BOSSCO EA218 Series User manual

EA218-140-A4-IOM-MAIN-Rev0-Feb 16
EA218 Series Electric Valve Actuator
I O Ms
Installation Operation & Maintenance Instructions
ON-OFF, FAILSAFE, MODULATING & FAILSAFE MODULATING FUNCTIONS
USER FRIENDLY ON-OFF ELECTRIC ACTUATOR WITH
LED STATUS LIGHT AND ALL EXTERNAL ELECTRICAL
CONNECTIONS
Models 140 & 300

INDEX
IDENTIFICATION LABEL
DO NOT remove the ID label from the actuator. Removal prevents us from being able to idenfy the
actuator and therefore the removal of any labels instantly invalidates the warranty irrespecve of the
supply date.
Item Detail
1BOSS Logo
2Working voltage range
3Motor duty rang
4Ambient temperature range
5Ingress protecon rang
6Serial Number
7CE mark
8BOSS Product Type
9BOSS Model Number
10 BOSS ID Number
11 Maximum break torque
12 Running and reseat torque
13 Run me for specied angle
14 ISO5211 Mounng opons
15 Barcode (factory use only)
Page Details Page Details
1Front cover 5Explanaon of the dierent funcons available
2Index, Structure, ID label 6Direcon of rotaon, posion indicators, working quadrant
3Safety instrucons, Principle of Operaon, Connectors 7LED light, manual override, torque limiter
4Wiring diagrams for on-o, failsafe and modulang 8Mounng, weatherproof rang, recycling, support
STRUCTURE OF BOSS EA218 QUARTER TURN ELECTRIC VALVE ACTUATORS
The BOSS EA218 range of electric actuators are simply a gearbox, a motor and a complex electronic circuit board containing a
small computer chip, are designed so that in normal circumstances there are no internal adjustments that need to be made
and that as all electrical connecons are external and the connecng plugs are supplied with the actuator, there is no need to
remove the actuator’s cover to connect them. Inside the actuator thee are no terminal strips or dip switches that require
user adjustment or seng. The EA218 is a maintenance free product.
Therefore removing the actuator’s cover may invalidate the warranty. If you feel you need to remove the cover, please check
with your supplier BEFORE removing the cover.
Page 2
⑨
⑩
⑭
⑪
⑫
⑬
⑥
⑤
③
②
①
④
⑦
⑧

SAFETY INSTRUCTIONS
Damage caused by non-compliance to these instrucons will not be covered by our warranty. It is essenal therefore that you read these instruc-
ons BEFORE installing or connecng the actuator.
SAFETY INSTRUCTIONS
BOSS EA218 Electric actuators operate with the use of live electricity. It is recommended that only qualied electricians or people instructed in
accordance with electrical engineering, and familiar with local health and safety direcves, be involved in the connecon of these actuators. It is
strongly recommended that each actuator has its own independent fused power supply system to protect it against the inuence of other electrical
devices connected to the system.
EXTERNAL ELECTRICAL CONNECTORS - DIN PLUGS - SUPPLIED WITH THE ACTUATOR
ELECTRICAL CONNECTORS (DIN Plugs) - DO NOT remove the cover to connect.
BEFORE connecng, ensure the voltage to be applied is within the range shown on the actuator’s ID label. Do NOT connect a voltage in excess of
24V to the low voltage actuators or irreparable damage will be caused and will NOT be covered by our warranty. All connecons are made using
the supplied external DIN plugs. There is no need to remove the cover to connect electrically - removing the cover may invalidate the warranty.
Always check with your supplier BEFORE removing the cover as they will give you informaon relevant to removing and replacing the cover. The
grey plug is for the external power signals, the black plug is for volt free (dry contact) end of travel conrmaon.
CONNECTOR
DIN:43650 ISO:4400 &
C193
Mini cable Ø Max cable Ø
8 mm 10.5 mm
8 mm 10.5 mm
Item Detail
1Gasket/ seal.
