DraughtMaster MODULAR 20 User manual

DRAUGHTMASTER
MODULAR 20
USER MANUAL
www.draughtmaster.com

The machine contains technical solutions protected by intellectual property
rights including patents and trade secrets belonging to Carlsberg Breweries A/S.
An obligation of strict confidentiality for the holder applies.
No part of this manual may be reproduced.
© 2020 – All Rights Reserved.
PROPERTY RIGHTS.
IMPORTANT.
3
CONTENT
1.0 GENERAL 4
1.1 SAFETY 4
1.2 SYMBOLS USED IN THIS MANUAL 5
1.3 DISCLAIMER AND NOTES TO INSTRUCTIONS 5
1.4 TRANSPORTATION/HANDLING/STORAGE 5
2.0 DESCRIPTION OF THE M20 SYSTEM 6
2.1 GENERAL OVERVIEW 6
2.2 THE SYSTEM 6
3.0 INSTALLATION AND TAKEN INTO USE 7
3.1 INSTALLATION 7
3.2 BEFORE STARTING UP / HANDOVER 7
3.3 STORAGE OPERATIONS CONDITIONS 8
3.4 SAFE USE 8
4.0MAINTENANCE & IN SERVICE 9
4.1 MAINTENANCE AND INSPECTION 9
4.2 CHECKS / SERVICE INTERVAL 9
4.3 CLEANING 9
5.0 TROUBLE SHOOTING 12
5.1 FAILURE INTRO / MODES 12
5.2 WARNINGS 12
5.3 OTHER FAILURES 12
6.0 APPENDIX 13
6.1 APPENDIX A UNIT DRAWING / DIAGRAM 13
6.2 APPENDIX B COPY OF MARKING PLATE 14
6.3 APPENDIX C EU DECLARATION 15
6.4 APPENDIX D INSTRUCTION FOR CHANGING A KEG 16
6.5 APPENDIX E CLEANING CYCLE 18

54
1.1 SAFETY
1.0 GENERAL
The Equipment positioning, installation and disassembly must be carried on by trained and specialized
personnel. Personnel must have carefully read and understood equipment user manuals. For installation use
standard tools only as listed in this manual. The Equipment is not suitable for installation outdoors and/or in
places exposed to atmospheric agents (rain, direct sunlight, etc.).
1.2 SYMBOLS USED IN THIS MANUAL
Refer to Appendix A sec. 6.1.
Prior to commencing any use and/or operating, personnel must have carefully read and understood this manual
to ensure a safe and intended use.
IMPORTANT NOTE:
This manual may include short description and illustrations, which are intended as guidance and summary
for parts of the operation such as i.e. the cleaning module. The Operation Manual supplied with the
cleaning module (where applicable in the actual installation), must be carefully read and understood.
Illustrations in this manual are provided to aid the basic understanding for the user and may deviate from the
actual design. This manual must be placed at the disposal of the operating and maintenance personnel at
all times. Please store these instructions as reference for operation and service. Carlsberg Breweries A/S
declines any risk and liability for operations carried out on the equipment without respecting the instructions
given in this manual and the supporting manuals for integrated equipment.
• Do not stand under suspended loads during loading/unloading operations.
• Arrange suitable area with flat floor for equipment unloading and storage operations for correct and safe
lifting operations refer to following identifications regarding weight identified on equipment.
• Do not push or pull the equipment to move it as it may tip over.
• Do not make modifications to the equipment and parts supplied with equipment.
Any missing or faulty parts must be replaced with original parts.
• The equipment must be levelled, otherwise its operation could be aected.
• The equipment has a safety valve (set at 3,3 bar) which must not be tampered with in any way.
• Never clean the plastic surfaces with acid substances or oils.
• The equipment is not suitable for installation in areas exposed to water sprays, therefore do not clean with
jets of water.
• Do not use the detergents containing chlorine, solvent-based detergents (i.e. trichloroethylene) or
abrasive powders.
