Note
THOROUGHLY READ THROUGH THE ENTIRE MANUAL BEFORE
OPERATING THIS MACHINE!
PURPOSE
ØThe purpose of the 12”Z1 LRB/TS Core Drill is to drill through masonry, concrete or other mineral rock
types using annular coring bits.
ØThese drills are designed to be bolted to the drilling surface through their base.
oNOTE: Make sure the base fits completely on the surface and the base is securely fastened using
wedge anchors to bolt to the surface.
ØThese machines can be used vertically, horizontally or overhead (inverted) provided an acceptable work
environment. NOTE: For safety, when drilling horizontally or overhead a safety chain/strap should always
be used.
oCAUTION: If drilling overhead you are only permitted to use dry type core bits with a dust
collection system. “Wet” type holes overhead would allow water into the motor and create an
extremely dangerous situation.
OPERATIONAL PRINCIPLES
ØThe main drilling shaft rotates in a forward clockwise direction. The main drilling motor connects to the
tool spindle to make contact with a surface and slowly bore a hole. Using the feed handles on the side of
the drill, the user can raise or lower the drilling motor.
ØThese drills are ONLY to be used with diamond impregnated coring bits.
oWhen drilling with “wet” type bits, the bit ends pulverizes the material and the water brings the
material out of the cut.
oWhen drilling with “dry” type bits, the bit end pulverizes the material and dust brings the material
out of the cut.
MACHINE COMPONENTS
ØThe main components of the 12”Z1 LRB/TS are the spindle, gearbox, motor, carriage, drill stand and
wheeled base. The spindle is driven by the transfer case and the motor.
oThese components must be not be removed except by a qualified technician. Power must be
disconnected prior to any service.
Chapter
3

12”Z1/TS CORE DRILL
7
ØThis machine has one primary adjusting point for the angle between the drill stand and the drill motor. The
angle Adjusting bolt (12 below) can be loosened to adjust the angle and retightened when desired angle is
achieved. NOTE: The drill carriage can also be locked in place by twisting until the locking bolt engages
towards the carriage. To unlock the carriage pull out the bolt and turn.
TRANSPORTING THE MACHINE
ØWhen transporting the machine, always lock the carriage bolt.
ØAlways carry the machine with both hands.
ØDO NOT transport the machine with bits in the spindle.
ØWhen using the wheels, tilt the machine back towards the operator and once the wheels are engaged with
the ground pull or push the machine on the ground.
oAvoid dragging the vacuum rubber. You can take the rubber out if not using.
ØIf transporting inside a vehicle, it is recommended to transport it on its side so as to avoid the item falling
over.
ØDO NOT carry/pull the machine by the cord.
ØDO NOT allow the cord or plug to drag along the floor when transporting.
1) Motor Brush Holder
2) Motor On/Off Switch
3) Top Bolt for Binding in Ceilings
4) Drill Motor
5) Carriage Adjusting Bolts
6) Water Hose and Valve
7) Drill Carriage
8) Feed Handle
9) Gearbox
10) Spindle
11) Drill Stand
12) Angle Adjusting Bolt
13) Stand Base
14) Base Wheels
15) Leveling Bolts

12”Z1/TS CORE DRILL
8
RUNNING THE MACHINE
ØDo all pre-operational and operational safety checks from Chapter 1.
ØConsider your security and stability as well as the orientation of the machine in the work area.
oConsider the work surface material, condition, strength, density and rigidity. These factors
directly affect the tools efficiency.
ØSecure the machine base to the work surface by using a wedge anchor, vacuum system or other method to
ensure the base does not move.
ØUse the four leveling bolts on the corners of the base to level the machine if needed.
oIf not using the vacuum base, you can either take out the vacuum foam or adjust the leveling
bolts down ½” past the foam. It is generally recommended to take the foam out when not using
as it can cause tears in the foam material transporting and moving the machine.
ØAfter placing the machine in work area, connect a safety chain or strap if necessary.
oA safety chain should attach to the machine (preferably through the carrying handle or O bolt) as
well as attached to the work area in such a manner that prevents the machine from detaching or
falling from the work area.
ØIf necessary, adjust drilling angle.
oLoosen the lower side bottom bolt on the base as necessary.
oAdjust the angle and tighten the side bolt
ØEnsure the feed handles are securely attached to the feed spindle.
ØEnsure the work surface is free of debris, oil, etc.
ØSelect and set up fluid delivery method or dust system.
