Dettson VTK1 Assembly instructions

2015-12-04 X40142 Rev.J
Manufactured by:
Industries Dettson inc.
3400 Industrial Boulevard
Sherbrooke, Quebec - Canada
J1L 1V8
Caution: Do not tamper with
the unit or its controls. Call a
qualified service technician.
Printed in Canada
Printed on 100% recycled paper
INSTALLER / SERVICE TECHNICIAN:
USE THE INFORMATION IN THIS MANUAL FOR THE INSTALLATION AND
SERVICING OF THE FURNACE AND KEEP THE DOCUMENT NEAR THE
UNIT FOR FUTURE REFERENCE.
HOMEOWNER:
PLEASE KEEP THIS MANUAL NEAR THE FURNACE FOR FUTURE
REFERENCE.
Models:
VTK1
VTK2
VTK098
VTK3
KLAVT0101DET
KLAVT0201DET
VTK-53A
VTK-54A
VTK-64A
VTK-65A
SEALED COMBUSTION
SYSTEM
(DIRECT VENT)

2
TABLE OF CONTENTS
1.0 SAFETY REGULATIONS....................................3
1.1 SAFETY LABELING AND WARNING SIGNS3
1.2 IMPORTANT NOTICE...................................3
2.0 INSTALLATION...................................................3
2.1 GENERAL.....................................................3
2.2 POSITIONING ..............................................4
2.2.1 Installation considerations .....................4
2.3 INSTALLATION OF THE COMPONENTS....5
2.3.1 Installing the terminal in the wall............5
2.3.2 Insulated flexible venting.......................6
2.3.3 Connection to the furnace breech .........7
2.3.4 Connection to the vent terminal.............7
2.4 CONNECTION OF THE AIR INTAKE PIPE..8
2.4.1 Additional parts required (not included in
VTK kit)..................................................8
2.4.2 Intake pipe length..................................8
2.4.3 Beckett AFII Burner ...............................8
2.4.4 Beckett NX Burner.................................8
2.4.5 Riello 40-BF burner................................8
2.4.6 Terminal connection ..............................8
2.4.7 Intermediate piping................................9
2.5 INSTALLATION OF THE BVSO JUMPER....9
3.0 OPERATION........................................................9
3.1 COMBUSTION GAS TEMPERATURE
VERIFICATION.............................................9
3.2 BURNER POST PURGE DELAY
ADJUSTMENT..............................................9
4.0 MAINTENANCE...................................................9
FIGURES
Figure 1: Minimum clearance............................................... 4
Figure 2: Components identification.....................................5
Figure 3: Installation of the terminal in the wall.................... 6
Figure 4: Installation of the stabiliser shroud........................6
Figure 5: Pressure switch location .......................................6
Figure 6: Caulking around the stabiliser shroud................... 6
Figure 7: Installation of the transition / terminal coupling..... 7
Figure 8: Seams alignment ..................................................7
Figure 9: Connection to the breech plate............................. 7
Figure 10: Connection to the vent terminal .......................... 8
Figure 11: BVSO jumper ...................................................... 9
Figure 12: Dimensions ....................................................... 11
Figure 13: Wiring Diagram................................................. 11
Figure 14: Parts List........................................................... 12
TABLES
Table 1: Minimum clearance around a vent system.............4
Table 2: Maximum and minimum vent pipe length............... 4
Table 3: Approved furnaces for used with VTK / IFV .........10
Table 4: Parts List .............................................................. 12

3
1.0 SAFETY REGULATIONS
1.1 SAFETY LABELING AND WARNING SIGNS
The words DANGER, WARNING and CAUTION are used to
identify the levels of seriousness of certain hazards. It is
important that you understand their meaning. You will notice
these words in the manual as follows:
DANGER
Immediate hazards that WILL result in death, serious
bodily injury and/or property damage.
WARNING
Hazards or unsafe practices that CAN result in death,
bodily injury and/or property damage.
CAUTION
Hazards or unsafe practices which CAN result in minor
bodily and /or material damage.
1.2 IMPORTANT NOTICE
WARNING
If the advice given in this manual is not heeded, it will
lead to consequences resulting in death, serious bodily
injury and/or property damage.
WARNING
Installations or repairs performed by unqualified
persons can result in hazards to them and to others.
Installations must conform to local codes or, in the
absence of same, to codes of the country having
jurisdiction.
The information contained in this manual is intended for
use by a qualified technician, familiar with safety
procedures and equipped with the proper tools and test
instruments.
Failure to carefully read and follow all instructions in
this manual can result in death, bodily injury and/or
property damage.
a. It is the homeowner’s responsibility to engage a
qualified technician for the installation and
subsequent servicing of this venting system.
b. Do not start the heating system if any part of it is
immersed in water. Call a qualified service
technician immediately, to assess the damage and
to replace all critical parts that are in contact with
water.
c. Do not store gasoline or any other flammable
substances, such as paper, carton, etc. near the
furnace.
IMPORTANT: All local and national code requirements
governing the installation of oil burning equipment, wiring
and flue connection MUST be followed. Some of the codes
that may apply are:
CSA B139: Installation Code for oil burning
equipment.
ANSI/NFPA 31: Installation of oil burning equipment.
ANSI/NFPA 90B: Warm air heating and air conditioning
systems.
ANSI/NFPA 211: Chimneys, Fireplaces, Vents and solid
fuel burning Appliances.
ANSI/NFPA 70: National Electrical Code
CSA C22.1: Canadian Electrical Code
or CSA C22.10
Only the latest issues of the above codes should be used,
and are available from either:
The National Fire Protection Agency
Batterymarch Park
Qunicy, MA 02269
or
The Canadian Standards Association
178 Rexdale Blvd.
Rexdale, Ontario M9W 1R3
CAUTION
ENVIRONMENTAL HAZARD
Failure to follow this caution may result in
environmental pollution.
Remove and recycle all components or materials (i.e.
oil, electrical and electronic components, insulation,
etc.) before unit final disposal.
2.0 INSTALLATION
2.1 GENERAL
WARNING
Do not enclose the vent pipe in a ceiling or combustible
structure.
This sealed combustion system, must be installed in strict
accordance with this manual. A 3" (7.62 cm) diameter
outdoor combustion air pipe must be connected directly
to the oil burner and the coaxial vent terminal to ensure
the proper functioning to the unit.
Only Beckett AFII and NX burners, as well as Riello BF type
burners may be used with this sealed combustion system
(VTK / KLAVT).
A Sealed Combustion System is by definition a leak-free
system. DO NOT PERFORATE THE VENT OR OUTDOOR
COMBUSTION AIR PIPE! Use the test port in the breech
plate supplied with this kit to take smoke and CO
2
readings.

