DEELAT D1140772 User manual

Ultrasonic Thickness
Gauge and Meter |
D1140772 • D1141137
User Manual
WWW.DEELAT.COM

User ManualUser Manual
Ultrasonic Thickness Gauge and Meter |D1140772 • D1141137 Ultrasonic Thickness Gauge and Meter |D1140772 • D1141137
ULTRASONIC THICKNESS GAUGE AND METER | D1140772 • D1141137
- 2 -
ULTRASONIC THICKNESS GAUGE AND METER | D1140772 • D1141137
- 3 -
1.1. Scope of application
1. Introduction
Deelat’s Ultrasonic Thickness Gauge is a handheld measurement device that measures the thickness
of most common industrial materials. In order to measure the thickness, it uses a microprocessor
to emit a sound pulse and measure the amount of time it takes for the pulse to return a probe to the
device.
It is commonly used in operations where the thickness of a container or pipe might decrease due to
usage with certain media or when under pressure. The thickness must then be measured to ensure
safety of operation.
It is also used in manufacturing processes where these container or pipes are being built to ensure
the correct thickness has been achieved.
Deelat’s Ultrasonic Thickness Gauges are suitable for measuring materials that conduct ultrasonic
waves such as metal, plastic, ceramic, glass and also as long as the measured part is presented in two
parallel surfaces to measure the thickness.
These devices (D1140772 and D1141137) are not suitable for measuring the thickness of cast iron.
1.2.1 > Standard packing:
1 x Ultrasonic Thickness Gauge (Device)
1 x Transducer (10mm 5MHz)
Coupling Agent: 1 Pc (50ml)
4mm Calibration Piece
1.2. Package Contents
1. Introduction 3
2. Conditions for Proper Operation 7
3. Operating Instructions 8
4. Measurement Tips 11
5. Precautions for Accuracy 14
6. Maintenance 16
7. Table of sound velocity 17

User ManualUser Manual
Ultrasonic Thickness Gauge and Meter |D1140772 • D1141137 Ultrasonic Thickness Gauge and Meter |D1140772 • D1141137
ULTRASONIC THICKNESS GAUGE AND METER | D1140772 • D1141137
- 4 -
ULTRASONIC THICKNESS GAUGE AND METER | D1140772 • D1141137
- 5 -
1.2.2 > Parts description:
1.2.3 > LCD diagram
— Low battery indicator
— Coupling indicator m/s
— Sound velocity unit
— Thickness unit
— Sound velocity indicator
— Thickness indicator
— Store / recall indicator
- — Stored unit indicator
— Calibration indicator
1.2.4 > Keypad diagram
— ON/OFF key
— Calibration key
— Sound velocity key
— Mode shift key
+ — Back light active key
— Sound velocity, thickness, thickness unit adjust/recall key
— Sound velocity, thickness, thickness unit adjust/recall key
1.3. Specication
VEL
STORE
CAL
Ultrasonic th icknes s gauge
LCD Screen
Keypad
Receiving Socket Transmitting Socket
Transducer
Casing
Calibration Piece Battery compartment
(rear case)
LCD display
KEYPAD
•Display: 4-digital LCD display
•Minimum display unit: 0.1 mm
•Working frequency: 5MHz
•Measuring Range: 1.2 – 220.0mm (steel)
•Minimum limit for tube measuring: ø20*3mm (steel) Accuracy: +/- (1%H+0.1)mm H denotes the
measured thickness.
•Sound velocity range: 1000 to 9999 m/s Measuring sound velocity with a given thickness:
measuring range:1000 to 9999 m/s.
—When the given thickness is over 20mm, the accuracy is +/-1%; when the given thickness
is less than 20mm, the accuracy is+/-5%.
•Operation temperature: 0°C to 40°C
•Power supply: 3*1.5V AAA alkaline batteries
• Operation current: Normal operation current ≤50mA
With Backlight turned on, the current is ≤120mA
Stand-by current: ≤20uA
•Size: 72*146*29mm
•Weight: 202g

User ManualUser Manual
Ultrasonic Thickness Gauge and Meter |D1140772 • D1141137 Ultrasonic Thickness Gauge and Meter |D1140772 • D1141137
ULTRASONIC THICKNESS GAUGE AND METER | D1140772 • D1141137
- 6 -
ULTRASONIC THICKNESS GAUGE AND METER | D1140772 • D1141137
- 7 -
•Auto calibration to ensure accuracy
•Auto linear compensation: Deelat’s advanced software program enhances the precision by
correcting the non-linear accuracy of the transducer.
