Cirus Controls SpreadSmart Rx User manual

Rev Z Page 1 11/28/2011
Copyright © 2011 by Cirus Controls, LLC. All Rights Reserved. No part of this material may be reproduced without the express
written permission of Cirus Controls LLC for each reproduction.
SpreadSmart Rx
TM
(with Touch Screen)
Operation Manual

Rev Z Page 2 11/28/2011
Copyright © 2011 by Cirus Controls, LLC. All Rights Reserved. No part of this material may be reproduced without the express
written permission of Cirus Controls LLC for each reproduction.
Configuration Log Page.................................................................................................. 4
Limited Warranty........................................................................................................ 5
Revision Level of this Manual........................................................................................ 6
Package Contents ............................................................................................................ 6
Functional Overview and Fundamental Operating Parameters ...................................... 6
Open Loop or Closed Loop Spreading ....................................................................... 6
Distance or Area Spreading of Granular Mat’l. with Proportional Gate .................... 7
“Prescription Spreading” and/or “Operator Choice” Spreading................................. 7
Temperature Response Spreading............................................................................... 7
Load and Rate Calculator............................................................................................ 7
High Current Electric Pre-Wet Systems ..................................................................... 8
Single or Two-Tier Anti-Ice System........................................................................... 8
Data Recording and Drive by Download™ for Data.................................................. 9
Operating Functions Matrix – SpreadSmart Rx.......................................................... 9
Basic Operation Controls:......................................................................................... 10
Startup Checklist – SpreadSmart Rx
TM
........................................................................ 10
Installation Steps........................................................................................................... 10
STEP 1 - Installation................................................................................................. 10
Guard Against RF Interference................................................................................. 10
Installing the control unit .......................................................................................... 11
Connecting the cabling ............................................................................................. 11
STEP 2 – Power Verification.................................................................................... 11
Multiple Uses of touch screen buttons (=key pad switches): ................................... 11
STEP 3-Set up Wizard .............................................................................................. 12
STEP 4: “Un-Calibrated” Automatic Mode ............................................................ 12
STEP 5: Speedometer Calibration ........................................................................... 13
STEP 6- Pre-Delivery Functional Test with Diagnostics ......................................... 14
Using stored calibration files to configure multiple trucks....................................... 14
Post Delivery Steps ....................................................................................................... 15
STEP A - Material Setup & Calibration ................................................................... 15
Material Setup........................................................................................................... 15
Granular Drop Test - Open or Closed Loop ................................................................. 15
STEP B - Spinner Calibration with Granular Material............................................. 17
STEP C - Post Delivery Functional Test .................................................................. 18
Managing Materials – Granular, Pre-Wet and Anti-Ice................................................ 18
Choosing a material name and recording data:......................................................... 19
Changing “Materials” program during normal operation......................................... 19
Temp Response
TM
Prescription Set Up – for each material type.............................. 19
Recording Spreading Data for each named material ................................................ 21
Managing Information on SpreadSmart Rx
TM
............................................................. 21
Battery Backup for Date and Time ........................................................................... 22
Accessing Storm and Season Totals (SST) from SpreadSmart Rx
TM
...................... 22
Downloading Storm and Season Totals (SST) from SpreadSmart Rx
TM
................. 23
Re-Setting Totals (SST) on SpreadSmart Rx
TM
....................................................... 23
Other Downloads – Calibration/System Settings Data............................................. 24
Operational Modes - Description.................................................................................. 25

Rev Z Page 3 11/28/2011
Copyright © 2011 by Cirus Controls, LLC. All Rights Reserved. No part of this material may be reproduced without the express
written permission of Cirus Controls LLC for each reproduction.
Accessing the “Mode” Screens................................................................................. 25
Automatic Mode – Ground speed oriented............................................................... 25
Alarms....................................................................................................................... 25
Manual Mode – Ground speed triggered .................................................................. 26
No Speedometer Mode – Ground speed simulated................................................... 26
Testing the Boom Tiers using No Speedometer Mode............................................. 27
Test Mode – No ground speed interaction................................................................ 27
Unload Mode – Granular or Anti-Ice........................................................................ 27
Using Unload Mode to Re-circulate the material in the anti-ice tanks..................... 28
Contrast ..................................................................................................................... 28
Speedometer with Re-settable Odometer (miles & feet) .......................................... 28
Material ..................................................................................................................... 29
Fill Tank.................................................................................................................... 29
Common Methods of Operation in Automatic Mode ................................................... 29
Using Named Materials with Flexible Rates: ........................................................... 29
Using Named Materials/Rates with no changes allowed:......................................... 29
Using Named Materials with Programmed Rate Change Increments: ..................... 29
Load and Rate Calculation........................................................................................ 30
Operating Instructions- Other Settings ..................................................................... 33
Other Settings- Return to Set Up Wizard ................................................................. 33
Configuration of System without using Set up Wizard ................................................ 33
Summary of Setup Parameters.................................................................................. 33
Auger / Conveyor Set up and Trimming................................................................... 35
Spinner and Zero velocity Set Up and Baseline Trimming ...................................... 36
Standard Spinner Configuration and Trimming ....................................................... 36
Zero velocity spinner configuration.......................................................................... 37
Pre-Wet Pump Set up and Trimming........................................................................ 39
Anti-Ice System – Configuration and Trimming Steps ............................................ 40
Validation of Flow Meter Ratings using SpreadSmart Rx ....................................... 42
Optional Equipment ...................................................................................................... 43
In Dash Mount on International Cabs....................................................................... 43
Temperature Sensor .................................................................................................. 43
GPS Receiver ............................................................................................................ 43
Drive by Download
TM
(DBD3.x) ............................................................................. 43
Using the DBD 3.x and DAT software..................................................................... 44
Using the Report Writer – Data Analysis Tool......................................................... 45
Material Detection Module
TM
(MDM)..................................................................... 45
Automatic Proportional Gate Control....................................................................... 48
SpreadSmart System Troubleshooting Guide............................................................... 51
Diagnostics – on board.................................................................................................. 52
Glossary of Terms......................................................................................................... 53
Appendix A: System Drawings ................................................................................... 55
Appendix B: Spare parts list ......................................................................................... 55
Appendix D – Typical Frequency Settings by Valve Mfg ........................................... 55
Appendix E – Anti-Ice Flow and Boom Arrangement ................................................. 56

