Cetetherm PRESSOSMART MP195NL User manual

USERS’ MANUAL
PRESSOSMART WITH OPEN & CLOSED EXPANSION VESSELS
Doc : MANUAL Pressosmart 2020 01 EN

Table of contents
Unit description...........................................................................................................Page 3
Schematics diagrams .................................................................................................Page 6
Hydraulic connections ................................................................................................Page 8
Wiring diagram –Terminal block location...................................................................Page 9
Electrical consumptions............................................................................................Page 10
Commissioning instructions –Setting example ........................................................Page 12
Maintenance.............................................................................................................Page 13
Options.....................................................................................................................Page 14
Trouble shooting guide.............................................................................................Page 17
Fuses........................................................................................................................Page 19
Controller components .............................................................................................Page 19
Display / Keypad.......................................................................................................Page 20
Hour and date setting...............................................................................................Page 21
Setpoints...................................................................................................................Page 22
Technician Menu......................................................................................................Page 23
Network leakage detection .......................................................................................Page 24
Pressure Recorder ...................................................................................................Page 25
History ......................................................................................................................Page 26
Self-Test...................................................................................................................Page 26
Restoring Factory Settings .......................................................................................Page 27
Keypad Quick functions –Reset Alarms ..................................................................Page 27
Displayed Messages ................................................................................................Page 28
Extra control box for closed vessel systems.............................................................Page 29
•Zero adjust …………………………………………………………………..Page 29
•Error messages …………………………………………………………......Page 30
Mounting instructions................................................................................................Page 31
Exploded views and spare parts...............................................................................Page 34
General drawings .....................................................................................................Page 38
Declaration of conformity..........................................................................................Page 42
Warranty...................................................................................................................Page 43

3
DESCRIPTION OF THE UNIT
The pressurization units are designed for indoor installation in plant rooms where the ambient temperature
should always be above 0°C.
The drawings below show the location of the different components and the position of the inlet and outlet
connections.
MP195NL (1 pump) with open tank
MP4N (1 pump) With open tank
Parts list on next page
MP5N (2 horizontal pumps) with open tank
1 Tank
9 Setting tee
2 Filling
electrovalve
10 Drain
3 Control box
11 Overflow
4 Pump
12 Installation
collector
5 Pressure
sensor
13 Pressure
vessel
6 Lack of water
sensor
14 Overflow
valve
7 Low level
sensor
15 Cover
8 Check valve

4
MP7N (2 vertical pumps, 2 pressure relief valves) With open tank
The « lack of water » level sensor is placed bellow the filling level sensor
The overflow connection is located bellow the filling electro valve at a distance higher than
50mm
So open tanks include a natural disconnection.
PART LIST MP4N/MP5N/MP7
1Cold water valve
2Feeling electrovalve
3Control box
4Installation valve 1’’
5Pressure sensor
6Lack of water sensor
7Feeling sensor
8Check valve
9 Setting Tee
10 Pump(s)
11 Drain cock 1’’
12 Overflow
13 Pressure Relief Valve(s)
14 Water tank storage
15 pump inlet
16 Outlet collector
17 PRV outlet
18 Anti-hammer vessel (option)

5
MP4N (1 horizontal pump) / MP5N, MP7N (2 horizontal pumps) with Closed tank
The unit you have received includes the following components:
•1 or 2 pumps mounted on a frame, with check valve and gate valve
•1 or 2 overflow valve(s) with filter(s) on MP4N/MP5N/MP7
•1 control box
•1 pressure sensor
•1 filling line with electro valve and setting valve
•2 level sensors to screw in the tank (open tank only)
•1 water storage tank delivered separately (except MP195NL including the open tank and anti-hammer
vessel)
•CLOSED TANK ONLY: 1 membrane closed water storage tank with adjustable feet, weight sensor,
specific control card into the control box.
Please read carefully mounting instructions delivered with closed expansion vessel.
They explain how to install feet, top air vent and bottom collector connected to the
pump unit.
As per chosen options, the following components should be delivered:
•1 pressure vessel, ready for fitting (except MP195NL including this)
•1 cartridge filter 89 µm
•1 impulsion volumetric counter (10 liters/pulse) for the network leakage detection
•1 manual tank filling by pass line
PARTS’ LIST MP4N/MP5N/MP7N
1Cold water valve
8Check valve
15 Tank Inlet/Outlet collector
2Feeling electrovalve
9 Setting Tee
16 Network collector (left or right)
3Control box
10 Pump(s)
17 PRV outlet
4Top air vent
11 Weight control box
18 Anti-hammer vessel (option)
5Pressure sensor
12 Safety valve (Tank overflow)
19 Tank drain valve
6Weight Sensor + adjustable foot
13 Pressure Relief Valve(s)
20 Atmoshpere pipe
7Adjustable foot
14 Closed Water tank storage
2
3
5
6
7
8
9
10
12
13
14
15
16
17
18
4
19
1
20
11

