CTI 2500P-J Series Operating instructions

CTI Janus Programmable Automation Controller IOG 1
CTI 2500P-Jxxx
Janus Programmable Automation Controller
Installation and Operation Guide
Version 1.01

2 CTI Janus Programmable Automation Controller IOG
Copyright 2020 Control Technology Inc.
All rights reserved.
This manual is published by Control Technology Inc. (CTI) 5734 Middlebrook Pike, Knoxville, TN 37921. This manual
contains references to brand and product names which are trade names, trademarks, and/or registered
trademarks of Control Technology Inc. Siemens®and Series 505®are registered trademarks of Siemens AG. Other
references to brand and product names are trade names, trademarks, and/or registered trademarks of their
respective holders.
DOCUMENT DISCLAIMER STATEMENT
Every effort has been made to ensure the accuracy of this document; however, errors do occasionally occur. CTI
provides this document on an “as is” basis and assumes no responsibility for direct or consequential damages
resulting from the use of this document. This document is provided without express or implied warranty of any
kind, including but not limited to the warranties of merchantability or fitness for a particular purpose. This
document and the products it references are subject to change without notice. If you have a comment or discover
an error, please call us at 1-800-537-8398 or email us at sales@controltechnology.com.

CTI Janus Programmable Automation Controller IOG 3
REVISION HISTORY
V1.0
4/28/2020
Initial Release
V1.01
5/20/2020
Corrected typos and improved formatting.
Added details to battery installation (Section 3.2.4)

4 CTI Janus Programmable Automation Controller IOG
PREFACE
This Installation and Operation Guide (IOG) provides information regarding installation, setup, and operation of
the CTI Janus Programmable Automation Controller, also referred to as the Janus Controller in this manual.
This document is not intended to serve as a programming reference for application development. A
comprehensive and thorough programming reference for application development is provided by the Janus
Workbench online help system. This online help is critical for gaining an initial understanding of the product and is
intended to be used as a reference for various aspects of the products features. The online help search feature
provides for a quick way locate targeted information.

CTI Janus Programmable Automation Controller IOG 5
USAGE CONVENTIONS
NOTE
Notes alert the user to special features or procedures.
CAUTION
Cautions alert the user to procedures that could damage equipment.
WARNING
Warnings alert the user to procedures that could damage equipment and endanger the user.


CTI Janus Programmable Automation Controller IOG 7
TABLE OF CONTENTS
PREFACE .............................................................................................................................................. 4
USAGE CONVENTIONS....................................................................................................................... 5
TABLE OF CONTENTS........................................................................................................................ 7
CHAPTER 1 INTRODUCTION........................................................................................................ 10
1.1 Janus Controller Overview.....................................................................................................10
1.2 Janus Programming Software................................................................................................12
CHAPTER 2 FRONT PANEL.......................................................................................................... 13
2.1 Status Indicator LEDs............................................................................................................. 13
2.2 Alphanumeric Display.............................................................................................................13
2.3 Battery..................................................................................................................................... 14
2.4 Ethernet Communications Ports............................................................................................ 14
2.5 External SD Card Slot ............................................................................................................15
2.6 Clear Exception Pushbutton................................................................................................... 15
2.7 Remote I/O Port...................................................................................................................... 16
2.8 Profibus DP Port.....................................................................................................................16
CHAPTER 3 INSTALLATION ......................................................................................................... 17
3.1 Installation Planning................................................................................................................17
3.1.1 Safety Considerations.................................................................................................. 17
3.1.2 Electrical Interference................................................................................................... 18
3.1.3 Grounding..................................................................................................................... 18
3.1.4 Choosing the IP Address and related Parameters...................................................... 18
3.1.5 Power Requirements....................................................................................................18
3.1.6 SD Card Selection........................................................................................................ 19
3.2 Installing the Controller........................................................................................................... 19
3.2.1 Unpacking the Module .................................................................................................19
3.2.2 Internal SD Card Installation........................................................................................20
3.2.3 Setting the Module Switches........................................................................................ 21
3.2.4 Inserting the Battery.....................................................................................................22
3.2.5 Physical Installation...................................................................................................... 23
3.2.6 Connecting the Controller to a Data Network..............................................................23
3.2.7 Applying Power to the Base......................................................................................... 23
3.2.8 Startup from Factory Defaults......................................................................................23
3.2.9 Setting the IP Address..................................................................................................24
CHAPTER 4 CONFIGURATION..................................................................................................... 27
4.1 General Settings.....................................................................................................................27
4.2 Network Settings..................................................................................................................... 28
4.2.1 IP Parameters............................................................................................................... 28
4.2.2 DNS Configuration .......................................................................................................28
4.2.3 Internal Ethernet Switch Configuration........................................................................28

