cam ZPH Series User manual

Original
operating manual
Flexibility & experience
Fork positioner
ZPH-series
Operating manual
12/2021 – V01
from serial n°
CC09501

2/40
© 12-2021. CAM attachments is a trademark of TVH Parts Holding NV, Brabantstraat 15, B-8790 Waregem. All rights reserved. No part of this publication may
be reproduced or communicated in any form or by any means, electronic or mechanical, including copying, recording or use in an information storage
or retrieval system, without prior and explicit permission of TVH Parts Holding NV. Printing errors reserved. Photographs and illustrations are included for
reference purposes only.
Responsible editor: TVH Parts Holding NV, Brabantstraat 15, BE-8790Waregem
TVH is a supplier of after-market spare parts and accessories that are suitable for the maintenance and repair of OEM equipment.

3/40
www.tvh.com/zphrv01
BG Bulgarian
Можете да намерите това ръководство на Вашия език чрез линка, посочен по – долу.
CS Czech
Tento návod najdete ve svém jazyce prostřednictvím odkazu níže.
DA Danish
Du kan finde denne vejledning på dit sprog via nedenstående link.
DE German
Sie finden diese Bedienungsanleitung in Ihrer Sprache unter folgendem Link.
EL Greek
Μπορείτε να βρείτε αυτό το εγχειρίδιο στη γλώσσα σας μέσω του παρακάτω συνδέσμου.
EN English
You can find this manual in your language via below link.
ES Spanish
Encontrarás este manual en tu propio idioma a través del siguiente enlace.
ET Estonian
Oma emakeelse juhendi leiate allolevalt lingilt.
FI Finnish
Löydät tämän manuaalin omalla kielelläsi alla olevan linkin taka.
FR French
Vous trouverez ce manuel dans votre langue via le lien ci-dessous.
GA Irish
Tá an lámhleabhar seo ar fáil i do theanga tríd an nasc thíos.
HR Croatian
Ovaj prirucnik mozete pronaci na svom jeziku putem donjeg linka.
HU Hungarian
Ez a kézikönyv az Ön nyelvén az alábbi link alatt található.
IS Icelandic
Hægt er að finna þessa handbók á þínu tungumáli á tenglinum hér að neðan.
IT Italian
Cliccando sul link sottostante troverai il manuale nella tua lingua.
LT Lithuanian
Šį vadovlėlį savo kalba rasite spustelėję žemiau esančią nuorodą.
LV Latvian
Rokasgrāmatu latviešu valodā Jūs varat atrast izmantojot zemāk esošo saiti.
MT Maltese
Tista’ssib dan il-manwal bil-lingwa tiegħek permezz tal-link ta’hawn taħt.
NL Dutch
Je vindt deze handleiding in jouw taal via onderstaande link.
NO Norwegian
Du finner denne håndboken på ditt språk via linken nedenfor.
PL Polish
Niniejsza instrukcja obsługi dostępna jest w Twoim języku za pośrednictwem poniższego linku.
PT Portuguese
Pode encontrar este manual no seu idioma através do link abaixo.
RO Romanian
Puteți găsi acest manual în limba dvs. prin link-ul de mai jos.
SK Slovak
Manuál vo vašom jazyku môžete nájst v priloženom vysvietenom riadku.
SL Slovenian
Ta priročnik najdete v svojem jeziku preko spodnje povezave.
SV Swedish
Du kan hitta denna manual på ditt språk via länken nedan.
TR Turkish
Bu kılavuzu aşağıdaki bağlantıdan kendi dilinizde bulabilirsiniz.

4/40
Thank you for using our product. For your safety and to ensure a correct operation, we would like to
bring to your attention some aspects of this manual:
• This booklet supplies useful instructions for the correct operation and maintenance of the product.
It is therefore necessary to pay the utmost attention to all of the paragraphs that illustrate the most
simple and secure way to operate and use this product.
• This booklet must be considered an integral part of the machine and must be included with the
deed of sale.
• Neither this publication, nor part of it, can be reproduced without written authorisation on the part
of the manufacturer.
• All of the information reported herein is based on data available at the moment of printing;
the manufacturer reserves the right to carry out modifications to its own products at any moment,
without notice and without incurring in any sanction. It is therefore suggested to always check for
possible updates.
The person responsible for the use of the product must make sure that all of the safety rules in force in
the country of its use are applied, to guarantee that the equipment is used in conformity with the use
for which it is destined and to avoid any dangerous situation for the user.
The following warning signs are used in this manual to warn you for dangers and risks:
Informative, be careful.
Warning, can lead to injury and damage if instructions aren’t followed.
Danger, can lead to serious or fatal injury and serious damage if instructions aren’t
followed.
The following conventions are used in this manual:
1 2
46
35
1 Right
2Left
3 Bottom
4Top
5 Front
6 Back
Unless otherwise stated, directions apply as seen from the operator’s control seat when facing
the attachment.

