DV Systems D20 Installation and operation manual

D20, D20VSD, D20TD, D20TDVSD-C
Feb ‘14
- 1 -
Quick Start ……………............................................. 2
Safety Precautions …………………………………… 5
Unpacking and Inspection …………………………... 6
Installation – Mechanical ……………………………. 7
Lubrication ……………………………………………. 9
Installation – Electrical ………………………………. 10
Start-up Procedures …………………………………. 13
Preventative Maintenance Schedule ………………. 14
Common Compressor Faults ………………..………… 16
Variable Speed Drive ………………………….……. 17
Separator Filter & Refrigerated Air Dryer …………. 20
Trouble-Shooting Guide ……………………………… 23
Warranty ……………………………………………….. 26
If you require assistance, please contact your local DV Systems Distributor or Authorized Service
center. You may contact the manufacturer directly as follows:
Phone: (705) 728-5657 Web: www.dvsystems.ca
D20, D20VSD,
D20TD, D20TDVSD
Rotary Screw
Air Compressor
Units
- - -
nstallation
And
Start-up Data
Contents:
Page:
Please read this manual before
installing or using your Air
Compressor Unit. t contains
valuable information that will
help in the receiving,
installation, use, and
maintenance of the Unit.
Please keep this manual in a
safe place for future reference.
All of the information, policies, and
procedures in this reference manual apply
exclusively to DV Systems.

D20, D20VSD, D20TD, D20TDVSD-C
Feb ‘14
- 2 -
18”
36”
18
”
18
”
Quick Start
Mechanical Installation.
(Refer to Page 7)
Shipping Cleats
The Unit should be located in a dry, clean, cool,
dust free, and well ventilated area.
Allow a minimum 18” around and 36” above Unit.
The ambient temperature should be between
10°C and 40°C (50°F and 104°F).
Ensure that the floor under the Unit is smooth,
level and capable of bearing the weight of the
Compressor.
If installed in a compressor room, ensure that
the room is adequately ventilated
Note: Dimensions indicated are typical for all
variations of D20 Series’ Units.
The ‘D20 Series’ Screw Units are
shipped with (3) Shipping Cleats
painted in orange that must be
removed prior to operating the
Unit.
(2) Cleats are located at the Air end /
VFD Housing Mounts.
(1) Cleat is located at the Motor
Mount
(1) Cleat at Motor
(2) Cleats at Air end / VFD Housing Mounts

D20, D20VSD, D20TD, D20TDVSD-C
Feb ‘14
- 3 -
Quick Start (cont’d)
Lubrication.
Rotation.
(Refer to Page 9) (Refer to Page 11)
Check the oil after
the Unit has been at
rest for a minimum
of 30 minutes.
Some Units are not equipped with an ‘Anti
Rotation’ Switch. Operating the Unit in the
reverse direction will cause irreparable
damage.
The Inverter to the Motor is pre-wired at the
factory.
Remove the Front Door and pay close
attention to the arrow located on the Motor
indicating correct rotation. Turn Unit on and
immediately turn off using the Emergency
Stop Button.
If the rotation is not correct, simply change
two of the motor leads to the Inverter.
Oil Fill Plug

D20, D20VSD, D20TD, D20TDVSD-C
Feb ‘14
- 4 -
Quick Start (cont’d)
Unit Operation.
Shown below is the ‘CSC300’ Controller which regulates the operation of the Unit. It is used to start and stop the
Unit, and it provides information as to system pressure, temperature, etc.
Starting the Unit: Press the ‘Start’ Button.
Stopping the Unit: Press the ‘Stop’ Button
Note:
1. Do not stop the Unit using the ‘Emergency Stop’ Button unless there is a danger to the product or of
personnel injury.
2. Do not stop the Unit by use of a disconnect or breaker.
Using the Emergency Stop Button, disconnect, or breaker to stop the Unit will not
allow the Unit to go through an unloading sequence, and could result in damage to
the Motor, Starter, or other electrical components. Damage caused in this manner
is not covered by the manufacturers Warranty.
Enter, Up, Down & Escape
.
Used in the programming and changing
of operating parameters of the Unit.
Emergency Stop
.
Will quickly shut the
Unit off. Is only to be
used in an
emergency.
Digital Readout
.
Indicates Unit pressure,
temperature, etc.
St
op
.
Causes the Unit to
enter ‘Idle’ mode
and then shut off.
St
art
.
Starts the Unit.

D20, D20VSD, D20TD, D20TDVSD-C
Feb ‘14
- 5 -
Safety Precautions
In order to operate the Compressor Unit safely and correctly, we have opted to use the following symbols to make
you aware of important points. These points relate to user safety and preventing equipment problems. Please pay
close attention to these sections.
The following hazards may occur during the normal use
of the equipment. Please read the following chart.
Area: Hazard: Safeguards:
What may occur if precautions are not
observed.
Tampering with the Unit while under Relieve all pressure from the Unit
full or partial pressure may cause an before attempting any repair or
explosion. maintenance work.
As the Unit starts and stops Shut off all power to the Unit before
automatically, serious injury may attempting to repair or maintain
result from working on the Compressor the Compressor.
with the power still in the 'on' position.
As the Unit starts and stops Shut off all power to the Unit before
automatically, do not come into attempting to repair or maintain
contact with moving parts. the Compressor.
Air compressed by the Unit is not Never breath untreated compressed
suitable for inhaling. It may contain air produced by the Compressor.
vapours harmful to your health.
Compressor Air End, Motor, and Never touch the Air End, Motor, or
Tubing become hot when running. Tubing during or immediately after
Touching these areas may cause operation.
serious burns.
As the electrical components on the Do not install in hazardous locations.
Compressor are General Purpose, The Compressor must be a minimum
there is a potential for explosion, should of 20 feet (6.1 meters) from any source
vapours be present in the area. of potentially explosive vapours.
What to look for. How to avoid the hazard.
20FT
6 . 1 m
Important safety Information.
A hazard that may cause
serious injury or loss of life.
Important information that
indicates how to prevent
damage to equipment, or how
to avoid a situation that may
cause minor injury.
Information that you should
pay special attention to.

