Bug-O Systems STW-3000 Technical reference manual

INSTRUCTIONS
AND
PARTSMANUAL
STW-3000
PROGRAMMABLE
STIFFENER
WELDER
A DIVISION OF WELD TOOLING CORPORATION
3001 WEST CARSON STREET PITTSBURGH, PENNSYLVANIA USA 15204-1899
PHONE: 1-800-245-3186 http://www.bugo.com TELEFAX: 1-412-331-0383
Please record your equipment identification information below for future reference. This information can be
found on your machine nameplate.
Model Number
Serial Number
Date of Purchase
Whenever you request replacement parts or information on this equipment, always supply the information you
have recorded above.

2
1. The equipment is not waterproof.
Using the unit in a wet environment
may result in serious injury. Do not
touch equipment when wet or standing
in a wet location.
2. The unused connectors have power on
them. Always keep the unused
connectors covered with the supplied
protective panels. Operation of the
machine without the protective panels
may result in injury.
3. Never open the equipment without
first unplugging the power cord or
serious injury may result.
4. Verify the customer-supplied power
connections are made in accordance
with all applicable local and national
electrical safety codes. If none exist,
use International Electric Code (IEC)
950.
5. Never remove or bypass the equipment
power cord ground. Verify the
equipment is grounded in accordance
with all applicable local and national
electrical safety codes. In none exist,
use International Electric Code (IEC)
950.
Read the instruction manual before
installing and using the equipment.
1. Do not plug in the power cord without
first verifying the equipment is OFF
and the cord input voltage is the same
as required by the machine or serious
damage may result.
2. Always verify both the pinion and
wheels are fully engaged before
applying power or equipment damage
may occur.
3. Do not leave the equipment
unattended.
4. Remove from the worksite and store
in a safe location when not in use.
Faulty or careless user installation is
possible. As a result, never stand or
walk underneath equipment.
1. Never try to stop the pinion from
moving except by removing power
or by using the STOP control.
2. Do not remove any protective panels,
covers or guards and operate
equipment.
PROTECT YOURSELF AND OTHERS FROM SERIOUS INJURY OR DEATH. KEEP
CHILDREN AWAY. BE SURE THAT ALL INSTALLATION, OPERATION, MAINTENANCE
AND REPAIR PROCEDURES ARE PERFORMED ONLY BY QUALIFIED INDIVIDUALS.
ELECTRIC SHOCK can kill.
READ INSTRUCTIONS.
EQUIPMENT DAMAGE
POSSIBLE.
FALLING EQUIPMENT
can cause serious
personal injury and
equipment damage.
MOVING PARTS can
cause serious injury.
SAFETY

3
HIGH FREQUENCY WARNINGS
SPECIAL PRECAUTIONS ARE REQUIRED WHEN USING PLASMA,
TIG OR ANY WELDING PROCESS THAT USES HIGH FREQUENCY
TO STRIKE AN ARC.
WARNING: HIGH FREQUENCY CAN EFFECT MACHINE
OPERATION AND THEREFORE, WELD QUALITY
Read the precautions below before installing and using the equipment.
PRECAUTIONS:
1) Some plasma or welding cables are strong sources of high frequency
interference. NEVER lay a plasma or welding cable across the controls of the
machine.
2) Always physically separate the plasma or welding cable leads from the machine
cables. For example, the plasma or welding cable leads should NEVER be
bundled with a pendant cable or the machine power cord. Maximize the separa-
tion between any machine cables and the plasma or weldingcables.
3) Strictly follow the grounding procedures specified for the plasma or welding unit.
NOTE: Some plasma and welding units produce exceptionally large amounts of
high frequency noise. They may require a grounding rod be driven into the earth
within six feet (2 meters) of the plasma or welding unit to become compatible
with an automatic cutting or welding process.
4) If the high frequency is produced using a spark gap, adjust the points so the gap
is as small as possible. The larger the gap, the higher the voltage and the higher
the interference.
5) Some plasma or welding units will inject high frequency interference into the AC
power line. Use separate power line branches whenever possible to power the
plasma or welding source and the machine. Do not plug them into the same
outlet box.
6) High frequency noise may enter the machine through the plasma or welding
supply remote contactor leads. Some plasma and welding sources can produce
noise spikes of up to several thousand volts. These sources are notcompatible
with automated cutting and welding equipment. It is recommended that the
remote contactor leads on these plasma or welding sources not be connected to
the machine. An alternate solution is to purchase a separate remote contactor
isolation box.

4
LIT-STW-3000-IPM-0506
Patents Pending
5...Introduction / Set-Up&Operation
6...Controls (Main)
7...Controls (Programming Center)
9...TechnicalData/ Dimensions
10 ..(STW-3000)StiffenerWelder / Major Components /PartsList
11... Wiring Detail
12 ..Wiring Detail / ElectricalComponent Chart
13 ..(STW-2140-L)CornerFollowerLeft/ExplodedView/Parts List
14 ..(STW-2140-R)CornerFollowerRight/ExplodedView/PartsList
15 ..(STW-2150-L) Gun HingeLeft / ExplodedView / Parts List
16 ..(STW-2150-R)GunHingeRight/ExplodedView/Parts List
17 ..(STW-2170-A)CaptureWheelAssembly“A”/Exploded View / Parts List
18 ..(STW-2170-B)CaptureWheelAssembly“B”/Exploded View / Parts List
19 ..(STW-2115) DriveLatch / Exploded View / Parts List
20 ..(STW-2060)Flow-Meter&ValveAssembly/Exploded View / Parts List
21 ..(STW-2120)DriveUnitAssembly/ExplodedView
22 ..(STW-2120)DriveUnitAssembly/PartsList
23 ..(STW-2195) Spool Support Bracket / Exploded View / Parts List
24 ..Accessories (Spools)
25 ..Warranty
TABLE OF CONTENTS
STW-3000
PROGRAMMABLE STIFFENER WELDER
INSTRUCTIONS AND PARTS MANUAL

