Dover Midland A-720 Series Instruction manual

Installation, Operation & Maintenance Manual
Part No.: A-720/A-721/A-721-B/A-724, Rev. 1.8
Issue Date: Jan 3, 2022
Supersedes: A-720/A-721/A-721-B/A-724, Rev. 1.7
Top-Transfer 2"Angle Valve
A-720, A-721 and A-724 Series
Installation, Operation
& Maintenance Manual
www.midland.com

Installation, Operation & Maintenance Manual
2Top-Transfer 2" Angle Valves A-720, A-721, A-721-B and A-724 Series
SECTION 1 | REGULATIONS AND SAFETY REQUIREMENTS...........................................................................................3
1.1 Regulations........................................................................................................................................................ 3
1.2 Safety Warnings and Precautions.................................................................................................................... 3
SECTION 2 | INTRODUCTION...........................................................................................................................................4
2.1 Component Identification and Parts Listings ................................................................................................. 4
SECTION 3 | VALVE INSTALLATION.................................................................................................................................8
3.1 Installation and Required Tools ...................................................................................................................... 8
SECTION 4 | OPERATING PROCEDURE..........................................................................................................................10
4.1 Opening the Valve ......................................................................................................................................... 10
SECTION 5 | VALVE QUALIFICATION ............................................................................................................................11
SECTION 6 | VALVE DISASSEMBLY ..............................................................................................................................15
SECTION 7 | VALVE REASSEMBLY AND TESTING PROCEDURES .................................................................................19
7.1 Cleaning........................................................................................................................................................... 19
7.2 Reassembly Procedure .................................................................................................................................... 19
7.3 Testing Procedure............................................................................................................................................ 25
7.4 Post-Test Procedures ....................................................................................................................................... 25
SECTION 8 | MAINTENANCE.........................................................................................................................................26
8.1 Prior to Maintenance Tasks Performed ........................................................................................................ 26
8.2 Leak Repair on a Mounted Valve .................................................................................................................. 26

3
Top-Transfer 2" Angle Valves A-720, A-721, A-721-B and A-724 Series
1 REGULATIONS AND SAFETY REQUIREMENTS
1.1 REGULATIONS
Midland angle valves are used in contact with a variety of products, many of which are hazardous materials. The acceptance
and transportation of products are regulated by the DOT and AAR in the U.S.A., and in Canada by CTC and Transport
Canada. Regulations of other governmental bodies must be complied with for stationary and mobile applications. All
personnel should be familiar with and follow these regulations. Nothing in these instructions is intended to conflict with
or supersede these regulations. The information in this document was gathered from knowledgeable sources. However,
Midland Manufacturing Corporation makes no representations or guarantees about its accuracy or completeness, and
assumes no liability for this information.
Specifications are subject to change without notice.
Midland valves are used in connection with a variety of products, many of which are hazardous materials and could
cause serious injury or damage if mishandled. This valve should only be installed, operated and maintained by qualified
personnel. Read all of these instructions carefully before proceeding.
Operation of the valve must conform to all applicable specifications from TC, AAR, DOT, CFR (Parts 173.31, 174.67, etc.)
and other governmental bodies, along with the operating instructions of your company.
1.2 SAFETY WARNINGS AND PRECAUTIONS
Please carefully read each of the following warnings and cautions prior to performing any work.
WARNING: Toxic Hazard. Always use extreme caution and proper equipment when involved with hazardous
materials. To avoid exposure to toxic or hazardous materials, make sure the tank car is empty and clean,
and that the work area is free of hazardous chemicals before removing or installing any valve.
• Wear protective clothing and equipment suitable for withstanding the materials to
which you may be exposed
• Position yourself on the upwind side of the valve when possible
• Work in a well-ventilated area
• Work with a partner who can help you in the event of an emergency
• Follow approved safety precautions for hazardous or toxic materials
• Obtain MSDS sheets for all the commodities used with the associated valve
CAUTION: Valve Leakage. Loose nuts and damaged gaskets may result in leaks at the valve-mounting joint.
CAUTION: Sealing Surface Damage. A damaged sealing surface on the valve flange may prevent
proper sealing on the tank-car mounting and result in leakage of the tank contents.
WARNING
CAUTION
CAUTION

