Brunswick GS-X Series Installation and operating instructions

Operations & Service Manual
GS-X Pinsetter with
Advanced (CE) Guarding
March 2017 / 47-902748-000

GS-X Series Pinsetter with Advanced (CE) Guarding
Operation and Service Manual
© March 2017 by Brunswick Bowling Products. All rights reserved.
Frameworx, GS-X, and GS-Series are trademarks of Brunswick Bowling Products.
Manual Part No. 47-902748-000
Notice: If available, updates to this manual can be found on-line at www.brunswickbowling.com.
Condential proprietary information. All information contained in this document is subject to change
without notice.
Brunswick Bowling Products
525 West Laketon Avenue
Muskegon, MI 49441-2601
U.S.A.
231.725.330 0

Section Rev. February 2017 Safety Section 1
CONTENTS
SAFETY ALERTS ............................................................................................................................3
Notes & Warnings ..........................................................................................................................3
Safety Notice to Users of This Manual.............................................................................................4
Pinsetters Equipped with Safety Power Controllers .........................................................................5
Specialist Personnel .......................................................................................................................5
General Safety Information and Protective Measures....................................................................5
Tests Performed Before the First Commissioning .........................................................................6
Functional Checks of the Protective Devices.................................................................................6
Care and Maintenance....................................................................................................................8
Safety Guidelines for GS-Series Pinsetters.......................................................................................9
Machine Guards ..............................................................................................................................11
GS Safetty Mirror.........................................................................................................................13
Safety Power Controller...............................................................................................................14
Pinsetter Power-up Procedure - Safety Controller .......................................................................16
Pinsetter Restart Procedure - Safety Controller ...........................................................................16
Pinsetter Status Light / Machine Power on Sequence.....................................................................17
Software Version 4.9.08 and prior................................................................................................17
Software Version 4.9.09 and later ................................................................................................17
Pinsetter Access Points....................................................................................................................18
Work Areas .....................................................................................................................................19
Area 1 - Floor ..............................................................................................................................20
Area 2 - Ball Accelerator Platform...............................................................................................21
Area 3 - Standing Platforms ........................................................................................................22
Area 4 - Pindeck...........................................................................................................................23
Area 5 - Distributor ......................................................................................................................24
Stopping Machine in Mid-Cycle.....................................................................................................25
Clearing Error Codes and Correcting Pinsetter Stops.....................................................................26
Clearing Pins Jammed in Distributor ..............................................................................................27
Clearing an Elevator jam.................................................................................................................28
Removing Pin(s) From Under the Sweep .......................................................................................29
Correcting Ball Return Stops ..........................................................................................................30
Machine Cleaning ...........................................................................................................................31
Cleaning the Transport Band .......................................................................................................31
Cleaning the Distributor Belts .....................................................................................................32

2 Safety Section Section Rev. February 2017
Intentionally Blank Page

Section Rev. February 2017 Safety Section 3
SAFETY ALERTS
Notes & Warnings
Throughout this publication, “Warnings”, and “Cautions” (accompanied by one of the International
HAZARD Symbols) are used to alert the mechanic to special instructions concerning a particular
service or operation that may be hazardous if performed incorrectly or carelessly. They are dened
below. OBSERVE AND READ THEM CAREFULLY!
These “Safety Alerts” alone cannot eliminate the hazards that they signal. Strict compliance to these
special instructions when performing the service, plus training and “Common Sense” operation are
major accident prevention measures.
NOTEorIMPORTANT!:Willdesignatesignicantinformationalnotes.
WARNING! Will designate a mechanical or nonelectrical alert which could
potentially cause personal injury or death.
WARNING! Will designate electrical alerts which could potentially cause
personal injury or death.
CAUTION! Will designate an alert which could potentially cause product
damage.
Will designate grounding alerts.

4 Safety Section Section Rev. February 2017
SAFETY NOTICE TO USERS OF THIS MANUAL
This manual has been written and published by the Service Department of Brunswick Bowling
Products to aid the reader when servicing or installing the products described.
It is assumed that these personnel are familiar with, and have been trained in, the servicing or
installation procedures of these products, which includes the use of common mechanic’s hand tools and
any special Brunswick or recommended tools from other suppliers.
We could not possibly know of and advise the reader of all conceivable procedures by which a service
might be performed and of the possible hazards and/or results of each method. We have not attempted
any such wide evaluation. Therefore, anyone who uses a service procedure and/or tool, which is not
recommended by Brunswick, must rst completely satisfy himself that neither his nor the product’s
safety will be endangered by the service procedure selected.
All information, illustrations and specications contained in this manual are based on the latest product
information available at the time of publication.
It should be kept in mind, while working on the product, that the electrical system is capable of violent
and damaging short circuits or severe electrical shocks. When performing any work where electrical
terminals could possibly be grounded or touched by the mechanic, the power to the product must be
disconnected prior to servicing and remain disconnected until servicing is complete.