5/40
CONTENTS
1. INTRODUCTION ..................................................................................................... 6
2. DESCRIPTION ........................................................................................................ 7
2.1. Technical data......................................................................................................................7
2.2. Operating pressure and oil flow rate......................................................................................8
2.3. Main components of the product .........................................................................................8
2.4. Placem ent of the decals.......................................................................................................9
2.5. Type plate..........................................................................................................................10
3. SAFETY INSTRUCTIONS .........................................................................................11
3.1. Explanation of the safety decals ..........................................................................................11
3.2. General safety instructions..................................................................................................12
4. TRANSPORT AND STORAGE....................................................................................13
5. ASSEMBLY AND INSTALLATION...............................................................................14
5.1. Packing list.........................................................................................................................14
5.2. Safety instructions for assembly and installation of the product............................................14
5.3. Installation of the product ..................................................................................................14
6. OPERATION..........................................................................................................18
6.1. Safety instructions for operating the product.......................................................................18
6.2. Operating instructions. . . . . . . . . . . . . . . . . . . . . . . . . . . . . . . . . . . . . . . . . . . . . . . . . . . . . . . . . . . . . . . . . . . . . . . . . . . . . . . . . . . . . . . . . . . . . . . . . . . . . . . . 19
7. MAINTENANCE .....................................................................................................21
7.1. Safety instructions for the maintenance of the product........................................................21
7.2. Maintenance schedule .......................................................................................................21
7.3. Maintenance instructions ...................................................................................................22
8. TROUBLESHOOTING..............................................................................................24
9. FINAL DECOMMISSIONING AND DISPOSAL ..............................................................25
10. ANNEXES .............................................................................................................26
10.1. CE certificate......................................................................................................................26
10.2. Hydraulic diagram..............................................................................................................28
10.3. Spare parts list....................................................................................................................29

6/40
1. INTRODUCTION
This manual contains all the necessary information on the installation and operation of the ZPH-fork
positioner.
Some of the maintenance operations should only be carried out by professional technicians. If you
require this information and the maintenance steps, please contact your dealer. Also included in this
manual are a number of safety instructions to create a safe working environment.
The fork positioner allows you to hydraulically move the forks closer together or further apart,
individually or together. These products are applicable to the material handling, warehousing and
manufacturing industries, allowing the forklift driver to accurately adjust the spacing of the forks for
clear and wide view.
Check your machine manual to make sure you opt for the fork positioner with the correct load
capacity. Do not use this product for any other purposes.
Please read the manual thoroughly and observe the safety procedures before putting the unit into
operation. The operator and all persons who come into contact with the equipment should read it
carefully and regularly and have access to it at all times.
Keep this manual near the equipment and in a safe place for future reference!
Contact your dealer for any further questions or concerns you may have. We guarantee a long period
of trouble-free operation if the unit is operated and maintained correctly.
We hope you will enjoy working with your fork positioner.
This fork positioner may be unsafe if adequate maintenance is neglected.Therefore, adequate
maintenance facilities, trained personnel and procedures should be provided. Maintenance
and inspection shall be performed in conformity with the following practices:
1. A scheduled planned maintenance, lubrication and inspection system should be followed
(see maintenance instructions chapter 7).
2. Only qualified and authorised personnel shall be permitted to maintain, repair, adjust and
inspect the fork positioner.
3. Modifications and additions which affect capacity and safe operation shall not be
performed by the customer or user without the manufacturer’s prior written approval.
Capacity, operation and maintenance plates or decals shall be changed accordingly.
4. If modifications are made without the written approval of the manufacturer, the warranty
will no longer apply.
Any person in charge of putting the machine into operation, the operation itself or the
maintenance of the machine, is urged to carefully read and observe the following instructions.
Make sure that the operators of this product are familiar with the safety instructions and follow
all the procedures.
Neglecting these instructions can risk injury or death.