5
INTRODUCTION:
The Programmable Stiffener Welder mechanizes two wire feeders to weld various types of stiffeners on
one or both sides simultaneously. The unit features independent wire feeder controls for voltage, wire
feed speed, cold wire jog and gas purge. When intermittent stitch welding is required the unit feature
programmable control of weld length and travel speed, skip length, reverse drive crater fill, pre-weld
and post-weld gas purge times. Please see the Technical Data information in this manual for unit
capacities.
SET-UP & OPERATION:
(Refer to the Controls Sections pg. 6, 7 and Major Components section pg. 9, 10 in this manual.)
1. Center the unit over the work piece. Connect welding cables and wire feeder control cables for each
feeder to the welding power sources. Connect the welding gas hoses to each Flow Meter/Valve
Assembly. Plug the unit into an available 110 VAC 50/60 Hz power source.
2. Turn power “ON” to both welding power sources. Turn power “ON” to the control panel by toggling
the “ON/OFF” switch on the upper rear right hand side of the control box to the “ON” position. Ensure
both welding torches are active by toggling the Weld Contactor Switches located on each side of
the control box to the “ON” position.
NOTE: Ensure that the Emergency Stop Switch located on the top of the control box is in the released
position. If the Emergency Stop Switch remains depressed, no input power will be supplied to the unit.
3. Adjust the Capture Wheel Assemblies so that they contact the side of the work. Swing the Drive
Unit into position against the work piece and engage the Drive Latch and tighten to ensure constant
pressureon the workpiece between the DriveAssembly, Work Piece and Capture WheelAssemblies.
NOTE: Move the unit forward and reverse using the Travel Manual Jog switch located on the front
lower left of the control box to ensure proper tension has been applied by the Drive Latch to move the
unit smoothly along the work piece.
4. Align the left and right Corner Followers and welding guns for the desired weld placement. The
Corner Followers canbe adjustedup, down, in and out to achieve the placementyou desire.Coarse
torch angle adjustment should be made with the positioning of the corner followers. The
Corner Followers are also equipped with a gun angle adjustment knob to achieve the desired torch
angle and correct position of the welding wire with respect to the joint. Purge the shield gas to each
welding gun by pressing the Shield Gas Purge button located on the left and right sides of
the control panel for each Flow Meter/Valve Assembly.
5. Set all welding parameters. Wire feeder wire speed and voltage are set independently from each
other utilizing the Lincoln LN-10 Controller. All other welding parameters are set using the soft touch
Programming Center. Please refer to the controls section of the manual.
6. When you are ready to begin your weld cycle press the Weld Cycle Start button located on the
control panel below the soft touch Programming Center. To stop the weld cycle pres the Weld
Cycle Stop button.
NOTE: In case of emergency, press the Emergency Stop switch located on the top of the control box
to kill all power to the unit including the weld cycle. Once the Emergency Stop switch is returned to the
released position you will need to press the Cycle Start button to resume your cycle.

6
CONTROLS (MAIN):
VOLTAGE CONTROL: Set on Lincoln LN-10 Control.
WIRE SPEED CONTROL: Set on Lincoln LN-10 Control.
WIRE JOG: Jog wire forward and reverse using the controls on the Lincoln LN-10 Control.
WELD CONTACTOR ON/OFF SWITCH: Allows operator to turn the contactor on or off for the
assigned welding torch.
SHIELD GAS PURGE: Allows operator to activate shield gas solenoid to purge welding gun and
check the gas rate on the assigned regulators.
MAIN WELD CYCLE START: Initiates automated weld cycle.
MAIN WELD CYCLE STOP: Halts automated weld cycle.
TRAVEL MANUAL JOG: Allows operator to move the unit forward or backward without welding.
EMERGENCY STOP: When pressed causes all functions to stop.
PROGRAMMING CENTER: See controls for programming center pg. 7.
Programming Center
Emergency Stop
Shield Gas
Purge (A)
Main Weld
Cycle Start
Travel
Manual
Jog
Main Weld
Cycle Stop
Shield Gas
Purge (B)
Weld
Contactor
SwitchA
Weld
Contactor
Switch B

