Bug-O Systems K-BUG 4000 Technical reference manual

INSTRUCTIONS
AND
PARTS MANUAL
A DIVISION OF WELD TOOLING CORPORATION
280 TECHNOLOGY DRIVE CANONSBURG, PENNSYLVANIA 15317-9564 USA
PHONE: 412-331-1776 http://www.bugo.com FAX: 412- 331- 0383
COMPACT
WALL-FOLLOWING
FILLET WELDER
K-BUG 4000
K-BUG 4002
K-BUG 4004
Please record your equipment identication information below for future reference. This information can be found
on your machine nameplate.
Model Number
Serial Number
Date of Purchase
Whenever you request replacement parts or information on this equipment, always supply the information you
have recorded above.
LIT-KBUG-4000-IPM-0916
Bug-O Systems is guided by honesty, integrity and
ethics in service to our customers and in all we do.

2
SAFETY
PROTECT YOURSELF AND OTHERS FROM SERIOUS INJURY OR DEATH.
KEEP CHILDREN AWAY. BE SURE THAT ALL INSTALLATION, OPERATION,
MAINTENANCE AND REPAIR PROCEDURES ARE PERFORMED ONLY BY
QUALIFIED INDIVIDUALS.
EQUIPMENT DAMAGE
POSSIBLE.
ELECTRIC SHOCK can kill.
1) The equipment is not waterproof. Using
the unit in a wet environment may result
in serious injury. Do not touch equipment
when wet or standing in a wet location.
2) The unused connectors have power on
them. Always keep the unused connec-
tors covered with the supplied protective
panels. Operation of the machine without
the protective panels may result in injury.
3) Never open the equipment without rst
unplugging the power cord or serious
injury may result.
4) Verify the customer-supplied power
connections are made in accordance
with all applicable local and national
electrical safety codes. If none exist,
use International Electric Code (IEC)
950.
5) Never remove or bypass the equipment
power cord ground. Verify the equipment
is grounded in accordance with all appli-
cable local and national electrical safety
codes. If none exist, use International
Electric Code (IEC) 950.
READ INSTRUCTIONS.
Read the instruction manual before
installing and using the equipment.
1) Do not plug in the power cord without rst
verifying the equipment is OFF and the
cord input voltage is the same as required
by the machine or serious damage may
result.
2) Always verity both the pinion and wheels
are fully engaged before applying power
or equipment damage may occur.
3) Do not leave the equipment unattended.
4) Remove from the work site and store in
a safe location when not in use.
1) Never try to stop the pinion from moving
except by removing power or by using the
STOP control.
2) Do not remove any protective panels,
covers or guards and operate equipment.
MOVING PARTS can
cause serious injury.
FALLING EQUIPMENT
can cause serious
personal injury and
equipment damage.
Faulty or careless user installation is
possible. As a result, never stand or walk
underneath equipment.

3
PRECAUTIONS:
1) Some plasma or welding cables are strong sources of high frequency interference.
NEVER lay a plasma or welding cable across the controls of the machine.
2) Always physically separate the plasma or welding cable leads from the machine
cables. For example, the plasma or welding cable leads should NEVER be bundled
with a pendant cable or the machine power cord. Maximize the separation between
any machine cables and the plasma or welding cables.
3) Strictly follow the grounding procedures specied for the plasma or welding unit.
NOTE: Some plasma and welding units produce exceptionally large amounts of high
frequency noise. They may require a grounding rod be driven into the earth within six
feet (2 meters) of the plasma or welding unit to become compatible with an automatic
cutting or welding process.
4) If the high frequency is produced using a spark gap, adjust the points so the gap is as
small as possible. The larger the gap, the higher the voltage and the higher the inter-
ference.
5) Some plasma or welding units will inject high frequency interference into the AC
power line. Use separate power line branches whenever possible to power the
plasma or welding source and the machine. Do not plug them into the same outlet
box.
6) High frequency noise may enter the machine through the plasma or welding supply
remote contactor leads. Some plasma and welding sources can produce noise spikes
of up to several thousand volts. These sources are not compatible with automated
cutting and welding equipment. It is recommended that the remote contactor leads on
these plasma or welding sources not be connected to the machine. An alternate
solution is to purchase a separate remote contactor isolation box.
HIGH FREQUENCY WARNINGS
WARNING: HIGH FREQUENCY CAN EFFECT MACHINE
OPERATION AND THEREFORE, WELD QUALITY.
SPECIAL PRECAUTIONS ARE REQUIRED WHEN USING PLASMA,
TIG OR ANY WELDING PROCESS THAT USES HIGH FREQUENCY
TO STRIKE AN ARC.
Read the precautions below before installing and using the equipment.

4
TABLE OF CONTENTS
COMPACT WALL-FOLLOWING
FILLET WELDER
K-BUG 4000, K-BUG 4002
INSTRUCTIONS AND PARTS MANUAL
PAGE
5 ..........Introduction
5 ..........Features
5 ..........Technical Data
5 ..........Dimensions
6 ..........User Interface
6 ..........Welding Modes
7 ..........Intermittent Welding
7 ..........Intermittent Welding Lock Out
7 ..........Stop Sensor Operation
8 ..........Time Settings
8 ..........Global Parameters
9 ..........Converting Units
10 .........Installation and Operation
10 .........Maintenance
11-12 ......Troubleshooting
13 .........K-BUG 4000 Assembly View
14 .........K-BUG 4000 Wiring Diagram
15 .........KBUG-4010 Carriage Assembly / Exploded View
16 .........KBUG-4010 Carriage Assembly / Parts List
17 .........KBUG-1060 Guide Arms / Exploded View / Parts List
17 .........KBUG-4090 Torch Clamp Assembly / Parts List
18 .........KBUG-4050 Control Panel Assembly / Exploded View / Parts List
18 .........Accessories
19 .........SBG-450 Gun & Cable Assembly / Exploded View / Parts List
20 .........Warranty

