Comparc ALPHA TIG 252 - DP User manual

OWNER´S MANUAL
TIGPROCESS(GTAW)
OUTPUTTYPE:AC/DC
PROCESSES
STICKPROCESS(SMAW)
DESCRIPTION
PM1328 REV. 0
E:21-01-2021
AC/DC ARC WELDING POWER SOURCE
ALPHATIG252-DP
GIVETHISMANUALTOTHEOPERATOR
VISIT OUR WEBSITE AT: www.comparcwelders.ca
303-192
T M
OWNER´S MANUAL

TABLE OF CONTENTS
SECTION 1 - SAFETY PRECAUTIONS - READ BEFORE USING ............................................i
SECTION 1 SAFETY SIGNAL WORDS.................................................................................1
SECTION 2. ESPECIFICATIONS..............................................................................................1
2 - 1. VOLT-AMPERECURVES. .................................................................................. 1
2 - 2. DUTY CYCLE. .............................................................................................................................. 2
SECTION 3 -- INSTALLATION .................................................................................................2
3 - 1. SELECTING A LOCATION AND MOVING WELDING POWER SOURCE................................. 2
3 - 2. SELECTINGANDPREPARINGWELDOUTPUTCABLES............................................................... 3
3 - 3. LOWERFRONTPANEL.................................................................................................................. 3
3 - 4. CONNECTINGOUTPUTTERMINALS .............................................................................................. 4
3 - 5. RC14INFORMATIÓN&CONNECTIONS ......................................................................................... 4
3 - 6. REMOTE14CONNECTIONS. ......................................................................................................... 5
3 - 7. 120VOLTSACDUPLEXRECEPTACLE. ........................................................................................ 5
3 - 8. INPUTVOLTAGECONNECTIONS................................................................................................... 5
3 - 9. SHIELDINGGASCONNECTION ..................................................................................................... 6
SECTION 4 -- FUNCTION OF CONTROLS .............................................................................7
4 - 1. CONTROLSOFWELDINGPOWERSOURCE ................................................................................ 7
4 - 1a. PULSERCONTROLS....................................................................................................................10
4 - 2. WHAT IS PULSING? ..................................................................................................................12
SECTION 5 -- MAINTENANCE & TROUBLESHOOTING ..................................................13
5 - 1. ROUTINEMAINTENANCE.............................................................................................................13
5 - 2. TROUBLESHOOTING .................................................................................................................14
5 - 3. OVERLOADPROTECTION. .......................................................................................................15
5 - 4. OVERHEATING...........................................................................................................................15
5 - 5. ADJUSTING SPARK GAPS. ......................................................................................................15
SECTION 6 -- ELECTRICAL DIAGRAM .................................................................................16
SECTION 7 -- PARTS LIST ....................................................................................................17
SECTION 8 -- TUNGSTEN ELECTRODE .............................................................................21
WARRANTY

i
SECTION 1 - SAFETY PRECAUTIONS -READ BEFORE USING
WARNING
- DANGER! - Indicates a hazardous situation which, if not avoided, will result in death or serious injury. The possible hazards
are shown in the adjoining symbols or explained in the text
- Indicates a hazardous situation which, if not avoided, could result in death or serious injury. The possible hazards are shown
in the adjoining symbols or explained in the text.
- The symbols shown below are used throughout this manual to call attention to and identify possible hazards. When you
see the symbol, watch out, and follow the related instructions to avoid the hazard. The safety information given below is
only a summary of the more complete safety information found in the Safety Standards.
- Only qualified persons should install, operate, maintain, and
repair this unit.
- During operation, keep everybody, especially children, away.
ARC WELDING can be hazardous.
ELECTRIC SHOCK can kill.
Touching live electrical parts can cause fatal shocks
or severe burns. The electrode and work circuit is
electrically live whenever the output is on. The input
power circuit and machine internal circuits are also
live when power is on. In semiautomatic or automatic
wire welding, the wire, wire reel, drive roll housing,
and all metal parts touching the welding wire are electrically live.
Incorrectly installed or improperly grounded equiment is a hazard.
1.- Do not touch live electrical parts.
2.- Wear dry, hole-free insulating gloves and body protection.
3.- Insulate yourself from work and ground using dry insulating
mats or covers.
4.- Disconnect input power or stop engine before installing or
servicing this equipment.
5.- Properly install and ground this equipment according to this
Owner's Manual and national, state, and local codes.
6.- Turn off all equipment when not in use.
7.- Do not use worn, damaged, undersized, or poorly spliced cables.
8.- Do not wrap cables around your body.
9.- Ground the workpiece to a good electrical (earth) ground.
10.- Do not touch electrode while in contact with the work (ground)
circuit.
11.- Use only well-maintained equipment. Repair or replace damaged
parts at once.
12.- Wear a safety harness to prevent falling if working above floor
level.
13.- Keep all panels and cover securely in place.
ARC RAYS can burn eyes and skin;
NOISE can damage hearing.
Arc rays from the welding process produce intense
heat and strong ultraviolet rays that can burn eyes and
skin. Noise from some processes can damage hearing.
1.- Wear a welding helmet fitted with a proper shade
of filter (see ANSIZ49.1 listed in Safety Standards) to protect
FUMES AND GASES can be hazardous
to your health.
Welding produces fumes and gases. Breathing these
fumes and gases can be hazardous to your health.
1.- Keep your head out of the fumes. Do not breath the fumes.
2.- If inside, ventilate the area and / or use forced ventilation at the arc
to remove welding fumes and gases.
3.- If ventilation is poor, use an approved air-supplied respirator.
4.- Read the Material Safety Data Sheets (MSDSs) and the
manufacturer´s instruction for metal, consumables, coatings, and
cleaners.
5.- Work in a confined space only if it is well ventilated, or while wearing
an air-supplied respirator. Shielding gases used for welding can
displace air causing injury or death. Be sure the breathing air is safe.
6.- Do not weld in locations near degreasing, cleaning, or spraying
operations. The heat and rays of the arc can react with vapors to
form highly toxic and irritating gases.
7.- Do not weld on coated metals, such as galvanized, lead, or cadmium
plated steel, unless the coating is removed from the weld area, the
area is well ventilated, and if necessary, while wearing an air-
supplied respirator. The coatings and any metals containing these
elements can give off toxic fumes if welded.
FLYING SPARK AND HOT METAL can
cause injury
Chipping and grinding cause flying metal . As welds
cool, they can throw off slag.
1.- Wear approved face shield or safety goggles. Side shields
recommended.
2.- Wear proper body protection to protect skin.
your face and eyes when welding or watching.
2.- Wear approved safety glasses. Side shields recommended.
3.- Use protective screens or barriers to protect others from flash and
glade; warn others not to watch the arc.
4.- Wear protective clothing made from durable, flame- resistant mate
rial (wool and leather) and foot protection.
5.- Use approved ear plugs or ear muffs if noise level is high.

