Drehmo i-matic User manual

MODBUS loop redundant board
for i-matic actuators
Complementary operating manual
for devices with MODBUS loop redundancy
INFORMATION
This installation manual has to be used in conjunction
with the actuator operating manual!
This manual must be kept for future use.

Document history
File revision
Date
Changes
0 2009-11-15 First release (T-OF)
1 2013-09-06 Description of revised process image. FO signals added. Command STOP added. Enable
signals and ESD signal moved. (T-OF)
2 2014-07-07 Added description for firmware download via IrDA interface. Changed pictures of interface board
to current version. Updated descriptions for diagnosis LEDs. (T-OF)
Update Bus connection
3 2016-02-18 Added signal ESD active to process image, starting with FW rev. V2.02.0010. (T-OF)
Contact
DREHMO GmbH
Zum Eichstruck 10
57482 Wenden
Germany
Service
Tel.: +49 2762 9850-206
Fax: +49 2762 9850-205
E-Mail: drehmo@drehmo.com

DREHMO – i-matic Modbus loop redundant board page 3 of 32
Complementary operating manual
Table of contents
1 Warnings and notes ............................................................................................................... 5
1.1 Standards / directives....................................................................................................... 5
1.2 Commissioning (Electrical connection) ......................................................................... 5
1.3 Maintenance ...................................................................................................................... 5
1.4 Warnings and notes.......................................................................................................... 5
2 Preface................................................................................................................................... 6
2.1 Structure of the interface board ...................................................................................... 6
2.2 Repeater feature ............................................................................................................... 6
2.3 Transmission technique/Physical layer ......................................................................... 7
2.4 Protection functions / Data secure mechanisms.......................................................... 7
3 Electrical connection .............................................................................................................. 8
3.1 Mains connection (Standard) .......................................................................................... 8
3.2 Bus connection (Standard).............................................................................................. 8
3.3 Shield connection.............................................................................................................. 9
3.4 Bus termination ................................................................................................................. 9
3.5 Lightning protection (option)............................................................................................ 9
3.6 Bus cable.......................................................................................................................... 10
4 Jumper / LED’s of the interface board .................................................................................. 11
4.1 Location of the components on the interface board.................................................. 11
4.2 Connectors....................................................................................................................... 12
4.3 Diagnosis LED’s.............................................................................................................. 12
4.3.1 LED RES................................................................................................................... 12
4.3.2 LED DBG .................................................................................................................. 12
4.3.3 LED CAN................................................................................................................... 12
4.3.4 LED CH1................................................................................................................... 13
4.3.5 LED BA1+BA2.......................................................................................................... 13
4.3.6 LED DX1+DX2 ......................................................................................................... 13
4.4 Diagnosis via LCD Display of the actuator ................................................................. 13
5 Communication specific parameters MODBUS RTU ............................................................ 14
5.1 Communication parameters MODBUS RTU .............................................................. 14
5.1.1 Parameter settings using the display ................................................................... 14
5.1.2 Parameter settings using a parameterization tool.............................................. 18
6 MODBUS ............................................................................................................................. 19
6.1 MODBUS protocol layer................................................................................................. 19
6.1.1 Supported function codes....................................................................................... 19
6.1.2 MODBUS addressing model.................................................................................. 19
6.1.3 Valid Offsets/Subfunction codes ........................................................................... 20
6.2 Cyclic data........................................................................................................................ 22
6.2.1 Input register............................................................................................................. 22
6.2.2 Output register ......................................................................................................... 24
6.3 Special function codes ................................................................................................... 26
6.3.1 Read exception-Status (Function code 07)......................................................... 26
6.3.2 Report Slave ID (Function code 17) ..................................................................... 26
7 System functions.................................................................................................................. 27

DREHMO – i-matic Modbus loop redundant board page 4 of 32
Complementary operating manual
7.1 Firmware download ........................................................................................................ 27
7.1.1 Required items......................................................................................................... 27
7.1.2 Step by step description ......................................................................................... 28
7.1.3 Firmwaredownload using IrDA Converter............................................................ 31
8 Appendix .............................................................................................................................. 32
8.1 Reference......................................................................................................................... 32

