DeltaPoint Manifold DPM-12GM-6-P1A-FP10-F-V1 User manual

DeltaPoint Manifold
Installation and Operation Manual
12 GPM PROFINET Unit
Model DPM-12GM-6-P1A-FP10-F-V1
™
ROCON LLC
1755 East Nine Mile Road
PO Box 249
Hazel Park, MI 48030-0249
TEL (248) 542-9635 FAX (248) 398-4274
Website: www.flowmeters.com

DPM-12GM-6-P1A-FP10-F-V1 10/31/2018 2
ROCON LLC
TABLE OF CONTENTS
PROPRIETARY NOTICE..........................................................................................................................3
SPECIFICATIONS –12 GPM (45 LPM) UNIT..........................................................................................5
HOW VORTEX SHEDDING FLOW METER WORKS..............................................................................6
UNIT FRONT VIEW ..................................................................................................................................7
FRONT VIEW, ELECTRICAL ENCLOSURE, COVER REMOVED..........................................................8
UNIT REAR VIEW.....................................................................................................................................9
UNIT SIDE VIEW ....................................................................................................................................10
HOW THE DELTAPOINT MONITORS COOLING WATER IN THE ROBOTICS CELL ........................11
INSTALLATION.......................................................................................................................................12
START-UP TEST CYCLE ...................................................................................................................13
ELECTRICAL CONNECTORS ...............................................................................................................14
INDICATOR LIGHTS, PROGRAMMING KEYPAD, AND LCD MESSAGES EXPLAINED....................15
User Menu Features ...............................................................................................................................16
PROFINET LED LIGHTS ....................................................................................................................19
PROFINET SETUP.................................................................................................................................20
PROFINET I/O MAP SUMMARY............................................................................................................32
PROFINET I/O MAP DETAILS ...............................................................................................................32
INPUTS................................................................................................................................................32
STATUS Byte Bit Summary.................................................................................................................33
OUTPUTS............................................................................................................................................34
Front Panel Controls and Corresponding Bits ........................................................................................35
MAINTENANCE......................................................................................................................................36
Shut-Off Valve .....................................................................................................................................36
Check Valve ........................................................................................................................................36
Cleaning...............................................................................................................................................36
Note.....................................................................................................................................................36
TROUBLESHOOTING............................................................................................................................37
Replacing the Flow Sensor.....................................................................................................................39
DIMENSIONS .........................................................................................................................................43
APPENDIX..............................................................................................................................................44
Check Valve Specifications.................................................................................................................44
Shut-Off Valve Specifications..............................................................................................................44
RMA NOTICE RETURN MATERIAL AUTHORIZATION.....................................................................45
RMA FORM.............................................................................................................................................46
ROCON / DELTAPOINT WARRANTY ...................................................................................................47

DPM-12GM-6-P1A-FP10-F-V1 10/31/2018 3
ROCON LLC
PROPRIETARY NOTICE
The information contained in this publication is derived in part from proprietary and patented data. This
information has been prepared for the express purpose of assisting in installation, operation, and
maintenance of the instruments described herein. Publication of this information does not convey any
rights of use or reproduction other than in connection with the installation, operation and maintenance
of the equipment described herein. Universal Flow Monitors, Inc. and Rocon LLC reserve the right to
change the information contained in this publication at any time and without prior notice.

DPM-12GM-6-P1A-FP10-F-V1 10/31/2018 4
ROCON LLC
USING THIS MANUAL
In order to use this manual, you will need the model code that can be found on the nameplate of the
flowmeter, as shown on the example below (see MODEL CODES). The Model Code allows you to
determine minimum and maximum flow capabilities for the Delta Point water saver.