ØSelect the gear you will be using.
oDo not force the gear shifter when changing between gears. There is a neutral position between
gear 1 and gear 2.
oChange gears when the machine is stopped or almost stopped.
ØIf using the machine horizontally with the water system, connect hose to the side of the machine using the
connector.
oThis connector takes standard ¾” US garden hose hookup.
oMake sure the water valve is in the off position.
§This is generally at a 90 degree angle from the valve hose.
oPartially turn the water spigot on (usually half a turn).
§CAUTION: DO NOT turn the hose on fully! You need sufficient water when using wet
type bits. Using too much water pressure can cause the bits to not cut properly as well
as water entering the gearbox.
ØSelect appropriate size cutting bit. See section below for details on securing bit.
ØCheck that the machine is firmly attached to the work area.
ØPlug the machine into power source.
oForm a loose knot in the power cord close to the plug connection to prevent fluid from running
down the cord and into the power receptacle.
ØTurn feed handle raising the cutter until the bit is above the work surface.

12”Z1/TS CORE DRILL
9
ØOpen the water valve to allow water to come out to the work surface.
ØATTENTION: BE AWARE THESE MACHINES ARE EXTREMELY POWERFUL. THEY HAVE A TREMENDOUS
AMOUNT OF TORQUE, WHICH MIGHT NOT BE SUITABLE FOR ALL POTENTIAL USERS. ESPECIALLY IN
LOW GEAR AND WITH LARGER BITS. DESPITE THE SAFETY CLUTCH, THESE DRILLS CAN STILL
INJURE THE USER. IF IN DOUBT, CONTACT A PROFESSIONAL FOR ADVICE.
ØTurn the machine on by flipping the breaker switch to the “on” position.
ØVery slowly engage the cutting bit with the material surface by lightly engaging the hand crank down
towards the material.
oNOTE: During the initial stages of contact the bit may wander.
ØAfter about 1/8” of cutting has been achieved in the work surface, slightly more force can be applied. This
will be the normal amount of force the rest of the hole.
oNOTE: Do not force the hole. Let the machine do most of the work. Excessive physical effort
should be avoided as it can cause damage to the machine or the user.
oIf the unit jams in a hole, stop the drill immediately to prevent injury. Disconnect the drill from the
power supply and loosen the cutter by turning drill spindle counterclockwise. Never attempt to
free bit by starting motor!
§After an interruption in drilling, make sure the drill bit is free and turns before restarting
the hole. Be very careful at this point to make certain the drill does not bind when
restarting.
ØMake sure to keep the cutting material lubricated.
ØEase up on feed pressure as the cutter starts breaking through the backside of the material.
oBe certain all is clear on the output side of this core to prevent injury to persons or property.
ØFinish drilling the hole.
ØTurn the motor off and disconnect power once the drill is safely back up in the non-drilling position.
ØTurn water valve off.
ØUnbolt the wedge anchor.
ØDisconnect safety chain/strap and move the drill to a new drilling location.
INSTALLING CORING BITS
ØWARNING: Core bits can be sharp and should only be handled with gloves so as not to cut the user during
installation or removal.
ØCheck that the bits are not damaged.
oCoring bits that are damaged should not be used.
ØMake certain the machine is unplugged from power.
ØRaise the drill motor to ensure ample room to install the bit.
oApply grease to the spindle thread to prevent corrosion and allow easier core bit removal.
ØInsert the coring bit and screw it onto the drill spindle.
ØTighten the bit until fully tightened.
oUse wrenches that fit the spindle and coring bit to fully tighten.

12”Z1/TS CORE DRILL
10
Troubleshooting
Note
SERVICING SHOULD ONLY BE DONE BY A QUALIFIED TECHNICIAN.
DON’T FORGET TO UNPLUG POWER TO UNIT PRIOR TO SERVICE!
PROBLEM
SOLUTION
Motor does not turn on.
1) Check external power source (extension cord, breaker, etc).
2) Loose internal wire. Check and secure if necessary.
3) Motor brushes defective. Replace if necessary.
4) Check to ensure the motor on/off switch is operable. Replace if
necessary.
Excessive sparking
when motor is running.
1) This may indicate the presence of debris in the motor or worn out
carbon brushes. Check the brushes for unusual wear and replace
if necessary. Clean out the internal motor armature if necessary.
2) Armature has a rough edge. Inspect and replace if necessary.
Hole is not cutting.
