BOC Edwards TCU 40 Plus User manual

W95900011
Revision F
June, 2004
Instruction Manual
BOC EDWARDS
301 Ballardvale Street Wilmin ton, MA 01887
Telephone: (978) 658-5410 Telex: 710-347-7672 Fax: (978) 658-7969
TCU 40/80
plus
Single Channel
Temperature Control Unit


TCU 40/80 plus Temperature Control Unit i
TABLE OF CONTENTS
SECTION TITLE PAGE
1 PREFACE ………………………………………………………………………………………….. 1
1.1 SAFETY CONSIDERATIONS …………………………………………………………………. 1
2 TCU 40/80
plus
…………………………………………………………………………………….. 3
2.1 SCOPE OF THE MANUAL …………………………………………………………………….. 3
2.2 DESCRIPTION FOR THE TCU 40/80
plus
…………………………………………….………. 3
2.3 LOCKOUT PROCEDURE ……………………………………………………………………… 3
2.4 SAFETY FEATURES ……………………………………………………………………………4
3 QUICK START PROCEDURE ……………………………………………………………………. 5
3.1 POWER UP ………………………………………………………………………………….….. 5
3.2 SETPOINT ERIFICATION …………………………………………………………………… 5
4 PRODUCT DESCRIPTION ……………………………………………………………….………. 6
4.1 REFRIGERATION AND COOLANT CIRCUITS …………………………………………….. 6
4.2 REFRIGERATION ……………………………………………………………………………… 9
4.2.1 IF COOLING IS REQUIRED ………………………………………………………………. 9
4.2.2 IF COOLING IS NOT REQUIRED ………………………………………………………….9
4.3 COOLANT CIRCUIT …………………………………………………………………………… 10
4.4 TEMPERATURE MONITORING ……………………………………………………………… 10
4.5 FRONT PANEL …………………………………………………………………………………. 10
4.6 REAR PANEL ……………………………………………………………………………………12
4.7 SPECIFICATIONS ……………………………………………………………………………… 13
4.8 DIMENSIONS …………………………………………………………………………………... 14
5 INSTALLATION ……………………………………………………………………………………15
5.1 RECEI ING AND UNPACKING ……………………………………………………………… 15
5.2 LOCATION ………………………………………………………………………………………15
5.2.1 SECURING THE UNIT ……………………………………………………………………….15
5.2.2 INSTALLING THE SECONDARY CONTAINMENT RECEPTACLE ……………………. 15
5.2.3 FLOOR LE ELERS …………………………………………………………………………. 15
5.3 STACKING ……………………………………………………………………………………… 16
5.3.1 TIE-BOLTS …………………………………………………………………………………...16
5.4 FACILITIES ……………………………………………………………………………………...16
5.4.1 50 Hz Installations………………………………………………………………………………16
5.4.2 WATER AND COOLANT CONNECTIONS ………………………………………………...16
5.4.3 WATER ………………………………………………………………………………………..18
5.4.4 COOLANT …………………………………………………………………………………….18
5.4.5 REMOTE CONNECTIONS ………………………………………………………………….. 18
6 OPERATION ……………………………………………………………………………………….. 19
6.1 PREPARATION ………………………………………………………………………..………...19
6.2 POWERING UP THE TCU 40/80 plus …………………………………………………………. 19
6.3 CHANGING THE SETPOINT ALUE (S 1) ………………………………………………….20
6.4 TEMPERATURE CONTROLLER PID SETTINGS …………………………………..……….. 20
6.5 REMOTE SET POINT ………………………………………………………………………….. 20
6.6 FLOW RATE ADJUSTMENT ………………………………………………………………….. 21