2Terminal strip
3Cable securing screws x 4
4Housing
5Grommet
6Washer & seal
7Gland nut
8SS Securing screw
❶
❸
❷
❺❹
❽❻
❼
Page 3
PRINCIPLE OF OPERATION
The standard funcon of an EA218 electric valve actuator is power open, power close. It stays put on mains power failure. On receipt of a
connuous power signal, the motor runs and via a planetary gearbox system, rotates the output sha. The motor is stopped by internal
cams, ed to the output sha, striking micro-switches which cuts power to the motor. When a subsequent connuous reversing signal is
received, the motor will turn in the opposite direcon, reversing the direcon of rotaon of the output sha. The actuator can be jog con-
trolled by switching the power on to start and o to stop. Be aware that during the ‘o’ period the an-condensaon heater is de-energised.
As we provide an-condensaon protecon, damage caused by condensaon is not covered by our warranty.
Uniquely the EA218 can have this standard open-close funconality changed by installing user friendly plug and play kits, to create failsafe,
modulang and failsafe modulang funconality.

WIRING DIAGRAMS
We recommend a fused independent supply for each actuator and it is very important that the power supply earth connecon is made to prevent
the current-free voltage on the non-live pin prevenng the actuator working. This current-free voltage disappears as soon as the motor runs, but
in non-earthed systems it can stop the EA218 from working.
The posion conrmaon switches are volt free and can have a dierent voltage applied than the power supply voltage e.g. 220V/1ph power
supply, 24VDC for posion conrmaon. For ease, the schemac below shows the same voltage for both power and posion conrmaon. See
notes at the boom of this page regarding use of the volt fee contacts (end of travel conrmaon).
Funcon opons with the EA218 electric actuator:
ON-OFF ELECTRIC ACTUATOR
Standard funcon is power open, power close. Stays put on
loss of external power. Power remains on at all mes.
FAILSAFE ELECTRIC ACTUATOR
Fails to pre-set posion on loss of external power.
Power open, power close, fails to pre-set ‘safe’ posion on
loss of external power using internal industrial trickle charged
rechargeable NiCad baery. Can be set to fail close (NC or
normally closed) or fail open (NO or normally open) on loss of
external power. The failsafe electric actuator moves to the
posion command applied at the me external power is re-
stored.
MODULATING ELECTRIC ACTUATOR
Movement proporonal to input signal
Power is applied connuously. Movement of valve
actuator is then controlled by an internally ed
digital posioner and is proporonal to changes
supplied in an input control signal. This input
signal is typically 0-10VDC, or 4-20mA. An output
signal is supplied as standard providing closed
loop control. Fails closed on loss of control signal
(or see conguraon opons below), stays put on
loss of external power.
Conguraon opons:
1) Closes on loss of control signal
2) Opens on loss of control signal
3) Stays put on loss of control signal
IMPORTANT NOTES
EXTERNAL POWER SUPPLY/ COMMAND SIGNALS, AND POWER SUPPLY SIZING
The EA218 electric actuator is designed to have connuous (not pulsed) external power applied at all mes. It’s internal thermostac an-
condensaon heater uses the external power to funcon, so switching o the power at end of travel switches this protecon o. Damage caused by
the eects of condensaon is not covered by our warranty as we provide protecon against it as standard. It is imperave that the power supply has
sucient capacity to drive the EA218 electric actuator. Ensure that safety factor of 3 is used to cover inrush on start-up, and for increased draw over
me as the brushed DC motor wears.
Another issue with using the end of travel conrmaon signals to switch o the command signals is that as they are set around 5 degrees ahead of
the nal motor stop posion (fully open, or fully closed), if used to switch o the power, the valve will not reach the nal motor stop posions.
EA218 FAILSAFE MODULATING ACTUATOR
Combinaon of failsafe & modulang kits above: Uses baery failsafe system and digital posioner plug and play funcon conversion kits to provide fail to
a safe posion funcon on loss of external power in a modulang applicaon.
Page 4
EA218 MODULATING WIRING (0-10V or 4-20mA)
②
③
①
N/- L/+
VAC/VDC
External Power
+
-
+4-20mA or
0-10VDC
Input
Output
4-20mA or
0-10VDC
Do not connect
③
①②
Control Signal I/O
L/+ N/-N/-
Note: Above doed line is
customer supplied
Posion Conrmaon
CLOSE OPEN
VAC/VDC
②
③
①
L/+ N/-N/-
CLOSE OPEN
②
③
①
N/- L/+
OPEN
CLOSE
VAC/VDC
Note: Above line above is customer supplied
External Power Posion Conrmaon
VAC/VDC
EA218 ON-OFF & FAILSAFE WIRING (Same connecon for either)
②
③
①

EXPLAINATION OF THE DIFFERENT FUNCTION OPTIONS
Power to open, power to close: Stays put on mains power failure.
