Bug-O Systems CIR-O Technical reference manual

A DIVISION OF WELD TOOLING CORPORATION
PHONE:1-412-331-1776 http://www.bugo.com FAX:1-412-331-0383
280 TECHNOLOGY DRIVE CANONSBURG, PENNSYLVANIA, 15317-9564 USA
CIR-O
INSTRUCTIONS
AND
PARTS MANUAL
Please record your equipment identication information below for future reference.
This information can be found on your machine nameplate.
Model Number:_________________________________________
Serial Number:_________________________________________
Date of Purchase:_______________________________________
Whenever you request replacement parts or information on this equipment, always
supply the information you have recorded above.
LIT-CIRO-IPM-0319
Bug-O Systems is committed to empowering our customers by providing operator
controlled mechanized solutions for their welding, cutting and custom applications.

SAFETY
PROTECT YOURSELF AND OTHERS FROM SERIOUS INJURY OR
DEATH. KEEP CHILDRENAWAY. BE SURE THATALL INSTALLATION,
OPERATION, MAINTENANCE AND REPAIR PROCEDURES ARE
PERFORMED ONLY BY QUALIFIED INDIVIDUALS.
1. Do not plug in the power cord without
rst verifying the equipment is OFF
and the cord input voltage is the same
as required by the machine or serious
damage may result.
2. Do not leave the equipment unattended.
Remove from the work site and store in
a safe location when not in use.
Read the instruction manual before
installing and using the equipment.
1.The equipment is not waterproof. Using
the unit in a wet environment may result
in serious injury. Do not touch the
equipment when wet or standing in a
wet location.
2.Never open the equipment without rst
unplugging the power cord or serious
injury may result.
3.Verify the customer-supplied power
connections are made in accordance
with all applicable local and national
electrical safety codes. If none exist,
use International Electric Code (IEC)
950.
4.Never remove or bypass the equipment
power cord ground. Verity the equipment
is grounded in accordance with all
applicable local and national electrical
safety codes. If none exist, use
lnternational Electrical Code (IEC) 950.
ELECTRIC SHOCK can kill.
READ INSTRUCTIONS
EQUIPMENT DAMAGE
POSSIBLE.
1. Never try to stop the pinion from moving
except by removing power or by using
the STOP control.
2.Do not remove any protective panels,
covers or guards and operate equipment.
FALLING EQUIPMENT
can cause serious personal
injury and equipment
damage.
Faulty or careless user installation is
possible. As a result, never stand or
walk underneath equipment.
MOVING PARTS can cause
serious injury.
CAUTION
DO NOT LEAVE EQUIPMENT UNATTENDED
WHEN NOT IN USE!
Remove from work site and store in a safe location.
223
NOTES

4............TECHNICAL DATA
5,6.........OPERATING INSTRUCTIONS
7............BUG-5100-F DC III DRIVE UNIT
8............CIR-O / EXPLODED VIEW
9............CIR-O / PARTS LIST
10..........BUG-5100-F DC III DRIVE UNIT / EXPLODED VIEW
11.......... BUG-5100-F DC III DRIVE UNIT / PARTS LIST
12..........BUG-5100-F DC III DRIVE UNIT / WIRING DIAGRAM
12..........ELECTRICAL COMPONENT CHART
13..........VACUUM SUPPORT KIT
14..........VACUUM PUMP / EXPLODED VIEW
15..........VACUUM PUMP / PARTS LIST
16..........TEMPLATE KIT
17..........TEMPLATE KIT / PARTS LIST
18..........CIR-O WITH ANNULAR CARRIAGE
19..........CIR-O SPEED RANGE CHART
20..........TROUBLESHOOTING GUIDE
21..........WARRANTY
CIR-O
PRECISION CIRCLE BURNER,
BEVELER AND WELDER
INSTRUCTION AND PARTS MANUAL
PAGE
TABLE OF CONTENTS
THIS PRODUCT IS COVERED BY ONE OR
MORE PATENTS WORLD WIDE.
3
22
NOTES

4
TECHNICALDATA
Net Weight: CIR-3303,3323,3313 CIR-4404,4424,4414 CIR-5505,5525,5515
48 lbs. (21.8 kg) 65 lbs. (29.5 kg) 90 lbs.(40.9 kg)
Shipping
Weight: 66 lbs. (30.0 kg) 90 lbs. (40.8 kg) 128 lbs. (56.0 kg)
Speed Range: See chart on page 19.
Power Requirement: 120 VAC/50-60/1 240 VAC/50-60/1 42 VAC/50-60/1
CIR-3303 CIR-3323 CIR-3313
CIR-4404 CIR-4424 CIR-3313
CIR-5505 CIR-5525 CIR-5515
Cutting Range: Inside Diameter Outside Diameter
CIR-3301,3323,3313 3"-14" (75-356 mm) 26"-56" (660-1422 mm)
CIR-4404,4424,4414 3"-22" (75-559 mm) 34"-64" (864-1626 mm)
CIR-5505,5525,5515 3"-30" (75-760 mm) 42"-72" (1060-1830 mm)
24" (610 mm)
32" (813 mm)
40" (1016 mm)
CIR-3
CIR-4
CIR-5
25.50" (648 mm)
33.87" (860 mm)
42.25" (1070 mm)
“X”
“X” = 8.19 (208 mm)
With 2" Legs.
“X” = 11.19 (284 mm)
With 5" Legs.
21
WARRANTY
LIMITED 3-YEAR
WARRANTY
MODEL ___________________________
SERIAL NO. _______________________
DATE PURCHASED: ________________
WHERE PURCHASED: ______________
For a period ending one (1) year from the date of invoice, Manufacturer warrants
that any new machine or part is free from defects in materials and workmanship and
Manufacturer agrees to repair or replace at its option, any defective part or machine.
HOWEVER, if the invoiced customer registers the Product Warranty by returning the
Warranty Registration Card supplied with the product within 90 days of the invoice
date, or by registering on-line at www.bugo.com, Manufacturer will extend the war-
ranty period an additional two (2) years which will provide three (3) total years from
the date of original invoice to customer. This warranty does not apply to machines
which, after Manufacture’s inspection are determined by Manufacturer to have been
damaged due to neglect, abuse, overloading, accident or improper usage. All ship-
ping and handling charges will be paid by the customer.
The foregoing express warranty is exclusive and Manufacturer makes no represen-
tation or warranty (either express or implied) other than as set forth expressly in
the preceding sentence. Specifically, Manufacturer makes no express or implied
warranty of merchantability or fitness for any particular purpose with respect to any
goods. Manufacturer shall not be subject to any other obligations or liabilities what-
soever with respect to machines or parts furnished by Manufacturer.
Manufacturer shall not in any event be liable to Distributor or any customer for any
loss of profits, incidental or consequential damages or special damages of any kind.
Distributor’s or customer’s sole and exclusive remedy against Manufacturer for any
breach of warranty, negligence, strict liability or any other claim relating to goods de-
livered pursuant hereto shall be for repair or replacement (at Manufacturer’s option)
of the machines or parts affected by such breach.
Distributor’s Warranty:
In no event shall Manufacturer be liable to Distributor or to any customer thereof for
any warranties, representations or promises, express or implied, extended by Dis-
tributor without the advance written consent of Manufacturer, including but not limited
to any and all warranties of merchantability or fitness for a particular purpose and
all warranties, representations or promises which exceed or are different from the
express limited warranty set forth above. Distributor agrees to indemnify and hold
Manufacturer harmless from any claim by a customer based upon any express or
implied warranty by Distributor which exceeds or differs from Manufacturer’s express
limited warranty set forth above.
HOW TO OBTAIN SERVICE:
IF YOU THINK THIS MACHINE IS NOT OPERATING PROPERLY, RE-READ THE
INSTRUCTION MANUAL CAREFULLY, THEN CALL YOUR AUTHORIZED BUG-O
DEALER/DISTRIBUTOR.IFTHEYCANNOTGIVEYOUTHENECESSARYSERVICE,
WRITE OR PHONE US TO TELL US EXACTLY WHAT DIFFICULTY YOU HAVE
EXPERIENCED. BE SURE TO MENTION THE MODEL AND SERIAL NUMBERS.

