Cattron CANplus CP640 User manual

CANplusTM CP640
Control Panel Operation Manual
9M02-1000-A001-EN

CANplusTM CP640 - EN
Control Panel Operation Manual
2
9M02-1000-A001-EN
Revision B
Revision History
VERSION
DATE
NOTES
A
10/2018
B
12/2020
Document rebranded and contact information updated
Any information furnished by Cattron™ and its agents is believed to be accurate and reliable. All specifications are subject to change without notice.
Responsibility
for the use and application
of Cattron products rests with the end user since Cattron and its agents cannot be aware of all potential
uses.
Cattron
makes no warranties as to non-infringement nor as to the fitness, merchantability, or sustainability of any Cattron products for any specific
or
general uses. Cattron Holdings, Inc., or any of its affiliates or agents shall not be liable for incidental
or consequential damages of any kind. All
Cattron
products are sold pursuant to the Terms and Conditions of Sale, a copy of which will be furnished upon request. When used as a tradename
herein,
Cattron means Cattron Holdings,
Inc. or one or more subsidiaries of Cattron Holdings, Inc. Cattron™, corresponding logos, and other marks
are
trademarks
or registered trademarks of Cattron Holdings, Inc. Other marks may be the property of third parties. Nothing herein provides a license
under
any Cattron or any third party intellectual property right.

CANplusTM CP640 - EN
Control Panel Operation Manual
3
9M02-1000-A001-EN
Revision B
Contents
1 Important Safety and Emissions Information ...................................................................................................... 5
1.1 Safety Notation......................................................................................................................................... 5
1.2 Safety Instructions.................................................................................................................................... 5
1.3 Auxiliary Engine Stop Disclaimer ............................................................................................................. 6
1.4 General Emissions Disclaimer ................................................................................................................. 7
1.5 Exhaust Emissions Compliance Disclaimer............................................................................................. 7
2 Overview.............................................................................................................................................................. 8
3 Display ............................................................................................................................................................... 10
3.1 Adjusting Lighting and Contrast ............................................................................................................. 10
3.2 Button Bar .............................................................................................................................................. 10
3.3 Analog Gauge Pages ............................................................................................................................. 11
3.4 Digital Gauge Pages .............................................................................................................................. 12
3.5 Single Analog Gauge ............................................................................................................................. 12
3.6 Active Alarms ......................................................................................................................................... 12
3.7 Alarm List ............................................................................................................................................... 12
3.8 Service Timers ....................................................................................................................................... 13
3.9 Menus .................................................................................................................................................... 13
3.9.1 Menu Tree................................................................................................................................. 14
3.9.2 Access Levels ........................................................................................................................... 16
4 Manual Operation .............................................................................................................................................. 18
4.1 Throttle Control ...................................................................................................................................... 18
4.2 Ramp Throttle ........................................................................................................................................ 18
4.3 Rotary Throttle Control........................................................................................................................... 19
4.4 Stopping the Engine............................................................................................................................... 19
4.5 AutorampTM ............................................................................................................................................ 19
5 Configuration ..................................................................................................................................................... 22
5.1 Display Menu ......................................................................................................................................... 22
5.2 CANplusTM Software Suite and CANplusTM Config Kit .......................................................................... 22
5.3 CANplusTM Customizer Software Suite and a USB Drive...................................................................... 22
6 Miscellaneous.................................................................................................................................................... 24
6.1 Emissions System Functionality ............................................................................................................ 24
6.2 CP640 Panel Wiring............................................................................................................................... 24

CANplusTM CP640 - EN
Control Panel Operation Manual
4
9M02-1000-A001-EN
Revision B
6.2.1 Typical J1939 Wiring Topology................................................................................................. 25
6.2.2 Engine Harness Connector....................................................................................................... 25
6.2.3 Sealed Connectors ................................................................................................................... 26
6.2.4 Unsealed Connectors ............................................................................................................... 26
6.2.5 Harness Routing ....................................................................................................................... 26
6.3 Engine Starter Excitation Connection .................................................................................................... 26
6.3.1 Starter Relay ............................................................................................................................. 26
6.3.2 Battery Circuit Requirements .................................................................................................... 27
6.3.3 Battery Positive Connection...................................................................................................... 27
6.3.4 Voltage Drop ............................................................................................................................. 27
6.3.5 Suppression of Voltage Transients (Spikes)............................................................................. 27
6.3.6 Welding on Equipment with Electronic Controls ....................................................................... 28
6.4 Control System Troubleshooting............................................................................................................ 28
6.4.1 Testing a Warning or Shutdown................................................................................................ 29
6.4.2 Testing CAN.............................................................................................................................. 29
6.5 Diagnostic Trouble Codes (DTC)........................................................................................................... 30
6.5.1 Typical SPNs............................................................................................................................. 30
6.5.2 FMI ............................................................................................................................................ 30
7 Technical Support.............................................................................................................................................. 32