ii TCU 40/80 plus Temperature Control Unit
7 MAINTENANCE ……………………………………………………………………………………22
7.1 HAZARD WARNINGS ………………………………………………………………………….22
7.2 HAZARDS ………………………………………………………………………………………. 24
7.3 FILLING THE RESER OIR …………………………………………………………..……….. 24
7.4 DRAINING/BLEEDING THE COOLANT RESER OIR ……………………………………... 25
7.5 TEMPERATURE PROBE CALIBRATION ……………………………………………………. 25
7.6 PRE ENTI E MAINTENANCE SCHEDULE ……………………………………………….. 25
7.7 SEMI-ANNUAL PRE ENTATI E MAINTENANCE ………………………………………... 26
7.7.1 REQUIRED EQUIPMENT …………………………………………………………………... 26
7.7.2 PREPARATION ……………………………………………………………………………... 26
7.7.3 ERIFY SYSTEM STATUS ………………………………………………………………… 26
7.7.4 REFRIGERATION LEAK CHECK …………………………………………………………. 26
7.7.5 FLUORINATE LEAK CHECK ……………………………………………………………… 26
7.7.6 WATER LEAK CHECK …………………………………………………………………….. 26
7.7.7 INSULATION REPAIR ……………………………………………………………………... 27
7.7.8 LAMP CHECK/REPLACEMENT …………………………………………………………... 27
7.8 ANNUAL PRE ENTATI E MAINTENANCE ………………………………………………..28
7.8.1 REQUIRED EQUIPMENT …………………………………………………………………... 28
7.8.2 REQUIRED SUPPLIES ……………………………………………………………………… 28
7.8.3 SOLENOID AL E COIL REPLACEMENT ……………………………………………… 28
7.8.4 SYSTEM CHECK ……………………………………………………………………………. 30
7.9 PRE ENTATI E MAINTENANCE CHECKLIST …………………………………………….39
8 TROUBLESHOOTING …………………………………………………………………………….. 40
9 ACCESSORIES AND SPARE PARTS ……………………………………………………………..54
10 OPTIONS …………………………………………………………………………………………… 55
10.1 LON WORKS …………………………………………………………………………………… 55
10.1.1 REFERENCE ………………………………………………………………………………… 55
10.1.2 O ERALL DESCRIPTION …………………………………………………………………. 55
10.1.3 REQUIREMENTS …………………………………………………………………………… 56
10.1.4 INTERFACES ………………………………………………………………………………... 59
10.2 RS232 TEL ………………………………………………………………………………………. 71
10.2.1 BLOCK DIAGRAM …………………………………………………………………………. 71
10.2.2 OPERATION MODE AND CONTENTS OF FUNCTION …………………………………. 71
10.2.3 DESCRIPTION OF EXTERNAL CONTROL AND MONITORING SIGNALS …………... 73
10.3 RS485 SERIAL COMMUNICATION ………………………………………………………….. 92
10.3.1 MODIFIED ELECTRICAL CONTROLS DRAWER …………………………………………...92
10.3.2 RS485 MODICON MODBUS PROTOCOL ………………………………………………… 92
10.3.3 INSTALLATION AND SE-UP OF RS485 INTERFACE BOX ASSEMBLY ……………... 93
10.3.4 RS485 MODICON MODBUS PROTOCOL SPECIFICATION FOR TCU 40/80 ………….. 102
10.3.5 RS485 4X MEMORY MAP FOR TCU 40/80 HEAT EXCHANGER ………………………. 103
10.3.6 RS485 TCU 40/80 MESSAGE EXAMPLE ………………………………………………….. 104
APPENDIX ……………………………………………………………………………………………………105
RETURN OF BOC EDWARDS EQUIPMENT – PROCEDURE (FORM HS1) ………….…………….. 106
RETURN OF BOC EDWARDS EQUIPMENT – DECLARATION (FORM HS2) ……………………...107
LEGAL NOTICES, LIMITATIONS AND DISCLAIMERS …………………………………………….. 108
MSDS (MATERIAL SAFETY DATA SHEET) – “SU A” HP62 ……………………………………….109

TCU 40/80 plus Temperature Control Unit iii
ILLUSTRATIONS
FIGURE TITLE PAGE
FIGURE 1 – REFRIGERATION AND COOLANT COMPONENTS …………………………………… 6
FIGURE 2 – REFRIGERATION AND COOLANT COMPONENTS …………………………………… 7
FIGURE 3 – REFRIGERATION AND COOLANT CIRCUITS …………………………………………. 9
FIGURE 4 – FRONT PANEL ……………………………………………………………………………… 10
FIGURE 5 – ELECTRICAL REAR PANEL ……………………………………………………………… 12
FIGURE 6 – TCU DIMENSIONS …………………………………………………………………………. 14
FIGURE 7 – TCU DIMENSIONS …………………………………………………………………………. 14
FIGURE 8 – STACKED TCU 40/80
plus
SYSTEMS ……………………………………………………… 16
FIGURE 9 – SYSTEM REAR IEW ……………………………………………………………………… 17
FIGURE 10 – WATER CONNECTIONS …………………………………………………………………. 18
FIGURE 11 – TEMPERATURE CONTROLLER ………………………………………………………… 20
FIGURE 12 – LAMP REPLACEMENT …………………………………………………………………… 27
FIGURE 13 – SOLENOID COIL REPLACEMENT ……………………………………………………… 29
FIGURE 14 – ELECTRICAL DRAWER ANALOG………………………………………………………. 49
FIGURE 15 – ELECTRICAL DRAWER SCHEMATIC …………………………………………………. 51
FIGURE 16 – REMOTE INTERFACE ……………………………………………………………………. 53
FIGURE 17 – O ERALL LTCI ARCHITECTURE ……………………………………………………… 55
FIGURE 18 – LTCI PHYSICAL LAYOUT ………………………………………………………………. 56
FIGURE 19 – ELECTRICAL REAR PANEL …………………………………………………………….. 65
FIGURE 20 – ELECTRICAL DRAWER LONWORKS……………………………………………………. 66
FIGURE 21 – ELECTRICAL DRAWER SCHEMATIC …………………………………………………….68
FIGURE 22 – REMOTE INTERFACE ……………………………………………………………………… 70
FIGURE 23 – BLOCK DIAGRAM ………………………………………………………………………….. 71
FIGURE 24 – “RUN”/”STOP” SIGNAL ……………………………………………………………………..73
FIGURE 25 – CONTROL SIGNAL STATE …………………………………………………………………74
FIGURE 26 – PIN ASSIGNMENT FOR TCU-TEL CABLE ……………………………………………….. 75
FIGURE 27 – ELECTRICAL REAR PANEL ………………………………………………………………..84
FIGURE 28 – RS232 ELECTRICAL DRAWER ……………………………………………………………. 86
FIGURE 29 – RS232 POWER DISTRIBUTION SCHEMATIC …………………………………………….88
FIGURE 30 – ASSEMBLY CABLE TCU HOST COMMUNICATION …………………………………… 90
FIGURE 31 – ASSEMBLY CABLE TCU RS232 COMMUNICATION ……………………………………91
FIGURE 32 – RS485 ELECTRICAL DRAWER COMPONENT LAYOUT ………………………………..94
FIGURE 33 – RS485 ELECTRICAL DRAWER SCHEMATIC ……………………………………………. 96
FIGURE 34 – RS485 INTERFACE BOX – PHYSICAL DIMENSIONS …………………………………... 98
FIGURE 35 – RS485 INTERFACE BOX WITH TOP CO ER REMO ED ………………………………. 99
FIGURE 36 – MICROPROCESSOR PCA – JP7 PIN DESCRIPTION AND FUNCTION …………………99