D20, D20VSD, D20TD, D20TDVSD-C
Feb ‘14
- 6 -
Unpacking and Inspection
It is the responsibility of the receiver of the goods, either the Distributor or Customer, to ensure that the product
has been shipped in full, and has arrived in suitable condition. Damage to the product may not be visible at time
of off-loading, but may only become apparent upon unpacking or start-up.
Some areas to initially check are as follows:
a) Check for damage to the crating and/or packaging.
b) Check the exterior of the Cabinet for damage, either cosmetic or mechanical.
c) If there is mechanical damage, open the Cabinet to determine whether there is any internal
damage to the Unit.
Should there be damage to the product or shortages in shipment:
1) Stop any further unpacking or operation of the product.
2) Make note of the problem on the Freight Bill, should it concern a shortage or visible
damage to the product.
3) Should the damage be noticed only after the product has been received, contact the
transport company immediately to file a claim.
Depending on the problem, it may be wise to photograph the damage. Also, it may
be wise to discuss with the carrier representative the time allotted to give notice of loss
or damage to the product; there may be guidelines which limit timeframes of same.
4) Do not attempt further unpacking or operation of the product. Also, do not discard
any packing material used.
5) A Loss or Damage Claim must be submitted to the carrier and supported by the
following documents:
- Copy of Freight Bill of Lading
- Copy of the Invoice and Estimate to repair, in case of damage
- Damage Report
- Copy of photos, if applicable
Each DV Systems Air Compressor is carefully tested and
inspected before shipment. Though every attempt is made to
ensure the safe and complete shipment of our product, freight
damage or misplacement of goods may occur.
Shipments of DV Systems products are the property of the
Consignee when the products leave our facility. DV Systems Inc.
is not responsible for any damages or shortages caused to the
product after it has left our shipping dock.

D20, D20VSD, D20TD, D20TDVSD-C
Feb ‘14
- 7 -
The Compressor must not be operated in
a confined area where the heat from the
Unit cannot readily escape.
Installation – Mechanical
Moving of the Unit.
When moving the Air
Compressor, the forklift or hand
lift forks go under the Unit from
the directions as indicated.
Please be advised that care
must be taken when moving and
positioning the Units as they are
top heavy.
Loc
ation of the Unit.
Items to consider when installing the Unit are as
follows:
The Unit should be located in a dry, clean, cool,
dust free, and well ventilated area. If possible,
the Compressor should be located in a
separate room or area, away from the general
operations of the shop.
Allow a minimum of 18” around and 3 feet above
the Unit for easy access to the various sides,
this being for both the proper ventilation of the
Unit and ease of servicing.
Ensure that the floor under the Unit is smooth,
level and capable of bearing the weight of the
Compressor. The Compressor must sit
squarely on the floor.
If installed in a compressor room, ensure that the
room is adequately ventilated. (One
Horsepower produces approximately 2500
BTU/HR.) See Pages 8 and 9.
The ambient temperature should be between
50°F and 104°F (10°C to 40°C).
If installing the Unit on a mezzanine, ensure that
the structure can safely support the weight of
the Unit. As well, the sound level of the Unit
may increase due to the harmonics created by
the structure; use Vibration Pads to lessen this.
Many common Compressor problems can be
attributed to the location or installation of the Unit.
Make sure the Unit is in a suitable location, and
installed correctly.

D20, D20VSD, D20TD, D20TDVSD-C
Feb ‘14
- 8 -
Installation – Mechanical (cont’d)
Shown below are items which assist in making a good installation. These are both intake and exhaust ductwork,
helping the Unit to a) draw in clean outside air and b) exhaust the warmer air away from the Unit. The warmer air
may be used, with the inclusion of a damper in the exhaust ducting, to warm the interior of the building during the
colder months of the year.
Intake and Exhaust Ducting