5
INTRODUCTION
Your new CIR-O is ready for operation when you receive it. A few minutes
spent reading the following will help you become familiar with the operation
and capabilities of your machine.
The CIR-O Carriage (C) should operate freely on the Ring Track (D). The
carriage has three adjustable Wheel Logs (A). By loosening the Flat Socket
Head Screws (B) these logs may be rotated for adjustment. To check Wheel
(AA) adjustment, hold one wheel and move the carriage. When properly
adjusted the wheel should barely slip.
The Cam Clutch (E) engages the drive pinion to the Ring Gear (F) by chang-
ing the position of the Drive Module (I). The Thumb Nut (H) locks the Cam
Clutch (E) in position.
Turning the Potentiometer Knob (K) regulates speed. The Switch (J)
controls forward-o-reverse. Throw the switch in the direction you want the
carriage to travel.
The CIR-O is furnished with four symmetrically-located Legs (L). A variety
of Magnetic Feet and legs (S), (T), (U), and (V) are available to increase
the versatility of the CIR-O machine.
OPERATINGINSTRUCTIONS
X
YWP
F
D
S
U
L
T
V
C
R
AA
A
B
O
Q
I
KJEH
Z
20
PROBLEM CAUSE REMEDY
Does not run- No power to Check power line supply voltage.
Indicator light o. machine. Plug in line cord rmly.
Does not run, Wiring shorts. Disconnect machine and
indicator light o. examine internally; rewire at fault.
Circuit breaker
tripped. If none found, throw direction switch
to ‘OFF’, reset breaker and plug in.
Shorted motor. If breaker does not trip, replace
drive unit.
Faulty speed If breaker trips again, replace
control board. control board.
(OR)
Burned out
transformer. Replace transformer.
Does not run. Bad connection. Check wiring connections, 12 VAC
indicator light on. should appear across secondary
of transformer.
Tighten terminal screws on speed
control board.
Faulty speed If DC Volts = 0 across leads to
control board. motor; replace control board.
Unit runs, but no Faulty speed Replace control board.
control over speed. control board. (Check connection rst).
NOTE:
Make sure unit is pugged into correct voltage.
(120 VAC, 240 VAC, 42 VAC) corresponding to model number rating.
12 VAC should appear across secondary of transformer in all DC III Drive
Units.
TROUBLESHOOTINGGUIDE

6
POWER SUPPLY
The DC III drive operates on 120 volt, (42VAC), (240VAC), 50/60 Hz. The Circuit
Breaker (O) protects the unit against overload or electrical faults,
CAUTION: IF THE CIRCUIT BREAKER OPENS, FIND AND CORRECT THE
CAUSE OF FAILURE BEFORE RESETTING.
TORCH
The Torchholder (P) will accept any standard American machine torch (barrel
diameter 1-3/8" (34 mm) with 1/4"-square (6 mm) 32-pitch rack). The 32-pitch
pinion is standard. Specify a 24-pitch pinion if desired. The Short Hose As-
sembly (Q) connects the torch to the Quick-acting Manifold Assembly (R).
The supply hoses are to be connected to the open side of the quick-acting
manifold assembly.
Proper torch operation is essential to quality cuts. We suggest that you follow
the torch manufacturers’ instructions carefully, being sure to use a clean tip of
the proper size.
MAGNETIC SUPPORTS
Several Types of magnetic supports are available for use with the CIR-O to
stabilize the machine as listed below:
(S) Outrigger Support Assemblies; CON-1010 - used in multiples of two
or four to stabilize CIR-O on plate, cylinders or heads where two legs must
be longer than the other two,
(T) Magnet Foot Assemblies; CIR-9000 - may be used in sets of four or
more to position CIR-O on vertical or out-of-position, at surfaces.
(U) Leg and Magnet Foot Assemblies; CON-1040 (four required) - may be
used for at or irregular surfaces.
(V) Oset Leg and Magnet Assemblies; CIR-9002 (four required) - use with
a bevel cutting head or adjustable tip adaptor - to eliminate the “blind” spot
under the ring.
SETUP
A center-punch mark and a radius mark are the only layout required. The Center
Pin Assembly (Z) extends below the CIR-O base and is placed in the center-
punch mark. The CIR-O is then eased down to the work on the center pin. This
movement locates the entire machine “on center.” The Rack (W) with Torch-
holder (P) is then positioned over the radius mark.
OPERATION
In order to provide a smooth start, it is recommended that the starting hole be
drilled or pierced inside or outside the radius mark. Center the torch tip over the
radius mark and secure the Rack Stop (X) rmly against the Post Assembly
(Y). [The side of the post assembly to which the rack stop is positioned depends
upon whether the material inside or outside the cut is scrap]. Begin the cut from
the starting hole and, after carriage travel is begun, move the Torch Rack (W)
slowly against the Rack Stop (X). This action “feathers-in” the cut eliminating
a notch.
OPERATING INSTRUCTIONS (CONT’D.)
19
CIR-O SPEED RANGE CHART
Capacities and Speed Ranges
3 .4-8 75 10-210
6 .8-16 150 20-420
10 .4-28 250 35-700
14 2-39 350 50-1000
26 3.5-70 650 90-1805
30 4-80 750 105-2100
34 4.5-92 850 120-2400
38 5.2-105 950 130-2640
42 5.7-115 1050 150-3000
46 6.3-125 1140 160-3200
50 6.8-135 1250 175-3500
56 7.6-155 1420 200-4000
3 .3-5 75 7-140
6 .6-11 150 14-280
10 .9-18 250 23-460
14 1.3-26 350 32-650
18 1.7-33 450 42-840
22 2-40 550 50-1000
34 3.2-63 850 80-1600
38 3.5-70 950 87-1760
42 3.9-78 1050 97-1950
46 4.3-85 1150 105-2130
50 4.6-93 1250 115-2300
54 5-100 1350 125-2500
58 5.4-110 1450 135-2700
64 6-120 1625 150-3000
3 .2-4 75 5-100
6 .4-8 150 10-210
10 .7-13 250 17-350
14 1-19 350 42-500
18 1.3-25 450 32-640
22 1.5-30 550 38-760
26 1.8-37 650 45-900
30 2-41 750 52-1050
42 2.9-57 1050 73-1458
46 3.2-63 1150 80-1600
50 3.4-68 1250 87-1750
54 3.7-75 1350 94-1900
58 4-80 1450 100-2000
62 4.3-85 1550 105-2150
66 4.5-90 1650 115-2300
72 4.9-100 1825 125-2500
DIAMETER
IPM
INCH IPM
DIAMETER
INCH
CIR-III
INSIDE
RING
CIR-IV
CIR-V
OUTSIDE
RING
INSIDE
RING
OUTSIDE
RING
INSIDE
RING
OUTSIDE
RING

7
DRIVE UNIT OPERATION
Rotating Cam Knob (B) will move the drive pinion in and out of engagement
with the ring gear.
To lock drive into position, tighten the 1/4-28 Wing Nut (A).
To disengage the drive pinion from the ring gear, loosen the 1/4-28 Wing
Nut (A) and turn Knob (B) counterclockwise. Turn Knob (B) clockwise to
engage the drive pinion with the ring gear, re-tighten the 1/4-28 Wing Nut
(A) to lock in position.
When Power Cord (C) is plugged into the appropriate power source, Pilot
Light (D) will glow. Switch (E) controls the direction of travel, with the cen-
ter position set at “OFF”. Knob (F) controls the speed. Circuit Breaker (G)
protects the unit against overload or electrical faults.
CAUTION: IF THE CIRCUIT BREAKER OPENS, FIND AND CORRECT
THE CAUSE OF FAILURE BEFORE RESETTING.
TECHNICAL DATA
DC III DRIVE UNIT
Power Requirement: BUG-5100-F 120 VAC/50-60/1
BUG-5102-F 240 VAC/50-60/1
BUG-5104-F 42 VAC/50-60/1
Dimensions: 7.12" L x 6.75" W x 6.75" H
(180 x 172 x 172 mm)
Net Weight: 16 lbs. (7.3 kg)
Shipping Weight: 20 lbs. (9.1 kg)
Speed: 2-50 ipm (50-1270 mm/min)
(Measured at Drive Pinion)
Load Capacity: *30 lbs. (14 kg)
[Measured at Drive Pinion]
*Note: Speed and load ratings apply at radius of ring
gear. Speed is proportional to radius at any other
point, and load rating is inversely proportional to
radius.
BUG-5100-F DC III DRIVE UNIT
A
B
E
FDG
C
18
CIR-O WITH ANNULAR CARRIAGE
CIR-3304 CIR-0 III w/ANNULAR CARRIAGE
CIR-4405 CIR-0 IV w/ANNULAR CARRIAGE
CIR-5506 CIR-0 V w/ANNULAR CARRIAGE
ITEM QTY PART NO DESCRIPTION
1 1 BUG-2440 Base, Post (Block)
2 1 BUG-5100-F DC III Drive Unit Assembly (150: 1)
3 1 BUG-9180-10 7/8" (22 mm) Rod, 10" (254 mm) Long
4 1 CIR-1010-3 Twin Hose Assembly 32" (812 mm)
42" (1066 mm): CIR-1010-4
50" (1270 mm): ClR-1010-5
5 1 CIR-5031 Carriage Plate-Annular
6 4 CON-1003 Leg 2" (50 mm)
7 1 CON-(3,4,5)000 Ring & Gear Assembly
8 1 GOF-3025 2-Hose Quick-Acting Manifold
9 1 PAN-1010 Panograph Assembly with Torchholder
5
2
4
8
3
9
1
6
7