ii
CYLINDERS can explode if damaged.
Shieldinggas cylinders contain gas under highpressure.
If damaged, a cylinder can explode. Since gas cylinders
are normally part of the welding process, be sure to
treat them carefully.
1.- Protect compressed gas cylinders from excessive heat, mechanical
shocks, and arcs.
2.- Install and secure cylinders in an upright position by chaining them
to a stationary support or equipment cylinder rack to prevent falling
or tipping.
3.- Keep cylinders away from any welding or other electrical circuits.
4.- Never allow a welding electrode to touch any cylinder.
5.- Use only correct shielding gas cylinders, regulators, hoses, and
fittings designed for the specific application; maintain them and
associated parts in good condition.
6.- Turn face away from valve outlet when opening cylinder valve.
7.- Keep protective cap in place over valve except when cylinder is in
use or connected for use.
8.- Read and follow instructions on compressed gas cylinders, associated
equipment, and CGA publication P-1 listed in Safety Standards.
ENGINES can be hazardous.
WARNING
ENGINE EXHAUST GASES can kill.
Engines produce harmful exhaust gases.
1.- Use equipment outside in open, well-ventilated
areas.
2.- If used in a closed area, vent engine exhaust outside and away from
any building air intakes.
ENGINE FUEL can cause fire or
explosion.
Engine fuel is highly flammable.
1.- Stop engine before checking or adding fuel.
2.- Do not add fuel while smoking or if unit is near any sparks or open
flames.
3.- Allow engine to cool before fueling. If possible, check and add fuel
to cold engine before beginning job.
4.- Do not overfill tank - allow room for fuel to expand.
5.- Do not spill fuel. If fuel is spilled, clean up before starting engine.
MOVING PARTS can cause injury.
Moving parts, such as fans, rotors, and belts can cut
fingers and hands and catch loose clothing.
1.- Keep all doors, panels, covers, and guards closed
and securely in place.
2.- Stop engine before installing or connecting unit.
3.- Have only qualified people remove guards or covers for maintenance
and troubleshooting as necessary.
4.- To prevent accidental stating during servicing, disconnect negative
(-) battery cable from battery.
5.- Keep hands, hair, loose clothing, and tools away from moving parts.
6.- Reinstall panels or guards and close doors when servicing is finished
and before starting engine.
SPARKS can cause BATTERY GASES
TO EXPLODE; BATTERY ACID can
burn eyes and skin.
Batteries contain acid and generate explosive gases.
1.- Always wear a face shield when working on a
battery.
2.- Stop engine before disconnecting or connecting battery cables.
3.- Do not allow tools to cause sparks when working on a battery.
4.- Do not use welder to charge batteries or jump start vehicles.
5.- Observe correct polarity (+ and -) on batteries.
WELDING can cause fire orexplosion.
Sparks and spatter fly off from the welding arc. The
flying sparks and hot metal, weld spatter, hot workpiece,
and hot equipment can cause fires and burns. Acciden-
tal contact of electrode or welding wire to metal objects
can cause sparks, overheating, or fire.
1.- Protect yourself and others from flying sparks and hot metal.
2.- Do not weld where flying sparks can strike flammable material.
3.- Remove all flammables within 35ft (10.7 m) of the welding arc. If
this is not possible, tightly cover them with approved covers.
4.- Be alert that welding sparks and hot materials from welding can
easily go through small cracks and openings to adjacent areas.
5.- Watch for fire, and keep a fire extinguisher nearby.
6.- Be aware that welding on a ceiling, floor, bulkhead, or partition can
cause fire on the hidden side.
7.- Do not weld on closed containers surch as tanks or drums.
8.- Connect work cable to the work as close to the welding areas as
practical to prevent welding current from traveling long, possibly
unknown paths and causing electric shock and fire hazards.
9.- Do not use welder to thaw frozen pipes.
10.- Remove stick electrode from holder or cut off welding wire at
contact tip when not in use.
11.- Wear oil-free protective garments such as leather gloves, heavy
shirt, cuffless trousers, high shoes, and a cap.

STEAM AND PRESSURIZED HOT
COOLANT can burn face, eyes, and
skin.
The coolant in the radiator can be very hot and under
pressure.
1.- Do not remove radiator cap when engine is hot. Allow engine to cool.
2.- Wear gloves and put a rag over cap area when removing cap.
3.- Allow pressure to escape before completely removing cap.
- Additional Symbols For Installation, Operation, And Maintenance
NOISE can damage hearing.
Noise from some processes or equipment can damage hearing.
- Wear approved ear protection if noise level is high.
FALLING EQUIPMENT can injure
-Use lifting eye to lift unit and properly installed
accessories only, NOT gas cylinders. Do not
exceed maximum lift eye weight rating (see
Specifications).
-Use equipment of adequate capacity to lift and support unit.
-If using lift forks to move unit, be sure forks arelong enough to extend
beyond opposite side of unit.
-Keep equipment (cables and cords) away from moving vehicles
when working from an aerial location.
OVERUSE can cause OVERHEATING
-Allow cooling period; follow rated duty cycle.
-Reduce current or reduce duty cycle before starting to
weldagain.
-Do not block or filter airflow to unit.
STATIC (ESD) can damage PC boards.
-Put on grounded wrist strap BEFORE handling boards or parts.
-Use proper static-proof bags and boxes to store, move, or ship PC boards.
ARC WELDING can cause interference.
-Electromagnetic energy can interfere with sensitive
electronic equipment such as microprocessors, computers,
and computer-driven equipment such as robots.
-Be sure all equipment in the welding area is
electromagnetically compatible.
- To reduce possible interference, keep weld cables as short as possible, close
together, and down low, such as on the floor.
-Locate welding operation 100 meters from anysensitiveelectronic equipment.
-Besurethisweldingmachineisinstalledandgroundedaccordingtothismanual.
-If interference still occurs, the user must take extra measures such as moving
thewelding machine, using shielded cables, usingline filters, or shieldingthe work
area.
-Read and follow all labels and the Owner’s Manual carefully before installing, operating, or servicing unit.
Read the safety information at the beginning of the manual and in each section.
- Definitions
iii


