BOSSCO 356 User manual

GAS PRESSURE REGULATOR
356
P1 max 500 mbar
DN15 - DN 20 - DN 25 - DN 32 - DN 40 - DN 50
DN 65 - DN 80 - DN 100
EN
EC approval according to EN 88-1, compliant with Regulation (EU) 2016/426
CE-51CL4012/ED01
MADE IN ITALY
II 2G - II 2D

2
EN
INDEX
pag.
English ........................................................................................................................................................ 3
Drawings......................................................................................................................................................10
Dimensions (table 1) .....................................................................................................................................13
Regulation spring data (table 3).......................................................................................................................14
Diagram .......................................................................................................................................................15

3
EN
1.0 GENERAL INFORMATION
This manual shows you how to safely install, operate and use the device.
The instructions for use ALWAYS need to be available in the facility where the device is installed.
ATTENTION: installation/maintenance needs to be carried out by qualified staff (as explained in
section 1.3) by using suitable personal protective equipment (PPE).
For any information pertaining to installation/maintenance or in case of problems that cannot be solved with the instructions,
contact the manufacturer by using the address and phone numbers provided on the last page.
1.1 DESCRIPTION
Device which supplies a preset and constant “downstream” pressure value (P2) (within the intended operating limits) when the
inlet pressure (P1) and/or the flow rate (Q) changes. The compensated obturator ensures precision when adjusting the outlet
pressure (P2) even in the case of high and sudden variations in the inlet pressure.
It is fitted with:
• a spring to adjust the outlet pressure;
• a safety membrane;
• output pressure test nipple (with some exceptions) to control the outlet pressure (P2). On some models the pressure
test nipple is also present on the input;
Reference standards: EN 88-1 – EN 13611.
1.2 KEY OF SYMBOLS
ATTENTION: Attention
is drawn to the technical
details intended for
qualified staff.
DANGER:
In the event of
inobservance, this may cause damage
to tangible goods, to people and/or pets.
DANGER: In the event
of inobservance, this may
cause damage to tangible
goods.
1.3 QUALIFIED STAFF
These are people who:
•Are familiar with product installation, assembly, start-up and maintenance;
•Know the regulations in force in the region or country pertaining to installation and safety;
•Are trained in first aid.
1.4 USING NONORIGINAL SPARE PARTS
•To perform maintenance or change parts (e.g. spring, filter element, etc.) ONLY manufacturer-recommended parts can be
used. Using different parts not only voids the product warranty, it could compromise correct device operation.
•The manufacturer is not liable for malfunctions caused by unauthorised tampering or use of non-original parts.
1.5 IMPROPER USE
•The product must only be used for the purpose it was built for.
•It is not allowed to use fluids other than those expressly stated.
• The technical data set forth on the rating plate must not, under any circumstances, be exceeded. The end user or installer is in
charge of implementing correct systems to protect the device, which prevent the maximum pressure indicated on the rating plate
from being exceeded.
•The manufacturer is not responsible for any damage caused by improper use of the device.

