DMQ QS5 Series User manual

I

P/N: QSD 501 –ENG –Rev 3 –2012

I
Chapter 1
First Steps
1.1
Know the QS5
1
1.1.1
Front panel
1
1.1.2
Connectors
2
1.2
Install or replace batteries
2
1.3
Connecting the transducer
5
1.4
The “Q” key
6
1.5
Display illumination and contrast
6
1.5.1
Display backlight illumination
6
1.5.2
Display contrast
7
1.6
Locking and unlocking the keypad
7
Chapter 2
Measuring with the QS5
2.1
Numerical measure screen (Normal)
9
2.1.1
Screen mode-1 (Min., Max.)
9
2.1.2
Screen mode-2 (Percentage Value)
10
2.1.3
Screen mode-3 (Datalogger)
11
2.2
Keys in numerical measure modes
11
2.3
BScan graphic measure screen
14
2.4
Keys in BScan graphic measure sceen mode
15
2.5
Zero calibration (Auto)
15
2.6
1-Point and 2-Point calibration
17
2.7
Changing the material velocity
19
2.7.1
Change to a known velocity
19
2.7.2
Change velocity using a known
thickness value
19
2.8
Adjusting trigger and gain
20
2.9
Understanding the coupling icons and the
energy level indicator
21
2.9.1
Coupling icons
21
2.9.2
Coupling energy level indicator
22
2.10
Measuring thru-coating or thru-paint
25

II
Chapter 3
Menu system and editing
3.1
Instructions on using the menu system
28
3.1.1
Text editor
29
3.2
Main menu
31
3.2.1
Change measuring unit
31
3.2.2
Alarm settings
31
3.2.3
Set BScan range
33
3.2.4
Select language
33
3.2.5
Unit information
34
3.3
General configuration options
34
3.3.1
Set time and date
35
3.3.2
Set time and date format
35
3.3.3
Set keypad sensitivity
36
3.3.4
Set auto-off time
37
3.3.5
Adjust display contrast
37
3.3.6
Beep activation
38
3.3.7
Introduction screen
38
3.3.8
Owner information
38
3.3.9
Lock configuration options
40
3.3.10
Model upgrade licenses
41
3.3.11
Return to factory default settings
42
3.4
Measuring configuration options (Ultrasonic)
43
3.4.1
Set material velocity
43
3.4.2
Select measure mode
44
3.4.3
Adjust gain
45
3.4.4
Adjust trigger
45
3.4.5
Select refresh rate
45
3.4.6
Select transducer frequency
46
3.4.7
Select coating type
46
3.4.8
Select calibration mode
47
3.4.9
Hold last value
48
3.4.10
Energy level compensation (DAC)
48
3.4.11
Material condition analyzer
49

III
3.4.12
Nums Zoom measuring screen mode
50
3.4.13
Continuous measuring monitor
50
3.4.14
Adjust pulser excitation voltage
51
3.4.15
Return to factory default settings
52
Chapter 4
Using the Datalogger
4.1
Understanding how data is organized
53
4.2
Memory menu
53
4.3
Creating a file
54
4.4
Actions over single files
55
4.4.1
View data in a single file
56
4.4.2
The “Q” key in a grid
56
4.4.3
The “Q” key in a histogram
57
4.4.4
The “Q” key in a SCAN graphic
59
4.4.5
Send data from a single file
60
4.4.6
Rename a file
60
4.4.7
View file size
60
4.5
Actions over all files
60
4.5.1
Send all files
61
4.5.2
Erase all files
61
4.6
The Datalogger in the measuring screen
62
4.6.1
Datalogger information
62
4.6.2
Quick memory menu (Mem key)
63
4.7
Connecting to a PC with DataCenter
64
4.8
Datalogger configuration
65
4.8.1
Configure communications
65
4.8.2
Capture modes
66
4.8.3
Set number of values
67
4.8.4
Selecting fixed batch
67
4.9
Advanced Datalogger configuration
68
4.9.1
Store every (N) number of values
68
4.9.2
Record operator actions
68
4.9.3
Record date and time
69

IV
Tips on how to measure correctly
Technical specifications
Additional information
Unit maintenance
QS5 accessories
Error messages
Our website: www.demeq.com
Technical support

