Dover MIDLAND A-1402C Series Instruction manual

Installation, Operation & Maintenance Manual
www.midland.com
Part No.: A-1402C, Rev. 1.3
Issue Date: May 2, 2022
Supersedes: A-1402C, Rev. 1.2 (Sept. 27, 2016)
External-Style Pressure Relief Valve
A-1402C Series
Installation, Operation
& Maintenance (IOM) Manual

Installation, Operation & Maintenance Manual
2External-Style Pressure Relief Valve A-1402C Series
SECTION 1 | INTRODUCTION.......................................................................................................................................... 4
1.1 Technical Specifications .................... .............................................................................................................. 4
1.2 Valve Perspectives ............................................................................................................................................. 6
1.3 Pre-Installation Regulations / Requirements................................................................................................... 8
1.3.1 Regulations........................................................................................................................................... 8
1.3.2 Safety Precautions ............................................................................................................................... 8
1.3.3 Precautions for Mounted-Valve Repair .............................................................................................. 8
1.3.4 Required Tools ..................................................................................................................................... 9
SECTION 2 | VALVE INSTALLATION.............................................................................................................................. 10
2.1 Preliminary Considerations ..........................................................................................................................10
2.2 Procedure .......................................................................................................................................................10
2.3 Leak Inspection ...............................................................................................................................................12
2.4 Valve Operation Notes and Precautions ......................................................................................................12
SECTION 3 | VALVE DISASSEMBLY.............................................................................................................................. 13
3.1 Procedure .......................................................................................................................................................13
SECTION 4 | VALVE INSPECTION ................................................................................................................................. 16
4.1 Inspection Procedures ................................................................................................................................... 17
4.1.1 Top Guide............................................................................................................................................17
4.1.2 Adjusting Screw Threads ..................................................................................................................17
4.1.3 O-Ring Retainer Grooves ................................................................................................................... 17
4.1.4 Valve Body ......................................................................................................................................... 17
4.1.5 Plug...................................................................................................................................................... 18
4.1.6 Sealing Surface (Valve Mounting) ...................................................................................................18
4.1.7 Valve Spring ........................................................................................................................................ 19
4.1.8 Spring Guide ...................................................................................................................................... 19
4.1.9 Rupture Disc ....................................................................................................................................... 20
4.1.10 Rupture Disc Flange ..........................................................................................................................20
4.1.11 O-Rings................................................................................................................................................21
4.1.12 Special Inspection Considerations.....................................................................................................21

3
External-Style Pressure Relief Valve A-1402C Series
SECTION 5 | VALVE ASSEMBLY ................................................................................................................................... 22
SECTION 6 | SPECIAL GUIDELINES AND PRECAUTIONS ON PRESSURE TESTING AND ADJUSTMENT ..................... 23
6.1.1 Determining Applicable Pressure Values ....................................................................................................23
6.1.1 Test Stand and Gauge Requirements ..........................................................................................................23
SECTION 7 | VALVE PRESSURE TESTING PROCEDURE ................................................................................................ 24
7.1 Without Rupture Disc Installed ...................................................................................................................24
SECTION 8 | VALVE ADJUSTMENT PROCEDURE.......................................................................................................... 25
8.1 Procedure Without Rupture Disc Installed ..................................................................................................26
8.2 Valve Pressure Testing Procedure With Rupture Disc Installed ................................................................26
8.3 Post-Test Procedure .......................................................................................................................................27
SECTION 9 | MAINTENANCE ....................................................................................................................................... 28
9.1 Prior to Maintenance Tasks Performed ....................................................................................................... 28
9.1.1 Retesting of Valves in Storage .......................................................................................................28
SECTION 10 | WARRANTY............................................................................................................................................ 28

Installation, Operation & Maintenance Manual
4External-Style Pressure Relief Valve A-1402C Series
1.0 INTRODUCTION
The A-1402C Series External-Style Pressure Relief Valves are corrosion-resistant safety valves improved to include redundant seals
to atmosphere, eliminating potential leak paths and further increasing the long life and reliability in Chlorine transportation.
• Corrosion-resistant materials provide maximum protection from wet Chlorine
• Successfully used in Chlorine and AHCL applications
• Triple seals on all potential leak paths to atmosphere
1.1 TECHNICAL SPECIFICATIONS
Figure 1-1 Valve Specifications

5
External-Style Pressure Relief Valve A-1402C Series
Valve Model Rupture Disc
Setting (PSIG)
Flow Rate @ 10%
> R.D. Setting
(SCFM)
Minimum Vapor
Tight Pressure
(PSIG)
Minimum Vapor
Tight Pressure
(PSIG)
A-14377C-ML 375 7070 356 285
A-14227C-ML 225 4367 213 171
Valve Model Outer Spring Inner Spring Name Plate Adjusting Screw
Part #
Rupture Disc
Part #
A-14377C-ML 15-375-SS 14-13-SS 14-377-ML-C 15-112-SS 14-23-TA-375-F
A-14227C-ML 15-150-MO 14-13-SS 14-227-ML-C 15-11-SS 14-23-TA-225-F
Table 1-1 Technical Specifications Per Valve Model