Rev Z Page 4 11/28/2011
Copyright © 2011 by Cirus Controls, LLC. All Rights Reserved. No part of this material may be reproduced without the express
written permission of Cirus Controls LLC for each reproduction.
Configuration Log Page
Use this page to log your system configuration information. Store in a safe place.
SpreadSmart Rx
TM
System
Today’s Date: _________________ Information logged by ____________________
SpreadSmart Rx
TM
Serial # ____________
Hydraulic Valve Type ____________
Coil Frequency ____________
Granular System Capacity
Auger Sensor Pulses per Pound (kg) ____________
Pre-Wet System Capacities
Pre-Wet Tank Volume (gallons or liters) ____________
Pre-Wet Pump Max Volume Rating (gpm or lpm) ____________
Flow Meter (sensor) Rating (pulses/gal or liter) ____________
Anti-Ice System Capacities
Anti-Ice Tank Volume ____________
Anti-Ice Pump Max Volume Rating ____________
Tier 1 (Low Flow) Boom Rating (max gpm) ____________
Tier 2 (High Flow) Boom Rating (max gpm) ____________
Flow Meter (sensor) Rating (pulses/gallon) ________

Rev Z Page 5 11/28/2011
Copyright © 2011 by Cirus Controls, LLC. All Rights Reserved. No part of this material may be reproduced without the express
written permission of Cirus Controls LLC for each reproduction.
Limited Warranty
Cirus Controls, LLC.
What and who is covered?
This warranty covers all defects in materials or workmanship in your Cirus Controls system under
normal use, maintenance and service. This warranty coverage applies only to the original owner
and is not transferable.
How long is the warranty period?
This warranty coverage runs for a period of 1 year from the date of initial installation (or 13
months from date of shipment from Cirus Controls), whichever occurs first. Replacement parts
are warranted for the remaining portion of the original warranty period or thirty (30) days from
date of shipment from our factory (whichever is greater).
How can you get service?
Cirus Controls’ obligation under this warranty is limited to repairing and/or replacing, at Cirus
Controls’ option, any part or parts that are determined, by Cirus Controls, to be defective. To be
eligible for any claim under this warranty, the owner (or Cirus authorized dealer) must return any
defective part(s) to the factory, within the applicable warranty period (as set out above).
What will we do?
Cirus Controls’ may, at its option, elect to grant adjustments in the field through an authorized
representative and may thereby elect to waive the requirement that parts be returned to Cirus
Controls’ factory. The repair or replacement of defective parts under this warranty will be made
without charge to the owner except for transportation of the part to our authorized repair location.
What is not covered under this warranty?
Cirus Controls will not assume any expense or liability for repairs made outside our plant without
our prior written consent. We are not responsible for damage to any associated equipment or
product and will not be liable for loss of time, profit, inconvenience, commercial loss or direct
consequential, special or incidental damages.
The provisions of this warranty do not apply to any product or parts which have been subject to
misuse, negligence or accident, or which have been repaired or altered outside of Cirus Controls’
factory in any way (in the judgment of Cirus Controls) so as to affect adversely its performance
or reliability. Neither does this warranty apply to normal maintenance service and parts or to
normal deterioration due to wear and exposure.
This warranty is expressly in lieu of other warranties, expressed or implied, in fact or by law,
including any implied warranty of merchantability of fitness for a particular purpose. The
remedies of repair or replacement as set forth are the only remedies under this warranty, Cirus
Controls’ disclaims any obligations or liability for loss of time, profit, inconvenience,
commercial loss or direct consequential, special or incidental damages. This warranty is in lieu
of any other obligation or liability of Cirus Controls’ of any nature whatsoever by reason of the
manufacture, sale, lease or use of such products and Cirus Controls neither assumes, not
authorizes anyone to assume for it, any other obligation or liability in connection with such
products.

Rev Z Page 6 11/28/2011
Copyright © 2011 by Cirus Controls, LLC. All Rights Reserved. No part of this material may be reproduced without the express
written permission of Cirus Controls LLC for each reproduction.
Revision Level of this Manual
At the time of release, this manual was accurate, but Cirus Controls reserves the right to make
revisions and alterations to this manual from time to time without notice.
Rev Letter Date Detail
V 1/26/10 Updated Frequency Table, Dwgs, AIP Mod
W 10/19/10 Load & Rate Calculator, Update Gate Control, AI Power Module
X 3/8/11 General Update
Y 6/1/11 Touch Screen added
Z 11/22/11 General update
Package Contents
A complete SpreadSmart Rx
TM
spreader control system contains the following items:
1) SpreadSmart Rx
TM
control unit
2) Color TFT touch screen display and operator interface - one touch day/nite viewing;
3) This manual
4) Power Cable, Speedometer/Remote Blast/Pass Cable
5) Hydraulic control cable (s)
6) Sensor Cable(s): defined as part of your system configuration;
If any of these items are missing, please contact your distributor immediately for replacement.
Functional Overview and Fundamental Operating Parameters
The SpreadSmart Rx
TM
spreader control is a simultaneous three media (granular, pre-wet and
anti-ice), ground speed oriented closed loop system. It is designed to accurately control multiple
application rates based on ground speed and sensor feedback. Installations may run the auger and
pre-wet pump in closed or open loop configuration. The system is also capable of controlling a
closed loop spinner and complete, 3 boom anti-ice systems simultaneously. The system is
designed to be “set it and forget it”, where the operator sets the application rates and the system
does the rest, starting and stopping dry, pre-wet and anti-ice applications as the vehicle starts and
stops, and varying the auger speed and pre-wet/anti-ice pump rates as the vehicle speeds up and
slows down to deliver consistent material per lane mile traveled.
Open Loop or Closed Loop Spreading
SpreadSmart Rx
TM
is designed to spread granular and /or liquid material with feedback
sensors: “Closed Loop operation” or without: “Open Loop operation.” Use of feedback sensors
allows SpreadSmart Rx
TM
to actually measure output and compare it to signal output to make
real-time adjustments for more consistent control throughout the range of operating conditions.
Selecting Closed Loop Operation: during Setup wizard for each device (auger, spinner,
pre-wet, and anti-ice) the choice of “Sensor Present – yes” results in closed loop operation for
the system must be selected. A choice must be made for each device. Sensor types for closed
loop systems vary. See Attachment A for a drawing to set pull up resistors if non-standard
sensors are used. Factory defaults are shown.
Selecting Open Loop Operation: during Setup wizard for each device (auger, spinner,
pre-wet, and anti-ice) the choice of “Sensor Present – no” results in open loop operation for the
system selected. A choice must be made for each device.
NOTE: we do not recommend that open loop operation be used as the normal operating mode for
pre-wet or anti-ice systems since that choice over-rides the pump protection that would prevent a
pump from running dry and damaging it.

