Dive Gear Express DGX Gears D6 User manual

DGX Gears D6
Second Stage Service Manual

Copyright © 2022 Dive Gear Express
All Rights Reserved.
Revision 2 Published 09/23/2022
Revision Date Changes
102/19/2021 Initial publication
1a 03/25/2022 Replaced photo for Fig. 28
2 09/23/2022 Minor technical edits for clarity; replaced Fig. 3, removed
Figs. 4 and 5 and renumbered subsequent Figs.; replaced
Figs. 24, 25, and 26

1. Overview
(1) The availability of subassemblies and components, repair parts, specialized tools, and maintenance
manuals does not imply qualification to assemble and/or service scuba equipment. Improper service
of dive equipment can lead to severe injury or death. Dive Gear Express recommends that non-qualified
individuals seek professional training/mentoring before attempting repairs or servicing on any diving
equipment.
Failure to follow the procedures outlined herein may result in serious injury or
death!
(2) In the following pages will be found the disassembly, assembly, tuning and troubleshooting steps
for these components. Photos are used throughout to illustrate the procedures.
Please pay special attention to all Caution Notes!
(3) Whenever an item of extra importance needs to be observed, a “Caution Note:” will appear, followed
by the required information. See below.
Caution Note: This must be read and followed!
(4) Included in this manual is a list of recommended/required tools for each disassembly, assembly,
and testing section. They are identified in each section where they are used.
(5) A schematic diagram is located at the rear of this manual. The diagram contains the detailed parts
lists. The diagram also includes the torque specifications for parts where required.
(6) A general troubleshooting guide with space for notes is also included for those using a printed
version. Those who prefer an electronic version should keep detailed notes in an accessible location
for their own observations and service tips, as well as a record of service.
(7) Throughout the text, parts are referenced using the item number on the schematic to facilitate
locating each individual component.
(8) Parts should not be taken out of their packaging until the actual assembly stage is reached, and the
user is ready to lubricate, where necessary, and install them.
(9) Ensure the service area is free of any environmental factors that may cause problems during the
servicing of your regulators. The area must be clean and organized. The use of nitrile gloves is highly
recommended for final rinsing and assembly. This will minimize the risk of skin oils contaminating the
internal components of the regulator.
(10) Ensure that all required servicing/testing air supplies are available and at the proper test pressures
if not using a regulated supply from a single source. “Modified Grade E” air as typically delivered at a
dive shop fill station is preferred.
Caution Note: Only use air from a breathing air source! Do not use a hardware
store shop compressor.

Cleaning and Rinsing - General Considerations
(11) Cleaning and rinsing of the components should be done using clean, fresh water.
(12) Only use degreasers that leave no organic residue (e.g., Extreme Simple Green, Blue Gold Cleaner,
or any clear liquid dish soap that does not contain scents or dyes).
(13) To remove corrosion, use a 50/50 vinegar/water solution and nylon brushes. Areas of heavy
corrosion not removed with vinegar can be addressed with mild phosphoric acid solutions available
from scuba supply houses.
(14) Allow parts to air dry without the use of loop-weave cloths that may leave fibers.
(15) Once all service procedures have been completed and bench testing done, in-water testing in a
confined environment such as a swimming pool is recommended to confirm proper function before
taking the regulator on an actual dive.