4
EN
2.0 TECHNICAL DATA
• Use : non-aggressive gases of the three families (dry gases)
• Ambient temperature (TS) : -15 ÷ +60 °C
• Maximum operating pressure : 500 mbar
• Class : A (P2 ± 15%)
• Mechanical resistance : Group 2 (according to EN 13611)
• Rp threaded connections in line : (DN 15 - DN 20 - DN 25 - DN 32 - DN 40 - DN 50) according to EN 10226
• Flanged connections that can couple with
PN 16 flanges
:
(DN 65 - DN 80 - DN 100) ISO 7005 / EN 1092-1
• Rc or NPT threaded or ANSI 150 flanged connections
: on request
• In compliance with : Regulation (EU) 2016/426 (Appliances burning gaseous fuels)
ATEX Directive 2014/34/EU
2.1 MODEL IDENTIFICATION
35501216: Rp 1/2 DN 15 P2: 18÷40 mbar
35501238: Rp 3/4 DN 20 P2: 18÷40 mbar
35501260: Rp 1 DN 25 P2: 18÷40 mbar
35501271: Rp 1 1/4 DN 32 P2: 13÷23 mbar
35501282: Rp 1 1/2 DN 40 P2: 13÷23 mbar
35501293: Rp 2 DN 50 P2: 13÷23 mbar
35501301: DN 65 P2: 13÷27 mbar
35501312: DN 80 P2: 13÷27 mbar
35501323: DN 100 P2: 15÷27 mbar
3.0 COMMISSIONING THE DEVICE
3.1 OPERATIONS PRIOR TO INSTALLATION
•It is necessary to close the gas upstream of the device prior to installation;
• Make sure that the line pressure DOES NOT EXCEED the maximum pressure declared on the product label;
•Protective caps (if any) must be removed prior to installation;
•The pipes and inside of the device must be clear of any foreign bodies;
•IMPORTANT: to avoid possible pumping and/or disturbances in the gas flow, a straight pipe section equal to at least 5
DN must be installed (downstream of the regulator).
•IMPORTANT: install manual gas closing devices (e.g. ball valves) upstream and downstream of the regulator to protect
it from any pipe leak test;
If the device is threaded:
•make sure that the pipe thread is not too long, to prevent damaging the body of the device when screwing it on;
If the device is flanged:
• make sure the inlet and outlet counter-flanges are perfectly coaxial and parallel in order to prevent unnecessary
mechanical stress to the body. Also calculate the space to insert the seal gasket;
• With regard to tightening operations, equip yourself with one or two calibrated torque wrenches or other controlled locking
tools;
•The safety regulations on handling loads in force in the country of installation must be complied with. If the device to
be installed exceeds the weight allowed, suitable mechanical equipment and adequate slings must be used. Necessary
precautions must be taken during the handling phases so as not to damage/ruin the external surface of the device.
•If the regulator is not fitted with a filter, it is advisable to install an adequate filter upstream;
•With outdoor installation, it is advisable to install a protective roof to prevent rain from oxidising or damaging parts of the
device.
•According to the plant geometry, check the risk of an explosive mixture arising inside the piping;
•If the regulator is installed near other devices or as part of an assembly, compatibility between the regulator and
these devices must be evaluated beforehand;
• Provide a protection against impacts or accidental contacts if the device is accessible to unqualified personnel.

5
EN
3.2 INSTALLATION (see example in 3.4)
Threaded devices:
•Assemble the device by screwing it, with the due seals, onto the plant with pipes and/or fittings whose threads are consistent
with the connection being attached.
•Do not use the neck of the top cover (4) as a lever to help you screw it on, only use the specific tool;
•The arrow, shown on the body (11 ) of the device, needs to be pointing towards the application;
Flanged devices:
•Assemble the device by flanging it, with the due seals, onto the plant with pipes whose flanges are consistent with the
connection being attached. The gaskets must be free from defects and must be centred between the flanges;
• If, after installing the gaskets, there is still an excessive space in between, do not try to reduce the said gap by excessively
tightening the bolts of the device;
•The arrow, shown on the body (11 ) of the device, needs to be pointing towards the application;
•Insert the relative washers inside the bolts in order to prevent damage to the flanges during tightening;
•When tightening, be careful not to “pinch” or damage the gasket;
•Tighten the nuts or bolts gradually, in a “cross” pattern (see the example below);
•Tighten them, first by 30%, then by 60% and finally 100% of the maximum torque (see the table below according to
EN
13611);
Diameter DN 65 DN 80 DN 100
Max. torque (N.m) 50 50 80
•Tighten each nut and bolt again clockwise at least once, until the maximum torque has been achieved uniformly;
•Common procedures (threaded and flanged devices):
•The regulator is normally positioned before the utility. Primarily evaluate the possibility of installing the regulator as shown in
the installation example in 3.4, namely in an optimal position pos. a(see figures below);
•Should this not be possible, the following factors must be considered:
1. if installed as shown in pos. bthe maximum P2 value declared on the rating plate could be less by a few mbar.
2. if installed as shown in pos. cthe life span of the product could be shorter than the duration that could be obtained
if installed in the optimal position a;
3. if installed as shown in pos. d, besides that indicated for pos. cit is recommended to install a filter after the
regulator that protects it from debris that could enter from downstream from above (due to gravity);
a b dc
•During installation, avoid debris or metal residues from getting into the device;
•To guarantee mechanical tension-free assembly, we recommend using compensating joints, which also adjust to the pipe’s
thermal expansion;
•If the device is to be installed in a ramp, it is the installer’s responsibility to provide suitable supports or correctly sized
supports, to properly hold and secure the assembly. Never, for any reason whatsoever, leave the weight of the ramp only on
the connections (threaded or flanged) of the individual devices;
•In any case, after the installation check the tightness of the system, avoiding to subject the membrane of the regulator
(therefore, the downstream pipe section) to a pressure higher than 300 mbar;

