CPT CPDP-104 User manual

Circle Guide For Drill Press
Model CPDP-104
Web Site: www.circleperfecttools.com
Facebook: www.facebook.com/circleperfecttools
Tutorials: www.circleperfecttools.com/#!VIDEOS/c20ku
FAQ: www.circleperfecttools.com/#!faq/cavw
©2014 Circle Perfect Tools, LLC. All rights reserved

GENERAL SAFETY RULES
Safety is a combination of common sense, staying alert and knowing how to use a tool.
WARNING: To avoid mistakes that could cause serious injury, do not attach Circle Guide For Drill Press
until you have read and understood the following:
1. READ and become familiar with the entire installation instructions on
how to attach Circle Guide For Drill Press.
2. LEARN the tool's application, limitations and possible hazards.
3. REMOVE ADJUSTING KEYS AND WRENCHES. Form a habit of
checking to see that keys and wrenches are removed from drill press
before turning ON.
4. KEEP WORK AREA CLEAN. Clutter areas and benches invite accidents.
5. DON'T USE IN DANGEROUS ENVIRONMENT. Don’t use power tools in
damp or wet locations, or expose them to rain.
Keep work area well lighted.
6. KEEP CHILDREN AWAY. All visitors should be kept at a safe distance
from work area.
7. MAKE WORKSHOP CHILDPROOF with padlocks.
8. DON'T FORCE THE TOOL. It will do the job better and safer at the
rate for which it was designed.
9. USING THE RIGHT TOOL. Do not force tool or attachments to do a
job for which it was not designed.
10.
USE PROPER EXTENSION CORD. Make sure your extension cord is in condition.
11. DRESS PROPERLY. Do not wear loose clothing, neckties, or jewelry that
can get caught and draw you into moving parts. Wear protective
hair covering to contain long hair.
12. ALWAYS WEAR SAFETY GLASSES WITH SIDE SHIELDS. Everyday
eyeglasses have only impact resistant-lenses, they are NOT
safety glasses.
13. SECURE WORK. Use clamps or a vise to hold work when practical,
it is safer than using your hand and frees both hands to operate
the tool.
14.
DO NOT OVERREACH. Keep proper footing and balance at all times
15. DISCONNET TOOLS. When not in use or when changing attachments,
blades, bits, cutter, etc. all tools should be disconnected from
power source.
16. AVOID ACCIDENTAL STARTING. Be sure switch is off when plugging
in any tool.
17. NEVER LEAVE TOOL RUNNING UNATTENDED. TURN THE POWER OFF.
DO NOT LEAVE TOOL UNTIL IT COMES TO A COMPLETE STOP.
18. PROTECT YOUR LUNGS. Wear a face or dust mask if the operation
is dusty.
19. PROTECT YOU HEARING. Wear hearing protection during extended
periods of operation.
20. KEEP FINGERS AWAY FROM REVOLVING BITS.

UNPACKING
This product requires assembly
Carefully remove the product and any accessories from
the box. Makes sure that all items listed in the packing
list are included. Inspect the product carefully to make
sure no breakage or damage occurred during shipping
Do not discard the packing material until you have
carefully inspected and satisfactorily operated the
product. If any parts are damaged or missing, please
contact us via email at info@circleperfecttools.com.
1 Centering Bit (Steel) ( .25 inch x 5) (1) 9 Rotation Plate (PVC) (1)
2 Centering Tool (PVC) (1)
3 Center Pins (PVC/Steel) (3) 11 Lock Down Knob (1)
4 Alignment Pin (Steel) (1) 12 Fender Washer (12)
5 Rotation Alignment Pin (Steel) (1) 13 Hex Nuts (1/4" x 20) (8)
6 Slide Plate (PVC) (1) 14 Hex Key (5/32 SA) (1))
7 Left Alignment Plate (PVC) (1) 15 Table Mount (Wood) (1)
8 Right Alignment Plate (PVC) (1) 16 Degree Gear (PVC) (4)
17 Safety Disk (PVC) (1)
10 Mounting/Lock Down Bolts-1/4 inch (9)
ASSEMBLY
WARNING:
Do not attempt to modify this product or create
accessories not recommended for use with this
product. Any such alteration or modification is
misuse and could result in a hazardous condition
leading to possible serious personal injury.
WARNING:
Do not connect power supply until assembly is
complete. Failure to comply could result in
accidental starting and possible serious personal
injury.