On receipt of a connuous power signal, the motor runs and via a planetary gearbox system,
rotates the output sha. The motor is stopped by internal cams, ed to the output sha, strik-
ing micro-switches which cuts power to the motor. When a subsequent connuous signal is re-
ceived, the motor will turn in the opposite direcon, reversing the direcon of rotaon of the
output sha. The actuator can be jog controlled by switching the power on to start and o to
stop.
Failsafe Function: Power open, power close, fails to pre-set position on
power failure
Under normal operaon the EA218 failsafe electric actuator operates as an on-o actuator as
above. Whilst power is applied, an internal industrial rechargeable baery is trickle charged to
ensure it is fully charged. In the event of external power failure, the power source is switched
from external to internal and baery power is used to send the actuator to the pre-set 'safe'
posion, if not already in that posion. Standard fail posion is closed (fail closed or normally
closed) but fail open (normally open) can be set. On resumpon of external power, the actuator
will move relave to the command signal being applied at the me power is restored. This safety
system is called BSR (Baery 'Spring Return'). The BSR is a plug and play kit that can either be
supplied installed and tested by us, or supplied as a simple to install and user friendly retro-t kit.
Modulating Function: Movement of the actuator is proportional to an
input signal via a digital positioner. Stays put on loss of external power.
The is a self-calibrang and auto-adjusng Digital Posioning System supplied as a retro-t opon
to the range of reversible electric actuators to produce modulang funconality. The self-
calibrang feature senses the motor stop closed posion and sets the span from this posion,
and then auto-calibrates the steps between open and closed for either 4-20mA or 0-10VDC con-
trol signals. Hunng has been virtually eliminated in the DPS and as soon as the actuator arrives
at the required posion relave to the input signal, it stops. On receipt of a control input signal
the actuator will move to the posion relave to the input signal eg: using a 4-20mA signal, 4mA
input signal closes the actuator, a 12mA signal sets the actuator at 45° and a 20mA signal opens
the actuator. Each subsequent change of input signal will cause a corresponding change to the
actuator posion. This funconality can be reversed (reverse acng) if required. An output signal
in the same form as the input signal is supplied as standard. In the case of control signal failure,
the actuator will move to the closed posion (or open if congured reverse acng). In the case of
external power failure, the actuator will stay in the posion it saw at the moment of power inter-
rupon, and will move to the signal it sees on resumpon of external power.
Failsafe Modulating Function: Fails to pre-determined safe position on
loss of control signal or on loss of external power
The EA218 Modulang actuator fails to safe posion on loss of power. By installing both the BSR
and DPS funcon conversion kits, the EA218 can provide failsafe modulang funcon in all mod-
els.
EA218 ON-OFF ACTUATOR
DPS can be set to FAIL FREEZE
on loss of control signal.
Can be set to fail open, or fail closed
EA218 FAILSAFE ACTUATOR
EA218 MODULATING ACTUATOR
EA218 FAILSAFE MODULATING
ELECTRIC ACTUATOR
Page 5

The BOSS EA218 operates in the 0° to 90° quadrant shown in the diagram to the le. If it is oper-
ated manually and returned into automac mode whilst the actuator’s indicator is outside the
working quadrant, on the rst automac movement the EA218 will rotate unl it acvates the
correct nish posion relave to the command signal - the actuator may rotate well beyond its
normal 90° rotaon to reset its posion. This extended rotaon is normal in these circumstances.
EA218 OPENS counter-clockwise
ACTUATOR OPEN
DIRECTION OF ROTATION & VISUAL POSITION INDICATION (2 Way valves)
EA218 CLOSES clockwise CLOSED
VISUAL POSITION INDICATION (3 Way valves)
Typical ow arrangement for L port DIVERTING 3 way ball valves. Other ow paths are available.