5
INTRODUCTION
The K-BUG 4000 is a compact, light weight, wall-travelling unit designed to mechanize horizontal llet
welding. It is able to follow vertical or inclined walls of straight or curved (R > 1000 mm) prole. The
machine is capable of performing continuous and intermittent (stitch) welds.
FEATURES
• Compact - 14.6 x 8.9 x 11.3 in (370 x 226 x 288 mm)
• Lightweight - 14 lb (6.4 kg)
• Continuous and intermittent welds
• Digital speed display
• Precision speed control for consistent weld quality
• User adjustable time settings for puddle build-up, pause time and crater-ll
• Drive wheels rated to 400 °F (204 °C)
TECHNICAL DATA
Power Input
K-BUG 4000 120VAC / 50-60 Hz / 1 Phase
K-BUG 4002 240VAC / 50-60 Hz / 1 Phase
K-BUG 4004 42VAC / 50-60 Hz / 1 Phase
Weight 14 lb (6.4 kg)
Drive Motor 24 VDC, 12 W, 5000 RPM
Travel Speed 0.3 - 77 in/min (0.1 - 195 cm/min)
Torch Angle Adjustable
Running Angle 90°
DIMENSIONS
Min. 8.2" (208.3 mm)
Max. 10.8" (274.3 mm)
Min. 9.7" (246.4 mm)
Max. 13.3" (337.8 mm)
14.5" (368.3 mm)

6
USER INTERFACE
1. Cycle Start Button - Push button to initiate
weld cycle. Weld contact will close, according to
time settings, if the Weld Switch is set to Auto,
the carriage will travel in the direction selected
by the Travel Direction Switch.
2. Cycle Stop Button - Push button to stop
welding cycle.
3. Travel Direction Switch - Set switch to
determine direction of carriage travel.
4. Speed Adjustment Knob - Rotate knob to
adjust carriage travel speed. Turning clockwise
(right) will INCREASE speed.
NOTE: Travel Speed Adjustment Knob is also
used for setting the INTERMITTENT WELDING
function (pg.7) and the time settings.
5. Weld Auto / Off Contactor - When switched to
AUTO, weld contact will close with cycle start.
Switched to the right, weld contact will remain
open upon cycle start.
6. Digital Speed Display - Numerically displays
real-time travel speed in in/min (cm/min). Also
displays parameters during setup of intermittent
function and time settings.
7. Indicator LED’s - Indicate active parameter
during intermittent welding.
A. Weld Length
B. Non-Weld Length
C. Total Length
WELDING MODES
The K-BUG 4000 offers three weld modes - Continuous, Total Length Intermittent and User Dened
Intermittent. The value shown in the speed display will vary based on what welding mode the machine
is operating in. Speed is displayed only during Continuous welding
1. Continuous Welding
• No LED’s lit when Cycle Start button is pressed
• Displays speed while welding (0.1 in/min)
2. User Dened Intermittent Welding
• A or B LED lit when Cycle Start button is pressed
• User sets Welding Speed before pressing Cycle Start button
• Display will countdown each program parameter in order
- With A LED lit, the display will countdown Puddle Build-up timer, u, then Weld On
distance, A, then Crater Fill timer, n.
- With B LED lit, the display will countdown Weld Off distance, B
NOTE: Machine travels at higher speed during Non-Welding travel
• The intermittent cycle will repeat until the user presses Cycle Stop button or the Stop
S
ensor is
tripped
6
7
1 2
5
3
4

7
3. Total Length Intermittent Welding
• C LED lit when Cycle Start button is pressed
• User sets Welding Speed before pressing Cycle Start button
• Display will countdown total distance remaining (1.0 in)
• A or B LED will light as appropriate for welding mode
NOTE: Machine travels at higher speed during Non-Welding travel
• The intermittent cycle will continue until the Total Length is satised or the Stop Sensor is
tripped
INTERMITTENT WELDING
The Travel Speed Adjustment Knob is used for entering the parameters for intermittent or stitch
welding. Follow the steps below to enter the welding parameters.
1. Press the Travel Speed Adjustment Knob. The A LED will illuminate.
2. Turn the Travel Speed Adjustment Knob (clockwise + / counterclockwise -) to set the WELD
LENGTH. The length adjusts.*
3. Press the Travel Speed Adjustment Knob again. The B LED will illuminate.
4. Turn the Travel Speed Adjustment Knob to set the NON-WELD LENGTH. The length adjusts.*
5. Press the Travel Speed Adjustment Knob again. The C LED will illuminate.
6. Turn the Travel Speed Adjustment Knob to set the TOTAL LENGTH. The length adjusts.*
7. Press the travel Speed Adjustment Knob again. All LEDs are unlit.
*Note: measurement is in inches or cm. according to the unit setting - refer to Converting Units on pg.9.
Intermittent Welding is available in two forms - User Dened and Total Length. With User Dened
welding, user enters values for Weld Length and Non-Weld Length. Either A or B LED must be lit when
pressing Cycle Start Button. Intermittent Weld continues until user presses Cycle Stop Button.
For Total Length welding, user enters values for all three stitch parameters. C LED must be lit when
pressing Cycle Start Button. Intermittent welding ends when Total Length has been met.
INTERMITTENT WELDING LOCK OUT
To lock out the intermittent (stitch) welding controls, press and hold the Travel Speed Adjustment knob
for three (3) seconds. All of the LEDs will ash. To unlock the intermittent welding controls, press and
hold the Travel Speed Adjustment Knob for three (3) seconds. While in lockout, the machine will be
unable to perform intermittent welding.
STOP SENSOR OPERATION
The K-BUG 4000 is equipped with a magnetic proximity sensor, mounted internal to the carriage, on the
non-torch side. When the sensor detects the end of the work piece, it stops carriage travel and initiates
weld shutdown (crater ll).
WELDING MODES, CONT’D.

