delta-mobrey DMSP400 Series User manual

1 / 53
IOM-DMSP400: NOVEMBER 2020
USER’S MANUAL
ULTRASONIC LEVEL TRANSMITTER: DMSP400 and DMSP500 series
DELTA MOBREY LTD.
Hudson House, Albany Park Camberley Surrey, GU16 7PL, UK.
+44 (0) 1252 729140, fax +44 (0) 1252 729168
www.delta-mobrey.com, e-mail: sales@delta-mobrey.com

2 / 53
APPROVALS:
BKI ATEX, Certificate No.: BKI20ATEX0019 X
The Delta Mobrey Sonar Pulse (DMSP) range represents the next evolution in
Delta Mobrey’s range of ultrasonic level measurement instrumentation

3 / 53
BASIC CONCEPTS AND ELEMENTS OF THE ULTRASONIC MEASUREMENT

4 / 53
CONTENTS
1. INTRODUCTION.....................................................................................5
2. TECHNICAL DATA.................................................................................6
2.1 GENERAL DATA ...................................................................................6
2.2 ADDITIONAL DATA FOR EXPLOSION-PROOF DEVICES ................................7
2.3 SPECIAL DATA OF THE TWO-WIRE DMSP400 AND DMSP500 .................8
2.4 DIMENSIONS........................................................................................9
2.5 SPECIAL CONDITIONS OF SAFE USE ......................................................10
2.6 MAINTENANCE.REPAIR,AND STORAGE CONDITIONS .............................10
Software upgrade...................................................................................................................................................................................................10
3. INSTALLATION ....................................................................................11
3.1 LIQUID LEVEL MEASUREMENT .............................................................11
3.2 OPEN CHANNEL FLOW MEASUREMENT ................................................13
3.3 INSTALLATION AND ELECTRICAL CONNECTION ......................................13
3.4 LOOP CURRENT CHECKING ................................................................14
4. PROGRAMMING ..................................................................................14
4.1 PROGRAMMING WITHOUT DISPLAY MODULE .........................................15
4.2 PROGRAMMING WITH THE DISPLAY MODULE ........................................18
Display Module.......................................................................................................................................................................................................19
STEPS OF THE DISPLAY MODULE ......................................................................................................................................................................................19
INDICATIONS OF THE DISPLAY MODULE AND LED STATUS.....................................................................................................................................................20
QUICKSET................................................................................................................................................................................................................21
FULL PARAMETER ACCESS ..............................................................................................................................................................................................23
5. PARAMETERS –DESCRIPTIONS AND PROGRAMMING................ 25
5.1 MEASUREMENT CONFIGURATION ........................................................ 25
5.2 CURRENT OUTPUT ............................................................................ 31
5.3 RELAY OUTPUT ................................................................................. 32
5.4 DIGITAL OUTPUT ................................................................................ 32
5.5 MEASUREMENT OPTIMISATION............................................................ 33
5.6 VOLUME MEASUREMENT .................................................................... 37
5.7 VOLUME FLOW MEASURING ............................................................... 38
5.8 32-POINT LINEARISATION................................................................... 44
5.9 INFORMATIONAL PARAMETERS (READ OUT PARAMETERS) .................... 45
5.10 ADDITIONAL PARAMETERS OF THE FLOW METERING........................... 47
5.11 SUPPLEMENTARY PARAMETER OF THE LOGGER .................................. 47
5.12 TEST PARAMETERS ......................................................................... 48
5.13 SIMULATION .................................................................................... 49
5.14 ACCESS LOCK................................................................................. 49
6. ERROR CODES ................................................................................... 50
7. PARAMETER TABLE .......................................................................... 51
8. SOUND VELOCITIES IN DIFFERENT GASES ................................... 53