Section Rev. February 2017 Safety Section 5
PINSETTERS EQUIPPED WITH SAFETY POWER CONTROLLERS
The GS-X Pinsetter Safety Controller system must be commissioned and serviced only by specialist
personnel.
Specialist Personnel
Specialist personnel (Center Mechanics) are dened as persons who:
• have undergone the appropriate technical training and
• who have been instructed by the responsible pinsetter operator in the
operation of the pinsetter and the current valid safety guidelines and
• who have access to the “Safety Photoelectric Switch System L 4000” operating instructions.
General Safety Information and Protective Measures
Safety Notes
Please observe the following procedures in order to ensure the correct and safe use of the GS-X
Pinsetter Power Controller system.
• The national/international rules and regulations apply to the installation, commissioning, use
and periodic technical inspections of the GS-X Pinsetter Safety Controller system, in particular:
• Machine Directive 98/37/EEC
• Equipment Usage Directive 89/655/EEC
• the work safety regulations/safety rules
• other relevant health and safety regulations
• Users of the pinsetter equipped with the GS-X Pinsetter Safety Controller system are
responsible for obtaining and observing all applicable safety regulations and rules.
• It is imperative that all notes created during the TestsPerformedBeforetheFirst
Commissioning and FunctionalChecksoftheProtectiveDevice sections of this manual are
observed.
• The tests must be carried out by the center mechanic and must be recorded and documented to
ensure that the tests can be reconstructed and retraced at any time.
• The operating instructions must be made available to the user of the pinsetters equipped with
the GS-X Pinsetter Safety Controller system. The pinsetter operator is to be instructed in the
use of the device by center mechanic and must be instructed to read the operating instructions.

6 Safety Section Section Rev. February 2017
Tests Performed Before the First Commissioning
The purpose of the tests before the rst commissioning is to conrm the safety requirements specied
in the national/international rules and regulations, especially in the Machine and Equipment Usage
Directive (EU Conformity).
• To ensure correct function, test as dened in the Functional checks of the protective device
section.
• The distance between the sender and receiver must not exceed the maximum distance of 7
meters.
• Access to the hazardous point of the pinsetter must only be possible through the protective
elds.
• It must not be possible to climb over, creep underneath or pass around the protective devices.
• Make sure that the operating personnel of the pinsetters protected by the GS-X Pinsetter Power
Controller system are correctly instructed by specialist personnel before being allowed to
operate the pinsetters. Instructing the operating personnel is the responsibility of the machine
owner.
Functional Checks of the Protective Devices
The effectiveness of the protective devices must be checked daily, or before work is commenced, by a
specialist or by authorized personnel.
Prior to each test verify on the safety evaluation device UE 401 that the green LED illuminates. If this
is not the case, make sure that this condition is reached. The tests are otherwise meaningless.
1. Completely cover each light beam with a test piece that is not transparent (at least 30 mm
diameter) at the following positions:
• Directly in front of the sender.
• In the middle between sender and receiver.
• Directly in front of the receiver.
2. Open the rear pinsetter access door with the interlock switch.
3. Open the masking unit interlock switch.
4. Press the emergency stop switch.