7
CONTROLS (PROGRAMMING CENTER):
DIGITAL DISPLAY: Visual display to supply welding motion information to operator.
SHIELDING GAS PREFLOW: Programmable time to allow the flow of shielding gas prior to striking
the arc.
TRAVEL SPEED: Speed at which the unit moves during welding.
WELD LENGTH: Distance the unit travels forward while welding in Skip mode.
BACKUP DISTANCE: Distance the unit travels in reverse after completed weld length.
SHIELDING GAS POSTFLOW: Programmable time to allow the flow of shielding gas after the arc
has extinguished.
SKIP LENGTH: Distance between welds. (Must include backup distance).
INCREASE VALUE: Pressing this button increases the value shown in the digital display.
DECREASE VALUE: Pressing this button decreases the value shown in the digital display.
FUNCTION SELECT: Allows the user to cycle through the welding programming functions.
SKIP/CONTINUOUS MODE SELECT: Allows the user to select skip mode or continuous mode for
the welding operation.
SKIP WELD INDICATOR LIGHT: When illuminated the machine will weld in skip mode.
CONTINUOUS WELD INDICATOR LIGHT: When illuminated the machine will weld in continuous
mode.
Note: It is possible to change from Continuous to Skip welding “on-the-fly”. To change modes, press
the Continuous/Skip Select button. If the machine is making a continuous weld, the backup
function and postflow will occur immediately. The machine will move the programmed skip distance
and proceed to make the programmed skip welds. If the machine is making a skip weld, the machine
will continue to weld until the Continuous/Skip Select button or the Stop button is pressed.
PUDDLE DELAY:
There are two internal settings in the Control Module that do not appear in the normal setting
selection on the control panel keypad/display. These are time delays at weld start and stop, when
the wire feed is on but travel is stopped, in order to allow for puddle buildup.
To set the time delays:
1. Power off, (power switch on back of control box); hold Cycle Stop button in, and turn power
on. Release Stop button. LED No.1 and 3 should light; and the display shows the start puddle
buildtime.
2. Adjust delay time as required using UP and DOWN arrow buttons.
3. Briefly push Function Select (cycle settings) button. LED No. 3 and 5 should light, and display
shows the end crater fill time.
4. Adjust delay time as required.
5. Push Function Select button again, then power off.
6. Power on to operate machine as usual, now with new settings in place.

8
Weld
Length
Travel Speed
Preflow Time
Increase Value
Decrease Value Skip Weld
Indicator
Function Select Continuous
Weld Indicator
Continuous/Skip
Select
Skip Length
Postflow Time
Backup Distance
Digital Readout
CONTROLS(PROGRAMMINGCENTER CONT’D.):

9
TECHNICALDATA:
Programmable Weld/Skip Travel Speed: 0"-36" ipm (0-900mm/min)
Programmable Reverse Drive Crater Fill: 0"-1" (0-25mm)
Programmable Pre-Weld/Post Weld Gas Purge: 0-10 seconds
Net Weight: 250 lbs. (113 kg)
Stiffener Size Range: Height 4"-18" (102-457mm)
Width 4"-12" (102-305mm)
Wire Spool Capacity: 10, 20, 60 lbs. each side
DIMENSIONS:
23.000
(58.42cm)
48.657
(123.6m) 25.470
(64.7 cm)
52.063
(132.2cm)

10
(STW-3000) STIFFENERWELDER/MAJORCOMPONENTS /PARTSLIST
ITEM QTY PART NUMBER DESCRIPTION
1 1 Lifting Plate / Control Mount
2 1 Lincoln DM-10 Feeder
3 2 Lincoln LN-10 Wire Feeder Control
4 1 STW-2140-L Corner Follower Left
5 1 STW-2140-R Corner Follower Right
6 1 STW-2150-L Gun Hinge Left
7 1 STW-2150-R Gun Hinge Right
8 1 STW-2170-A Capture Wheel Assy. “A”
9 1 STW-2170-B Capture Wheel Assy. “B”
10 4 STW-2142 3" Phenolic Caster
11 1 STW-2115 Drive Latch
12 2 STW-2060 Flow Meter / Valve Assy.
13 2 STW-2190-18 Leg 18"
14 1 STW-2066 Left Leg Support
15 1 STW-2067 Right Leg Support
16 2 STW-2151 Wheel Mt. Plt.
17 1 STW-2054 Deck Plt.
18 1 STW-2120 Drive Unit
19 1 STW-2195 Spool Support Bracket
20 1 STW-1050 STW Motion Control Box
2
13
10
11
14 13 64
5
7
20
3
1
12
17
13
10 8
15 13 910
16
18
16
19

11
WIRINGDETAIL
See Electrical Component Chart pg. 11

12
WIRINGDETAIL / ELECTRICALCOMPONENT CHART
ELECTRICAL COMPONENT CHART
ITEM PART # DESCRIPTION
CB1 BUG-2923 .7 AMP CIRCUIT BREAKER
PC1 BUG-1770 MOTOR CONTROL BOARD
PC2 PCB-2231 RELAY BOARD
PC3 STW-2235 CONTROL MODULE
PM1 BUG-9486 PANELCONNECTOR, 2-T,M
PM2 BUG-9486 PANELCONNECTOR, 2-T,M
PM3 CON-06RP04F SHELL 18, RECEPTACLE, PANEL
PM4 CON-06RP04F SHELL 18, RECEPTACLE, PANEL
PM5 CON-04RP03M SHELL 16S, RECEPTACLE, PANEL
PM6 BUG-9856 PANEL CONNECTOR, 2-T,F
SW1 SWT-EPF3 ROUND, FLUSH, GREEN SWITCH
SW2 SWT-EPF4 ROUND, FLUSH, RED SWITCH
SW3 BUG-2255 TOGGLE SWITCH, DPDT, ON OFF ON
SW4 SWT-1111 NOR, OPEN PUSH BUTTO, BLACK
SW5 SWT-1111 NOR, OPEN PUSH BUTTO, BLACK
SW6 SWT-5225 TOGGLE SWITCH
SW7 SWT-5225 TOGGLE SWITCH
SW8 ARM-2279 TOGGLE SWITCH, DPST, ON NONE ON
SW9 SWT-EPFH ROUND, MUSHROOM, LATCHINH, RED SWITCH
T1 BUG-5001 120 VAC -20VAC TRANSFORMER

