Denon MC2000 User manual

SERVICE MANUAL
D&M Holdings Inc.
MODEL JP E3 E2 EK EA E1 E1K E1C
MC2000
PPP
DJ Controller
Ver. 3
S0620-0V03DM/DG1302
• Some illustrations using in this service manual are slightly different from the actual set.
• Please use this service manual with referring to the operating instructions without fail.
• For purposes of improvement, specications and design are subject to change without notice.
Please refer to the
MODIFICATION NOTICE.

2
CONTENTS
SAFETY PRECAUTIONS ..........................................................3
NOTE FOR SCHEMATIC DIAGRAM.........................................4
TECHNICAL SPECIFICATIONS................................................5
DIMENSION ...............................................................................5
DISASSEMBLY ..........................................................................6
SPECIAL MODE ......................................................................12
1. Special mode setting...........................................................12
2. Version Up mode.................................................................12
3. Version indicate mode .........................................................13
4. Adjusting mode of the touch sense sensitivity.....................14
5. Initialization of parameters ..................................................14
6. Adjusting interval time of MIDI command transmission.......15
7. SW, VOLUME, ENCODER and LED TEST.........................16
WHEN THE MICROPROCESSOR IS
REPLACED WITH A NEW ONE ..............................................23
PROCEDURE FOR UPGRADING
THE VERSION OF THE FIRMWARE ......................................23
TROUBLE SHOOTING............................................................32
WIRING DIAGRAM..................................................................41
BLOCK DIAGRAM...................................................................43
POWER BLOCK DIAGRAM....................................................44
Level DIAGRAM ......................................................................45
PRINTED WIRING BOARDS...................................................46
CONTROL ..............................................................................46
I/O ..........................................................................................48
SCHEMATIC DIAGRAMS (1/2) ...............................................50
CONTROL UNIT .....................................................................50
I/O UNIT ..................................................................................51
EXPLODED VIEW....................................................................52
PARTS LIST OF EXPLODED VIEW........................................53
PACKING VIEW .......................................................................55
PARTS LIST OF PACKING & ACCESSORIES.......................55
SEMICONDUCTORS ...............................................................57
1. IC's ......................................................................................57
PARTS LIST OF P.C.B. UNIT ..................................................68
CONTROL P.C.B ASS'Y..........................................................68
I/O P.C.B ASS'Y.......................................................................71
CROS FADER P.C.B ASS'Y....................................................75
PHONE P.C.B ASS'Y...............................................................75

3
SAFETY PRECAUTIONS
The following items should be checked for continued protection of the customer and the service technician.
LEAKAGE CURRENT CHECK
Before returning the set to the customer, be sure to carry out either (1) a leakage current check or (2) a line to chassis
resistance check. If the leakage current exceeds 0.5 milliamps, or if the resistance from chassis to either side of the
power cord is less than 460 kohms, the set is defective.
Be sure to test for leakage current with the AC plug in both polarities, in addition, when the set's power is in each state (on,
off and standby mode), if applicable.
CAUTION Please heed the following cautions and instructions during servicing and
inspection.
◎Heed the cautions!
Cautions which are delicate in particular for servicing
are labeled on the cabinets, the parts and the chassis,
etc. Be sure to heed these cautions and the cautions
described in the handling instructions.
◎Cautions concerning electric shock!
(1) An AC voltage is impressed on this set, so if
you touch internal metal parts when the set is
energized, you may get an electric shock. Avoid
getting an electric shock, by using an isolating
transformer and wearing gloves when servicing
while the set is energized, or by unplugging the
power cord when replacing parts, for example.
(2) There are high voltage parts inside. Handle with
extra care when the set is energized.
◎Caution concerning disassembly and
assembly!
Through great care is taken when parts were
manufactured from sheet metal, there may be burrs
on the edges of parts. The burrs could cause injury if
ngers are moved across them in some rare cases.
Wear gloves to protect your hands.
◎Use only designated parts!
The set's parts have specic safety properties (re
resistance, voltage resistance, etc.). Be sure to use
parts which have the same properties for replacement.
The burrs have the same properties. In particular, for
the important safety parts that are indicated by the z
mark on schematic diagrams and parts lists, be sure to
use the designated parts.
◎Be sure to mount parts and arrange the wires
as they were originally placed!
For safety seasons, some parts use tapes, tubes or
other insulating materials, and some parts are mounted
away from the surface of printed circuit boards.
Care is also taken with the positions of the wires by
arranging them and using clamps to keep them away
from heating and high voltage parts, so be sure to set
everything back as it was originally placed.
◎Make a safety check after servicing!
Check that all screws, parts and wires removed or
disconnected when servicing have been put back in
their original positions, check that no serviced parts
have deteriorate the area around. Then make an
insulation check on the external metal connectors and
between the blades of the power plug, and otherwise
check that safety is ensured.
(Insulation check procedure)
Unplug the power cord from the power outlet,
disconnect the antenna, plugs, etc., and on the power.
Using a 500V insulation resistance tester, check that
the insulation resistance value between the inplug and
the externally exposed metal parts (antenna terminal,
headphones terminal, input terminal, etc.) is 1MΩ or
greater. If it is less, the set must be inspected and
repaired.
Many of the electric and the structural parts used in
the set have special safety properties. In most cases
these properties are difcult to distinguish by sight, and
the use of replacement parts with higher ratings (rated
power and withstand voltage) does not necessarily
guarantee that safety performance will be preserved.
Parts with safety properties are indicated as shown
below on the wiring diagrams and the parts list in this
service manual. Be sure to replace them with the parts
which have the designated part number.
(1) Schematic diagrams.......Indicated by the z mark.
(2) Parts lists.......Indicated by the z mark.
The use of parts other than the
designated parts could cause electric
shocks, res or other dangerous
situations.
CAUTION Concerning important safety
parts

