STEPCRAFT SK15 User manual

Operating Manual.
EN
05/21
Tool Magazine SK15 for M-Series (Art. No. 12367 / 12368 / 12370)

3
EN
Table of Contents
Description . . . . . . . . . . . . . . . . . . . . . . . . . . . . . . . . . . . . . . . . . . . . . . . . . 2
1 General Instructions . . . . . . . . . . . . . . . . . . . . . . . . . . . . . . . . . . . . . . . . . 3
1.1 Information and Explanation of used Terminology.............................................................................. 3
1.2 General Safety Warnings................................................................................................................. 4
1.3 Intended Scope of Use ................................................................................................................... 5
1.4 Description of Components / Scope of Delivery ................................................................................. 5
2 Installation of the Tool Magazine . . . . . . . . . . . . . . . . . . . . . . . . . . . . . . . . 6
2.1 Required tools for the assembly ...................................................................................................... 6
2.2 Preparation of the CNC Machine ..................................................................................................... 6
2.3 Installation of the Piston into the Z-Axis........................................................................................... 7
2.4 Installation of the Tool Magazine ..................................................................................................... 9
2.5 Connection of the Electrical Components ....................................................................................... 12
2.6 Function check ........................................................................................................................... 18
3 Operation . . . . . . . . . . . . . . . . . . . . . . . . . . . . . . . . . . . . . . . . . . . . . . . . 19
3.1 Tool Changer Switch..................................................................................................................... 19
3.2 Software setup ............................................................................................................................ 19
3.3 Tool Length Sensor ...................................................................................................................... 20
3.4 Offsetting your tools using UCCNC ................................................................................................ 20
3.4.1 Offsetting a single Tool with UCCNC ........................................................................................... 21
3.5 Using the Tool Magazine with UCCNC ............................................................................................ 21
3.6 Offsetting and using your Tools using WinPC-NC ............................................................................. 21
4 Technical Data . . . . . . . . . . . . . . . . . . . . . . . . . . . . . . . . . . . . . . . . . . . . 22
5 Limited Warranty . . . . . . . . . . . . . . . . . . . . . . . . . . . . . . . . . . . . . . . . . . 22

4
EN
Description
The new Tool Magazine for the STEPCRAFT M-Series makes working with the Automatic Tool Changer even more con-
venient! With up to ten (seven for M.500 variant) Retainer Rings for the Tool Holder SK15, the Tool Magazine offers
plenty of space for a wide variety of end mills. Two Retainer Rings for the Tool Holder SK15 are already included,
others are optionally available. Thanks to the integrated tool length sensor, the length of the different end mills can be
determined quickly and automatically.
Additionally, the Tool Magazine features an innovative, pneumatic lifting mechanism for the simultaneous use of Ex-
haust Adapter and Automatic Tool Changer. When a tool is picked up or put down, the Exhaust Adapter automatically
moves upwards clearing the way for the change of tool. This makes milling even more clean and efcient. The speed
of the lifting mechanism can be individually adjusted via a throttle. Furthermore, the metal connector of the Exhaust
Adapter can be held permanently in the highest position.
The Tool Magazine is delivered as partially assembled module and simply inserted in place of the last table panel (MDF
or aluminum). With the help of the enclosed plugs, unused tool slots can be easily closed and, thus, protected against
dust and debris. The Tool Magazine is connected to the mainboard of the STEPCRAFT M-Series and to compressed air.
For this purpose, a compressor is required with at least 9-10 bar that is not included in the scope of delivery.
You can order the separately available Retainer Rings for the Tool Holder SK15 from our online shop:
https://www.stepcraft.us/shop
Art.No. Name Compatible
with Image
12420 Retainer Ring for Tool Holder SK15
M.500
M.700
M.1000