13
(STW-2140-L)CORNERFOLLOWERLEFT/EXPLODEDVIEW/PARTSLIST
ITEM QTY PART NUMBER DESCRIPTION
1 1 ARM-2358-4.1 Leg 4-1/8"
2 1 WPD-2041 Clamp Block
3 1 BUG-2708 Clamp
4 1 BUG-1857 Knob w/Set Screw
5 4 BUG-2593 Glide “Flat”
6 2 BUG-2841 Washer 5/8" O.D. x 5/16" I.D.
7 1 CON-1029 Washer 5/16" x .015" Thk.
8 1 FAS-0453 Set Scr 1/4-20 x 1/4" HDP
9 1 FAS-0535 Soc Hd Cap Scr 10-24 x 1/2"
10 1 FAS-0557 Soc Hd Cap Scr 1/4-20 x 3/4"
11 2 FAS-0654 Soc Hd Shd 5/16" x 3/8" x 1/4-20
12 2 FAS-0957 Flt Hd Soc 1/4-20 x 3/4"
13 1 MUG-1515 Collar
14 1 PAN-1235 Slide Assy.
15 1 PAN-2125 Mounting Arm Assy.
16 1 PAN-2131-L Mounting Plate, Left
17 1 PAN-2133-L Slide Plate
18 1 PAN-2134 Screw Retainer
19 1 PAN-2135 Screw Block
20 1 PAN-2136 Adjusting Screw
21 1 PAN-2137 External Retaining Ring
22 1 WAS-0230 #10 SAE Washer
13
1
15
14
10
922 16
5
12 21 17 611
19
2
20
8
7
4
18
3

14
ITEM QTY PART NUMBER DESCRIPTION
1 1 ARM-2358-4.1 Leg 4-1/8"
2 1 WPD-2041 Clamp Block
3 1 BUG-2708 Clamp
4 1 BUG-1857 Knob w/Set Screw
5 4 BUG-2593 Glide “Flat”
6 2 BUG-2841 Washer 5/8" O.D. x 5/16" I.D.
7 1 CON-1029 Washer 5/16" x .015" Thk
8 1 FAS-0453 Set Scr 1/4-20 x 1/4" HDP
9 1 FAS-0535 Soc Hd Cap Scr 10-24 x 1/2"
10 1 FAS-0557 Soc Hd Cap Scr 1/4-20 x 3/4"
11 2 FAS-0654 Soc Hd Shd 5/16" x 3/8" x 1/4-20
12 2 FAS-0957 Flt Hd Soc 1/4-20 x 3/4"
13 1 MUG-1515 Collar
14 1 PAN-1235 Slide Assy
15 1 PAN-2125 Mounting Arm Assy
16 1 PAN-2131-R Mounting Plate, Left
17 1 PAN-2133-R Slide Plate
18 1 PAN-2134 Screw Retainer
19 1 PAN-2135 Screw Block
20 1 PAN-2136 Adjusting Screw
21 1 PAN-2137 External Retaining Ring
22 1 WAS-0230 #10 SAE Washer
(STW-2140-R)CORNERFOLLOWERRIGHT/EXPLODEDVIEW/PARTSLIST
1
15
13
14
10
922 16
5
12 21 17
611
18
4
7
8
20
19
2
3

15
(STW-2150-L) GUN HINGE LEFT / EXPLODED VIEW / PARTS LIST
ITEM QTY PART NUMBER DESCRIPTION
1 1 STW-2151 Wheel/Hinge Plate
2 1 STW-2152 Hinge Plate “A”
3 1 STW-2154 Hinge Plate “C”
4 1 STW-2155 Hinge Rod
5 1 STW-2156 Mounting Bar
6 1 STW-2158 Vertical Mounting Rod
7 1 STW-2159 SS Pin 1/8" Diameter x 1"
8 1 STW-2160 Clamp Block (Round/Square)
9 1 STW-2168 Hinge Plate “E”
10 1 STW-2178 Knurled Knob Plunger
11 6 FAS-0559 Soc Hd Cap Scr 1/4-20 x 1"
12 1 FAS-0599 Soc Hd Cap 3/8-16 x 1"
13 2 FAS-2693 Soc Hd Shr 1/2" x 1" x 3/8-16
14 1 FAS-0999 Flt Hd Soc 3/8-16 x 1"
15 1 FAS-1301 Hex Nut 1/2-13
16 1 STW-2165 Clamp Block LG (Round/Square)
13 10
2
4
7
3
1
13
15
12
9
16
5
8
6
14
11