4
NOTE FOR SCHEMATIC DIAGRAM
WARNING:
Parts indicated by the z mark have critical characteristics. Use ONLY replacement parts recommended by the manufacturer.
CAUTION:
Before returning the set to the customer, be sure to carry out either (1) a leakage current check or (2) a line to chassis resistance check. If
the leakage current exceeds 0.5 milliamps, or if the resistance from chassis to either side of the power cord is less than 460 kohms, the set
is defective.
WARNING:
DO NOT return the set to the customer unless the problem is identied and remedied.
NOTICE:
ALL RESISTANCE VALUES IN OHM. k=1,000 OHM / M=1,000,000 OHM
ALL CAPACITANCE VALUES ARE EXPRESSED IN MICRO FARAD, UNLESS OTHERWISE INDICATED. P INDICATES MICRO-MICRO
FARAD. EACH VOLTAGE AND CURRENT ARE MEASURED AT NO SIGNAL INPUT CONDITION. CIRCUIT AND PARTS ARE SUBJECT
TO CHANGE WITHOUT PRIOR NOTICE.
NOTE FOR PARTS LIST
Parts indicated by "nsp" on this table cannot be supplied.
When ordering a part, make a clear distinction between "1" and "I" (i) to avoid mis-supplying.
A part ordered without specifying its part number can not be supplied.
General-purpose Carbon Chip Resistors are not included are not included in the P.W.Board parts list.
(Refer to the Schematic Diagram for those parts.)
Parts indicated by the zmark have critical characteristics. Use ONLY replacement parts recommended by the manufacturer.
General-purpose Carbon Film Resistor in the P.W.Board parts list. (Refer to the Schematic Diagram for those parts.)
Part indicated by "★" mark is not illustrated in the exploded view.
WARNING:
1.
2.
3.
4.
5.
6.
●Resistors
RD : Carbon
RC : Composition
RS : Metal oxide film
RW: winding
RN : Metal film
RK : Metal mixture
P : Pulse-resistant type
NL : Low noise type
NB : Non-burning type
FR : Fuse-resistor
F : Lead wire forming
2B : 1/8 W
2E : 1/4 W
2H : 1/2 W
3A : 1 W
3D : 2 W
3F : 3 W
3H : 5 W
F : ±1%
G:±2%
J : ±5%
K : ±10%
M : ±20%
Ex.: RN
Type
14K
Shape
and per-
formance
2E
Power
182
Resist-
ance
G
Allowable
error
FR
Others
*Resistance
1800ohm=1.8kohm1 8 2
Indicates number of zeros after effective number.
2-digit effective number.
1.2ohm1 R 2
2-digit effective number, decimal point indicated by R.
1-digit effective number.
: Units: ohm
●Capacitors
CE : Aluminum foil
electrolytic
CA : Aluminium solid
electrolytic
CS : Tantalum electrolytic
CQ : Film
CK : Ceramic
CC : Ceramic
CP : Oil
CM: Mica
CF : Metallized
CH : Metallized
HS : High stability type
BP : Non-polar type
HR : Ripple-resistant type
DL : For change and discharge
HF : For assuring high frequency
U : UL part
C : CSA part
W : UL-CSA part
F : Lead wire forming
0J : 6.3 V
1A : 10 V
1C : 16 V
1E : 25 V
1V : 35 V
1H : 50 V
2A : 100 V
2B : 125 V
2C : 160 V
2D : 200 V
2E : 250 V
2H : 500 V
2J : 630 V
F : ±1%
G:±2%
J : ±5%
K : ±10%
M : ±20%
Z : ±80%
: - 20%
P : +100%
C : ±0.25pF
D : ±0.5pF
= : Others
Ex.: CE
Type
04W
Shape
and per-
formance
1H
Dielectric
strength
3R2
Capacity
M
Allowable
error
BP
Others
・Units:μF.
2200μF2 2 2
Indicates number of zeros after effective number.
2-digit effective number. ・Units:μF.
2.2μF2 R 2
2-digit effective number, decimal point indicated by R
1-digit effective number.
*Capacity (electrolyte only)
・When the dielectric strength is indicated in AC,"AC" is included after the dielectric strength value.
*Capacity (except electrolyte)
・Units:pF
2200pF=0.0022μF2 2 2
Indicates number of zeros after effective number. (More than 2)
2-digit effective number. ・Units:pF
220pF2 2 1
2-digit effective number.
Indicates number of zeros after effective number. (0 or 1)
NOTE FOR PARTS LIST

