Dover Petro Vend PV100 User manual

Petro Vend PV100® Installation, Operation and
Maintenance
Part Number: M1900
Revision: 12
PV100®

IMPORTANT: Before you use this manual, make sure you have the most recent revision.
Look at the revision of this document to make sure it agrees with the most current revision
found in the FMS Technical Library. Download the latest revision if necessary.
All references to other manuals and instructions in this manual can be found in the FMS
Technical Library. Make sure you have the most recent revision.
READ CAREFULLY: OPW Fuel Management Systems and Dover Fueling Solutions cannot
be held responsible for installations, configurations or use of its products that does not comply
with the most recent documentation available.
NOTE: It will be necessary to have Single Sign-On (SSO) credentials to get access to
manuals, instructions, software updates and other important assets. Speak with your FMS
sales representative or contact FMS Customer Service at 1-888-679-3835 (1-888-OPW-
FUEL) for information. Once you have been approved for SSO credentials go to the FMS
Technical Library to find the most recent revisions of all manuals and instructions.
OPW Fuel Management Systems is a part of Dover Fueling Solutions.
Copyright Information
© 2023 Dover Fueling Solutions. All rights reserved. DOVER, the DOVER D Design, DOVER FUELING
SOLUTIONS, and other trademarks referenced herein are trademarks of Delaware Capital Formation.
Inc./Dover Corporation, Dover Fueling Solutions UK Ltd. and their affiliated entities.
Contact OPW Fuel Management Systems
200A Parker Drive; Suite 400 ● Austin, TX 78728
Visit us at https://www.doverfuelingsolutions.com/.
Sales Support: (888) 679-3835 (7:30 a.m. to 4:00 p.m., US CST) • Email orders to:
Call 1-877-OPW-TECH (877-679-8324) Monday through Friday, 7 a.m. to 6 p.m., US CST
M1900_r12 PV100® Installation, Operation and Maintenance | Dover Fueling Solutions 2

M1900_r12 PV100® Installation, Operation and Maintenance | Dover Fueling Solutions 3

Table of Contents
Section 1 Precautions 7
1.1 USB Flash Drives 7
1.2 Safety Warnings 9
1.3 Information Panels 9
1.4 Hazardous Areas 11
1.4.1 NFPA/NEC – Class I, Div. 1 & Div. 2 11
1.4.2 Installation Requirement 12
1.5 FCC Compliance 15
Section 2 Introduction 16
2.1 Terminology 16
2.2 Versioning 16
2.3 System Technical Specifications 17
2.3.1 Fuel Control System 17
2.4 Pump Control 18
2.4.1 Mechanical Pump Control 18
Section 3 Pre-Installation Information 19
3.1 Conduit/Wiring Requirements 19
3.1.1 Conduit Sealing 19
3.1.2 Pedestal Conduits 20
3.1.3 Grounding 20
3.1.4 Power Requirements 21
3.1.5 Pulser Wire 21
Section 4 System Installation 22
4.0.1 Typical Installation Overview 22
Section 5 Mechanical PCM Pump Control 25
M1900_r12 PV100® Installation, Operation and Maintenance | Dover Fueling Solutions 4

5.1 Power Conduit Installation 25
5.2 PCM Conduit Installation 26
5.2.1 Pump Control/Pulser Conduit 26
5.2.2 Pump Pulser Conduit 26
5.3 System Power Wiring 26
5.4 PCM Pump Dispenser Wiring 28
5.4.1 Pump/Dispenser Wiring 28
5.4.2 Pump/Dispenser Pulser Wiring 30
5.5 PCM Startup/Configuration 30
5.5.1 Configuration (DIP Switches) 30
5.5.2 PCM Testing 32
Section 6 Complete the Installation 34
Section 7 System Configuration 35
7.1 Terminal Setup/Test Menu 35
7.1.1 Display Menu 36
7.1.2 Keypad Menu 36
7.1.3 Reader Menu 36
7.1.4 Tones Menu 37
7.1.5 System Network Number Menu 37
7.1.6 Petro-Net™ Setup Menu 38
7.1.7 Miscellaneous Menu 38
7.1.8 Pump Control Menu 39
7.1.9 Software Updates 39
7.2 Management Menu 40
7.2.1 Site Management 41
7.3 Pump Management 44
M1900_r12 PV100® Installation, Operation and Maintenance | Dover Fueling Solutions 5