8
TIME SETTINGS
The K-BUG 4000 offers three adjustable time settings - Puddle Build-Up, Pause Time and Crater Fill.
The Travel Speed Adjustment knob is used for setting each of the timers, as described below.
Puddle Build-up Time (u)
1. While pressing the Cycle Start button, connect the power cord to an appropriate power supply.
2. The Display will show “u0.0” ashing.
3. Turn the Travel Speed Adjustment knob until the desired build-up time is displayed.
4. Default setting is 1.0 seconds. Available range is 0.0 - 9.9 seconds.
Crater Fill Time (n)
1. Press Cycle Start button once more.
2. The Display will show “n0.0” ashing.
3. Turn the Travel Speed Adjustment knob until the desired crater ll time is displayed.
4. Default setting is 1.0 seconds. Available range is 0.0 -9.9 seconds.
Pause Time (E). After welding, a brief rest before Crater Fill.
1. Press the Cycle Start button once more.
2. The Display will show “E0.0” ashing.
3. Turn the Travel Speed Adjustment knob until the desired stop time is displayed.
4. Default setting is 0.5 seconds. Available range is 0.0 - 9.9 seconds.
When nished setting times, press the Cycle Stop button to exit time setup mode. The machine is now
ready to be setup for welding.
A graphic display of the user adjustable time settings.
GLOBAL PARAMETERS
A menu of Global Parameters is maintained in the K-BUG 4000. The menu consists of six (6) items as
described in Table 1, below. Access to the menu is locked when DIP Switch #1 is in the OFF Position.
Table 1: Global Parameters
Display Description Default Range Units
n.0* Travel Speed Coefcient 1.0 0.1, 1.0, 2.0, 2.5,
5.0, 10.0
cm/mn, in/min
n.1 Motor Overload Stop Time 20.0 - 9.9 sec
n.2* Travel Motor Reduce Ratio 40 20 - 200 base g x 10 : 1
n.3* Diameter of Travel Wheel 50 0.0 - 99.9 mm
n.4 Show Mode off off / on
n.5 Operating Units U2 U1 / U2 U1 (cm/min), U2 (in/min)
* Indicates parameters NOT to be changed by the User. Changing these parameters can harm machine
performance.
u E n
Travel
Weld “On”
(time)
Travel
Weld “Off”

9
ACCESS THE GLOBAL PARAMETER MENU
1. With machine unplugged from A/C power supply, remove the six (6) screws securing the Control
Interface (Legend Plate and Main PCB) to the Control Panel.
2. Remove the Control Interface and turn it over.
3. Locate DIP Switch 1 and 2 on the Main PCB, see
illustration at right.
4. Turn DIP Switch 1 to the “ON” position.
5. Turn over Control Interface. And secure to Control panel.
6. Plug in machine to A/C power supply of appropriate
voltage.
7. “0” should be shown in the Display.
8. Press and release Cycle Start button to cycle through
the six parameters (0, 1, 2, 3, 4, 5).
9. Use the Travel Speed Adjustment knob to change the
parameter setting.
10. When nished, unplug machine, remove Control
Interface and turn it over.
11. Turn DIP switch 1 to the “OFF” position to lock global
parameter menu.
12. Re-assemble Control Panel and plug in machine to begin operation.
CONVERTING UNITS
By default, the K-BUG 4000 will be factory set to operate in English units (in/min) and the K-BUG
4002 will be set to operate in Metric units (cm/min). If it is necessary to change units, follow the steps
to access the Global Parameters Menu, above. Use the Cycle Start button until “5” is shown on the
Display. Turn the Travel Speed Adjustment knob right or left to select the desired Units. Choose “U1”
for Metric (cm/min) or “U2” for English (in/min).
Rear of Main PCB. Note DIP switch
placement on left hand side. Move
Switch 1 up to the ON position.
GLOBAL PARAMETERS, CONT’D

10
INSTALLATION AND OPERATION
1. Welding Preparation - Secure the necessary welding supplies
• Welding Power Source (3 phase, 440/380/220V AC)
• Wire Feeder
• Tank of appropriate shielding gas, with pressure and ow regulators and appropriate ttings
• Torch for gas shielded automated welding
• Basic Weld Prep Tools
2. Cable Connections
• Connect welding torch conduit cable to wire feeder
• Connect Weld Contactor lead from Torch to Main Cable Connector on machine body
• Connect Control Cable to the Control Box Connector on the machine body
• Connect Control Power Source Cable to the Welding Power Source
CAUTION: Carefully route power cable as it may become entangled during operation, resulting
in damage to people or equipment.
3. Welding Process
• Switch ON the Primary Side Distribution Board of the Welding Power Source
• Switch ON the Control Power Source on the front panel of the Welding Power Source
• Equip the Wire Feeder with wire
• Set the Carriage so the torch is at the weld starting point
• Install the Guide Arms offset in the direction of travel (leading arm slightly shorter than
following arm) for better positioning of the electrode in the joint
• Adjust the target angle and position of the Torch using the Torch Adjustment Slider
• Verify machine is in the proper welding mode. Set stitch welding parameters, if needed
• Verify adequate Shielding Gas Supply
• Start Welding - Switch Welding Switch to AUTO, verify desired travel direction is set and
travel speed is > 0 and press Cycle Start button
• Press Cycle Stop button when welding is complete. Turn Welding Switch to OFF
• Conrm Welding End
MAINTENANCE
The K-BUG carriage should be periodically checked and cleaned to maximize service life.
Before use:
Check all screws in the torch clamp and guide rollers. Tighten as needed. Loose fasteners may
cause uneven travel or inconsistent weld quality.
During use:
Monitor wheels, motor and welding torch for abnormal noise or overheating.
After each use:
1. Clean control panel to remove dust and other debris.
2. Inspect carriage base, wheels, guide rollers, slide adjustment, magnets and torch for weld
spatter or other debris. Clean as needed.
3. Inspect power cable and torch cable for cracked, cut or damaged insulation. Replace as
needed.
4. Inspect connectors for damaged pins or loose connections. Replace as needed.

