C-Tech 16-T0012/P User manual

I
Dynamic Cone Penetrometer 16-T0012/P

I
CONTENTS
I. Introduction .....................................................................................................................................................1
II. Security ............................................................................................................................................................1
III. Description ......................................................................................................................................................3
IV. Operation .........................................................................................................................................................5
V. Technical data .............................................................................................................................................. 10
VI. Maintenance ................................................................................................................................................ 11
Warranty Card ...................................................................................................................................................... 15
Packing List .......................................................................................................................................................... 16

-1 -
I. Introduction
Below you will find important information on how to use the pneumatic ram probe 16-T0012/P,
referred to in the further text 16-T0012/P.
A suitable compressor is required to operate the 16-T0012/P. This compressor must be designed for
the operation of the pneumatic ramming probe and have the required performance data.
Appropriate use
The 16-T0012/P is approved and intended only for light and medium-heavy ramming probes in
accordance with DIN 22476-2, in combination with a compressor. It may not be used for any other
purpose.
Warranty claim and operating licence expire in case of improper use. Operating with a compressor
not approved by the manufacturer may result in serious safety defects and the expiry of the operating
licence and warranty.
Liability
In the event of improper use or technical modifications, the manufacturer's liability is generally
excluded.
Guarantee
The legal warranty is 12 months from the date of purchase. Wear parts are excluded from the
warranty. The warranty expires in case of manipulation of the device.
II. Security
Read the following section carefully, which contains important information about your personal safety
and product protection.
Responsibility of the user

-2 -
As a user of the 16-T0012/P, you are responsible for the intended handling. Conscientiously instruct
employees and invite them to read the manual. Never leave the device unattended in the area to
prevent abuse by third parties, such as children.
ATTENTION-Note in this manual
Note highlighted "ATTENTION". A "ATTENTION" is always subject to imminent damage to the product
caused by improper handling or operation contrary to the information provided in this manual.
WARNING-Note in this manual
Note highlighted "WARNING." A "WARNING" always appears in the event of imminent danger to the
user or third parties due to improper handling of the product or an operation contrary to the
information provided in this manual.
General safety instructions
In the case of negligent use of the 16-T0012/P, risks of injury are possible, for example:
Blows due to the falling ramming weight
Blows by tipping down the 16-T0012/P by breaking a component
Damage to hearing in case of non-compliance with hearing protection recommendations
Protective equipment
The user of the 16-T0012/P must wear the following protective clothing:
1. Helmet
2. Hearing protectors
Stay at the device
Maintain a safety distance of at least 1 meter to the 16-T0012/P in operation to prevent injury due

- 3 -
to the device falling down (e.g. in case of breakage).
Always stay in the immediate range of the regulating valve or compressor unit when operating the
16- T0012/P to enable immediate shutdown in the event of malfunctions or hazards.
Maintenance intervals
The regular operation of the 16-T0012/P requires regular maintenance, which must be carried out
daily or at larger intervals, depending on the maintenance point.
A list of the necessary testing and maintenance work can be found in chapter 6.1.
In order to ensure safe operation of the 16-T0012/P, you are obliged to have the work carried out by
a qualified person in accordance with the maintenance list.
WARNING!
Neglecting maintenance intervals can lead to damage to man or machine!
III. Description
Below you will find information on the structure of the 16-T0012/P and the controls.
View and structure

- 4 -
NO.
Name
NO.
Name
NO.
Name
NO.
Name
1
Cylinder handle 5 B type pin 9 Round nut 13 bolt
2
Briquetting 6 handle 10 Circlip 14 Briquetting
3
20kg hammer 7 Connector 11 piston 15 Cylinder
4
Flat end 8 Trachea joint 12 Nuts
Scope of delivery and accessories
Packing List
1 10kg weight and cylinder with handle
1 set of four-stroke gasoline engine and air compressor, with hose connector, with bracket 1
additional 20kg hammer
1 air hose
12 probe rods φ22*1000mm, with scale marks every 100mm 1 instruction manual
2 spanners 19mm for 22mm probe 12 threaded connectors M16

- 5 -
1 set extractor
2 5CM2cone heads
2 10CM2cone heads
20 10CM2disposable cone heads
1 M8 Allen wrench
1 set of safety rod device
Safety components
Safety pin with cotter pin to secure the ram probe on the striker.
2 safety bars for guiding the ram probe at the start of the probing.
WARNING!
The use of safety components increases occupational safety and is mandatory.
IV. Operation
The Operation section provides you with the information you need to put the PR13 into operation
immediately. Particular attention is drawn to possible dangers for humans or machines. However,
read section 2 "Safety" before reading further here and putting the PR13 into operation.
Check rule maintenance
1. Is the interior of the cylinder oiled with a suitable lubricant and is the piston rod free of dirt? (see
5.2) Check the resistance-free fall of the ram weight.
2. Is the service cone greased?
3. Are there safety bolts and cotter pins for the striking piece?
4. Is the inner assembly O-ring for the piston lock undamaged and in position? (Slowly pull out
the cylinder tube and check the upper stop)

