CBS S1500 User manual

- Custom Biogenic Systems -
2300 LN2Storage Unit
Set-up & Technical Manual
51255 Oro Drive • Shelby Township, MI 48315 • U.S.A.
1.800.523.0072 • Ph: 586.566.7200 • Fax: 586.566.7205
Visit our website at: www.custombiogenics.com
Leading the World with Innovative Cryopreservation Technology Solutions

Custom Biogenic Systems, warrants all manufactured
cryogenic equipment to be free from defects in
workmanship or materials, for a period of three years.
Custom Biogenic Systems' liabilities under the warranty
shall be limited to correcting or replacing the defective
workmanship or materials. A claimant under the warranty
must notify Custom Biogenic Systems within ten (10)
days after discovery of the defect. Custom Biogenic
Systems reserves the right, at their discretion, to correct
the defect(s) in the field without return shipment to
Shelby Township, Michigan.
This warranty does not cover defects on cryogenic
equipment resulting from abusive handling and
subsequent structural failure.
Product Warranty
Storage Unit Model Number ________
Serial Number _________
For Technical Assistance Call: 1-800-523-0072
Phone: (586) 566-7200 Fax: (586) 566-7205
We at Custom Biogenic Systems are proud of our work, and appreciate your purchase of this
product. With proper care, this equipment will be trouble-free for many years to come.
Before setting up and using your new cryogenic storage unit, first check to see that all parts
are accounted for and that no damage has occurred during shipping. Also, read this manual
completely before proceeding to set-up. If at any time you are unsure of the procedures for
set-up and use of this product, please contact CBS or your CBS sales representative.
- Important Information -

Safety...........................................................................page 1
V Series and S Series Vessel Descriptions..........................3
Initial Set-up........................................................................4
Operation.............................................................................4
Cryomonitor Software........................................................5
Front Panel controls- ALL..................................................6
Series 1500 & 3000 Back Panel ..........................................7
Series 5000 Back Panel.......................................................8
Series S1500 & S3000 Back Panel Connections..................9
Series V1500 & V3000 Back Panel Connections.................10
Series S5000 Back Panel Connections...............................11
Series V5000 Back Panel Connections...............................12
V Series Manual Fill Instructions.....................................13
Remote Alarm Wiring.........................................................14
Storage Unit Parameters..................................................14
LCD Display Functions........................................................15
Normal Operating Mode..................................................16
Programming Mode.........................................................18
Liquid Nitrogen Manifold Assembly and Parts list
S1500 & S3000................................................................25
V1500, V3000, S5000 & V5000........................call factory
5000Controller Assembly.................................................26
5000 Controller Internal Wiring.....................call factory
1500 & 3000Controller Assembly.....................................27
1500 & 3000Controller Internal Wiring..........................28
1500 & 3000 Assembly and Parts list................................29
5000 Assembly and Parts list...........................................30
Verification & Calibration
S Series Level Display Verification & Calibration........31
V Series Level Display Verification & Calibration........32
V & S Series High & Low Alarm Setpoint Verification...34
V & S Series Temperature Display Verification.............34
Troubleshooting................................................................35
Cleaning & Maintenance.....................................................40
Accessories.......................................................................41
Table of Contents
www.custombiogenics.com

1
- Liquid Nitrogen Safety -
WARNING
LIQUEFIED GASES ARE EXTREMELY COLD LIQUIDS – LIQUID
NITROGEN EXISTS AT -196˚C. BECAUSE OF THESE COLD
TEMPERATURES, LIQUEFIED GASES WILL “BURN“ IF THEY
COME INTO CONTACT WITH SKIN. NEVER ALLOW DIRECT
SKIN CONTACT WITH LIQUID NITROGEN OR SERIOUS BURNS
WILL RESULT.
ALTHOUGH LIQUID NITROGEN ITSELF IS NON-TOXIC, WHEN
RELEASED INTO A CONFINED SPACE IT CAN DISPLACE OXYGEN
CAUSING ASPHYXIATION. ENTERING AN OXYGEN DEFICIENT
ROOM CAN CAUSE UNCONSCIOUSNESS WITHOUT WARNING.
ALWAYS CHECK AIR QUALITY UPON ENTERING A ROOM
WHERE CRYOGENIC LIQUIDS ARE BEING USED, AND IF
POSSIBLE, HAVE AIR RESPIRATORS AVAILABLE.
INTRODUCING EQUIPMENT WHICH IS AT ROOM TEMPERATURE
INTO LIQUID NITROGEN IS ALWAYS SOMEWHAT HAZARDOUS.
BEWARE OF SPLASHING AND “BOILING” WHICH MAY
OCCUR. ALL PERSONNEL PERFORMING THESE OPERATIONS
SHOULD BE FULLY INFORMED OF PROPER HANDLING
PROCEDURES, AND SHOULD ALWAYS WEAR A FACE SHIELD
AND PROTECTIVE CLOTHING.
LIQUEFIED GASES SHOULD NEVER BE USED IN COMBINATION
WITH OTHER SUBSTANCES WITHOUT KNOWING WHAT THE
RESULT WILL BE. WHEN IN DOUBT, CONTACT A COMPETENT
AUTHORITY.
IMPORTANT: The following section on LIQUID NITROGEN SAFETY should be read carefully
and followed completely, but is by no means a complete volume on the safe use of cryo-
genic liquids. All personnel should have a complete knowledge of the correct procedures,
as well as the hazards of working with liquid nitrogen. Failure to do so could result in
serious injury or death.
☞

