Dover NORRISEAL 1001 Series Operating instructions

P. . Box 40525 · Houston, Texas USA 77240-0525
Tel: 713·466·3552 · Fax: 713·896·7386
www.norriseal.com
1001-0113O — ©2013, January 2013
I
NTRODUCTION
C A U T I O N
T e instructions provided erein s ould
be completely reviewed and understood
prior to installing, operating or repairing
t is equipment. All ATTENTION, CAU-
TION, DANGER and WARNING notes
must be strictly observed to prevent seri-
ous injury or equipment malfunction.
cope
This manual includes installation,
operation and maintenance infor-
mation for 1.5 through 6.0-in.
Norriseal Series 1001, 1001A, and
1001X evel Controllers.
Description
The Series 1001, 1001A, and 1001X
evel Controllers are designed for
general purpose use in liquid level
and interface control applications
calling for either modulating
(Throttle) or on/off (Snap) pneumatic
service and can be direct or reverse
acting. Electric switch models are
also available.
Norriseal level controllers are
equipped standard with horizontal
or vertical PVC 1.88 x 12-in. displac-
ers. Displacer options include Acrylic
and 316 S.S. materials in various
lengths and diameters, including
hinged models, to accommodate a
wide range of control applications.
The 1001 has a smaller case than the
1001A or 1001X and has a knurled
knob screw type closure. The 1001A
and 1001X have lever latch door
closing mechanisms and have a
sealed door. The 1001 and 1001A
have the case mounted left or right
of the body, while the 1001X is cen-
ter-back mounted.
C A U T I O N
Before disassembly or maintenance, all
pressures in t is device must be relieved.
Failure to relieve pressures may result in
personal injury or device damage. T e
resulting uncontrolled venting or spilling
of process fluids may cause personal
injury, loss of process control or environ-
mental contamination.
Controller Identification
Controller model numbers are typi-
cally 13 positions long (example:
2SM60-SRDA-BG). Refer to Table 1
— Model Designation on page 2 for
specific information on the controller
nomenclature.
A nameplate attached to the inside of
the case by the lower door hinge
includes the controller model and
serial numbers as well as other infor-
mation pertinent to the controller
assembly, such as supply and out-
put pressures, displacer material and
rating, body size and material, ANSI
class, and pressure and temperature
limits.
Always use only Norriseal replace-
ment parts when servicing level con-
trollers. Please refer to the serial and
model numbers when ordering
replacement parts.
Page 1 of 12
O
PERATING AND
M
AINTENANCE
M
ANUAL
Series 1001, 10 01A, 10 01XL Level Control
CONTENT
PAGE
I
NTRODUCTION
1
Scope 1
Description 1
Controller Identification 1
P
RINCIPLE OF
O
PERATION
3
P
ILOT
O
PERATION
4
1.0 L
EVEL
C
ONTROLLER
I
N TALLATION AND
TART
-
UP
5
1.0 L
EVEL
A
DJUSTMENT
6
1.2 L
IQUID
L
EVEL
I
NTERFACE
6
2.0 L
EVEL
C
ONTROLLER
M
AINTENANCE
7
2.1 L
EVEL
C
NTR LLER
P
REVENTIVE
M
AINTENANCE
7
2.2 L
EVEL
C
NTR LLER
D
ISASSEMBLY
7
2.3 L
EVEL
C
NTR LLER
R
EASSEMBLY
7
2.4 P
IL T
R
EM VAL
/R
EPLACEMENT
8
2.5 L
EVEL
C
NTR LLER
D
ISASSEMBLY
C
ASE
M
UNTING
C
NVERSI N
9
2.6 L
EVEL
C
NTR LLER
D
ISASSEMBLY
P
IL T
A
CTI N
C
NVERSI N
9
2.7 L
EVEL
C
NTR LLER
B
DY
D
ISASSEMBLY
9
2.8 L
EVEL
C
NTR LLER
B
DY
R
EASSEMBLY
9
3.0 R
EPAIR
K
IT
10
T
ABLE
Table 1 — Model Designation 2
Table 2 — Wiring Diagrams 10
Tabla 3 — Trouble Diagnosis 11
A
B
S
Q
u
a
l
i
t
y
E
v
a
l
u
a
t
i
o
n
s
,
I
n
c
.
M
a
n
a
g
e
m
e
n
t
S
y
s
t
e
m
C
e
r
t
i
f
i
c
a
t
i
o
n

P. . Box 40525 · Houston, Texas USA 77240-0525
Tel: 713·466·3552 · Fax: 713·896·7386
www.norriseal.com 1001-0113O — ©2013, January 2013
O
PERATING AND
M
AINTENANCE
M
ANUAL
Series 10 01, 1001A, 10 01X L Level Control
Page 2 of 12
End Connection Size
1.5 in. 15
2 in. 2
3 in. 3
4 in. 4
6 in. 6
Material – Body/ haft/Block
C.S./303/303 –
C.S.NACE/316/316 N
316/316/316 S
316NACE/316/316 R
Case Mounting
eft Hand
Right Hand R
AcciPilot Action
Direct Acting D
Reverse Acting R
Service Condition
Standard (1001 Only) A
Vibration (Standard
On 1001A/1001X ) B
Pressure Gauges
Bronze 0–30 psi –
Bronze 0–60 H
316 SS 0–30 J
316 SS 0–60 K
iquid Filled 0–30 Brz (1001A/X )
iquid Filled 0–60 Brz (1001A/X ) M
Seal/Bearing Material/Temp
Buna/303/180°F A
Viton/303/400°F F
EPR/303/275°F E
Aflas/316/400°F S
Enclosure
Standard Case (1001 Only) A
Sealed Case/Cover G
Sealed Case/Cover
Piped Exhaust H
Sealed Case/Cover
Marine Internals K
Sealed Case/Cover
Piped Exhaust and
Marine Internals J
Displacers
PVC (Standard): –20 to 140°F
(6170 psi)
(6170 psi)
Acrylic: –20 to 200°F
Aluminum: –70 to 400°F
(6170 psi)
316 SS: –70 to 400°
(2000 psi)
Pilot
Pneumatic Snap (On/Off) S
Pneumatic Throttle (Modulating) T
EnviroSave (Snap) B
EnviroSave – Vibration C
Electric DPDT – Ex-Proof D
Electric SPDT – Ex-Proof E
Electric DPDT – Splash-Proof F
Electric SPDT – Splash-Proof O
Electric DPDT – Hermetic Seal
Electric SPDT – Hermetic Seal K
End Connection Style
Screwed MNPT SM
Flanged – Raised Face RF
Flanged – Ring Type Joint RJ
Flanged – Special 4 Bolt SF
Beveled – Slip On BS
Beveled – Butt Weld Sch 40 B4
Beveled – Butt Weld Sch 80 B8
Beveled – Butt Weld Sch 160 B1
Beveled – Butt Weld SCH XXH BX
Grooved GV
Socket Weld SW
Union – Dover DU
Union – Yale YU
Union – Acme AU
Pressure Rating
AN I Rating
AN I
150 285 02
300 740 07
400 960 09
1000 10
600 1480 14
1500 15
2000 20
900 2220 21
2500 25
3000 30
1500 3750 36
4000 40
5000 50
6000 60
2500 6170 60
eries
1001
1001A
1001X
T A B L A 1 . D E T E R M I N A C I Ó N D E L M O D E L O
1001A 2 SM 60 - S R D A - B G

P. . Box 40525 · Houston, Texas USA 77240-0525
Tel: 713·466·3552 · Fax: 713·896·7386
www.norriseal.com
1001-0113O — ©2013, January 2013
WA R N I N G
Maximum allowable pressures for t e
level controller body and t e maximum
allowable pressure at t e maximum tem-
perature for t e level controller are s own
on t e nameplate mounted in t e case. If
pressure to t e level controller is capa-
ble of exceeding t ese limits, install relief
valves or ot er over-pressure protection
devices in t e pressure lines.