V
And thank you for purchasing a QS5 ultrasonic corrosion and wall
thickness gauge.
At dmq we develop, manufacture and distribute software and quality
control instruments offering innovation and solutions that come as a
direct result of listening to your needs as a user. We apply some of the
latest technology available in the industry to build instruments that are
robust, precise, and easy to operate.
We are convinced that our products would not be complete without
permanent technical and after sales support. So in addition to a great
product we offer:
Quick answers to your inquiries.
Unlimited access to technical information as well as
application notes.
Special offers for registered customers.
Firmware and software upgrades at no charge.
Attention to your inquiries and suggestions.
We hope that the QS5 will meet and exceed your application needs.

VI
The information included in this manual applies to all QS5 series
ultrasonic corrosion and wall thickness gauges including models B, DL,
E and DLE.
dmq is a registered trademark of demeq S.R.L and its affiliate
companies.
The information contained in this manual is intended to educate users
on the operation of the QS5 gauges. Failure to read and understand
this manual can lead to measurement errors. Decisions based on
measurements and or results that are erroneous can lead to property
damage, personal injury or even death. Demeq S.R.L assumes no
responsibility as a result of the improper use of our instruments.
ASTM E797
The user must be trained in ultrasonic testing procedures and on how
to properly configure the unit for testing. All of the following should
be taken into consideration:
Understand the theory on sound wave propagation.
Select the instrument as well as the transducer that is best
suited for your application.
Know the specific requirements for the test you will be
conducting.
This manual provides all of the information needed to configure and
operate the QS5 gauge. However there are additional factors that can

VII
affect tests done with this instrument. Specific information on those
factors is outside the scope of this manual. When in doubt you should
always seek expert advice or refer to specific textbooks on ultrasonic
testing. Additional information can also be found on the internet and
through local government agencies as well as in technical institutes.
The QS5 operates with dual crystal transducers that use the “pitch-
catch” principal. Dual crystal transducers use two piezoelectric crystals
whereby one crystal is excited with short electrical pulses from the unit
sending short acoustic waves into the test piece. The second crystal
then receives the acoustic waves reflected at the end of the test piece.
The frequency of the acoustic waves changes between 2 and 10 MHz
depending on the probe being used.
All QS5 gauges operate in Echo-1 or normal (no coat) mode where a
measurement is the result of the sum of the time delay from the
transducer and the time it takes for the acoustic wave to rebound back
to the transducer after it reaches the end of the test piece. In Echo-2 or
thru-paint mode (QS5 E and QS5 DLE only), the unit measures the time
interval between the first and second echoes and does not take into
consideration the time delay from the transducer.

VIII
Figure 1: Echo-1 and Echo-2 mode acoustic wave representation
In ultrasonic testing information is obtained from measuring sound
waves. Users must be very careful when making assumptions in
regards to the entire test piece condition when there are areas that
have not been inspected. In large and massive test pieces it would be
practically impossible to test the entire piece and therefore conclusions
for the whole piece based solely on the areas that have actually been
inspected, should only be done by experienced operators. Only trained
users should evaluate test pieces that could present erosion and or
corrosion.
In order to minimize test result errors the following must be observed:
Before taking actual measurements the unit and transducer have to be
calibrated. Calibration of the transducer is also known as zero
calibration or delay calibration (Page 15). If the unit and transducer are
not calibrated, or calibrated incorrectly, the resulting measurements
will be unreliable. Each and every time a transducer is changed it must
be calibrated to the unit.
Because the sound velocities in materials will often vary significantly
from published values, best results are obtained when the instrument
is calibrated on a reference test block made from the same material as
that of the actual test piece. The block should be flat, of a smooth
finish, and be as thick as the maximum thickness of the test piece.
Careful consideration by the user must be made when evaluating the
accuracy of a thickness value because considerable changes in the
sound velocity of a material may have occurred as a result of a
treatment. So for example a test piece made of steel that has been
thermally treated, will look the same as a regular test piece made of