2
- Liquid Nitrogen Safety -
HANDLING LIQUID NITROGEN
Personnel handling liquefied gases should be thoroughly
instructed as to the nature of these materials. Proper training
is essential to safety, and will ensure the accident-free use of
this equipment.
Because of their low temperatures, liquefied gases will burn
the skin much in the same way as hot liquids can. For this reason,
always wear the proper protective clothing when handling
these materials. It is advised that during use, handlers of liquid
nitrogen should protect themselves by wearing goggles or face
shields, cryogenic gloves large enough to allow quick removal
and a cryogenic apron. It is preferable that shoes worn at these
times have high tops, as to not permit accidentally spilled liquid
from entering, as well as pant legs which come down over the
tops of shoes for further protection.
Also because of the extremely low temperatures, liquid nitrogen
should only be handled and transported in approved containers.
Many materials become brittle and may shatter when put into
contact with liquid nitrogen and other cryogenic liquids.
FIRST AID
In the event a person is burned by liquefied gas, the following
first aid treatment should be given while awaiting the arrival of
medics or a doctor:
1) If the material has contacted skin or eyes, flood those areas
with large quantities of unheated water and protect frozen
areas with loose, bulky, dry and sterile dressings.
2) If the skin is blistered or there is a chance that the eyes have
been affected, seek medical help immediately.
www.custombiogenics.com

3
- V Series and S Series Descriptions -
Throughout this manual references are made to
the"S Series" and "V Series" storage unit vessels. In
order to give a complete understanding of the
difference between these two models, the diagrams
at right are being provided. They show clearly the
difference between the two, and the characteristics
of each. Although the two are quite different physically,
they operate in essentially the same way, and the
electronic controls are identical for them both.
Whenever there is a different procedure or operation
for one, we've clearly stated the different instructions
for each model. When not stated as different, the
procedure or operation is the same for both.
What makes these two designs so different is this
basic fact:
With the S Series models, the liquid nitrogen is
contained within the storage vessel, and the stored
samples are, or are potentially, in contact with the
liquid.
With the V Series or Isothermal models, the liquid
nitrogen is contained inside the vessel walls, and the
stored samples never come into contact with the liquid
nitrogen except in the case of an accidental overfill.
To understand the way the system operates, see
the OPERATION section on the next page for a basic
explanation of the mechanics of the system. Also, be
sure to read this manual completely before attempting
to use this equipment. If you are still not sure how to
use this equipment properly, contact a competent
authority, rather than risking your safety or the safety
of the stored samples.
When the unit is placed into service, check daily to
ensure proper operation and safety of the stored
samples. For the V Series units it is essential to lift the
lid each day and check for vapor and signs of proper
freezing.
S Series Vessel
V Series (Isothermal) Vessel
Liquid nitrogen is contained within
the vessel, and is in direct contact
with the inventory system
Liquid nitrogen is contained inside
the vessel Walls, and does not contact
the inventory system

4
www.custombiogenics.com
- Initial Set-up -
The S Series Storage Units are designed to maintain liquid nitrogen levels within specified
parameters inside a cryogenic storage vessel. The V Series Storage Units are designed to
maintain liquid nitrogen levels within specified parameters inside the walls of a cryogenic
storage vessel.This is achieved by measuring gravitational weight of the liquid nitrogen with
a pressure sensing unit in the controller. The controller activates the FILL solenoid valve when
the liquid level goes below the LOW level setpoint, and deactivates the solenoid valve, stopping
the fill, when the level reaches the HIGH setpoint.
Units equipped with the Bypass Option have an additional solenoid valve to vent vapor or gas
from the transfer lines before the FILL solenoid is activated. In the description below, the part
of the sequence which is unique to the Bypass Option is in [brackets]. All other information
refers to units with or without the Bypass Option.
During regular operation, the sequence of events is as follows: When liquid level in the vessel
falls below the low level setpoint, a signal is sent to the controller. At this time the FILL solenoid
valve is activated, allowing the flow of liquid into the vessel. [The Bypass Option will activate
the VENT solenoid first to release gas or vapor from the transfer lines. The venting will continue
until the line temperature reaches approximately -130˚ to -140˚ C. This can be adjusted, consult
the factory for more information. When the line reaches this temperature the vessel will begin
to fill.] When the liquid level reaches the high level setpoint a signal is sent to the controller
which deactivates the solenoid valve and stops the flow of liquid into the vessel. As long as the
unit is powered up, this fill sequence repeats as necessary, maintaining the desired liquid level.
Check unit daily to ensure proper operation and safety of the stored samples. For the V Series
units it is essential to lift the lid each day and check for vapor and signs of proper freezing.
- Operation -
As a first step in the set-up procedure, be sure to read this manual completely to become
more familiar with this equipment. Next, remove all packing materials and wipe unit with a
clean cloth inside and out to remove any debris left from shipping. Once the unit is wiped
down, complete the following steps:
1) Connect LN2supply to the storage unit, but do not not open the manual supply valve until
instructed to do so.
2) Connect Remote Alarm or Auto Dialer if desired.
3) Plug unit into an appropriate power source.
4) Turn the power Keyswitch to the "ON" position.
5) Adjust the Liquid Level Setpoints. See display #16 on page 20 for instructions.
6) Open the manual valve on the supply tank. Check for leaks at the connection points, then
proceed to normal operation.
7) Check unit daily to ensure proper operation and safety of the stored samples. For the V Series
units it is essential to lift the lid each day and check for vapor and signs of proper freezing.