See Appendix
1.3 DISCLAIMER AND NOTES
TO INSTRUCTIONS
1.4 TRANSPORTATION/HANDLING
/STORAGE
Do not remove, tamper with or make the equipment identification labels / marking illegible (also applies to
cleaning module). In case of eye contact with cleaning detergent, rinse immediately with plenty of water and
seek medical advice. Wear suitable protective clothing, gloves and eye / face protection according to local
legislation requirements. In case of accident or if you feel unwell, seek medical advice immediately (show
the label where possible). The cleaning detergent material and its container must be disposed of as hazardous
waste. Recommended safety personal protection sheet.
Protect
garments Safety
footwear Gloves Glasses Ear
protectors Mask
Transport
Handling
Unpacking
Installation
Normal use
Adjustments
Routine cleaning
Extraordinary cleaning
Maintenance
Dismantling
Scrapping
CAUTION! Safety
helmet
PPE required
PPE available or to be used
if necessary
PPE not required

76
2.0 DESCRIPTION
OF THE M20 SYSTEM
2.1 GENERAL OVERVIEW
Draught Master (DM) Modular 20 (M20) is a draught equipment system using PET (polyethylene terepht-
halate) kegs used in Europe since 2011. The kegs are available in a 20L. size and suitable for recycling. The
assembly includes a Modular 20 unit (keg module), which is a pressurized plastic vessel (air working pressure
2.8 – 3.0 bar) supported by an external frame/structure that is designed to facilitates the beer keg.
The system employs a combination of equipment such as cleaning equipment and pressure source that provide
the necessary cleaning and pressure possibility to pressurize the keg module in GF PP Polymer, where the
20L keg container containing carbonized liquids, such as beer is inserted. Here the beer it driven through in-
sulated polymer pythons parsing a beer cooler and forward to tap or taps in a serving area for serving customers.
The steel kegs and couplers are replaced by keg modules and the CO2 equipment (cylinder + regulators) by
a compressor. The compressor is allocated in a semiautomatic cleaning module which allows the bar sta to
clean himself.
2.2 THE SYSTEM
The advantages of the system are:
• Better quality of beer for Consumer.
• No CO2 bottles.
• Light one-way kegs.
• Less waste of beer.
• Long shelf life (6 months before opening, 31 days once
opened).
• Lower environmental impact. This is coupled to the
Draught Master system either in the cellar or in under
bar outlets.
The system uses a bespoke compressed air system that is also an integrated cleaning system. The pressure
driven cleaning system uses advanced technology tracking the line cleaning activity in the outlet and when
the maximum length of time between cleans elapses then the system will stop dispensing and the screen on
the cleaning unit will flash to indicate this. Only after the lines have been cleaned will it then allow product
to be dispensed. The system does have a postpone button which can be used once only each time; this is
for when the total time elapsed and it can be extended by 1 day. The cleaning unit will require a permanent
water supply. A drain tube is fitted to the cleaning unit, so this will need to be either routed to a drain or
a suitable container such as a 5 lt. container. The cleaning unit can be located away from the keg modules
(up to 4 m away through the extension pipe connection). If the cleaning module is located next to the keg
module then place it on the left side as the water/compressed air outlet is situated on the right side of the
cleaning unit.
3.0 INSTALLATION
AND TAKEN INTO USE
3.1 INSTALLATION
DM Modular 20 is installed by a professional Technician appointed by Carlsberg Breweries A/S before handed
over and taken into use by the customer. The installation can contain of an Cleaning equipment, min. one Keg
Module, Pythons, beer cooler, foam stop and beer boost pump. The installation is mounted on a rack or base
pallet with or without wheels. Depending on installation the modules can also be stacked in layers.
Before start up and during handover the customer should be handed out the troubleshooting card and be part
of a step-by-step instructions according to troubleshooting. The technician should give examples and physically
show customer how to clean, how to change a keg, and check beer is running correctly through taps.
The Technician will go true the following points together with the customer:
• How to change the keg incl. the handling of the kegs from cardboard opening to keg loading into the keg
modules including the keg storage.