CANplusTM CP640 - EN
Control Panel Operation Manual
5
9M02-1000-A001-EN
Revision B
1 Important Safety and Emissions Information
1.1 Safety Notation
This manual uses the following conventions to present IMPORTANT SAFETY INFORMATION to you. Please
read and follow ALL SAFETY INSTRUCTIONS.
WARNING
IMPORTANT AND URGENT SAFETY INFORMATION – A HAZARD THAT WILL, IF NOT AVOIDED,
CAUSE SERIOUS INJURY OR LOSS OF LIFE.
CAUTION
IMPORTANT SAFETY INFORMATION – A HAZARD THAT MIGHT CAUSE SERIOUS INJURY OR
LOSS OF LIFE.
Note: Additional Important Information
1.2 Safety Instructions
Please read and follow all safety instructions.
CAUTION
THIS DOCUMENT MUST BE COMPLETELY READ AND UNDERSTOOD PRIOR TO INSTALLING,
TESTING OR OPERATING THE EQUIPMENT DESCRIBED WITHIN. FURTHER, THIS DOCUMENT
MUST BE RETAINED FOR CURRENT AND FUTURE USERS OF THIS EQUIPMENT. FAILURE TO
STRICTLY FOLLOW THE WARNINGS AND DANGERS PRESENTED WITHIN THIS DOCUMENT
COULD RESULT IN DAMAGE TO EQUIPMENT, DAMAGE TO PROPERTY, BODILY INJURY OR
DEATH.
CAUTION
CANPLUS
TM
PRODUCTS ARE NOT DESIGNED OR APPROVED FOR USE AS CRITICAL
COMPONENTS OF ANY SAFETY DEVICE OR SYSTEM THAT IS INTENDED TO PREVENT
BODILY INJURY, PROTECT LIFE OR PREVENT PROPERTY DAMAGE.
CAUTION
THE SPECIFYING ORIGINAL EQUIPMENT MANUFACTURER (OEM) AND/OR INSTALLER OF
ANY CANPLUSTM PANEL IS RESPONSIBLE FOR ALL SAFETY LABELING AND OPERATOR
EDUCATION REGARDING THE SAFE OPERATION OF THIS PANEL AND THE OPERATION OF
THE SPECIFIC MACHINE THAT THIS PANEL IS INSTALLED UPON, INCLUDING CONFORMANCE
TO EXHAUST EMISSIONS REGULATIONS.
!
!
!
!
!

CANplusTM CP640 - EN
Control Panel Operation Manual
6
9M02-1000-A001-EN
Revision B
CAUTION
CANPLUS
TM
PRODUCTS ARE NOT DESIGNED FOR, OR INTENDED FOR USE ON,
APPLICATIONS REQUIRING EXPLOSIVE PROOF COMPONENTS. FURTHER, CANPLUSTM
PRODUCTS ARE NOT DESIGNED FOR, OR INTENDED FOR APPLICATION WITHIN,
HAZARDOUS OR EXPLOSIVE ENVIRONMENTS.
CAUTION
THE INSTALLER OF THIS CANPLUS
TM
PRODUCT IS SOLELY RESPONSIBLE FOR ENSURING
THAT ALL OSHA, ANSI, CE OR OTHER APPLICABLE STANDARDS ARE MET WITH RESPECT TO
CANPLUSTM PANEL APPLICABILITY, MACHINE GUARDING, GENERAL SAFETY GUIDELINES,
LABELING AND WARNINGS.
CAUTION
THE INSTALLER OF THIS CANPLUS
TM
PANEL AND/OR CANPLUS
TM
HARNESS IS
RESPONSIBLE FOR THE CORRECT SIZING AND INTEGRATION OF A SUITABLE
FUSE/BREAKER ON THE UNSWITCHED DC CIRCUIT SUPPLYING POWER TO THE CANPLUSTM
PANEL.
CAUTION
ONLY TRAINED AND QUALIFIED PERSONS MAY PERFORM INSTALLATION, TESTING,
SERVICE OR REPAIR WORK ON THE CANPLUSTM PRODUCT.
Note: The seller hereby expressly disclaims all warranties, either expressed or implied, including any implied
warranty of merchantability or fitness for a particular purpose, and neither assumes nor authorizes any
other person to assume for it any liability in connection with the sale of such products.
1.3 Auxiliary Engine Stop Disclaimer
This panel or harness may include an optional Auxiliary Engine Stop feature. Please note that the Auxiliary
Engine Stop feature is NOT intended to function as the machine/equipment Emergency Stop or to be
purposed as an Emergency Stop for safety purposes. The machine manufacturer must provide a separate
Emergency Stop switch to meet safety mandates or emergency machine shutdown functionality. The sole design
intent of the Auxiliary Engine Stop feature is to provide for engine shutdown in the event of a keyswitch
malfunction. The panel key/lever switch should always be used as the primary engine shutdown method.
!
!
!
!