- 6 -
Location
WARNING!
Operation of a compressor with a combustion engine in closed rooms is excluded
and can lead to life-threatening poisoning.
Set up
Screw the striking piece onto the probe rod and place the 16-T0012/P with the anvil on the striking
piece. Insert the safety bolt through the holes in the anvil and striker and secure it with the split pin.
Put the open pipe end of the main safety rod over the safety bolt (see picture) and secure with a pin.
Insert the open end of the air hose regulating valve into the quick coupling on the safety rod.
For better stability when setting up the ramming probe with additional weight, the auxiliary securing
rod can be placed at right angles to the main securing rod on the socket of the main securing rod
and secured with a plug. The ram probe can be held and guided safely by 2 people.
WARNING!
Always keep a safety distance of at least 1 meter during operation and wear a hard
hat.

- 7 -
DPL operation
DPM operation, 2x fuse recommended
Push
the
open pipe
end over the safety bolt of
the
ram probe
and
secure it with a
pin.
Support
socket for auxiliary safety rod, starting
at a
right angle.
Regulating valve, inserted in the hose
section of the safety rod.
Main safety rod
Auxiliary safety bar (2-man operation
recommended for probing approach
with additional weight)

- 8 -
Configure ramming weight (according to DIN 22476-2)
DPL(10kg drop weight X 0.5m drop height):
Operation without additional weight.
DPM (30 kg drop weight x 0.5 m drop height):
Add additional weight with the side of the larger inner diameter forward via the ram probe and place
on the impact socket of the 16-T0012/P. Slide the fastening clamp all the way to the additional weight
and tighten it well. Make sure that the blow-off hole, which is now behind the additional weight,
remains free.
Perform ramming
1. The compressed air supply line from the appropriate compressed air source (technical data see
5.1) must be provided with the appropriate clutch nipple on the exit side.
ATTENTION!
Observe the required performance data of the compressed air source (see 5.1).
Operating with too high pressure or unsuitable air can lead to damage to the 16-
T0012/P and risk of accidents.
2. When the compressor is off, spray oil through the plug-in clutch nipple into the hose line, or lift
the cylinder tube slightly and spray oil through the now visible gap above the control seal.
3. With the regulating valve open, connect the compressed air hose to the brass coupling of the
ram probe. The ram probe starts to beat when the regulating valve is closed and can thus be set
to the desired number of strokes per minute.
The ram probe must not hit top dead center, but must trigger and fall down before the cylinder
is fully extended and strikes. Striking the upper end of the piston rod leads to falsified
measurement values and can damage the device and lead to accidents.
WARNING!
If the piston rod limit is broken, there is a risk of injury if the ram cylinder jums out
of the piston rod guide.

- 9 -
ATTENTION!
A lack of lubrication, wear or contamination can lead to malfunctions, e.g. the
ramming cylinder comes into contact with the upper end of the piston rod. Bumping
against the upper end of the piston rod falsifies the probing result and can break the
piston rod limit.
NOTE: Renew the piston rod limitation (see chapter "Maintenance": Mounting O-ring inside 22 x
4 mm,) after each malfunction as described above and remedy the cause. Possible causes can
be: Wear of plastic pistons or valve control plates, contamination of the cylinder barrel,
insufficient lubrication or wrong lubricant as well as too little or too much air supply.
WARNING!
Keep a safety distance of at least 1 meter from the 16-T0012/P in operation to
prevent injuries caused by the device falling down (e.g. in the event of a break); a
blow to the head or body can lead to serious injuries.
NOTE: Remove the safety bar (s) as soon as the ram linkage stands alone and straight in the
ground. Long- term operation with the safety rod attached considerably increases the wear of
the safety bolt.
4. You can stop the ram probe at any time by opening the regulating valve or switching off the
compressor unit.
NOTE: Protect the ram probe from contamination. With every probe, check that there is sufficient
lubrication (perfect triggering at top dead center and free fall of the ram weight) and lubricate
with Spray if necessary.
Transport
Secure the 16-T0012/P for transport with the supplied transport clip. It prevents the ram cylinder
from extending unintentionally and protects the piston from dirt and damage. Make sure that the
brass coupling is inside the intended hole to protect it from damage. Secure the inserted transport
clasp with bolts and split pin.