6
Pressure
Ph High alarm Hst+14
Open
Pressure relief
Valve(s)
Closed Hst+9
Neutral Zone
P1 Stop Hst+7
E
P2 Stop
d
d
P1 ON
E
P2 ON Hst+1
Hst
Pb Low P alarm Hst-2
SCHEMATIC DIAGRAM MP195NL/MP4N OPEN TANK
Arrêt P1
SCHEMATIC DIAGRAM MP5N/MP7N OPEN TANK
On these units, there may be 1 or 2 pressure control valves.
When the network is heating, the pressure increases. The overflow valve(s) open then and the network water
goes into the tank. When the temperature and pressure decrease, the pump(s) start in order to reach the
required pressure. Level sensors into the tank allow the automatic tank filling and pump(s) stop if the water
level is too low inside the tank. The controller manages the pressure set point and eventual defaults.
Pressure
Ph High P alarm Hst+14
Open
Pressure Relief
Valve
Closed Hst+9
Neutral zone
P1 Stop Hst+7
Start Pump
d
P0 Hst+2
Hst
Pb Low P alarm Hst-2

7
Pressure
Ph High alarm Hst+14
Open
Pressure relief
Valve(s)
Closed Hst+9
Neutral Zone
P1 Stop Hst+7
E
P2 Stop
d
d
P1 ON
E
P2 ON Hst+1
Hst
Pb Low P alarm Hst-2
SCHEMATIC DIAGRAM MP4N CLOSED TANK
Arrêt P1
SCHEMATIC DIAGRAM MP5N/MP7 CLOSED TANK
On these units, there may be 1 or 2 pressure control valves.
Same principle than open tank system except that the water level is calculated from the water weight inside
the tank. For this, a weight sensor is connected to an electronic card inside the control box. This card power
supplies the weight sensor and acquires its signal, translated into inner water level, replacing the standard
water level sensors.
Pressure
Ph High P alarm Hst+14
Open
Pressure Relief
Valve
Closed Hst+9
Neutral zone
P1 Stop Hst+7
Start Pump
d
P0 Hst+2
Hst
Pb Low P alarm Hst-2

8
HYDRAULIC CONNECTIONS
Specific to closed membrane vessel:
▪place the vessel in the heating room and install setting feet + sensor foot at the
opposite of pump unit at first. Check that it is stable and vertically + horizontally aligned.
If not, adjust the setting feet.
▪Then, install the air vent and the bottom collector on the expansion tank in line with
the pump unit.
•The tank storage must be at the same level or a higher level than the pump module. Connect the tank
to the pump module as per figures 15 and 17 on the previous drawings (MP4N/MP5N/MP7). On the
MP195NL, these connections are factory made.
If you are using 2 or more expansion vessels, they must be of the same size and
on the same ground level as shown bellow :
Open tanks :
Connect drain connection together.
Use a T plus gate valve for drain.
Tank2 not to be equipped with level
sensor and filling line.
Closed tanks :
Drain valve is OK for both tanks.
Use a T under tank1 and connect
second tank to it
Tank2 not to be equipped with
weight sensor nor control box.
FOR OPEN / CLOSED :
TANK 1 = TANK 2
•It is necessary that the expansion piping which connects the network to the module has an equal or
larger diameter than the pressurization unit’s.
•Connect the collector to the network (Rep.12 for MP195NL and Rep.16 on MP4/5/7) and deposit the
valve wheel. Respect an ascending slope towards the network and use a pipe diameter so that the
expansion flow has a speed lower than 0.1m/s.
•The optional expansion vessel must be connected to the fouling collector (Rep.16 on MP4N/5N/7).
Don’t forget the drain valve included in this option.
•Connect the cold-water input to the automatic tank filling line (Rep.2 on MP195NL Rep.1 on
MP4N/5N/7). This line can be horizontally or vertically placed.
•If you have a cartridge filter delivered as an option, it is important that you connect it before the
automatic filling line.
•Connect the overflow (Rep.11 on MP195NL Rep.12 on MP4N/5N/7) to the sewer.
SPECIFIC TO OPEN TANKS:
•Install the level sensors Rep.6,7 inside the tank (except on MP195N). Push these sensors on a
length of 12 centimeters.
Nota: The upper sensor is factory marked