iv TCU 40/80 plus Temperature Control Unit
ILLUSTRATIONS (continued) ….
FIGURE TITLE PAGE
TABLE 1 – SAFETY FEATURES ………………………………………………………………………….. 4
TABLE 2 – FRONT PANEL INDICATORS ……………………………………………………………… 5
TABLE 3 – REFRIGERATION AND COOLANT COMPONENTS ………………………………………..8
TABLE 4 – FRONT PANEL CONTROLS ………………………………………………………………….. 11
TABLE 5 – FRONT PANEL LED INDICATORS ………………………………………………………….. 11
TABLE 6 – TEMPERATURE CONTROLLER …………………………………………………………… 11
TABLE 7 – DESCRIPTION OF REAR PANEL COMPONENTS AND INDICATORS ………………… 12
TABLE 8 – FRONT PANEL POWER UP INDICATOR CONDITIONS ………………………………… 19
TABLE 9 – ELECTRICAL HAZARDS CLASSIFICATIONS …………………………………………… 24
TABLE 10 – PRE ENTI E MAINTENANCE SCHEDULE ……………………………………………….25
TABLE 11 – FAULTS IDENTIFIED BY FRONT PANEL LAMPS ……………………………………….. 40
TABLE 12 – FAULTS INDICATED BY THE FRONT PANEL LED INDICATORS …………………….. 42
TABLE 13 – FAULTS IDENTIFIED BY REAR PANEL INDICATORS …………………………………..46
TABLE 14 – MISCELLANEOUS FAULT CONDITIONS ………………………………………………….47
TABLE 15 – ACCESSORIES ………………………………………………………………………………...54
TABLE 16 – ANALOG TEMPERTURE SIGNAL CHARACTERISTICS ………………………………... 58
TABLE 17 – LTCI NETWORK ARIABLES ……………………………………………………………… 61
TABLE 18 – DEFINITIONS OF N OSTATUS NETWORK ARIABLE ……………………….……….. 62
TABLE 19 – DESCRIPTION OF REAR PANEL COMPONENTS AND INDICATORS ………………….65
TABLE 20 – A AILABLE FUNCTIONS …………………………………………………………………... 72
TABLE 21 – PIN ASSIGNMENTS AT THE TCU HOST CONNECTION ……………………….……….. 75
TABLE 22 – CONTROL CODE ……………………………………………………………………………...76
TABLE 23 – HEADER CODE ………………………………………………………………………………. 76
TABLE 24 – DESCRIPTION OF REAR PANEL COMPONENTS AND INDICATORS ………………….85
TABLE 25 – TCU 40/80 “J72J1” CONNECTOR MODIFIED FOR RS485 ……………………….………..100
TABLE 26 – HOST RS485 COMMUNICATION CONNECTOR …………………………………………..101

TCU 40/80 Temperature Control Unit 1
1. Preface
1.1 Safety Considerations
Many safety features have been designed into the TCU 40/80 plus to protect the operator and the
equipment. The following symbols are used in this manual to indicate the various safety
conditions.
General Alert
General Alert symbol denotes the potential of
personal hazards or equipment failure.
Warnings are given when failure to observe the
instruction could result in injury or death to
persons.
Cautions are given where failure to observe the
instruction could result in damage to the
equipment, associated equipment and process.
Statement on avoiding the hazard.
Electric Shock
Electric Shock symbol denotes the presence of
high voltage or current. It calls attention to the
procedure, practice, or the like, which if not done
correctly or adhered to could result in injury or
death.
Statement on avoiding the hazard.
Eye Protection
Eye Protection symbol denotes a hazard which
could cause injury or irritation to the eyes.
Statement on avoiding the hazard.
Toxic Gases
Toxic Gases symbol denotes a personal hazard.
It calls attention to the procedure, practice, or the
like, which if not done correctly or adhered to
could result in injury or death.
Statement on avoiding the hazard.

2 TCU 40/80 plus Temperature Control Unit
Hot Surfaces
Hot Surfaces symbol denotes a hazard which
could cause injury or burns.
Statement on avoiding the hazard.
Hand
Protection
Hand Protection symbol denotes a hazard which
could cause injury or burns
Statement on avoiding the hazard.
High Pressure
High Pressure symbol denotes a personal hazard
or equipment failure. It calls attention to the
procedure, practice, or the like, which if not done
correctly or adhered to could result in equipment
damage, injury or death.
Statement on avoiding the hazard.
Extreme
Temperatur
e
Extreme Temperature symbol denotes a hazard
which could cause injury or burns.
Statement on avoiding the hazard.

TCU 40/80 Temperature Control Unit 3
2. TCU 40/80 plus
2.1 Scope of the Manual
This manual provides information on the installation, start-up and operation of Edwards High Vacuum
Model 40/80 Temperature Control Unit (TCU 40/80 plus).
The Quick Start Procedure on page 5 is a step by step guide for the start up and use of an installed,
working system.
Installation, starting on page 17, provides instructions and information for installing the system. The
installer must have sufficient technical understanding of electrical and mechanical systems to properly use
this information.
Operation, starting on page 21, provides more complete instructions on the preparation and use of the
system.
2.2 Description of the TCU 40/80 plus
The TCU 40/80 plus is a single-channel temperature control unit engineered for temperature control of
remote heat loads.
From distances up to 50 feet, the TCU 40/80 plus can cool the heat load generated by the process
equipment. The coolant circulates through the TCU 40/80 plus, where it is cooled or heated as required,
then is transferred to the process equipment, and returns in a closed loop. The TCU 40/80 plus maintains
supply coolant at a temperature between -40 °C and +80 °C, selectable in 0.1 °C increments, with a
tolerance of ±1.0 °C.
2.3 Lockout Procedure
To prevent accidental or unauthorized starting of the TCU 40/80 plus during maintenance, disconnect the
power cord from the receptacle and install an appropriate lock-out device (Hubbell Small PlugoutÔor
equivalent) on the end of the power cord.