Installation, Operation & Maintenance Manual
6External-Style Pressure Relief Valve A-1402C Series
Figure 1-2 Exploded View
1.2 VALVE PERSPECTIVES

7
External-Style Pressure Relief Valve A-1402C Series
Figure 1-3 Cross-Sectional View with Callouts
Item Qty. Part Name
1 1 Top Guide
2 1 Stem
3 1 Plug
4 1 Body
5 1 Outer Spring
6 1 Follower
7 1 Guide
8 1 Top Nut
9 1 Top Gasket
10 1 Shaft Seal
11 1 Adjusting Seal
12 1 Seal Retainer
13 1 Inner Spring
14 1 Cap
15 1 Seal Screw
16 4 Stud
17 4 Nut
18 1 Wire Seal
19 1 Retainer
20 1 Seat O-Ring
21 1 Plug O-Ring
22 1 Flue O-Ring
23 1 Rupture Disc
24 1 Flue
25 8 Rupture Disc Flange Bolts
26 1 Rupture Disc Flange
27 1 Purge Valve
28 1 Name Plate
29 1 Protective Cap/Chain
30 1 Flange O-Ring (inner)
31 1 Flange O-Ring (outer)
32 1 Filler Gasket

Installation, Operation & Maintenance Manual
8External-Style Pressure Relief Valve A-1402C Series
1.3 PRE-INSTALLATION REGULATIONS / REQUIREMENTS
1.3.1 Regulations Midland External-Style Valves are used in contact with a variety of products, many of which are
hazardous materials. The acceptance and transportation of products are regulated by the DOT and AAR in the U.S.A.,
and in Canada by CTC and Transport Canada. Regulations of other governmental bodies must be complied with
for stationary and mobile applications. All personnel should be familiar with and follow these regulations. Nothing
in these instructions is intended to conflict with or supersede these regulations. The information in this document
was gathered from knowledgeable sources, but Midland Manufacturing Corporation makes no representations or
guarantees about its accuracy or completeness and assumes no liability for this information.
Specifications are subject to change without notice.
1.3.2 Safety Precautions Midland valves are used in connection with a variety of products, many of which are hazardous
materials and could cause serious injury or damage.
This valve should only be installed, operated and maintained by qualified personnel.
Read all of these instructions carefully before proceeding.
1.3.3 Precautions for Mounted-Valve Repair When performing maintenance on a pressure relief valve that is
mounted on a railcar, observe the following precautions.
• Wear protective clothing and equipment suitable for withstanding the materials to which you may be exposed
• Position yourself on the upwind side of the valve when possible
• Work with a partner who can help you in the event of an emergency
• Follow approved safety precautions for hazardous or toxic materials
CAUTION: Toxic Hazard. Always use extreme caution and proper equipment when involved with hazardous
materials. To avoid exposure to toxic or hazardous materials, make sure the tank car is empty and clean, and that
the work area is free of hazardous chemicals before removing or installing any valve.
WARNING: These external-style pressure relief valves are spring-loaded assemblies with a large amount of
stored potential energy in the spring. Handle with care to avoid damage to the valve stem, which could result in
breakage and ejected piece parts.
WARNING: When assembling or disassembling the valve, DO NOT position oneself directly in front of the spring
and stem. Instead, position oneself to the side away from the valve. Unexpected component failure – valve-stem
or spring breakage – may cause a sudden energy release that can discharge component parts a short distance in
an uncontrolled manner. Personal injury may be a result.
CAUTION
WARNING
WARNING

9
External-Style Pressure Relief Valve A-1402C Series
1.3.4 Required Tools
Before arriving at the installation site obtain the required tools and supplies prior to performing the procedures
indicated in this guide.
Tongue Mounting
Figure 2-1 Gasket-Sealing Surfaces
Recommended Wrenches
SAE Component Torque (ft.-lbs.) Item #
5/16” Hex 3/8” Rupture Disc
Flange Bolt 25 25
9/16" 1/2" Top Guide Nut 50 17
1-1/2" 1" Top Lock Nut 45 8
1/2" 1/8" NPT Needle Valve Wrench Tight 27
1-1/16"
Flats on Small Valve
O-ring Retainer, 5/8"
Mounting-stud Nuts
1-1/4"
Flats on Large Valve
O-ring Retainer, 3/4"
Mounting-stud Nuts
Table 1-2 Required Tools
Other Tools and Supplies
Screwdrivers Pipe Wrench
Wheel Puller Lint-free Cloth
Silicone Grease (or equivalent lubrication) Emery Paper (400 grit, cut in 1" strips)
Torque Wrench Wire Brush
Table 1-3 Additional Recommended Tools & Supplies