8
CIR-O / EXPLODED VIEW
20
21
74
11
18
24
22
6
5
13
19
23
17
2
3
16
12
15
1
10
914
8
17
CIR-9030 [FOR CIR-3]
CIR-9040 [FOR CIR-4]
CIR-9050 [FOR CIR-5]
ITEM QTY PART NO. DESCRIPTION
1 1 BUG-2440 Base, Post (Block) - Order separately
2 1 BUG-2915 Torchholder Assembly
3 1 BUG-9180-10 1/8" (22 mm) rod, 10" (254 mm) Long
4 4 CIR-9031 Spacer Leg
5 1 CIR-9032 Aluminum Master Template Guide
(For CIR-3)
6 4 CON-1004 Alignment Bars (included with
Ring Gear Assembly)
7 4 CON-1040 Magnet Foot and Leg Assembly-Order
separately-use of 4 recommended
with this kit
8 4 FAS-0257 Rnd Hd Scr 1/4-20 x 3/4"
9 8 FAS-2553 Soc Hd Cap Scr 1/4-20 x 1-1/2"
(included with Ring Gear Assembly)
10 1 PAN-1009 Tensioner
11 1 PAN-1018 Rod w/Key-10" (254 mm) Long
12 1 PAN-1033 Rod Clamp
13 -------------- Torches are not furnished with kit,
order separately
TEMPLATE KIT / PARTS LIST
24
12
11
13*
1
210
9
8
7
5
6

9
PARTS LIST / CIR-O
ITEM QTY PART NO. DESCRIPTION
1 2 BUG-1996 Fixed Leg & Wheel Assembly
2 3 BUG-1998 Adjustable Leg & Wheel Assembly
3 5 BUG-2010 Wheel w/Bearing
4 1 BUG-2407 Post Assembly (Vertical)
5 1 BUG-2440 Base Post (Block)
6 1 BUG-2915 Torchholder Assembly
7 1 BUG-5100-F DC III Drive Unit Assembly (150:1)
120 VAC 240 VAC BUG-5102-F
42 VAC- BUG-5104-F
8 4 CIR-9002 Oset Leg & Magnet Foot (Optional)
9 4 CIR-9020 Magnet Foot
10 4 CIR-9021 Leg (Specify Length w/Sux)
Lengths Available: 5" (127 mm)
8" (203 mm) 10" (254 mm)
11 1 CIR-1010-3 Twin Hose Assembly 32" (812 mm)
42" (1066 mm) CIR-1010-4
50" (1270 mm) CIR-1010-5
12 1 CON-(3,4,5)000 Ring & Gear Assembly
13 1 CON-(3,4,5)041 Carriage Plate
14 4 CON-1003 Leg-2" (50 mm)
15 1 CON-1042 Center Pin Support Bar
16 1 CON-1043 Center Pin Assembly 9" (228 mm)
17 3 FAS-0986 Fit Hd Soc Sor 5/16-24 x 5/8
18 2 FAS-2736 Fil Hd Set 10-24 x 2-1/4
19 1 GOF-3025 2-Hose Quick-Acting Manifold
20 1 HOB-1025 Rack Stop
21 1 PAN-1015 Rack 22-5/8" (574 mm)
22 1 PAN-1033 Rod Clamp
23 1 PAN-1043 Spacer
24 2 WAS-0230 #10 Washer
CIR-O / PARTS LIST
16
The purpose of the TEMPLATE KIT is to permit cutting of elliptical and
obround holes. The manner of accomplishing this job involves dragging the
torch barrel against a template which is made 11/16" (18 mm) larger on the
radius than the cut-out desired (when using standard US machine torches).
The TEMPLATE KIT consists of a master layout template (aluminum sheet),
which is used to locate the bolt holes and center on the actual template which
should be made from 1/8" (3 mm) masonite or similar material.
A full-size drawing of the shape to be cut, should be made showing a center
point, then add 11/16" (18 mm) to the radius. (Because the torch body drags
against the template, adding one-half the diameter of the torch to the drawing
will put the center of the torch tip in the right position.)
MAKING THE TEMPLATE
Lay the aluminum master layout template on the masonite board. Transfer
the holes from the master by tracing with a pencil or use a quick-drying spray
paint. Next, position the oversized drawing, so that the center point is directly
over the center on the template and the shape is located symmetrically be-
tween the ‘leg holes’ (see sketch Page 17, number 8. Trace [or spray] the
outline onto the template.)
Next, drill the holes in the template. Then, cut-out the outside circle (outside
of the template) and the shape to be cut (on the inside).
MOUNTING THE TEMPLATE
The four CIR-9031 spacer legs should be screwed into the ring gear. (Remove
existing 2" (50 mm) legs.) The template is then placed on these legs and the
2" (50 mm) legs, or 5" (127 mm) legs, when using the recommended CON-
1040 leg and foot assemblies) are screwed - through the template - into the
CIR-9031 spacer legs, which clamp the template under and parallel to the
ring gear. Insert four round head screws (see sketch Page 17, number 12)
through the template - into the alignment bars (see sketch Page 17, number 7.)
SET UP
Place the rod [see sketch Page 17 number 5 in the base post on the carriage.
Slip the tensioning assembly (see sketch Page 17, number 6) on the rod.
Install machine torch in torchholder - make sure torch is straight up-and-down
in both planes. Adjust tensioning assembly so that torch maintains rm contact
with template when carriage is rotated. Connect hoses. Place machine on
work - locate feet and lock in position.
STARTING THE CUT
Lock tensioning assembly so that the torch tip is over scrap area, piece - or
start the cut in starting hole. When preheat is complete start motor (carriage
travel), release tensioning assembly and let it gradually swing to template -
(this action ‘feathers’ the start into the cut.)
TEMPLATE KIT

10
BUG-5100-F DC III DRIVE UNIT /
EXPLODED VIEW
2
7
31
8
22
26 5
6
35
14 15
17
25
9
21
27
29
4
11 10
24
32
29
1
3
15 28
13
16
30
12 23
20
19
33
18
34
15
ITEM QTY PART NO. DESCRIPTION
1 1 ARV-2017 1/4" Brass Vacuum Relief Valve
2 1 ARV-2014 Vacuum Gage
3 1 ARV-2018 1/4" NPT Union Cross, Female
4 2 ARV-2012 1/4" NPT Nipple
5 1 ARV-2016 1/4" NPT Brass Check Valve, F
6 2 ARV-1107 3/8" Hose Barb x 1/4" NPT-M
7 2 ARV-1005 11/16" x .112 Thk
8 1 ARV-1004-P Hose 3/8" ID x 11/16" OD
9 1 ARV-1012 Female Quick Connector
10 1 ARV-2019 Pump
11 1 ARV-1999 Foot Support
12 1 ARV-2021 120 VAC Power Cord w/Switch
13 1 ARV-2013 Handle
14 1 ARV-2011 Body
15 4 ARV-2010 Vane
16 1 ARV-2009 Shroud
17 2 ARV-2003 End Cap
18 2 ARV-2004 Felt
19 2 ARV-2005 O-ring
20 2 ARV-2002 End Cap Assembly
21 1 ARV-2001 Filter / Muer
22 1 ARV-2006 Muer Box
23 1 ARV-2007 Gasket
24 1 ARV-2008 End Plate
VACUUM PUMP / PARTS LIST
ARV-2020 VACUUM PUMP KIT, 120 VAC 60 HZ/1 PH
ARV-2030 VACUUM PUMP KIT, 220 VAC 50 HZ/1 PH
The VACUUM PUMP KITS are 1/6 HP units that provide 15" (381 mm) Hg.
on continuous duty. The ARV-2020/2030 Pump will support 30 vacuum cups.
A Repair Kit, ARV-1029 is available for the ARV-2020 and ARV-2030 pumps.
The kit contains (4) vanes, (1) body gasket, lter felts for the muer, oiler
lter, oiler wick, a cover gasket and separator felt for the oiler lter.
LUBRICATION OF ARV-2020 AND ARV-2030 VACUUM PUMP KITS:
Fill jar to line indicated on “oil level decal” to avoid wetting felt, which would
increase oil feed. Use SOCONY DTE LIGHT OIL OR EQUIVALENT PETRO-
LEUM BASE OIL WITHOUT DETERGENTS. One lling should last 20-50
hours of operation. For slower feed, pull wick downward so that less wick is
exposed to air stream. Using the same oil as above, oil the motor bearings
yearly with 1/2 teaspoon or 30 drops.

