DMM DYN2 Series User manual

DYN2 Series
AC Servo Drive
Type - A General-Purpose Pulse/Analog
Specication Manual
MM
DDynamic Motor Motion
Technology Corporation
Manual Code
Revision
Assem_obcover_FP01001
WEIGHT:
A3
SHEET 1 OF 1
SCALE:1:2
DWG NO.
TITLE:
REVISION
DO NOT SCALE DRAWING
MATERIAL:
DATE
SIGNATURE
NAME
DEBUR AND
BREAK SHARP
EDGES
FINISH:
UNLESS OTHERWISE SPECIFIED:
DIMENSIONS ARE IN MILLIMETERS
SURFACE FINISH:
TOLERANCES:
LINEAR:
ANGULAR:
Q.A
MFG
APPV'D
CHK'D
DRAWN
Hardware Version
Firmware Version
: AH10
: AH10
: DYN2MS-01E-0814A1
: A1
Copyright © 2014 DMM Technology Corp.
Published In Canada
This manual must be kept available for the user

2
DYN2MS-01E-0814A1
■ Safety Notice ■
The user or operator should read through this manual completely before installation, testing, operation, or
inspection of the equipment. The DYN2 series AC Servo Drive should be operated under correct circum-
stances and conditions. Bodily harm or damage to equipment and system may result if specications
outlined in this document are not followed. Take extra precaution when the warning convention is used.
■ Notations Used ■
All specication and units of measurement used in the manual are in METRIC:
Mass: Kilogram [kg]
Length: Millimeter [mm]
Time: Seconds [s]
Temperature: Celsius [C]
!
WARNING

3
DYN2MS-01E-0814A1
Product Manual Preface
The user or operator should read through this manual completely before installation, testing, operation,
or inspection of the equipment. The DYN2 series AC Servo Drive should be operated under correct
circumstances and conditions. Bodily harm or damage to equipment and system may result if spec-
ications outlined in this document are not followed. Take extra caution at details when the warning
convention is used.
This manual is available on the DMM Technology Corp. website. A physical copy or reference to the
on-line availability must be kept convenient to the servo drive user or operator for references.
Contact DMM Technology Corp. if the user or operator has any questions or concerns regarding use.
The DYN2 AC Servo Drive is not designed or certied to implement safety into a system and should
not be used in applications where the servo drive maintains safety to personnel or machine.
To reect improvements, additions, revisions, changes or corrections made to the product or manual,
this document is updated accordingly and divided into revisions to reect each version.

4
DYN2MS-01E-0814A1
Manual Contents
Safety Notice 2
Notations Used 2
Product Manual Preface 3
Manual Contents 4
A.1 Introduction 5
A.2 Name Plate 5
A.3 Servo Drive Model Number 5
1 GENERAL SPECIFICATION 6
1.1 Drive Overall Specication 6
1.2 Control Block Diagram 7
1.3 Encoder Specication 7
2 CONNECTIONS AND WIRING 8
2.1 DYN2 Servo Drive Body Layout 8
2.2 Connector and Signal Specication 9
2.3 JP3 Main I/O Details 11
2.4 JP3 I/O Connection Circuit 15
2.5 Main Power Supply Requirements 19
3 START UP 20
3.1 Mounting and Installation 20
3.2 Timing Chart 21
3.3 DMMDRV Software Communication 23
4 OPERATION 24
4.1 Position Servo Mode 24
4.2 Speed Servo Mode 27
4.3 Torque Servo Mode 29
4.4 RS232 Command Input Mode 30
4.5 Absolute Zero Position Index Output (ZRI) 30
5 PARAMETERS AND TUNING 31
5.1 Parameters Outline 31
5.2 Servo Drive Gain Tuning 33
6 MAINTENANCE 35
6.1 Alarm Specications 35
6.2 Drive Maintenance 36
APPENDIX A - SERVO DRIVE DIMENSIONS 37
APPENDIX B - RS232 Protocol Denition 38
APPENDIX C - Operation Examples 39
Warranty and Liability 40
Product and Manual Disclaimer 41