D20, D20VSD, D20TD, D20TDVSD-C
Feb ‘14
- 9 -
Lubrication
Oil Fill Plug
Oil Drain Valve
Oil Drain Tube
Initial Start
-
up.
Each Compressor Unit built is extensively tested at
the factory before shipment. The Unit is shipped with
the original oil in it as used for testing purposes.
Check the Oil level and for any Oil leaks on a daily
basis. This must be done when the Unit is off. Top up
the Oil level on a monthly basis.
Use only DV Systems ‘DEV-3000’ Synthetic Oil. Also,
do not mix the ‘DEV-3000’ with any other lubricant.
Subsequent Oil Changes.
Switch off the unit.
Drain the existing oil from the Unit. (Please be
advised that the Unit cannot be drained fully of oil, as
some oil may remain in various components ie
Cooler, Tubing, etc.)
Fill the reservoir to just below the treads of Oil Fill
Plug. Do not under or overfill. See drawing below.
Use only DV Systems ‘DEV-3000’ Synthetic Oil,
available in both 1 US gallon (3.8 litre) jugs or 5 US
gallon (5 x 3.8 litre) pails. Any remaining oil may be
used for ‘top-ups’.‘
The ‘MK-D20’ Maintenance Kit includes:
(2) DEV-3000-K1 2 x 1 Gal. of Synthetic Oil
(2) DSC-002196 Air Intake Filter
(2) DSC-002197 Oil Filter
(1) DSC-001148 Air/Oil Separator Filter
Do not attempt to operate the Unit without
first checking whether there is oil in the Oil
Reservoir. Add oil as required. Serious
damage may result from use, however
limited, without oil.
Use of improper oil may negatively affect
Compressor performance or shorten Unit life.
Resulting problems are not covered by the
DV Systems Inc. Air Compressor Warranty.
Condensation (water) may form in the Oil
Reservoir with the oil. If this occurs, as the
water will tend to settle on the bottom of the
Reservoir, drain the water from the Reservoir
until you notice oil draining. Top up the
Reservoir with new oil using only the DV
Systems ‘DEV-3000’ oil.

D20, D20VSD, D20TD, D20TDVSD-C
Feb ‘14
- 10
-
Installation - Electrical
When making power and control wiring connections, please observe the following precautions:
Ensure that all wiring, fusing, etc is done in a manner that meets with the appropriate codes and
regulations.
See the sales drawings and electrical schematic contained in this manual for information about Motor
nameplate amps, this used to determine the appropriate Disconnect / Breaker and Wiring sizes.
General Information
.
It is your responsibility to ensure that the Compressor
Unit is electrically connected in a safe and correct
manner. Any electrical work should be carried out
by a competent Electrician, and be done in such
a way that it meets all applicable Codes and
Regulations.
Ensure that a suitable Fused Disconnect or Breaker
(by others than DV Systems) is installed in the
electrical supply before the Compressor Unit.
The sales drawing found at the back of this booklet
indicates the amp rating for the Unit. This information
is required in sizing a Disconnect, Fuses, and/or a
suitable Breaker. As well, an electrical schematic is
enclosed for reference.
Electrical wiring and conduit from the building supply,
through the Compressor Cabinet, and to the Switch
in the Compressor Control Panel, must be rated for
110°C or higher.
Failure to observe any of the above precautions could result in severe personal injury or death,
and/or damage to the Unit.
Failure to correctly connect the
Compressor to your building's electrical
services may result in serious personal
injury or damage to the equipment.
Install all covers and panels before
applying power to the Unit.
Before servicing the Unit, ensure the
power source has been shut down and
locked off.
Read and understand the information
contained in this manual before installing
or operating the Unit.
Wiring Practices
.

D20, D20VSD, D20TD, D20TDVSD-C
Feb ‘14
- 11
-
The Electrician is to bring
power to the Unit at the
Electrical Panel accessible
by means of opening the
Unit Side Door and Control
Box Cover as shown at
right.
Refer to the enclosed
sales drawing and
electrical schematic in
determining the correct
Disconnect / Breaker and
Wire size.
Installation – Electrical (cont’d)
Wiring must be done in a manner that the full Motor nameplate voltage +/- 10% is available at the Motor terminals
during start-up. Contact your local Distributor or Service Centre if additional information is needed.
The Warranty that exists on the Electric Motor is that of the original manufacturer. In the event of a Motor failure,
contact your DV Systems Distributor or Service Centre for the location of the nearest authorized Motor Service
Centre.
It is critical that the Motor and Air End in the Rotary Screw Unit be turning in the correct manner. Irreparable
damage will be done if the Unit rotates in the opposite direction.
This unit equips with Advanced Phase Detection which prevents unit from rotating in the reversed direction. If the
following error is visible on the Screen and the Unit will not start, simply switch power leads L1 and L3. Press the
‘Reset’ key on the Controller to reset the error message.
E:0090 Phase Sequence
Note: If the Motor is replaced or Motor Leads are re-wired, visually check for correct Motor Rotation before
installing the belts.
Electrical Connection
.
Motors
.
Motor
.
Motor/Air End Rotation
.
Power Cable
Cooling Fan Rotation
.
To ensure that the Unit operates at optimum
temperatures, a Cooling Fan is located on the top
of the Unit to draw warm air from the Cabinet
Enclosure. It is imperative that the Fan rotate in
the correct direction.
A label inside the Unit as shown indicates the
proper Fan rotation.
If the Cooling Fan rotation is incorrect, change
two of the Fan leads connected to the bottom of
the Starter.
Wiring from
Cooling Fan
Wires to Starter
to change Fan
Direction