11
ITEM QTY PART NO. DESCRIPTION
*1 1 BUG-1393 Volt Trap 120 VAC
*2 1 BUG-1415 Pilot Light 120 VAC
*3 1 BUG-1550 Gear Motor 150:1
4 1 BUG-1725 Precision Speed Control
5 1 BUG-2255 Toggle Switch
6 1 BUG-2767W Wing Nut 1/4-28
7 1 BUG-2924 Reset Button Seal
8 1 BUG-2988 End Plate
9 1 BUG-5111 Cover
10 1 BUG-5112 End Plate
11 1 BUG-5113 Cam Clutch
12 1 BUG-5114 Swivel Plate
13 1 BUG-5116 Stud
14 1 BUG-5119 Knob
15 1 BUG-5120 Cam Clutch Assembly
(includes Items 6,11,13,14,17,35)
16 4 BUG-5121 Stand O
17 1 BUG-5122 Delrin Washer
18 1 BUG-5128 Drive Pinion w/Long Shaft
19 1 BUG-5131 Sleeve
20 1 BUG-9444 Tool Kit
*21 1 BUG-9445 Power Cord 120 VAC
22 1 BUG-9446 Cord Grip
23 1 BUG-9614 Needle Bearing
*24 1 BUG-9675 Transformer 120 VAC
25 1 BUG-9677 Potentiometer
26 1 BUG-9687 Knob
27 2 FAS-0112 Pan Hd Scr 6-32 x 1/4
28 8 FAS-0114 Pan Hd Scr 6-32 x 3/8
29 7 FAS-0124 Pan Hd Scr 8-32 x 3/8
30 1 FAS-0654 Soc Hd Shidr Scr 5/16 x 3/8 x 1/4-20
*31 1 BUG-2923 Circuit Breaker w/Reset .7A
32 2 FAS-1320 Hex Nut 8-32
33 4 FAS-2824 Fit Hd Slt Scr 8-32 x 1-3/4
34 1 GOF-3019 Handle
35 1 WAS-0240 1/4 Washer
*See Electrical Component Chart for 240 VAC and 42 VAC part numbers.
BUG-5100-F DC III DRIVE UNIT / PARTS LIST
14
VACUUM PUMP / EXPLODED VIEW
21
4
3
2
1
56
78
7
6
9
10
11
13
14
15
16
17 18 20
19 22
23
24
12

12
BUG-5100-F DC III DRIVE UNIT / WIRING
DIAGRAM / ELECTRICAL COMPONENT CHART
120 (42) VAC
INPUT
240 VAC
INPUT
CB BLK
BLK
WHT
A
D
V
WHT
TTAN
TAN
RED
12 VAC
YEL
DK. BLU
DK. BLU
WHT/BLU
P
1
2
3
4
5
6
7
8
POT M- M+
AC
F
S
M
PK
GY
RED
BLK
CB
BLK
A
WHT
D
BLK T
12 VAC
ELECTRICAL COMPONENT CHART
ITEM DESCRIPTION BUG-5100-F BUG-5102-F BUG-5104-F
120 VAC 240 VAC 42 VAC
A Power Cord BUG-9445 GOF-3115 BUG-9442
CB Circuit Breaker BUG-2923 (.7A) BUG-2952 (.5A) BUG-2933 (2A)
D Pilot Light BUG-1415 BUG-1428 BUG-1427
V Volt Trap BUG-1393 BUG-1563 BUG-1393
T Transformer BUG-9675 GOF-3112 BUG-1466
M Gear Motor * BUG-1550 (150:1)
F Precision Speed Control BUG-1725
S Toggle Switch BUG-2255
P Potentiometer Control BUG-9686
* BUG-1600 (50:1)
BUG-1595 (100:1)
PART NUMBER
13
CON-1006 VACUUM SUPPORT KIT can be mounted on any CIR-O or CON-
O ring base with standard CON-1003 legs. Vacuum pump kits are available
for operation on 120 VAC [ARV-2020] or 240 VAC [ARV-2030]
Each vacuum cup holds 50 lbs (22 kg).
(Dirt and scale block vacuum lines; blow-out when clogged).
Keep ame 4" (100 mm) away from cups when burning or welding. Silicone
vacuum cups will withstand a temperature of 600°F (318° C).
ITEM PART NO. DESCRIPTION
1 ARV-1004-14 Hose 14" (355 mm)
2 ARV-1005 Hose Clamp
3 ARV-1013 Male Quick Connector 1/4 NPT
4 ARV-2020 Vacuum Pump Kit (I 20 VAC/60 Hz/1 Ph)
ARV-2030 Vacuum Pump Kit (220 VAC/60 Hz/1 Ph)
5 ARV-1034 Choke Nipple
6 ARV-1107 3/8" Hose Barb 1/4 NPT
7 ARV-1109 Protective Cap
8 ARV-1116 Vacuum Cup (Silicone) 50 lbs. (22 kg)
9 CON-1007 Vacuum Leg
10 CON-1020 Double Swivel Clamp Assembly
Vacuum Pump is not included in CON-1006 Vacuum Support Kit.
VACUUM SUPPORT KIT
10 12
9 6
7
8
5
3
4

12
BUG-5100-F DC III DRIVE UNIT / WIRING
DIAGRAM / ELECTRICAL COMPONENT CHART
120 (42) VAC
INPUT
240 VAC
INPUT
CB BLK
BLK
WHT
A
D
V
WHT
TTAN
TAN
RED
12 VAC
YEL
DK. BLU
DK. BLU
WHT/BLU
P
1
2
3
4
5
6
7
8
POT M- M+
AC
F
S
M
PK
GY
RED
BLK
CB
BLK
A
WHT
D
BLK T
12 VAC
ELECTRICAL COMPONENT CHART
ITEM DESCRIPTION BUG-5100-F BUG-5102-F BUG-5104-F
120 VAC 240 VAC 42 VAC
A Power Cord BUG-9445 GOF-3115 BUG-9442
CB Circuit Breaker BUG-2923 (.7A) BUG-2952 (.5A) BUG-2933 (2A)
D Pilot Light BUG-1415 BUG-1428 BUG-1427
V Volt Trap BUG-1393 BUG-1563 BUG-1393
T Transformer BUG-9675 GOF-3112 BUG-1466
M Gear Motor * BUG-1550 (150:1)
F Precision Speed Control BUG-1725
S Toggle Switch BUG-2255
P Potentiometer Control BUG-9686
* BUG-1600 (50:1)
BUG-1595 (100:1)
PART NUMBER
13
CON-1006 VACUUM SUPPORT KIT can be mounted on any CIR-O or CON-
O ring base with standard CON-1003 legs. Vacuum pump kits are available
for operation on 120 VAC [ARV-2020] or 240 VAC [ARV-2030]
Each vacuum cup holds 50 lbs (22 kg).
(Dirt and scale block vacuum lines; blow-out when clogged).
Keep ame 4" (100 mm) away from cups when burning or welding. Silicone
vacuum cups will withstand a temperature of 600°F (318° C).
ITEM PART NO. DESCRIPTION
1 ARV-1004-14 Hose 14" (355 mm)
2 ARV-1005 Hose Clamp
3 ARV-1013 Male Quick Connector 1/4 NPT
4 ARV-2020 Vacuum Pump Kit (I 20 VAC/60 Hz/1 Ph)
ARV-2030 Vacuum Pump Kit (220 VAC/60 Hz/1 Ph)
5 ARV-1034 Choke Nipple
6 ARV-1107 3/8" Hose Barb 1/4 NPT
7 ARV-1109 Protective Cap
8 ARV-1116 Vacuum Cup (Silicone) 50 lbs. (22 kg)
9 CON-1007 Vacuum Leg
10 CON-1020 Double Swivel Clamp Assembly
Vacuum Pump is not included in CON-1006 Vacuum Support Kit.
VACUUM SUPPORT KIT
10 12
9 6
7
8
5
3
4