Rev Z Page 7 11/28/2011
Copyright © 2011 by Cirus Controls, LLC. All Rights Reserved. No part of this material may be reproduced without the express
written permission of Cirus Controls LLC for each reproduction.
Distance or Area Spreading of Granular Mat’l. with Proportional Gate
When setting up the auger/conveyor section of your system, select the method that causes the
controller to manage the amount of material spread by:
a) Pounds (Kg) per Mile Driven = Distance Spreading. the controller manages the material
released by the auger/conveyor. The operator controls spinner speed and therefore the
“spreading pattern” occurs as the operator has set it. Material dispensed will correlate to
ground speed and distance traveled, but is not spread in a uniform thickness over the road at
any speed.
b) Pounds (Kg) per Lane Mile Driven = Area Spreading. In this format, the controller
manages the material released by the auger/conveyor as well as controlling the spinner speed
needed to disperse material uniformly within the lane width specified (0.1 lanes up to 3.0
lanes in 0.1 lane increments). Auger and spinner speeds are controlled and both correlate to
ground speed and distance traveled resulting in a uniform thickness of material spread
regardless of ground speed during spreading.
c) Proportional Control of hydraulically powered rear gate on conveyor is optional.
“Prescription Spreading” and/or “Operator Choice” Spreading
For users want to follow specific spreading methods, SpreadSmart offers a wide array of
definable spreading prescriptions to allow users to precisely manage their spreading parameters.
Detailed instructions are included in “managing materials.”
a) Invoice by assigning different spreading prescriptions for different jurisdictions. Define your
spreading prescriptions/categories so you’ll always know how much material was dropped on
federal roads, state roads, county roads, municipal roads and private roads. Be able to track
total material spread as well as each individual category of materials spread.
b) Unique calibration settings named for wet or dry material: Since wet material weighs more
than dry material, spread amounts per revolution of the auger will vary if material is wet or
dry. This problem is correctable if the calibration values take actual material weight into
account. Naming each granular material calibration to correlate to the conditions under
which granular material is stored improves the accuracy of data collected during spreading.
Temperature Response Spreading
SpreadSmart Rx ™ offers the user the ability to control all spreading parameters in direct
response to changes in measured road temperature. By correlating up to (5) spreading
prescriptions to each of (5) temperature ranges for which those prescriptions apply, the anti-icing
and de-icing performance is optimized. See System Setup and Temp Response™ Settings in the
Materials section for detailed setup instructions.
Load and Rate Calculator
SpreadSmart Rx ™ allows operator to calculate, properly load liquid and granular materials on
spreading vehicles and set the liquid and granular rate(s) to:
1) Fully consume the maximum amount of pre-wet salt brine capacity on a vehicle for a
given length of route.
2) Use Anti-icing tanks (on board or pulled with trailer) simultaneous with granular
and pre-wet systems and fully consume the loaded liquid.
3) Using the amount of salt brine available on a fully loaded truck, calculate the amount of
dry granular salt material to load onto that truck to deliver a particular total
amount of salt for the planned route
a. (Total salt pounds for route = liquid salt + granular salt)

Rev Z Page 8 11/28/2011
Copyright © 2011 by Cirus Controls, LLC. All Rights Reserved. No part of this material may be reproduced without the express
written permission of Cirus Controls LLC for each reproduction.
High Current Electric Pre-Wet Systems
The pre-wet channel on
SpreadSmart Rx
TM
is rated for a maximum current capacity of 6 amps. If you
are using an electric pre-wet pump that is rated for higher source current levels, contact Cirus Controls for
the Electric Pre-Wet Driver current management module.
Single or Two-Tier Anti-Ice System
The SpreadSmart Rx
TM
anti-ice system offers automatic integration of two tier dispensing of
anti-ice liquids. By choosing the boom and its nozzles with specific flow rates in mind, the
system offers a wide range of material delivery capability. The anti-ice system automatically
recognizes when the controller asks for output rates that require the output of the
Low Flow Tier 1 boom alone, the High Flow Tier 2 boom alone or the combination of Tiers 1 &
2 (note: Tier 1 is set up with the lowest output nozzles and tier 2 with the highest output nozzles).
Nozzles are chosen so as not to overlap output rates between booms. AI Power Module allows the
SS Rx to switch power to the high current lines for the boom valves.
Details for Single Tier Anti-Ice System
SpreadSmart Rx
TM
will also operate an anti-ice system with a single row of dispensing booms
(one, two or three for left, right and center dispensing). To configure the SpreadSmart Rx
TM
for
a system with a single tier, answer “yes” to single tier relay as described below and verify that the
boom valves are wired to the tier 1 output signals.
Boom Rating Maximum Flow Rate Range Max Gallons/Lane Mile @ 60mph
Tier 1- Low Volume 0 - 8 GPM 8 GPLM ( = 8 GPM)
Tier 2- High Volume 8 - 48 GPM 48 GPLM ( = 48GPM)
Tier 1 + Tier 2 (total) 48-56 GPM 56 GPLM ( = 56GPM)
Note: the gallons per lane mile output at which the system switches between tiers is dependent
upon the boom rating of each tier.
60
5.0 10.0
15.0
20.0
25.0
30.0
35.0
40.0
45.0
50.0
55.0
60.0
55
4.6 9.2
13.8
18.3
22.9
27.5
32.1
36.7
41.3
45.8
50.4
55.0
50
4.2 8.3
12.5
16.7
20.8
25.0
29.2
33.3
37.5
41.7
45.8
50.0
45
3.8 7.5
11.3
15.0
18.8
22.5
26.3
30.0
33.8
37.5
41.3
45.0
40
3.3 6.7
10.0
13.3
16.7
20.0
23.3
26.7
30.0
33.3
36.7
40.0
35
2.9 5.8
8.8
11.7
14.6
17.5
20.4
23.3
26.3
29.2
32.1
35.0
30
2.5 5.0
7.5
10.0
12.5
15.0
17.5
20.0
22.5
25.0
27.5
30.0
25
2.1 4.2
6.3
8.3
10.4
12.5
14.6
16.7
18.8
20.8
22.9
25.0
20
1.7 3.3
5.0
6.7
8.3
10.0
11.7
13.3
15.0
16.7
18.3
20.0
15
1.3 2.5
3.8
5.0
6.3
7.5
8.8
10.0
11.3
12.5
13.8
15.0
10
0.8 1.7
2.5
3.3
4.2
5.0
5.8
6.7
7.5
8.3
9.2
10.0
5
0.42
0.83
1.25
1.67
2.08
2.5
2.92
3.33
3.75
4.17
4.58
5.0
5
10
15
20
25
30
35
40
45
50
55
60
Table 1
Gallons per lane mile (GPL
-
M)
System capacity required (GPM) for single lane application at various rates and speeds.
Ground spee
d (mph)
Colored boxes
indicate which
boom tier is in
operation at any
particular
combination of
MPH and GPL-M
settings. Color and
Tier reference is
above. For
multiple lane
system capacities,
multiply the single
lane capacity by
the total number of
lanes required.