4 TCU 40/80 plus Temperature Control Unit
2.4 Safety Features
The safety features listed in Table are designed into the TCU 40/80 plus.
Table 1 - Safety Features
Component
Ref. Des. *
Function
EMERGENCY OFF
button (EMO)
(PB1)
Shuts off power to major system components.
Remote EMERGENCY
OFF
(J72J2) Remote shut off of power to major system components.
Drawer safety switch (LS1) Upon opening the drawer, shuts off power to major system
components.
Pressure switch (PS1) Protects the refrigeration system against high discharge
pressure. Interrupts operation at 300 psig.
Condenser pressure relief
valve
(W2) Vents refrigerant to the atmosphere above 350 psig. Fail
safe for PS1, works even if there is no power applied to the
system.
Reservoir pressure relief
valve
(W1) Protects the reservoir from over-pressure.
Temperature switch (TS1) Protects the process fluid from exceeding 99 °C
Coolant flow switch (FS1) Protects the process equipment from inadequate coolant
flow rates.
Coolant float switch (LLS1) Protects against low level in the coolant reservoir by
stopping the equipment.
Coolant float switch (LLS3) Protects against overfill of the coolant reservoir. Indication
on front and rear panels.
Thermal overload (K3) Protects the pump motor from excess current.
Surge suppression VR1-4 Protects the TCU 40/80 plus against voltage surges and
power line transients.
Line phase monitor PMR1 Protects the equipment against incorrect wiring of the
supply phases and low voltage burn-out.
Current sensor CSR1 Protects the compressor against abnormal conditions.
Secondary containment Captures fluids (internal to the TCU) in the event of a leak.
* See Figure 3 on page 10

TCU 40/80 Temperature Control Unit 5
3. Quick Start Procedure
This Quick Start procedure is for easy start
up and operation of an installed and fully
working TCU 40/80 plus. If your TCU 40/80
plus is not installed, go to Installation,
Section 5 on page 17. Detailed operating
instructions are in Operation, Section 6 on
page 21. If at any time an alarm occurs,
press STOP and correct the fault indicated
by the display as directed in the
Troubleshooting Guide, Section 8 on page
43. Press RESET and START to continue
operation.
3.1 Power Up
Before applying power, verify that
all water and coolant lines are
connected to the system. The
handles on both coolant line valves
should be in the open position. For
the location of these connections,
refer to Figure 9 on page 19.
To power up the TCU 40/80 plus:
1. READY light should be on. If
the ready light is not on see
Powering Up the TCU 40/80
plus on page 21.
2. Press RESET. Verify that
front panel indicators are as
shown in the Reset column of
Table 2 on this page.
3. Press START. Verify that
front panel indicators are as
shown in the Start Condition
column of Table on this
page.
If in steps two or three any front
panel indicators do not match, refer
to the Troubleshooting Guide
Section 8 on page 43 for corrective
action.
4. Verify that the coolant
pressure gauge (located on the
front access panel) reads less
than 100 psig.
Table 2 - Front Panel Indicators
Indicator Reset
Condition
Start
Condition
Power On Green Green
Reset White White
Facility Power Off Green
Facility Water Green Green
Circuit Breakers Green Green
Compressor Off Green
Temperature Green Green
Flow Off Green
Normal Level Green Green
Low Level Off Off
Remote RTD
(Optional)
Green
(if used)
Green
(if used)
3.2 Setpoint Verification
Verify that the manual mode
setpoint value (SV1) displayed on
the temperature control is the value
desired. To change the Setpoint
value see Changing the Setpoint
Value (SV1) Section 6.3 on page
22.
Do not to exceed the normal
operating parameters. The system
is designed to operate from -40 °C
to +80 °C.

TCU 40/80 Temperature Control Unit 6

6 TCU 40/80 plus Temperature Control Unit
4. Product Description
4.1 Refrigeration and Coolant Circuits
Figure 1, Figure 2, and Table 3 on page 80 describe the refrigeration and coolant components of the TCU
40/80 plus
Figure 1- Refrigeration and Coolant Components
(G:\Technical Documents\MANUALS\W95900011- All)

TCU 40/80 Temperature Control Unit 7
Figure 2 - Refrigeration and Coolant Components
(G:\Technical Documents\MANUALS\W95900011- All)