Installation, Operation & Maintenance Manual
4Top-Transfer 2" Angle Valves A-720, A-721, A-721-B and A-724 Series
2 INTRODUCTION
Tank cars equipped with the Midland A-720, A-721-B and A-724 Series Top-Transfer Angle Valves offer long-term reliability
and ease of maintenance leading to more efficient operations.
Applications include:
• Liquefied Petroleum Gas (LPG) applications
• For the loading and unloading of pressure tank cars
2.1 COMPONENT IDENTIFICATION AND PARTS LISTINGS
ITEM QTY DESCRIPTION A-720 A-721 A-724
PART NO. MATERIAL PART NO. MATERIAL PART NO. MATERIAL
1 1 HANDWHEEL 720-1-AL ALUMINUM 720-1-AL ALUMINUM 720-1-AL ALUMINUM
2 1 STEM 720-2A-SS STAINLESS 720-2A-SS STAINLESS 720-2A-SS STAINLESS
3 1 GASKET RETAINER ASSY 720-301-CS STEEL 720-301-CS STEEL 720-301-SS STAINLESS
4 1 BODY 720-4-CS STEEL 721-4B-DI DUCTILE IRON 720-4-SS STAINLESS
5 1 SPRING, COIL 720-5-SS STAINLESS 720-5-SS STAINLESS 720-5-SS STAINLESS
7 1 OUTLET FLANGE 720-71-CS STEEL 720-71-CS STEEL 720-71-SS STAINLESS
8 1 PACKING SCREW W/ INSERT 720-8-CS STEEL 720-8-CS STEEL 720-8-N60 NITRONIC 60
9A 1 PACKING WASHER TOP 720-93-SS STAINLESS 720-93-SS STAINLESS 720-93-SS STAINLES
9B 1 SPACER 720-95-SS STAINLESS 720-95-SS STAINLESS 720-95-SS STAINLESS
10 1 WIPER 713-33-PK PEEK 713-33-PK PEEK 713-33-PK PEEK
11 4 PACKING 720-11-TF TEFLON™720-11-TF TEFLON™720-11-TF TEFLON™
12 1 STEM SEAL 720-12-BN* BUNA-N* 720-12-BN* BUNA-N* 720-12-BN* BUNA-N*
13 1 “O” RING OUTLET 720-131-BN* BUNA-N* 720-131-BN* BUNA-N* 720-131-BN* BUNA-N*
14A 1 HANDWHEEL NUT 10-15-SS STAINLESS 10-15-SS STAINLESS 10-15-SS STAINLESS
14B 1 WASHER 308-12-CS STEEL 308-12-CS STEEL 308-12-CS STEEL*
15A 4 BOLT 724-15-SS STAINLESS 724-15-SS STAINLESS 724-15-SS STAINLESS
15B 4 LOCKWASHER 724-152-SS STAINLESS 724-152-SS STAINLESS 724-152-SS STAINLESS
16 1 OUTLET PLUG & CHAIN* 720-16-CS STEEL, PLATED 720-16-CS STEEL, PLATED 720-16-SS STAINLESS
18A 1 STEM RETAINER 720-18-SS STAINLESS 720-18-SS STAINLESS 720-18-SS STAINLESS
18B 2 NUT 720-181-SS STAINLESS 720-181-SS STAINLESS 720-181-SS STAINLESS
21 1 PACKING LOCK NUT 720-21-CS-G STEEL 720-21-CS-G STEEL 720-21-CS-G STEEL
22 1 NAMEPLATE 720-22-SS STAINLESS 720-22-SS STAINLESS 720-22-SS STAINLESS
Table 2-1 A-720/A-721/A-724 Component Parts Listing
*Alternate materials available