Section Rev. February 2017 Safety Section 7
Each of these individual tests must produce the following result:
• During the light beam test, the receiver for the related safety photoelectric safety switch must
have no LED illuminated.
• On the safety evaluation device UE 401, only the red LED must illuminate.
• As long as the light beam, interlock or emergency stop switch is interrupted, it must not be
possible to initiate the dangerous state of the machine.
No further operation of the pinsetter is allowed if the green or yellow LED on the safety evaluation
device UE 401 illuminates during the test, even if the green or yellow LED illuminates only for a short
period. In this case, the installation of the GS-X Pinsetter Power Controller system must be checked by
specialized personnel.
The proper functioning of the interlock devices must be checked weekly, by a specialist or by authorized
personnel.
Prior to the tests, turn off and lockout the main power switch on the GS-X Pinsetter Power Controller
system.
a. Unplug the rear door interlock cable from the GS-X Pinsetter Power Controller box and verify
that when the interlock switch is closed (rear door closed) there is continuity from pin 1 to 2
and from pin 3 to 4 of the connector. Then verify that when the interlock switch is opened (rear
door opened) there is no continuity from pin 1 to 2 and from pin 3 to 4 of the connector. This
should be done with a multi-meter.
b. Unplug the masking unit interlock cable from the GS-X Pinsetter Power Controller box and
verify that when the interlock switch is actuated (masking unit down) there is continuity from
pin 1 to 2 and from pin 3 to 4 of the connector. Then verify that when the interlock switch
is opened (masking unit up) there is no continuity from pin 1 to 2 and from pin 3 to 4 of the
connector. This should be done with a multi-meter.
c. With the emergency stop switch on the GS-X Pinsetter Power Controller box in the non-
pressed position, verify that there is continuity between the two orange wires on the switch and
continuity between the two brown wires on the switch. Then with the emergency stop switch
on the GS-X Pinsetter Power Controller box in the pressed position, verify that there is no
continuity between the two orange wires on the switch and no continuity between the two
brown wires on the switch. This should be done with a multi-meter between the two
brown wires on the switch. This should be done with a multi-meter.

8 Safety Section Section Rev. February 2017
Care and Maintenance
The lenses for the sensors must be cleaned regularly or if dirty. Avoid scratching the lenses and the
formation of droplets on the lenses as these could change the optical properties.
• Do not use aggressive cleaning agents.
• Do not use abrasive cleaning agents.
Static charges cause dust particles to be attracted to the lens. You can prevent this effect by using the
antistatic plastic cleaner (SICK Part No. 5 600 006) and the SICK lens cloth (Part No. 4 003 353).
How to clean the lens:
• Use a clean and soft brush to remove dust from the lens.
• Then wipe the lens with a clean and damp cloth.
After cleaning, check the position of sender and receiver to make sure that it is not possible to climb
over, creep below or stand behind the protective device.

Section Rev. February 2017 Safety Section 9
SAFETY GUIDELINES FOR GS-SERIES PINSETTERS
As with all machinery, a certain amount of risk is involved in working on the GS-Series Pinsetter.
However, if the necessary care, knowledge and responsibility are exercised, damage to the pinsetter and
accidents involving people can be avoided. The following steps should be taken:
1. ONLY PROPERLY TRAINED PEOPLE ARE QUALIFIED TO WORK ON OR OPERATE
THE PINSETTER.
2. Never operate the pinsetter without ALL factory supplied guarding in place.
3. Never operate the pinsetter if a guard or safety device is damaged or improperly tted to the
machine.
4. Never bypass, disable, or tamper with the safety interlocks or pinsetter function switches.
5. Never attempt to climb over or around any mechanical barrier or machine guard.
6. Reinstall all the machine guards and the ladder after any troubleshooting or maintenance work
has been done on the pinsetter(s) or ball accelerator.
7. Always face toward the machine when using the ladder to climb onto or off the machine. Only
one person should be on the ladder at any time.
8. Suitable clothing must be worn (for example: rubber-soled shoes). Do not wear loose clothing
such as neckties or smocks that could get caught in moving parts. Remove rings, watches,
earrings, bracelets and other jewelry to avoid injury.
9. Care should be taken while near the front of the machine. Accidentally blocking the photocell
beam will cause the pinsetter to cycle.
10. Always turn the pinsetter off before working on the machine. Use the rear mechanic’s switch
mounted on the pin elevator or toggle the stop/run switch on the Nexgen box to the stop
position.
11. If more than one person is working on a machine or if a stop/run switch will be out of reach
while working on the machine, turn off both stop/run switches to prevent a person from turning
on the pinsetter before the other person says he/she is clear of the pinsetter.
12. When working on both machines of a lane pair or components that are common to both
machines (for example: an electronic control box or ball accelerator) power must be turned off
at the Nexgen box or Power Safety Controller and the input power cable must be removed from
the box. In addition the main power switch on the Nexgen or Safety Controller must be locked
into the off position using a suitable locking mechanism.
13. The sweep boards for the lane pair must be dropped to the guarding position when working on
the pinsetter or the ball accelerator to prevent a bowling ball from entering the pinsetter.
14. Prior to performing service work underneath the setting table, place a jack stand or other
suitable support under the center of the table.