• How to remove the keg from the keg module, stressing the importance of waiting for the decompression
of the chamber before removing the lid.
• How to preform a cleaning process where applicable.
• Safety instructions..
• What are the error messages of cleaning modules.
• The countdown (number of days till the next cleaning process).
• How to react to basic messages from the system to avoid – troubleshooting before calling for service.
• Check ice bank in cooler.
• Avoid leaving the detergent in the pipes throughout the night because it aects their functionality.
• How to use the equipment, including the periodical gasket cleaning, pressure chamber
cleaning, and hints to ease the lid opening/closing.
• Check power supply for cleaning module.
• Check cleaning detergent is connected to cleaning module before opening.
• Check the water valve is connected and open.
• How to read trouble shooting instructions.
The Technician have gone true the following points before handover:
• Go through entire installation for any leaks:
• Connections at the beer cooler.
• Connections at the keg modules.
• Connections at the cleaning modules
• Check connections at beer tower for any leaks.
• Check light in product branding.
3.2 BEFORE STARTING UP / HANDOVER

8
3.4 SAFE USE INCL. CHANGE OF KEGS
When changing keg, please follow Instructions on Cardboard box packaging and Instructions In handling and
changing keg supplied by the Technician.
Always place the lid in a safe place when changing keg and never leave any part of the equipment on surfaces
that are not clean or where they could fall from.
See Appendix
Always place the kegs away from sources of heat (and sunlight) and in any case at a room temperature
between +4° to +35°C.
The equipment must only be operated within temperature between +4° to +35°C.
FOR BEER KEGS THE FOLLOWING APPLY:
• Only use original Carlsberg Breweries A/S brands kegs.
• Kegs must be stored vertically and used according to
specifications on the cardboard box.
• Keg exceeding +35 C must not be used.
3.3 STORAGE OPERATIONS CONDITIONS
SAFE OPERATION:
Always ensure to release the pressure by the use of the Pressure release pin before opening the lid. Do not
push or pull the equipment to move it as it may tip over unless it is on wheels.
BE AWARE OF BELOW WHEN HANDLING THE KEG AND EQUIPMENT:
• Do NOT use any tools on equipment in for example trying to open and close the lid.
• Do NOT force volume expanded beer kegs into the keg module.
• Do NOT subject the equipment to impact, mechanical shock or weight load.
• Do NOT use or operated the equipment with damaged or broken parts.
• Do NOT remove / replace original parts of equipment’s design.
• Do NOT repair equipment yourself.
IN CASE OF FAILURE OR DAMAGED TO EQUIPMENT,
PLEASE CONTACT SERVICE TECHNICIAN.
WARNING!
Always remember to ensure the equipment and parts are not defect (such as modular, lid, gaskets, cleaning
module). This may be specified and written as service intervals or agreements made for technician visits to
cover (including cleaning). Integrated equipment’s intended lifetime are registered by the Carlsberg service
technicians and are replaced accordingly during service intervals.
Lag of service checks or maintenance according to specifications may lead to failure of the system and/or
parts in the system subject to wear and tear.
4.2 CHECKS / SERVICE INTERVAL
4.1 MAINTENANCE AND INSPECTION
4.0 MAINTENANCE
& IN SERVICE
IMPORTANT NOTICE BEFORE CLEANING:
It is recommended to place on the tap the “red sign”
showing that cleaning is in progress.
4.3 CLEANING
During cleaning the use of detergents with content of chlorine or substances such as thinners,
trichloroethylene, ammonia, etc. is prohibited.
IMPORTANT NOTE:
The Operating Instructions for the cleaning module must be clearly read and followed.
Below is a short illustration of the process.
WARNING:
CLEANING IN PROGRESS
9

10
During cleaning the use of detergents with content of chlorine or substances such as thinners,
trichloroethylene, ammonia, etc. is prohibited.
IMPORTANT NOTE:
The Operating Instructions for the cleaning module must be clearly read and followed.