7/40
2. DESCRIPTION
2.1. Technical data
Always check the type plate for the correct information.
W6 – Minimal width lift truck carriage
W3 – Maximal width of the forks
Without forks
Total sideshifter stroke 100 + 100 mm
With sideshifter
Model Capacity W8–W9 W4 W6 W3 LL HCG VCG Weight
ISO2328
kg/mm mm mm mm mm mm mm mm kg
ZPH25T-1020P-CD01A 2500/500 294–852 1020 895 120 62 26 228 59 2
ZPH25T-1020P-CD01A.I 2500/500 294–930 1020 895 120 62 26 228 70 2
ZPH25T-1040P-CD01A 2500/500 294-872 1040 895 120 62 26 228 70 2
ZPH25T-1100P-CD01A 2500/500 294-932 1100 895 120 62 26 228 73 2
ZPH25T-1150P-CD01A 2500/500 294-982 1150 895 120 62 27 228 75 2
ZPH25T-1700P-CD01A 2500/500 294-1532 1700 1500 120 62 27 298 105 2
ZPH35T-1150P-CD01B 3500/500 294-982 1150 935 125 68 29 297 90 3
ZPH50T-1350P-CD01B 5000/500 385-1325 1350 1150 150 84 44 296 196 3
ZPH35T-1100P-CD01B 3500/500 294-932 1100 935 125 68 28 296 87 3
Without sideshifter
Model Capacity W8–W9 W4 W6 W3 LL HCG VCG Weight
ISO2328
kg/mm mm mm mm mm mm mm mm kg
ZPH25-980P-CD01A 2500/500 294-812 980 895 120 75 34 226 78 2
ZPH25-1020P-CD01A 2500/500 294–852 1020 895 120 75 35 226 82 2
ZPH25-1040P-CD01A 2500/500 294-872 1040 895 120 75 35 226 86 2
ZPH25-1100P-CD01A 2500/500 294-932 1100 895 120 75 36 226 92 2
ZPH25-1150P-CD01A 2500/500 294-982 1150 895 120 75 36 226 96 2
ZPH35-1150P-CD01B 3500/500 294-982 1150 835 125 79 39 302 96 3
ZPH35-1100P-CD01B 3500/500 294-932 1100 935 125 79 39 302 92 3

8/40
2.2. Operating pressure and oil flow rate
Positioning
Model Operating pressure Oil flow rate Hydraulic
functions
Min
Recommended
Max Min
Recommended
Max
bar bar bar l/min l/min l/min
ZPH25T 140 160 160 4 8 12 2
ZPH25 140 160 160 4 8 12 1
ZPH35T 140 160 160 4 8 12 2
ZPH35 140 160 160 4 8 12 1
ZPH50T 140 160 160 4 8 12 2
Sideshifting
Model Operating pressure Oil flow rate Hydraulic
functions
Min
Recommended
Max Min
Recommended
Max
bar bar bar l/min l/min l/min
ZPH25T 155 160 210 4 8 12 2
ZPH25 – – – – – – 1
ZPH35T 155 160 210 4 8 12 2
ZPH35 – – – – – – 1
ZPH50T 155 160 210 4 8 12 2
• A flow rate less than recommended will result in a lower rotating. speed.
• A flow rate greater than the maximum can result in excessive heating, reduced system
performance and reduced hydraulic system life.
2.3. Main components of the product
With sideshifter PH
4
5
1
2
6
3
Without sideshifter
4
5
2
3
N° Component
1Sideshifting device
2Adjust device
3 Frame
4Sliding pads
5Lifting hook
6Locking tab

9/40
2.4. Placem ent of the decals
The safety and warning labels should be placed as described in the pictures below. See chapter 3 for
the explanation of the safety warnings. If the decals are damaged or missing, replace them.
3
2
2
1
2
N° Decal Explanation Reference
1XXXXX.XXXX.XXXXXXXXXX
CATALOGUENUMBER
NO.D’IDENTIFICATION
KATALOGNUMMER
CATALOGUSNUMMER
NUMERODE REFERENCIA
NUMERODI CATALOGO
DONOT EXCEED THE LIFT TRUCK RES IDUALCAPACITY • DE RESTCAPACITEIT VAN DE HEFTRUCK M AGNIET OVERSCHREDEN WORDEN • DI E RESTKAPAZITAT DES GABELSTAPLERS DARF NICHT UBERSCHRITTE N WERDEN •
NEPAS DEPASSER LA CAPACITE RESIDUELLE DU CHARIOT ELEVATEUR • NO EXCEDER LA C APACIDAD RESIDUAL DE LA CARRETILLA ELEVADORA • NON S UPERARELA PORTATARESID UADEL CARRELLO ELEVATORE
RATEDCAPACITY
CAPACITENOMINALE
NENNTRAGFAHIGKEIT
NOMINALECAPACITEIT
CAPACIDADNOMINAL
PORTATANOMINALE
kg
XXXXXX
WEIGHT
MASSE
MASSE
GEWICHT
PESO
MASSA
kg
XXXXXX
THICKNESS
EPAISSEUR
DICKE
DIKTE
ESPESOR
SPESSORE
mm
XXXX
RECOMMENDEDOPERATING PRESSUR E
PRESSIOND’UTILISATION RECOMMANDE
ANBEFOHLENARBEIT DRUCK
AANBEVOLENWERKDRUK
PRESIONOPERATIVA RECOMENDADA
PRESIONEDI ESERCIZIO R ACCOMANDATA
bar
XXXX
MAXIMUM
MAXIMA
MASSIMA
bar
XXXX
VERTICAL
VERTICAL
VERTICAL
VERTICAAL
VERTICAL
VERTICALE
mm
XXXXX
HORIZONTALCENTRE O F GRAVITY
CENTREDE GRAVITE HORIZO NTAL
HORIZONTALEIGENSCHWERPUNKT
HORIZONTAALZWAARTEPUNT
CENTRODE GR AVIDADH ORIZONTALE
CENTRODI GR AVITAORIZZONTALE
mm
XXXXX
SERIALNUMBER
NO.DE SERIE
SERIENNUMMER
SERIENUMMER
NUMERODE SERIE
NUMERODI SERIE
XXXXX/XX/XXXXX
YEAR
ANNE
JAHR
JAAR
ANO
ANNO
XXXX
Manufactured in the EU for:
TVH Parts Holding NV
Brabantstraat 15 • B-8790Waregem
www.camattachments.com With this type plate
you can identify
your product
166TA5424
2 CAUTION:
Relief pressure
before take cylinder
away
Contact
your dealer
3
1
2
3
4
1. Warning
2. Important:
Carefully read
the manual
before using the
equipment and
carrying out the
maintenance
operations.
3. Important: Risk
of limb crushing.
4. Important:
Pressurised
liquids.
165TA4750