C A U T I O N
W en ordered, t e controller body, dis-
placer material, and configuration were
selected to meet particular pressure, tem-
perature, and fluid conditions. Bodies and
displacers are limited in t eir operating
pressure and temperature ranges as well
as t eir ability to resist corrosion. Do not
apply any ot er conditions to t e
controller wit out first contacting your
Norriseal sales office or your sales
representative.
P
RINCIPLE OF
O
PERATION
Force Balance Principle
The operation of the Series 1001,
1001A, and the 1001X evel
Controllers is based on the Force
Balance Principle. A spring balances
the weight of a displacement type
sensing element. As liquid rises
around the displacer, the amount of
force available to the pilot is pro-
portional to the weight of the liquid
displaced. The force available is
transmitted to the pilot thrust pin
through a lever and fulcrum. The
higher the level, the greater the force
available to the pilot thrust pin.
The control is direct acting (rising
level increases pilot output) when
the pivot point of the lever is on the
spring side of the control case. The
control is reverse acting (rising level
decreases pilot output) when the
pivot point of the lever is on the
opposite side of the control case
from the spring.
Adjusting Proportional Band
Proportional band is the ratio of used
displacer length to total length of dis-
placer. For example, if 6 in. of level
change will develop a 3 to 15 psi out-
put signal with a 12-in.-long vertical
displacer, the level controller is said
to have a 50% proportional band.
By moving the fulcrum closer to the
pivot point, the proportional band is
increased. ikewise, by moving the
fulcrum toward the snap ring
decreases the proportional band. A
3 to 15 psi or 6 to 30 psi output sig-
nal may be obtained over any po tion
of the displacer by adjusting the
fulcrum.
Adjusting Level
The spring is used to balance the
weight of the displacer. As level
increases, the weight of the displacer
decreases. The spring tension
increases and is transmitted to the
O
PERATING AND
M
AINTENANCE
M
ANUAL
Series 10 01, 1001A, 10 01X L Level Control
Page 3 of 12
Figure 1 — Direct acting, right hand mount controller
Figure 2 — Adjusting proportional band
Pilot Snap Ring
Sensitivity Fulcrum
Pivot Pin
Thumb Screw
Torque Bar
Balance Spring
Adjusting Knob
Level Adjusting Bar
Decrease
Proportional Band
Increase
Proportional Band

P. . Box 40525 · Houston, Texas USA 77240-0525
Tel: 713·466·3552 · Fax: 713·896·7386
www.norriseal.com 1001-0113O — ©2013, January 2013
pilot thrust pin through the lever and
fulcrum.
By increasing tension on the spring,
a lower level is sensed. By decreas-
ing tension on the spring, a higher
level is required to produce the same
force as before.
Spring compression can be reduced
to a point where a hydrocarbon liq-
uid level will rise above the displacer
without transmitting enough force
to the pilot to produce an output. If
properly adjusted, water, with a
higher specific gravity, will rise to the
displacer resulting in a change in
weight of the displacer. This will
produce an output, thus sensing the
interface level of water and hydro-
carbon. This wide range of control
makes liquid interface sensing
possible.
P
ILOT
O
PERATION
As described in Principle of
Operation, force from the balance
spring is transmitted via the lever
and fulcrum to the thrust pin of the
pilot.
Snap, Relief, and Envirosave™Pilots
These pilots have
two seats. The upper
seat (D) is sealed by
a ball (A). On Snap
pilots (see Figure 4),
the ball seat is a
metal seat and on the
Relief and Envirosave
pilots, there is an
elastomeric seat
ensuring zero-leak-
age seals. The upper
seat controls supply
air and the ball is
held in the closed
position by the supply air pressure.
When mechanical force upward
from the thrust pin (B) is sufficient
to overcome supply air pressure
holding the ball to the seat, the ball
snaps upward, supply air flows
downward and out the output port
(H), and the lower port is sealed by
the spherical end of the thrust pin
preventing supply air from escaping.
As the upward force on the thrust
pin is decreased to a point where
supply air pressure overcomes the
upward force, the ball once again
seals the supply air and simultane-
ously opens the lower exhaust port
venting gas from the control valve
actuator.
On the Relief pilot, the passage
between the supply air and the out-
put port is significantly larger per-
mitting supply air to exit the output
port at a faster rate.