5 / 53
Thank you for choosing Delta Mobrey instrument.
We are sure that you will be satisfied throughout its use.
1. INTRODUCTION
Application
The DMSP400 and DMSP500 compact ultrasonic level transmitters from
DELTA MOBREY are an excellent tool for the level measurement of liquids.
Level measurement technology based on the non-contacting ultrasonic
principle is especially suited for applications where, for any reason, no
physical contact can be established to the surface of the material to be
measured.
Such reasons may include corrosive attack by the process medium against
the measuring device material (acids), possible contamination (sewage) or
particles of the process medium adhering to the measuring device
(adhesive materials).
Principle of Operation
The ultrasonic level metering technology is based on the principle of
measuring the time required for the ultrasound pulses to make a round trip
from the sensor to the level to be measured and back. The sensor emits an
ultrasonic pulse train and receives the echoes reflected. The intelligent
electronic device processes the received signal by selecting the echo
reflected by the surface and calculates from the time of flight the distance
between the sensor and the surface which constitutes the basis of all output
signals of the DMSP400 and DMSP500.
A Total beam angle of 5–7at -3 dB as is featured by most of DELTA
MOBREY’s transducers ensuring a reliable measurement in narrow tanks with
uneven side walls as well as in process tanks with various protruding objects.
Furthermore, as a result of the narrow beam angle –the emitted ultrasonic
signals have an outstanding focusing –deep penetration through gases,
vapour and foam is ensured.
rr
D
X D
1 m 0,21 m
2 m 0,3 m
5 m 0,56 m
10 m 1 m
15m 1,45 m
X
Diameters
corresponding to
5° beam angle.
Dead Band is a feature common to all ultrasonic level meters.
It is specified as “Minimum measuring distance” in the Technical Data Table.
Measurement within this range can not be interpreted.
Minimum measuring distance (Xm) is determined by the design of the unit within which the measurement is not possible (Dead Zone). This distance can be
extended by programming in order to avoid disturbing effects of possible disturbing echoes coming from fixed objects. (Close-end Blocking).
Maximum measuring distance (XM) is the greatest distance (determined by the design of the unit) which can be measured by the unit under ideal conditions.
The maximum measuring distance of the actual application (H) must not be greater than XM.

6 / 53
2. TECHNICAL DATA
2.1 GENERAL DATA
Transducer materials
PVDF
Housing material
Plastic: Glass fibre plastic PBT; Metal: Paint coated aluminium, Stainless steel
Process temperature
PP, PVDF and PTFE transducers: -30 °C …+90 °C (-20 °F … 190 °F)
Stainless Steel transducer: -30 °C … +100 °C (-20 °F … 210 °F), 120 °C [250 °F] for max. 2 hours
Ambient temperature
Aluminium housing -30 °C …+70 °C (-20 °F … 160 °F) with display -25 °C …+70 °C (-10 °F … 160 °F),
Plastic housing: -25 °C …+70 °C (-10 °F … 160 °F)
Pressure (1) (Absolute)
0.5 –3 bar (0.05 –0.3 MPa) (7.3 –43.5 psi), Stainless steel versions 0.9 –1.1 bar (0.09 –0.11 MPa) (13 –16 psi)
Seals
PP transducer: EPDM
All other transducer versions: FPM
Ingress protection
Sensor: IP68
Housing: IP67 (NEMA 6)
Power supply
12(3) –36 V DC, / 48 mW –720 mW, galvanic isolation; protection against surge transients
Accuracy (2)
(0.2% of the measured distance plus 0.05% of the range)
Resolution
Depending on the measured distance < 2 m: 1 mm, 2 –5 m: 2 mm, 5 –10 m: 5 mm, > 10 m: 10 mm
(< 6.5 ft: 40 mil; 6.5 ft to 16 ft: 80 mil; 16 ft to 32 ft: 200 mil; > 32 ft: 400 mil )
Outputs
Analogue: 4 –20 mA (3.9 –20.5 mA), Rmax = (Ut–12 V) / 0.02 isolated protection against surge transients
SPDT relay 30 V / 1 A DC; 48 V / 0.5 A AC
Loop power test connectors: 2 pins for mV meter range 200 mV, 0.5%
Display: 6 digits, icons and bargraph
Serial communication: HART interface (terminal resistor 250 Ohm)
Electrical connection
2x M20x1.5 Metal, Cable 7 –13 mm or M20x1.5 Plastic, Cable 6 –12 mm and
2x ½″NPT for cable gland; Wire cross section: 0.5 –1.5 mm2[20 –15 AWG]
Electrical protection
Class III
(1) For pressures below 1 bar representative of Delta Mobrey should be consulted.
(2) Under optimal circumstances of reflection and stabilised transducer temperature.
(3) Only partial operation is provided. Reliable operation without any restrictions is guaranteed at >13.4 V terminal voltage.

7 / 53
2.2 ADDITIONAL DATA FOR EXPLOSION-PROOF DEVICES
3.2.1 ATEX APPROVAL No.: BKIxxxxxxxx (approval pending)
TYPE
DMSP500 series
Ex marking (ATEX)
II 1 G Ex ia IIB T6…T4 Ga
Intrinsically safe data
Ci ≤ 15 nF, Li ≤ 200
H, Ui ≤ 30 V, Ii ≤ 140 mA, Pi ≤ 1 W
Ex power supply, loading
Uo < 30 V, Io < 140 mA, Po < 1 W
Medium temperature
PVDF transducer: -20 °C …+80 °C. Temperature class T6..
Ambient temperature
With metal housing: -30 °C … +70 °C; with display: -25 °C … +70 °C; with plastic housing: -20 °C … +70 °C