DREHMO – i-matic Modbus loop redundant board page 5 of 32
Complementary operating manual
1 Warnings and notes
1.1 Standards / directives
DREHMO products are designed and manufactured in compliance with recognized standards and
directives. This is certified in a declaration of incorporation and a declaration of conformity.
The end user or the contractor must ensure that all requirements with respect to assembly,
electrical connection, and commissioning at the place of installation are met.
They include among others:
•Applicable configuration directives for fieldbus applications.
•National regulations, laws, and prescriptions.
1.2 Commissioning (Electrical connection)
During operation of electrical devices it is unavoidable that certain parts carry dangerous voltages.
All personnel working with this device must be familiar with the safety and warning instructions in
this manual and observe the instructions given. Safety instructions and warning signs on the
device must be observed to avoid personal injury or property damage.
1.3 Maintenance
Maintenance directives have to be carefully attended. Otherwise a safe operation of the actuator
or control unit can’t be assured.
1.4 Warnings and notes
Read these instructions carefully before installation and commissioning. Failure to follow them
may lead to personal injury or to material damage.
The following signs draw special attention to safety-relevant procedures in these operation
instructions:
This symbol signifies „additional information“.
Failure to observe may lead to damage occurring.
This symbol signifies „attention“.
Failure to observe may result in damage and personal injury.
This symbol signifies „warning!“
Failure to observe may result in damage and severe personal injury.

DREHMO – i-matic Modbus loop redundant board page 6 of 32
Complementary operating manual
2 Preface
2.1 Structure of the interface board
The MODBUS interface board DiM-17 is equipped with two galvanically separated autonomous
RS485 interfaces. In conjunction with the integrated powerful controller a reapeater functionality is
given. This allows to extend the RS485 communication over larger distances.
In addition the board is equipped with a relay which connects the attached segments in case of a
loss of the repeater functionality to increase the availability.
Controller
DUART
2.2 Repeater feature
The repeater within each interface separates the network into segments. Each connection
between two actuators can therefore be seen as a single point to point connection. The repeater
reconditions the MODBUS signal with a delay of 0.5 tBit.

DREHMO – i-matic Modbus loop redundant board page 7 of 32
Complementary operating manual
2.3 Transmission technique/Physical layer
Data is transmitted by means of a physical connection over a twisted pair two wire cable. The
interface board supports transmission rates up to 115200 Baud.
Bus access is handled in master/slave mode. Only one master can be active at a time (Mono
master mode). The master acts with polling mode and a request / response cycle.
In one master system theoretically 247 slaves can be addressed.
The used protocol is MODBUS RTU.
2.4 Protection functions / Data secure mechanisms
As protection mechanisms against data violation MODBUS RTU implements a parity check for
each byte and a 16 bit CRC for every MODBUS telegram.
In addition a watchdog within the slaves monitors the correct connection to the master. The
behavior of the actuator as well as the timeout value is parameterizable.
The master should also implement a communication monitoring resulting in a failure signalization
in case of communication loss or malfunction.

DREHMO – i-matic Modbus loop redundant board page 8 of 32
Complementary operating manual
3 Electrical connection
3.1 Mains connection (Standard)
Work on electrical equipment and electrical installation work on actuators must be
carried out by electricians or under supervision by fully qualified engineers, in
accordance with the valid electrical regulations.
Wiring should be carried out according to the enclosed wiring diagram. All control
cables shall be shielded to guarantee the electromagnetic compatibility of the
actuator. The main power cable need not be shielded.
The overcurrent protection of the actuator has to be installed inside the power
network. For rated values, see design data.
Pay special attention to the grounding of the actuator (refer to wiring diagram). Electrical
protection is not obtained until all covers are closed.
3.2 Bus connection (Standard)
Wiring is carried out according to the wiring diagram supplied with the actuator. The locations of
the connection terminals are shown in the following picture:
channel 1
shield
channel 1
shield
channel 2
channel
2
diagnosis
channel 1
diagnosis
channel 2