Cleaning of Regulator Parts
(16) Cleaning of parts that are going to be reused is one of the most critical steps in servicing the
regulator. As was stated earlier, use the proper solutions for the job at hand. Removal of hydrocarbons
and debris should be accomplished before attempting removal of corrosion. Areas of corrosion are
often also coated with old lubricant or oily contaminants. Before attempting to remove corrosion, use
warm detergent and a soft brush to remove oils and debris. Then use an acidic solution to remove
corrosion. Once corrosion has been removed, inspect parts and repeat detergent washing as needed.
Wearing nitrile gloves throughout the process reduces the risk of contaminating the parts with skin oils.
(17) First, prepare a warm solution of detergent from the list above. Immerse both plastic and metal
parts and agitate thoroughly. Protect critical delicate parts (such as the Orifice) by washing them
separately or isolating them in a small plastic container with holes. Wash the diaphragm separately,
using your fingertips to remove debris. Use a soft nylon brush and/or soft rags soaked in detergent to
scrub away visible debris and contaminants. Corrosion will likely not be removed during this step. Rinse
repeatedly in clean water.
(18) Now address visible corrosion by submerging metal parts only in a 1:1 dilution of white vinegar
and hot water. Do not immerse plastic parts in an acid bath - it will degrade the plastic and make it
more susceptible to cracking. Agitate the parts occasionally and allow parts to stand in the acidic
solution for ten minutes. Wearing gloves, remove and inspect parts, and reimmerse them for an
additional ten minutes if visible corrosion is still noted. Removal of corrosion will leave bare brass
behind, which will not affect regulator function, but will necessitate more frequent future inspection
and service. After the acid bath, rinse all metal parts thoroughly.
(19) Best practice is to neutralize any possible residual acid remaining in crevices and threads, by
immersing all acid-treated parts in a neutralizing solution of warm water and sodium bicarbonate
(baking soda) in a ratio of 1 tablespoon per gallon of water. After a brief neutralizing soak, again rinse
all parts thoroughly. In areas with high mineral content in the water, a final rinse with distilled water
should be considered. A plastic colander is excellent for drainage after rinsing. For very small parts, a
mesh strainer for sink drains works well. Often sold as a set, they are inexpensive and can be used for
many types of regulator components. Again, protect delicate parts from contact with hard metal
surfaces. Retained final rinse water should be allowed to stand and examined for a surface sheen
indicative of residual hydrocarbon residue. If noted, return to step (17) above.
(20) After washing and rinsing the regulator parts, allow them to air dry. Using a drying rack will facilitate
this. Do not lay the parts on a paper towel or loop-weave cloth towel. Doing so runs the risk of having
fibers stick to them that will cause issues with sealing. If a cloth is used as an aid to drying, make sure
to use a tight, flat weave lint-free cloth that has previously been well washed to remove fabric sizing.

Inspection After Cleaning
(21) Before assembling the regulator, it is necessary to inspect all the cleaned components. Using a
magnifying glass or inexpensive USB microscope, ensure all parts are clean and contaminant-free, and
check the components for damage that may have been hidden by corrosion or lubricant. Look for
scratches that may affect the sealing surfaces of the regulator.
(22) Lay all parts out on a padded work surface following the schematic. A rubber or silicone mat of
suitable size that is clean and free of contaminants works well for this.
(23) Now that all parts have been cleaned and checked, the assembly can begin. Remove the new parts
from the service kit bag and lay them out following the schematic, matching them to the old parts for
size. Then make sure all old parts that are to be replaced have been discarded or segregated.
Caution Note: Removing parts from their packaging, before they are to be used,
runs the risk of mixing them up. Some O-rings are very close in size but are not
interchangeable! Keep the parts in their packaging until you are ready to
exchange them for their used equivalent.
(24) As with the parts that have been cleaned, it is a good idea to inspect the new parts as well. Inspect
the LP Seat to ensure it is free of any defects. Check all the O-rings and inspect them as you use them
for nicks or imperfections. Inspect the washers to ensure they are free of burrs or other defects that
could affect their function. It is critical to use the parts list on the schematic to ensure that all new parts
are present and accounted for in their required quantities.
(25) Lubrication can be overdone.Doing so runs the risk of trapping excess dirt or debris on the parts.
One way of reducing the risk of overdoing it is to use the lube-in-a-bag method - Fig. 1
Fig. 1

This involves using a small clean plastic bag containing a small amount of lubricant. The O-ring is
inserted into the bag, worked around to evenly coat with lube while squeezing off excess, then taken
out of the bag and used in its location - Fig. 2.
Fig. 2.
(26) Another way is to apply a small amount of lubricant to the gloved index finger and massage the O-
ring between the thumb and index finger.
(27) Under most circumstances, a lubricant should be used very sparingly or not at all. In nearly all
scuba applications, if you can see the lubricant, too much has been applied. Before using any lubricant,
any existing lubrication should be removed before new is applied. In dynamic applications, it is used to
reduce excessive wear. Static O-rings do not generally require the use of lubricant.
(28) Do not unnecessarily lubricate parts. Certain parts are specifically noted to be installed without
lubrication. It also helps to keep those parts clean and free of debris that will cling to the lubricant. Not
lubricating unnecessarily helps to keep those parts clean and free of debris that might otherwise cling
to the lubricant.