DPM-12GM-6-P1A-FP10-F-V1 10/31/2018 5
ROCON LLC
SPECIFICATIONS –12 GPM (45 LPM) UNIT
Supply Voltage 24 VDC @ 750 mA (valve on)
Minimum Water Flow: 0.8 GPM (3 LPM)
Maximum Water Flow: 12.0 GPM (45 LPM)
Flow Measurement Accuracy: ±0.24 GPM (±0.9 LPM)
Flow Measurement Repeatability: 0.25% of actual flow
Minimum Detectable Leak: 0.5 GPM (1.9 LPM)
Response Time (Cap Pulled To Fault): 1.0 sec. typical with 30 feet. ¾ hose (9 meters)
Restart Delay: 1.0 –3.0 sec. (user selectable) (See Note 1)
Water Temperature Range: 40 °F (4.4 °C) - 180 °F (82 °C)
Temperature Probe Accuracy: ±2 °F (±1 °C) from 32–200 °F (0–93 °C)
Operating Temperature Range: 32 °F (0 °C) - 122 °F (50 °C)
Storage Temperature: -4 °F (-20 °C) - 158 °F (70 °C)
Port Size: ¾” NPTF (¾” BSPP)
Supply Water Pressure
Minimum: 15 PSIG (1.0 bar)
Maximum: 100 PSIG (7 bar)
Differential Water Pressure
Minimum: 2 PSID (.14 bar)
Maximum: 90 PSID (6 bar)
Pressure Drop Across Manifold
(Including shut-off valve, manifold,
¾” I.D. 8-ft. hose, check valve): 2.1 PSIG @ 6 GPM @ 70 °F (.14 bar @ 22.7 LPM @ 21 °C)
Wetted Parts (Body and Sensor): Brass, PVDF
Electrical Enclosure: Aluminum
Weight: 14 lb. (6.4 kg.)
Pressure Drop Data
GPM
1.5
2.0
3.0
4.0
5.0
6.0
7.0
8.0
9.0
10.0
11.0
12.0
13.0
14.0
15.0
PSID
0
.5
1
1.2
1.6
2.1
3.2
4.2
6
8.1
10.2
12.7
15.1
17.9
20.9
*Measured from inlet shut-off valve, through the unit, ¾”I.D. 8 ft hose loop, back through the unit and check valve.
Caution: The unit shall be supplied by a SELV (separated extra-low voltage) source in
accordance with CSA Standard C22.2 No.1010.1-92 Annex H.
Environmental conditions: This device has been designed for use in Installation Category
I, pollution degree 4, at altitudes up to 2000 meters (6560 ft.),
either indoors or outdoors as defined in CSA Standard C22.2
No.1010.1-92.
Note 1: There is an additional 3-second delay at power-up associated with displaying the firmware
banner. This delay is bypassed if a remote restart is sent to the instrument.

DPM-12GM-6-P1A-FP10-F-V1 10/31/2018 6
ROCON LLC
HOW VORTEX SHEDDING FLOW METER WORKS
When fluid passes by a bluff, oscillations occur. Examples of these oscillations in nature include the
swirls produced downstream of a rock in a rapidly flowing river, or the waving of a flag in the wind with
the bluff being the flag pole.
DeltaPoint Unit Supply Water Leg example above: The fluid strikes a bluff body (A), generating
vortices (B) (eddies) that move downstream. The vortices form alternately, from one side to the other.
A piezoelectric sensor housed in a sensor tube (C) directly downstream of the bluff senses the
pressure zones created by the vortices. The sensor generates a frequency directly proportional to the
vortices (flow). The pulses are then measured by the microprocessor.
Each DeltaPoint Unit has two vortex shedding flow meters. One flow meter monitors the supply path,
and the other flow meter monitors the return path along with the temperature probe.
PLEASE NOTE: Bluff / Sensors not effected by dirty water.