8 CTI Janus Programmable Automation Controller IOG
4.3 Security Settings..................................................................................................................... 29
4.4 Clock Settings......................................................................................................................... 30
CHAPTER 5 OPERATION .............................................................................................................. 31
5.1 Controller Operation Overview............................................................................................... 31
5.2 Controller Startup.................................................................................................................... 33
5.3 Clear Exception Pushbutton Operation .................................................................................34
5.4 HTTP Data Server..................................................................................................................35
CHAPTER 6 UPDATING FIRMWARE............................................................................................ 37
6.1Overview.................................................................................................................................37
6.2 Front Panel SD Card Firmware Update................................................................................. 37
6.3 Remote Firmware Update...................................................................................................... 38
6.4 Direct File Replacement......................................................................................................... 39
CHAPTER 7 LEGACY I/O SUPPORT............................................................................................ 41
7.1 RS-485 I/O Support................................................................................................................41
7.1.1 CTI 2500 Series I/O Support........................................................................................41
7.1.2 Siemens 505 and Series 500 I/O Support...................................................................41
7.1.3 Connecting to Remote I/O ...........................................................................................42
7.1.4 Dual RBC Support........................................................................................................45
7.1.5 Configuring Local and Remote I/O.............................................................................. 45
7.2 Profibus DP I/O.......................................................................................................................46
7.2.1 Connecting to the Profibus Network............................................................................46
7.2.2 Configuring a Profibus DP Network............................................................................. 48
CHAPTER 8 JANUS PAC MODELS.............................................................................................. 49
APPENDIX A: SYSTEM ERROR CODES......................................................................................... 51
CPU Startup Errors .......................................................................................................................51
Controller Startup Errors ...............................................................................................................52
Firmware/Configuration Update Errors......................................................................................... 53
Execution Errors............................................................................................................................ 54
SD Card Errors.............................................................................................................................. 54
I/O Subsystem Errors.................................................................................................................... 55
Profibus Network Errors................................................................................................................ 56
Client Communication Errors........................................................................................................ 56
Hardware Errors............................................................................................................................ 58
APPENDIX B: IP ADDRESS INFORMATION................................................................................... 59
IP Address Nomenclature.............................................................................................................59
Using the Subnet Mask.................................................................................................................61
CIDR Notation................................................................................................................................62
Selecting an IP Address................................................................................................................ 62
Selecting a Multicast Address....................................................................................................... 63
APPENDIX C: ETHERNET PORT OPERATION............................................................................... 65
Ethernet Port Operation................................................................................................................65
Alternate IP Subnets ..................................................................................................................... 66
APPENDIX D: PRODUCT SPECIFICATIONS .................................................................................. 68
Environmental Specifications........................................................................................................ 68
Battery Specifications.................................................................................................................... 69
Agency Approvals..........................................................................................................................69

CTI Janus Programmable Automation Controller IOG 9
LIMITED PRODUCT WARRANTY..................................................................................................... 70
REPAIR POLICY .................................................................................................................................72

