Cattron DYNAGEN ES52 User manual

ES52
User Manual

DynaGenTM ES52 - EN
User Manual
2
9M02-9253-A001-EN
Revision A
Revision History
VERSION
DATE
NOTES
2.10
08/2012
Improved crank disconnect procedure. Added VTS2 connection to technical
notes. Made other minor changes.
3.0
12/2015
Updated Troubleshooting note for flashing Over-speed. Updated technical
notes for 10A diode to apply only to EI, FE and LT (cooldown). Removed
reference to hour meter; not available on ES52. Updated wiring guidelines
section. Changed max temp in Specifications. Clarified that Aux Input is also
failure, as for Oil and Temp. Cleaned up Troubleshooting section on loss of
speed during cranking. Added new DynaGen logo. Changed wiring diagram to
clarify that Auto/Test switch is actually a switch. Clarified section on Test/RSC.
Reorganized remote start contacts and added section on pins 12 to 19 in I/O
table. Added 20A fuse blown to unit inoperable section in Troubleshooting.
4.0
08/2017
Added Zero Speed RestartTM feature to manual. Added default settings. Added
title page picture. Relabeled “Oil Switch Verification”. Added section to
Troubleshooting about unit not cranking. Added flashing Over-crank to LED
tables.
5.0
04/2019
Added remote start contact relay to wiring diagram. Improved Oil Verification
section. Clarified that 69 Hz/1080 Hz refers to Over-speed, not crank
disconnect.
A
09/2021
Document rebranded, and contact information updated.
B
09/2022
Updated branding information.
Any information furnished by Cattron™ and its agents is believed to be accurate and reliable. All specifications are subject to change without notice.
Responsibility for the use and application
of Cattron products rests with the end user since Cattron and its agents cannot be aware of all potential uses.
Cattron makes no warranties as to non-infringement nor as to the fitness, merchantability, or sustainability of any Cattron products for any specific
or general uses. Cattron Holdings, Inc., or any of its affiliates or agents shall not be liable for incidental
or consequential damages of any kind. All
Cattron products are sold pursuant to the Terms and Conditions of Sale, a copy of which will be furnished upon request. When used as a tradename
herein,
Cattron means Cattron Holdings, Inc. or one or more subsidiaries of Cattron Holdings, Inc. Cattron™, corresponding logos, and other marks
are
trademarks or registered trademarks of Cattron Holdings, Inc. Other marks may be the property of third parties. Nothing herein provides a license under
any Cattron or any third party intellectual property right.

DynaGenTM ES52 - EN
User Manual
3
9M02-9253-A001-EN
Revision A
Contents
1 Overview.............................................................................................................................................................4
1.1 Receipt of Shipment and Warranty Return Information ..........................................................................4
1.2 Limited Warranty .....................................................................................................................................4
1.3 DynaGen ES52 Support Webpage .........................................................................................................4
1.4 ES52 Specifications ................................................................................................................................4
2 Introduction.........................................................................................................................................................6
3 Wiring Installation Guidelines .............................................................................................................................7
3.1 Wire Sizing ..............................................................................................................................................7
3.2 Wiring Guidelines ....................................................................................................................................8
3.3 Terminal Descriptions .............................................................................................................................9
3.4 General Wiring Diagram .......................................................................................................................11
3.5 Adjustments and Setup Procedures .....................................................................................................12
3.5.1 Factory Settings .......................................................................................................................13
3.5.2 Selecting the Engine Speed Range .........................................................................................14
3.5.3 Low Oil Pressure Switch Verification .......................................................................................14
3.5.4 Selecting a Timer Function ......................................................................................................15
3.5.5 Adjusting Timer Duration .........................................................................................................16
3.5.6 Crank and Crank Rest .............................................................................................................16
3.5.7 Selecting the Maximum Number of Crank Tries ......................................................................16
3.5.8 Crank Disconnect and Over-Speed Pot Adjustment................................................................17
3.5.9 Loss of Speed (During Cranking).............................................................................................17
3.5.10 Warm Up ..................................................................................................................................18
4 Operation ..........................................................................................................................................................19
4.1 ES52 Startup / Shutdown Behavior ......................................................................................................19
4.2 Zero Speed Restart Feature .................................................................................................................19
4.3 Oil Verification .......................................................................................................................................19
4.4 Front Panel LED Indications .................................................................................................................19
5 Troubleshooting Guidelines..............................................................................................................................21
6 Technical Notes on Frequently Asked Questions ............................................................................................24
7 Technical Support.............................................................................................................................................26

DynaGenTM ES52 - EN
User Manual
4
9M02-9253-A001-EN
Revision A
1 Overview
Please read this manual before installing the unit.
1.1 Receipt of Shipment and Warranty Return Information
Upon receipt of shipment, carefully remove the unit from the shipping container and thoroughly examine the unit
for shipping damage. In case of damage, immediately contact the carrier and request that an inspection report
be filed prior to contacting Cattron.
All returned items are to be shipped prepaid and include a Return Material Authorization (RMA) number issued
by Cattron.
1.2 Limited Warranty
For warranty information, please refer to the standard terms and conditions of sale at www.cattron.com.
1.3 DynaGen ES52 Support Webpage
For up-to-date manuals and other information, please visit www.cattron.com.
1.4 ES52 Specifications
Parameter Specification
Operating VDC Limits 3.3 VDC min – 30 VDC max (provided minimum 8 VDC present at
starting
Standby Current Draw 12.2 mA at 12 VDC (12.4 mA at 24 VDC)
Operating Current Draw 140 mA at 12 VDC (80 mA at 24 VDC)
Reverse Polarity Protected Internal protection will prevent damage to unit under a reverse polarity
condition; re-connect power leads properly, and normal operation will
resume
J1113-11 Transients Pulse 1A (Supply Disconnect), Pulse 2A (Sudden Disconnect), Pulse 4
(Starter Motor Engagement), Pulse 5 (Load Dump); details of the test
parameters are available, please contact Cattron at www.cattron.com
Speed Sensing Input Accepts Generator AC output directly
Fly Wheel Alternator
Engine Alternator
Magnetic Pickup
Speed Sensing Maximum Rating Withstands line voltage up to 300 VAC
Operating Temperature Range -40°C to +70°C
Operating Humidity Range 0 to 95% non-condensing
Fuel & Crank Contact Output 10A maximum each continuous sourcing (+Bat) output
Annunciation Outputs Sourcing (+Bat) outputs (300 mA maximum per output)
Lamp Test Terminal Close to +Bat to test LEDs