8 / 53
2.3 SPECIAL DATA OF THE TWO-WIRE DMSP400 AND DMSP500
TYPE
DMSP***A
DMSP***C
DMSP***B
DMSP***N
DMSP***D
DMSP***E
DMSP***F
DMSP***G
DMSP***L
DMSP***M
DMSP***P
DMSP***Q
Transducer material
PVDF
PVDF
PVDF
Maximum measuring
distance * [m / (ft)]
4 (13)
6 (20)
8 (26)
10 (33)
15 (49); 20 (66)
25 (82)
Min. measuring distance*
(Dead band) [m / (in)]
0.2 (8)
0.25 (10)
0.35 (14)
0.45 (18)
0.6 (24)
Total beam angle (-3 dB)
6°
5°
7°
5°
7°
Measurement frequency
80 kHz
80 kHz
50 kHz
60 kHz
40 kHz
20 kHz
Process connection
1½″thread
2″thread
Flange
* (from the transducer face)

9 / 53
2.4 DIMENSIONS
DMSP***A/C
DMSP***B/N
DMSP***D/E
~89
1 1/2" BSP
or NPT
BSP length 15
NPT length 22
2 x M20x1.5
2 x 1/2" NPT
~60
97.5
2 x M20x1.5
2 x 1/2" NPT
~60
~89
97.5
2" BSP
or NPT
BSP length 15
NPT length 22
2 x M20x1.5
2 x 1/2" NPT
~89
97.5
2" BSP
or NPT
BSP length 15
NPT length 22
~80
DMSP***F/G
DMSP***J/K
DMSP***L/M/P/Q
74
JIS 10K 80A
DIN DN80 PN16
ANSI 3" 150 psi
~89
2 x 1/2" NPT
2 x M20x1,5
97,5
19
~46
122
JIS10K125A
ANSI5"150psi
DINDN125PN16
*
~89
2xM20x1.5
2x1/2"NPT
97.5
19
~43
~89
2xM20x1,5
2x1/2"NPT
97,5
19
~62
DINDN150PN16
ANSI6"150psi
JIS10K150A
Ø148
* Min required flange size

10 / 53
2.5 SPECIAL CONDITIONS OF SAFE USE
•Intrinsically safe units with Ex ia IIB marking can only be used in certified intrinsically safe loops with the previously given technical data.
(see values in Additional data for Ex approved models under Point 3)
•The PTFE transducers are made of plastic that can be loaded electrostatically therefore:
–Filling and emptying speed should be selected according to the medium
–Fog development of the dangerous material during filling should be avoided.
–Cleaning of the plastic enclosure is not allowed in hazardous space.
•Equipment with plastic housing are susceptible to electrostatic charges, thus the devices must be protected against electrostatic charges.
•The aluminium content of equipment with metallic enclosure exceeds the limit, the devices must be protected against impact and friction effects.
•The device can be mounted into tanks with up to 3 bar process pressure. The apparatus is not suitable as a fire resistant barrier between the inside and
the outside area. After mounting the unit, pressure test of the system should be carried out on a regular basis in accordance to the local regulations at
1.5 times higher pressure than the nominal pressure value.
•Devices should be grounded by connecting their grounding screws to the equipotential system.
•The device should read or programmed through IR port only outside of the explosive hazardous atmosphere because the infrared interface connected
to the computer is not an explosion-proof apparatus.
2.6 MAINTENANCE.REPAIR,AND STORAGE CONDITIONS
DMSP400/500 units do not require maintenance on a regular basis.
The need for cleaning of the sensor head may occur. Cleaning should be performed by utmost care where scraping or denting of the transducer have to be
avoided.
Repair under or after the guarantee period should only be carried out by DELTA MOBREY. Devices for repair should only be returned duly cleaned and
disinfected.
Unused devices must be stored within the ambient temperature range specified in the technical data, with a maximum of 98% relative humidity.
Software upgrade
Based on the observations & needs of our customers DELTA MOBREY constantly improves and revises the operating software of the device. The software can
be upgraded with the help of the IrDA communication port of the DISPLAY MODULE or an eLink (USB) communication adapter plugged into the DISPLAY
MODULE slot. For more information about software updates please contact DELTA MOBREY.