10/40
2.5. Type plate
N° Explanation
1CAM attachments logo
2Equipment capacity
3Equipment name
4 Address
5Horizontal centre of gravity
6Serial number
7CE logo
8Year of construction
9Vertical centre of gravity
10 Thickness
11 Recommended operating pressure
12 Maximum operating pressure
13 Equipment weight
XXXXX.XXXX.XXXXXXXXXX
CATALOGUE NUMBER
NO. D’IDENTIFICATION
KATALOG NUMMER
CATALOGUS NUMMER
NUMERO DE REFERENCIA
NUMERO DI CATALOGO
DO NOT EXCEED THE LIFT TRUCK RESIDUAL CAPACITY • DE RESTCAPACITEIT VAN DE HEFTRUCK MAG NIET OVERSCHREDEN WORDEN • DIE RESTKAPAZITAT DES GABELSTAPLERS DARF NICHT UBERSCHRITTEN WERDEN •
NE PAS DEPASSER LA CAPACITE RESIDUELLE DU CHARIOT ELEVATEUR • NO EXCEDER LA CAPACIDAD RESIDUAL DE LA CARRETILLA ELEVADORA • NON SUPERARE LA PORTATA RESIDUA DEL CARRELLO ELEVATORE
RATED CAPACITY
CAPACITE NOMINALE
NENNTRAGFAHIGKEIT
NOMINALE CAPACITEIT
CAPACIDAD NOMINAL
PORTATA NOMINALE
kg/mm
XXXXXX
WEIGHT
MASSE
MASSE
GEWICHT
PESO
MASSA
kg
XXXXXX
THICKNESS
EPAISSEUR
DICKE
DIKTE
ESPESOR
SPESSORE
mm
XXXX
RECOMMENDED OPERATING PRESSURE
PRESSION D’UTILISATION RECOMMANDE
ANBEFOHLEN ARBEIT DRUCK
AANBEVOLEN WERKDRUK
PRESION OPERATIVA RECOMENDADA
PRESIONE DI ESERCIZIO RACCOMANDATA
bar
XXXX
MAXIMUM
MAXIMA
MASSIMA
bar
XXXX
VERTICAL
VERTICAL
VERTICAL
VERTICAAL
VERTICAL
VERTICALE
mm
XXXXX
HORIZONTAL CENTRE OF GRAVITY
CENTRE DE GRAVITE HORIZONTAL
HORIZONTALEIGENSCHWERPUNKT
HORIZONTAAL ZWAARTEPUNT
CENTRO DE GRAVIDAD HORIZONTALE
CENTRO DI GRAVITA ORIZZONTALE
mm
XXXXX
SERIAL NUMBER
NO. DE SERIE
SERIEN NUMMER
SERIE NUMMER
NUMERO DE SERIE
NUMERO DI SERIE
XXXXX/XX/XXXXX
YEAR
ANNE
JAHR
JAAR
ANO
ANNO
XXXX
Manufactured in the EU for:
TVH PARTS HOLDING NV
Brabantstraat 15 • B-8790 Waregem
www.camattachments.com
1 4
1211
3
2
8
9
13 10
65 7