10 Safety Section Section Rev. February 2017
15. Fire extinguishers must be on hand and maintained properly. Keep oily rags and other
combustibles in approved re proof containers.
16. If more than one person is working on a machine, be sure the other person is CLEAR before
restarting the machine.
17. When working in the pinsetter area while machines are in operation, ear protection should
be worn. Sound levels greater than 83db can be experienced within 1.6 meters of operating
machines.
18. Never remove the V-belt from the setting table motor without rst lowering the table to the new
pin setting position (pindeck).
19. Never work on or around the pinsetter while under the inuence of alcohol, drugs, or any other
substance that can impair your physical abilities or mental judgment.
20. Always use the correct tools for the job.
21. The GS-Series pinsetter is designed for use as a 10 pin bowling machine. Do not use the
machine or any of its subassemblies for any other purpose.
22. Poisonous or toxic cleaners must not be used. Always check the material safety data sheets
before using new cleaners.
23. Always use factory approved parts when repairing the pinsetter. Using substandard parts may
pose a safety risk.
24. Always make sure that a bowler is not positioned to throw a ball before putting yourself
between the bowler and the machine. It is good practice to have another employee positioned
near any bowler to ensure they cannot throw a ball and/or place a sign on the approach to
indicate the lane is not available for bowling.

Section Rev. February 2017 Safety Section 11
MACHINE GUARDS
The GS Pinsetter is equipped with guards and safety interlocks to prevent injury and to limit access
to moving parts of the pinsetter. A Safety Controller disconnects power to the pinsetters on a lane pair
whenever an interlock is activated. Refer to gure titled Advanced(CE)GuardPackages.
Advanced(CE)GuardPackages
(1) SAFETY POWER CONTROLLER (2) MECHANIC’S REMOTE DISPLAY (3) ELEVATOR GUARD
(4) BACK OF MACHINE (5) REAR DOOR (6) DOOR INTERLOCK SWITCH
(7) FRONT OF MACHINE (8) END GUARD (9) MACHINE ACCESS POINT
(10) PLATFORM GUARDS (11) SAFETY PHOTO SENSORS (12) MASKING UNIT INTERLOCK
SWITCH
(13) NEXGEN CONTROLLER W/O DISPLAY (14) FOLDING PLATFORM

12 Safety Section Section Rev. February 2017
Folding Platform
The front of each pinsetter is equipped with a folding platform. When deployed, the platform provides
access to the front part of the pinsetter. From the deployment position, the platform can open to allow
safe entry to the pindeck area of the machine. An integrated ball stop prevent balls from entering the
pinsetter when the platform is deployed. Refer to gure titled FoldingPlatform.
FoldingPlatform
(1) READY TO BOWL (2) DEPLOYED PLATFORM (3) OPENED FOR PINDECK ACCESS
(4) BALL STOP (5) PINDECK

Section Rev. February 2017 Safety Section 13
GS Safetty Mirror
Safety Mirror

14 Safety Section Section Rev. February 2017
Safety Power Controller
The Safety Power Controller is installed with pinsetters equipped with the advanced guarding package.
The controller interfaces the masking unit and rear door interlock switches and the safety photo sensor
and in turn controls the 3 phase power to the Nexgen box.
(9)
3 PHASE
POWER IN
(13)
CONTROL
MODULE
(11)
CONTACTORS
(10)
POWER OUT
TO NEXGEN
(12)
POWER
SUPPLY
(2)
RESTART
BUTTON
(3)
EMERGENCY STOP
BUTTON
(7)
FUSE
(8)
MAIN
POWER
SWITCH
(6)
RESTART PHOTOSENSORS
LED (GREEN)
(5)
READY FOR RESTART
LED (YELLOW)
(4)
POWER ON
LED (RED)
(14)
FRONT
PHOTOSENSOR
RESTART
(15)
DOOR
INTERLOCK
(16)
MASKING UNIT
INTERLOCK
(17)
SEND
PHOTOSENSOR
(18)
RECEIVE
PHOTOSENSOR
BOTTOM VIEW
(1)
HOLD TO RUN
ACCESS HOLE
Safety Power Controller
(1) Hold To Run Access Hole - Location to mount the optional Hold-To-Run Switch.
(2) Restart Switch - Button used to restart the Safety Controller, as indicated by the yellow restart
LED, after a power failure or interruption of power caused by activating an interlock sensor.
(3) Emergency Stop Switch - Push this button to immediately remove power from the Nexgen box
and shut down power to both pinsetters of the lane pair.
(4) Power On LED (Red) - This LED Turns “On” when the Safety Controller power contactors
are energized to provide power to the Nexgen.
(5) Ready For Restart LED (Yellow) - This LED Turns “On” when all interlock switches and
sensors are in the ready to operate position and the Safety Controller is ready for a restart. Refer
to (2) RestartSwitch.
(6) Restart Photo Sensors LED (Green) - This LED Turns “On” when the photosensor beam at
the masking unit has been interrupted. Once the cause of the interruption has been determined,
press the Photosensor Restart button to reset the photosensor circuit