•Use and keys to make quick adjustments to the sound velocity /thickness. They are also used
for quick recall of recent stored data (measurements)
• Coupling status indication: Watch for the coupling icon to conrm if the coupling has been
successful.
•10 thickness measurement storage and recall functions are available, so that you can take
multiple readings when measuring multiple items.
•Sound velocity measurement: With a given thickness by a sample hardware to measure the sound
velocity, which avoid the further conversion or consultation of the table.
•12 different sound velocity settings allowing for measurement of different materials.
•Low battery indicator
•Auto power off mode: This will save you battery life.
•Deelat’s Ultrasonic Thickness Gauge has stored memory that retains all recent settings even
when the unit is powered off.
1.4. Features
2.1. Conditions for curved surfaces
2. Conditions for Proper Operation
When the material that you are measuring has a curved surface like piping, the curvature radius
must be more than or equal to10 mm, and the wall thickness must be more than or equal to 3 mm.
This requirement is most applicable to steel, as the data generated for other materials will not be
exact.
2.2. Texture Condition:
2.3. Working Temperature Condition:
Material thickness readings and sound velocity readings can/will change when there are changes in
temperature.
The transducer is made of propylene, in order to avoid damage to the transducer and maintain
the precision of the readings we recommend that the surface temperature of the material being
measured should not exceed 60°C otherwise you may incur damage to the transducer.
Operation temperature: 0~40°C
Relative humidity: <90%RH Hardware/workpiece/material temperature: <60°C
Avoid using on materials that have heavy vibration / corrosive material. Avoid impact and humidity.
This gauge can have varying results based on the texture of the material being measured. For
example, if you are measuring pipe that contains rust or other non-smooth surfaces it can affect the
measurement reading. You can minimize errors by using a 2.5MHz transducer.

User ManualUser Manual
Ultrasonic Thickness Gauge and Meter |D1140772 • D1141137 Ultrasonic Thickness Gauge and Meter |D1140772 • D1141137
ULTRASONIC THICKNESS GAUGE AND METER | D1140772 • D1141137
- 8 -
ULTRASONIC THICKNESS GAUGE AND METER | D1140772 • D1141137
- 9 -
3. Operating Instructions
1> Connect the transducer with the Ultrasonic Thickness
Gauge unit, and press to turn on the device. The LCD will
display ash the full screen for 0.5 second with the back light
present, followed by the icon which will continue scanning
for 2 cycles. After completing the startup procedure, the LCD
display will set up the last applied sound velocity setting,
indicating the gauge is ready for use.
2> Press VEL to enter your sound velocity adjustment, and
press or to select your desired velocity (There are 12
velocity settings stored in this unit). If you need to customize
the sound velocity, during the adjustment press VEL again to
enter velocity revision, while pressing or to revise the
velocity. VEL and m/s icon will continue blinking until set.
Press VEL to conrm to save the revised velocity, and the
unit will go back to normal status (VEL and m/s icon will no
longer blink)
3.1. Before Measuring
3.3. Measuring Thickness
3.4. Sound Velocity Measurement
3.5.Data storage
3.2. Calibration
A calibration should be made whenever the batteries or
transducer has been replaced. This calibration is important to
ensuring precise measurement. If necessary, this step should
completed when the accuracy of measurement is critical. Prior
to calibration, apply coupling agent on the standard calibration
piece supplied, and couple the transducer to the calibration piece.
Press CAL to enter calibration mode and the vertical bar will
keep scanning with CAL, VEL, m/s display, until the LCD display
4.0mm indicating the calibration is completed. After calibration,
sound velocity will return to your selected value, and be ready
to measure.
Get a measurement of sound velocity for a
specic known thickness of the material you are
measuring. Obtains the thickness of material
by using a vernier caliper / micrometer. Then
couple the transducer with that sample material
until a reading displays on the LCD. Remove
the transducer and press or to adjust
the reading to match the thickness by caliper/
micrometer, and then press VEL to display the
sound velocity and save it in current sound
velocity memory storage.