1
SECTION 2. ESPECIFICATIONS
SECTION 1 SAFETY SIGNAL WORDS
IMPORTANT: Statements identify special instructionsnecessaryforthemostefficientoperation
ofthisequipment.
WARNING WARNINGstatementsidentifyproceduresorpracticeswhichmustbefollowedto
avoid serious personal injury or loss of life.
CAUTION CAUTIONstatementsidentifyproceduresorpracticeswhichmustbefollowedto
avoid minor personal injury or damage to this equipment.
Thefollowingsafetyalertsymbolandsignalwordsareusedthroughoutthismanualtocallattention
toandidentifydifferentlevelsofhazardandspecialinstructions.
Imagesshown in this manual mustbe takenas a referenceand the real unit may
changeslightly.
CAUTION
RATED
WELD
OUTPUT
AMPERAGE
RANGE
MAX
OPEN
CIRCUIT
VOLTAGE
INPUTAMPERESATACBALANCED
RATEDOUTPUT,60Hz,
SINGLEPHASE
KVA KW
WEIGHT
SHIP
Kg(Lb)
TYPEOF
OUTPUT
230 Vac 460 Vac
250A at 30V 5-310 A 95.6A80V
60%
DUTY CYCLE
186
(193.5)
CC
AC/DC
47.8A 22 11.8
OVERALL
DIMENSIONS
mm (in)
DEPTH
1232 (48 ½)
WIDTH
559 (22 ½)
HEIGHT
838 (33)
*
INCLUDES WHEELS AND LIFTING EYE.
2-1 VOLT-AMPERE CURVES.
Figure 2-1 Volt-Ampere Curves
Thevolt-amperecurvesshowtheminimumandmaximumvoltageandamperageoutputcapabilitiesoftheweldingpower
source.Curvesofothersettingsfallbetweencurvesshown.
RMS DC VOLTS
80
0
70
60
50
40
30
20
10
80
50
200
250
300
350
400
100
150
450
5
0
0
A
B
80
0
70
60
50
40
30
20
10
80
50
200
250
300
350
400
100
150
450
5
0
0
A
B
AC Mode. DC Mode.
A .- Arc control at MIN.
B .- Arc control at MAX.
AC VOLTS
AC AMPERES RMS DC AMPERES
575 Vac
38.2A

2
Figure 2-2 WeldingPowerSourceDutyCycleChart.
WELDING LONGER THAN RATED DUTY CYCLE can damage unit or gun
and void warranty.Do not weld at rated load longer than shown below.
Definition:
DutyCycleispercentageof10minutesthat
unit or electrode holder can weld at rated
loadwithoutoverheating.
0
10
MINUTES
60 % Duty Cycle
6 Minutes Welding 4 Minutes Resting
WARNING
2-2 DUTY CYCLE.
Rated Output
Figure 3-2 LocationAnd MovementOfWelding PowerSource.
2
Rear
Left
Front Right
Top 1
Figure 3-1 TypicalProcessConnections.
3.1 SELECTING A LOCATION AND MOVING WELDING POWER SOURCE.
SECTION 3 INSTALLATION
CAUTION SEE SAFETY SIGNAL AT THE BEGINING THIS MANUAL
1.- 18 in (480 mm). Open Space On
Right Side And Left Of Unit For
Good Airflow.
2.- Lifting Eye. Useonly tolift unit.
SMAW
Work
GTAW
Work
Welding Power
Source With
HFOff
Welding Power
Source With
HFOn

3
3-2 SELECTING AND PREPARING WELD OUTPUT CABLES.
1.-WeldOutputCable.Determinetotalcable
length in weld circuit and maximum welding
amperes.UseTable3-1toselectpropercable
size.Useshortestcablespossible. Donotuse
damagedcables.
2.-TerminalLugUselugsofproperamperage
capacity andhole sizefor connectingto work
clamp, orelectrodeholder.
3.- Insulated Electrode holder.
4.- GTAW torch. Install according to
manufacturer'sinstructions.
5.- Work Clamp. Install onto work cable.
Figure 3-3 Selecting AndPreparingWeldOutputCables
3/4" (19
mm)
Tools
Needed
1
3 m (10 ft) }
3 m (10 ft)
2
34
5
For Example ,
Total Cable
Length in
Weld Circuit =
20 ft (6 m)
3-3 LOWER FRONT PANEL.
Figure 3-4 Panel Front Lower.
Tools Needed
3/8" (9.5mm)
Removescrewfromlowerpanelandopenaccessdoor.
1.- Spark gaps(See section 5-5).
2.-GasOutput.
3.- Overload protection (See section 5-2).
4.- Receptacle remote14 RC14 (See section3-5).
5.- Duplex receptacle 120V, 15A.
6.- Work terminal (See section 3-4).
7.- Electrode terminal (See section3-4).
CLOSEACCESSDOOR
ELECTRODE
CB1
10 AMP.
GAS
WORK
RC 14
120 V.
15 A.
OUTPUT
1 2 43 5
6
7
60 Thru
100%
Duty Cycle
100
150
200
250
300
350
400
500
4
3
3
2
1
1/0
1/0
2/0
4
3
2
1
1/0
2/0
2/0
3/0
4
2
1
1/0
2/0
3/0
3/0
4/0
3
1
1/0
2/0
3/0
4/0
4/0
2-2/0
2
1/0
2/0
3/0
4/0
2-2/0
2-2/0
2-3/0
1
2/0
3/0
4/0
2-2/0
2-3/0
2-3/0
2-4/0
1/0
3/0
4/0
2-2/0
2-3/0
2-3/0
2-4/0
3-3/0
1/0
3/0
4/0
2-2/0
2-3/0
2-4/0
2-4/0
3-3/0
10 To 60%
Duty Cycle 10 Thru 100% Duty Cycle
Welding
Amperes
150 ft
(45 m) 200 ft
(60 m) 250 ft
(70 m) 300 ft
(90 m) 350 ft
(105 m) 400 ft
(120 m)
100 ft (30 m) Or Less
* Weld cable size (AWG) is based on either a 4 volts or less drop ora current density of not more than 300 circular mils
perampere.Useweldcable with insulationratingequal toor greaterthanthe open-circuit voltageof theunit.
Table 3-1 Weld Cable Size*
Total Cable (Copper) Length In Weld Circuit Not Exceeding