Section Rev. February 2017 Safety Section 15
(7) Fuse - .25A slow blow fuse used to protect power going to the power supply module.
(8) Main Power Switch - Controls the 3-phase power Nexgen. In the off position, this switch will
disconnect power to the Nexgen box and disable both pinsetters and the ball accelerator.
(9) 3 Phase Power In - Input power connection for the 3-phase power. This voltage can be 208,
230 or 380 - 415 VAC.
(10) Power Out to Nexgen - Power conection for 3-phase power to the Nexgen box.
(11) Contactors - Power contactors used to disconnect 3-phase power whenever the emergency off
switch is pressed or an interlock switch/sensor is tripped
(12) Power Supply - DC power supply for the photo sensor controller and the photo sensor receiver
and transmitter.
(13) Controller - The module that monitors the photo sensor receiver and transmitter and the
interlock switches. The display on the controller provides information as to the status of the
module and the interlock switches and photo sensors.
(14) Front Photosensor Restart - Connection for the photosensor restart button. The button is
typically located on the back of the odd lane pinsetter, under the nexgen display, but may be
mounted at the front of the pinsetters on the making unit frame.
(15) Door Interlock - Connection rear door interlock switches.
(16) Masking Unit Interlock - Connection for the masking unit interlock switch.
(17) Send Photo Sensor - Connection for the safety photo sensor transmitter unit located at the front
of the pinsetters.
(18) Receive Photo Sensor - Connection for the photosensor receiving unit located at the front of
the pinsetters.

16 Safety Section Section Rev. February 2017
Pinsetter Power-up Procedure - Safety Controller
1. Verify that the photosensors are aligned with no obstructions, the masking unit and ball
return door interlocks switches are closed and the emergency stop switch on the safety
controller in not activated (Twist the E-stop button to deactivate). Turn main power switch to
the “On”
position.
- The safety controller will start an initial power up diagnostics to verify conditions.
- The green “Restart Photosensor” LED will illuminate.
2. Press the photosensor restart button to activate the photosensor located on the masking unit.
- The green LED will go off and the yellow “Ready for Restart” LED will illuminate.
3. Press the blue “Restart” button located on the GS-X Safety Controller box to activate the
interlock switches.
- The yellow LED will go off and the red “Power On” LED will illuminate.
- Power will be supplied to the GS-X Nexgen.
VERIFY ALL INTERLOCKS
AND SENSORS ARE IN
THEIR PROPER POSITION
TURN THE MAIN POWER
SWITCH ON
(GREEN LED ON)
PRESS PHOTO SENSOR
RESTART BUTTON
(YELLOW LED ON)
PRESS RESTART BUTTON
ON CONTROLLER
(RED LED ON)
REMOVE THE SOURCE
OF THE SENSOR
OBSTRUCTION
PRESS PHOTO SENSOR
RESTART BUTTON
(YELLOW LED ON)
PRESS RESTART BUTTON
ON CONTROLLER
(RED LED ON)
VERIFY ALL INTERLOCKS
ARE IN THEIR PROPER POSITION
(YELLOW LED ON)
PRESS RESTART BUTTON
ON CONTROLLER
(RED LED ON)
Pinsetter Restart Procedure - Safety Controller
The photo sensor has been obstructed (Green, “Restart Photosensor” LED, “ON”)
1. Remove obstruction from photosensors.
2. Press the photosensor restart button to re-activate the photosensors.
3. Press the blue “Restart” button located on the GS-X Safety Controller box.
REMOVE THE SOURCE
OF THE SENSOR
OBSTRUCTION
PRESS PHOTO SENSOR
RESTART BUTTON
(YELLOW LED ON)
PRESS RESTART BUTTON
ON CONTROLLER
(RED LED ON)
The Ball Return Interlock or Masking Unit Interlock is triggered.
1. Return the masking unit and/or the ball return access door to the “closed” position.
2. Press the blue “Restart” button located on the GS-X Safety Controller box to re-activate the
interlock switches.
VERIFY ALL INTERLOCKS
ARE IN THEIR PROPER POSITION
(YELLOW LED ON)
PRESS RESTART BUTTON
ON CONTROLLER
(RED LED ON)