1> Press and hold STORE for 2 second to enter
the data store mode,. The LCD will display
THICKNESS in mm and an M icon as the rst
memory unit. If the rst memory unit is not
being registered, the LCD will display 0.0.
2> Press or to select your desired memory
unit (1-10).
3> After selecting the memory unit of choice,
the new measurement will be replace the
existing memory unit after you have taken your
new measurement.
Apply the coupling agent on the material to be measured to
couple the transducer with the material and the LCD display will
display the thickness reading.
Notes: icon on the screen indicates proper coupling. If the
icon ashes or does not display you have not achieved proper
coupling. After removing the transducer, the reading will be held
and can be stored.
Full screen
Coupling has
been achieved
Adjusting actual
thickness
Take new
measurement
and save your
data
Measuring the
thickness
Select memory
unit
Velocity adjustment
Calibration Status
Last applied sound
velocity & registered
unit
Measurement
Complete
Velocity read out
Measurement &
Storage completed
Velocity revision
Calibration Complete

User ManualUser Manual
Ultrasonic Thickness Gauge and Meter |D1140772 • D1141137 Ultrasonic Thickness Gauge and Meter |D1140772 • D1141137
ULTRASONIC THICKNESS GAUGE AND METER | D1140772 • D1141137
- 10 -
ULTRASONIC THICKNESS GAUGE AND METER | D1140772 • D1141137
- 11 -
Prior to measuring, remove all the dust, dirt, rusting and grease if possible from the material that is
to be measured.
3.6. Review Saved Data
4.1. Clean the Surface
4.2. Reduce uneven surfaces
4.3. Rough surfaces resulting from Machining
4.4. Measuring Pipe and Tubing
4.5. Odd shaped materials
4.6. Non Parallel Surfaces
3.7. Low Battery Indication
3.8. LCD back light & Automatic power off
In normal status, press and hold STORE for 2 seconds. You will
enter into review data mode. Now you can press or and
it will display the saved data orderly. Press STORE to exit the
review mode and back to normal status.
When icon ashes, replace the batteries for in order to continue using the device.
Before turning on the Ultrasonic Thickness Gauge, press and hold CAL, and press button to turn
on the back-light mode., the back light will be activated for every operation and will turn on and
remain on for 7 seconds. This unit will be turn off automatically in 2 minutes when not in use.
4. Measurement Tips
When measuring cylindrical parts to determine the thickness of the pipe wall, it will be important
to maintain proper orientation of the transducer. If the diameter of the pipe is larger than
approximately 4 inches, measurements should be made with the transducer oriented so that the
center metal line on the tip is perpendicular (at right angle) to long axis of the pipe. For smaller pipe
diameters, two measurements should be performed, one with the center metal line perpendicular,
and another with the center line parallel to the long axis of the pipe.
The smaller of the two displayed values should then be taken as the thickness at that point.
Measuring uneven and irregular surfaces will result in errors. Try to smooth out the surface if
possible by milling or polishing or using a coupling agent that has higher viscosity.
Texture that is created during the machining process of a material can also cause reading errors.
Adjust the angle of attack between the transducer and the uneven surface might provide more
accurate readings. There is a metal center piece on the tip of the transducer. This tip can be angled so
that the center metal line is crossing your uneven portion.
For measuring materials that are odd shaped or complex shapes refer to point 4.4 above. (Take the
smaller of the readings as this will be the most accurate reading.
To get the accurate results, the surface being measured must have the measuring side parallel to
the opposite side. Meaning, if the opposite side is uneven it will be more likely to obtain an incorrect
reading.
Review saved data

User ManualUser Manual
Ultrasonic Thickness Gauge and Meter |D1140772 • D1141137 Ultrasonic Thickness Gauge and Meter |D1140772 • D1141137
ULTRASONIC THICKNESS GAUGE AND METER | D1140772 • D1141137
- 12 -
ULTRASONIC THICKNESS GAUGE AND METER | D1140772 • D1141137
- 13 -
The size & sound velocity of the material being measured will change as the temperature changes.
When the accuracy of your measurement is critical, take 2 measurements from 2 different samples
of the material under the same temperature to determine the most accurate reading. When taking
measurement for steel parts in high temperature, this method may be adopted to obtain the correct
reading.