5
Top-Transfer 2" Angle Valves A-720, A-721, A-721-B and A-724 Series
ITEM QTY DESCRIPTION A-721-B
PART NO. MATERIAL
1 1 HANDWHEEL 720-1-AL ALUMINUM
2 1 STEM 720-2A-SS STAINLESS
3 1 GASKET RETAINER ASSY 720-3-CS STEEL*
4 1 BODY 721-42B-DI DUCTILE IRON
5 1 SPRING, COIL 720-5-SS STAINLESS STEEL
6 1 RETAINER COVER 720-6-CS STEEL*
7 1 OUTLET FLANGE 720-71-CS STEEL
8 1 PACKING SCREW W/ INSERT 720-8-CS STEEL
9 1 PACKING WASHER TOP 720-93-SS STAINLESS STEEL
10 1 SEAT SEAL 720-10-TF TEFLON™*
11 4 PACKING 720-11-TF TEFLON™
12 1 STEM SEAL 720-12-BN BUNA-N
13 1 “O” RING OUTLET 721-13-GY GYLON 3510
14A 1 HANDWHEEL NUT 10-15-SS STAINLESS STEEL
14B 1 WASHER 308-12-CS STEEL
15A 4 BOLT 724-15-SS STAINLESS STEEL
15B 4 LOCKWASHER 724-152-SS STAINLESS STEEL
16 1 OUTLET PLUG & CHAIN* 720-16-CS STEEL, PLATED
18A 1 STEM RETAINER 720-18-SS STAINLESS STEEL
18B 2 NUT 720-181-SS STAINLESS STEEL
19 1 PIN 720-19-SS STAINLESS STEEL*
20 1 RETAINER NUT 720-20-CS STEEL*
21 1 PACKING LOCK NUT 720-21-CS-G STEEL
22 1 NAMEPLATE 721-22B-SS STAINLESS STEEL
23 1 SPACER 720-95-SS STAINLESS STEEL
24 1 WIPER 713-33-PK PEEK
Table 2-2 A-721-B Component Parts Listing
*Retainer assembly consisting of Items 3, 6, 10, 19, & 20 will be 720-301-CS.
2.1 COMPONENT IDENTIFICATION AND PARTS LISTINGS (CONT.)

Installation, Operation & Maintenance Manual
6Top-Transfer 2" Angle Valves A-720, A-721, A-721-B and A-724 Series
Figure 2-1 A-720/A-721/A-724 Valve Dimensions & Component Identifications

7
Top-Transfer 2" Angle Valves A-720, A-721, A-721-B and A-724 Series
Figure 2-2 A-721-B Valve Dimensions & Component Identifications

Installation, Operation & Maintenance Manual
8Top-Transfer 2" Angle Valves A-720, A-721, A-721-B and A-724 Series
3 VALVE INSTALLATION
Keep the new Angle Valve in its original shipping container. This will ensure that it remains clean and will protect the gasket face from
nicks and other damage.
Prior to installation, ensure that the valve remains clean, and the gasket-sealing surfaces are not damaged.
3.1 INSTALLATION AND REQUIRED TOOLS
NOTICE: Conform to all regulations and your company’s installation instructions.
It is not the intention of this pamphlet to conflict with or supersede these requirements.
CAUTION: Be sure the car is empty and clean, and that the work area is free of hazardous chemicals
that may have been in the car, before removing a valve or installing a new one.
3.1.1 Remove the old valve and then insert a soft rubber plug into the tank opening to prevent debris from
entering the tank during cleaning of the valve-mounting groove and studs on the man-way cover plate.
3.1.2 Wire-brush the stud threads of the cover plate until clean. Properly installed studs will extend 3/4" within the cover plate.
3.1.3 Remove the gasket in the groove of the cover plate. Avoid scratching the metal in the bottom of the groove.
Discard the used gasket.
3.1.4 Examine the sides of the groove to verify that there are no dents or burrs. Since the valve fits tightly in the groove,
any peening of the groove edges may make it difficult to properly fit the valve’s tongue into the groove.
3.1.5 Up to this point, the new valve should have been kept in its original shipping container and a
special plastic protector should have been positioned over the tongue on the bottom of the valve.
3.1.6 If the valve is reconditioned, or retested, inspect the tongue by running your fingernail around the edge of the tongue
to ensure it is free of nicks, gouges and burrs. The tolerance on the tongue is plus or minus 0.003"; therefore,
any irregularity in this surface will make it difficult to seat the valve on the cover plate groove.
3.1.7 Properly install the new gasket into the groove of the cover plate.
3.1.8 Start all four (4) nuts on the studs while the valve is still on the cover plate.
3.1.9 Gently lower the valve down onto the cover plate until you feel the tongue goes down into the groove on the cover plate.
NOTICE
CAUTION
SAE WRENCH COMPONENT(S)/DESCRIPTION
7/16" Socket STEM RETAINER (ITEM 18)
1-1/16" PACKING SCREW (ITEM 4)
3/4" SAE or 3/4" Crowfoot Wrench MOUNTING NUTS (NOT SUPPLIED)
OTHER TOOLS, SUPPLIES, AND EQUIPMENT:
Silicone Grease (or equivalent lubrication) TO GREASE APPROPRIATE SEALING SURFACES
Lint-Free Cloth TO CLEAN SEALING SURFACES
Emery Paper (400 grit, cut in 1" strips)
Wire Brush TO CLEAN DEBRIS AND SURFACES
Table 3-1 Required tools for valve installation