5
EN
NOTICE
All instructions, warranties and other collateral documents are subject to change at the sole discretion of
STEPCRAFT GmbH & Co. KG. For up-to-date product literature, visit www.stepcraft.us for customers from North America and
Mexico or www.stepcraft-systems.com for customers from the rest of the world.
Meaning of Special Language
The following terms are used throughout the product literature to indicate various levels of potential harm when operating this
product. The purpose of safety symbols is to attract your attention to possible dangers. The safety symbols, and their explanations,
deserve your careful attention and understanding. The safety warnings themselves do not eliminate any danger. The instructions or
warnings they give are not substitutes for proper accident prevention measures.
Meaning of Special Language
NOTICE Procedures which, if not properly followed, create a possibility of physical property damage AND a little or
no possibility of injury.
Procedures which, if not properly followed, create a probability of physical property damage AND a possibil-
ity of serious injury.
Procedures which, if not properly followed, create a probability of property damage, collateral damage, seri-
ous injury or death OR create a high probability of supercial injury.
Read the ENTIRE instruction manual, to become familiar with the products features and how to operate it.
This includes the entire relevant documentation of the M-Series and all accessories! Failure to operate the
products correctly can result in damage to the products, personal property and cause serious injury, electric
shock and/or re.
Do not attempt disassembly, use with incompatible components or augment product in any way without the
approval of STEPCRAFT GmbH & Co. KG or STEPCRAFT, Inc. This manual contains instructions for safety
and operation. It is essential to read and follow all the instructions and warnings in the manual, prior to
assembly, setup or use, in order to operate correctly and avoid damage or serious injury.
SAVE ALL WARNINGS AND INSTRUCTIONS FOR FUTURE REFERENCE.
Age recommendation: For advanced handcrafters ages 16 and above. This is not a toy.
Should you encounter any doubts or require any further information, please do not hesitate to contact us before com-
missioning of the product. Our contact details can be found on the front page of this manual.
1 General Instructions
1.1 Information and Explanation of used Terminology
These operating instructions explain the STEPCRAFT Tool Magazine and inform you about the correct and safe handling
of the CNC accessory.
This symbol placed next to a construction step indicates a step you can skip in case you don’t own a
STEPCRAFT exhaust adapter. It’s also possible that a grey frame indicates a single sub-step you can skip.

6
EN
SIGNAL WORD Work Area Safety
NOTICE Keep work area clean and well lit. Cluttered or dark areas invite accidents.
NOTICE Keep children and bystanders at a distance while operating this product. Distractions can cause you to
lose control and can result in accidents.
SIGNAL WORD Personal Safety
Stay alert, watch what you are doing and use common sense when operating the power tool. Do not use
the power tool while you are tired and/or under the inuence of drugs, alcohol or medication. A moment of
inattention while operating the power tool may result in serious personal injury.
Depending on the application eld of the machine (private or commercial), observe the applicable occu-
pational safety and health, safety and accident prevention and environmental regulations as well.
NOTICE All persons who operate the power tool must have read and fully understood all relevant safety and operat-
ing instructions. Misunderstanding may result in personal injury.
NOTICE Dress properly. Do not wear loose clothing or jewelry. Keep your hair, clothing and gloves away from oscil-
lating parts so that they cannot be caught.
SIGNAL WORD Use of the Power Tool
Do not alter or misuse the tool. Any alteration or modication is a misuse and may result in serious per-
sonal injury.
NOTICE Do not use the power tool if the switch cannot be turned on and/or off. Any power tool that cannot be
controlled with the switch is dangerous and must be repaired.
NOTICE Do not leave a running CNC System and power tool unattended, turn power off. Only when a CNC router or
power tool comes to a complete stop and is disconnected from the mains it is safe.
SIGNAL WORD Mechanical Safety
Do not reach into the area of the tool. The proximity of the blade to your hand may not always be obvious.
Never reach into the working area of the Tool Length Sensor while it is in operation. Contact with moving
parts during operation can lead to incorrect zero points and can result in personal injury or damage to
property.
NOTICE Take care that the machine does not collide with the clamping xtures when dening the safety height in
your CNC control software and positioning the power tool.
SIGNAL WORD Thermal Safety
Do not touch the insertion tool after use. After usage, the blade can be too hot to be touched with bare
hands.
1.2 General Safety Warnings