10 CTI Janus Programmable Automation Controller IOG
CHAPTER 1
INTRODUCTION
1.1 Janus Controller Overview
The CTI Janus Process Automation Controller (PAC) is an advanced, high-performance CPU with unmatched built-in
communications capabilities. All CPU models provide a number of beneficial features.
Flexible Programming Support
The Janus controller allows you to program in languages that best fit your application requirements and your
programming expertise. The following IEC 61131-3 compliant languages are supported:
Relay Ladder Logic (RLL)
Function Block Diagram (FBD)
Structured Text (ST)
Sequential Function Chart (SFC)
Instruction List (IL)
A single project can contain programs written in different languages. Programs written in one language can be
easily translated to another language to help with long term application support.
Integrated Ethernet Communications
Extensive communications support is included in the Janus controller, eliminating the need for separate
communications modules. The controller provides four isolated Ethernet ports, any of which can be used to
provide redundant network paths or to connect to different networks. The controller can be configured with
multiple IP addresses and communicate concurrently on up to four different IP networks.
Ethernet Data Communications Protocols
The controller supports the following data communications protocols:
CAMP Client (used to communicate with CTI 2500 Series CPUs and Ethernet modules)
CAMP Server (allows data access from HMI/SCADA workstations using CAMP Client drivers
CTI Enhanced Data Cache Client (optimized interface to CTI 2500 Series CPUs)
Ethernet I/P Tag Client (used to communicate with Rockwell Logix controllers)
Ethernet I/P Server (allows data access from HMI/SCADA workstations using Tag Client drivers)
MQTT Client (support for IIOT (Industrial Internet of Things).
Custom TCP/UDP client and server applications using network socket management functions
Ethernet I/O Protocols
The controller supports:
Open Modus Client (TCP or UDP)
Open Modbus Server (TCP or UDP)
Ethernet I/P Scanner (supports Implicit I/O messages and CIP Explicit messages)
Ethernet I/P Adapter (provides an interface for EIP I/O Scanners and CIP Explicit Message Clients)
Profinet Controller I/O support is planned for the near future

CTI Janus Programmable Automation Controller IOG 11
Web Server Interface
The controller contains an embedded web server, which provides an interface to detailed information regarding
the controller configuration, operation, and history. The web server can be used to:
Obtain information about the product and application
Configure the product settings
Update product firmware
Perform file transfer operations
Access user-generated graphics pages (monitor and control application)
View diagnostic information (such as error and status info)
Access operational statistics
View Event Log
Supports user created web pages that access controller application data. (See Section 5.4 HTTP Data
Server).
The web server can be accessed by entering the controller IP address in the URL box of your browser.
Online Change Support
The controller supports a comprehensive change facility that allows you to make extensive changes to the user
program, then download the changed program without bumping the I/O. See the Janus Workbench Help for
detailed information and limitations.
Security
The controller employs a Secure Boot technology, which ensures the firmware loaded to the controller is an
authenticated CTI version. Access to the application program (using Workbench) and access to the web server can
be configured to require username/password authentication. You can also enable encryption between a web
browser and the controller web server.
Compatibility
The Janus Controller is designed to work in the same plant environment as the CTI 2500 Series PLC, supporting
many of the legacy interfaces. It is compatible with existing CTI 2500 Series and Siemens Series 505 local and
remote I/O and Profibus-DP I/O. It can function as an Ethernet CAMP server, allowing it to communicate with
existing HMI/SCADA workstations and CTI 2572/2572-A/2572-B communications modules. It can also act as a
CAMP client for peer-to-peer communications to existing CTI products. The Enhanced Data Cache Client protocol
facilitates high speed communications with CTI 2500 Series PLCs.
High Performance
All Janus Controllers are powered by an ultra-high performance SoC (System on Chip) with ARM®+ FPGA
architecture providing extreme I/O bandwidth with low system power requirements. This architecture provides
capability to simultaneously execute logic and I/O communications which translates to sub-millisecond cycle times
for many small applications.