Below is a short illustration of the process.
Start a cleaning process shall be done as following below list.
• Open the water supply and start with cleaning mode.
• Be aware about the compressor cycles (Start/stop).
• Check cleaning flow through taps in bar (colour).
• At the end of countdown start the rinsing mode.
• At the end of the cleaning process make sure to flush with water and then move to beverage mode.
• Remove the tube from detergent bottle and tight the cap of the bottle to preserve the eectiveness of the
detergent.
WARNING:
Excess detergent might exit the tube
11
System Error:
Abnormal conditions like continuous com-
pressor operation, compressor overcurrent, a
predefined time without cleaning cycle or “bear
cut” will be monitored and can be displayed.
NOTE:
Report the date when the cleaning has been done. This to show to the Health Authorities in case of check.
Cleaning sequence may be directed by local legislation or as recommended by the Carlsberg Breweries A/S
service technicians.
HUMAN INTERFACE:
Beverage Mode:
Device is waiting for cleaning
or rinsing process by pressing
corresponding button.
Cleaning Mode:
After the default specified 20 minutes
cleaning, the device allows the operator
to switch to rinsing process by pressing
the corresponding button.
Rinsing Mode:
With 10 minutes, delay in Rinsing Mode
and according to requirement’s it is possible
to switch to Beverage or Cleaning Mode
by pressing the corresponding button.

12 13
5.0 TROUBLE SHOOTING
5.1 FAILURE INTRO / MODES
5.2 WARNINGS
To manage the Equipment see instructions cards on cleaning modules
and keg modules, There is also provide a report to note the date of
installation (by Technician) and the cleaning process date (by Customer).
The following warnings can appear, see dedicated operation manual for cleaning module.
• CLEANING UNIT BLOCKED (with message: “error compressor” on the display)
The pressure is low on all keg modules, on the display of the cleaning unit there’s a message stating
“compressor error”.
CLEANING UNIT BLOCKED (With message: “No cleaning” on the display)
Cleaning unit does not work, on the display the picture of a the cleaning symbol bottle will appear.
NO PRESSURE ON KEG MODULES (compressor can’t fill the air)
No pressure on keg modules. One or more keg module doesn’t reach the right pressure.
5.3 OTHER FAILURES
Failures that can appear during the equipment life time or if exposed to misuse.
• WATER LEAKAGES.
Shut of the water valve and contact Technician.
NO INFO ON DISPLAY
Turn of power and turn it on again, still no Info on display contact Technician.
BUMPER RING DEFECT.
Contact Technician for new one.
GASKETS DIRTY.
Wipe the gasket clean with a clean damp cloth and do not leave any particles on a gasket if noticed,
they could result in microleaks and defects.
6.1 APPENDIX A
UNIT DRAWING/DIAGRAM
6.0 APPENDIX

14 15
6.3 APPENDIX C
EU DECLARATION
6.2 APPENDIX B
COPY OF MARKING PLATE
(Placed visible on the equipment)

16 17
1
8
0
°
1
8
0
°
10
psi
0
1
2
3
4
bar
30
50
10
psi
0
1
2
3
4
bar
30
50
10
psi
0
1
2
3
4
bar
30
50
OK!
NO!
STORE THE KEGS AT
TEMPERATURES BELOW 35° C
9.1 9.2
MODULAR 20 INSTRUCTIONS FOR CHANGING A KEG
01
Depressurise the keg by
pulling the pin upwards to
the automatic stop. Make
sure that the pin is in the
position shown in the image.
06
Lean the keg against the pres-
sure module as shown in the
image, raise it up and slide it
into the pressure module.
CAUTION! Do not force
to fix the keg in the module
and do not turn it.
02
Check the system
pressure before
opening the cover.
07
The new keg is now
correctly positioned.
03
When it is depressurised,
rotate the cover a half-turn
anticlockwise.
08
Return the cover
to its position.
04
Remove the cover
from its position.