Throttle Pilot
The Throttle pilot
(see Figure 5) also
has two seats to
admit supply gas
and exhaust “used”
gas. A diaphragm
(E) is used to sense
pressure/force feed-
back and a spring
assists closing pres-
sure on the thrust
pin.The Throttle
pilot is operationally
similar to the Snap
pilot except that the output pressure
is proportional to the mechanical
force applied to the thrust pin (C). As
the thrust pin force changes, the pilot
seeks to maintain equilibrium by
either decreasing (exhausting) out-
put loading pressure or increasing
output loading pressure. Supply air
does not flow when the loading
pressures of the pilot are balanced.
Electric Pilot witches
Two standard switches are available:
SPDT (Single Pole Double Throw)
and DPDT (Double Pole Double
Throw) in Splash-Proof, Explosion-
Proof, or Hermetically Sealed
configurations.
O
PERATING AND
M
AINTENANCE
M
ANUAL
Series 10 01, 1001A, 10 01X L Level Control
Page 4 of 12
Pilot
Sensitivity Fulcrum
Pivot Pin
Thumb Screw
Torque Bar
Level
Adjusting
Bar
Adjusting Knob
Snap Ring
Figure 3 — Reverse acting, left hand mount controller
Resorte de
equilibrio
Figure 4 —
Snap pilot
Force
Figure 5 —
Throttle pilot
Force

P. . Box 40525 · Houston, Texas USA 77240-0525
Tel: 713·466·3552 · Fax: 713·896·7386
www.norriseal.com
1001-0113O — ©2013, January 2013
Hermetically Sealed switch pilots are
terminated in a junction box U listed
Class I, Div. 1, Groups C & D and
Class II, Div. 1, Groups E, F, & G. The
switches themselves are hermeti-
cally sealed for hazardous locations
listed U and CSA Class I, Div. 1,
Groups A, B, C, & D and Class II, Div.
1, Groups E, F, & G.
Explosion-Proof switch pilots listed
by U and CSA for use in hazardous
locations Class I, Div. 1, Groups C &
D and Class II, Div. 1, Groups E, F, &
G. A switch listed for Class I, Div. 1,
Group B is available. CSA requires
the following statement for Class I,
Group B:
C A U T I O N
To prevent t e emission of ot particles,
joint surfaces must be t oroug ly cleaned
before closing cover
1.0 L
EVEL
C
ONTROLER EN
I
N TALLATION AND
TART
-
UPD
C A U T I O N
W en making connection to t e vessel,
observe all safety requirements of t e
area w ere t e work is being done. Be
especially careful of pressure vessels.
WA R N I N G
Turn off and lock out all electrical power
before beginning installation.
DA N G E R
Special attention is required for level con-
trollers wit t e electric switc option.
Install approved conduit seals wit in 18
in. (0.5 M) of t e enclosure as required
by National and Canadian Electrical
Codes. Serious personal injury and/or
property damage can result if seals are
not installed.
C A U T I O N
Install a conduit seal wit a drain loop or
ot er means to prevent condensate from
entering t e enclosure. Failure to do so
will allow moisture to enter t e enclo-
sure. T is can cause equipment damage
or malfunction..
C A U T I O N
Be sure t at all wiring and conduit con-
forms to t e requirements of t e National
Electric Code and any enforcing agencies
aving jurisdiction over t e installation.
Be sure t at special conditions, suc as
areas aving explosion azards, are given
full consideration.
1. After unpacking the controller,
visually inspect the unit for any
evidence of shipping damage.
Shipping damage claims must be
filed with the carrier who handled
the package(s). Remove any for-
eign material that may have col-
lected during crating and
shipment. Remove the flange or
thread protectors from the body
end connection.
2. Insure that screwed and gasket
surfaces on both the controller
and the vessel are free of any for-
eign materials.
3. The controller normally ships in 3
or 4 pieces: the controller body/
case assembly, the displacer, the
displacer arm, and, for vertical
installations, the swivel. For
O
PERATING AND
M
AINTENANCE
M
ANUAL
Series 10 01, 1001A, 10 01X L Level Control
Page 5 of 12
Figure 6 — Hermetically sealed electric switch
Figure 7 — Explosion-proof electric switch

P. . Box 40525 · Houston, Texas USA 77240-0525
Tel: 713·466·3552 · Fax: 713·896·7386
www.norriseal.com 1001-0113O — ©2013, January 2013
this(reason some field assembly
is required. Insert the displacer
arm in the opening in the con-
troller body. Carefully align the dis-
placer arm in the body shaft and
screw the arm into the shaft. If this
is a vertical installation, screw the
swivel onto the free end of the dis-
placer arm. Screw the displacer
either into the free end of the dis-
placer arm (horizontal application)
or the free end of the swivel (ver-
tical application).
4. Install the controller using good
piping practice. For flanged bod-
ies, use a suitable gasket between
the body and vessel flanges. For
threaded (NPT) bodies, use TFE
tape or pipe thread sealant on
external pipe threads.
C A U T I O N
T e Bodies are rated ANSI 150, 300, 600,
900, 1500 or 2500 class. Do not install t e
level controller in a system w ere t e
working pressures can exceed t ose
marked on t e nameplate.
5. Connect instrument air to the
controller supply connection on
the back of the controller. The
supply and output connections are
clearly marked. On the 1001 con-
troller, it is the upper connection.
On the 1001A and 1001X con-
trollers, it is the connection on the
right when looking at the rear of
the controller case. Connect the
control valve signal line to the out-
put connection.
6. Open the case and rock the torque
bar by hand to verify the displacer
arm moves freely and is NOT rest-
ing against the vessel nozzle or
other obstruction. The arm must
be reasonably centered in the con-
nection opening, parallel to the
ground. If necessary, turn the
adjusting knob under the Balance
Spring to position the arm in the
center of the connection opening.
1.1 L
EVEL
A
DJU TMENT
NOTE: All controllers are factory pre-
set for average level and sensitivity
1. With the displacer arm centered
in the vessel nozzle as described
in paragraph 1.0, Step 6, to lower
the level, turn the adjusting knob
under the Balance Spring
C OCKWISE to increase com-
pression on the Balance Spring
(decrease level). To raise the level,
turn the knob COUNTER-C OCK-
WISE to decrease compression on
the Balance Spring (increase
level).
2. Adjust the proportional band
(dump span) by first loosening the
thumb screw on the Sensitivity
Fulcrum. Slide the fulcrum along
the Flapper Bar toward the snap
ring (toward the pilot) to
DECREASE proportional band and
INCREASE SENSITIVITY. Slide the
fulcrum along the Flapper Bar
away from the snap ring (away
from the pilot) to INCREASE pro-
portional band and DECREASE
SENSITIVITY. Tighten the thumb
screw on the Sensitivity Fulcrum
when the proper span is selected.
