CiDRA Sonartrac GVF-100 Installation and operation manual

CiDRA Corporation 50 Barnes Park North Wallingford, CT 06492
Tel. 203-265-0035 Fax. 203-294-4211 www.cidra.com
MODEL GVF-100 GAS VOLUME
FRACTION MONITORING SYSTEM
INSTALLATION & STARTUP
MANUAL


Copyright © 2006 CiDRA Corporation Page i
20639-01 Rev 03
Table of Contents
1 INTRODUCTION.................................................................................1-1
1.1 Sensor Head Description and Function..............................................1-1
1.2 Transmitter Description and Function ................................................1-1
2 INTELLECTUAL PROPERTY NOTICES.............................................2-1
3 EQUIPMENT SAFETY COMPLIANCE ...............................................3-1
3.1 Safety.................................................................................................3-1
3.2 North American Emissions.................................................................3-1
3.3 European Emissions and Immunity....................................................3-1
3.4 CE Marking.........................................................................................3-2
4 WARRANTY........................................................................................4-1
5 GENERAL SAFETY GUIDELINES......................................................5-1
5.1 Introduction.........................................................................................5-1
5.2 Safety Precautions.............................................................................5-1
5.3 Definitions of Symbols........................................................................5-1
5.3.1 General Warning or Caution.........................................................5-2
5.3.2 Grounding.....................................................................................5-2
5.3.3 On.................................................................................................5-2
5.3.4 Off.................................................................................................5-2
5.3.5 General Warnings ........................................................................5-3
5.3.6 General Cautions .........................................................................5-4
6 UNPACKING AND PARTS LIST.........................................................6-1
6.1 Unpacking ..........................................................................................6-1
6.2 Inventory of Parts...............................................................................6-1
6.3 Class I, Division 2 Labels...................................................................6-2
7 SENSOR INSTALLATION...................................................................7-1
7.1 Class I, Division 2, Groups A, B, C, and D Rated Equipment ............7-1
7.2 Tools Required For Installation ..........................................................7-1
7.3 Sensor Installation Guidelines............................................................7-2
7.4 Process Piping Considerations ..........................................................7-2
7.4.1 Pipe Preparation...........................................................................7-3
7.4.2 Determine the Pipe Inner Diameter (ID).......................................7-3
7.5 Sensor Band Installation ....................................................................7-4
7.5.1 Sensor Band Short Test...............................................................7-9
7.6 Sensor Cover Installation.................................................................7-10
7.6.1 Fiberglass Cover Installation......................................................7-11
7.6.2 Stainless Steel Cover Installation...............................................7-14
7.6.3 Sensor Assembly Cable Connection..........................................7-18
7.6.4 Rain Boot Installation .................................................................7-19
7.6.5 Sensor Calibration Label............................................................7-20
7.7 Sensor to Transmitter Cable Connections .......................................7-21
7.7.1 Sensor End Cable Attachment...................................................7-21
7.8 Installations on Tubing .....................................................................7-22
8 TRANSMITTER INSTALLATION.........................................................8-1
8.1 Transmitter Power Requirements.......................................................8-1
8.2 Transmitter Environmental Conditions ...............................................8-1
8.3 Transmitter Mounting Instructions......................................................8-1
8.3.1 Bulkhead Mounting.......................................................................8-2
8.3.2 Pipe Mounting ..............................................................................8-2
8.4 Transmitter Cable Connections..........................................................8-3

Copyright © 2006 CiDRA Corporation Page ii
20639-01 Rev 03
8.4.1 Transmitter Housing Cable Entry.................................................8-3
8.4.2 Transmitter Output, Sensor and Sensor Head Connections........8-4
8.4.3 Transmitter Electrical Power Cable Installation..........................8-10
8.4.4 Sensor Calibration Label............................................................8-12
9 TRANSMITTER FUNCTIONS.............................................................9-1
9.1 Transmitter Layout .............................................................................9-1
9.2 Transmitter Output Definitions............................................................9-2
9.3 Transmitter Input Definitions ..............................................................9-6
9.4 Keypad...............................................................................................9-7
9.5 Transmitter Display ............................................................................9-8
9.5.1 Operational Mode.........................................................................9-8
9.5.2 Menu Mode ................................................................................9-12
10 TRANSMITTER SETUP....................................................................10-1
10.1 Transmitter Menus ...........................................................................10-1
10.1.1 Basic Config Menu.....................................................................10-1
10.1.2 Output Config Menu...................................................................10-3
10.1.3 Input Config................................................................................10-9
10.1.4 Customize Menu ......................................................................10-10
10.1.5 Communications Menu.............................................................10-11
10.1.6 Diagnostics Menu.....................................................................10-11
10.1.7 Info Menu .................................................................................10-13
10.2 Resetting Processor.......................................................................10-14
10.3 Resetting to Factory Defaults.........................................................10-15
11 TRANSMITTER STARTUP & OPERATION......................................11-1
11.1 Initial Start-up...................................................................................11-1
11.1.1 Initial Setup.................................................................................11-1
12 TRANSMITTER USB PORT..............................................................12-1
12.1 USB Port File Naming Convention...................................................12-3
12.2 Save Snapshot.................................................................................12-4
12.3 Load Configuration...........................................................................12-4
12.4 Advanced Functions.........................................................................12-5
13 SENSOR REMOVAL PROCEDURE.................................................13-1
Appendix A SONARtracTM GVF-100 SPECIFICATIONS ............................ A-1
Appendix B SONARtracTM EC DECLARATION OF CONFORMITY........... B-1
Appendix CSYSTEM CONTROL DRAWING SONARtracTM, NON-
INCENDIVE........................................................................................ C-1
Appendix DMATERIAL SAFETY DATA SHEETS......................................D-1
Appendix ECONVERSION FACTORS ...................................................... E-1
Appendix FPHYSICAL PROPERTIES OF WATER....................................F-1
Appendix GEND USER LICENSE AGREEMENT......................................G-1
Appendix HSPARE PARTS LIST...............................................................H-1