Installation, Operation & Maintenance Manual
10 External-Style Pressure Relief Valve A-1402C Series
2 VALVE INSTALLATION
2.1 PRELIMINARY CONSIDERATIONS
2.1.1 New valves are tested, adjusted and sealed at Midland. If a new valve
has been left in its original packaging, is undamaged and is not more
than six months old, it may be installed on a tank car without retesting
or recalibration.
2.1.2 Prior to installation, ensure that the valve remains clean and that the
gasket-sealing surfaces (Figure 2-1) are not damaged.
2.2 PROCEDURE
2.2.1 Remove the old valve and then insert a soft rubber plug into the tank
opening to prevent debris from entering the tank during cleaning of
the valve-mounting groove and studs on the manway cover plate.
2.2.2 Wire brush the threads of the mounting studs to remove rust or scale.
Nuts should move freely on clean studs. Studs should not exhibit excessive
corrosion.
2.2.3 Remove and discard all used gasket material.
2.2.4 Using a lint-free cloth and appropriate cleaning solvent, wipe clean the valve and cover plate sealing surfaces and the
mounting-stud threads.
2.2.5 For tongue-and-groove mountings, examine the sides of the groove. Because the valve tongue fits tightly into the
groove, any peening-over of the edges of the groove may make it difficult to properly fit the valve tongue into the
groove. If the sides of the groove are peened over, make corrections to meet the AAR groove tolerances.
2.2.6 Install the new gasket. Ensure it is fully seated. When a groove gasket is fully seated, 1/16" of free space should
remain above the gasket to permit locating and entry of the valve tongue.
Figure 2-1 Gasket-Sealing Surfaces
CAUTION: Groove Damage. In order to avoid groove damage, do not scratch the metal in the bottom of the
groove when removing the old gasket.
CAUTION: Do not use a sharp tool to press the new gasket into place or gasket damage may result.
CAUTION
CAUTION

11
External-Style Pressure Relief Valve A-1402C Series
2.2.7 Inspect the tongue of a reconditioned or retested valve by running
your fingernail around its inner and outer edges to check for damage.
The tongue dimensions have diameter tolerances of ±0.003", thus
any excess material on these diameters will make it difficult to fit the
tongue into the groove. If the tongue is peened over, remove excess
material to meet AAR tongue tolerances.
2.2.8 Remove the rubber plug (which was inserted in step
1) from the cover plate.
2.2.9 Install filler gasket (Item 32) over the mounting studs.
2.2.10 Hold the valve by the flue assembly (Figure 2-2) and lower it gently into
the mounting. Align the body holes over the studs and lower the valve
while positioning the valve tongue in the cover plate groove.
2.2.11 Install the nuts and tighten them in 1/3-torque increments in a
diagonally alternating sequence to a torque specified by the gasket
specified, as shown in Figure 2-3.
Figure 2-3 Mounting-Nut
Tightening Sequence
CAUTION: To prevent Tongue Damage, do not install a valve
having damaged sealing surfaces.
CAUTION: Tongue Not in Coverplate Groove. Verify that the
valve tongue has fit into the coverplate groove. It must be so
engaged before continuing with the next step or valve damage
may result.
CAUTION: Uneven Gasket Compression. Do not over-tighten
the nuts on one side of the valve as this may tilt the valve and
result in uneven gasket compression.
CAUTION
CAUTION
CAUTION
Figure 2-2 Valve with Flue Assembly
and Filler Gaskets

Installation, Operation & Maintenance Manual
12 External-Style Pressure Relief Valve A-1402C Series
2.3 LEAK INSPECTION
2.3.1 Test all newly installed valves under pressure to confirm that no leaks are present
2.4 VALVE OPERATION NOTES AND PRECAUTIONS
WARNING: Valve Leakage. Improper valve-tongue seating in the flange groove, loose nuts and damaged
gaskets may result in leaks at the valve-mounting joint. Also, valves equipped with rupture discs should only be
tested to 50% of rupture disc setting.
NOTE: Operation of the valve must conform with all applicable TC, AAR, DOT specifications
(Parts 173.31, 174.67, etc.), other governmental bodies, and the operating instructions of your company.
The pressure relief valves are spring-loaded and are actuated by overpressure in the railcar tank.
There are no provisions for manual activation of the valve.
CAUTION: Needle Valve Closure. For valves equipped with rupture discs, be sure that the needle valve is
closed and the plug is installed, if required.
CAUTION: Incorrect Setting. Never adjust the spring compression of a valve while it is mounted on the vessel
cover plate or incorrect settings may result.
CAUTION
CAUTION
WARNING
NOTE