5
- Optional CryoMonitor Software -
2300 CRYO MONITOR
Tank ID: 1Apr 15, 2001 09:49 AM Exit
Database
Custom Biogenic Systems 800 523-0072 Fax 810 566-7205
2300 CRYO MONITOR
Tank ID: 1Apr 15, 2000 04:10 AM Exit
Database Setup
VIEW
Alarms
Custom Biogenic Systems 800 523-0072 Fax 810 566-7205
AlarmType
Temperature
DATE
REPORT
Today
This Month
Specify
From
All
04/15/2001
1 04/15/2001 08:00:18 AM -191.1˚ C
1 04/15/2001 11:00:15 AM -189.9˚ C
1 04/15/2001 12:00:11 PM -190.3˚ C
1 04/15/2001 01:00:09 PM -191.2˚ C
1 04/15/2001 02:00:07 PM -189.7˚ C
1 04/15/2001 04:00:10 PM -190.5˚ C
04/15/2001
Apply
To
Print
Preview Printer Setup
AA
TEMPERATURE
Tank ID Time Temperature
Setup
COMM Port
COM 1
ID 1
18
3
ReportTitle
Alarms
TANK DATABASE DISPLAY
Temperature
FAHRENHEIT
CELCIUS
LEVEL
ALARMS
INCHES
CENTIMETERS
TEMPERATURE
FAHRENHEIT
HIGH LEVEL
LOW LEVEL
LID TEMPERATURE
-180
CELCIUS
Set Clock Transfer Settings
1
3
2
5
4
8
10
12
9
11
6
7
13
CryoMonitor software is available to connect your storage unit directly to a PC for full access to
the setup and monitoring of the system electronics. Pictured below are the SETUP and DATABASE
menus of the software. Contact Custom Biogenic Systems or your sales representative for
more information about the Cryomonitor Software.
Setup Menu
Database Menu
Setup Menu Controls
1) COMM Port -
Connects the Cryomonitor
Software to the desired port on your PC.
2) Report Title -
Displays which data will be
printed in the report.
3) Tank ID -
Select which storage
tank info will be displayed.
4) Level -
Measurement selection.
5) Temp. -
Select Fahrenheit or
Celsius for the system electronics.
6) Alarms -
Select LOW, HIGH and
TEMPERATURE Alarm setpoints.
7) Database Display -
Select Fahrenheit
or Celsius for the database display.
Database Menu Controls
8) View -
Alarms or Temperature history.
9) Alarm Type -
View specific alarm types
or all alarms in database report.
10) Date -
Choose dates when viewing
database history.
11) From/To -
Further specify dates
when viewing database history.
12) Report -
Preview/Print reports.
13) Visual Database -
View history as
specified in the software setup.

6
Program
Lock
POWER
OFF ON
19
2 8
3 4 5 6 7
1a
1) Key-Switch Power Control -
Main power control switch for the unit.
1a) Power-On Indicator Light -
Lights-up when power is turned on.
2) LCD Display Window -
Text interface for the storage unit electronic settings. See page 15 for
complete listing of all display menus and functions.
3) First Menu Select Button -
This is used to select various control menus and to make
changes in programming as shown by the text which appears above the button.
4) Second Menu Select Button -
This is used to select various control menus and to make
changes in programming as shown by the text which appears above the button.
5) Third Menu Select Button -
This is used to select various control menus and to make
changes in programming as shown by the text which appears above the button.
6) Fourth Menu Select Button -
This is used to select various control menus and to make
changes in programming as shown by the text which appears above the button.
7) Scroll "Down" Button -
Scrolls to lower numbers when programming electronics.
8) Scroll "Up" Button -
Scrolls to higher numbers when programming electronics.
9) "Program/Lock" Key-Switch -
Switches the controller between the Standard Operating
Mode and the Program Mode. Also protects electronic programming from being changed
by unauthorized personnel.
- Front Panel Controls -
www.custombiogenics.com