11
ITEM QTY PART NO. DESCRIPTION
*1 1 BUG-1393 Volt Trap 120 VAC
*2 1 BUG-1415 Pilot Light 120 VAC
*3 1 BUG-1550 Gear Motor 150:1
4 1 BUG-1725 Precision Speed Control
5 1 BUG-2255 Toggle Switch
6 1 BUG-2767W Wing Nut 1/4-28
7 1 BUG-2924 Reset Button Seal
8 1 BUG-2988 End Plate
9 1 BUG-5111 Cover
10 1 BUG-5112 End Plate
11 1 BUG-5113 Cam Clutch
12 1 BUG-5114 Swivel Plate
13 1 BUG-5116 Stud
14 1 BUG-5119 Knob
15 1 BUG-5120 Cam Clutch Assembly
(includes Items 6,11,13,14,17,35)
16 4 BUG-5121 Stand O
17 1 BUG-5122 Delrin Washer
18 1 BUG-5128 Drive Pinion w/Long Shaft
19 1 BUG-5131 Sleeve
20 1 BUG-9444 Tool Kit
*21 1 BUG-9445 Power Cord 120 VAC
22 1 BUG-9446 Cord Grip
23 1 BUG-9614 Needle Bearing
*24 1 BUG-9675 Transformer 120 VAC
25 1 BUG-9677 Potentiometer
26 1 BUG-9687 Knob
27 2 FAS-0112 Pan Hd Scr 6-32 x 1/4
28 8 FAS-0114 Pan Hd Scr 6-32 x 3/8
29 7 FAS-0124 Pan Hd Scr 8-32 x 3/8
30 1 FAS-0654 Soc Hd Shidr Scr 5/16 x 3/8 x 1/4-20
*31 1 BUG-2923 Circuit Breaker w/Reset .7A
32 2 FAS-1320 Hex Nut 8-32
33 4 FAS-2824 Fit Hd Slt Scr 8-32 x 1-3/4
34 1 GOF-3019 Handle
35 1 WAS-0240 1/4 Washer
*See Electrical Component Chart for 240 VAC and 42 VAC part numbers.
BUG-5100-F DC III DRIVE UNIT / PARTS LIST
14
VACUUM PUMP / EXPLODED VIEW
21
4
3
2
1
56
78
7
6
9
10
11
13
14
15
16
17 18 20
19 22
23
24
12

10
BUG-5100-F DC III DRIVE UNIT /
EXPLODED VIEW
2
7
31
8
22
26 5
6
35
14 15
17
25
9
21
27
29
4
11 10
24
32
29
1
3
15 28
13
16
30
12 23
20
19
33
18
34
15
ITEM QTY PART NO. DESCRIPTION
1 1 ARV-2017 1/4" Brass Vacuum Relief Valve
2 1 ARV-2014 Vacuum Gage
3 1 ARV-2018 1/4" NPT Union Cross, Female
4 2 ARV-2012 1/4" NPT Nipple
5 1 ARV-2016 1/4" NPT Brass Check Valve, F
6 2 ARV-1107 3/8" Hose Barb x 1/4" NPT-M
7 2 ARV-1005 11/16" x .112 Thk
8 1 ARV-1004-P Hose 3/8" ID x 11/16" OD
9 1 ARV-1012 Female Quick Connector
10 1 ARV-2019 Pump
11 1 ARV-1999 Foot Support
12 1 ARV-2021 120 VAC Power Cord w/Switch
13 1 ARV-2013 Handle
14 1 ARV-2011 Body
15 4 ARV-2010 Vane
16 1 ARV-2009 Shroud
17 2 ARV-2003 End Cap
18 2 ARV-2004 Felt
19 2 ARV-2005 O-ring
20 2 ARV-2002 End Cap Assembly
21 1 ARV-2001 Filter / Muer
22 1 ARV-2006 Muer Box
23 1 ARV-2007 Gasket
24 1 ARV-2008 End Plate
VACUUM PUMP / PARTS LIST
ARV-2020 VACUUM PUMP KIT, 120 VAC 60 HZ/1 PH
ARV-2030 VACUUM PUMP KIT, 220 VAC 50 HZ/1 PH
The VACUUM PUMP KITS are 1/6 HP units that provide 15" (381 mm) Hg.
on continuous duty. The ARV-2020/2030 Pump will support 30 vacuum cups.
A Repair Kit, ARV-1029 is available for the ARV-2020 and ARV-2030 pumps.
The kit contains (4) vanes, (1) body gasket, lter felts for the muer, oiler
lter, oiler wick, a cover gasket and separator felt for the oiler lter.
LUBRICATION OF ARV-2020 AND ARV-2030 VACUUM PUMP KITS:
Fill jar to line indicated on “oil level decal” to avoid wetting felt, which would
increase oil feed. Use SOCONY DTE LIGHT OIL OR EQUIVALENT PETRO-
LEUM BASE OIL WITHOUT DETERGENTS. One lling should last 20-50
hours of operation. For slower feed, pull wick downward so that less wick is
exposed to air stream. Using the same oil as above, oil the motor bearings
yearly with 1/2 teaspoon or 30 drops.

9
PARTS LIST / CIR-O
ITEM QTY PART NO. DESCRIPTION
1 2 BUG-1996 Fixed Leg & Wheel Assembly
2 3 BUG-1998 Adjustable Leg & Wheel Assembly
3 5 BUG-2010 Wheel w/Bearing
4 1 BUG-2407 Post Assembly (Vertical)
5 1 BUG-2440 Base Post (Block)
6 1 BUG-2915 Torchholder Assembly
7 1 BUG-5100-F DC III Drive Unit Assembly (150:1)
120 VAC 240 VAC BUG-5102-F
42 VAC- BUG-5104-F
8 4 CIR-9002 Oset Leg & Magnet Foot (Optional)
9 4 CIR-9020 Magnet Foot
10 4 CIR-9021 Leg (Specify Length w/Sux)
Lengths Available: 5" (127 mm)
8" (203 mm) 10" (254 mm)
11 1 CIR-1010-3 Twin Hose Assembly 32" (812 mm)
42" (1066 mm) CIR-1010-4
50" (1270 mm) CIR-1010-5
12 1 CON-(3,4,5)000 Ring & Gear Assembly
13 1 CON-(3,4,5)041 Carriage Plate
14 4 CON-1003 Leg-2" (50 mm)
15 1 CON-1042 Center Pin Support Bar
16 1 CON-1043 Center Pin Assembly 9" (228 mm)
17 3 FAS-0986 Fit Hd Soc Sor 5/16-24 x 5/8
18 2 FAS-2736 Fil Hd Set 10-24 x 2-1/4
19 1 GOF-3025 2-Hose Quick-Acting Manifold
20 1 HOB-1025 Rack Stop
21 1 PAN-1015 Rack 22-5/8" (574 mm)
22 1 PAN-1033 Rod Clamp
23 1 PAN-1043 Spacer
24 2 WAS-0230 #10 Washer
CIR-O / PARTS LIST
16
The purpose of the TEMPLATE KIT is to permit cutting of elliptical and
obround holes. The manner of accomplishing this job involves dragging the
torch barrel against a template which is made 11/16" (18 mm) larger on the
radius than the cut-out desired (when using standard US machine torches).
The TEMPLATE KIT consists of a master layout template (aluminum sheet),
which is used to locate the bolt holes and center on the actual template which
should be made from 1/8" (3 mm) masonite or similar material.
A full-size drawing of the shape to be cut, should be made showing a center
point, then add 11/16" (18 mm) to the radius. (Because the torch body drags
against the template, adding one-half the diameter of the torch to the drawing
will put the center of the torch tip in the right position.)
MAKING THE TEMPLATE
Lay the aluminum master layout template on the masonite board. Transfer
the holes from the master by tracing with a pencil or use a quick-drying spray
paint. Next, position the oversized drawing, so that the center point is directly
over the center on the template and the shape is located symmetrically be-
tween the ‘leg holes’ (see sketch Page 17, number 8. Trace [or spray] the
outline onto the template.)
Next, drill the holes in the template. Then, cut-out the outside circle (outside
of the template) and the shape to be cut (on the inside).
MOUNTING THE TEMPLATE
The four CIR-9031 spacer legs should be screwed into the ring gear. (Remove
existing 2" (50 mm) legs.) The template is then placed on these legs and the
2" (50 mm) legs, or 5" (127 mm) legs, when using the recommended CON-
1040 leg and foot assemblies) are screwed - through the template - into the
CIR-9031 spacer legs, which clamp the template under and parallel to the
ring gear. Insert four round head screws (see sketch Page 17, number 12)
through the template - into the alignment bars (see sketch Page 17, number 7.)
SET UP
Place the rod [see sketch Page 17 number 5 in the base post on the carriage.
Slip the tensioning assembly (see sketch Page 17, number 6) on the rod.
Install machine torch in torchholder - make sure torch is straight up-and-down
in both planes. Adjust tensioning assembly so that torch maintains rm contact
with template when carriage is rotated. Connect hoses. Place machine on
work - locate feet and lock in position.
STARTING THE CUT
Lock tensioning assembly so that the torch tip is over scrap area, piece - or
start the cut in starting hole. When preheat is complete start motor (carriage
travel), release tensioning assembly and let it gradually swing to template -
(this action ‘feathers’ the start into the cut.)
TEMPLATE KIT