CANplusTM CP640 - EN
Control Panel Operation Manual
7
9M02-1000-A001-EN
Revision B
1.4 General Emissions Disclaimer
This panel may include provision(s) for operator input such as FORCE REGENERATION, INHIBIT
REGENERATION, INTERLOCK and others specific to US and International emissions regulations.
Responsibility for emissions-related inputs and compliance with emissions regulations is solely that of the owner
and/or operator of the machine/engine on which this panel is connected.
1.5 Exhaust Emissions Compliance Disclaimer
This panel is equipped with operator-programmable parameters. The engine/machine as a function of the
emissions system can/could initiate, via the engine ECU (Engine Control Unit), certain required emissions
operations such as regeneration of the DPF (Diesel Particulate Filter), or other emissions system maintenance,
while the engine is running. The owner/operator of the engine/machine is solely responsible for any adverse
effects or damage to the engine, engine emissions system or other damage that could occur as a result of
starting or stopping the engine/machine during any ECU initiated emissions event.

CANplusTM CP640 - EN
Control Panel Operation Manual
8
9M02-1000-A001-EN
Revision B
2 Overview
The CANplusTM CP640 control panel is an economical platform for EPA Tier 3, EPA Tier 4 (interim) and EPA
Tier 4 electronically governed diesel engines. Graphical gauge pages or a single large analog gauge are
displayed on the 3.5” diagonal LCD. Virtually any SAE J1939 parameter reported by the ECU (Engine Control
Unit) can be displayed, including, but not limited to the following: RPM, coolant temperature, oil pressure, engine
hours, voltage, exhaust emissions system state and diagnostic codes. The backlit display is clearly readable in
both bright sunlight and total darkness and is housed in a rugged IP66 rated housing. The CP640 can optionally
include three bright LEDs to indicate Faults, Warnings and Emission-Related Alerts.
All components are installed in a heavy-duty, vibration-isolated metal enclosure designed to withstand the most
extreme industrial applications. External weather-resistant switches and controls facilitate convenient operator
inputs/controls. Active fault conditions are displayed in plain language on popup messages and can be viewed in
the fault list. Various diagnostic screens allow detailed investigation of the CAN bus data stream.
Note: All diagnostic and emissions-related messages displayed on the CP640 are generated by the engine
ECU or other attached devices. The operator must be familiar with the engine manufacturer ECU
messages and icons in order to react accordingly with respect to emissions compliance, service and
diagnostic message response.

CANplusTM CP640 - EN
Control Panel Operation Manual
9
9M02-1000-A001-EN
Revision B

CANplusTM CP640 - EN
Control Panel Operation Manual
10
9M02-1000-A001-EN
Revision B
3 Display
The CANplusTM display is a robust, sunlight-viewable 3.5” QVGA color display with five integrated backlit buttons
housed in a rugged, water-tight IP66 rated enclosure. The five soft keys simplify and enhance the user interface
by providing a configurable auditory beep and positive tactile feedback when pressed.
The display can show virtually any SAE J1939 parameter reported by the ECU, including RPM, engine
temperature, oil pressure and diagnostic codes. It can be easily configured to customer preference, including
gauge type (analog or digital), gauge arrangements, gauge size, units and language.
Note: Different software versions may have slightly different displays.
3.1 Adjusting Lighting and Contrast
When the menu bar is not visible, press button 5 (button on far right) to open the lighting and contrast menu bar.
The display has multiple back-lighting levels allowing the display to be viewed in the dark. The level is adjusted
by pressing button 1 to decrease or button 2 to increase the display illumination. Contrast is adjusted in the same
manner using buttons 3 and 4.
Note: The display adjusts the contrast with the ambient temperature. Manual contrast adjustments are only
necessary with extreme climate change.
Exit the menu by pressing button 5. The lighting and contrast settings are retained after the unit is powered off.
3.2 Button Bar
Pressing any of the first four soft keys on the display will prompt the “button bar” key function legend to appear at
the bottom of the display above the keys. The button bar will show an icon above the button which corresponds
to its current function, as shown below.

CANplusTM CP640 - EN
Control Panel Operation Manual
11
9M02-1000-A001-EN
Revision B
3.3 Analog Gauge Pages
Analog Gauge Pages provide four independently configurable pages of analog gauges. To enable Analog Gauge
Pages, press any of the first four buttons to show the top level button bar and then press button 1 to cycle
through the pages, as shown below.
Note: Some items like Engine Hours are displayed as a digital value even on the Analog Gauge Pages.