11
TROUBLESHOOTING
Symptom Cause Repair
Control panel
Display is not LIT
when machine is
plugged in
Disconnected Control Cable Connect control cable to machine
Faulty Control Cable Replace Cable
Control Box Fuse Tripped or
Disconnected
Replace fuse. If problem persists,
contact service rep.
No Arc when
Welding Auto/Off
Switch turned to
AUTO
Weld Auto/Off Switch set to OFF Turn Weld Auto/Off Switch to AUTO
Loose contact of Welding Leads Check ground connections. Verify good
contact on clean, unpainted surface.
Faulty or incorrectly wired Welding
Auto/Off Switch
Check Wiring. Replace Switch, if
needed
Stop Sensor does not detect work
piece.
Reposition carriage so Stop Sensor is
over work piece.
Carriage does not
travel when Cycle
Start Button is
pushed
Failed drive component Check Motor, Drive Chain and Gearbox.
Replace as needed
Faulty or incorrectly wired Cycle Start
Button
Check Wiring. Replace button , if
needed
Faulty MAIN PCB Replace MAIN PCB
Torch targets wrong
position
Loose fastener on Torch Clamp or
Slide Assembly
Check and tighten screws, replace if
needed.
Slide is hard to
adjust
Dust or other debris on slide parts Clean slide parts. Lubricate with light oil
Carriage stops
during automatic
welding
Obstacle in carriage path Remove obstacles
Carriage is at end of work piece. Stop
Sensor doesn’t detect work piece.
Reposition carriage so Stop Sensor is
over work piece.
Distance traveled exceeds Total
Length
See “Intermittent Welding” on page 7 for
instructions to set Total Length
Arc continues after
Welding Auto/Off
Switch is set to OFF
The Welding Auto/Off Switch is still
set to Auto
Turn Weld Auto/Off Switch to OFF
Faulty or incorrectly wired Welding
Auto/Off Switch
Check Wiring. Replace Switch, if
needed.
Unable to perform
Intermittent Welding
Intermittent Welding is locked Press and hold Travel Speed
Adjustment knob for 3 seconds.

12
TROUBLESHOOTING, CONT’D.
K-BUG ERROR LIST
NO. SYMPTOM CAUSE SOLUTION
E-03 Motion Stop Main PCB EET ROM Error Main PCB Replacement
E-05 Travelling Stop Auto-Stop Travelling Motor Push and release Stop Button
may be overloaded / shorted
IF UNRESOLVED:
1. Check for loose wiring connec-
tion at drive motor and weave
motor if equipped (see below).
2. Replace motor or motor reducer
3. Replace main PCB

13
ITEM QTY PART NO. DESCRIPTION
1 1 KBUG-4010 Carriage Assembly
2 1 KBUG-4050 Control Panel Assembly
3 1 KBUG-4090 Torch Clamp Assembly
4 1 KBUG-4070 Slide Assembly
5 1 KBUG-1060 Guide Arm Assembly
6 1 KBUG-4040 Cable Anchor
* 1 KBUG-2274-XX 120 VAC Power Cord
* 1 KBUG-2273-XX Weld Contact Cable
* 1 KBUG-1003 Metric Hex Key Set
* = Not shown
Note:
1. XX = Cable length: 15, 25, 50 ft (4.5, 7.5, 15 m)
2. For KBUG-4002, Power Cord is KBUG-2272-15.
K-BUG 4000 ASSEMBLY VIEW
1
3
4
5
2
6

14
K-BUG 4000 WIRING DIAGRAM
INPUT POWER
KBUG-1126
DISPLAY & SWITCH
MAIN PCB
120 VAC 50 - 60 Hz 1Ph
240 VAC 50 - 60 Hz 1Ph
TORCH
EXTERNAL SENSOR
(STOP)
CN1
CN6
CN2
J2
J1
J2
J1
M1
TS11CS501
KBUG-1049
HEADER-S08
HEADER-S08
HEADER-S08
HEADER-S08
1
2
3
4
5
1
2
3
1
2
3
4
5
6
FND0
FND1
FND2
FND3
EN_UP_SW
EN_DN_SW
EN_PUSH_SW
GND
1
2
3
4
5
6
7
8
1
2
3
4
5
6
7
8
1
2
3
4
5
6
7
8
1
2
3
4
5
6
7
8
1
2
3
4
5
6
DC +24 V
P-GND
MA_CW/CCW
MA_PULSE
MA_PWM
MA_RUN/STOP
DA0
DA1
DA2
DA3
DA4
DA5
DA6
DA7
PA0
PA1
PA2
PA3
PA4
PA5
PA6
PA7
FND0
FND1
FND2
FND3
EN_UP_SW
EN_DN_SW
EN_PUSH_SW
GND
AC+
EARTH
AC-
WELD_COM
TORCH
KBUG-1126

15
KBUG-4010 CARRIAGE ASSEMBLY / EXPLODED VIEW
1
2
7
6
5
4
3
8
14
13
12
11
10
16
21
20
19
18
17
22
23
27
26
25
24
9
15

16
KBUG-4010 CARRIAGE ASSEMBLY / PARTS LIST
ITEM QTY PART NO. DESCRIPTION
1 1 KBUG-4011 Body, Rear
2 1 KBUG-4012 Body Side, Left
3 1 KBUG-4013 Body, Bottom
4 1 KBUG-4014 Body Side, Right
5 1 KBUG-4015 Body, Top
6 1 KBUG-4028 Body Cover
7 1 KBUG-4032 Handle
8 1 KBUG-4027 Magnet, Small
9 1 KBUG-4024 Magnet Bracket (1)
10 1 KBUG-4029 Sensor Cover
11 1 KBUG-4031 Sensor
12 1 KBUG-4034 Magnet, Large
13 1 KBUG-4026 Magnet Plate
14 2 KBUG-4025 Magnet Bracket (2)
15 1 KBUG-4023 Motor Bracket (BD)
16 1 KBUG-4037 Geared Motor
17 1 KBUG-4038 Motor Bracket (BLDC)
18 1 KBUG-1049 DC Brushless Motor
19 3 KBUG-4021 Wheel Shaft Bushing (2)
20 3 KBUG-4035 Chain Sprocket
21 2 KBUG-4017 Wheel Shaft Cover (1)
22 1 KBUG-4022 Chain
23 2 KBUG-4016 Wheel Shaft
24 4 KBUG-1036 Wheel, 50mm
25 2 KBUG-4018 Wheel Shaft Cover (2)
26 2 KBUG-4019 Wheel Shaft Bushing (1)
27 4 KBUG-4036 Roller Bearing