7.4 Proprietary Card File (PCF) Management 45
7.4.1 Clearing Totals 47
7.4.2 Reporting 47
7.5 Dual Card Security Feature 52
Section 8 System Maintenance 58
Appendix A - PV100® Primary Board 59
Appendix B - Termination Codes 60
Appendix C - Menu of Display Screens 62
Appendix D - Replacement Parts 66
Appendix E - Pedestal Dimensions 69
Warranty 71
M1900_r12 PV100® Installation, Operation and Maintenance | Dover Fueling Solutions 6

Section 1 Precautions
1.1 USB Flash Drives
There are two (2) internal USB ports on the PV100 Main Board.
The J7 USB port (top) is used to connect the Main Board to the Door Port with the installed cable.
The J9 USB port (bottom) is for the provided metal industrial-grade USB key that is used to store data for
Totals and Transactions.
NOTICE: Use the metal industrial-grade USB Flash Drive that was provided with your unit
to store Totals and Transactions. Use this key only in the PV100 J9 USB port to prevent
loss of data.
To prevent data loss DO NOT use the plastic Manuals USB key (identified by the OPW
"diamond" logo) in the USB ports of the PV100. This key must only be used in a PC.
M1900_r12 PV100® Installation, Operation and Maintenance | Dover Fueling Solutions 7

IMPORTANT: The sub-sections that follow contain important safety and compliance
information related to the installation and operation of this unit. Read these instructions
carefully before you continue with the installation.
M1900_r12 PV100® Installation, Operation and Maintenance | Dover Fueling Solutions 8

1.2 Safety Warnings
This manual contains many important Safety Alerts. There can be a risk of injury or damage to property if you
do not obey these alerts. The panels below show the types of safety warnings that can be seen and how
each is specified.
DANGER: Indicates an immediately hazardous condition that, if not prevented, will
result in death or serious injury.
WARNING: Indicates a possibly hazardous condition that, if not prevented, could
result in death or serious injury.
CAUTION: Indicates a possibly hazardous situation that, if not prevented, could
result in minor or moderate injury.
NOTICE: Indicates important information not related to hazards. A condition that, if not
prevented, can result in property damage.
SAFETY INSTRUCTIONS: Indicates instructions and procedures related to safety or
gives the location of safety equipment.
1.3 Information Panels
NOTE: This panel gives more information about an instruction or procedure.
M1900_r12 PV100® Installation, Operation and Maintenance | Dover Fueling Solutions 9

IMPORTANT: This panel contains special information that is important and must be read and
obeyed.
REMINDER: This panel shows information that has been given before in the manual that is
important to show again.
TIP: A step or procedure that is recommended to make another step or procedure easier.
INFORMATION: This panel shows references to more information in other sources.
READ CAREFULLY: This panel points to information that must be fully read and understood
before doing the procedure(s) that comes after.
M1900_r12 PV100® Installation, Operation and Maintenance | Dover Fueling Solutions 10

1.4 Hazardous Areas
A fuel dispenser is a hazardous area as specified in the National Electrical Code. The installation must agree
with the codes that follow:
lNational Electrical Code (NFPA No. 70)
lMotor Fuel Dispensing Facilities and Repair Garages Code (NFPA No. 30A)
1.4.1 NFPA/NEC – Class I, Div. 1 & Div. 2
The Class I, Division 1 and Class I, Division 2 hazardous areas are specified below:
Class I locations. Class I locations: Where flammable gases or vapors are or can be in the air in
quantities sufficient to cause explosive or ignitable mixtures. Class I locations include:
lClass I, Division 1. A Class I, Division 1 location is a location where:
nThere can be concentrations of flammable vapors during normal operation.
nThere can be concentrations of flammable vapors during repair or maintenance
operations or when the leakage of liquid fuel can occur.
nA release of concentrations of flammable vapors can occur as a result of
equipment failure, incorrect operation or unsatisfactory procedures that could also
cause a failure of electrical equipment.
lClass I, Division 2. A Class I, Division 2 location is a location where:
nAn accidental failure or incorrect operation of vapor containment system equipment
or containers that can release hazardous vapors from flammable liquids or gases.
nA failure or incorrect operation of positive mechanical ventilation precautions result
in the release of hazardous concentrations of flammable gases or vapors.
nConcentrations of flammable gases or vapors can occasionally flow from a
containment or ventilation system to an adjacent Class I, Division 1 location. This
flow of gases or vapors must be prevented by sufficient positive-pressure
ventilation from a source of clean air. Sufficient precautions to prevent ventilation
failure must be installed.
DANGER: To prevent the possibility of explosion or fire, do not use electrical
or battery operated power tools in or near the Hazardous Area! Only use
pneumatic or hand tools.
M1900_r12 PV100® Installation, Operation and Maintenance | Dover Fueling Solutions 11