11 / 53
3. INSTALLATION
3.1 LIQUID LEVEL MEASUREMENT
POSITION
The optimal position of the DMSP400 and DMSP500 is on the
radius r = (0.3 –0.5) R of the (cylindrical) tank / silo.
(Take also sonic cone on page 1 into consideration.)
SENSOR ALIGNMENT
The sensor face has to be parallel to
the surface of the liquid within 2 –3.
TEMPERATURE
Make sure that the transmitter will
be protected against overheating by
direct sunshine.
Sunshade

12 / 53
OBSTACLES
Make sure that no in-flow path or objects
(e.g. cooling pipes, ladders, bracing
members, thermometers, etc.) or no tank
wall of the ragged surface protrude into
the sensing cone of the ultrasonic beam.
One fix object in the tank / silo that
disturb the measurement can be blocked
out by the appropriate programming of
the DMSP400 and 500.
STAND-OFF PIPE
The structure of the stand off pipe should be rigid; the inner rim where the ultrasonic beam
leaves the pipe should be rounded.
L
Ø D
r
L
Dmin
DMSP***A/C
DMSP***B/N
DMSP***D/E
150
50
60
60
200
50
60
75
250
65
65
90
300
80
75
105
350
95
85
120
FOAM
Foaming of the liquid surface may render ultrasonic level
metering impossible. If possible, a location should be found,
where foaming is the least (device should be located as far as
possible from liquid inflow) or a stilling pipe or well should be
used.
r
Ø D
L
L
Dmin
DMSP***F/G
DMSP***J/K/L/M
DMSP***P/Q
90
80
*
*
200
80
*
*
350
85
*
*
500
90
*
*
* For values contact your distributor
WIND
Intensive air (gas) movements in the vicinity of the ultrasonic
cone is to be avoided. A strong draft of wind may "blow away"
the ultrasound.
Devices with lower measuring frequency (40, 20 kHz) are
recommended.
FUMES / VAPOURS
For closed tanks containing chemicals or other liquids, which creates fume / gases above the
liquid surface especially for outdoor tanks exposed to the sun,
a strong reduction of the nominal measuring range of the ultrasonic device is to be
considered during device selection.
Devices with lower measuring frequency (40, 20 kHz) are recommended in these cases
units.

13 / 53
3.2 OPEN CHANNEL FLOW MEASUREMENT
•For ultimate accuracy, install the sensor as close as possible above the expected maximum water level (see minimum measuring range).
•Install the device in a place defined by the characteristics of the metering channel along the longitudinal axis of the flume or weir. In case of Parshall
flumes supplied by DELTA MOBREY the location of the sensor is marked.
•In some cases foam may develop on the surface. Make sure that the surface, opposite to the sensor remain free of foam for proper sound reflection.
•From the point of view of measurement accuracy the length of the channel sections preceding and following the measuring flume and their method of
joining to the measuring channel section are of critical importance.
•Despite of the most careful installation, the accuracy of flow metering will be lower than that of specified for the distance measurement. It will be
determined by the features of the flume or weir applied.
3.3 INSTALLATION AND ELECTRICAL CONNECTION
Installation of the (BSP or NPT) threaded models
•Screw the unit in to its place. Use open wrench for
tightening; max torque is 20 Nm
•After tightening the enclosure can be rotated to the proper
position. (Safety bolt prevents rotation more than 350°)
•The unit may be damaged by electrostatic discharge (EDS)
via its terminal, thus apply the precautions commonly used
to avoid electrostatic discharge e.g. by touching a properly
grounded point before removing the cover of the enclosure.
21
Display unit
connector
Connect or for
meas. of loop current
4...20 mA loop current
and suppl.voltage (HART)
GND
1/2” NPT
1/2” NPT
M20x1.5
M20x1.5
I
23456C2
5
4 6
C1
(Only normal
version)
2 3
12
U
1
RELAY
•Ensure that the power supply is turned off at the source.
•With removal of the cover of the housing and taking out the display module (if any), the
screw terminals can be accessed. Suggested cable core cross section:
0.5 –1.5 mm2* [20 –15 AWG]. Arrange grounding by the inner or outer grounding
screw first.
•Switch on the unit and make necessary programming.
•After programming ensure proper sealing and closing of the cover.

14 / 53
3.4 LOOP CURRENT CHECKING
After removing the cover (and the Display Module if there is any) the actual loop current can be measured with an accuracy of 0.5% by connecting an voltmeter
(in the range of 200 mV) to the points indicated on the drawing above
4. PROGRAMMING
The DMSP400 and DMSP500 can be programmed by the following two ways:
•Programming without Display Module see 5.1.
Assignment of the levels to the 4 and 20 mA current output, error indication by the analogue signal and damping can be set.
•With the DISPLAY MODULE, see 5.2.
All features of the unit can be set, such as measurement configuration and optimisation, 32-point linearisation, dimensions for 11 tanks with different
shape and for 21 different open channels (flume, weir, etc).
Devices with the type number DMSP400 and DMSP500 are already equipped with the Display Module.
The DMSP400 and DMSP500 is fully operational without the Display Module. The Display Module is only needed for programming and/or displaying
measurement values.
The unit will measure during programming in accordance with the previous parameters. The new, modified parameters will only be effective after
returning to the Measurement Mode
If the transmitter is left in Programming Mode by mistake, it will automatically return to Measurement Mode after 30 minutes and will operate with the parameters
entered during the last completed programming.
The DMSP400 and DMSP500 will be delivered with the following Factory Default:
Current output, display and bargraph: LEVEL
Current output and bargraph proportional to the level
4 mA: assigned to the minimum level 0%
20 mA: assigned to the maximum level 100%
Error indication by the current output: hold last value
Damping: 60 sec