7
- Series 1500 & 3000 Back Panel -
*1) Vent Probe Connector -
The vent thermocouple plugs in here.
2) Printer Port -
Connect a laser printer here for direct printout of activity log.
*3) Vent Solenoid Valve Connector -
The vent solenoid valve plugs in here.
4) Computer Port -
A computer terminal may be connected here for remote programming
and monitoring.
5) Sensor Hose Connector -
This port connects the sensor hose from the vessel.
6) Lid Switch Connector -
The lid monitor switch plugs in here and gives a text message on the
LCD screen whenever the lid is opened. This information is also stored in memory and will
appear in the activity log.
7) Lid Probe Connector -
The lid temperature thermocouple plugs in here.
8) Fill Solenoid Valve Connector -
The fill solenoid valve plugs in here.
9) Level Alarm Connector -
This port is used to attach an Auto-Dialer or a Remote Alarm
Monitor; This connector will give high and low level alarms, as well as power-loss alarm if
power to the unit is cut off.
10) Fuse -
1 amp Buss fuse; 220 volts slow-blow.
11) Power Cord -
This is the main power supply cord to the unit, be sure to check for proper
voltage - See voltage requirements listed on the controller.
IMPORTANT: Numbers 1 and 3 are installed only on units equipped with the Bypass Option
REMOTE LEVEL
ALARM
VENT
THERMOCOUPLE
PRINTER PORT COMPUTER PORT
LID
SWITCH
LID TEMPERATURE
THERMOCOUPLE
Series 2300
1
AMP
120
V
SERIAL NUMBER
PRESSURE
SENSOR
PORT
CUSTOM BIOGENIC SYSTEMS 1-800-523-0072
VENT SOLENOID
VALVE OUTLET
(24V .63 amps max)
FILL SOLENOID
VALVE OUTLET
(24V .63 amps max)
T
T
T
T
13678910 114
** 25

8
- Series 5000 Back Panel* -
1) Lid Temperature Alarm Connector - This port is used to attach an Auto-Dialer or a Remote
Alarm Monitor.
2) Level Alarm Connector - This port is used to attach an Auto-Dialer or a Remote Alarm
Monitor; This connector will give high and low level alarms, as well as power-loss alarm if
power to the unit is cut off. May also be wired in series with the Lid Temp Alarm
connector to work on the same line.
3) Fuse - 1 amp Buss fuse; 220 volts slow-blow.
4) Power Cord - This is the main power supply cord to the unit, be sure to check for proper
voltage - See voltage requirements listed on the controller.
* Design is changing - Contact factory for the latest information.
1 2 3
4
BottomView of Controller Box
www.custombiogenics.com

9
- Series S1500 & S3000 Connections -
S1500 & S3000
AutofillWith
Bypass Option
S1500 & S3000
Standard Autofill
Lid Temperature
Probe Connector
Lid Monitor
Switch Connector
Lid Temperature
Probe Connector
Lid Monitor
Switch Connector
Fill Solenoid
Connector
Sensor
Hose
Fill Solenoid
Connector
Vent Solenoid
Connector
Vent Probe
Connector Sensor
Hose

V1500 &V3000 Manifold
AutofillWith Bypass Option
Fill Solenoid Wire
Vent Solenoid Wire
Sensor Hose
Vent Probe Wire
Lid Probe Wire
Lid Switch Wire
V1500 &V3000 Manifold
Standard Autofill Fill Solenoid Wire
Sensor Hose
Lid Probe Wire
Lid Switch Wire
10
- Series V1500 & V3000 Connections -
www.custombiogenics.com

11
Sensor
Hose
S5000 Manifold
Standard Autofill
Fill Solenoid Wire
To Control Unit
S5000 Manifold
AutofillWith Bypass Option
Fill Solenoid Wire
Vent Solenoid Wire
Sensor
Hose
To Control Unit
Vent Probe Wire
- Series S5000 Connections -

12
V5000 Manifold
Standard Autofill
Fill Solenoid Wire
Sensor
Hose
To Control Unit
V5000 Manifold
AutofillWith Bypass Option
Fill Solenoid Wire
Vent Solenoid Wire
Sensor
Hose
To Control Unit
Vent Probe Wire
www.custombiogenics.com
- Series V5000 Connections -