Copyright © 2006 CiDRA Corporation Page iii
20639-01 Rev 03
List of Figures
Figure 1 General Warning or Caution Symbol..........................................5-2
Figure 2 Grounding Symbol......................................................................5-2
Figure 3 On Symbol..................................................................................5-2
Figure 4 Off Symbol..................................................................................5-2
Figure 5 Class I Division 2 Label Information............................................6-2
Figure 6 Sensor Band Screw and Alignment Pins....................................7-4
Figure 7 Sensor Band Screw Tightening Sequence.................................7-6
Figure 8 Sensor Band Screw Assembly....................................................7-6
Figure 9 Sensor Band Spacer Tool...........................................................7-7
Figure 10 Sensor Band Spacing Tool Installed on Sensor Screw ..............7-7
Figure 11 Installed Sensor Band.................................................................7-8
Figure 12 Upper Sensor Cover Assembly Outside View ..........................7-10
Figure 13 Upper Sensor Cover Assembly Inside View.............................7-10
Figure 14 Orientation (Clocking) of Sensor Cover....................................7-11
Figure 15 Sensor Cover Bolt Installation...................................................7-12
Figure 16 Sensor Cover Bolt Tightening Sequence..................................7-13
Figure 17 Stainless Steel Cover Assembly...............................................7-14
Figure 18 Applying Joining Compound to Gasket Edge ...........................7-15
Figure 19 Boot Gasket Band Kit................................................................7-15
Figure 20 Boot Gasket Band Installation...................................................7-15
Figure 21 Splice Protector Plate Installation.............................................7-16
Figure 22 BAND-IT®Model C001 Tool Use..............................................7-16
Figure 23 Final Alignment and Securing of Gasket Band.........................7-17
Figure 24 Band Termination......................................................................7-17
Figure 25 Boot Gasket Fender Assembly.................................................7-18
Figure 26 Sensor Assembly Cable Installation .........................................7-18
Figure 27 Sensor Calibration Label...........................................................7-20
Figure 28 Elastomeric Strip Installation on Tubes.....................................7-22
Figure 29 Bulkhead Mount Hole Pattern.....................................................8-2
Figure 30 Pole Mount Kit.............................................................................8-2
Figure 31 Power and Signal Interconnects.................................................8-3
Figure 32 Transmitter Housing Cable Gland Holes ....................................8-3
Figure 33 Terminal Board Layout................................................................8-4
Figure 34 Transmitter Output Terminals.....................................................8-5
Figure 35 Transmitter Sensor Terminals.....................................................8-6
Figure 36 Sensor Head to Transmitter Cable Connection Terminals .........8-7
Figure 37 Armored Cable Stiffener Plate Installation..................................8-8
Figure 38 Removal of Cable Armor.............................................................8-9
Figure 39 Armored Cable Connector Installed............................................8-9
Figure 40 Armored Cable Installation........................................................8-10
Figure 41 Transmitter Power Connection .................................................8-11
Figure 42 Sensor Calibration Label...........................................................8-12
Figure 43 Transmitter Layout......................................................................9-1
Figure 44 Transmitter Output Terminals.....................................................9-2
Figure 45 Pulse Switch Closure..................................................................9-3
Figure 46 Alarm Switch Closure..................................................................9-3
Figure 47 Internally (Transmitter) Powered 4–20mA Loop.........................9-4
Figure 48 Externally Powered 4–20mA Loop..............................................9-5
Figure 49 Transmitter Sensor Terminals.....................................................9-6