5
DYN2MS-01E-0814A1
A.1 Introduction
This manual documents all features and specications for the DYN2 series AC Servo Drive Type A -
General Purpose Pulse/Analog. The servo drive features standard pulse train and analog command input
modes compatible with universal motion controllers, PLC’s or CNC controllers. Control modes include po-
sition, speed or torque servo mode with standard signal connections and interfacing for seamless integra-
tion into any system. A high resolution 16-bit (65,536pulse/rev) encoder combined with outstanding 10ms
instantaneous position response optimizes performance in high-demand applications.
Gain adjustment is simplied with 3 parameter tuning for fast and easy adjustments while maintaining crit-
ical application and response exibility. All testing and tuning is done through a RS232 or USB interface
with a host PC running DMMDRV GUI software for fast and easy set up. Drive status is internally moni-
tored by 22 parameters for consistent and reliable performance.
Standard servo motor and encoder/motor power cable pair options available. Measuring only 32mm [W] x
85mm [H] x 75mm [D], the DYN2 AC Servo drive can power up to 0.75kW (7.1Nm) capacity. The perfect
servo drive for any small to medium capacity application.
A.2 Name Plate
A.3 Servo Drive Model Number
Model Number
Input / Output Specications
Protection
Country of Origin
Lot / Serial Number
Hardware / Software Version
Note the name plate is region specic and may vary between each region model.
DYN2 - T L A 6 S - 00
DMM Servo Drive Series
DYN2 AC Servo Drive
Low Voltage DC Input
Voltage Class
T60V
H48V
S24V
Motor Capacity
150W - 200W
L400W - 750W
Command Type
APulse / Analog
Encoder
4 14bit [16,384ppr]
6 16bit [65,536ppr]
Model Type
SStandard
** Custom

6
DYN2MS-01E-0814A1
1.1 Drive Overall Specication
1 GENERAL SPECIFICATION
Data Specication
Input
Rated Voltage 60VDC ± 10%
Permissible Input Voltage 24VDC ~ 75VDC
Rated Current 16A
Output
Rated Voltage Peak. +75VAC
Between any two motor phase
Rated Current [L] Capacity Model: Peak. 20A
[1] Capacity Model: Peak 10A
From any single motor phase
Motor Capacity 50W ~ 750W
Drive Interface Power
Supply (JP2 Pin. 12)
Voltage 5VDC +/-%5
Max. Current Draw 50mA
Control Method SVPWM
Dynamic Brake Integrated
Encoder Feedback 14/16-bit Single-Turn Absolute
Protection Functions Current, Voltage, Temperature, Over Power, Posi-
tion Lost Follow
Position Servo
Command Reference Pulse*1 Pulse+Sign, A/B Phase Quadrature 90° Phase
Differential, CW+CCW
Max. Input Frequency 500kHz
Input Voltage 5VDC ± %5 (Higher voltage available as option)
Over drive photocoupler diode
Positioning Feedback Z Index Pulse*2
Speed Servo
Speed Control Range 0:5000
Input Reference Voltage -10VDC ~ +10VDC ± %5
3,000rpm at ± 5VDC
Max Input Voltage ± 12VDC
Torque Servo Input Reference Voltage -10VDC ~ +10VDC ± %5
Max Input Voltage ± 12VDC
Environment
Protection IP10
Operation Temperature 0~55°C
Storage Temperature -20 ~ 65°C
Max. Operation Humidity 95RH% (no dew)
Max. Storage Humidity 95RH% (no dew)
Mass 0.2kg
1. CW+CCW command format available as option.
2. See section 4.5 for Z index pulse details

7
DYN2MS-01E-0814A1
1.2 Control Block Diagram
1.3 Encoder Specication
Main Power
Input
RS232
Serial Port
JP2
+
-
Switching
Power Supply
+5VDC
+15VDC
Main Control
Inverter Circuit
Isolated Gate Control
CPU
Current
Sensor
Current
Sensor
A
B
C
LED S1
Isolated I/O Interface
JP4
JP3
Encoder
Feedback
A/D Analog Input
Voltage Protection
DYN2 AC Servo Drive
■ Model
Model Number Type Resolution Data Type Interface Type Measurement Voltage Status
ABS-14-00 Absolute 14bit [16,384ppr] 4-Wire Serial Differential Driver/
Receiver Magnetic +5VDC A
ABS-16-00 Absolute 16bit [65,536ppr] 4-Wire Serial Differential Driver/
Receiver Magnetic +5VDC A

