Canary Systems MDT SMART Link-485 User manual

5 Gould Road, PO Box 2155
New London, NH 03257 USA
Voice: (603) 526-9800
info@canarysystems.com
www.canarysystems.com
Integrating the MDT SMART Link-485
1
Integrating the MDT SMART Link-485
Sensor Application Note #32
Overview
MDT’s SMART MPBX is a flexible borehole extensometer with up to six anchor points and an integrated
electronic readout head. As each anchor moves, fiberglass rods within the MPBX produce a very precise
change in resistance at the wiper terminals. This resistance change is converted to a voltage, relative to a
reference voltage. The displacement is calculated as a ratio of this data. The displacement data from each
anchor is interpreted, and rock movement mapped. The MDT SMART Link-485 connects to the MPBX readout
head and provides a 2 wire RS-485 half duplex serial interface which can be connected to a Campbell
ScientificCR6 Datalogger via a RSCOM2A RS-485 to RS-232 converter (provided by RESmith). The goal of
this document is to walk through the configuration of an MDT SMART Link-485 and configuring MultiLoggerto
ingest the data being produced by the MDT SMART MPBX.
System Wiring and Configuration
A converter is typically required to convert the RS-485 output of the MDT SMART Link-485 to RS-232. Figure
1 is the wiring diagram connecting a SMART Link-485 to a Campbell ScientificCR6 using an RESmith
RSCOM2A converter. The RSCOMA2A provides a low-cost, highly configurable signal converter.
(Figure 1 - Connection path between CR6, RSCOM2A and two SMART Link-485. You can have one or more SMART Link-485s all
connecting to the same RSCOM2A.)
Note - In Figure 1, wiring for COM1 is used. Use alternate ports for other COM ports.

Integrating the MDT SMART Link-485
2
(Figure 2 - Side view of RSCOM2A)
Note - Two of the internal jumpers inside the RSCOM2A converter need to be moved from their factory default position
to function properly with SMART Link-485, shown in Figure 3.
(Figure 3 - RSCOM2A Converter showing updated jumper positions)
Function Test
Prior to completing final connection to the CR6 Datalogger, it is recommended to test the operation of the
SMART Link-485. Ideally this is completed prior to grouting the unit into the drill hole.
(Figure 4 - Components needed for testing operation of SMART Link-485)
A 12V power source is required for the SMART Link-485 and the RSCOM2A, a 12V battery works well.
Wiring connection paths are shown previously in Figure 1. The RSCOM2A ships with a ribbon cable with an
RJ11 connector on one end and a 9-pin serial connection on the other.
First, connect the RJ11 to the RSCOM2A and the serial connection to a straight-through serial cable connected
to a serial port on a computer. Next launch a terminal emulation program (HyperTerminal was used for this
document) on a computer.

Integrating the MDT SMART Link-485
3
Configure the COM port as follows:
Bits per second (baud rate): 57600
Data bits: 8
Parity: None
Stop bits: 1
Flow Control: Hardware
(Figure 5 - Terminal emulation program configuration)
The SMART Link-485 will be in a low power, sleep mode and it takes a sequence of 2 commands (one to wake
the unit and one to return data). This is desirable to avoid accidentally awakening the SMART-Link 485 in
electrically noisy environments.
The command you need to send to the MDT SMART Link-485 is the serial number of the SMART Link-485
concatenated with “RDAAM” followed by a carriage return and line feed<CR><LF>.
(Figure 6 - Location of serial number on SMART Link-485)
Issuing a “RD” command triggers a new data sample and produces a response which includes the initial
reading, the current reading and the delta. The first “A” in the RDAAM command tells the system to send data
from all ports and the second “A” in the command tells the system to send results for all channels. The “M” is
telling the system to respond in metric units or millimeters. This command needs to be sent 2 times in quick
succession (less than 1 second). It is recommended that the command be copied to the clipboard so that it
can be pasted to the HyperTerminal session followed by the <Enter> key then quickly pasted again to the
HyperTerminal session followed by the <Enter> key. If the system is working properly you should see
something like the example response from the SMART Link-485 in Figure 7 after sending the second
command.
Note - There is a separate serial number assigned to the extensometer which is returned in the response. In the
example in Figure 6, the serial number of the SMART Link-485 is LK180427 and the command sent in is
“LK180427RDAAM”. The serial number of the extensometer is MDTC-M0618-01 which is in the response, shown in
Figure 7.