9
ELECTRIC CONNECTIONS
•Connect the unit to the main power
•Connect the “alarms”
The French DTU 65-11 requires the stopping of the installation in case of:
•Lack of water
•Low pressure
•High pressure
Please also refer to your local rules.
All the default information is signaled on the display and is relayed by an inversor volt free contact
(see next page)
Main supply: 230V (+10/-10 %) –1 Phase –50 Hz + Earth
WIRING DIAGRAMS
ELECTRONIC VERSION –ALL MODELS
The diagram below shows the electric wiring of external components of a 2 pumps
pressurization unit. In case of 1 pump, just suppress the connections to relay R2.
Relays are used as follows:
- P1 and P2 for the 2 pumps (as per equipment)
- R1 for the general default relay
- P4 for the electrovalve

10
ELECTRICAL CONSUMPTIONS
Model
Pump type
P elec.
(kW)
I
(A)
Model
Pump type
P elec.
(kW)
I
(A)
MP195 L1/S1
CM3-5
0.5
3.8
MP5N 6xx
2xCM3-6
1.35
8.8
MP195 L2/S2
CM3-6
0.67
4.4
MP5N 7xx
2xCM3-7
1.8
10.8
MP4N 3xx
CM3-3
0.5
3.8
MP5N 8xx
2xCM3-8
1.8
10.8
MP4N 4xx
CM3-4
0.5
3.8
MP7-10
2xCR3-10
1.5
10.5
MP4 N 5xx
CM3-5
0.5
3.8
MP7-13
2xCR3-13
2.2
15.1
MP4N 6xx
CM3-6
0.67
4.4
MP7-15
2xCR3-15
2.2
15.1
MP4N 7xx
CM3-7
0.9
5.4
MP7T-10*
2xCR3-10
1.5
3.8
MP5N 3xx
2xCM3-3
1
7.6
MP7T-11*
2xCR3-11
2.2
5.1
MP5N 4xx
2xCM3-4
1
7.6
MP7T-13*
2xCR3-13
2.2
5.1
MP5N 5xx
2xCM3-5
1
7.6
MP7T-15*
2xCR3-15
2.2
5.1
* 380V 3 Phases + N + Earth power supply (special units, please consult).

11
SPECIFIC WIRING DIAGRAM FOR CLOSED VESSEL SYSTEMS, CI8021 CARD
Detail of the mechanical card mounting
Wires’ colors are indicated on the PCB.
If another type of sensor is used (4 or 6 wires), please
refer to other labels that indicate power supply and
signal terminals.
The wire are to be connected to the terminals + ALIM /
+ SENSE / - SIGNAL / + SIGNAL / - SENSE / –ALIM
For a stable measure, connect the weight sensor’s shield cable on « Châssis » terminal.
To be operational, the CI8021 card MUST be used with software version >= V 2.5.
Carte Puissance
Carte option
Entretoise
Vis
4 wires sensor to connect on terminals :
Châssis (Yellow) / - ALIM (Black) / + SIGNAL (White) / - SIGNAL (Green) / + ALIM (Red)

12
COMMISSIONING
The installation and use instructions should be respected, and the factory settings remain unchanged.
•Open the different valves on the unit,
•Drain the pump(s)
•Closed tank collector : a gate valve plus a cap are located on the upper part, allowing to easily air venting
while commissioning the unit, to remove air from the collector. Once done, close the valve and screw the
cap.
•OPEN EXPANSION VESSELS ONLY: Set the level sensors inside the tank. For that, pull on the electric
cables until it doesn’t move any more. Then, push both cables 12 centimeters inside the tank. Screw the
stuffing boxes of each cable.
•CLOSED EXPANSION VESSELS ONLY: Before water filling starting up the unit, RESET THE VOLUME
VALUE if different of zero. The controler display should indicate the water volume inside the tank, so should
be at zero before water filling by pressing the OK key. The zero volume is done by accessing to the
Technician menu at line “Zero setting”. At this point, press + key, then + and – to confirm.
THE ZERO ADJUSTMENT MUST BE DONE WITH AN EMPTY VESSEL !
If it is not the case, power off the control box and open the drain valve located on the
collector to remove water. Once done, close the drain valve and power on the control
box.
•Check the expansion vessel pressure (about 0.1 bar less than the pressure set point). The setting must be
done without water into the vessel.
•Power on the unit by the main control panel. The first time, the controller indicates “lack of water” and opens
the electrovalve to start filling the vessel. Once the filling volume has been reached, the pump(s) start,
pressurizing the installation.
•As per the unit type, both pumps should start together if required pressure is not reached at the unit start
up. A cyclic permutation will shift the starting pump in order to have the same worked hours for each pump
(MP5/MP7 only).
•Check the starting pump pressures on the display compared to set pressure on the controller.

