Bug-O Systems AVC-2060 Technical reference manual

INSTRUCTIONS
AND
PARTS MANUAL
A DIVISION OF WELD TOOLING CORPORATION
280 TECHNOLOGY DRIVE CANONSBURG, PENNSYLVANIA 15317-9564 USA
PHONE: 412-331-1776 http://www.bugo.com FAX: 412- 331- 0383
PLASMA HEIGHT
CONTROL
AVC-2060
for WPD-2100 Pendulum Weaver
Please record your equipment identication information below for future reference. This information can be
found on your machine nameplate.
Model Number
Serial Number
Date of Purchase
Whenever you request replacement parts or information on this equipment, always supply the information
you have recorded above.
LIT-AVC-2060-IPM-1120
Bug-O Systems is committed to empowering our customers by providing operator
controlled mechanized solutions for their welding, cutting and custom applications.

2
SAFETY
PROTECT YOURSELF AND OTHERS FROM SERIOUS INJURY OR DEATH.
KEEP CHILDREN AWAY. BE SURE THAT ALL INSTALLATION, OPERATION,
MAINTENANCE AND REPAIR PROCEDURES ARE PERFORMED ONLY BY
QUALIFIED INDIVIDUALS.
EQUIPMENT DAMAGE
POSSIBLE.
ELECTRIC SHOCK can kill.
1) The equipment is not waterproof. Using
the unit in a wet environment may result
in serious injury. Do not touch equipment
when wet or standing in a wet location.
2) The unused connectors have power on
them. Always keep the unused connec-
tors covered with the supplied protective
panels. Operation of the machine without
the protective panels may result in injury.
3) Never open the equipment without rst
unplugging the power cord or serious
injury may result.
4) Verify the customer-supplied power
connections are made in accordance
with all applicable local and national
electrical safety codes. If none exist,
use International Electric Code (IEC)
950.
5) Never remove or bypass the equipment
power cord ground. Verify the equipment
is grounded in accordance with all appli-
cable local and national electrical safety
codes. If none exist, use International
Electric Code (IEC) 950.
READ INSTRUCTIONS.
Read the instruction manual
before installing and using the
equipment.
1) Do not plug in the power cord without rst
verifying the equipment is OFF and the
cord input voltage is the same as required
by the machine or serious damage may
result.
2) Always verity both the pinion and wheels
are fully engaged before applying power
or equipment damage may occur.
3) Do not leave the equipment unattended.
4) Remove from the worksite and store in
a safe location when not in use.
1) Never try to stop the pinion from moving
except by removing power or by using the
STOP control.
2) Do not remove any protective panels,
covers or guards and operate equipment.
MOVING PARTS can
cause serious injury.
FALLING EQUIPMENT
can cause serious
personal injury and
equipment damage.
Faulty or careless user installation is
possible. As a result, never stand or
walk underneath equipment.

3
PRECAUTIONS:
1) Some plasma or welding cables are strong sources of high frequency interference.
NEVER lay a plasma or welding cable across the controls of the machine.
2) Always physically separate the plasma or welding cable leads from the machine
cables. For example, the plasma or welding cable leads should NEVER be bundled
with a pendant cable or the machine power cord. Maximize the separation between
any machine cables and the plasma or welding cables.
3) Strictly follow the grounding procedures specied for the plasma or welding unit.
NOTE: Some plasma and welding units produce exceptionally large amounts of high
frequency noise. They may require a grounding rod be driven into the earth within six
feet (2 meters) of the plasma or welding unit to become compatible with an automatic
cutting or welding process.
4) If the high frequency is produced using a spark gap, adjust the points so the gap is as
small as possible. The larger the gap, the higher the voltage and the higher the inter-
ference.
5) Some plasma or welding units will inject high frequency interference into the AC
power line. Use separate power line branches whenever possible to power the
plasma or welding source and the machine. Do not plug them into the same outlet
box.
6) High frequency noise may enter the machine through the plasma or welding supply
remote contactor leads. Some plasma and welding sources can produce noise spikes
of up to several thousand volts. These sources are not compatible with automated
cutting and welding equipment. It is recommended that the remote contactor leads on
these plasma or welding sources not be connected to the machine. An alternate
solution is to purchase a separate remote contactor isolation box.
HIGH FREQUENCY WARNINGS
WARNING: HIGH FREQUENCY CAN EFFECT MACHINE
OPERATION AND THEREFORE, WELD QUALITY.
SPECIAL PRECAUTIONS ARE REQUIRED WHEN USING PLASMA,
TIG OR ANY WELDING PROCESS THAT USES HIGH FREQUENCY
TO STRIKE AN ARC.
Read the precautions below before installing and using the equipment.

4
TABLE OF CONTENTS
PLASMA HEIGHT CONTROL
INSTRUCTIONS AND PARTS MANUAL
5 ......... Introduction
5 ......... Specications
5 ......... Items Supplied
6 ......... Sensor Options for Plasma Power Sources
6-9 ........ Setup
10 ........ AVC-2060 Plasma Height Control / Exploded View / Parts List
11 ........ AVC-2051-10 MDS AHC 10' (3.0 m) Remote Control
12 ........ CAS-1500-18 Height Slide Assembly / Exploded View / Parts List
13 ........ AVC-1550-PL-ID Volt Sensor Assembly, Internal Divider Model / Exploded View / Parts List
14 ........ AVC-1550-PL-RV Volt Sensor Assembly, Raw Voltage Model / Exploded View / Parts List
15 ........ AVC-1550-PL-PS Volt Sensor Assembly, Power Source Model / Exploded View / Parts List
16 ........ AVC-2055 Control Box / Exploded View
17 ........ AVC-2055 Control Box / Parts List
18 ........ AVC-2050-PL-ID Connection Diagram
19 ........ AVC-2050-PL-RV Connection Diagram
20 ........ AVC-2050-PL-PS Connection Diagram
21 ........ AVC-2055-WD Control Box / Wiring Diagram / Parts List
22 ........ AVC-1002-WD Wiring Diagram
23 ........ CAS-2058 MDS AHC Wiring Harness / Wiring Diagram / Parts List
24 ........ AVC-2051-10-WD MDS AHC 10' (3.0 M) Remote Control / Wiring Diagram / Parts List
25 ........ Troubleshooting
26 ........ Warranty
PAGES
AVC-2060
FOR WPD-2100 PENDULUM WEAVER