1) Cutting bit is dull. Replace bit.
2) Work area material is not appropriate for bit type.
Bit is jammed while
coring.
1) Debris is lodged between core hole and bit. Rotate bit in both
directions to and inspect bit for debris.
2) Make sure stand is secured to work surface.
Coring speed has
reduced.
1) Bit has hit rebar. Adjust feed control to prevent motor overload
while cutting through rebar.
2) Diamonds on bit have glazed over. Deglaze bit or dress diamond
rim on bit and check water flow rate.
3) Diamonds on bit have worn away. Replace core bit.
4) New core bit. Core at slow rate with new bits for 2-3 coring cycles.
5) The safety clutch is slipping. Tighten clutch.
6) Drilling progress is prevented by an accumulation of dust. Use
suitable vacuum cleaner.
7) Water flow rate is too low. Increase water flow.
8) Core is stuck in the core bit. Remove core.
Core bit appears to
wobble.
1) Spindle is damaged. Replace spindle and check bearings.
2) Bit is bent or damaged. Replace bit.
3) The core bit is not screwed securely onto the spindle.
4) Coring material is attaching to the bit. Inspect bit and increase
water flow rate.
Water escapes at the
water swivel or gear
housing.
1) The water pressure is too high. Turn down water flow.
2) The shaft seal is defective. Replace seal
3) The water hose is damaged. Replace hose.
Chapter
4

12”Z1/TS CORE DRILL
11
General Maintenance
ØInspect electrical cords and electrical connections.
ØKeep machine clean and free of debris.
ØCheck for misalignment, binding and breakage of all moving parts. If damaged, repair tool before use.
ØKeep cutting tools sharp and clean. Sharp bits are less likely to bind and are easier to control.
Occasional Maintenance
ØHave the power tool serviced by a qualified service technician using identical replacement parts.
oChange motor brushes:
1) Disconnect drill from power.
2) Unscrew left and right side brush holder caps using a flathead screw driver.
3) Take out old brushes.
oIf you need to, use the screw driver to nudge them out.
4) Replace with exact same size new brushes.
5) Screw in brush holder caps tightly.
oAdjusting Carriage:
1) Periodically check and adjust slides as necessary.
2) Use hex wrench to loosen the hex bolts on the carriage. There are four hex bolts on
each adjusting slide. Backing out the bolts will loosen feed tension, while tightening
the bolts will increase feed tension.
3) Adjust the bolts evenly while moving the handle up and down so that there’s no free
play yet not binding anywhere through its range of travel.
oChange Gear Oil:
1) Change if necessary using NLGL-2 grade grease. This service is generally done around
the 50 hour service mark.
oAdjust Safety Clutch:
1) Adjust clutch as necessary.
oNOTE: A torque wrench is necessary for this service.
oLocate the hex screws holding the gear housing together and remove them.
Chapter
5

12”Z1/TS CORE DRILL
12
oGently pull the gear housing apart. You may use a couple flat screwdrivers to
gently apply pressure to separate the housings.
oTake the main clutch nut off of the clutch. Apply some Loctite type of thread
glue on the clutch threads.
oReapply the nut to the thread.
oHold the spindle in place using the box wrench. See diagram below.
oUse the torque wrench to tighten the clutch nut.
oTorque the tensioning nut to 15 NM (130ft/lbs).
oWith the clutch nut tightened, reassemble the housings. Make sure the
orientation of the internal gears is correct and the housings mate correctly.
oReattach the bolts that hold the housing together.