9
Top-Transfer 2" Angle Valves A-720, A-721, A-721-B and A-724 Series
3.1.10 Wrench-tighten the nuts a little bit at a time, going alternately in a crisscross pattern, from 1 to 3, then 2 to 4. Do not tighten
down too much on one side because this will shift the valve at an angle and may make it impossible to get a tight gasket seal.
3.1.11 Torque the nuts to a level prescribed by your engineering department. In absence of a recommended company practice,
on clean and lubricated threads, it should be safe to torque the mounting nuts to 150 to 200 ft-lb.
3.1.12 After the nuts have been tightened down on the cover plate, the valve should be “closed.” To seal the valve, it is only
necessary to torque the valve handwheel approximately 20 to 30 ft-lb. Under no circumstances should a “cheater” or handle
extension be used to close this valve, as over- tightening will damage the valve’s Teflon®seat.
3.1.13 Inspect the valve for leaks according to your company’s procedures for this testing. The primary areas to check are in the
side-port area, the packing gland area, the flange connection between the cover plate, and the valve and seat. In order to
check the seat for leaks on an installed valve on the tank car, pressure may be applied to the outlet flange with the valve
in the “closed” position. Look for any pressure decay. Keep in mind that some compensation would need to be made for
pressure changes as temperature changes. This is recommended in the event that there is no procedure in place from your
company to test the valve’s seat when installed on a tank car. When closing the valve, hand-tighten. If it does not seal,
remove the valve for repair per Maintenance Instructions in Section 8.0.
Side-Port Area
Mounting Flange Connection
Figure 3-1 Inspect Side-Port Area and Seat
Packing Gland Area
NOTICE
NOTICE: If the valve is painted, ensure that the gold-colored locknut is masked before painting.

Installation, Operation & Maintenance Manual
10 Top-Transfer 2" Angle Valves A-720, A-721, A-721-B and A-724 Series
4 OPERATING PROCEDURE
4.1 OPENING THE VALVE
NOTICE: Operation of the valve must conform with all applicable CTC, AAR, DOT specifications
(Parts 173.31, 174.67, etc.), other governmental bodies, and the operating instructions of your company.
NOTICE
4.1.1 Wrench-tighten the nuts a little bit at a time, going alternately in a crisscross pattern, from 1 to 3, then 2 to 4. Do not tighten
down too much on one side because this will shift the valve at an angle and may make it impossible to get a tight gasket seal.
CAUTION: Do not use an extension or cheater on the valve handle. If it does not move freely, report this to
the tank car supervisor. The tank may be pressurized, contain solidified product, or the valve may be jammed.
4.1.2 Examine the pipe plug. Be sure its threads are clean, free from corrosion, not worn or crossed. Also, examine the threads
on the side port to see that they are in good operating condition.
4.1.3 This valve has an adjustable packing gland. Routine maintenance consists of periodic inspection and adjustment of the packing
nut (item 8) to compensate for the stem seal wear. This may be done by loosening the gold locknut (item 21) and tighten the
packing screw to 65 ft-lb using a 1-1/16” wrench. More frequent observations are recommended under extreme operating
conditions. Unnecessary overtightening will cause excessive frictional drag on the valve stem. Then torque the locknut (Item 21)
to 65 ft-lb in order to keep the packing screw from unwinding during operations.
CAUTION
Plug
Figure 4-1 Plug and Packing Locknut
Packing Locknut