4
LocationOf
Terminals
GTAWConnectionsSMAWConnections
Figure 3-5 Weld Output Connections.
Gas Or Water
Hose
1
2OR
3-4 CONNECTING OUTPUT TERMINALS.
WARNING ELECTRICSHOCKcankill.
1.- Work Weld Output Terminal.
2.- Electrode Weld Output Terminal.
3.-AccessDoor.
Connect cables as shown.
Close and secure accessdoor.
2
1
3
Use only a proper torch cable
adapter positioned so it does not
hit frame, hardware, or door during
operation.
1
2
3/4" (19
mm)
Tools
Needed
Figure 3-6 Remote 14Connections.
R C1 4
3
4
2
1
Tools needed:
1/4" (6.3 mm)
3-5 RC14 INFORMATIÓN & CONNECTIONS.
1.- Receptacle Remote RC14 (See Section 3-6)
2.- Keyway.
3.- Plug.
4.- Threated collar.
To connect this receptacle, align keyway, insert
plug,andtightenthreatedcollar.
Electrode
Terminal Work
Terminal Electrode
Terminal
Work
Terminal

5
Figure 3-8 ConnectingTo 120 Vac DuplexReceptacleRC1.
3-7 120 VOLTS AC DUPLEX RECEPTACLE.
24 Volts AC.
3-6 REMOTE 14 CONNECTIONS.
REMOTE 14 SOCKET* SOCKET INFORMATION.
Figure 3-7 Remote 14Connections.
*THEREMAININGSOCKETSARENOTUSED.
Turn on welding power source and open access door
120 Volts AC Duplex receptacle
Receptacle Is protected from overload by circuit breaker CB1
Close Access Door
120 VAC
15 AMP.
OUTPUT
(CONTACTOR)
AMPERAGE
A
B
C
D
E
KChassis common.
+10VDC Output to remote control
Contact Closure to A completes 24 VAC contactor control circuit.
Remote control circuit common.
0 to +10 VDC input command signal from remote control
Figure 3-9InputVoltageJumperLinksLocation.
3-8 INPUT VOLTAGE CONNECTIONS
Tools nedded:
7/16" (11.1mm)
3/8" (9.5mm)
Jumperlinksallowsoperationondiferentinputvoltages(230,460and575)andarefactorysetforthehighestinput
voltage. Check input voltageavailable at site. Openaccessdoor in rear panel to checkjumper links.
1.- Input Power Switch.
2.- Access Door.
3.- Input Voltage Label - Only one is On Unit.
4.- Input Terminal Board.
5.- Input Voltage Jumper Links. Move links to match input voltage. For example: Use 230Volts position
when 230 Volts input power is available .
6.- Ground Connection.
Close and latch access door.
WARNING Electic shock can kill. High frequency radiation can interfere whith radio navegation,
safety services, computers and communications equipment.
1
3
2
4
6
6
5
JUMPER LINKS LOCATION
2 0 VOLTS
3
460 VOLTS
575 VOLTS
L1
1 2 3 4 5 6
1 2 3 4 5 6
1 2 3 4 5 6
L2
L1
L2
L1
L2

6
3-9 SHIELDING GAS CONNECTION.
Figure 3-10 ShieldingGas Conections.
5/8"(15.9mm)
1 1/8"(28.6mm)
ToolsNeeded
Obtain gas cylinder and chain to running gear, wall, or other stationary support so cylinder cannot fall and break off valve.
1.-CAP.
2.- CYLINDER VALVE. Remove cap, stand to side of valve, and open valve slightly. Gas flow blows dust and dirt from valve.
Close valve.
3.-CYLINDER.
4.- REGULATOR/FLOWMETER. Install so face is seetical.
5.-GAS HOSE CONNECTION. Fitting has 5/8-18 right-hand threads.
6.- FLOW ADJUST. Typical flow rate is 15 cfh(Cubic Feed per Hour). Make sure flow adjust is closed when opening cylinder
to avoid damage to the flowmeter.
7.-GASVALVE.
8.-GASINFITTING.
9.- GAS OUT FITTING. The gas fittings have5/8-18 Right-hands threads. Obtain proper size, type, and length hose, and make
connections as follows:
Connect hose from shielding gas supply regulator/flowmeter to gas in fitting. Connect shielding gas hose from torch to gas
Out fitting.
Close acces door.
WARNING CYLINDER can explode if damaged.
BUILDUP OF SHIELDING GAS can harm healt or kill.
1
2
3
4
6
5
9
8
7
IN - GAS - OUT
GAS
ARGON
TO USE GAS VALVE
OUTPUT CONTACTOR
PANEL
REMOTE

7
CAUTION SEE SAFETY SIGNAL AT THE BEGINING
THIS MANUAL
SECTION 4 FUNCTION OF CONTROLS
FIGURE 4-1. CONTROLS
PULSEPER
SECONDCONTROL
CURRENTBACKUP
CONTROL
POSTFLOW
TIMECONTROL
ACBALANCE
CONTROL
POWER
SWITCH
HIGHFREQUENCY
SWITCH
CRATERCONTROL
ANDSWITCH
OUTPUT
SELECTOR
SWITCH
OUTPUT
(CONTACTOR)
SWITCH
4-1. CONTROLS OF WELDING POWER SOURCE
PERCENTAGE
TIMEPULSE
CONTROL
AMPERAGECONTROL
SWITCH
AMMETER
VOLTMETER
ENABLING
PULSER
SWITCH
ARCCONTROL
ANDSWITCH AMPERAGE
ADJUSTMENT
CONTROL
ON
POWER
OFF
ON
REMOTE
OUTPUT CONTACTOR
Figure 4-2 Power switch.
Las terminales de salida están energizádas cuando
el Switch esta en NORMAL y energizáda la unidad.
1.- POWER SWITCH. Use switch to turn unit and fan On and Off.
1.- OUTPUT CONTACTOR SWITCH. Useswitch to
select way of controling unit output. For front panel
control, place switch in ON position. For remote
control, place switch in REMOTE position.(See
section 3-6).
Weld output terminals are energized when switch OUTPUT
and switch POWER are in ON position.
Figure4-3 OutputSwitch.