5
INTRODUCTION
The AVC-2060 is an Plasma Height Control (PHC) for the Pendulum Weaver (WPD-2100) that controls
the tip to work distance and maintains a constant voltage, which provides a more uniform result.
Available in three models, by voltage. Plasma Height Control senses the actual voltage, compares
this value to the set point, and raises or lowers the torch accordingly. It features motion based on the
plasma source “ok to move” signal and automatically shuts off when voltage drops too low (generally
below 36 volts).
The AVC-2060 Plasma Height Control is available as original equipment or as a retrot unit designed
to provide automated height control on the BUG-O Modular Drive Systems (MDS) with a Pendulum
Weaver (WPD-2100). Height Slide Assembly (CAS-1500) replaces the welding clamp originally
supplied on the Pendulum Weaver.
SPECIFICATIONS
Net Weight: 14.5 lbs (6.6 kg)
Travel: 13" (330 mm)
Carrying Capacity: 10 lbs (4.5 kg)
Operating Range: 36 to 300 Volts
Minimum Recommended Standoff: 1/8" (3.2 mm)
ITEMS SUPPLIED
AVC-2060 Plasma Height Control for WPD-1200 Linear Weaver includes:
CAS-1500-18 Height Slide Assembly
CAS-1558 Pendulum Weaver Adaptor for CAS-1500-18
AVC-1550-PL-?? Hall Effect Current Sensor Assembly
AVC-2051-10 MDS AHC 10' (3.0 m) Remote Control
AVC-2055 MDS AHC Control Box
“??” is the volt sensor option:
ID for use with Internal Divider
RV for use with Raw Voltage of blowback start type sources
PS for installation inside the Power Source for HF or capacitive discharge type sources
Sensitivity
Difference between DC cutting voltage and set point (ΔV)
ΔV > 32 32 > ΔV > 15 15 > ΔV > 3 3 > ΔV > 0.4 0.4 > ΔV
Nominal
Maximum
Slide Speed
24 in/min
(609 mm/min)
24 in/min
(609 mm/min)
1.55 in/min
per volt
(39.3 mm/min
per volt)
0.46 in/min
per volt
(11.8 mm/min
per volt)
slide may
not move
Nominal Time
to Reach 90%
Speed
0.2 seconds 0.2 - 2 seconds 2 seconds 2 seconds slide may
not move

6
SETUP
AVC-2060 Plasma Height Control
This is available as original equipment or as a retrot unit designed to provide Plasma Height Control
on BUG-O Modular Drive Systems (MDS) with the Pendulum Weaver (WPD-2100).
CAS-1500-18 Height Slide Assembly
This replaces the Gun Mounting Group originally supplied on the Pendulum Weaver. To install, begin
by remove the WPD-2050 Gun Mounting Group from the weaver, [Refer to Modular Drive System
Instructions and Parts Manual]. Install Pendulum Weaver Adapter CAS-1558. Slide clamp on bottom of
Height Slide Assembly CAS-1500-18 onto the CAS-1558 and lock in position.
CAS-1558 Pendulum Weaver Adaptor
SENSOR OPTIONS FOR PLASMA POWER SOURCES
Manufacturer Model
AVC
Sensor
Option
AVC
On/Auto
Switch
Position
Additional Connection Instructions
ESAB®1 Cutmaster 82 with full-
featured automation
interface PCB option
-ID Auto Contactor wires plug into AVC-1550, which
sends them to the plasma source.
Hypertherm®2 Powermax45 XP® with
CPC port and voltage
divider
-ID Auto Contactor wires plug into AVC-1550, which
sends them to the plasma source.
Hypertherm®Powermax65® with
CPC port and voltage
divider
-ID Auto Contactor wires plug into AVC-1550, which
sends them to the plasma source.
Hypertherm®Powermax85® with
CPC port and voltage
divider
-ID Auto Contactor wires plug into AVC-1550, which
sends them to the plasma source.
Hypertherm®Powermax105® with
CPC port and voltage
divider
-ID Auto Contactor wires plug into AVC-1550, which
sends them to the plasma source.
Hypertherm®Powermax125® with
CPC port and voltage
divider
-ID Auto Contactor wires plug into AVC-1550, which
sends them to the plasma source.
Hypertherm®Powermax1650®-RV Auto AVC-1002 will need to be installed and will
need to connect to J15 and J16. Contactor
wires will need to be connected to the AVC-
1550 and then AVC-1003 (sold separately) can
connect the AVC-1550 to the machine inter-
face connection for arc start and arc transfer.
Lincoln
Electric®3
Tomahawk1538®-RV On AVC-1002 will need to be installed and will
need to connect to the EL2 and OUT1. Con-
tactor wires will need to connect to the Toma-
hawk’s accessory connector. A competent
person must determine how to best make
these connections.