11
Top-Transfer 2" Angle Valves A-720, A-721, A-721-B and A-724 Series
5 VALVE QUALIFICATION
NOTICE: Whenever angle valves are retested, it is recommended that new O-rings be installed. The Teflon®seat seal
and packing should be replaced, if there is any question about their serviceability. All replacement parts must be
obtained from Midland Manufacturing Corp. No re-machining of any parts is permitted. By not observing these
prohibitions the purchaser assumes full responsibility and liability for the proper functioning of the valves.
NOTICE
5.1.1 HANDWHEEL. This part is designed to fail when the stem is over-torqued. If a spoke is cracked, or broken off,
the handwheel must be replaced.
5.1.2 STEM. Roll the stem on a flat and true surface. It will be apparent if the stem is bowed. If you attempt to straighten it,
do not grip or deflect it on the ground surface in the packing seal area, nor in the acme thread, where deformation of the
metal would make it difficult to move it freely. All nicks, burrs, pits, scratches, etc., must be eliminated, or discard the stem.
Inspect for cracks in the thread root area. If any are detected, discard the stem. Screw the stem through the acme thread
of the body with packing screw in place to make sure it moves freely without any binding.
Figure 5.1.1 Handwheel
Figure 5.1.2 Valve Stem

Installation, Operation & Maintenance Manual
12 Top-Transfer 2" Angle Valves A-720, A-721, A-721-B and A-724 Series
5.1.3 BODY. Inspect the part for corrosive degradation, particularly in the seat, threads, packing sealing and the side port areas.
Clean off these areas to be sure they are free of corrosion, contamination, pits, scratches, etc., that could form leak paths.
The threads are 1/2"-13 for the valve on the side flange. If any of the threads are stripped or corroded, discard the body.
5.1.4 RETAINER ASSEMBLY. If the Teflon® seat is deformed by the body insert to a depth of 1/16-inch, or if it has embedded
debris, discard it. Replace it with a new seat seal from the factory. This part is custom made for use on Midland valves only
and must be purchased from Midland.
5.1.5 OUTLET FLANGE. The surfaces where the O-ring fits, and the flat gasket surfaces must be free of nicks, scratches, and pits.
Similarly, the 2" or 3" NPT must be in good condition. It can be cleaned with the standard NPT hand tap. However, a thread
gage should be used to be sure the thread is not oversized. The standard hand-tight engagement is 0.436 inches for the
thread. The acceptable tolerance is plus or minus one thread. If this tolerance is exceeded, a new part must be obtained.
Figure 5.1.5 Outlet Flange
Figure 5.1.3 Valve Body
Figure 5.1.4 Gasket Retainer

13
Top-Transfer 2" Angle Valves A-720, A-721, A-721-B and A-724 Series
5.1.6 PACKING SCREW. The thread is 1¼"-12 on the valve. It must be clean and sharp without nicks, scratches,
pits, and other defects that would strip or gall the thread when screwed into the body.
5.1.7 BOTTOM SPACER WITH WIPER: The outer surfaces of the spacer surfaces must be free of nicks, scratches, and pits.
The internal wiper is clean without nicks and other defects. This part is custom made for use on Midland valves only
and must be purchased from Midland.
5.1.8 The remainder of the parts are O-rings, packing, gaskets, bolts, several types of nuts, lock washers, pins, etc.
These are inexpensive parts and to ensure that the right sizes, hardness, strengths, materials, and correctly
dimensioned parts are used, these replacement parts should be obtained from the factory.
Figure 5.1.6 Packing Screw
Figure 5.1.7 Bottom Spacer with Wiper

Installation, Operation & Maintenance Manual
14 Top-Transfer 2" Angle Valves A-720, A-721, A-721-B and A-724 Series
NOTICE
WARNING
NOTICE
5.1.9 Special Inspection Considerations
5.1.9.1 Previous procedures may not cover all conditions encountered in the field. Therefore, it is the responsibility of the repair agency
to obtain approval from Midland for inspection, evaluation, repair and maintenance procedures not covered herein.
5.1.9.2 Facilities performing recommended dye-penetration and magnetic-particle testing must carry out such testing according to a
qualified procedure conducted by certified trained personnel.
5.1.9.3 Evaluation of critical component metal surfaces of the valves after cleaning, inspection and specialized testing performed by
agencies other than the repair facility are the responsibility of the repair facility
5.1.9.4 Where numerical tolerances cannot be provided, the disposition of the internal integrity and surface quality of parts is under
the jurisdiction of the repair facility and dependent on its experience and judgment.
NOTICE: Repair work is limited to cleaning and polishing.
WARNING: Machining Not Allowed. Without consent from the valve manufacturer or car owner, machining,
grinding, welding or other alterations to the valve seat or stem seat is not allowed per AAR M1002,
Paragraph A3.11.1 of the Tank-Car Specifications.
NOTICE: Please refer to paragraph A3.11.2 of the Tank-Car Specifications and consult
Appendix E for dimensions and applicable tolerances.