5
TECHNICAL SPECIFICATIONS
DIMENSION
nAudio (0 dBu=0.775 Vrms, 0 dBV =1 Vrms)
• LINE inputs 1 Stereo
Unbalanced RCA terminal
Input impedance: 10 kΩ
Level: 0 dBV
Signal to Noise ratio: Over 82 dB
• Microphone inputs 1 Monaural
Microphone : Balanced 1/4 in. TRS terminal
(Tip: hot, Ring: cold, Sleeve: ground)
Input impedance: 10 kΩ
Level: –48 – –20 dBu (Unity = –40 dBu)
• USB AUDIO inputs 2 Stereo (4 Monaural) 16 bit, Fs: 48 kHz USB B
• MASTER output
Unbalanced: Stereo RCA terminal
Load impedance: 10 kΩ
Level: 2.55 dBV (Max +10dBV)
Frequency response: 20 Hz – 20 kHz (±1 dB)
THD: Less than 0.05 %
Crosstalk: Less than –85 dB (1 kHz)
• Headphone output Stereo 1/4 in. (1 mm)
Load impedance: 40 Ω
Level: Over 50 mW
nGeneral
USB MIDI input/output: IN: 1ch, OUT: 1ch MIDI 1.0, USB B
Channel fader: PPM 7 Point LED –20 – +10 dB, Peak
CH fader: 45 mm slim type fader
Cross fader: 45 mm fader
Power supply voltage: 5 V (USB Bus Power)
Power consumption: 500 mA
Operating
temperature:
+5 °C – +35 °C
Operating humidity: 25 % – 85 %
Storage temperature: –20 °C – +60 °C
400mm
10.6mm
11.5mm
50.0mm
240.0mm
4.6mm