- 10 -
V. Technical data
Specifications
Length
850 mm
Max diameter
102 mm (without additional weight)
Total weight
130 kg
Ramm weight
10 kg
Additional weights
1 x 20 kg for DPM, optional
Drop height
0.5 m
Required air volume
max. 15,000 l/h Max.
Operating pressure
approx. 1.0 bar
Guaranteed sound power level
106 dB(A)
Resources
Lubricant: available in DIY stores and specialist retailers
Compressed air source: Compressor unit.
Connection coupling
turned inwards in a
protected position.

- 11 -
VI. Maintenance
Below you will find information on maintenance and maintenance of the 16-T0012/P. Read this
section carefully as inadequate care and inadequate maintenance can result in damage.
NOTE: Always turn off the compressed air source or unplug the hose line before performing
maintenance or cleaning.
Service device
Maintenance list
Measure
Interval daily
Interval
see operating instructions
chapter
Check cylinder interior oiling and lubrication of
the impact cone
● 1/2 Bh - 6.1.1
Check the function of the upper cylinder stop
●- 6.1.2
Disassemble and clean the device
- as needed 6.1.3
Abbreviations: Bh = Hours of operation
1. Regular oiling of the interior of the cylinder is necessary for the proper operation of the ram probe.
With the compressor switched off, spray Ballistol oil through the disconnected coupling nipple
into the hose line, or lift the cylinder tube a little and spray oil through the now visible gap above
the control seal.
The conical impact surface of the piston rod should have a thin layer of grease (universal multi-
purpose grease), the lubrication surface is visible when the cylinder barrel is raised a few
centimeters.
2. Check the function of the upper cylinder tube stop before each probing operation. To do this, pull
the cylinder tube completely out until it stops and check that the stop is seated consistently. The
stop consists of an O-ring held in a groove and can be damaged if the ram probe malfunctions
repeatedly (the cylinder strikes the upper end of the piston rod during operation). A damaged O-
ring must be replaced immediately. To replace the O-ring, please proceed as described below.

- 12 -
3. The proper function can be restricted by using an unsuitable lubricating oil (resin spray oils ) or
by improperly placing the ram probe in the field.
Proceed as follows to dismantle and clean the ram probe:
①.Senkrecht vertically.
②.Remove two M6 x 25 screws for the traverse. The traverse now rises a few millimeters.
③.Lift the cylinder tube a few centimeters and push the valve ring down until the outer
assembly O-ring is exposed. Remove the O-ring from its groove and pull the now exposed
Ventilschaft
Traverse with
Screws M6 x 25 (medium-tight glued)
Ventilring
Outer mounting- O-ring
PA pistons
Inner Mounting-O-ring with fuse sea
ring

- 13 -
control head upwards out of the cylinder barrel.
④.To dismantle the cylinder tube, the locking circlip and the inner assembly O-ring are now
removed from the piston rod and the cylinder tube is pulled off upwards. The piston is now
in the cylinder barrel and is carefully pushed out with a non-metallic rod (e.g. wooden handle).
NOTE: Do not use sharp objects for cleaning. After cleaning, lubricate all parts with or
another non-resinous oil spray.
⑤.Carefully put the cylinder tube back on the piston rod. Carefully guide the impact side of the
pipe over the piston rod so as not to damage the plastic lining inside the impact cone. Let
the cylinder ear rest on the impact cone.
⑥.Put the piston back on the fit at the upper end of the piston rod
and secure it with the inner assembly O-ring and circlip. The
circlip must lie all the way around the O-ring in the piston rod
groove and must not be able to move axially.
⑦.Reassemble the control head in reverse order. Secure the two
M6 x 25 screws of the traverse with medium-strength screw
adhesive.
⑧.Let the cylinder ear fall onto the cone several times to check that it falls without resistance.
Remove unnecessary lubricants.
Setting the control head
1. The total amount of the control valve should be approx. 7 mm. Check the game between open
and closed control plate when the cylinder tube is raised. The adjustment is made by the in- or
out-turning of the two counter nuts on the valve shaft. Counter the nuts after the setting is
finished.
2. When the operating condition is in place, the control plate must not be pressed through the
piston rod to the valve ring, nor shall it have a gap size greater than 2 mm. The gap size can be
adjusted by removing or adding the balancing plate(s). Recommended dimensions:1 - 2 mm.
If the control plate is pressed to the valve ring despite the removal of all compensating plates,
the spring seat must be reworked by a specialist.