WARNING: To prevent possible fire or explosion, do not mount your system
site controller or any other electrical part of the system, including printers and
modems, within or above the defined "hazardous" areas.
IMPORTANT: It is the installer's responsibility to know and obey all local codes.
OPW Fuel Management System’s fuel control systems are listed for use in a non-classified area. All of the
equipment must be installed outside of the hazardous areas.
NOTE: Local codes can dictate specific installation requirements. Installation is subject to
approval by the local authority that has jurisdiction at the site.
1.4.2 Installation Requirement
OPW-FMS Terminals are designed to be installed above the hazardous area when using the terminal’s
associated pedestal.
The pedestal can be mounted in the hazardous area but a seal-off must be the first fitting for all conduits that
go into the area.
IMPORTANT: All unused knockout holes that have been removed must be sealed.
M1900_r12 PV100® Installation, Operation and Maintenance | Dover Fueling Solutions 12

Dispenser Installations
WARNING: Knockouts and installation hardware are provided for all
cabinetry. Do NOT drill holes in the enclosures. This would violate the safety
listing of the system.
CAUTION: Be sure to wear all required personal protective
equipment (PPE). This includes safety glasses, hardhat, safety
shoes and reflective vest.
Barricade the work area before installation.
Be sure to obey all applicable Lockout/Tagout (LOTO)
procedures before installation.
M1900_r12 PV100® Installation, Operation and Maintenance | Dover Fueling Solutions 13

IMPORTANT: It is recommended to do a check of the electrical system with a multimeter to
make sure all connections are de-energized before you proceed with the installation.
M1900_r12 PV100® Installation, Operation and Maintenance | Dover Fueling Solutions 14

1.5 FCC Compliance
This system complies with Part 15 of the Federal Communications Commission (FCC) Rules & Regulations.
Operation is applicable to these conditions:
lThis device must not cause harmful interference.
lThis device must accept interference received. This includes interference that can cause undesired
operation.
M1900_r12 PV100® Installation, Operation and Maintenance | Dover Fueling Solutions 15

Section 2 Introduction
This installation, operation and maintenance (IOM) manual details the installation startup, testing,
configuration, and general troubleshooting instructions for the PV100®Fuel Control System by OPW Fuel
Management Systems. The PV100®system is designed with an integrated fuel-site controller to control the
system operation.
The PV100®provides a turnkey system; the only configuration required for immediate use after installation is
configuration of the network number. Upon network number configuration, all purchased cards can be
manually configured with unique PINs on the first use of the card. After configuration of the card’s PIN, a
second swipe will provide access to purchased pumps within the system.
2.1 Terminology
The abbreviations below identify terms assigned to specific components and functions within the Fuel
Control System.
lFuel Island Terminal (FIT): Generic term used to describe the fuel management system.
lFuel Site Controller (FSC): Hardware/firmware used to control the fueling system.
lPump Control Module (PCM) Client: Hardware used for controlling mechanical pumps.
lDirect Pump Control (DPC): Hardware used for communicating to electronic pumps.
2.2 Versioning
The PV100®uses two (2) separate pieces of software. One controls the Fuel Island Terminal (FIT) and
Pump Control Module (PCM), and another controls the operation of the Fuel Site Controller (FSC).
The FIT/PCM piece supplies the user interface that controls the card reader (or HID proximity reader),
keyboard and display. The interface also controls and monitors pump activity.
The FIT/PCM software uses a version number that shows three pieces of information. The number has a
format of “X.XXx.”
lThe first digit identifies the number of the FIT/PCM product and stays the same for the life of the
product (the number for the PV100®is “2”).
lThe next two digits after the decimal point show a major revision to the product (the starting value is
“.01”).
lThe last piece is a lower case alpha character that increases when a minor modification to the
FIT/PCM occurs (the starting value is “a”).
The FSC piece of software controls the daily operations of the PV100®. This software uses a version number
that shows four pieces of information. The number has a format of “X.XX.XXx.”
lThe first digit identifies the number of the FSC software and stays the same for the life of the product
(the number for the PV100®FSC is “3”).
NOTE: The FSC uses battery backed-up RAM to save the vital configuration of the FSC (e.g.,
card file setup, pump configuration, transaction data, etc.) in the event of a power failure.
M1900_r12 PV100® Installation, Operation and Maintenance | Dover Fueling Solutions 16