6
DISASSEMBLY
• Disassemble in order of the arrow in the following gure.
• In the case of the re-assembling, assemble it in order of the reverse of the following ow.
• In the case of the re-assembling, observe "attention of assembling".
• If wire bundles are untied or moved to perform adjustment or replace parts etc., be sure to rearrange them neatly as
they were originally bundled or placed afterward.
Otherwise, incorrect arrangement can be a cause of noise generation.
Bottom BASE
Refer to "DISASSEMBLY
2. BOTTOM BASE"
and "EXPLODED VIEW"
I/O PCB ASS'Y
Refer to "DISASSEMBLY
11-4. I/O PCB ASS'Y"
and "EXPLODED VIEW"
I/O PCB ASS'Y
(Ref. No. of EXPLODED VIEW : 6)
PHONE PCB ASS'Y
Refer to "DISASSEMBLY
3. PHONE PCB ASS'Y"
and "EXPLODED VIEW"
PHONE PCB ASS'Y
(Ref. No. of EXPLODED VIEW : 8)
TOP PANEL ASS'Y
Refer to "DISASSEMBLY
4. TOP PANEL ASS'Y"
and "EXPLODED VIEW"
TOP PANEL ASS'Y
(Ref. No. of EXPLODED VIEW : 2)
WHEEL ASS'Y
Refer to "DISASSEMBLY
10. WHEEL ASS'Y"
and "EXPLODED VIEW"
WHEEL ASS'Y
(Ref. No. of EXPLODED VIEW : 3)
CROSS FADER PCB ASS'Y
Refer to "DISASSEMBLY
6. CROSS FADER PCB ASS'Y"
and "EXPLODED VIEW"
CROSS FADER PCB ASS'Y
(Ref. No. of EXPLODED VIEW : 5)
CONTROL PCB ASS'Y / SOFT KNOB
Refer to "DISASSEMBLY
5. CONTROL PCB ASS'Y / SOFT KNOB"
and "EXPLODED VIEW"
CONTROL PCB ASS'Y
(Ref. No. of EXPLODED VIEW : 7)
BUTTON
Refer to EXPLODED VIEW

7
Disassembl
y
Illustration
1.Dismantle the packaging, taking out
the machine .
2. Remove the screws form bottom base .
3. Disconnect the FCC cable,then remove
the panel from bottom base .
1
2
3
4
7
8
5
6
11
12
13 14
螺絲*14
602-XM610-522
9
10
CONTROL PCB
I/O PCB
Remove the FFC cable
from I/O PCB(REF
N
O.CN300A)
SCREW *14
CN300A

8
Disassembl
y
Illustration
4.Remove the rotary knob *20 and
push knob*5 from panel .
5.Remove the screws *14 from panel .
6-1. Remove the nuts*20 and washer *20
from panel .
6-2. Remove the screws *2 from
crossfader pcb ass'y .
1
602-HP1010K-182
螺絲*14
2
6
5
3
4
10
9
7
8
14
13
12
11
面板
(數量各20P.S.)
602-PTF3010-585
螺絲*2
鎖付VR之螺母與墊圈
Screw *14
p
anel
N
ut *20
Washer *20
Screw *2

9
Disassembl
y
Illustration
7-1.Remove the screws *21 from control pcb ass'y .
7-2.Remove the ground plates *6 and the screws*6 .
8. Remove the solder *2 ,then remove the
control pcb ass'y .
9.Remove the square buttons and rotary buttons .
SOLDER*

10
Disassembl
y
Illustration
10-1.Remove the wheel ass'y*2 .
10-2. Remove the spring & wire ass'y *2 .
11-1. Remove the screws *7 from the bottom base.
11-2. Remove the nut *2 and washer *2 from phone jack.
11-3. Remove the rotary knob(small) *2 .
E-RING

11
Disassembl
y
Illustration
11-4. Remove the screws *4 from I/O pcb ass'y,
then remove the I/O pcb ass'y .
602-QMX2BPM-322
自攻螺絲*2 602-B300-041
螺絲*2
I/O基板整組
Screw *2
Screw *2
I/O pcb ass'y

12
SPECIAL MODE
1. Special mode setting
Turns on MC3000 while pressing buttons A, B and C.
Mode A B C Contents
Version Up mode 2 4 6 Firmware Upgrade
Version indicate mode 1 4 6 Firmware version display
Adjusting mode of the touch sense sensitivity 345Adjust sensitivity of JOG wheel.
Initialize mode 2 4 5, 6 Return to factory default setting.
MIDI transmission time mode 1 4 7 MIDI command transmission interval time
SW, VOLUME, ENCODER and LED TEST ---Test of each function. (Use PC)
ALL LED ON 2 4 SEL. All LED turn on
2. Version Up mode
Version up processing
z Refer to "PROCEDURE FOR UPGRADING THE VERSION OF THE FIRMWARE" for the procedure of the rmware
update. (Refer to 23 page.)
1 2 3 4 765