13
External-Style Pressure Relief Valve A-1402C Series
3 VALVE DISASSEMBLY
3.1 PROCEDURE
3.1.5 Loosen the set screw (Item 15 of Figure 1-3) thus securing the cap (Item 14).
3.1.6 Use a pipe wrench and unscrew the cap as shown in Figure 3-1. Remove the cap.
3.1.7 Remove the top gasket or bumper (Item 9 of Figure 1-3).
3.1.1 Remove the protective cap (blue) and cut the seal wire (Item 18 of Figure 1-3) to release the cap chain. Unscrew and
remove the flue (tube) from around the valve.
3.1.2 If present, remove the plastic protector from the base or tongue of the valve.
3.1.3 If present, remove the flue O-ring (See Item 22 of Figure 1-3).
3.1.4 Remove the rupture disc flange bolts (Item 25 of Figure 1-3) from the valve base. Separate the disc flange from the
valve base and remove the rupture disc (Item 23) inner and outer O-rings (Items 30 and 31 respectively;
see Figure 1-3).
Figure 3-1 Valve Cap Removal Figure 3-2 Flue and Protective Cap
CAUTION: Spring-loaded Assembly. During valve-spring disassembly, the valve contains springs under load. DO
NOT attempt to disassemble the valve without first reading these instructions or injury may result.
Spring pressure must be adjusted to minimum and a bench clamp or press used for disassembly.
CAUTION: Flange Damage. To prevent flange handle damage during dissambly, handle the valve body and
rupture disc flange carefully after disassembly. Avoid allowing their machined surfaces to contact the metal
workbench and hand tools or damage may result.
CAUTION
CAUTION

Installation, Operation & Maintenance Manual
14 External-Style Pressure Relief Valve A-1402C Series
3.1.8 Loosen the top nut (Item 8 of Figure 1-3) one turn counterclockwise.
3.1.9 With a locking bench clamp (Figure 3-3), apply
pressure to the adjusting screw (Item 11 of
Figure 1-3). While so clamped, remove the four
nuts (Item 17) securing the top guide (Item 1) to
the valve base.
3.1.10 Slowly release the clamp to relieve remaining valve spring pressure and
then lift the top guide housing off the valve base.
3.1.11 Remove the adjusting screw (Item 11 of Figure 1-3) and top nut (Item 8) from the
top guide and from one another.
3.1.12 From the valve stem (Item 2 of Figure 1-3) remove the follower (Item 6),
outer spring (Item 5), inner spring (Item 13) and the guide (Item 7).
3.1.13 Lift the stem (Item 2 of Figure 1-3) and seal retainer (Item 12) straight up and off
the shaft and off the plug (Item 3).
3.1.14 Remove the shaft seal (Item 10 of Figure 1-3) from the seal retainer (Item 12).
3.1.15 Lift or pry up the retainer (Item 19 of Figure 1-3). It will likely lift off with the valve
plug (Item 3) as a single unit.
3.1.16 Remove the plug from the retainer.
CAUTION: Rupture Disc Seat Damage.
When clamping the valve, support the base
only near the edges to prevent damage
to the rupture disc's raised face on the
underside of the valve body (Figure 3-4).
CAUTION
CAUTION: O-Ring Groove Damage. Remove the O-rings from the retainer using
only a non-scratching tool or scratching and gouging of the O-ring may result.
CAUTION
Figure 3-3 Clamping for Top Guide Removal
Figure 3-4 Underside of Valve Body Flange
Figure 3-5 Valve After
Top Guide Removal
Figure 3-6 Valve Stem
and Seal Retainer
Raised-Face
Rupture Disc

15
External-Style Pressure Relief Valve A-1402C Series
3.1.17 Remove the two (2) O-Rings (Items 20 and 21 respectively; see Figure 1-3) from the retainer using only a non-scratching tool.
3.1.18 Unscrew and remove the needle valve (Item 27 of Figure 1-3) from the valve body.
Figure 3-7 Retainer, Valve
Stem, O-Rings and Plug
Figure 3-8 Retainer with O-Ring

Installation, Operation & Maintenance Manual
16 External-Style Pressure Relief Valve A-1402C Series
4 VALVE INSPECTION
Follow the guidelines in this section for inspecting the condition of valve components after disassembly.
In some instances a component can be properly evaluated for damage or cracks only with the use of
specialized techniques, such as dye-penetration or magnetic-particle testing, according to a qualified
procedure by certified trained personnel. Such testing is indicated within this document where mandatory.
Additionally, specific inspections must be performed during and after reassembly of the valve to ensure proper
and reliable operation.
Figure 4-1 Valve Components (Inspection)