AMPERAGE CONTROL
REMOTE
PANEL
CONTROL
HIGH FREQUENCY
21
To Use High
Frequency circuit
Connect Remote
Control Device
8
12
12
CONTINUOUS
HIGH FREQUENCY
OFF
ON
POSTFLOWTIME
Use control to set the length of time gas flows
after the welding stops.
Adjust time according to size of tungsten
electrode in torch.
Figure 4-4 PostflowTime Control
1.-HIGHFREQUENCYSWITCH.
START.-Provides HF for arc starting only
OFF.- Provides no HF. Use OFF for SMAW
Welding.
CONTINUOUS.- Provides HF Continuosly
throughout the weld.
2.-HIGHFREQUENCYINTENSITYCONTROL
(See Figure 3-3). Use control to change
amount of HF energy used to start and
maintain the arc. Set as low as practical to
prevent interfering with electronic equipment.
Figure4-5 HighFrequencyControls.
Figure4-6 AmperageControls
1.-AMPERAGEADJUSTMENTCONTROL.Use con-
trol to select weld amperage. The numbers are weld
amperes. The amperage adjustment control may be
adjusted while welding.
2.- AMPERAGE CONTROL SWITCH. Use switch to
select way of controling amperage adjustment.
For frontpanelcontrol,place switchin PANELposition.
For remote control, place switch in REMOTE 14
position (See Section 3-6).
1.-ARCCONTROL.ForSMAW welding,usecontroltohelpstart
an arc or make vertical or overhead welds. Control increases
short-circuit amperage at low arc voltage (See Figure 2-1).
When set at 0, short-circuit amperage at low arc voltage is the
same as normal welding amperage. When set at 100, short-
circuit amperage at low arc voltage increases to help arc
starting.
2.-ARC CONTROL SWITCH. PlaceSwitch inthe ONposition to
turn on arccontrolcircuitry. When switch is in the OFF position,
no additional amperage is available at low arc voltages. Place
switch in the OFF position while performing GTAW.
Figure 4-7 Arc Controls
Connect Remote Device
To use post flow time
circuit
POST-FLOW TIME
PANEL
REMOTE
PANEL
REMOTE

9
1Max=200 ADC
Min= 0 A DC 23
ON
REMOTE
OUTPUTCONTACTOR
Adjust Remote Control
Min=0 A DC
Percentege Of Range=50%
Output=100 A DC (50% of 0 to 200)
1.- Fingertip Control
2.- Remote Foot Control.
3.- Remote Hand Control
Figure 4-8 Example OfCombination RemoteAmperage Control.
Set Switches Set Output Set Control
SET TO 3 FOR BALANCED AND DC WELDING
1.-ACBALANCECONTROL.
Use control to change the AC output square
wave.
Turn control towards 10 to obtain deeper
penetration. Turn control towards 0 to obtain
more cleaning action of the workpiece. The
wave shape of position 3 (Balanced), Cleaning
action, and is a recomended starting point for
GTAW.
50%Electrode
Negative
32%Electrode
Positive
68%Electrode
Negative
55%Electrode
Positive
45%Electrode
Negative
50%Electrode
Positive
BALANCED
MORE
PENETRATION
MORE
CLEANING
AC Balance Control Waveforms Examples.
Figure 4-9 AC Balance Control
FIGURE4-10.OUTPUTSELECTOR
1.-OUTPUT SELECTOR SWITCH. Use switch to select weld
output type.
1
CLEANING PENETRATION
DC
AC
DC REVERSE POLARITY
SELECTOR
STRAIGHT
POLARITY
PANEL
REMOTE
DC
AC
DC REVERSE POLARITY
SELECTOR
STRAIGHT
POLARITY

10
FIGURE 4-12. Pulser switch.
ON: In this position the output current from power source will be in pulsed mode in accord to
backup and peak amperage values.
OFF: In this position the power source disables the pulsed mode, but the amperage level are
set by controlling the peak amperage.
IMPORTANT
The switch may be placed in position on or off before or during the welding process.
4-1A. PULSER CONTROLS.
Figure 4-13 %On time control.
The % ON TIME control provides a means of selecting the pulse width. Rotating the control clockwise
increases the peak output time in relation to the entire pulse time as set on the PULSES PER SECOND
control. The scale surrounding the control is calibrated from 5 to 95 percent and represent the peak
output on time during one pulse.
IMPORTANT:
The %ON TIME control may beadjustedwhile welding.
ON
OFF
1.-CRATERTIMECONTROL
Usecontrol toset time to taperweld ouput from
setting of the amperage adjustment control to
the minimum of the unit.
2.-CRATERTIMESWITCH
ON- Provides Crater time
OFF- Provides No Crater time
Place switch in the OFF position for SMAW.
Figure 4-11 Crater TimeControls.
1
2
To use crater time circuit
Connect Remote control device
PANEL
REMOTE
ON
REMOTE
OUTPUTCONTACTOR
PULSER
SWITCH
ON
ON
ON
ON
ON
OFF
OFF
REMOTECONTROL
SWITCH POSITION
ON or OFF
ON or OFF
ON or OFF
OFF
ON
ON or OFF
ON or OFF
WELDING POWER SOURCE
OUTPUT (CONTACTOR)
SWITCH POSITION
ON
REMOTE
ON
REMOTE
REMOTE
REMOTE
ON
OPENCIRCUIT
VOLTAGE
AVAILABLE
AVAILABLE
AVAILABLE
NOTAVAILABLE
AVAILABLE
NOTAVAILABLE
AVAILABLE
TABLE 4-1
AVAILABILITY OF OPEN-CIRCUIT VOLTAGE WHEN WELDING
POWER SOURCE IS ENERGIZED

11
Figure4-15BackgroundAmperagecontrol.
The PULSES PER SECOND control provides a means of selecting the pulse
selecting. Rotating the control clockwise increases the pulse frequency.
The scale is calibrated from 0.5 to 20 pulses per second.
IMPORTANT:
The PULSES PER SECOND control may be adjustedwhile welding.
RANGE SELECTION:
The PULSER CIRCUIT BOARD has an internal
jumper for selecting the desired range for the PUL-
SES PER SECOND control (J1 or J2), see figure.
For this unit J1 are not removed of position (range 0.5
to 20 pps). PULSER CIRCUIT BOARD PC2
IMPORTANT:
TheBACKGROUNDAMPERAGEcontrol maybeadjustedwhilewelding.
The BACKGROUND AMPERAGE controlprovides a means of selecting the weld
output background amperage level. The BACKGROUND AMPERAGE isa percentage
of the peak amperage and can never be set to a value higher than the peak amperage.
Rotating the control clockwise increases the background amperage.
The scale is calibrated from 0 to 100 percent and should not be read as an amperage
or voltage.
J2
ó
J1