CANplusTM CP640 - EN
Control Panel Operation Manual
12
9M02-1000-A001-EN
Revision B
All 16 gauges may be configured to create an application-specific view of the data. With Tech or Admin level
access, the four analog gauge pages can be configured using the following menu: Configuration →Display →
Gauges →Quad Gauge Pages.
3.4 Digital Gauge Pages
Digital Gauge Pages display the same data as the Analog Gauge Pages, but in digital only format, as shown
below. To enable Digital Gauge Pages, press any of the first four buttons to show the top level button bar and
then press button 2 to cycle through the pages.
Note: The 16 gauges are the same for Analog and Digital Gauge Pages. Adjustments in either Analog Gauge
Pages or Digital Gauge Pages affect the same gauge in the other mode.
3.5 Single Analog Gauge
Single Analog Gauge uses the entire display for a single large analog gauge. To enable the Single Analog
Gauge, press any of the first four buttons to show the top level button bar and then press button 3 to cycle
through the available gauges. The active displayed gauge is stored when power is removed.
3.6 Active Alarms
When an active alarm is received, a flashing popup window is overlaid on the current screen. The popup
includes a plain language description in addition to the standard SPN/FMI (Suspect Parameter Number/Failure
Mode Indicator) pair defined by the SAE J1939 standard. Additionally, if enabled, the beeper sounds as an
audible cue.
Note: Standard J1939 abbreviations are used for alarms, as follows:
MS = Most Severe
MOD = Moderately Severe
LS = Least Severe
3.7 Alarm List
The Alarm List is accessed by pressing any button while an alarm popup is displayed or by pressing any of the
first four buttons to show the button bar and then button 4. Alarms not yet acknowledged are shown in white text
on a red background, while acknowledged alarms are shown in white on black. The list also indicates when the
alarm occurred if engine hours are available. The most recent alarm is displayed at the top of the list. The list can
be scrolled using buttons 1 and 2 and alarms acknowledged by pressing button 3. The Alarm List can be closed
by pressing button 5 once the alarms are acknowledged.

CANplusTM CP640 - EN
Control Panel Operation Manual
13
9M02-1000-A001-EN
Revision B
An alarm indicator is displayed near the upper right corner of the display as long as alarms are active. The
indicator and alarm messages in the list are automatically removed when the alarm has not been received for a
few seconds.
Note: Only active faults are displayed in the alarm list. Once a fault is corrected, it is automatically removed
from the list. To view previously active faults, press the “STORED” button.
3.8 Service Timers
The CP640 display provides 16 service timers to alert the operator of required maintenance. The time interval for
each timer can be adjusted in increments of 10 hours. A popup message is displayed after completion of the
display’s self-test if a timer (or timers) has expired, alerting the user that service is required. The message is
displayed on each power-up until the elapsed timer is disabled or reset. The service timers can have their
respective names customized to monitor engine- and pump-related parameters. All 16 service timers can be
monitored via wireless telemetry.
3.9 Menus
The menu pages can be accessed by pressing and holding button 5. After 1 second, the top-level menu page
will appear. From there the functions of the five display buttons change to allow navigation and selecting and
modifying parameters.

CANplusTM CP640 - EN
Control Panel Operation Manual
14
9M02-1000-A001-EN
Revision B
The menus pages can also be accessed by pressing and holding the optional Rotary Control using RotaryPlus
technology:
•Push and hold the rotary for 1 second to open the menus main page
•Move down through the menu choices with clockwise rotations
•Move up through the menu choices with counter clockwise rotations
•Select menus, options and entries by pushing in the rotary knob (click)
•Increase numerical entries with clockwise rotations
•Decrease numerical entries with counter clockwise rotations
•Push in the rotary knob twice quickly (double click) to back up to the previous menu
•At any time, push and hold the rotary for 1 second to cause the display to completely back out of the
menu mode showing the main gauges
3.9.1 Menu Tree
The menu tree is shown below. Some menus items are suppressed based on the access level currently allowed.
The color of the text in the tree indicates the minimum access level required for this particular item to be
available for displaying.
Black = User
Green = Tech
Red = Admin

CANplusTM CP640 - EN
Control Panel Operation Manual
15
9M02-1000-A001-EN
Revision B
Display
•
Language
•
Units
-
Distance
-
Pressure
-
Volume
-
Temperature
•
Button Beep – ON/OFF
•
Gauges
–
Quad Gauge Pages (configure which gauges will be displayed)
*
1-4
•
Voltmeter – 12 V / 24 V
System
•
Restore Defaults (recall factory defaults)
•
Import Config (import a new configuration file from the USB port)
•
Export Config (export current configuration to a file on the UBS port)
•
PINs (see the Access Levels section)
–
Elevate Access Level
–
Entry – On/Off
–
Change
•
CAN bus
–
TSC1 Address (panel sends the TSC1 messages from this CAN address)
–
Panel Address (CAN address for the panel)
–
CM1 Address (panel sends the CM1 messages from this CAN address)
–
Config Address (panel address for Config program)
•
Engine Type
•
Engine Specific Settings
•
Date and Time
•
About
Throttle
•
Min / Idle / Max RPM
•
Switch/Rotary
–
Increments
–
Max Change per Second
•
Autoramp (see the AutorampTM section)