Rev Z Page 9 11/28/2011
Copyright © 2011 by Cirus Controls, LLC. All Rights Reserved. No part of this material may be reproduced without the express
written permission of Cirus Controls LLC for each reproduction.
Data Recording and Drive by Download™ for Data
SpreadSmart records storm and season totals automatically, but with the addition of Drive by
Download™ option, can record more information and automatically download it.
See Optional equipment section for more detail.
Operating Functions Matrix – SpreadSmart Rx
Desired Function Control Operating Mode Notes
Normal Operation
Normal operation with spreading data
collection and ground speed orientation;
Use Automatic Mode Normal operating mode; System
powers up with “pass on” as the
default setting;
“Pause” normal operation, Select “pass” to turn on,
select again to turn off,
Rates may be changed while in pass
mode.
Spread at Max. Rate temporarily Select “blast” Timed or “latched on” modes
Operation with operator settings and
ground speed triggering; data is not
recorded.
Use Manual Mode Operating mode – ground speed
triggered, must have valid ground
speed signal to operate.
Simulated automatic operation without
ground speed input (signal or motion of
truck). Spreading data is recorded.
Use No Speedo Mode Operating Mode – does not require
ground speed signal.
Unload Granular Material Use Unload Mode Operating Mode
Unload Anti-Ice Tank Use Unload Mode Operating Mode
Changing Materials Use Materials Screen Set Up step
System Setup and Testing
Technician test of system function with
feedback;
Use Test Mode Used for initial setup; Use as
operating mode with no ground
speed signal
Validate multi-tier
Anti-Ice system in a stationary truck;
Use No Speedo Mode Used for initial setup;
Special Operations Choices
Dispense Material while truck is stopped
– dispensing ceases automatically when
truck moves;
Use Unload Mode Special Operation
Automatic spreader operation without
truck wheels turning.
Use No Speedo Mode Operating mode, simulates truck
speed,
Re-Circulate A.I. Tank Use Unload Mode Stationary Truck,
SpreadSmart Rx
TM
TFT-Color Touch Screen Electronics (CPU)

Rev Z Page 10 11/28/2011
Copyright © 2011 by Cirus Controls, LLC. All Rights Reserved. No part of this material may be reproduced without the express
written permission of Cirus Controls LLC for each reproduction.
Basic Operation Controls:
1) Power: system is wired to the truck ignition and comes on with the truck.
2) Dry, Pre-Wet and Anti-Ice each has individual on/off buttons on screen.
3) Anti-Ice Booms have individual on/off controls for each of the three booms.
4) Auger, Spinner, Pre-wet and Anti-Ice up/down buttons control the application rate in
various run modes. The spinner doubles as a button used to navigate the menu functions.
5) Blast/Pass Buttons have the dual use for navigating menus and for Blast/Pass function.
a. Pass is enabled during every power cycle to prevent un-intended spreading;
6) Color screen displays settings, menu items and material outputs.
Startup Checklist – SpreadSmart Rx
TM
Step Task Completed by:
1
Installation - Mount the control unit in the truck cab and connect hydraulic
control cable, sensor cable, power and speedometer cable to the appropriate
valve coils and feedback sensors;
2
Power Verification – power up the unit and verify that the LCD displays
the Setup Wizard. Wait to perform the wizard until all hydraulics and
spreader hardware is installed in the truck. At this point, no other functions
are possible until all hydraulic systems are installed in the truck.
3
Set Up Wizard: follow the step-by-step controller instructions to: a)
enable the systems installed in the truck (auger, spinner, pre-wet, anti-ice,
sensors, etc); b) complete “pre-delivery trim” of the selected hydraulic
systems.
4
“Un-calibrated” automatic mode - Choose “yes” when asked to run un-
calibrated; Normally, trucks are delivered to customers without performing
drop test calibration. Note: if unable to get into “un-calibrated” automatic
mode, step 3 needs to be verified and/or repeated.
5
Calibrate Speedo - Verify speedometer signal input to the spreader and
choose system set up, trims/cal to calibrate the spreader speedometer to
match the truck speedometer.
6 Pre-Delivery Functional Test – Using No-Speedo mode, test and verify
ground speed operation, off rate indications, and alarms.
Post Delivery Steps:
A
Truck ID, Material Setup - Input truck ID, program up to (10 each)
Granular, Pre-Wet and Anti-Ice material names to establish operational
parameters for granular, pre-wet and anti-ice systems.
B
Drop Test Calibration of Auger and Spinner – Load truck with granular
material and perform drop test calibration (Closed or Open Loop) for each
Granular material customer defined.
C
Post Delivery Functional Test - Verify that the system functions properly
and is stable at the ground speed and material delivery rates the customer
desires;
Installation Steps
STEP 1 - Installation
Guard Against RF Interference
Even properly guarded sources of radio frequency (rf) noise can “leak” and interfere with in-cab
electronics. Take care when installing radios and radio antenna cable to keep at least 12” spacing

Rev Z Page 11 11/28/2011
Copyright © 2011 by Cirus Controls, LLC. All Rights Reserved. No part of this material may be reproduced without the express
written permission of Cirus Controls LLC for each reproduction.
between them and any cabling for the SpreadSmart Rx
TM
. Take particular care with
SpreadSmart Rx
TM
installations that have dash mounted LCD’s.
Installing the control unit
The control unit should be mounted in a position where the display is easily seen (often on the
dash board) and the operator can easily reach the controls of the unit. It should not, however, be
mounted in a position such that it interferes with the drivers line of sight of the roadway.
Connecting the cabling
Connections for Power (connect to ignition hot source), 5/12v switch for sensors, Aux for WiFi
bridge power, Hydraulics, Anti-Ice booms, Sensors and speedo/remote blast/ pass switches.
Connections: Drive by Data, Temp/GPS, LCD display, Bus, & PC.
STEP 2 – Power Verification
At this stage, the system can be powered up to verify electrical connections, but will not operate
the hydraulics until the Set up Wizard is complete.
Turn on the power to the truck. The unit should start up, lighting the display, displaying the
SpreadSmart Rx
TM
logo, and will display the Set-Up Wizard screen.
Multiple Uses of touch screen buttons (=key pad switches):
To keep the operator interface easy to use, the SpreadSmart Rx
TM
makes multiple uses
of the buttons on the touch screen. The label on the touch screen indicates the use of the button
during normal operation. Included throughout this manual are multiple uses of some of the
buttons for programming and set up of the system. In all cases, the buttons are referred to by the
name that appears next to them on the touch screen.