12
4-3 WHAT IS PULSING?
Pulsing refers to the alternate raising and lowering of the weld output at a periodic rate.(Ver Fig. 4-16).
Thehighest valueis called peak amperage, and thatis thepulse, heats themolten weld puddle, the lowestvalue iscommonly
called background amperage and allows a degree of cooling molten weld puddle.
The weather that increases at peak amperage and remains at this value (it is called pulse width) along with remaining time
in background amperage level, forming a total period cycle or pulse. Then in each cycle there is a pulse.
The number of cycles that occur in a second is known as frequency or cycles per second that we express here as pulses
per second (pps)
The PULSER allows the operator to control the value of:
a) BACKGROUND AMPERAGE.
b) PULSE WIDTH, as percentage of pulse or total cycle.
c) Number of PULSES PER SECOND (pps) or frequency.
Thecombined effect gives the operator bettercontrolof penetration, beadwidth, crowning, undercutting, and puddle sag inout-
of-position welding, specially vertical-up.
Figure4-16 Pulsedoutput.
8
0
%
O
n
t
i
m
e
P
u
l
s
e
s
p
e
r
s
e
c
o
n
d
T
o
t
a
l
p
u
l
s
e
p
e
r
i
o
d
A
m
p
e
r
a
g
e
T
i
m
e
2
0
%
O
n
t
i
m
e
B
a
c
k
g
r
o
u
n
d
a
m
p
e
r
a
g
e
p
e
r
i
o
d
A
m
p
e
r
a
g
e
T
i
m
e
Peak amperage level
(Heat molten
weld puddle) Background amperage level
(Cool )molten weld puddle
A
m
p
e
r
a
g
e
50% On time
T
i
m
e

13
14
3
O
21.-SHIELDINGGASMETAL.
2.-VALVE.
3.-FINGERTIPCONTTOL.
4.-FOOTCONTROL.
Open valve on cylinder just before welding.
Finger tip control, or foot control turns weld
output and gas flow on and off.
Close valve on cylinder when finished welding.
Figure 4-17 Shielding Gas.
FIGURE 4-18. Sequence Of Gas
TungstenArcWelding(GTAW)AndGas
Tungsten ArcSpot Welding.
FIGURE 4-19. SequenceOfShieldedMetal Arc
Welding(SMAW).
Select Tungsten (See Section 6)
Install Tungsten Into Torch
Put On Personal Safety Equipment
Turn On Shielding Gas
Turn On Welding Power Source
Begin Welding.
Install &Connect Equipment
Set Controls
1
8
7
6
5
4
3
2Select Electrode
Put On Personal Safety Equipment
Set Controls
Begin Welding.
Install & Connect Equipment
Insert Electrode Into Holder
1
7
6
5
4
3
2
Turn On Welding Power Source
SECTION 5
MAINTENANCE & TROUBLESHOOTING
5-1 ROUTINE MAINTENANCE.
TIME
EVERYMONTH
EVERY3MONTHS
EVERY6MONTHS
MAINTENANCE
WARNING SEE SAFETY SIGNAL AT THE BEGINING THIS MANUAL
Above normal equipment use: Check all labels ( see 6 month entry ), repair any damaged insulation
or replace Electrode-holder or work cable, clean internal parts ( see 6 month entry ), clean and tighten
connections at holder cable and work clamp.
Replace Unreadable Labels, Tape Or Replace Cracket Cables, Clean And Tighten Weld Terminals,
Replace Cracket Parts.
Blow Out Or Vacuum inside. (During Heavy Service Clean Monthly)

14
Lack of high frequency at tungsten
electrode, difficulty in starting and
arc.
5-2 TROUBLESHOOTING.
Tungsten electrode oxidizing and
not remaining bright after conclusion
of weld.
Unit provides only maximum or
minimum weld output.
Weld output always above or
always below set value.
Electronic board PC1.
Erratic weld output
No control of weld output.
No weld output, fan runs.
No weld output, unit completely
inoperative
TROUBLE REMEDY
CAUSE
Gas shutting off too quickly after end of weld.
Loose gas fittings on regulator or gas line. This
will siphon oxygen into the weld zone.
Insuficient gas flow.
Drafts blowing gas shield away from tungten.
Contaminated tungten.
High frequency switch in OFF position.
Increase time settings of post-flow time control (See
figure 4-11).
Check and tighten all gas fittings.
Increase gas flow setting.
Shield weld zone from drafts.
Prepare tungsten as instructed in section 8.2.
PlaceHIGHFRECUENCYinSTARTorCONTINUOUS
position.
Consult your dealer or Service Center to review unit.
Electronic board PC1. Consult your dealer or Service Center to review unit.
Electronic board PC1. Consult your dealer or Service Center to review unit.
AC Balance control R3.
Circuit Board PC1.
Amperage control switch S5 position.
Amperage adjustment control R1.
Check and replace R3.
Place S5 in PANEL position, if no remote control is
begin used. Place S5 inREMOTE position andbe sure
remotecontrol Is connected toREMOTE 14 receptacle
RC2 (See Section 3-5 & Figure 4-6).
Check And Replace R3.
Electronic board PC1. Consult your dealer or Service Center to review unit.
No AC BALANCE control
No HIGH FREQUENCY, No gas flow,
and no spot time (If applicable) Circuit Breaker CB1. Check and reset CB1 if necessary.
Improperly prepared tugsten.
Wandering Arc - Poor Control Of
Direction Of Arc
Use of tungsten considerably larger
than recommended.
Prepare tungsten as instructed in section 8-2.
Use proper size tungsten (See Table 8-1).
Use of tungsten larger than recomended for
welding amperage. Consult your dealer or Service Center to review unit.
Disipation of high frequency from SMAW electrode
holder lead. Be sure to disconnect SMAW electrode cable from
weld output terminal when GTAW welding
Improper spark gap.
Weld cable leakage.
Check spark gaps and readjust if necessary (See
section 5.5)
Check cables and torch for cracked or deteriorated
insulation or bad connections. Repair or replace
necessary parts.
Consult your dealer or Service Center to review unit.
Output contactor switch S3 position
Remote control device.
Thermostat TP1 open (Thermal shutdown) or not
working.
Electronic board PC1
Place S3 in ON position if no remote control is
used.PlaceS3inREMOTEpositionandbesureremote
control is connected to receptacle RC2.
Check and repair or replace remote control device.
Allow unit to cool for approximately 15 minutes with
fan on.
Consult your dealer or Service Center to review unit.
Line disconnet switch in the OFF position.
Line fuse (s) open.
Improper electrical input connections.
Input voltage jumpers links not in proper positions.
Power switch.
Place line disconnect switch in the ON position.
Check and replace line fuse(s).
See section 3-8 for proper input connections.
See section 3-8 for proper jumper link position.
Check and replace S1 if necessary.
Table of contents
Other Comparc Welding System manuals
Popular Welding System manuals by other brands