11/40
3. SAFETY INSTRUCTIONS
3.1. Explanation of the safety decals
If the decals are damaged or missing, please replace them
Make sure that all the safety messages are legible.
Replace damaged stickers asking the manufacturer for new ones.
If the part to be replaced bears a sticker, ensure that a new sticker is applied to the new part.
Decal Explanation Reference
CAUTION:
Relief pressure before take cylinder away
Contact
your dealer
1
2
3
4
1. Warning
2. Important: Carefully read the manual before
using the equipment and carrying out the
maintenance operations.
3. Important: Risk of limb crushing.
4. Important: Pressurised liquids.
165TA4750

12/40
3.2. General safety instructions
• Do not operate the product unless you are of age.
• The person responsible for the use of the product must make sure that all of the safety rules
in force in the country of its use are applied, to guarantee that the equipment is used in
conformity with the use for which it is destined and to avoid any dangerous situation for the
user.
• The operator should wear safety shoes and gloves when using or maintaining the fork
positioner.
• People who come into contact with this equipment and apply procedures, working
practices or use tools that are not described in this manual are responsible for the safe and
proper operation of the equipment.
• Never allow people to climb on the equipment or load, or walk under it.
• Do not use the equipment to lift or transport people.
• Do not use the fork positioner for any other purposes than those intended.
• Never exceed the maximum allowed capacity that is indicated on the type plate.
• The safety precautions and warnings are indicated in the manual and on the equipment by
means of visual messages.
Failure to pay attention to these warning messages may jeopardise the safety of the operator
with serious consequences for himself and for other people.
In addition to the safety regulations described in this section, please take note of all the
information provided in the manual of the lifting device onto which the fork positioner is to be
mounted.
Failure to comply with the basic safety norms or precautions may lead to accidents during
operation, maintenance or repair of the equipment.
It is often possible to avoid accidents by recognising potentially dangerous situations before
they occur. The operator must be aware of potential dangers and possess the training,
competence and the equipment necessary to correctly carry out the work.
CAM attachments cannot under any circumstances be held responsible for accidents or
damage resulting from the use of the equipment by inadequately trained personnel or if
inappropriate use has been made of the same, as well as the, even partial, non-observance of
the safety norms and the intervention procedures contained in the present manual and in that
of your lifting device.
CAM attachments cannot envisage each possible circumstance that may result in danger.
Therefore the warnings given in this publication and which appear on the equipment are not
exhaustive.
In the event that equipment, procedures, work methods or working techniques are used that
are not specifically advised by the CAM attachments company, it is necessary to make sure
that there is no danger to the operator or other people.

13/40
4. TRANSPORT AND STORAGE
1. Transport
If you want to transport the fork positioner on a pallet, make sure that the attachment is securely
attached so that it can’t fall off.
Safely transport the fork positioner by following the next steps:
1. Check the type plate to know the weight of the fork positioner. Select the appropriate material
according to the weight (rope, cable, hook, etc.).
2. Attach the lifting device in the lifting hook.
3. Lift the fork positioner with a crane. Only use a crane with sufficient capacity and secure the fork
positioner to the crane, so that it can be lifted safely.
4. Place the fork positioner onto a pallet.
5. Secure the attachment onto a transport pallet with retaining bands.
6. Wrap the attachment with film to protect it from weather influences and corrosion during
transport.
• Adjust your driving speed while driving over rough terrains and slopes.
• Only transport the fork positioner in its lowest position.
• Before transporting the fork positioner, carefully read the instructions in the manual of the
lifting device.
2. Storage
The fork positioner must always be stored in a dry, frost-free and temperature-controlled environment.
Do not store this product outside in a wet environment.
Store the fork positioner in a safe place and make sure it can’t fall over.
Lubricate metal parts with an anti-corrosive agent.
Avoid direct sunlight.
Do not leave the truck unguarded without applying the handbrake and switching off the
engine first.

14/40
5. ASSEMBLY AND INSTALLATION
5.1. Packing list
Description Amount Reference
ZPH fork positioner 1See technical
data 2.1
Operating manual 1 167TA1384
Spare part list 1See 10.3 Spare
parts list
5.2. Safety instructions for assembly and installation of the product
• Wear safety gloves and safety shoes when assembling the fork positioner.
• The assembly and installation must be carried out by an expert.
• Make sure that the goods and packaging are in good condition.
• Before commissioning, carry out a risk analysis on the assembly of the CAM attachment on
the forklift
• Before using the fork positioner, carefully read the instructions in the manual of your lifting
device.
5.3. Installation of the product
• Before installing the equipment, a thorough visual check must be carried out to make sure
that no damage occurred during the transportation and handling stage.
• If one or more components are damaged, it is necessary to notify CAM attachments and
agree on the measures to be taken.
1. Remove the packing materials carefully.
2. Place the fork positioner on a flat surface.
3. Remove the two bottom hooks with their screws, bolts and washers.
Before lifting the equipment, make sure that the lifting device (ropes, cables,
hooks, etc.) are adequate for the weight of the equipment (see identification label).
Check the stability of the equipment before lifting.