13
- V Series Manual Fill Instructions -
The unique design of the new Isothermal Storage Unit is such that it is no longer necessary
to fill the storage chamber with liquid nitrogen. Instead, the inner walls of the storage vessel
are filled with liquid nitrogen and the storage chamber holds no liquid at all. Because of this
unique design the manual filling of this equipment is very different from storage units of the
past. Use the following instructions to manually fill the Isothermal Storage Unit in the event
of a power outage or if the autofill is not working properly.
For correct manual filling of the Isothermal unit perform the following steps:
1) Turn off the liquid nitrogen supply valve at the supply tank.
2) Disconnect the supply line from the Isothermal Unit at the port on the side of the unit.
3) Remove the cap from the manual fill port, on the left side of the unit.
4) Place the cap on the autofill port where the supply line was connected, and tighten down.
5) Connect the liquid nitrogen supply line to the manual fill port, and tighten down.
Without power there will be no digital display to give the liquid level, and the liquid can-
not be seen visually since it is contained inside the walls of the Isothermal Unit. With this in
mind, there are two ways to gauge the liquid level when manually filling the Unit.
The first method is to watch the coloration of the inside of the storage vessel as the liquid
is filling the walls. There will be a slight variation in the color of the tank walls at the liquid
level as it moves up inside the walls. The walls of the vessel will look somewhat "wet" below
the liquid level line. It may be necessary to look carefully to perceive this change in the look
of the tank walls, but it will be there. Remember, however, not to place your head down into
the vessel when watching for this change, as this may be hazardous to your health.
The second way to gauge the fill level is the last resort, because it is only noticeable when
the vessel is nearly full. When the tank is nearing maximum fill, liquid nitrogen will begin to
"spatter" through the vents located near the top edge of the inner walls of the vessel. When
this is seen, the supply valve should be shut off immediately before the liquid nitrogen
begins pouring into the vessel, creating potentially adverse conditions.
Check unit daily to ensure proper operation and safety of the stored samples. For the V Series
units it is essential to lift the lid each day and check for vapor and signs of proper freezing.
IMPORTANT: NEVER attempt to manually fill the Isothermal Storage Unit by opening the lid
and placing a fill line over the edge into the vessel. This is an incorrect fill method and may
cause damage to the stored samples.
CAUTION: Before opening the supply valve to fill the Isothermal Unit, read the following
text to learn how to gauge the liquid level, so the Storage Unit does not overfill and create
hazardous conditions.

14
www.custombiogenics.com
- Remote Alarm Wiring -
Locate the Remote Alarm Connector on the controller (#9 on page 7; #2 on page 8). This is
where the remote alarm or auto dialer will plug into the control unit.
First, wires from the remote alarm or auto dialer must be connected to the plug-end which
plugs in to the Remote Alarm Connector. Use the diagram to connect wires from the remote unit.
When unit goes into an alarm condition or loses power, the contacts will close, thereby
sending a signal to the remote alarm or auto dialer.
Normally
Closed
Normally
Open
Common
Remote Alarm
connector jack
on unit back panel
Push into place
(only goes one way) Remote Alarm connector
(be sure to push in
side pin after wiring)
Remote Alarm
Connector
Remote Alarm
Connection
Procedure
Diagram shows connections
for wiring arrangement with
controller on and no alarm
present.
Cooling medium: Liquid nitrogen only (supplied by a pressurized cryogenic transport vessel)
Operating Pressure: 22 p.s.i.
Power Supply Voltage: 120 Volts AC 60 Hz standard - 220 Volts AC 60/50 Hz optional
Amperage: 1 amp max
Fuse: 1 amp Slow Blow - 220 Volts AC (automotive glass tube type fuse)
Operating levels for LN2: 0 to 28 inches (higher fill heights may be used, call factory for further info)
Specifications:
IMPORTANT: Operating pressure 22 p.s.i. max/18 p.s.i. min. If the pressure is greater or less,
the efficiency of your liquid nitrogen storage unit will be adversely affected.
Liquid Nitrogen Capacity (liters):
Static Evaporation Rate (liters/day):
Static Holding Time (days):
External Dimensions (inches/cm):
Width:
Depth:
Height:
Usable Interior Height (inches/cm):
Usable Interior Diameter (inches/cm):
Weight Empty (lbs/kg):
Weight Full (lbs/kg):
S1500
145
4
41
22/558
31/787
41/1041
29/736
20/508
156/70
414/188
V1500
30
5
6
26/660
37/939
45/1143
29/736
21/534
327/148
383/174
S3000
345
7
49
34/863
43/1092
42/1066
29/736
31/787
350/159
965/438
V3000
70
9
8
37/939
48/1219
47.5/1205
29/736
31/787
600/272
720/327
S5000
615
9
61
43/1092
50/1270
48/1219
29/736
40/1016
700/318
1794/815
V5000
93
11
8
47/1194
54/1371
52/1320
29/736
40/1016
936/425
1100/500
S5000EH
714
9
79
43/1092
50/1270
54/1371
34/864
40/1016
755
1984
V5000EH
140
11
12
47/1194
54/1371
58/1473
34/864
40/1016
997/453
1247/566
- Storage Unit Parameters -