Section Rev. February 2017 Safety Section 17
PINSETTER STATUS LIGHT / MACHINE POWER ON SEQUENCE
The red light located on top of the elevator provides the operator with valuable information concerning
the state of the machine. The meaning of the light depends on what software version in installed on the
Nexgen box’s CPU PCB.
NOTE:Thelight’sfunctionisselectableinNexgenboxeswithrmwareversion4.95.21orhigher.
Software Version 4.9.08 and prior
Slow-ashing red light indicates an
error has occurred. The pinsetter
needs attention. Turn machine off and
lock out power before servicing.
No light indicates the pinsetter may be
READY TO RUN. A signal from a
remote location will cause the pinsetter
to start WITHOUT WARNING. Stay
clear of machine. Turn off the
Stop/Run switch before servicing.
Software Version 4.9.09 and later
Rapid-ashing red light indicates the
pinsetter is GETTING READY TO
RUN. Stay clear of machine & keep
guards in place.
Slow-ashing red light indicates an
error has occurred.
The pinsetter needs attention. Turn
machine off and lock out power before
servicing.
Solid red light indicates the pinsetter is
READY TO RUN. A signal from a
remote location will cause the pinsetter
to start WITHOUT WARNING. Stay
clear of machine. Keep guards in place.
No light indicates the pinsetter is off.
Safe to Service. Lock out power
before servicing.