12 CTI Janus Programmable Automation Controller IOG
1.2 Janus Programming Software
The Janus Controller is programmed using Janus Workbench. Janus Workbench is a full-featured Integrated
Development Environment (IDE) tool that includes a configuration tool, programming editor, debugger, data
monitor, and simulator. The application program may be developed in any of five IEC-61131 programming
languages. A complete library of functions is provided to perform the following tasks:
Complex mathematical computations
Boolean logic
Data conversion
String handling
Timer/Counter operations
PID control
Alarm monitoring
Data Logging and file access functions
Protocol driver management
The programming architecture enables the “building block” approach to application design which encourages the
re-use of well-documented and proven code sections. Custom logic using complex data types such as structures
and enumerations can be embedded into Sub-Programs and User Defined Function Blocks (UDFBs) and re-used in
multiple applications.
Janus Workbench also provides a means to select and configure fieldbus drivers supported by the controller.
For more information, refer to the Janus Workbench Help system.

CTI Janus Programmable Automation Controller IOG 13
CHAPTER 2
FRONT PANEL
2.1 Status Indicator LEDs
2.2 Alphanumeric Display
The Alphanumeric Display is used to display IP parameters (i.e. IP addresses and subnet
information) and active error status information. If desired, the display of IP
parameters can be disabled using the embedded web server. When an error state is
active, the corresponding error code is displayed. When multiple error states are
active, the highest priority active error code is displayed. See APPENDIX A SYSTEM
ERROR CODES for a list of system error codes and descriptions.
LED
Color
State
Indication
CPU GOOD
BLUE
Off
Not operational –module initialization
failure or no power
Flash
N/A
On
Module hardware/firmware passed all
power-on tests and operation is normal
RUN
BLUE
Off
Application program stopped or not loaded
Flash
Program loaded but logic is not running
(LOGIC STOP state).
I/O interface and communication protocols
are active.
On
Application program is executing (RUN
state)
ERROR
YELLOW
Off
No active errors
Flash
Critical error that prevents application from
entering RUN mode (Error Code displayed
on front panel)
On
After software boot, indicates active error
conditions. These errors can occur while in
RUN mode and will not prevent application
from transferring to RUN mode.
(Error Code displayed on front panel)
On initial power up, this signals that the
hardware is powered and ready for
software boot.

14 CTI Janus Programmable Automation Controller IOG
2.3 Battery
A replaceable high-power Lithium Metal Oxide battery provides an auxiliary power source to provide an orderly
system shutdown when DC power from the backplane is lost while the controller is in RUN state. The battery is
accessible through the front panel battery cover and can be replaced while the application is running.
The battery circuit is automatically enabled when the backplane power is removed. After a successful shutdown,
the battery circuit is disabled to preserve battery life. See Section 3.2.4: Inserting the Battery for instructions
regarding battery installation and care.
2.4 Ethernet Communications Ports
The RJ-45 Ethernet ports, labeled PORT A, PORT B, PORT C, AND PORT D, are identical in their operation and usage.
Each port is capable of operating at 1000Mb (1Gb) full duplex. If connected to a device that does not support 1Gb
data rates, a port will auto-negotiate a slower speed (10Mb or 100Mb) with the device. All ports can be used for
multiple purposes, such as programming and monitoring, data communications with SCADA workstations and
other devices, and Ethernet I/O. Duplicate IP Address detection, broadcast/multicast storm protection and traffic
rate limiting are enabled for each port.
By default, Ethernet frames arriving at a port are forwarded only to the controller microprocessor. Ethernet frames
are not forwarded between the ports, preventing the accidental creation of loops. If ports are connected to
different networks, this behavior prevents traffic on a network from entering the other networks. To allow for
special situations, forwarding between ports can be enabled in the web server CONFIGURATION/NETWORK SETTINGS
page. See Section 4.2.3 Internal Ethernet Switch Configuration.
Each Ethernet port connector contains two embedded LEDs. The LINK LED (top) indicates whether the Ethernet
port is successfully connected to another Ethernet device, such as a network switch. The ACTIVITY LED (bottom)
provides visual indication that Ethernet packets are being received or transmitted via the port. See the following
table below for details.
LED
State
Indication
Link
Off
Ethernet link is not available.
On
Ethernet link is available.
Act
(Activity)
Off
No Ethernet frames are being transmitted on the network to
which the port is connected.
On
(Blinking)
Ethernet frames are being transmitted on the network to
which the port is connected