CANplusTM CP640 - EN
Control Panel Operation Manual
16
9M02-1000-A001-EN
Revision B
–
RPM Settings
*
Intermediate
*
Run
–
Time Profile
*
Warm Up
*
Ramp to Intermediate
*
Ramp to Run
*
Ramp to Cooldown
*
Cooldown
Telemetry
•
Status
•
Address (CAN address for the telemetry device)
Service Timers
•
Timers 1-16 (each timer is listed separately)
–
Hours remaining
–
Reset
Tier 4 Control
•
Inhibit – OFF/ON (inhibit Regenerations)
•
Request Force (request a Force Regeneration; depending on conditions, ECU may not honor)
•
Status (database Viewer for Tier 4 related status messages from the ECU)
Database Viewer
3.9.2 Access Levels
The available menu items are dependent upon the current access level. The current access level is shown in the
upper right corner while in the menus. The CP640 supports up to three independent PINs that are configurable.
The standard CANplusTM configuration has the following PINs settings:
•
User = 1000
•
Tech = 1111
•
Admin = 2222
•
Menu PIN Required = OFF
Elevate Access Level
When the panel is turned on, the access level reverts to the User level. To gain access to the Tech or Admin
levels, use the Elevate Access Level menu, as follows: Configuration →System →PIN Settings →Elevate
Access Level.

CANplusTM CP640 - EN
Control Panel Operation Manual
17
9M02-1000-A001-EN
Revision B
The panel will prompt for a PIN input. User, Tech or Admin level access will be granted based on which PIN is
entered. For example, if the Tech level PIN is entered, Tech level access will be granted, and similarly if Admin
or User level PINs are entered. If the entered PIN does not match User, Tech or Admin, then “Incorrect PIN” is
displayed and the access level reverts to User.
Once elevated, the access level stays in effect until the panel is turned off.
PIN Change
PINs can be changed via the menu as follows: Configuration →System →PIN Settings →PIN change.
The PIN that is changed is the PIN for the current access level. For example, at the User level, only the User PIN
can be changed. To change the Tech PIN, use the Elevate Access Level menu and enter the correct Tech PIN.
Then go to the PIN Change menu to change the Tech PIN.
Menu PIN Required OFF
•
Accessing the menu is allowed with no PIN input required
•
Only User access level items are displayed
•
Use the Elevate Access Level menu to access the Tech or Admin menu items
Menu PIN Required ON
•
PIN is required to access the menu
•
User, Tech or Admin level access will be granted based on which PIN is entered. If the PIN does not
match the User, Tech or Admin PIN, then the panel will display “Invalid PIN”
Once an access level is granted, that level is retained until the key is turned off. When the key is turned back to
the ON position, the access level reverts back to User and follows the Menu PIN Required setting.

CANplusTM CP640 - EN
Control Panel Operation Manual
18
9M02-1000-A001-EN
Revision B
4 Manual Operation
Use the following steps for manual operation:
1.
Ensure that the Auxiliary Engine Stop (if fitted) is not activated.
2.
Turn the keyswitch to the run position.
3.
Turn the keyswitch clockwise to the start position and hold until the engine successfully starts.
4.
Release the keyswitch.
If the engine fails to start, the keyswitch must be returned to the off position prior to subsequent start attempts.
Note: The ECU will not preheat unless conditions warrant. If necessary, starting the engine may be
attempted by turning the key to the start position without waiting for preheat to expire.
4.1 Throttle Control
Throttle operation is determined by the type of throttle operator(s) installed along with the configured values of
the following parameters:
•
Minimum Requested RPM
•
Idle RPM
•
Intermediate RPM
•
Run RPM
•
Maximum Requested RPM
The ECU determines how the engine responds to the throttle requests and will not allow the engine speed to fall
below the ECU minimum RPM or go above the ECU maximum RPM. The ECU minimum and maximum RPM
values are determined by the ECU “payload” and typically require the engine manufacturer’s configuration tool to
adjust them. The ECU will honor RPM requests that are above the ECU’s minimum RPM as well as RPM
requests that are below the ECU’s maximum RPM.
Therefore, to avoid confusion, it is best not to set the panel’s Minimum Requested RPM below the ECU’s
minimum RPM or set the panel’s Maximum Requested RPM above the ECU’s maximum RPM.
For example, the panel’s Minimum Requested RPM is set to 800 RPM, yet the ECU payload defines the engine
minimum speed to be 900 RPM. In this case, the engine will not run at 800 RPM despite the control panel
requesting a lower engine speed. The ECU will ignore all RPM requests that are below 900 RPM, resulting in a
minimum speed of 900 RPM.
Note: The panel’s Minimum Requested RPM and Maximum Requested RPM can be configured using the
CANplusTM Software Suite, or via menus within the display (if enabled by PIN). See the Configuration
section for more information.
4.2 Ramp Throttle
The standard Ramp Throttle uses a momentary rocker switch to adjust the requested engine speed. All throttle
requests are sent directly to the engine using CAN throttle control.