6
EN
1
2
345
6
8
9
7
7
10
11
piping applicaon
discharge in open air
internal thermal unit
non-hazardous venlated zone*
external roof
12
3.4 GENERIC EXAMPLE OF AN INSTALLATION
1. Manual reset solenoid valve
2. Jerk ON/OFF valve
3. Gas filter
4. OPSO shut off valve
5. 356 BOSS pressure regulator
6. Relief valve
7. Pressure gauge and relative button
8. Vent valve
9. Ball valve
10. Gas detector
11. Remote jerk ON/OFF valve lever control
12. Expansion joint/anti-vibration mount
3.3
INSTALLATION IN PLACES WHERE THERE IS THE RISK OF EXPLOSION (DIRECTIVE 2014/34/EU)
The regulator complies with Directive 2014/34/EU as a device of group II, category 2G and as device of group II, category
2D; consequently, it is suited for installation in zones 1 and 21 (besides zones 2 and 22) as classified in Annex I of Directive
99/92/EC.
The regulator is not suited for use in zones 0 and 20 as defined in the aforementioned Directive 99/92/EC.
To determine the qualification and size of the danger zones, please refer to standard IEC EN 60079-10-1.
If the device is installed and serviced in full compliance with all the conditions and technical instructions provided in this
document, it does not pose a source of specific hazards: in particular, under normal operating conditions, the regulator emits a
flammable substance into the atmosphere ONLY if both the working membrane (9) and the safety membrane (7) malfunction:
in which case (and only if so), the regulator constitutes a source of emission of explosive atmosphere of continuous degree
and, as such, it can generate danger zones 0, as defined in Directive 99/92/EC.
In particularly critical installation conditions (unattended areas, poor maintenance or poor ventilation) and especially if there
are potential sources of ignition and/or hazardous equipment near the regulator in regular operation, as they may generate
electric arcs or sparks, a preliminary assessment of the compatibility between the regulator and such equipment must be
carried out.
In any case, every useful precaution must be adopted so as to prevent the regulator from generating zones 0: for example,
annually verify regular operation, possibility of changing the degree of emission of the source or intervening on the external
explosive substance discharge. For this purpose the threaded hole of the top cover (4) can be connected to the outside (using
appropriate fittings and pipes) by removing the dust cap (6).
* if the zone is ATEX classified follow that indicated in 3.3
5 DN