15
Top-Transfer 2" Angle Valves A-720, A-721, A-721-B and A-724 Series
6 VALVE DISASSEMBLY
6.1.1 Before valve disassembly, open and close the hand wheel to run the stem (item 2) up and down to ensure that the
stem is neither bent nor binding in the threaded part of the body (item 4). Bent stems must be straightened to
proceed with the disassembly.
6.1.2 Place the valve in a vise, gripping it on the flat faces of the 6” square flange with the stem horizontal
and the side-port on the top.
6.1.3 Remove the pipe plug (item 16).
Body
Figure 6-1 Turn handwheel
Figure 6-2 Pipe plug removed
Handwheel

Installation, Operation & Maintenance Manual
16 Top-Transfer 2" Angle Valves A-720, A-721, A-721-B and A-724 Series
6.1.4 Take off the four (4) side flange bolts and lock washers (items 15A and 15B, respectively).
6.1.5 Carefully remove side outlet flange (item 7). It may be necessary to insert two (2) screwdrivers (180° degrees apart)
between the flange and the valve body to pry it out. Care to be taken so not to damage the mating surfaces
between the body and flange
Figure 6-4 Remove outlet flange
Figure 6-3 Remove flange bolts and washers

17
Top-Transfer 2" Angle Valves A-720, A-721, A-721-B and A-724 Series
Figure 6-5 Rotate handwheel to view nuts
Nuts
6.1.6 Raise the hand wheel slightly to lift the gasket retainer (item 3). Rotate it so that the two (2) nuts (item 18) are facing out the
side flange opening. Tighten down on the handwheel to keep the gasket retainer from rotating out of position.
6.1.7 Take a 7/16” socket wrench and unscrew the nuts. Using a block of steel that spans both sides of the U-bolt (about 1” wide),
tap the block to loosen the U-bolt and push it out about 1/4". Open the handwheel again and rotate the gasket retainer 180°,
then tighten down on the handwheel to put tension on the gasket retainer. Then use a tool to pull the U-bolt out.
Figure 6-6 Remove nuts and U-Bolt
U-Bolt

Installation, Operation & Maintenance Manual
18 Top-Transfer 2" Angle Valves A-720, A-721, A-721-B and A-724 Series
6.1.8 Raise the stem (item 2) up in the body as far as it will go. It now is possible to take the gasket retainer out of the valve.
Needle-nose pliers may be helpful in gripping the gasket retainer to extract it through the side port opening.
6.1.9 Take a 7/16” socket wrench and unscrew the nuts. Using a block of steel that spans both sides of the U-bolt (about 1” wide),
tap the block to loosen the U-bolt and push it out about 1/4". Open the handwheel again and rotate the gasket retainer 180°,
then tighten down on the handwheel to put tension on the gasket retainer. Then use a tool to pull the U-bolt out.
6.1.10 The packing gland (item 11) can now be pulled out of the body with the standard packing tools.
6.1.11 Loosen or remove the packing locknut (see step number 6.1.9). Turn the handwheel to lower or raise the stem as far as it will
go. Then take off the handwheel nut, washer, and handwheel. Gripping on the flats of the stem square with an open-end
wrench or vise grips continue to unwind the stem down. If the stem cannot be taken out the last few threads by hand, it may
be necessary to lightly grip the bottom of the stem with vise grips to disengage it from the body.
6.1.12 Remove the packing top washer, coil spring and bottom space through the top of the valve.
Figure 6-9 Loosen locknut and remove packing
Packing Locknut
Packing Gland
Figure 6-7 Remove retainer
Retainer
Figure 6-8 Remove packing gland