15
This section shows each display window and gives important information necessary for
understanding and operating the LCD text functions of the 2300 Controller.
To start, the index below shows where in this section to find each and every function of the
controller. This will enable the user to correctly program all functions of the storage unit to
meet their individual needs.
The overall operation consists of two basic modes: the Standard Operating Mode, and the
Program Mode. The unit is in the Standard Operating Mode when the Program/Lock Keyswitch
on the front panel (page 6, number 9) is turned to LOCK. To enter the Program Mode the key
must be inserted and the switch turned to PROGRAM.
In the Standard Operating Mode there are 6 different displays possible. They are as follows:
Standard Display - Display number 1 - page 16
Standard Display while unit is filling - Display number 2 - page 16
Standard Display with lid open - Display number 3 - page 17
Alarm Condition Display - Display number 90 - page 17
Alarm Condition Display with audible alarm muted - Display number 91 - page 17
Printing Report - Display number 99 - page 17
The Alarm Condition Display will give the specific cause of each alarm condition that
may be occurring. The following is a list of the possible alarm conditions:
Low Alarm Fill Valve
High Alarm Bypass Valve
Source Alarm Open Lid Probe
Temperature Alarm Open Vent Probe
In the Program Mode there are various displays possible. The following is a list of programming
functions and the corresponding display windows. For each of these programming functions
there may be sub-menus that follow the primary display window. The sub-menus are not listed
here but are shown and explained following the primary windows. The primary programming
functions are as follows:
Main Menu - Display number 4 - page 18
Provides access to:
Date/Time Settings - Display number 8 - page 19
Tank ID Settings - Display number 13 - page 19
Liquid Level Settings - Display number 15 - page 20
Main Menu 2 - Display number 5 - page 18
Provides access to:
Lid Temp Settings - Display number 19 - page 20
Report Functions - Display number 22 - page 21
Bypass Settings - Display number 24 - page 21
Main Menu 3 - Display number 6 - page 18
Provides access to:
Control Validation - Display number 40 - page 21
Fill Timer Settings - Display number 7A - page 18
Return to Main Menu - Display number 4 - page 18
- LCD Display Functions -

16
LIQUID LEVEL XX.XCM LID TEMP.-XXX C
LOW SET XX.XCM HIGH SET XX.XCM
SYSTEM STATUS NORMAL
FILL/START FILL/STOP REPORT
This is the standard display
which will appear during normal
operation under most circum-
stances.
Press this button to
begin a manual fill Press this button to
advance to display
#99 and print report
(see page 17)
#1
o
- LCD Display Functions -
Using the diagrams to understand the display functions
Sample Display Window
X's are used in place of numbers in the display window diagrams, since the actual numbers will vary
Standard Operating Mode Display Windows
LIQUID LEVEL XX.XCM LID TEMP.-XXX C
LOW SET XX.XCM HIGH SET XX.XCM
SYSTEM STATUS NORMAL
FILL/START FILL/STOP REPORT
#1
o
This is the standard display
which will appear during normal
operation under most circum-
stances.
Press this button to
begin a manual fill Press this button to
advance to display
#99 and print report
(see page 17)
LIQUID LEVEL XX.XCM LID TEMP.-XXX C
LOW SET XX.XCM HIGH SET XX.XCM
SYSTEM STATUS NORMAL FILLING
FILL/START FILL/STOP REPORT
#2
o
** **
This display will appear during
normal operation when either a
manual or automatic fill is
occurring.
Press this button
to stop filling Press this button to
advance to display
#99 and print report
(see page 17)
Below is a sample display window as they're shown in the following section. Use the diagram
to become familiar with the way this section is organized, and how the information is presented
in reference to each display window and it's functions.
The text to the right of the
display explains the specifics
of the display message and
why it is occurring
The text below the buttons
explains the function of each
of the buttons. also tells
which display the button will
advance to, and the page
number where it can be found
in the instruction manual.
This number to the left
of each window is a
general identification
number used only to
organize the displays
for this manual. This
number will not appear
anywhere on the
controller or the actual
display windows
www.custombiogenics.com