7
AVC-2055 MDS AHC Control Box
This mounts directly on top of the MDS Drive. Align the socket on the top of the MDS Drive with the
plug on the bottom of the AHC Control Box and seat it rmly and secure in place with the four (4)
screws, one (1) in each corner.
AVC-2051-10 MDS AHC 10' (3.0 m) Remote Control
To install, align the plug in the bottom of the male portion of this Remote Control with the socket on
top of the AVC-2055. Seat this plug rmly and secure in place with the four (4) screws, one (1) in each
corner.
Position and Clamp Torch
With CAS-1500-18 installed on the Linear Weaver Cross Arm, secure the torch in the clamp located on
the end of the Height Slide Assembly. Arrange cables so that they do not interfere with the movement of
the machine before securing the cable in the cable anchor.
Connect Control Cables
Connect weld contact outlet pins A&B, on the MPD-1000 Drive unit to the power source contact circuit.
If using -ID sensor, use the provided cable to connect to the volt sensor.
Install Voltage Sensor
Connect AVC-1550 type voltage sensor according to the connection diagram on page 15 of this
manual. The connections will vary based on whether you have a type -ID, -RV, or -PS sensor assembly.
Choose whether the AVC-1550 sensor will use “Ok to Move” signal or always provide voltage.
The sensor can switch off its feedback based on a power source’s “Ok to Move” signal. On the AVC-
1550-PL-ID and AVC-1550-PL-RV, this is done with the “Auto/On” switch on the side of the box. In
the “Auto” position, the sensor will automatically switch feedback on or off based on the “Ok to move”
signal; in “On”, it will always provide feedback, although the control still has its own lower limit of about
36V below which it will not respond. On the AVC-1550-PL-PS, which gets installed inside the power
source, this is done with the CAS-1529 wiring harness (shown in the connection diagram for the AVC-
2050-PL-PS); the wires either need to connect to terminals provided by the plasma power source to
use the “Ok to move” signal, or shorted together if no such signal is provided by the power source. This
may have already been done for you if you ordered a system with the sensor installed.
On systems that provide an “Ok to move” signal, it is better to use it, since it will prevent the initial
open-circuit voltage before an arc is transferred from showing up on the feedback signal. If your power
source does not have an “Ok to move” signal, you’ll want to try to get the arc transferred as quickly as
possible to reduce the impact of the open-circuit voltage, and be prepared to use the manual jog switch
to correct movement due to that initial higher voltage.
Installing the AVC-1550-PL-PS (applies to this model only)
If you choose to install the AVC-1550-PL-PS yourself, you can use the connection diagram for AVC-
2050-PL-PS.
The CAS-1530 wiring harness plugs into J1 on the PCB-1273.
CAS-1529 is provided to plug into J3. The “Ok to move” signal drives a 12VDC relay on the PCB-1273.
J3 includes diodes to avoid reverse polarity on the connection. J3 pin 1 is connected to the PCB-1273’s
+15V source through a diode and a 120 Ohm resistor, and pin 2 goes to the relay coil through another
diode; the other end of the relay coil is connected to the Bug-O machine’s common power return, which
is not isolated. This connection method will work for dry contact closure or optical isolators, provided the
polarity is respected (Pin 1 goes to the optical isolator positive terminal or sink and pin 2 to the optical
isolator negative terminal or source).
J2 does not need to be connected.
You will need to identify which contactor cable you need and how to wire it based on the plasma source
you are using. There are pins on J3 to take a trigger input in, but they only route the signal to J2 to go
back out to the power source, so that a single cable can be used between other AVC-1550 models and
the power source.
SETUP, CONT’D.

8
VERIFY SETUP
Before striking an arc, take a moment to verify the machine is set up correctly. With the tractor “ON”
and the Arc “OFF”, run the machine and verify it is moving in the intended direction. Verify torch is in the
proper position as well as the Drive Unit travel speed. Use the Up – Down JOG Toggle Switch on the
Control Box (AVC-2051) to make sure enough vertical travel is available.
SETUP, CONT’D.
Plug in MDS System with AHC
Inspect the power cord before each use. Do not use if damaged. Plug in the machine to a power
outlet of the appropriate voltage.
Power ON the MDS System with AHC
CAUTION: machine may start moving as soon as it is powered “ON.” Use the power switch on the
MPD-1000 Drive Unit to turn the power “ON” and “OFF” to the machine. For operator safety, set weld
pattern to “NO WEAVE” and the Drive Unit to “OFF” before turning on the machine.
Position the Torch
Proper setup of the torch is critical to a successful operation. In addition to manually positioning the
torch within the clamp, the torch must also be properly set with respect to three mechanical controls:
The Torch Mounting Group, the Plasma Height Controller (PHC), and the motion control position.
Pendulum Mechanism: The pendulum mechanism offers a weave amplitude that varies with distance
to work piece. Center the pendulum motion before placing the torch over the
work area.
Height Slide Assembly: A clamp, CAS-1510 Dual Position Clamp Block is provided mounted to the
bottom of the Height Slide Assembly. This Clamp Block requires a 7/8" (22.2
mm) diameter rod for mounting. Typically, user will mount the Height Slide
Assembly to the welding group already on the BUG-O. Consult with your
Local Bug-O distributor or the factory for assistance if you require help with
mounting the control box.
Tractor Position: Use the tractor Carriage Travel Switch to position the Drive Unit so the torch
is over its starting point. The operator can increase or decrease the tractor
travel speed at any time using the speed control on the MDS Control Module.
Set Motion Parameters
Use the Weaver Control Module (MDS-1005) to set the motion parameters.
[Refer to Modular Drive System Instructions and Parts Manual]
The operator can temporarily override Plasma Height Control using the Up – Down JOG Toggle
Switch on the Remote Control (AVC-2051-10) while cutting. Plasma Height Control resumes as soon
as the jog switch is released. To disable the Plasma Height Control, move the Manual – Automatic
Toggle Switch on the Remote Control (AVC-2051-10) to Manual.