4.7. Inuence of Temperature on the Material being Measured
4.8. Materials that induce acoustic absorption 4.10.
4.11. Selecting a transducer
4.9. Reference Calibration Piece
To calibrate the device, a known thickness or sound velocity of the material is necessary. When
calibrating you must use either the sample Calibration piece or a calibration piece of your own that
has a known thickness and/or sound velocity. This Ultrasonic Thickness Gauge comes with a 4.0mm
calibration piece attached to the front. It can be removed for use, and please refer to the calibration
diagram on how to calibrate.
The supplied calibration piece may not be adequate when measuring different materials. The
supplied calibration piece is great for measuring steel, however you will require additional
calibration pieces that match your application to get the most accurate readings. After calibrating
to the calibration piece, the effects of variation of sound velocity will be minimized. To achieve the
best accuracy having a set of calibration pieces of varying weights is useful to keep handy depending
on your application. However, generally, using one calibration piece will generate an accurate
measurement.
The calibration piece should be made of the same material and ideally the same thickness as the
parts to be tested. First take a reading of the thickness of the calibration piece using a micrometer.
When measuring thin material that has a thickness that is close to the minimum limit range of this
unit, please use a calibration piece to dene the exact limit of the measured material (1.2mm for
steel). Do not measure any material that has a thickness under the minimum limit.
When the material to be measured is a complex alloy in a large size use a calibration piece that has a
similar thickness and similar material if possible.
Most metals have different molecular structures depending on the composition, therefore the sound
velocity will be slightly different. To achieve an exact reading, the calibration piece should have a
similar structure as the measured material if possible.
Attempting to measure materials that are porous or made of ber or granular in composition will
cause acoustic dispersion making it difcult attain accurate readings and not suitable for use with
this type of Ultrasonic Thickness gauge.
The transducer might become worn after heavy use and this will affect the measurements.
When the following occur, please replace the transducer:
A. The reading remains the same when measuring varying thicknesses.
B. You achieve a reading without taking any measurements.
ITEM Characteristic Range Operation temperature
5MHz ø10mm General-purpose 1.00mm to 300.0mm(steel) -10 to 60°C
5MHz ø6mm Thin workpeice 1.00mm to 50.0mm(steel) -10 to 60°C
2.5MHz ø10mm General-purpose 1.00mm to 300.0mm(steel) -10 to 60°C
You can check the most common sound velocity on the tables provided in this manual and use in the
place of taking calibration for calibration piece. However, please note that this is simply a close guide,
and occasionally the sound velocity will differ caused by different physical / chemical factors. The
sound velocity of mild steel is adopted on the reference table.
This Ultrasonic Thickness Gauge has the function to measure the sound velocity, so the velocity
can be obtained prior to measuring the thickness. Once Sound velocity has been measured, you can
proceed with measuring the thickness.

User ManualUser Manual
Ultrasonic Thickness Gauge and Meter |D1140772 • D1141137 Ultrasonic Thickness Gauge and Meter |D1140772 • D1141137
ULTRASONIC THICKNESS GAUGE AND METER | D1140772 • D1141137
- 14 -
ULTRASONIC THICKNESS GAUGE AND METER | D1140772 • D1141137
- 15 -
When using the ultrasonic thickness gauge, if the thickness of the material to be measured is less
than the minimum limit your will receive a faulty reading.
Always use a sample testing piece to know the minimum limit of the material being measured.
When measuring thin materials that are beyond the minimal limit, an error might occur where
the reading is double the actual thickness. To prevent this from happening ensure you know the
minimum limit of the material being measured.
5.1. Thin Materials
5.2. Rusty Surfaces
5.3. Re-calibrate when measuring different materials
5.4. Abrasions/Imperfections on the transducer
5.5. CAL (Calibration) Function
5. Precautions for Accuracy
Measuring rusty surfaces can result in incorrect reading. The material you are measuring may also
have rust on the inside of the pipe which can be hard to spot.
If you suspect that the material you are measuring has rust, make sure to make test measurement
from different spots, and angles to ensure you are getting an accurate reading.
A faulty reading will be obtained when measuring a new material if you have forgotten to re-
calibrate the velocity of the new material. Always re-calibrate the velocity when you are measuring
a new material.
The transducer is made of propylene, and after long periods of use the surface will become rough,
and decline in sensitivity, which can lead to inaccurate readings. Polish the transducer to and remove
rough spots and this will allow for accurate readings. If you are still getting inaccurate readings the
transducer should be replaced.