2. Tool List - Fig. 3
1. Magnehelic or Other Cracking Effort Gauge
2. Side-Cutting Snips
3. Thin Adjustable or Open End Hose and 11/16” Wrenches
4. 3/16” Hex Key
5. Thin Brass Pick
6. Blunt Brass Pick and Blunt Brass Spade
7. Thin Wooden Dowels
8. Second Stage In-Line Adjusting Tool (Hex Adjusting Tip)
Fig. 3
(1) The In-Line Adjusting Tool with IP Gauge and Brass O-Ring Pick Set can be found at Dive Gear
Express using the link below.
https://www.divegearexpress.com/tools/scuba-tools
(2) Tools may also be purchased from Scuba Tools at the link below.
www.scubatools.com
(3) Additional useful items are a magnifying glass or inexpensive USB microscope, nitrile gloves and,
to aid in rinsing, a plastic colander and small mesh strainers for smaller parts.

3. Preliminary Testing
(1) Preliminary testing of the regulator is necessary to identify any problems with the first and second
stages and verify overall regulator function. This testing will include:
1. Visual inspection of the regulator
2. Inspection of the hoses
3. Cracking effort and negative pressure test
Visual inspection is done to identify issues that could affect servicing and to ensure that pressurizing
the system will not compromise the safety of the service technician.
Check all connections to make sure they are secure.
Check that on the first stage, there are no extruded O-rings, and hoses are tight.
Detailed inspection of hoses is done to ensure it is safe to pressurize the regulator set. Look for
evidence that might lead to hose failure. Check all hose connection crimps. Defects must be taken care
of before pressurizing the system! Replacement of any suspect hoses is recommended.
Caution Note: Defects in hoses require replacement before pressurizing the
regulator! Failure to do so may result in serious injury!
(2) The Intermediate Pressure (IP) of the first stage should be confirmed before testing the second
stage.
(3) The standard operating range for the system is with an IP of 135 psi.

4. Second Stage Evaluation
(1) The negative pressure test verifies the seals of the Diaphragm and Exhaust Valve, confirms proper
O-ring seal and verifies housing integrity. With the supply pressure off, and attached to a first stage on
a cylinder, attempt a normal breath from the second stage. You should be unable to draw any air. If
flow is obtained, remove the second stage from the hose and try to draw air while sealing the hose inlet
with your finger. If a flow is still present, the Diaphragm and Exhaust Valve need to be checked for
damage. Salt accumulation, sand, and defects in the housing or O-rings may also allow airflow when
the air inlet is covered. Carefully check all of these.
(2) Cracking effort testing is most accurately done with the use of a magnehelic gauge. A container of
water can be used by measuring the depth to which a stage can be submerged face-down parallel to
the water. This gives an indication at which level of effort the second stage will open. The normal range
for the adjustable second stage is 1.0 to 2.2 inches of water. Less pressure may be desired by the diver,
but the initial factory setting of 1.1 should be used. This permits a break-in period for the LP seat. It is
normal to see this initial setting drop as the LP seat takes a set.
(3) The housing should be inspected for signs of damage. Scratches, gouges, missing parts, damaged
exhaust ports, or a loose faceplate that will not tighten may be an indication of a damaged housing.
(4) After the negative pressure test, test the purge button, and look for defects. Check the lever and
breathing effort knob. Do they move freely and with no indication of stiffness? Do they feel like there is
sand or grit in them?
(5) A problem with housing integrity should be dealt with before starting the rebuild. A defective housing
will compromise final testing and pose a safety hazard to the user.
Caution Note: A damaged Main Housing, Top Cover, or Diaphragm cannot be
repaired. They must be replaced.
(6) Having completed the initial evaluation and determined that service is necessary, the rebuild of the
regulator can take place.