9
AVC-2051-10 Remote Control
If using the -RV type sensor, make sure your power source uses a starting method that does not use
high frequency such as blowback start or touch start rather than HF start or capacitive discharge, as
that may cause premature failure, electromagnetic interference, or an unsafe condition. If HF start or
capacitive discharged is used, use the -ID type sensor if your power source has an internal divider, or
the -PS type sensor if it does not.
Up – Down JOG
Toggle Switch
Volt Dial
Manual – Automatic
Toggle Switch
SETUP, CONT’D.
To set your PLASMA HEIGHT CONTROL:
(Reference AVC-2051 Control Box)
y Connect voltage sensor to power source according to sensor wiring instructions.
y Set the height control (Manual - Automatic Toggle Switch) to manual mode.
y Conrm the switch on the height slide faces away from the work piece.
y Set the torch height manually (Up - Down JOG Toggle Switch) to where you want it.
y Make a small cut and record the volt reading from the power source.
y Now, dial this number, volt reading, into the Height Control (Volt Dial).
y Turn the height control (On - Off Toggle Switch) back on.
y Run the system and it should run at the same height and thus voltage.
Alternate Setup:
If you already know what voltage you normally use or have charts specifying a voltage that has worked
well for you in the past that gives you at least 1/8" (3.2 mm) of standoff, you can begin by entering that
voltage on the dial then testing. Adjust the voltage if necessary to account for tolerances in the height
control system.
If this does not work please consult “Trouble Shooting Page” in the back of this manual.
The operator can temporarily override Plasma Height Control using the manual jog switch on AVC-2051
Control Box. PHC resumes as soon as the jog switch is released. To disable the PHC, move the
Manual -- Automatic Toggle Switch on the AVC-2051 Control Box to manual.
Plasma Source, Cutting Torch, and PHC Setup

10
AVC-2060 PLASMA HEIGHT CONTROL / EXPLODED VIEW / PARTS LIST
For use with machine barrel plasma torch: Remove standard torch clamp from
CAS-1500-18, mount clamp block sideways, and install BUG-5188.
ITEM QTY PART NO. DESCRIPTION
1 1 CAS-1500-18 Height Slide Assembly 18"
2 1 CAS-1558 Pendulum Weaver Adaptor for CAS-1500
3 1 AVC-2051-10 MDS AHC 10' (3.0 m) Remote Control
4 1 AVC-2055 MDS AHC Control Box
5 1 BUG-2708 Clamp
6 1 BIG-5188 Torch Holder Assembly
* 1 CAS-1553 Connecting Cable Hall Effect
*Not Shown
1
2
4
3
5
6

11
AVC-2051-10 MDS AHC 10' (3.0 M) REMOTE CONTROL
ITEM QTY PART NO. DESCRIPTION
1 1 AVC-2045-M AVC Pendant, Male End
2 1 BUG-9676 Dial Counter
3 1 CAS-2045-F CAS Pendant, Female End
4 1 CAS-2052 Guard
5 1 CWO-6335 Toggle Switch, DPDT, On-None-On
6 1 FAS-0525 Soc Hd Cap 8-32 x 1/2
7 1 MUG-1199 Toggle Switch, DPDT, On-Off-On
8 1 PLT-1001 Man / Auto
9 1 PLT-1002 In / Out
10 1 POT 5483 Potentiometer, 10k 3 Turn
11 1 WRE-3659/50 50 Cond. Round Ribbon Cable
2,10
1 3
11
4,6
5
8
7
9

12
ITEM QTY PART NO. DESCRIPTION
1 1 CAS-1512 Torch Mount Plate
2 1 CAS-1509-18 18" Height Arm Mounting Bar
3 2 CAS-1523 End Cap
4 1 CAS-1505-18 18" Height Arm Assembly
5 2 PWS-1028 Fixed Wheel & Leg Assembly
6 1 CAS-1522 Mounting Plate
7 1 CAS-1511 Steel Pinion
8 2 CAS-1517 CAS Drive Motor Cover Mount Angle
9 2 CAS-1510 Dual Position Clamp Block
10 1 PRS-1025 Motor
11 1 CAS-1518 CAS Drive Motor Cover Panel A
12 1 CAS-1521 CAS Drive Motor Outer Cover
13 1 CAS-1519 CAS Drive Motor Cover Panel B
14 1 BUG-1034 Panel Connector, 4-T, M
15 1 CAS-1503-P Arm Cover
16 2 PWS-1029 Adjustable Wheel & Leg Assembly
17 1 UCW-0261-03-02-00-0 Quick Disconnect Clamp Assembly
18 1 BUG-2708 Clamp
19 4 GOF-3036 QD Female, Fully Insulated
20 2 GOF-3037 QD Male, Fully Insulated
F1 2 MET-0975-SS Flt Hd Soc Scr M6 x 14
F2 8 MET-0553-SS Soc Hd Cap Scr M4 x 10
F3 4 MET-0559-SS Soc Hd Cap Scr M4 x 20
F4 4 MET-0147-SS Pan Hd Phil Scr M3 x 16
F5 8 MET-0542-SS Soc Hd Cap Scr M3 x 8
F6 8 MET-0541-SS Soc Hd Cap Scr M3 x 6
F7 4 FAS-1305 Hex Nut 4-40
F8 4 FAS-1204 But Hd Sk Hd Scr 4-40 x 3/8
F9 4 WAS-0201 #4 Internal Star Lockwasher
* 1 CAS-1557 Control to Slide Cable 3ft
* Not Shown
CAS-1500-18 HEIGHT SLIDE ASSEMBLY / EXPLODED VIEW / PARTS LIST
F6
12
F5
11
13
1
F1
3
2
F7,F9
18
9
F2
15
16
F8
8
F4
710
6
F3
5
4
19
19
20
17
14