13
MAINTENANCE
Warning! Before operating on a unit, ensure that electrical supply of
the control box is OFF.
Only authorized people should work on the unit
The Cetetherm pressurization units require little maintenance. For that, you just have to check:
•The filter(s) is(are) clean,
•The overflow valve(s) operate correctly,
•The expansion vessel should be inflated 0.1 bar less than the pressure set point,
•There is no leakage and the unit is clean,
•The different settings and security functions,
•The pump(s) do(es) not require any particular maintenance.
Cut off the electrical supply before working on it
SETTING EXAMPLE
An 8th floor apartment. That means 8+1(Level 0)+1 (underground)=10 levels of about 3 meters each.
The static height is 3*10=3 bar (1 meter=0.1 bar).
The different parameters should be as follows:
Parameter
MP195NL
/MP4N
MP5N/
MP7N
Parameter
MP195NL/
MP4N
MP5N/
MP7N
Setpoint P(bar)
3.2
3.2
.t1 (sec.)
6
6
Hysteresis (bar)
0.5
0.5
.t2 (sec.)
-
1
Threshold gar (bar)
-
0.2
.t3 (sec.)
1
1
High pressure (bar)
4.2
4.2
.t4 (sec.)
6
6
Low pressure (bar)
2.8
2.8
.t5 (sec.)
1
1
With
.t1= Temporisation after lack of water default
.t2= Cascade temporisation .t3= Pump(s) stop temporisation
.t4= Filling temporisation .t5= Low pressure temporisation.
Overflow valve(s) set 0.2 bar more than (Setpoint+Hysteresis)

14
PRESSOSMART OPTIONS
1- Anti-hammer vessel (Ref. VASABMP01/ VASABMP02/ VASABMP03)
MP4N MP5N
MP7
2- Cold water inlet strainer (Ref. OPTMPFILT)
The strainer and its mounting accessories should be placed before the filling electrovalve on the
cold water inlet, as illustrated bellow :
Install a gate valve, eventually a bypass before the strainer.
Except MP4N models, the
vessel can be mounted on
the left or on the right side of
the collector, as per needs.

15
3- Filling water flow meter (Ref. OPTMPDETECT)
The flow meter and its accessories has to be installed before the filling electrovalve, as illustrated
bellow :
The left arrow represents the cold water inlet, filling the storage tank.
Install a gate valve before the flow meter.
Flow meter output is one (1) pulse every ten (10) liters.
Flow meter’ s electric wires must be connected to one of the two available C (common) and I3
terminals of the power board CI572P as per the electric wiring diagram shown below:
4- Room flooding sensor option (Ref. INONDMP)
This level sensor must be connected to one of the two available C (common) and I4 terminals of
the power board CI572P as per the electric wiring diagram shown below:

16
5- 8 relays optional card (Ref. OPT8RELAYMP). OPEN TANK ONLY.
The 8 relays’ card allows to report separately Pump 1, 2 (as per equipment), sensor defaults, low
pressure, high pressure, lack of water, network leakage and flooded room by actioning a specific
contact issued from a relay.
You still have general default relay on the power board.
Each default relay has an inverted contact, which can be normally closed (NC) or normally opened
(NO).
Mounting
If the card has not been factory mounted, please refer to following instructions.
Connect the card to point as shown below.
The extra card is fixed to the power board by 5 M3 screws . In the case you add this card in an
existing control box, please refer to the schematic diagram bellow.
Carte Puissance
Carte option
Entretoise
Vis
Relays’ assignment :
R5 : Low pressure alarm
R6 : High pressure alarm
R7 : Lack of water in the tank
R8 : Pressure sensor default
R9 : Pump 1 trip
R10 : Pump 2 trip*
R11 : Network leakage
R12 : Flooded room
* : As per equipment
Each default relay has an inverted contact,
which can be normally closed (NC) or
normally opened (NO).
Customer wirings directly on this card.