15 / 53
4.1 PROGRAMMING WITHOUT DISPLAY MODULE
Programming is only possible if the DMSP400 and DMSP500 is in Level
Measuring Mode and receives valid echo i.e. “VALID” LED is lit!
The following can be programmed without display module
•Assignment of the 4 mA to a required e.g. min. level / max. distance
•Assignment of the 20 mA to a required e.g. max. level / min. distance
•Error indication by the current output (Hold, 3.6 mA or 22 mA)
•Damping (10, 30 or 60 sec)
•Reset to the factory default
Note: Current output can also be assigned in inverted mode:
4 mA = 100% (Full), 20 mA = 0% (Empty)
RELAY
Procedure of programming: press button in the relevant sequence and check the state of the LED-s. Symbols for the states of the LED-s:
= LED is off, = LED is blinking, = LED is on, = LEDs are blinking alternatively = Dont care
Minimum level, (0%, empty tank) assignment to 4 mA
Action
Led state following the action
B
B
Use level in tank or a fix target e.g. the wall
1) Check for a valid ECHO
= Valid ECHO, transmitter programmable
2) Press NEXT button steadily
= DMSP400/500 in programming mode
3) Press UP button steadily
= 4 mA assigned to the distance (see picture)
4) Release buttons
= Programming completed

16 / 53
Maximum level (100%, full tank) assignment to 20 mA
Action
Led state following the action
B
B
Use level in tank or a fix target e.g. the wall
1) Check for a valid ECHO
= Valid ECHO, transmitter programmable
2) Press NEXT button steadily
= DMSP400/500 in programming mode
3) Press DOWN button steadily
= 20 mA as signed to the distance
(see picture)
4) Release buttons
= Programming completed
“Error state” indication by the analogue signal (Check for a valid echo as above)
As a result of this setting the value of the analogue output will be 3.8 mA; 22 mA or according last value (hold) until the error is ceased.
Action
Led state following the action
1) Press button steadily
= DMSP400/500 in programming mode
2) Press any of the DOWN ,
ENTER
E
,
NEXT
buttons steadily
–hold last value
= –3.6 mA
–22 mA
3) Release buttons
= Programming completed

17 / 53
Damping time setting (Check for a valid echo as above)
Action
Led state following the action
1) Press ENTER
E
button steadily
= DMSP400/500 in programming mode
2) Press any of the NEXT ,
UP ,
DOWN
buttons steadily
–10 sec
= –30 sec
–60 sec
3) Release buttons
= Programming completed
RESET: Returning to the default (Check for a valid echo as above)
Action
Led state following the action
1) Press NEXT button steadily
= DMSP400/500 in programming mode
2) Press ENTER
E
button steadily
= Default loaded
Indication of mistakes (by LEDs) made during programming
Action
Led state following the action
Possible correction
Attempted programming
= blinking twice = no Echo
Find a valid Echo
Attempted programming
= blinking three times = no access possible
With Display Module only See 5.2 (P99)
Attempted programming
= blinking four times = DMSP400/500 not in
Level Measurement Mode
With Display Module only See 5.2 (P01)

18 / 53
4.2 PROGRAMMING WITH THE DISPLAY MODULE
The DMSP400 and DMSP500 should be adjusted to the process by programming the parameters. The Display Module can be used to display the parameters
during programming and measurement values during measurement.
The Display Module supports two separately accessible programming modes representing 2-layers of programming complexity, depending on user choice.
PLUG-IN DISPLAY MODULE
QUICKSET
FULL
PARAMETER
ACCESS
QUICKSET (5.2.4)
Recommended as a simple and fast way to set up the DMSP400/500 by 6 basic parameters
for the following basic settings, marked by abbreviations easy to remember
•Engineering unit for the display (Metric or US)
•Maximum measuring distance (H)
•Assignment of min level to 4 mA
•Assignment of max level to 20 mA
•Error indication by the current output
•Damping time
Full Parameter Access (5.2.5)
All features of the DMSP400/500 such as:
•Measurement configuration
•Outputs
•Measurement optimisation
•11 pre-programmed tank shapes for volume calculation
•21 pre-programmed formula for flow metering
•32-point linearisation