CANplusTM CP640 - EN
Control Panel Operation Manual
19
9M02-1000-A001-EN
Revision B
Note: Throttle control requires CAN throttling to be enabled in the ECU. CAN throttling is also known as
Torque Speed Control or TSC1.
When first started, the requested engine speed is Idle RPM.
•
Pressing and releasing the rabbit icon increases the speed by the switch/rotary increment value
(default = 50 RPM)
•
Pressing and holding the rabbit icon causes the speed to continue to increase (ramp) until the
maximum speed is achieved
•
Pressing and releasing the turtle icon decreases the speed by the switch increment value (default =
25 RPM)
•
Pressing and holding the turtle icon causes the speed to decrease (ramp) until the minimum speed is
achieved
•
The CP640 will smoothly ramp the RPM up and down using the Max RPM change / s value (default =
500). This value can be changed in the Throttle →Switch/Rotary →Max Change / s menu.
4.3 Rotary Throttle Control
The optional Digital Rotary Throttle uses a rotary switch to simulate the operation of a throttle. When the engine is
first started, the requested engine speed is always Idle RPM. Turning the throttle knob clockwise increases the
requested engine speed by the switch/rotary increment value (default = 50 RPM). Turning the throttle knob
counter-clockwise decreases the requested engine speed.
4.4 Stopping the Engine
To stop the engine, simply turn the key to the “OFF” position. Do not use the Auxiliary Engine Stop (if fitted) to
stop the engine under normal conditions.
4.5 AutorampTM
The optional Autoramp™ feature allows the use of configurable warm up and cooldown profiles to help protect
engines and other assets such as plumbing, or to ensure proper ramp up and down of pressure or flow.
The Autoramp™ feature uses the configurable Autoramp™ RPM and time profiles. The settings are described in
the following table; the diagram shows the settings and their relationships to each other.
Setting
Description
Idle RPM
Selects the RPM that the control system will request for idle speed. If the engine is
started, it will always begin running at Idle speed.
Intermediate RPM Selects the RPM that the control system will request for intermediate speed.
Intermediate speed is a specific speed point at which the engine will pause during
the ramping up cycle. The Intermediate speed pause duration is configurable in the
Autoramp →Time Profile menu. The intermediate speed can be used to prime a
pump or charge lines during the optional automatic ramp operation.
Run RPM Selects the RPM that the control system will request for run speed. The run speed
is the normal operating speed.