16
(STW-2150-R)GUNHINGERIGHT/EXPLODEDVIEW/PARTSLIST
ITEM QTY PART NUMBER DESCRIPTION
1 1 STW-2151 Wheel/Hinge Plate
2 1 STW-2152 Hinge Plate “A”
3 1 STW-2153 Hinge Plate “B”
4 1 STW-2155 Hinge Rod
5 1 STW-2156 Mounting Bar
6 1 STW-2158 Vertical Mounting Rod
7 1 STW-2159 SS Pin 1/8" Diameter x 1"
8 1 STW-2160 Clamp Block (Round/Square)
9 1 STW-2167 Hinge Plate “D”
10 1 STW-2178 Knurled Knob Plunger
11 6 FAS-0559 Soc Hd Cap Scr 1/4-20 x 1"
12 1 FAS-0599 Soc Hd Cap 3/8-16 x 1"
13 2 FAS-2693 Soc Hd Shr 1/2" x 1" x 3/8-16
14 1 FAS-0999 Flt Hd Soc 3/8-16 x 1"
15 1 FAS-1301 Hex Nut 1/2-13
16 1 STW-2165 Clamp Block LG (Round/Square)
16 5
8
6
3
14 13
12
9
10
15
7
4
2
13
1
11

17
(STW-2170-A)CAPTUREWHEELASSEMBLY“A”/EXPLODEDVIEW/PARTSLIST
2
10
1
12
4
5
3
13
11
8
7
6
9
ITEM QTY PART NUMBER DESCRIPTION
1 1 STW-2135 Hinge Bearing Block
2 1 STW-2138 Shaft Collar 3/4" I.D.
3 1 STW-2173 Follower Hinge
4 1 STW-2174 Five Lobe Knob / Insert
5 1 STW-2175-A Female Tube Weldment
6 1 STW-2179 2" Caster / Iron Wheel
7 1 STW-2180 Male Tube Weldment
8 1 FAS-0454-Cone Set Scr 1/4-20 x 3/8" Cone Point
9 4 FAS-0555 Soc Hd Cap Scr 1/4-20 x 1/2"
10 4 FAS-2554 Soc Hd Cap Scr 1/4-20 x 1-3/4"
11 1 FAS-0455-HDP Set Scr 1/4-20 x 1/2" Half Dog
12 1 SPR-1001-LH Left Follower Spring

18
(STW-2170-B)CAPTUREWHEELASSEMBLY“B”/EXPLODEDVIEW/PARTSLIST
2
1
12
3
5
8
7
6
911
13
4
10
ITEM QTY PART NUMBER DESCRIPTION
1 1 STW-2135 Hinge Bearing Block
2 1 STW-2138 Shaft Collar 3/4" I.D.
3 1 STW-2173 Follower Hinge
4 1 STW-2174 Five Lobe Knob/Insert
5 1 STW-2175-B Female Tube Weldment
6 1 STW-2179 2" Caster/Iron Wheel
7 1 STW-2180 Male Tube Weldment
8 1 FAS-0454-Cone Set Scr 1/4-20 x 3/8" Cone Point
9 4 FAS-0555 Soc Hd Cap Scr 1/4-20 x 1/2"
10 4 FAS-2554 Soc Hd Cap Scr 1/4-20 x 1-3/4"
11 1 FAS-0455-HDP Set Scr 1/4-20 x 1/2" Half Dog
12 1 SPR-1001-RH Right Follower Spring

19
(STW-2115) DRIVE LATCH / EXPLODED VIEW / PARTS LIST
ITEM QTY PART NUMBER DESCRIPTION
1 4 FAS-0557 Soc Hd Cap Scr 1/4-20 x 3/4"
2 1 STW-2116 Drive Latch Weldment
3 1 STW-2118 Screw 1/2-13 x 3-1/2"
4 1 STW-2119 Level Mount
5 1 STW-2174 Five Lobe Knob Insert 1/2-13 RT
6 4 WAS-0240 1/4" SAE Washer
1
6
5
3
4
2
6
1