13
3. Version indicate mode
Conrmation of version
Pressing (SHIFT+BROWSE1+FWD) at the same time, then connect MC2000 to a PC for conrmation of F/W version.
How to read the version number
Firmware Version LED (Ver A.XYZ. After Ver1.000, it is commercial version).
A : LEFT DECK (for commercial version No.)
X, Y, Z : RIGHT DECK
1 2 3 4 5 6 7 8 9
A (LEFT DECK)
FX1-1 FX1-2 FX1-3 LOOP IN LOOP OUT AUTO HOT CUE 1 HOT CUE 2 HOT CUE 3
X (RIGHT DECK)
FX2-1 FX2-2 FX2-3 - - - - - -
Y (RIGHT DECK)
LOOP IN LOOP OUT AUTO - - - - - -
Z (RIGHT DECK)
HOT CUE 1 HOT CUE 2 HOT CUE 3 HOT CUE 4 SYNC CUE PLAY VINYL MODE -
Example : Ver1.132
DECK A side : FX1-1
DECK B side : FX2-1, LOOP IN, LOOP OUT, AUTO, HOT CUE 1, HOT CUE 2
Seven places of LED turns on.
Press SHIFT to return to normal mode.
1 2 3
4 5
8 9
6
7
6
57
8
1 2 3 4
1 2 3
1 2 3
A: The 1st digit numeric display. X: The 2nd digit numeric display. Y: The 3rd digit numeric display.
Z: The 3rd digit numeric display.

14
4. Adjusting mode of the touch sense sensitivity
The unit can control the sensitivity of the touch sensor for the Jog Wheel in 9 steps (-4 to 0 to +4).
“-4” is the lowest sensitivity, and “+4” is the highest sensitivity.
The default setting is “0”.
(1) Pressing (SHIFT+LOAD A+LOAD B) at the same time, then connect MC2000 to a PC.
(2) Press CUE, and switch the jog wheel that you want to adjust.
(e.g.) If you press CUE of the left side, only CUE of the left side turns on, and jog wheel of the left deck is chosen to
adjust it.
(3) Rotate the track selection knob, and adjust the sensitivity. The button lights according to the set sensitivity.
Adjust level -4 -3 -2 -1 0 1 2 3 4
Buttons HOT CUE 1 HOT CUE 2 HOT CUE 3 LOOP IN LOOP OUT AUTO FX1/2-1 FX1/2-2 FX1/2-3
(4) Press the track selection knob to memorize adjustment data.
(5) Press SHIFT, then the mode switches back from the sensitivity adjustment mode to the normal mode.
5. Initialization of parameters
Return to factory default setting.
(1) Pressing (SHIFT+BACK+FWD+LOAD B) at the same time, then connect MC2000 to a PC .
(2) Return to default setting, and these data (as follows) turn to factory default setting.
Upon completion of the adjustment, it automatically restarts, start in Normal mode.
Initialize Data Factory default Range
JW transmission interval time 4ms 3ms ⇔20ms
Sensitivity of JOG Wheel 0 -4 ⇔4
2 3 4
-1 0
-3 -2
1
-4
2 3 4
-1 0
-3 -2
1
-4
Left deck Right deck

15
6. Adjusting interval time of MIDI command transmission
Setting the MIDI command transmission interval time.
Depending on the computer specications and OS type, the computer may not be able to receive the MIDI commands
transmitted from this unit correctly.
In this case, use the following operation to set the MIDI command transmission interval time to a suitable value.
(1) Pressing (SHIFT+BROWSE1 +BROWSE2) at the same time, then connect MC2000 to a PC .
The following LED turns on, and the unit switches to the setting mode for MIDI command transmission interval time.
(2) Rotate SEL..
The relationship between LED display position and the MIDI command transmission interval time is as shown in the
diagram as follows. The factory setting is 4 msec.
(3) Press SEL..
The MIDI command transmission interval time is entered.
(4) Press SHIFT.
The settings are completed, and unit exits the setting mode.
How to read the interval time
Interval time [ms] - - 3 4 5 6 7 8 9 10
LEFT DECK HOT CUE 1 HOT CUE 2 HOT CUE 3 HOT CUE 4 LOOP IN LOOP OUT AUTO FX1-1 FX1-2
FX1-3
Interval time [ms] 11 12 13 14 15 16 17 18 19 20
RIGHT DECK HOT CUE 1 HOT CUE 2 HOT CUE 3 HOT CUE 4 LOOP IN LOOP OUT AUTO FX2-1 FX2-2
FX2-3
Example : 13ms
LEFT DECK : HOT CUE1-4, LOOP IN, LOOP OUT, AUTO, FX1-1 ~ FX1~3
RIGHT DECK : HOT CUE1-3
13 places of LED turns on.
Press [SHIFT] to return to Normal Mode.
8 9 10
5 6
3 4
7
18 19 20
15 16
12 13 14
17
11
3 ~ 10ms 11~20ms