19
Top-Transfer 2" Angle Valves A-720, A-721, A-721-B and A-724 Series
Figure 7-1 Reassembly Steps 7.2.1 through 7.2.7
7 VALVE REASSEMBLY AND TESTING PROCEDURES
7.1 CLEANING
NOTICE: Do not use solvents or grease lubricants that are incompatible with the products in the tank.
For example, a petroleum-based grease may cause a chemical reaction when it comes in contact with chlorine.
Contact your supervising engineer for suitable cleaning and lubricating material recommendations.
O-rings and metallic parts that fit together should be lightly greased.
7.2 REASSEMBLY PROCEDURE
NOTICE
7.2.1 Place the lower spacer with wiper (item 10) in the body (item 4) with the wiper side up; see Figure 7-1.
7.2.2 Put the spring (item 5) in the body; see Figure 7-1.
7.2.3 Install the upper (curved) packing washer (item 9) in the body, with the convex side up; see Figure 7-1.
7.2.4 The 2" valve use four (x4) Teflon™V-rings (item 11) in the body; see Figure 7-1.
7.2.5 Insert the stem seal (item 12) with Teflon™insert in the packing screw (item 8); see Figure 7-1.
7.2.6 Thread the packing screw into the body by pushing down against the spring and turning clockwise to engage the thread.
Wrench tighten a couple of turns.
7.2.7 Screw down the packing locknut (item 21) a couple of threads on the packing screw); see Figure 7-1.
Packing Locknut
(Item 21)
Stem Seal
(Item 12)
Packing Gland
(Item 11)
Spring
(Item 5)
Packing Screw
(Item 8)
Packing Washer
(Item 9)
Spacer with Wiper
(Item 10)

Installation, Operation & Maintenance Manual
20 Top-Transfer 2" Angle Valves A-720, A-721, A-721-B and A-724 Series
Figure 7-2 Reassembly steps 7.2.8 through 7.2.10
7.2.8 From the bottom side of the body, insert the handwheel end of the stem (item 2). Screw the stem up until the handwheel flats
clear the top of the packing screw; see Figure 7-2.
7.2.9 Put on the handwheel (item 1), and then the handwheel lock washer (item 14). By hand, screw the handwheel nut (item 14)
onto the stem as far as it will go; see Figure 7-2.
7.2.10 Turn the handwheel counter clockwise to move the stem up into the neck of the body. It should move easily. After several
turns, stop when the stem thread come into contact with the lower packing washer (item 9); see Figure 7-2.
Valve Stem
(Item 2)
Nut
(Item 14A)
Handwheel
(Item 1)
Washer
(Item 14B)
This manual suits for next models
2
Table of contents
Other Dover Control Unit manuals
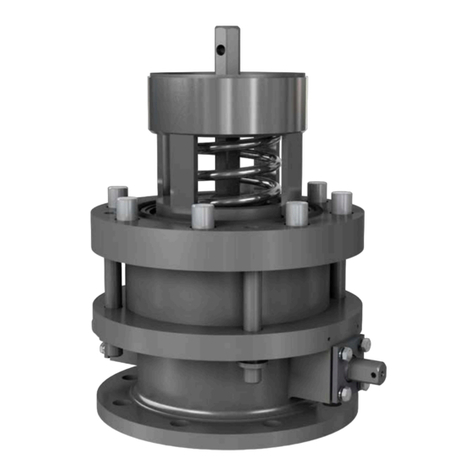
Dover
Dover Midland A-547PL Series Instruction manual
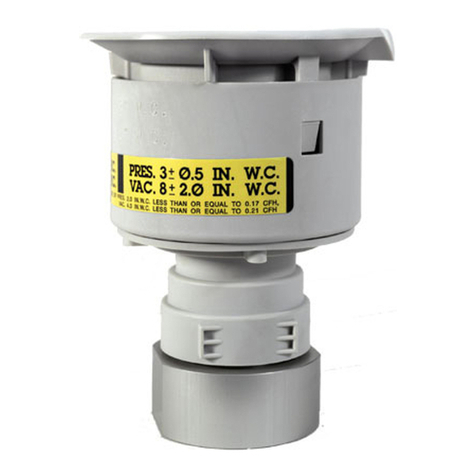
Dover
Dover OPW 623V Series User manual
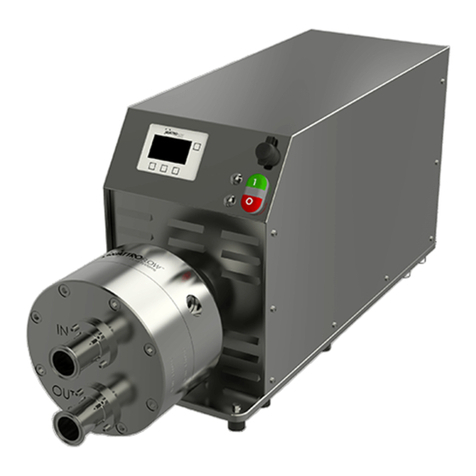
Dover
Dover PSG Quattroflow Q-Control User manual