1.2 L
IQUID
L
EVEL
I
NTERFACE
NOTE: All controllers are factory pre-
set for average level and sensitivity.
1. Set the Sensitivity Fulcrum 1⁄4 in.
from the snap ring, reduce the
spring tension slowly by turning
the adjusting knob COUNTER-
C OCKWISE, and let the UPPER
fluid rise to submerge the
displacer. Fine tune after the dis-
placer is fully submerged in the
UPPER fluid by slowly increasing
spring tension (turning adjusting
knob C OCKWISE) until an output
signal is obtained. Then back the
tension off slowly (turning adjust-
ing knob COUNTER-C OCKWISE)
until the output signal pressure
returns to zero.
2. et the lower fluid rise until the
desired interface level is reached.
Fine tune by slowly increasing
spring tension (turning adjusting
knob C OCKWISE) until an output
signal is obtained. Then back the
tension off the Balance Spring
slowly (turning adjusting knob
COUNTER-C OCKWISE) until the
output signal pressure returns to
zero.
O
PERATING AND
M
AINTENANCE
M
ANUAL
Series 10 01, 1001A, 10 01X L Level Control
Page 6 of 12
Pivot
Pin
Torque Bar
Balance
Spring
Adjusting
Knob
Sensitivity
Fulcrum
Snap Ring
Direct acting Reverse acting
Figure 8 — How to make level adjustments

P. . Box 40525 · Houston, Texas USA 77240-0525
Tel: 713·466·3552 · Fax: 713·896·7386
www.norriseal.com
1001-0113O — ©2013, January 2013
3. If a longer dump span is desired,
move the fulcrum farther away
from the snap ring and repeat the
above procedure.
2.0 L
EVEL
C
ONTROLLER
M
AINTENANCE
WA R N I N G
Before attempting any repairs, isolate t e
controller from t e system and make sure
t at all pressure is released from t e
controller body. S ut off and vent supply
and output (signal air) lines to t e
controller. On electric pilots, disconnect all
power to t e controller.
1. Isolate the controller from the
process.
2. Shut off the output and supply
lines to the controller. If the pilot is
electric, turn off and lock out all
electrical power to the controller.
3. Release the process pressure.
Controller parts are built to withstand
a great deal of wear under normal
operating conditions and will rarely
need to be repaired. Should repair
be necessary, the following sections
describe the procedures for disas-
sembling and re-assembling the
controller for normal maintenance
and troubleshooting.
2.1 L
EVEL
C
ONTROLLER
P
REVENTUIVE
M
AINTENANCE
1. In normal service, O-Rings and
the bearings on the main shaft
should last for many years. If a
leak occurs, replace the O-Rings.
Order a evel Seal Kit ( SK)
from Norriseal.
2. If the controller is used in high-
paraffin service or interface con-
trol with a horizontal displacer,
remove and inspect the body of
the controller after three (3)
months of service and check for
debris buildup. Future inspection
times after initial inspection can
be gauged by how much buildup
of debris occurred in the initial
three (3) months of service.
2.2 L
EVEL
C
ONTROLLER
D
I A EMBLY
NOTE: T ese instructions do not
apply to t e pilot. See Paragrap 2.4
for instructions for removing and/or
replacing t e pilot.
1. Relax all tension on Balance
Spring.
2. Remove the Balance Spring and
upper spring retainer.
3. Remove the stud bolt holding the
adjusting knob and remove both
from the case.
4. Remove the lock nut from the
Flapper Bar. Slide the Flapper Bar
off of the Pivot Pin. NOTE: DO
NOT remove either Pivot Pin from
the case. They are press-fit into
the case and not meant to be
removed. Do not remove the
Sensitivity Fulcrum or the thumb
screw.
5. Remove the lock nut from the
torque bar. Slide the torque bar
off of the shaft.
6. While holding the evel Adjusting
Bar still, loosen the two cap
screws until the evel Adjusting
Bar is free on the shaft. NOTE: It is
not necessary to remove or adjust
t e adjusting screw on t e Level
Adjusting Bar unless converting
t e case mounting. Slide t e Level
Adjusting Bar from t e s aft. Slide
t e spacer from t e s aft.
7. Remove the two cap screws
holding the case to the body.
Remove the case from the body.
2.3 L
EVEL
C
ONTROLLER
R
EA EMBLY
1. Mount the case to the body with
two cap screws. Tighten the
screws to 6 ft.-lbs.
2. Slide the spacer on the shaft.
3. If the level adjusting screw has
been removed or adjusted during
disassembly, position the screw
so that there is an equal amount of
thread showing above and below
O
PERATING AND
M
AINTENANCE
M
ANUAL
Series 10 01, 1001A, 10 01X L Level Control
Page 7 of 12
Level Adjusting Bar
Balance Spring
Left hand mount Right hand mount
Reverse acting controller
Figure 9 — How to make level adjustments
Flapper
Bar
Snap
Riing
Pilot Pilot
Adjusting Knob
Sensitivity
Fulcrum
Pivot Pin
Thumb Screw
Torque Bar

P. . Box 40525 · Houston, Texas USA 77240-0525
Tel: 713·466·3552 · Fax: 713·896·7386
www.norriseal.com 1001-0113O — ©2013, January 2013
the evel Adjusting Bar. The cap
on the level adjusting screw will
be pointing AWAY from the two
cap screws on the shaft end of the
evel Adjusting Bar.
4. Slide the evel Adjusting Bar onto
the shaft against the spacer with
the evel Adjusting Screw OPPO-
SITE the controller body. Snug,
but do not tighten, the cap screws
that secure the bar to the shaft.
5. Temporarily slide the Torque Bar
onto the shaft. Position the evel
Adjusting Bar so that the Torque
Bar is parallel with the displacer
arm when the round tip of the
level adjusting screw is touching
the Torque Bar.
6. Remove the Torque Bar and
tighten the cap screws that secure
the evel Adjusting Bar to the
shaft, starting with the screw near-
est the slotted end of the evel
Adjusting Bar, taking care not to
overtighten.