ASSEMBLY INSTRUCTIONS
Set Drill Press Table approximately 6
inches from the Drill Press chuck.
Align Drill Press Table with Drill Press
chuck. Once aligned, lock table with
table lock.
Attach Table Mount to Drill Press
table using 1/4 inch connector
bolts/washer/nuts thru mounting
slots. Hand tighten at this point.
Attach both Alignment Plates to Table
Mount by inserting the 1/4 inch
connector bolts/washers/nuts into
the designated holes of Table Mount.
Hand tighten at this point.
Step 1 - Aligning Drill Press Chuck and Drill Press table
Step 2 - Attaching Table Mount
Step 3 - Attaching Alignment Plates

Insert Center Pin thru the bottom of
Slide Plate in the pocket closest to the
drill channel. Make sure Center Pin is
flush with the bottom of Slide plate.
Step 4 - Inserting Center Pin
Step 5 - Attaching Slide Plate
Step 6 - Securing Alignment Plates
Slide the Slide Plate between the two
alignment plates that are mounted on
Table Mount. Insert lock down bolt
through designated slot in the Slide
Plate and hole of Table Mount.
Tighten the Left Alignment Plate bolts
to Table Mount, then push both the
Slide Plate and Right Alignment Plate
snug up against the Left Alignment
Plate, tighten the Right Alignment
Plate bolts to the Table Mount. Make
sure that Slide Plate can still slide
between the two Alignment Plates.
Tighten all bolts using the allen
wrench supplied.

Insert Centering Bit into the Drill Press
Chuck. Position Centering Tool over
Center Pin. Move Table Mount so the
Centering Bit will lower into the bit hole
of the Centering Tool. Tighten the two
exposed 1/4 inch bolts. Release
Alignment Pin, loosen Lock Down Bolt,
move the Slide Plate back and then
tighten the final two bolts. Remove
Centering Tool The tool is now ready for
radial distance drilling only.
Insert short Alignment Pin into the
Left Alignment Plate at the "For Black
Scale" position. Slide the Slide Plate
to the 5 inch mark of the Left
Alignment Plate. Seat the Alignment
Pin into the Slide Plate. Secure Slide
Plate into place by tightening the Lock
Down bolt.
Step 7 - Inserting Alignment Pin and securing Slide Plate
Step 8 - Centering Circle Guide to Drill Press Bit
Step 9 - Attaching Rotation Plate (for use with Degree Gears)
Lower the Rotation Plate over the
Center Pin thru the hole in the upper
degree gear pocket. Press Rotation
Plate feet into holes of Slide Plate.
Insert Long Alignment Pin into the
designated slot in the Rotation Plate.

Step 1:
Step 2:
After preparing the material you can proceed to setting up the Circle Guide and Drill Press.
Step 1:
Step 2: Move the Slide Plate away from the drill bit until it is stopped by the Lock-Down Bolt.
Step 3:
Step 4:
Step 5:
Step 6:
Place material onto the Center Pin through the 1/8" (English) or 3mm (Metric) hole.
Start by releasing the Alignment Pin and loosening the Lock-Down Bolt.
Basic Operations
Preparing Material
Drilling Holes in Material (without Degree Gears)
Remove any abrasive particles and/or spurs from face of material before rotating to prevent
damage to the surface of the Circle Guide tool.
The Circle Guide tool requires the rotation of material around a Center Pin. Please perform these basic steps
before drilling to prepare your material.
Drill a 1/8" (English) or 3mm (Metric) hole in material which will be the center point of your circle.
Drill the hole as perpendicular as possible to ensure precise rotation around the Center Pins.
Move the Slide Plate into desired position in order to set the radial distance. If using a set
measurement, insert the Alignment Pin into set measurement position and then tighten the Lock-
Down Bolt. If not using a set measurement, simply tighten the Lock-Down Bolt at current position.
Insert the desired drill bit into the Drill Press.
Turn on Drill Press and proceed to drilling a hole. Smoothly rotate material when drill bit is raised
to drill holes in circular pattern at the current radial distance. Repeat steps as needed.