19 / 53
Display Module
Symbols used on the LCD
•DIST –Distance (measuring) mode
•LEV –Level (measuring) mode
•VOL –Volume (measuring) mode
•FLOW –Open channel (flow metering) mode
•PROG –Programming mode
(device under programming)
•RELAY –‘C2’ circuit of the relay is closed
•T1 –TOT1 volume flow totaliser
(resetable aggregate)
•T2 –TOT2 volume flow totaliser (aggregate)
•FAIL –Measurement / device error
•–Level changing direction
•Bargraph assigned to the current output or
echo strength
Symbols used on the frame
•M–Metric system
•US –US calculation system
LEDS lit
•COM –digital (Hart) communication
•VALID –presence of valid echo
IrDA –Infrared communication port for logger
readout, diagnostics and software upgrade.
STEPS OF THE DISPLAY MODULE
Programming will be performed by the pressing and releasing the relevant one or two keys (simultaneously).
Single key pressing
ENTER
E
to select parameter address and go to parameter value
to save parameter value and return to parameter address
NEXT to move the blinking (sign of change) of the digit to the left
UP to increase value of the blinking digit
DOWN to decrease value of the blinking digit
Double key pressing
Press the two keys simultaneously for desired programming step.
yy parameter address (P01, P02…P99)
xxxx parameter value (dcba)
bargraph
yy:xxxx