DynaGenTM ES52 - EN
User Manual
5
9M02-9253-A001-EN
Revision A
Parameter Specification
Actual Unit Weight 0.67 lb (0.30 kg)
Shipping Weight 1 lb (0.45 kg)
Unit Dimensions 3.302” x 3.342” x 1.8”
Shipping Dimensions 4” (10.16 cm) x 4” (10.16c m) x 3” (7.62 cm)

DynaGenTM ES52 - EN
User Manual
6
9M02-9253-A001-EN
Revision A
2 Introduction
The ES52 provides Automatic Start/Stop and protection control for all types of engine-driven equipment.
Simplicity of use, safety, features, versatility, and over-all quality are paramount, providing the most cost effective
and reliable solution available. Ours is one of the smallest controllers available, with the best value per dollar-
cost, backed by an industry leading five-year or 17,500-hour warranty.
The ES52 maintains backward compatibility to the extent that it can replace similar products without substantial
rewiring. Functionally, however, it is loaded with unique features, as follows:
•“No speed signal” detection: Should the frequency of the speed sensing signal go to Zero while the
engine is running, or fail to appear during cranking, a No Speed Failure is asserted and specifically
indicated
Note: Speed signal detection during cranking can be disabled via an onboard Dip Switch. In some
cases when using the generator main power as the speed signal source, it is required to disable
this shutdown (when the residual is very low).
•Differential speed sensing inputs (for twisted-pair connection): Very effective interference prevention by
means of noise cancellation
•Excellent EMI handling: Software detection of, and recovery from, noise corruption
•Replaceable Relays: Replaceable relays provided within onboard sockets; relays rated 20A at 30 VDC
•Replaceable Fuse: Onboard replaceable 20A fuse, mini-fuse (standard automotive type)
•Reverse Polarity Protection: No requirement for series diode on supply
•3.3 VDC to 30 VDC, -40ºC to +85ºC Operation: Works anywhere, anytime
•Zero Speed RestartTM: Prevents starter pinion wear by ensuring that no engagement of the starter is
possible unless the speed is Zero
•Oil BypassTM: Waits 15 seconds from start for 1-3 crank tries, and 20 seconds for more than 3 crank
tries, before enabling low oil pressure monitoring; this requires no user setting
•Four Timer Functions: Glow Plug, Smart ChokeTM, Air-Gate and Slow
•Rest Time Indication: Provides feedback between crank attempts
•Warm Up: Turns on an output which can control a load device; Warm Up timer output is provided on all
ES52 units via Terminal 19 and Warm Up timer is fixed at 2 minutes
•Small Size: 3.302” x 3.342” x 1.842”; 0.67 lb

DynaGenTM ES52 - EN
User Manual
7
9M02-9253-A001-EN
Revision A
3 Wiring Installation Guidelines
WARNING
THE CONTROLLER DOES NOT GENERATE A WARNING PRIOR TO
AUTOMATIC
ENGINE
START. DO NOT WORK ON THE ENGINE WHILE POWER IS APPLIED TO THE UNIT. IT IS
HIGHLY RECOMMENDED THAT WARNING SIGNS BE PLACED ON THE ENGINE EQUIPMENT
INDICATING THE ABOVE.
Following these instructions will help avoid common installation problems during wiring and setup:
•Battery must be disconnected before any wiring connections are made
•Wire length from the engine to the controller should not exceed 6 m (20 ft)
3.1 Wire Sizing
Wiring size and type should be as specified below. Use stranded wire, since solid wire tends to crack, break
and loosen over time.
Terminal Wire Size Current (max) Function
CON 1 18 100 mA Speed signal connection via onboard connector
1 18 100 mA LED Test Switch
2 18 7 mA Oil Pressure Switch
3 18 7 mA High Temperature Switch
4 18 7 mA Auxiliary Input Switch
5 14 10 A Starter Solenoid/Pilot Relay
6 12 20 A Battery Negative (-)
7 12 20 A Auto Switch
8 12 20 A RSC1 (Remote Start Contact Connection)
9 12 20 A RSC2 (Remote Start Contact Connection)
10 12 20 A Start/Stop Connection
11 14 10 A Fuel Solenoid/Pilot Relay
12 18 300 mA Timer Output
13 to 18 18 300 mA Annunciation Outputs
19 18 300 mA Warm up Output
20 18 300 mA Annunciator Common Ground Only
(DO NOT use this as main ground connection)
!

DynaGenTM ES52 - EN
User Manual
8
9M02-9253-A001-EN
Revision A
3.2 Wiring Guidelines
WARNING
DO NOT APPLY EXTERNAL VOLTAGE TO ANNUNCIATOR OUTPUTS (TERMINALS 13
TO 18). THIS WILL DAMAGE THE ES52. IF THIS MAY OCCUR IN YOUR APPLICATION,
PLACE A DIODE IN SERIES WITH EACH AFFECTED ANNUNCIATOR OUTPUT.
•DO NOT use wire smaller than 18 AWG
•The connections supplying DC power to the ES52 panel should preferably run directly from the battery
posts with no splices or other connections except a 25A fuse connecting the positive line directly to the
+Battery terminal. Avoid, as much as possible, using the chassis (aluminum or iron engine parts) as a
return conductor for battery negative voltage; copper wiring is recommended. Failure to follow the above
may result in erratic operation, due to large voltage drops across the wiring connections
•DO NOT short the Crank output or Fuel outputs to ground, as this will cause the onboard 20A fuse to
blow and may result in damage to the ES52’s onboard relays
•When replacing the fuse, removable terminals, and relays, only use factory recommended parts
•DO NOT use AC coil slave relays from controller outputs. Use intermediate relays of suitable size and
coil rating
Note: All ES52 engine controllers are shipped standard with 12 VDC coil relays for +12 VDC
systems. If the engine controller is used in a +24 VDC system, the onboard relays MUST be
replaced with 24 VDC coil relays.
•DO NOT exceed the maximum rated current and voltage on each of the controller outputs. Do not
exceed 10A for the Fuel output, 10A for the Crank output, and 300 mA for the Annunciation and Timer
outputs
•The Annunciation and Timer outputs are internally protected against overload and short circuit (fault)
Note: When a fault appears on one of the annunciation outputs, only that specific output becomes
un-operable; all other annunciation outputs and the entire front panel LEDs continue to
operate. When the fault is removed and the unit is restarted, the output resumes proper
operation.
•Two wires must be connected for the speed signal
•Diodes are provided across Fuel, Crank, and Annunciation outputs, to protect the outputs from inductive
kick-back. Diodes should be placed across slave relay contacts when used to actuate any inductive
loads, such as solenoids, to protect the contacts from damage caused by arcing. In addition to
prolonging the useful life of the relays, placing such diodes will help reduce generated electrical noise
•To verify the operation of engine controller outputs, measure voltage (i.e., set meter to read in volts)
when outputs should be ON
!