CANplusTM CP640 - EN
Control Panel Operation Manual
20
9M02-1000-A001-EN
Revision B
Note: The minimum engine speed is controlled by the ECU. Requesting a lower speed causes the engine to
run at the ECU minimum speed. RPM limits are configured into the panel to limit the requested speed.
Changing the panel’s Minimum Requested RPM and Maximum Requested RPM requires a Tech Level
Password or higher in order to access those settings. Those values can also be adjusted using the
CANplusTM Configuration Suite.
Note: If an Intermediate RPM is not desired, it can be set to the same speed as Idle RPM while also setting
Ramp Up s (seconds) to 0 seconds.
Note: Intermediate and Run RPM settings are only applicable during the optional automatic ramp operation
and have no affect when the panel is manually started.
To utilize the optional Autoramp™ feature, the Autoramp™ RPM and Time setting must be configured. Once
configured, turn the key to the ON position from the OFF position without cranking the engine. With the engine off,
press and release the Autoramp™ switch at the top right of the control panel. After releasing the switch, the
Autoramp™ LED will start blinking, and the panel will automatically start the engine. The panel will follow the
configured Autoramp™ RPM and time profiles until the Run Speed is achieved, at which point the LED will turn
solid green.
Table of contents
Other Cattron Control Panel manuals
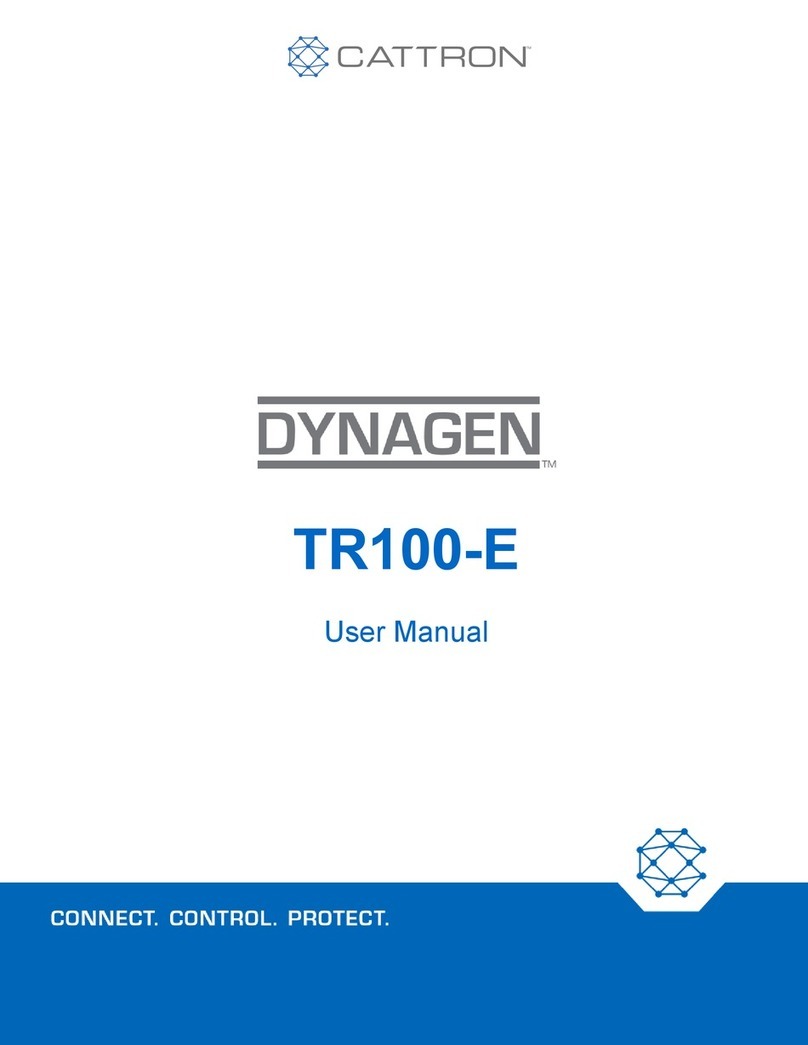
Cattron
Cattron DYNAGEN TR100-E User manual
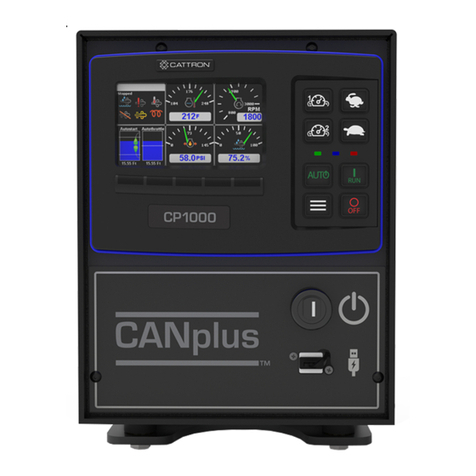
Cattron
Cattron CANplus CP1000 User manual