12”Z1/TS CORE DRILL
13
Parts List – Motor and Gearbox
NO
Name
NO
Name
NO
Name
1
Spring ring for holes
36
Shaft sleeve
71
Brush assembly
2
Washer
37
Hex nut
72
Brush holder
3
Rubber sealing 42x55x8
38
Needle bearing BK1816
73
Rivet of label
4
Label
39
Seal ring
74
Label
5
Water sealer
40
Adapter of water switch
75
M5x10 socket head cap screw
6
Adjust shim
41
Water switch
76
Rear cover of shell
7
Main spindle
42
Ball valve
77
M4x14 nut bolt
8
Spring ring for holes 52
43
Binding ring
78
Socket head cap screw M4x90
9
6205 bearing
44
Shim
79
Spring washer
10
Label
45
Binding bolt
80
Plain washer
11
Seal gland
46
Water adapter with machine
81
Nut
12
Small cover plate
47
6201 bearing
82
Washer
13
M4x6 nut bolt
48
No7 gear spindle
83
Spring washer
14
Spring plate
49
Ball thrust bearingAXK3047
84
M5x6 nut bolt
15
Pin 10x30
50
No6 gear
85
Cover of switch box
16
Spring column pin
51
Copper tube
86
M4x10 nut bolt
17
Spring
52
Flat key C4x12
87
Seal of switch box
18
Spring plate
53
Change speed spindle
88
Electric capacity
19
Column pin A3x25
54
Ball thrust bearingAXK4060
89
Switch
20
Button
55
Copper tube
90
Switch box
21
Spring for shaft
56
No4 gear
91
ST4.2x13 nut bolt
22
Middle cover
57
Ball thrust bearingAXK1730
92
Wire with plug
23
Mechanic stick
58
6200 bearing
93
PRCD switch (Optional)
24
Inner hexagonal screwM6x105
59
Gear spindle
94
Protecting jacket
25
Spring washer
60
Flat key C4x16
95
Ring of wire
26
Plain washer
61
No2 gear
96
M4x16 nut bolt
27
Gear box
62
6201 bearing
28
Pressing ring
63
Armature
29
Small friction disk
64
Draught ring
30
No8 gear
65
Bead flange
31
Spline tube
66
Stator
32
Outer friction disk
67
Cover of stator
33
Friction disk
68
6202 bearing
34