18 Safety Section Section Rev. February 2017
PINSETTER ACCESS POINTS
It may become necessary to enter the pinsetter to perform maintenance tasks or correct a problem with
the machine. If entering the pinsetter is needed, only enter using the locations as shown in the gure
titled PinsetterAccessPoints.
CAUTION: Only use the access points as recommended. With pinsetters
equipped with Safety Controllers, these access points are protected with
interlock switches and/or photo sensors that will automatically disconnect
power to both pinsetters on the lane pair. Do not attempt to bypass, disable or
tamper with these interlocks.
Pinsetter Access Points
(1) ACCESS DOORS (2) BACK OF MACHINE (3) PLATFORM
(4) FRONT ACCESS
Table of contents
Other Brunswick Video Gaming Accessories manuals
Popular Video Gaming Accessories manuals by other brands
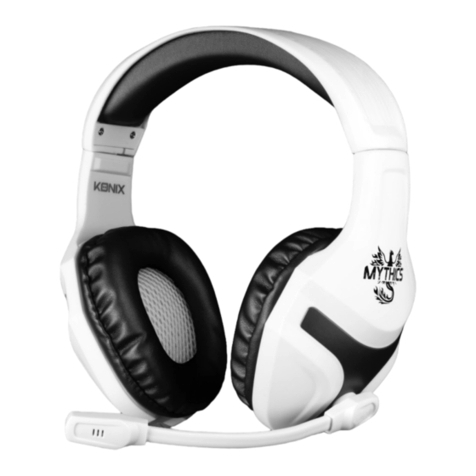
Konix
Konix MYTHICS GAMER PACK user manual
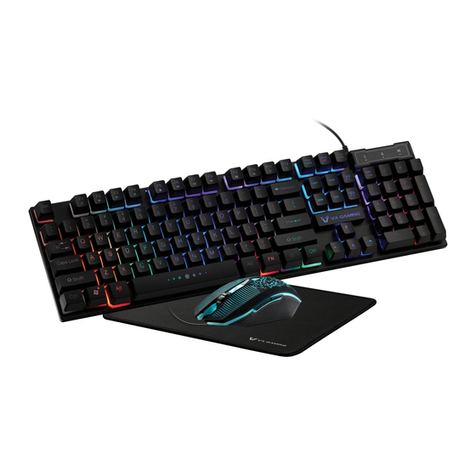
volkano
volkano VX Gaming Artemis Series instruction manual
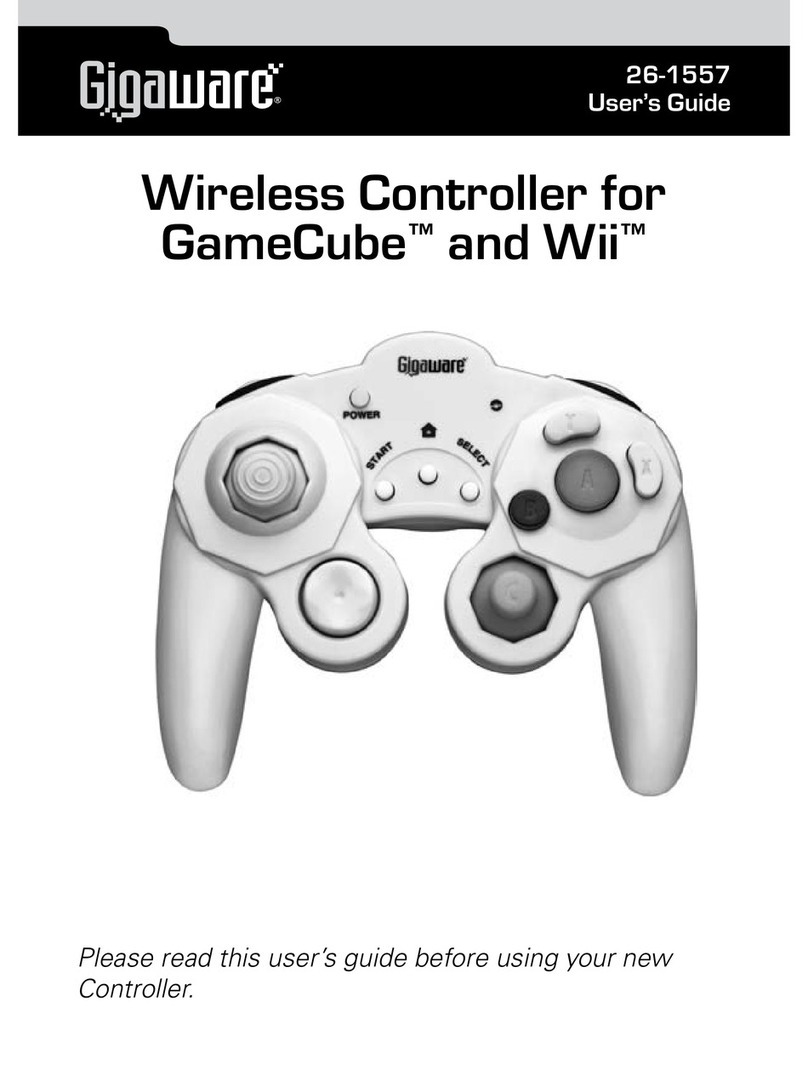
Gigaware
Gigaware 26-1557 user guide
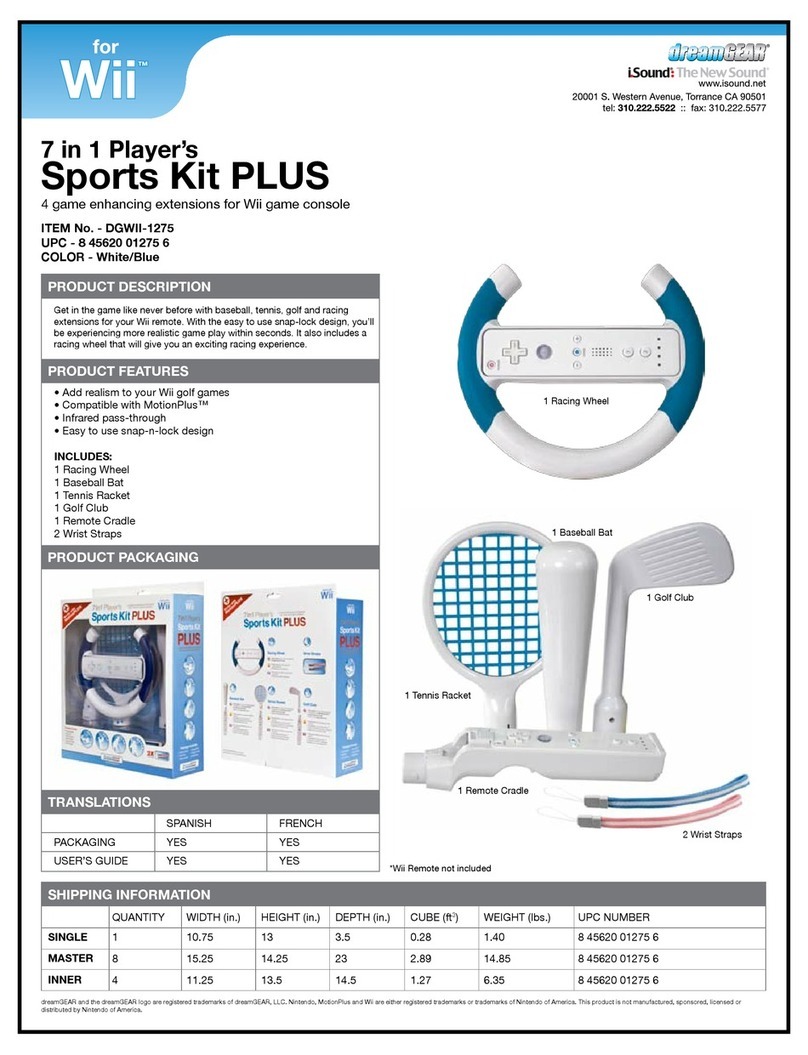
DreamGEAR
DreamGEAR DGWII-1275 user guide
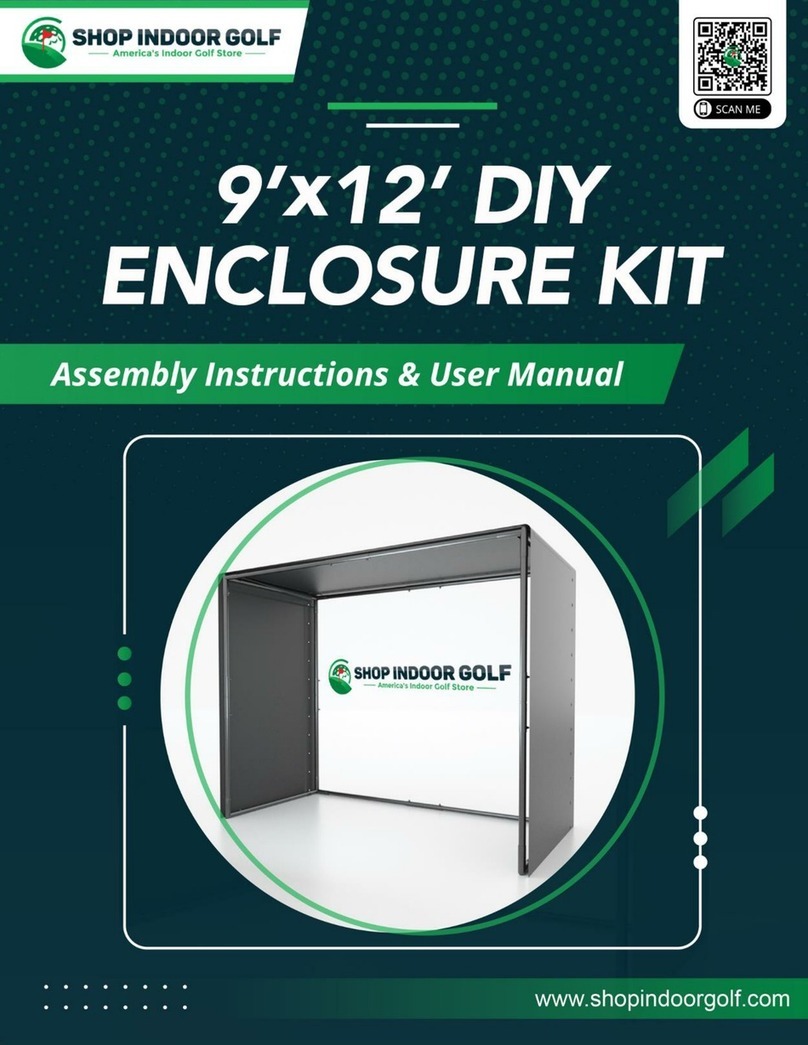
SHOP INDOOR GOLF
SHOP INDOOR GOLF DIY Golf Simulator Enclosure Assembly instructions & user manual
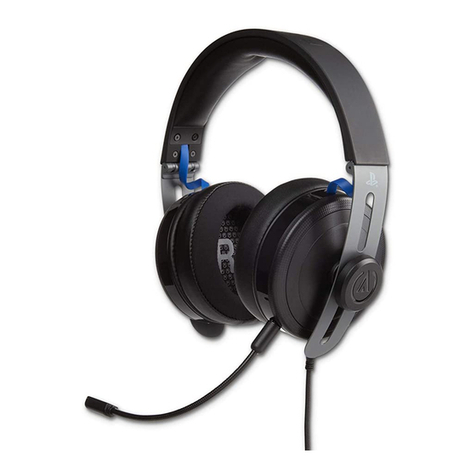
Power A
Power A Fusion Pro Wireless Controller user manual