Copyright © 2006 CiDRA Corporation Page iv
20639-01 Rev 03
Figure 50 Transmitter Front Panel Keyboard..............................................9-7
Figure 51 GVF Startup Screen....................................................................9-8
Figure 52 Operating Transmitter Display....................................................9-9
Figure 53 Initialization Mode.....................................................................9-11
Figure 54 GVF Measurement Screen.......................................................9-12
Figure 55 Typical Menu Screen................................................................9-14
Figure 56 Editing Parameter By Digits......................................................9-14
Figure 57 Editing Whole Parameter..........................................................9-15
Figure 58 Output Configuration Example Screen .....................................10-4
Figure 59 4-20mA Trim Message box.......................................................10-4
Figure 60 Speed Of Sound and Gas Volume Fraction Pulse Output........10-6
Figure 61 Test Passes Display Example ................................................10-11
Figure 62 Test Failed..............................................................................10-11
Figure 63 Error Codes Listed in Event Log.............................................10-14
Figure 64 Sensor Max/Min Display.........................................................10-14
Figure 65 System Start Display.................................................................11-1
Figure 66 Sensor Cable Connector Removal ...........................................13-1
List of Tables
Table 1 SONARtracTM GVF-100 Parts List...............................................6-1
Table 2 Installation Tools For SONARtracTM GVF-100 Monitoring System7-1
Table 3 Gauge Block and Screw Size......................................................7-5
Table 4 List of Transmitter Signal Outputs...............................................8-5
Table 5 Sensor to Transmitter Cable Terminal Connections....................8-8
Table 6 Keypad Functions in Operational and Menu Modes....................9-7
Table 7 Line 1 and Line 2 Values.............................................................9-9
Table 8 Status Line Code.........................................................................9-9
Table 9 Status Line Messages...............................................................9-10
Table 10 Quality Message Definitions .....................................................9-10
Table 11 Mode Message Definitions........................................................9-10
Table 12 SONARtracTM GVF Menu Diagram Software Release 03.03.XX9-13
Table 13 Transmitter Menu Tree Software Release 03.03.XX................9-16
Table 14 Maximum Pulse Per Second Based On Pulse Width ...............10-5
Table 15 Alarm Triggers ..........................................................................10-7
Table 16 Transmitter Setup Template .....................................................11-6
Table 17 USB Port Menu.........................................................................12-2
Table 18 USB Port File Naming Convention............................................12-3
Table 19 USB Port File Name Examples.................................................12-3

Copyright © 2006 CiDRA Corporation Page 1-1
20639-01 Rev 03
1 INTRODUCTION
The CIDRA Corporation SONARtracTM Model GVF-100 (Gas Volume
Fraction) Monitoring System is a clamp-on process monitoring system
used to measure the gas volume fraction (amount of entrained air /
gas) contained in a fluid within process pipes on a real-time basis.
The SONARtracTM GVF-100 utilizes patented array processing
techniques to listen to and interpret the acoustic field generated by
machinery, piping and flow present in process flow. The clamp-on
design eliminates the need for cutting pipe or interrupting process flow
during installation.
The SONARtracTM GVF-100 consists of a common transmitter and
sensor heads sized for different pipe diameters.
SONARtracTM gas volume fraction meters certified for use in
hazardous areas are rated for use in Class I, Division 2, Groups A, B,
C, and D environments (per US and Canadian standards).
This manual covers the basic installation and setup of the
SONARtracTM Model GVF-100 Monitoring System. In all cases, local
safety and operating practices take precedence over the information
contained within this document.
For additional information, contact your local sales agent or CiDRA
Corporation Customer Support by telephone at 1-877-243-7277
1.1 Sensor Head Description and Function
The SONARtracTM sensor head contains no moving parts. The sensor
head includes a sensor band and a fiberglass or stainless steel cover
assembly to protect the sensor band. The sensor band is wrapped
around and clamped onto the process pipe. A multi-conductor cable
electrically connects the sensors to an electronic module mounted in
the cover assembly. Signals from the electronic module exit through a
NEMA 4X rated connector mounted to the outer surface of the cover
assembly.
1.2 Transmitter Description and Function
The SONARtracTM transmitter receives electrical signals from the
sensor head. The signals are processed using SONARtracTM array
processing firmware that displays the calculated results on an integral
LCD screen. Results can also be transmitted using the 4–20mA
analog output, pulse output, alarm output or the RS-485/232 digital
output. The electronic assembly is housed in a rugged NEMA 4X
enclosure.