8
DYN2MS-01E-0814A1
2 CONNECTIONS AND WIRING
2.1 DYN2 Servo Drive Body Layout
Assem_obcover_FP01001
WEIGHT:
A3
SHEET 1 OF 1
SCALE:1:2
DWG NO.
TITLE:
REVISION
DO NOT SCALE DRAWING
MATERIAL:
DATE
SIGNATURE
NAME
DEBUR AND
BREAK SHARP
EDGES
FINISH:
UNLESS OTHERWISE SPECIFIED:
DIMENSIONS ARE IN MILLIMETERS
SURFACE FINISH:
TOLERANCES:
LINEAR:
ANGULAR:
Q.A
MFG
APPV'D
CHK'D
DRAWN
■ JP1
Power Supply Input
■ JP5
Servo Motor Power
■ JP3
I/O Port
■ JP2
RS232 Port to PC
■ S1 Drive Status LED
[ Green LED ]
■ JP4
Encoder Feedback Port
(1) Drive Body Grounding Terminal
[ M3 x 5mm Max. ]
*Located on left side of body
(1)
■ Pin Layout
JP1
+
-
JP2
Gnd
NC
NC
JP3
12
11
10
9
8
7
6
5
4
3
2
1
JP4
Gnd
S-
S+
+5V
JP5
C
B
A
NC
RxD
TxD
+5V
DO NOT reverse JP1 DC
input polarity!
Top side of servo drive
Bottom side of servo drive

9
DYN2MS-01E-0814A1
2.2 Connector and Signal Specication
▐ JP1 - Power Supply Input
Connector Type: 5.00mm Pitch Terminal Block
Drive Header: Phoenix MSTBA 2,5/ 2-G
Plug Connector: Phoenix MSTB 2,5/ 2-ST
Recommended Wire Gauge: 0.8mm2 (AWG18)
▐ JP2 RS232 Port to PC
Connector Type: 2.54mm Pitch Rectangular
Drive Header: Molex 70553-0041
Plug Connector: Molex 50-57-9407
Recommended Wire Gauge: 0.3mm2 (AWG22)
Signal Layout:
Pin 1: GND
Pin 2~4: NC
Pin 5: RS232 signal input, RxD, TTL/CMOS level.
Pin 6: RS232 signal output, TxD, TTL/CMOS level.
Pin 7: +5(V) output, <10(mA), generated in board.
In order to connect JP2 with PC’s RS232 port, an intermediate cable with level shift buffer is necessary.
Intermediate cable shipped with drive tuning cable [Model No. CA-MRS232-6].
▐ JP3 I/O Port - Position Command Input
Connector Type: 3.5mm Pitch Terminal Block
Drive Header: Phoenix MC 1,5/12-G-3,5
Plug Connector: Phoenix MC 1,5/12-ST-3,5
Recommended Wire Gauge: 0.6mm2 (20AWG)
Signal Layout:
Pin 1: GND (Bottom side of drive)
Pin 2: Analog Command Reference ±10VDC
Pin 3: DIR-, B-, CCW- Pulse Reference
Pin 4: DIR+, B+, CCW+ Pulse Reference
Pin 5: STEP-, A-, CW- Pulse Reference
Pin 6: STEP+, A+, CW+ Pulse Reference
Pin 7: Signal Common for Pin. 8, 9, 10, 11.
Pin 8: Alarm Output
Pin 9: OnPosition Output
Pin 10: Absolute Zero Position Index Output
Pin 11: Drive Disable Input
Pin 12: Drive Internal +5VDC Supply (Top side of drive nearest to JP5)

10
DYN2MS-01E-0814A1
▐ JP4 Encoder Feedback Port
Connector Type: 2.54mm Pitch Rectangular
Drive Header: Molex 70553-0038
Plug Connector: Molex 50-57-9404
Recommended Wire Gauge: 0.3mm2 (AWG22)
Signal Layout:
Pin 1: +5VDC Supply
Pin 2: S+
Pin 3: S-
Pin 4: Gnd
▐ JP5 Servo Motor Power
Connector Type: 5.00mm Pitch Terminal Block
Drive Header: Phoenix MSTBA 2,5/ 3-G
Plug Connector: Phoenix MSTB 2,5/ 3-ST
Recommended Wire Gauge: 0.8mm2 (AWG18)
Signal Layout:
Pin 1: A Phase
Pin 2: B Phase
Pin 3: C Phase
Motor frame should be grounded through Drive Body Grounding Terminal [ M3 ] located on heat sink side.
Crimp an M3 terminal lug onto the servo motor frame wire (Yellow/Green) and attach the lug to the drive
body grounding terminal. Do not use a screw longer than 5mm.
2.2 Connector and Signal Specication