8 TCU 40/80 plus Temperature Control Unit
Table 3 - Refrigeration and Coolant Components
Item Component Name Function
1 Reservoir A holding tank for the Fluorinert coolant
2 Level Switch Monitors the coolant level in the reservoir
3 Compressor Compresses the refrigerant fluid
4 Crankcase Regulator Protects the compressor against pressure overload
5 Suction Service Valve Allows isolation at the compressor
6 Discharge Service Valve Allows isolation at the compressor
7 Temperature Switch High limit switch for reservoir heater
8 Pressure Switch Limits maximum allowable discharge pressure
9 Condenser Transfers heat from the compressed refrigerant to the facility water
10 Filter Dryer Removes contaminants and moisture from the refrigerant
11 Safety Cooling Valve Limits the discharge temperature
12 Motor Drives the coolant pump
13 Pump Circulates the Fluorinert coolant
14 Bypass Valve Regulates coolant flow
15 Hot Gas Bypass Valve Regulates cooling capacity
16 Subcooler Further cools the refrigerant that is returning to the compressor
17 Solenoid Valve SV2 Allows refrigerant to pass through the hot gas bypass valve, then to
the compressor suction line when energized
18 Solenoid Valve SV1 Allows refrigerant to pass to the TEV when energized
19 Sight Glass Allows visual inspection of the refrigerant charge and presence of
moisture in the system
20 TEV
(Thermostatic
Expansion Valve)
Allows the refrigerant to expand from a liquid to a gas
21 Heater Raises the temperature of the coolant when the process requires
heating
22 Flow Switch Monitors the flow rate
23 Heat Exchanger Extracts heat from the coolant and transfers it to the refrigerant
24 Pressure Relief Valve Discharges refrigerant from the system to the atmosphere in the event
of severe over-pressure condition

TCU 40/80 Temperature Control Unit 9
Bypass valve
Fill port Pressure
relief
valve
Level switch
Flow
switch
Circulation
pump
Temperature
switch
Drain valve
Heater
TS1
Coolant supply
RTD
temperature
probe
Plate
heat
e changer
Subcooler
Crankcase
pressure
regulator Compressor TEV
bulb
Pressure
switch
Bypass
valve
Hot gas
solenoid valve
SV2
Pressure
relief
valve
Filter
dryer
Safety
cooling
TEV
Water in
Water out
Condenser
PS1
Main cooling
solenoid valve
SV1
Thermal
e pansion
valve
Vent
valve
Coolant
return
FS1
TEV
bulb
Service
valve
Service
valve
Figure 3 - Refrigeration and Coolant Circuits
(G:\Technical Documents\MANUALS\W95900011- All)
4 2 Refrigeration - (See figure 3 above)
1 Refrigerant gas enters the compressor at low temperature and pressure It leaves the compressor at high
pressure and temperature
2 The gas passes into the condenser, where heat is removed by the external water supply, causing the gas
to condense into a liquid
3 The cool liquid refrigerant exits the condenser and passes through a filter dryer that removes any
residual moisture or contaminants
4.2.1 If Cooling Is Required:
1 Solenoid valve SV1 opens (coil energized), allowing the refrigerant to flow into the Thermostatic
Expansion Valve (TEV) The pressure drop across the TEV causes the refrigerant to change from
a liquid to a mixture of liquid and gas
2 The liquid and gas mixture enters the heat exchanger where it becomes entirely a gas The
process of expansion from a liquid to a gas reduces the temperature by absorbing energy
3 The refrigerant leaving the heat exchanger returns to the compressor through the sub-cooler and a
crankcase pressure regulator The sub-cooler further cools the refrigerant entering the TEV
4.2.2 If Cooling Is Not Required:
1 Solenoid valve SV1 closes (coil de-energized)
2 Hot refrigerant from the compressor is passed through SV2 (coil energized) and a hot gas bypass
valve before returning to the compressor suction line This bypassing allows the compressor to run
continuously
3 Cooling, required to prevent the compressor from overheating, is provided by allowing some of
the liquid from the condenser to pass through the safety cooling automatic expansion valve into
the suction line, thus maintaining the discharge gas temperature below 99 °C

10 TCU 40/80 plus Temperature Control Unit
4. Coolant Circuit
Coolant is pulled from the reservoir by the circulation pump and transferred to the heat exchanger where it
is cooled by the refrigeration system as required It then flows to the process equipment by means of the
coolant supply hose The coolant returns to the TCU 40/80 plus reservoir by means of the coolant return
hose The coolant system requires 8 liters of coolant for the reservoir plus the volume of the circulation
lines and any other spaces filled with coolant that are attached to the TCU 40/80 plus To increase the
coolant temperature, the reservoir uses an electrical resistance heater that is controlled by the temperature
controller The heater must be fully submerged at all times, and if the coolant in the reservoir falls below
3 5 liters, a level switch causes the status alarm signal to automatically shut down the TCU 40/80 plus
A three-float level switch, a thermostat, and a flow sensor provide coolant status signals to the TCU 40/80
plus control system
4.4 Temperature Monitoring
A Resistance Temperature Device (RTD) monitors the temperature of the coolant leaving the TCU 40/80
plus and transmits this information to the temperature controller The TCU 40/80 plus compares the output
of the RTD to the selected process temperature (SV1) and determines if the coolant needs to be cooled or
heated The temperature controller then operates the main cooling solenoid valve or heater The coolant
temperature at the supply port on the rear panel is measured by a local, internally connected RTD If
sensing of process equipment temperature is needed, connect an RTD to J72J3 at the rear panel (See Figure
5 on page 13) For remote connection schematic details, see Figure 16 on page 56
4.5 Front Panel
Figure 4 shows the Front Panel Table 4, Table 5 and Table 6 identify its controls and indicators
Figure 4 - Front Panel
(G:\Technical Documents\MANUALS\W95900011- All)