D20, D20VSD, D20TD, D20TDVSD-C
Feb ‘14
- 12
-
AC Motor Maintenance Instructions
Cleaning.
To ensure that the Motor operates at optimum temperatures and provides years of trouble-free service,
periodically clean the outside of the Motor Housing of any build-up of dust, etc. Though it is not anticipated that, if
installed correctly and in a suitable environment, there should be much build-up on the Motor, keeping the
Housing clean will allow the Motor to operate more efficiently.
Lubrication.
This is a ball bearing motor. The bearings have been lubricated at the factory. Motors that do not have re-grease
capability are factory lubricated for the normal life of the bearings.
Noted below is a chart outlining the interval at which the Motor should be lubricated, this based on the Motor
horsepower. This must be part of a regular maintenance schedule.
Motor HP Interval Weight of Grease Volume of Grease
in Hours Ounces Grams Cubic Inch Teaspoon
20 2,000 0.81 23.1 1.5 5.2
The above chart is based on a standard environment in which the Motor is operating of 40°C. For other
conditions, please multiply the Hour Interval from the chart above by the factor as indicated below.
Severity of Duty Factor Environmental Conditions
Standard 1.0 40°C, clean, little corrosion
Severe 0.5 50°C, moderate dirt, corrosion
Extreme 0.1 > 50°C, severe dirt, abrasive dust
Low Temperature 1.0 < 30°C
Lubricant.
Baldor motors are pre-greased, normally with Chevron SR #2. Equivalent and compatible greases are Texaco
Polystar, Shell Dolium R and Amoco Rykon Premium #2.

D20, D20VSD, D20TD, D20TDVSD-C
Feb ‘14
- 13
-
Do not attempt to operate the Unit without first checking
whether there is oil in the Oil Reservoir. Add oil as required.
Serious damage may result from use, however limited, without
oil.
Initial Start
-
up
1) Remove the Side Door, and ensure that there is
sufficient Oil in the Oil Reservoir. Refer to the
‘Lubrication’ section (page 9) in this manual for
proper type and level of Oil.
2) Do a visual inspection of the Unit, and ensure
that all fasteners are sufficiently tightened. This
must be done, as some fasteners may become
loose in transit.
Start-up Procedures
Do not place any materials in close proximity
to the Compressor. Placing materials against
or close to the Unit will limit the cooling
required, and could lead to premature failure.
3) Place the Fused Disconnect / Breaker in the ‘On’
Position. Check that there is power to the
Controller.
4) During normal operation of the Unit, keep the
Access Panels closed at all times.
5) Ensure the Ball Valve on the Unit is closed, press
the ‘Start’ Button, and run the Unit up to
maximum pressure. The Unit will run up to
approx. 110 psi, at which point the Motor will
continue to run but not compress air.
6) Once the Unit reaches 110 psi, it will idle for 2
minutes and shut off.
7) Open the Ball Valve slightly and allow the air to
bleed from the Tank. Once the pressure reaches
approx. 100 psi, the Unit will start and begin to
compress air after a short delay.
8) Measure the amp draw as the Unit reaches
maximum pressure.
9) Close the Ball Valve, allow the Unit to reach
maximum pressure, idle, and shut off. Once off,
check the various fittings etc inside the Cabinet to
ensure there are no internal leaks.
10) Once you are confident that there are no internal
leaks, the Unit will be ready for normal use.
Shut off all power to the Compressor Unit
before attempting any repair or maintenance.
Adjusting the settings of the Controller could adversely affect
the performance of the Unit. Only those individuals with
knowledge of the Unit should make any adjustments.
Unit Controls
Start Button
Allows the Unit to
start.
Stop Button
Use this to shut
the Unit off. Allows
the Unit to idle and
then stop after
several seconds.
Emergency Stop Bu
tton
Do not use to normally stop the Unit. To be used to
stop the Unit in emergencies only. Normal use will
damage electrical controls and Shaft Seal.

D20, D20VSD, D20TD, D20TDVSD-C
Feb ‘14
- 14
-
Preventative Maintenance Schedule
Noted on the following pages are general Maintenance guidelines based on average working conditions. Should
the Unit be worked under extreme conditions, please contact your DV Systems Distributor for further input. As
well, all maintenance/service work must be carried out by a qualified Technician.
The typical operating temperature of the Unit, this dependent on ambient temperatures, is between 70°C and
85°C.
If the operating temperature of the Unit is too low (less than 70°C):
condensation will build up in the system and mix with the oil, causing internal component problems in the
Unit
Change the ambient conditions to increase the operating temperature.
If the operating temperature of the Unit is too high (above 85°C):
the oil will oxidize and lose its properties, this causing internal damage to components as well
to combat this, the oil must be changed more often than noted below.
When servicing the Air Compressor, shut off all
power to the Unit, and drain it of air pressure.
It is the responsibility of the Compressor owner
to ensure that a regular Maintenance Schedule
is followed.
Note:
For Compressor Units used in an environment where the ambient temperature is above
90°F (32°C), the components marked with a ‘ # ’ (on the chart on the following page) must
be changed more frequently.
Regular Maintenance Items.
DV Systems offers a Maintenance Kit for your Unit,
namely:
MK-D20
Each Kit consists of the following items, these
suitable for approximately 4000 hours of operation.
(2) DEV-3000-K1 2 x 1 Gal. of Synthetic Oil
(2) DSC-002196 Air Intake Filter
(2) DSC-002197 Oil Filter
(1) DSC-001148 Air/Oil Separator Filter
Internal Access for Maintenance.
The internal components of the Unit are accessible
for servicing by way of removing the Front Door and
Side Door as shown.
The Belt access is by way of the Rear Panel.
Front Door
Side Door
Rear Panel