After preparing the material you can proceed to setting up the Circle Guide and Drill Press.
Step 1:
Step 2: Move the Slide Plate away from the drill bit until it is stopped by the Lock-Down Bolt.
Step 3:
Step 4:
Step 5:
Step 6:
Step 7:
Step 8:
Step 9:
Step 10:
Drilling Holes in Material (with Degree Gears)
Start by releasing the Alignment Pin and loosening the Lock-Down Bolt.
Insert the desired drill bit into the Drill Press.
Lift material off the Center Pin and place aside.
Move the Slide Plate into desired position in order to set the radial distance. If using a set
measurement, insert the Alignment Pin into set measurement position and then tighten the Lock-
Down Bolt. If not using a set measurement, simply tighten the Lock-Down Bolt at current position.
Turn on Drill Press and proceed to drilling a hole. Release the Rotation Alignment Pin and rotate
material when drill bit is raised. Lock into next Degree Gear slot and drill another hole. Continue
this process to drill holes in a circular pattern at the current radial distance. Repeat steps as
needed.
Attach the desired Degree Gear by first placing the material onto the Center Pin using 1/8"
(English) or 3mm (Metric) hole (bottom of material facing up). Place double-sided tape on smooth
side of Degree Gear and then place onto material using the Center Pin (gears facing up).
Place the Rotation Plate on top of the Slide Plate using Center Pin and ensure it seats into position.
Now place material back onto the Center Pin with Degree Gear facing down. Ensure the Degree
Gear seats into the designated hole in the Rotation Plate.
Insert the Rotation Alignment Pin into the Rotation Plate and lock into the Degree Gear slot.
NOTE: You can also mount using screw holes in Degree Gear instead of double-sided tape.

Step 1: Loosen the Lock-Down Bolt and release Alignment Pin.
Step 2: Move the Slide Plate to desired measurement position.
Step 3: Insert Alignment Pin into Slide Plate (should click into position).
Step 4: Tighten the Lock-Down Bolt and ensure the Slide Plate is held firmly in position.
Step 5: Perform drilling and repeat as necessary.
Step 1: Loosen the Lock-Down Bolt and release Alignment Pin.
Step 2: Move the Slide Plate to desired position.
Step 3: Tighten the Lock-Down Bolt and ensure the Slide Plate is held firmly in position.
Step 4: Perform drilling and repeat as necessary.
Tip 1:
Tip 2:
Tip 3:
Using Set Measurements
Using Infinite Variability
When using harder material, ensure the material does not overheat from excessive drilling as this
may cause damage to the surface of the Circle Guide tool.
Tips
To prolong the life span of the tool's surface, make sure to remove any abrasive particles and/or
spurs from face of material before rotating to prevent damage to the surface of the Circle Guide
tool.
When using large drill bits or Forstner bits, do not drill hole all the way through the material. First
start by drilling a pilot hole half way through the material, then flip over material and finish drilling.
This will also prevent drilling holes through the Circle Guide tool.
The Circle Guide for Drill Press provides the ability to set the Slide Plate into positions simply by moving Slide
Plate into desired position and ONLY tightening the Lock-Down Bolt. This provides "infinite" positions between
the minimum and maximum radial distance settings allowing operator to make incrementally small
adjustments or set Slide Plate into a position which cannot be locked into by using the Alignment Pin.
The Circle Guide for Drill Press provides the ability to lock in the radial distance at set measurements every
1/16" (English) or 2mm (Metric). This operation provides precise repeatability by allowing operator to recall to
a prior position.