7
EN
1 Tool changer board M-Series
2 Cylinder head screw M6x16 DIN912
3 STEPCRAFT EasyFix clamping nut
4 Compressed air tube 6 mm
5Tool changer switch unit
6 Compressed air hose 4 mm
7 Jack plug adapter
8 Schott connector
9 Threaded bolt AG-M3
10 Metal connector exhaust adapter
11 Intake air throttle
12 Compressed air piston
13 Lifting arm
14 Compressed air hose 3 mm
15 Tool Magazine partly pre-assembled
10
11
12
13
14
Tool Magazine partly pre-assembled
Image may differ due to different models
15
This product is constructed for private and smaller industrial applications. The Tool Magazine is only to be operated by
technically skilled persons, who are experienced in dealing with drilling/milling machines, including CNC machines or
3D-printing machines. The product has to be operated with caution – basic mechanical skills are required. The improp-
er operation of the product can lead to damage to the product and property and can cause serious injuries.
Please read these operating instructions as well as all accompanying documents in their entirety (including all relevant
documents from your CNC machine) before using this product in order to become familiar with the characteristics and
the operation of the product.
1.4 Description of Components / Scope of Delivery
1.3 Intended Scope of Use
1
2 3 4 5 6
7 98
Tool Length Sensor
Tool 1

8
EN
2 Installation of the Tool Magazine
Disconnect the plug from the power source and/or the battery pack from the power tool before making any
adjustments, changing accessories, or storing power tools. Such preventive safety measures reduce the
risk of starting the power tool accidentally.
2.2 Preparation of the CNC Machine
Move the gantry of your CNC machine to the front right. This way, you can ensure the correct length of the later to be
installed compressed air hoses. Turn off your machine and interrupt the power supply.
2.1 Required tools for the assembly
• WERA toolbox, that comes with your CNC machine
• Open-ended spanner/socket spanner 7 mm
• Pipe wrench
• Wire cutting pliers and wire strippers
• A pair of sharp scissors or a sharp knife
This chapter will lead you through the installation of the tool changer. Experience with the tools listed in chapter 2.1 is
required. The symbol highlights steps, that you can skip in case you do not own a STEPCRAFT exhaust adapter.

9
EN
Remove the Z-axis by unscrewing the four M5x8
cylinder head screws. See chapter 3.4 (construction
manual) of your CNC machine for reference. Detach
the metal connector exhaust adapter, in case you
already have installed one.
Now remove the tool holder. See chapter 1.4 (con-
struction manual) of your CNC machine for reference.
Place the Z-axis cautiously on the machine table.
2.3 Installation of the Piston into the Z-Axis
Please skip chapter 2.3 if you do not own an exhaust adapter.
Cautiously expand the arms of the lifting arm (13).
The created pretension is necessary to safely connect
the lifting arm (13) to the metal connector (10) later
on.
Thread the long black 3 mm air hose (14) from the
top through the small hole in the motor holding plate
Z-axis, to be found next to the stepper motor.
The end of the air hose is threaded through the Z-axis
prole as shown in the picture.

10
EN
Reconnect the tool holder to the Z-axis. The lifting
arm (13) and guide rods have to remain accessible.
Be careful not to squish the black air hose and make
sure it does not touch the threaded lead screw.
Fasten the four screws of the tool holder with a torque
of 3 Nm.
Slightly compress the arms of the lifting arm (13) to
t them through the slit in the metal connector (10).
Attach the metal connector (10) to the guide rods
using both M5x12 screws. You may have to hold the
guide rods with a pipe wrench to keep them from
turning.
Insert the lifting arm (13) and then the compressed
air piston (12) into the middle hole of the lower part
of the Z-axis.
The two guide rods are to be inserted into the holes on
the left and right side. The thread has to face out.
Connect the black air hose with the piston.
Now reattach the entire Z-axis. See chapter 3.2 to
3.4 (construction manual) of your CNC machine for
reference.
Please skip chapter 2.3 if you do not own an exhaust adapter.

11
EN
2.4 Installation of the Tool Magazine
Connect the black 4 mm air hose (6) to the free con-
nection of valve
V2
.
Check for good t by gently pulling the air hose.
To make sure not to confuse the cables, you should mark the cables of the
right valve (closer to tool length sensor) V2. Mark the cables of left valve
as V1 and the Tool Length Sensor with
TLS.
Connect the supplied 6 mm air hose (4) to the upper
connector of valve
V1
. The long 6 mm air tube (be-
longing to the tool changer) has to be connected to
the lower connector of
V1
.
Check for good t by lightly pulling the air hoses.
Your Tool Magazine is ready for assembly now.
6 mm air hose (4)6 mm air hose (4)
6 mm air hose of6 mm air hose of
tool changertool changer

12
EN
Remove the control cover of your CNC machine. See
chapter 3.3.1 (construction manual) of your CNC
machine for reference.
In order to assemble the Tool Magazine, remove the
last panel of your machine table. Unscrew the STEP-
CRAFT EasyFix nuts and lift the panel In case you
have an MDF machine table, you will have to addi-
tionally remove the last T-slot prole. See chapter
4.0 (construction manual) of your CNC machine for
reference.
Place the Tool Magazine onto your machine table. Be
sure the tool magazine cannot fall down.