Copyright © 2006 CiDRA Corporation Page 2-1
20639-01 Rev 03
2 INTELLECTUAL PROPERTY NOTICES
CiDRA Corporation’s Process Monitoring Products may be covered by
one or more of the following granted U.S. Patent(s): 6,354,147,
6,587,798, 6,609,069, 6,435,030, 6,691,584, 6,732,575, 6,782,150,
6,862,920, 6,889,562, 6,732,150. Other patents are pending; see
www.cidra.com for the latest listing of patents.
This manual is covered by U.S. and international copyright laws. No
part of this manual may be reproduced, modified or transmitted in
whole or in part in any form or by any means, electronic or
mechanical, including photocopy, recording, or any information
storage and retrieval system, without permission in writing from
CiDRA Corporation.
Third party end-user license agreements (“EULA”) are provided in
Appendix G of this document.
Copyright © 2006 by CiDRA Corporation, all rights reserved.
SONARtrac, SONARstick and logo are trademarks of CiDRA
Corporation.

Copyright © 2006 CiDRA Corporation Page 3-1
20639-01 Rev 03
3 EQUIPMENT SAFETY COMPLIANCE
3.1 Safety
This equipment is listed with TÜV Rheinland of North America, Inc., a
nationally recognized testing laboratory, and certified for ordinary
location use per the following US, Canadian, and European standards:
UL 61010A-1, CSA C22.2 No. 1010, and EN 61010-1:2001.
If so marked, this equipment is certified by Underwriters Laboratories
for use in areas that - under fault conditions - include explosive gas
atmospheres as defined by Class I, Division 2, Groups A, B, C, and D
per compliance with these US and Canadian standards: UL 1604, UL
508, CSA C22.2 No. 213, and CSA C22.2 No. 142.
3.2 North American Emissions
This equipment is compliant with Class A limits for radiated and
conducted radio noise emissions, as defined in Subpart A of Part 15 of
the FCC rules, as well as the requirements defined in ICES-003 for
Canada.
This Class A digital apparatus complies with Canadian ICES-003.
Cet appareil numérique de la classe A est conforme à la norme NMB-
003 du Canada.
3.3 European Emissions and Immunity
This equipment is compliant with the requirements set forth in EN
61326-1:1997, Electrical Equipment for Measurement, Control and
Laboratory Use - EMC requirements as well as EN 55011:1998
Industrial, Scientific, and Medical (ISM) Radio Frequency Equipment -
Radio Disturbance Characteristics - Limits and Methods of
Measurement.
For the purpose of Electromagnetic Compatibility (EMC) requirements,
this product is categorized as Group 1, Class A ISM equipment. This
categorization applies to Industrial, Scientific or Medical equipment
that intentionally generates or uses conductively coupled (but not
intentionally radiated) radio-frequency energy that is necessary for the
internal functioning of the equipment. The level of EMC compliance is
consistent with industrial use but not for domestic purposes.
CAUTION
Class A equipment is intended for use in an industrial
environment. There may be potential difficulties in ensuring
electromagnetic compatibility in other environments, due to
conducted as well as radiated disturbances.

Copyright © 2006 CiDRA Corporation Page 3-2
20639-01 Rev 03
3.4 CE Marking
This equipment is CE marked for ordinary location use and complies
with the following European Directives:
73/23/EEC Low-Voltage Directive
89/336/EEC EMC Directive
Further details are listed in the EC Declaration of Conformity (P/N
20634-01), a copy of which can be found in Appendix B of this
Document as well as on our website at http://www.cidra.com.

Copyright © 2006 CiDRA Corporation Page 4-1
20639-01 Rev 03
4 WARRANTY
The terms and conditions, including warranty, of the purchase of
CiDRA’s Process Monitoring Products is outlined in the document
entitled “CiDRA’s Terms and Conditions of Sale”.

Copyright © 2006 CiDRA Corporation Page 5-1
20639-01 Rev 03
5 GENERAL SAFETY GUIDELINES
CiDRA Corporation recommends the installer fully read this manual
prior to installing and operating the SONARtracTM system.
Note: Items that pertain to systems rated for Class I, Division 2,
Groups A, B, C, and D operation are highlighted in italic print.
5.1 Introduction
This manual is intended to be a general installation guide for the
CiDRA SONARtracTM GVF-100 System. It is not intended to cover the
installation details for every process due to the wide variety of
applications and processes on which the system can be used. In all
cases, local safety and operating practices should take precedence
over instructions contained within this manual.
5.2 Safety Precautions
The following style of Warnings and Cautions are used throughout the
manual to draw attention to information regarding personnel safety
and equipment care. They are not intended to replace local or plant
safety procedures.
WARNING
Situation has the potential to cause bodily harm or death.
CAUTION
Situation has the potential to cause damage to property or
equipment.
5.3 Definitions of Symbols
The following terms and symbols are used in this document and on
the SONARtracTM system where safety related issues occur.