17
TROUBLESHOOTING GUIDE
FINDINGS
PROBABLE CAUSE
SOLUTION
Low pressure alarm
Pump(s) stripped
Change
Overflow valve open too wide
Set
Low pressure alarm set point too
high
Set
Pump(s) do not start
Fuse(s) splashed
Replace and control
Set point too high
Set
Relay scratched
Replace
Pump(s) out of order
Replace
Pump No. inversed in 1pump
mode
Set
High pressure alarm
Overflow valve too screwed
Set
Overflow valve fooled or blocked
Clean or replace. WARNING:
unscrew the spring before
dismounting
High pressure set point too low
Set
Pump(s) always on
Pump(s) bad drained
Drain
Pump(s) fooled
Clean
Not enough output pressure
Check the quotation
Overflow valve open too wide
Set
Pressure set point too high
Set
Too high differential value
Set (Standard value=0.5)
Network leakage
Check
Setting tee closed
Open 1 turn
Lack of water default
Level sensor incorrectly placed
(open tank only)
Modify and set (12cm)
Level sensors out of order (open
tank only)
Replace
Bad calibration of the zero weight
(closed tank only)
Check weight calibration in this
users’ manual
Cold water valve closed
Check or open
Electrovalve or relay out of order
Replace

18
TROUBLESHOOTING GUIDE
Cont..
FINDINGS
PROBABLE CAUSE
SOLUTION
Sensor default
Sensor broken
Replace
Disconnected wire
Refer to the electric diagram
Pump Start/Stop….
Differential too low
Set
Pressure vessel too low
Check and replace if necessary
Setting tee open too wide
Open 1 turn
Insufficient pipe diameter
Check dimensions. Close the
setting tee
Tank overflow
Undersized tank
Check the quotation
Electrovalve is open
See next paragraph
Manual network feeding open
Check and close if necessary
Feeling temporisation too high
Set
Electro valve still open
High level sensor out of order
(open tank only)
Replace
Bad volume settings (closed tank
only).
Check the set volumes into the
technician menu
Fooled by impurities in the valve
Clean and check if there is a 100
µm filter before the electro valve
No display
630mA Fuse out of order
Replace and control
No power from main control panel
Power on the unit on main panel
Electronic card out of order
Replace
Fooled sensor
Clean
Different pressure compared to
real pressure
Sensor default
Check
Bad calibration
Adjust the scale correction
Power off the control box before any maintenance operation

19
FUSES
The ‘’Power Board’’ is fitted with a set of fuses to protect the different components against overload:
- Each of the pumps fitted to the unit (FU 1 + FU 2)
- Filling electro valve (FU4)
- Supply circuits of the controller and pressure sensor (FU 5),
Fuse
FU 1
FU 2
FU4
FU 5
Protects
Pump 1
Pump 2
Electro valve
Transformer
Size
6 x 32
6 x 32
6 x 32
5x20
Rating
10 A
10 A
10 A
630 mA
Voltage
250 V
250 V
250 V
250 V
CONTROL BOX COMPONENTS
POS
DESIGNATION
CODE
1
Power board
CI572P
2
Logic board
CI 616
3
Display / Keypad
LEXAN
POWER BOARD LOGIC BOARD Safety fuses
IP54 PLASTIC BOX
Display / Keypad Bipolar switch