7. Slide the Torque Bar back onto the
shaft with the counter-sunk hole
for the spring retainer facing
down. (For left hand mount, the
hole is on the left side. For the
right hand hole, the hole is on the
right side.) Secure the Torque Bar
with the lock nut leaving 1⁄16-in.
clearance between the nut and the
Torque Bar. NOTE: DO NOT
tighten this nut; the Torque Arm
must move freely.
8. Slide the Flapper Bar onto the
Pivot Pin. If converting the case
mounting, remove the thumb
screw from the Sensitivity Fulcrum
and screw it into the opposite side
of the Fulcrum. Try to keep the
Fulcrum positioned in the same
place on the Flapper Bar. Use the
left Pivot Pin for left hand mount
direct acting or right hand mount
reverse acting. Use the right Pivot
Pin for right hand mount direct
acting or left hand mount reverse
acting. Secure the Flapper Bar
with the lock nut. NOTE: DO NOT
tig ten t is nut; t e Flapper Bar
must move freely.
9. Install the stud bolt and lower
spring retainer in the lower pilot
case. The bolt stud will be on the
left for left hand mount and on the
right for right hand mount.
10. Install the spring and upper
spring retainer, centering the
retainer pin with the hole in the
Torque Bar.
2.4 P
ILOT
R
EMOVAL
/R
EPLACEMENT
WA R N I N G
Before attempting any repairs, isolate t e
controller from t e system and make sure
t at all pressure is released from t e
controller body. S ut off and vent supply
and output (signal air) lines to t e con-
troller. On electric pilots, disconnect all
power to t e controller.W A R N I N
C A U T I O N
Pneumatic and Electric Pilot cases are
NOT interc angeable. Do not attempt to
replace a Pneumatic Pilot wit an Electric
Pilot or vice versa.
A. Pneumatic Pilots
1. Remove the supply and output
lines from the rear of the
controller.
2. For the 1001 controller, the pilot
is held in place by two cap screws
mounted through the top of the
case. Remove these cap screws
and remove the pilot from the
case.
3. For the 1001A and 1001X con-
trollers, the pilot is held in place
by four cap screws in the Pilot
Clamp. Remove these four cap
screws and remove the pilot from
the case.
4. If necessary, rebuild the pilot
following the instructions pro-
vided in the Pilot Re-build Kit
(PRK). Alternately the pilot can be
totally replaced. Pilot action may
be converted from snap to throttle
or vice versa by using a Pilot
Conversion Kit (PCK). Use only
genuine Norriseal parts kits or
pilots.
5. Re-install the pilot by reversing
instructions 1 through 3 above.
While the Pilot Gasket may not
need replacing on the 1001A and
1001X controllers, replacement
is recommended.
B. Electric Pilots —
Explosion Proof
1. DISCONNECT THE POWER
SUPPLY CIRCUIT BEFORE
CONTINUING.
2. Disconnect the wire leads.
Remove the screws holding the
basic switch in the case and then
the basic switch.
3. Place the replacement switch in
the insulator, insert the screws,
and place the assembly in the
case.
4. Tighten the screws and connect
the lead-in wires.
5. Be certain the small compression
spring is returned to its position
between the top of the basic
switch and the internal lever (or
above the internal lever in the case
of the CCW actuated switches).
O
PERATING AND
M
AINTENANCE
M
ANUAL
Series 10 01, 1001A, 10 01X L Level Control
Page 8 of 12

P. . Box 40525 · Houston, Texas USA 77240-0525
Tel: 713·466·3552 · Fax: 713·896·7386
www.norriseal.com
1001-0113O — ©2013, January 2013
C. Electric Pilots —
Hermetically ealed
1. DISCONNECT THE POWER
SUPPLY CIRCUIT BEFORE
CONTINUING.
2. Disconnect the wire leads.
Remove the conduit coupling on
the top of the case, then the
switch nut, washer and O-ring.
Remove the switch. oosen the
four screws retaining the switch
adapter and remove the switch
adapter.
3. Place the replacement switch in
the switch adapter, tighten the
screws, and place the assembly
in the case.
4. Replace the O-ring, washer and
switch nut. Tighten the switch nut,
replace and tighten the conduit
coupling, and connect the lead-in
wires.
2.5 L
EVEL
C
ONTROLLER
C
A E
M
OUNTING
C
ONVER ION
1. Completely disassemble the con-
troller following the disassembly
instructions in Paragraph 2.2.
2. Reassemble the controller follow-
ing the instructions in Paragraph
2.3. The evel Adjusting Screw
will be placed at a 90° angle to that
in the original configuration. The
thumb screw in the Fulcrum will
be screwed into the opposite side
of the Fulcrum. The evel
Adjusting Bar, evel Adjusting
Screw, Fulcrum, Torque Bar,
Flapper Bar, Balance Spring and
stud bolt will all be on opposite
sides of the case from the original
configuration.
2.6 L
EVEL
C
ONTROLLER
P
ILOT
A
CTION
C
ONVER ION
1. Relax all tension on the Balance
Spring. 2. Remove the lock nut
from the Flapper Bar. Slide the
Flapper Bar off of the Pivot Pin.
3. Remove the thumb screw from
the Sensitivity Fulcrum and
replace it in the opposite hole on
the Fulcrum from which it was
removed.
4. Replace the Flapper Bar on the
Pivot Pin on the opposite side of
the case, with the thumb screw on
the Sensitivity Fulcrum pointing
out.
5. Secure the Flapper Bar with the
lock nut. NOTE: DO NOT tighten
this nut; the Flapper Bar must
move freely.
6. Adjust the tension on the Balance
Spring.
2.7 L
EVEL
C
ONTROLLER
B
ODY
D
I A EMBLY
1. Remove the body from the con-
troller assembly by following the
controller disassembly instruc-
tions in Paragraph 2.2.
2. Remove the two bearing blocks
(11⁄4-in. wrench) and the shaft.
Remove and discard the O-rings
in the body, on the shaft, and in
the bearing blocks.
2.8 L
EVEL
C
ONTROLLER
B
ODY
R
EA EMBLY
1. Using new O-rings, install the
large O-ring over the threads of
the bearing block. Install the new
Teflon backup rings in each bear-
ing block, pressing them into
place with a 5⁄16-in. diameter rod.