Lincoln Electric
Lincoln Electric FlexCool 35 Operator's manual

WIELANDER+SCHILL
WIELANDER+SCHILL IM 240-i Operation manual
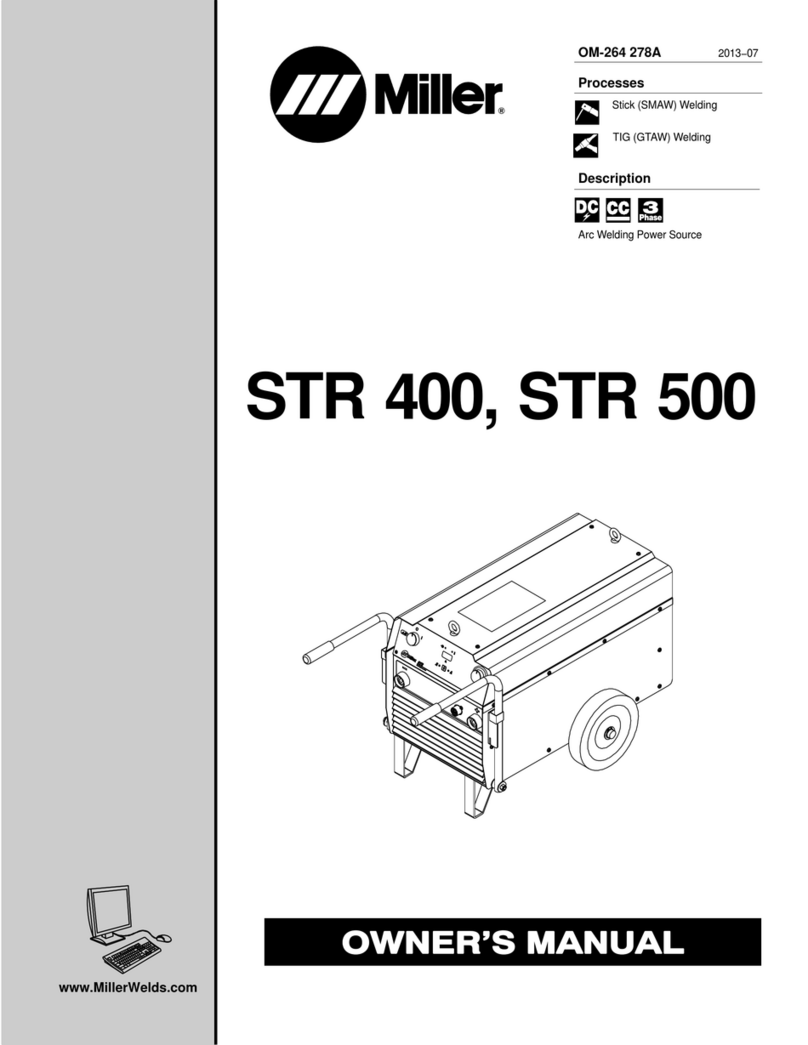
Miller
Miller STR 500 owner's manual
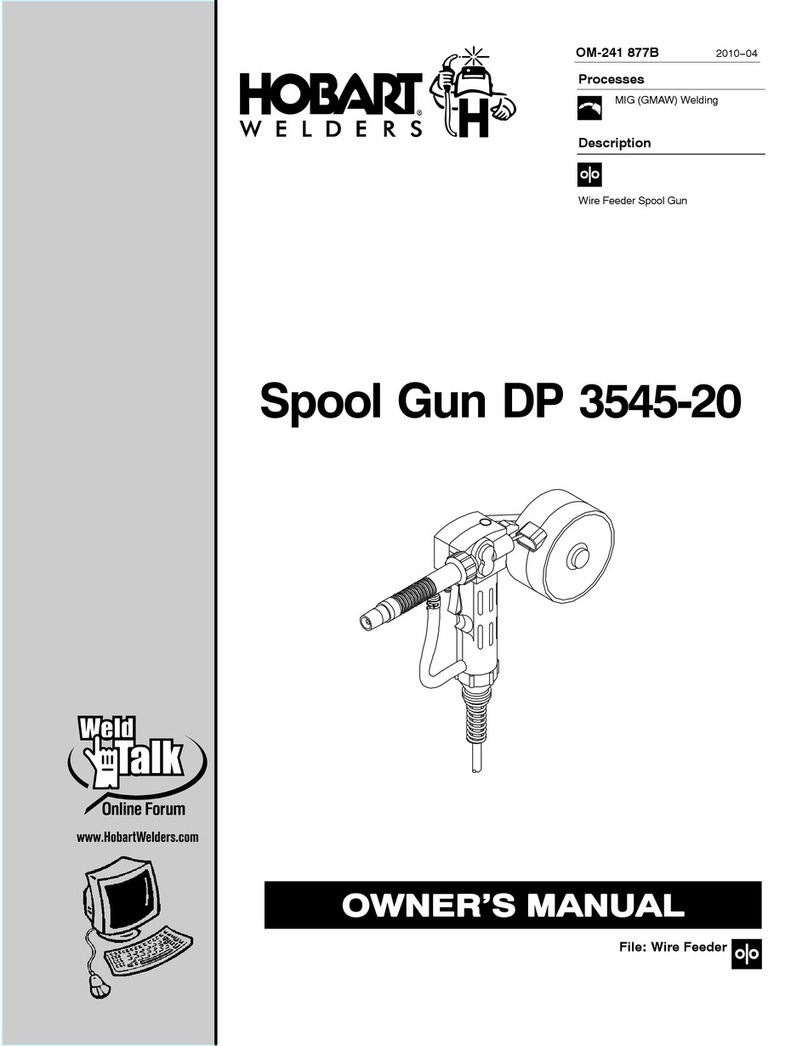