5. Second Stage Disassembly
(1) Additional tips for performing disassembly of the D6 Second Stage can be found in our video at:
https://www.youtube.com/watch?v=W12VDuCKOCE
(2) Ensure the system is depressurized. The use of small, clean containers to hold parts is
recommended.
(3) In the following steps, the part numbers from the schematic will be used with their description. The
numbers on the photos also correspond with the parts list on the schematic. Items in the service kits
are identified in the same way. Have both in front of you while following the instructions. Be sure to
keep all old parts organized and separate from new ones in the service kit. The old washers and O-rings
marked with an asterisk (*) will be replaced with new ones from the service kit and the remaining parts
will be cleaned and reused. Take care with O-ring (04*) and O-ring (20*) as they are very close in size.
1. Remove the Second Stage from the hose. The Main Housing cover consists of the Purge Button
Retainer (08), Purge Button (09) and Top Cover (10). Unscrew the cover from the Main Housing (01) -
Fig. 4. Remove the Diaphragm Washer (07) and the Diaphragm (06). This reveals the Adjust Tube
assembly in the Housing - Fig. 5.
Fig. 4Fig. 5

2. Remove the Heat Sink Nut (05) - Fig. 6. Holding the Lever (18) down, slide/pull the Adjust Tube
assembly out of the Main Housing as one unit - Fig. 7. Inspect the Exhaust Valve (11*) by using a pick
or dowel and gently press all around the edge to check that it is pliable and not stuck or torn. – Fig. 8.
Fig. 6Fig. 7Fig. 8
3. Slide the Deflector Knob (16) off the assembly while holding down the Lever - Fig. 9. After sliding the
Deflector Knob off, carefully allow the Lever to come up slowly. Remove the O-ring (15*) from the
Deflector Knob and O-ring (04*) from the inlet side of the Main Housing - Fig. 10.
Fig. 9Fig. 10

4. Turn the Adjust Knob (27) slightly with the assembly over a flat surface, allowing the Pin (19) to drop
out - Fig. 11. This will allow the Adjust Knob to be removed. Remove the O-ring (20*) from the Adjust
Tube (17) - Fig. 12.
Fig. 11 Fig. 12
5. Remove the Knob Adjust Core (29) from the Adjust Knob with a pick. Insert the pick and pop the core
out - Fig - 13. Remove the O-ring (26*) from the Adjust Knob. Remove O-rings (28* and 30*) from the
Knob Adjust Core - Fig. 14.
Fig. 13 Fig. 14

6. Holding the Lever upright, use a thin wooden dowel to push the assembly consisting of the LP Seat
(21*), Piston (22), O-rings (23*), Main Spring (24), and Balance Cylinder (25) out of the Adjust Tube. You
may hear a slight click as you do this when the LP Seat end passes the Lever. Remove the Lever from
the Adjust Tube - Fig. 15. An alternative method is to carefully remove the Lever by lifting one leg out
of the hole and rotating the Adjust Tube to allow the other side to come out - Fig 16. DO NOT BEND
THE LEGS OF THE LEVER TO DO THIS.
Fig. 15 Fig. 16
7. Remove the LP Seat from the Piston. Pull the Piston and Main Spring out of the Balance Cylinder and
remove the O-rings (23*) from the Piston - Fig. 17.
Fig. 17

8. Use the hex end of the In-Line Adjusting Tool or 3/16” hex wrench to loosen the Orifice (13) in the
Adjust Tube. Push the Orifice out with a thin wooden dowel from the threaded end. Do not use a metal
tool. Remove the O-ring (14*) from the Orifice - Fig. 18.
Fig. 18
9. The disassembled Adjust Tube assembly with the Heat Sink Nut is shown below. Note that the O-
ring (04*) from under the Heat Sink Nut is similarly sized, but thicker than the O-ring (20*) from the
Adjust Tube - Fig. 19.
Fig. 19