17
KBUG-1060 GUIDE ARMS / EXPLODED VIEW / PARTS LIST
1
2
3
4
5
ITEM QTY PART NO. DESCRIPTION
1 2 KBUG-1061 Guide Roller Bushing
2 2 KBUG-1062 Guide Roller
3 2 KBUG-1063 Guide Roller Cover
4 2 KBUG-1064 Guide Roller Slide Bracket
5 2 KBUG-1065 Guide Arm
6 2 KBUG-1068 Guide Roller Sleeve
6
KBUG-4090 TORCH CLAMP ASSEMBLY / PARTS LIST
1
3
ITEM QTY PART NO. DESCRIPTION
1 1 KBUG-2080 Torch Clamp Assembly
2 1 KBUG-4095 Slide Bar Clamp
3 1 KBUG-3076 Bushing
4 1 KBUG-4097 HDH-Torch Clamp Base
4
2

18
1
2
3
4
56
7
8
9
10
11
12
KBUG-4050 CONTROL PANEL ASSEMBLY / EXPLODED VIEW / PARTS LIST
ITEM QTY PART NO. DESCRIPTION
1 1 KBUG-4051 Panel
2 2 KBUG-1122 Toggle Switch Cover
3 1 KBUG-1123 Legend Plate
4 2 KBUG-1124 Push Button Cover (BS)
5 1 KBUG-1125 Display
6 1 KBUG-1126 Main PCB
7 1 KBUG-1127 Push Button Cover - 2
8 1 KBUG-1128 Push Button Cover -1
9 1 KBUG-1129 Volume Knob
10 1 KBUG-1131 Fuse Holder w/ Fuse
11 1 KBUG-1132 Power Connector, 4T (Female)
12 1 KBUG-1133 Torch Connector, 2T (Female)
* 1 KBUG-1173 Weld Contact Connector (Male)
* 1 KBUG-1174 Power Connector (Male)
* Not Shown
ACCESSORIES
KBUG-1067 Magwheel Add-On Kit
Magnetic guide wheels available for curved
or irregular seams.

19
PARTS LIST WIRE SIZE
ITEM QTY PART NO. DESCRIPTION
.035
(.9 mm)
.040
(1.0)
.045
(1.2)
.052
(1.4)
1/16
(1.6)
5/64
(2.0)
1 1 BUG-3159-35 16S-35 (.9 mm) Contact Tip X
1 1 BUG-3159-45 16S-45 (1.2 mm) Contact Tip X
1 1 BUG-3159-52 16S-52 (1.4 mm) Contact Tip X
1 1 BUG-3159-116 16S-116 (1.6 mm) Contact Tip X
1 1 BUG-3159-564 16S-564 (2.0 mm) Contact Tip X
1 1 PWS-4436-1.0 16S-40 (1.0 mm) Contact Tip X
2 1 PWS-4447 27S62 H.D. Nozzle ⅝" X X X X X X
3 1 PWS-4449 PX57HD Gas Diffuser X X X X X X
4 1 CWO-8017 Case w/ Binder Screws (Front) X X X X X X
5 1 PWS-4411 Case w/ Binder Screws (Back) X X X X X X
6 1 STW-3044 450 Amp Cable X X X X X X
7 1 R174-T Connector, Small Lincoln
7 1 R174-L Connector, ¾" Lincoln
7 1 R174-M Connector, Miller
7 1 R174-X Connector, Euro
8 1 CWO-8009 44-3545-15 Cable Liner X X X
8 1 CWO-8011 44-116-15 Cable Liner X X
8 1 CWO-8012 44-564-15 Cable Liner X
** 1SBG-1004 Gas Hose Assembly X X X X X X
** 2SBG-1005 Gas Hose Clamps X X X X X X
** Not shown. Required only with standard Lincoln guns (SBG-450-L).
SBG-450-_-___-__ GUN & CABLE ASSEMBLY / EXPLODED VIEW / PARTS LIST
Whip Length: 15 (15 ft / 4.6 m) or 25 (25 ft / 7.6 m)
Wire Size: 035, 040, 045, 052, 116, 564
Connector Type: E (Euro), L (Lincoln ¾"), M (Miller), T (Lincoln, small)
4
4
5
5
7
3
1
2
6
8
6