lThe next two digits after the decimal point show that the card file configuration has been changed. An
increase in this value shows that:
nALL card file information such as PIN, Prompt and available pumps must be reconfigured.
nCard Pump Totals are lost.
lThe next two digits show when any other system configuration has changed. The pump configuration,
stored transaction data and all saved data will be lost when this software update occurs.
Reconfiguration of this information will be necessary.
lThe last piece is a lowercase alpha character that increases when a minor modification to the FSC
occurs (the starting value is “a”).
NOTE: If the card file number increases, the system configuration number can also change.
This will show that a full-system cold start will occur. A complete reconfiguration of the FSC
stored data will be necessary.
If only the system configuration number increases, a partial cold start of the FSC will occur. A
reconfiguration of pump and system control settings will be necessary.
2.3 System Technical Specifications
This section details the technical specifications (i.e., dimensions, operating temperature range, power and
wiring requirements) of the system and pump control.
2.3.1 Fuel Control System
PV100®Technical Specifications
Cabinet Dimensions (H x W x D): 27 cm x 36 cm x 25 cm (10.75” x 14.25” x 9.75”
Pedestal Dimensions (H x W x D): 122 cm x 36 cm x 20 cm ( 48” x 14” x 8”)
Power Requirements: 115/230 VAC, 50/60 Hz, 200 W Max
Operating Temperature Range -40°C – +50°C (-40°F – +122°F )
Keypad Numeric/Function: Standard
Magnetic Card Reader: Optional
Proximity Card Reader: Optional
Chipkey Reader: Optional
Graphics Display: Standard 15.2 cm (6") monochrome
Enclosure: Powder Coated Steel
Pedestal: Powder Coated Aluminum
Internal Fuel Site Controller: Standard
M1900_r12 PV100® Installation, Operation and Maintenance | Dover Fueling Solutions 17

PV100®Technical Specifications
Internal Pump Control: Standard Mechanical - 2 hoses
Optional - Mechanical or Electronic - 4 hoses
NOTE: Optional items may require additional cost
2.4 Pump Control
2.4.1 Mechanical Pump Control
Mechanical Pump Control is used when the dispensers connected to the system provide pulse inputs with
in-use detection of handle switch or voltage sense.
To support this type of operation, one (1) or two (2) stand-alone relay boards, referred to as the “Pump
Control Client Module” or “PCM Client” (OPW Part #: 20-4405), is mounted on the back wall of the PV100®
enclosure, providing control for up to two (2) hoses. A second "PCM Client" board can be added to control a
total of four (4) hoses.
Mechanical Pump Control Specifications (PCM)
Relay Contact Rating: 240-volts A; 20 A, 3.0 HP Max.
“In-Use” Detection: Voltage Sense 120-240 VAC or Handle Switch
Pulser Type: Single Channel
Pulser Input: Mechanical (contact); Electronic (5-12 VDC)
Pulser Divide Rate: Pulser Divide Rate:
Max. Pulse Speed: 6,000 Mechanical; 100,000 Electronic
M1900_r12 PV100® Installation, Operation and Maintenance | Dover Fueling Solutions 18