Rev Z Page 12 11/28/2011
Copyright © 2011 by Cirus Controls, LLC. All Rights Reserved. No part of this material may be reproduced without the express
written permission of Cirus Controls LLC for each reproduction.
STEP 3-Set up Wizard
The SpreadSmart Rx
TM
system must be configured and trimmed before it can be run in
automatic mode. Prior to initial operation, following the Set up Wizard will set the basic
operating parameters. The settings chosen here affect all aspects of system performance.
Set up Wizard is a step-by-step, menu driven sequence that allows you to configure the controller
to match the equipment set on the truck and to run automatic trimming sequences to align the
controller settings with the hydraulic system on the truck. After successful completion of the
wizard, the truck will be ready to run, but will not be calibrated until the granular drop test and
spinner calibrations have been complete. The Wizard will walk you through the following steps:
1) Password ______________ to enter setup wizard;
2) Select Units – standard or metric
3) PWM Frequency – match with coils on truck;
4) Systems Installed on Truck:
a. Auger, spinner, pre-wet, anti-ice;
5) Automatic Trimming:
a. For each system you enable (by answering yes) the set up wizard will give
you the option to run automatic trimming. These steps should not be
completed until all hydraulics are installed and ready to test.
b. Note: when trimming Anti-Ice system, turn all 3 boom valves on.
6) Press “pass” to complete, save configuration and re-start SpreadSmart Rx.
7) Choose to:
a. Complete Granular Calibration (completed by customer using his material).
b. Run System Un-Calibrated
To bypass the Wizard and leave the system un-configured, answer “no” to each of the four
questions. The SpreadSmart will display the “mode” screen, but none of the output signals will
function until turned on at a later time.
STEP 4: “Un-Calibrated” Automatic Mode
Choose “yes” when asked to run un-calibrated. Normally, trucks are delivered to customers
without performing granular drop test calibration. Note: if unable to get into “un-calibrated”
automatic mode, step 3 needs to be verified and/or repeated.
WARNING
Potential for injury due to unexpected
startup or movement of mechanical
equipment.
Unexpected startup or movement of
mechanical equipment may cause in-
jury to eyes and extremities.
During initial startup and te sting, the
spreader components may start with-
out warning. Stay clear of the auger,
spinner, and liquid nozzles until initial
power up and programming are com-
plete.

Rev Z Page 13 11/28/2011
Copyright © 2011 by Cirus Controls, LLC. All Rights Reserved. No part of this material may be reproduced without the express
written permission of Cirus Controls LLC for each reproduction.
Note: this screen will re-appear every time the system is powered up until the granular
calibration is satisfactorily completed, but only on controllers with the auger activated. It is not
necessary to calibrate to run the system unless you are seeking accurate spreading amounts.
This warning screen can be disabled by selecting the “perform calibration now” and pressing
“pass” for every question asked until you reach a screen offering you the option to disable this
warning by pressing “pass.” (Selecting “pass” in this manner causes you to reach the end of the
drop test without doing the test correctly). It is not recommended that you disable this warning.
STEP 5: Speedometer Calibration
The speedometer sensor emits a stream of pulses, which increase as the speed increases. The
SpreadSmart Rx
TM
uses this information to determine speed, using a “pulses per mile” setting.
This can be set either by driving the truck at 30 MPH (steady speed), by driving the truck over a
known mile (fixed distance) or by “matching the truck speedometer.” Fixed distance calibration
is more accurate, but “steady speed” or “matching” calibrations are faster.
1) Enter configuration menu by selecting the yellow “system setup” button. You will be asked
for a password, enter “_____” using the spinner controls to change the digits, and the blast/pass
controls to change cursor positions. Run the cursor past the end to enter setup mode.
2) Use spinner button, select “Trim/Cal”,
a) Use GPS as Speedo – answer yes if GPM antenna is source of speedo signal.
Default is “no” when you use the truck speedometer/transmission for speedo signal
b) Speedo Pulses / MI – hit pass to begin calibration of speedometer
“Steady Speed” Calibration
1) Select speedometer calibration;
2) Select steady speed calibration;
3) Bring the truck to 30 miles per hour and remain at that speed;
4) Press pass to start calibration;
5) Calibration will complete after several seconds;
The unit will take several samples of the speed sensor output, average, and determine the number
of pulses per mile. The whole process takes about 10 seconds.

Rev Z Page 14 11/28/2011
Copyright © 2011 by Cirus Controls, LLC. All Rights Reserved. No part of this material may be reproduced without the express
written permission of Cirus Controls LLC for each reproduction.
“Fixed Distance” Calibration
If using fixed distance calibration, the best method is to drive a mile using mile markers.
Although driving a mile in stop and go traffic would work, more accurate results are achieved
if driving a steady speed on a highway.
1) Select speedometer calibration.
2) Select fixed distance calibration.
3) Once the instructions are on the screen, drive to the first mile marker and press pass.
4) Drive to the next mile marker, and press pass again as the vehicle passes the marker.
5) The speedometer is now calibrated.
“Match Truck Speedometer” Calibration
1) Select speedometer calibration;
2) Select match Speedometer calibration;
3) Bring the Truck to a steady, maintainable speed (10-30 mph);
4) Using the “spinner” button, adjust the pulses per mile/km until the resulting mph/kph
matches the value displayed on the truck speedometer.
Press “pass” to accept setting and return to Trim/Cal menu.
STEP 6- Pre-Delivery Functional Test with Diagnostics
In No-Speedo mode or Test mode, operate and verify ground speed operation (auto or manual),
warnings, and hydraulic functionality. Use Diagnostics from the Mode screen to trouble shoot
problems.
Using stored calibration files to configure multiple trucks
Once the set up wizard has been completed, the stored calibration file can be downloaded
to your laptop computer and subsequently uploaded to a new truck before running the set
up wizard. See “Other downloads” for instructions. Once upload is complete, power
cycle the controller and the set up wizard will passed. Drop test calibration must still be
completed.