Copyright © 2006 CiDRA Corporation Page 5-2
20639-01 Rev 03
5.3.1 General Warning or Caution
Figure 1 General Warning or Caution Symbol
The Exclamation Symbol in Figure 1 appears in Warning and Caution
tables throughout this document. This symbol designates an area
where personal injury or damage to the equipment is possible.
5.3.2 Grounding
Figure 2 Grounding Symbol
The Grounding Symbol in Figure 2 appears on labels affixed to the
SONARtracTM system. This symbol identifies a terminal intended for
connection to an external (ground) conductor for protection against
electric shock in case of a fault, or the terminal of a protective earth
(ground) electrode.
5.3.3 On
Figure 3 On Symbol
The On Symbol in Figure 3 represents the Power ON condition of the
power switch on the SONARtracTM system, if so equipped.
•Class I, Division 2 rated systems do not have this switch.
5.3.4 Off
Figure 4 Off Symbol
The Off Symbol in Figure 4 represents the Power Off condition of the
power switch on the SONARtracTM system, if so equipped.
•Class I, Division 2 rated systems do not have this switch.

Copyright © 2006 CiDRA Corporation Page 5-3
20639-01 Rev 03
5.3.5 General Warnings
Observe these general warnings when operating or servicing this
equipment:
•Prior to operation of this equipment, personnel should read the
instruction manual thoroughly.
•For systems installed in Class I, Division 2 areas, Power Entry and
Inputs/Outputs must be installed in accordance with Article
501.10(B)(1) of the National Electrical Code ANSI/NFPA 70:2005.
•For systems installed in Class I, Division 2 areas, Sensor Head
Cable must be installed in accordance with Article 501.10(B)(3) of
the National Electrical Code ANSI/NFPA 70:2005.
•Only equipment rated for Class I, Division 2, Groups A, B, C, and
D should be installed in those areas. Verify the system rating on
the equipment labels (refer to Section 6.3 of this manual).
•Use a damp cloth to wipe sensor band cover and transmitter when
installed in Class I, Division 2 areas to dissipate potential static
charge buildup.
WARNING
Using a dry cloth to clean the transmitter enclosure can cause
static discharge, which could result in an explosion in an
explosive atmosphere. Always use a damp cloth to clean the
transmitter enclosure.
•If the sensor band was shipped with a sensor band shorting plug
installed on the sensor band to preamplifier cable connector,
ensure the sensor band shorting plug is installed on the sensor
band cable prior to installing sensor band. Sensors bands with an
‘R” in the Part Number suffix (e.g. Part #: 20686-26-R) do not
require a shorting plug.
•As for any electrical equipment in Class I, Division 2 installations
wherein explosive atmospheres might be present, it is especially
important to de-power and remove the SONARtracTM meter from
service if its appearance or operating behavior indicates that it is
damaged or malfunctioning and/or that its safety features have
been otherwise compromised.
•Trained personnel must carry out service on this equipment.
•Follow all warnings on the unit and in the operating instructions.
•This equipment is grounded through the grounding conductor of
the power cord.
•Ensure all power cords, sensor to transmitter cable and signal
cables are properly routed to eliminate damage to them. Cable
conduit may be desirable to minimize potential damage.

Copyright © 2006 CiDRA Corporation Page 5-4
20639-01 Rev 03
•Prior to servicing, lockout all electrical power sources.
•Care should be taken when using the operator keypad to avoid
touching any electrical connection or contact points.
•Do not wear rings or wristwatches when servicing this equipment.
•Use only the specified fuse(s) with the correct type number,
voltage and current ratings as referenced in the appropriate
locations in the service instructions or on the equipment.
5.3.6 General Cautions
Observe these cautions when operating or servicing this equipment:
•Read the instructions for proper input voltage range selection.
•There are no user serviceable parts inside the SONARtracTM
sensor band. Modification or disassembly may void the system
warranty.
•Disconnect power to transmitter prior to replacing fuse(s).
•Use only CiDRA specified replacement parts.
•Follow static sensitive device precautions when servicing.
•This product should only be powered as described in the manual.
•Do not run power and signal wires in a common conduit.

Copyright © 2006 CiDRA Corporation Page 6-1
20639-01 Rev 03
6 UNPACKING AND PARTS LIST
6.1 Unpacking
The SONARtracTM GVF-100 will typically be packaged in three
shipping containers. One box will contain the sensor band and sensor
cover assemblies, and installation hardware; the second box will
contain the transmitter assembly and installation hardware; and the
third box will contain the sensor to transmitter cable assembly.
Note: Cidra Corp. recommends the original packing materials be
saved in the event that the system is removed or relocated.
CAUTION
Use care in unpacking and transporting system. Improper
handling may result in damage to system components.
Whenever possible use the original packing materials to transport the
system to the installation site to minimize the likelihood of damage.
WARNING
Static discharge may occur when handling sensor band and
packing material. Remove from packing materials when entering
hazardous areas. Always keep the sensor band shorting plug
installed until sensor band is installed on the process pipe.
6.2 Inventory of Parts
Table 1 lists the parts contained in the shipping containers.
Description
SONARtracTM GVF-100 Gas Volume Fraction Process Monitoring
System
Sensor Head Cable
Installation Hardware
Sealant, Joint and Thread, PTFE Paste, 3.5 oz Tube – included with
fiberglass sensor cover assemblies
Gauge, Spring Gap (used for sensor installation) - included with sensor
band assembly
Model GVF-100 Gas Volume Fraction Process Monitoring System
Installation & Startup Manual
Kit, Parts, Pole Mounting (Option)
Sensor Rain Guard Kit for vertical installations (Option)
Table 1 SONARtracTM GVF-100 Parts List