Table of contents
Popular Power Tools manuals by other brands
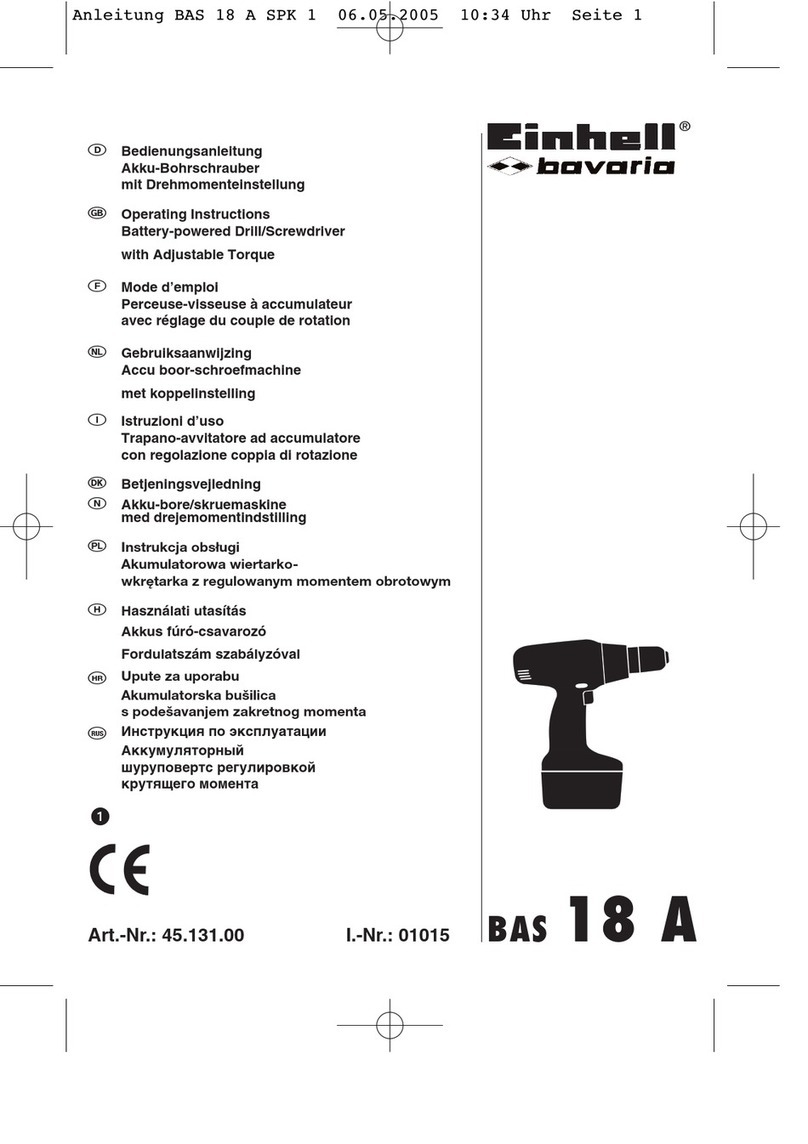
EINHELL Bavaria
EINHELL Bavaria BAS 18 A operating instructions