Cattron
Cattron CANplus CP750-E User manual

Cattron
Cattron DYNAGEN TR100 User manual
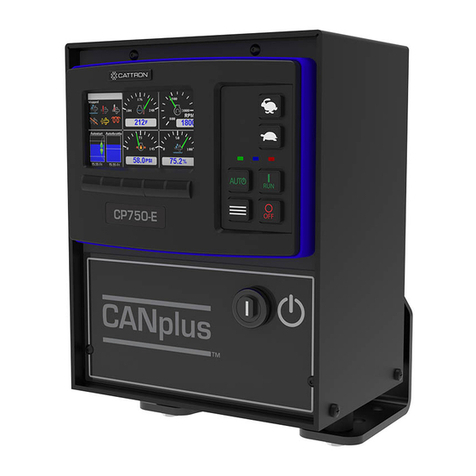
Cattron
Cattron CANplus CP750-E User manual
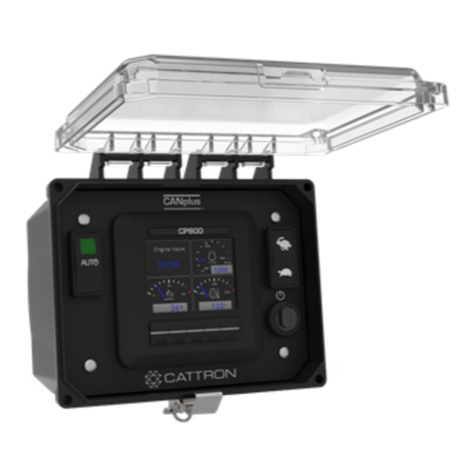
Cattron
Cattron CANplus CP800 User manual
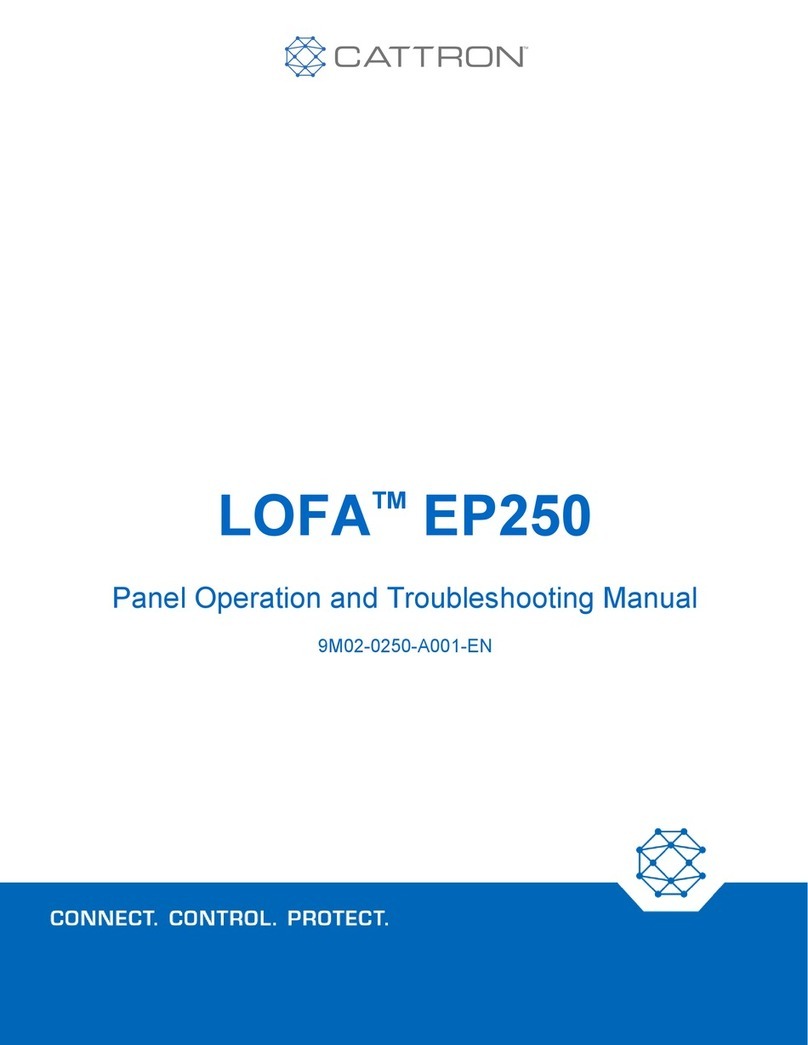
Cattron
Cattron LOFA EP250 Operating instructions

Cattron
Cattron CANplus CP750 MODBUS User manual
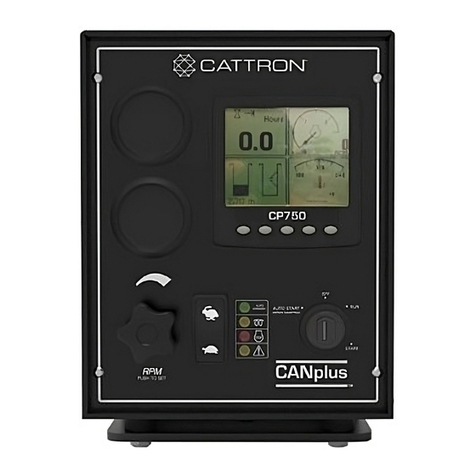
Cattron
Cattron CANplus CP750 MODBUS Instruction sheet
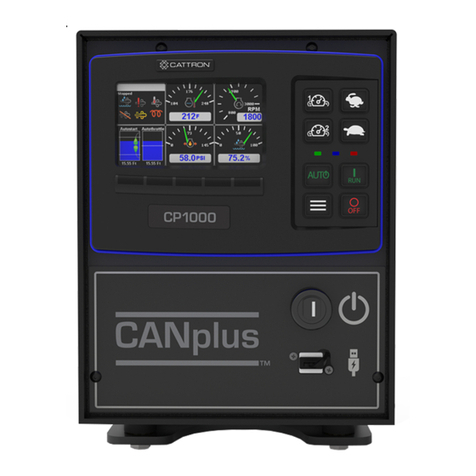
Cattron
Cattron CANplus CP1000 User manual