13
AVC-1550-PL-ID VOLT SENSOR ASSEMBLY, INTERNAL DIVIDER MODEL /
EXPLODED VIEW / PARTS LIST
ITEM QTY PART NO. DESCRIPTION
1 1 CAS-1525 AVC Voltage Enclosure
2 1 CAS-1526 Sensor Legend Plate
3 1 CAS-1532 AVC Harness Volt To Pwr
4 1 CAS-1531 AVC Harness Volt To Bug CNN
5 1 PLUG-2666 Hole Plug
6 1 PWS-0305 Main Current Sense Harness
7 1 PCB-1273-PL-ID PCB Board
8 1 FAS-0104 4-40 x 3/8 Pan Hd Screw
9 12 FAS-1305 4-40 Hex Nut
10 12 MET-0151-N *Pan Hd Slotted Screw
11 4 WAS-0201 #4 Internal Star Lockwasher
*Do not overtighten
1
2
3
4
5
6
7
8
9
10
11

14
AVC-1550-PL-RV VOLT SENSOR ASSEMBLY, RAW VOLTAGE MODEL /
EXPLODED VIEW / PARTS LIST
ITEM QTY PART NO. DESCRIPTION
1 1 CAS-1525 AVC Voltage Enclosure
2 1 CAS-1526 Sensor Legend Plate
3 1 CAS-1532 AVC Harness Volt To Pwr
4 1 CAS-1531 AVC Harness Volt To Bug CNN
5 1 CRS-1598 Hole Plug
6 1 PWS-0305 Main Current Sense Harness
7 1 CAS-1527 Raw Volt Sense Cable
8 1 PCB-1273-PL-RV PCB Board
9 1 FAS-0104 4-40 x 3/8 Pan Hd Screw
10 12 FAS-1305 4-40 Hex Nut
11 12 MET-0151-N *Pan Hd Slotted Screw
12 4 WAS-0201 #4 Internal Star Lockwasher
*Do not overtighten
1
2
3
4
5
6
7
8
9
10
11
12

15
AVC-1550-PL-PS VOLT SENSOR ASSEMBLY, POWER SOURCE MODEL /
EXPLODED VIEW / PARTS LIST
ITEM QTY PART NO. DESCRIPTION
1 2 CAS-1524 Voltage Sensor Mtg
2 16 STOF-2009 6-32 M/F Nylon
3 4 WAS-0210 #6 SAE Flat Washer
4 4 FAS-0112 Pan Hd Slt 6-32 x 1/4 Black
5 8 WSH 5432 #6 Flat Nylon Washer
6 1 PCB-1273 AVC Volt Sensor
7 4 FAS-1310 Hex Nut 6-32
8 1 CAS-1529 Ok To Move Harness
9 2 CAS-1530 Sense Harness
10 1 CAS-1528 AVC Voltage Leads
Note: Do not overtighten fasteners & standoffs
1
2
3
4
5
6
7
8
9
10

16
AVC-2055 CONTROL BOX / EXPLODED VIEW
13
19
12
11 9,10
3
4
5
6
7
8
14
17
17
17
16,24
16
17
17
18
18,19,24
20,23
21
22
18,24
1
2

17
AVC-2055 CONTROL BOX / PARTS LIST
ITEM QTY PART NO. DESCRIPTION
1 1 MDS-1058 Mounting Panel
2 1 MDS-1057 Rear Panel
3 1 PCB-1036 Connector 50-Pin, M
4 1 PCB-1070 MDS AHC Break Out Board
5 1 PCB-1035 Connector 50-Pin, F
6 1 CAS-2056 Front Panel
7 1 MUG-1156 Panel Connector, 4-T, F
8 1 CAS-1780 DC Speed Card w/ 1770 Interface
9 1 BUG-9677 Potentiometer, 10k Ohms
10 1 BUG-5759 Pot Shaft Seal 1/4"
11 1 CAS-2057 CAS-1050-500 Mounting Bracket
12 1 CAS-1060-PL Control Board, Plasma
13 1 BUG-9856 Panel Connector, 2-T, F
14 1 MDS-1044 Knob for Pot
*15 1 BUG-2005 Bug-O Label
16 4 FAS-0905 Flt Hd Soc Scr #4-40 x 1/2"
17 12 FAS-0114 Pan Hd Scr 6-32 x 3/8 Black
18 10 FAS-1305 Hex Nut 4-40
19 8 FAS-0204 Rnd Hd Slt Scr 4-40 x 3/8 Zinc
20 2 WAS-0221 #8 Internal Star Lock Washer
21 4 MET-0943 Flt Hd Soc M3 x 10
22 2 FAS-0914 #6-32 x 3/8" Flt Hd Socket
23 4 FAS-0722 Fil Hd Scr 8-32 x 1/4
24 12 WAS-0201 #4 Internal Star Lock Washer
* Not Shown