15/40
4. Strap and lift the fork positioner as indicated in the figure.The minimum capacity of the lifting
device must be 200 kg.
Check the type plate to know the weight of the fork positioner. Select the appropriate
material according to the weight (ropes, cables, hooks, etc.)
Lift the fork positioner with a crane. Only use a crane with sufficient capacity and secure
the fork positioner to the crane, so that it can be lifted safely.
5. Place the fork positioner parallel to the fork carriage of your lifting device.
6. Insert the fork positioner locking tab (A) in the seat (B) on the truck’s fork carriage. Centre the fork
positioner on the fork carriage.
7. Lift the fork positioner together with the fork carriage and set the two bottom hooks, securing
them with their bolts and their plates.
Screw dimension Driving torque (Nm)
8.8 type 10.9 type 12.9 type
M12 87 122 147
M14 138 194 235
M16 210 299 357
M20 411 578 696
M24 711 1000 –
B
A

16/40
8. Connect the required hydraulics function to the valves.
With sideshifter Without sideshifter
9. Remove the two bolts, washers and adjust block, shim plates.
10. Lift and insert the first fork in the fork positioner central zone (C) and shift it to the left. Insert the
second fork and shift it to the right.
Centre the two forks on the fork positioner.
C

17/40
11. Insert and tighten the two adjust block, shim plates and bolts, washers previously removed.
Your fork positioner is now ready for use!
After the assembly of the attachment and before putting the device into operation, check if all
the functions operate correctly.
Any failure of the safety devices can cause malfunctioning and damage to the attachment.
5.3.1. Bleed the hydraulic system before use
To avoid air from entering your hydraulic system, which could eventually cause damage to the fork
positioner, it’s necessary to bleed the hydraulic system before use.
1. Start your lifting device
2. Move your fork positioner several times in both directions to the maximum extension.
3. Inspect the hydraulic circuit for any leaks.

18/40
6. OPERATION
6.1. Safety instructions for operating the product
• A damaged or malfunctioning machine must never be used. If damage or malfunctions are
discovered during pre-operation inspection or function tests, the machine must be tagged
and removed from service.
• The lifting device may only be driven by qualified drivers who have also been trained in the
operation of a lifting device fitted with the equipment.
• Check all the parts of the equipment for rust, cracks or other damage before each use.
• Only use the equipment if it is in perfect condition.
• Only use the equipment in aisles and gangways that are wide enough for the necessary
manoeuvres to be made while driving or handling the load.
• If you use the equipment outdoors, never do so in high winds as the forklift could tip over.
• Check the correct installation before you put the fork positioner into use.
• Define and demarcate the working area and make sure that everyone stays sufficiently clear
of the fork positioner working area at all times.
• Be aware of overhead clearances and obstacles.
• Never stand or work under the fork positioner to prevent third parties from being hit by
falling objects during work.
• Adjust your speed according to the terrain.
• Never lift or transport an unlocked attachment.
• Do not use if there is a risk of unexpected movement, only use the vehicle on solid ground.
• Only operate the fork positioner from the operator’s seat and make sure you have a
complete overview of the work activities.
• Operate only in sufficiently illuminated areas.
• When the machine is not in use, avoid unexpected movement by ensuring the machine is
in a stable position.
• Do not leave the truck unguarded without lowering the load to the ground, applying the
handbrake and switching off the engine first.
• Do not wear loose clothing or belts, cuffs, large sleeves, scarves, shirts or anything else that
may get caught in the moving parts.
• For safety reasons, arbitrary adaptations or modifications to the equipment are prohibited.
• In the event of non-envisaged workmanship or intervention or following a procedure
different to that indicated in the manual, consult CAM attachments before proceeding in
order to ascertain its feasibility.
• Transportation of non-permitted materials is forbidden.
• Not intended for use in areas at risk of explosion and fire.
• Do not lift loads on inclines or gradients.
• Make sure that the load cannot move or fall.
• Before using the fork positioner, carefully read the instructions in the manual of your lifting
device.
• In the event of injury caused by oil escaping under pressure, immediately seek medical
assistance.