20 / 53
Enter into or quit programming modes
Basic steps while parameter address is blinking
Basic steps while parameter value is blinking
E
Q
u
ic
k
s
e
t
FullParameter
Access
E
Returntodefault*
* LOADreadout **CANCELreadout
C
a
n
ce
la
llm
o
d
ifica
tio
n
s**
Parametervalue
Default
E
Displaydefaultvalue
*cancellationimmediatelyactive
C
an
c
elallm
o
d
ifica
tio
n
s
re
tu
rn
to
p
ara
m
e
tera
d
d
re
ss
*
Parametervalue
Actual
GET LEVEL function
Special function used only in level and distance measurement modes UP + DOWN
Notes:
If after pressing ENTER
E
blinking does not spring over from the parameter address to the parameter value this means that
•the parameter is either a read-out type, or
•the secret code prevents the modification (see P99)
If the modification of the parameter value is not accepted i.e. the parameter value keeps blinking after pressing ENTER
E
,
•the modified value is either out of the range, or
•the code entered is not a valid code
INDICATIONS OF THE DISPLAY MODULE AND LED STATUS
RELAY
LED indication
•VALID (ECHO)-LED
lit in case of
valid echo.
•COM-LED
see description of HART
•RELAY-LED
ON –when the ‘C2’ circuit of the relay
is closed
This manual suits for next models
1
Table of contents
Other delta-mobrey Transmitter manuals
Popular Transmitter manuals by other brands
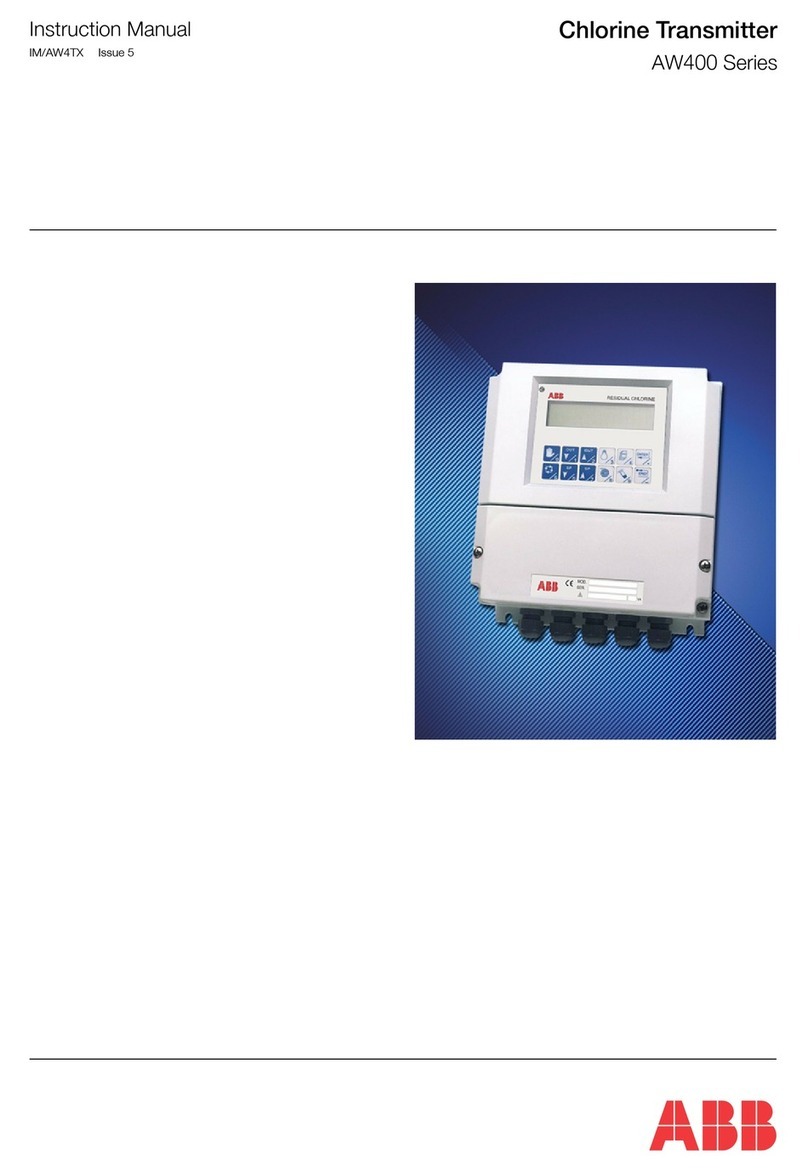
ABB
ABB AW400 Series instruction manual
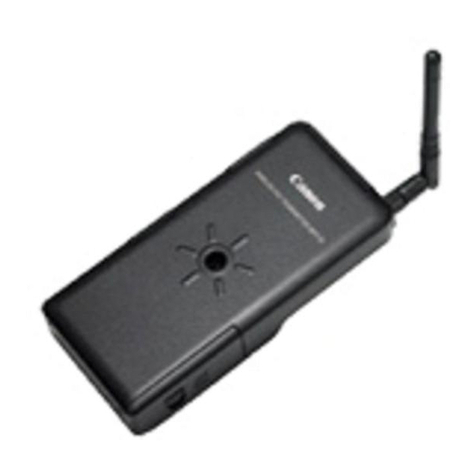
Canon
Canon EOS 5D - Focusing Screen Ee-A instruction manual
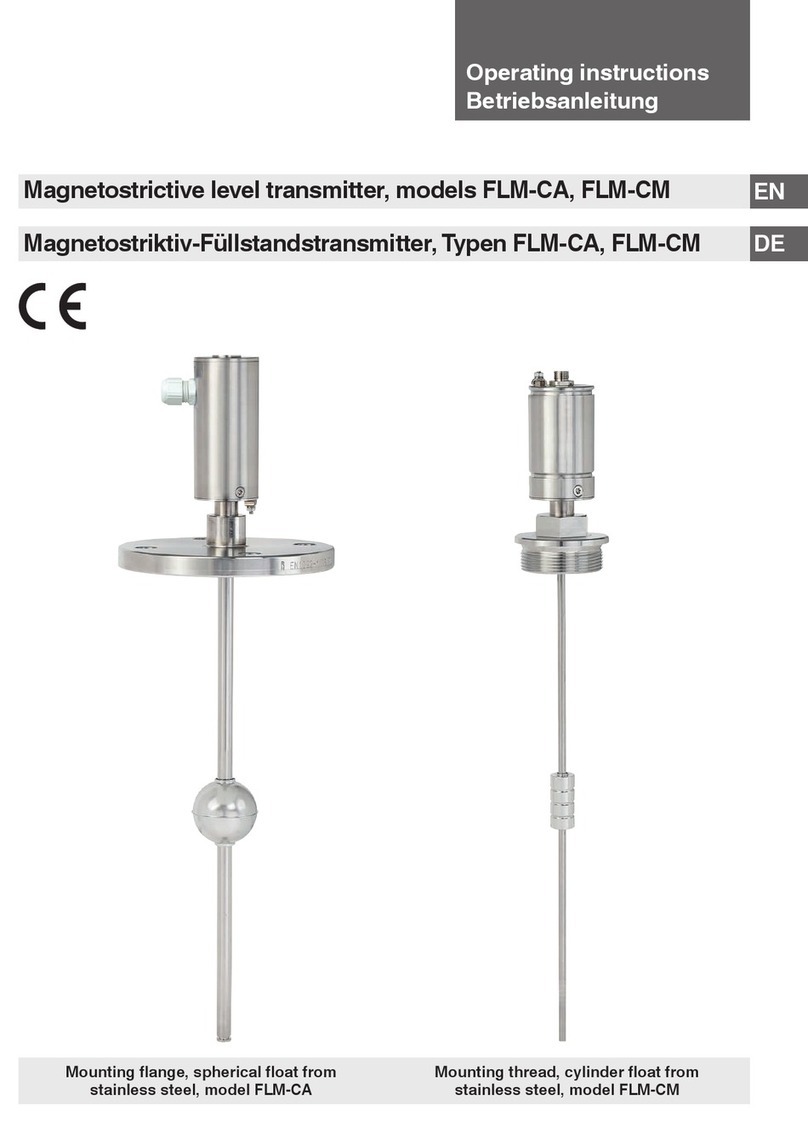
WIKA
WIKA FLM-CA operating instructions
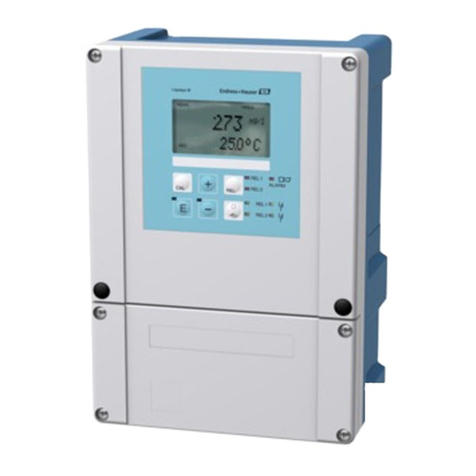
Endress+Hauser
Endress+Hauser Mycom S CLM 153 operating instructions
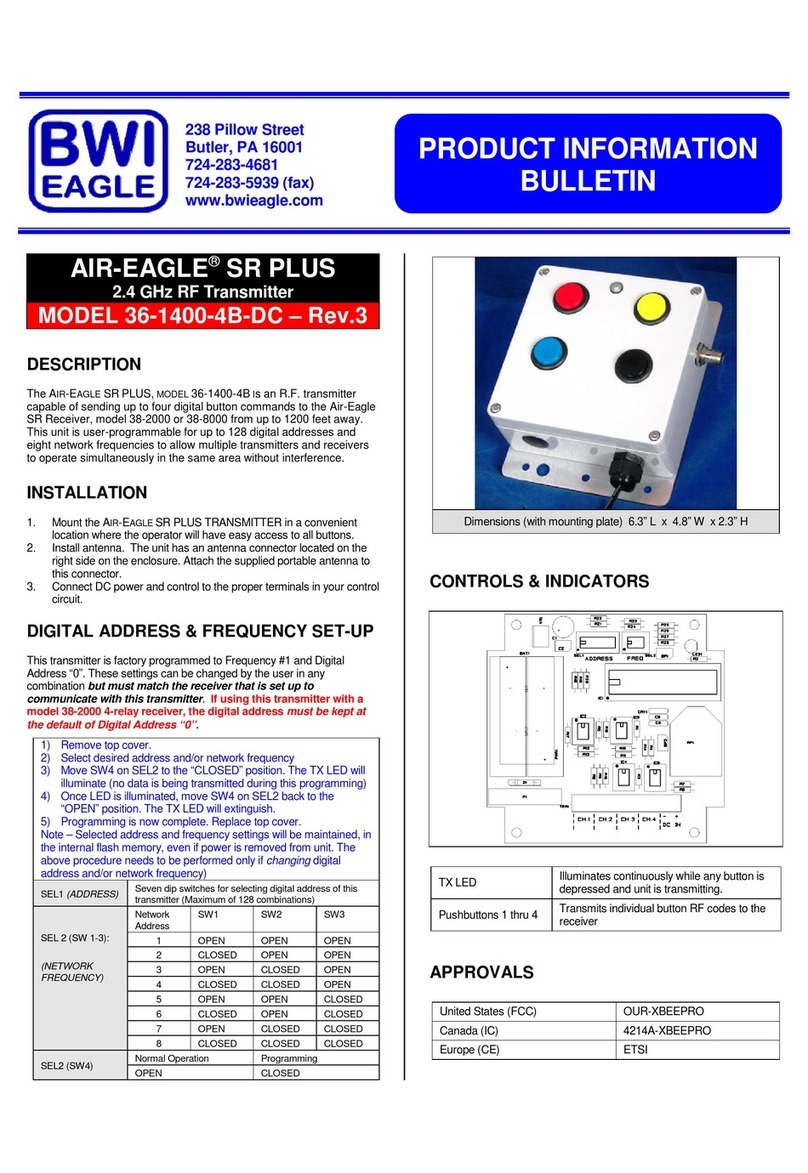
BWI Eagle
BWI Eagle AIR-EAGLE SR PLUS 36-1400-4B-DC Product information bulletin
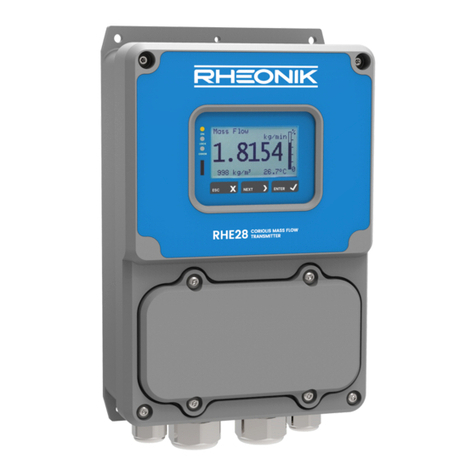
RHEONIK
RHEONIK RHE28 Installation & start?up guide