10. With side-cutting snips, carefully cut the Tie Wrap (02*) holding the Mouthpiece (03) - Fig. 20.
Remove the Mouthpiece and check that the Main Housing (01), Exhaust Cover (12) and Exhaust Valve
(11*) are undamaged and free of debris. The Exhaust Cover is not usually removed during service.
The cover is fitted in such a way at the factory that removing it is likely to damage the Cover. Removal
may also damage the flange that holds it in place - Fig. 21.
Fig. 20 Fig. 21
If removal (to replace the Exhaust Valve) is necessary, soak the Main Housing and Exhaust Cover
together in hot tap water for three minutes to soften the Cover. Then peel the wings from each side of
the Main Housing flange and slide the Exhaust Cover down and off.
This completes the disassembly of the D6 Second Stage.

(4) The photographs below show the disassembled second stage - Fig. 22 and the Service Parts Kit -
Fig. 23. All the parts not in the service kit need to be washed, rinsed and dried, as discussed previously.
O-rings and washers that will be replaced with new from the service kit should be discarded.
Fig. 22
Fig. 23

6. Second Stage Assembly
(1) Additional tips for performing reassembly of the D6 Second Stage can be found in our video at:
https://www.youtube.com/watch?v=alL4njr5kxI
(2) Before starting the assembly of the second stage, complete a thorough inspection of all parts to be
reused. Refer to the Overview Inspection section for details. At this time, open the service kit and lay
out the parts. Use the schematic to identify each part.
Caution Note: Only use enough lubricant to lightly coat the O-rings and ensure no
debris is trapped on them.
1. Install the LP Seat (21*) into the end of the Piston (22). Note the orientation of the Step, which will
be discussed in steps 6., 7. and 8. below - Fig. 24. Lubricate and install the O-rings (23*) on the Piston
- Fig. 25.
Fig. 24 Fig. 25

2. Assemble the Balance Cylinder (25), Main Spring (24) and Piston as shown in Fig. 26.
Fig. 26
3. Place the O-ring (14*) on the Orifice (13) - Fig. 27. Insert the Orifice into the Adjust Tube (17) using
the 3/16” hex - Fig. 28.
Fig. 27 Fig. 28