Integrating the MDT SMART Link-485
4
(Figure 7 - Response from SMART Link-485)
The fields of the string in Figure 7 are as follows:
"S" - start of the sample/string/response.
"MDTC-M0618-01" - the serial number of the extensometer connected to the SMART Link-485.
"IDE" - indicates the location where the information about the MPBX was read from. The "E" indicates the
SMART ID is external to the Link-485, this is usually the case when using SMART Link-485.
If this had been "IDI", the "I" standing for "internal" would indicate that the information about the
MPBX was read from within the Link-485 (an extra SMART ID is added inside the Link-485). This
would be the case when the Link-485 is paired/bonded to a specific legacy instrument that does not
have a SMART ID memory chip built in. The Link-485 would have the serial number of the MPBX
penciled in on the label under the "Paired SMART Instrument SN".
"23.5" - temperature in Celsius
"645" - this is a legacy value for Voltage that MDT has kept for backwards compatibility issues. This value
divided by 56 gives you volts DC. In the example 645/56 =11.5Vdc.
"M" - precedes the first reading (position) and indicates Metric units.
Three values following “M” - first value is the initial value, the second value is the current reading (this
is the value that will be reported in MultiLogger) and the third value is the delta. There are as many of
these 3 value entries as there are sensors on the SMART Link-485 (in the example there are six).
"AAM" - echo of the port, channel and unit command issued: All ports, All channels, Metric units.
MultiLogger Configuration
Typically, the Direct Connect Channel configuration would be used for configuring the SMART Link-485.
However, since the number of Direct Connect Channels in a Campbell CR6 Datalogger are limited to 12 and
each position requires a channel; if the system must read more than 2 MPBXs with 6 positions each, there
would be insufficient channels. In this case, use a Multiplexer configuration, the following section details this
configuration.
Note - A gage type has been added to support reading the MDT SMART Link-485. Contact Canary Systems
if your
installation of software does not list the required gage types.
Direct Connect Channel Configuration
Add a Campbell CR6 MCU to the network, double-click to load the Logger form. Then, select the Direct
Connect option on the Program tab, as shown in Figure 8.
(Figure 8 - Program tab of the MultiLogger
program configuration outlining the Direct Connect option)

Integrating the MDT SMART Link-485
5
When configuring the Direct Connect Channels, select MDT SMART Link-485 as the Gage Type.
(Figure 9 - Direct Connect Channel configuration form, note the Gage Type (Make | Mode) selection for Channel 1)
Subsequent channels would be configured with each SMART Link-485 position.
(Figure 10 - Example of Direct Connect Channel configuration for channel 2)
Multiplexer Configuration
If more channels are required than can be supported using Direct Connect configuration then a multiplexer may
be configured. The Multiplexer configuration simply acts as a placeholder for the measurements.
Use the Multiplexers button on the Program tab to display the Configure Multiplexers form.
(Figure 11 - MultiLogger
Configure Program outlining the Multiplexers option)

Integrating the MDT SMART Link-485
6
When configuring the Multiplexers, select Virtual as the Model and MDT SMART Link-485 as the Gage Type.
(Figure 12 - Channel configuration when using Multiplexers)
The Channels drop-down determines how many channel placeholders are available.
Press the Edit Channels button to configure the channels.
Note - Channel configuration is similar for Direct Connect and Multiplexers.
(Figure 13 - Channel configuration when using Multiplexers)
Activating MultiLogger
Once all channels are configured select Start/Update to download the program and then Activate the logger.
(Figure 14 - MultiLogger
- Text Monitor)