Rev Z Page 15 11/28/2011
Copyright © 2011 by Cirus Controls, LLC. All Rights Reserved. No part of this material may be reproduced without the express
written permission of Cirus Controls LLC for each reproduction.
Post Delivery Steps
STEP A - Material Setup & Calibration
Material Setup
Configure up to (10) Granular, (10) Pre-Wet and (10) Anti-Ice material names to establish
operational parameters operation. See Managing Materials section for full instructions.
1) Enter configuration menu by selecting the yellow “system setup” button. You will be asked
for a password, enter “_____” using the spinner controls to change the digits, and the blast/pass
controls to change cursor positions. Run cursor past the end of the password to enter setup mode.
2) Using the spinner button, select “Materials” to begin.
Granular Drop Test - Open or Closed Loop
With the auger, spinner, and pre-wet configured and trim values present, the SpreadSmart Rx
TM
will
operate in automatic. Until doing a material drop test, the unit will use default values and be less accurate.
Closed Loop Drop Test (auger/conveyor sensor present):
For accurate material delivery, a drop test must be performed for each named type of granular material.
Conveyor Spreaders: accuracy is a function of the gate height settings on the truck. If multiple gate
settings are used in normal operation, a material name and drop test must be run for each gate setting (Salt
2, Salt 3, Salt 4 etc). Changes in the gate setting without changing the calibration will result in less
accurate dispensation of granular material.
1) Enter configuration menu by simultaneously hold the auger and pre-wet button down to enter the
“configuration screen.” You will be asked for a password, enter it using the spinner controls to change the
digits, and the blast/pass controls to change cursor. Move cursor past the end to enter setup mode.
2) Using the spinner button, select “Materials,” and select material type.
a) Pick the material type you wish to calibrate (i.e. salt).
b) Scroll down to pulses per pound.
WARNING
Potential for injury due to unexpected
operation of auger.
Entanglement in the auger will cause
severe injury to extremities, with pos-
sible loss of extremities.
During initial startup and testing, the
auger may start without warning. Stay
clear of the auger during all startup,
programming, and operation proce-
dures.
Do not attempt to clear a jammed au-
ger with the hydraulic or control sys-
tem active.

Rev Z Page 16 11/28/2011
Copyright © 2011 by Cirus Controls, LLC. All Rights Reserved. No part of this material may be reproduced without the express
written permission of Cirus Controls LLC for each reproduction.
c) Press pass to select between calibration modes:
i) Weigh Truck (requires truck scales);
ii) Weigh Material Dropped (requires 75 lb. scale and bucket for weighing);
d) Read the instructions and page through them using the pass button.
a. Weigh truck – run the auger at 50% and unload at least a yard of material;
b. Weigh Material – run the auger at 50% and unload 300-500 lbs of material.
f) Enter weight of material dropped.
g) Accept the new calibration value in pulses/lb (note that max lbs/min is changed by the system
as a result of the new value in pulses/lb).
Drop Test is now complete for the material selected. Note that for maximum accuracy and
performance, a drop test must be performed for each type of granular material (salt, sand,
combinations, other material, etc.).
Open Loop Drop Test (no sensor on auger/conveyor)
A drop test must be performed for each named type of granular material (salt, sand, mixture, etc).
Drop tests performed on open loop systems will improve accuracy, but cannot achieve the accuracy of a
closed loop system. In addition, accuracy of open loop system is dependent on the accuracy of the
hydraulic trimming for the auger. Best trimming requires a hand held tachometer to properly identify the
max rpm of the auger (and the max trim of the auger hydraulic channel).
Conveyor Spreaders: accuracy is a function of the gate height settings on the truck. If multiple gate
settings are used in normal operation, a material name and drop test must be run for each gate setting (Salt
2, Salt 3, Salt 4 etc). Changes in the gate setting without changing the calibration will result in less
accurate dispensation of granular material.
1
)
Enter configuration menu by selecting the yellow “system setup” button
.
You will be asked for a
password, enter “_____” using the spinner controls to change the digits, and the blast/pass controls to
change cursor positions. Run the cursor past the end of the password to enter setup mode.
2) Using the spinner button, select “Materials,” and select material type.
a) Pick the material type you wish to calibrate (i.e. salt).
b) Scroll down to maximum LB/min.
c) Press pass to select between calibration modes:
i) Weigh Truck (requires truck scales);
ii) Weigh Material Dropped (requires 75 lb. scale and bucket for weighing);
d) Read the instructions and page through them using the pass button.
a. Weigh truck – run the auger at 50% and unload at least a yard of material;
b. Weigh Material – run the auger at 50% and unload 300-500 lbs of material.
e) Enter weight of material dropped.
f) Accept the new calibration value in pulses/lb (note that max lbs/min is changed by the system
as a result of the new value in pulses/lb).

Rev Z Page 17 11/28/2011
Copyright © 2011 by Cirus Controls, LLC. All Rights Reserved. No part of this material may be reproduced without the express
written permission of Cirus Controls LLC for each reproduction.
g) Drop Test is now complete for the material selected.
Note that for maximum accuracy and performance, a drop test must be performed for each type of
granular material (salt, sand, combinations, other material, etc.).
Enter configuration menu by selecting the yellow “system setup” button.
STEP B - Spinner Calibration with Granular Material
The controller can be operated in linear spreading mode (pounds per mile) or area spreading
mode (pounds per lane mile). To accurately spread material over an area, spinner speed must be
calibrated to spread material in a pattern of a particular width. There are four trim settings for the
spinner that cannot be set automatically: a one and three lane wide pattern for “normal”
dispensing rates as well as one and three lane wide settings for “blast” dispensing rates. To trim
these settings accurately, the unit must be filled with material to set spread widths.
Detailed instructions for zero velocity spinner are listed in “detailed spinner trims.”
1) Enter configuration menu by selecting the yellow “system setup” button. You will be asked
for a password, enter “_____” using the spinner controls to change the digits, and the blast/pass
controls to change cursor positions. Run cursor past the end of the password to enter setup mode.
Set the One Lane Spinner speed:
2) Select trim/cal. Select spinner trim.
e) Select the “one lane wide” trim setting and follow the on screen instructions.
f) Increase the auger setting until a small amount of granular material is being augured.
g) Increase the spinner setting until a 1 lane wide (12 feet measured) pattern is thrown.
h) Press pass to accept the one lane speed setting.
Three lane Spinner: Follow the same procedure for setting 3 lanes wide (36 foot) pattern.
Set the blast spinner settings (allows “blast setting on the auger to be spread uniformly in a
width between 1 lane and 3 lanes).
1) Use the spinner key to go down to the “one lane blast” trim setting.
2) Set the auger to dispense the amount of material dispensed while in blast mode.
3) Increase spinner speed to create a “one lane wide” pattern.
4) Press “pass” to accept the “one lane blast” setting.
5) Follow the same procedure for three-lane blast trim calibration.
6) Once the one and three lane trim for both normal and blast amounts have been set, the
spinner is calibrated.
WARNING
Potential for injury due to unexpected
operation of spinner.
Granular material thrown off the spin-
ner will cause severe eye injury, with
possible permanent loss of vision.
Contact with a moving spinner will
cause injury to extremities and other
body parts.
During initial startup and te sting, the
spinner may start without warning.
Stay clear of the spinner during all
startup, programming, and operation
procedure s.
Do not attempt to clear a jammed spin-
ner with the hydraulic or control sys-
tem active.