09
Rotate the cover a half-turn
clockwise. When starting to
close the cover, pay attention
to the starting point
(detail in the image).
To close the cover, pull the pin
upwards and guide the cover
until it is closed (9.1 - 9.2).
05
Get a new keg and
remove the plastic
protection.
10
The cover is closed correctly if
you hear a click and the closing
pin is in the initial position. At this
point, the system automatically
reaches service pressure.
CAUTION! The beer will be ready
for dispensing when the gauge
reaches 3 bars. This will take
approx. 20 seconds.
HANDLING THE KEG
PREVENTIVE MAINTENANCE
If there is beer resi-
due in the pressure
module, clean it with
water and mild soap.
If there is stagnant
water, remove the
rubber stopper as
shown in the image.
Every month, remove the cover seal and clean it with
tap water. Replace it without drying it. To ensure
correct positioning, insert a finger into the seal and
position it correctly using circular movements.
CAUTION! Once the keg has been inserted into
the pressure module, it may not be removed. If it is
removed for any reason, a new keg must be inserted.
CHANGING KEG
Version 3.0
CAUSES PROBLEMS SOLUTIONS
No beer
comes out
of the tap
The pressure
module does
not reach ser-
vice pressure
The cover
does not
close
The beer
is pouring
slowly
The beer
is cloudy The beer is
warm and/or
too frothy
The beer
quality has
been com-
promised
Beer is
leaking onto
the floor
The beer
has no
head
The keg is empty. Insert a new keg.
The cover seal is dirty or damaged.
The cover is not closed correctly.
The cover seal or the keg
is not positioned correctly.
Beer is leaking within
the pressure module.
The pressure is insucient or
the flow regulator is not open.
The beer is past its best before date.
The beer is not being
cooled correctly.
The cleaning cycle has not been
carried out frequently enough.
The glass was not cleaned correctly.
The air circuit is leaking.
The keg is empty. Insert a new keg.
Wait 30 seconds. If the system does not reach service pressure,
check the cover seal.
Remove the cover, check that the keg and the cover seal
are positioned correctly, close the cover again.
Empty the drip tray and reposition the keg. Contact Carlsberg
Technical Customer Services if the problem persists.
Check that the manometer is displaying the correct pressure
and that the flow regulator is open.
Check the beer’s expiry date. If it has expired, change the keg;
if not, carry out a cleaning cycle.
Check that the cooling system is working correctly (if it was not
active, it will take 3-4 hours for the beer to cool); if not, contact
Carlsberg Technical Customer Services.
Check the date of the last cleaning cycle; carry out a new
cleaning cycle and taste the beer.
Only use glasses that have been cleaned with detergents
designed for use with beer glasses; clean them separately
from other tableware.
Contact Carlsberg Technical Customer Services.
IF THE PROBLEM PERSISTS DESPITE THE ABOVE INSTRUCTIONS,
PLEASE CONTACT CARLSBERG TECHNICAL CUSTOMER SERVICES.
Version 3.0
MODULAR 20 SOLVING TECHNICAL PROBLEMS
6.4 APPENDIX D
INSTRUCTION FOR CHANGING A KEG

18 19
B
eve
r
age
Cleani
n
g
Rinsing
Beverage
Cleaning
Rinsing
EVERY 6 WEEKS WHEN NECESSARY
Version 3.0
MODULAR 20 CLEANING CYCLE
01
Remove the empty
container.
04
Fit the filter on the suction
hose and pass the tube
through the stopper
of the container.
02
Remove the stopper
of the new container.
05
Screw the stopper
and tube onto the
container.
03
Clean the filter, the valve and the
suction hose: Use hot water only.
Do not use detergents.
Wear protective goggles.
06
Position the detergent
container in its specified
location. The cleaning cycle
can now begin.