Typical ow arrangement for T port DIVERTING 3 way ball valves. Other ow paths are available
Typical ow arrangement for T port MIXING 3 way ball valves. Other ow paths are available
ACTUATOR CLOSED
Q
Q = Working quadrant
OPEN
CLOSED
STANDARD WORKING QUADRANT
ADJUSTING THE WORKING QUADRANT
Should the required working angle be dierent to the standard factory set 0° to 90°, it is possible to adjust the internal cams to extend the motor’s running
me and therefore increase the working angle; (to 180° for boom entry 3 way ball valves for example), but we recommend contacng your supplier to get
advice on how to correctly and safely make these adjustments. Detailed instrucons are available on request.
OPEN
Page 6

MANUAL OVERRIDE
Select ‘MAN’ for hand operaon
Selecng ‘MAN’ by moving the selector lever from ‘AUTO’ disengages the output drive, but the motor connues to run. Aer a short me the EA218 realises
the end of travel cam has not been reached, the motor is running with no load which indicates the valve is not jammed—therefore the actuator is in manual
mode. The motor then stops and the LED sequence 4 above starts to advise the user that the actuator is in ‘MAN’.
As a safety measure, the EA218 will not respond to external command signals whilst in manual mode. On returning the selector lever to ‘AUTO’ the LED re-
turns to being solidly lit, and the actuator will respect whatever command signal is being applied at the me the selector lever is returned to ‘AUTO’.
❸
Select ‘AUTO’ to return to automac operaon
❶❷
Select ‘MAN’DO NOT TURN THE EA218 HAND WHEEL
WITHOUT FIRST SELECTING ‘MAN’ OR
IRREPARABLE DAMAGE WILL BE CAUSED
TO THE ACTUATOR’S GEARBOX.
SUCH DAMAGE IS NOT COVERED BY THE
WARRANTY
Turn by hand to operate
LED blinks, see sequence
in table below
ELECTRONIC TORQUE LIMITER
The EA218 has an electronic torque limiter (ETL) to protect the internal gears from mechanical damage should the valve become blocked or jammed. The ETL
constantly measures the motor current and using a complex algorithm in the on-board chip, senses the rise in motor current seen at the point of blockage and
cuts the power to the motor.
At this point the LED will blink in the sequence shown in the table on page 8, and the chip in the actuator will operate the unit in the opposite direcon to the
blockage for a few degrees, in order to relax the gearbox, and allow for the manual override to be ulised if required.
Page 7
The LED light is a standard feature in the EA218 and it serves 3 main funcons:
1) When on / lit, it advises users that the actuator has external power applied to it.
2) When connuously lit, the EA218 is funconal and awaits external commands to operate
3) If the LED blinks, there is a problem that is prevenng the EA218 from working. The sequence of the blinks gives the user an indicaon of the cause. The
most common of these are to advise that either the valve is jammed and the EA218’s electronic torque limiter has acvated, or that the actuator is in manual
mode. See table on the following page for the common LED sequences.
EA218 with power, LED on.
MULTI-COLOUR LED STATUS LIGHT
EA218 without power, LED o.
Provides connuous at-a-glance actuator status feedback
MULTI-COLOUR LED:
RED = CLOSED
GREEN = OPEN
See table on following page for
LED sequence and colours.

Main features of the EA218 electric actuator’s mul-colour LED status light.
Valve closed Solid RED
Valve opening Blink GREEN / AMBER
Valve open Solid GREEN
Valve closing Blink RED / AMBER
EA218 responds to remote commands - normal opening and closing.
EA218 does not respond to remote commands - normal opening and closing.
Torque limiter acvated, valve closing Blinks RED
Torque limiter acvated, valve opening Blinks GREEN
‘MAN’ Manual mode selected Double blinks AMBER
EA218 in baery mode (external power lost) with BSR failsafe system installed
Baery back-up acvated, valve closing Slow blinks RED
Baery back-up acvated, valve opening Slow blinks GREEN
MULTI-COLOUR LED STATUS LIGHT
Page 8

MOUNTING THE EA218 ACTUATOR TO 1/4 TURN VALVES
EA218 Actuators have mounng facilies in accordance with ISO:5211 and DIN:3337 allowing them, in many cases, to mount directly onto similarly compliant
valves without the need for a mounng kit (bracket and drive adaptor / connector). The main advantages of direct mounng the actuators is to greatly assist in
ensuring concentricity of the actuator output drive with the valve stem which eliminates side loadings (which result in increased wear on the valve stem and
seals), reducing the eects of backlash in the drivetrain as there are fewer parts connected, and allowing valves to be partly dismantled for installaon into the
pipe without disturbing the valve to actuator connecon.