11
DYN2MS-01E-0814A1
2.3 JP3 Main I/O Details
■ Terminal Layout
12
11
10
9
8
7
6
5
4
3
2
1
+5VDC
ENA
ZRI
ONPOS
ALM
COM
PUL+, A+, CW+
PUL-, A-, CW-
DIR+, B+, CCW+
DIR-, B-, CCW-
AGIN
GND
Drive internal +5VDC
270Ω
270Ω
270Ω
DYN2 Servo Drive
( Host Controller )
A/D
WARNING
!
● Note the directionality of the JP3 connector and pins before making connections. Pin1
is located nearest to the bottom of the servo drive. Pin12 is located nearest terminal JP5
(Servo Motor Power).

12
DYN2MS-01E-0814A1
2.3 JP3 Main I/O Details
■ JP3 Signal Specication
Pin No. Signal Symbol Type
12 Drive Internal +5VDC Supply +5VDC Output
Description Connection Circuit
- Drive internal +5VDC output
- Max Current Draw: 50mA
- Relative ground side with JP3 Pin.1
N/A
Pin No. Signal Symbol Type
11 Drive Disable Input ENA Input
Description Connection Circuit
- Apply +5VDC between Pin.7 Common to Disable servo drive
- Motor coasts when disabled (shaft free)
- Disable clears all pulse/analog commands
- Disable clears all position error
- Max. Voltage: +5VDC±%10
- Max. Current: 20mA
[ A ]
*See section 2.4
Refer to Section 2.4 JP3 I/O Connection Circuit for example connection diagram. Standard I/O
levels are +5VDC±%10. Contact DMM if the controller uses 12~24VDC level I/O.
Pin No. Signal Symbol Type
10 Absolute Zero Position Index Output ZRI Output
Description Connection Circuit
- Transistor ON (Signal LOW) if servo on Zero Position.
- Triggered at signal falling edge
- Zero Position output xed to one mechanical motor shaft position per revolu-
tion. Accuracy maintained by absolute encoder.
- Used for precision zeroing, or indexing applications.
- Max. Voltage: 30V
- Max. Current: 30mA
[ B ]
*See section 2.4

13
DYN2MS-01E-0814A1
2.3 JP3 Main I/O Details
Refer to Section 2.4 JP3 I/O Connection Circuit for example connection diagram.
Pin No. Signal Symbol Type
9OnPosition Output ONPOS Output
Description Connection Circuit
- Transistor ON (Signal LOW) if servo Off Position.
- Transistor OFF (Signal HIGH) if servo On Position.
- Servo On Position if motor position error within value set by OnPosRange
parameter.
- Max. Voltage: 30V
- Max. Current: 30mA
[ B ]
*See section 2.4
Pin No. Signal Symbol Type
8Servo Alarm ALM Output
Description Connection Circuit
- Transistor ON (Signal LOW) if servo drive alarmed or faulted
- Servo drive triggers protective alarm relative to Current, Voltage, Tempera-
ture, Over Power, Position Lost Follow
- Max. Voltage: 30V
- Max. Current: 30mA
[ B ]
*See section 2.4
Pin No. Signal Symbol Type
7Common COM Output
Description Connection Circuit
- JP3 I/O Pin. 8, 9, 10, 11 Control Signal Common. [ A ] [ B ]
*See section 2.4

14
DYN2MS-01E-0814A1
2.3 JP3 Main I/O Details
Refer to Section 2.4 JP3 I/O Connection Circuit for example connection diagram.
Pin No. Signal Symbol Type
6
5
4
3
STEP+, A+, CW+ Pulse Reference
STEP-, A-. CW- Pulse Reference
DIR+, B+. CCW+ Pulse Reference
DIR-, B-. CCW- Pulse Reference
STEP+
STEP-
DIR+
DIR-
Input
Description Connection Circuit
- Position command reference pulse input
- Compatible pulse form include:
♦ Pulse + Direction
♦ A/B phase quadrature with 90° phase differential
♦ CW + CCW
- Max. input pulse frequency: 500kHz
- Max. Voltage: +5VDC±%10
- Max. Current: 20mA
- Line Drive / Open Collector circuit on Controller Side
- Input pulse electronically scalable with GEAR_NUM parameter
[ C ]
*See section 2.4
Pin No. Signal Symbol Type
2
1
Analog Command Reference
Ground AGIN
GND
Input
N/A
Description Connection Circuit
- Analog command reference for Speed/Torque servo mode
- Voltage reference ±10VDC
- ±12VDC max input voltage
- Max current: 0.6mA
[ D ]
*See section 2.4