Hobart Welding Products
Hobart Welding Products Spool Gun DP 3545-20 owner's manual
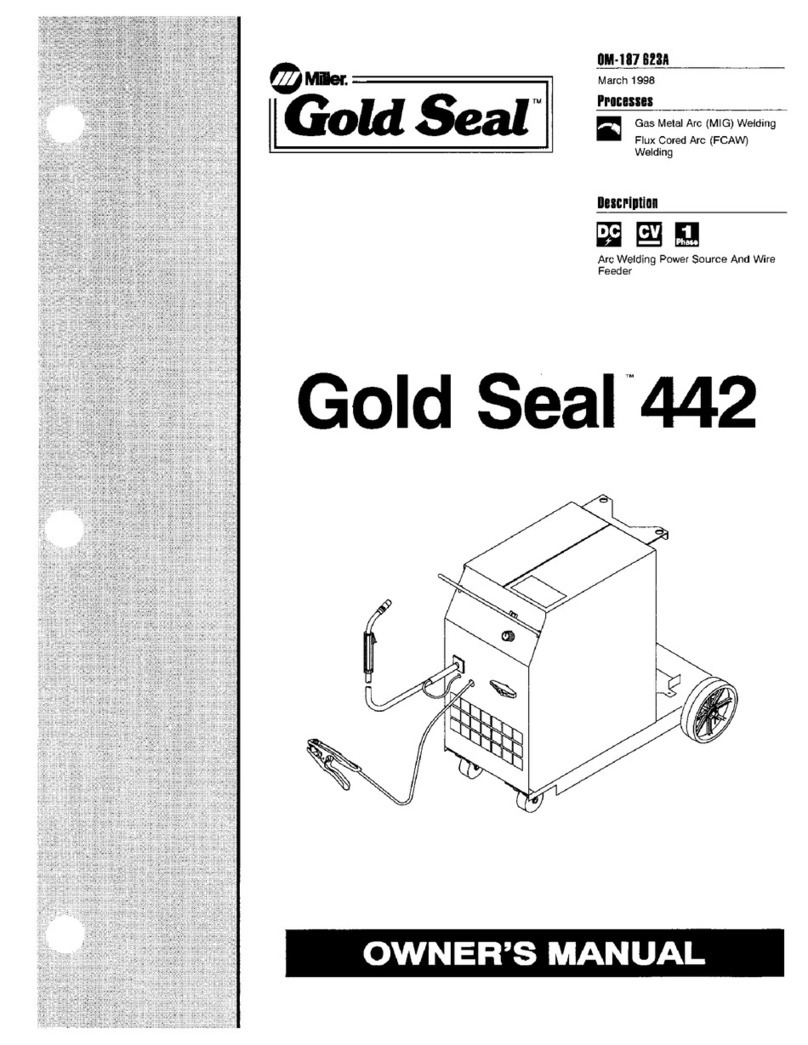
Miller
Miller Gold Seal 442 owner's manual
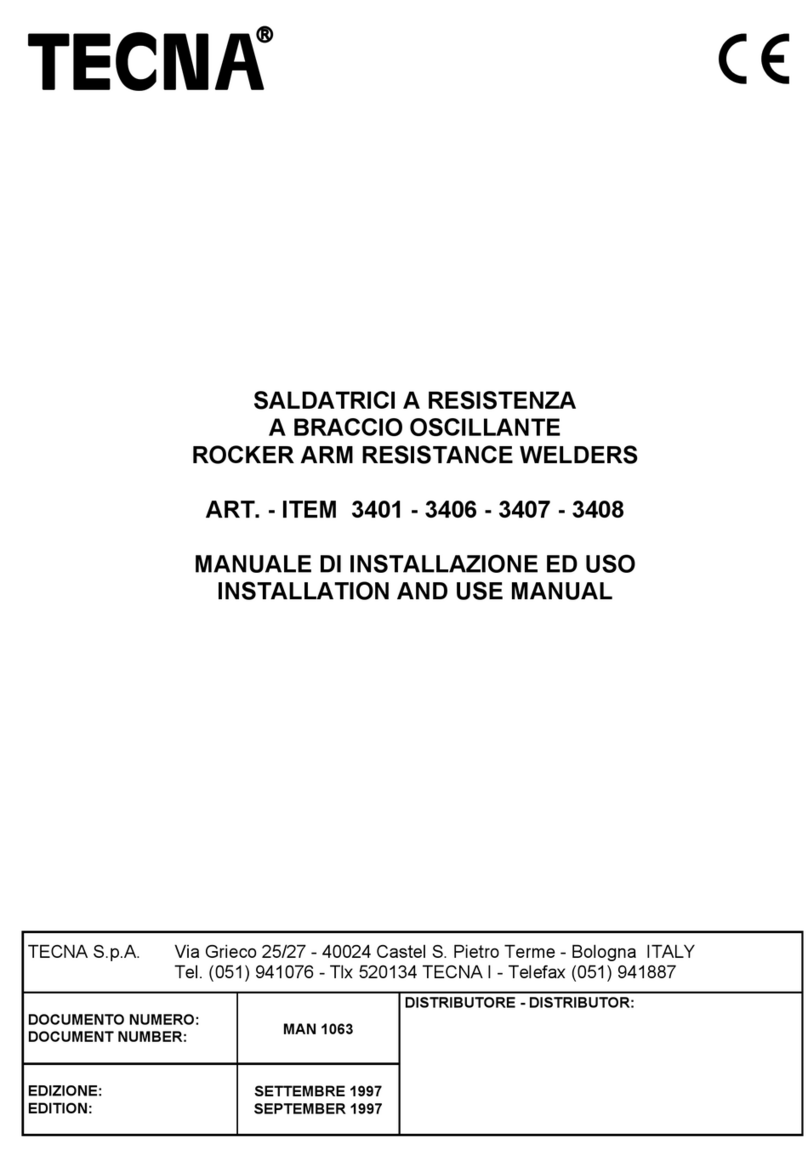
TECNA
TECNA 3401 Installation and use manual