DREHMO – i-matic Modbus loop redundant board page 9 of 32
Complementary operating manual
Connection data:
Strip length: 9 mm
Wire insertion angle relative to PCB: 45°
Connection technology: Phoenix Contact PTSA 1,5/ 2-3,5-Z
Cross section (solid-conductor): 0.5 to 1.5 mm²
Cross section (multi-conductor): 0.5 to 1.5 mm²
Cross section (multi-conductor): 0.5 to 1 mm² (ferrule without plastic shroud)
Pay attention to the ESD protection of the bus circuit board. Especially good personal
earthing is required.
If the bus circuit board is disassembled from its housing transport and storage must
meet ESD requirements.
3.3 Shield connection
The strain-reliefs in front of the terminal connections for the fieldbus can be used to connect the
cable shields to ground instead of the preferred usage of EMC cable glands.
3.4 Bus termination
RS485 networks have to be terminated at the beginning and the end of a segment, to avoid
reflections on the line and for a conditioning of the signals. The termination is automatically
controlled by the loop redundant interface itself depending on the communication state. Therefore
a separate switch for controlling the terminators is obsolete.
3.5 Lightning protection (option)
The connection board can be equipped with dedicated components for lightning protection as an
option.

DREHMO – i-matic Modbus loop redundant board page 10 of 32
Complementary operating manual
3.6 Bus cable
Only cables according to the specification for RS-485 (MODBUS RTU) should be used: 1
Impedance 135 to 165 Ohm, at a test frequency of 3 to 20 MHz
Line capacity < 30 pF per meter
Wire diameter > 0,64 mm
Wire gauge > 0,34 mm² (equivalent AWG 22), max. 1,5 mm²
Loop impedance < 110 Ohm per km
Shielding Copper mesh screen or mesh screen with foil screen
Respect a distance of minimum 20 cm between the bus cable and other cables. If possible, bus
cables should be laid in a separate, conductive, and earthed cable tray.
Make sure to avoid potential differences between the individual devices on the bus (perform a
potential equalization).
There is not standardized color marking for RS485 wiring.
Usually the marking is a follows: P/B = brown and N/A = white
The maximum values at a given transmission rate in conjunction with the above given cable
parameters are as follows:
Bit
rate [kbit/s]
Bit time
Max.
s
egment
leng
t
h
[m]
Max.
stub length
[m]
300 3.3 ms 1200 500
600 1.7 ms 1200 500
1200 833.3 µs 1200 500
2400 416.7 µs 1200 500
4800 208.3 µs 1200 500
9600 104 µs 1200 500
19200 52 µs 1200 500
38400 26 µs 1200 100
57600 17.36 µs 1200 100
115200 8,68 µs 1000 33
1See reference: ‚Modbus over serial line’

DREHMO – i-matic Modbus loop redundant board page 11 of 32
Complementary operating manual
4 Jumper / LED’s of the interface board
4.1 Location of the components on the interface board

DREHMO – i-matic Modbus loop redundant board page 12 of 32
Complementary operating manual
4.2 Connectors
The interface board is equipped with several connectors. The function of the connectors is as
follows:
Connector
Meaning
Description
X1 TEST Test connector for diagnosis purposes via a signal converter
and a terminal program. Also the firmware update of the
interface board can be done via this connector.
X2 HOST Connector to host system. The power supply and the
communication with the host system is done via this
connector. To ensure a secure communication to the host
system the pins 1-2 and 3-4 must be shortened with a
jumper.
X4 RS485 CH2 RS485 interface channel 2.
X5 RING/LWL Connector for other components. E.g. a fiber optics converter
or a bus interface board can be connected via this plug.
X6 RS485 CH1 RS485 interface channel 1.
4.3 Diagnosis LED’s
4.3.1 LED RES
This LED indicates the state of the RESET signal of the controller. Is this LED off the RESET
signal is activated. A normal program flow is not possible in this case. For a correct execution of
the application the LED has to be constantly on.
4.3.2 LED DBG
This LED indicates the correct program execution flow with a flash rate of 1Hz. If the LED keeps
off, the user program is not executed. In this case the interface board either has a malfunction, the
firmware is missing or the bootloader mode for a firmware download is activated.
4.3.3 LED CAN
This LED indicates the state of the CAN communication to the main board. If this LED is
constantly on, the communication is carried out with no failure. If this LED is off the
communication is disturbed.