15
DYN2MS-01E-0814A1
2.4 JP3 I/O Connection Circuit
■ Type [ A ] Connection Circuit - General Input Circuit
Applicable Signals:
Pin No. Signal Symbol Type
11 Drive Disable Input ENA Input
Open Collector Notes:
- Sink circuit shown.
Source circuit can also
be used.
Relay/Switch Notes:
ENA 270Ω
11
COM 7
+5VDC
ENA 270Ω
11
COM 7
+5VDC

16
DYN2MS-01E-0814A1
2.4 JP3 I/O Connection Circuit
■ Type [ B ] Connection Circuit - General Output Circuit
Applicable Signals:
Pin No. Signal Symbol Type
10
9
8
7
Absolute Zero Position Index Output
OnPosition Output
Servo Alarm
Common
ZRI
ONPOS
ALM
COM
Output
Output
Output
N/A
Collector Output Notes:
Photo Coupler Notes:
Relay Notes:
10, 9, 8
COM 7
1kΩ
+5VDC
10, 9, 8
COM 7
+5VDC
1kΩ
10, 9, 8
COM 7
5~24VDC

17
DYN2MS-01E-0814A1
2.4 JP3 I/O Connection Circuit
■ Type [ C ] Connection Circuit - Position Reference Pulse Input
Applicable Signals:
Pin No. Signal Symbol Type
6
5
4
3
STEP+, A+, CW+ Pulse Reference
STEP-, A-. CW- Pulse Reference
DIR+, B+. CCW+ Pulse Reference
DIR-, B-. CCW- Pulse Reference
STEP+
STEP-
DIR+
DIR-
Input
Line Driver Notes:
- Twisted pair cable with
shield grounded on
receiver side.
Open Collector
(DYN2 Internal Power Supply) Notes:
- Twisted pair cable with
shield grounded on
receiver side.
Open Collector
(External Power Supply) Notes:
- Power supply provid-
ed by host controller or
external source.
- Twisted pair cable with
shield grounded on
receiver side.
270Ω
6, 4
5, 3
+5VDC
270Ω
6, 4
5, 3
12+5VDC
1GND
270Ω
6, 4
5, 3

18
DYN2MS-01E-0814A1
2.4 JP3 I/O Connection Circuit
■ Type [ D ] Connection Circuit - Analog Command Reference Input
Applicable Signals:
Pin No. Signal Symbol Type
2
1
Analog Command Reference
Ground AGIN
GND
Input
N/A
Notes:
- Twisted pair cable with
shield grounded on
receiver side.
2
1
AGIN
GND
D/A Converter
Op-amp
Potentiometer
etc.

19
DYN2MS-01E-0814A1
2.5 Main Power Supply Requirements
The DYN2 servo drive has a minimum operation input of +24VDC and max input of +75VDC. The servo
drive’s internal over-voltage alarm is triggered at +80VDC input and will shut down at this level. Consider
the voltage/speed gradient of the servo motor when selecting power supplies.
A smoothing (reservoir) capacitor is recommended after the DC power supply. The recommended capacity
is 100V 1,000uF. Connect a fuse before the servo drive according to the circuit size.
AC-DC Power Supply
110~240VAC Supply
R S T
-
WARNING
!
● DO NOT reverse the polarity of the DC input power. Reversing the polarity will perma-
nently damage the servo drive and may cause electric shock. Ensure polarity is correct
before powering ON the servo drive.
+
JP1
+
-
1000uF
100V
1000uF
100V
Servo Drive Model Max. Motor Capacity Recommended Fuse
DYN2-T1A6S-00 200W 20A
DYN2-TLA6S-00 750W 20A
Fuse
DYN2 Servo Drive