13
EN
Take the tool change cover off the control holding plate (larger one) and
drill a 6 mm hole right into the middle. Drill another 3 mm hole as shown.
Feed all cables coming from the Tool Magazine
through the small hole in the rear panel of your CNC
machine. Now feed all the air hoses through the large
hole in the rear panel of your CNC machine.
Fix the Schott connector (8), using the counter nut, in
the smaller hole of the control holding plate.
88
Secure the short 6 mm air hose (4) to the Schott
connector (8). Check for good t by lightly pulling the
air hose.
4488
Connect the 4 mm air hose (6) to the black side of the
intake air throttle (11). Check for good t by lightly
pulling the air hose.
1111
66

14
EN
Thread the long 6 mm air hose and the Tool Length Sensor (TLS)
cable through the large hole of the control holding plate. Feed
the long 6 mm air hose and the TLS cable through the drilled
holes, just as shown.
Feed the black 3 mm air hose through the
remaining 3 mm hole.
Connect the black 3 mm air hose (14) to the intake air throttle (11).
Check for good t by lightly pulling the air hose.
1111
1414
2.5 Connection of the Electrical Components
In case you already own a STEPCRAFT LED Set,
release its power supply cables from the 30V termi-
nal on the machine control mainboard. Later on, the
LED Set’s power supply will be provided via the tool
changer board (1).
Cut approximately 10 cm from the
V1
cable pair.
Remove the insulation as shown.

15
EN
Now connect the cable pair to the
30V
terminal on
the machine control mainboard.
Clamp the black cable to the minus, and the red cable
to the plus terminal.
Connect the other end of the cable pair to the
30V in
terminal on the tool changer board (1).
Clamp the black cable to the minus, and the red cable
to the plus terminal.
Pay attention to the polarity!
In case you already own a STEPCRAFT LED-Set, con-
nect its power supply cables to the
30V out
terminal
on the tool changer board (1).
Clamp the wire cable to the minus, and the red wire
to the plus terminal.
Pay attention to the polarity!

16
EN
Remove the screw next to the label
S1
on the ma-
chine control board. This screw will be reused to
mount the tool changer board (1) later on.
Now screw the threaded bolt (9) into the screw hole
next to the label
S1
on the machine control board.
Insert the tool holder board (1) into the extension
socket (labeled
SV4
) on the machine control board.
Secure the tool changer board (1) with the previously
removed screw.

17
EN
The emergency stop switch can only effect the stop of all components if these components are electroni-
cally connected with the emergency stop switch.
Release one of the clamps of the emergency switch
wires. Now attach this cable to the
GND
terminal on
the tool changer board (1).
Connect the
V1
wires to the
V1
terminal on the tool
changer board (1).
Pay attention to the polarity!
Connect the
V2
wires to the
V2
terminal on the tool
changer board (1).
Pay attention to the polarity!
V2V2 V1V1
Check your machine control board for a two-pole connection between the
two jack sockets (labeled WLZ). Proceed with the instructions as follows.

18
EN
Connector does not exist Connector exists
Plug the Tool Length Sensor cable onto the
machine control board as shown.
Connect the jack plug adapter (7) with the plug of
the Tool Length Sensor cable. The plugs lock percep-
tibly.
Now lead that cable out of the control holding plate
as shown.
Insert the jack plug into one of the
probe sockets.
2-pole WZL Connector

19
EN
Unscrew the vision panel from the control cover.
The tool changer switch unit (5) holds a three-pole
plug. Connect this plug to the tool changer board (1)
as shown. The pins are labeled
JP3
.
It is important that the jumper stays connected exact-
ly as shown in the image!
Take the two-pole plug of the tool changer switch unit
(5) and connect it to the tool changer board (1) as
shown. The pins are labeled
Mode 1.
The black cable has to face the edge of the tool
changer board (1). Pay attention to the polarity!
Replace the vision panel with the tool changer switch
unit (5). Pay attention to the alignment of the switch.
It should face the center of the machine, thus allow-
ing you to see the status signal of your controller.