DPM-12GM-6-P1A-FP10-F-V1 10/31/2018 7
ROCON LLC
UNIT FRONT VIEW
A = Solenoid NC 2way Shutoff Valve 1 = Supply
B = Manual Bypass Knob 2 = To Cell
C = Check Valve 3 = From Cell
D = Cover - LCD Screen 4 = Return
E = Cover - LED / Program Buttons
F = ID Tag
G = PROFINET Connector
H = Power Supply Connector
I = USB Port –Firmware update & Data Logging
I

DPM-12GM-6-P1A-FP10-F-V1 10/31/2018 8
ROCON LLC
FRONT VIEW, ELECTRICAL ENCLOSURE, COVER REMOVED
A = Motherboard (CPU and Keypad)
B = LCD Screen
C = Analog Board (power supply and sensor amplifiers)
D = Supply Flow Sensor
E = Return Flow Sensor
F = Return Temperature Sensor
G = Solid State Relay (supply water control)
H = Optional Drawback / Venturi Solid State Relay
I = USB Port (Firmware Updates / Data Logging)
J = 24 VDC Solenoid Valve Cable
K = Optional Venturi Solenoid Valve Cord Grip
Flow Sensor
Temperature Sensor
B
A
C
D
E
F
G
H
I
J
K

DPM-12GM-6-P1A-FP10-F-V1 10/31/2018 9
ROCON LLC
UNIT REAR VIEW
Supply flowmeter bluff
Return flowmeter bluff
USB Port for firmware updates

DPM-12GM-6-P1A-FP10-F-V1 10/31/2018 10
ROCON LLC
UNIT SIDE VIEW
E = Valve manual override knob
F = Stamped “C”
F
E
A = Power connector
B = PROFINET connectors
C = Shutoff valve DIN connector with LED
D = Supply valve
E = Valve manual override knob
A
B
C
D
E

DPM-12GM-6-P1A-FP10-F-V1 10/31/2018 11
ROCON LLC
HOW THE DELTAPOINT MONITORS COOLING WATER IN THE
ROBOTICS CELL
Each DeltaPoint unit has two vortex shedding flow meters. One flow meter monitors the supply path,
and the other flow meter monitors the return leg. The fluid strikes a bluff body, generating vortices
(eddies) that move downstream. The vortices form alternately, from one side to the other. A
piezoelectric sensor housed in a sensor tube directly downstream of the bluff senses the pressure
zones created by the vortices. The sensor generates a frequency directly proportional to the vortices
(flow). The pulses are then measured by the microprocessor.
An internal temperature sensor, housed in a small thermo-well downstream of the return flow sensor,
measures the fluid temperature.
The robotic cooling water enters through the SUPPLY port and travels through the inlet flow sensor,
continues through the TO CELL port and to the equipment to be cooled. Water that has cooled the
equipment reenters the unit through the FROM CELL port, through the return flow sensor and is then
discharged into the plant return water system.
The inlet and outlet flow meter signals are compared. When a cap is pulled or a hose bursts the flow in
the return leg drops below the supply leg. The microprocessor detects this difference and signals the
PROFINET master to stop welding. It also shuts off the cooling water via a solenoid valve in the supply
leg and a check valve in the return leg, thus stopping the water flow in both directions.

DPM-12GM-6-P1A-FP10-F-V1 10/31/2018 12
ROCON LLC
INSTALLATION
1. DeltaPoint unit is preferred to be mounted on the outside of the fence line, for ease of service.
2. DeltaPoint can be mounted in any orientation: horizontally, vertically or at any other angle. The
orientation has no effect on performance. It is suggested that unions or hosing be used when
connecting to the main supply and return piping, this will facilitate ease of maintenance or removal
of unit if needed.
Caution: Brass pipe nipples installed on the “Supply” and “From Cell” ports cannot be removed.
They are needed for proper operation of the flow sensors
3. See DIMENSIONS for mounting hole pattern.
4. Connecting fluid ports: The unit has ¾-inch NPT female pipe ports. Port 1 “SUPPLY” cooling water
into the unit, Port 2 “TO CELL” cooling water to tooling or robot, Port 3 “FROM CELL” returns water
from the cell or robot. Port 4 “RETURN” cooling water leaving the DeltaPoint unit.
5. Units can be installed where the pipe or hose diameter is larger than the port size. Do not exceed
1-inch pipe or hose diameter with the 12 GPM unit.
Caution: Water flow cannot exceed 15 GPM for a 12 GPM unit.
6. Open the water inlet ball valve SLOWLY to prevent water hammer damage to the SENSORS.
7. Connect the electrical power and PROFINET cables. All units have an Electrical Callout Tag
reference page 20 that describes the pin number, location, wire color and function.