18
AVC-2050-PL-ID CONNECTION DIAGRAM

19
AVC-2050-PL-RV CONNECTION DIAGRAM

20
AVC-2050-PL-PS CONNECTION DIAGRAM
Table of contents
Other Bug-O Systems Welding System manuals
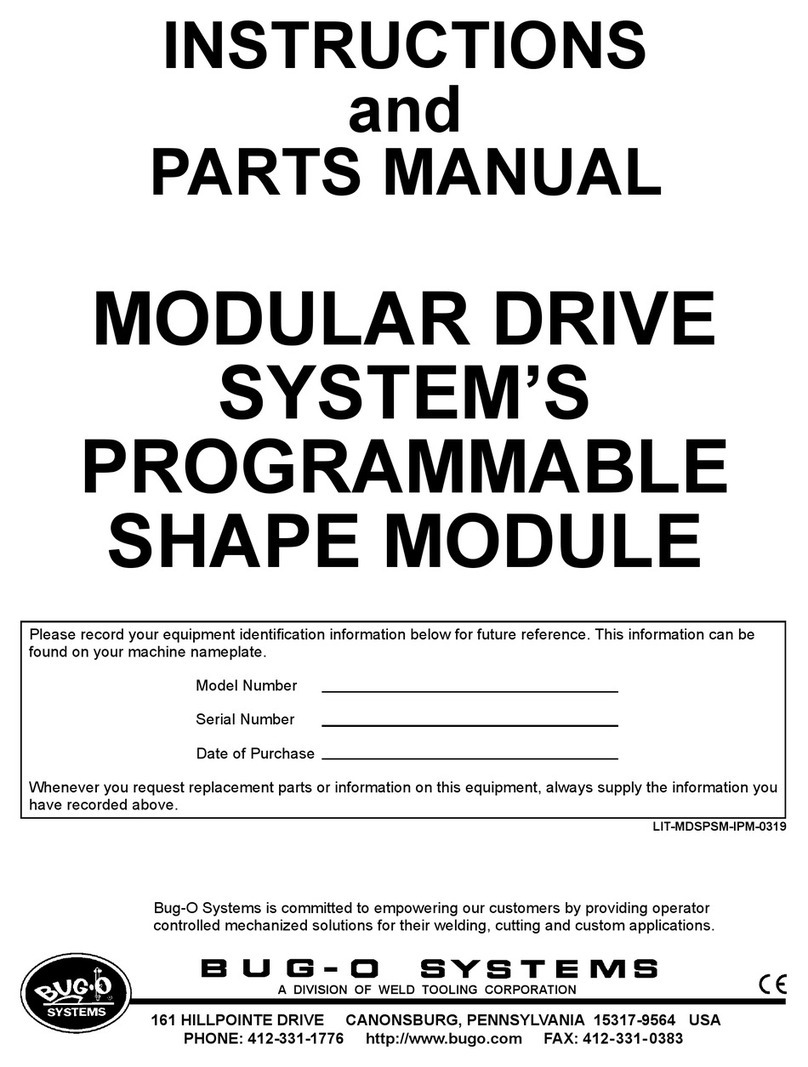
Bug-O Systems
Bug-O Systems MDS Series Technical reference manual