19/40
6.2. Operating instructions
Please see chapter 7 for the daily maintenance schedule.
• The lifting device with attachment installed needs to be approved for use prior to
commissioning.
• Be sure to obtain the manufacturer’s certification concerning the residual capacity of the lift
lifting device, after installing the attachment.
6.2.1. Load lifting
Perform the daily maintenance check before each use as described in chapter
7.3.‘Maintenance instructions’
1. Before starting
First, use the hydraulic levers to check which levers operate which function.
Use all the functions several times with no load to check if they function normally and smoothly.
Before lifting a load, operate the forks several times to remove air from the circuit.
Before lifting a load, position the fork.
Don’t adjust the fork with a load!
2. Loading
1. The load must be positioned against the body of the forks and not towards the tips of the lifting
forks.
Make sure that the load cannot move or fall.This can cause accidents.
2. The forks must be spaced inside the pallets.
After lifting the load, always position the forks in the centre.
Correct pick-up Incorrect pick-up
Correct pick-up
Forks
Incorrect pick-up
Forks

20/40
6.2.2. Load handling
Don’t drive with a non-centred load (shifted towards the left or right).
Make sure that loads can’t move freely, they may fall and cause accidents.
1. Set the forks of your lifting device in the correct position and as wide as possible for the load to be
carried.
2. Adjust the forks to the correct width so you can provide a more even distribution.
3. Pick up the load parallel to the floor. Always use both forks if you want to transport the goods.
4. When moving your lifting device, lift the load 200 mm from the ground.
If you are using a lift truck, make sure you tilt the mast backwards.
5. To unload, firstly bring the upright to a vertical position and then slowly lower the forks.
200 mm
This manual suits for next models
16
Table of contents
Other cam Valve Positioner manuals
Popular Valve Positioner manuals by other brands

innove
innove VP100 INSTALLATION PROCEDURE
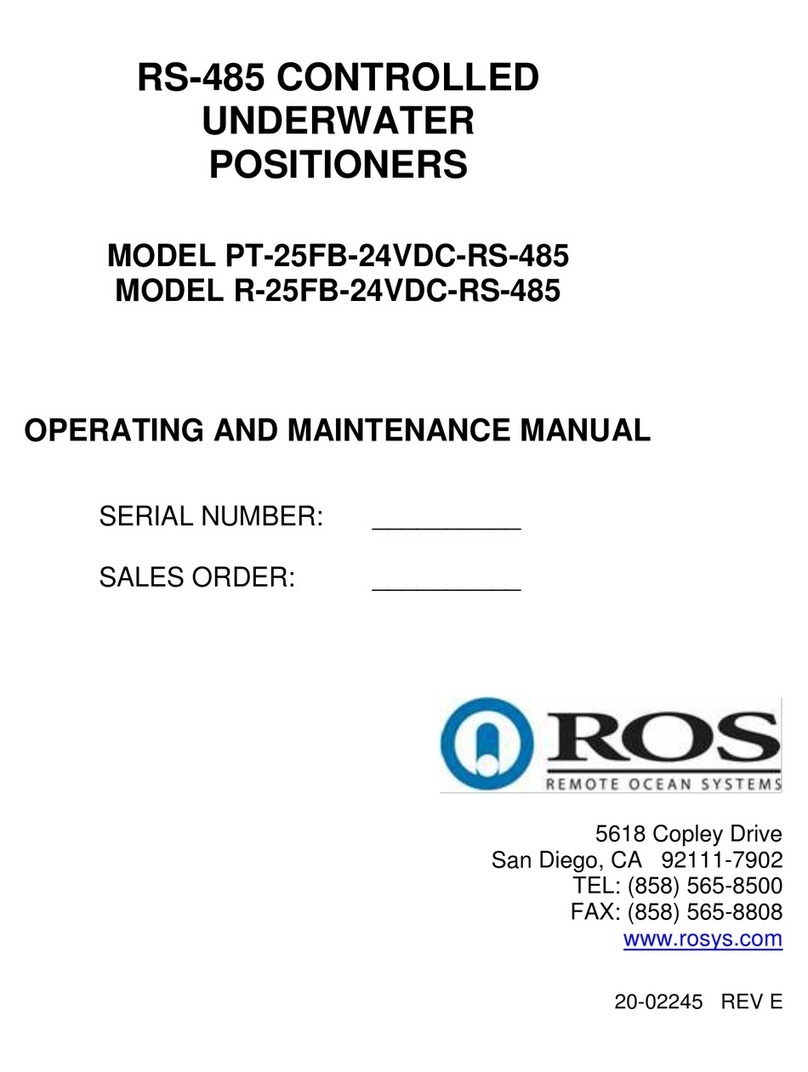
Ros
Ros PT-25FB-24VDC-RS-485 Operating and maintenance manual
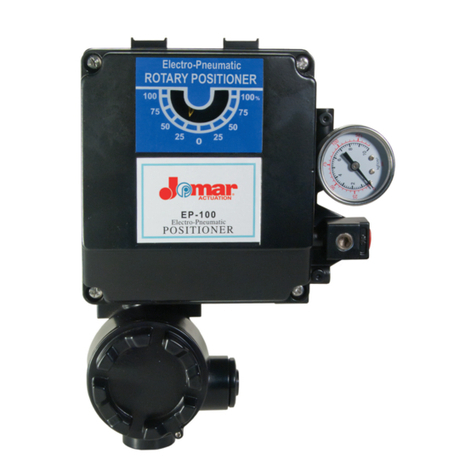
JOMAR
JOMAR AEP-100 Installation, operation & maintenance instructions