DPM-12GM-6-P1A-FP10-F-V1 10/31/2018 13
ROCON LLC
START-UP TEST CYCLE
Shut-Off Fault Alarm and PROFINET Master Fault Alarm Test
If unit is operational with water flow present:
1. Turn one of the cooling water shutoff valves OFF.
2. The LCD screen indicates “Water Flow Fault.”
3. The LED status lights indicate that:
a) Minimum/Low Flow –Solid (Yellow)
b) Shut-Off Closed –Solid (Red)
4. The DIN Connector LED on Solenoid Valve is OFF, because the shut-off valve solenoid coil is
deactivated.
5. Confirm that the PROFINET master received “Water Flow Fault” through the PROFINET
communication (see PROFINET I/O MAP).
6. Open the cooling water ball valve; push RESTART. Unit should be activated as described above.
7. If no problems occurred, proceed to the next test. If unit did not pass, see TROUBLESHOOTING.
Leak and Response Time Test
If unit is operational with water flow present:
1. Pull off one of the weld gun arm electrode caps.
2. The water shuts off and the LCD screen indicates “Fault.” Status Lights #1 and #3 are activated.
3. Reinstall weld gun cap.
4. Send a remote RESTART (through PROFINET) or push RESTART on the front panel of the unit
and wait 3 seconds for the unit to return to normal operation.
5. Pull off the other weld gun arm cap. And verify Steps 1-4, above.
6. If a faster response time is needed, lower the response time and/or the leak rate (see USER
MENU).
CAUTION:
•If the setting gets too low or is too fast, false leak faults could occur. Continue testing until
satisfactory results are obtained.
7. When the unit passes the above tests, it is ready for the production line.

DPM-12GM-6-P1A-FP10-F-V1 10/31/2018 14
ROCON LLC
ELECTRICAL CONNECTORS
Supply Power Connector
1 = 0V Out
2 = 0V Sensor
3 = Chassis GND
4 = 24V Sensor
5 = 24V Out
Dual PROFINET
Ports
Supply
Power

DPM-12GM-6-P1A-FP10-F-V1 10/31/2018 15
ROCON LLC
INDICATOR LIGHTS, PROGRAMMING KEYPAD, AND LCD
MESSAGES EXPLAINED
Color
Status
Function
Comments
1
Green
Solid
OK
Programmable. Flow => Flow OK setpoint. LCD shows “Flow
OK”
1
Green
Solid
Temperature Fault
Programmable. Temperature exceeds Temp. Fault setpoints
High or Low. LCD shows “Fault” on the second line.
1
Red
Solid
Low Flow, Minimal
Flow
See below.
2
Yellow
Solid
Low Flow
Non-programmable. Flow is between Min Flow and Flow OK
setpoints. LCD shows “Low”
2
Yellow
Solid
Minimal Flow
Programmable. Flow =< Min Flow setpoint. LCD shows “Min”
3
Red
Solid
Valve Shut
Shut-off valve closed. Can happen when leak exceeds Leak
Rate setpoint or flow < Low Flow. In both cases the LCD will
display “Fault”.
4
Yellow
Solid
In Bypass
“BYPASS” button pushed, shut-off valve forced open. Note:
When the front panel “BYPASS” button is pushed it sends a
signal to the PROFINET controller, Bypass must be set by this
controller.
5
Green
Solid
Power On
24V-DC power present
6
Green /
Red
Solid
PROFINET Module
Green LED OK - Red LED indicates error (internal)
7
Green /
Red
Solid or
Flashing
PROFINET Network
Flashing Green LED means waiting for scanner communication
Red LED indicates error
7
5
4
3
2
1
6