TCU 40/80 Temperature Control Unit 11
Table 4 - Front Panel Controls
Control Name Description
Power On Lights green when power is being supplied to the TCU 40/80 plus
Reset Resets alarms and makes the TCU 40/80 plus ready to operate The white light
indicates that the TCU 40/80 plus is ready to operate
Emergency Off Removes power from all TCU 40/80 plus circuits except the EMERGENCY
OFF circuit To shut off power, push EMERGENCY OFF (EMO) To reset,
rotate the EMERGENCY OFF button clockwise as shown on the switch
Start/Stop Starts and stops the operation of the TCU 40/80 plus
Alarm Emits a high pitched sound when there is a fault condition which has caused the
TCU 40/80 plus to stop operation
Mute Silences the audible alarm
Table 5 - Front Panel LED Indicators
LED Name Condition Description
Facility Power Green
Red
Power phases are normal
Power phases are reversed or low line voltage
Facility Water
Green
Red
Water pressure and flow are normal
Water pressure or flow are not adequate (See Specifications
Section 4 7 on page 14
Circuit Breakers
Green
Red
Rear panel circuit breakers 2, 3, and 4 are on
One or more of these breakers is tripped or off
Compressor Green
Red
Compressor is operating normally
Compressor has stopped operating
Coolant Temperature Green
Red
Coolant reservoir temperature is normal
Coolant temperature is above the operating range
Coolant Flow
Green
Red
Coolant flow is normal
Coolant flow is not adequate
Coolant Normal Level Green
Amber
Coolant level is normal
Coolant level is over filled
Coolant Low Level Off
Amber
Red
Coolant level is normal
Coolant level is low
Coolant level is very low
Remote RTD
Off
Green
Remote RTD not connected
Remote RTD temperature probe is in use
Table 6 - Temperature Controller
Controls and
Indicators
Description
Process Value (PV) The present temperature of the coolant, as indicated by the internal RTD or the
remote RTD
Setpoint Value (SP) The TCU 40/80 plus regulates to this temperature, as set by the operator
Pushbuttons Used to program the controller
Remote Mode Led
(AUX)
Indicates mode of operation:
Off indicates local operation
On indicates remote operation

12 TCU 40/80 plus Temperature Control Unit
4.6 Rear Panel **
Figure 5 shows the rear panel Table 7 identifies the controls and indicators on the rear panel
Figure 5 - Electrical Rear Panel
(G:\Technical Documents\MANUALS\W95900011- All)
Table 7 - Description of Rear Panel Components and Indicators
Label Description
J72J3 Five-pin connector for remote RTD interface See Figure 16 on page 56 for
pinouts
CB7 24 VAC 1-pole, 2 Amp circuit breaker Isolates the 24 VAC transformer Normally on
(in)
CB8 24 VDC 1-pole, 2 Amp circuit breaker Isolates the 24 VDC power supply output
Normally on (in)
J72J2 Nine pin connector for remote EMERGENCY OFF, start-stop operation, and
remote setpoint operation enable See Figure 16 on page 56 for pinouts
CB4 Reservoir Heater 3-pole, 10 Amp circuit breaker Normally on (up)
CB3 Circulation Pump 3-pole, 6 Amp circuit breaker Normally on (up)
CB2 Compressor 3-pole, 16 Amp circuit breaker Normally on (up)
CB1 Main Power 3-pole, 25 Amp circuit breaker Normally on (up)
Normal/Overfill Normal, LED Green
Overfilled, LED Amber
Low/Fault Low, LED Amber
Fault, LED Red
200/208 VAC 3 PH
50/60 Hz 30A Mains input power connector
CB5-XFMR 2-pole, 0 5 Amp circuit breaker Isolates the equipment transformer
CB6-PSU 2-pole, 0 3 Amp circuit breaker Isolates the power supply
J72J1 37 pin D-subminiature connector, for setpoint value signal, process value
signal, and remote fail and warning signals
See Figure 16 on page 56 for pinouts
** Note: If LONWORKS/RS-485/RS-2 2 option is chosen, see specific chapter for modified rear panel
details.

TCU 40/80 Temperature Control Unit 13
4.7 Specifications
Parameter Conditions Specification
Temperature Ramp Coolant Short Circuit Conditions
+25 °C to +80 °C Elapsed Time: <25 Minutes
+25 °C to -30 °C Elapsed Time: <15 Minutes
Cooling capacity @ process
equipment
150 watt coolant line losses;
coolant water @ 15 °C
Process Coolant @ -40 °C 750 Watts
Process Coolant @-20 °C to +80
°C
2400 Watts
Heating Element 2800 Watts
System Flow @20 °C, 60 psig 3 gpm (11 36 l pm)
Process Temperature Range -40 °C to +80 °C
Setpoint Resolution ± 0 1 °C
Temperature Regulation ± 1 0 °C Typical
Facility Water Requirements +10 °C (-0° +2°) to
+26 °C (+0° -2°)
3 to 6 gpm
(11 36 to 22 71 l pm)
Power Requirements 3-Phase Delta (Balanced Load),
4 Wire (3 Phases & Earth Gnd),
200 To 208 VAC, 50/60 Hz
30 Amp Outlet
Ambient Operating Temperature +10 °C to +40 °C
Weight
416 lbs (190kg) Dry Weight
460 lbs (210 kg) Wet Weight
832 lbs (308 kg) Dry Weight
Dual Stacked
920 lbs (420 kg) Wet Weight
Dual Stacked
Dimensions 22" wide x 30" deep x 35" high
(56 cm x 76 cm x 89 cm)
Altitude Up to 2000 Meters
(6562 ft )
Max Relative Humidity Up to 31 °C 80%
Above 31 °C Derate Linearly to 50% @ 40 °C
Transient Over-Voltage IEC 664, Installation Category II 2 5 kV
Pollution Degree IEC 664 2 Π
Sound Pressure Level At a distance of 1meter 65dB(A)
Other manuals for TCU 40 Plus
1
This manual suits for next models
1
Table of contents
Other BOC Edwards Control Unit manuals
Popular Control Unit manuals by other brands