17
External-Style Pressure Relief Valve A-1402C Series
4.1 INSPECTION PROCEDURES
4.1.1 Top Guide
4.1.11 The Top Guide (Figure 4-1) is principally a structural part. There should
be no paint on any components covered by the cap, or between
adjacent surfaces on the top guide and valve body. The vent area of
the valve body must be unobstructed by foreign matter that would
hinder free flow of discharging fluid.
4.1.2 Adjusting Screw Threads
4.1.2.1 The threads of the adjusting screw (Figure 4-1) should be clean and
lightly lubricated.
4.1.3 O-Ring Retainer Grooves
4.1.3.1 The grooves (Figure 4-2) must be free of gouge marks, corrosion, pits and rust. Since the O-rings must seal against
these surfaces, any irregularities can cause the valve to leak. Clean the groove by sanding it lightly with emery paper
(400 grit). If this does not effectively clean the groove, replace this part.
4.1.4 Valve Body
4.1.4.1 The sealing surfaces are the crown of the seat and rupture disc, sealing surface (Figure 4-3). Clean the seat with
emery paper (400 grit) then wipe it clean with a cloth and a suitable solvent. Run your fingernail around the surface
to detect any flaws.
NOTE: Repair work is limited to cleaning and polishing. See Paragraph A4.11.1 of the Tank Car Specifications.
NOTE
Figure 4-3 Valve Body Seat
Figure 4-4 Valve Plug
Figure 4-2 Retainer O-ring Grooves

Installation, Operation & Maintenance Manual
18 External-Style Pressure Relief Valve A-1402C Series
4.1.5 PLUG
4.1.5.1 The sealing surface is the plug seat (Figure 4-4) Clean the plug with the emery paper (400 grit) then wipe it clean
with a cloth and a suitable solvent. Run your fingernail over the seat surface to detect any flaws.
4.1.6 SEALING SURFACE (VALVE MOUNTING)
4.1.6.1 The underside of the rupture disc flange is the surface that seals to the mounting plate on the railcar (Figure 4-5).
Machining of this surface is permitted. A good seating surface is necessary to ensure there are no leaks in this area.
NOTE: Repair work is limited to cleaning and polishing. See Paragraph A4.11.1 of the Tank Car Specifications.
NOTE: Please refer to paragraph A4.11.2 of the Tank Car Specifications and consult Appendix E for dimensions
and applicable tolerances.
NOTE
NOTE
WARNING: Machining Not Allowed. Machining, grinding, welding or other alterations to the valve seat or
plug seat is not allowed per AAR M1002, Paragraph A4.11 of the Tank Car Specifications.
WARNING
Figure 4-5 Machinable Surfaces (Tongue Flange)

19
External-Style Pressure Relief Valve A-1402C Series
4.1.7 VALVE SPRING
4.1.7.1 This part is highly stressed. The exterior surface must be free of pitting, cracks, and corrosion. If any corrosion
is observed on the spring, use magnetic-particle or dye-penetration inspection (performed by certified trained
personnel) to evaluate the exterior surface and ensure that it is free of cracks and corrosion pits.
4.1.7.2 Test the springs by pressing them to 80% of maximum deflection in a press for two (2) minutes. Remove from the
press and then measure the spring free-height. If free-height is less than the minimum indicated in Table 4-1, replace
the spring.
4.1.8 SPRING GUIDE
4.1.8.1 This structural part has guides on its outer edges (Figure 4-8). Move it up and down the length of the top guide as
indicated below. If it binds, look for dents or gouged surfaces on the inside of the top guide. Repair the damage to
allow free movement of the spring guide.
WARNING: Valve Sticking. If the spring guide binds in the top guide bore, the valve may stick in the open
position or be prevented from opening. Always ensure free travel of the spring guide before reassembling the valve.
WARNING: Valve Spring Failure. Defects in coil springs, such as cracks and corrosion pits, can act as stress
concentrators. Failure to detect these defects can result in coil-spring breakage and uncontrolled valve venting.
WARNING
WARNING: Deficient Valve Travel. Coil springs that have taken a “set,” resulting in an undersize free-height,
will not allow the valve to open fully.
WARNING
WARNING
Spring Part Number Wire Size (REF)
(Inches)
Height at 80% of
Max. Deflection (Inches)
Minimum Free-Height
(Inches)
14-13-SS 0.19 3.12 4.63
15-375-SS 0.34 3.61 5.00
15-150-MO 0.28 2.80 4.00
Table 4-1 Minimum Free-Heights for Springs After Pressing 80% of the Maximum Deflection for 2 Minutes