20
(STW-2060)FLOW-METER&VALVEASSEMBLY/EXPLODEDVIEW/PARTSLIST
ITEM QTY PART NUMBER DESCRIPTION
1 1 ARV-1113 1/4 NPT 900 Street Elbow
2 1 BUG-9096 Outlet Bushing, Oxygen, Right
3 1 BUG-9102 Magnetic Valve For Use With Oxygen
4 1 CIR-1012 Hose Nut, Oxygen, Right Hand
5 1 CIR-1013 1/4" Hose Nipple
6 1 CIR-1016 Hose Clamp 9/16" Crimp Type
7 2 FAS-0545 Soc Hd Cap Scr 10-30 x 1/2"
8 1 STW-2061 Argon Flowmeter
9 1 STW-2062 Modified Cord Grip
10 1 STW-2063 1/4" I.D. Hose Barb
11 1 STW-2064 Inert Gas Male RH
12 2 STW-2065 Clamp 2-Ear 8-11mm
13 1 CON-PS04M Plug, Straight, 4 Pin, Male
NS 26" 1000-4-002 1/4" I.D. x 3/8" O.D. Tube
3
2
9
8
10
11
45 612
1
7
13
Table of contents
Other Bug-O Systems Welding System manuals
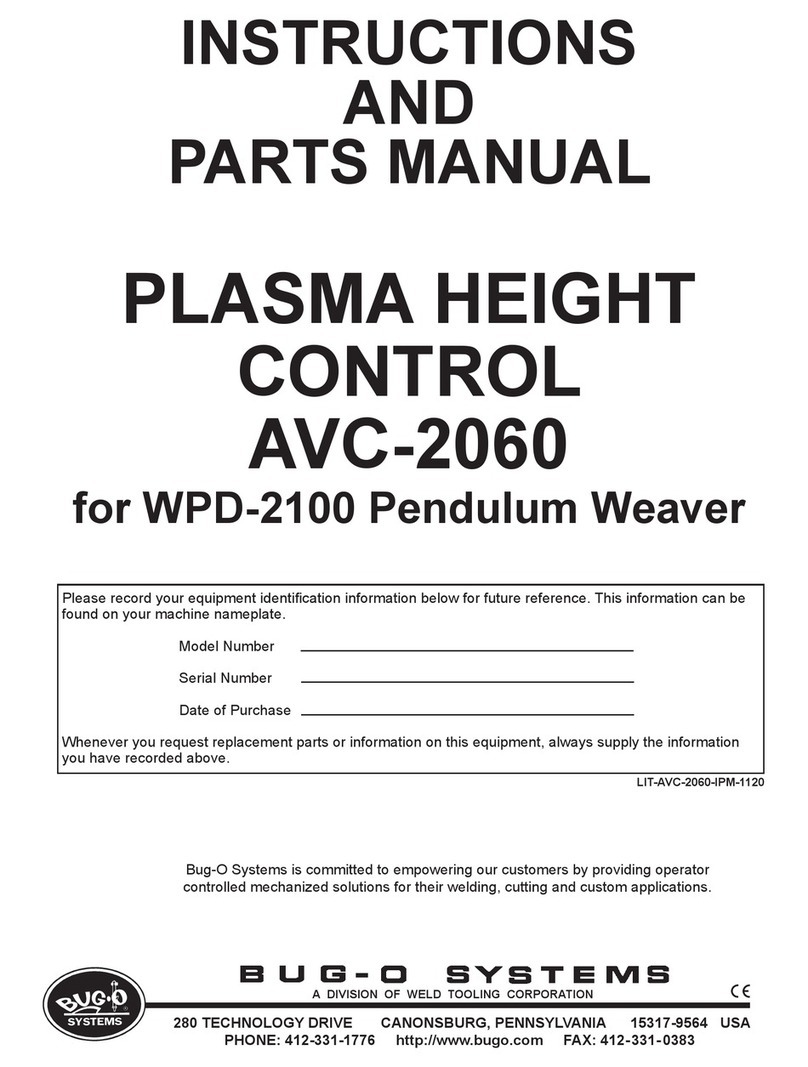
Bug-O Systems
Bug-O Systems AVC-2060 Technical reference manual
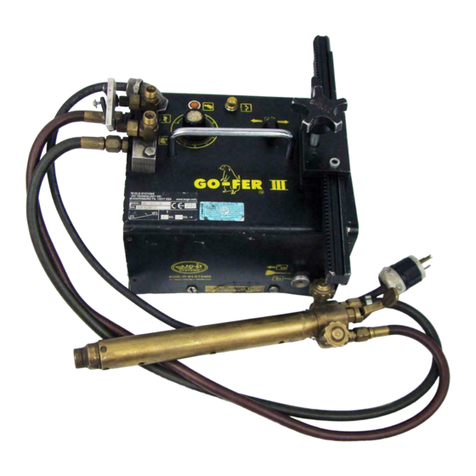
Bug-O Systems