20
DISPLAY / KEYPAD
KEY
FUNCTION
1
White Left arrow to scroll in the Clock menu
2
White Right arrow to enter then scroll into the Clock menu
3
Yellow Left arrow to scroll in the Pressure and Technician menus
4
Yellow Right arrow to enter then scroll in the Pressure menu
5
- key for decreasing the parameter values shown in the menus
6
+ key for increasing the parameter values shown in the menus or confirm validation
7
Validation / Enter key
8
Hidden Reset key to restore parameters to factory settings
IN NORMAL MODE
The display shows the following information:
Hour Date
Pressure
When plugging the unit on electricity, display indicates for 3 seconds the software version. Ex: V. 2.5
This manual suits for next models
4
Table of contents
Popular Control Unit manuals by other brands
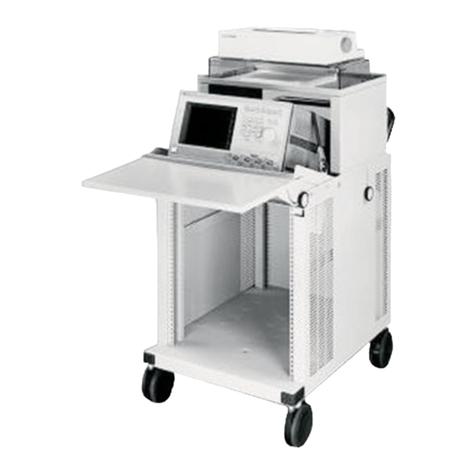
Keysight
Keysight 35181K installation guide

Equinox Systems
Equinox Systems SuperSerial PM16-RJ/422 Hardware manual addendum
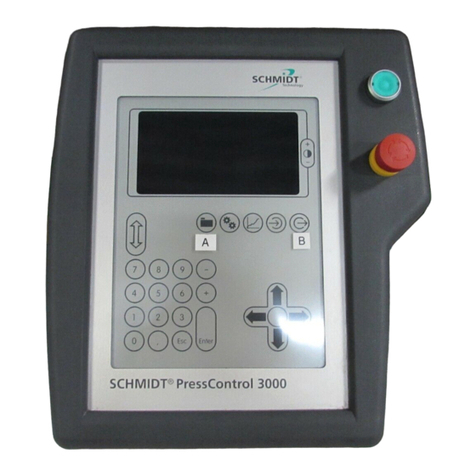
Schmidt
Schmidt PressControl 3000 Operator's manual