4. Turn the Orifice clockwise into the Adjust Tube 4-5 turns until the threads have engaged - Fig. 29.
Fig. 29
5. Lubricate the O-ring (20*) and place it in the groove on the Adjust Tube (17) - Fig. 30.
Fig. 30
Other manuals for DGX Gears D6
2
Table of contents
Other Dive Gear Express Controllers manuals
Popular Controllers manuals by other brands
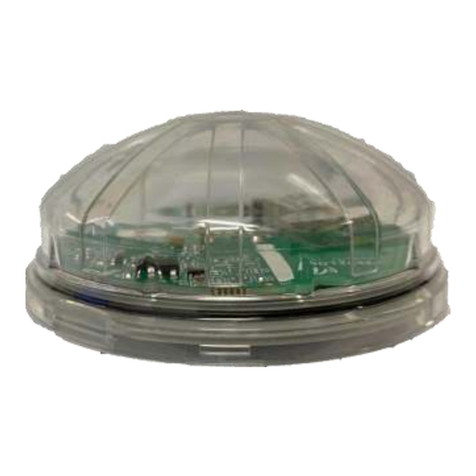
Luminext
Luminext Zhaga Wirepas OLC400 Installation instruction
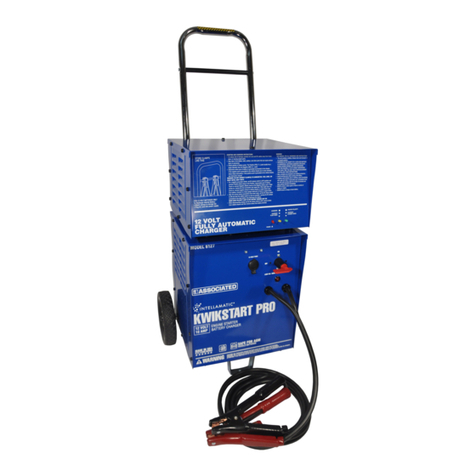
Associated Equipment
Associated Equipment KwikStart Pro Series Operator's manual
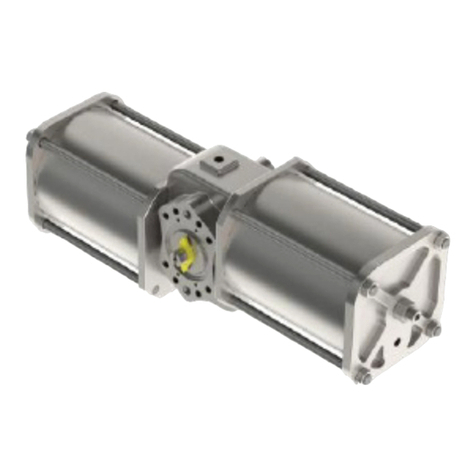
Emerson
Emerson Bettis RGS Q Series Installation, operation and maintenance manual
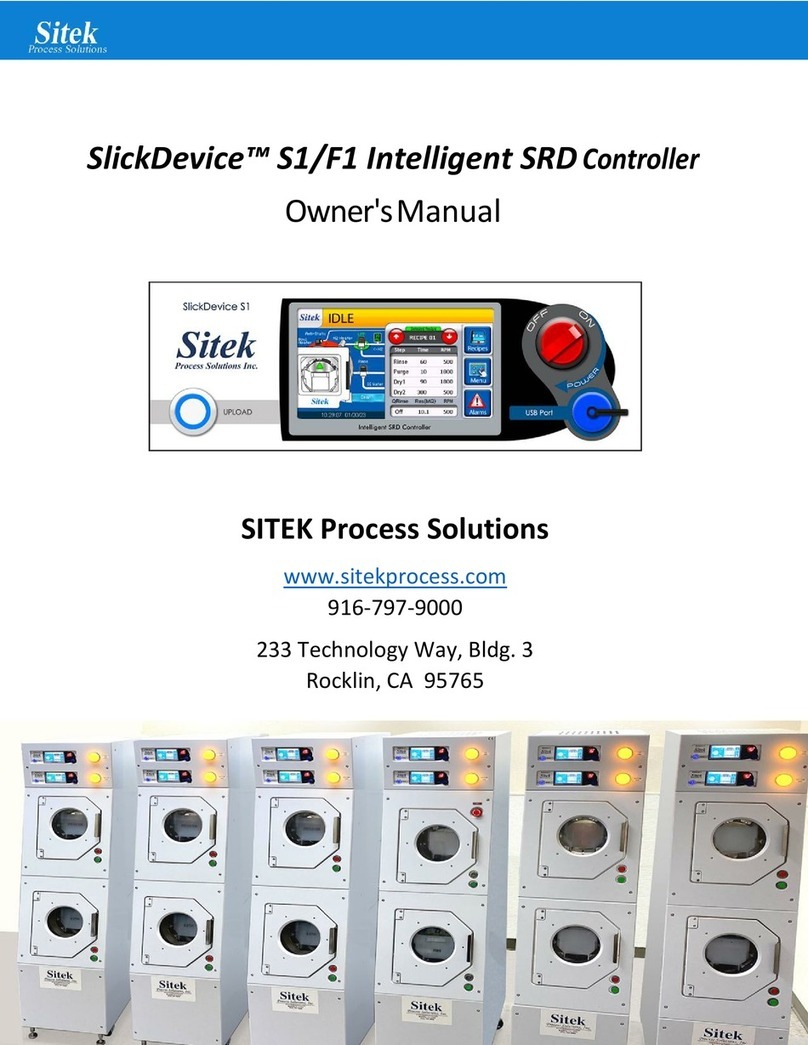
SITEK
SITEK SlickDevice S1 owner's manual

SIIG
SIIG UltraATA 133 PCI Quick installation guide

attocube
attocube ANC300 user manual