The CAL (calibration) button is used to calibrate the unit with the calibration piece on the panel. You
can also use this key to calibrate other materials.
The coupling agent will transmit the ultrasonic wave between the transducer and the gauge.
Selecting the wrong coupling agent for the job will lead to inaccurate readings. Typically a single drop
of couping agent will be sufcient.
It is important to use a low viscosity agent (this kit comes with low viscosity coupling agent) for
smooth surfaces, while a high viscosity agent (such as Glycerin) should be used on rough/vertical/
aluminum surfaces.
5.6. Multilayer and Composite Materials
5.7. Oxidized Surfaces
5.8. Abnormal readings
5.9. Selecting a coupling agent
Do not use this ultrasonic thickness gauge for measuring uncoupled multilayer objects as the wave
will not pass through. It also cannot be used for composite material since the wave will not travel
through the object at an even speed, the ultrasonic reection principle will not be performed
properly.
Some metals such as aluminum will have an oxide layer, which will prevent the metal from oxidizing
further. This can sometimes lead to an inaccurate reading. The more oxidized the layer, the reading
will be more tolerant and produce a more accurate result. Please be aware of this when measuring
and then
Make sure to calibrate using a calibration piece that is the same material as what you are trying to
measure. You will also want to use a caliper/micrometer to obtain the actual thickness and input this
as you calibrate.
If you use an ultrasonic thickness gauges regularly you should be able to distinguish an abnormal
reading resulting from corrosion to the surface of objects or incorrect calibration. If you are new
to using this device, you will need to review the procedures in this manual to x/avoid abnormal
readings.

User ManualUser Manual
Ultrasonic Thickness Gauge and Meter |D1140772 • D1141137 Ultrasonic Thickness Gauge and Meter |D1140772 • D1141137
ULTRASONIC THICKNESS GAUGE AND METER | D1140772 • D1141137
- 16 -
ULTRASONIC THICKNESS GAUGE AND METER | D1140772 • D1141137
- 17 -
6.1. Replace the Battery
6.2. Prevent scratches and wear on the transducer