Rev Z Page 18 11/28/2011
Copyright © 2011 by Cirus Controls, LLC. All Rights Reserved. No part of this material may be reproduced without the express
written permission of Cirus Controls LLC for each reproduction.
STEP C - Post Delivery Functional Test
In Non-Speedo mode verify system functions and is stable at the ground speed and delivery rates
the customer expects.
For trouble shooting ideas, see the trouble shooting section of this manual or the diagnostics
screen in the SpreadSmart Rx mode screen.
Note: it is recommended that you save all settings after completion of all system setup and
calibration to a PC for safekeeping. In the event of loss of this setting information, it can be
uploaded from the stored file in a matter of minutes. Storing this information is described in
the section of the manual “Other Downloads.
Managing Materials – Granular, Pre-Wet and Anti-Ice
For maximum flexibility of operation, SpreadSmart Rx
TM
allows you to define operating
programs by using the “Name” to designate either a different material (salt/sand; Brine/KCl, etc);
or to designate a different material distribution rate (Salt 500, Salt 1000, etc); or to use several of
each within the 10 choices/material the system offers. The word “material” is used for
consistency even though you are allowed to name either a “unique material” (salt or sand) or a
unique set of distribution conditions for the same actual material (salt, salt 500, salt abc, etc.).
To enter the materials screen:
1) Enter configuration menu by selecting the yellow “system setup” button. You will be asked
for a password, enter “_____” using the spinner controls to change the digits, and the
blast/pass controls to change cursor positions. Run the cursor past the end of the password to
enter “Configuration screen”. Changing settings without authorization can result in
performance variations; password should only be given to authorized personnel.
2) Move the arrow to “materials” and select “pass” to enter the materials screen.
Choose the material you wish to define your settings for (granular, pre-wet or anti-ice) and
make the following four settings for each individual “material” you wish to “name.”
1) Name: Up to 10 granular programs, 10 pre-wet programs and 10 anti-ice programs) can be
defined (each named with up to 8 characters). In normal operation, the operator selects his
material from those defined on this list. The “name” is used to identify the ten different
material types or distribution settings. Ex: “Salt” is often used generically and doesn’t have
a pre-programmed distribution rate. The operator is then free to adjust his distribution rate
using the Auger button. “Salt 500” is a pre-programmed setting that could deliver 500 lbs /
lane mile of salt. In that case, the operator cannot change the rate without changing material
type. This also applies for pre-wet and anti-ice.
2) Min and Max Rate settings for each material: These are the lowest and highest settings the
operator can select while in automatic mode, in pounds per lane mile. The system allows the
minimum to be set at 0 and the max at 9999. In typical applications, minimum is usually set
no lower than 100 lbs and maximum not above 3,000 lbs.
To “pre-program” a specific rate, set the min and max at the same value (eg. 500lbs/lane
mile), thereby “locking” the rate only at that value for that material.
3) Blast mode setting: is the number of pounds per lane mile that are dispensed when the truck
is in blast mode (automatic mode only).

Rev Z Page 19 11/28/2011
Copyright © 2011 by Cirus Controls, LLC. All Rights Reserved. No part of this material may be reproduced without the express
written permission of Cirus Controls LLC for each reproduction.
4) Small and large rate change increment settings: are the amount that the dispensed rates are
changed when the rate button is pressed, and how much the rates are changed when the rate
button is pressed and held.
Choosing a material name and recording data:
SpreadSmart Rx
TM
records all spreading output for each uniquely named material. The
Spreading Performance Report uses this information to produce combined material reports and
individual reports for each named material. To ensure integrity in the combined materials reports,
material names are limited to 8 characters and must follow this convention:
Material Name must be consistent: all materials named Salt with a space following
the “t” will add correctly together in the following example.
a. Salt
b. Salt 500
c. Salt 1000
Inconsistent Material Names will not add together correctly
d. Salt500
e. Salt 1000
f. Salt Special
Note: This naming convention affects the combined material reports and if not followed
consistently, will make the summary reports inaccurate.
Changing “Materials” program during normal operation
Once your materials set up is complete, an operator can select any programmed choice by
selecting “materials change” from the main “mode” screen before the system drops into
automatic operation mode. From there, the operator can choose any of the programmed material
types designated in the prior section.
Temp Response
TM
Prescription Set Up – for each material type
For any material type, you can also create up to four Temp Response™ prescriptions to
automatically change spreading rates as a function of road temperature. The user, for their local
conditions, determines the actual temperature/spreading rate relationship. Temp Response™
prescriptions can be run for one material (salt) or for combinations (salt and pre-wet), but each is
configured individually. English or Metric units are shown based on the system setup choice.
To set a temperature controlled, granular spreading prescription, enter configuration menu
by selecting the yellow “system setup” button. Enter your password using the spinner controls to
change the digits, and the blast/pass controls to change cursor positions. Run the cursor past the
end of the password to enter setup mode.
Scroll down to Prescription, Use “Anti-Ice” paddle to select Prescription RX1- RX4. Incomplete
prescriptions are listed as “undefined.” Up to four prescriptions are can be created for each
media type (Granular = 4; Pre-Wet =4; Anti-Ice = 4).