Lincoln Electric
Lincoln Electric POSIMATIC PS08 Safety instruction for use and maintenance
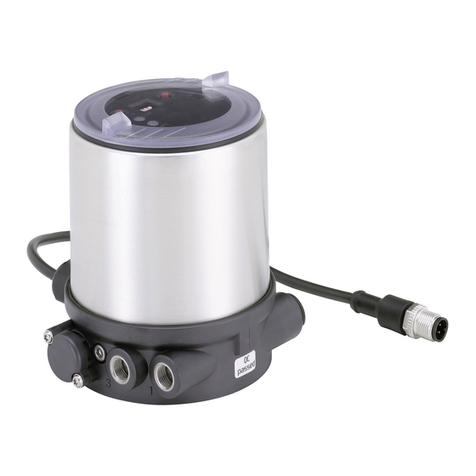
Burkert
Burkert TopControl Basic 8694 REV.2 quick start
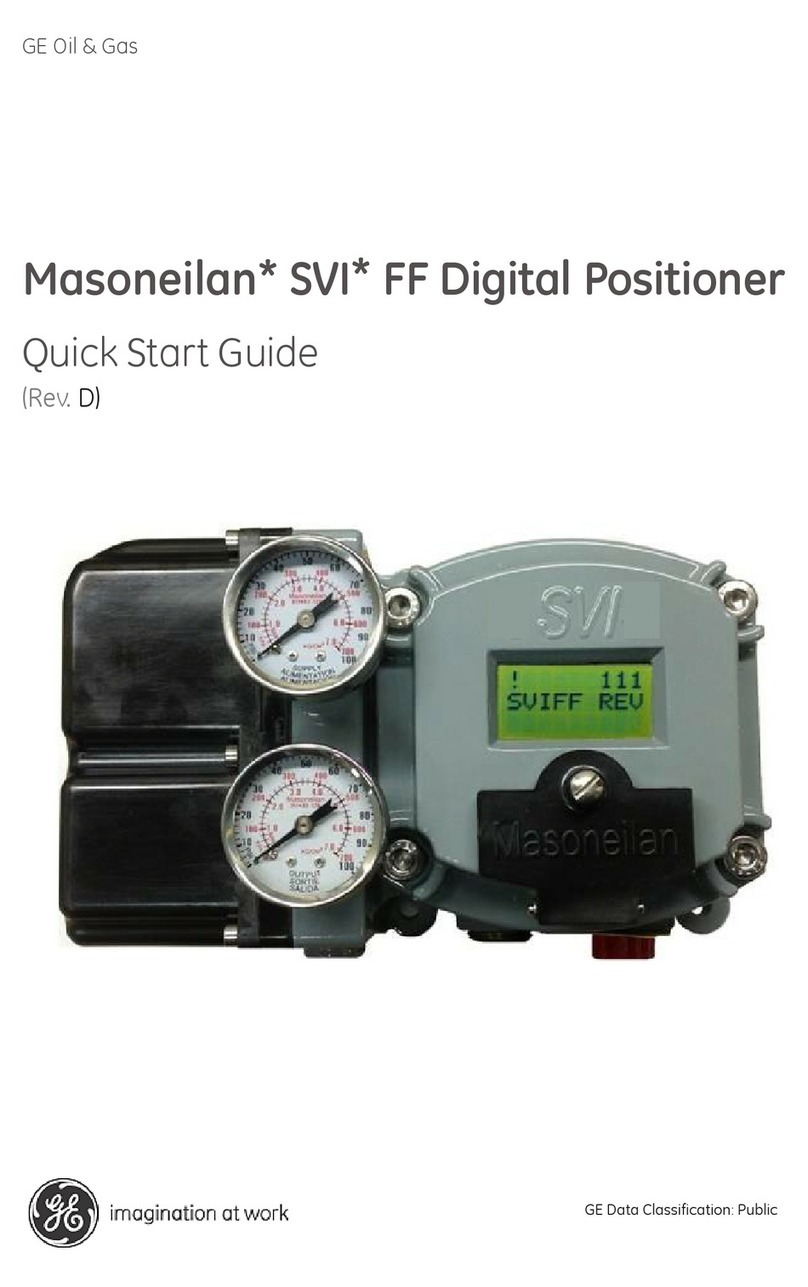
GE
GE Masoneilan SVI FF Quick starter guide