Grundfos
Grundfos COMFORT PM Series manual

Water Worker
Water Worker WWDPC installation manual
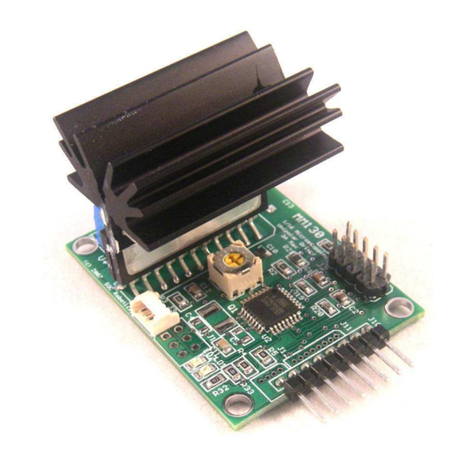
SOC Robotics
SOC Robotics MM130 Technical reference manual

PLASTITALIA
PLASTITALIA I Plast 105 user manual

Schlage
Schlage GF3000 Gravity Force Series installation instructions

Val-Matic
Val-Matic 5906R/8A02X021 O & M Manual
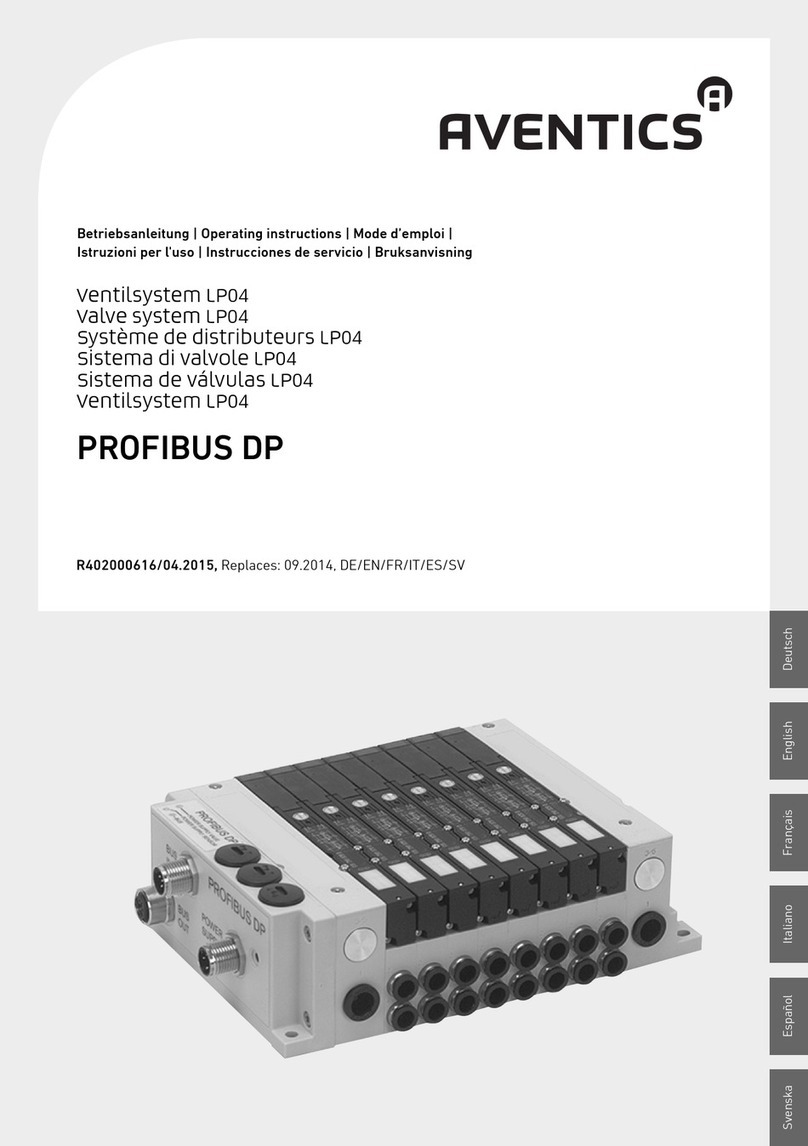
Aventics
Aventics PROFIBUS DP Operating