Install the new O-rings in each
bearing block, pressing them into
place with a 5⁄16-in. diameter rod.
NOTE: A lig t oil applied to t e
O-rings will assist in t e assem-
bly procedure.
Figure 10 — End-on cutaway view of
controller body. As shown, the case
would mount to the left of the body
C A U T I O N
If t e bearing blocks are removed from
t e body for any reason, t e backup rings
and O-rings must be re-packed (pressed
into place). It is recommended t at new
backup rings and new O-rings be used.
2. Replace the outboard bearing
block (with the “hubcap”) on the
side of the body AWAY from the
case mounting bolt holes.
3. Insert the shaft into the body and
firmly seat in the outboard bear-
ing.
4. Replace the remaining bearing
block on the body and tighten.
5. Reattach the body to the case per
Paragraph 2.3, step 1.
3.0 R
EPAIR
K
IT
Norriseal provides three repair kits
for use in controller maintenance:
a evel Seals Kit ( SK), a Pilot Repair
Kit (PRK), and a Pilot Conversion Kit
(PCK).
O
PERATING AND
M
AINTENANCE
M
ANUAL
Series 10 01, 1001A, 10 01X L Level Control
Page 9 of 12

P. . Box 40525 · Houston, Texas USA 77240-0525
Tel: 713·466·3552 · Fax: 713·896·7386
www.norriseal.com 1001-0113O — ©2013, January 2013
O
PERATING AND
M
AINTENANCE
M
ANUAL
Series 10 01, 1001A, 10 01X L Level Control
Page 10 of 12
CODE CIRCUITRY ELECTRICAL RATING
“E” EXQ
or
“O” OP-Q
Single Pole Double Throw (SPDT)
U and CSA isted:
15 amps, 125, 250 or 450 VAC
0.50 amp 125 VDC
0.25 amp 250 VDC
“D” EXD-Q
or
“F” OPD-Q
Double Pole Double Throw (DPDT)
U and CSA isted:
10 amps, 125 or 250 VAC
0.30 amp 125 VDC
0.15 amp 250 VDC
T A B L E 2 — W I R I N G D I A G R A M S
STANDARD SWITCH
Green – Ground
Blue – N.O. 1
Black – Com 1 Red – N.C. 1
Blue – N.O. 2
Black – Com 2
Red – N.C. 2
CODE CIRCUITRY ELECTRICAL RATING
“K” Hermetic
030
Single Pole Double Throw (SPDT)
U , CSA and FM isted:
11 amps, 125/250 VAC
5 amps Res, 25 VDC
0.50 amps, 125 VDC
“D” EXD-Q
or
“F” OPD-Q
Double Pole Double Throw (DPDT)
U , CSA and FM isted:
11 amps, 125/250 VAC
5 amps Res, 28 VDC
0.50 amps 125 VDC
HERMETICALLY SEALED SWITCH
Green – Ground
Blue – N.O. 1
Black – Com 1 Red – N.C. 1
Purple – N.O. 2
Yellow – Com 2 Black – N.C. 2
Red – N.C.
Blue – N.O.
Green – Ground

P. . Box 40525 · Houston, Texas USA 77240-0525
Tel: 713·466·3552 · Fax: 713·896·7386
www.norriseal.com
1001-0113O — ©2013, January 2013
O
PERATING AND
M
AINTENANCE
M
ANUAL
Series 10 01, 1001A, 10 01X L Level Control
Page 11 of 12
Pilot output pressure gauge indicates output
pressure signal when fluid level is below
displacer on a direct acting controller OR when
fluid level is above displacer on a reverse acting
controller.
1. Balance Spring is too compressed and puts
too much pressure on the Torque Bar.
2. The displacer arm is set too high or the dis-
placer is hitting something inside the vessel.
1. Back off the spring retainer until the output
pressure signal goes off. Re-check when the
fluid level rises (direct acting) or falls (reverse
acting).
2. Check the displacer arm by moving the
leveling adjusting bar up and down. If the
adjusting bar will move in only one direction,
this indicates the displacer arm is riding
at either the top or bottom of the vessel
connection. If it moves too freely, the
displacer has become disconnected from the
displacer arm. Re-center the displacer arm in
the vessel connection.
Pilot output pressure gauge indicates no output
pressure signal when fluid level is above
displacer on a direct acting controller OR when
fluid level is below displacer on a reverse acting
controller.
1. Balance Spring is insufficiently compressed
and doesn’t put enough pressure on the
Torque Bar.
2. The displacer arm is set too low or the
displacer is hitting something inside the
vessel.
1. Compress the spring retainer until an out-
put pressure signal is indicated on the out-
put pressure gauge. Re-check when the fluid
level falls (direct acting) or rises (reverse
acting).
2. Check the displacer arm by moving the lev-
eling adjusting bar up and down. If the adjust-
ing bar will move in only one direction, this
indicates the displacer arm is riding at either
the top or bottom of the vessel connection.
If it moves too freely, the displacer has
become disconnected from the displacer
arm. Re-center the displacer arm in the
vessel connection.
Controller does not repeat at the same fluid level
after each dump and sometimes fails to either
dump or shut-off. (The torque bar does not
bounce back fast when depressed and appears
to be hard to move.)
Paraffin or debris has built up inside the level
control body. Remove controller from service and clean out
the body with a solvent.
n interface control, the vessel occasionally
loses all fluid or the vessel overflows, espe-
cially with temperature change. The displacer
arm is free and the displacer is not hitting inside
the vessel.
The displacer is not big enough to handle the
interface differential. Close specific gravity of
two fluids and a temperature change can cause
this problem.
Provide exact specific or API gravities of both
fluids to Norriseal Engineering for exact sizing
of the displacer that should be used..
A Pneumatic Pilot bleeds air continuously. Materia extraña debajo de la bola en un piloto de
Foreign matter under the ball on a snap control
pilot or under the peanut on a throttle control
pilot.
OR
The tru-arc ring on the snap pilot thrust pin may
have been dislocated.
Remove the pilot following the instructions in
Paragraph 2.4. Remove the two cap screws
from the bottom of the pilot. Clean the pilot
thoroughly. If a Snap Pilot, make sure the dimen-
sion between the tru-arc ring and the bottom of
the pin is 3⁄4 in. If not, gently tap the tru-arc
ring into the proper location. Reassemble the
pilot.