3. FILLING THE LINES WITH BEER
2. RINSING PROCEDURE
1. CLEANING PROCEDURE
1 Place a sign at the tapping point that indicates that a cleaning cycle is in progress.
2 Open the water inlet valve.
3 Press the Clean button ( ).
4 At the tapping point, open the taps one by one.
5 The pipes are emptied of beer and detergent starts to emerge. It is green. Close the tap and open the
next one. Repeat this procedure for all taps. Repeat the procedure from the first tap until the colour
of the detergent is purple (it may be necessary to repeat the procedure more than once for an indivi-
dual tap). NOTE During the cleaning procedure, the container for the mixture is cyclically filled
and the flow of detergent is stopped for approx. 40 seconds as it fills. This is a normal part of the
procedure – do not close the tap and the cleaning procedure will continue.
6 When the detergent changes colour and becomes purple at all taps and the display flashes,
wait at least 20 minutes before moving on to phase 2.
7 Move on to phase 2.
NOTE Only detergent approved by Carlsberg may be used. The use of any other detergent could
damage the system and cause safety issues.
In the final phase, the lines are drained of water and prepared for tapping of the beer.
1 Press the beer button (X).
2 Close the water inlet valve ( ).
3 Open the taps one by one.
4 Water comes out first, followed by beer.
5 Now you can begin tapping the beer.
NOTE Remember to note the date of every cleaning cycle on the report.
SAFETY STANDARDS
If the detergent accidentally comes into contact with the eyes, rinse immediately
with plenty of water and, if necessary, consult a doctor. If possible, show them the
label / Wear protective clothing, gloves and a mask to protect the face and eyes /
The liquid detergent and its container are to be treated as toxic waste.
1 Press the rinse button ( ). This mode stops the flow of detergent and rinses the lines with
water. This rinsing procedure must be carried out accurately to ensure that every residue of
detergent is removed before moving on to the next step. Allow the water to flow until it is
completely clean and transparent.
2 The display flashes when the rinsing procedure is finished. Move on to phase 3.
NOTE The rinsing procedure can also be used separately to rinse the system with water
before the complete cleaning cycle.
REPLACING THE DETERGENT CONTAINER
The display flashes alternately blue and green. The container for the mixture is filled in beer
mode > the water valve is not closed correctly.
If the machine temperature rises above 65°, the compressor switches o and a thermometer
symbol appears on the display.
The process is stopped if there is insucient detergent in the container during cleaning.
For the procedure to resume, check the detergent container and the peristaltic pump.
The display flashes alternately red and white.
If cleaning is due while the machine is in operation, the beer block alarm appears on the display.
The display flashes alternately red and white.
The display flashes alternately red and white.
1 The compressor doesn't start due to an unstable current.
2 The compressor continues to function for 15 minutes, causing loss of air
or a malfunction of the pressure sensor.
If the display flashes alternately red and white:
1 The peristaltic pump is blocked.
2 The peristaltic pump is defective.
If a cleaning procedure is overdue, an alarm is shown on the display and the beer block
is activated. If it is not possible to carry out a cleaning procedure, the system permits
an additional day once only. The display flashes alternately red and white.
Close the valve/water inlet tap. Clean the water valve with compressed
air and, if necessary, contact Carlsberg Technical Customer Services.
The compressor restarts when the temperature goes below 50°.
Replace the detergent container.
Carry out a cleaning procedure.
Restart the machine. Contact Carlsberg Technical Customer Services
if the problem persists.
Check the pump and, if necessary, contact Carlsberg Technical
Customer Services.
Carry out a cleaning procedure immediately.
IF THE PROBLEM PERSISTS DESPITE THE ABOVE INSTRUCTIONS,
PLEASE CONTACT CARLSBERG TECHNICAL CUSTOMER SERVICES.