Dover
Dover PSG BLACKMER AIR VALVE Manual

Dover
Dover OPW Midland A-522-C2-CS-SJ-SU-ST Installation instructions
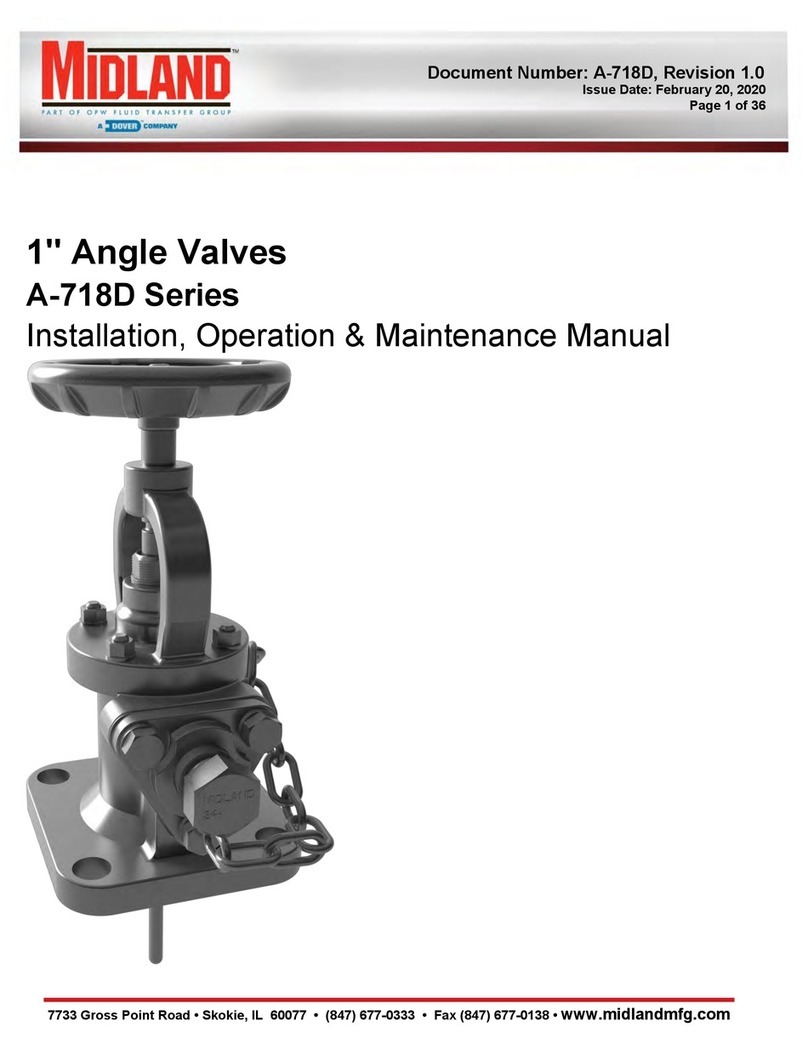
Dover
Dover Midland A-718D Series Instruction manual
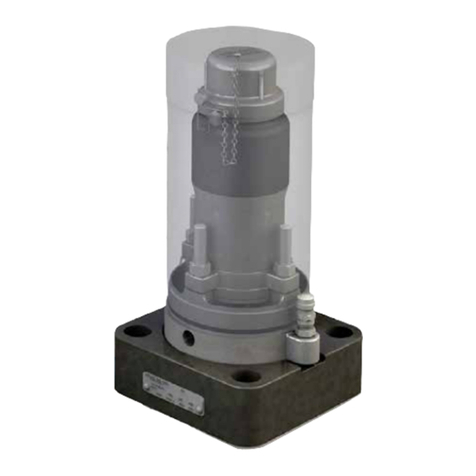
Dover
Dover MIDLAND A-1402C Series Instruction manual