T A B L E 3 . T R O U B L E D I A G N O S I S
PROBLEM SYMPTOM POSSIBLE CAUSE CORRECTIVE ACTION

P. . Box 40525 · Houston, Texas USA 77240-0525
Tel: 713·466·3552 · Fax: 713·896·7386
www.norriseal.com 10 01-0113O
O
PERATING AND
M
AINTENANCE
M
ANUAL
Series 10 01, 1001A, 10 01X L Level Control
Page 12 of 12
H E A D Q U A R T E R S, M A N U F A C T U R I N G P L A N T A N D S A L E S
P.O. Box 40525 • Houston, Texas USA 77240-0525
11122 West ittle York • Houston, Texas USA 77041-5016
Tel: 713·466·3552 • Fax: 713·896·7386
www.norriseal.com
Due to t e continuous improvement at Norriseal,
specifications and/or prices are subject to c ange
wit out notice or obligation.
™Envirosave and Norriseal are trademarks of Dover Corporation.
.
.
.
A
B
S
Q
u
a
l
i
t
y
E
v
a
l
u
a
t
i
o
n
s
,
I
n
c
.
M
a
n
a
g
e
m
e
n
t
S
y
s
t
e
m
C
e
r
t
i
f
i
c
a
t
i
o
n
©2013 Dover Corporation/Norriseal and its affiliates. This manual, including all text and
images, is a copyrighted work of Dover Corporation/Norriseal and its affiliates. It may not
be, in whole or in part, photocopied, scanned, or otherwise reproduced, revised, or