20
WARRANTY
FOR A PERIOD OF TWELVE (12) MONTHS FROM DELIVERY, BUG-O SYSTEMS WARRANTS TO THE ORIGINAL PURCHASER
(DOES NOT INCLUDE AUTHORIZED DISTRIBUTORS), THAT A NEW MACHINE IS FREE FROM DEFECTS IN MATERIAL
AND WORKMANSHIP AND AGREES TO REPAIR OR REPLACE, AT ITS OPTION, ANY DEFECTIVE PARTS OR MACHINE.
THIS WARRANTY DOES NOT APPLY TO MACHINES, WHICH AFTER OUR INSPECTION, ARE DETERMINED TO HAVE
BEEN DAMAGED DUE TO NEGLECT, ABUSE, OVERLOADING, ACCIDENT OR IMPROPER USAGE. ALL SHIPPING AND
HANDLING CHARGES WILL BE PAID BY CUSTOMER.
BUG-O SYSTEMS MAKES NO WARRANTY OF MERCHANTABILITY AND MAKES NO OTHER WARRANTY, EXPRESSED OR
IMPLIED, BEYOND THE WARRANTY EXPRESSLY SET FORTH ABOVE. BUYER’S REMEDY FOR BREACH OF WARRANTY,
HEREUNDER, SHALL BE LIMITED TO REPAIR OR REPLACEMENT OF NON-CONFORMING PARTS AND MACHINES. UNDER
NO CIRCUMSTANCES SHALL CONSEQUENTIAL DAMAGES BE RECOVERABLE.
HOW TO OBTAIN SERVICE:
IF YOU THINK THIS MACHINE IS NOT OPERATING PROPERLY, RE-READ THE INSTRUCTION MANUAL CAREFULLY,
THEN CALL YOUR AUTHORIZED BUG-O DEALER/DISTRIBUTOR. IF HE CANNOT GIVE YOU THE NECESSARY SERVICE,
WRITE OR PHONE US TO TELL US EXACTLY WHAT DIFFICULTY YOU HAVE EXPERIENCED. BE SURE TO MENTION
THE MODEL AND SERIAL NUMBERS.
LIMITED WARRANTY MODEL ____________________________
SERIAL NO. ________________________
DATE PURCHASED: _________________
This manual suits for next models
5