17
- LCD Display Functions -
LIQUID LEVEL XX.XCM LID TEMP.-XXX C
LOW SET XX.XCM HIGH SET XX.XCM
SYSTEM STATUS NORMAL LID OPEN
FILL/START FILL/STOP REPORT
#3
o
** **
This display will appear during
normal operation when the lid is
opened.
Press this button to
begin a manual fill Press this button
to stop filling Press this button to
advance to display
#99 and print report
(see page 17)
LIQUID LEVEL XX.XCM LID TEMP.-XXX C
SYSTEM STATUS STUCK VENT VALVE
FILL/START FILL/STOP MUTE REPORT
#90
o
** **
This display will appear when
an alarm condition is occurring.
The specific nature of the alarm
will be shown in line 3 of the
display text. The **ALARM** will
flash on and off in one second
intervals.
("Stuck Vent Valve" is shown only as an
example of the alarm display window. See
page 15 for a complete list of alarms.)
Press this button to
reset alarm. If it re-
occurs, repeat until all
alarms are corrected
Press this button to
mute audible alarm
and advance to
display #91
(next)
Press this button to
advance to display
#99 and print report
(see page 17)
Standard Operating Mode Display Windows
LIQUID LEVEL XX.XCM LID TEMP.-XXX C
SYSTEM STATUS STUCK VENT VALVE
FILL/START FILL/STOP SOUND
#91
o
** **
This display will appear when
an alarm condition is occurring
AND the audible alarm is muted.
("Stuck Vent Valve" is shown only as an
example of the alarm display window. See
page 15 for a complete list of alarms.)
Press this button to
begin a manual fill Press this button
to stop filling Press this button to
enable audible alarm
and return to
display #90
(above)
LIQUID LEVEL XX.XCM LID TEMP.-XXX C
LOW SET XX.XCM HIGH SET XX.XCM
SYSTEM STATUS NORMAL
FILL/START FILL/STOP PRINTING REPORT
#99
o
This display will appear during
normal operation when "REPORT"
is selected from displays 1, 2, 3
or 90. After the report is printed
the display will go back to what-
ever screen was showing when
the report was requested.
This manual suits for next models
5
Table of contents
Popular Storage manuals by other brands
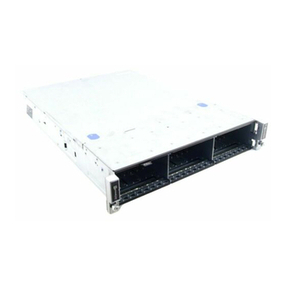
Intel
Intel JBOD 2000 Family Hardware guide
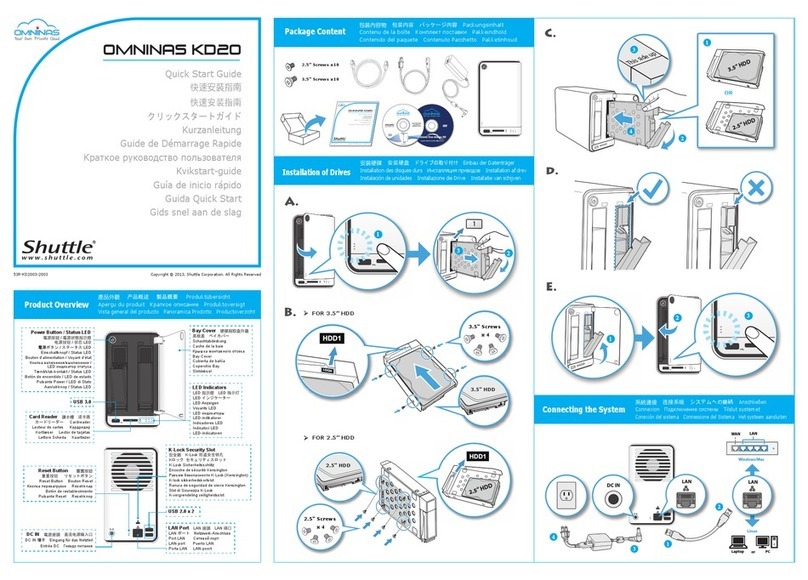
Shuttle
Shuttle OMNINAS KD20 quick start guide
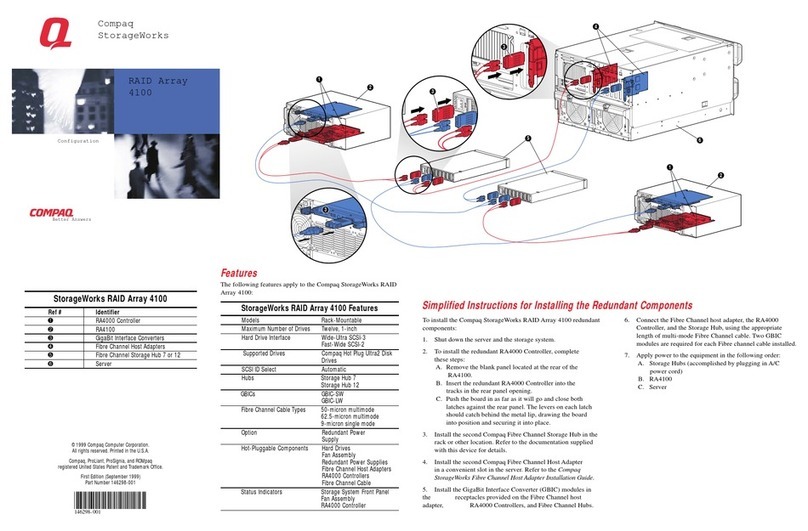
Compaq
Compaq StorageWorks 4100 - RAID Array Configuration guide
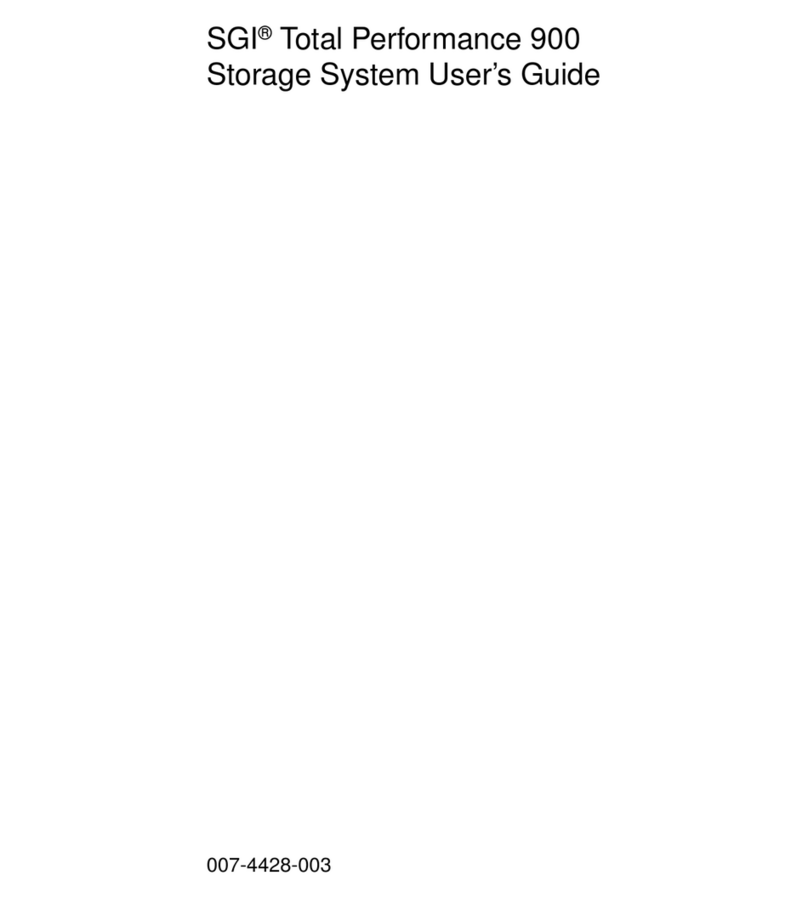
Silicon Graphics
Silicon Graphics TP900 user guide