The drive being inserted into the actuator’s female output drive must NOT be longer than the maximum depth of the female drive when the
assembly is bolted together. Resulng damage to the actuator and assembled components due to this assembly error will not be covered by our
warranty.
EA218
Model
Maximum
torque Nm
ISO5211 Output star
drive
Oponal star
output
Special execuon
on request
Maximum
Drive Depth
140 170 F07 & F10 22 1724
300 350 F07 & F10 22 17 F12 x 22 star24
WEATHERPROOF RATING
The EA218 electric actuators have an ingress protecon rang of IP67, which gives them total protecon
against almost all kinds of weather and allows the actuator to be submerged under less than 1m of water for
no more than 30 minutes. However, it cannot withstand being hosed down or pressure washed, or deluged in
water.
If the EA218 is to be exposed to hosing down or pressure washing, a plasc bag must be rst put over the
actuator to protect it from the direct hosing down. Even in these circumstances, do not pressure wash the
plasc bag close up.
Damage caused by water ingress is therefore not normally covered by the warranty.
RECYCLE AT END OF LIFE
BOSS is commied to protecng the environment.
Please remember at the end of the product’s life to dispose of the product responsibly,
and to recycle the product if the facilies are available.
TECHNICAL SUPPORT
Technical support:
Page 9
Telephone: 0844 800 721
Web: www.bssindustrial.co.uk
Email: peglerandl[email protected]om
This manual suits for next models
2
Table of contents
Other BOSSCO Controllers manuals
Popular Controllers manuals by other brands
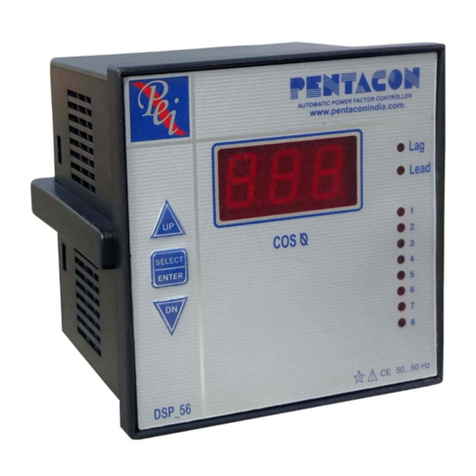
Pentacon
Pentacon DSP-56 Operation manual
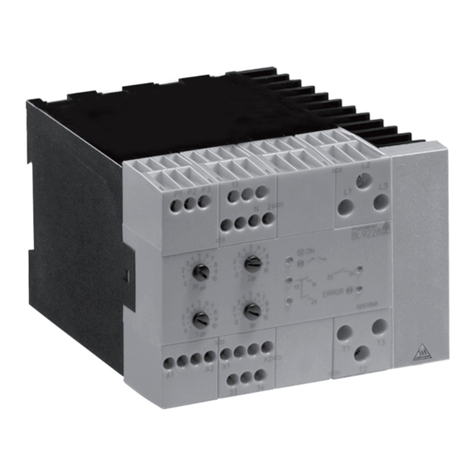
EDS
EDS BL 9228 quick start guide
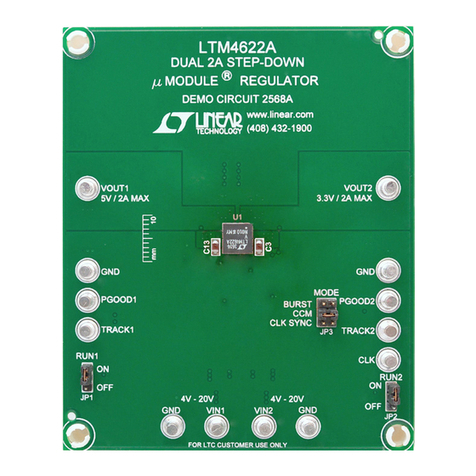
Linear Technology
Linear Technology Analog Devices LTM4622A datasheet
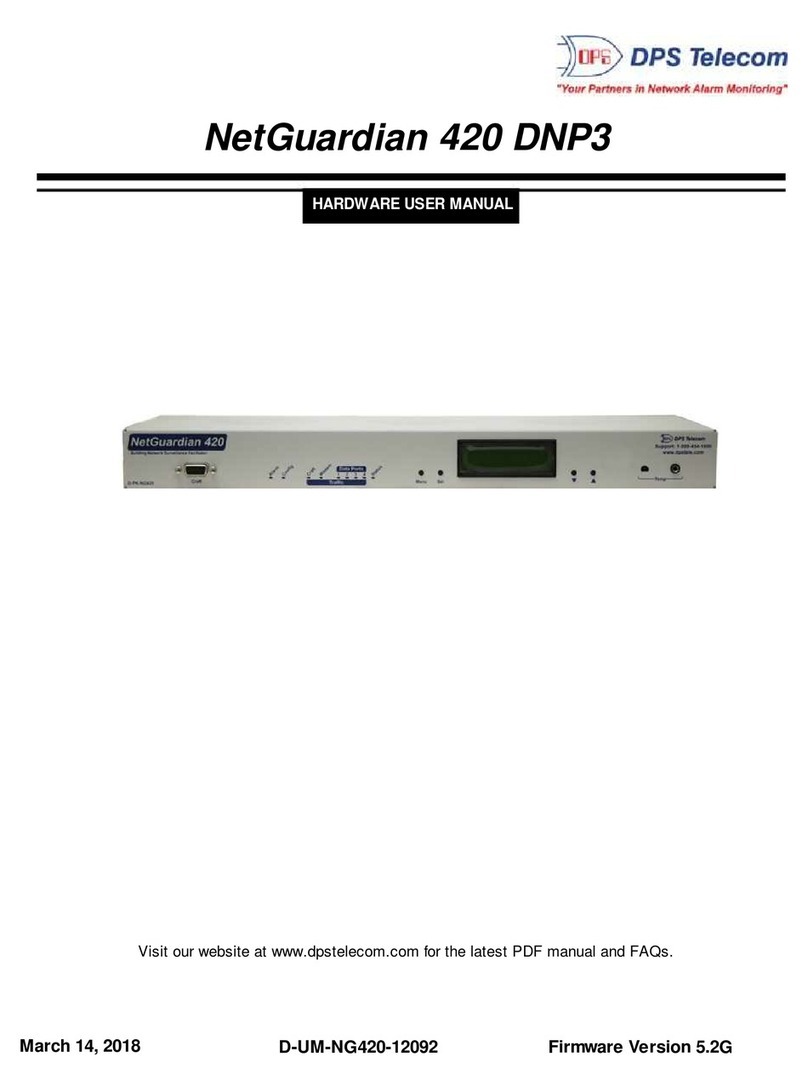
DPS Telecom
DPS Telecom NetGuardian 420 DNP3 Hardware user manual
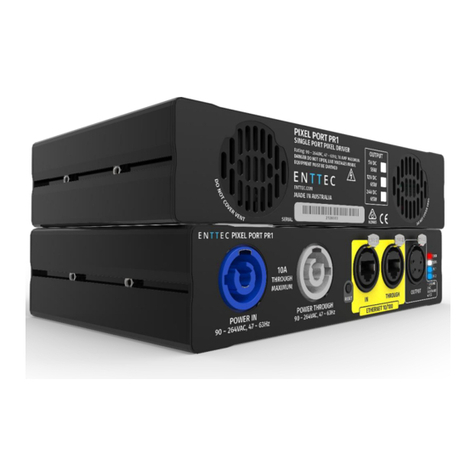
Enttec
Enttec PIXEL PORT user manual
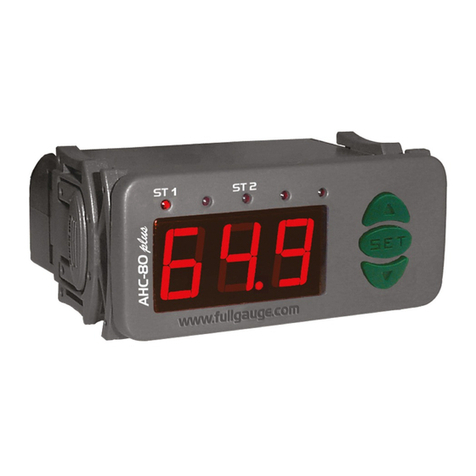
Full Gauge Controls
Full Gauge Controls AHC-80 plus quick start guide