DREHMO – i-matic Modbus loop redundant board page 13 of 32
Complementary operating manual
4.3.4 LED CH1
The LED indicates the primary channel from which commands are accepted. If LED CH1 is on
then channel 1 is the primary channel. If the LED is off channel 2 is the primary channel.
4.3.5 LED BA1+BA2
This LED’s indicate active MODBUS bus communication over the respective channel. The LED is
on if valid Modbus telegrams with correct checksum are detected on the respective channel.
(Valid baudrate and framing)
4.3.6 LED DX1+DX2
This LED’s indicate valid Modbus communication to the own address. This LED is on if valid
Modbus telegrams to the own address are received from the respective channel.
(Data exchange)
4.4 Diagnosis via LCD Display of the actuator
In addition to signalize the communication state via the LED’s, the state is graphically indicated on
the LCD display of the actuator. When using the loop redundant MODBUS interface 2 symbols
are shown whereas the upper one icon indicates the state of channel 1 and the lower one the
state of the channel 2.
The active channel (channel from which signals will be used to control the actuator) is displayed
inverse (meaning bright icon on dark background).
Symbol
Meaning
Bus not connected or wrong baud rate is selected, no valid MODBUS telegrams
detected.
Bus ok, valid MODBUS telegrams detected. Slave is not addressed directly by the
master via this channel.
Bus ok, the slave is addressed directly by the master via this channel.
F
i
eldbus
state

DREHMO – i-matic Modbus loop redundant board page 14 of 32
Complementary operating manual
5 Communication specific parameters MODBUS RTU
Each device in the MODBUS is accessed via its fieldbus address (Field device address). For each
bus system this address has to be unique. When delivered to the customer the address is set to
the default value of 247. It is possible to specify another address via customer specific
parameterization upon request during ordering process.
5.1 Communication parameters MODBUS RTU
BUS-Address: 1 to 247
Transmission
rates:
300, 600, 1200, 2400, 4800, 9600, 19200, 38400, 57600, 115200 Bit/s
Parity: According to MODBUS RTU specification
Even parity or odd parity with 1 stop bit
No parity with 2 stop bits
In addition the stopbits can be parameterized to a non specification
conform value.
Connection
watchdog timeout:
0,1 to 25,5 s
Frame per byte: 1 Start bit + 8 Data bits + 1 Parity Bit + 1 Stop bit or
1 Start bit + 8 Data bits + 2 Stop bit,
The communication specific parameters are set „non-intrusive“ via the actuators local operation
display or via a parameterization tool. The parameters are stored in an EEPROM to prevent from
loss in case of power failure.
MODBUS does not support an automatic detection of the communication parameters. Therefor
the settings within the device have to match those of the host (master).
The communication settings are also used to re-condition the bus signals by the repeater. For this
reason correct communication settings are also essential for a reliable repeater function.
Default values:
Address 247, 38400 Bit/s, no parity, 2 stop bits, Watchdog timeout 5s.
5.1.1 Parameter settings using the display
The MODBUS specific parameters can be set using the actuators display. The parameters can be
found beneath the menu item
Menu -> Parameter -> DCS/PLC System -> Interface -> MODBUS
For further information regarding the operation of the display please refer to the i-matic instruction
manual.
5.1.1.1 Primary slave address
Description This parameter defines the address with which the primary channel of the
modbus interface can be addressed.

DREHMO – i-matic Modbus loop redundant board page 15 of 32
Complementary operating manual
Range 1..247
Remark The value 247 is reserved for new devices and should not be used in a real
installation.
5.1.1.2 Secondary slave address
Description This parameter defines the address with which the secondary channel of the
modbus interface can be addressed.
Range 1..247
Remark The value 247 is reserved for new devices and should not be used in a real
installation. The secondary address is only used with the master/slave version
of the interface.
5.1.1.3 Automatic configuration
Description With this setting the automatic bus configuration can be enabled. If the
automatic configuration is enabled the communication speed (Baudrate) and
address settings will be detected automatically.
Range Disabled / Enabled
Remark The automatic configuration will only work with the loop redundant version if
the interface. With all other versions this item will be ignored. If the automatic
configuration is enabled the following parameters are obsolete:

DREHMO – i-matic Modbus loop redundant board page 16 of 32
Complementary operating manual
- Primary / secondary slave address
- Baudrate
- Parity
- Stopbits
The automatic configuration will only work with a serial frame of 11 bits / even
parity and 1 stopbit.
The detected communication settings will be stored in the interface memory.
After a restart of the interface the settings will be used for communication.
The detected communication speed and slave address can be determined in
the menu tree Actual values / Diagnosis.
5.1.1.4 Reset automatic configuration
Description Resets the detected communication settings and starts the automatic
detection.
Range No / Yes
Remark To restart the detection the entry Yes has to be selected. If the reset was
recognized by the control logic the display will return to No.
5.1.1.5 Baudrate
Description Communication parameter speed.
Range 115200 / 57600 / 38400 / 19200 / 9600 / 4800 / 2400 / 1200 / 600 / 300
Remark This parameter will be ignored if the loop redundant version is selected and
the automatic configuration is enabled.