8
CIR-O / EXPLODED VIEW
20
21
74
11
18
24
22
6
5
13
19
23
17
2
3
16
12
15
1
10
914
8
17
CIR-9030 [FOR CIR-3]
CIR-9040 [FOR CIR-4]
CIR-9050 [FOR CIR-5]
ITEM QTY PART NO. DESCRIPTION
1 1 BUG-2440 Base, Post (Block) - Order separately
2 1 BUG-2915 Torchholder Assembly
3 1 BUG-9180-10 1/8" (22 mm) rod, 10" (254 mm) Long
4 4 CIR-9031 Spacer Leg
5 1 CIR-9032 Aluminum Master Template Guide
(For CIR-3)
6 4 CON-1004 Alignment Bars (included with
Ring Gear Assembly)
7 4 CON-1040 Magnet Foot and Leg Assembly-Order
separately-use of 4 recommended
with this kit
8 4 FAS-0257 Rnd Hd Scr 1/4-20 x 3/4"
9 8 FAS-2553 Soc Hd Cap Scr 1/4-20 x 1-1/2"
(included with Ring Gear Assembly)
10 1 PAN-1009 Tensioner
11 1 PAN-1018 Rod w/Key-10" (254 mm) Long
12 1 PAN-1033 Rod Clamp
13 -------------- Torches are not furnished with kit,
order separately
TEMPLATE KIT / PARTS LIST
24
12
11
13*
1
210
9
8
7
5
6

7
DRIVE UNIT OPERATION
Rotating Cam Knob (B) will move the drive pinion in and out of engagement
with the ring gear.
To lock drive into position, tighten the 1/4-28 Wing Nut (A).
To disengage the drive pinion from the ring gear, loosen the 1/4-28 Wing
Nut (A) and turn Knob (B) counterclockwise. Turn Knob (B) clockwise to
engage the drive pinion with the ring gear, re-tighten the 1/4-28 Wing Nut
(A) to lock in position.
When Power Cord (C) is plugged into the appropriate power source, Pilot
Light (D) will glow. Switch (E) controls the direction of travel, with the cen-
ter position set at “OFF”. Knob (F) controls the speed. Circuit Breaker (G)
protects the unit against overload or electrical faults.
CAUTION: IF THE CIRCUIT BREAKER OPENS, FIND AND CORRECT
THE CAUSE OF FAILURE BEFORE RESETTING.
TECHNICAL DATA
DC III DRIVE UNIT
Power Requirement: BUG-5100-F 120 VAC/50-60/1
BUG-5102-F 240 VAC/50-60/1
BUG-5104-F 42 VAC/50-60/1
Dimensions: 7.12" L x 6.75" W x 6.75" H
(180 x 172 x 172 mm)
Net Weight: 16 lbs. (7.3 kg)
Shipping Weight: 20 lbs. (9.1 kg)
Speed: 2-50 ipm (50-1270 mm/min)
(Measured at Drive Pinion)
Load Capacity: *30 lbs. (14 kg)
[Measured at Drive Pinion]
*Note: Speed and load ratings apply at radius of ring
gear. Speed is proportional to radius at any other
point, and load rating is inversely proportional to
radius.
BUG-5100-F DC III DRIVE UNIT
A
B
E
FDG
C
18
CIR-O WITH ANNULAR CARRIAGE
CIR-3304 CIR-0 III w/ANNULAR CARRIAGE
CIR-4405 CIR-0 IV w/ANNULAR CARRIAGE
CIR-5506 CIR-0 V w/ANNULAR CARRIAGE
ITEM QTY PART NO DESCRIPTION
1 1 BUG-2440 Base, Post (Block)
2 1 BUG-5100-F DC III Drive Unit Assembly (150: 1)
3 1 BUG-9180-10 7/8" (22 mm) Rod, 10" (254 mm) Long
4 1 CIR-1010-3 Twin Hose Assembly 32" (812 mm)
42" (1066 mm): CIR-1010-4
50" (1270 mm): ClR-1010-5
5 1 CIR-5031 Carriage Plate-Annular
6 4 CON-1003 Leg 2" (50 mm)
7 1 CON-(3,4,5)000 Ring & Gear Assembly
8 1 GOF-3025 2-Hose Quick-Acting Manifold
9 1 PAN-1010 Panograph Assembly with Torchholder
5
2
4
8
3
9
1
6
7

6
POWER SUPPLY
The DC III drive operates on 120 volt, (42VAC), (240VAC), 50/60 Hz. The Circuit
Breaker (O) protects the unit against overload or electrical faults,
CAUTION: IF THE CIRCUIT BREAKER OPENS, FIND AND CORRECT THE
CAUSE OF FAILURE BEFORE RESETTING.
TORCH
The Torchholder (P) will accept any standard American machine torch (barrel
diameter 1-3/8" (34 mm) with 1/4"-square (6 mm) 32-pitch rack). The 32-pitch
pinion is standard. Specify a 24-pitch pinion if desired. The Short Hose As-
sembly (Q) connects the torch to the Quick-acting Manifold Assembly (R).
The supply hoses are to be connected to the open side of the quick-acting
manifold assembly.
Proper torch operation is essential to quality cuts. We suggest that you follow
the torch manufacturers’ instructions carefully, being sure to use a clean tip of
the proper size.
MAGNETIC SUPPORTS
Several Types of magnetic supports are available for use with the CIR-O to
stabilize the machine as listed below:
(S) Outrigger Support Assemblies; CON-1010 - used in multiples of two
or four to stabilize CIR-O on plate, cylinders or heads where two legs must
be longer than the other two,
(T) Magnet Foot Assemblies; CIR-9000 - may be used in sets of four or
more to position CIR-O on vertical or out-of-position, at surfaces.
(U) Leg and Magnet Foot Assemblies; CON-1040 (four required) - may be
used for at or irregular surfaces.
(V) Oset Leg and Magnet Assemblies; CIR-9002 (four required) - use with
a bevel cutting head or adjustable tip adaptor - to eliminate the “blind” spot
under the ring.
SETUP
A center-punch mark and a radius mark are the only layout required. The Center
Pin Assembly (Z) extends below the CIR-O base and is placed in the center-
punch mark. The CIR-O is then eased down to the work on the center pin. This
movement locates the entire machine “on center.” The Rack (W) with Torch-
holder (P) is then positioned over the radius mark.
OPERATION
In order to provide a smooth start, it is recommended that the starting hole be
drilled or pierced inside or outside the radius mark. Center the torch tip over the
radius mark and secure the Rack Stop (X) rmly against the Post Assembly
(Y). [The side of the post assembly to which the rack stop is positioned depends
upon whether the material inside or outside the cut is scrap]. Begin the cut from
the starting hole and, after carriage travel is begun, move the Torch Rack (W)
slowly against the Rack Stop (X). This action “feathers-in” the cut eliminating
a notch.
OPERATING INSTRUCTIONS (CONT’D.)
19
CIR-O SPEED RANGE CHART
Capacities and Speed Ranges
3 .4-8 75 10-210
6 .8-16 150 20-420
10 .4-28 250 35-700
14 2-39 350 50-1000
26 3.5-70 650 90-1805
30 4-80 750 105-2100
34 4.5-92 850 120-2400
38 5.2-105 950 130-2640
42 5.7-115 1050 150-3000
46 6.3-125 1140 160-3200
50 6.8-135 1250 175-3500
56 7.6-155 1420 200-4000
3 .3-5 75 7-140
6 .6-11 150 14-280
10 .9-18 250 23-460
14 1.3-26 350 32-650
18 1.7-33 450 42-840
22 2-40 550 50-1000
34 3.2-63 850 80-1600
38 3.5-70 950 87-1760
42 3.9-78 1050 97-1950
46 4.3-85 1150 105-2130
50 4.6-93 1250 115-2300
54 5-100 1350 125-2500
58 5.4-110 1450 135-2700
64 6-120 1625 150-3000
3 .2-4 75 5-100
6 .4-8 150 10-210
10 .7-13 250 17-350
14 1-19 350 42-500
18 1.3-25 450 32-640
22 1.5-30 550 38-760
26 1.8-37 650 45-900
30 2-41 750 52-1050
42 2.9-57 1050 73-1458
46 3.2-63 1150 80-1600
50 3.4-68 1250 87-1750
54 3.7-75 1350 94-1900
58 4-80 1450 100-2000
62 4.3-85 1550 105-2150
66 4.5-90 1650 115-2300
72 4.9-100 1825 125-2500
DIAMETER
IPM
INCH IPM
DIAMETER
INCH
CIR-III
INSIDE
RING
CIR-IV
CIR-V
OUTSIDE
RING
INSIDE
RING
OUTSIDE
RING
INSIDE
RING
OUTSIDE
RING