publicly displayed, without prior written permission from Norriseal. This manual is for use
only with the new Norriseal valves and/or controllers listed in the manual. It may not be
distributed with, and is not for use with, any remanufactured products.
Due to the continuous improvement program at Norriseal, specifications and/or prices
are subject to change without notice or obligation.
All trademarks contained herein are the property of their respective owners.
This manual suits for next models
2
Table of contents
Other Dover Control System manuals
Popular Control System manuals by other brands
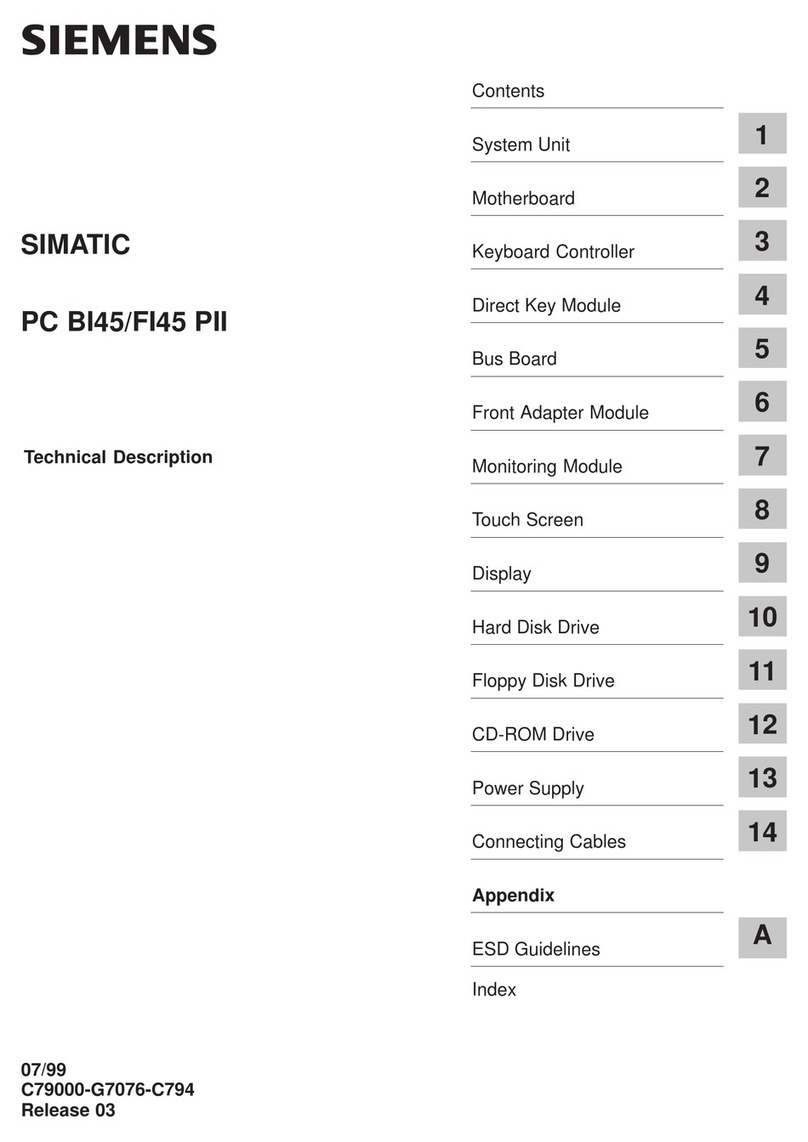
Siemens
Siemens SIMATIC PC BI45 Technical description
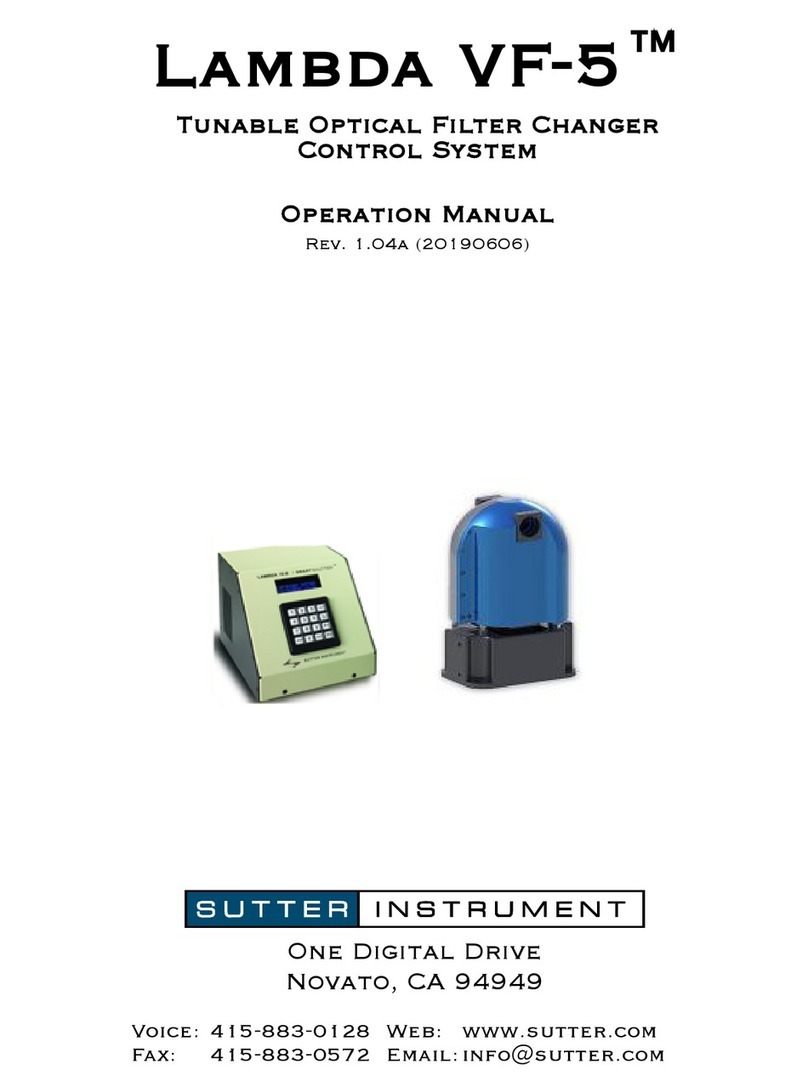
Sutter
Sutter Lambda VF-5 Operation manual
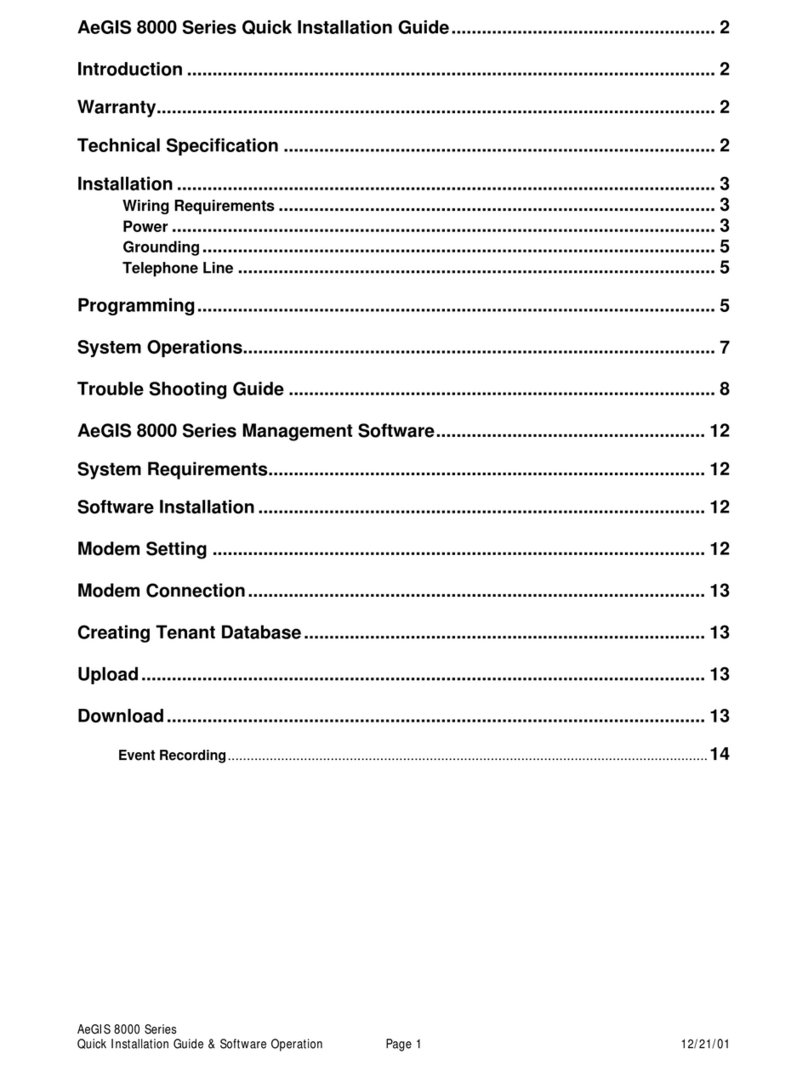
PACH & COMPANY
PACH & COMPANY AeGIS 8000 Series Quick installation guide
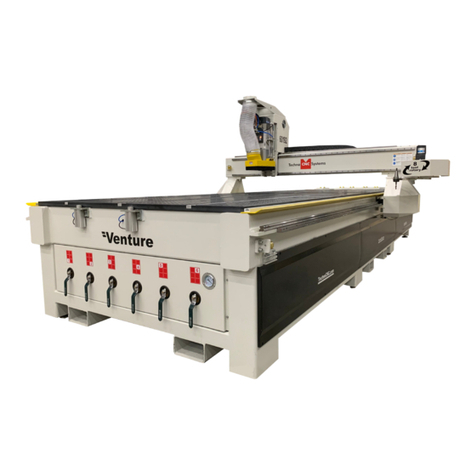
Techno CNC Systems
Techno CNC Systems Venture Series user manual

Dryer Master
Dryer Master DM510 Commissioning Guide
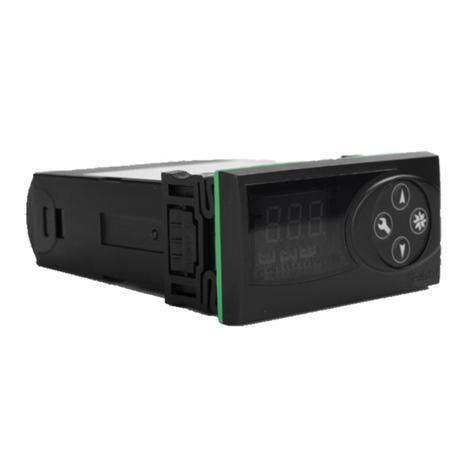
Elstat
Elstat ems25 Series product manual