CTI Janus Programmable Automation Controller IOG 15
2.5 External SD Card Slot
The front panel contains a receptacle for a full-size SD card. Standard (SD) and high capacity (SDHC) memory cards
may be used. This SD card is not required for controller operation, and no logic instructions will access (read or
write data) from this card. A bicolor STATUS LED, mounted in the front panel indicates the following conditions:
OFF: No SD card is inserted
GREEN: An SD card is inserted into the receptacle but it is not being accessed by the controller firmware.
When this condition exists, the card can be removed.
RED: The firmware is accessing the SD card (reading or writing). When this condition exists, you should
not remove the card. Removing the card will corrupt the data on the card.
This card has three primary uses as described below:
a) SD Card Ethernet Port Setup provides a method for the user to specify a fixed IP Address when the
controller has not been configured (i.e. on initial power-up or after configuration reset). This operation
executes only if Module Switch 2 = OPEN and Module Switch 4 = CLOSED. See SD Card Ethernet Port
Setup 3.2.9 for more information.
b) SD Card Firmware Update provides an alternate method for firmware update when Remote Firmware
Update is not allowed or connection from Janus Workbench is inconvenient. The SD Card Firmware
Update method is initiated on startup when Module DIP Switch 2 is set to CLOSED position. See Front
Panel SD Card Firmware Update for additional information.
c) File Operations allows you to transfer files between the internal SD card and the external SD card and/or
PC. For example, you could use this facility to backup controller system and/or application files while the
application is running. These operations can be selected via the web server File Management page.
2.6 Clear Exception Pushbutton
When enabled, the CLEAR EXCEPTION pushbutton provides a direct method to clear exceptions, reset controller
configuration values to default values, or restore factory defaults without requiring access to Janus Workbench or
the controller web server. See Section 5.3 for more information.
NOTE
The recessed pushbutton will function only when Switch 3 is in the CLOSED position.
See Section 3.2.3 Setting the Module Switches

16 CTI Janus Programmable Automation Controller IOG
2.7 Remote I/O Port
This DB-9 connector (labeled ‘Remote I/O’) provides the RS-485 serial interface to the legacy 505/2500 Remote
I/O network. The pinout for this connector is shown below:
2.8 Profibus DP Port
On models where the controller can be configured as Profibus master, this DB-9 connector (labeled ‘Profibus-DP’)
provides the RS-485 interface to the Profibus-DP network. The pinout for shown below. The cable shield is
connected to ‘Chassis Ground’. Pins 5-6 are used for the bias circuit.

CTI Janus Programmable Automation Controller IOG 17
CHAPTER 3
INSTALLATION
This section discusses the items to consider while planning the Janus Controller installation and the actual steps for
installation of the module.
3.1 Installation Planning
3.1.1 Safety Considerations
Before installing the controller, you must identify the personnel hazards that may be created in the event of a
system failure and provide interlocks and safety switches to prevent operation during a system failure.
WARNING
As a system designer, you should be aware that Control devices can fail in an unsafe condition. Unless you
incorporate proper safeguards, malfunction of the controller or associated devices, such as operator
interface equipment, could cause sudden equipment startup, shutdown, or other unexpected operation.
Such startup or shutdown or unexpected operation could result in death or serious injury to personnel,
and/or damage to equipment.
If you or your company are using CTI controllers with processes or equipment that requires the presence of
a person (such as an operator or attendant), you should be aware of this potential safety hazard and take
appropriate precautions.
Safety Recommendations
Consideration should be given to the use of an emergency stop function which is independent of the
programmable controller. Where the operator is exposed to the machinery, such as in loading or unloading a
machine tool, or where the machine cycles automatically, consideration should be given to the use of an
electromechanical override or other redundant means for stopping the machine cycle. If provision is required for
changing programs while the equipment is in operation, consideration should be given to the use of locks or other
means of assuring that such changes can be made only by authorized personnel. These recommendations are
intended as safeguards against the failure of critical components and the effects of such failures or the inadvertent
errors that might be introduced if programs are changed while the equipment is in operation.
Operator Safety Switches
Power should be configured so that it can be manually removed from all output devices. You must provide a
method that is independent of the control system for disconnecting power from the outputs when a machine is
not operating or the operator must reach into the machine. A non-electronic switch or directly wired relay must be
used to disconnect the power.
Emergency Stop Switch
You must provide a method for disconnecting power from the outputs if an emergency situation is encountered
with the machine operation. Use a non-electronic switch or relay that is wired external to the controller and that is
easily accessible.