DynaGenTM ES52 - EN
User Manual
9
9M02-9253-A001-EN
Revision A
3.3 Terminal Descriptions
Terminal # Description
CON1 (Speed) Speed signal input for crank disconnect, engine run, and Over-speed sensing. Generator
output, magnetic pickup (MPU) sensor, or alternator output can be used.
•Use at least twisted pair wiring for this connection.
•Polarity does not matter.
•Use two female 0.250” inch insulated female quick connects for the connection.
For MPU Sensor:
•One side of the MPU must both be grounded and connected to the controller,
otherwise erratic behavior can result.
Use a shielded MPU with a shielded cable grounded at one end only for best reliability.
1 Lamp test connecting +12/24 VDC to lamp test activates all the front panel LEDs.
Note: Annunciation outputs DO NOT activate under LED test.
2 Oil pressure input for proper operation, oil input must be connected to ground or +12/24
VDC via an oil switch. This switch must be the N.O. type, close on failure (low pressure).
When active, it shuts down the engine.
3 Temperature switch for proper operation, temperature input must be connected to
ground or +12/24 VDC via a temperature switch. This switch must be the N.O. type, close
on failure (high temperature). When active, it shuts down the engine.
4 Auxiliary input for proper operation, auxiliary input must be connected to ground or
+12/24 VDC via a sensor switch. This switch must be the N.O. type, close on failure.
When active, it shuts down the engine.
5 Crank output provides 10A maximum. Crank output closes to +12/24 VDC during
cranking, and opens when the engine has started, or during crank rest.
6 Battery ground connection for the controller module. A good ground connection, directly
from the battery, is required for proper operation.
7 Auto when +12/24 VDC is applied; the controller is in the standby mode waiting for a
Start/Stop signal (+12/24 VDC applied to Start/Stop).
8 - 9
Remote Start Contacts
RSC1 is tied internally to Auto (terminal 7) and RSC2 is tied internally to Start/Stop
(terminal 10), so when RSC1 and RSC2 are shorted, they bring the battery positive that is
at the Auto terminal to the Start/Stop terminal which causes the controller to start the
engine (see Start/Stop below) and provide power to the crank and fuel outputs.
This means the current for Crank output and Fuel output will pass through the remote
start contacts. The wiring and the remote device/switch must be rated for this current
draw. If this is a problem, then an external relay can be used. See the 25 section at the
end of this manual.

DynaGenTM ES52 - EN
User Manual
10
9M02-9253-A001-EN
Revision A
Terminal # Description
10 Start/Stop when +12/24 VDC is applied, the controller is powered and proceeds to start
the engine. The power for the crank output and fuel output is obtained from this
terminal. If the 20A fuse is blown, then the ES52 will not start.
11 Fuel output provides 10A maximum. Fuel output closes to +12/24 VDC when start signal
is actuated, and it opens when either an engine failure is detected or when the stop signal
is applied.
12 Timer output has one of four possible functions (Glow Plug, Smart Choke, Air-Gate or
Slow). This output closes to +12/24 VDC when activated.
13 Low oil pressure output closes to +12/24 VDC when the engine shuts down due to a
low oil pressure condition. Flashing Low Oil output indicates an Auxiliary Input failure.
14 High temperature output closes to +12/24 VDC when the engine shuts down due to a
high temperature condition.
15 Over-crank output closes to+12/24 VDC when the engine shuts down due to an Over-
crank failure.
16 Over-speed output closes to +12/24 VDC on an Over-speed failure and is open
otherwise. Flashing output indicates Loss of Speed Signal.
17
Engine running output closes to +12/24 VDC when the engine speed is greater than the
crank disconnect setting, and it opens when the engine stops. Flashing output indicates
Crank Rest period.
18 Engine failure output activates on any failure (closes to +12/24 VDC when activated).
19 Warm up output turns on after the controller has been running for 2 minutes and 10
seconds. Output turns on immediately if battery voltage is applied to Start/Stop (terminal
10) and the speed is greater than the crank disconnect pot setting when the controller is
not cranking.
Note: Pins 12 to 19
The maximum rating of each output depends on how many outputs are on simultaneously on pins 12
to 19. Do not exceed these values:
1 on = 300 mA, 2 on = 230 mA, 3 on = 160 mA, 4 on = 123 mA, 5 on = 91 mA, 6 on = 80 mA,
7 on = 66 mA, 8 on = 52 mA
Good practice is to use 50% of the maximum rating.
20 Common ground for annunciation outputs only. DO NOT USE AS MAIN GROUND TO
CONTROLLER UNIT.