4
Refer to Table 2 for the minimum and maximum dimensions
of the vent pipe.
2.2 POSITIONING
WARNING
Poisonous carbon monoxide gas hazard.
Even though the flexible venting is insulated, it must not
be run through an unheated space.
To do so can cause residual condensation inside the
stainless steel liner. This may eventually perforate the
liner and allow vent gasses to enter the dwelling,
potentially resulting in death, personal injury and/or,
property damage.
Important : The minimum clearance of the vent pipe in
relation to combustible material is specified in Table 1
below. This clearance must be maintained all along the pipe.
Table 1 : Minimum clearance around a vent system
PORTION OF VENT CANADA AND
UNITED STATES
Vent pipe, up to vent terminal* 3" (7,62 cm)
Vent terminal Zero
* Do not enclose venting.
WARNING
Do not enclose the vent pipe in a ceiling or combustible
structure.
Table 2 : Maximum and minimum vent pipe length
MODEL VENT PIPE
INSIDE. DIA.
MAX.
LENGTH
VENT PIPE
MIN.
LENGTH
VENT PIPE
VTK-53A & VTK1 7,62
cm (3") 6,10 m (20') ,91 m (3')
VTK-64A & VTK2 10,16 cm (4") 6,10 m (20') ,91 m (3')
VTK-65A, VTK3
& KLAVT0201DET 12,70 cm (5") 6,10 m (20') ,91 m (3')
VTK-54A, VTK098
& KLAVT0101DET 10,16 cm (4") 6,10 m (20') ,91 m (3')
The interior portion of the vent terminal must be installed in
an area where the temperature of the ambient and return air
is higher than 60°F (15°C). In addition, the furnace should
be located as closely as possible to the vent terminal, so
that the ducts are as short and direct as possible.
2.2.1 Installation considerations
The vent may be installed through a wall with a minimum
thickness of 2" (5,08 cm) and a maximum thickness of 15"
(38,10 cm). Select a location for the vent terminal in
accordance with all local and national codes. The following
requirements shall be considered to be minimum
requirements that can be overridden by stricter local and
national codes.
Figure 1 : Minimum clearance
CAUTION
Ensure that the area around the side wall venter is
always free of snow, ice and debris, since these will
hamper the proper functioning of the furnace.
The vent shall not terminate:
a. Directly above a paved sidewalk or paved driveway that
is located between two buildings, and that serves both
buildings;
b. Less than 7' (2.13 m) above any paved driveway;
c. Within 6' (1.82 m) (in Canada) of a window or door, or
mechanical air supply inlet to any building;*
d. Within 6' (1.82 m) (in Canada) from the soffit of the roof
of the structure;*
e. Above a gas meter/regulator assembly within 3' (0.91
m) of a vertical centreline of the regulator;
f. Within 6' (1.82 m) of any gas service regulator vent
outlet, or within 3' (0.91 m) of an oil tank vent, or an oil
fill inlet;
g. Within less than 1' (0.30 m) above ground level;
Note : The vent must be located at least 1' higher than the
highest anticipated accumulation of snow.
h. Within 6' (1.82 m) of any other combustion air inlet;
Note : It is possible that, when the system in not in
operation, combustion products may reach the interior of the
building.
i. Within 6' (1.82 m) of a property line;
j. Underneath a veranda, porch or deck;
k. So that the flue gasses are directed at combustible
material or any openings of surrounding buildings that
are within 6' (1.82 m);