5
INTRODUCTION
Your new CIR-O is ready for operation when you receive it. A few minutes
spent reading the following will help you become familiar with the operation
and capabilities of your machine.
The CIR-O Carriage (C) should operate freely on the Ring Track (D). The
carriage has three adjustable Wheel Logs (A). By loosening the Flat Socket
Head Screws (B) these logs may be rotated for adjustment. To check Wheel
(AA) adjustment, hold one wheel and move the carriage. When properly
adjusted the wheel should barely slip.
The Cam Clutch (E) engages the drive pinion to the Ring Gear (F) by chang-
ing the position of the Drive Module (I). The Thumb Nut (H) locks the Cam
Clutch (E) in position.
Turning the Potentiometer Knob (K) regulates speed. The Switch (J)
controls forward-o-reverse. Throw the switch in the direction you want the
carriage to travel.
The CIR-O is furnished with four symmetrically-located Legs (L). A variety
of Magnetic Feet and legs (S), (T), (U), and (V) are available to increase
the versatility of the CIR-O machine.
OPERATINGINSTRUCTIONS
X
YWP
F
D
S
U
L
T
V
C
R
AA
A
B
O
Q
I
KJEH
Z
20
PROBLEM CAUSE REMEDY
Does not run- No power to Check power line supply voltage.
Indicator light o. machine. Plug in line cord rmly.
Does not run, Wiring shorts. Disconnect machine and
indicator light o. examine internally; rewire at fault.
Circuit breaker
tripped. If none found, throw direction switch
to ‘OFF’, reset breaker and plug in.