Installation, Operation & Maintenance Manual
20 External-Style Pressure Relief Valve A-1402C Series
4.1.9 RUPTURE DISC
4.1.9.1 These valves include a rupture disc (Figure 4-6) beneath the main valve
assembly. Examine the disc for nicks, damage or any signs of stretching.
Replace the disc if any defects are observed.
4.1.10 RUPTURE DISC FLANGE
4.1.10.1 Look very carefully at the section of the disc flange (Figure 4-7) that is contoured
to hold the disc. No scratches, radial tool marks, nicks, burrs, or corrosion can
be present in the groove or the disc will fail to maintain a pressure-tight seal. If
dents, pits or gouges are observed, do not attempt to remove them by machining.
Discard the flange and obtain a new one.
4.1.10.2 Similarly, on the raised surface on the underside of the valve body flange
(also in contact with the rupture disc) must be completely free of imperfections,
see Figure 4-9.
Examine it carefully. No re-machining is permissible.
Replace the valve body if defects are observed.
Figure 4-6 Rupture Disc
Figure 4-7 Rupture Disc and Disc Flange Figure 4-8 Spring Guide
Figure 4-9 Underside of Valve Body Flange
This manual suits for next models
2
Table of contents
Other Dover Control Unit manuals
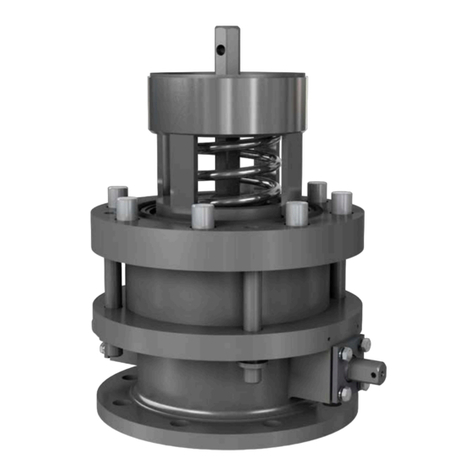
Dover
Dover Midland A-547PL Series Instruction manual

Dover
Dover OPW Midland A-522-C2-CS-SJ-SU-ST Installation instructions
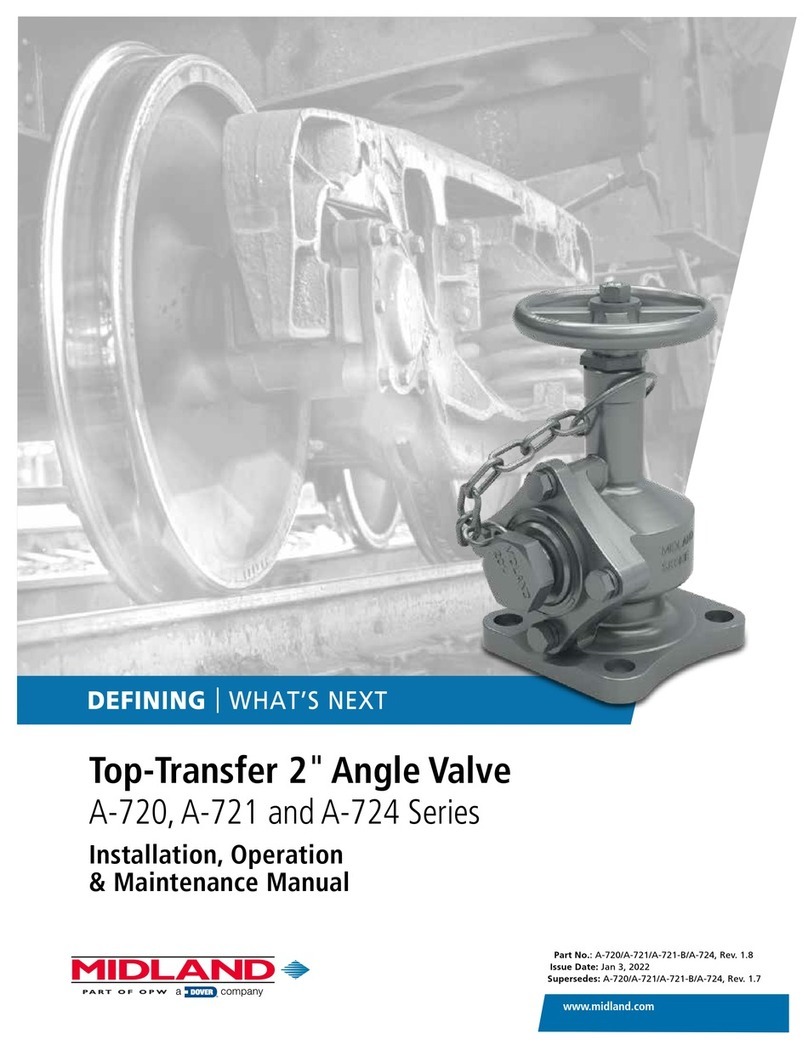
Dover
Dover Midland A-720 Series Instruction manual