DPM-12GM-6-P1A-FP10-F-V1 10/31/2018 16
ROCON LLC
User Menu Features
1. Pressing the PROGRAM button takes user into the “Options Menu”
2. Successive Presses of PROGRAM button displays the following menu options. Use UP
or DOWN button to increase or decrease the setpoints and press ENTER to save it.
a. IP address: To change the IP address, use ENTER button to navigate through
individual column
As usual UP and DOWN will add or subtract (in this case by 1) the address. Press
PROGRAM to enter.
Note: IP address is subject to be set by the Master (PLC/PROFINET Software). So,
whatever user sets can be later changed by the PLC in which case IP address set by
the user gets overridden and the new IP is displayed.
b. Subnet Mask: Same as IP address.
c. Set Flow OK: Sets the desired limit for optimum cooling to the weld tips.
d. Set Min Flow: Sets the limit for the minimum flow
e. Set Leak Rate: Sets the leak rate above which there is fault and the valve closes
f. Set Under Temp: Sets the warning limit for low temperature. Below this
temperature, the status bit for the under temperature is set.
g. Set Over Temp: Sets the warning limit for the higher temperature. Above this limit,
the status bit for the over temperature is set.
h. Response Time: Set the response time for the fault detection. Lower the value,
faster the response.
i. Restart Delay: Set the reset delay for the device after a reset command has been
issued locally or remotely.
j. Set Units: Set the units to be Metric or English.
k. BP Request Time: This is the time for which request is sent to the master and then
the bit clears itself after this time. The Bypass request bit is set for this time in the
status byte.

DPM-12GM-6-P1A-FP10-F-V1 10/31/2018 17
ROCON LLC
Important Note
Priority will always be given to the settings sent from the PROFINET Master. The change
of setpoints from the user button requires:
1. PROFINET Master is not connected or,
2. PROFINET Master sends 0 to the corresponding setpoints
3. PROFINET Master got disconnected and user resets the device locally pressing
RESTART button
Individual (Standalone) Button Press Features
1. PROGRAM: Pressing PROGRAM would take the user to the settings. See “Menu
Features” above
2. UP: Displays the current status bits
3. DOWN: Displays the return flow from the Gun (R) on the lower line of the LCD
4. ENTER: Shows the firmware version, current IP, Subnet and MAC.
5. RESET: Will reset the device after the reset time set by the user.
6. BYPASS: Sends a Bypass Signal to the PROFINET Master/Client.
LCD Display Features
The upper line of the LCD displays the Supply Flow, and Flow related faults (if any).
The lower line displays the temperature of the Gun supply and temperature related faults
(if any).
24.7 LPM
22°C OK
6.54 GPM
71°F OK
°F: Degree Fahrenheit, implies that the units are English
The unit of Flow is hence GPM
°C: Degree Celsius, implies that the units are Metric
The unit of Flow is hence LPM

DPM-12GM-6-P1A-FP10-F-V1 10/31/2018 18
ROCON LLC
Fault notification
Fault messages Display:
Fault messages for caploss or over or under temperature will be displayed next to the reading
that relates to the fault
Fault messages such as Return > Supply, Fault will be displayed in the lower row of the LCD
display.
PROFINET Master Commands such as Bypass or Shutoff will also be displayed in the lower
row of the LCD display
0.00 GPM
Return > Supply
6.10 LPM
70
°C Fault
10.5 LPM OK
27
°C Shutoff
10.5 LPM OK
27
°C Bypass
PNET RESET
Restart: 3,2,1…
10.5 LPM Fault
22.3
°C OK