DynaGenTM ES52 - EN
User Manual
11
9M02-9253-A001-EN
Revision A
3.4 General Wiring Diagram
Please see the following figures for the wiring diagram (Figure 1) and dimensions (Figure 2).
ATTENTION: All ES52 Controllers come with 12 VDC Relays for 12V systems. For 24V systems, replace
with 24VDC Relays.
ES52 Variant Note: A diode across Auto and Start/Stop terminals is required on versions of the ES52 with the
Cool-Down feature (ES52 EI, FE, and LT variants). See the 24 section at the end of this
manual for further information. The standard ES52 version does not require this.
Figure 1: Wiring Diagram

DynaGenTM ES52 - EN
User Manual
12
9M02-9253-A001-EN
Revision A
Figure 2: Dimensions
3.5 Adjustments and Setup Procedures
WARNING
THE FOLLOWING PROCEDURES WILL REQUIRE ENGINE OPERATION. BE SURE TO FOLLOW
ALL SAFETY GUIDELINES AND WIRING PROCEDURES.
The rear of the ES52 controller contains four adjustable potentiometers (abbreviated as “pots” throughout this
document and nine DIP switches.
Potentiometer (Pot) Adjustment
To increase a pot’s setting, turn it clockwise. To decrease it, turn it counterclockwise. Onboard pots are 20 turns
nominal; therefore, turn pots fully 20 turns to ensure that you are at either the minimum or maximum setting.
Each pot has a clutch to protect from overturning and thus potentially requires one to two turns to overcome this
clutch if the pot is at the minimum or maximum position before the value actually starts to change.
!

DynaGenTM ES52 - EN
User Manual
13
9M02-9253-A001-EN
Revision A
Potentiometers are shown in Figure 3as they appear on the rear of the ES52 series units. Figure 4shows the
label on the rear of these units.
1 – Crank Disconnect
2 – Over-Speed
3 – Crack / Rest
4 – Timer
Figure 3: Potentiometers
Figure 4: Label on Rear of ES52 Series Units
“Oil Bypass” period refers to the delay period (fixed at 15 seconds for 1-3 crank tries and 20 seconds for more
than 3 crank tries) immediately after the Engine Running LED illuminates (engine starts). During this period the
oil input is bypassed (ignored).
3.5.1 Factory Settings
The ES52 is set up with the following settings from the factory:
•20 Hz / 300 Hz Crank Disconnect in low- or high-speed mode respectively
•10 s Crank / Crank Rest
•10 s Timer output; Timer set to preheat functionality
•DIP switches 1 and 2 ON; all others OFF
CRANK TRIES
S1 S2 S3
off
on
off off
on on
on
on
on-Enabled
on on #
1
2
3
4
5
6
setup
off
on
on
on
TIMER
SPEED SETTING
off off
S4 S5
Slow
Choke
- single crank attempt - 4 to 256 sec
Range
on on
off off lo
hi
CRDC OVSP
12 - 140 44 - 300
60 - 4156 300 - 8492
S6
off
on Enabled
CRDC - Crank Disconnect (Hz)
OVSP - Overspeed (Hz)
(52 Model Only)
on
off on
off
on
off
on
off off
off
off
CRANK TRIES
LOSS OF SPEED
WHILE CRANKING
S1 S2 S3
off
on
off off
on on
on
#
1
2
3
4
5
6
off
on
on
on
TIMER
SPEED SETTING
off off
OIL VERIFICATION
S4 S5
Glow Plug
on on
off off lo
hi
CRDC OVSP
12 - 140 44 - 300
60 - 4156 300 - 8492
off
on
Disabled
S7 S8
S9
(52 Model Only)
Airgate
off
off off
Setting
on
off
off-Disabled
on
off
on
off off
off
off on

DynaGenTM ES52 - EN
User Manual
14
9M02-9253-A001-EN
Revision A
The steps to calibrate the ES52 controller to a specific system are as follows:
1. Select the Engine Speed Range (DIP switches 4 and 5).
2. Low Oil Pressure Switch Verification – verify the low oil pressure switch is enabled or disabled (DIP
switch 6).
3. Select a Timer function (DIP switches 7 and 8).
4. Adjust the Timer setting (only needed for Glow Plug and Slow functions).
5. Calibrate the Crank / Rest Time.
6. Select the maximum number of Crank Tries (DIP switches 1, 2 and 3).
7. Calibrate the Crank Disconnect / Over-speed settings.
8. Enable / disable Loss of Speed (During Cranking).
See the following sections for a more detailed explanation of each step.
3.5.2 Selecting the Engine Speed Range
Two speed ranges are provided to permit the greatest accuracy when adjusting the Crank Disconnect and Over-
speed settings. The speed ranges are selectable from DIP switches 4 and 5.
Generator output: When using generator output (50 or 60 Hz), speed range 1 (LO) is required.
Flywheel alternator: When using a flywheel alternator, speed range 1 (LO) is required. Refer to the engine’s
specification for the number of poles attached to the flywheel (i.e., 1 pole (60 Hz),
2 poles (120 Hz), and 4 poles (240 Hz)).
Engine alternator: An engine alternator would require speed range 1 (LO) or 2 (HI). Refer to the engine’s
specification for pulley ratio and number of poles before selecting the range.
Magnetic pickup: When using a magnetic pickup, speed range 2 (HI) is required.
Selection of the proper engine speed range is summarized in the following table.
Range SW 4 SW 5 Crank Disconnect (Hz) Over-Speed (Hz)
1 (LO) OFF OFF 12 - 140 Hz 44 - 300 Hz
2 (HI) ON ON 60 - 4156 Hz 300 - 8492 Hz
3.5.3 Low Oil Pressure Switch Verification
The low oil pressure switch must be the type that opens when oil pressure is normal and closes on Low Oil
pressure (failure condition or engine stopped). DIP switch 6 must be set to the ON position if you wish to
enable oil verification, and it must be set to the OFF position if oil verification is to be disabled.
If DIP switch 6 is ON, prior to Cranking, the controller will attempt to verify that the pressure switch is connected
and operating properly by checking if the circuit is closed. If the oil pressure switch does not work or the wire fails
to make the connection, the engine will be prevented from starting, and the ES52 will assume a ‘wait and see’
mode (as indicated by a steady Low Oil and flashing Engine Running LED). As soon as the oil pressure switch
closes, Cranking will proceed as usual.
If the engine starts, the controller will check for a Low Oil failure condition only after the Oil Bypass period.