18 CTI Janus Programmable Automation Controller IOG
3.1.2 Electrical Interference
Electrical interference conducted directly through wiring or inducted via electromagnetic coupling can adversely
affect the operation of control equipment. The major sources of electrical interference in an industrial
environment are devices that use high voltages and current, such as motors and welders.
The Janus Controller is designed to meet or exceed IEC standards for immunity to electrical interference. However,
care must be taken to ensure the control equipment is exposed to devices that serve as major sources of electrical
interference devices. To ensure a reliable control system, you will need to determine the source of the electrical
interference and employ suitable techniques to reduce its effect on the control system.
3.1.3 Grounding
It is very important that the all equipment is properly grounded. Lack of proper grounding may cause intermittent
or erratic operation or may cause the control system to fail. A properly installed grounding system will provide a
low-impedance path to earth ground, which will give all PLC internal filtering devices a good ground return for
reference. The earth ground of the building site typically provides reliable grounding; however, if excessive ground
current is present, a separate grounding electrode should be installed.
A common practice is to provide a central ground bus bar as a single point of reference within each enclosure,
connecting all chassis and power supply components to the bus bar. The bus bar is then connected to earth
ground. When connecting to the bus bar, use 1-inch copper braid or No. 8 AWG wire. To ensure good connections,
scrape paint or other non-conductive coatings away from mounting studs and from enclosure surfaces where
mounting bolts and washers make contact.
In addition to connecting the controller chassis and power supply to earth ground, you must ensure that the power
supply, controller and all modules installed in the base are installed securely and that the thumbscrews are
tightened.
3.1.4 Choosing the IP Address and related Parameters
Before you can use the Ethernet port, the controller must be configured with network parameters, including IP
address, network mask, and the default gateway. If you already have a network installed, you should contact your
network administrator to determine the values to be used. See APPENDIX B: IP ADDRESS INFORMATION for more
information on choosing an IP address. See Section 3.2.8 and Section 3.2.9 for information on setting the network
parameters.
3.1.5 Power Requirements
The Janus controller consumes 10 watts of +5 VDC power. To calculate the total power required for the base, you
need to add the power requirements for the other modules you will install in the base.

CTI Janus Programmable Automation Controller IOG 19
3.1.6 SD Card Selection
Size
There are three sizes of SD cards: standard, mini, and micro. The SD card receptacles on the Janus controller are
designed for a standard size card. A passive adapter can be used to accommodate the smaller mini or micro sizes,
if necessary.
Capacity
The Janus controller accepts standard SD cards and high capacity SDHC cards. SD cards, which have a maximum
capacity of 2 GB, are an older technology that may not be readily available. SDHC cards have a maximum capacity
of 32 GB and are widely available. For most applications, an SDHC card with a capacity of 16GB is sufficient.
Speed
The SD card access speed is indicated by a class rating, which indicates the minimum continuous write speed. For
example, a class rating of indicates 4 MB/sec. Class 4 SD or SDHC cards are usually sufficient for use in the front
panel SD receptacle. However, an SDHC card with a class rating of is required for the internal SD card.
3.2 Installing the Controller
3.2.1 Unpacking the Module
Open the shipping carton and remove the special anti-static bag that contains the module. Ensure you are properly
grounded and have discharged any static buildup before removing the unit from the static bag.
Do not discard the anti-static bag; use it for protection against static damage when the module is not inserted into
the I/O base.
CAUTION
The components on the Janus controller printed circuit card can be damaged by static electricity
discharge. To prevent this damage, the module is shipped in a special anti-static bag. Static
control precautions should be followed when removing the module from the bag and when
handling the printed circuit card during configuration.