IX
untreated steel, but the sound velocities vary significantly. Instruments
should be calibrated before and after testing to minimize errors.
Transducers must be in good condition and show no visible signs of
excessive wear or defects on their surface. Badly worn transducers can
provide erroneous measurements.
The thickness of the material being tested must be within the specified
thickness range of the transducer and the temperature of the material
must also be within the specified temperature range of the transducer.
Calibration as well as actual testing should be performed under similar
coupling conditions. Couplant must be applied in an even and
consistent manner to minimize variations in couplant layers that may
result in testing errors. The amount of couplant should be kept to a
minimum and consistent pressure should be applied on the transducer
when measuring.
Doubling refers to a thickness measurement that displays a reading
that is twice or even three times the real test piece thickness. Doubling
often may happen when trying to measure below and above the
specified range for the transducer and when using worn transducers.
When in doubt, the test piece thickness must be measured using other
methods and or instruments and the unit must then be calibrated
using reference test blocks of known thickness values that are made of
the same material as the actual test piece. This is very important when
measuring unknown test pieces for the first time.
When possible calibrate your instrument on-site using a test block that
is at the same temperature as the test piece in order to minimize
errors.

X
All QS5 series corrosion and thickness gauges are for industrial use
only and cannot be used in medical applications. The QS5 operates on
two AA size batteries. We strongly recommend that you use only top
brand name alkaline batteries.
Disposal of your QS5 gauge and its components must be done in
compliance with all applicable regulations.
Because of its complexity level, software is never really completely error
free. For this reason in software controlled instruments always make
sure that the operations required for your application are in correct
working order.
Demeq S.R.L provides a limited warranty for a period of 2 (two) years
on electronic units and for 6 (six) months on transducers from the date
of purchase and may be extended for up to 5 years.
Every instrument undergoes thorough testing during manufacturing as
well as before shipping. In the event warranty service where to become
necessary, dmq and or your local distributor or representative will
make a reasonable effort to replace your defective unit with another
new or used unit, while your instrument undergoes warranty repair.

Chapter 1 1
Figure 1.1: Front of the unit
1. Graphic LCD display with LED backlight illumination
2. Move Left key / Switch measuring modes: normal
measurements or Echo-1 / Thru-Paint or Echo-2 (Echo)
3. Move Up key / Manually store a value (Store)
4. Move Right key / Switch to graphical measure mode screen
(BScan)
5. Menu key / Enter and exit measure screen / Exit and return to
menus (Home)

2 Chapter 1
6. Move Down key / Quick access to memory menu screen
options (Mem)
7. Change backlight illumination key (On, Off, Auto)
8. Enter key / Edit values on the measure screen (Edit)
9. The key: Power On and Shutdown (touch and hold for 2
seconds) / Make quick and short touches to activate special
functions and features
10. Calibration disk
11. Horizontal scrolling center point (lock and unlock keypad on
measure screen)
12. Vertical scrolling center point (adjust LCD contrast)
Figure 1.2: Unit connectors
1. Receiving transducer connector (Type Lemo 00)
2. Emitting transducer connector (Type Lemo 00)
3. USB mini connector to connect to PC using a USB cable
(supplied with the unit)

Chapter 1 3
The QS5 is powered by 2 (two) AA batteries that are placed in the
battery compartment located in the back of the unit. To access to the
battery compartment slide the cover as shown in figure 1.3-1 and
gently push the extraction ribbon upward and slightly towards the
right to release the batteries (figure 1.3-2).
When you install new batteries, first insert the positive end of each
battery so that it coincides with the positive pole inside the battery
compartment as you see in figure 1.4-1. Always leave the extraction
ribbon underneath the batteries.
Figure 1.3: Removing batteries

4 Chapter 1
Figure 1.4: Replace / Insert batteries
Notes
Use new alkaline top brand batteries only.
Do not mix new and old batteries. Always replace both
batteries.
Rechargeable batteries type NiMH can be used but will
result in less time of continuous operation.