5
l. Less than 3' (0.91 m) from an inside corner of an "L"-
shaped structure;
m. So that the bottom of the vent termination opening is
less than 1' (0.30 m) above any surface that may
support ice, snow, or debris;
n. So that the flue gasses are directed toward brickwork,
siding or other construction, in such a manner that they
will be damaged from heat or condensation from flue
gasses.
CAUTION
Most codes have a notwithstanding clause which states that
products of combustion shall not enter the dwelling under
any circumstances, even if all other code requirements as to
construction and location have been complied with. The
installer is ultimately responsible to do whatever is
necessary to ensure that flue gasses do not enter the
dwelling.
* For installations in the U.S.A. refer to Section 6.7.3.4 of
the NFPA 31.
Figure 2 : Components identification
2.3 INSTALLATION OF THE COMPONENTS
Refer to Figure 2 for additional details on components
identification.
2.3.1 Installing the terminal in the wall
1. Open up a 6" (15,24 cm) hole for the VTK-53A / VTK1,
VTK-54A / VTK098 / KLAVT0101DET and VTK-64A /
VTK2 terminals and a 6¼” (15,88 cm) hole for the VTK-
65A / VTK3 / KLAVT0201DET terminal in the wall in
accordance with the location considerations outlined in
the previous section (2.2);
2. Fasten the wall plate to the inside-wall using 4 field-
supplied fasteners, appropriate for the wall material.
Note that the pressure control bracket (item G) must be
removed to access the top right wall plate screw hole
(item E). Install the wall plate so that the top of the hole
in the wall plate is positioned 1/8" (3.2 mm) higher than
the top of the 6" (15,24 cm) hole in the wall, see Figure
3. This will ensure the proper slope of the terminal for
the proper evacuation from the inside to the outside;
3. Remove the 3 screws (item C) holding the end cone
(item A) in place and remove the cone;
4. Remove the 4 screws (item C) holding the stabiliser
shroud (item B) in place and remove the stabiliser
shroud;
5. Insert the main body of the terminal through the wall
plate so that the end of the terminal extends about 2"
(5.08 cm) past the outside wall, see Figure 3;

6
Figure 3 : Installation of the terminal in the wall
6. Install the stabiliser shroud (item B), as shown in Figure
4 and replace the 4 mounting screws;
7. On concrete and block wall installations in particular, if it
appears that the flange on the back of the stabiliser
shroud is not large enough to cover the irregularities in
the hole, a field fabricated wall plate can be constructed
out of 304, 316, or 316L stainless steel;
Figure 4 : Installation of the stabiliser shroud
8. Silicone seal the circumference of the joint where the
stabiliser shroud connects to the main body of the
terminal, see Figure 4;
9. Apply caulking to the back plate of the stabiliser shroud
and push the terminal firmly back against the wall,
making sure the pressure switch (item G) is located
at the top, in a horizontal position as shown in
Figure 5;
10. Tighten the clamp on the wall plate (item E) to secure
the terminal in place;
11. While pushing down gently on the top of the stabiliser
shroud, install the 3-2" (5,08 cm) stainless steel screws
provided with the kit (item D) to secure the back of the
shroud to the wall. Do not over tighten the screws or it
will distort the stabiliser shroud. The screws will not be
necessary on a concrete or block wall as the mortar can
provide positive positioning;
12. Apply more caulking all around the seam where the
stabiliser shroud meets the wall to ensure an airtight
seal as shown in Figure 6;
Figure 5 : Pressure switch location
13. Reinstall the end cone (item A) and replace the three
mounting screws;
Figure 6 : Caulking around the stabiliser shroud
14. Support the vent and intake air piping so that a 1/4" to
1/2" (6 to 12 mm) slope from the inside out results in
proper drainage of the vent, see Figure 3.
2.3.2 Insulated flexible venting
WARNING
Cuts and abrasion hazard.
Always wear protective gloves and eye protection when
handling the vent material.
The process of cutting and fitting the flexible venting
material exposes the installer to sharp edges that could
cause severe cuts to the skin.
The flexible venting material (item I) comes in 3 lengths: 10’
(3,05 m), 15' (4,58 m) or 20' (6,10 m). The vent construction
is coaxial and comprises a 3” (7.62 cm), 4” (10,16 cm), or 5”
(12,70 cm) stainless steel corrugated flexible inner tube,
CAULKING
PRESSURE SWITCH
DNS-1094 Rev D
CAULKING
DNS-1311 Rev B