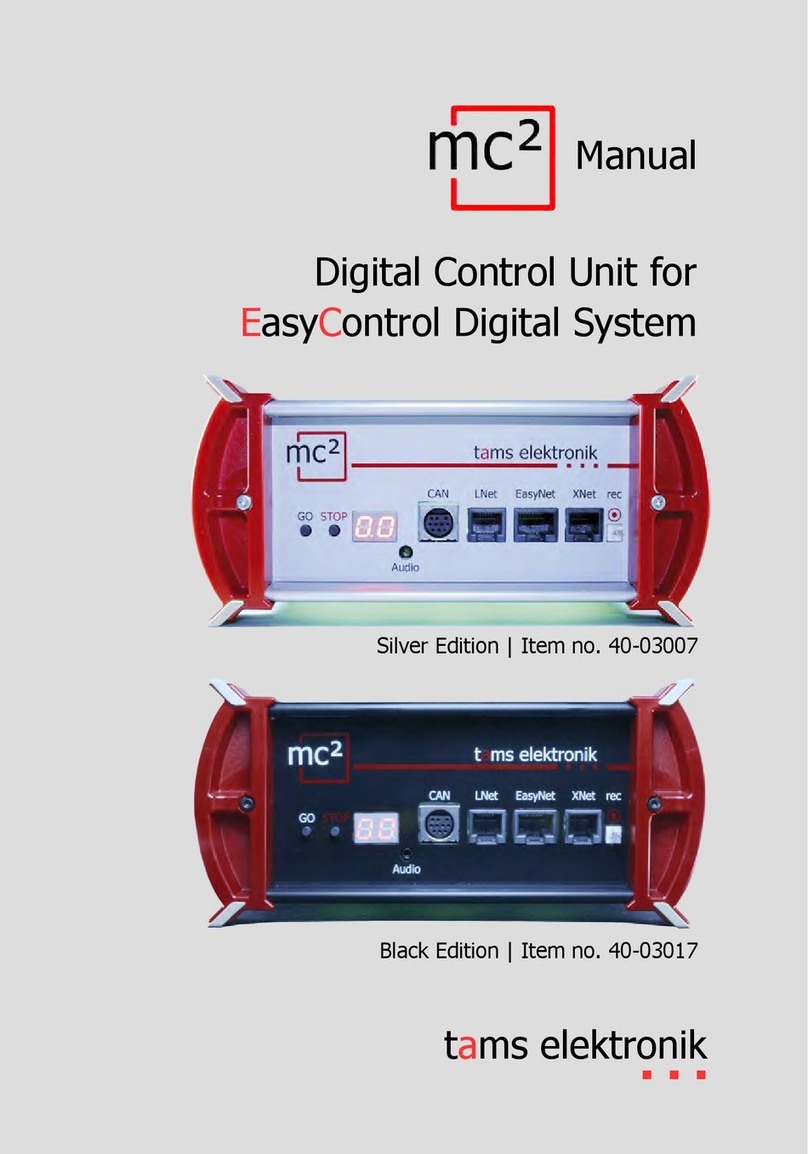
tams elektronik
tams elektronik mc2 EasyControl Digital System Silver... manual
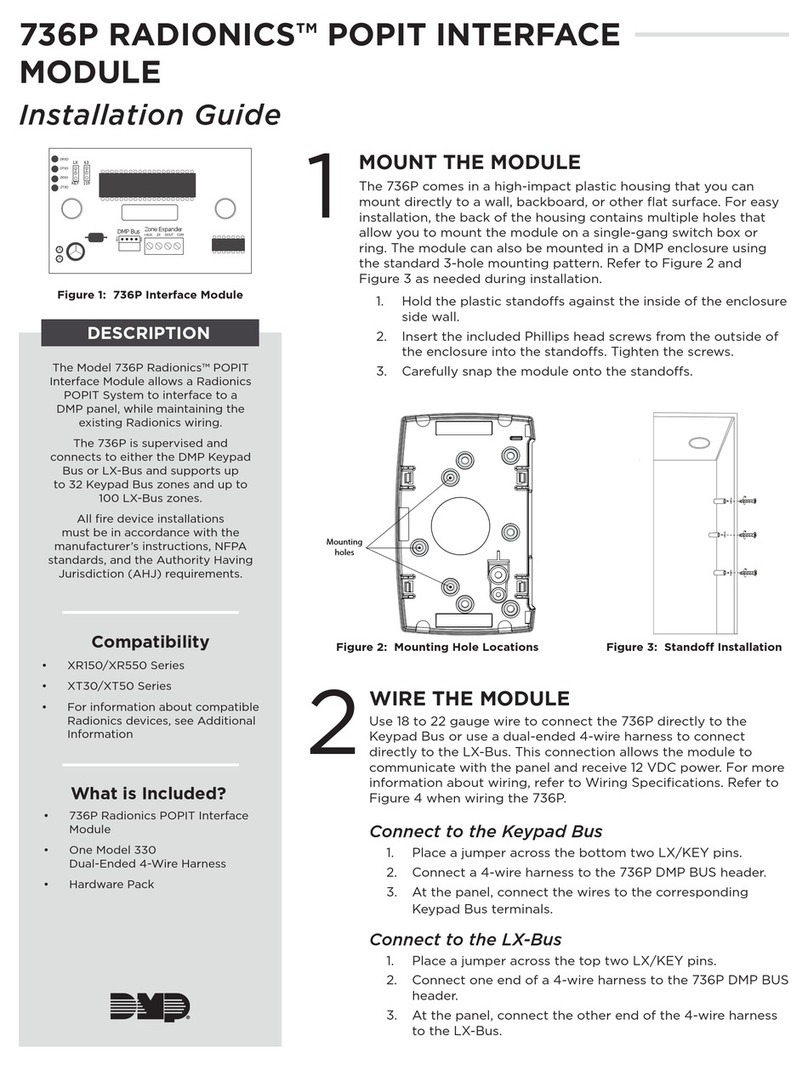
DMP Electronics
DMP Electronics 736P Radionics installation guide

Bosch
Bosch Heatronic 4000 Applications manual
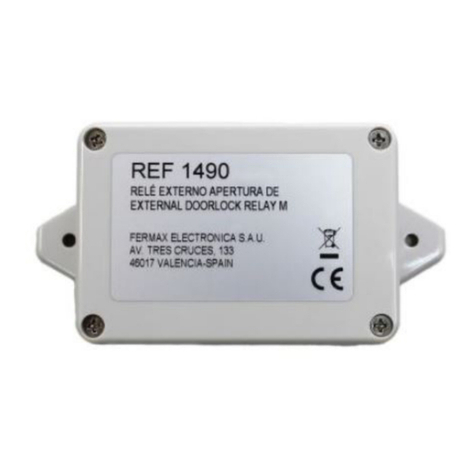
Fermax
Fermax MEET 1490 Installer manual

urmet domus
urmet domus alpha 1168/51 installation manual