Bug-O Systems GO-FER III-OX Technical reference manual
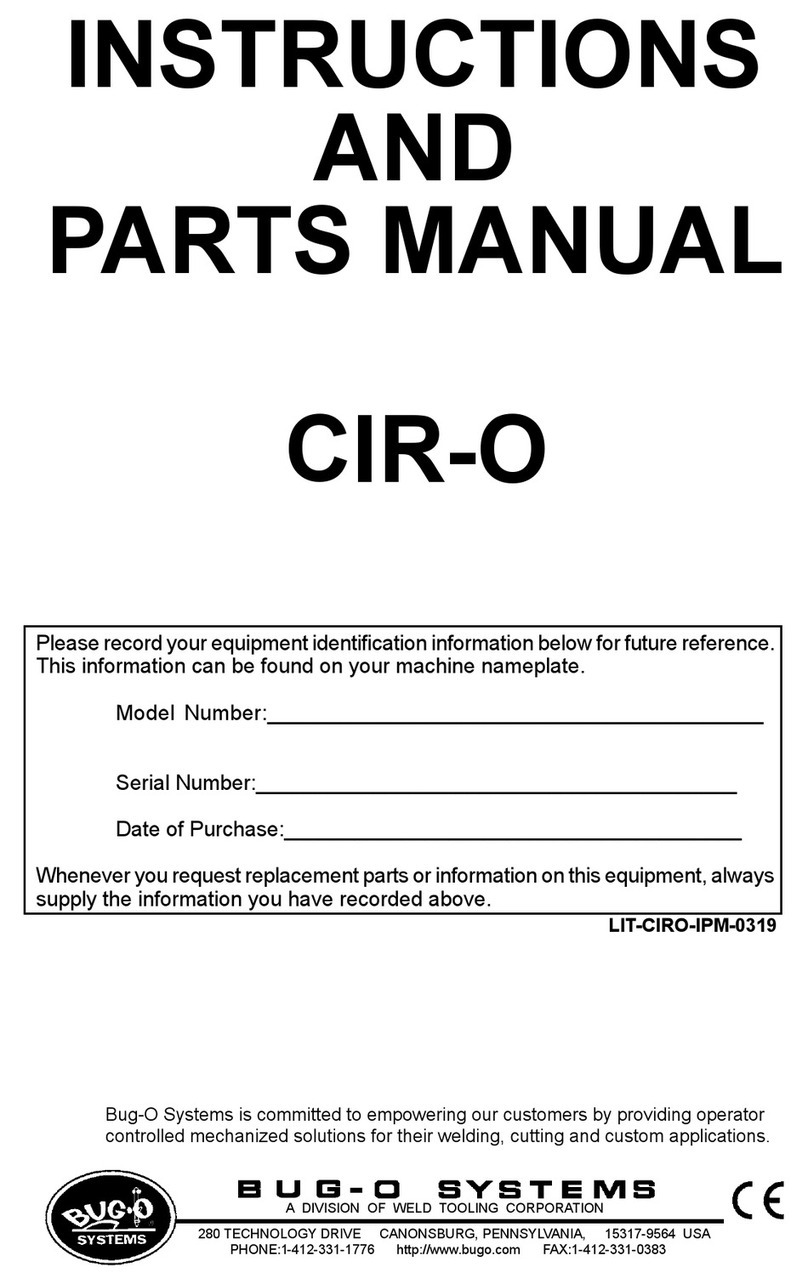
Bug-O Systems
Bug-O Systems CIR-O Technical reference manual
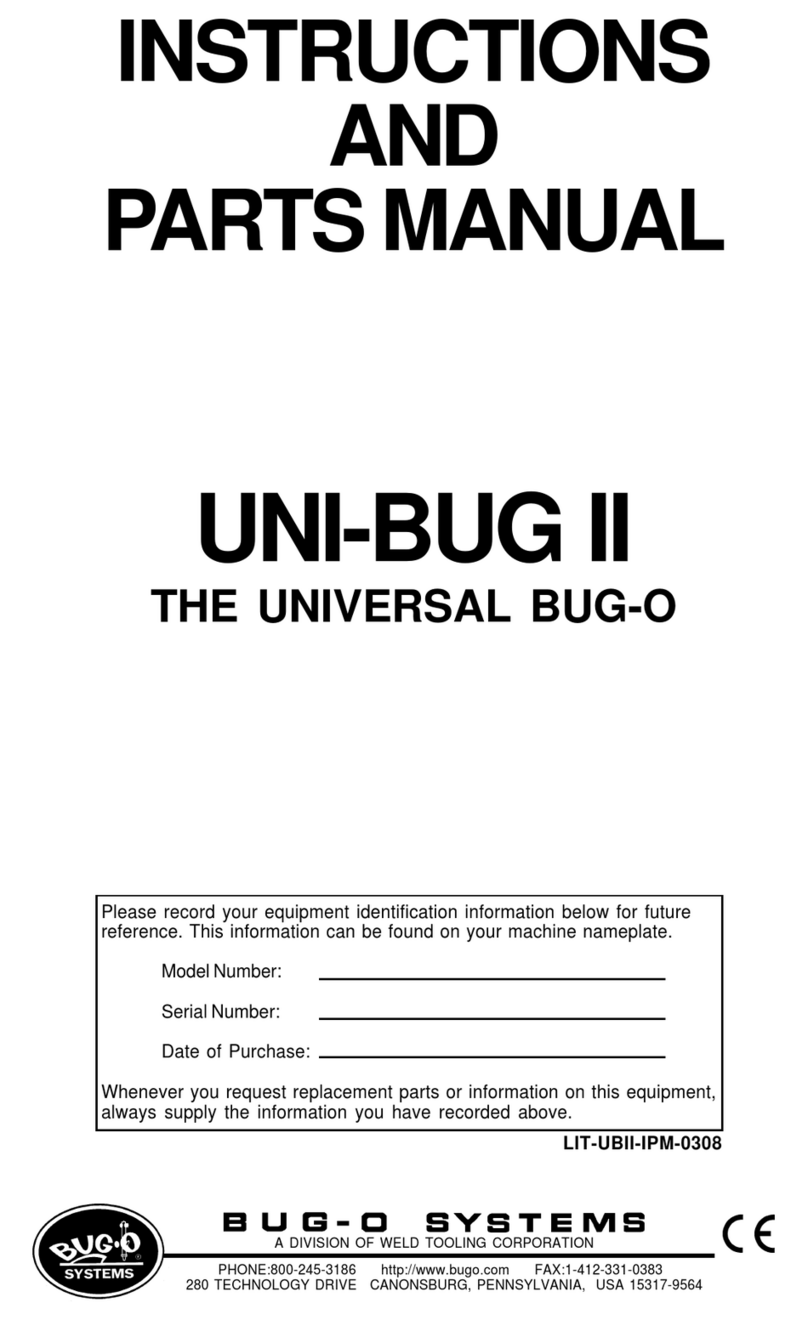
Bug-O Systems
Bug-O Systems UNI-BUG II Technical reference manual
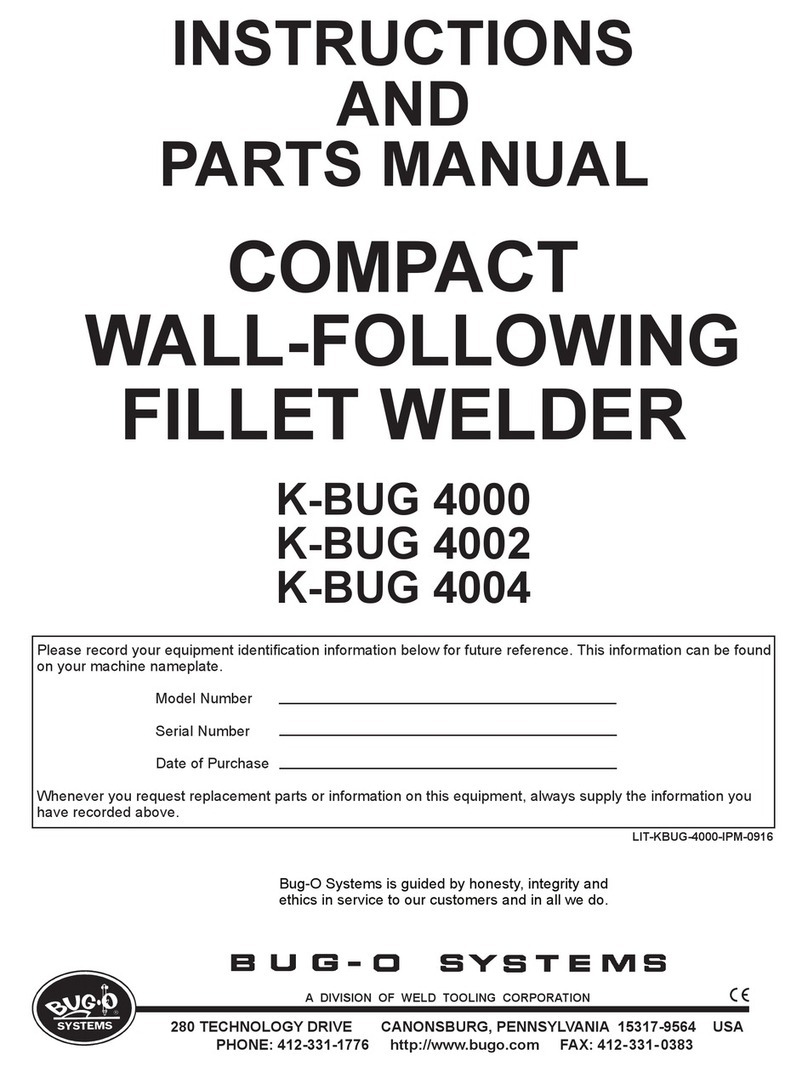
Bug-O Systems
Bug-O Systems K-BUG 4000 Technical reference manual
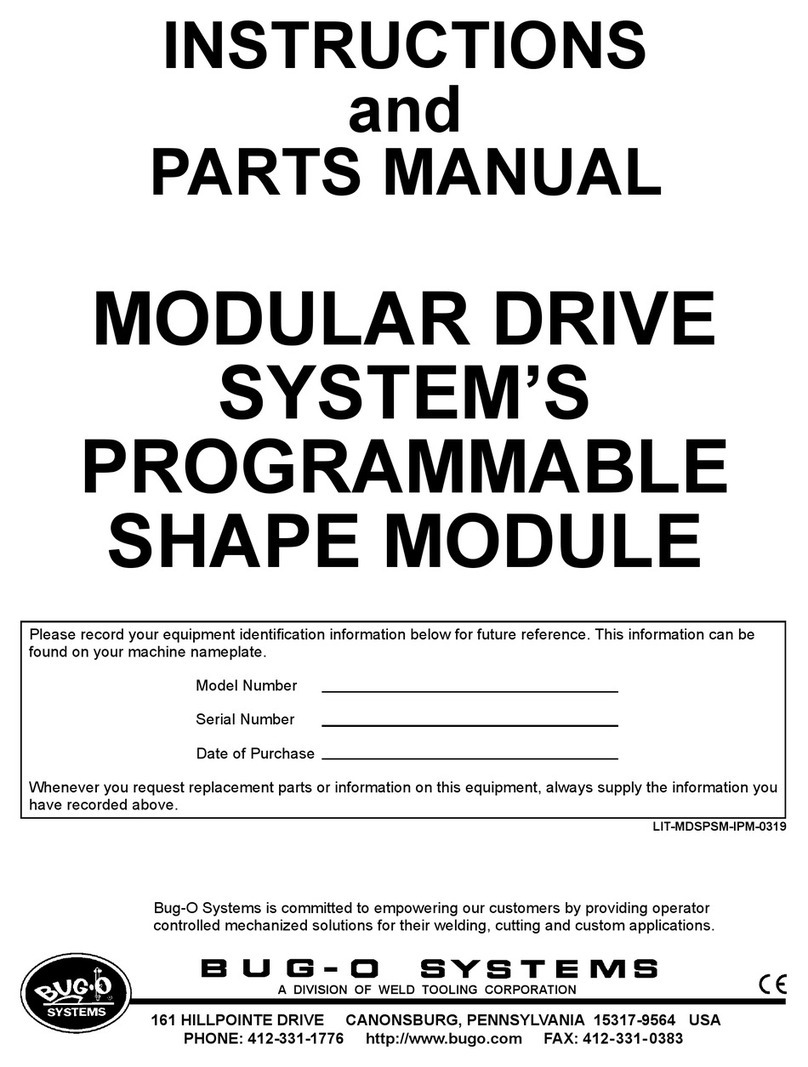
Bug-O Systems
Bug-O Systems MDS Series Technical reference manual