MODULAR 20 SOLVING TECHNICAL PROBLEMS
SCREEN WARNING CAUSES SOLUTION
Version 3.0
6.5 APPENDIX E
CLEANING CYCLE

DRAUGHTMASTER
Carlsberg Breweries A/S
100 Ny Carlsberg vej
1799 Copenhagen V
Denmark
www.draugthmaster.com
Table of contents
Popular Brewing System manuals by other brands
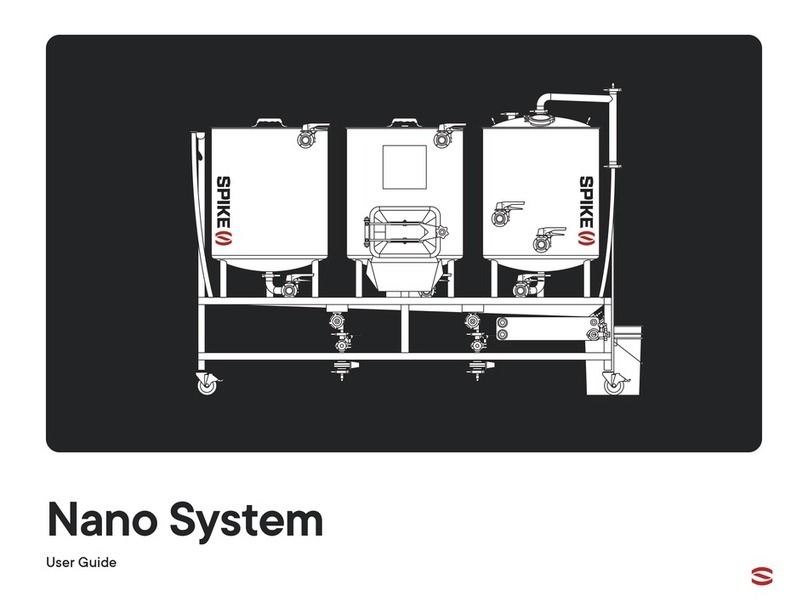
Spike
Spike Nano System user guide
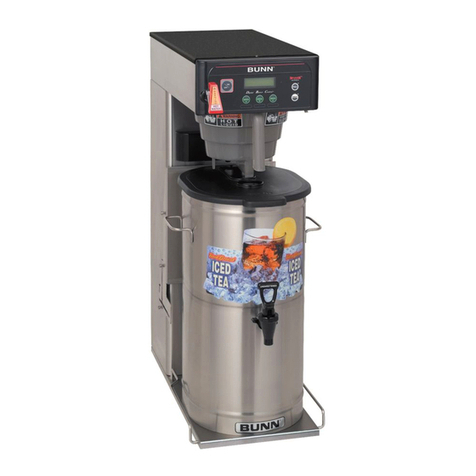
Bunn
Bunn ITCB Single Series Technical training