7
surrounded by insulation and covered with an outer tube of
4” (10,16 cm), 5” (12,70 cm), or 6” (15,24 cm) flexible
corrugated aluminium sleeve to protect the insulation.
Splicing vent lengths together is prohibited.
Minimum/maximum continuous vent lengths permitted for
installation are 3' (0,91 m) minimum and 20' (6,10 m)
maximum respectively.
2.3.3 Connection to the furnace breech
1. Determine the length of the flexible vent (item I) and cut
it as required;
2. Install the flexible vent in its ultimate position;
3. Proceed with the installation of the transition (item H) on
the flexible vent (item I). Apply some high-temperature
sealant (item M) on the threads of the transition piece to
ensure air tightness then screw the transition piece right
up to the end of the vent as shown in Figure 7. Make
sure that the seam on the corrugated stainless steel
flexible vent (item I) is well aligned with the seam of the
transition (item H), otherwise you will not be able to
screw it properly (see Figure 8). The corrugated
aluminium jacket fits inside of the transition outside ring
(item H);
WARNING
Make sure that the flexible vent (item I) is well secured
by the threads of the transition (item H) by pulling it. If
you can remove the transition (item H) without
unscrewing it, your installation will not be air tight.
Then, you must replace the defective part.
Figure 7 : Installation of the transition / terminal coupling
4. Apply a high temperature silicone bead (item M) around
the outside ring of the breech plate. Install the
transition (item H) piece on the furnace breech plate;
5. The installation of the transition must be such that the
port for pressure measurements is at the top and
accessible once the installation is completed. Do not
install the transition with the test port pointing
downward. For details, see Figure 9;
6. Complete the assembly by using 3 #8 x 1/2" self-drilling
screws (item J) as shown in Figure 9. The seal is
permanent and should never need to be disconnected
as the breech plate can be removed by unscrewing the
nuts;
7. Apply sealant (item M) to cover completely the self-
drilling screw heads (item J);
Figure 8 : Seams alignment
8. In order not to damage the sealant, only the breech
plate on the furnace should be removed if and as
required.
Figure 9 : Connection to the breech plate
2.3.4 Connection to the vent terminal
1. Install the terminal coupling (item K) on the flexible vent
(item I). Apply some high-temperature sealant (item M)
on the threads of the terminal coupling to ensure air
tightness then screw the transition piece right up to the
end of the vent as shown in Figure 7. Make sure that
the seam on the corrugated stainless steel flexible vent
(item I) is well aligned with the seam of the terminal
coupling (item K), otherwise you will not be able to
screw it properly (see Figure 8). The corrugated
aluminium jacket fits inside of the terminal coupling
outside ring (item K);
WARNING
Make sure that the flexible vent (item I) is well secured
by the threads of the transition (item H) by pulling it. If
you can remove the transition (item H) without
unscrewing it, your installation will not be air tight.
Then, you must replace the defective part.
DNS-1312 Rev A
SEAM OF THE TRANSITION / TERMINAL COUPLING
SEAM OF THE FLEXIBLE VENT
DNS-1342 Rev B

8
2. Apply a high temperature silicone bead (item M) around
the outside of the terminal coupling (item K). Install the
assembly consisting of the flexible vent (item I) and the
terminal coupling (item K) on the vent terminal (item F).
For details, see Figure 10;
3. Complete the assembly by using 3 #8 x 1/2" self-drilling
screws (item J) as shown in Figure 10;
4. Apply sealant (item M) to cover completely the self-
drilling screw heads (item J);
Figure 10 : Connection to the vent terminal
2.4 CONNECTION OF THE AIR INTAKE PIPE
The vent system requires additional parts, which are not
included with the kit. These additional parts must be
constructed of 3” (7.6 cm) Schedule 40 PVC, PVC-SWV,
SDR-26, SDR-21, Septic Sewer Pipe, or ABS plastic pipe.
Solvent cement suitable for the pipe material selected must
be used. Also, installation procedures, piping and fittings
must conform to the following ANSI /ASTM standards:
PVC ASTM D-1785
SDR26, SDR21 ASTM D-2241
Septic sewer pipe ASTM D-2729
PVC-DWV ASTM D-2665
PVC primer and solvent cement ASTM D-2564
ABS pipe and fittings ASTM D-2235
Procedure for cementing joints ASTM D-2855
CAUTION
The use of ducted outside combustion air is mandatory
for the venting system. This system operates on a
balanced flue principle and will not function properly if
the combustion air piping is not attached and sealed at
all connections between the vent terminal and burner
inlet. Make sure the piping is not obstructed or cut off.
2.4.1 Additional parts required (not included in VTK
kit)
a. 3” (7.6 cm) diameter elbows;
b. 3” (7.6 cm) diameter plastic pipe;
c. 3” (7.6 cm) 90°elbow, female-female (for terminal);
d. 3” (7.6 cm) female to 2" female reducer
(Riello 40-BF burner only);
e. 2" (5,08 cm) 90°elbow, street type, female-male
(Riello 40-BF burner only);
f. 3” (7.6 cm) female-female PVC or ABS coupling (not
sewer pipe) (Beckett AFII burner only);
g. Transition bushings to go from PVC or ABS to ASTM D-
2729 Septic Sewer Pipe (if applicable).
If PVC fittings are mixed with ABS fittings, use solvent
cement that is approved for bonding the two plastics.
2.4.2 Intake pipe length
The vent system has been certified for 37 equivalent meters
(120') of 7.6 cm (3") intake pipe. Count a 90° elbow
as 3.0 equivalent meters (10') and a 45° elbow as 1.5
equivalent meters (5') in the calculation.
For example:
2 lengths of 1.5 m ( 5') = 3.0 equivalent m (10')
1 lengths of 3.0 m (10') = 3.0 equivalent m (10')
3 elbows de 90° = 9.0 equivalent m (30')
2 elbows de 45° = 3.0 equivalent m (10')
1 elbows de 90° = 3.0 equivalent m (10')
1 elbows de 45° = 1.5 equivalent m ( 5')
Total = 22.5 equivalent m (73.8'),
which is acceptable.
2.4.3 Beckett AFII Burner
Remove the air inlet cover by removing the three screws.
Apply silicone sealant to the 3” (7.6 cm) adapter and insert
the end with the sealant in the burner opening. Secure in
place with three self-tapping sheet metal screws.
2.4.4 Beckett NX Burner
Remove the cover from the burner, then remove the air inlet
plate on top of the cover. Apply silicone sealant to the 3”
(7.6 cm) adapter and insert the end with the sealant in the
burner opening. Replace the burner’s cover.
2.4.5 Riello 40-BF burner
Fully insert the female end of the 2" (5,08 cm) 90°street
elbow into the combustion air fitting on top of the burner.
Fasten securely with 3 self-tapping sheet metal screws.
Cement the 2" (5,08 cm) end of the 3” (7.6 cm) female to
the 2" (5,08 cm) female reducer onto the male end of the 2"
(5,08 cm) - 90°elbow. If these parts are not easily obtained,
use a 3” (7.6 cm) - 90°elbow with the male end fitted over
the combustion air fitting. The fitting will have to be silicone
sealed as the fit will not be tight. Fasten securely with 3 self-
tapping sheet metal screws.
2.4.6 Terminal connection
Insert the 3” (7.6 cm) - 90°female-female elbow into the
stainless steel air intake fitting located on the right side of
the vent terminal (viewed from the rear). Fasten securely
with 3 self-tapping sheet metal screws.
DNS-1314 Rev A