Section 3 Pre-Installation Information
The installation instructions in this manual are written for a typical installation. Due to the flexibility of the
system and the unique nature of every site, it is not possible to show every potential installation scenario.
Local codes may dictate specific installation requirements. Installation is subject to approval by jurisdictional
authorities at the site of installation. See Safety Precautions at the beginning of this manual.
Use your smartphone camera to scan the QR code below to view the instructional video, PV100 Installation
and Startup. If you are viewing this manual on a computer or tablet, simply click on the URL below.
YouTube video URL:
https://www.youtube.com/watch?v=uCakQ4IvGrg&list=PLZ3d7sJYbYsfUKqz3XkijVTEer6svI55k&index=2
3.1 Conduit/Wiring Requirements
IMPORTANT: All wiring and conduit runs must conform to the National Electric Code (NFPA
No. 70), Code for Motor Fuel Dispensing Facilities and Repair Garages (NFPA No. 30A) and
all national, state and local codes.
All wiring running to the system must be installed in threaded, rigid metal conduit and have the
required sealoffs. AC and DC power wires can share conduit, provided they meet the Petro-
Net™ wiring specified; otherwise AC and DC power wires must be installed in separate
conduits.
3.1.1 Conduit Sealing
Conduit entering the hazardous area must have a seal-off installed 18 inches (46 cm) above grade to prevent
liquid or fumes from entering the area.
When running shielded cable through a seal-off, strip the cable jacket back so about three (3) inches (7.6 cm)
of jacketed cable protrudes past each seal-off.
WARNING: Shielded cable is NOT vapor-tight! DO NOT damage the shield
wire! Stripped section must be in the sealed-off area.
M1900_r12 PV100® Installation, Operation and Maintenance | Dover Fueling Solutions 19

Conduit Sealing
3.1.2 Pedestal Conduits
All conduits in the PV100 pedestal should terminate at the conduit plate. A seal-off must be installed in these
conduit runs. Install ½-inch or ¾-inch rigid steel conduits as applicable.
IMPORTANT: Any unused knockout holes that have been removed must be sealed in order to
meet NEC code.
3.1.3 Grounding
The PV100 incorporates internal noise suppression circuitry. To ensure safety and proper operation of the
equipment, all devices of the OPW-FMS system must be grounded.
A ground wire (preferably Green) must be connected between the device’s ground terminal and the main
electrical service panel. One earth ground connection is required per OPW-FMS device.
CAUTION: Do not rely on the conduit to provide ground connections.
M1900_r12 PV100® Installation, Operation and Maintenance | Dover Fueling Solutions 20
This manual suits for next models
1
Table of contents
Other Dover Control System manuals
Popular Control System manuals by other brands