Integrating the MDT SMART Link-485
7
Appendix A.
SMARTL Link-485 Pinouts and Color Codes
10 –Position Female Pinout
10 –Position Female
7 –Position Male Pinout
7 –Position Male
MultiLoggerand Canary Systems are Registered Trademarks of Canary Systems, Inc.
Campbell Scientificis a Registered Trademark of Campbell Scientific, Inc.
Table of contents
Popular Controllers manuals by other brands
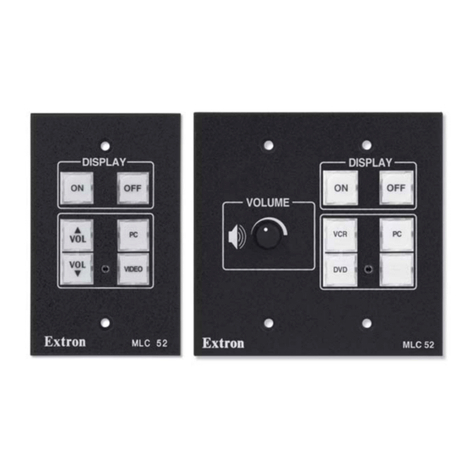
Extron electronics
Extron electronics Basic MediaLink Controllers MLC 52 IR user manual
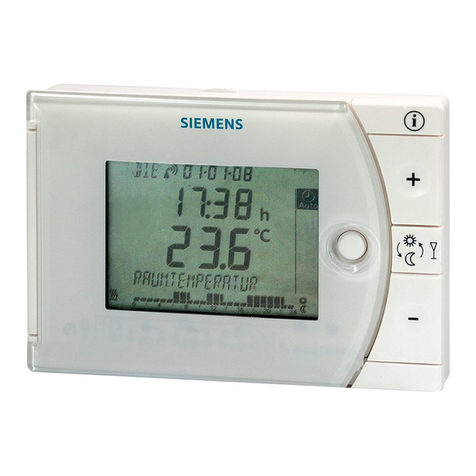
Siemens
Siemens REV13 series instruction manual
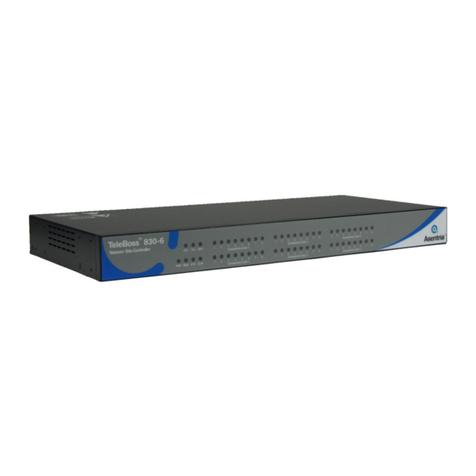
Asentria
Asentria TeleBoss 830 user manual
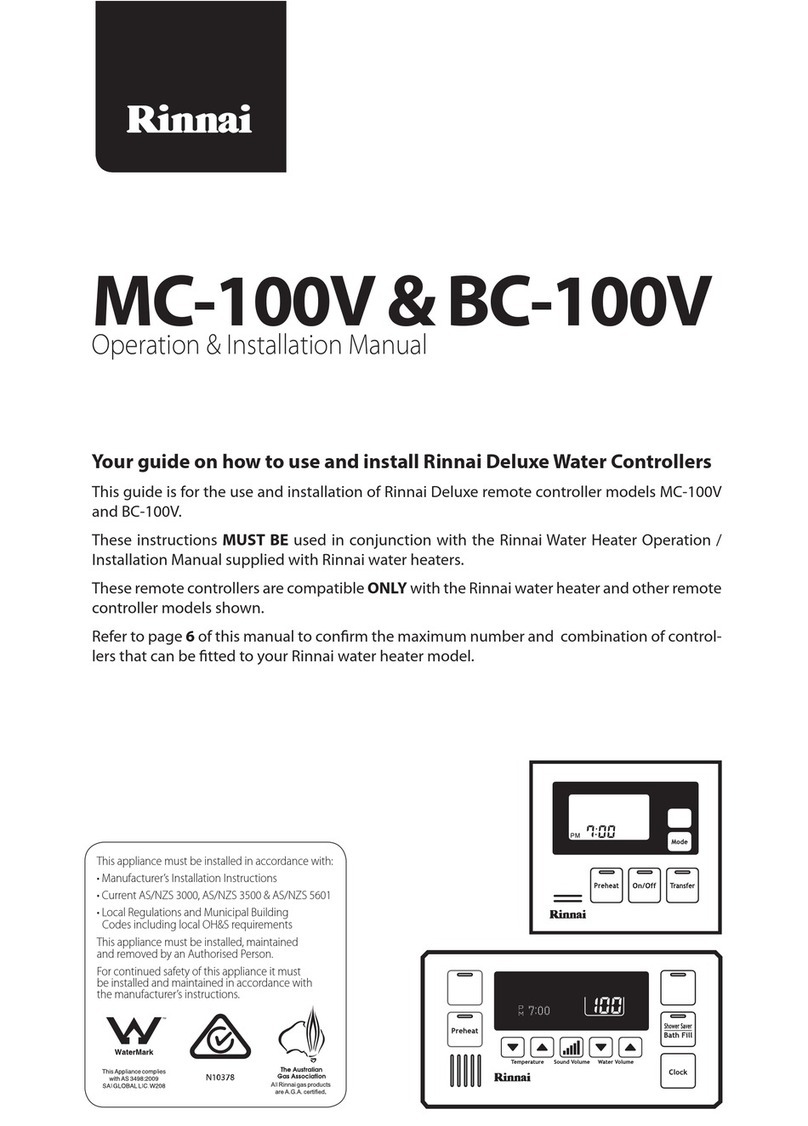
Rinnai
Rinnai MC-100V Operation & installation manual

Isimet
Isimet LA Series Installation, Operations, Start-up and Maintenance Instructions

DMP Electronics
DMP Electronics X1 COMPLIANCE GUIDE