D20, D20VSD, D20TD, D20TDVSD-C
Feb ‘14
- 15
-
Preventative Maintenance Schedule (cont’d)
Maintenance Item: Daily
Maintenance Interval (in 000’s of Hours)
2 4 6 8 10 12 14 16 18 20 22 24 26 28 30 32 34 36 38 40
Compressor Room
Temperature Inspect Ambient Temperature should be between 10°C and 40°C (50°F and 104°F)
Cleanliness Inspect
Air Compressor Unit
Check Oil Level Inspect
Replace Oil # (See Note b) (1) X X X X X
Replace Oil Filter # (2) X X X X X X X X X X
Replace Air / Oil Separator # (3) X X X X X
Replace Air Intake Filter # (4) X X X X X X X X X X X X X X X X X X X X
Check Belt Tension X X X X X X X X X X X X X X X
Replace Belts X X X X X
Replace Tank Relief Valve X X X
Replace Solenoid (5) X X X X X
Rebuild Intake Valve (6) X X X X X
Rebuild Thermo Valve (7) X X X
Rebuild Minimum Pressure Valve (8) X X X X X
Motor Bearing Lubrication Refer to Motor Manufacturer’s Recommendations on Page 12
Notes: a) For Compressor Units used in an environment where the ambient temperature is above 90°F (32°C),
or b) where the Unit temperature runs regularly above 80°C (175°F), the components marked with a
‘#’ must be changed twice as often (example: in 4000 hours instead of 8000), and not as noted
above.
b) The DV Systems Oil used in the Rotary Screw Units is rated as an 8000 hour Oil. A complete Oil
change must be done every 8000 hours of Unit operation, or every 12 months, whichever occurs first.
Please refer to the Warranty on Page 26 for further information.
c) If a component, during a regular inspection, has proven to be defective or unfit for regular operation, it
must be repaired or replaced.
Parts and Repair Kits based on the above chart are as follows:
(1) Oil: 2 x DEV-3000-K1
(2) Oil Filter DSC-002197
(3) Air / Oil Separator Filter DSC-001148
(4) Air Intake Filter DSC-002196
(5) Solenoid DSC-002199
(6) Intake Valve Repair Kit DSC-002203
(7) Thermo Valve Thermostat & Sealing Ring: DSC-002201 & DSC-002608
(8) Minimum Pressure Valve Repair Kit: DSC-002202

D20, D20VSD, D20TD, D20TDVSD-C
Feb ‘14
- 16
-
Common Compressor Faults
Common Faults.
Noted below are the most common Faults experienced.
‘CSC300’ Alarms.
There is an issue with the Unit, but it will still operate.
Code: Description: Most Common Items to Check:
A:0083 Motor phase imbalance Check supply voltage, fuses and cable
A:0119 Delivery Pressure High Solenoid not working, Intake Valve Orifice clogged, Transducer dirty or faulty, pressure changed
incorrectly, alternate external pressure source
A:0129 Delivery Temperature High Ambient temp high, Unit dirty, low oil level, no air flow through Unit, Temp Sensor defective
A:2816 Power Failure Occurred Press ‘Reset’ Button and restart Unit
A:4819 Routine Service Due Service Unit and reset Service Timer (Page ‘P16’ on Controller)
A:4809 Grease Service Due Service motor and reset Grease Service Timer (Page ‘P16’ on Controller)
‘CSC300’ Shutdown Errors.
There is an issue with the Unit, and the Unit will not operate until the Fault has been addressed.
Code: Description: Most Common Items to Check:
E:0010 Emergency Emergency stop switch is pressed
E:0070 Fan Motor Alarm Check electrical connections
E:0082 Motor Overload Motor drawing high amps, low voltage, high pressure settings, low oil level
E:0083 Motor phase Imbalance Check motor connections in the control panel and motor connection box
E:0090 Phase Sequence Rotation of Motor wrong, sequence order of supply cable incorrect
E:0091-
0093 Phase L1/L2/L3 Fault Check supply voltage, fuses and cable
E:0115 Delivery Pressure Sensor Fault Transducer not making good electrical contact, or defective
E:0119 Delivery Pressure High Solenoid Not working, Intake Valve Orifice clogged, Transducer dirty or faulty, pressure
changed incorrectly, alternate external pressure source
E:0125 Delivery Temp Sensor Fault Temperature Sensor not making good electrical contact, or defective
E:0129 Delivery Temperature High Ambient temp high, Unit dirty, low oil level, no air flow through Unit, Temp Sensor defective
E:0902 Anti-Rotation Rotation of Main Motor wrong, Solenoid Valve not relieving pressure
E:1902 Inverter Fault Variable frequency drive tripped. Check VFD screen for more info.