20 CTI Janus Programmable Automation Controller IOG
3.2.2 Internal SD Card Installation
The Janus controller uses a Secure Data (SD) card for storage of configuration data, executable program,
application program source files, and user data files. A high capacity SDHC card is pre-installed on all units shipped
from the factory. Contact CTI support if the SD card is missing. Because all configuration and operational files are
contained on the SD card, the complete controller profile can be transferred to another unit simply by swapping
SD cards.
The receptacle for the internal SD card is located on the controller circuit board as shown in the following picture.
To remove and replace the internal SD card:
Remove power to the base.
Remove the controller from the base.
To remove the card, apply insertion pressure until you hear a click, then release pressure.
To install the card, insert the card in the receptacle face up, with the beveled edge facing the receptacle.
Continue insertion until you hear a click, then release.
NOTE
A replacement SD card must have a write speed rating of at least 10 MB/s (Class 10). CTI recommends you
purchase an SD card with an industrial rating.
Switches
SD Card
Receptacle
This manual suits for next models
1
Table of contents
Other CTI Controllers manuals
Popular Controllers manuals by other brands
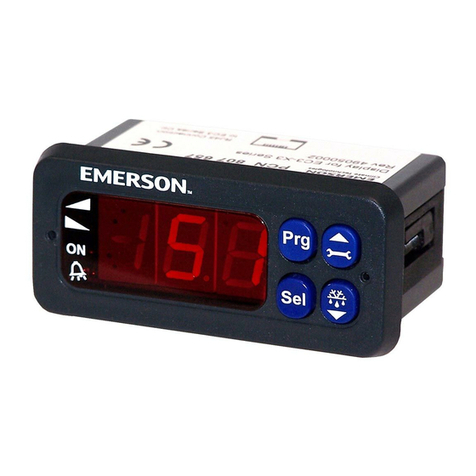
Emerson
Emerson ECD-002 operating instructions
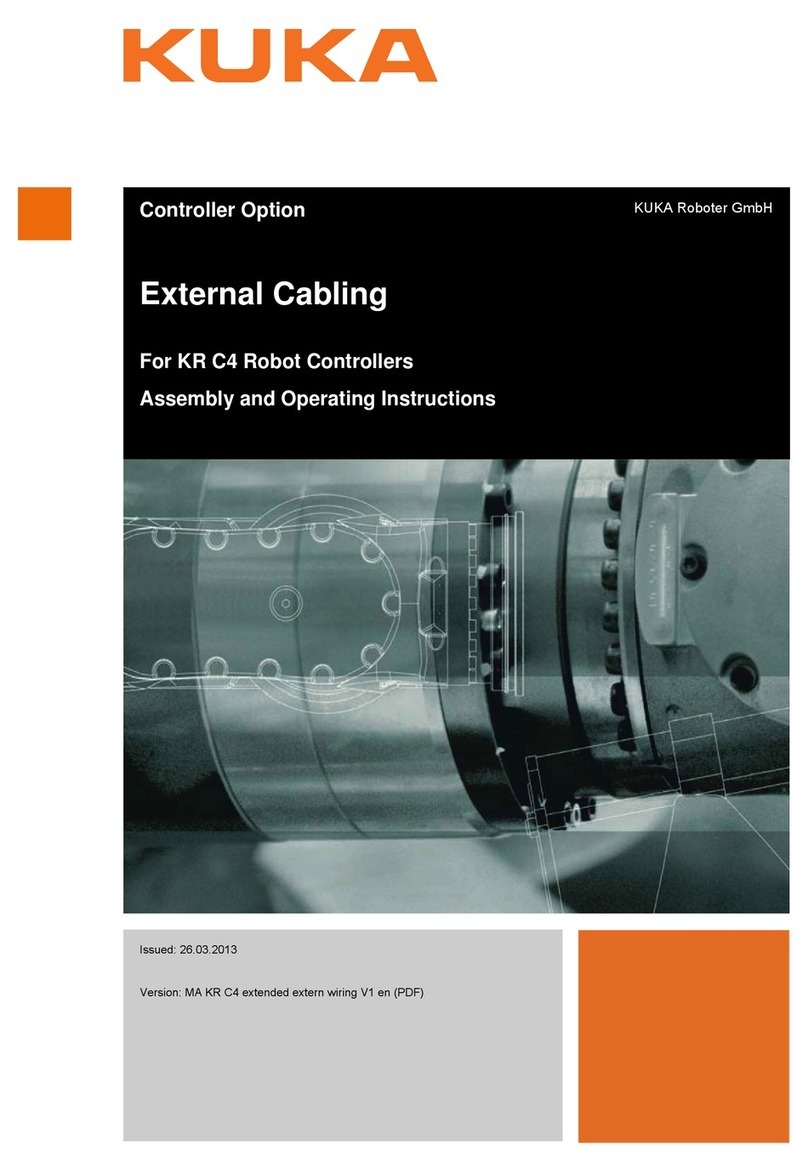
Kuka
Kuka KR C4 compact Assembly and operating instructions
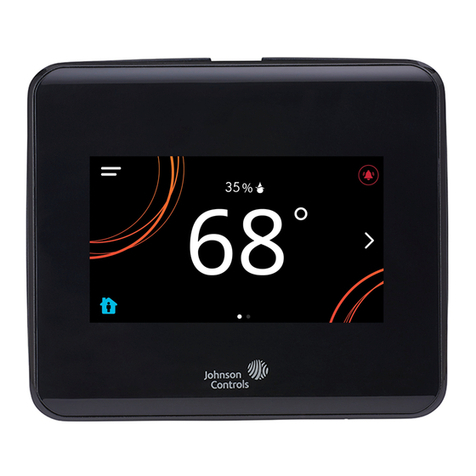
Johnson Controls
Johnson Controls TEC3000 Series quick start guide