9
2.4.7 Intermediate piping
Pipe as required between the terminal and the burner.
Ensure that the 3” (7.6 cm) piping is routed and supported in
accordance with local and national codes. Obey minimum
furnace clearances to combustibles when routing any
sections of 3” (7.6 cm) piping in the vicinity of the furnace.
2.5 INSTALLATION OF THE BVSO JUMPER
On units equipped with a BVSO connector, the jumper
provided and also included in kit #B03396 must be installed.
Refer to the instructions included with the kit and Figure 11
of this manual.
Figure 11 : BVSO jumper
3.0 OPERATION
The system is a sealed combustion system which means
that the furnace is isolated in relation to the interior of the
building. Therefore, the burner is not affected by pressure
fluctuations, making it ideal in buildings of air tight
construction.
A sealed combustion system can only be installed on
approved furnaces. Refer to the nameplate on the furnace
and Table 3 of this manual.
3.1 COMBUSTION GAS TEMPERATURE
VERIFICATION
After adjustments are made, based on the installation
instructions contained in the oil furnace manual, it is
recommended that a combustion gas temperature check be
made at the exit of the direct vent system. The reading
should be 93°C (200°F). In case it is impossible to obtain
this temperature after 5 minutes of operation, it is
recommended to relocate the furnace in order to shorten the
length of the vent pipe.
After the modification, let the system cool down for about 30
minutes and recheck by taking another reading, again after
a minimum of 5 minutes of operation. The temperature must
be at least 93°C (200°F).
3.2 BURNER POST PURGE DELAY ADJUSTMENT
The post purge delay on the oil-fired burners is factory set to
zero second. This delay is applicable for all installations with
chimney venting. For heating units installed with side wall
venting, the post purge delay must be set to 15 seconds
when installed with a Beckett burner. Post purge delay is not
necessary with a Riello Burner. Refer to the burner control
instruction manual and marking for proper adjustment of the
post purge delay.
4.0 MAINTENANCE
CAUTION
Before doing any servicing, be sure to shut off the fuel
supply and electrical power to the furnace. The 115 volt
circuit is dangerous and can potentially electrocute.
Refer to the installation manual for servicing the furnace.
Maintaining a sealed combustion system is the same as
maintaining a chimney with the following particularity:
Note: To perform maintenance service, remove the breech
plate by removing the brass nuts (see Figure 9). The
transition
(item H)
must not be removed from the flexible
vent pipe assemblies.
DNS-1165 Rev A