D20, D20VSD, D20TD, D20TDVSD-C
Feb ‘14
- 17
-
Variable Speed Drive
Your DV Systems D20 DENE Rotary Screw Compressor Unit may have been equipped with a Vacon ‘Variable
Speed Drive’, or ‘VSD’. A Compressor with an integral VSD can handle the constant loads for an extended period
of time (running at close to 100% duty cycle), but it can also run at slower speeds to accommodate lower air
demands at other times of the day.
Variable Speed Drives can reduce the overall energy costs associated with operating the Compressor Unit by
simply controlling the speed of the Motor and Air End to match consumption. As Rotary Screw Compressors
using the variable speed technology match the varying air demands and therefore have the ability to impact your
energy consumption, some energy providers have offered rebates when these Units are purchased. Consult your
local energy provider to determine if this applies.
Shown below is a D20 DENE Unit with a Variable Speed Drive.
VSD Interface
The VSD Controller Interface is shown at right. It
provides a means of operating, monitoring, and adjusting
the parameters of the Variable Speed Drive.
Please note that adjustments to the parameters of the
Variable Speed Drive should be made only by qualified
Technicians, or with the guidance of factory trained
personnel. Incorrect adjustments will affect the
performance of the Unit, and could result in damage to
the Drive.
Variable Speed Drive
‘CSC300’ Controller
Control Panel

D20, D20VSD, D20TD, D20TDVSD-C
Feb ‘14
- 18
-
Variable Speed Drive (cont’d)
Operating Screen
Typical Drive Status Indicators on Screen

D20, D20VSD, D20TD, D20TDVSD-C
Feb ‘14
- 19
-
Fault
Code
1 Over-current. Current too high in Motor Cable. Check loading.
Check Motor.
Check Cables.
2 Over-voltage. The DC link voltage has exceeded the limits.
- too short a deceleration time Make deceleration time longer.
- high voltage spikes in supply Check input voltage.
3 Ground Fault. Insulation failure in Motor or wiring. Check Motor wires and Motor.
8 System Fault. - component failure Reset the fault and restart the Unit.
- faulty operation
13 Frequency Converter under Heatsink temperature is below -10°C.
temperature.
14 Frequency Converter over Heatsink temperature is over 90°C. Check the amount and flow of cooling air.
temperature. Overtemperature warning is issued when the heatsink Check the heatsink for dust.
temperature exceeds 85°C. Check the ambient temperature.
Ensure the switching frequency is not too high
in relation to ambient temperature and motor
load
15 Motor stalled. Motor stall protection has tripped. Check Motor and load.
16 Motor over-temperature. Motor is overloaded. Decrease motor load.
17 Motor under-load. Motor under-load temperature has tripped. Check load.
22 EEPRON checksum fault. Parameter save fault. Should the fault re-occur, contact the Distributor.
- faulty operation.
- component failure.
25 Microprocessor watchdog - faulty operation. Reset the fault and restart the Unit.
fault. - component failure. Contact Distributor.
31 IGBT temperature IGBT Inverter Bridge overtemp protection has detected too Check loading.
(hardware). high a short term overload current. Check motor size.
Make identification run.
32 Fan cooling. Cooling Fan of frequency converter does not start when Contact Distributor.
ON command is given.
50 Analogue Input Iin < 4mA. Current at the analogue input is less than 4 mA. Check the current loop circuitry.
- control cable is broken or loose.
- signal source has failed.
52 Keypad communication The data connection between the control keypad and the Check keypad connection and possible keypad cable.
fault. frequency converter is broken.
54 Slot fault. Defective option board or slot. Check board and slot.
Contact the nearest Vacon Distributor.
56 PT100 board temperature Temperature limit values set for the PT100 board Find the cause of temperature rise.
fault. parameters have been exceeded.
Fault Possible Causes: Corrective Measures:
Variable Speed Drive (cont’d)
Common VSD Fault Codes
Noted below are the most common fault codes that may appear on the VSD. For a more thorough list, please
check the manual which deals exclusively with the Vacon Variable Speed Drive and which accompanied the Unit.