Woodward
Woodward SPM-D10/YB manual
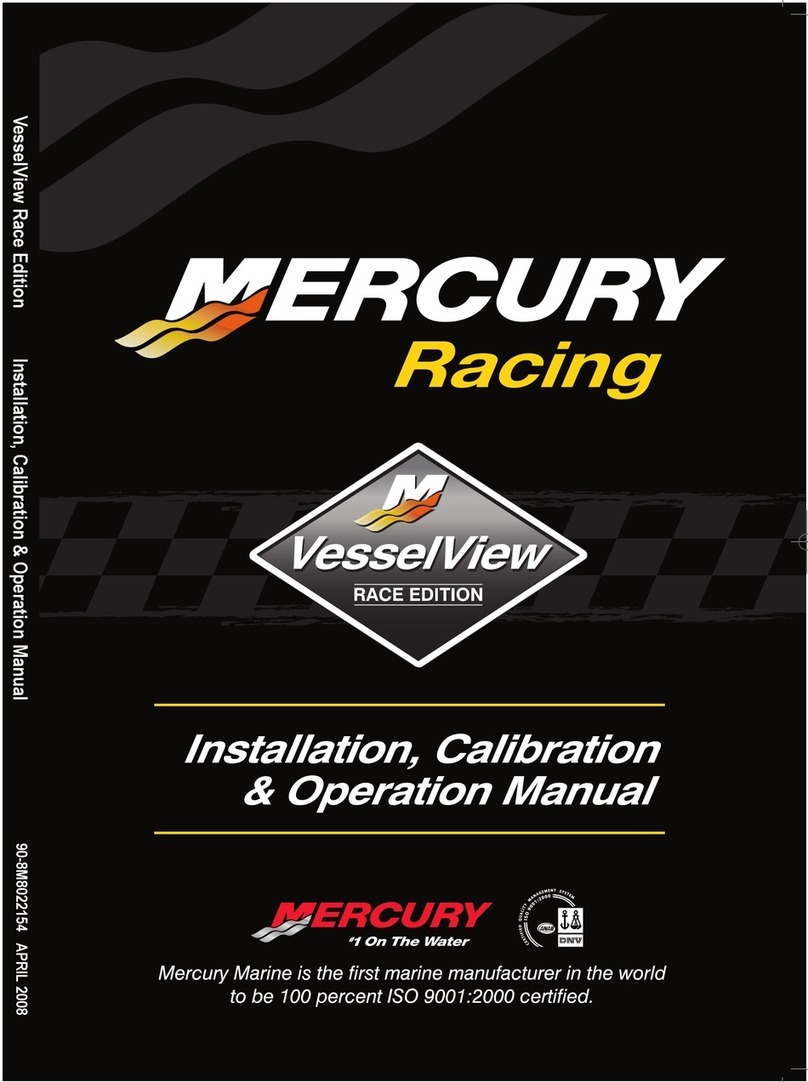
Mercury Racing
Mercury Racing VesselView Installation, Calibration & Operation Manual
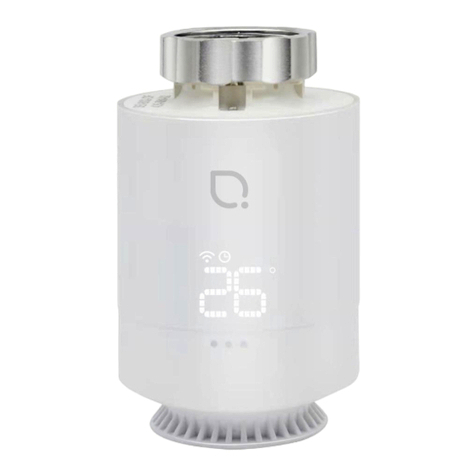
COQON
COQON HTHERMB1 manual
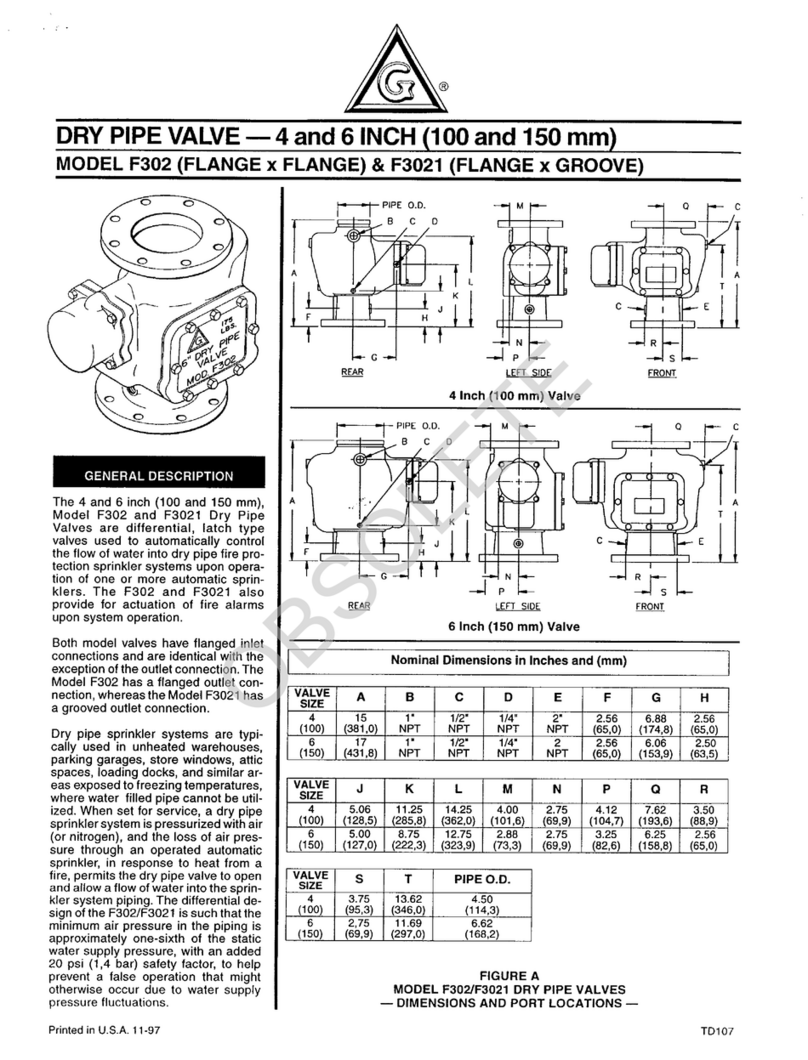
Tyco Fire Product
Tyco Fire Product Gem F302 instruction manual
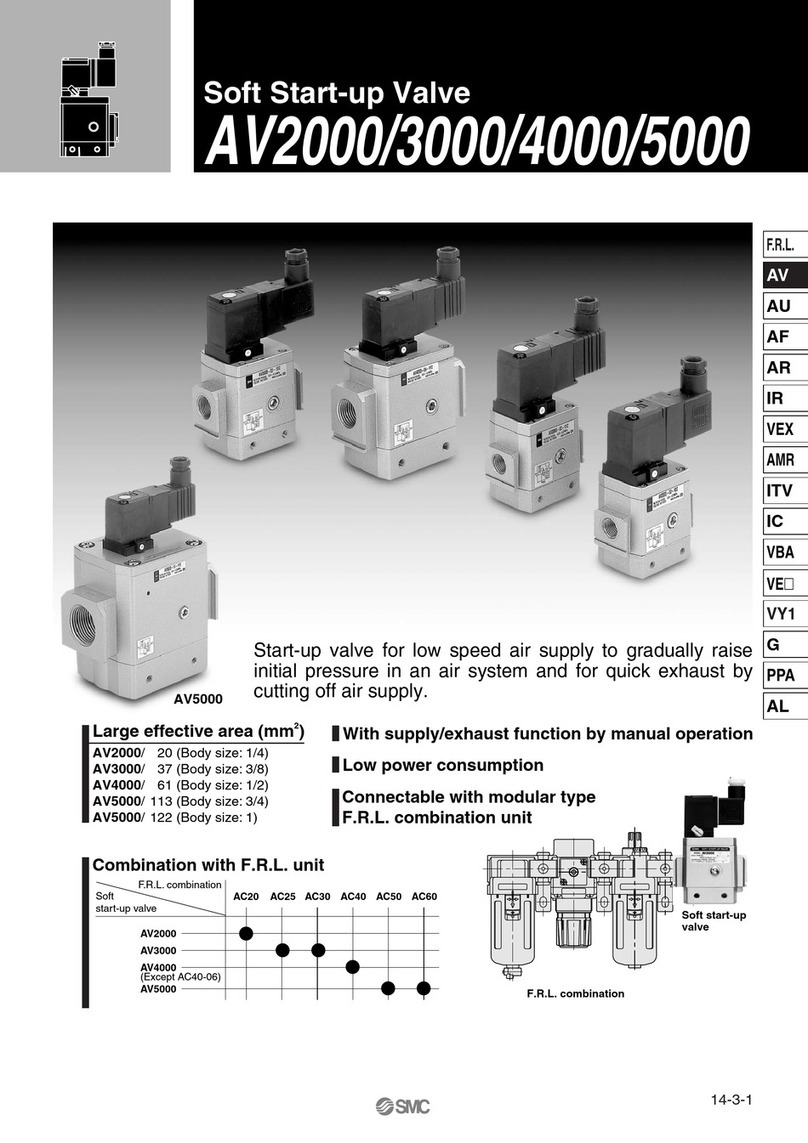