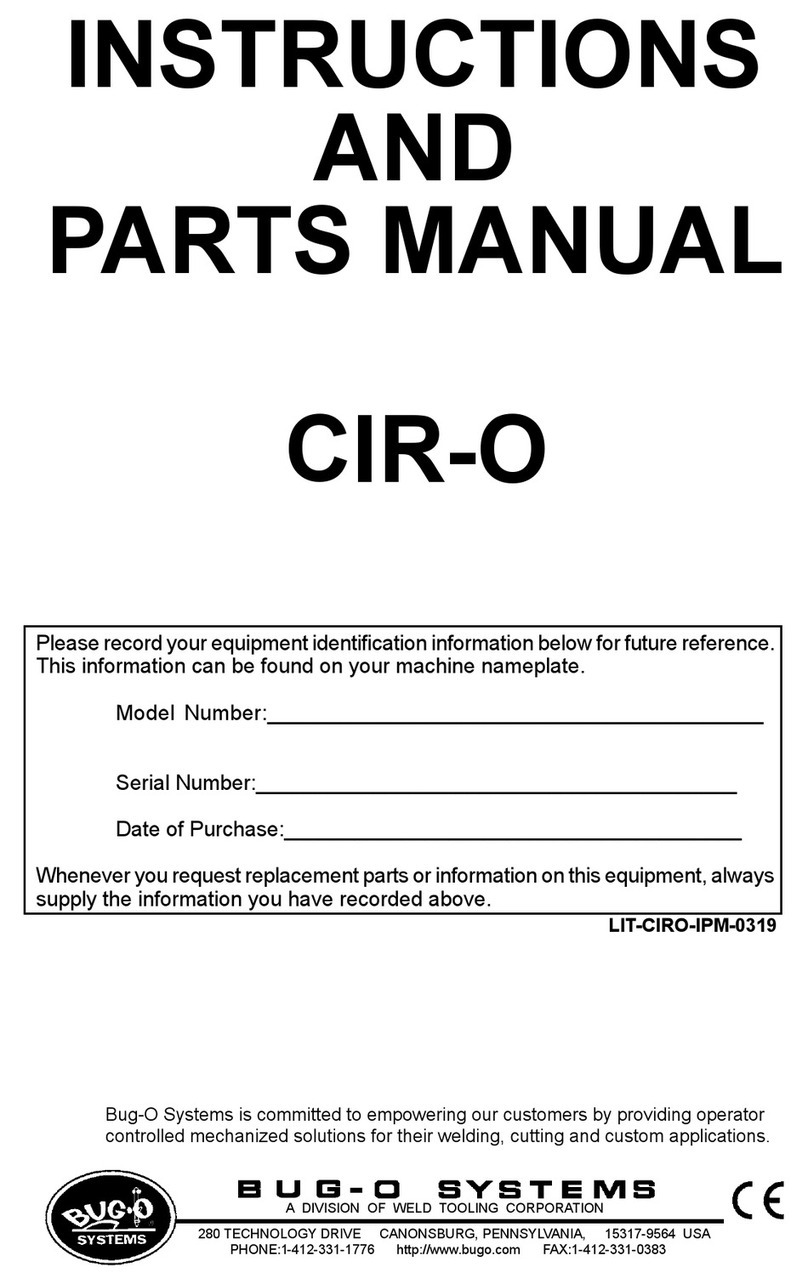
Bug-O Systems
Bug-O Systems CIR-O Technical reference manual
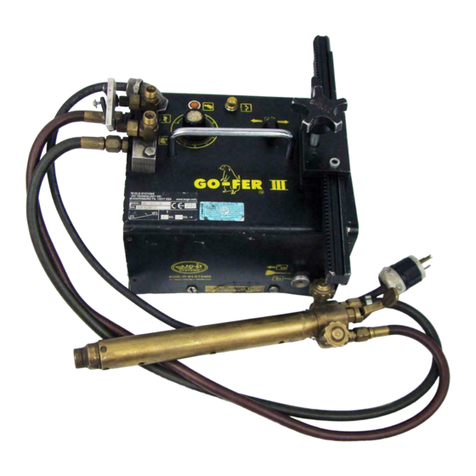
Bug-O Systems
Bug-O Systems GO-FER III-OX Technical reference manual
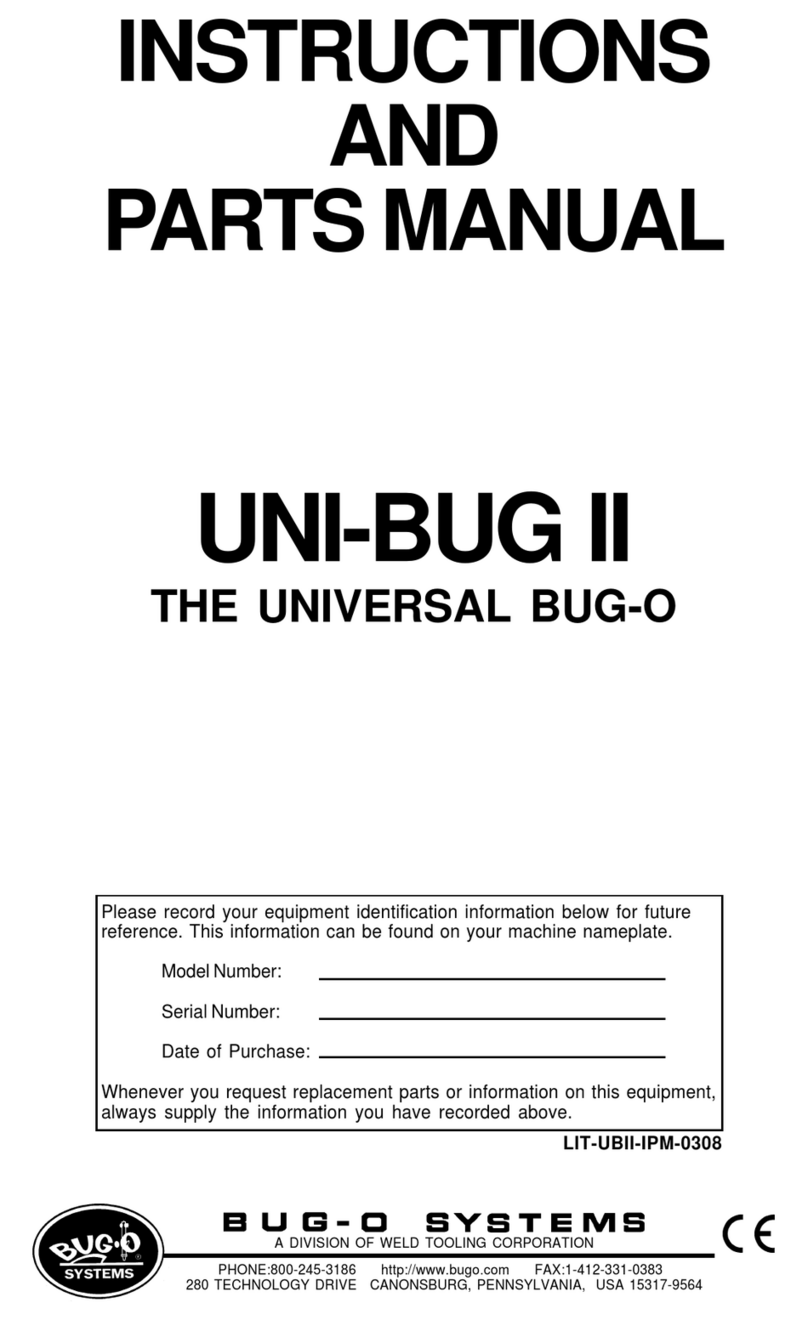