DPM-12GM-6-P1A-FP10-F-V1 10/31/2018 19
ROCON LLC
PROFINET LED LIGHTS
The Module Status LED has the follow states:
MS LED State
Description
Off
The PROFINET Module is not active/not powered.
Flashing Green
The PROFINET Module is in standby.
Solid Green
The PROFINET Module is ready
Flashing Red
The PROFINET Module has a recoverable fault.
Solid Red
The PROFINET Module has an unrecoverable fault
Flashing Green/Red
The PROFINET Module is self-testing
The Network Status LED has the follow states:
NS LED State
Description
Off
The PROFINET Module is not online.
Flashing Green
The PROFINET Module is online, but not connected.
Solid Green
The PROFINET Module has an active connection that is not timed out.
Flashing Red
The PROFINET Module has a timed-out I/O connection.
Solid Red
The PROFINET Module has a communication fault (usually this indicates a
duplicate IP Address).
Flashing Green/Red
The PROFINET Module is self-testing

DPM-12GM-6-P1A-FP10-F-V1 10/31/2018 20
ROCON LLC
PROFINET SETUP
Software Used
1. PROFINET Commander v3.1
2. Siemens “SIMATIC NET, PC Software, Edition 2008+SP2”
Setting up SIMATIC NCM Manager
1. Open the SIMANTIC NCM Manager software and double click on Configuration. Then go to
Options-> Install GSD file.
Table of contents
Popular Portable Generator manuals by other brands

Pinnacle Aquatic
Pinnacle Aquatic HYPROLYSER Compact 240 user guide
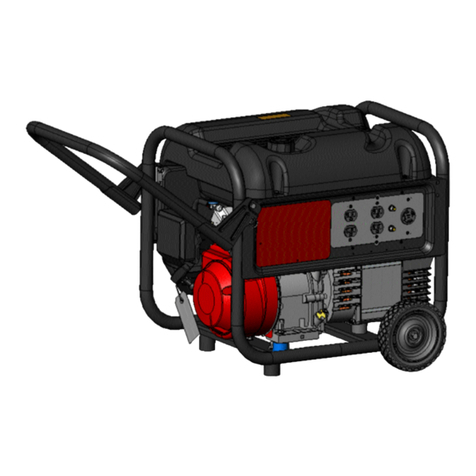
Powermate
Powermate PM0545007.03 manual
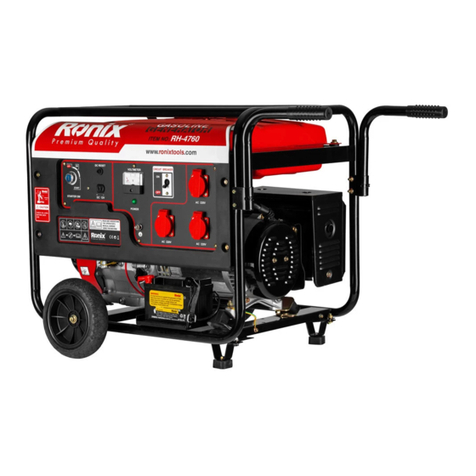
Ronix
Ronix RH-4760 manual
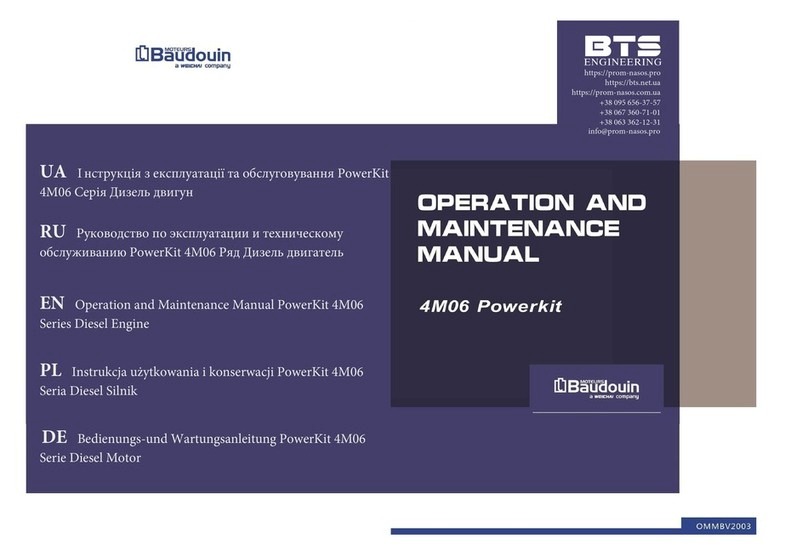
WEICHAI
WEICHAI Baudouin 4M06 Powerkit Operation and maintenance manual