SMC Networks
SMC Networks AV2000 manual
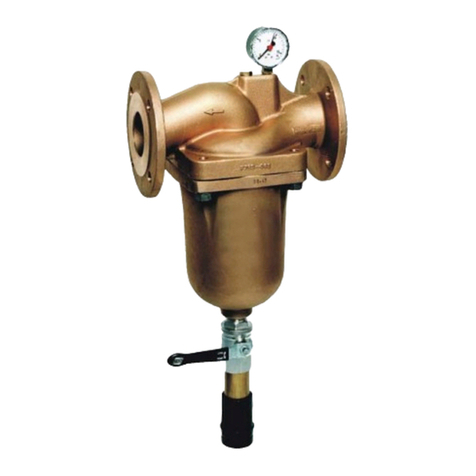
Kemper
Kemper Figure 708 Installation and operating instructions
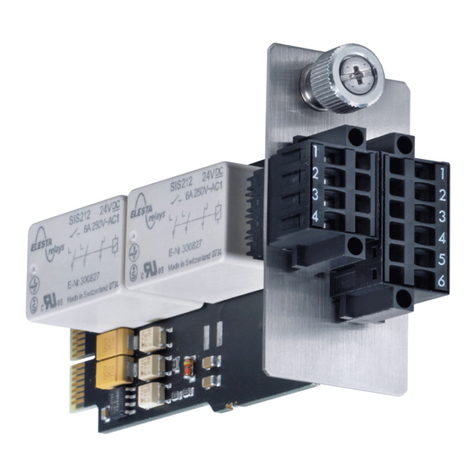
Beckhoff
Beckhoff AX5801 quick guide

Emerson
Emerson Anderson Greenwood 93 Series Installation and maintenance instructions

Eaton
Eaton SM65 Handbook