10
Table 3 : Approved furnaces for used with VTK / IFV
Burner Vent Terminal
Beckett Riello Terminal Insulated Flex Vent
AMP098 NX-56LQ R40-BF3 VTK-54A IFV-410A / IFV-415A / IFV-420A
AMP112 NX-56LQ R40-BF5 VTK-54A IFV-410A / IFV-415A / IFV-420A
AMP154 NX-50LC R40-BF5 VTK-65A IFV-510A / IFV-515A / IFV-520A
AMT098 NX-56LQ R40-BF3 VTK-54A IFV-410A / IFV-415A / IFV-420A
AMT112 NX-56LQ R40-BF5 VTK-54A IFV-410A / IFV-415A / IFV-420A
AMT154 NX-50LC R40-BF5 VTK-65A IFV-510A / IFV-515A / IFV-520A
HMT (Dettson) R40-BF5 VTK-65A IFV-510A / IFV-515A / IFV-520A
HMT (ICP) R40-BF5 VTK3 IFV508 / IFV520
NOLF105 (Dettson) AFII-85 R40-BF3 VTK-53A IFV-310A / IFV-315A / IFV-320A
NOLF105 (ICP) AFII-85 R40-BF3 VTK1 IFV315 / IFV323
NOUF105 (Dettson) AFII-85 R40-BF3 VTK-53A IFV-310A / IFV-315A / IFV-320A
NOUF105 (ICP) AFII-85 R40-BF3 VTK1 IFV315 / IFV323
OBLAAB036098AABE NX-56LQ R40-BF3 KLAVT0101DET KLAFV0101DET / KLAFV0201DET
OBLAAB048112AABF NX-56LQ R40-BF5 KLAVT0101DET KLAFV0101DET / KLAFV0201DET
OBLAAB060154AABG NX-50LC R40-BF5 KLAVT0201DET KLAFV0301DET / KLAFV0401DET
OBMAAB036098AABE NX-56LQ R40-BF3 KLAVT0101DET KLAFV0101DET / KLAFV0201DET
OBMAAB042112AABF NX-56LQ R40-BF5 KLAVT0101DET KLAFV0101DET / KLAFV0201DET
OBMAAB060154AABG NX-50LC R40-BF5 KLAVT0201DET KLAFV0301DET / KLAFV0401DET
OCF105 AFII-85 R40-BF3 VTK1 IFV315 / IFV323
ODH53F AFII-85 R40-BF3 VTK-53A IFV-310A / IFV-315A / IFV-320A
OHB53F AFII-85 R40-BF3 VTK-53A IFV-310A / IFV-315A / IFV-320A
OHB64F AFII-150 R40-BF5 VTK-64A IFV-410A / IFV-415A / IFV-420A
OLB53F AFII-85 R40-BF3 VTK-53A IFV-310A / IFV-315A / IFV-320A
OLB53R AFII-85 R40-BF3 VTK-53A IFV-310A / IFV-315A / IFV-320A
OLB64R AFII-150 R40-BF5 VTK-64A IFV-410A / IFV-415A / IFV-420A
OLF105 AFII-85 R40-BF3 VTK1 IFV315 / IFV323
OLR098 / OLV098 NX-56LQ R40-BF3 VTK098 IFV09810 / IFV09820
OLR105 AFII-85 R40-BF3 VTK1 IFV315 / IFV323
OLR112 / OLV112 NX-56LQ R40-BF5 VTK098 IFV09810 / IFV09820
OLR154 / OLV154 NX-50LC R40-BF5 VTK3 IFV508 / IFV520
OLR160 AFII-150 R40-BF5 VTK2 IFV415 / IFV423
OMF098 / OMV098 NX-56LQ R40-BF3 VTK098 IFV09810 / IFV09820
OMF112 / OMV112 NX-56LQ R40-BF5 VTK098 IFV09810 / IFV09820
OMF154 / OMV154 NX-50LC R40-BF5 VTK3 IFV508 / IFV520
OUF105 AFII-85 R40-BF3 VTK1 IFV315 / IFV323
OUF160 AFII-150 R40-BF5 VTK2 IFV415 / IFV423
OVLAAB036098AABF NX-56LQ R40-BF3 KLAVT0101DET KLAFV0101DET / KLAFV0201DET
OVLAAB048112AABG NX-56LQ R40-BF5 KLAVT0101DET KLAFV0101DET / KLAFV0201DET
OVLAAB060154AABG NX-50LC R40-BF5 KLAVT0201DET KLAFV0301DET / KLAFV0401DET
OVMAAB036098AABF NX-56LQ R40-BF3 KLAVT0101DET KLAFV0101DET / KLAFV0201DET
OVMAAB042112AABF NX-56LQ R40-BF5 KLAVT0101DET KLAFV0101DET / KLAFV0201DET
OVMAAB060154AABG NX-50LC R40-BF5 KLAVT0201DET KLAFV0301DET / KLAFV0401DET
SCH-105 AFII-85 R40-BF3 VTK-53A IFV-310A / IFV-315A / IFV-320A
SCH-160 AFII-150 R40-BF5 VTK-64A IFV-410A / IFV-415A / IFV-420A
SCL-105 AFII-85 R40-BF3 VTK-53A IFV-310A / IFV-315A / IFV-320A
SCL-160 AFII-150 R40-BF5 VTK-64A IFV-410A / IFV-415A / IFV-420A
TMP-105 AFII-85 R40-BF3 VTK-53A IFV-310A / IFV-315A / IFV-320A

11
Figure 12 : Dimensions
Figure 13 : Wiring Diagram

12
Figure 14 : Parts List
Table 4 : Parts List
1
2
3
4
5
6 7
8 9
10 1011 6
12
13
VTK-53A
VTK1
VTK-54A
VTK098
KLAVT0101DET
VTK-64A
VTK2
VTK-65A
VTK3
KLAVT0201DET
1 End Cone 4DETECK1 4DETECK1 4DETECK1 4DETECK1
2 Stabiliser Shroud 4DETTEK1 4DETTEK2 4DETTEK2 4DETTEK3
3 Screw Philips 8-32 x 1/2" SS N / D N / D N / D N / D
4 Screw Philips #10 x 2" SS N / D N / D N / D N / D
5 Interior Mounting Plate N / D N / D N / D N / D
6 Vent Terminal B03906-01 B03906-02 B03906-02 B03906-03
7 Pressure Gauge R99F033 R99F032 R99F032 R99F034
8 Connector with Port B03907-01 B03907-02 B03907-03 B03907-04
9A Insulated Flex Vent 10' long IFV-310A IFV-410A IFV-410A IFV-510A
9A Insulated Flex Vent 15' long IFV-315A IFV-415A IFV-415A IFV-515A
9A Insulated Flex Vent 20' long IFV-320A IFV-420A IFV-420A IFV-520A
10 Teks Screw #8 x 1/2" SS F03G009 F03G009 F03G009 F03G009
11 Connector without Port B03908-01 B03908-02 B03908-02 B03908-03
12 BVSO Jumper B03337 B03337 B03337 B03337
13 Hi Temp Silicone F10G005 F10G005 F10G005 F10G005
ITEM DESCRIPTION
Part No
This manual suits for next models
9
Table of contents
Other Dettson Fan manuals
Popular Fan manuals by other brands