ESCO Technologies
ESCO Technologies ETS-Lindgren EMGen 7003-003 user manual
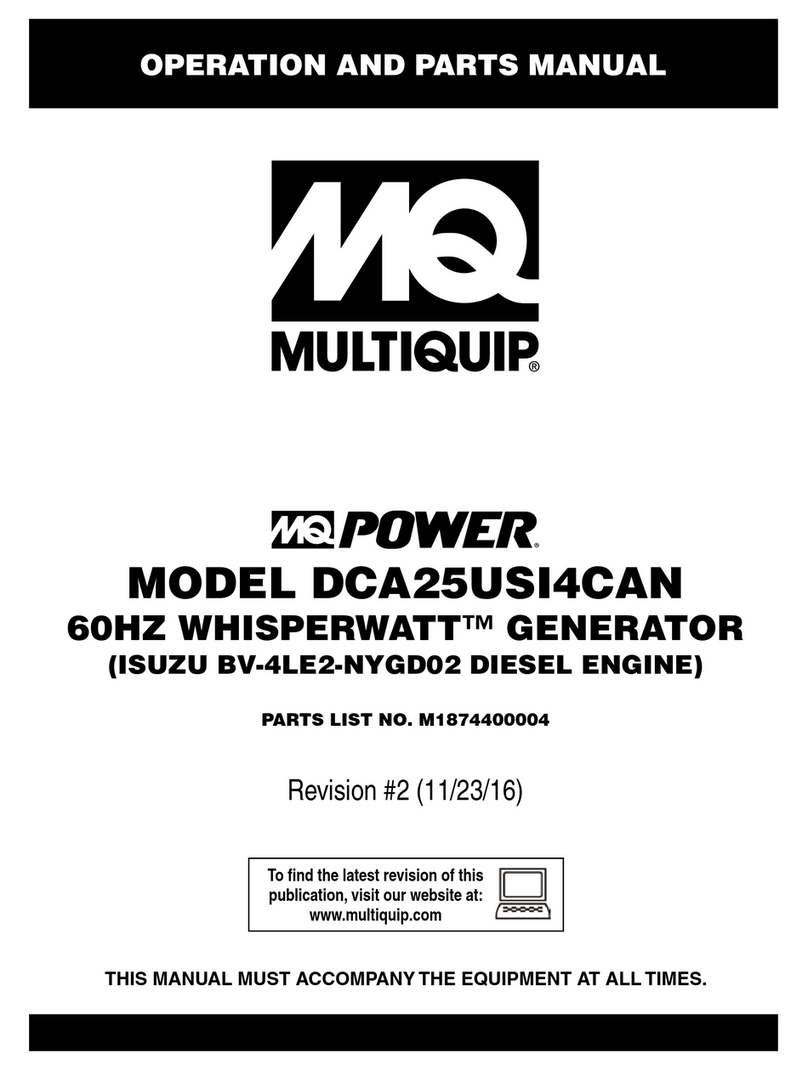
MULTIQUIP
MULTIQUIP WHISPERWATT DCA25USI4CAN Operation manual