DREHMO – i-matic Modbus loop redundant board page 17 of 32
Complementary operating manual
5.1.1.6 Parity
Description Communication parameter parity.
Range None / Even / Odd
Remark This parameter will be ignored if the loop redundant version is selected and
the automatic configuration is enabled.
5.1.1.7 Stopbits
Description Communication parameter stopbits.
Range 1 .. 2
Remark This parameter will be ignored if the loop redundant version is selected and
the automatic configuration is enabled.
5.1.1.8 Timeout
Description Watchdog time for communication monitoring in 0.1s. After expiration of this
time the actuator will execute the parameterized fail safe reaction.
Range 1..255 x 0.1s
Remark

DREHMO – i-matic Modbus loop redundant board page 18 of 32
Complementary operating manual
5.1.1.9 Redundancy
Description With this parameter the interface is adapted to different redundancy concepts.
Range Loop / Line reply act. Channel / Line reply both channels / Master/Slave
Remark - Loop: Interface acts like a repeater. Connection between two devices
can be seen as a point to point connection. The loop starts at the
master going to every device and ends at the master.
- Line reply act. channel: The interface can be accessed over two
independent connections with the same address. The reply of the
device will only be issued over the request channel.
- Line reply both channels: The interface can be accessed over two
independent connections with the same address. The reply of the
device will issued over both channels.
- Master/Slave: The interface is equipped with two independent modbus
channels. The addresses of the channels can be set individually.
5.1.2 Parameter settings using a parameterization tool
In addition to set the parameters using the display, parameters can also be set via the
parameterization tool i-matic Explorer.

DREHMO – i-matic Modbus loop redundant board page 19 of 32
Complementary operating manual
6 MODBUS
For commissioning of a MODBUS slave usually no specific configuration of the master my means
of a configuration file is necessary. The MODBUS RTU transmission is based on a simple
protocol which consists of the slave address, a function code, address values, payload and
checksum.
6.1 MODBUS protocol layer
6.1.1 Supported function codes
Function
Function
-
code
Meaning
Write Single Coil 05 (0x05) Sets a single bit in the slave to ON or OFF
Write Multiple Coils 15 (0x0F) Sets a count of continuous bits in the slave to ON or
OFF
Read Coils 01 (0x01) Reads back the state of continuous output bits back
from the slave
Read Discrete Inputs 02 (0x02) Reads back the state of continuous input bits from
the slave
Write Single Register 06 (0x06) Writes data (16bit) to a single holding register in the
slave
Write Multiple Register 16 (0x10) Writes a count of data (x times 16bit) to continuous
holding registers in the slave
Read Input Registers 04 (0x04) Reads the data from continuous input (16 bit)
registers in the slave
Read Holding Registers 03 (0x03) Reads back a count of data (x times 16bit) from
continuous holding registers in the slave
Read Exception Status 07 (0x07) Reads the content of 8 exception status outputs of
the slave
Diagnostics 08 (0x08) Diagnostic functions for checking the communication
status between master and slave
Report Slave ID 17 (0x11) Reads identification information from the slave for
stand alone configuration of the master
6.1.2 MODBUS addressing model
The MODBUS specification differs between two different addressing modes. The MODBUS data
model address and the MODBUS PDU address which has always an offset of -1 to the MODBUS
data model address. All in this document mentioned addresses are directly specified as the
address which has to be used in the MODBUS PDU. This is the reason that in some cases the
offset of 1 has to be subtracted to access the desired data. The following extract from the
MODBUS standard describes this:

DREHMO – i-matic Modbus loop redundant board page 20 of 32
Complementary operating manual
6.1.3 Valid Offsets / Subfunction codes
Object
Function
codes
Offset (de
cimal
)
Offset (hex)
Coil *) Write Single Coil (05)
Write Multiple Coils (15)
Read Coils (01)
0..262 0..106
Holding
Register
Write Single Register (06)
Write Multiple Register (16)
Read Holding Registers (03)
1000..1002 3E8..3EA
Discrete
Inputs *)
Read Discrete Inputs (02) 0..1028 0..404
Input Register Read Input Registers (04) 1000..1008 3E8..3F0
*) For further use. At present no function.
08 (0x08) Diagnostic
Subfunction
code
Subfunction
Meaning
00 (0x00) Return query data The data passed in the request data field will be
returned within the response (loop back).
10 (0x0A) Clear counter and
diagnostic register
Clear all counters and diagnostic registers. Counters
are also cleared upon power up.
Other manuals for i-matic
1
Table of contents
Other Drehmo Controllers manuals
Popular Controllers manuals by other brands
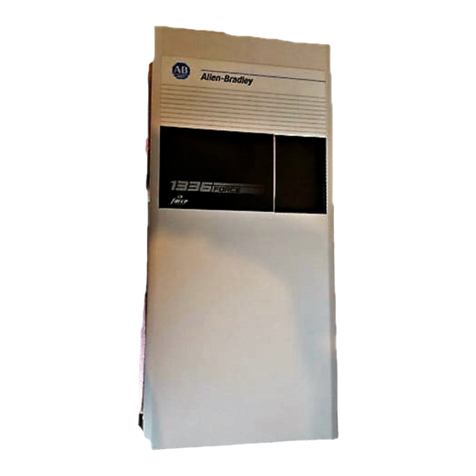
Allen-Bradley
Allen-Bradley 1336 FORCE user manual
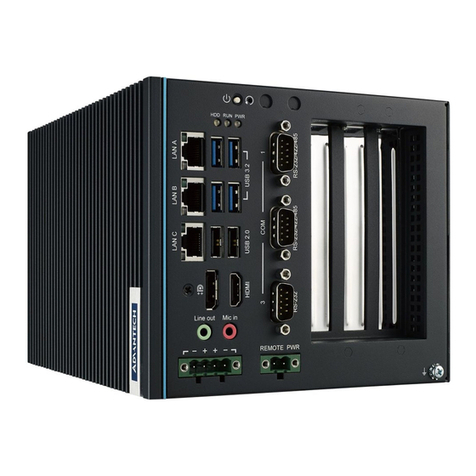
Advantech
Advantech UNO-348 manual

Barco
Barco Sedomat 1500 Specifications
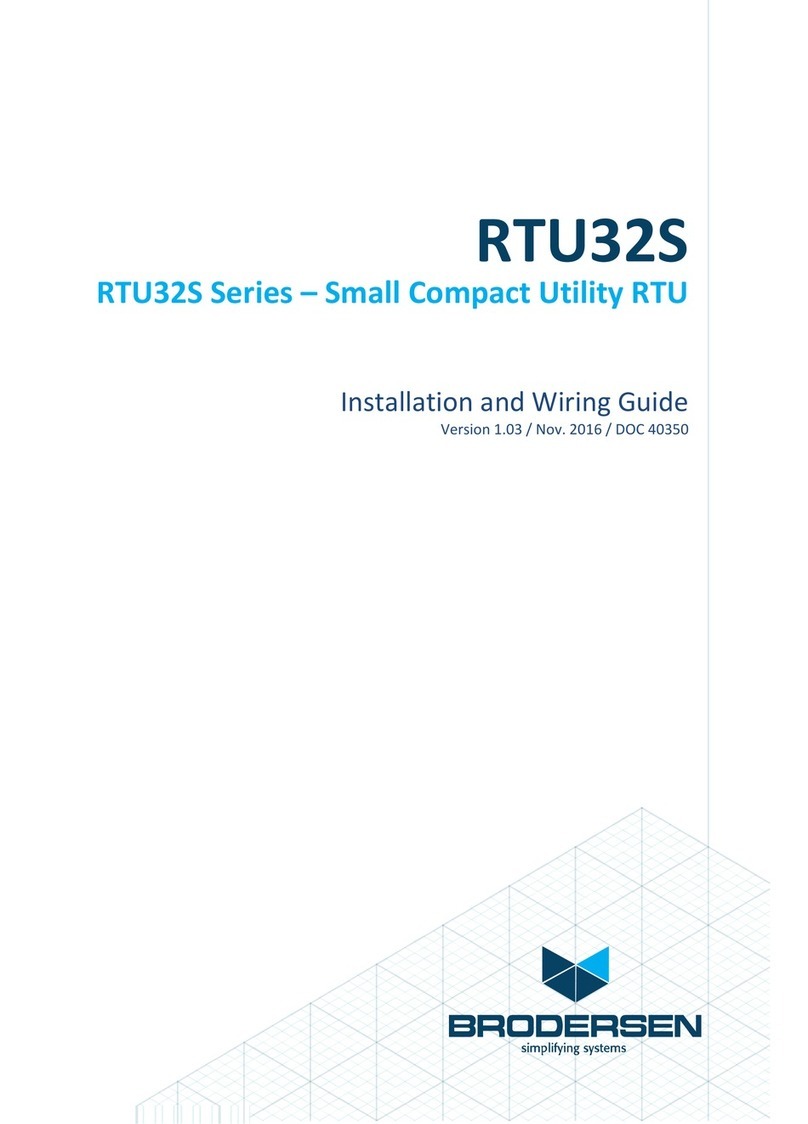
Brodersen
Brodersen RTU32S Series Installation and wiring guide