Inner spline friction disk
69
Shell
35
Disk spring
70
Brush cap cover
Chapter
6

12”Z1/TS CORE DRILL
14
Breakdown View – Motor

12”Z1/TS CORE DRILL
15
Breakdown View – Gearbox

12”Z1/TS CORE DRILL
16
Parts List – Tilting Stand
1
Handle ball
26
Hexagonal bolt
2
Operating stick for machine
27
Clamping washer
3
Lengthen sleeve
28
Supporting board
4
Clutch pin
29
Inner hexagonal oval screw
5
Ring for spindle
30
Elevating body cover
6
Ball-bearing
31
Inner hexagonal oval screw
7
Operating gear spindle
32
Handle
8
Pin
33
Inner hexagonal oval screw
9
Elevating body
34
Pin
10
Spring washer
35
Sliding wheel
11
Screw
36
Supporting case for sliding wheel
12
Square pipe assembly
37
Adjust bit
13
Position pipe assembly
38
Stop screw
14
Hexagonal bolt
39
Screw
15
Spring washer
40
Screw
16
Supporting board
41
Screw
17
Clamping washer
42
Track strip
18
Position screw assembly
43
Pin
19
Spring
44
Board for add thickness
20
Nut
21
Slurry Catcher Holder (slurry
catcher not included)
22
A type base
23
Hexagonal bolt
24
Wheel
25
Nut

12”Z1/TS CORE DRILL
17
Breakdown View – Drilling Stand
Table of contents
Other Bluerock Tools Drill manuals
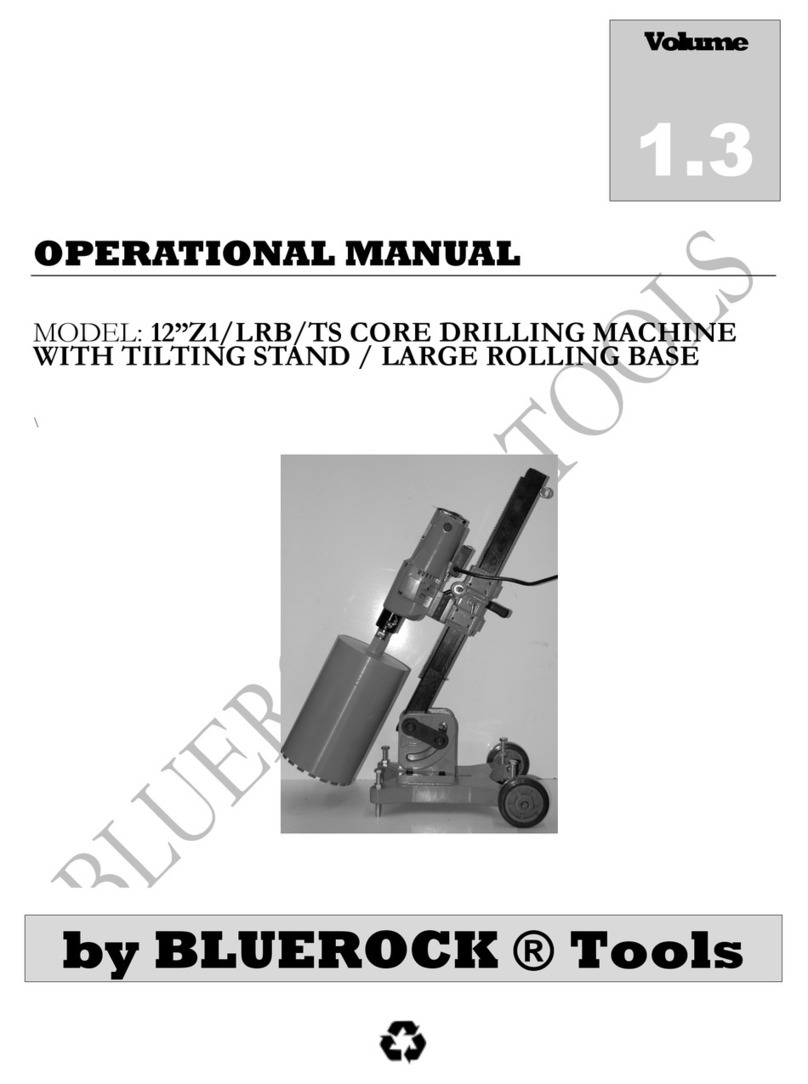
Bluerock Tools
Bluerock Tools 12"Z1/LRB/TS Quick start guide
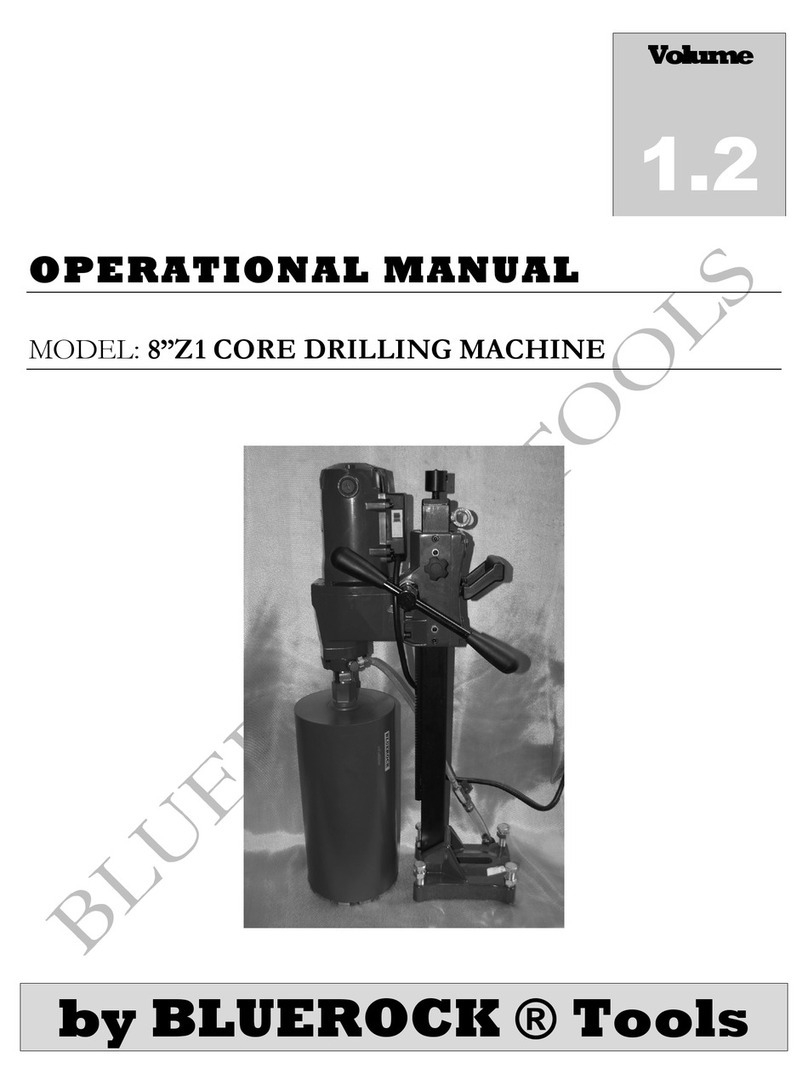
Bluerock Tools
Bluerock Tools 8"Z1 Quick start guide
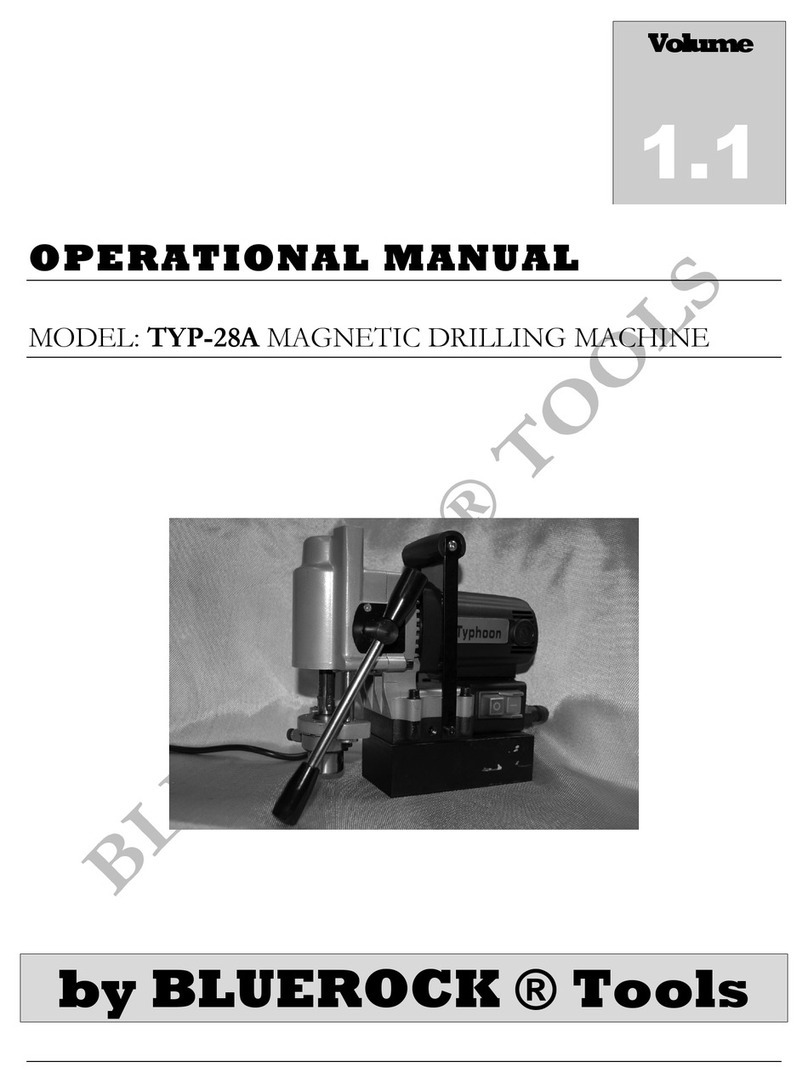
Bluerock Tools
Bluerock Tools TYP-28A Quick start guide
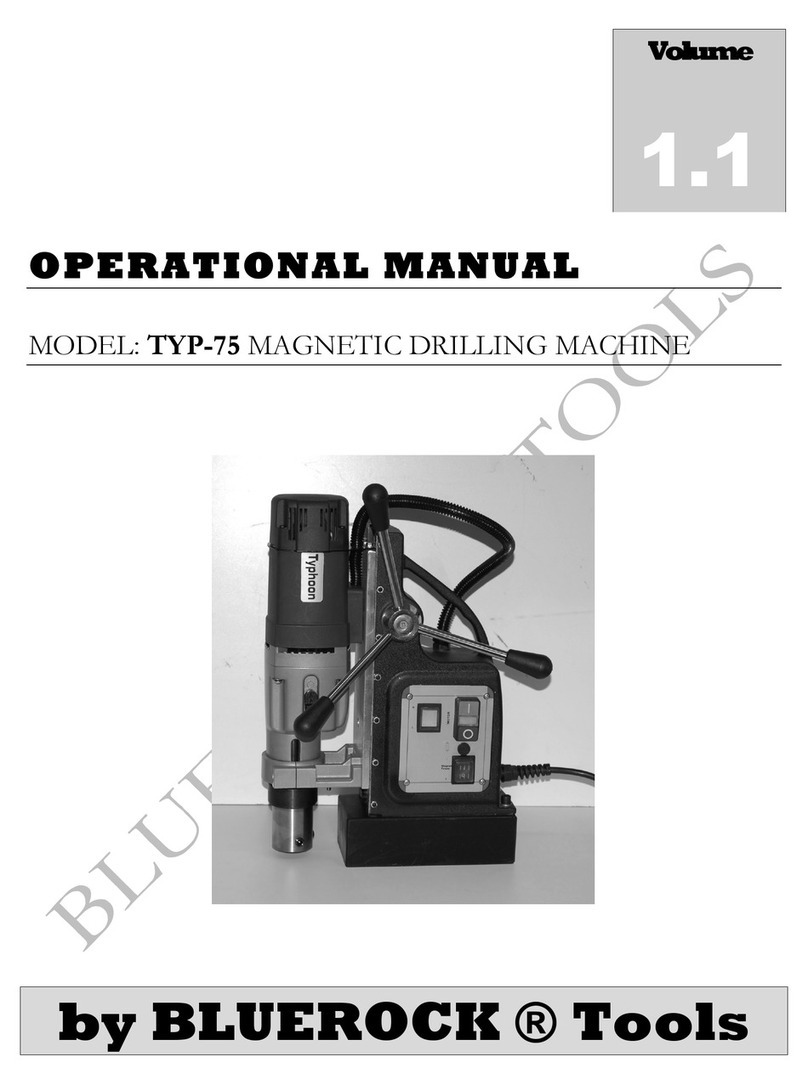
Bluerock Tools
Bluerock Tools TYP-75 Quick start guide

Bluerock Tools
Bluerock Tools Z1 TEL Quick start guide
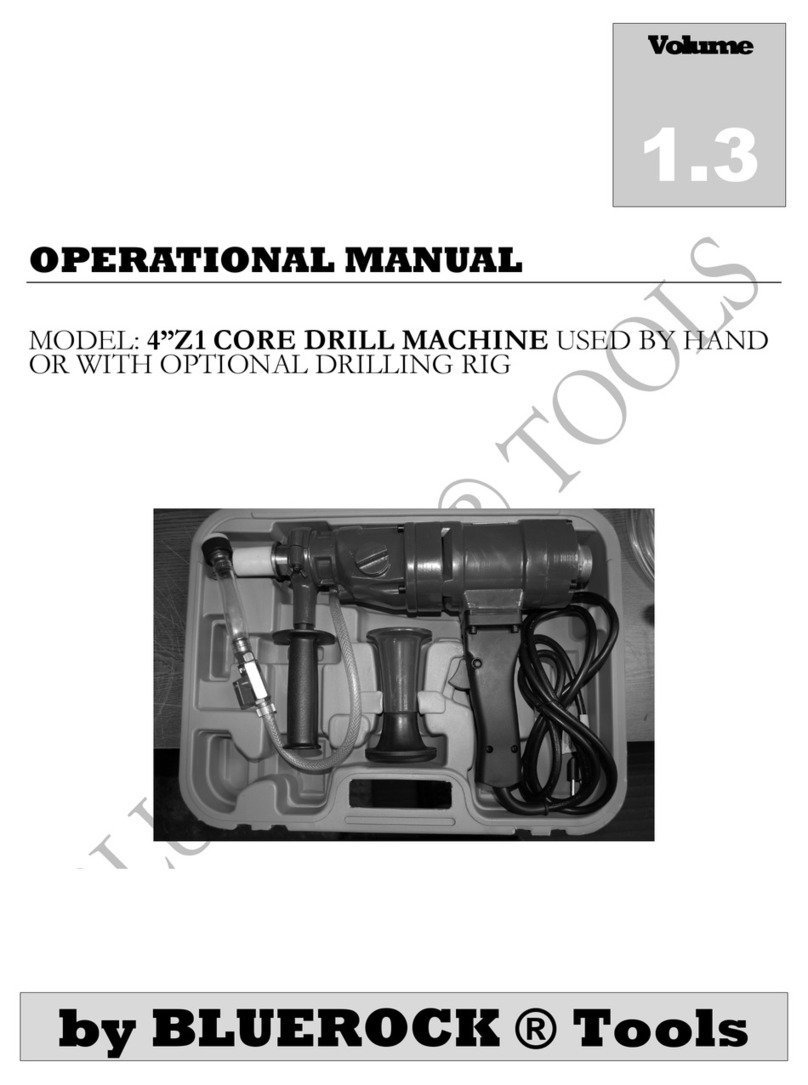
Bluerock Tools
Bluerock Tools 4"Z1 CORE DRILL MACHINE Quick start guide