DynaGenTM ES52 - EN
User Manual
15
9M02-9253-A001-EN
Revision A
Note that if this verification was not performed, a ‘bad connection’ of the oil switch might go unnoticed until such
time as the oil runs out and engine damage occurs!
Note:
i. Oil circuit verification is only performed under the following conditions:
a. On the first Cranking attempt.
b. If the engine has been previously running, and more than 5 minutes of rest have elapsed.
ii. If DIP switch 6 is set to the OFF position, the ES52 does not provide oil verification. The ES52 goes
immediately into cranking; it will then check for a low oil failure condition after the Oil Bypassperiod has
elapsed.
Low Oil Pressure Switch verification is summarized in the following table.
SW 6 Low Oil Pressure Switch Verification
ON Enabled
OFF Disabled
3.5.4 Selecting a Timer Function
The timer function is configurable from DIP switches 7 and 8. The output terminal associated with this timer
setting is terminal # 12. It has four configurable functions, of which two are adjustable, as follows:
Glow Plug: The Glow Plug timer is adjustable from 0 - 32 seconds. Glow Plug is a timing function used
with diesel engines. This output is energized on every Crank attempt for a set time prior to
cranking engine.
Choke: The choke function is used on gasoline engines having an electric choke. The choke output is
energized 2.5 seconds into the cranking cycle, but only on even numbered Crank attempts
(exception: single crank attempt mode allows choke). If the engine speed remains above the
Crank Disconnect setting, Choke output is turned off; but as soon as the speed falls below Crank
Disconnect, it is re-applied. This ON/OFF regulation will continue, if necessary, for as long as the
Oil Bypassperiod is in effect.
Air-gate: The air-gate output is used to control an air damper and only actuates for a fixed 10 seconds
immediately after an Over-speed Failure occurs. This feature is used for some diesel engines
that cannot be stopped quickly enough by merely shutting off the Fuel in the event of an Over-
speed condition. An electrically operated air damper is installed at the air intake, which
effectively ‘gags’ the engine to a stop. Refer to the engine’s manual for more information.
Slow: This function is adjustable from 0 - 256 seconds via the “Timer” pot. The “Timer” output
energizes when the engine speed goes above the Crank Disconnect speed (engine starts), and
it remains so for the prescribed duration. It is called “Slow” because it would, presumably, be
used to tell a governor to ‘go slowly’ for such applications as irrigation pumps, where running
slowly for the first minute or two prevents ‘water hammer’.
The timer settings are as specified in the following table.

DynaGenTM ES52 - EN
User Manual
16
9M02-9253-A001-EN
Revision A
SW 7 SW 8 Timer Function Adjustable Time
OFF OFF Glow Plug 0 - 32 seconds
ON OFF Air-gate Not Adjustable (fixed at 10 s)
OFF ON Choke Not Adjustable
ON ON Slow 0 - 256 seconds
3.5.5 Adjusting Timer Duration
This section applies to the Glow Plug and Slow timer functions only, as Air-gate and Choke do not use pots. The
Glow Plug is adjustable from 0 - 32 seconds; the Slow function is adjustable from 0 - 256 seconds.
For the Glow Plug setting (DIP switches 7 and 8 OFF):
1. Remove the wires connected to the Timer terminal # 12 and the Crank terminal # 5.
2. Apply power to the Start/Stop terminal # 10.
3. Measure the time that the “Timer” LED remains ON.
4. Remove power from the Start/Stop terminal # 10.
5. Increase or decrease pot setting as required. The pot resolution is 1.6 seconds/turn.
6. Return to step 2 as needed.
7. Re-connect the wires to the Timer terminal # 12 and the Crank terminal # 5.
For the Slow setting (DIP switches 7 and 8 ON):
1. Apply power to Start/Stop terminal # 10.
2. Allow the engine to Crank and start; the Engine Running LED turns ON.
3. The “Timer” LED will illuminate; measure the time that this LED remains ON.
4. Increase or decrease pot setting as required. The pot resolution is 12.8 seconds/turn.
5. Return to step 1 as needed.
3.5.6 Crank and Crank Rest
Enter the Setup Mode by setting DIP switches 1, 2 and 3 to the ON position. Apply power to Auto, and the
Over-crank LED will flash. The time between flashes indicates the Crank and Crank Rest time. Adjust the pot
accordingly to increase or decrease the Crank/Rest time.
3.5.7 Selecting the Maximum Number of Crank Tries
The Crank tries are adjustable from DIP switch positions 1, 2 and 3. Select the Crank tries most appropriate for
your application.
Note: An extended Crank attempt range is available, which extends the Crank time to a time spanning
from 4 to 256 seconds.
The number of Crank tries and the timer ranges are as specified in the following table.

DynaGenTM ES52 - EN
User Manual
17
9M02-9253-A001-EN
Revision A
Crank Attempts Switch 1 Switch 2 Switch 3 Time Range
SETUP ON ON ON 4 - 36 sec
6 OFF ON ON 4 - 36 sec
5 ON OFF ON 4 - 36 sec
4 OFF OFF ON 4 - 36 sec
3 ON ON OFF 4 - 36 sec
2 OFF ON OFF 4 - 36 sec
1 ON OFF OFF 4 - 36 sec
1 OFF OFF OFF 4 - 256 sec
3.5.8 Crank Disconnect and Over-Speed Pot Adjustment
From the factory, the Crank disconnect is set to 20 Hz in low-speed mode and 300 Hz in high-speed mode.
One turn gives approximately 6.4 Hz in low speed and approximately 205 Hz in high speed.
From the factory, the Over-speed is set to 69 Hz in low-speed mode and 1080 Hz in high-speed mode. One turn
gives approximately 13 Hz in low speed and approximately 410 Hz in high speed.
The best method to determine the proper Crank disconnect and Over-speed setpoints is to use a signal
generator (also known as a function generator). If you do not have one, you can adjust the pots knowing the
factory defaults and the Hz/turn numbers provided above.
3.5.9 Loss of Speed (During Cranking)
In the event there is a loss of speed, while cranking or running, the unit will shut down, and this is indicated by a
flashing Over-speed LED. Loss of speed is defined as no speed signal for at least 3 seconds. Loss of speed
begins 3 seconds into the crank cycle.
The Loss of Speed While Cranking portion can be disabled via DIP switch 9. When the DIP switch is in the UP
or ON position, the Loss of Speed While Cranking function is enabled. When the DIP switch is in the DOWN or
OFF position, the Loss of Speed While Cranking function is disabled.
Note: The Loss of Speed feature is maintained during all running conditions.
Note: If unit is configured for Generator Output, there may not be enough residual voltage during cranking
for this feature. It is recommended to disable this feature.
The following values are minimal recommended voltages for speed signal:
20 Hz – 0.075 V (75 mV)
60 Hz – 0.6V (600 mV)
4500 Hz – 0.8V (800 mV)