Chapter 1 5
Important
Do not remove batteries while the unit is powered as
this may affect the Datalogger (See Appendix:
“Additional information, Error Messages”)
The QS5 has two type Lemo “00” connectors located on top of the
unit. Because this is the standard for most dual crystal probes, you
could basically connect any probe to your QS5. Keep in mind that the
gain may need to be adjusted when changing probes.
To connect the probe, simply align any
of the male connectors located at the
end of the transducer cable to any of
the female connectors located on the
gauge and press gently until
connected.
To release the probe hold the knurled
section on the male connectors and
pull gently away from gauge until
released.
Figure 1.5: Connecting the transducer

6 Chapter 1
The has three functions:
When the unit is off, touch for 2 seconds to power on
the unit.
When the unit is on, touch for 2 seconds to shutdown
the unit.
With the unit on, making short touches to the will
activate special functions described in later chapters of this
manual.
Backlight illumination and contrast options can be changed from any
screen in the unit.
Touch to change the backlight illumination settings.
Figure 1.6: Backlight illumination options

Chapter 1 7
The display contrast on all dmq units is digital.
Touch the white dot located in the center of
the vertical scrolling bar between the -
keys and a contrast window will open.
Move your finger towards the top and or
bottom of the dotted line to adjust the contrast
on your display.
Figure 1.7: Display contrast adjustment
To lock the keypad place your finger on the white dot located in the
center of the horizontal scrolling bar between the - keys.
Move your finger to the right following the dotted line and a window
on the unit display will open with the word Lock. Continue moving
your finger in the same direction until you enter locked mode. The
window on the display will close and the locked keypad indicator will
show on the top right of the unit screen.
Figure 1.8: Locking the keypad

8 Chapter 1
Sliding the finger to the left will unlock the keypad.
Figure 1.9: Unlocking the keypad
\
Important
The keypad can only be locked and unlocked in the
measuring screens.
This manual suits for next models
4
Table of contents
Other DMQ Measuring Instrument manuals
Popular Measuring Instrument manuals by other brands
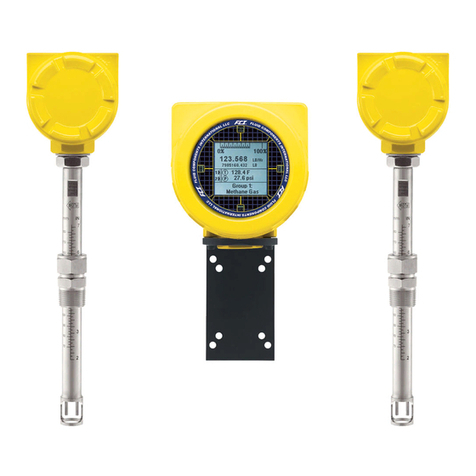
FCI
FCI ST100A Series Installation, operation and maintenance manual
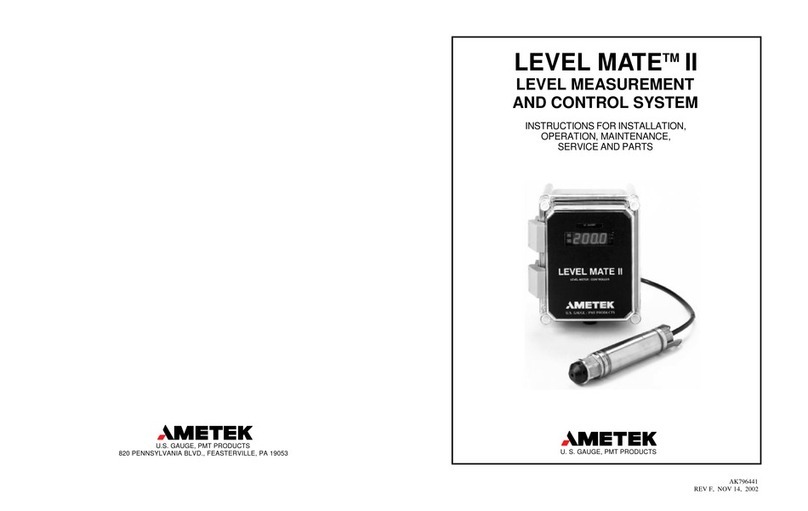
Ametek
Ametek Level Mate II INSTRUCTIONS FOR INSTALLATION, OPERATION, MAINTENANCE, SERVICE AND PARTS