Shorted motor. If breaker does not trip, replace
drive unit.
Faulty speed If breaker trips again, replace
control board. control board.
(OR)
Burned out
transformer. Replace transformer.
Does not run. Bad connection. Check wiring connections, 12 VAC
indicator light on. should appear across secondary
of transformer.
Tighten terminal screws on speed
control board.
Faulty speed If DC Volts = 0 across leads to
control board. motor; replace control board.
Unit runs, but no Faulty speed Replace control board.
control over speed. control board. (Check connection rst).
NOTE:
Make sure unit is pugged into correct voltage.
(120 VAC, 240 VAC, 42 VAC) corresponding to model number rating.
12 VAC should appear across secondary of transformer in all DC III Drive
Units.
TROUBLESHOOTINGGUIDE
Table of contents
Other Bug-O Systems Welding System manuals
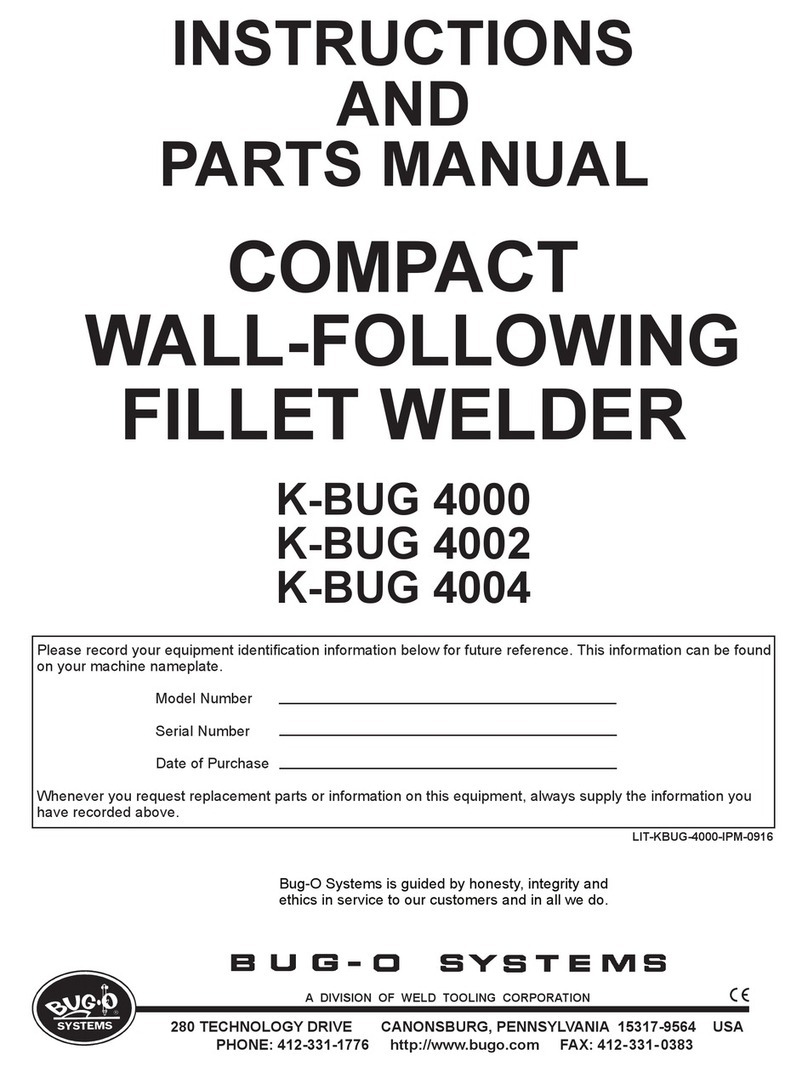
Bug-O Systems
Bug-O Systems K-BUG 4000 Technical reference manual
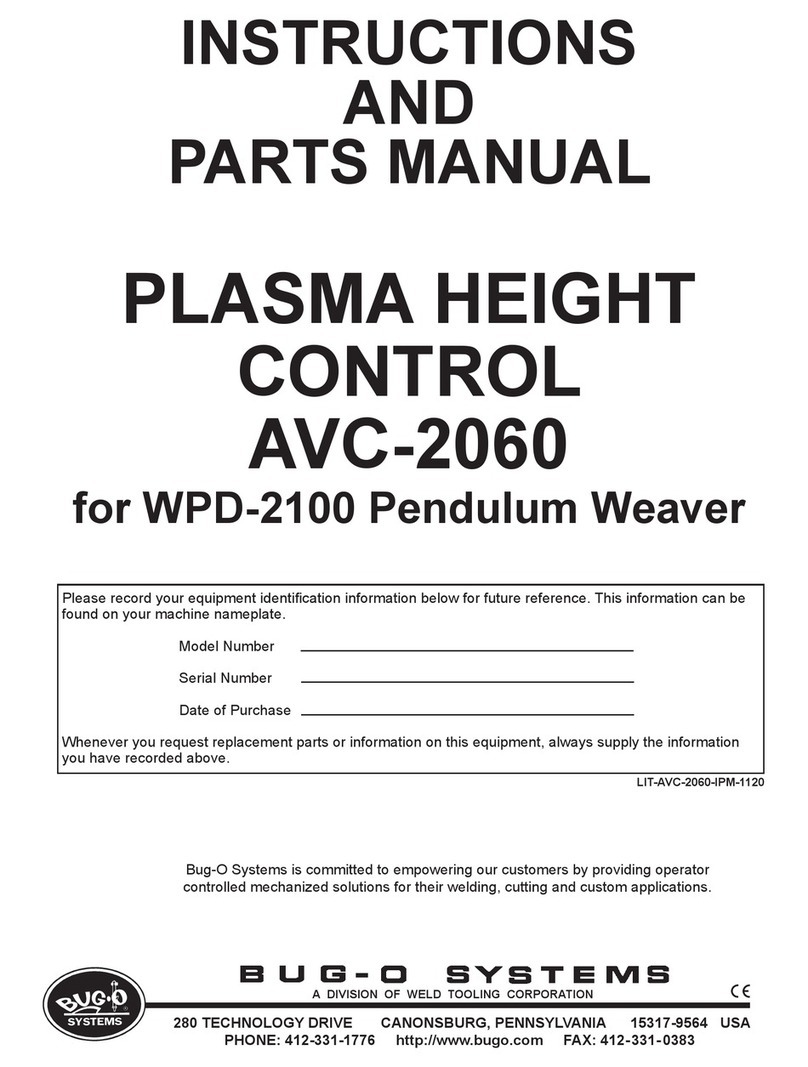
Bug-O Systems
Bug-O Systems AVC-2060 Technical reference manual
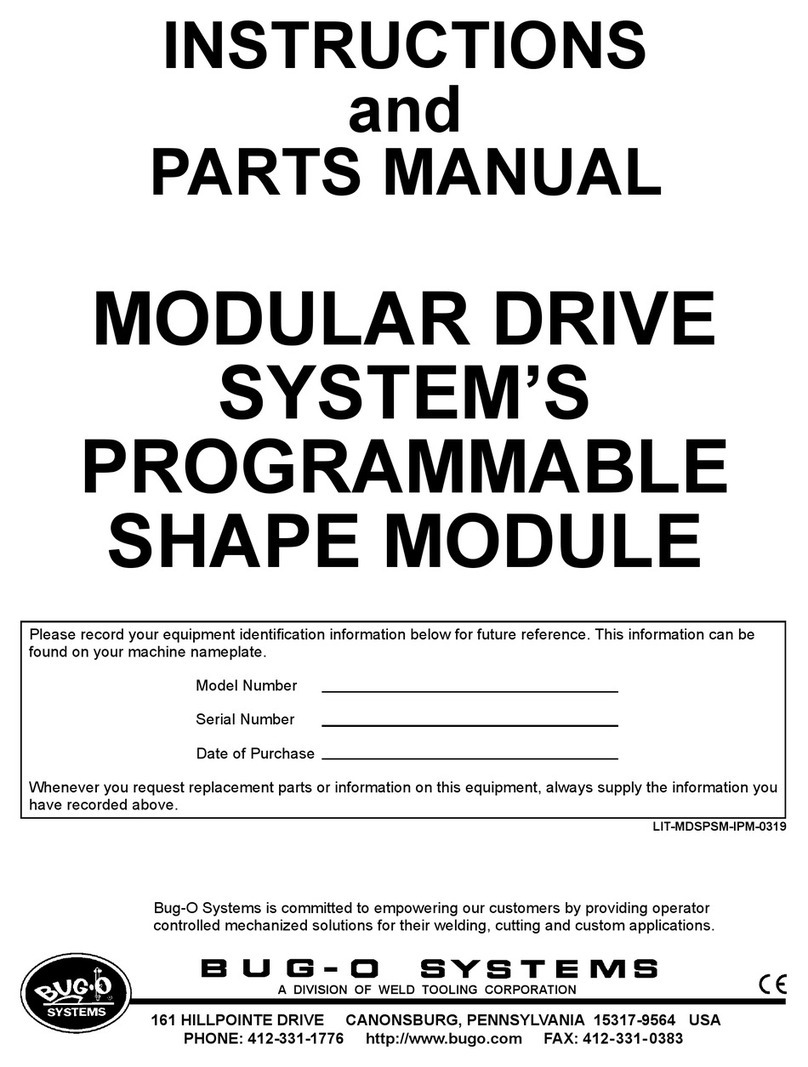
Bug-O Systems
Bug-O Systems MDS Series Technical reference manual
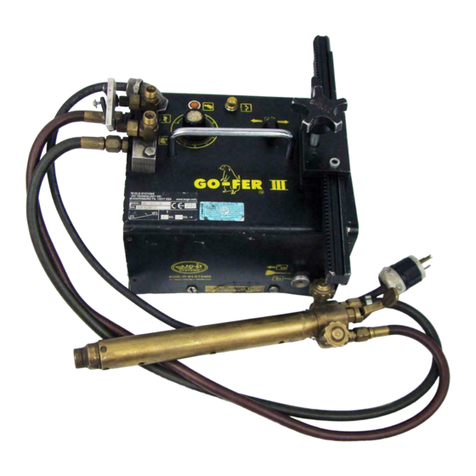
Bug-O Systems
Bug-O Systems GO-FER III-OX Technical reference manual
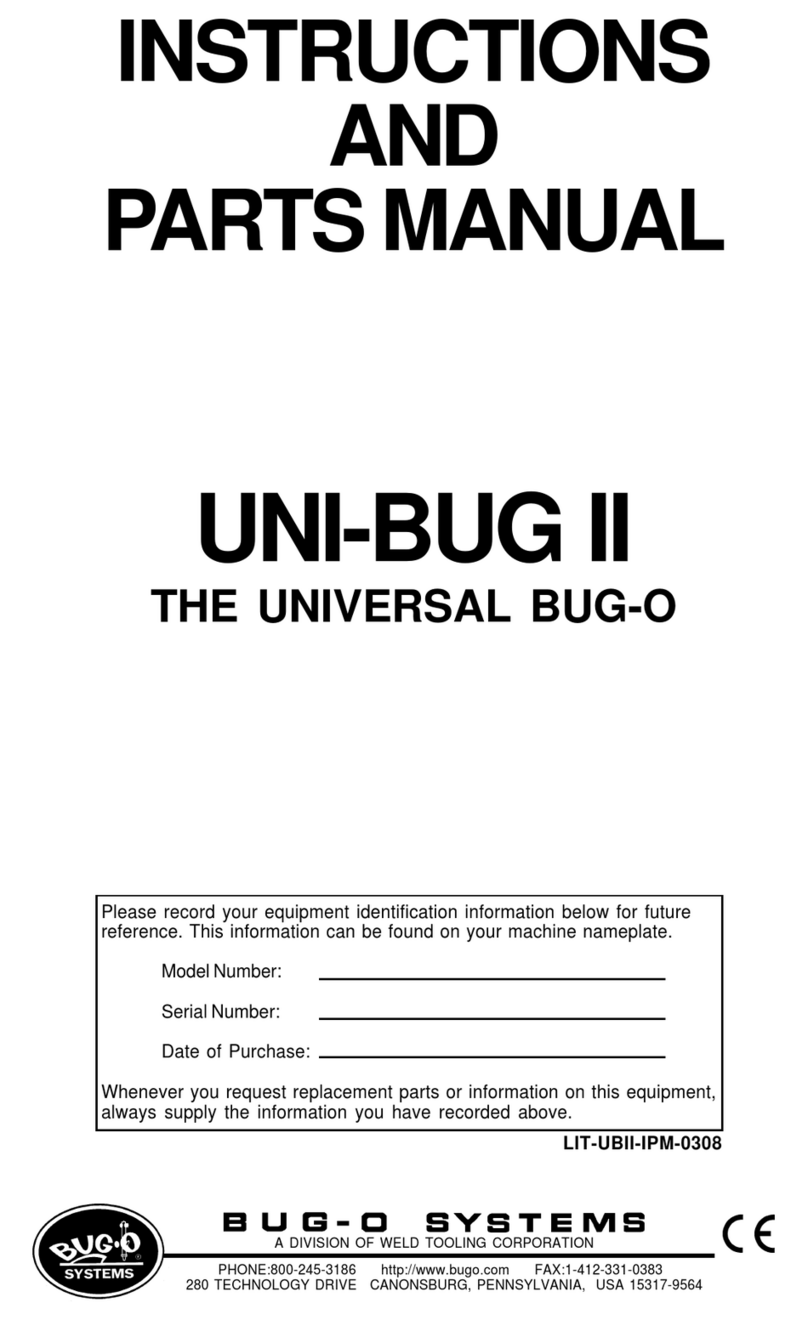
Bug-O Systems
Bug-O Systems UNI-BUG II Technical reference manual
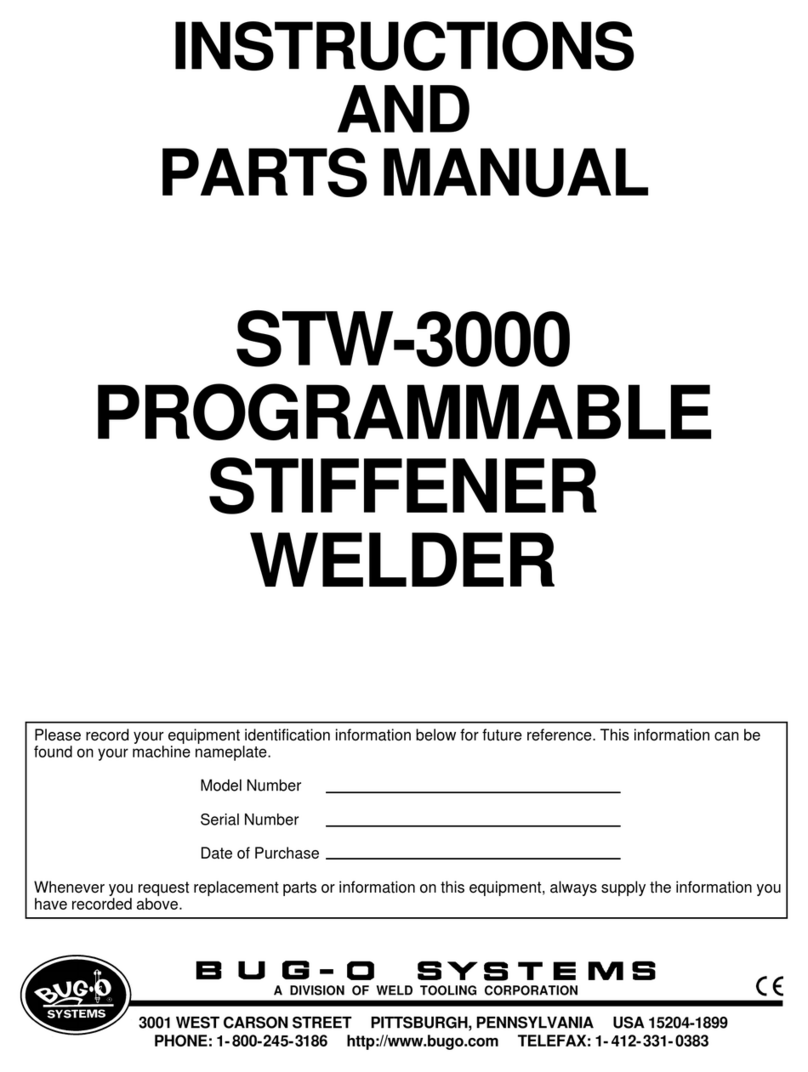
Bug-O Systems
Bug-O Systems STW-3000 Technical reference manual