Gardner Bender
Gardner Bender SP-7 manual
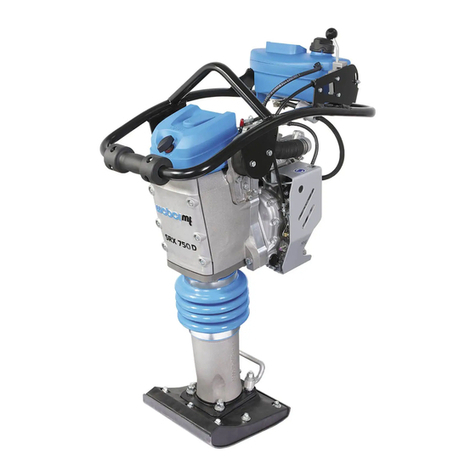
Weber mt
Weber mt SRX 750 D Series Operating and maintenance manual
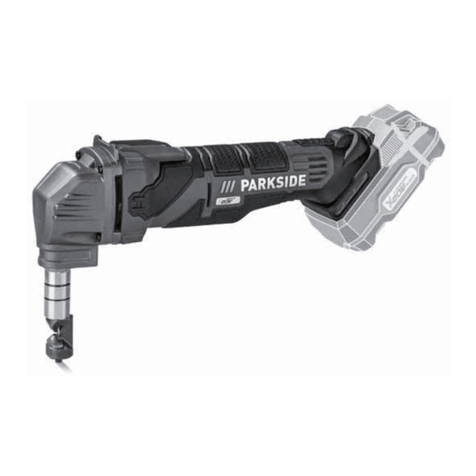
Parkside
Parkside PMKA 20-Li A1 Translation of the original instructions
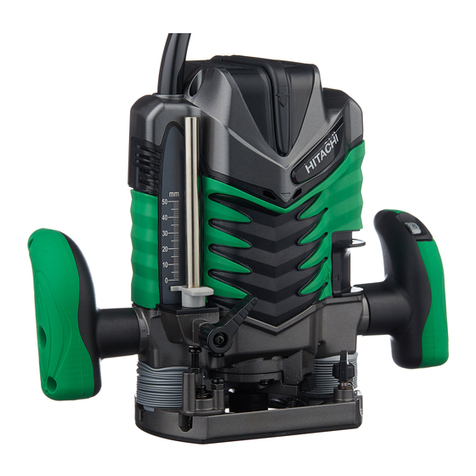
Hitachi
Hitachi M 8V2 Handling instructions
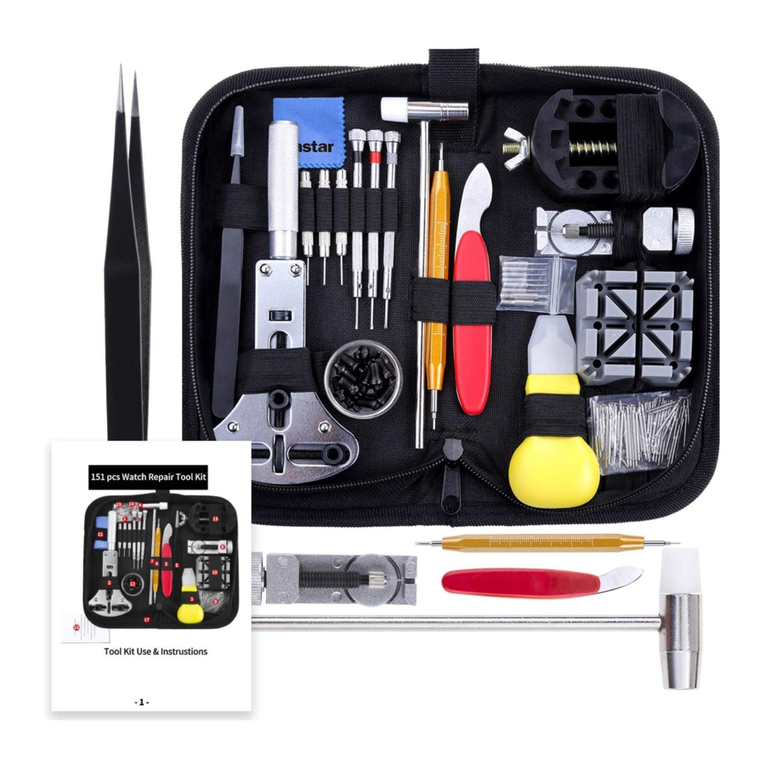
Vastar
Vastar B07H8D23L6 use instructions