Lovibond
Lovibond Tintometer MD100 instruction manual

Malvern
Malvern NANOSIGHT NS300 operating manual
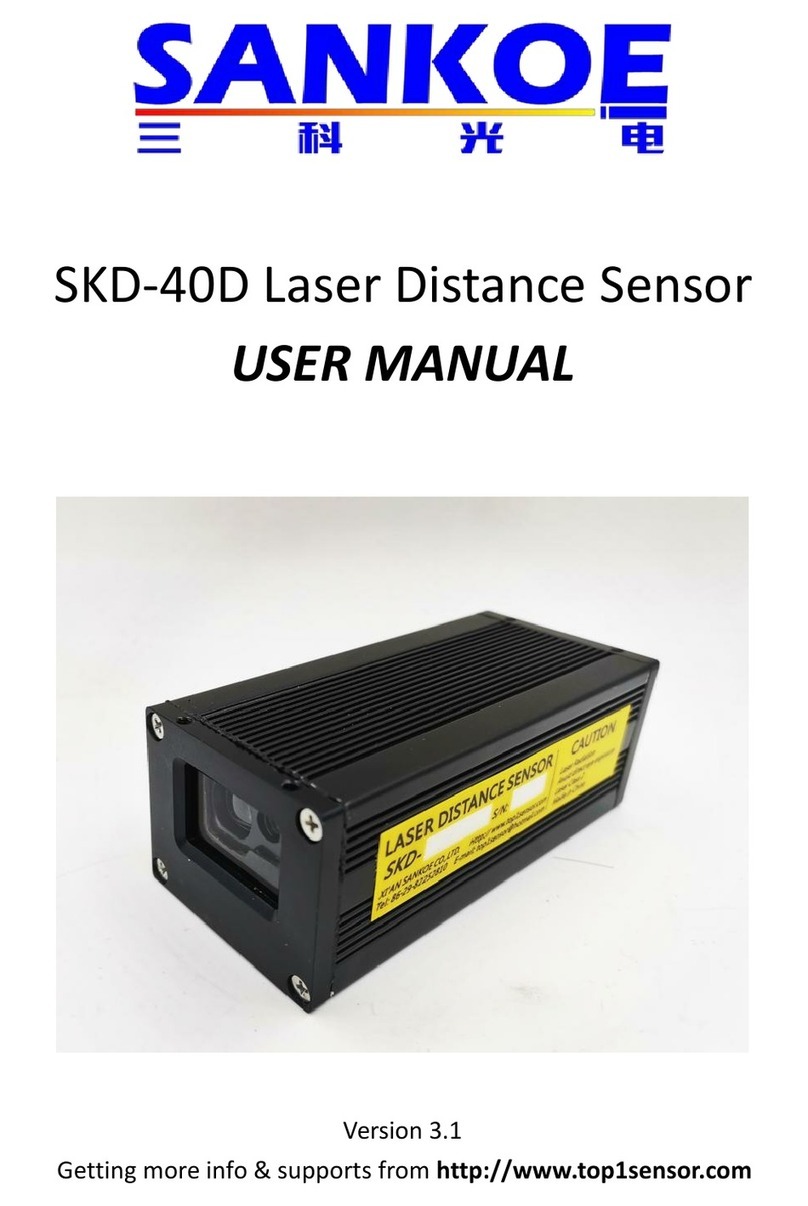
SANKOE
SANKOE SKD-40D user manual
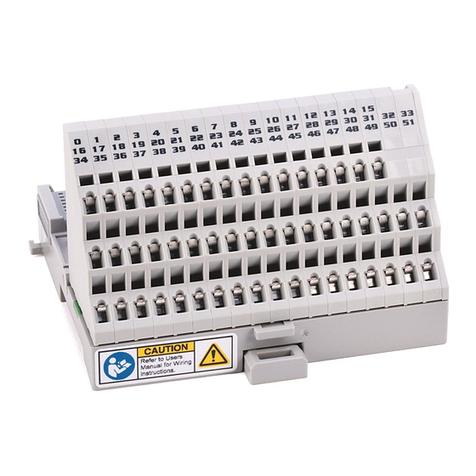
Rockwell Automation
Rockwell Automation Allen-Bradley 1440-TBS-J installation instructions