Avid Technology
Avid Technology ISIS 5000 Setup guide
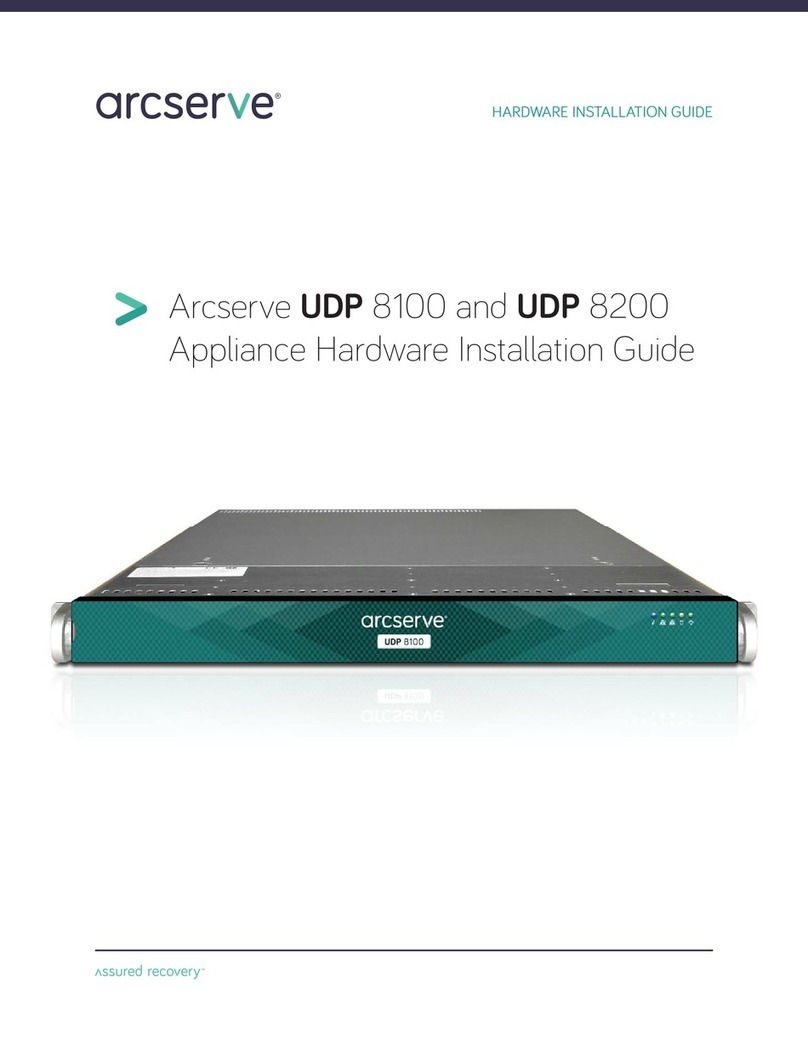
Arcserve
Arcserve UDP 8100 Hardware installation guide