Copyright © 2006 CiDRA Corporation Page 6-2
20639-01 Rev 03
6.3 Class I, Division 2 Labels
Transmitters and sensor covers rated for use in Class I, Division 2
areas are labeled with the following information (or a subset of it) so
they can be identified for use in those areas.
Telemetering Equipment For Use in Hazardous Locations
Class I, Division 2, Groups A, B, C, and D Hazardous Locations
Providing Nonincendive Field Circuits When Connected Per DWG #
20332-01
Figure 5 Class I Division 2 Label Information
WARNING
Use of non- Class I, Division 2 rated equipment in Class I,
Division 2 areas may result in a fire or explosion.

Copyright © 2006 CiDRA Corporation Page 7-1
20639-01 Rev 03
7 SENSOR INSTALLATION
7.1 Class I, Division 2, Groups A, B, C, and D Rated
Equipment
•Equipment so marked is suitable for use in Class I, Division 2,
Groups A, B, C, and D or non-hazardous locations only.
•WARNING – EXPLOSION HAZARD – Do not disconnect
equipment unless power has been removed or the area is known
to be non-hazardous.
•WARNING – EXPLOSION HAZARD –Substitution of components
may impair suitability for Class I, Division 2.
•WARNING – EXPLOSION HAZARD –Do not replace fuses unless
power has been switched off or the area is known to be non-
hazardous.
•WARNING – EXPLOSION HAZARD –Ensure a sensor band
shorting plug is installed on the sensor band cable connector
during installation and removal from process pipe.
7.2 Tools Required For Installation
The following tools are required for system installation. Additional
tools may be required based on particular installation needs.
Required Tools Recommended Tools
Cable cutter Wire number markers
Wrenches, 1/2 “x 9/16”, combination,
open-end, 2 ea Portable electric screw driver with 7/64”
hex driver bit
Wire strippers for 20 gauge wire Open end or combination wrench set
Allen wrench or hex driver, 7/64-inch for
No. 6 socket head cap screw, or 5/32-
inch for No. 10 socket head cap
Spring clamps to hold cover halves in
place temporarily
Spacer tool, sensor fastener (provided
with sensor band) Cable jacketing removal tool
Screw drivers, Blade, 3/16” and 1/4”,
Phillips medium blade Hacksaw and or armor cutter (armored
cable cutting)
14” Adjustable wrench (armored cable) Socket wrench set
Sandpaper, cleaning rags, etc as
required for pipe cleaning Volt-ohm meter
BAND-IT®Tool Model C001 (or
equivalent) for use with stainless steel
covers. Refer to www.band-it-idex.com
for distributor information.
Electricians tape
Table 2 Installation Tools For SONARtracTM GVF-100 Monitoring System

Copyright © 2006 CiDRA Corporation Page 7-2
20639-01 Rev 03
7.3 Sensor Installation Guidelines
The following are general installation guidelines and recommendations
for installing a SONARtracTM sensor.
•Where necessary, get a Hot Work Permit prior to installation of
system.
•Select locations with well-developed flow profiles.
•Avoid installation locations directly after piping configurations that
cause flow jetting.
•Install flow sensor upstream of control valves, “T”s, orifice plates,
and any other severe source of flow disturbance.
•Locate the sensor upstream of pipe taps such as those used for
temperature and pressure sensors.
•Good piping practices are required near flanges. This includes
good alignment of pipes, and properly sized and installed gaskets
that do not disturb the flow profile.
•Contact your local distributor or CiDRA Technical Support if you
have questions.
7.4 Process Piping Considerations
The SONARtracTM sensor head assembly mounts on the process
pipe. There is no need for breaking any process connections or for
shutting down the process. The sensor head must be installed in a
location that ensures a full pipe during operation.