Campbell Hausfeld
Campbell Hausfeld GN0800 operating instructions

Gude
Gude GSE 951 Translation of the original instructions
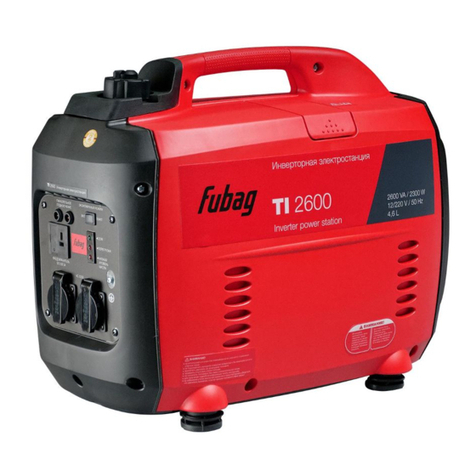
Fubag
Fubag TI1000 Operator's manual
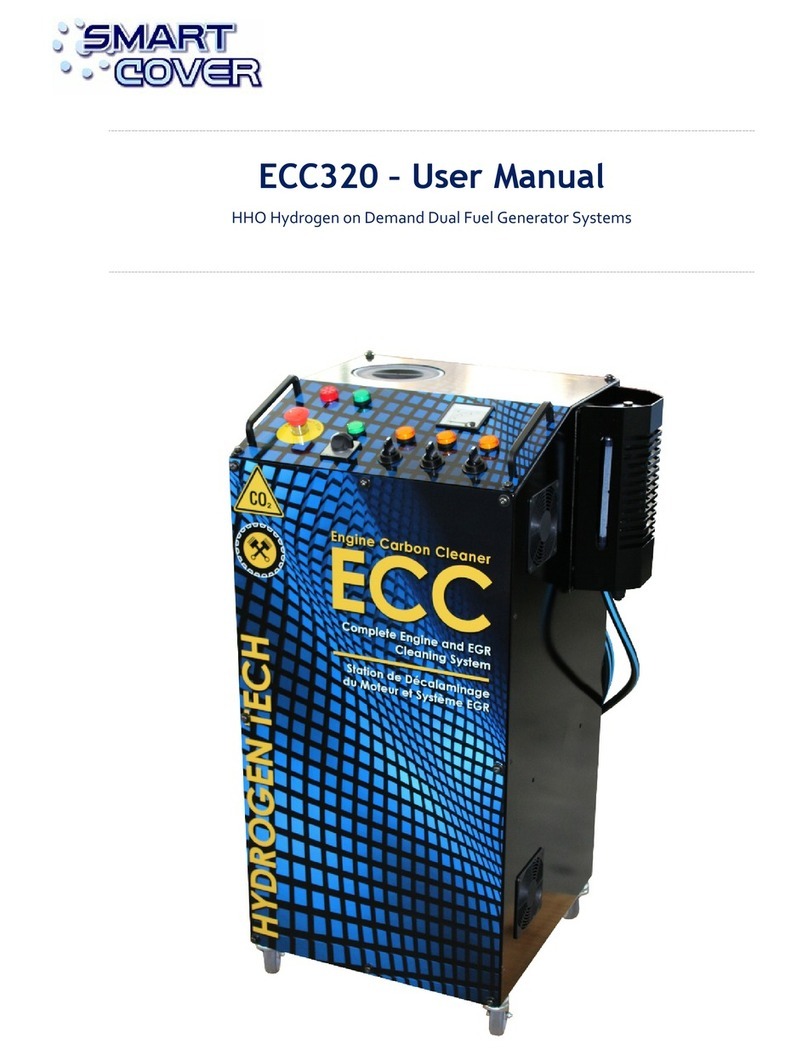
Smart Cover
Smart Cover ECC320 user manual
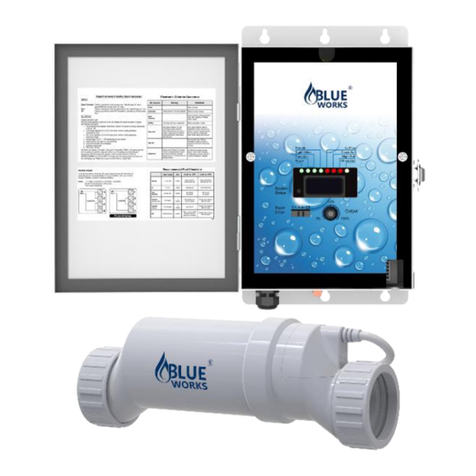
Blueworks
Blueworks BLH Series Installation and operation manual

NorthStar
NorthStar 6500 DPG owner's manual