Rev Z Page 20 11/28/2011
Copyright © 2011 by Cirus Controls, LLC. All Rights Reserved. No part of this material may be reproduced without the express
written permission of Cirus Controls LLC for each reproduction.
Change the Prescription from off to Rx1 and hit pass to enter values for prescription RX1:
In this example, the prescription has been set as follows:
Temperature Range (F) Salt Spread Rate
Above 35 degrees 200 (lbs/mile)
34-32 degrees 300 (lbs/mile)
31-29 degrees 350 (lbs/mile)
28-25 degrees 400 (lbs/mile)
Below 25 degrees 500 (lbs/mile)
(Note: these rates are for illustration only and are not process recommendations).
Select “blast” and return to the Granular material screen to confirm prescription is set:
Your prescription for your granular material named “salt” is now set. To set another granular
material, choose name #2-10, select Prescription RX2-4 and repeat the process.
When operating the SpreadSmart Rx or RDS, the letters Rx is added to the display to show that
Temp Response ™ is controlling the granular and pre-wet spreading rate.
For Pre-Wet or Anti-Ice prescription setting, choose one of those “materials” and begin the
naming and prescription setting process as above. Because the distribution rate varies with
material, a prescription must be set individually for each.
Table of contents
Popular Spreader manuals by other brands
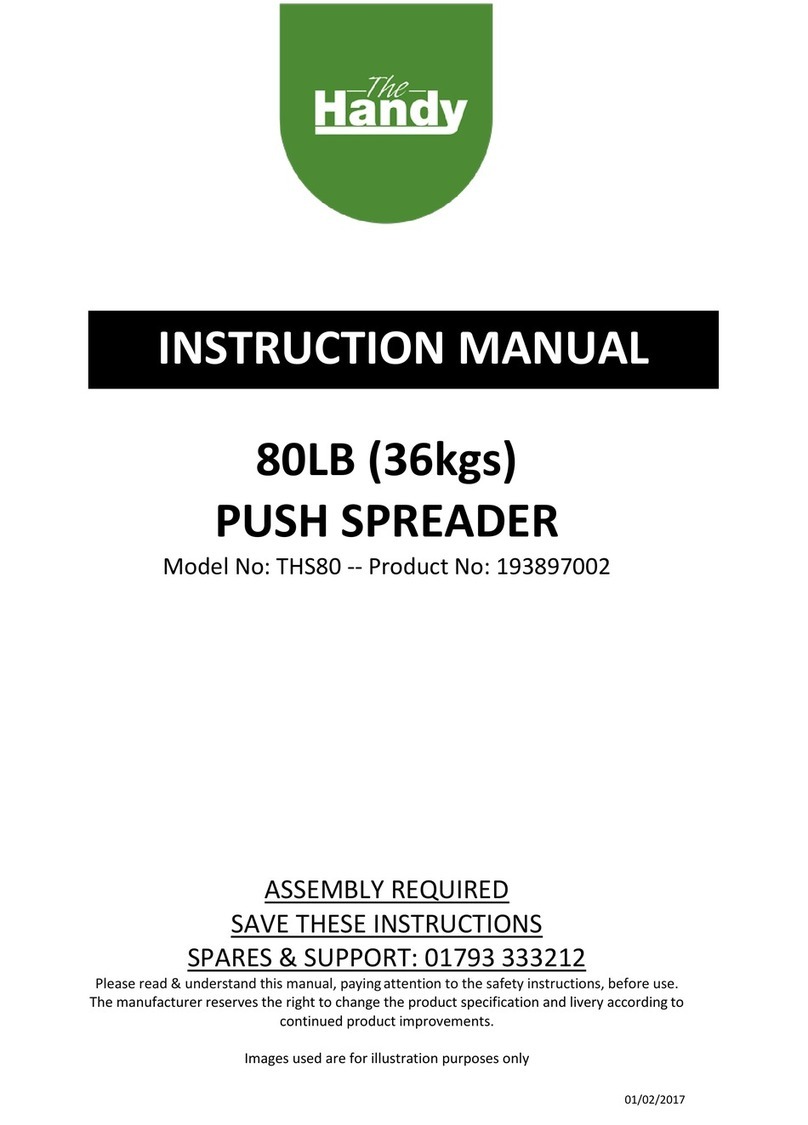
The Handy
The Handy THS80 instruction manual

Craftsman
Craftsman 486.24595 owner's manual

Western
Western Striker 98805 installation instructions

Farmhand
Farmhand 70LB Assembly and operating instruction
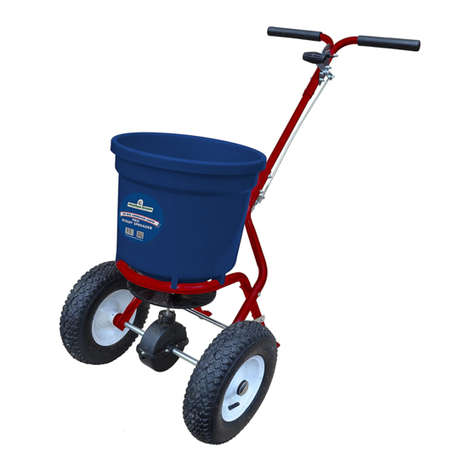
Jonathan Green
Jonathan Green DELUXE ROTARY SPREADER instruction manual
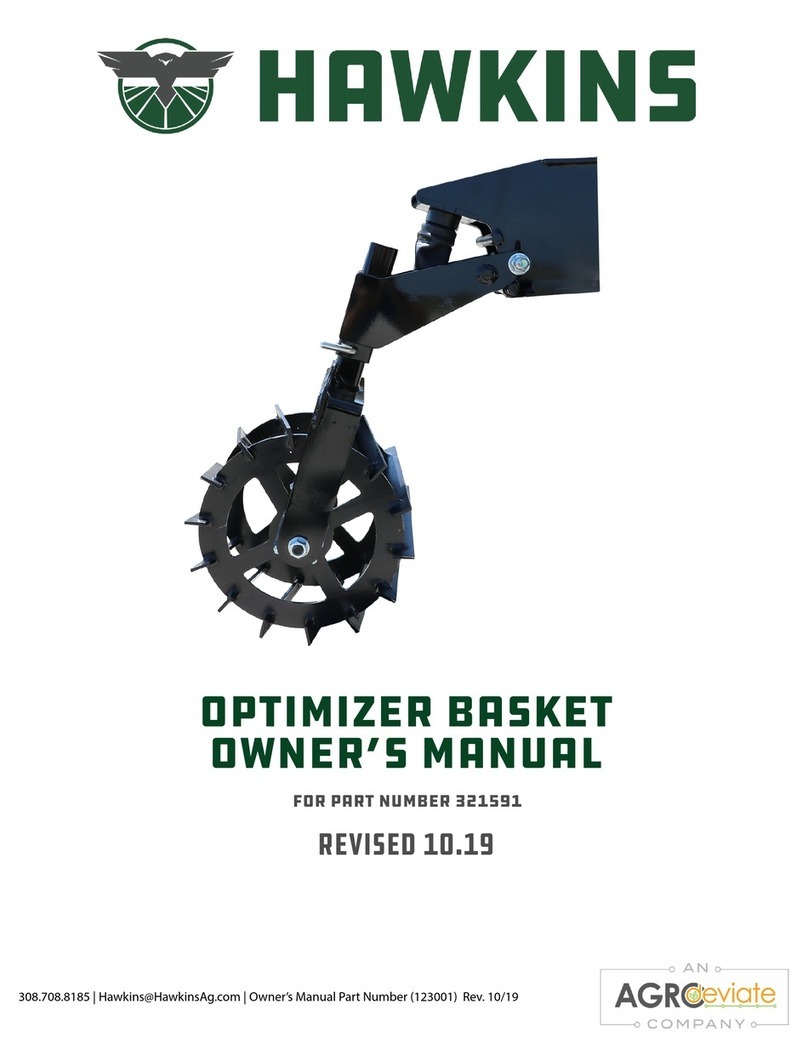
Hawkins
Hawkins 321591 owner's manual