Copyright © 2006 CiDRA Corporation Page 7-3
20639-01 Rev 03
7.4.1 Pipe Preparation
Remove pipe insulation if it is present.
WARNING
Asbestos containing insulation materials may be present.
Asbestos fibers have been known to cause health problems. If
unsure of the contents of pipe insulation materials contact the
plant representative for that area.
WARNING
Process Heating Tapes may be present. This may present an
electrical shock hazard. Follow plant Lock-out / Tag-out
requirements.
WARNING
Process pipes may be hot. A burn hazard may exist. Use care
when working with hot pipes.
Clean pipe surface using a scraper, sand paper strips, a water (or
solvent for greasy pipes) rinse and final wipe with a clean rag. The
pipe surface under the sensor band assembly should be clean and
free of rust and rust spots, grit, grease, protruding weld spots and
weld splatter. A good guideline is to clean the pipe as if it were going
to be painted.
Avoid dents as they can create flow disturbances within the pipe.
Select a location that ensures full contact between the sensor and the
pipe.
Painted surfaces are normally satisfactory provided they are smooth
and free of chips over 0.25-inch (6.4 mm) diameter. Ensure a smooth
painted finish by sanding the area where the sensor will be mounted.
Finally, wipe the pipe using a damp cloth rag or paper towel.
7.4.2 Determine the Pipe Inner Diameter (ID)
Record the nominal pipe size based on the pipe size and pipe
schedule, as this will be input into the transmitter.
Alternatively, measure and calculate the pipe ID. Accurately measure
the pipe outside diameter (OD). Use an ultrasonic thickness
measurement gauge to determine the wall thickness (tw) at a minimum
of 4 locations equally spaced around the pipe and average the
measurements. Calculate the pipe inner diameter (ID = OD – (2tw)).
(There are several vendors of ultrasonic thickness gauges.)
Table of contents
Other CiDRA Measuring Instrument manuals
Popular Measuring Instrument manuals by other brands
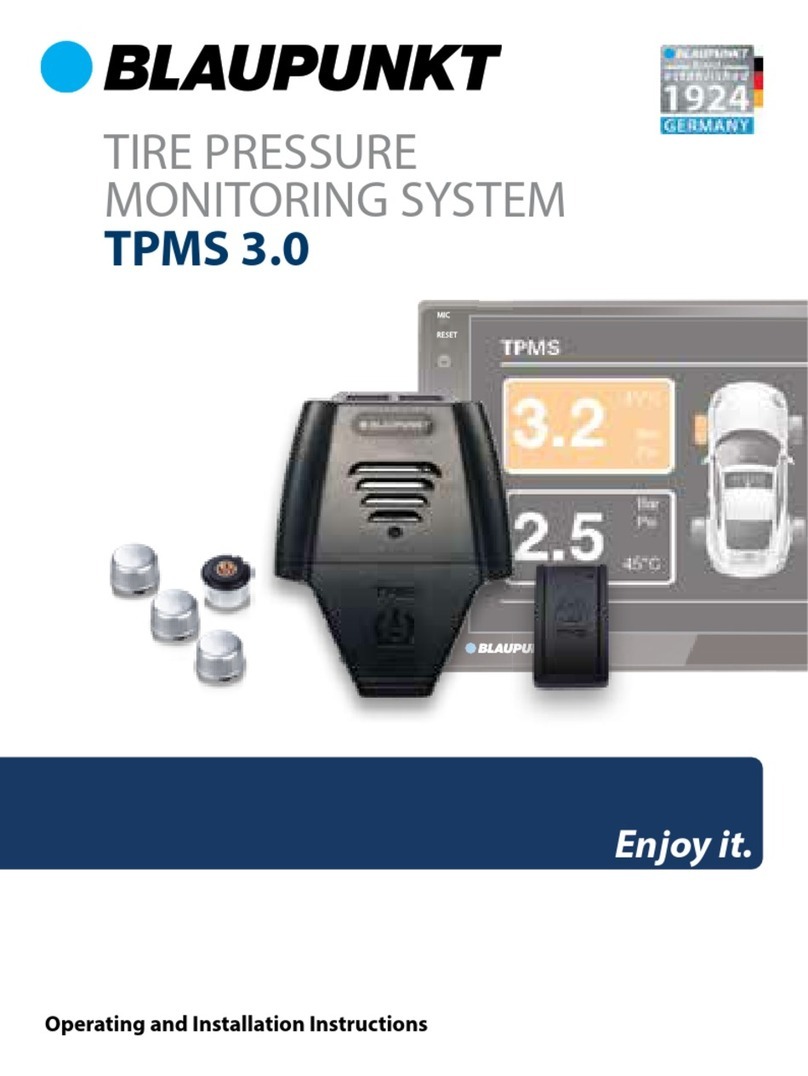
Blaupunkt
Blaupunkt TPMS 3.0 Operating and installation instructions
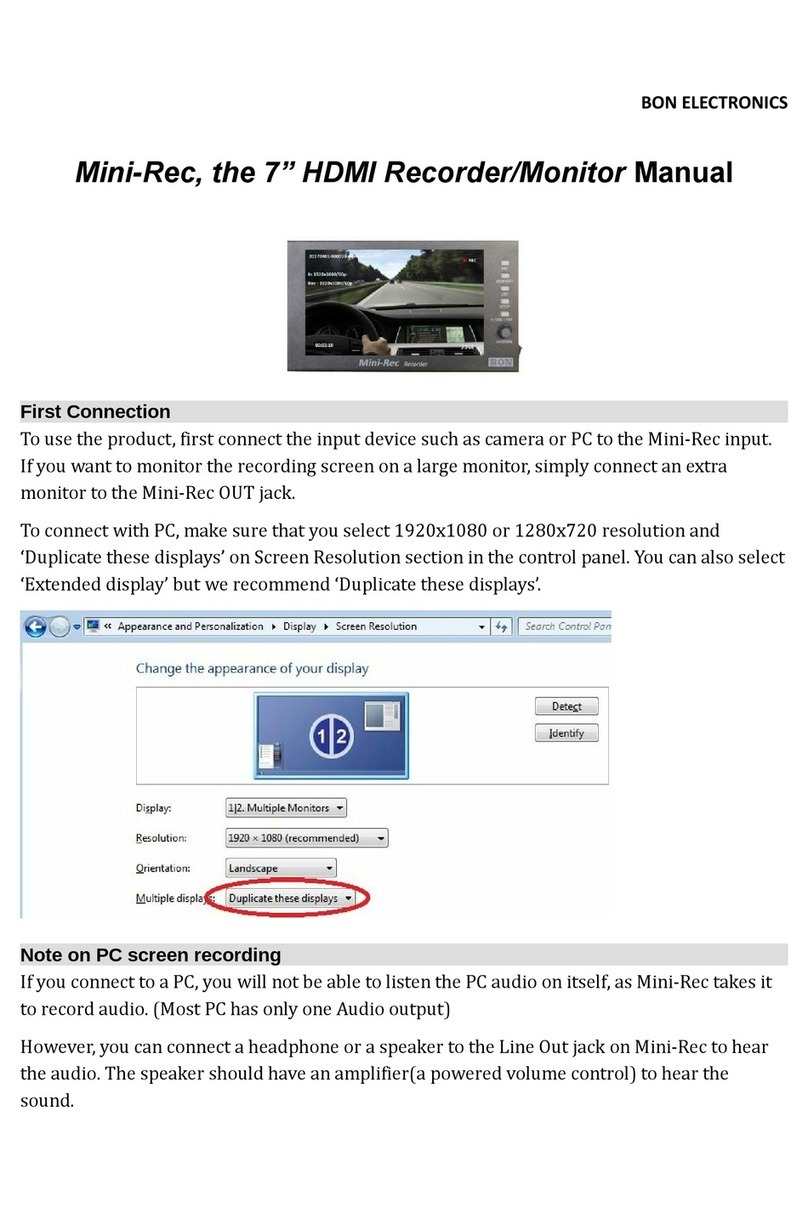
BON ELECTRONICS
BON ELECTRONICS Mini-Rec user manual