16
7. SW, VOLUME, ENCODER and LED TEST
Operating check procedure for the SW/VOLUME/ENCODER and LEDs on this unit with MIDI-OX.
[1] MIDI-OX Installation and Settings
Install MIDI-OX on the PC, and congure the PC environment.
(1) Download MIDI-OX (freeware).
Download from the URL below.
URL: www.midiox.com/
(2) Install MIDI-OX on the PC.
(3) Connect this unit to the PC, and switch the power on.
(4) Start MIDI-OX that you installed on the PC.
(5) In MIDI-OX, select [View] menu - [Input Monitor].
(6) Select [Window] menu - [Tile Horizontally].

17
(7) Open the [Actions] menu and check that “Stop Display” is shown.
If “Start Display” is shown, click “Start Display” so that “Stop Display” is shown.
[2] Check the SW/VOLUME/ENCODER
When SW/VOLUME/ENCODER is operated on this unit, the corresponding MIDI command is shown on MIDI-OX.
If the MIDI command is not shown on MIDI-OX even when the panel of this unit is operated, check the following.
(1) Select [Options] menu - [MIDI Device].

18
(2) Check whether the USB audio device is selected.
(3) Screen display when the EFX.1 button on this unit is switched ON-OFF.
Pressed button DATA1 column display
EFX.1 21
For details on the correspondence between operation on this unit and the contents of the screen display, see the
"MIDI command list" in the instruction manual.
Check that it is highlighted black.
If it is not highlighted, select it
so that it is highlighted black.

19
(4) Next, this is the screen display when the EFX.1 knob is moved either to the left or right.
Operated knob DATA1 column display
EFX.1 85
For details on the correspondence between operation on this unit and the contents of the screen display, see the
"MIDI command list" in the instruction manual.
(5) Next, this is the screen display when the TRACK SELECT knob on the unit is moved 1click to the right.
Operated knob DATA1 column display
TRACK SELECT 84
For details on the correspondence between operation on this unit and the contents of the screen display, see the
"MIDI command list" in the instruction manual.