Salda
Salda AMBERAIR Installation, operation and maintenance manual
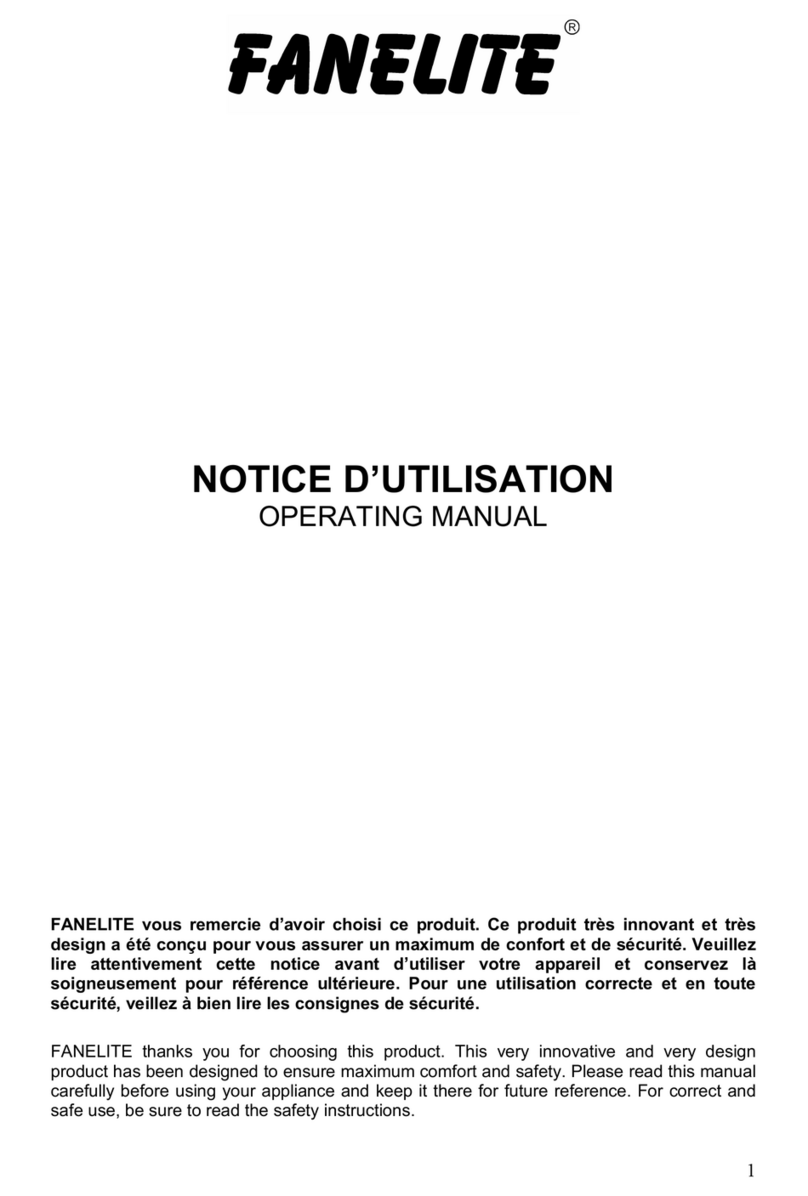
Fanelite
Fanelite PRICKLY 38YFT-7057M operating manual

Mitsubishi
Mitsubishi VL-100EU5-E installation manual
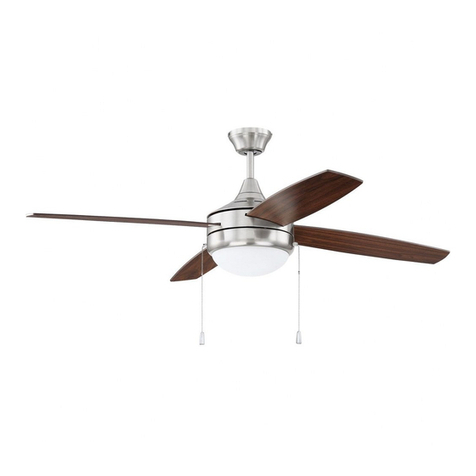
Craftmade
Craftmade PHA52 4 Series installation guide