AR
AR DC7210A Operating and service manual

Horiba Scientific
Horiba Scientific 9630-10D instruction manual
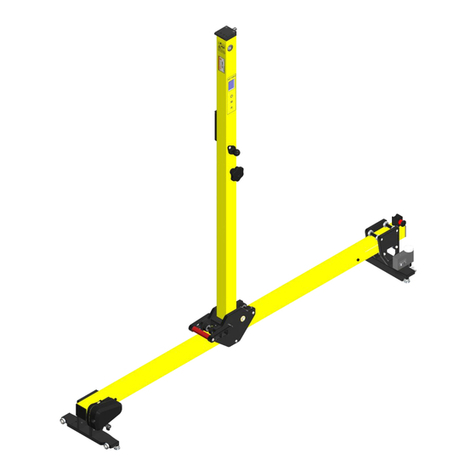
Abtus
Abtus ABT 8000 instruction manual
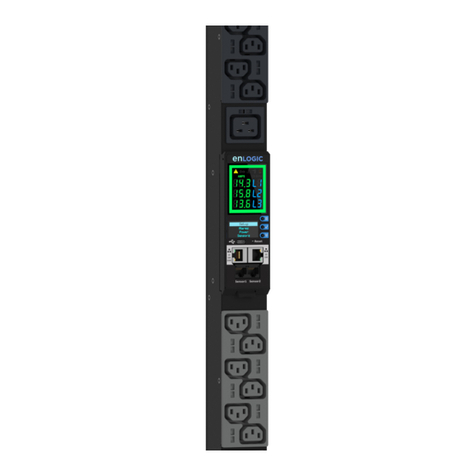
Enlogic
Enlogic Advantage Series user manual