Greenwood Air Management
Greenwood Air Management GRF1 manual
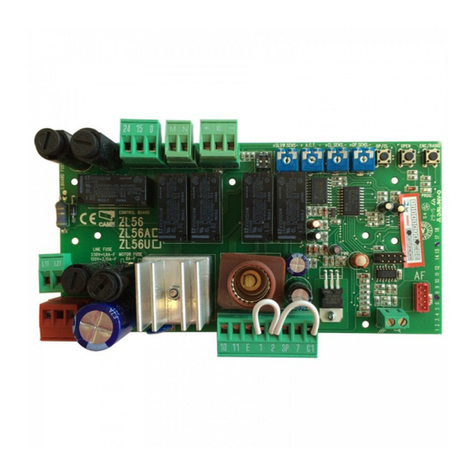
CAME
CAME ZL56 Original-spare parts
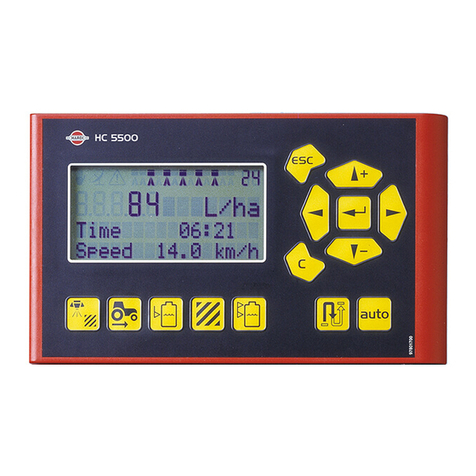
Hardi
Hardi COMMANDER 5500 Instruction book