Table of contents
Other Bug-O Systems Welding System manuals
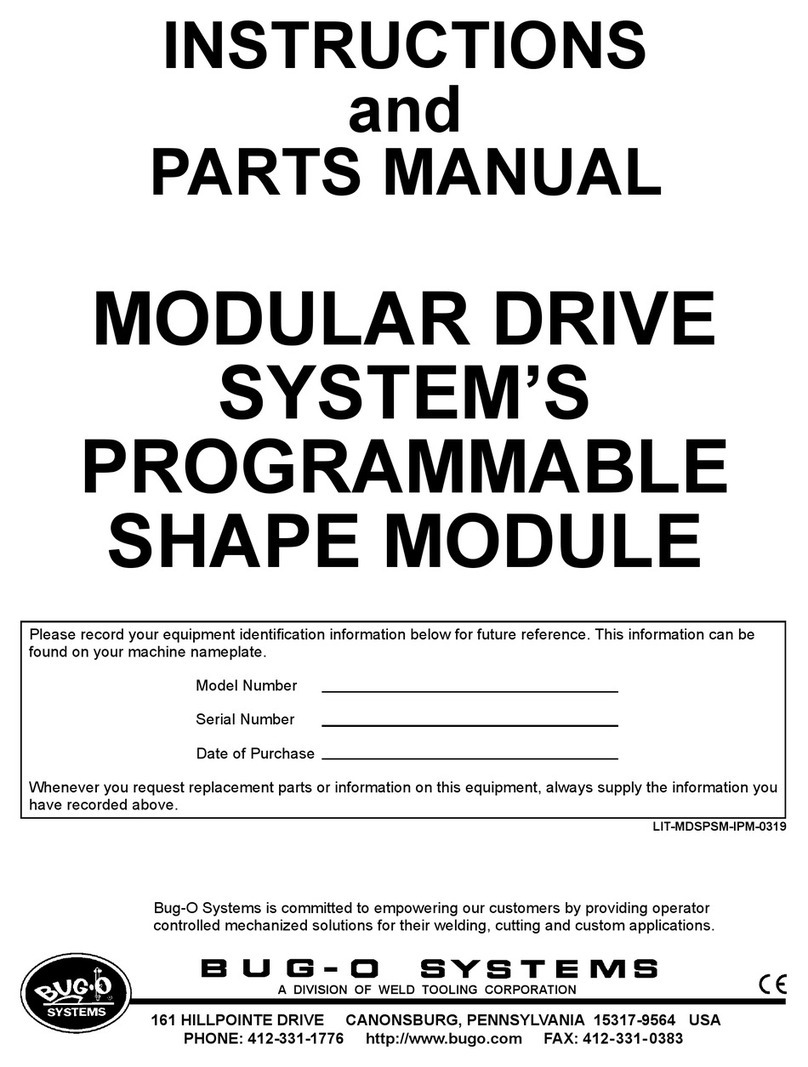
Bug-O Systems
Bug-O Systems MDS Series Technical reference manual
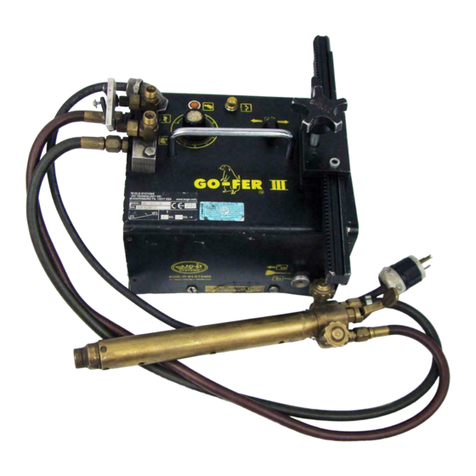
Bug-O Systems
Bug-O Systems GO-FER III-OX Technical reference manual
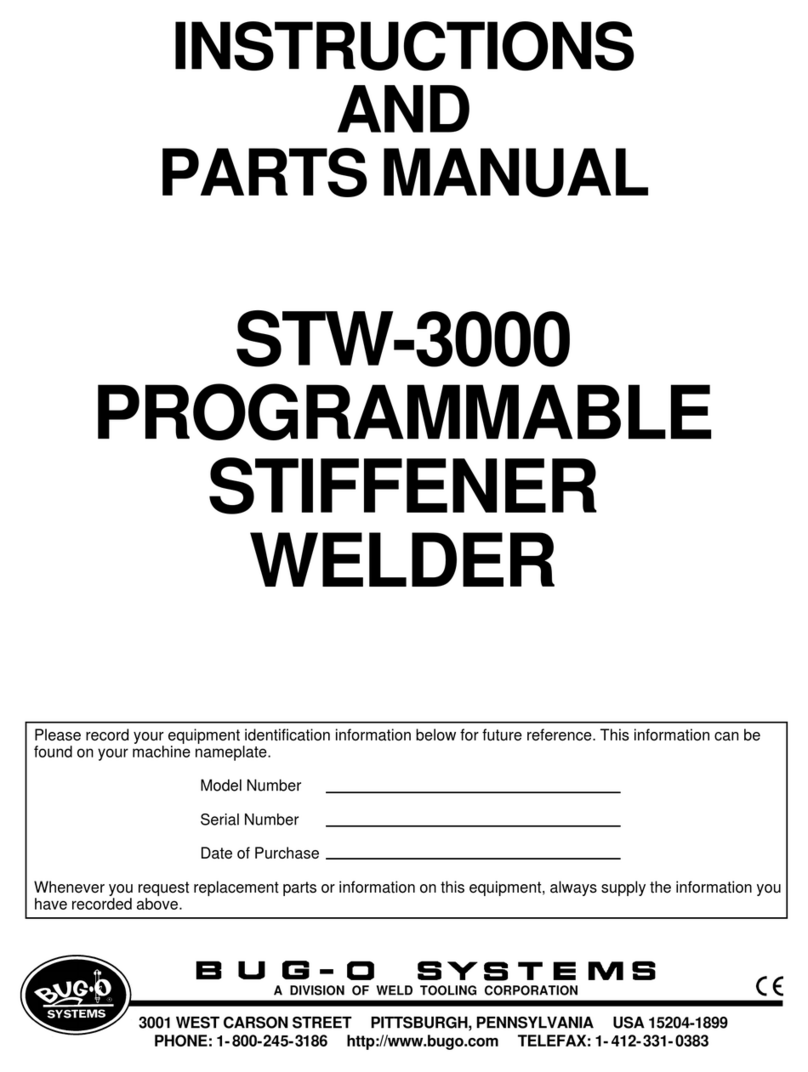
Bug-O Systems
Bug-O Systems STW-3000 Technical reference manual
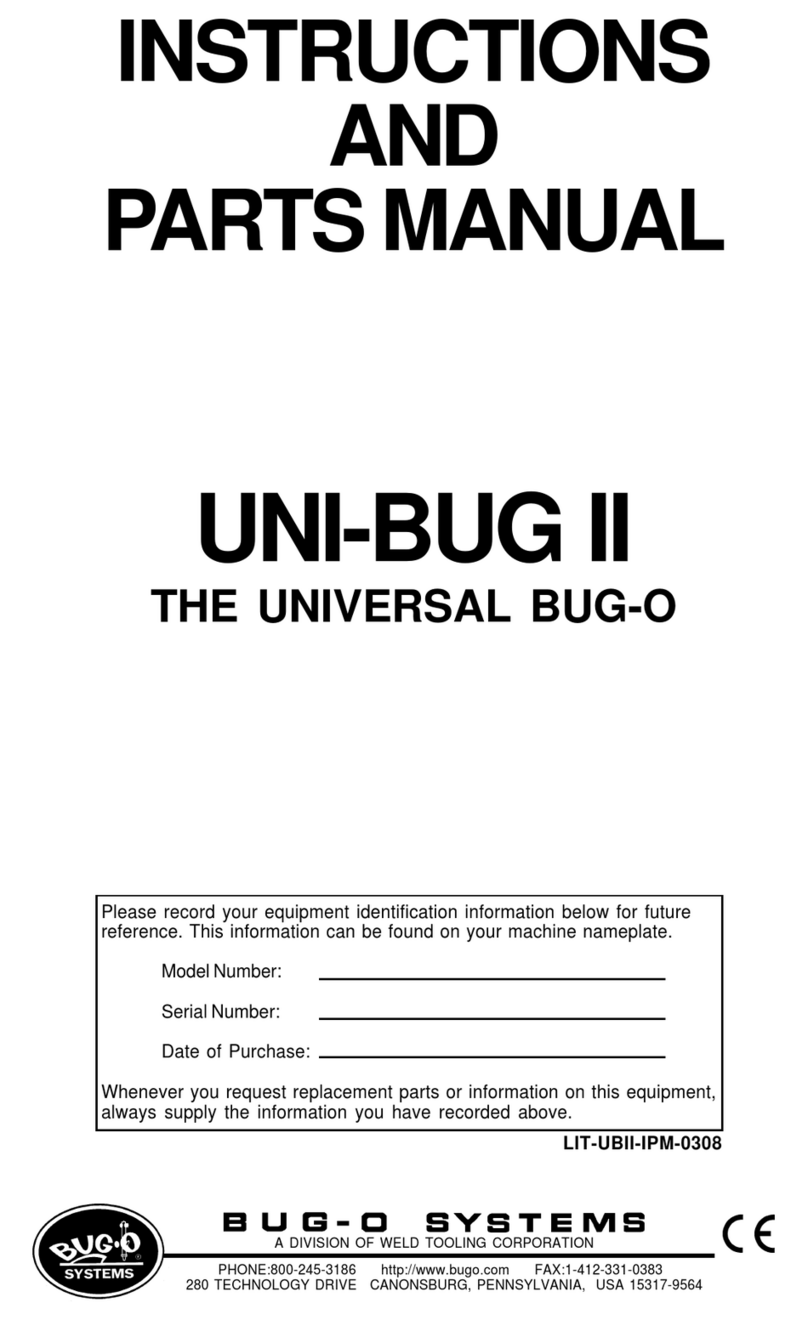
Bug-O Systems
Bug-O Systems UNI-BUG II Technical reference manual
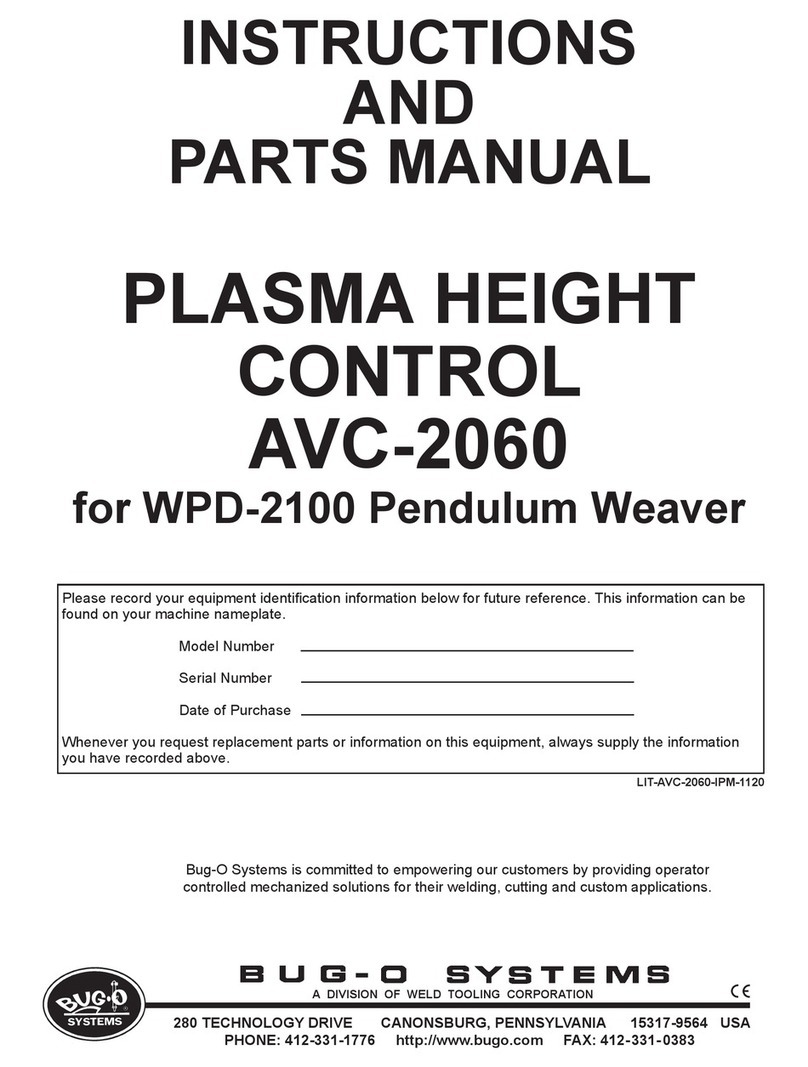
Bug-O Systems
Bug-O Systems AVC-2060 Technical reference manual
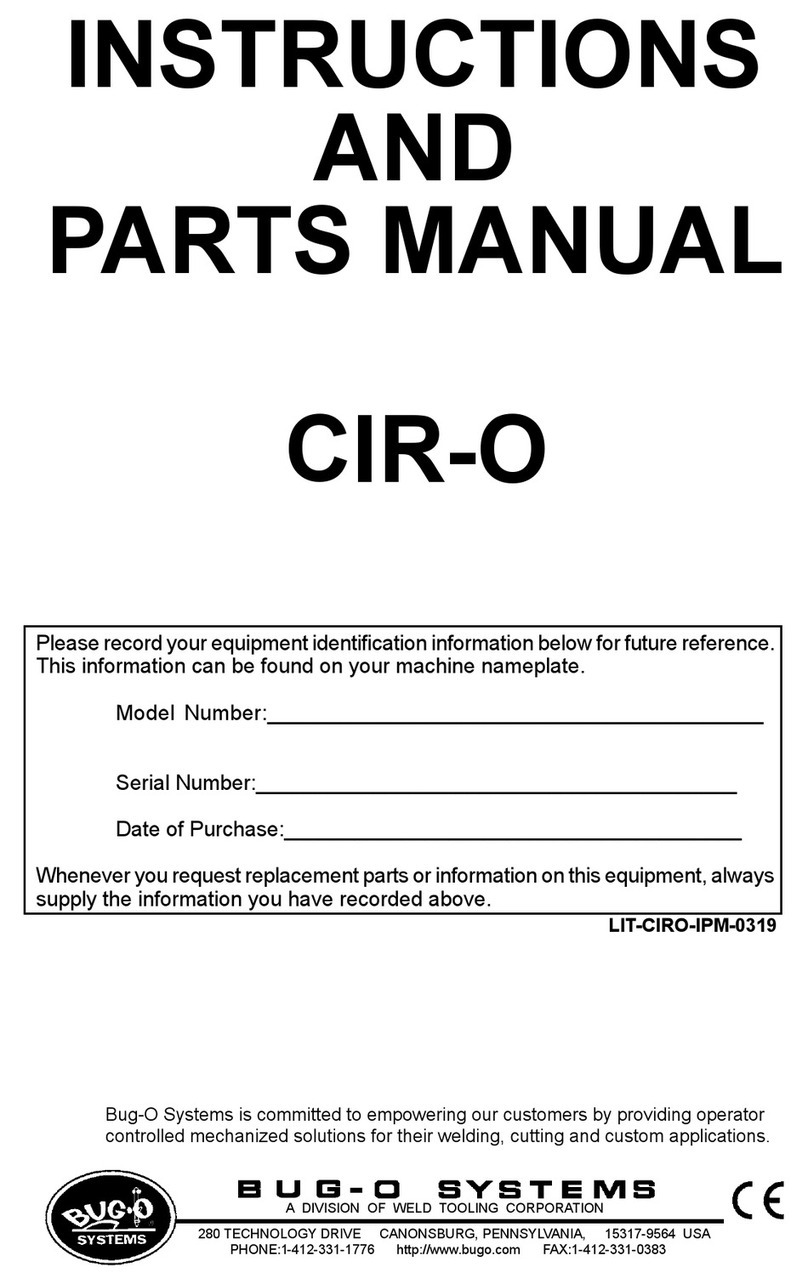
Bug-O Systems
Bug-O Systems CIR-O Technical reference manual