DynaGenTM ES52 - EN
User Manual
18
9M02-9253-A001-EN
Revision A
3.5.10 Warm Up
A Warm-up timer is provided on all ES52 series engine controllers. Terminal # 19 is the Warm-up timer output.
This output energizes 2 minutes after the engine running LED turns on (i.e., speed above crank disconnect
setting). When a stop signal is initiated, the Warm-up output turns off.
This Warm-up output can be used to control a load device; for example, allowing a generator to warm up before
connecting the load.

DynaGenTM ES52 - EN
User Manual
19
9M02-9253-A001-EN
Revision A
4 Operation
4.1 ES52 Startup / Shutdown Behavior
Note: The fuel output remains on during crank rest. There is no way to disable this.
4.2 Zero Speed Restart Feature
The ES52 has a starter protection feature where it will not turn on the crank output until the engine speed is zero.
•If the speed is not zero before cranking, preheat (timer) will be performed but the ES52 will pause until
the speed is 0 Hz or it will go into a failure (alternating Over-crank and Over-speed LEDs flashing) after
30 to 40 seconds
•If the speed is not zero during engine rest, the ES52 will not crank until it is zero. It will sit in engine rest
for 30 to 40 seconds and then go into failure (alternating Over-crank and Over-speed LEDs flashing)
4.3 Oil Verification
If Low Oil verification is enabled (DIP Switch 6 ON) and the low oil pressure switch fails verification, the controller
will remain in crank rest after the first crank attempt until the oil switch passes verification. During this time the
low oil pressure lamp will be on solid red. The engine run lamp will be on flashing green. See the setup section
on oil verification for more information.
4.4 Front Panel LED Indications
Figure 5shows the LED indicator lights on the front panel of the ES52.
Figure 5: LED Indicators
The following table lists the conditions that are indicated by the status of each of these LEDs.
What The LEDs Look Like Condition / Failure
No LEDs ON
“Ready”
– unit waiting for start signal; +12/24 VDC to Auto terminal
“OFF”
– no +12/24 VDC to Auto terminal