20
[3] Check the LED
When the MIDI command is sent from MIDI-OX, the LED lights/ashes/off/Dimmer.
(1) Select [View] menu - [Control Panel].
(2) These are explained in order of LED lights/off/ashes/Dimmer.
Example1 : When lighting the EFX.1 button on DECK A
In the MIDI-OX Control Panel, set the following parameters.
Control Event Channel Value
74) Brightness 1 92
When the Enter button on the PC keyboard is pressed, the EFX.1 button on the unit lights.
Other manuals for MC2000
3
Table of contents
Other Denon Controllers manuals
Popular Controllers manuals by other brands
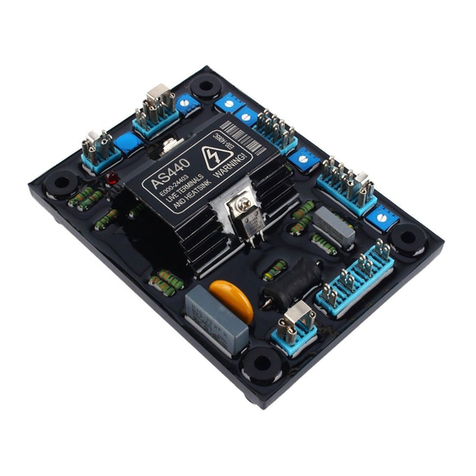
Datacom
Datacom AS440 Specification, Installation and Adjustments
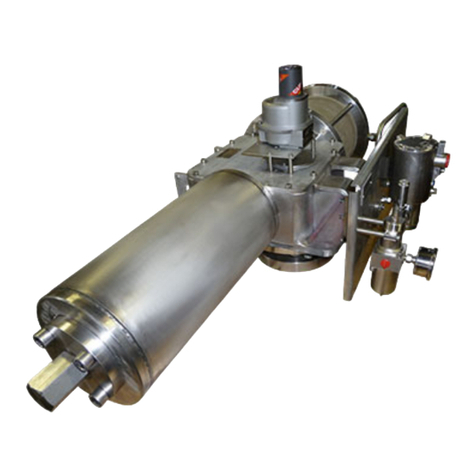
Paladon
Paladon PNS Series Installation, commissioning and maintenance manual
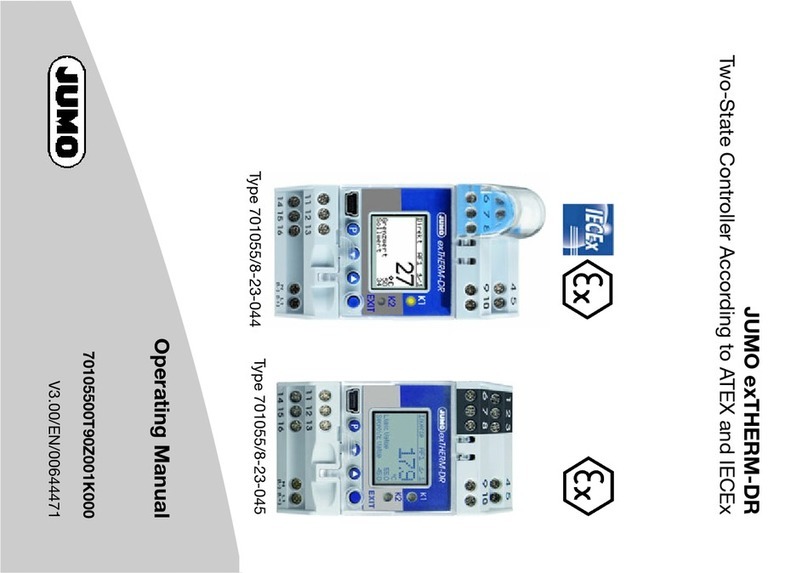
JUMO
JUMO exTHERM-DR operating manual
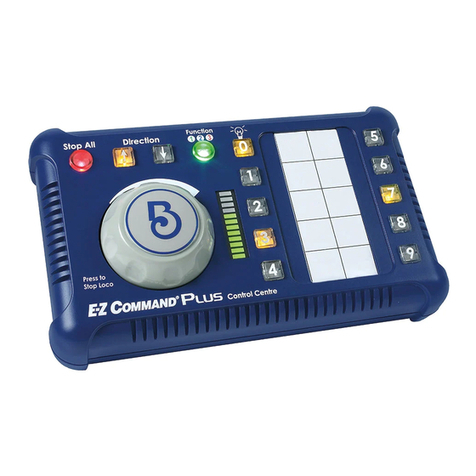
Bachmann
Bachmann E-Z Command Plus Setup and Programming Instructions
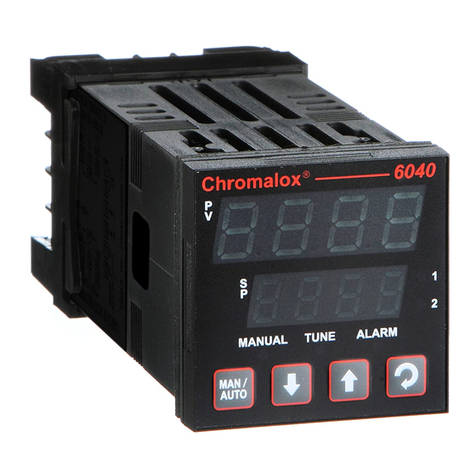
Chromalox
Chromalox 6040 Installation & operation manual
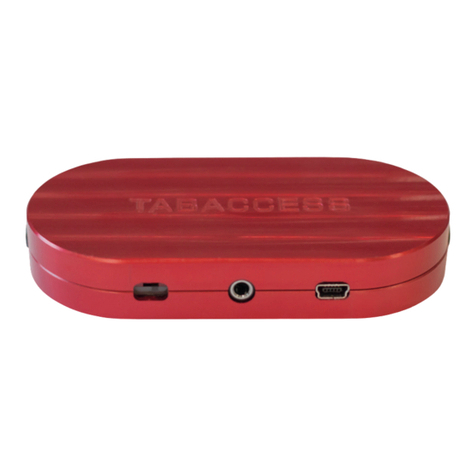
ZYROBOTICS
ZYROBOTICS TabAccess user guide