7
EN
4.0 FIRST STARTUP
Before commissioning, verify that:
•all of the instructions on the rating plate, including the direction of flow, are observed;
•the holes of the dust cap (6) are not clogged.
•IMPORTANT: The leak test of the piping must be performed while avoiding to subject the membrane of the
regulator (therefore, the downstream pipe section) to a pressure higher than 300 mbar. Use special manual gas
closing devices to prevent damaging the regulator;
•The pressurisation manoeuvre of the equipment must be carried out very slowly so as to avoid possible damage.
NOTE: under no circumstances should a blind cap be placed instead of the dust cap (6) as the regulator may
not work;
•Open the downstream vent valve partially;
•Slowly open the upstream shut-off devices (e.g. solenoid valves, OPSO shut-off valve, etc.);
•Wait until the downstream pressure stabilises at the calibration value P2 of the spring (indicated on the plate);
•Close the vent valve;
•Check the tightness of all the system gaskets and check the internal/external tightness of the regulator;
•Open the downstream shut-off valve very slowly;
•Check the operation of the regulator.
4.1 - RECOMMENDED PERIODIC CHECKS
•Use a suitable calibration tool to ensure the bolts are tightened as indicated in 3.2;
•Check the tightness of the flanged/threaded connections on the system;
•Check the tightness and operation of the regulator;
It is the responsibility of the final user or installer to define the frequency of these checks based on the severity of the service
conditions.
4.2 - ADJUSTING THE OUTLET PRESSURE
Before starting the system, make sure that the spring supplied with the regulator is suitable for the desired adjustment
pressure. The outlet pressure P2 (unless specifically requested) is factory set with the top cover (4) positioned as shown in
3.2 aand with the adjustment screw (2) set approximately at the minimum calibration value.
If the regulator is installed in different positions, check and reset the outlet pressure P2.
Adjust the outlet pressure as follows:
•Unscrew the cap (1);
• Unscrew the adjustment screw (2) and set it to the minimum calibration allowed (threaded end of the top cover (4));
•Start the system or make sure there is a minimum flow downstream of the regulator;
•To increase the pressure calibration downstream of the regulator, tighten the adjustment screw (2) to the desired value.
Perform the reading with a calibrated pressure gauge, installed downstream of the regulator to at least 5 DN (see example in 3.4);
•Screw the cap (1) back on and if necessary, seal it in that position using the appropriate seal holes (if present);
•Use pressure outlets (13) on the device only for zero flow or very low flow measurements.
4.3 - REPLACING THE SPRING
The step must be carried out without gas inside the regulator.
Replace the spring as follows:
•Unscrew and remove the cap (1) from the top cover (4);
•Completely loosen and take out the adjustment screw (2);
•Remove the spring washer (26);
•Remove the spring (3) from the top cover (4) and replace it with the new spring;
•Place the washer (26) on the new spring once again;
•Tighten the adjustment screw (2) and after starting the system as shown in 4.0, set the outlet pressure to the desired value
as shown in 4.2;
•Screw the cap (1) back on and if necessary, seal it in that position using the appropriate seal holes (if present);

8
EN
Filter element guides
Filter element guides
The filter element must be
placed inside these guides
* Only for versions equipped with an internal filter.
The filter element must be
placed inside these guides
fig. a: DN 15 ÷ DN 50 cover without bottom cover fig. b: DN 65 ÷ DN 100 cover without bottom cover
5.0 MAINTENANCE
•Before carrying out any dismantling operation on the device, make sure that there is no pressurised gas inside.
Check the condition of the filtering element (21) as follows*
• Loosen the fastening screws (17 ) and very carefully remove the bottom cover (16) from the body (11 );
• Extract the filter element and check its conditions. Blow it and clean it and, if necessary, replace it (see figures “a” and “b”
below for the positioning);
• Check the conditions of the sealing O-Ring of the bottom cover (16) and replace if necessary;
• Make sure the sealing O-Ring (18) of the bottom cover (16) is inside the relevant groove before putting it back on;
• Reassemble the bottom cover (16) and secure it in its original position, being very careful not to “pinch” or damage the
O-ring during tightening.
IMPORTANT:
1. for DN 15 ÷ DN 50 connections make sure that the centre pin (10) is centred in the guide of the bottom cover (16);
2. for DN 65 - DN 80 - DN 100 connections pay attention to the Teflon split ring (14): when reassembling the bottom
cover (16) it must be placed inside the specific guide (as shown in figure 3);
• Tighten the screws gradually, following a “cross” pattern, until the torque (tolerance -15%) indicated in table 2 on page 13
is reached. Use a calibrated torque wrench to do this.
• Check the body/cover seal;
NOTE: for internal inspections, it is recommended to:
• Also check the obturator’s integrity and, if necessary, replace the rubber seal (15);
• Replace the seals before reassembling.
• It is recommended to contact the Technical Department to check or replace the membranes.