VPEB
VPEB Dinamo user manual
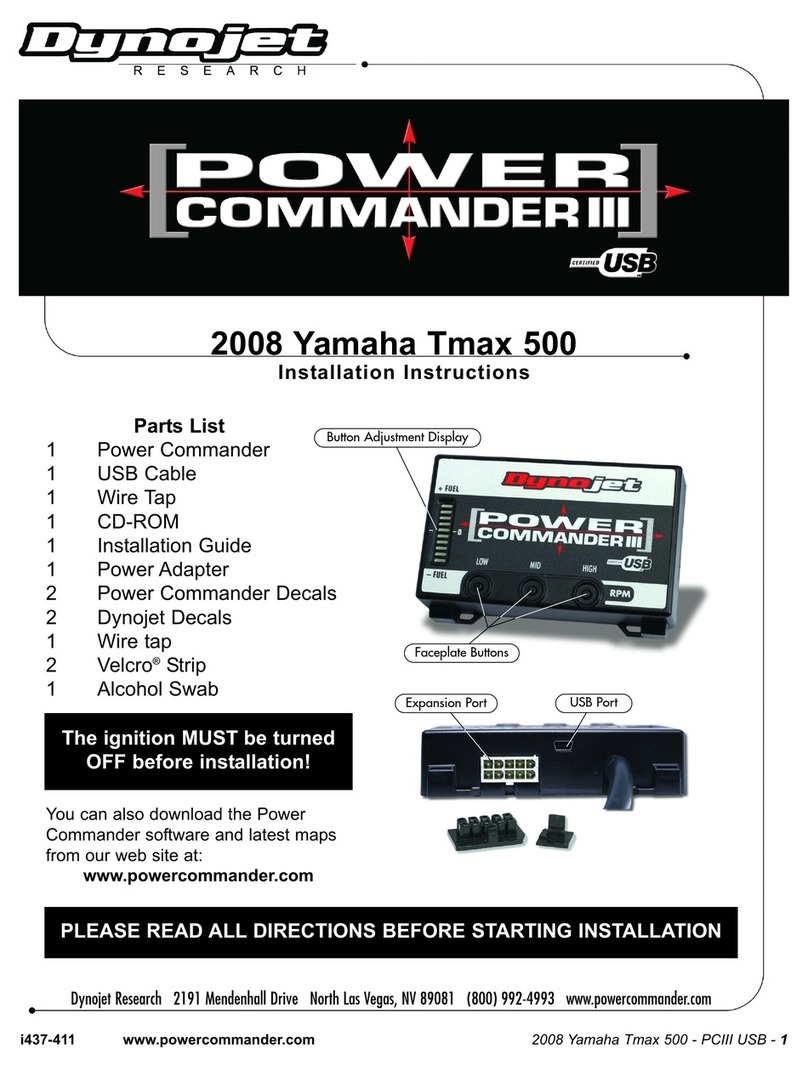
Dynojet
Dynojet POWER COMMANDER 3 Installation Instructions and Technical Information
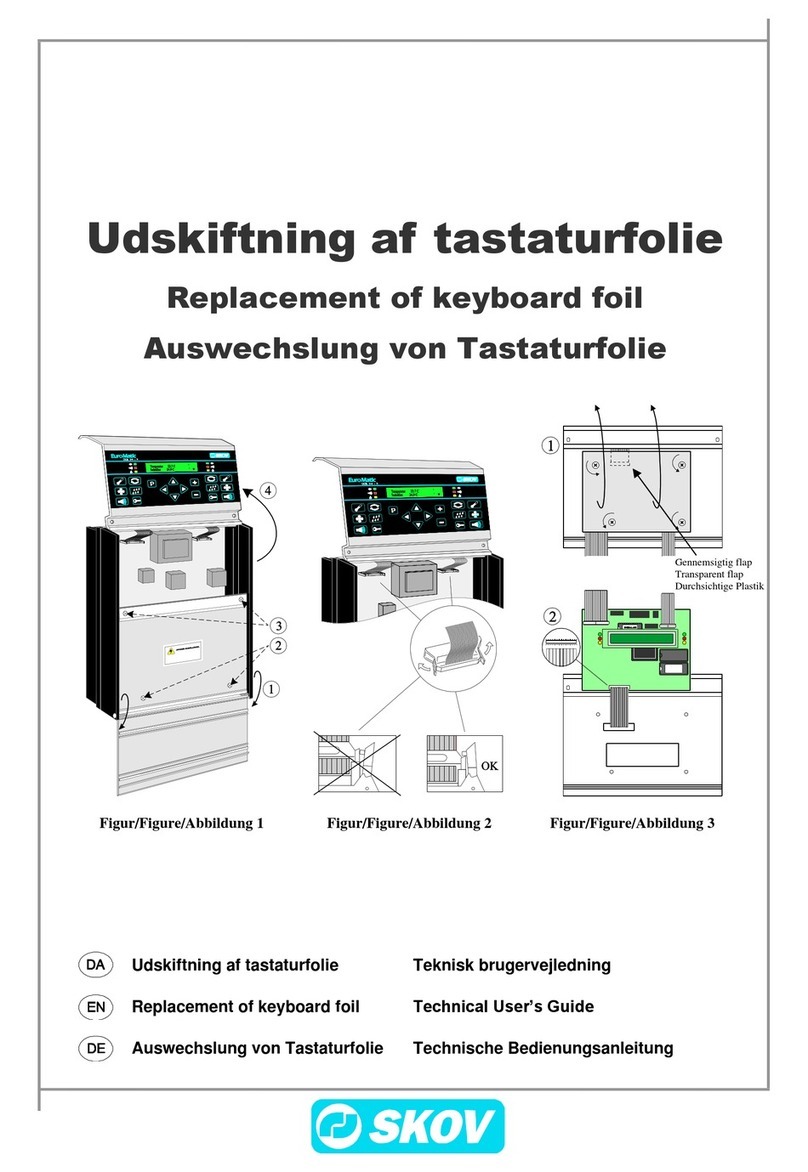
Skov
Skov DOL 34H Technical user guide
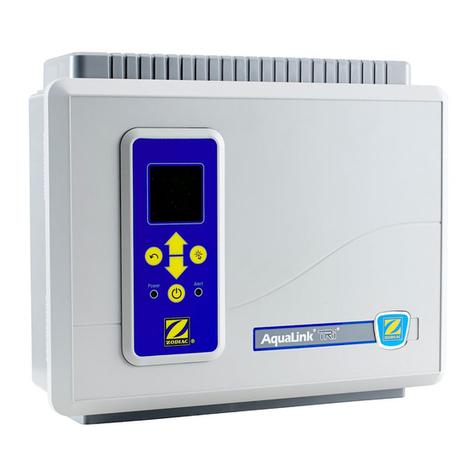
Zodiac
Zodiac AquaLink TRi Instructions for installation and use