Bug-O Systems
Bug-O Systems UNI-BUG II Technical reference manual
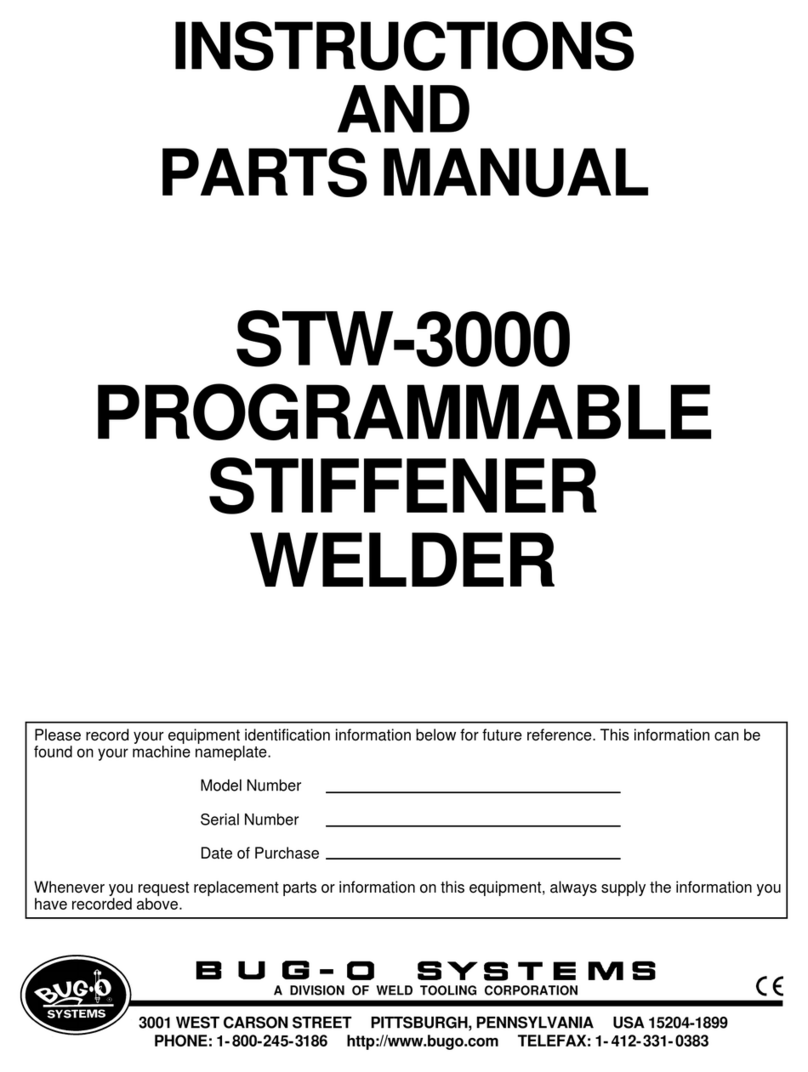
Bug-O Systems
Bug-O Systems STW-3000 Technical reference manual
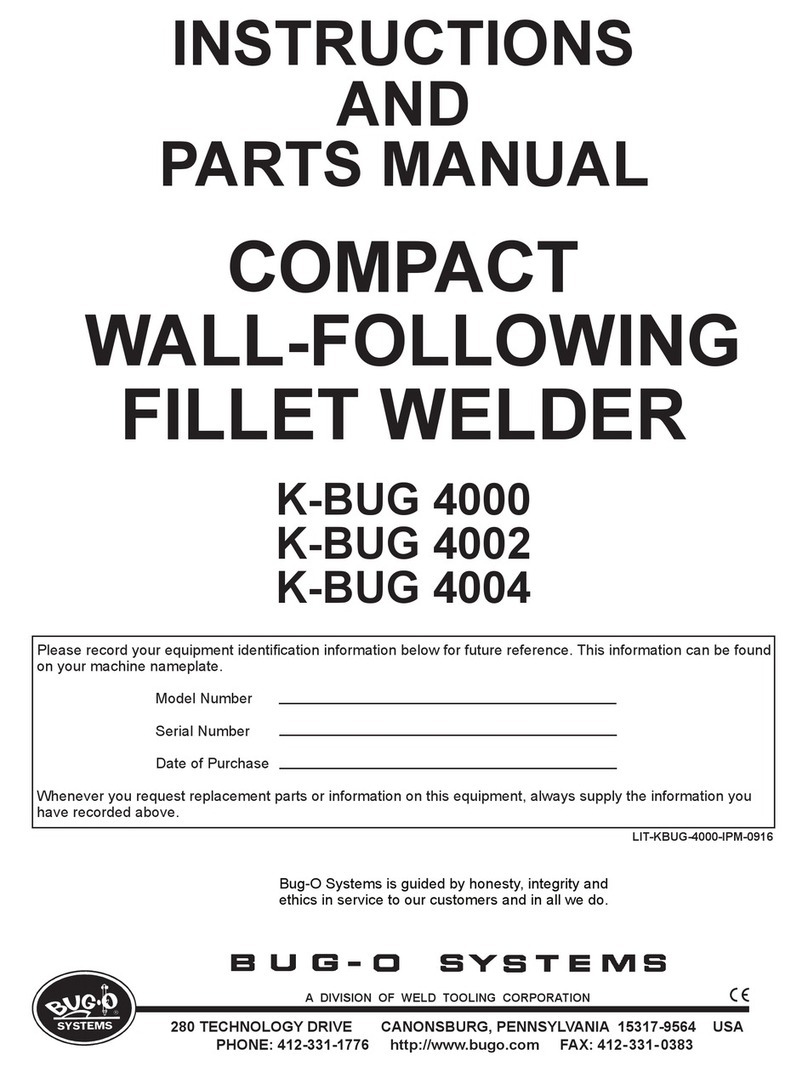
Bug-O Systems
Bug-O Systems K-BUG 4000 Technical reference manual