9
EN
6.0 TRANSPORT, STORAGE AND DISPOSAL
• During transport the material needs to be handled with care, avoiding any impact or vibrations to the device;
• If the product has any surface treatments (ex. painting, cataphoresis, etc) it must not be damaged during transport;
• The transport and storage temperatures must observe the values provided on the rating plate;
• If the device is not installed immediately after delivery it must be correctly placed in storage in a dry and clean place;
• In humid facilities, it is necessary to use driers or heating to avoid condensation.
• At the end of its service life, the product is to be disposed of in compliance with the legislation in force in the country where
this operation is performed.
7.0 WARRANTY
The warranty conditions agreed with the manufacturer at the time of the supply apply.
For damage caused by:
•Improper use of the device;
•Failure to observe the requirements described herein;
•Failure to observe the regulations pertaining to installation;
•Tampering, modification and use of non-original spare parts;
are not covered by the rights of the warranty or compensation for damage.
The warranty also excludes maintenance work, other manufacturers’s assembling units, making changes to the device and
natural wear.
8.0 RATING PLATE DATA
The rating plate data (see example provided here) includes the following:
• Manufacturer’s name/logo and address
• Mod.: = device name/model followed
by the connection diameter
• CE-51CL4012/ED01 = certification pin number
• P1 max = Maximum pressure at which product operation is guaranteed
• TS = Temperature range within which product operation is guaranteed
• P2 = Outlet pressure range
• Cl. A = Tolerance on P2 ( A= ± 15% )
• Gr. 2 = Mechanical resistance group 2 in accordance with EN 13611
• EN 88-1 = Product reference regulation
• = Conformity with Regulation (EU) 2016/426 followed by Notified Body No.
• = In compliance with ATEX Dir. followed by the protection mode
• year = Year of manufacture
• Lot = Product serial number (see explanation below)
• U2002 = Lot issued in year 2020 in the 2nd week
• 1728 = progressive job order number for the indicated year
• 00002 = progressive number referring to the quantity of the lot
Mod.: DN 50 BOSS 356
CODE: 35501293
P1 max: 500 mbar TS: -15+60 °C
P2:
13-23 mbar
CE-51CL4012/ED01 Cl.A Gr.2 EN 88-1
year: 2020 Lot: U2002 1728/00002
Lodge Way House, Lodge Way,
Harlestone Road,
Northampton NN5 7UG.
0051

10
EN
fig. 1
Threaded connections in line
DN 15 - DN 20 - DN 25

11
EN
fig. 2
Threaded connections in line
DN 32 - DN 40 - DN 50

12
EN
fig. 3
Flanged connections
DN 65 - DN 80 - DN 100
19mm

13
EN
fig. 1, 2 and 3
1. Closing cap
2. Adjustment screw P2
3. Calibration spring
4. Top cover
5. Toothed washer (except DN 15-20-25)
6. Dust cap
7. Safety membrane
8. Flange
9. Working membrane
10. Centre pin (on DN 15-20-25 obturator pin)
11. Body
12. Sensor tube
13. Pressure test niplle
14. Teflon ring (only on DN 65-80-100)
15. Sealing washer
16. Bottom cover
17. Bottom cover clamping screws
18. Bottom cover sealing O-Ring
19. Obturator
20. Compensation membrane
21. Filter element
22. Top disk for membrane
23. Top cover clamping screws
24. Bottom disk for membrane
25. Membrane/disc fixing nut
26. Spring washer
Table 2
Screw M5 M6
Max. torque (N.m)
Galvanised
6
10
Stainless Steel 4,5 7,5
Table 1
Overall dimensions in mm
Threaded connections in line
Flanged connections holes A B=(D+E) C D E
Rp DN 15 - Rp DN 20
Rp DN 25 -120 194 140 38,5 155,5
Rp DN 32 - Rp DN 40
Rp DN 50 -160 242 225 48,5 193,5
PN 16 - ANSI 150 DN 65 4 290 456 330 90 366
PN 16
DN 80 8310 463 330 97 366
ANSI 150
DN 80 4 290 456 330 90 366
PN 16 - ANSI 150
DN 100 8 350 502 330 106 396
The dimensions are provided as a guideline, they are not binding