Dover
Dover PSG BLACKMER AIR VALVE Manual
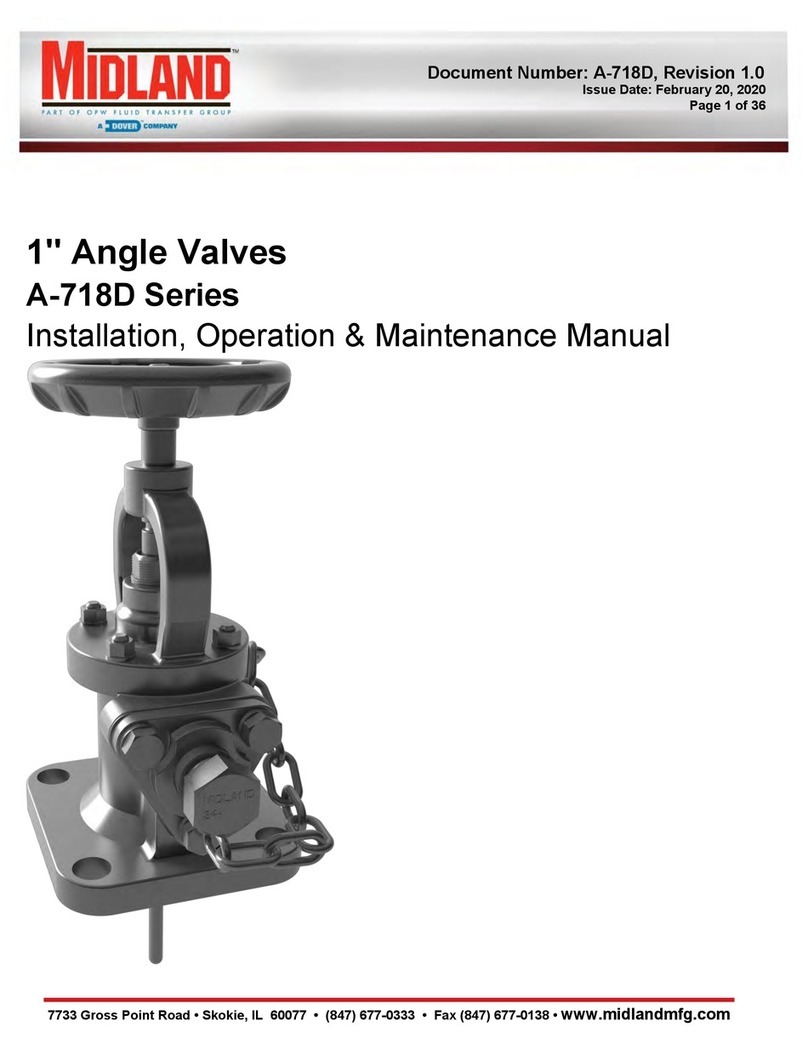
Dover
Dover Midland A-718D Series Instruction manual
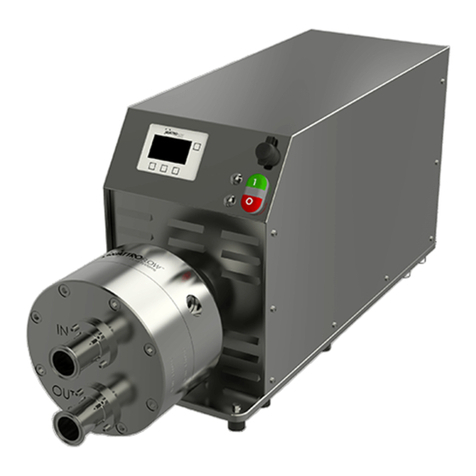
Dover
Dover PSG Quattroflow Q-Control User manual
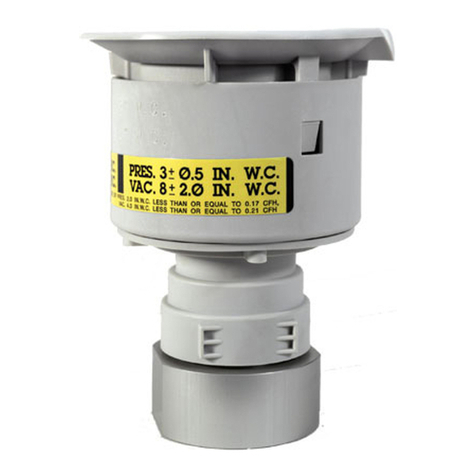
Dover
Dover OPW 623V Series User manual
Popular Control Unit manuals by other brands
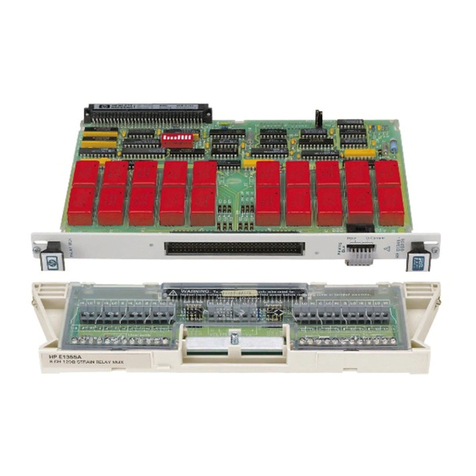
Agilent Technologies
Agilent Technologies HP E1355A user manual
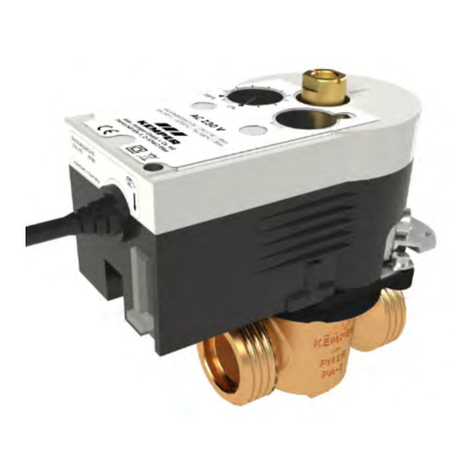
Kemper
Kemper KHS 686 04 Installation and operating manual