20
DYN2MS-01E-0814A1
3 START UP
3.1 Mounting and Installation
The DYN2 servo drive can be mounted vertically or horizontally (vehicle mount). The servo drives should
be mounted by its rear chassis to an electrically conductive metal panel or plate. When mounting multiple
servo drives, at least 1mm clearance should be left between each unit. The small size of the DYN2 servo
drive is compatible with modular mounting. It can be placed adjacent to other devices with 1mm clear-
ance. Also consider the size of the connectors and cables in front of the servo drive when mounting.
The control cabinet internal temperature should not exceed 40°C. If using a fan to cool the servo drives,
the air ow should parallel the direction of the heat sink n. The servo drive internally do not have a cool-
ing fan.
Assem_obcover_FP01001
WEIGHT:
A3
SHEET 1 OF 1
SCALE:1:2
DWG NO.
TITLE:
REVISION
DO NOT SCALE DRAWING
MATERIAL:
DATE
SIGNATURE
NAME
DEBUR AND
BREAK SHARP
EDGES
FINISH:
UNLESS OTHERWISE SPECIFIED:
DIMENSIONS ARE IN MILLIMETERS
SURFACE FINISH:
TOLERANCES:
LINEAR:
ANGULAR:
Q.A
MFG
APPV'D
CHK'D
DRAWN
Assem_obcover_FP01001
WEIGHT:
A3
SHEET 1 OF 1
SCALE:1:2
DWG NO.
TITLE:
REVISION
DO NOT SCALE DRAWING
MATERIAL:
DATE
SIGNATURE
NAME
DEBUR AND
BREAK SHARP
EDGES
FINISH:
UNLESS OTHERWISE SPECIFIED:
DIMENSIONS ARE IN MILLIMETERS
SURFACE FINISH:
TOLERANCES:
LINEAR:
ANGULAR:
Q.A
MFG
APPV'D
CHK'D
DRAWN
Assem_obcover_FP01001
WEIGHT:
A3
SHEET 1 OF 1
SCALE:1:2
DWG NO.
TITLE:
REVISION
DO NOT SCALE DRAWING
MATERIAL:
DATE
SIGNATURE
NAME
DEBUR AND
BREAK SHARP
EDGES
FINISH:
UNLESS OTHERWISE SPECIFIED:
DIMENSIONS ARE IN MILLIMETERS
SURFACE FINISH:
TOLERANCES:
LINEAR:
ANGULAR:
Q.A
MFG
APPV'D
CHK'D
DRAWN
>1mm >1mm
Airow
Direction
(Other Devices)
(Other Devices)
>1mm>1mm
This manual suits for next models
2
Table of contents
Popular DC Drive manuals by other brands
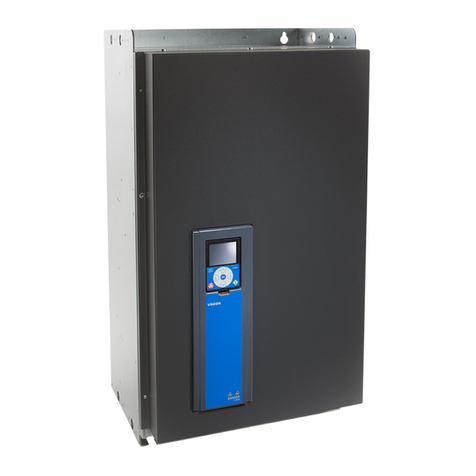
Vacon
Vacon 100 INDUSTRIAL Applications manual