14
EN
Table 3
Regulation spring data
Spring code dimensions in mm (dx De x Lo x it) Connections Setting (mbar)
MO-0402 1,5x29x85x10
DN 15 - DN 20 - DN 25
9 ÷ 28
MO-0500 1,6x29x115x12 18 ÷ 40*
MO-0825 2,2x29x100x12 40 ÷ 110
MO-0900 2,5x29x140x18,5 110 ÷ 150
MO-0970 2,5x29x155x16 150 ÷ 200
MO-0500 1,6x29x115x12
DN 32 - DN 40 - DN 50
8 ÷ 13
MO-0800 2x29x140x16 13 ÷ 23*
MO-0850 2,2x29x140x18 20 ÷ 36
MO-0970 2,5x29x155x16 33 ÷ 58
MO-1000 3,2x29x123x15,5 55 ÷ 100
MO-1370 3,5x29x125x14 90 ÷ 190
MO-1070 4x66,5x155x16
DN 65 - DN 80
7 ÷ 18
MO-1100 4,5x70x200x15,5 13 ÷ 27*
MO-1200 5x70x205x9,5 22 ÷ 58
MO-1400\ZN 6x70x214x10,5 50 ÷ 130
MO-1400\ZN + MO-1800\ZN 6x70x200x10,5 + 5,5x54,5x195x12,5 100 ÷ 200
MO-1070 4x66,5x155x16
DN 100
7 ÷ 16
MO-1100 4,5x70x200x15,5 15 ÷ 27*
MO-1200 5x70x205x9,5 27 ÷ 55
MO-1400\ZN 6x70x200x10,5 55 ÷ 130
MO-1400\ZN + MO-1800\ZN 6x70x200x10,5 + 5,5x54,5x195x12,5 130 ÷ 200
* Standard setting
it= total number of turns

15
EN
Capacity diagram
Diagram calculated with P1 = 50 mbar and regulator set out of service
dv = density relative to the air 1) methane
2) air
3) town gas
4) lpg