Kendal Lighting
Kendal Lighting AC-19856 installation instructions
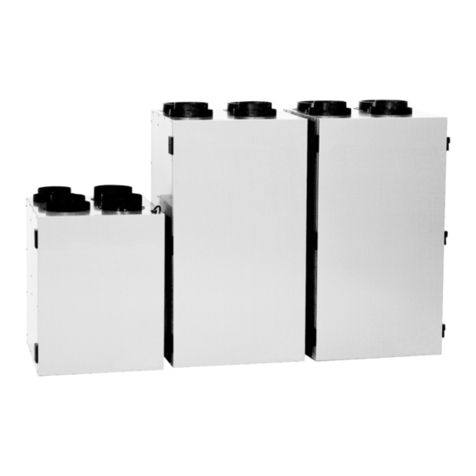
Venmar
Venmar 1.3 HE installation manual
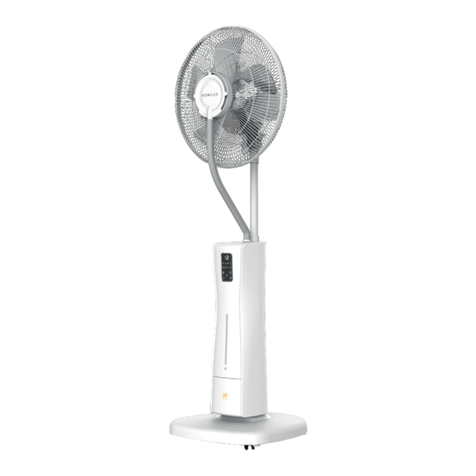
Newlux
Newlux WindPure Mist W500 Smart manual

Ruck Ventilatoren
Ruck Ventilatoren IsoBox RX S Series Assembly instruction
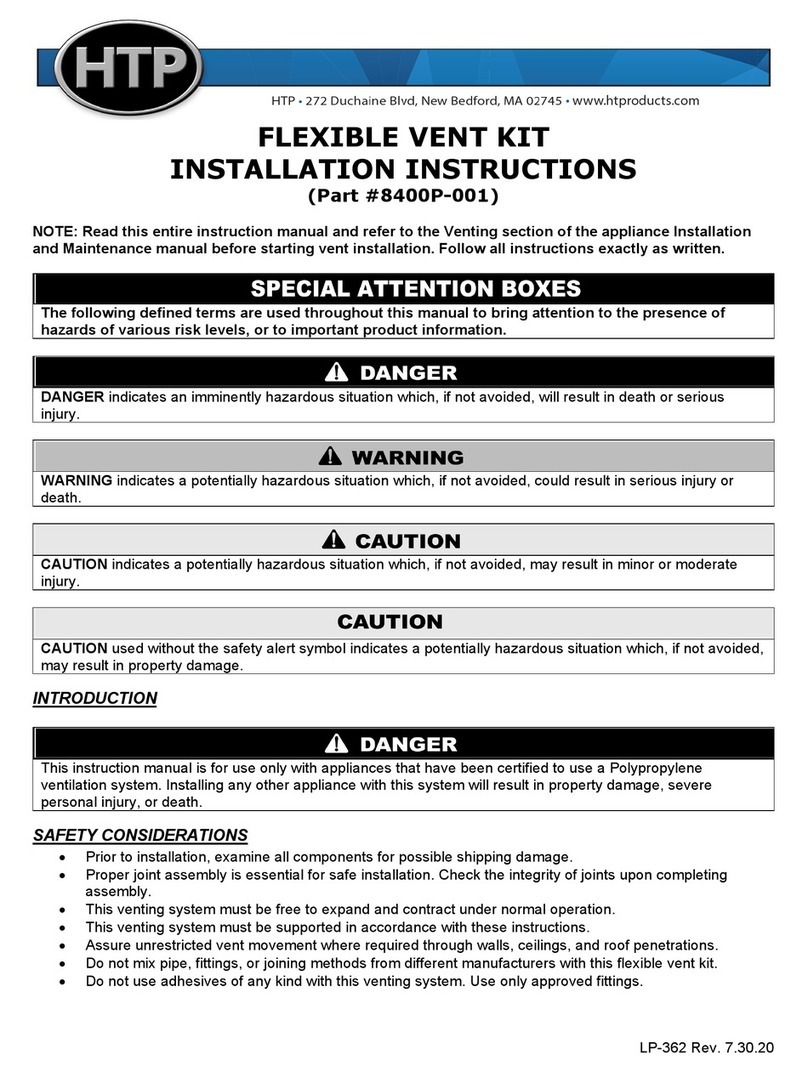
HTP
HTP 8400P-001 installation instructions
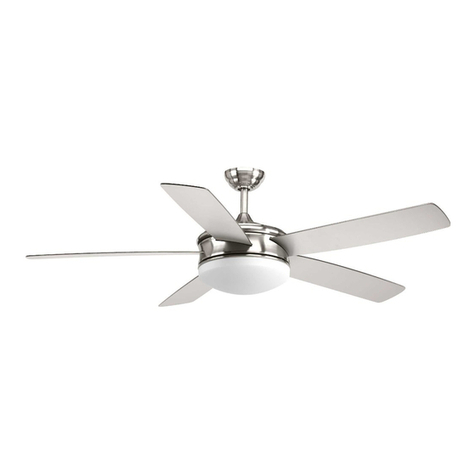
Progress Lighting
Progress Lighting AirPro P2548 installation manual

Vornado
Vornado 293HD owner's guide

Greenwood
Greenwood CMEV-3 installation instructions