Baxi
Baxi SILA RCV 300 Installation instructions, Functioning and Maintenance
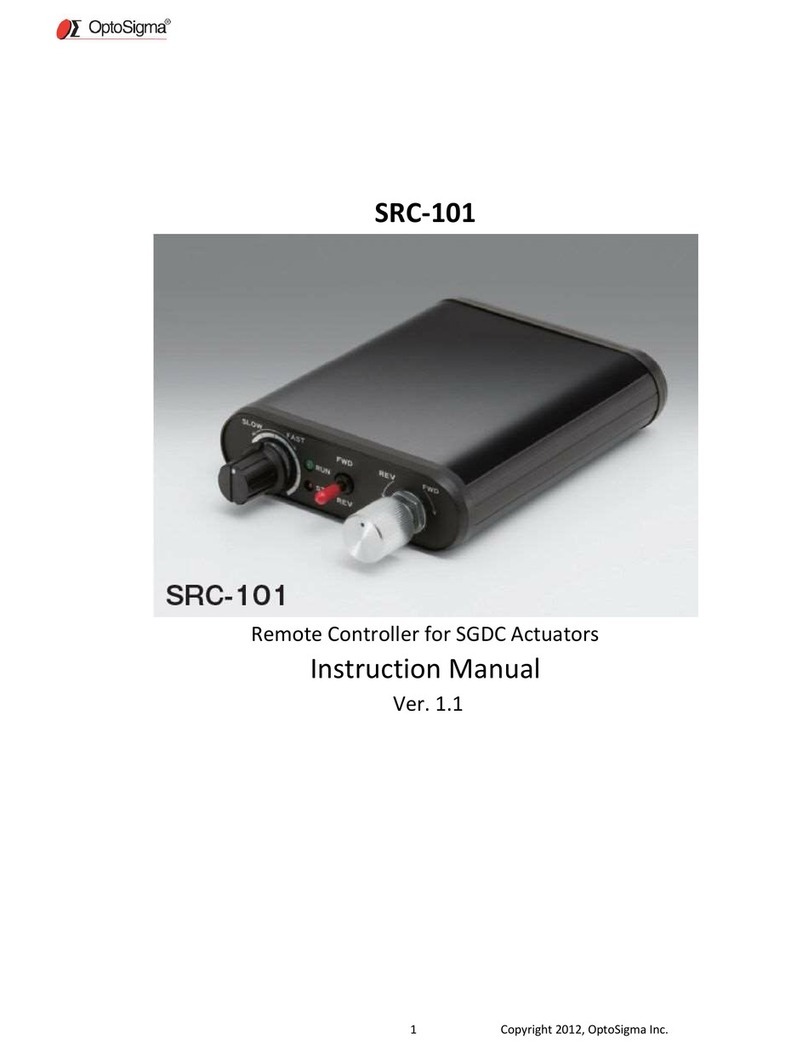
OptoSigma
OptoSigma SRC-101 instruction manual