20
EN
To perform these steps the tool magazine has to be fully assembled. Start your CNC software.
Now perform the following three test scenarios:
• Set the switch of the tool changer switch unit (5) to position O
Turn on the spindle in your CNC software. The piston (12) should release the metal connector (10). Now
open the collet using your CNC software. The tool changer should react.
• Set the switch of the tool changer switch unit (5) to position –
Turn on the spindle in your CNC software. The piston (12) should NOT release the metal connector (10). Now open
the collet using your CNC software. The tool changer should react.
• Set the switch of the tool changer switch unit (5) to position =
Turn on the spindle in your CNC software. The piston (12) should NOT release the metal connector (10). Now open
the collet using your CNC software. The tool changer should NOT react.
Should any one of these tests show unexpected behavior, check all sockets and connections.
If the tests are successful, continue with the next step.
The power supply has to be connected to the CNC machine before its connected to the power grid. Other-
wise there is a chance of damaging the electronics of your CNC machine.
Be sure to test the functionality of the emergency switch before using the machine. The switch has to be
capable of stopping the entire machine in case of an emergency!
2.6 Function check
In order to perform the function testing, your CNC machine has to be fully operational. A power and compressed air
supply is required. Test the emergency switch!
Reattach the control cover.

21
EN
Position –The Tool Magazine operates without the automatic lift.
Position OAll functions are available.
Position =All functions of the Tool Magazine are deactivated.
This mode is recommended for jobs that do not require an exhaust adapt-
er.
The Tool Magazine’s functions as well as the automatic lift of the exhaust adapter
are activated.
This mode is recommended when you are not using the Tool Magazine e.g. working
with a tangential knife or a laser.
The tool changer switch allows you to adjust the Tool Magazine to prefectly t your job requirements. The base position
of the switch is
0
, with all functions active.
3.1 Tool Changer Switch
3 Operation
The machine and all connected components have to be wired correctly and be in perfect condition.
The operator must have completely read and understood the entire documentation of the M-Series and corresponding
instructions. Furthermore, he has to be familiar with the use of CNC gantry milling systems and CNC software.
NOTICE All persons who operate the power tool must have read and fully understood all relevant safety and operat-
ing instructions. Misunderstandings may result in personal injury.
This chapter will walk you through the necessary steps which need to be followed in order to activate the Tool Magazine
in UCCNC. These steps assume that your Tool Magazine already has been assembled correctly.
Download the necessary macro les from this source:
https://www.stepcraft-systems.com/download/macros_atc_uccnc.zip
3.2 Software setup
Table of contents
Other STEPCRAFT Power Tools manuals
Popular Power Tools manuals by other brands
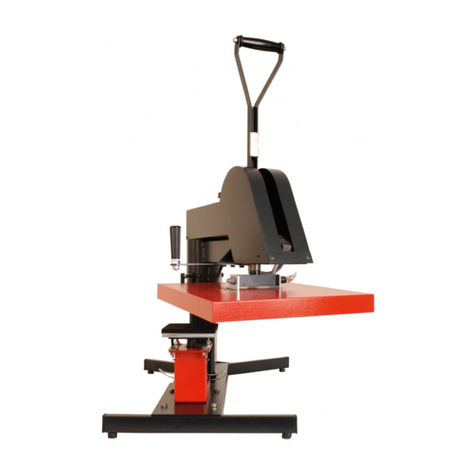
Lotus Press
Lotus Press LTS 140 Slide operating instructions
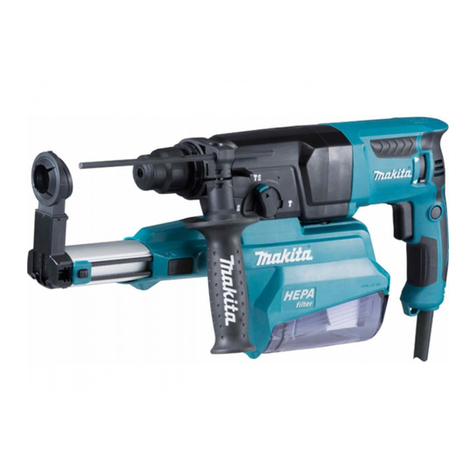
Makita
Makita HR2650 instruction manual