- 14 -
Note: all the above showing pics and sketchs are for reference only
Gap 1 – 2 mm

- 15 -
Warranty Card
Produce Name Dynamic Cone Penetrometer Date Of Manufacture
Produce Code 16-T0012/P Inspectors
Warranty Period The warranty period is 1 year from the date of purchase
Maintenance Record Form
Date Fault Conditions Signature Remarks

- 16 -
Packing List
Item.
Label
Number
1
4-stroke gasoline engine and air compressor with hose
connector and bracket
1
2
10kg weight and cylinder with handle
1
3
Additional weight 20kg
1
4
Air hose
1
5
Probe rod φ22*1000mm, with scale mark every 100mm 12
6
user's Guide
1
7
19mm spanner for 22mm probe
2
8
Threaded joint M16 12
9
Extractor
1
9.1 5CM2 cone head
2
10 10CM2 cone head
2
11 10CM2 disposable cone head 20
12 M8 Allen wrench
1
13 Safety rod device
1

- 17 -
Table of contents
Other C-Tech Measuring Instrument manuals
Popular Measuring Instrument manuals by other brands
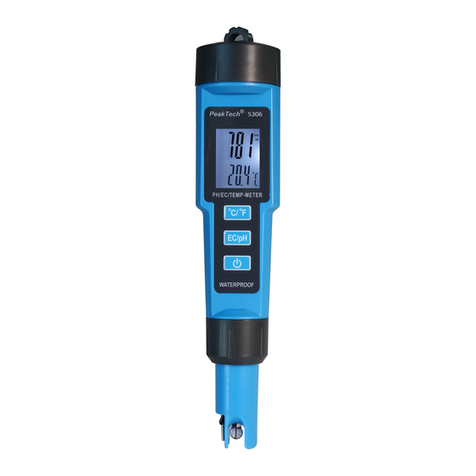
PeakTech
PeakTech 5306 Operation manual
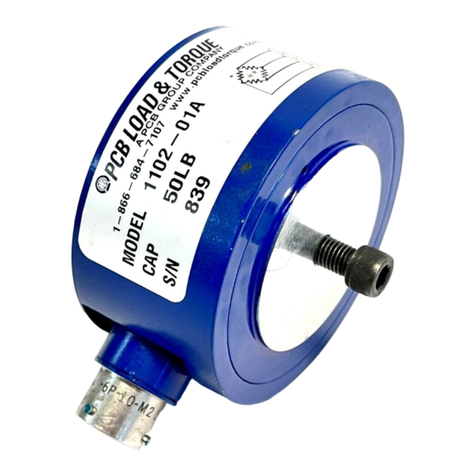
PCB Piezotronics
PCB Piezotronics 1102-05A Installation and operating manual

JUKI
JUKI PS900SB13090CKZ instruction manual
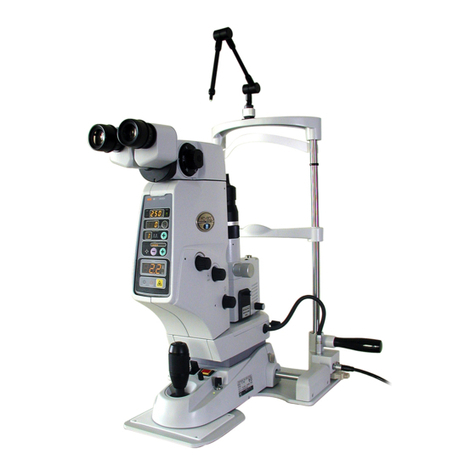
Nidek Medical
Nidek Medical YC-1800 Service manual
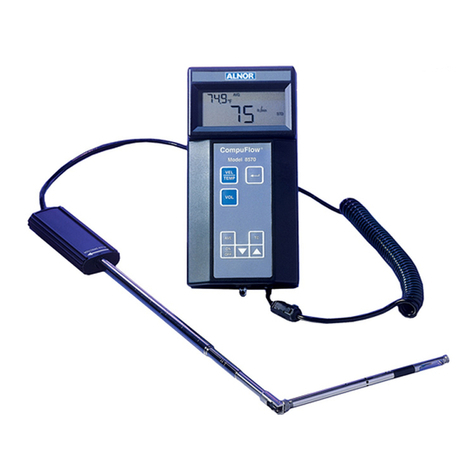
TSI Incorporated
TSI Incorporated Alnor CompuFlow 8570 owner's manual
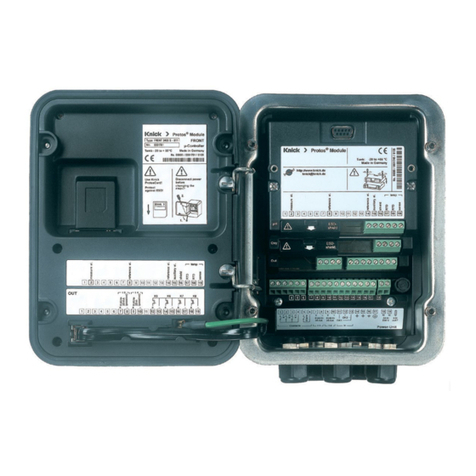
Knick
Knick Protos 3400X user manual