6.3. Cleaning the device
6.4. Cleaning the calibration piece
6.5.
Clean after each use as coupling agents can cause rust and corrosion.
Avoid impact to the gauge. Keep it stored in the carry case when possible.
6. Maintenance
A. We you see the low battery icon appear, replace the batteries
1. Turn off the gauge
2. Open the access panel
3. Replace the batteries
B. When the gauge is not being used for extended periods, remove the batteries.
Since the transducer is made of propylene is can be scratched easily. Be gentle when using on rough
surfaces and do not place it on materials that exceed 60°C, otherwise it may damage the transducer .
Dust and oils that adhere to the transducer can cause a shorter life, so be sure to clean the lead after
each use.
Do not use solvents or alcohol to clean the LCD screen or casing. Only use a moist cloth.
Sound velocities of common materials
Material Velocity(m/s) Material Velocity(m/s)
Aluminum 6320 Acetate resin 2670
Zinc 4170 Phosphor bronze 3530
Silver 3600 Turpentine 4430
Glod 3240 Glass 5440
Tin 3230 Incoloy alloy 5720
Iron/Steel 5900 Magnesium 6310
Brass 4640 Monel alloy 6020
Copper 4700 Nickle 5630
SUS 5790 Steel 4330 mild 5850
Acrylic resin 2730 Steel 330 5660
Water 20°C 1480 Titanium 6070
Glycerinl 1920 Zirconium 4650
soluble glass 2350 Nylon 2620
7. Table of sound velocity

User Manual
Ultrasonic Thickness Gauge and Meter |D1140772 • D1141137
ULTRASONIC THICKNESS GAUGE AND METER | D1140772 • D1141137
- 18 -
Notes:
This manual suits for next models
1
Table of contents
Popular Measuring Instrument manuals by other brands
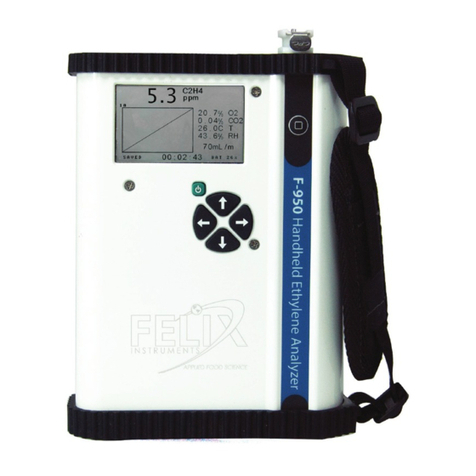
Felix Storch
Felix Storch F-950 Operation manual
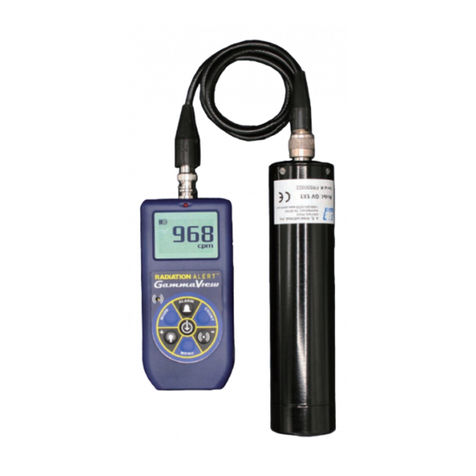
S.E. International
S.E. International Radiation Alert GammaView Operation manual
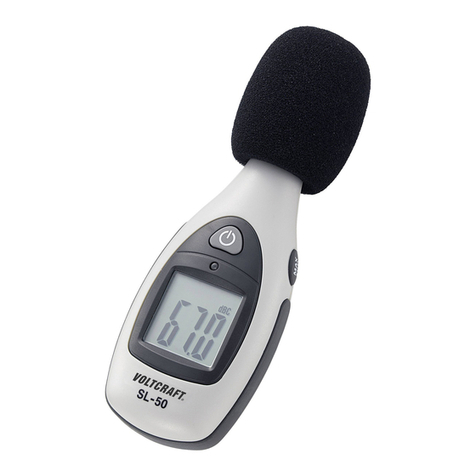
VOLTCRAFT
VOLTCRAFT SL-50 operating instructions
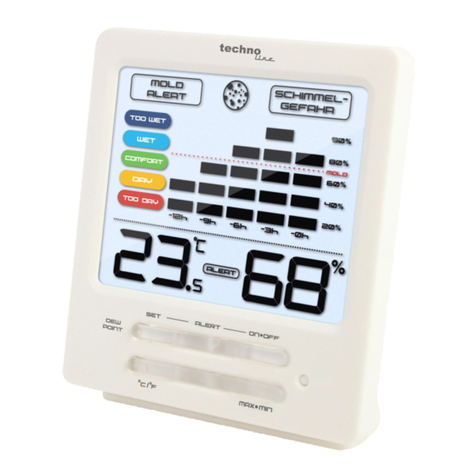
Technoline
Technoline WS 9420 instruction manual
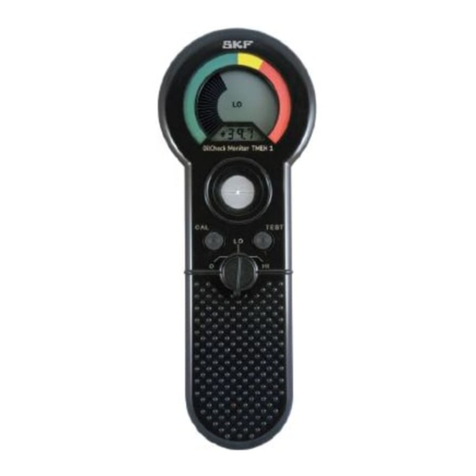
SKF
SKF TMEH 1 Instructions for use
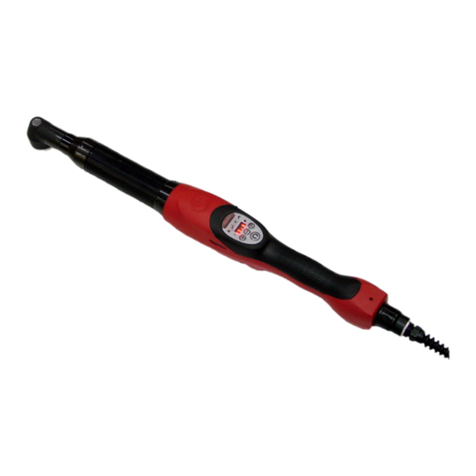
Desoutter
Desoutter EAP1.5-15 Series Operator's manual