Westfalia
Westfalia 17 16 94 instruction manual

Makita
Makita 5093DZ instruction manual
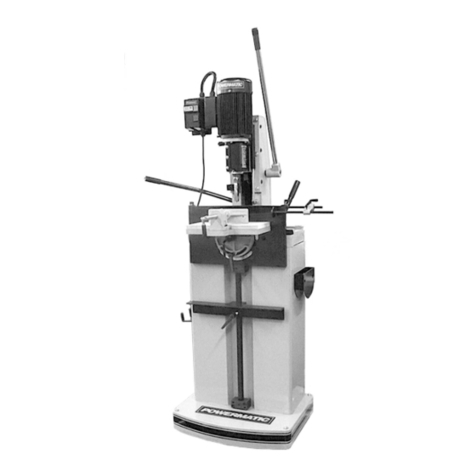
Powermatic
Powermatic 720HD Operating instructions and parts manual
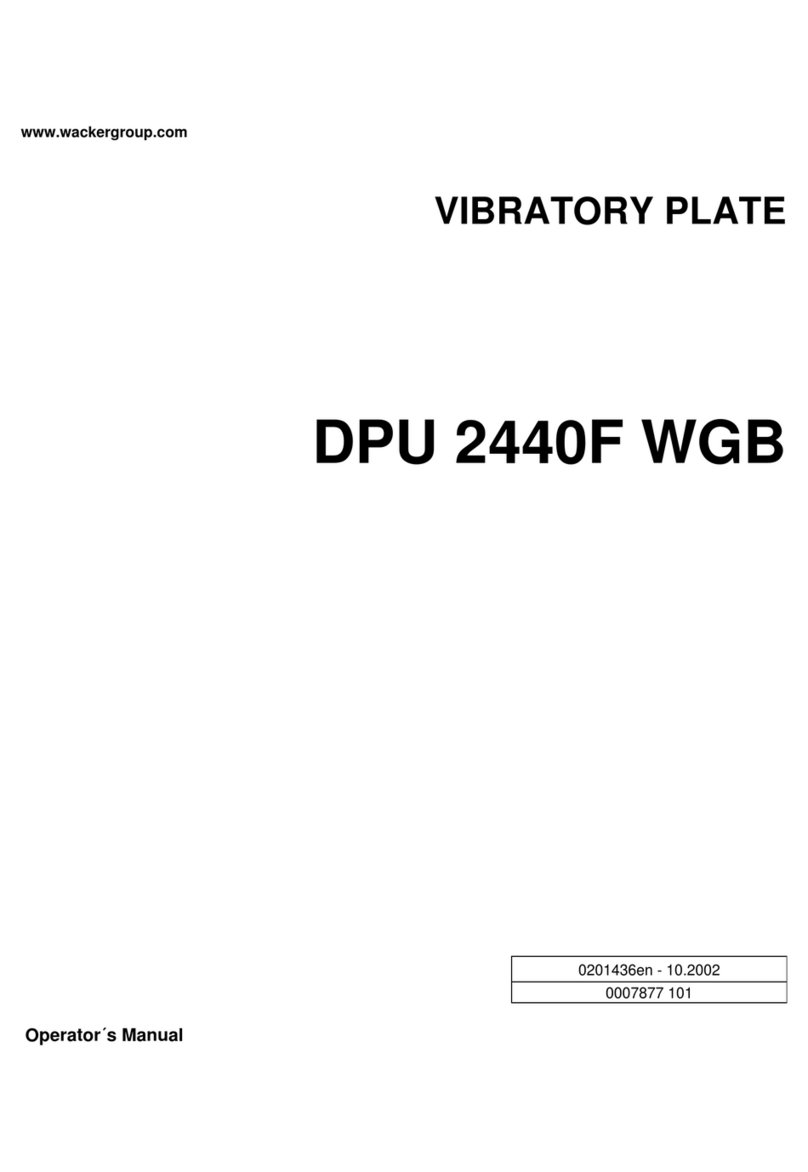
Wacker Neuson
Wacker Neuson DPU 2440F WGB Operator's manual