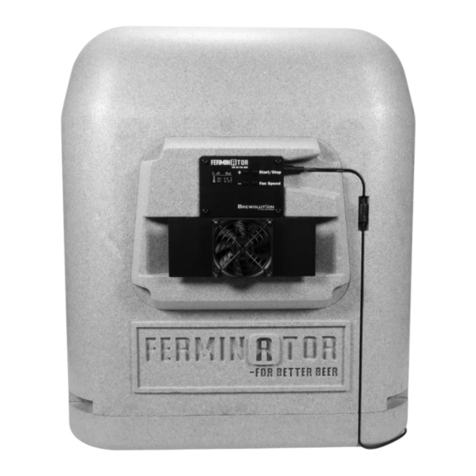
Brewolution
Brewolution FERMINATOR M07-2 instruction manual
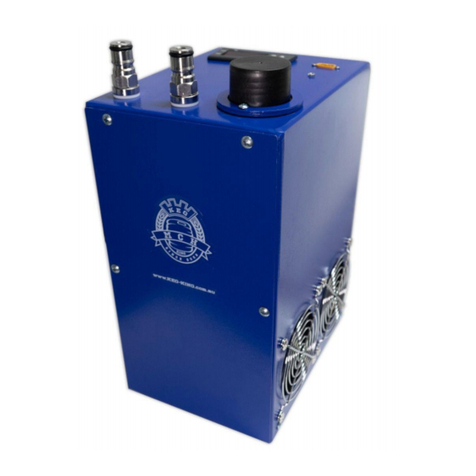
Keg King
Keg King Thermentor King User instruction manual
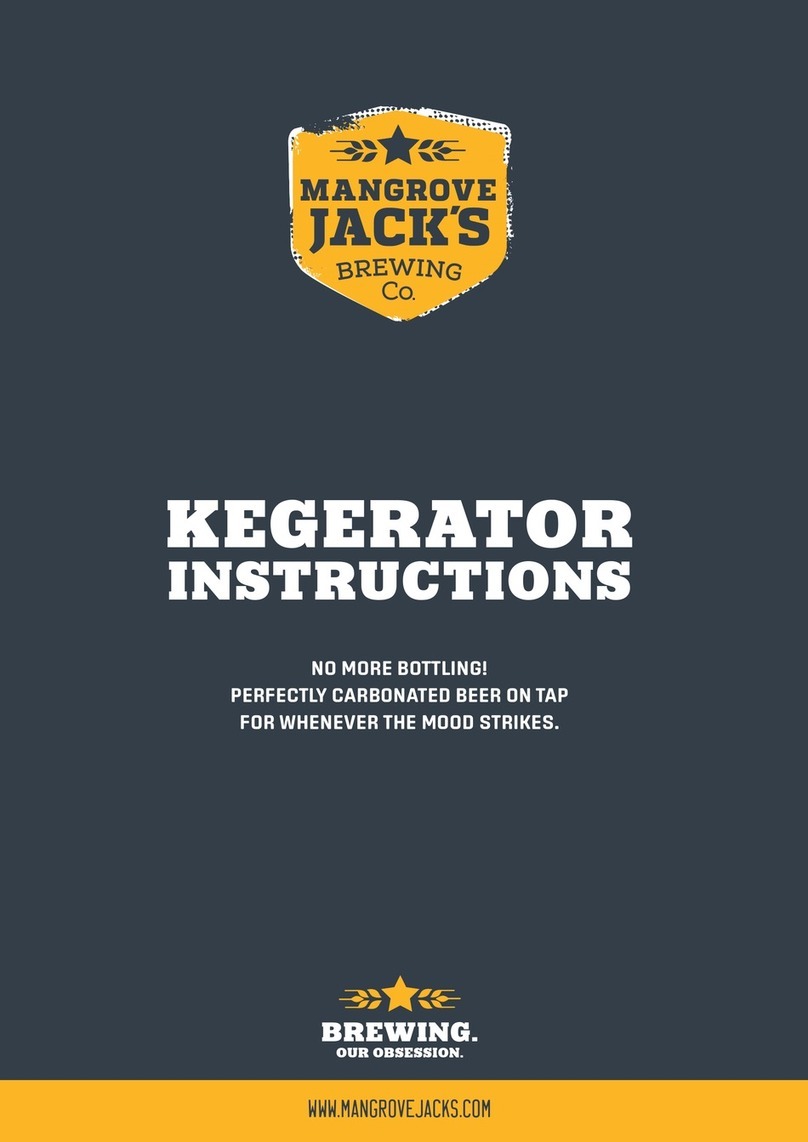
Mangrove Jack's
Mangrove Jack's Kegerator Series instructions
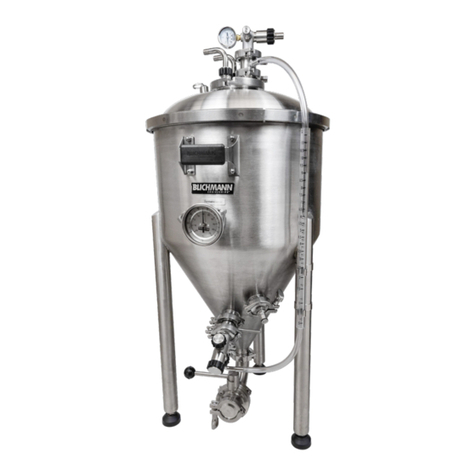
Blichmann Engineering
Blichmann Engineering Fermenator G4 Assembly operation maintenance