SEW-Eurodrive
SEW-Eurodrive Movidrive MDX61B operating instructions
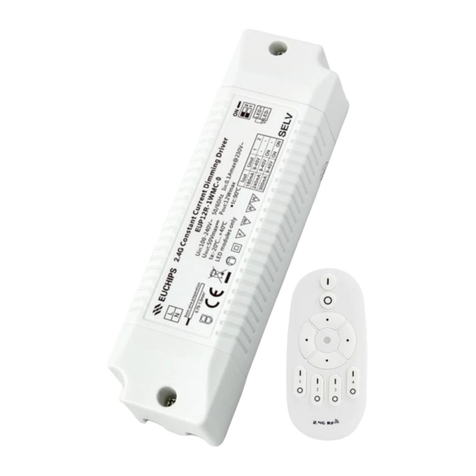
EUCHIPS
EUCHIPS EUP12R-1WMC-0 quick start guide
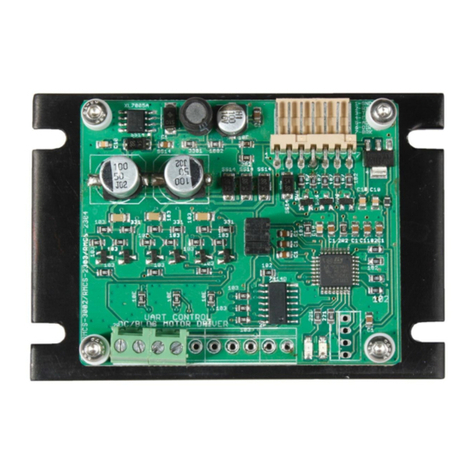
RHINO MOTION CONTROLS
RHINO MOTION CONTROLS RMCS-2304 operating manual
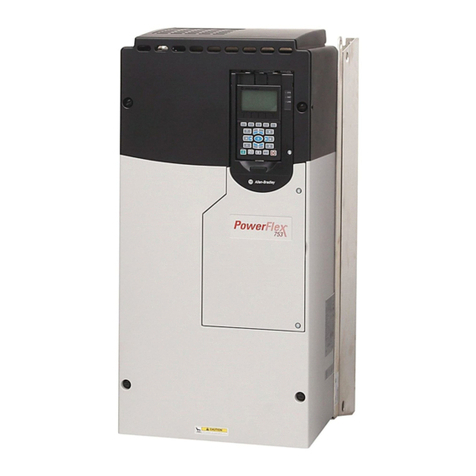
Rockwell Automation
Rockwell Automation Allen-Bradley PowerFlex 753 manual
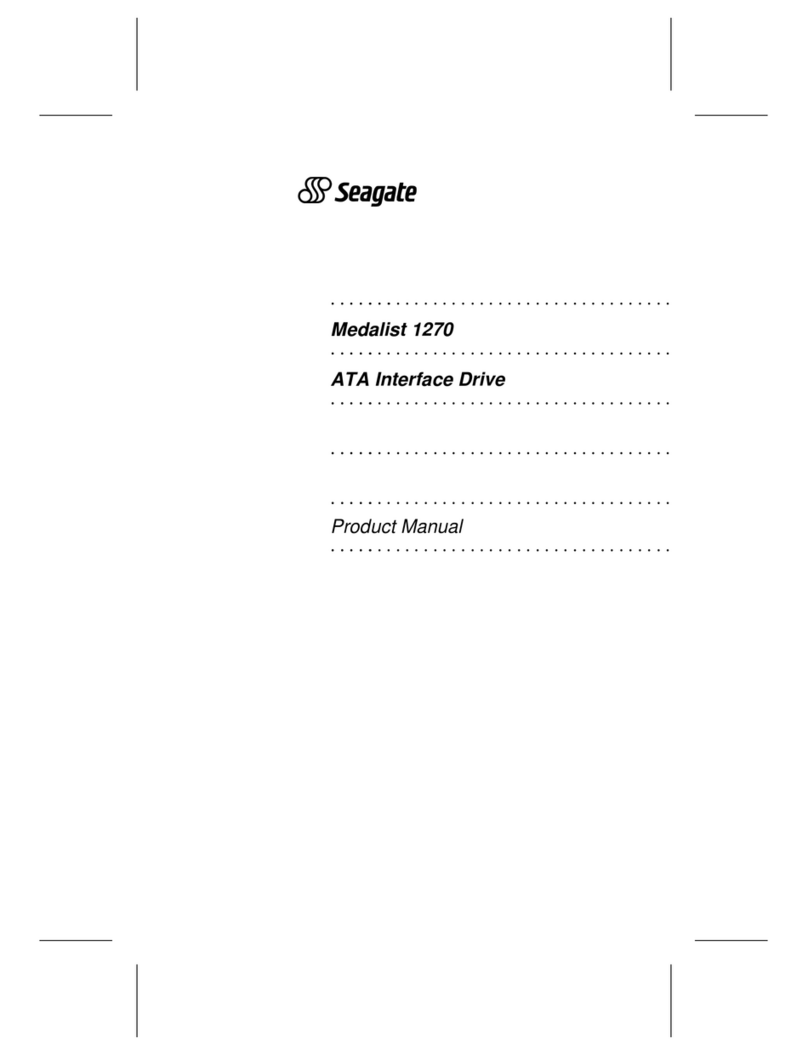
Seagate
Seagate MEDALIST 1270 product manual