D20, D20VSD, D20TD, D20TDVSD-C
Feb ‘14
- 20
-
Separator Filter and Refrigerated Air Dryer
Your Unit may be equipped with a Separator Filter and an ‘ASD Series’ Refrigerated Air Dryer Unit as indicated
below. These items are located in the compressed air lines after the air is compressed but before it enters the Air
Receiver. This allows for what is termed a ‘dry’ Tank.
More detailed information concerning the Dryer Unit is included in the Dryer manual. The information contained in
this manual is a ‘quick reference’ only.
To Air
Receiver
Dryer Controls
.
On/Off
Button
From Air
End
LED’s for
Compressor,
Drain, and Fan
Test/Programming
Buttons
Separator
Filter Unit Model and
Serial Numbers
Refrigerated
Air Dryer
Readout
This manual suits for next models
12
Table of contents
Other DV Systems Air Compressor manuals
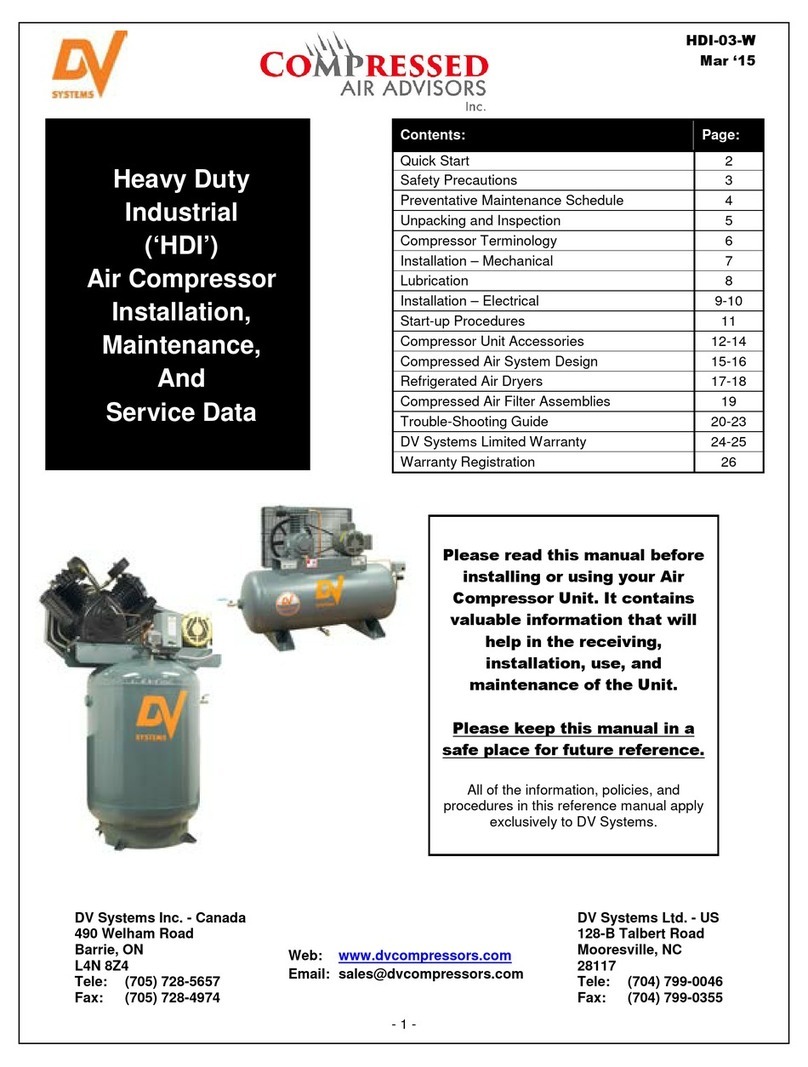
DV Systems
DV Systems HDI Manual
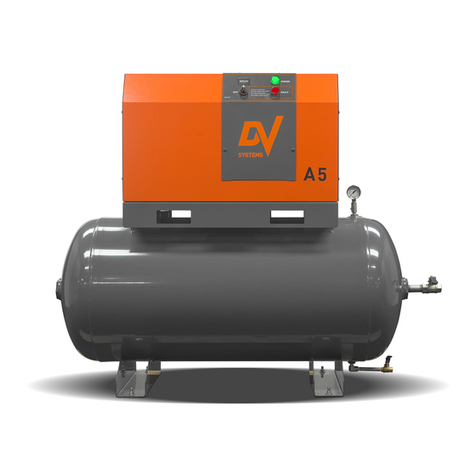
DV Systems
DV Systems A5 (T) Manual
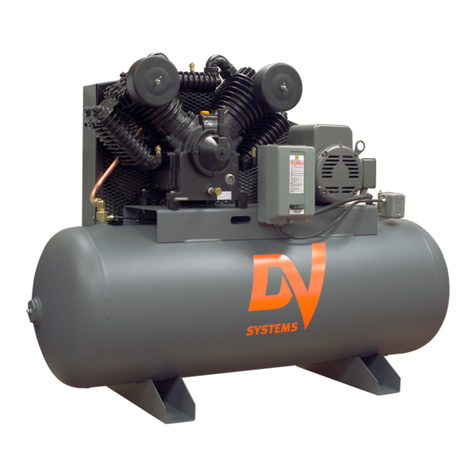
DV Systems
DV Systems IS5-4060-03 Manual
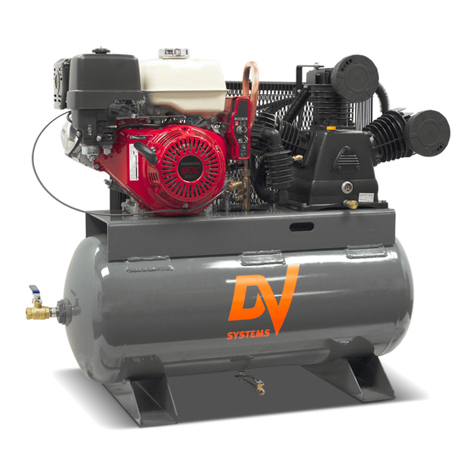
DV Systems
DV Systems IS13-5530 Setup guide
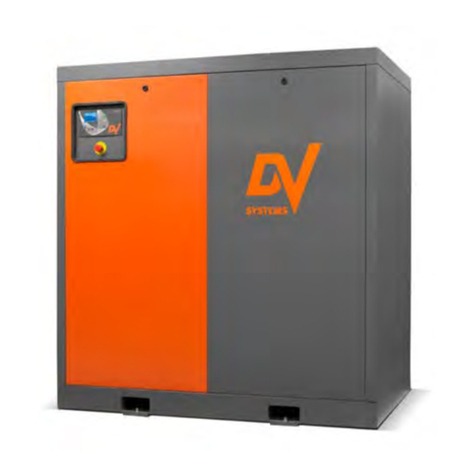
DV Systems
DV Systems H40, H50, H50VSD-C User manual
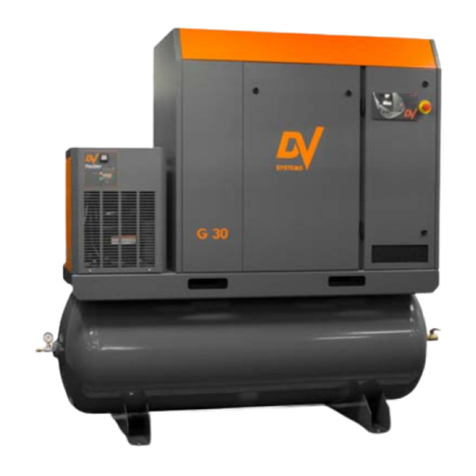
DV Systems
DV Systems G20 Manual
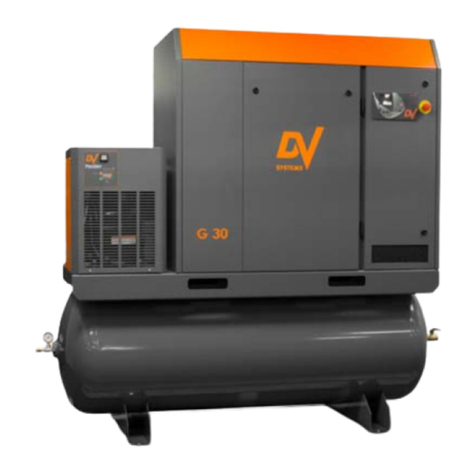
DV Systems
DV Systems G20 Installation manual
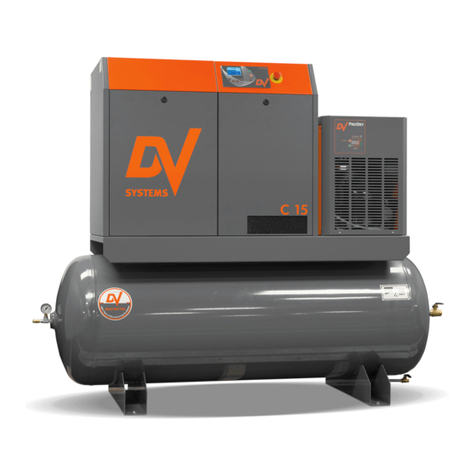
DV Systems
DV Systems C10 Installation manual
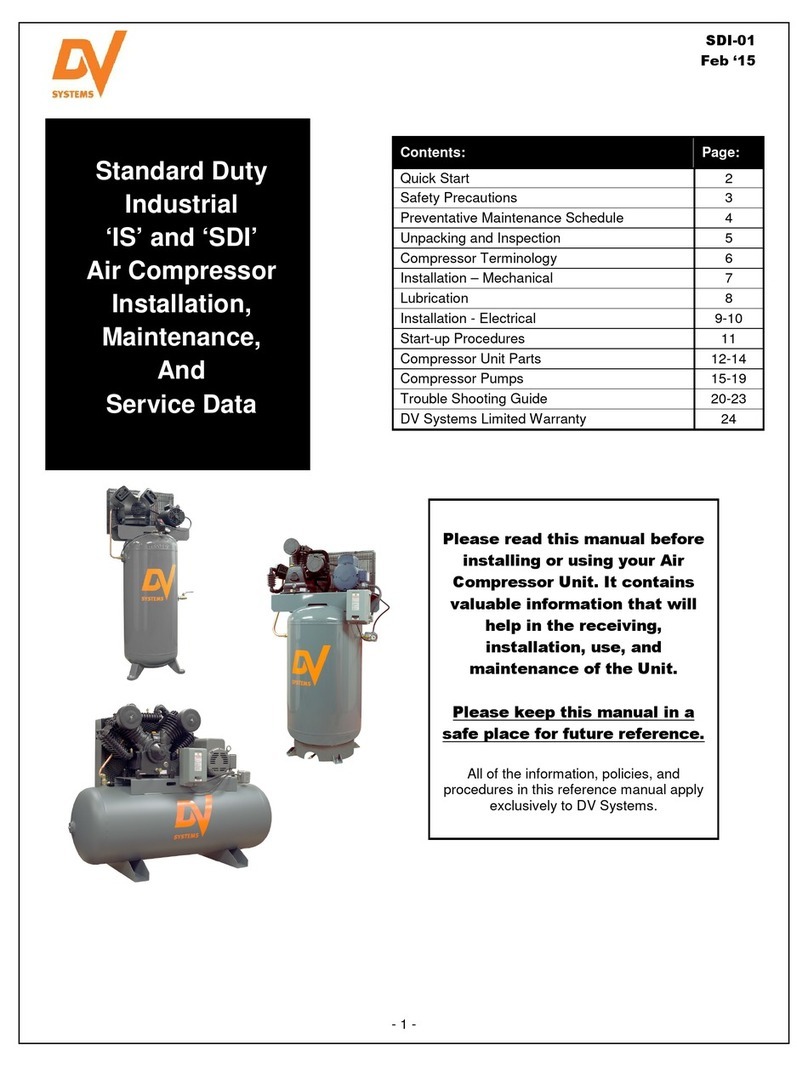
DV Systems
DV Systems IS Series Manual