DynaGenTM ES52 - EN
User Manual
20
9M02-9253-A001-EN
Revision A
What The LEDs Look Like Condition / Failure
Low Oil, steady
No other lights ON?
Is Engine Running Flashing?
Low Oil Pressure Failure
Oil switch is not closed (mis-wired or not installed); engine will
crank when oil switch verifies
Low Oil, flashing Auxiliary Input Failure
High Temperature, steady Over-temperature Failure
Over-Crank, steady Engine would not start after specified number of Crank tries
Over-Crank, flashing Unit is in setup mode; time between flashes indicates crank and
crank-rest time
Over-Speed, steady Speed Signal present above Over-speed setting
Over-Speed, flashing
Was engine Cranking?
Was engine Running?
No speed signal available while cranking
The speed signal was zero while running for 3 seconds; the
engine has stalled, or the speed signal has been lost
Engine Running, steady Engine Controller is in running mode of operation
Engine Running, flashing
No other lights ON?
Low oil pressure light ON?
Crank-rest period; cranking will resume soon
Oil verification failed; see Low Oil, steady above
“Timer”, steady
Is Over-Speed LED ON?
Is Engine Running LED ON?
Is the engine Cranking?
If the engine is not cranking or running
10-second Air-gate timer
Slow timer feature (pot adjustable)
Choke feature
Glow Plug timer feature (pot adjustable)
Over-Speed and Over-Crank LEDs
flash alternately
Invalid speed range – check DIP switches 4 and 5
Crank disconnect set too high (above Over-speed setting)
Speed was not zero at the start of cranking (timeout)
Table of contents
Other Cattron Control System manuals
Popular Control System manuals by other brands
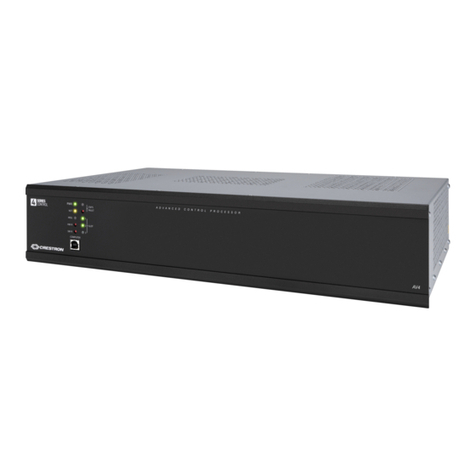
Crestron Electronics
Crestron Electronics 4 Series product manual
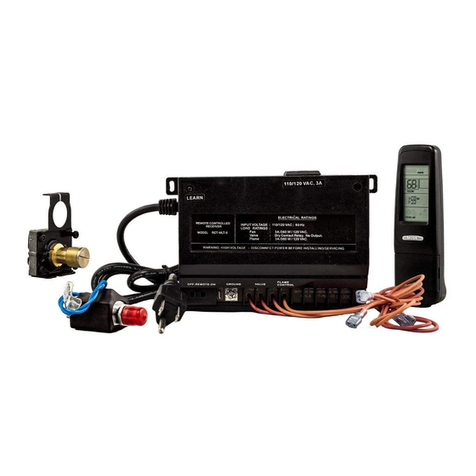
Skytech
Skytech RCTS-MLT-IV Installation and operation instructions
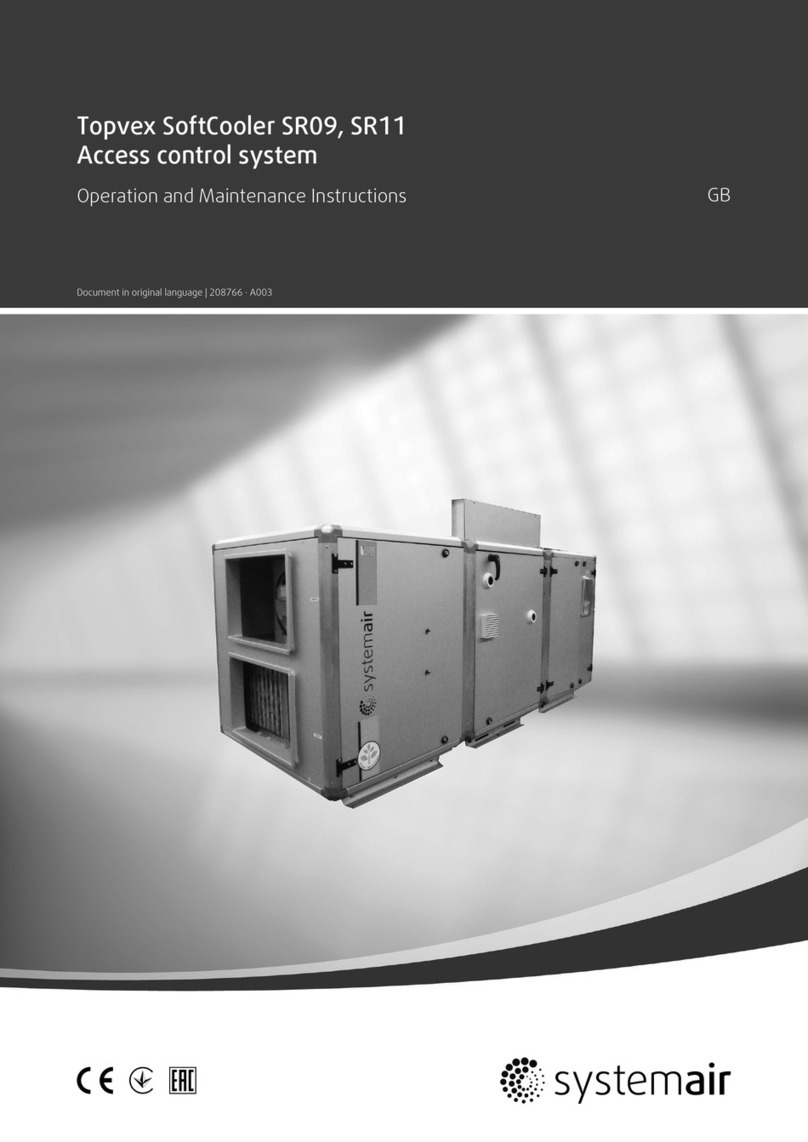
System air
System air Topvex SoftCooler SR11-L manual
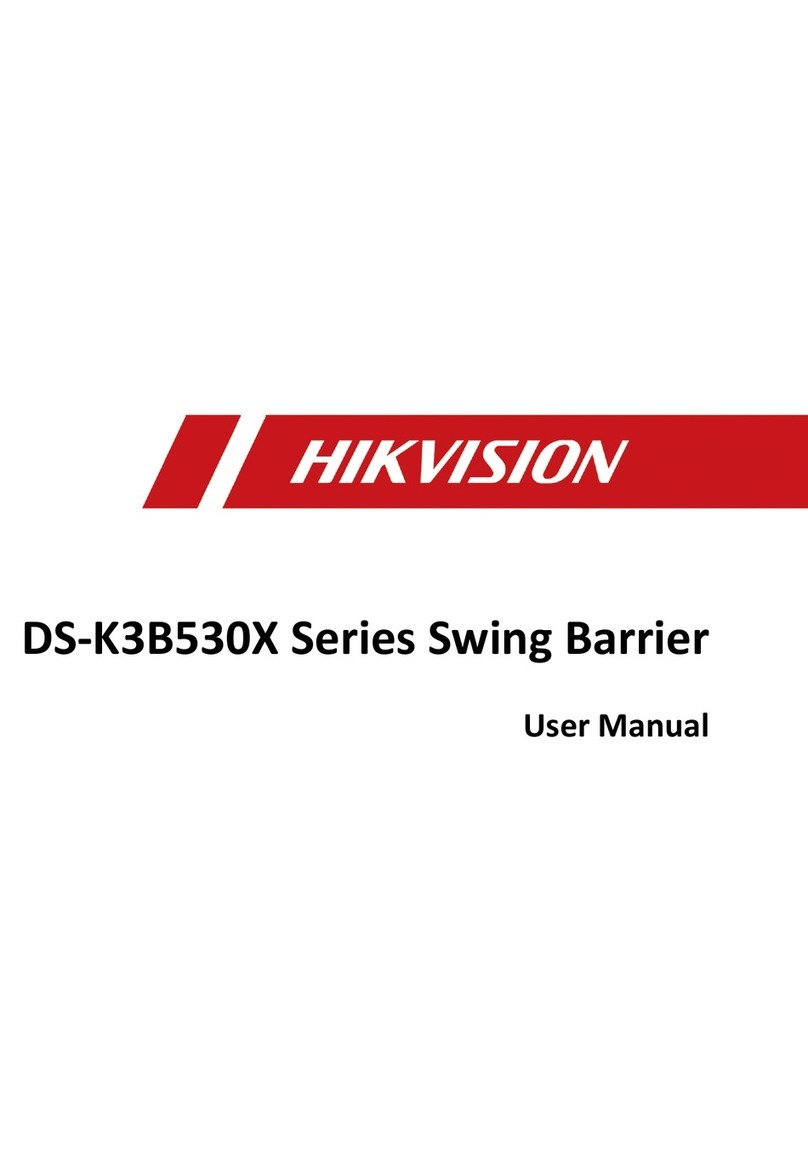
HIK VISION
HIK VISION DS-K3B530X Series user manual
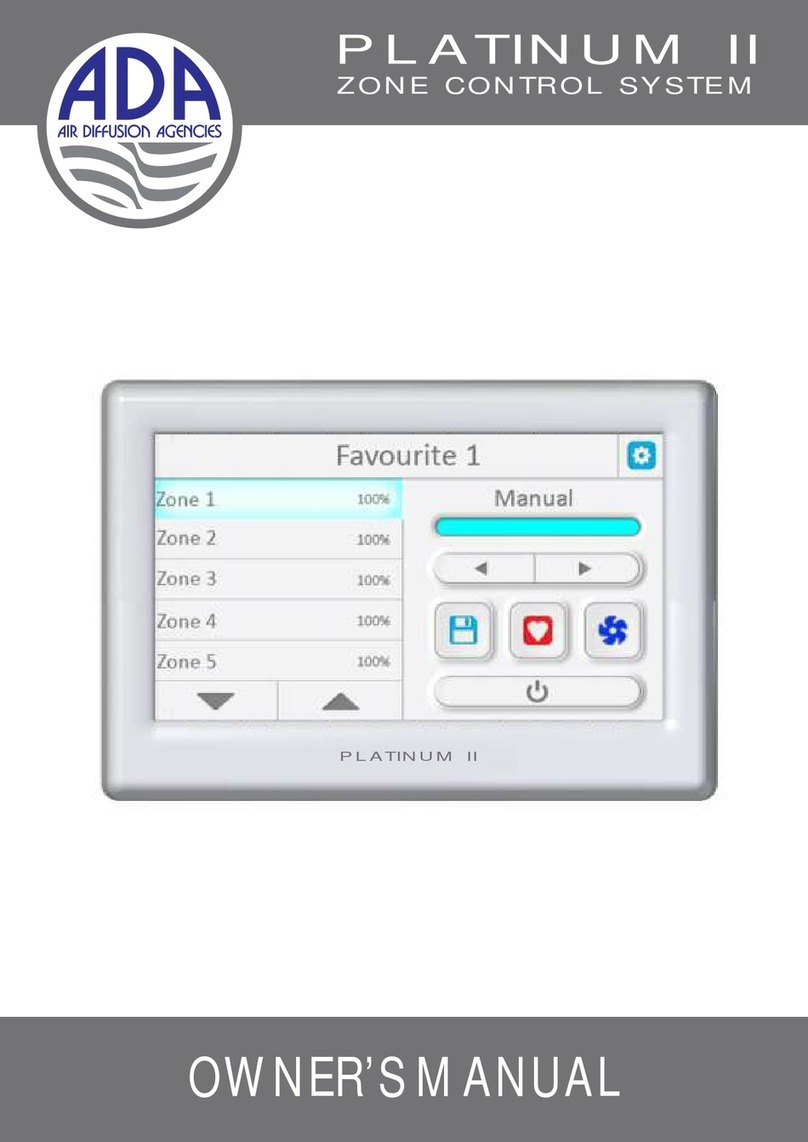
A/DA
A/DA PLATINUM II owner's manual
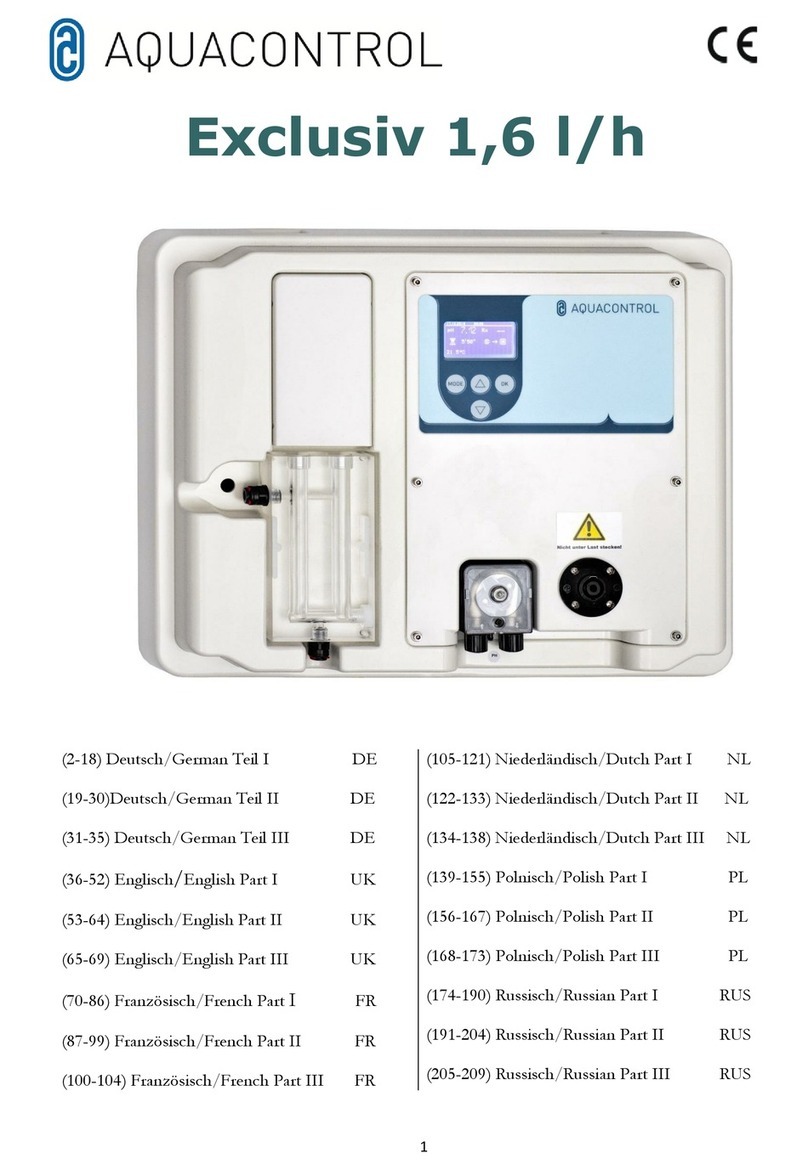
Aqua Control
Aqua Control Exclusiv 1,6 l/h manual