Aybey Elektronik
Aybey Elektronik AE-SMART installation manual
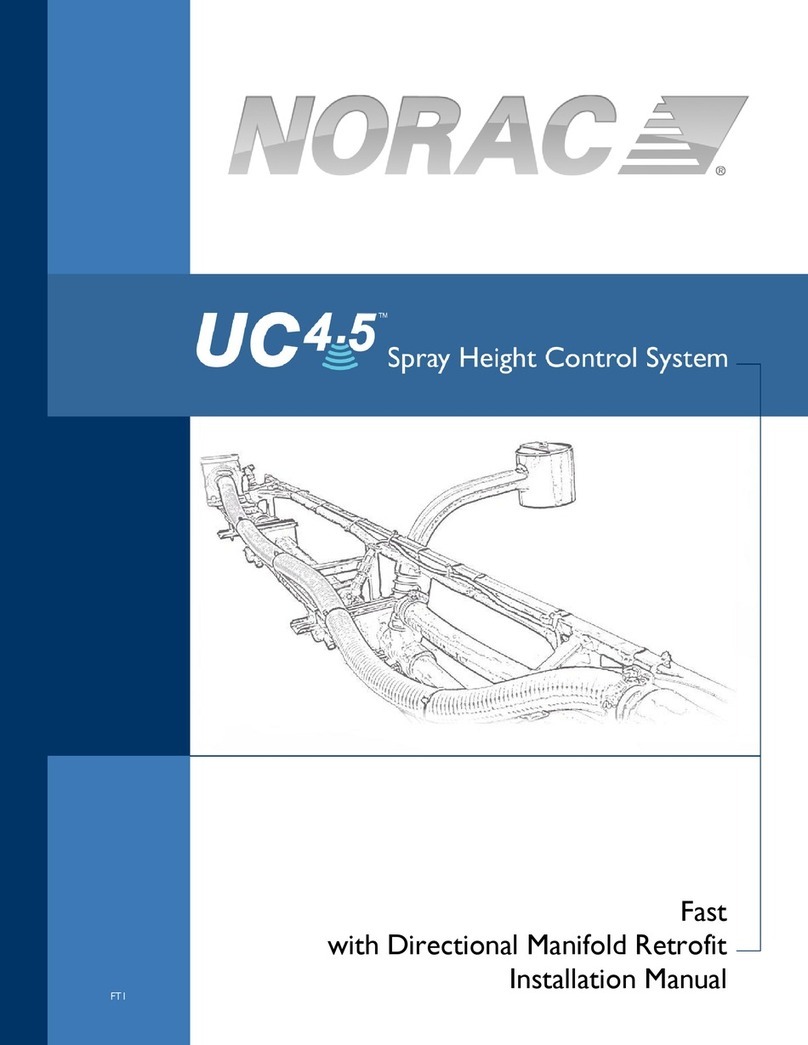
Norac
Norac UC4.5 installation manual