Mod. IT396.00 E
We reserve the right to any technical and construction changes.
Registered Office: Travis Perkins PLC, Lodge Way House, Lodge Way, Harlestone Road, Northampton NN5 7UG.
Telephone Number: 0116 245 5500
This manual suits for next models
9
Table of contents
Other BOSSCO Controllers manuals
Popular Controllers manuals by other brands
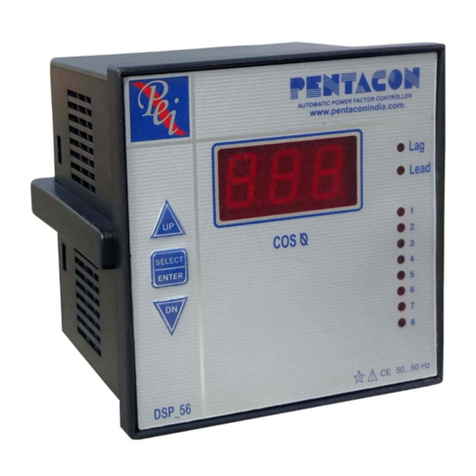
Pentacon
Pentacon DSP-56 Operation manual
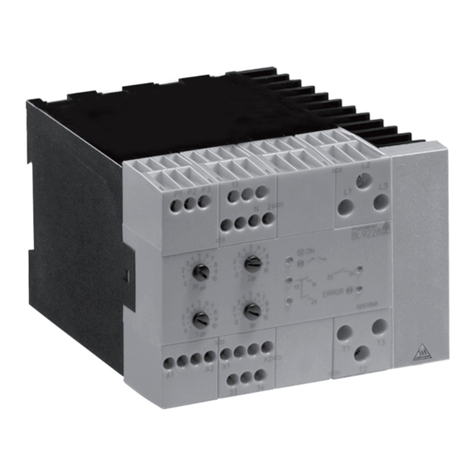
EDS
EDS BL 9228 quick start guide
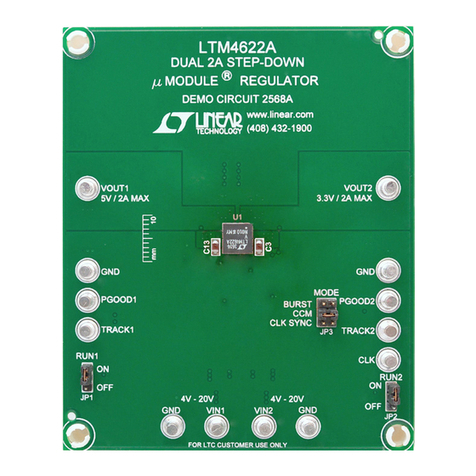
Linear Technology
Linear Technology Analog Devices LTM4622A datasheet
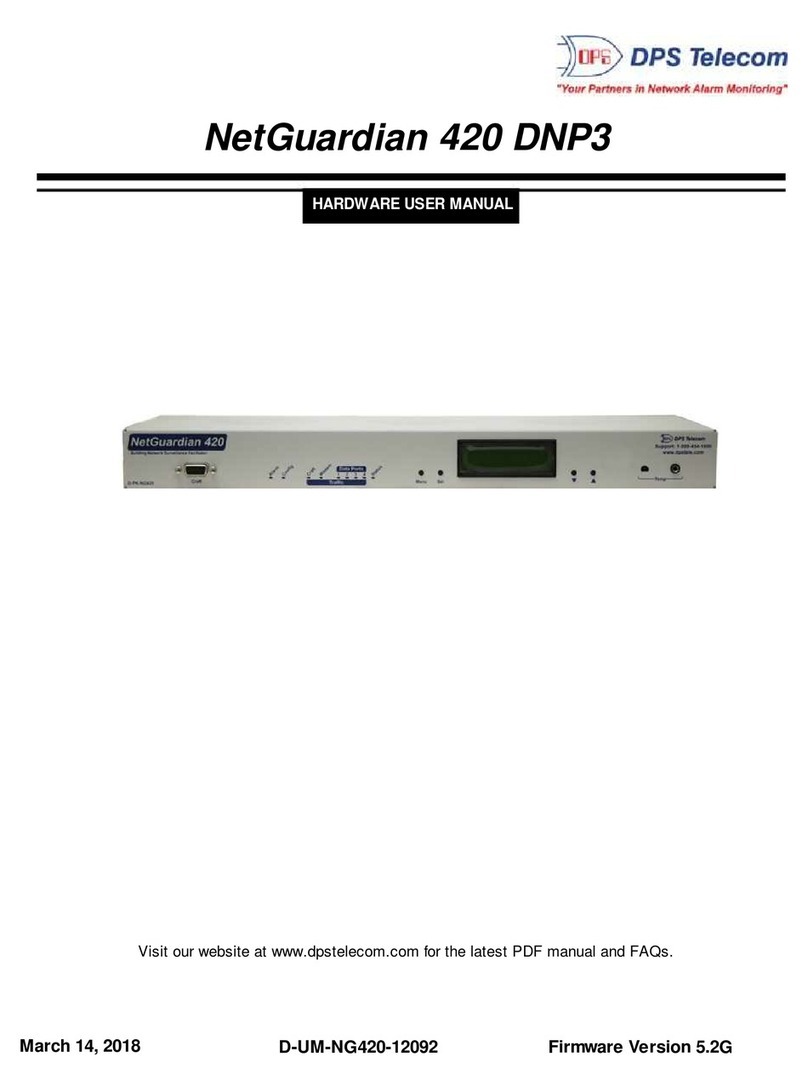
DPS Telecom
DPS Telecom NetGuardian 420 DNP3 Hardware user manual
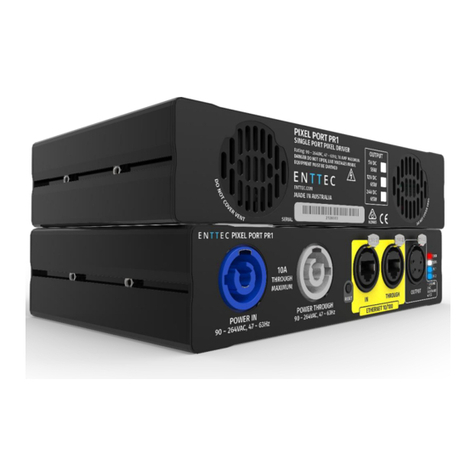
Enttec
Enttec PIXEL PORT user manual
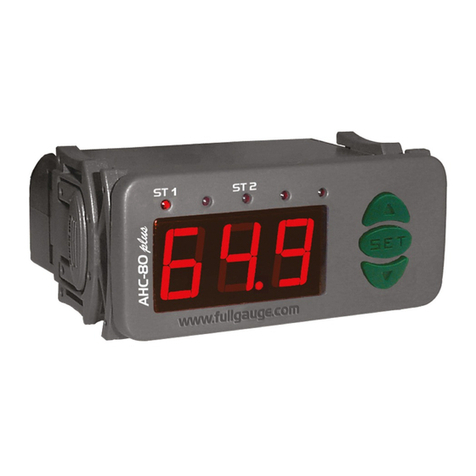
Full Gauge Controls
Full Gauge Controls AHC-80 plus quick start guide