Heritage Bathrooms
Heritage Bathrooms SDC05 Installation instructions and user guide
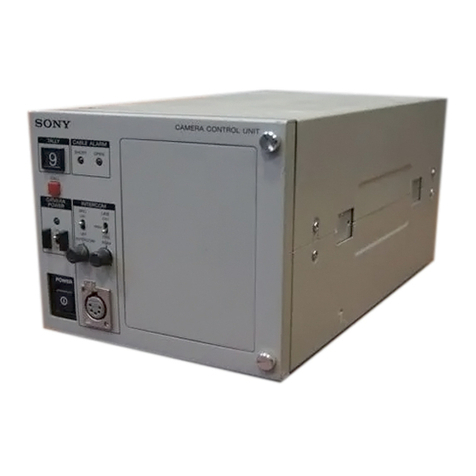
Sony
Sony CCU-TX7 Service manual

Pentek
Pentek 71620 operating manual
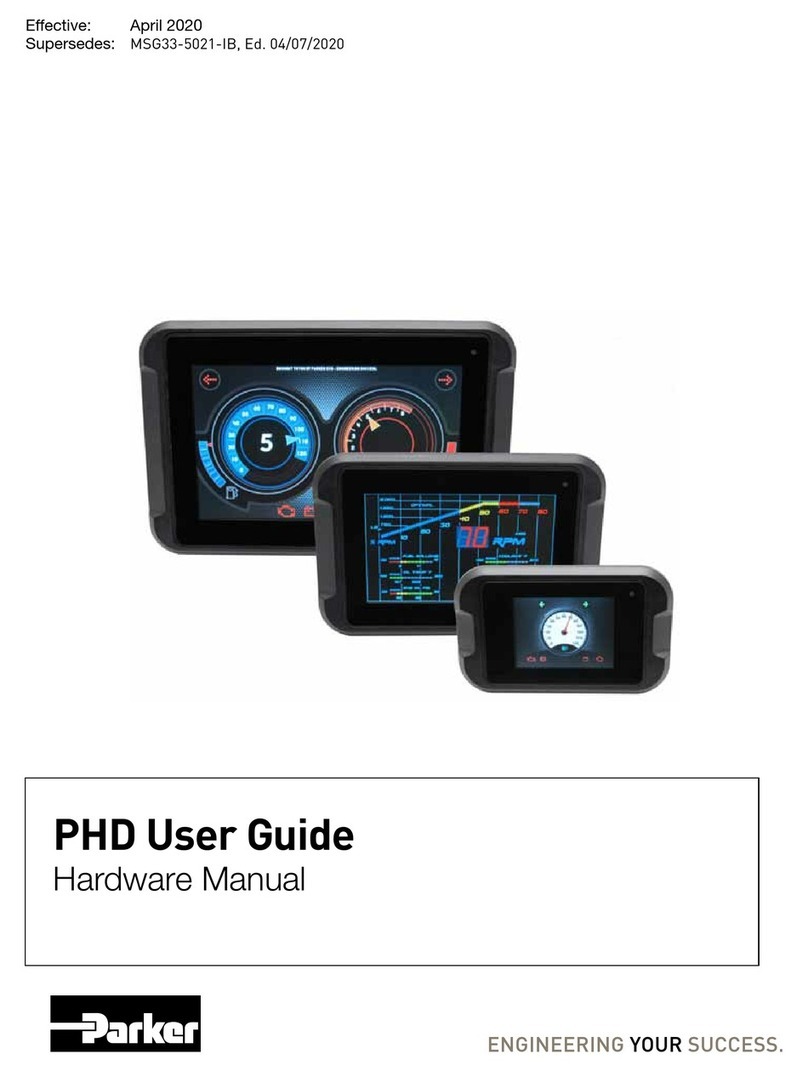
Parker
Parker PHD Series user guide